新骨格インナーフレームボディーに対応した
溶接プロセスの開発
従来のボディー骨格は、ルーフとサイドパネルそれぞれをインナー部分とアウター部分で構成部品化(サブコンプリート)した後にメインボディー形成工程でフロアと結合してホワイトボディーを組む手法を取っていた。そのため、構成部品同士の結合はアウター部分同士のスポット溶接結合、もしくはインナー部分同士のボルト締結かMIG(Metal Inert Gas)溶接が基本となっていた。
また、インナー部分同士のボルト締結は、ボルトやナットに加えガセット(補強部品)も必要となるなど、重量と部品点数の増加が課題だった。
インナーフレームボディー構造*6は、ルーフとサイドパネルのインナー部分(骨格)のみを先にフロアと結合(インナーフレーム工程)。これにより、従来構造の構成部品ではアウターパネルが袋構造となり、インナーフレームが溶接できないことから、主要フレーム部分をボルトで結合していたのに対し、スポット溶接による直接結合ができるようになった。そのため、応力集中箇所の減少や歪エネルギーの分散が可能となり、結合強度が従来の方法よりもさらに向上。一体化による部品点数削減や薄肉化、ボルトやガセット削減による軽量化を実現した。
また、インナーフレーム工程ではインナー部分同士を直接位置決めして結合、続くメインボディー形成工程(GW工程)ではインナーフレームに対しアウターを外板基準で結合。これにより室内側、外板側の双方の位置管理による精度保証が可能となった。
さらに、インナーフレーム構造により、作業者によるボルト締結やMIG溶接をすべてロボットによるスポット溶接に置換でき、難作業をなくすことができた。また、多工程にまたがっていた溶接工程を1カ所に集約したことにより、生産性の向上にも大きく貢献した。
- :車両の基本骨格であるホワイトボディー形成プロセスをこれまでの外板を含め剛体化してからボディー形成する手法から、先に内部部品(インナー)を骨格としてフロアに結合し、骨格部分のみを形成した後に外板(アウター)を溶接するプロセスへと変化した構造
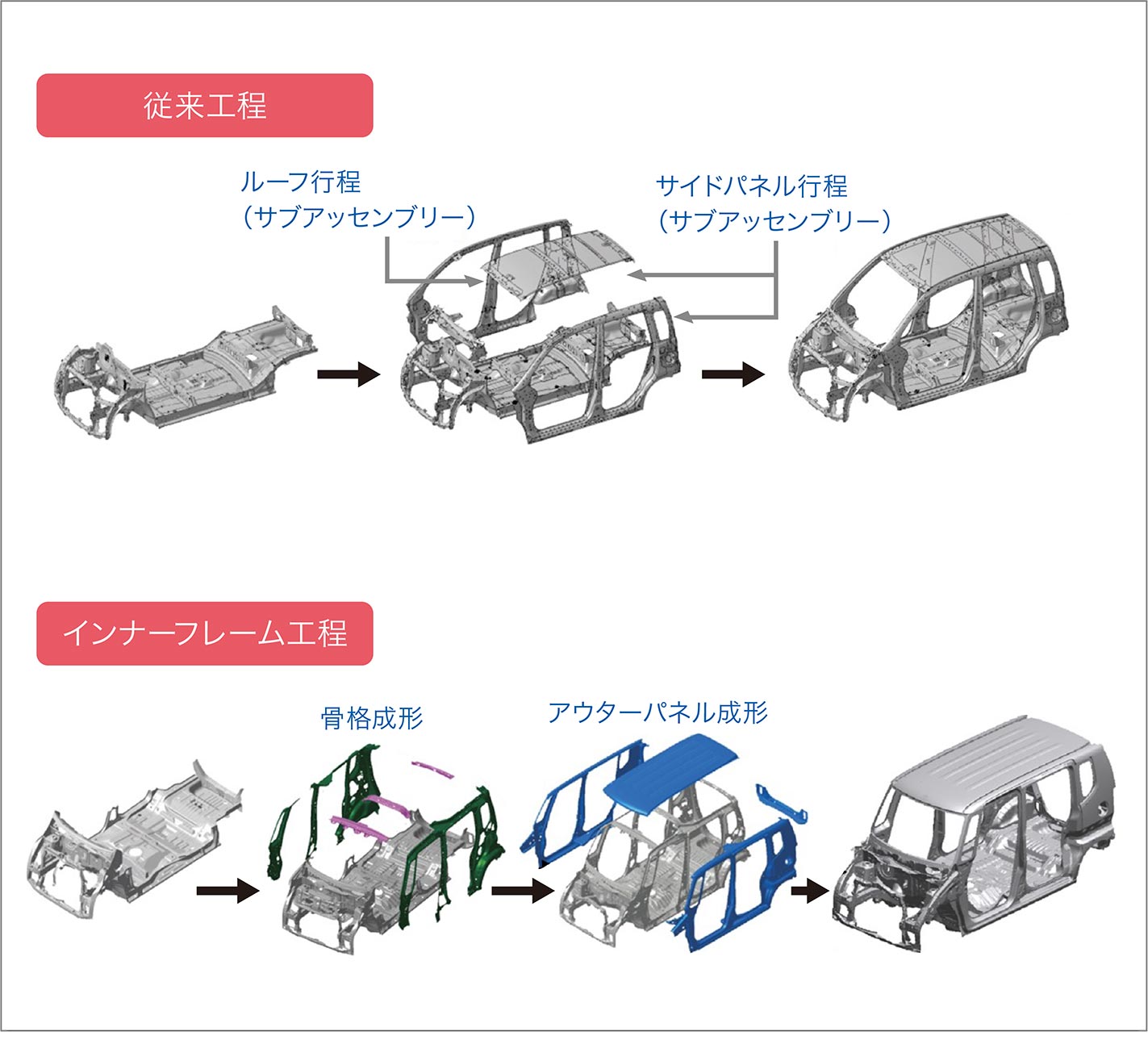
インナーフレームを採用した高効率継ぎ手骨格
設備・道具づくりから
製造DXによる理想の工場プロセスづくりへの転換
ホンダは生産分野において「ないものはつくる」の精神で設備・道具づくりを進め、ものづくりを進化させてきた。しかし、近年製品に求められる要求が大きく変わり、単一の設備・道具では解決できない問題・課題が数多く発生している。生産工場は車1台としてのトータル品質を捉える仕組みが求められるようになり、これらの変化に対応するため、デジタル技術を活用したさまざまな取り組みが進められ、近年急速な進歩を遂げている。
新機種導入時の溶接工程の高効率化
四輪車の生産においては、新機種導入時の溶接工程の高効率化を目指し、1990年代からデジタル技術を活用した溶接ロボットのオフラインティーチングシステム*7の開発に着手し、2001年から実施した体質改革「’01体改」によって導入が始まった。その後、2010年代からは、製品図データの3D化や、ロボットシミュレーターがUNIXワークステーションからWindows PCになりロボットシミュレーター導入コストが大幅に下がったことにより、オフラインティーチングの導入環境が整ってきた。また、シミュレーション技術を生かした試作車レスによる開発フローの適用により、新機種導入時間の短縮が必要となり、その主な施策としてオフラインティーチングの適用を拡大した。
こうした環境変化を好機と捉え、溶接の打点配分効率化システムや次世代溶接ロボットシミュレーションシステムの開発を加速。グローバルでの水平展開を念頭に置いた、デジタル技術の進化を含む製造DXの活用により、さらなる効率アップを図っている。
- :従来は現物のロボットで行っていたティーチング(教示)作業をソフトウェアのシミュレーションにより実現するシステム
高精度なボディーづくり
2017年ごろから高精度なボディーづくりを目的とする改革が始まった。それまでは部品ごとに精度を判断しており、量産時の部品精度のバラツキによる影響や組み合わせ時の精度に関する正確なデータを定量的には捉えられていなかった。そこで、デジタル化された製品図の3Dデータを活用し、良否判断ができるように計測・分析等が可能な複数のシステムを構築。さらに不具合の要因を飛躍的なスピードで顕在化させるコア技術として、寄与度分析エンジン*8を新たに開発した。これらのデジタルデータ化されたシステムによって、新機種の高精度なボディー製造が短期間で実現でき、グローバルでの高精度ボディーづくりに貢献している。
- :ホンダが独自に開発した 溶接工程における3500点以上に及ぶスポット打点から、オリジナルのアルゴリズムにより品質に関係の深い打点を100点程度まで絞り込み、さらに統計手法である正則化回帰によって原因を特定する上位5点まで絞り込むシステム。この5点を現物確認することで、従来では不可能だったスピードで不具合の原因特定が可能となった
ラインエンドテスターの開発・運用
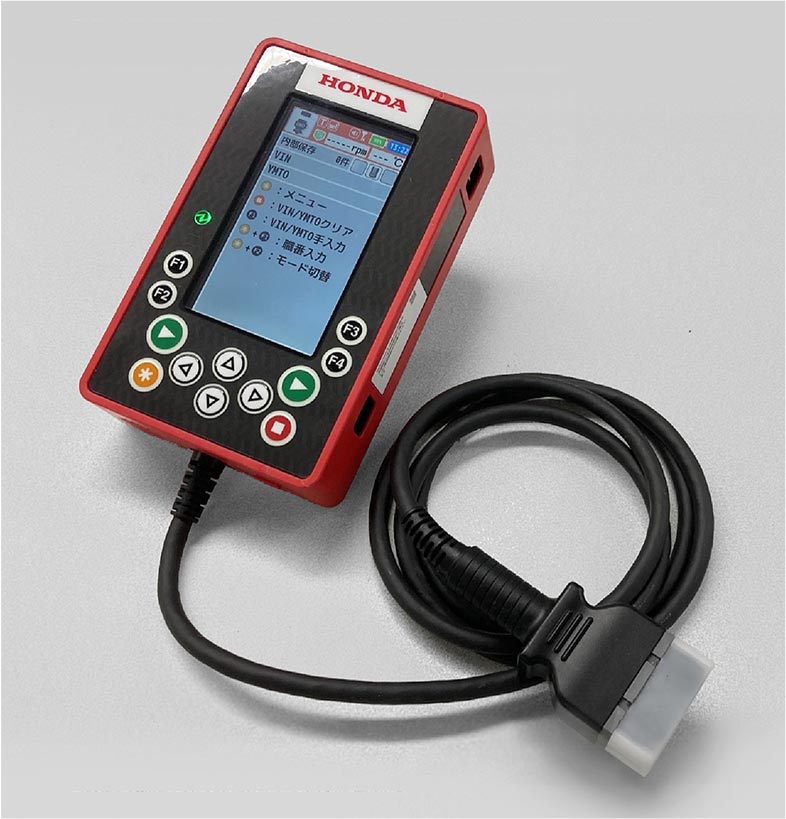
四輪車の電子制御システムの飛躍的な増大に伴い、それらの品質保証に対する効果的な検査のために、ホンダは独自の検査診断機、ラインエンドテスター(Line End Tester 以下、LET)を開発し運用している。
ホンダのLETの優位性は、同時に多くの検査が実施できることであり、これによりグローバル各拠点の量産ラインに電子制御システム検査が安く簡単に導入できるようになった。このLET技術は、ECUの機能学習・ECUへのプログラム書き込みにも活用しており、船外機やATV・二輪車の電装検査など、適用範囲を拡大させている。
官能評価の定量化を目指して
製造ラインの最終工程である検査工程(Vehicle Quality以下、VQ)には、測定装置などにより定量化された数値をもとに合否を判定する「定量評価」と、装置では判断できない、人によって判断する「官能評価」がある。官能評価は、お客様に沿った判断が可能なことや、複数の機種への対応が容易である一方で、人の入れ替わりや、地域ごとの違いによって均一な品質管理が難しく、品質不具合が市場で発生する可能性があった。この課題に対しては、視覚・聴覚といった人の感覚に頼った検査を、LETとインテリジェントパワーユニット(以下、IPU)などの電子制御部品との通信による定量的な検査に進化させたことで、LET検査の精度や効率が大幅に向上。それはラジオの受信感度検査などにすでに採用されており、さらなる検査精度向上、効率向上を目指し、電子制御システムの品質保証定量化が継続して進められている。
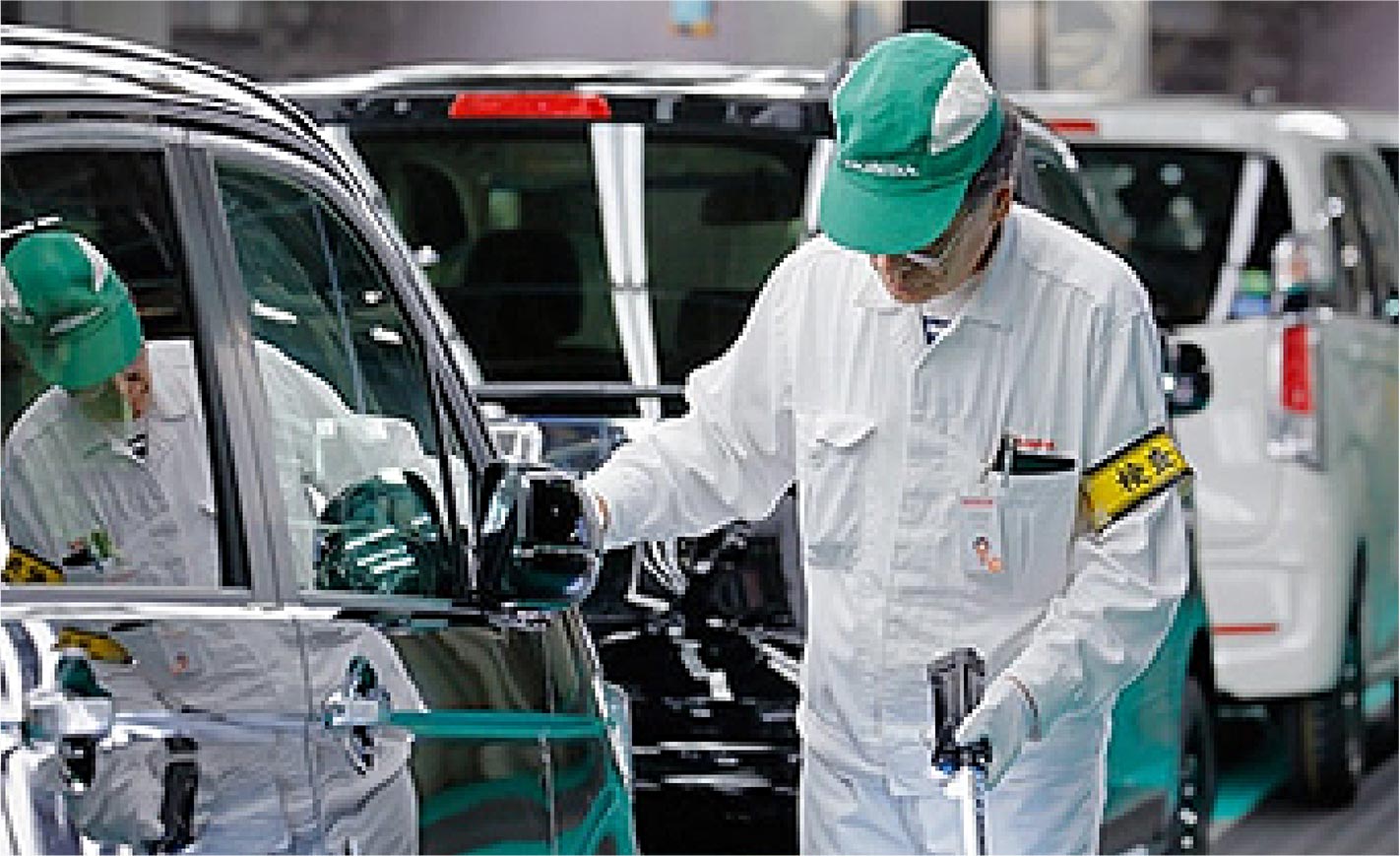
検査工程の中で行われる、人の判断による官能評価
LET技術を活用した作業の定量化と
検査の高精度化
LETは車両に直接接続され電子機器のほぼすべてにアクセス可能であり、さらに工場内の生産管理システムとも接続されることから、各工場の検査工程では、LETを用いて生産管理システムと同期しながら官能検査に加えて、トレーサビリティや法規適合検査を実施している。ほかにも盗難防止装置(イモビライザー)へのデータ書き込みやブレーキ液注入装置との連携、ハイブリッドカーなどの電動車に搭載されるIPUの事前検査装置、車両の総合検査を行うMDT(マルチドライビングテスター)*9、安全運転支援システムHonda SENSINGの検査装置などと連携している。LETの進化によって、車両側の情報と外部検査装置のゲートウェイとしてLETが機能するようになり、高精度な検査が可能となっている。
- :マルチドライビングテスター(MDT)は1989年に車両の新機能(TCS、ABS、LSD)の定量検査機としてスタートした、前後にローラーを持ち走行状態を再現して最終検査を行う装置。新機能追加や法令検査、新機能の学習などマルチな台上試験機として常に進化を続け、Honda SENSINGなどのADAS(運転支援機能)や、AD(自動運転)などの検査を視野に開発を続けている
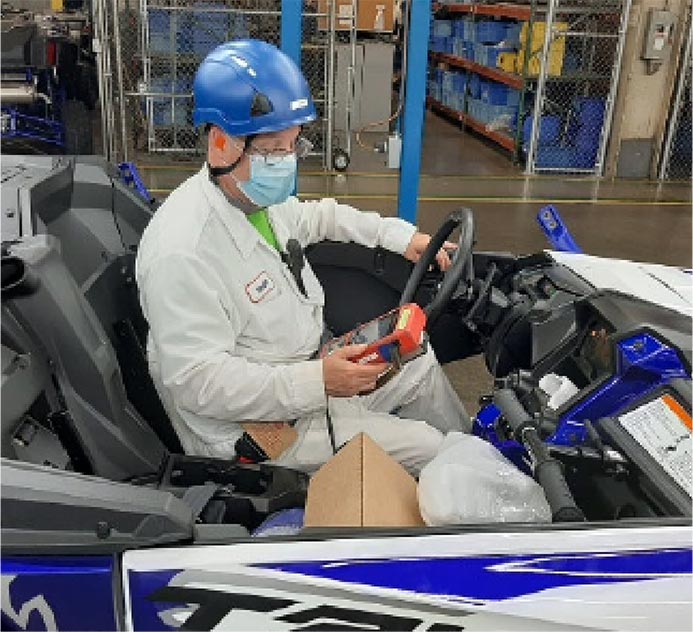
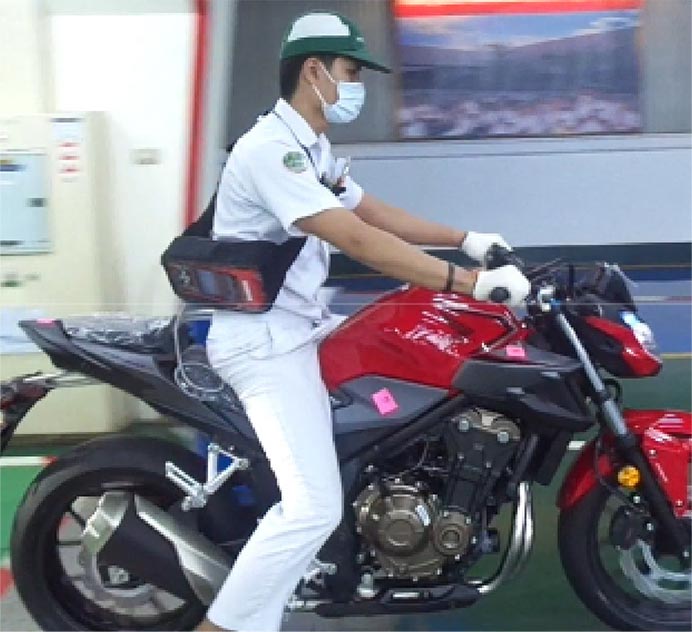
LETによる完成車検査
全世界同一品質の実現
VQにおける検査は完成車の状態で判断をしているが、その品質はすでに前工程の溶接や組み立てで決まっている。LETの進化によって、VQでの検査だけにとどまらず、作業者のケアレスミスの未然防止や従来では発見することが難しかった不具合の発見も容易となった。今後もデジタル技術をより一層進化させ、あらゆる作業の定量化を推し進め、定量化されたデータを活用し、工場全体の効率と製品品質の向上につなげていく。
競争力ある、強いものづくりの実現に向けて
ホンダのものづくりを支え、製品の高性能化・高機能化とともに進化と改革を続けてきた生産技術。今後ますます加速する電動化や環境問題に対し、ホンダが存在を期待される企業であり続けるためには、人々に必要とされる製品を具現化する生産技術の進化が不可欠である。
生産技術統括部 部長の山本創一(2023年3月当時)は、競争力ある、強いものづくりの実現に向けて次のように語った。
「ホンダの生産技術思想に、『世の中にないなら自分たちでつくる』との言葉があります。創業当初、自動車工場の設備を手がける専業メーカーも少なく、性能や品質的にも満足な物が入手できなかったこともあり、私たちの先輩たちは工場の生産体質に合う設備や金型を自らの手で具現化し、ホンダのものづくりに貢献してきました。四輪車後発メーカーのハンディを知恵と技術で克服した誇らしい歴史だと思います。
しかし、100年に一度と言われている自動車産業の大変革期を迎え、われわれに求められる生産技術も大きく変化しており、競争力ある商品を具現化する『コア技術やコア設備の開発』から、『開発・生産準備・調達・量産・リサイクル』まで一連の工程をつなぎ、生産プロセス全体を改革することが求められています。この大きな環境変化に柔軟に対応するためには、ホンダ生産技術のDNAをベースに、部門を超えた幅広い連携や他社との協業も視野に入れた戦略・体制を構築し、推進することが重要となります。
これから仕事の進め方が大きく変化していくことが予測され、何かと戸惑うことが多いかもしれません。しかし、仕事が広がり、求められる技術が変わっても、それを支えるエンジニアの本質は変わりません。物事の本質を見抜く力と最後まで諦めない姿勢を身につけ、会社が目指す方向を理解した上で、自分の役割と課題に真摯に向き合い、ものづくり改革を実現した時に得られる大きな達成感を味わってほしいと思います」
世界の主流となったモヒカン構造
1300クーペのルーフ両サイドは、スポット溶接された溝に組立工程でラバーを取り付ける構造が採用された。そのデザインがヘアスタイルの“モヒカンカット”に似ていたことから「モヒカンルーフ」と呼ばれるようになり、以後ホンダ車の特徴となった。
これは当時ボディーのサイド面を構成する部品が複数に分かれておりそれらを接合していたが、ボディー精度の問題や、つなぎ目を滑らかにするためのはんだ作業(はんだで隙間を埋める)など手間がかかる上にはんだ作業時の煙を吸い込むのが人体に悪影響を与えるため、その作業をなくしたいとの想いからだった。モヒカン構造を採用したことにより、ボディーの寸法精度は上がり作業工数も減り生産性が向上。さらに人体に有害な作業もなくなったのである。現在では世界で多くのメーカーがこの方式を採用しており、ホンダの先進性を物語る一例と言える。最新モデルではレーザー溶接によりモールディングも不要になりデザイン性も大幅に向上している。
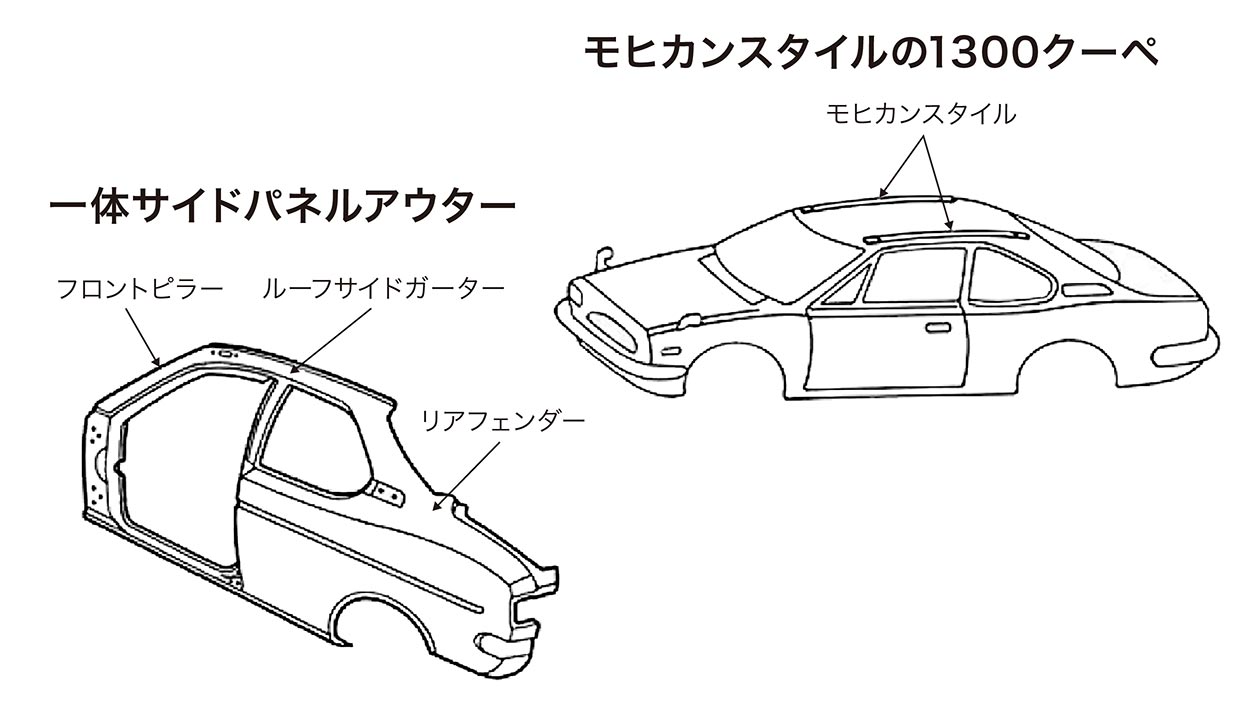
1300クーペで採用され、ホンダ車の特徴となっただけでなく、その後は多くの自動車メーカーが採用することとなった「モヒカンルーフ」
量産車世界初となるオールアルミモノコックボディー量産技術
初代NSXに採用した量産車で世界初となるオールアルミモノコックボディーの開発は、HGT・EG・材料メーカーが一体となって進められた。EGでは、プレス成形にふさわしい延性に優れたアルミ素材や、部材に破断や面ひずみがなく均一な張力を与える成形技術を開発。ボディー溶接設備では、通常のスチールボディー溶接に対し、ガンアームの高剛性化や大電流化を実現し、アルミ用のスポット溶接ロボットシステム・GWシステムなど、アルミボディー溶接システムを完成。スチールボディーの場合と比較して、ホワイトボディーだけで140kg、総重量では約200kgもの軽量化実現に大きく貢献した。
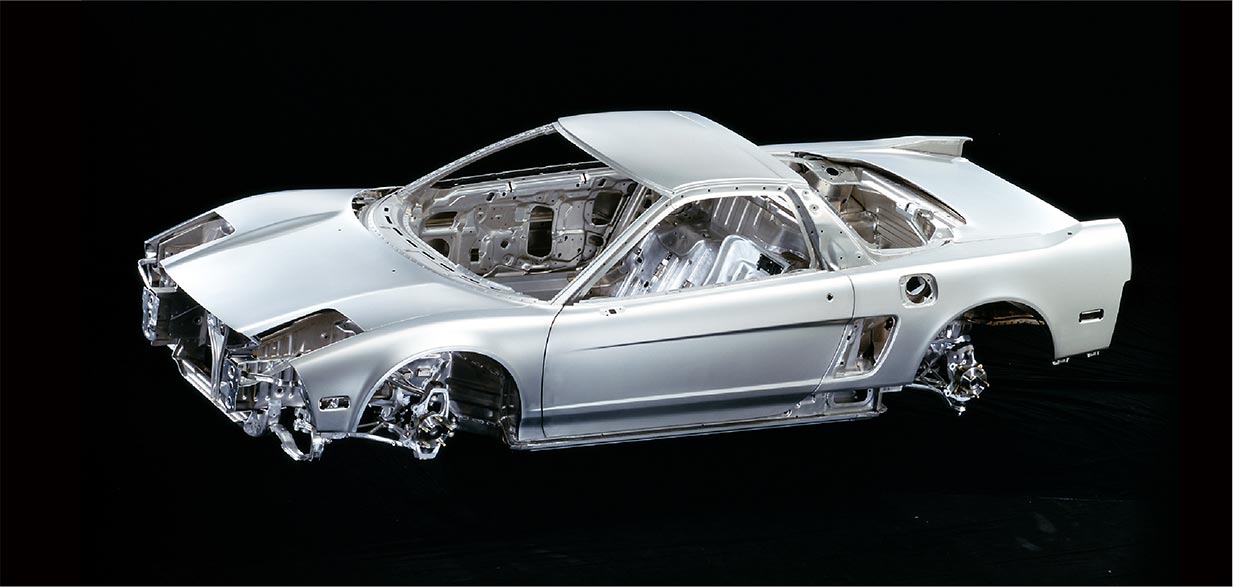
HGT・EG・材料メーカーが一体となって進めた、量産車世界初となったNSXオールアルミモノコックボディー
共創によって実現した
ハイブリッドシステム用「HAWモーター」の開発
発電用と駆動用の2モーターを用いたハイブリッドシステムi-MMDは、2013年6月に販売されたアコード ハイブリッドに初搭載された。しかし、このi-MMDは、一般的な丸銅線を使った分布巻きコイルのモーターを採用しており、他の機種、特にコンパクトクラスへの搭載を可能にするには、より小型のモーターを開発する必要があった。
HGTでは、2010年ごろより、分布巻きと並行して、角型断面の銅線を加工してコイルを組み上げるセグメントコンダクター巻きモーターの開発を始めていた。時を同じくしてEGでも、軽量・コンパクトで生産コストの低減も可能という、製法上の利点に着目し、同モーターの具現化を検討し始めていた。
このモーターを完成させ量産につなげるために、HGTとEG、さらに浜松製作所も加わった共同チームを発足させた。世界最高効率を目指した「HAW(Honda Advanced Winding)モーター」と命名して開発を加速させ、角形銅線の高密度な成形技術や絶縁皮膜の塗布技術などの確立によってこれを実現した。HAWモーターは分布巻きコイルモーターに対して、24%の小型化、23%の軽量化、37%のコストダウンを達成したのである。
HAWモーターを採用した進化型i-MMDは、2016年2月発売のオデッセイに搭載された。2020年2月には、e:HEVと名前を改め、フィットにも搭載され販売を開始。ハイブリッド車のみならずホンダ初の量産バッテリーEV、Honda eにも搭載され、以後さまざまな機種へ展開されている。
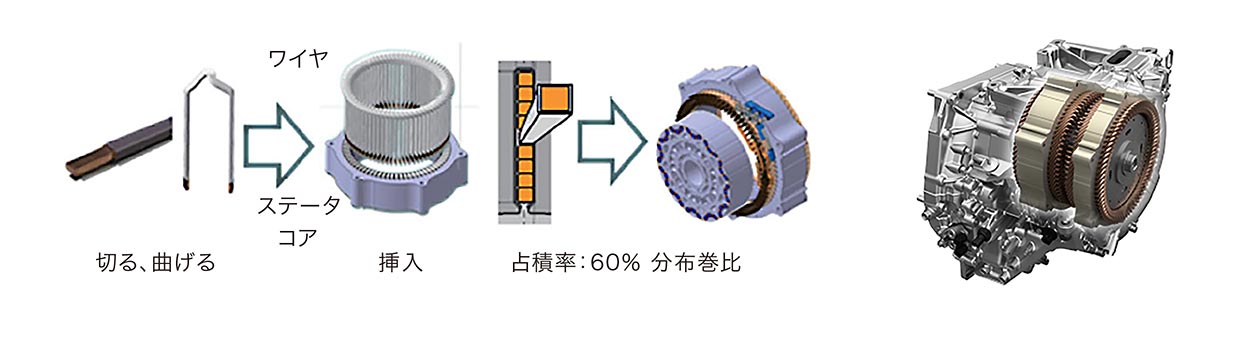
EG・HGT・浜松製作所との共創によって開発されたHAWモーターi-MMDは従来のi-MMDに比べて24%の小型化・23%の軽量化・37%のコストダウンを達成した