Sustainable impacts 2022/10/17
Hondaの技術力とグローバル展開で課題を解決せよ──新技術を導入した3人の軌跡
効率的な生産を実現するために、Hondaではコストダウンにつながる新技術開発について日々議論が重ねられています。開発した技術は、グローバルの生産現場に展開していきます。いくつもの壁を乗り越え新技術導入を達成した3名が、プロジェクトを振り返った今の想いを語ります。
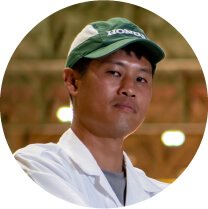
村田 啓輔Keisuke Murata
四輪事業本部 ものづくりセンター生産技術統括部 車体生産技術部 車体塑型技術課
2007年Hondaに新卒入社し、金型開発に携わる。MIC技術のグローバル導入のため、2018年4月に現在の所属となりプロジェクトに参画。北米に導入するチームで、各拠点への説明や調整を進める。
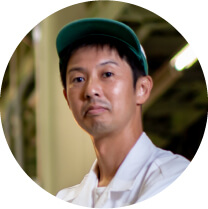
渡辺 智力Chiriki Watanabe
四輪事業本部 ものづくりセンター生産技術統括部 車体生産技術部 車体塑型技術課
前職で家庭用エアコンの設計に携わった後、2007年Hondaに中途入社。2015年のMIC技術開発プロジェクト開始当初からサブプロジェクトリーダーとして要素技術の開発に取り組み、グローバル展開までを担当した。
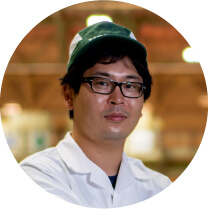
渡邊 公司Koji Watanabe
四輪事業本部 ものづくりセンター生産技術統括 部車体生産技術部 車体塑型技術課
HondaのバイクやF1が好きだったことがきっかけで、2010年Hondaに新卒入社。車の内装デザインに携わりたいと希望し、生産技術に配属され経験を積む。2015年のMIC技術の開発プロジェクト初期から参画し、導入までを担当した後、内装の加飾に関わる。
コスト削減とデザイン性向上を両立させる新技術を開発
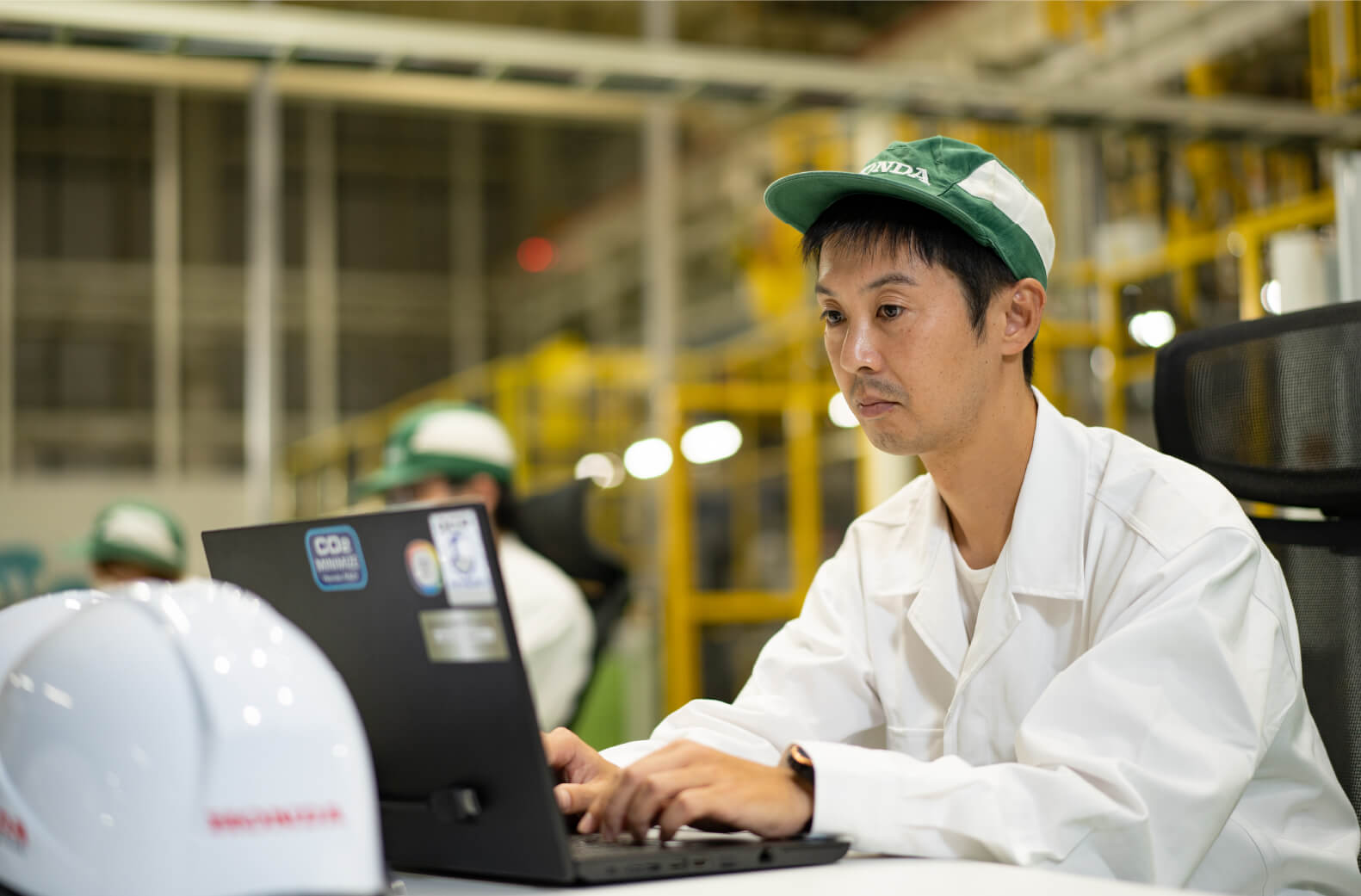
四輪の車体塑型技術課では、2015年頃からインストルメントパネル(インパネ)のコストを削減しながらデザイン性を高めるプロジェクトを進めてきました。村田、渡辺、渡邊の3人は、技術開発やグローバル導入に尽力した社員です。
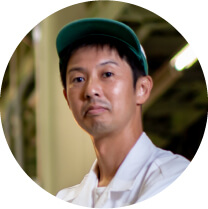
「クルマのインパネは、樹脂製のシートを大きな加熱炉で温めたあと金型で挟んで真空成形します。従来の方法では温めたシートが金型に当たる際、部位によって局部的に伸びてしまうことが難点でした。
今回導入したMIC(Multitask In Mold Clamp)技術導入CP(Crush Pad)製法と呼ばれる新技術では、今までより小さいシートを伸ばして金型の形状に沿わせるように折り曲げることで、均等に伸ばしながら破れないように成形できるようになったんです」
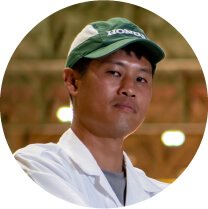
「従来は金型サイズより大きなシートを使っていたのですが、製品に使用しない70%ほどの部分は捨てなければならなかったんです。それでは歩留まりが悪いという問題がありました」
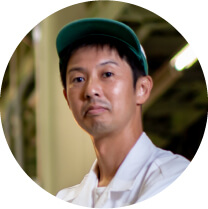
「また、伸び方が部位によってばらついているとデザインの制約にもつながります。インパネに分割ラインができてしまうと、デザイナーはノイズに感じてしまう。新技術を取り入れることで、コストダウンをしながら爽快な視界を叶えるデザインを実現できるようになりました」
MIC技術が確立したあとは、各拠点の設備を改造して導入することになりました。グローバル導入のタイミングで村田もプロジェクトに加わり、3人が北米への導入チームとして協力しました。
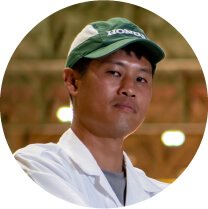
「モデルチェンジ前の機種を量産している拠点で、量産影響を最小限に抑えつつ低コストで新技術を導入する必要がありました。改造する拠点は日本とアメリカ、タイ、カナダの4カ国で、新規で導入する拠点はメキシコ、中国でした」
量産設備の改造はクレイジー?各拠点と仕様の調整に尽力
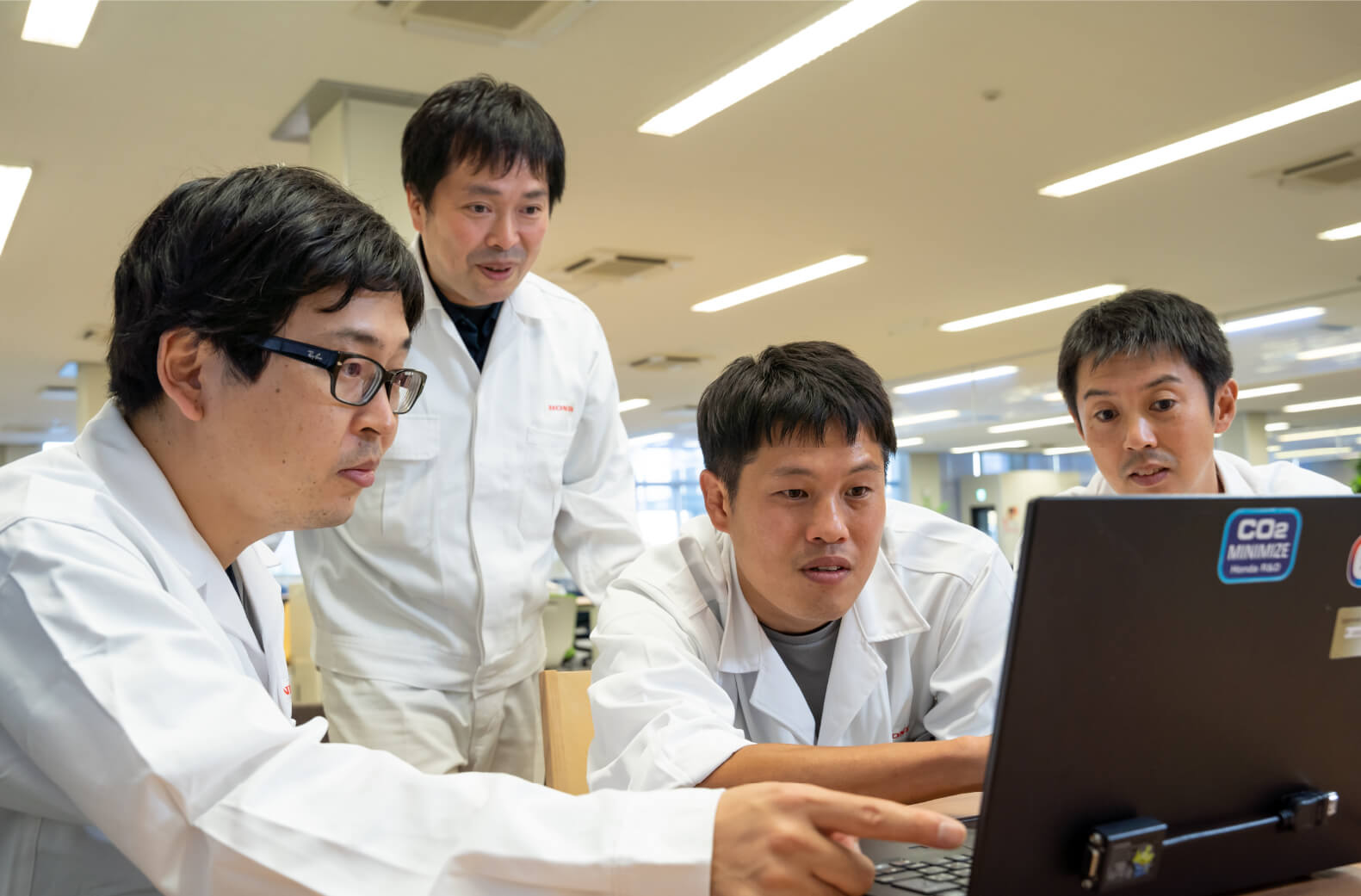
北米チームの3人は、異なる生産拠点を担当しながらも一緒にプロジェクトを進めていました。振り返って大変だったことは、量産に影響を出さずに設備を改造することでした。
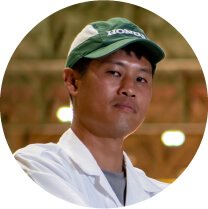
「今回は低コストを目指したプロジェクトだったので、新しく設備を作るのではなく従来の設備を改造する必要があったんです。設備は平日量産で使っているため、改造するなら土日や大型連休に仕上げなければいけません。
連休のタイミングは限られていたので、2つの拠点で同時期に改造しなければならず、一時的にかなりの負荷がかかることもありましたね」
さらに、各拠点との調整も難航したポイントです。
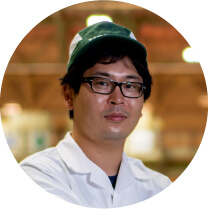
「たとえば生産ロボットひとつとっても、使いたいロボットが各拠点で違うんですよね。各拠点では今まで自分たちが使っていたロボットのメーカーに合わせたいけれど、我々としてはグローバルで統一仕様にしたい。その点をすり合わせ、最適な仕様にするための調整をすることに1番苦労しました」
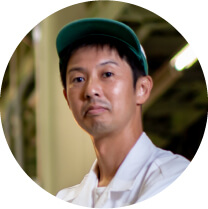
「これまでの技術導入では生産拠点ごとに最適化したことで、それぞれの拠点で独自のトラブルが発生し、なかなか収束しないケースがありました。そこで各拠点から意見を抽出しながら仕様を統一して、問題を解決しようとしたんですよね」
そもそも、「既存の量産設備を改造するのはありえない」という意見も各拠点から噴出しました。
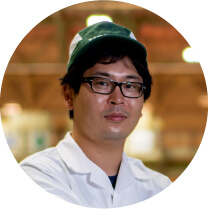
「プロジェクトリーダーが『コストダウンできるように設備を改造したい』と提案したとき、現地の方からクレイジーだと言われていましたね。Hondaの量産設備は、1分止めたら大損害になります。そのリスクがありながら改造するのはおかしいだろうと言われました。
また、設備の改造にあたっては、シートを高温に加熱する設備の中でシートを引っ張る必要があったのですが、熱があるところで動かすのはセオリーからするとご法度に近いんです。できるわけがないだろうという意見が、現地メンバーから寄せられました」
実機を見せて検証を重ね導入へ──成功例として評価いただく
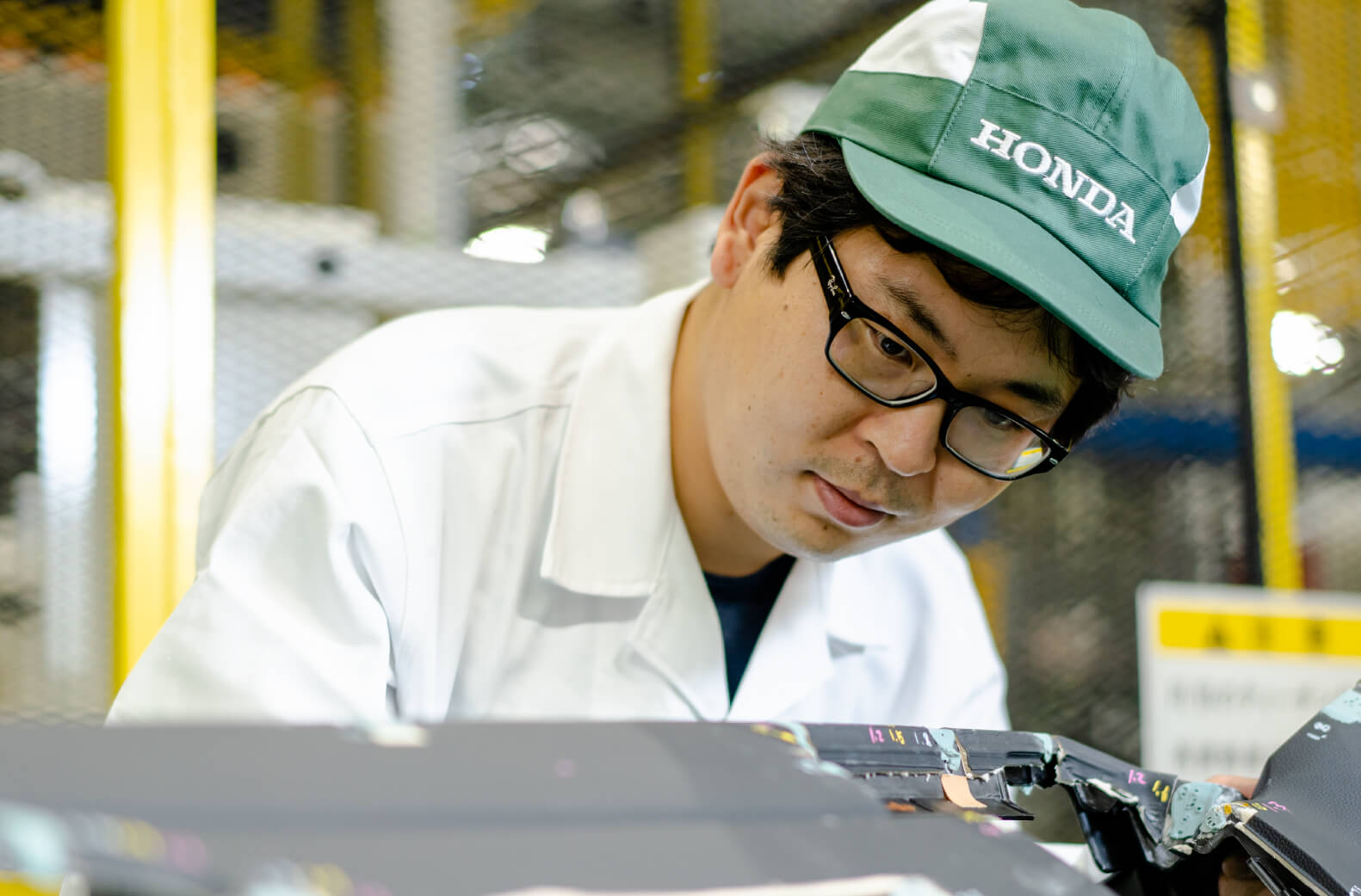
導入計画を提案した当初は、各拠点からすんなりと受け止めてもらうことができませんでしたが、日本にある同様の設備を改造し、現場・現物・現実の三現主義で実現性を証明しました。
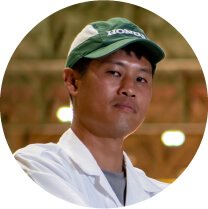
「栃木県にある事業所で設備を作り、カナダやアメリカのアソシエイツを招待して現物を見てもらいました。そこから『ここが気になる』と言われた箇所を一つひとつ丁寧に説明し、それでも納得できないと言われればさらに検証を重ねるという工程をひたすら繰り返しましたね」
毎週2時間のオンライン会議を2年弱続け、2019年8月から導入をスタート。夏休みや年末年始など連休日程でスケジュールを引き、設備改造やシステムアップに立ち会いました。最初に埼玉県寄居町にある工場への設備導入が行われた際、3人は感慨深さと不安の両方を抱えていたと振り返ります。
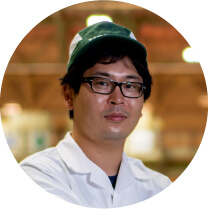
「寄居では改造してすぐにMIC技術を入れるのではなく、量産を続けながら設備を改造してMICをセットアップする形を取ったんです。そのため、自分が入れた設備に不具合がないか冷や汗をかきながら成形する様子を見ていました。実際に何度かトラブルが発生し、持ち帰って期限までに原因を検証しなければならなかったのはプレッシャーでしたね。
ただし、その経験あったからこそ、その後、海外拠点に導入するとき問題が発生しないように対処することができました。さまざまなケースに対応できたことは、結果的によかったと思います」
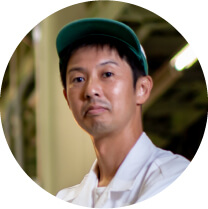
「自分たちが開発した生産技術がようやく形になり、今後製品を作り出して世の中に出回っていくんだと感慨深い想いがありました。その一方で、今後何も問題が出なければいいなとも思っていましたね」
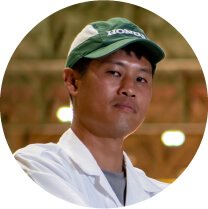
「私は北米拠点の改造直後が1番ヒヤヒヤしていましたが、改造が終わって既存の量産品がちゃんとできていると知り一安心して、そこからも大きなトラブルがなかったので安堵しました。現地メンバーは改造前までは半信半疑でしたが、導入が終わってからはトラブルの報告もなかったので、『ほらみろ、できただろう』と思っていました(笑)」
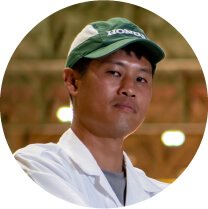
「寄居で設備を導入してから各拠点にフィードバックするやり方は、やはりよかったですよね。今回は標準化できていたからこそ、寄居で起こったトラブルを解消し他の拠点での設備導入時に、同様のトラブルの発生を防ぐことができました。マネジメント層からも、グローバル展開の成功例として認めてもらえているようです」
想像できることは、何でもできる。経験を活かして新技術の導入を進めたい
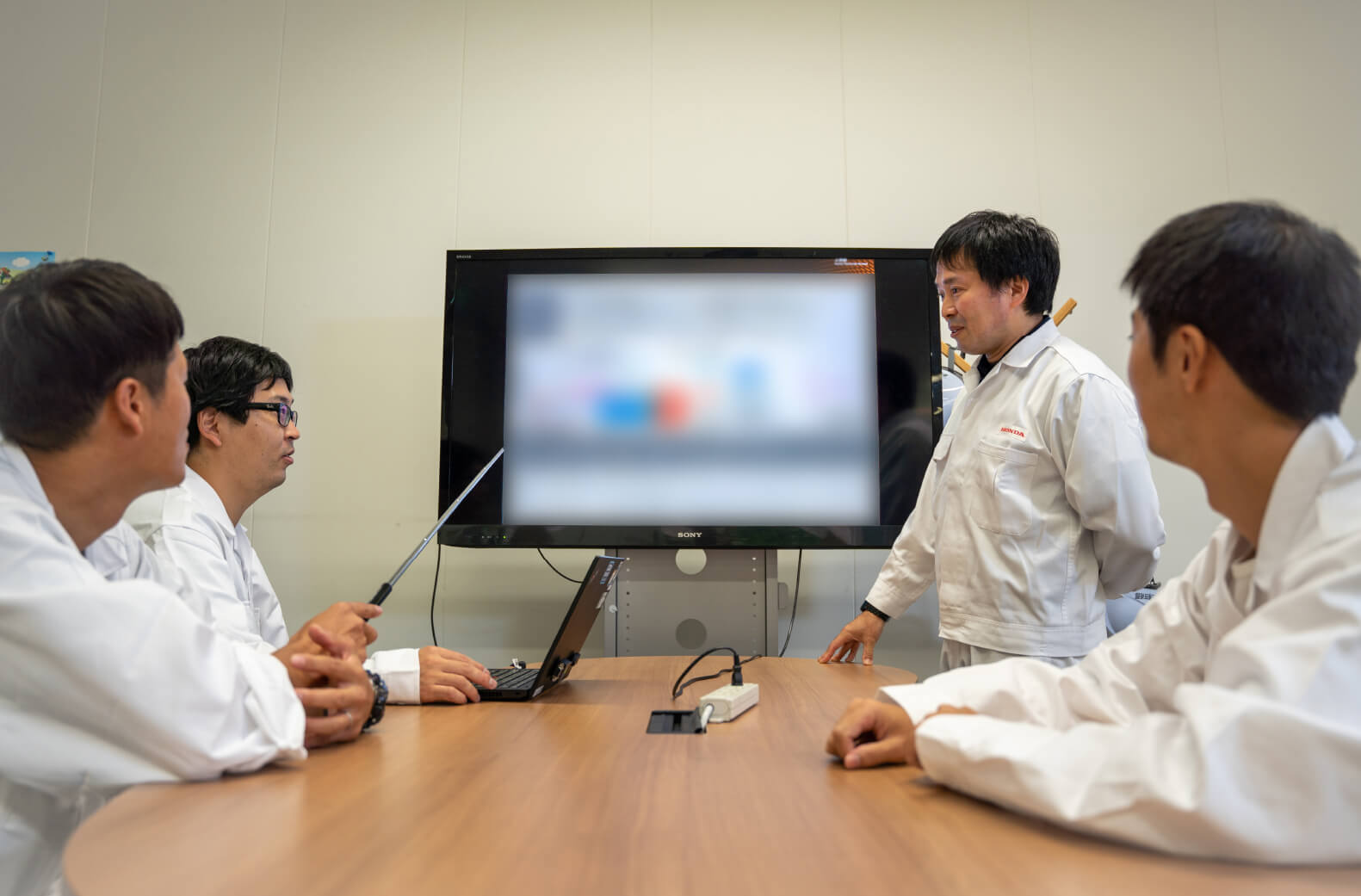
困難な状況でもプロジェクトを遂行しようと3人が思えたのは、それぞれモチベーションがあったからでした。
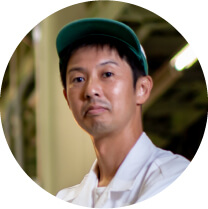
「量産設備の耐久性は懸念していましたが、新技術のもたらす効果には確信を抱いていたので絶対導入しようと強い気持ちを持っていました。グローバルに導入することで海外出張の経験が積めることも、魅力だと感じていましたね」
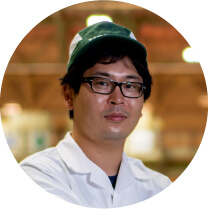
「当時プロジェクトリーダーが『想像できることは何でもできる』と言っていたんです。シートを加熱して金型に当てて折り曲げたり、加熱する枠を動かしたりするのは想像できるので、絶対実現できる。実際にそう考えて一つひとつ問題を解決していったら具現化できたのが印象的でしたね」
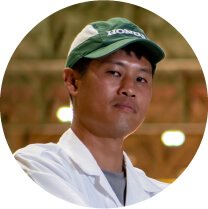
「プロジェクトリーダーの求心力は強かったですね。私も『せっかくHondaで働いているんだから、グローバルでの導入をやらないと楽しくないよね』という言葉に共感して、はじめてのグローバル導入をなんとかやり切ることができました」
今回のプロジェクトを経験したことで、3人はそれぞれ今後のビジョンを明確にしています。
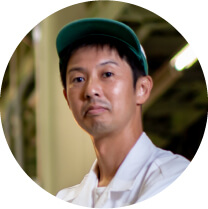
「今回自分たちが経験できたことを、もっと若い人たちにもしてもらいたいですね。さまざまな技術をグローバルで標準化し、導入する。このチームのメンバーは大変な経験をして耐える力、やり抜く力も鍛えられたので、今後もさまざまな壁を乗り越えていけると思っています」
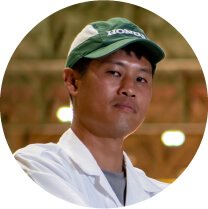
「これからも新技術を導入して、新しい工場体質に変えたり今まで作れなかったものを作ったりと、より良い姿を描けるようになれたらいいなと思います。今回の経験は大変でしたが、グローバルに新技術を導入するやりがいや楽しさを実感できたので、今後も続けていきたいですね」
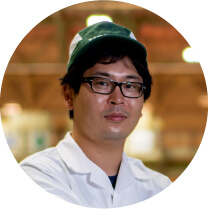
「私は入社時に『内装を格好良くしたい』と希望したところ、生産技術に配属されました。今回のプロジェクトでも、ノイズレスデザインに携われたのはよかったですね。
今後EVが拡大していくと、内装に必要な機能や部品が変わっていきます。そこで生産技術側から付加価値を提案していきたいと思っています」
一筋縄ではいかないプロジェクトを経験しながら、グローバル導入が成功した今は笑いながら思い出を語り、また挑戦したいと考えている3人。
Hondaのより良いものづくりに貢献するため、これからも経験を活かしチャレンジを続けます。