世界初の屋内全天候型全方位衝突実験施設
Hondaは世界初となる屋内全天候型全方位衝突実験施設を2000年4月に完成させた。現実に起きている事故実態を模した衝突テストを繰り返し行い、衝突テストの内容を充実させることで、人を中心に据えたより高い次元での衝突安全性を有していることを確認するのがこの施設の役割だ。
クルマやバイクに代表されるモビリティを開発する企業として、安全・安心に移動する喜びをお客さまに提供したい。クルマやバイクに乗っている人だけでなく、道を使う誰もが安全でいられる「事故に遭わない社会」をつくりたい。その思いを表すのが「Safety for Everyone」のグローバル安全スローガンである。
この考えのもと四輪車に関する交通事故の実態を調査してみると、死亡事故に占める割合の多くがクルマ対クルマ、あるいはクルマと歩行者の衝突事故であることがわかった。この調査結果は、リアルワールドに目を向けることの重要性を示している。現実の事故はどのように起きているのか、そしてどのように人は怪我をするのか──。
1993年度世界の交通事故実態
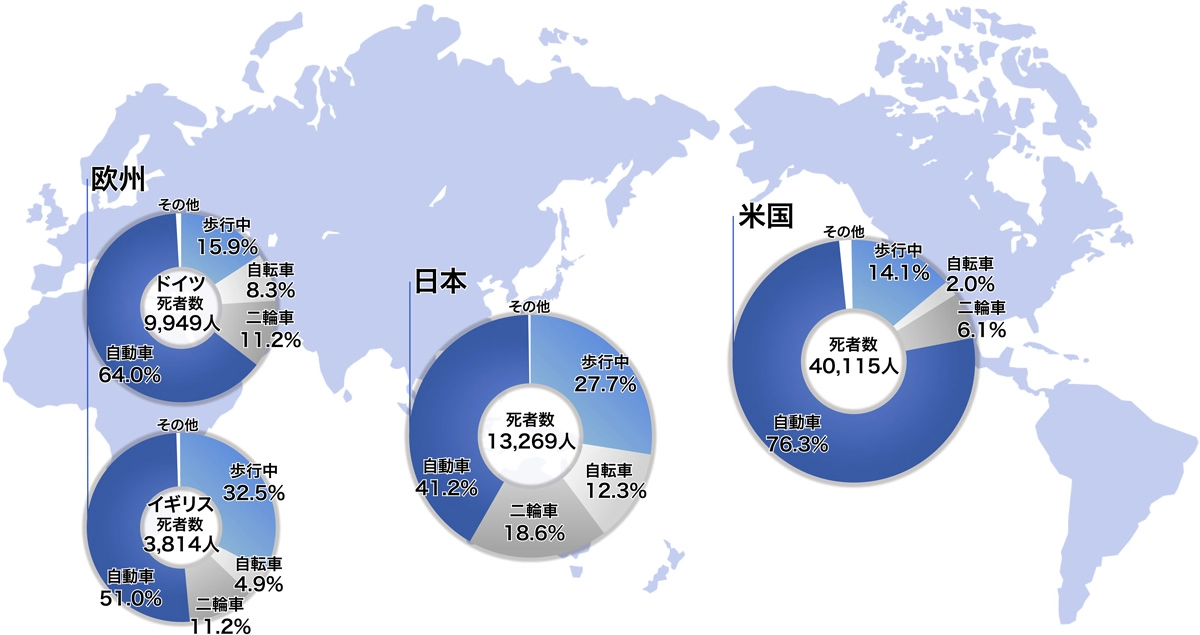
出典:交通統計
リアルワールドの事故実態を広く網羅した衝突テストを行うのは難しく、自社で大規模な施設を建設して取り組もうとする自動車メーカーは当時存在しなかった。Hondaは法規だけに対応するのではなく、自分たちで実際に起きている事故を研究し、そこで得られた知見をもとに独自の基準を設けてテストを行い、世界トップの安全性能を目指そうと考えた。それが、世界初の屋内全天候型全方位衝突実験施設を建設する動機になっている。
この施設は「屋内」であることがポイントだ。屋内全方位衝突実験施設が稼動する前は外部の施設でクルマ対クルマの衝突実験を行うことはできた。ただし屋外だったためテストのスケジュールは天候に左右された。屋内全方位衝突実験施設は文字どおり屋内で実験できるため年間を通じて天候に左右されず実験を行うことができる。また栃木の研究開発施設内にあるためアクセス性に優れ、研究開発の効率化につながる。
施設概要
衝突実験を行うエリアは南北方向に272m、東西方向に178m、屋根高は15mあり、130m四方にわたって柱のない空間となっている。ここに正面衝突の0度コースを基本に、15度刻み(180、15、30、45、60、75、90度)で合計8本のコースが設けられており、正面衝突だけでなく斜め前方からの衝突、斜め後方からの衝突、側面への衝突など、全方位からの衝突テストができ、リアルワールドの事故を再現できるようになっている。前面衝突は100%フルラップ、50%、25%オフセット衝突など、さまざまなオフセット率を再現することができる。
屋内全方位衝突実験施設レイアウト
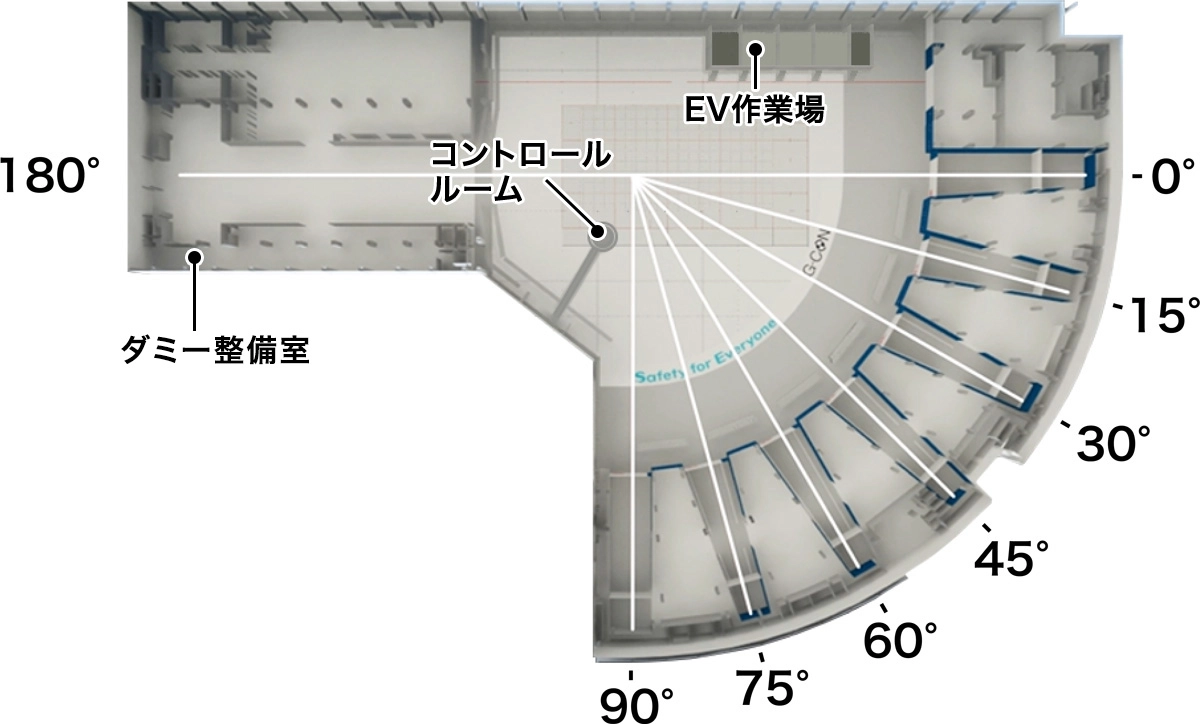
衝突試験用ダミー人形の姿勢を安定させたまま80km/hまで加速できるようにするため、各コースの長さは130mとした。ここでは2台のクルマを同時に最大80km/hで牽引することが可能。また、40km/h対60km/h、40km/h対80km/hなど、2台のクルマを異なる速度で衝突させる異速度衝突も可能としている。車両を牽引するウインチは、積み荷を満載したダンプトラックにも対応した高い能力を持たせている。

テストエリア 180°から0°方向
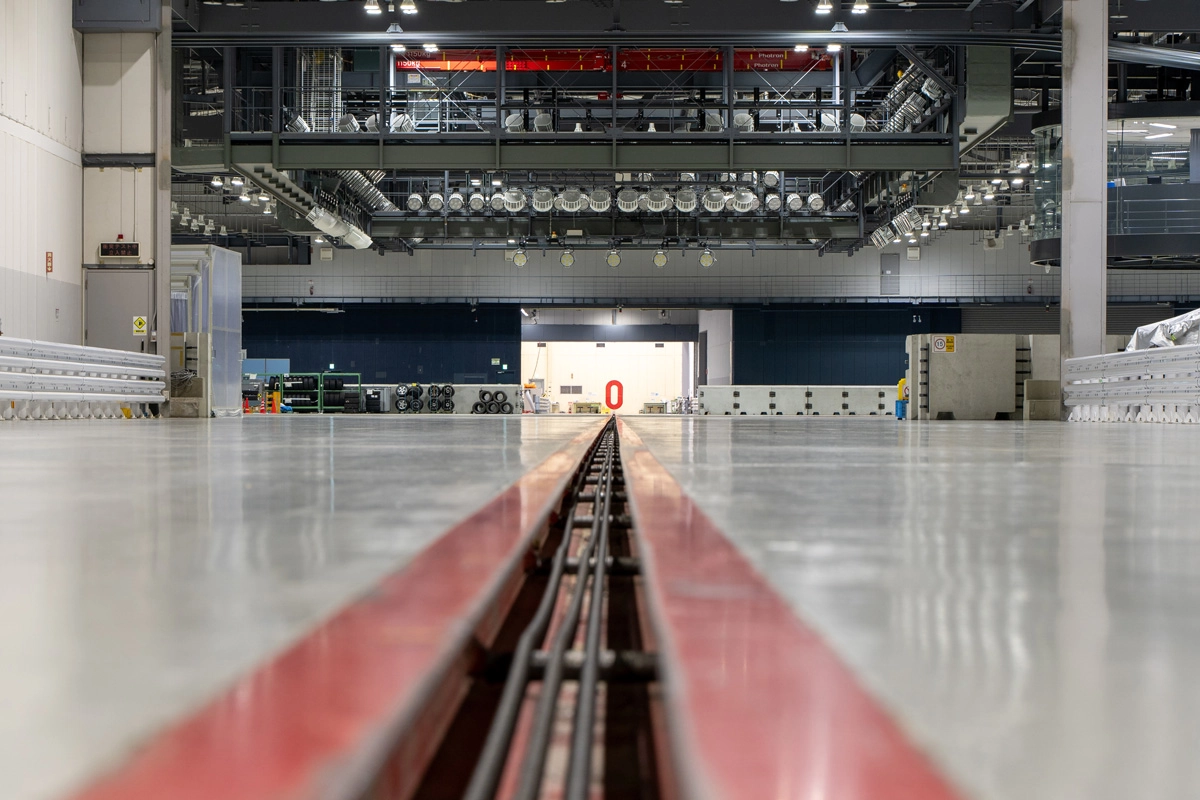
テストエリア
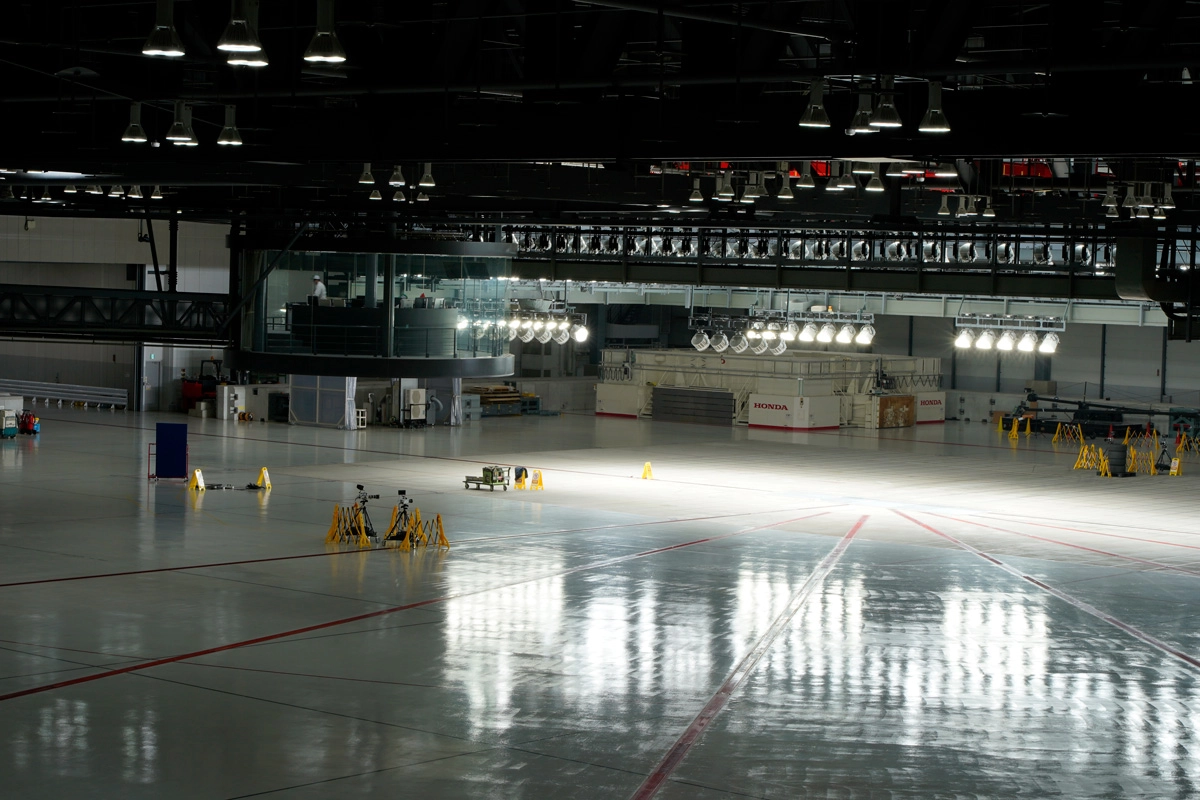
テストエリア 60°と45°の間
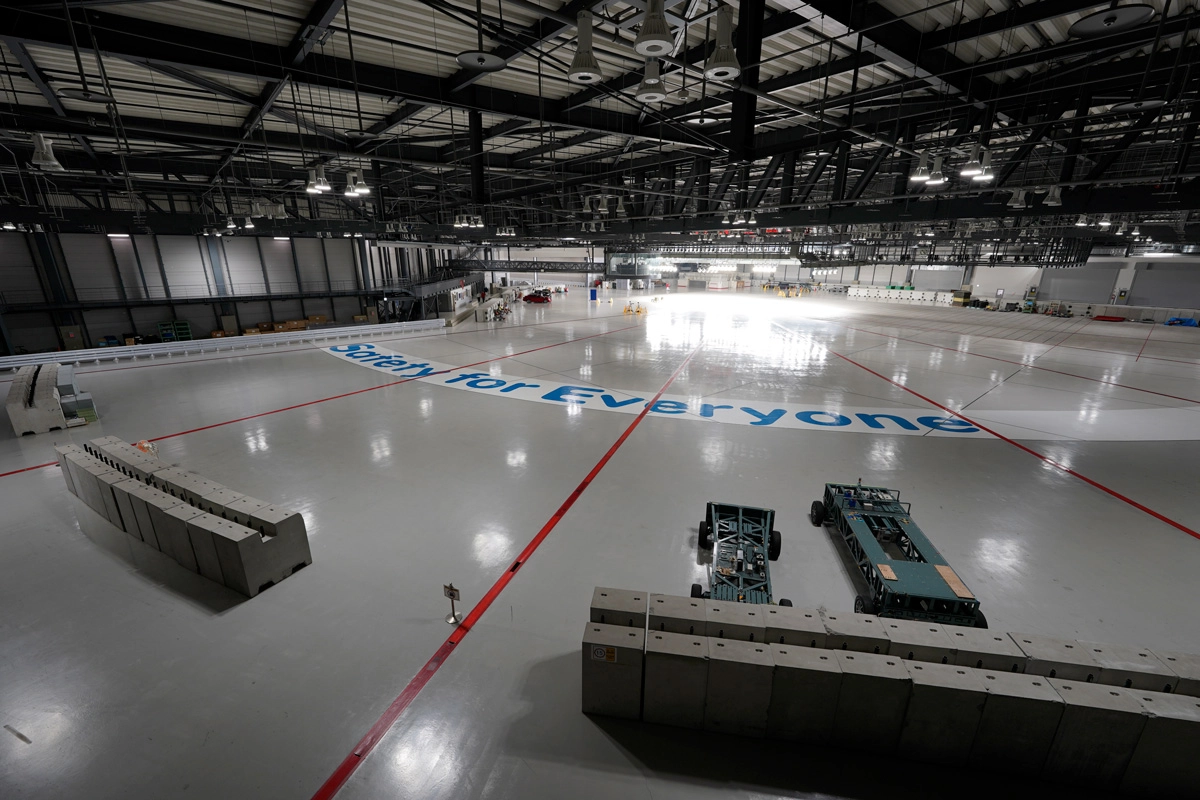
テストエリア 180°から0°方向
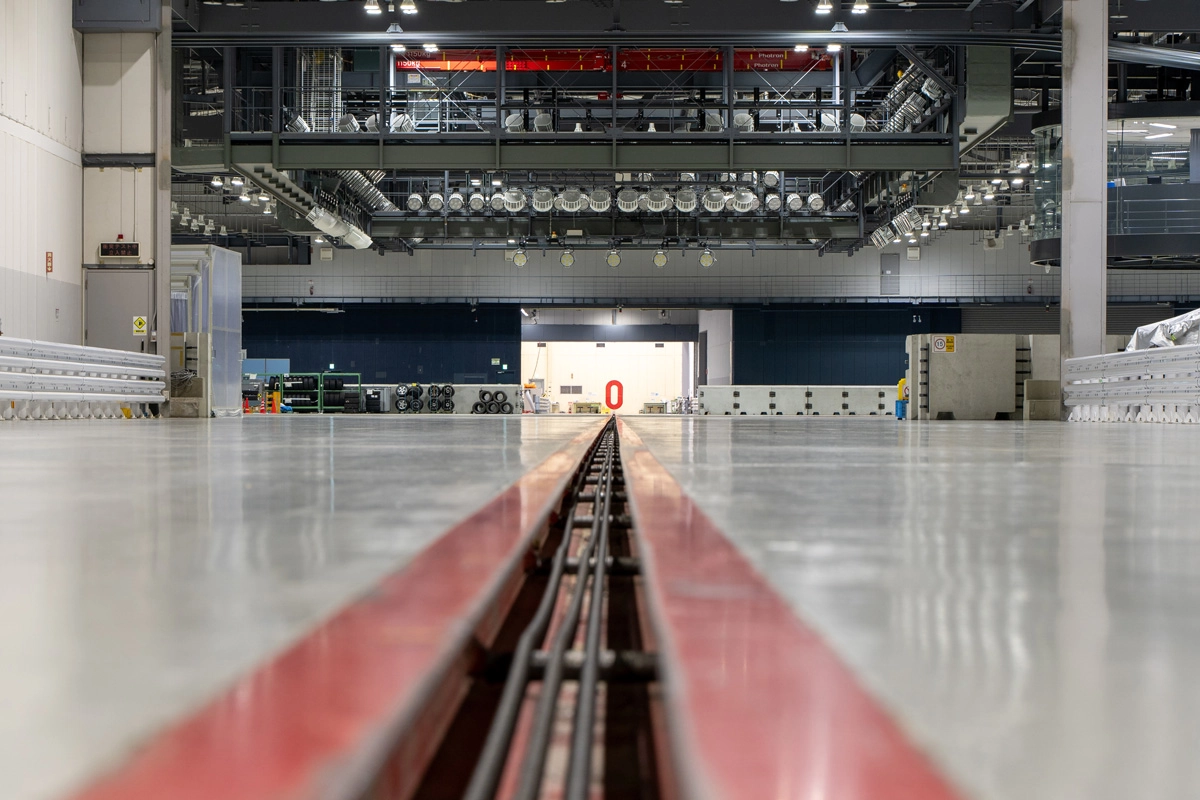
テストエリア
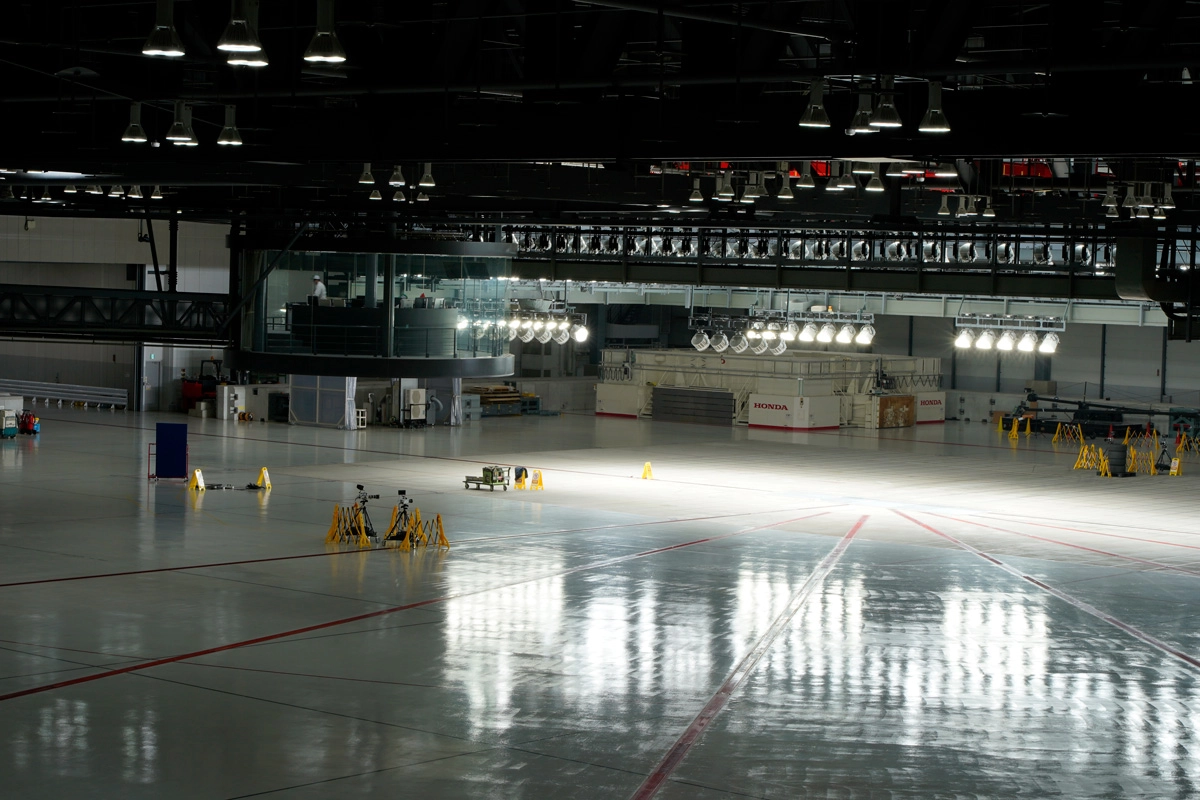
テストエリア 60°と45°の間
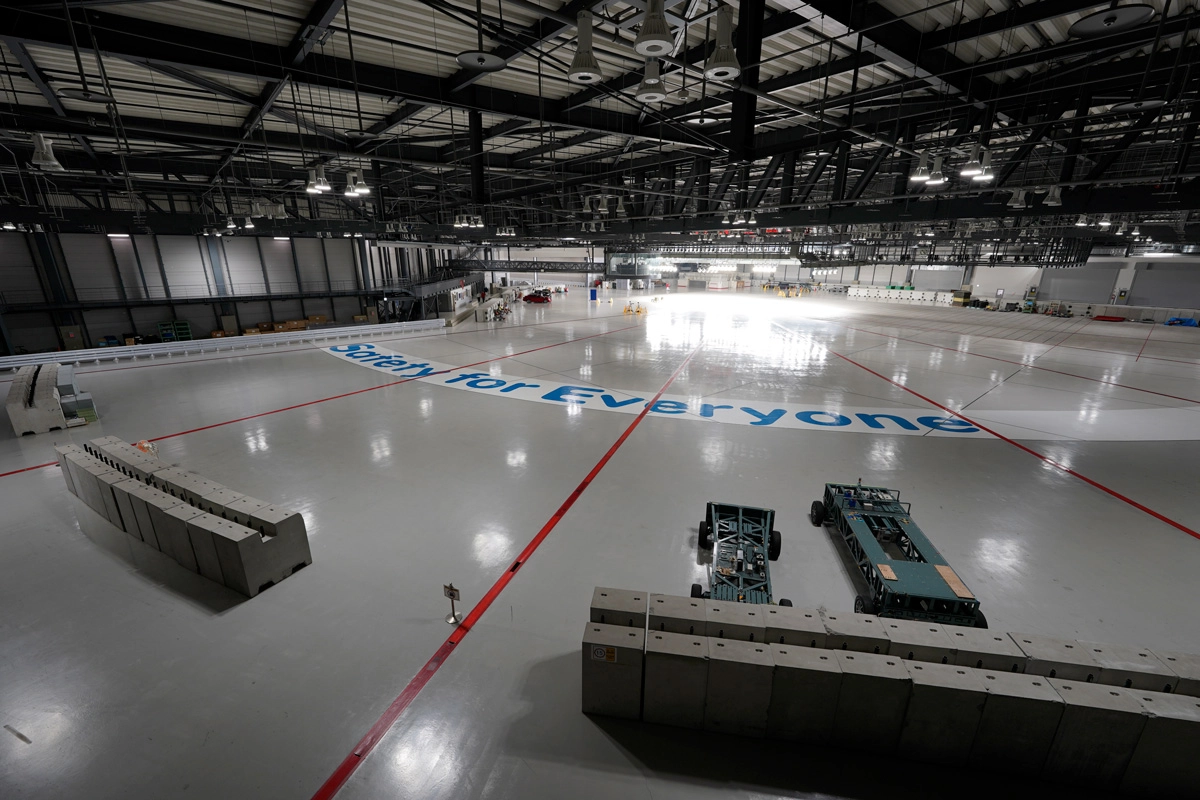
テストエリア 180°から0°方向
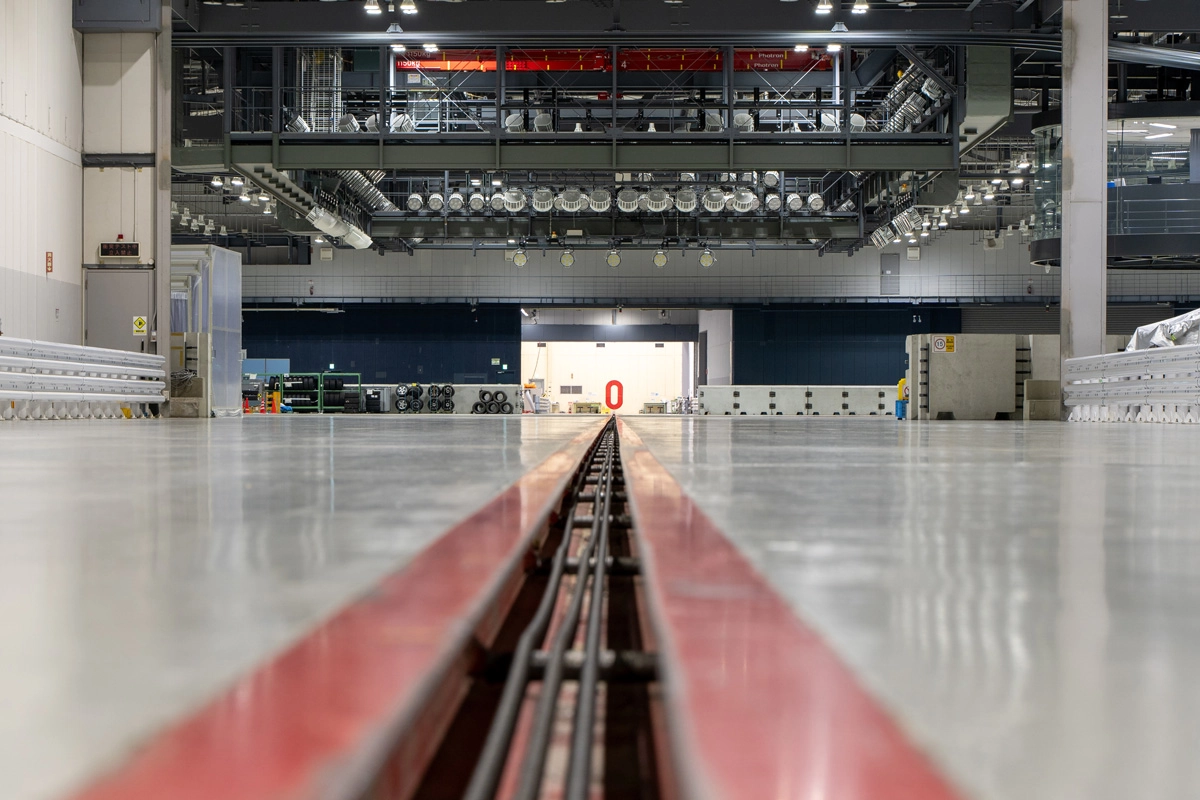

多様なバリア
衝突実験エリアではクルマ対クルマだけでなく、クルマ対バイクやクルマ対歩行者、クルマ対固定した移動式バリア(障壁)、静止したクルマ対ムービングバリア(台車式の衝突実験用試験装置)、クルマを横向きに回転させるダイナミックロールオーバーなど、さまざまな衝突形態の再現が可能。重さ160tの移動式バリアはGPSの測位により自走で所定の位置まで移動する仕組み。ムービングバリアは国によって異なる規定に合わせて10種類以上を用意している。バリアは細かく仕切ったセグメントごとに荷重センサーが埋め込まれており、衝突テストで得られたデータを解析し、研究開発に生かしている。

ダイナミックロールオーバーテスト
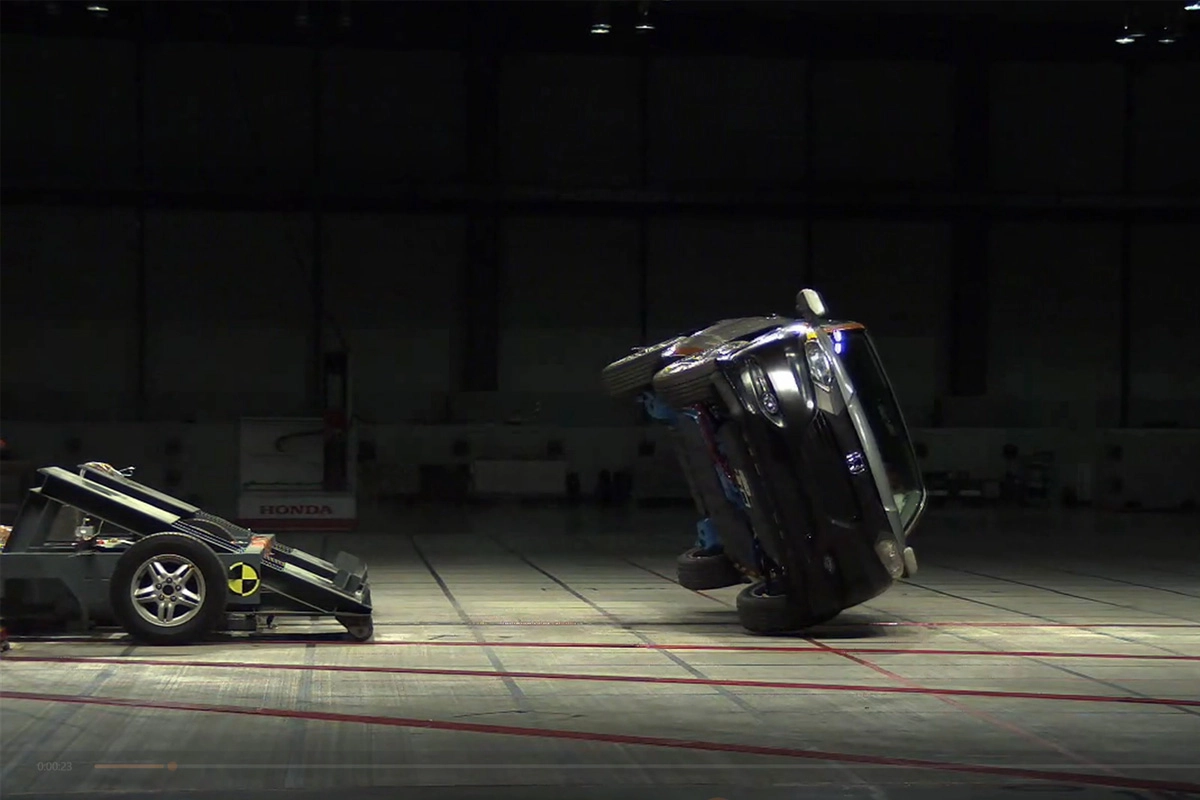
移動式バリアの全景
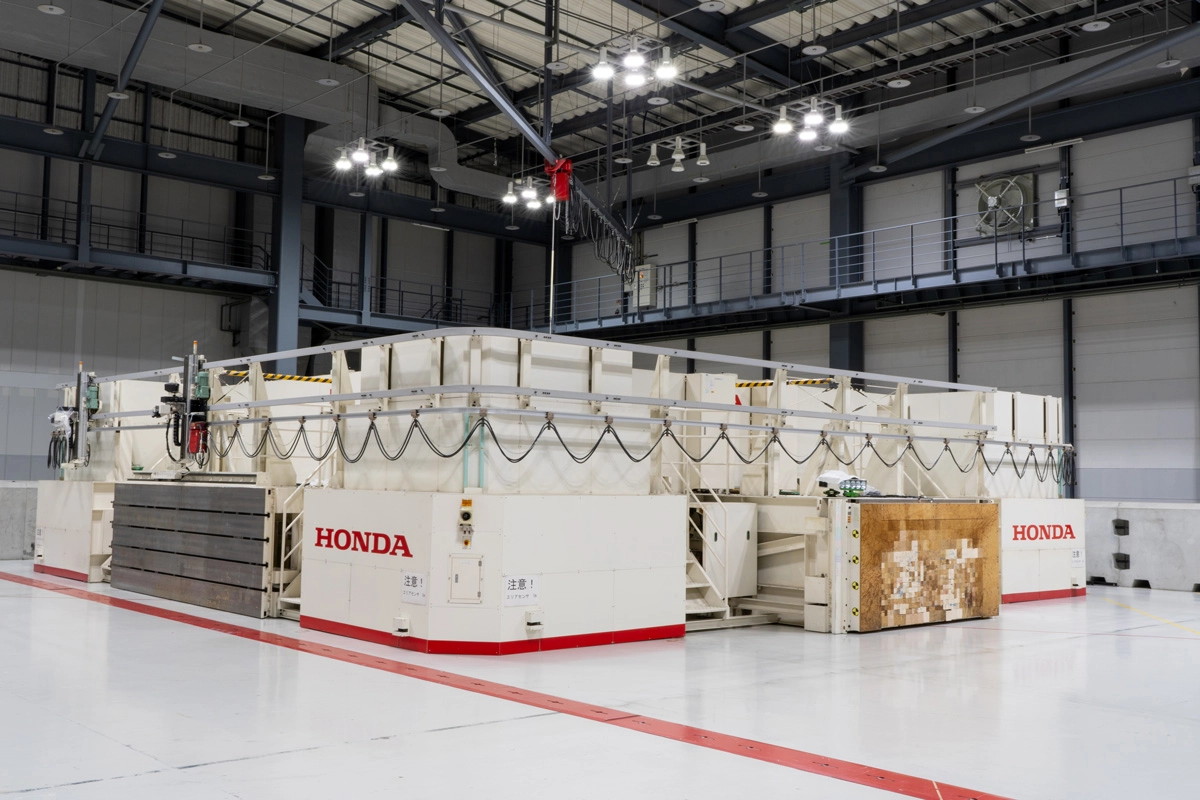
移動式バリアの壁面
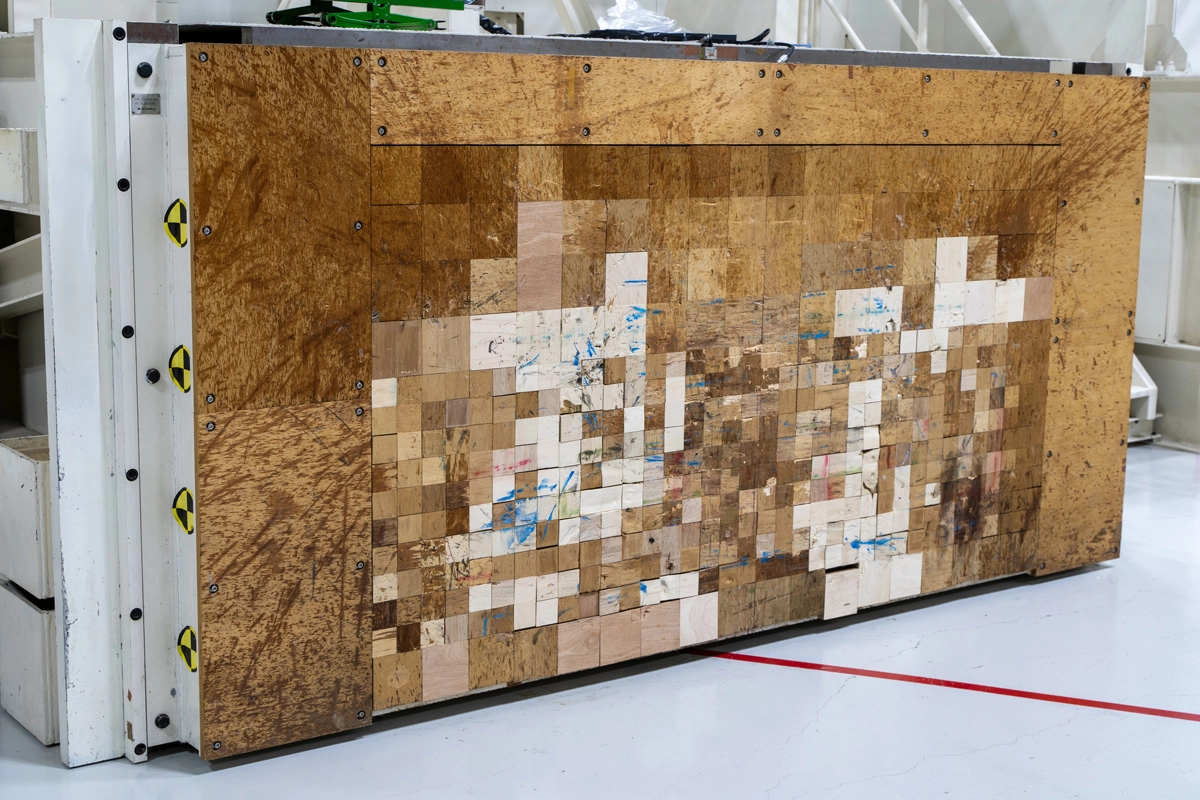
各正方形の壁版にセンサーが組み込まれている
移動式バリアのタイヤ
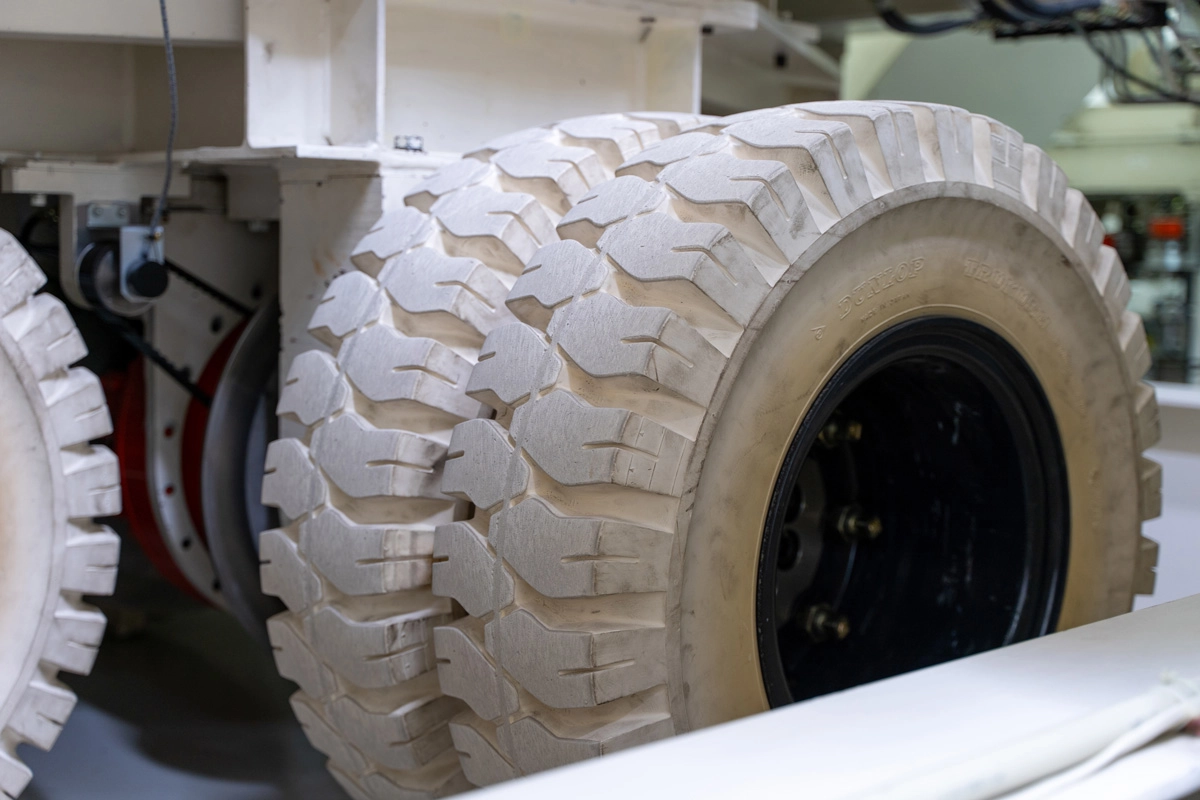
ムービングバリア
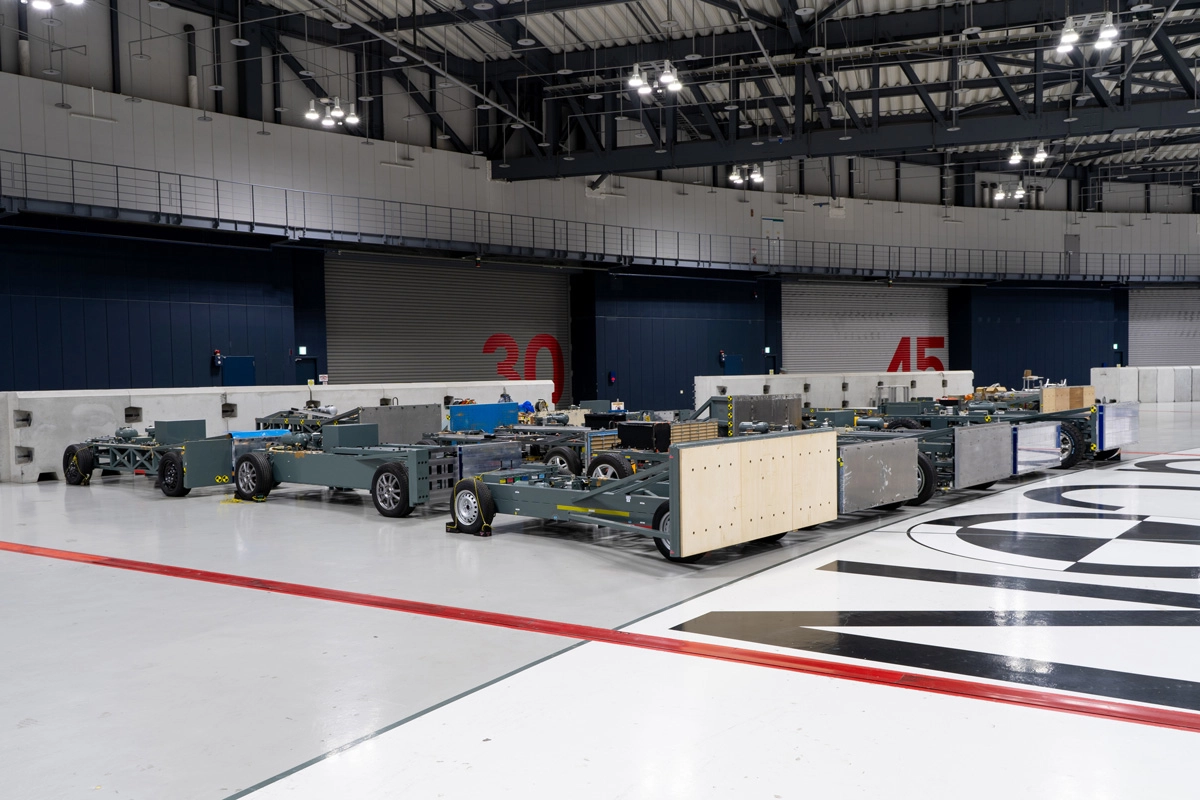
ムービングバリア後面衝突テスト
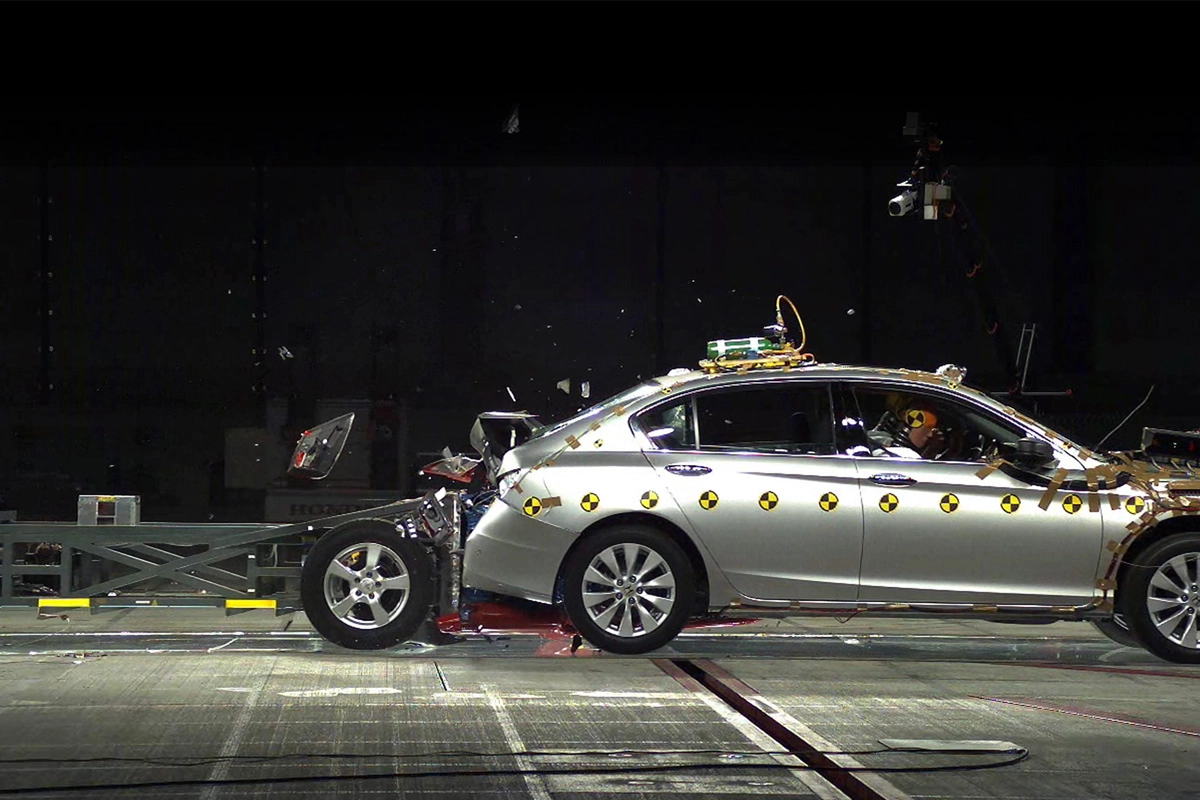
ムービングバリア後面衝突テスト(下から)
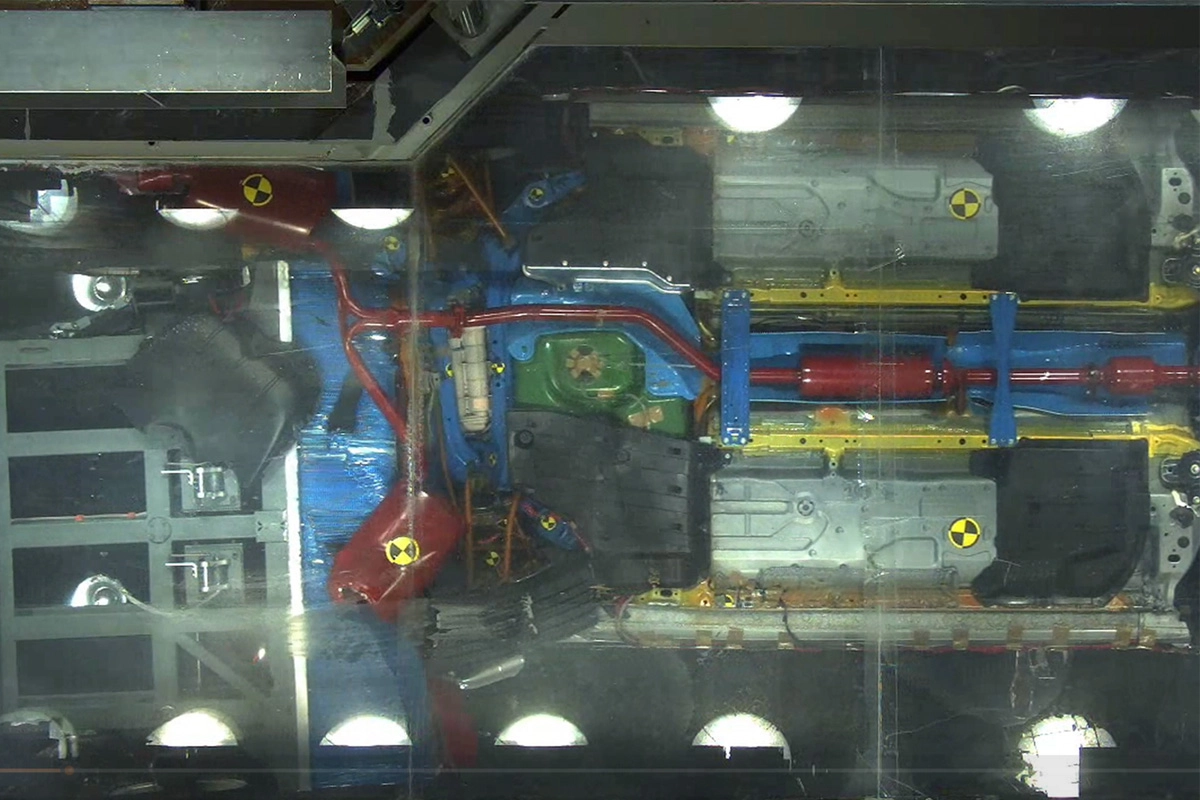
ダイナミックロールオーバーテスト
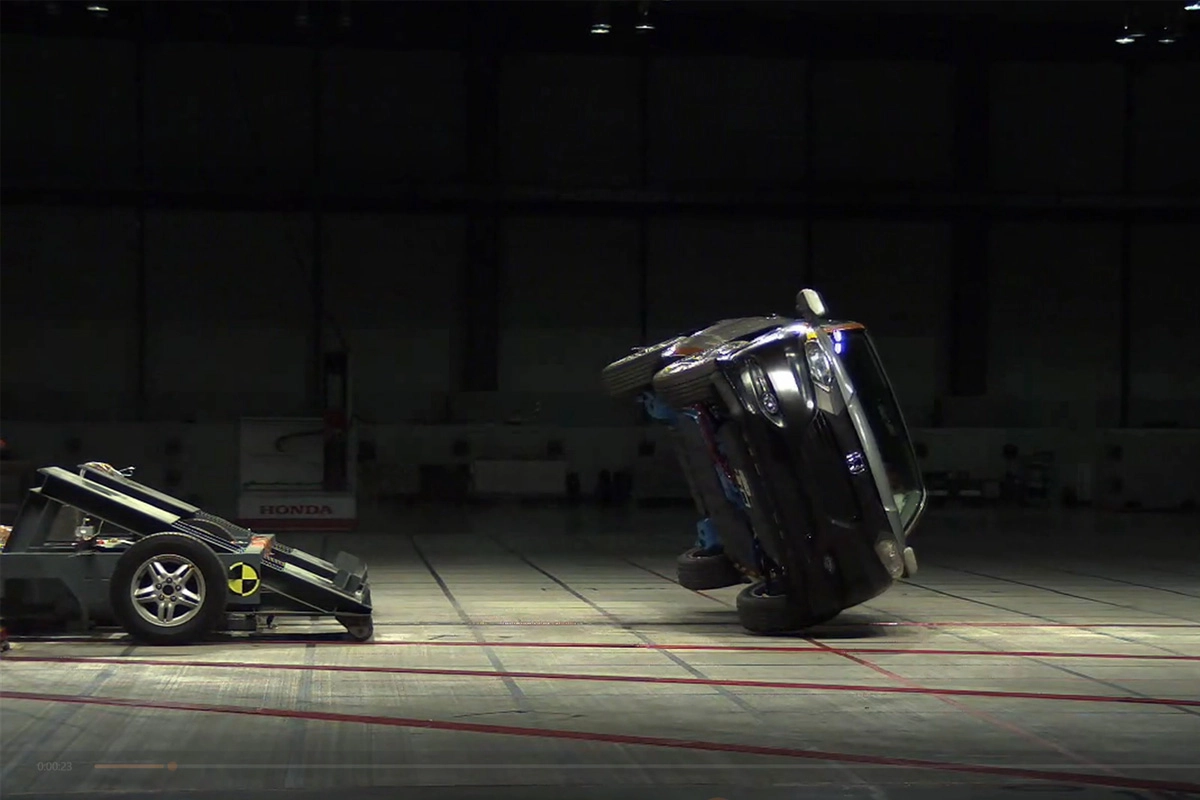
移動式バリアの全景
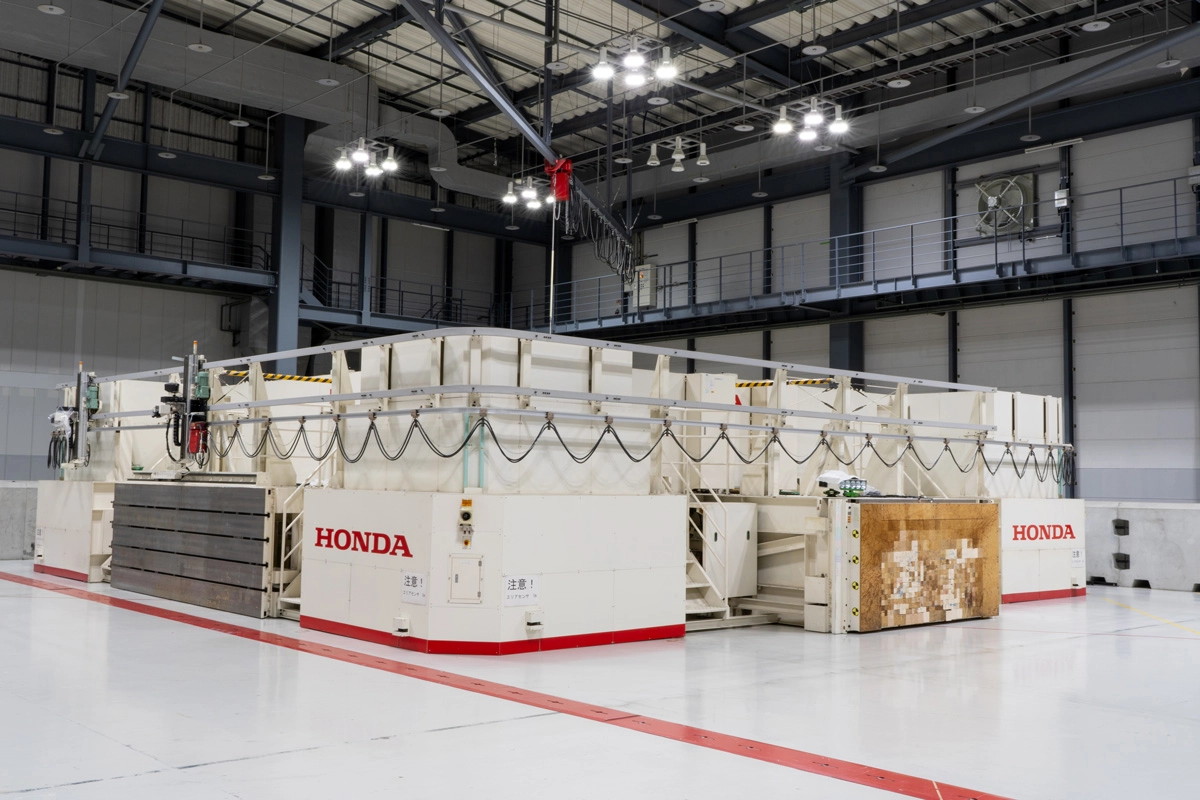
移動式バリアの壁面
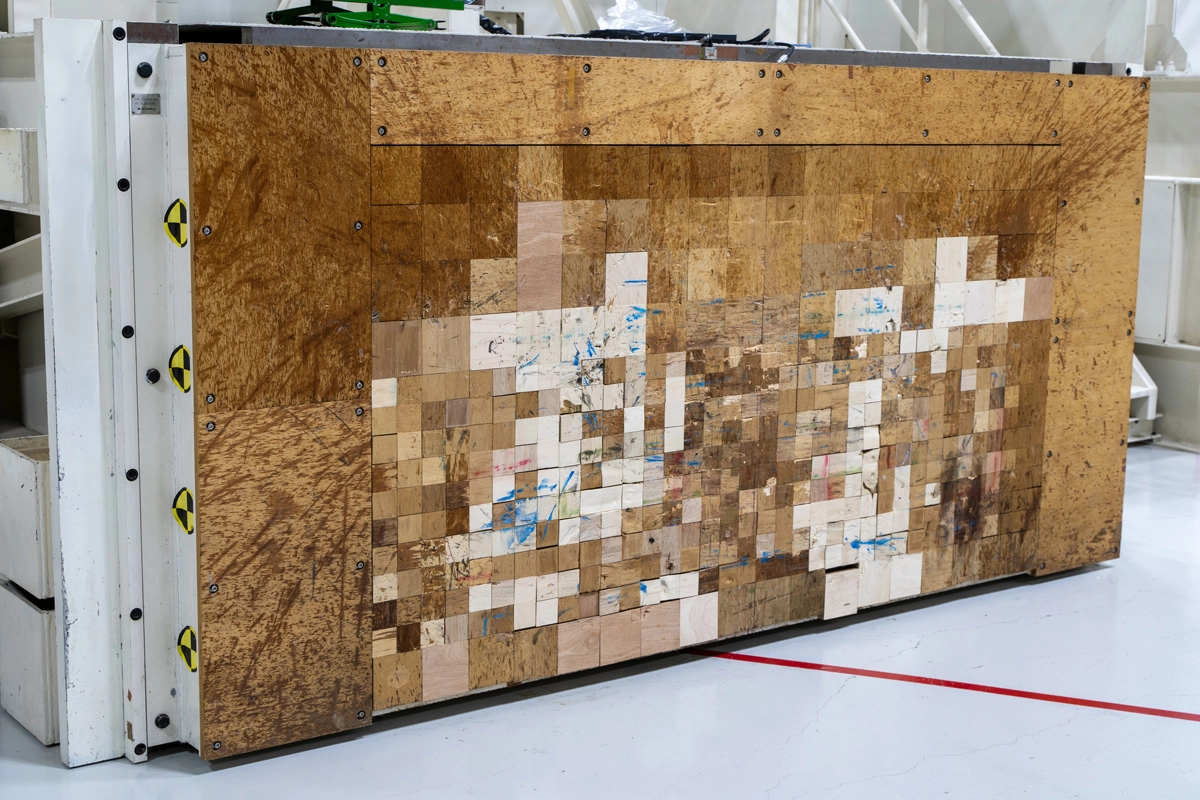
各正方形の壁版にセンサーが組み込まれている
移動式バリアのタイヤ
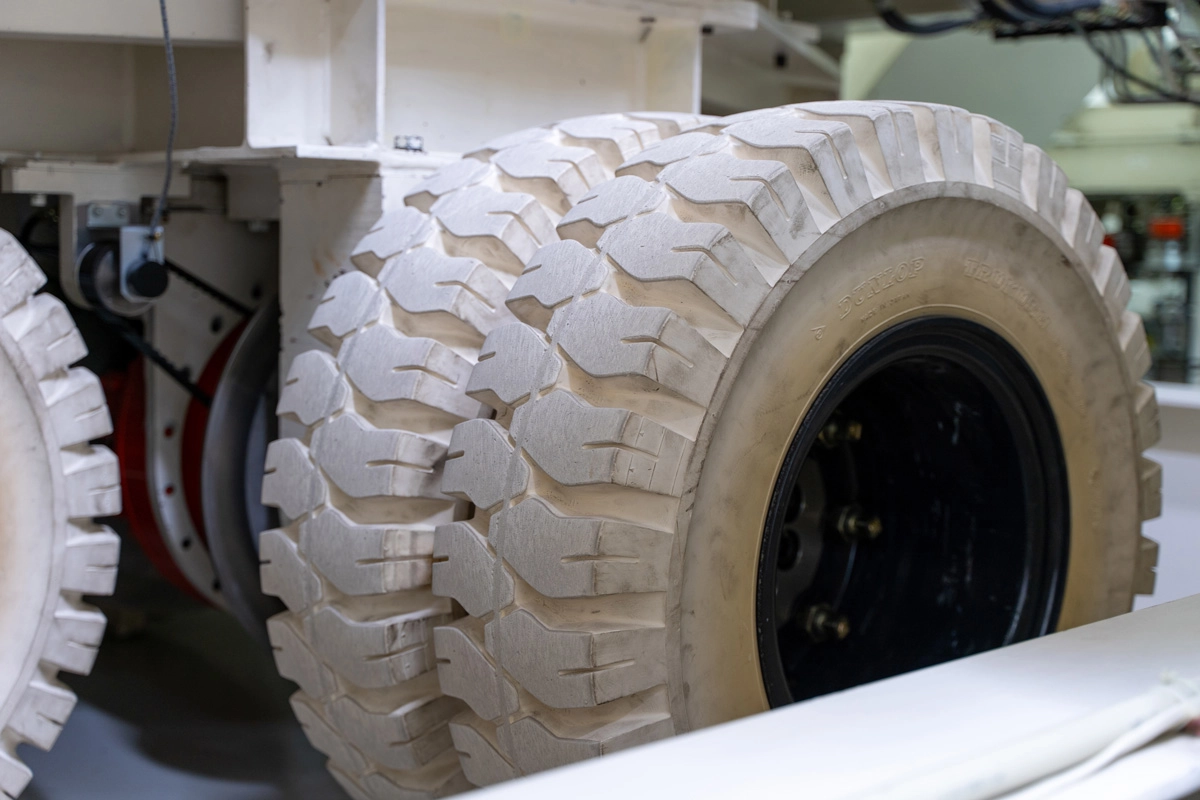
ムービングバリア
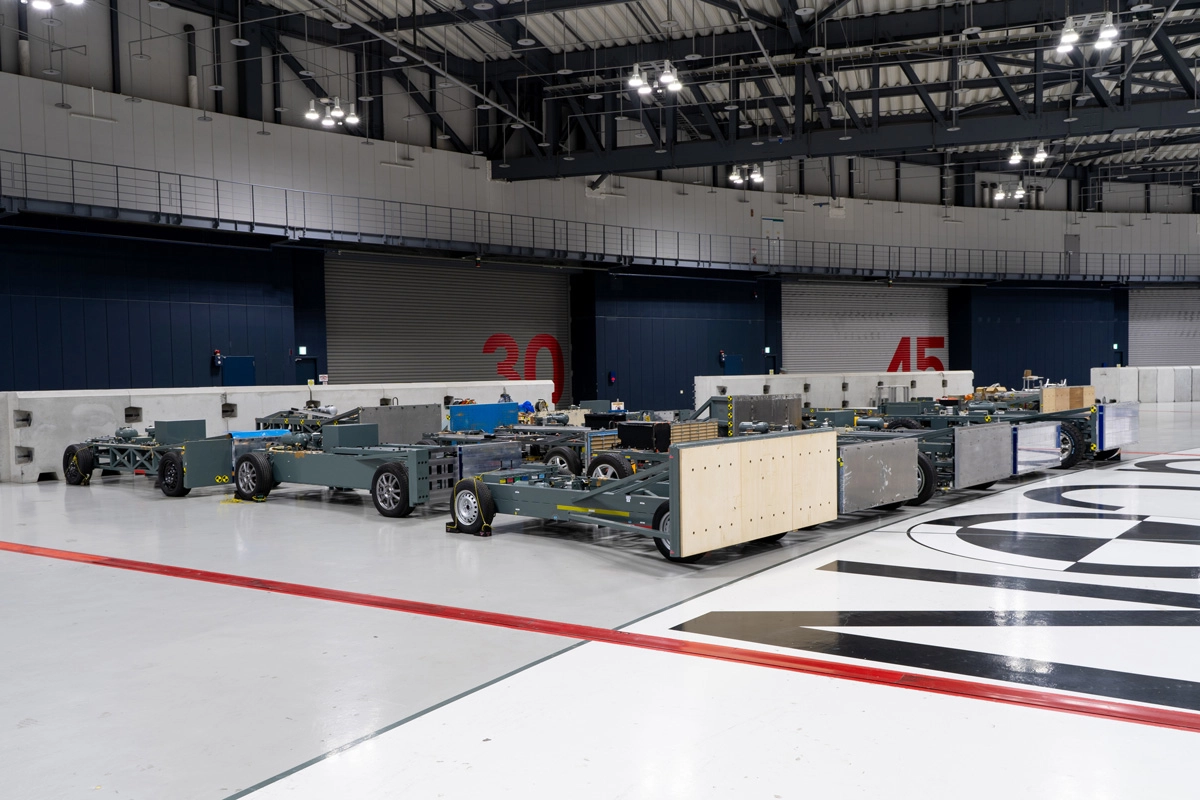
ムービングバリア後面衝突テスト
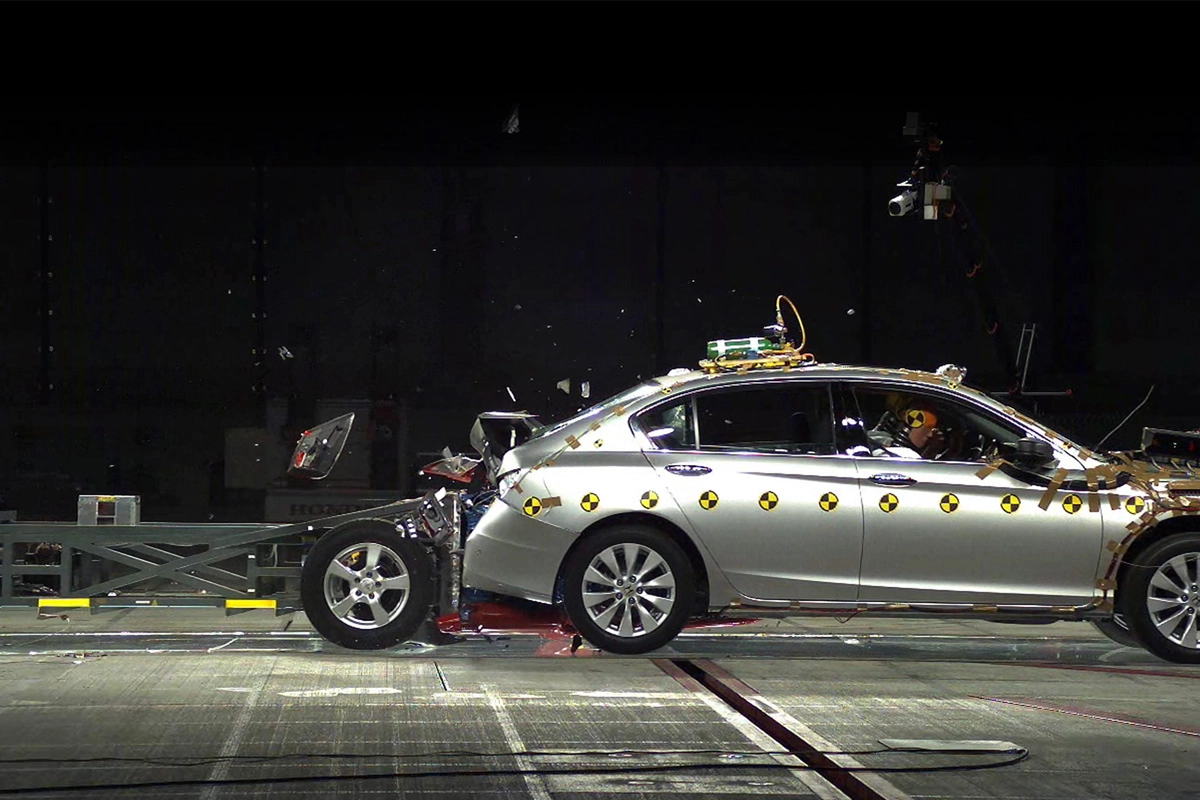
ムービングバリア後面衝突テスト(下から)
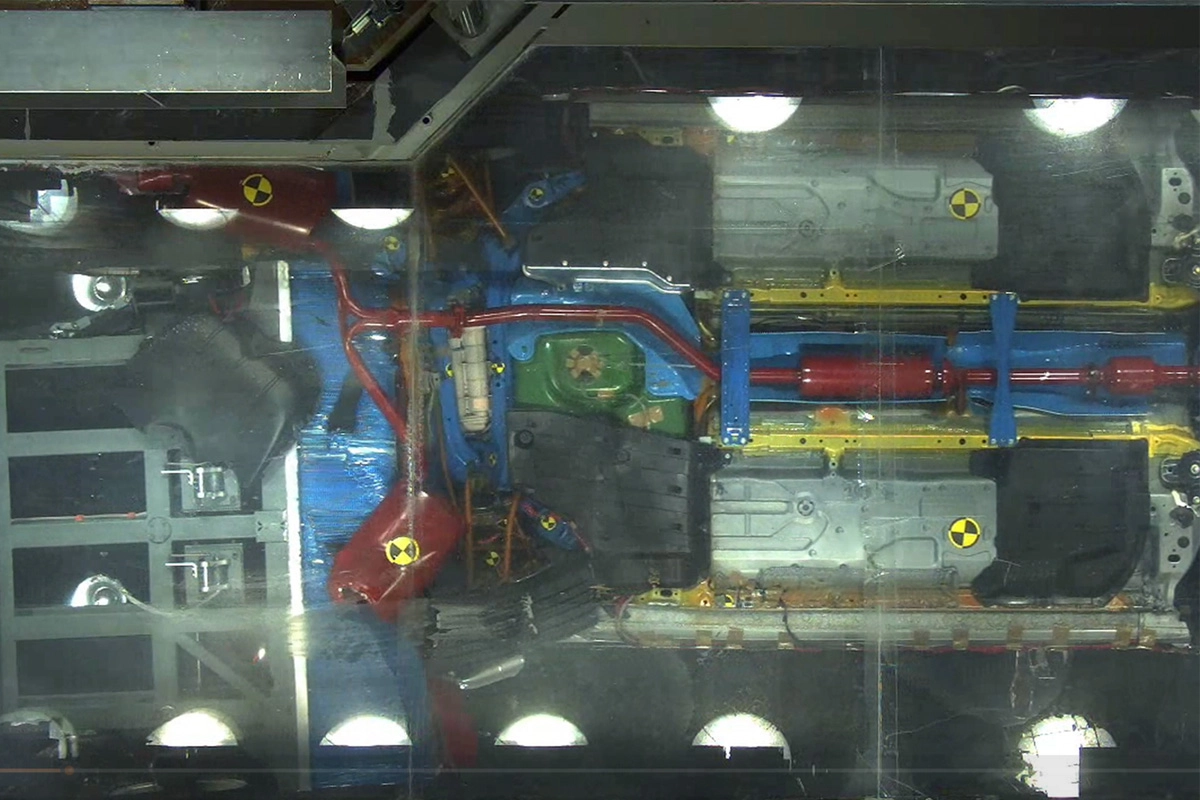
ダイナミックロールオーバーテスト
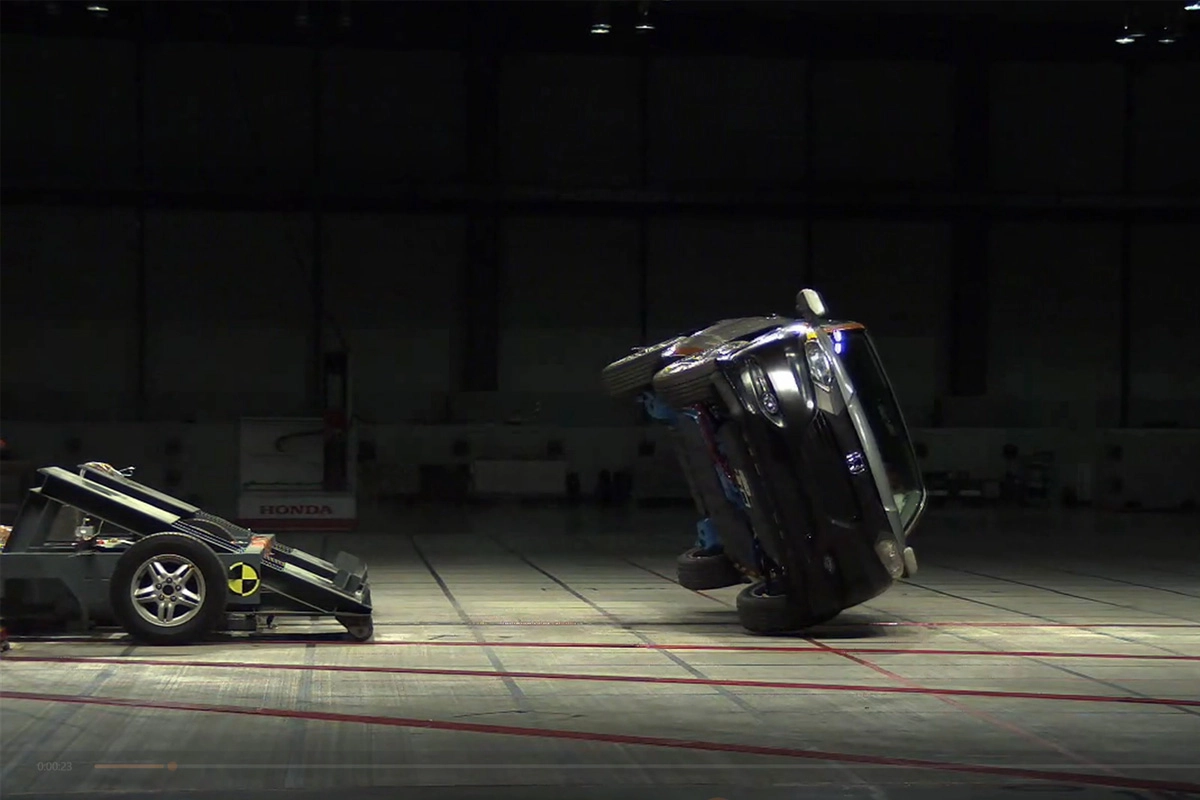

衝突テストの撮影
衝突ポイントには自動制御に対応した高速度カメラを設置し、車載用高速度カメラと合わせて、衝突時の車体変形の様子やダミー人形の挙動などをきめ細かく撮影できるようにしている。また、車体下部の変形の様子を見やすくするため、衝突ポイントの床には開口部を設けている。このエリアは透明のアクリル板に交換することが可能で、床下には高速度カメラが設置されており、衝突テスト時のアンダーフロアの状態が撮影できる。歪みのない映像を撮影するには離れた位置から対象物を狙う必要があるため、床下は深く掘り下げ、車体床面とカメラまでの距離を確保した。カメラが捉えた映像やダミー人形から収集した膨大なデータは、テスト後即座にコンピューターサーバーに転送され、研究開発に生かされる。高速度撮影に必要な光量を確保するための照明はLEDを使用している。
衝突テスト後はボディーの変形を三次元計測してデータを収集。シミュレーションデータとの突き合わせを行い、シミュレーション精度の向上や衝突安全性向上に役立てている。

シミュレーションデータ
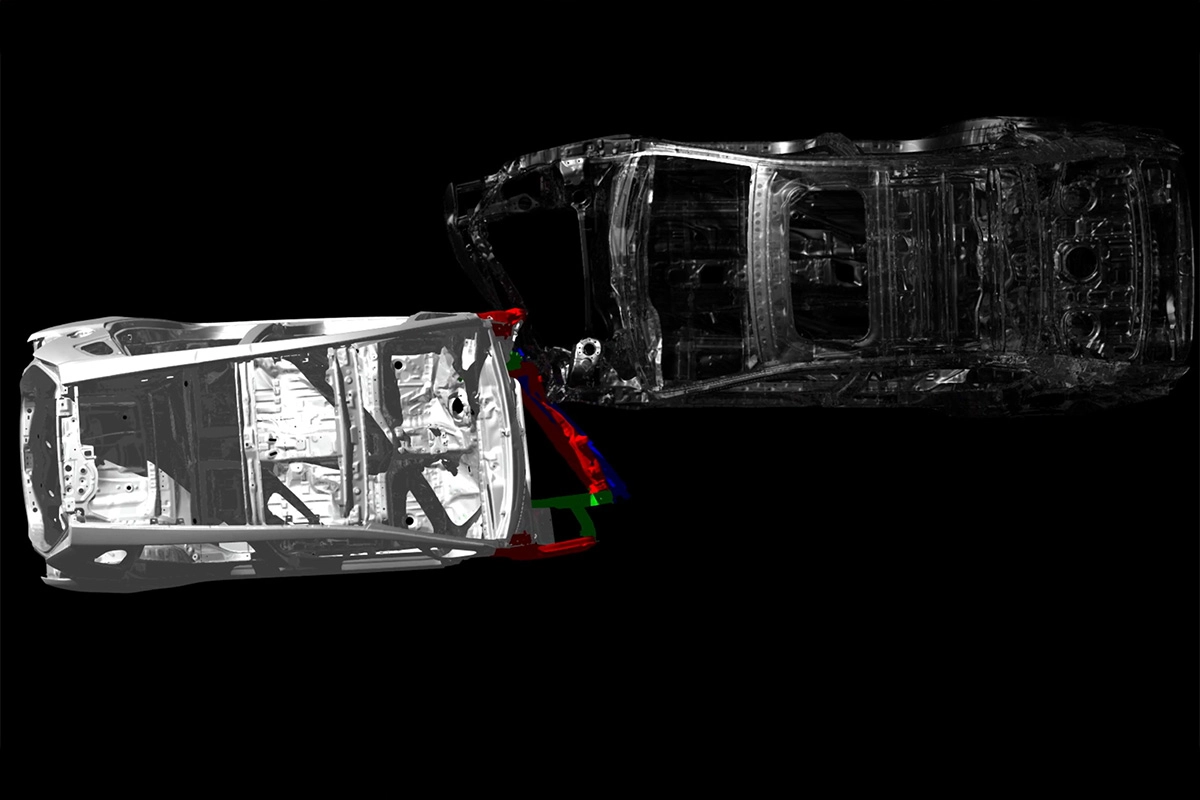
テストエリア
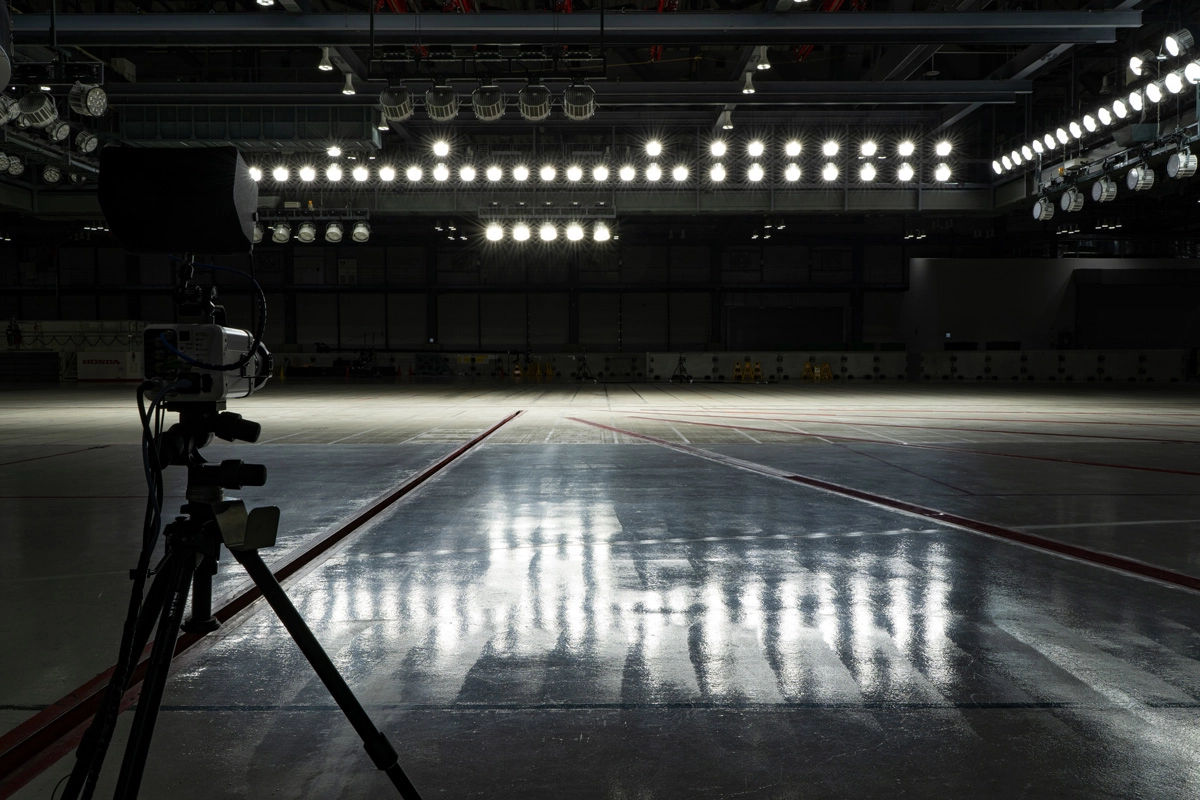
高速度カメラ
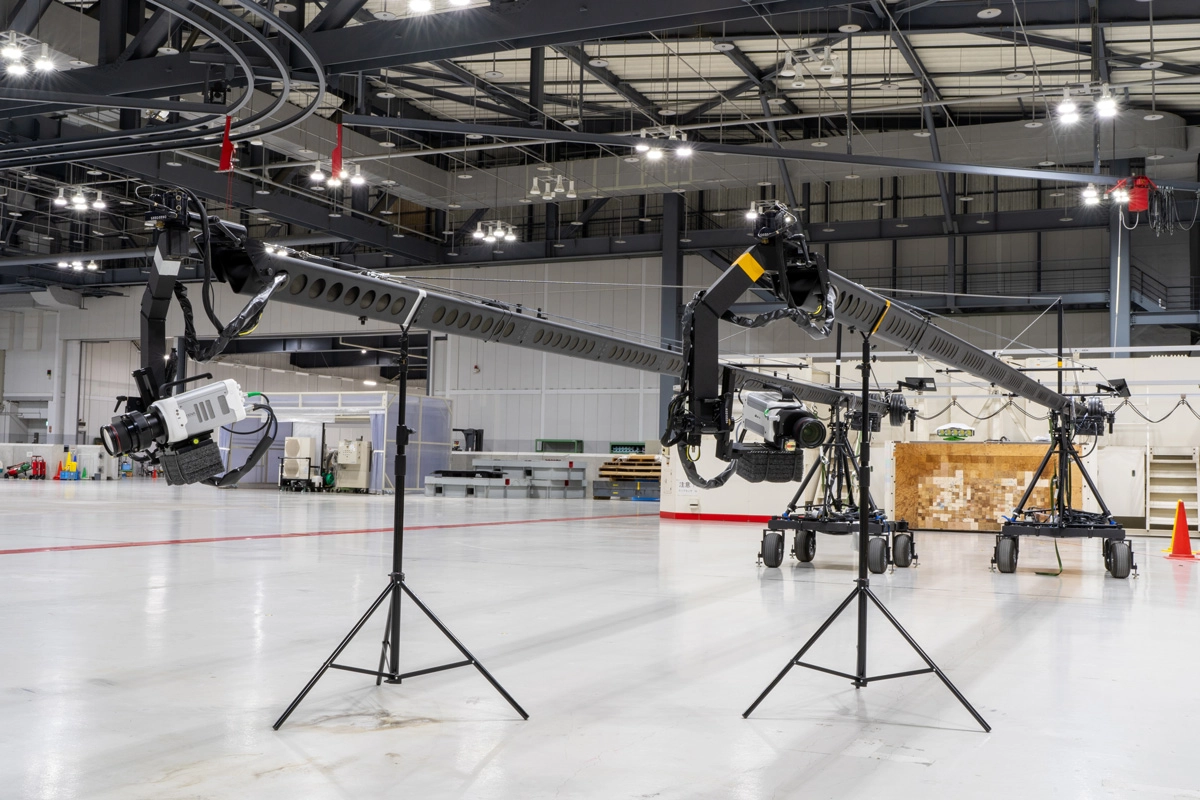
床のアクリル板
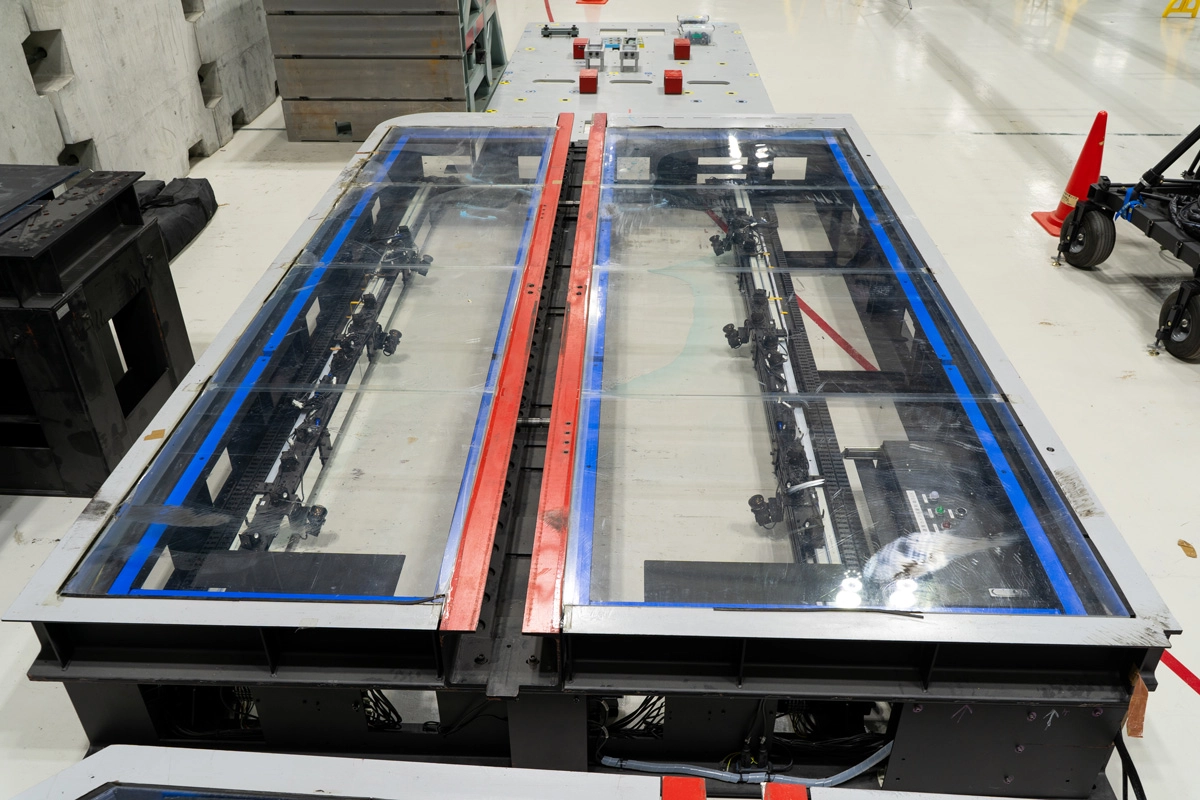
床開口部地下
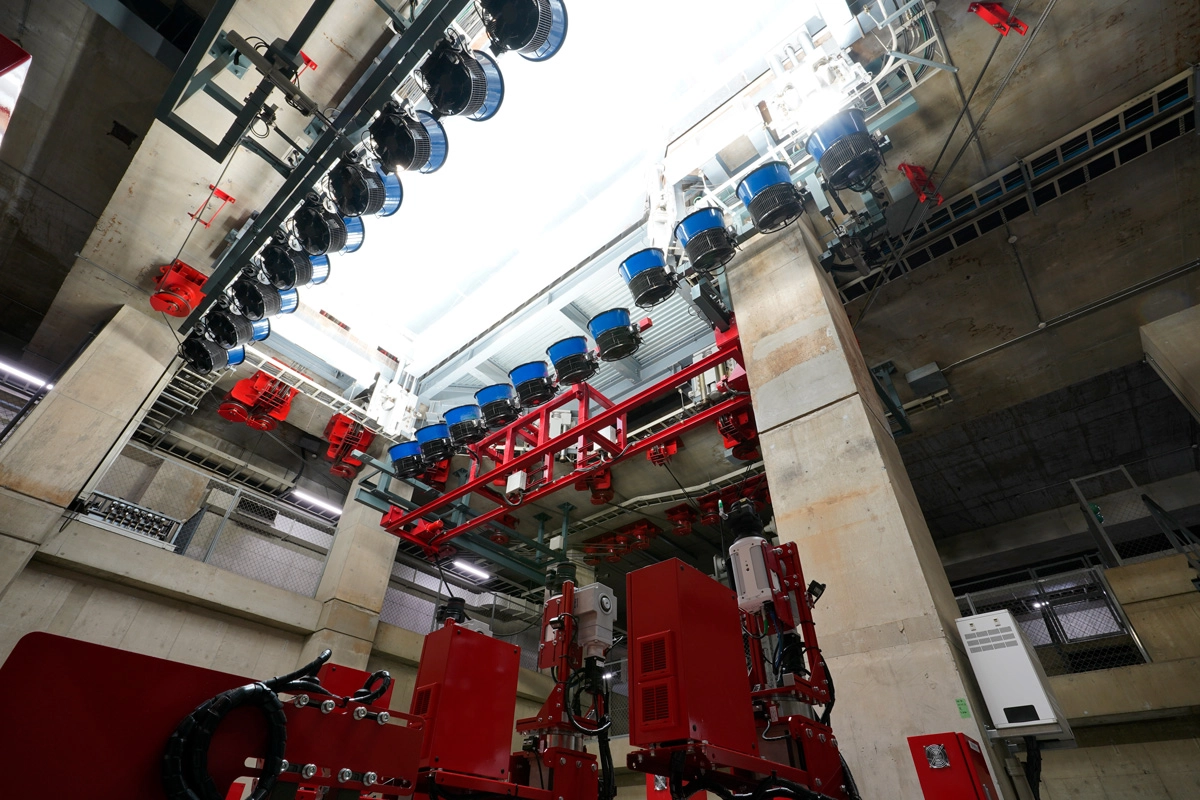
シミュレーションデータ
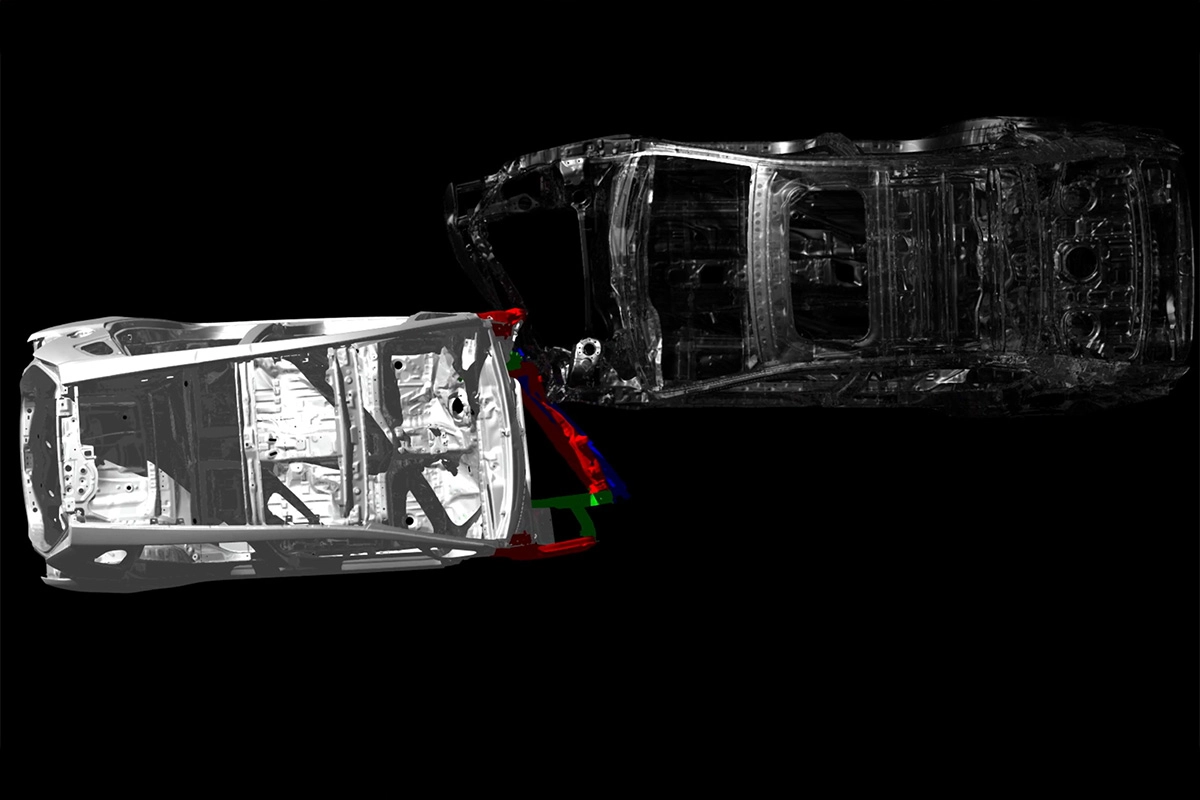
テストエリア
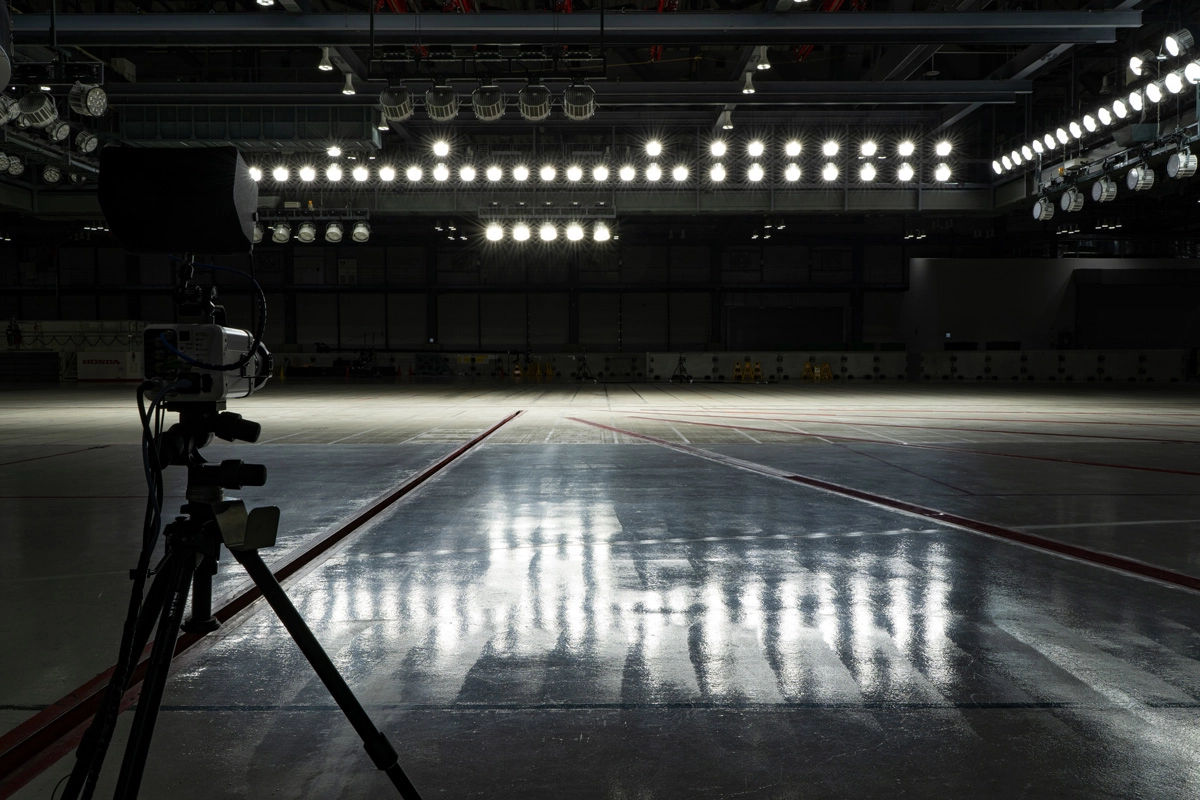
高速度カメラ
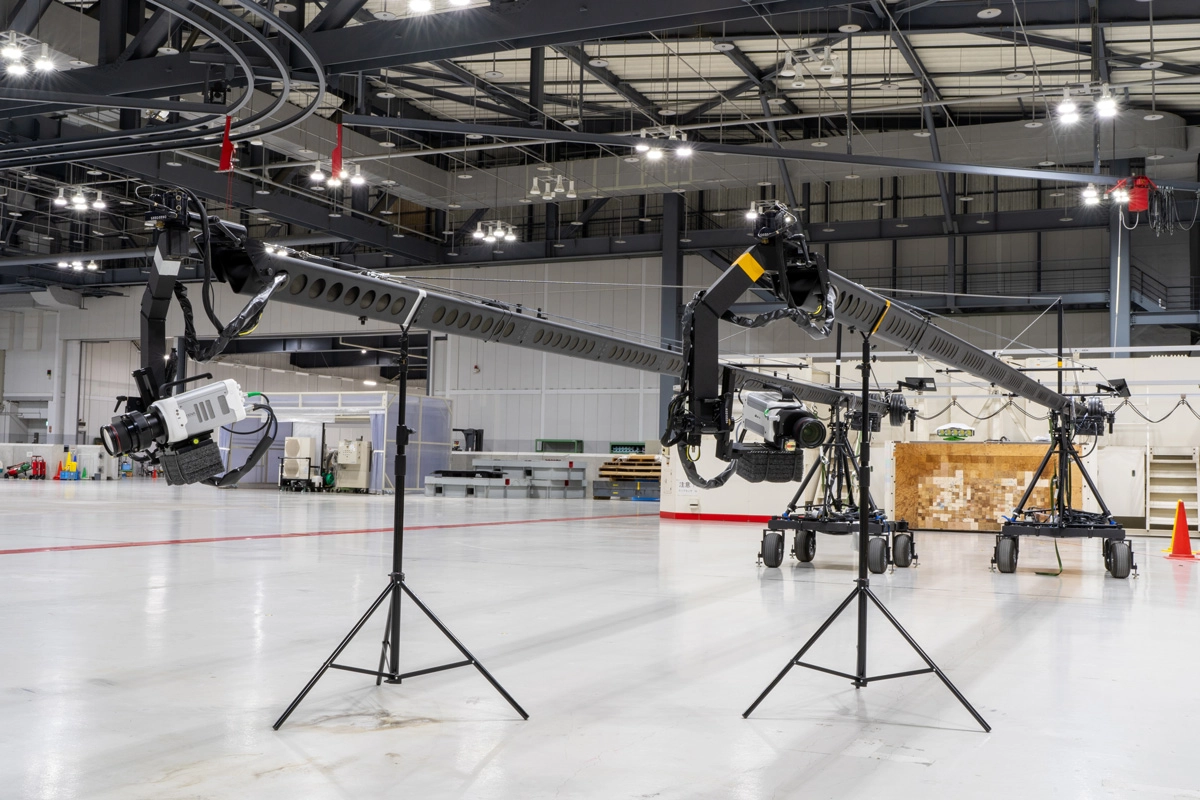
床のアクリル板
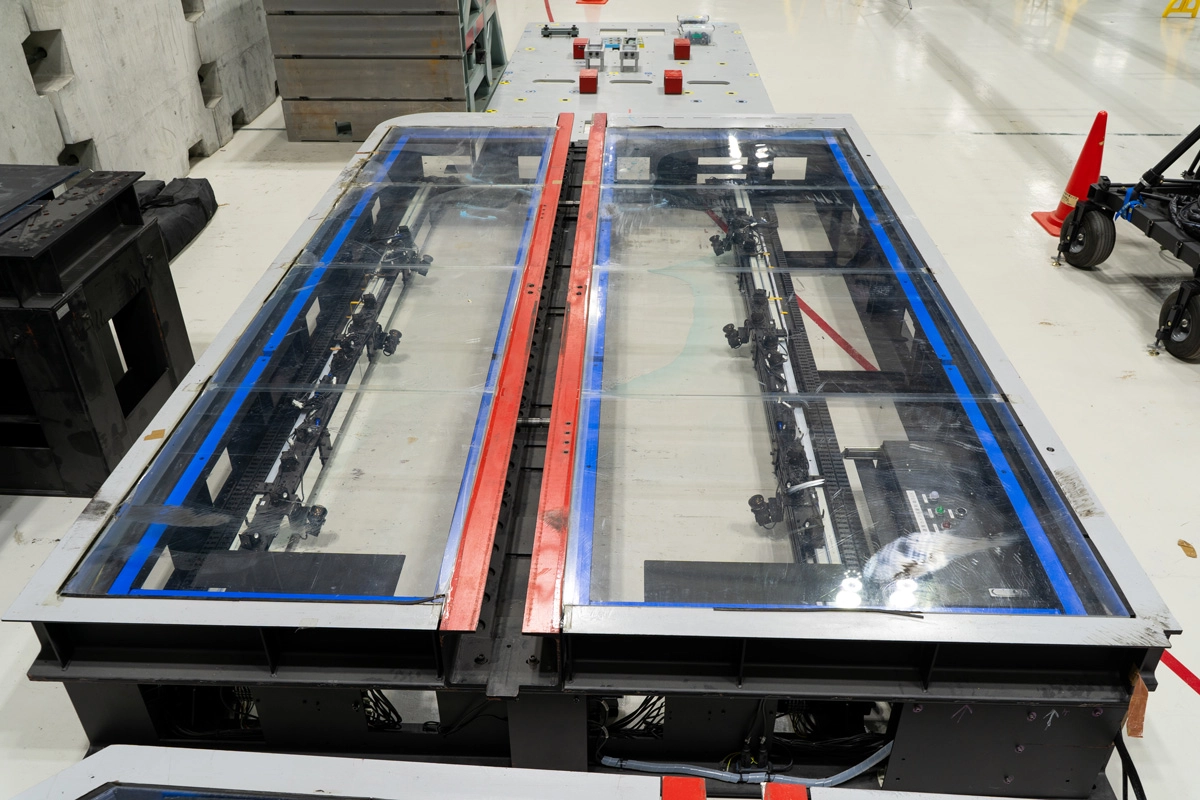
床開口部地下
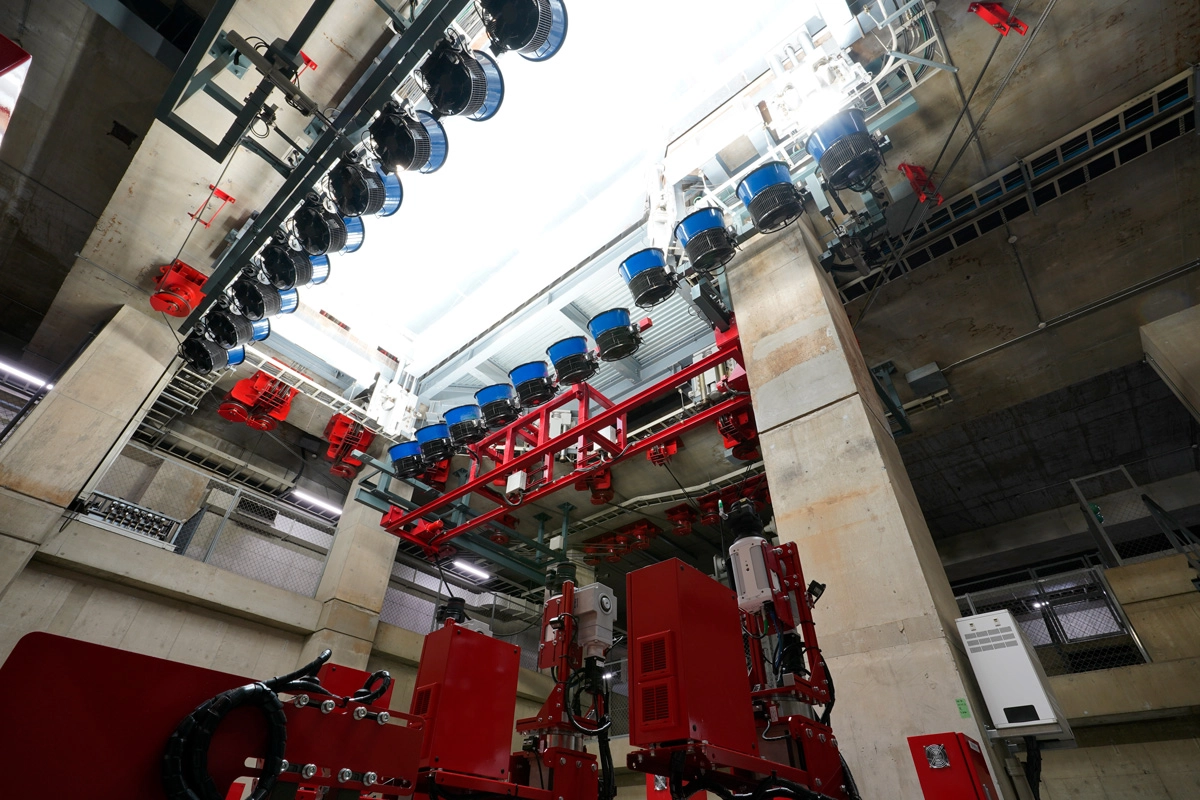
シミュレーションデータ
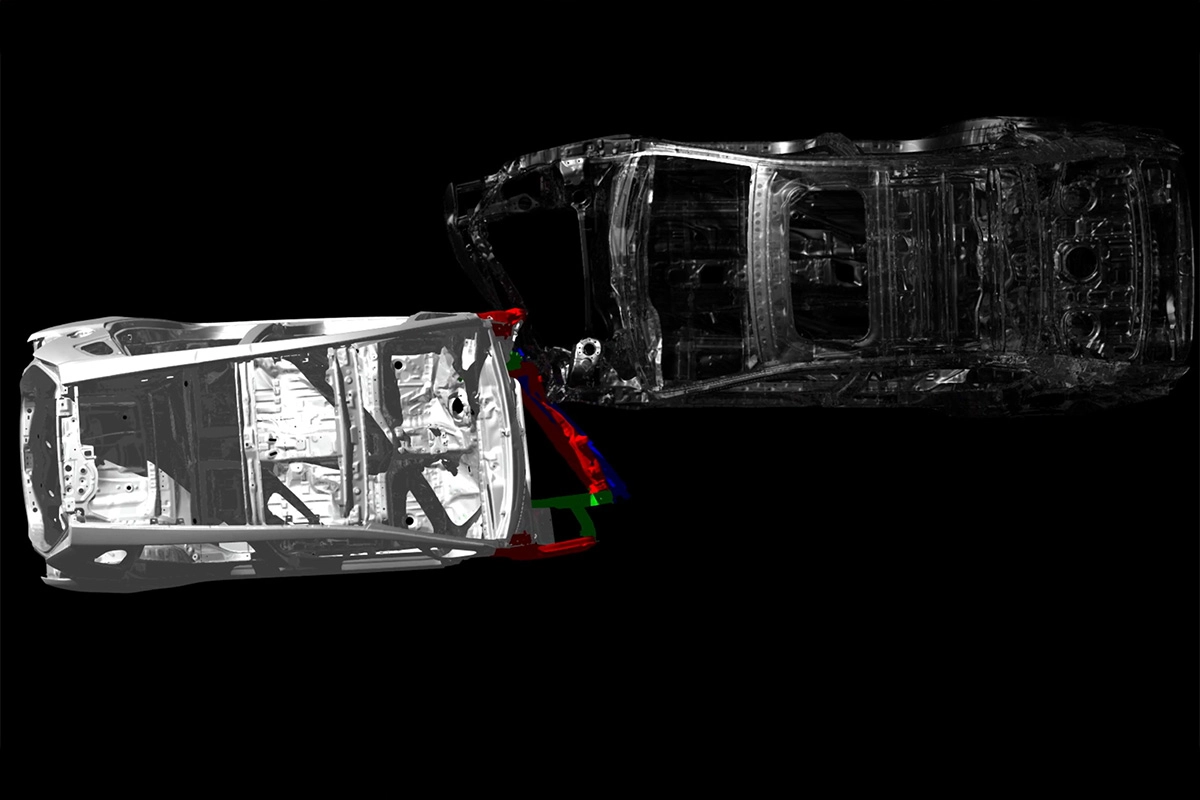

コントロールルーム
衝突テストに必要な制御を行うコントロールルームは、コースのすべてが見渡せつつ、安全を確保するため、床上4.5mの空中に設置した。ここでは衝突テストの開始/停止の操作をはじめ、照明やカメラ、実験車両の出し入れを行うシャッターの開閉や安全管理など、衝突実験に関する制御を一手に担っている。テストの効率化を図るため自動化システムを導入しており、衝突形態や照明、カメラの設定を記憶しておき、類似したテストを再現する際の準備期間短縮を図っている。

コントロールルーム
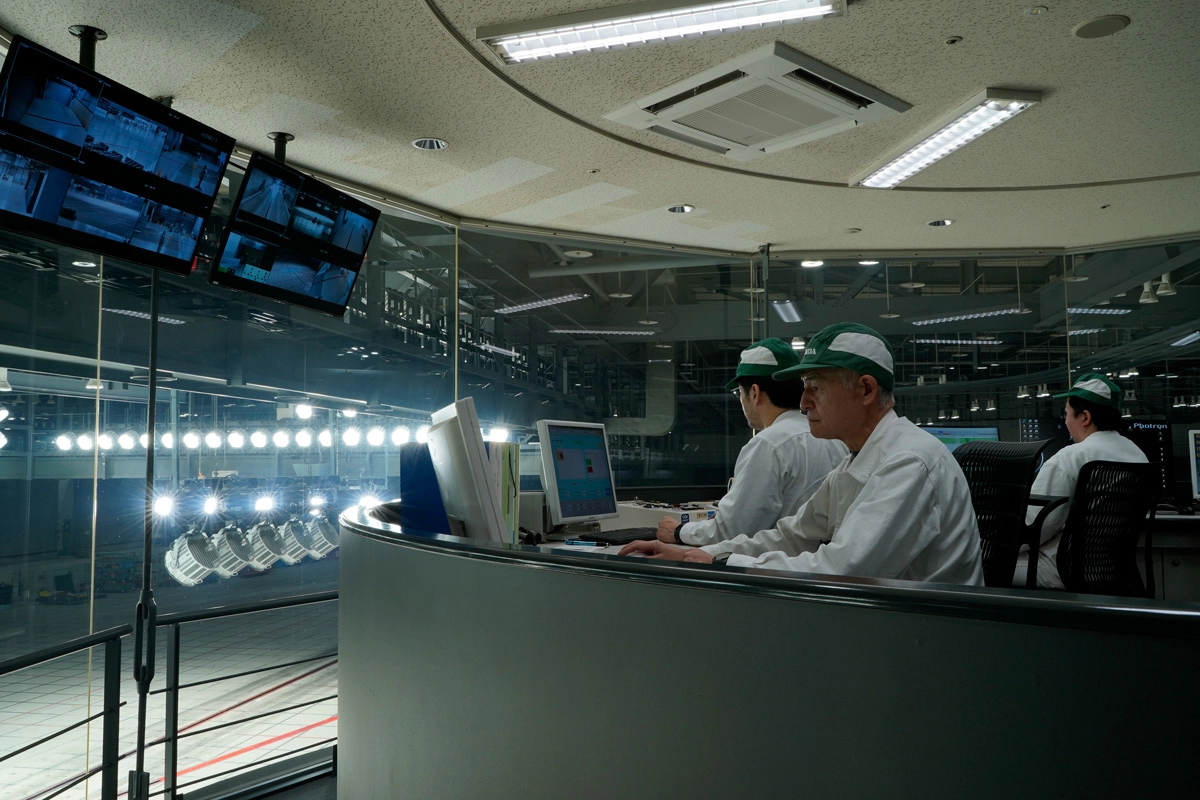
コントロールルーム
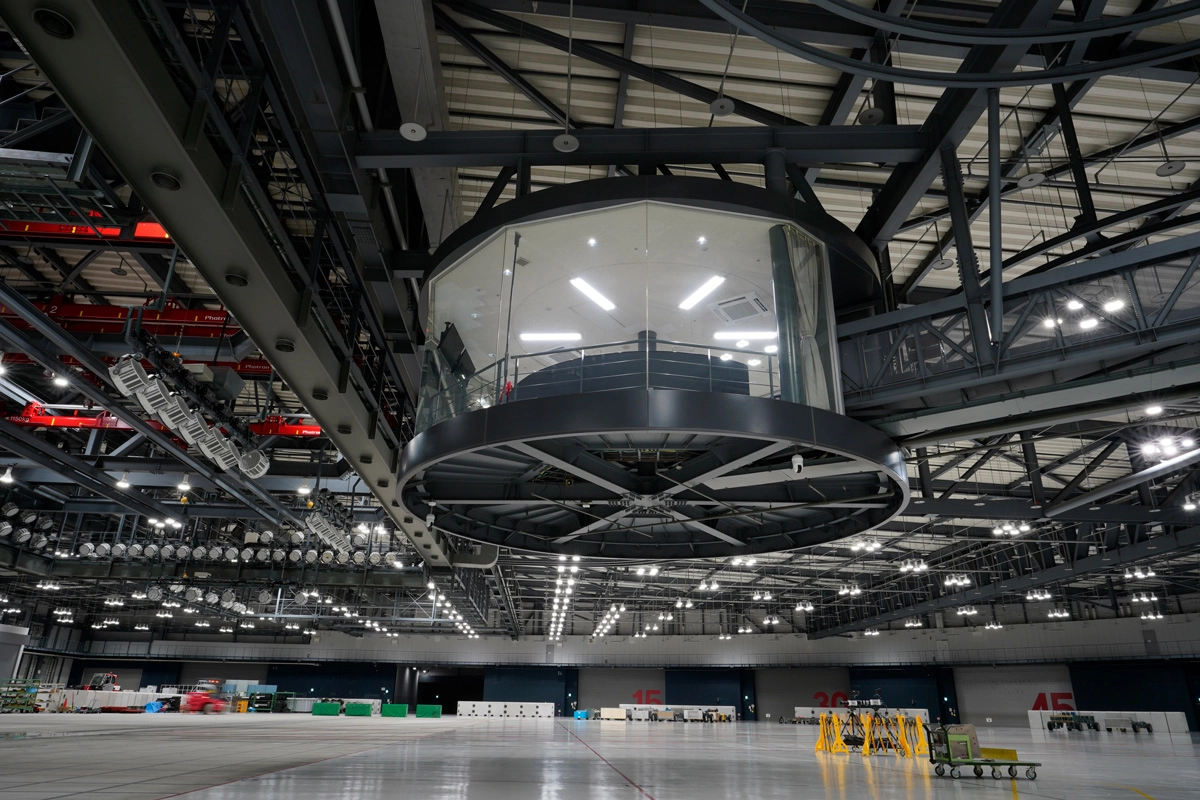
コントロールルーム
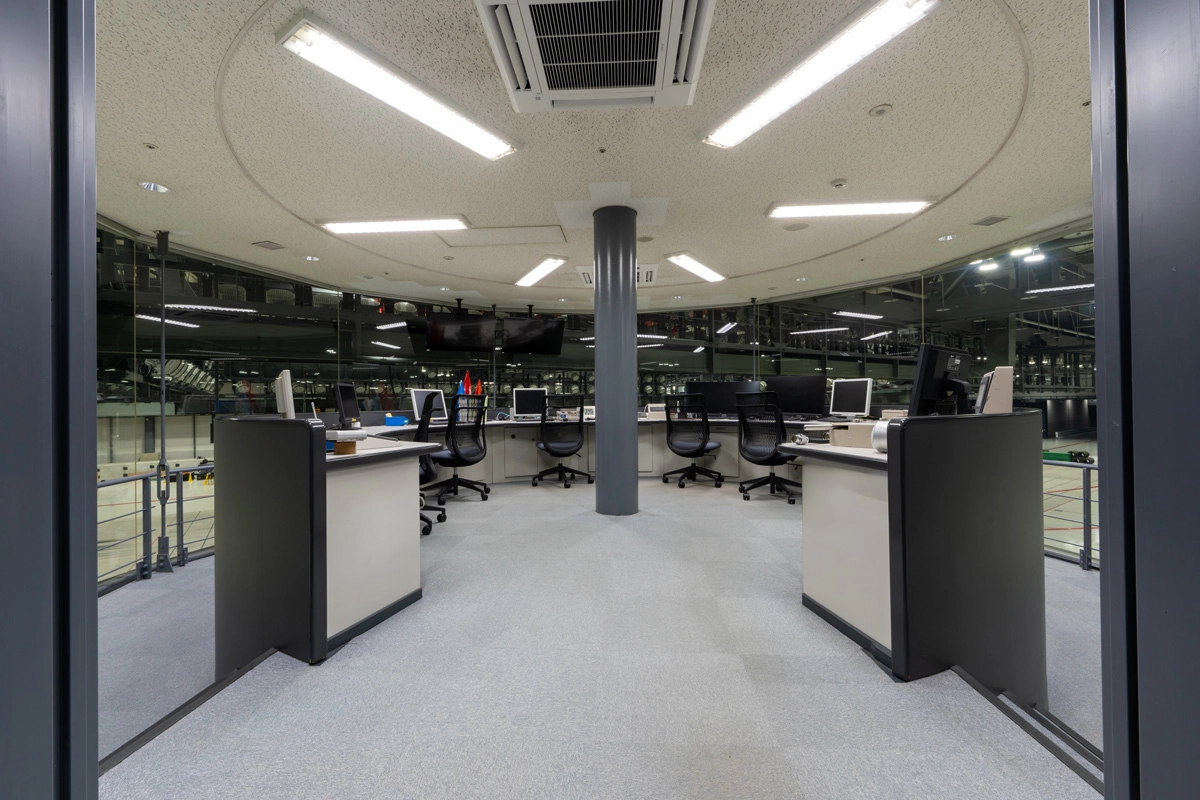
コントロールルーム
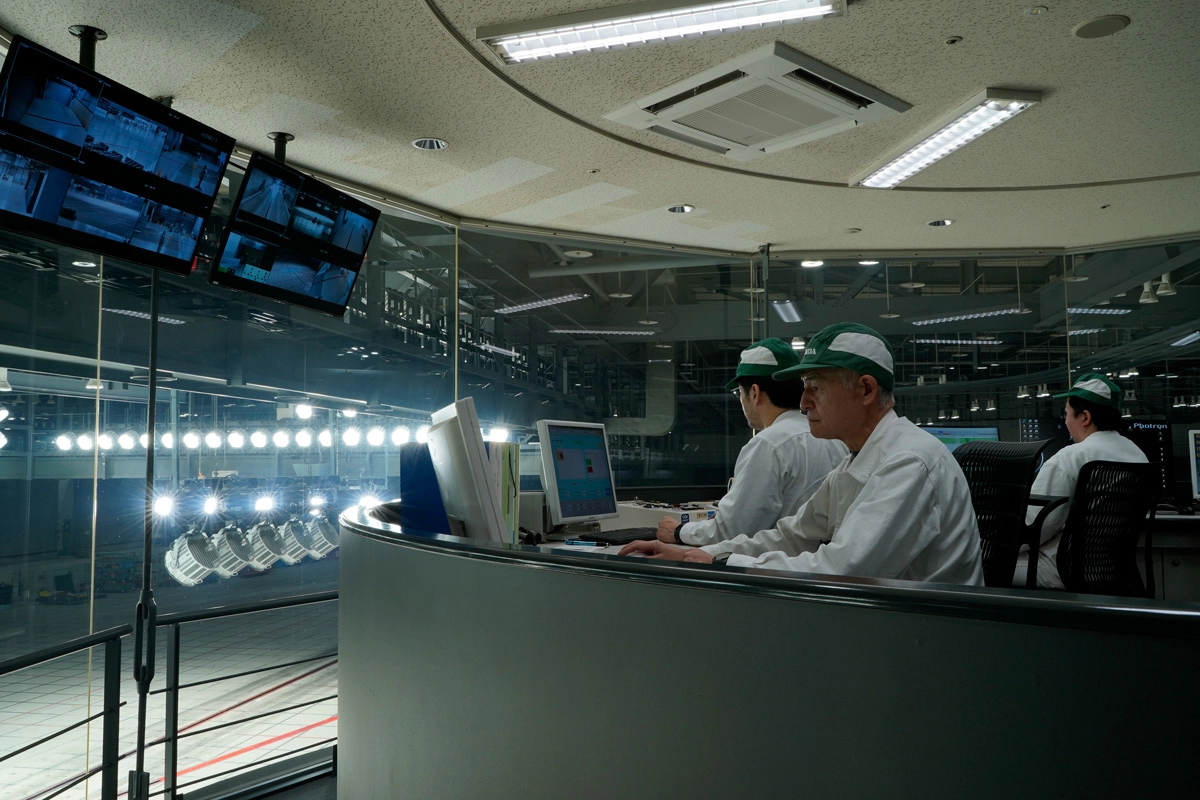
コントロールルーム
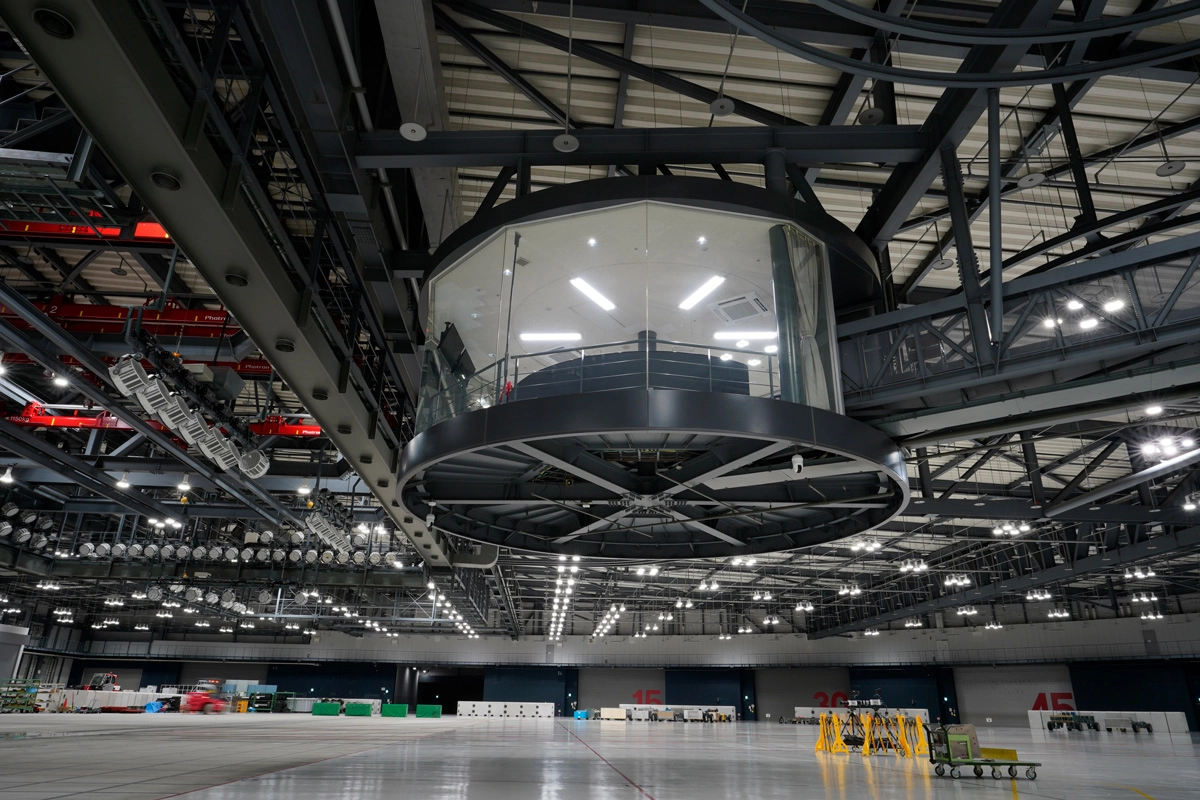
コントロールルーム
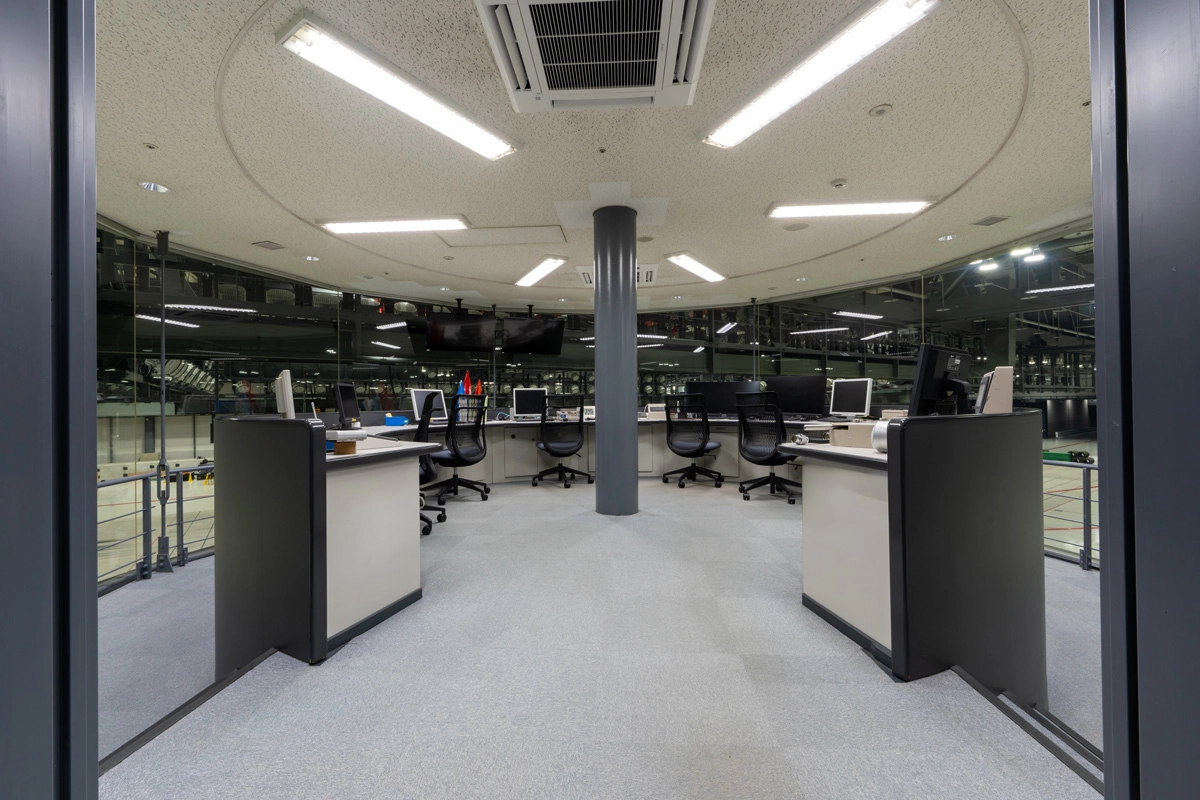
コントロールルーム
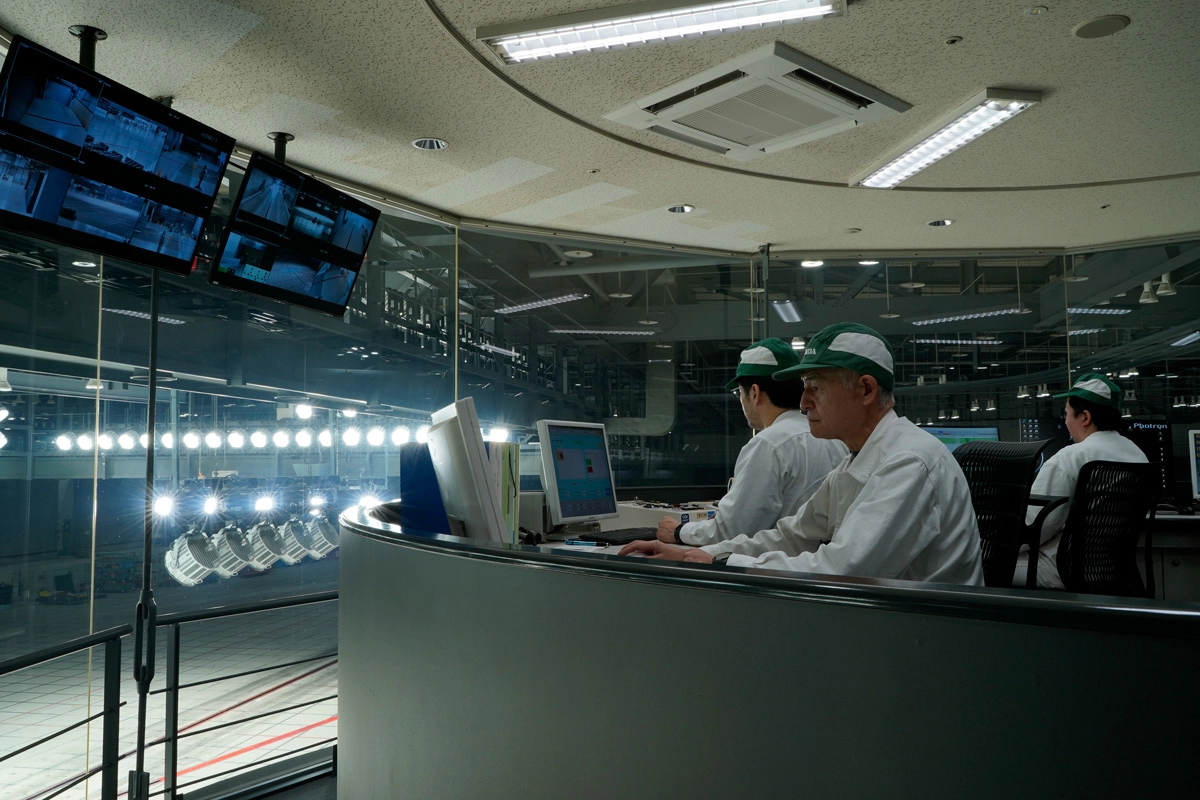

EV(電気自動車)の衝突テスト
急増するEVの衝突テストに対応するために新設したのがEV(電気自動車)作業場だ。EVが搭載するリチウムイオンバッテリーは強い衝撃が加わったり、物理的に損傷を受けたりすると発熱・発火する本質的なリスクを抱えている。HondaのEVが搭載するバッテリーパックは強い衝撃を受けても内部のリチウムイオンバッテリーが発火しない安全性を担保しているが、万が一に備え、EVは専用の作業場で計測や整備作業を行う。ここで万が一火災が発生した場合は延焼を防ぐ作業を行いつつ、鎮火後はフォークローダーで施設の外に運び、専用に設けたプールに水没させる設備を整えている。
衝突テスト後はEVもエンジン搭載車同様に、スタティックロールオーバー試験を実施するケースがある。車両を専用の装置に固定して横向きに360度回転させ、エンジン搭載車の場合は燃料の漏れ、EVのほかe:HEV(ハイブリッド車)など駆動用バッテリー搭載車の場合は電解液の漏れなどを検証する。

スタティックロールオーバー試験機
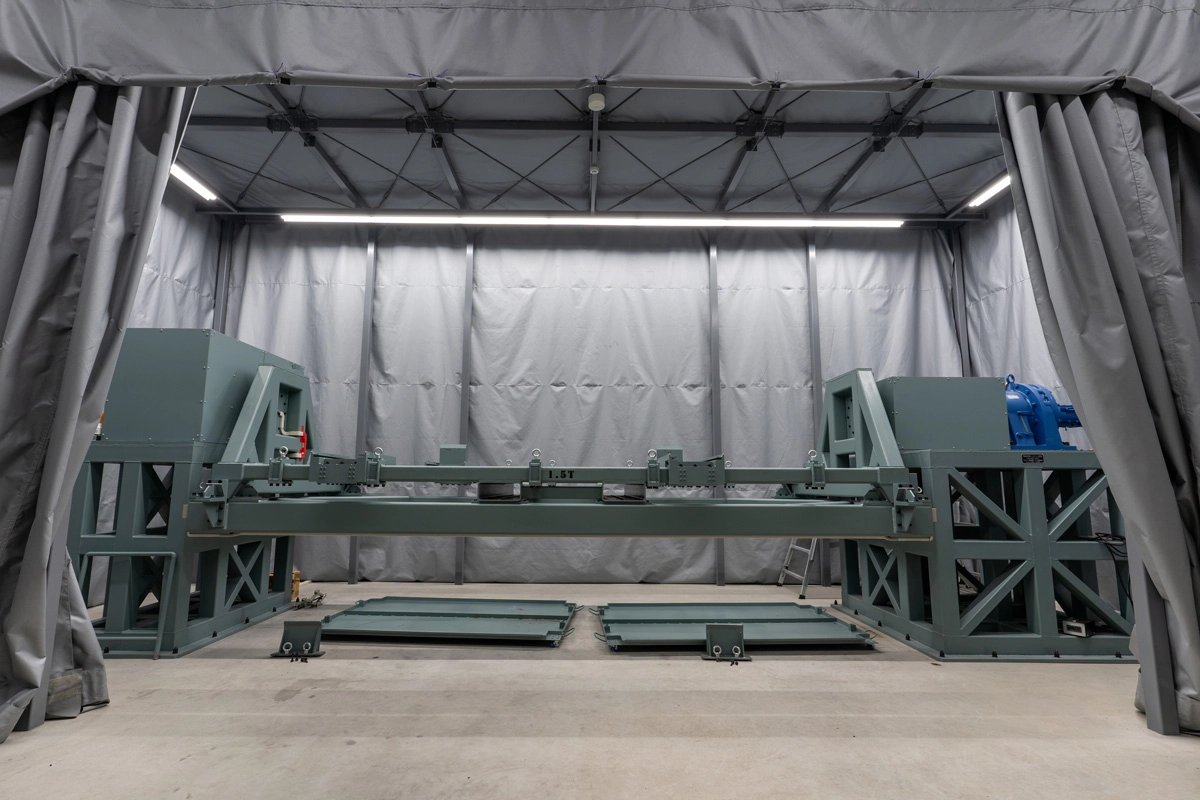
EV作業場
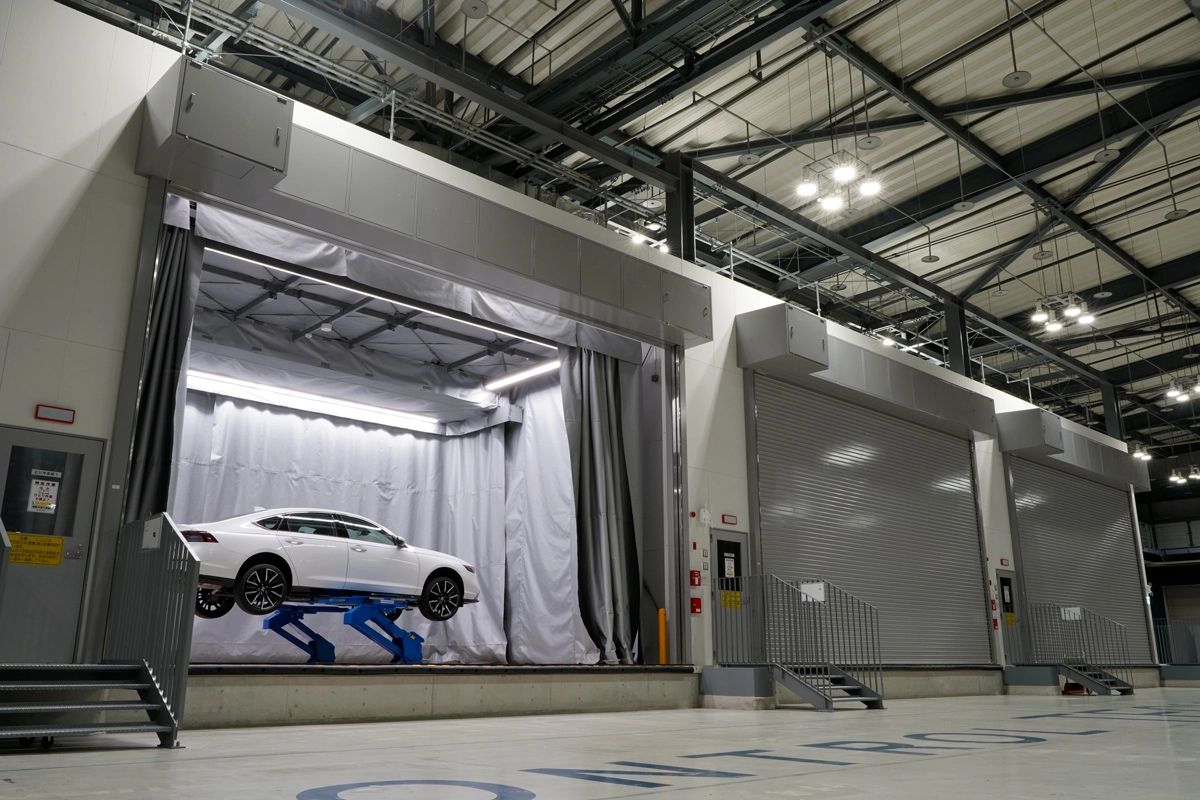
フォークローダー
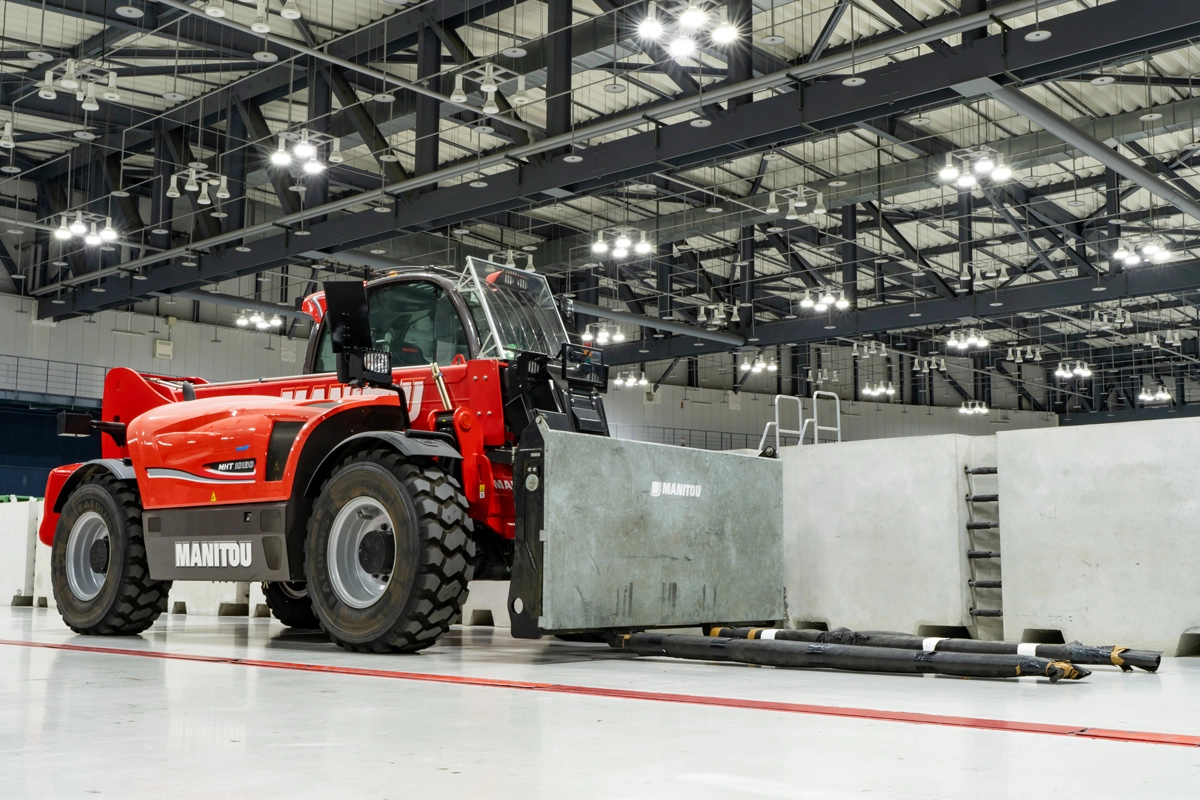
EV専用プール(水無し状態)
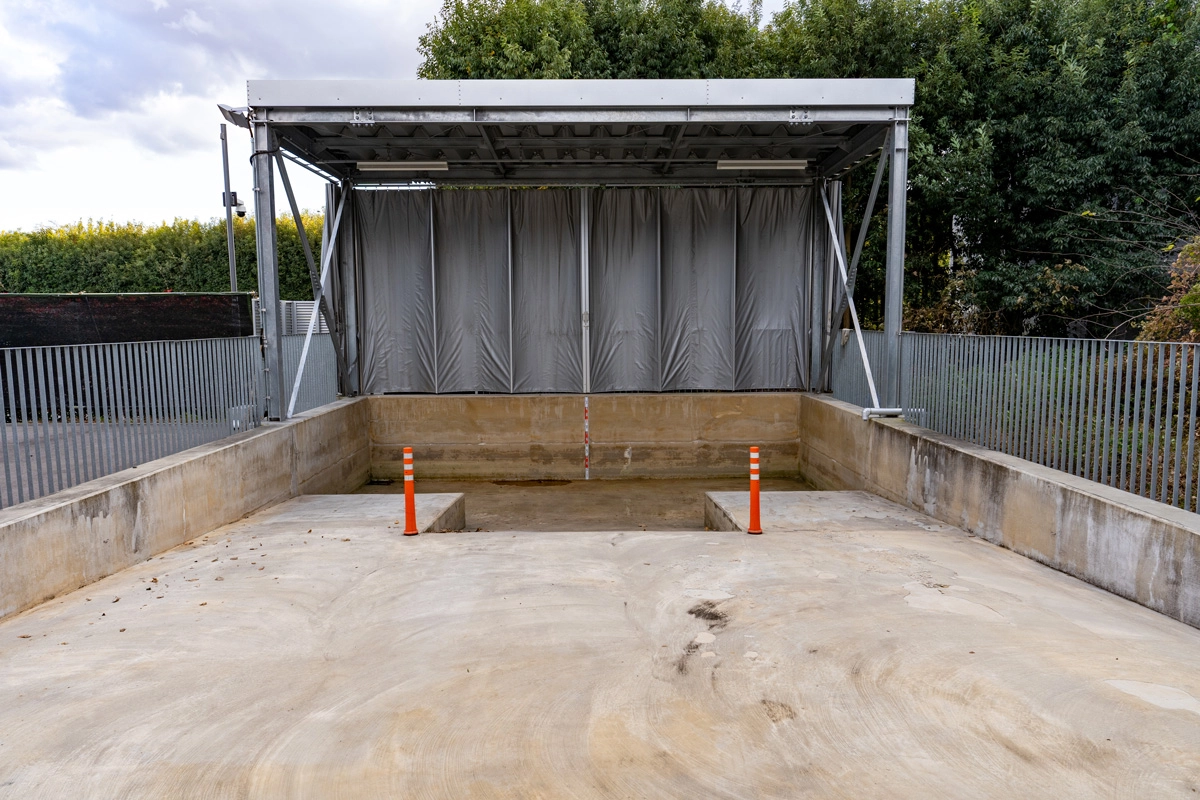
スタティックロールオーバー試験機
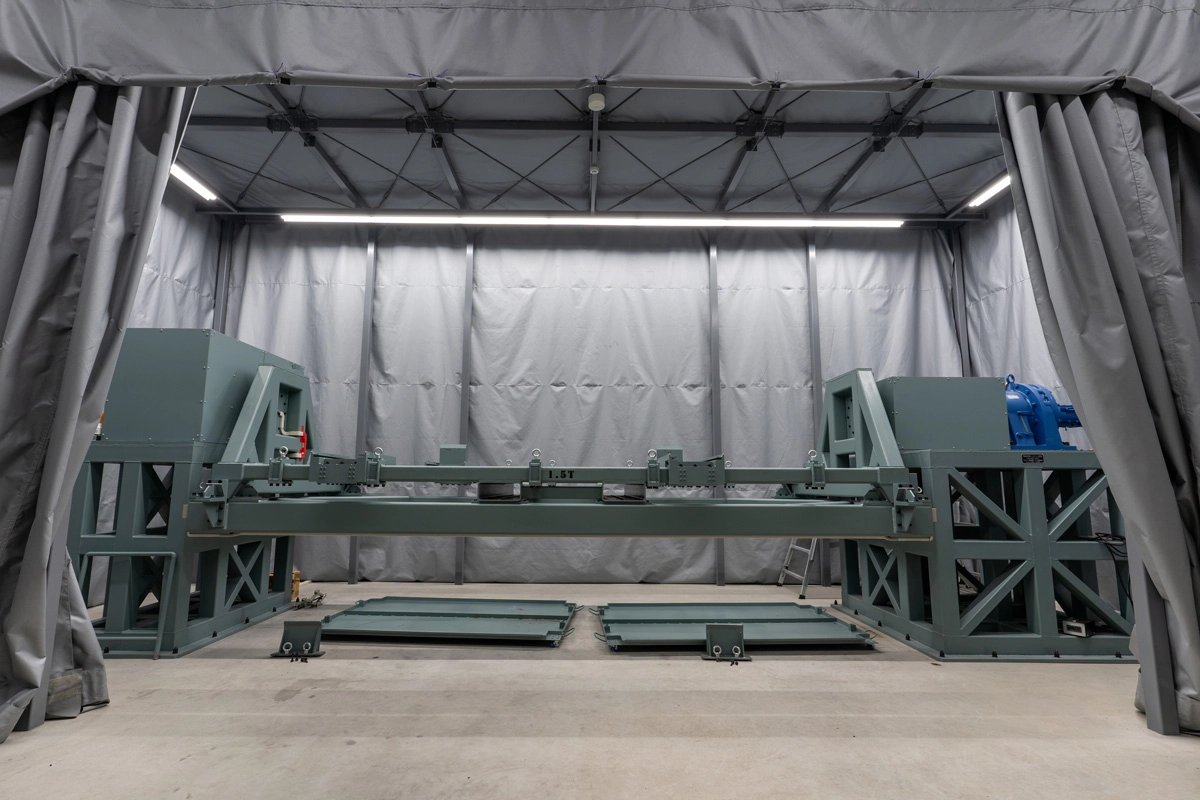
EV作業場
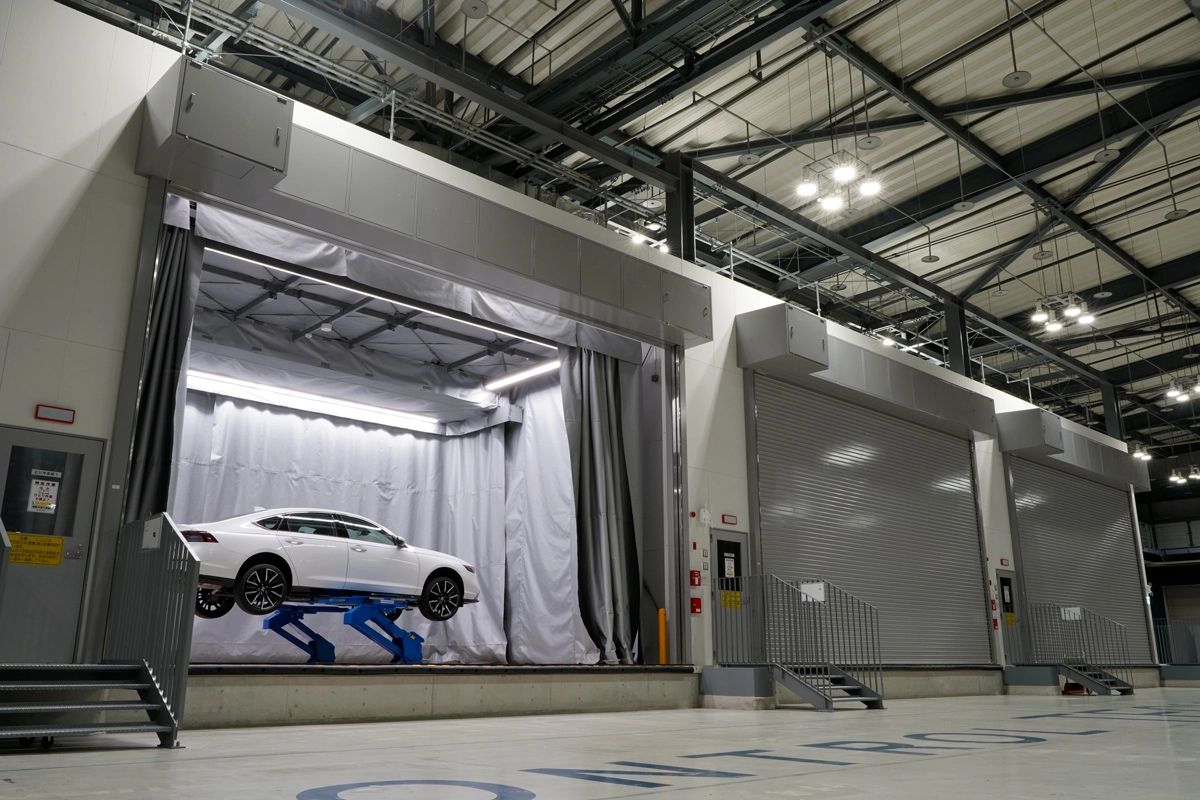
フォークローダー
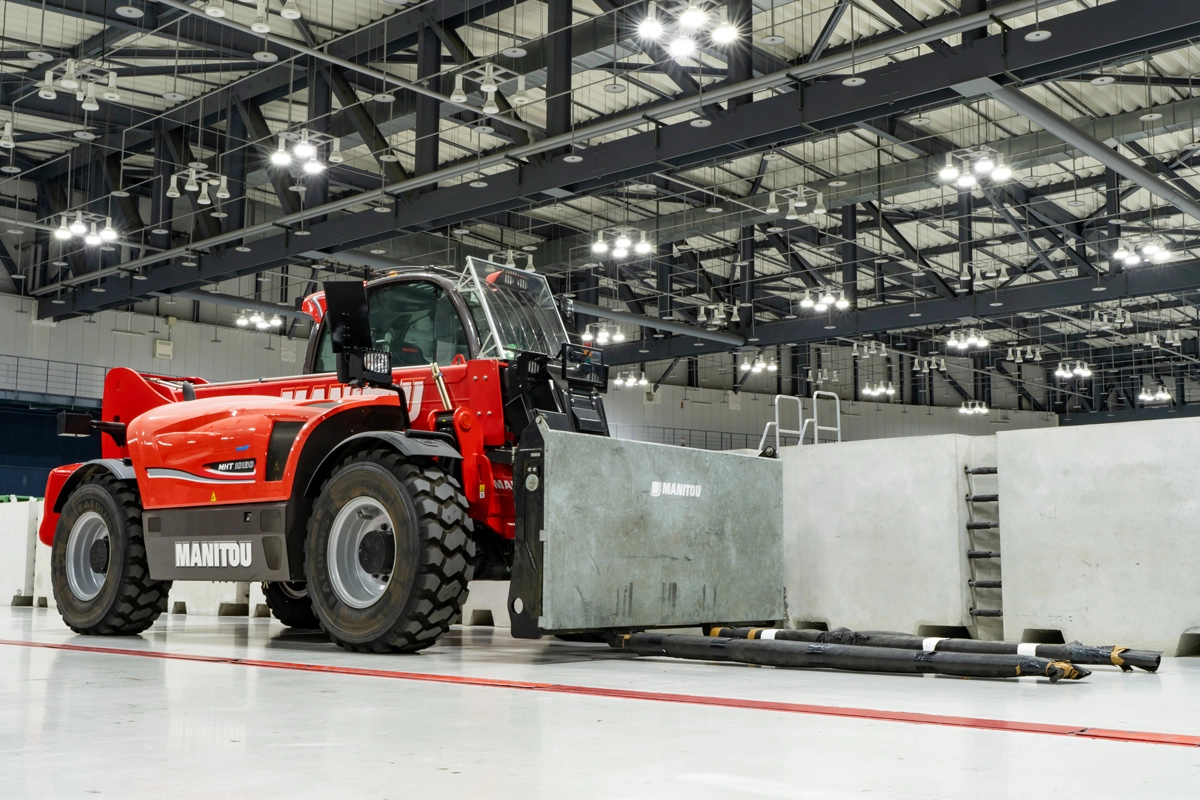
EV専用プール(水無し状態)
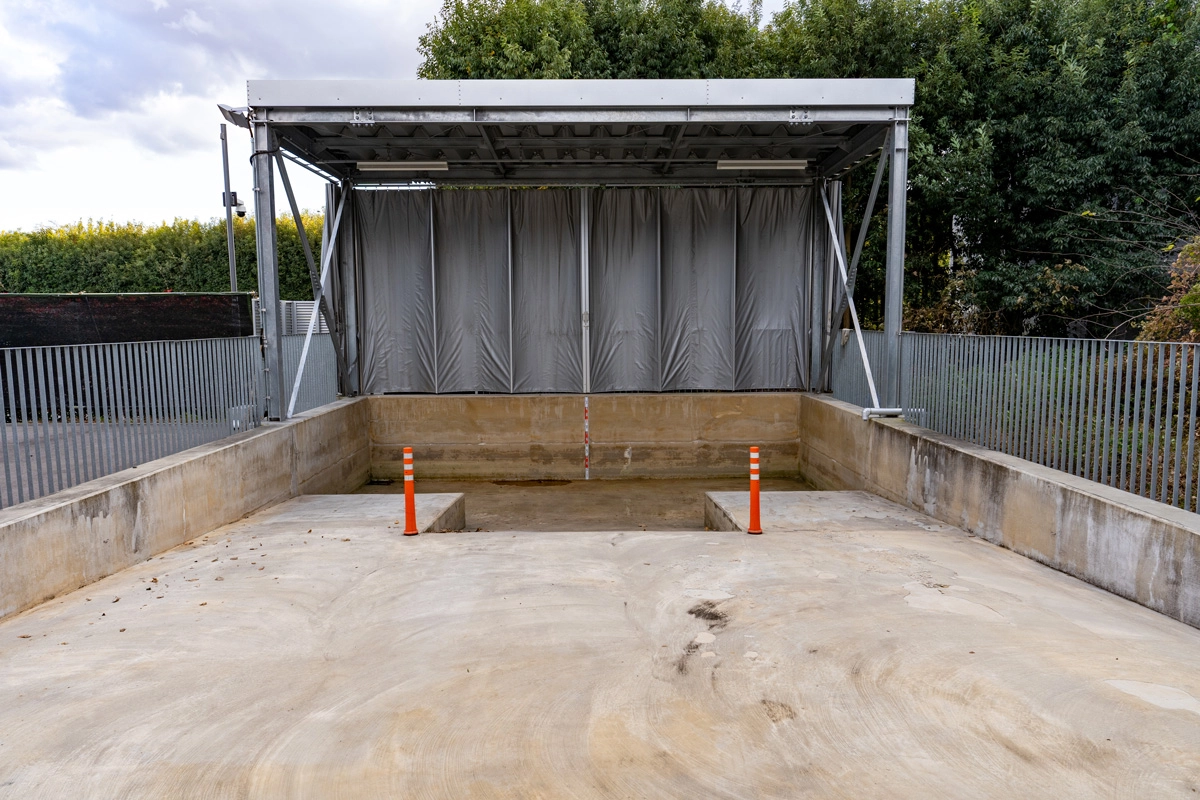
スタティックロールオーバー試験機
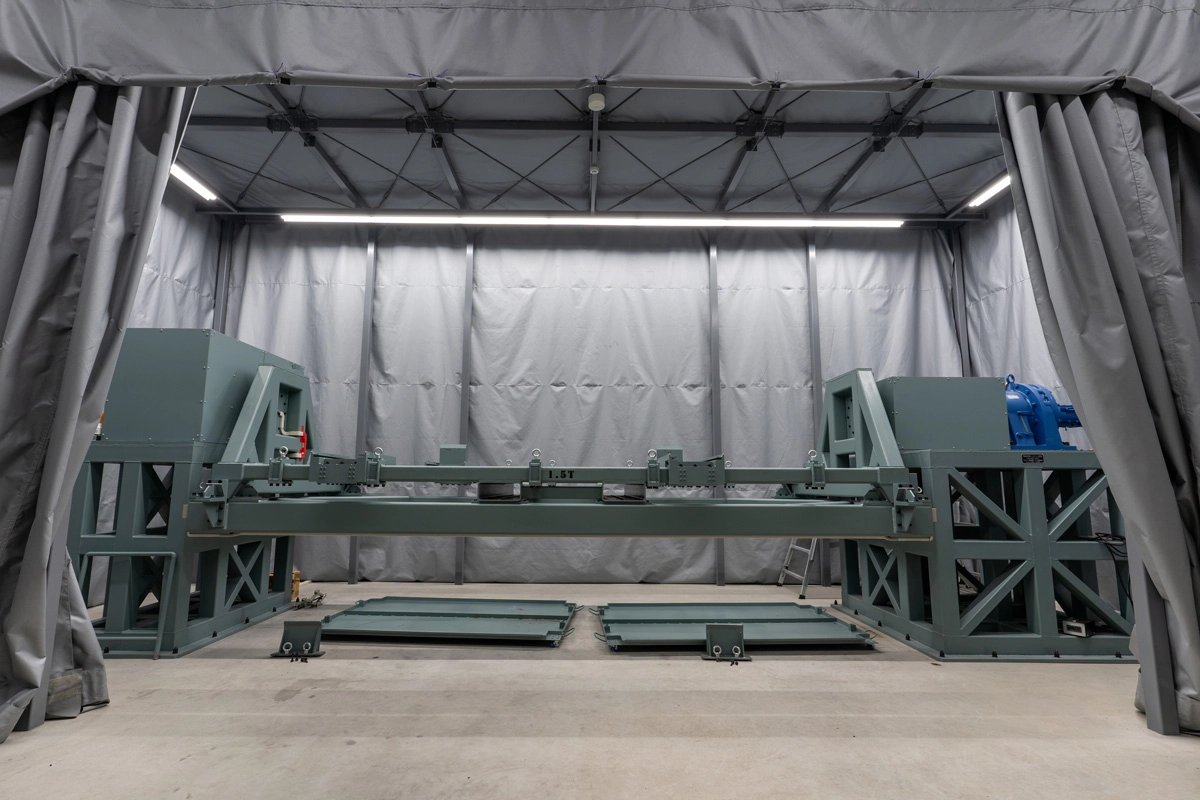

さまざまな設備と機能
屋内全方位衝突実験施設は衝突実験場のほかにもさまざまな設備や機能を備えている。ロールオーバーした際のルーフの強度を検証するルーフ強度試験機もそのひとつ。ほかにドアの強度を計測するサイドドア強度試験機や、ボンネットフードに人の頭部を模したインパクタをぶつける歩行者保護試験機などがある。
エアバッグやシートベルトの性能検証や対策の効果確認を行うために、衝突シミュレーターを用いたテストも行っている。
ピッチング付き油圧衝突シミュレーションシステムは、クルマの室内を再現したスレッド(台車)を油圧ピストンで打ち出し、その油圧ピストンの制御により実際に衝突したときと同じ減速の状況を精度高く再現する。実際の衝突時は車体が前傾姿勢になるため、この動きを再現するため油圧でピッチングを制御できるようにしているのも特徴だ。
衝突の瞬間を撮影する高速度カメラやLED照明が設置されているのは、衝突実験エリアと同じ。前面フラットバリアモードのみでなく、斜めに衝突させるオブリークモードにも対応する。スレッドを発射するカタパルト(射出機)は4台設置。次のテストに向けた準備をあらかじめ済ませておくことでリードタイムを短縮することができ、テストの効率化を図っている。

正面衝突テスト
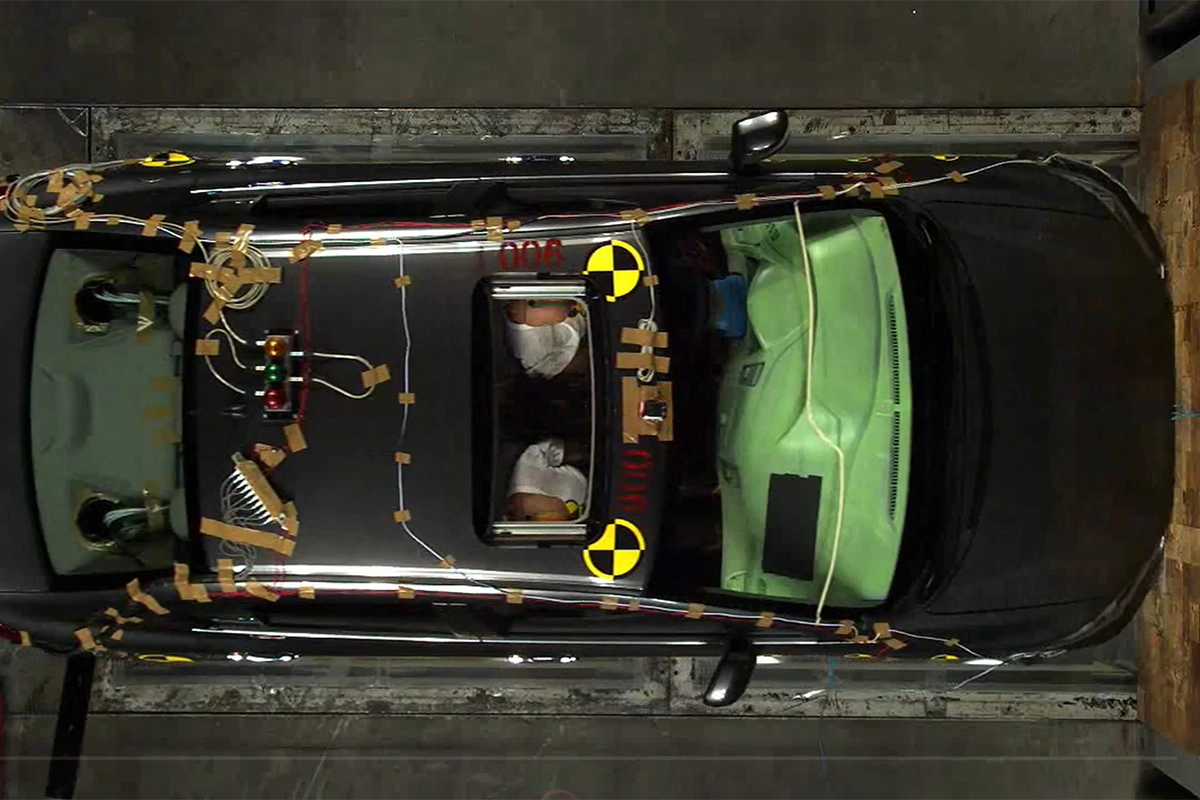
ルーフ強度試験機
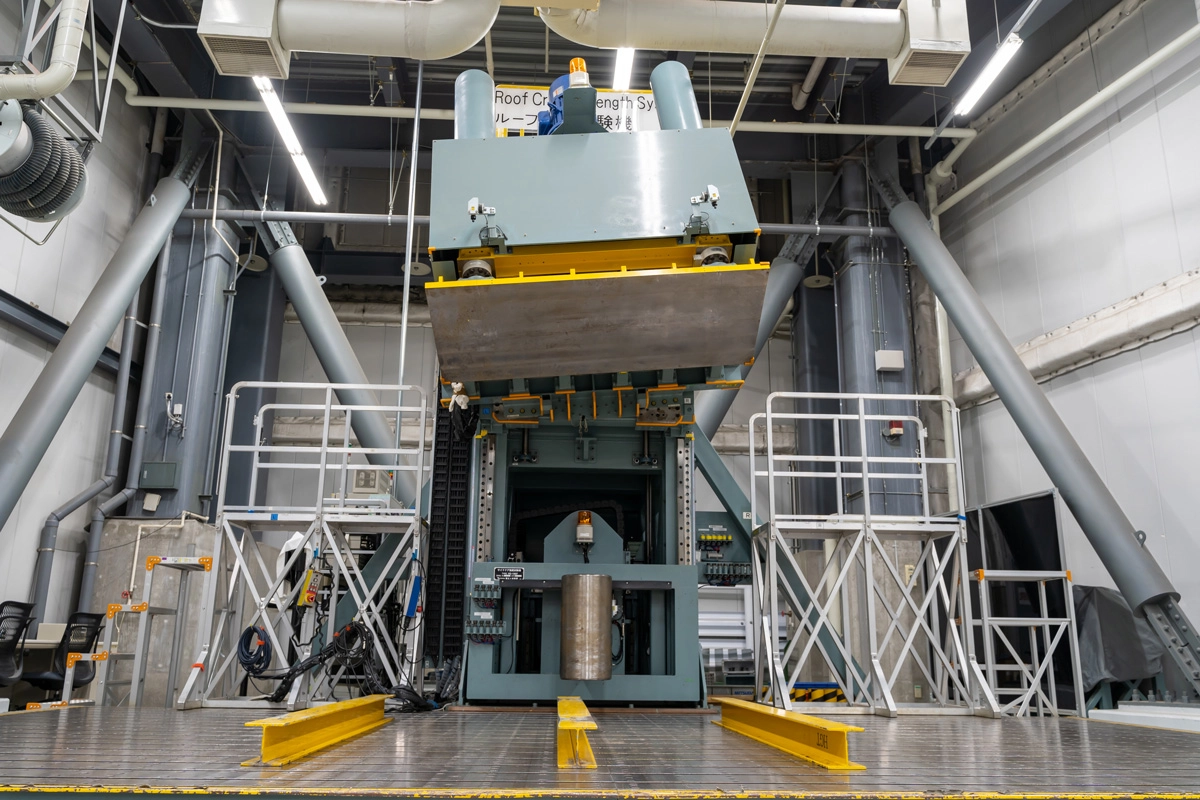
ルーフ強度テスト
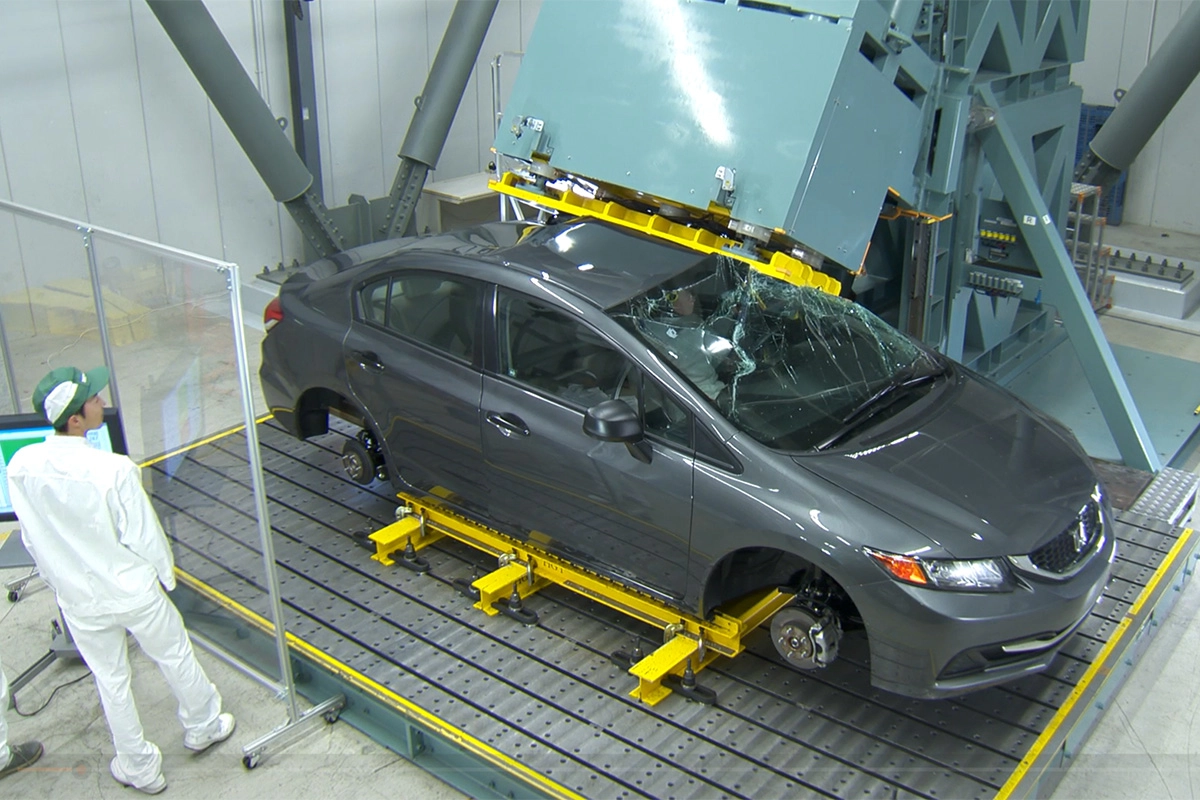
ピッチング付き油圧衝突シミュレーター
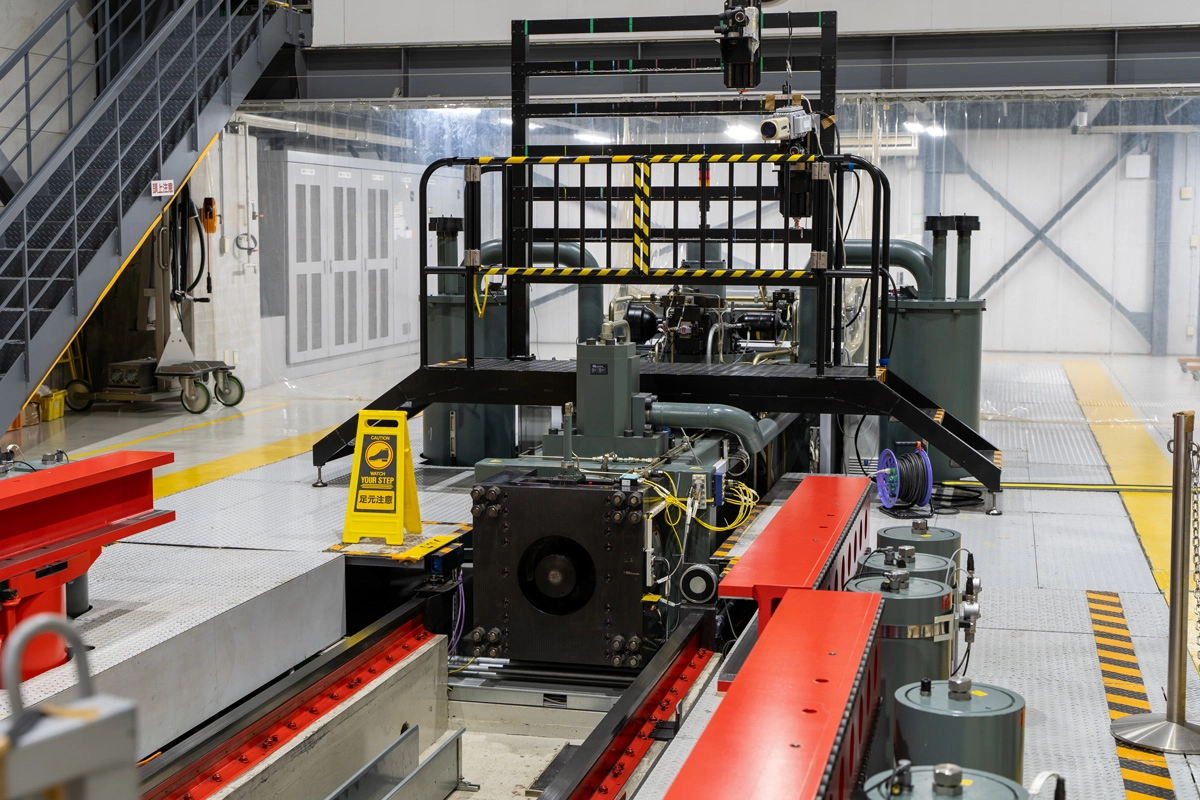
正面衝突試験場
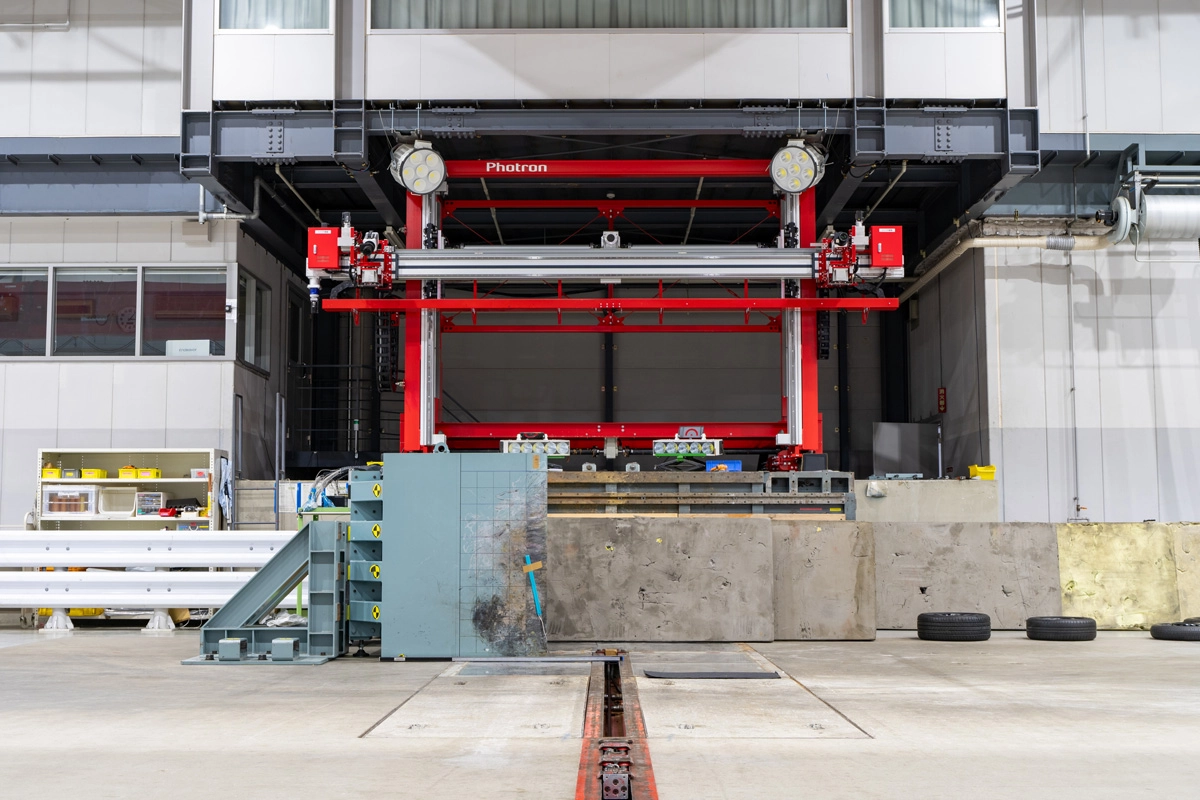
正面衝突テスト
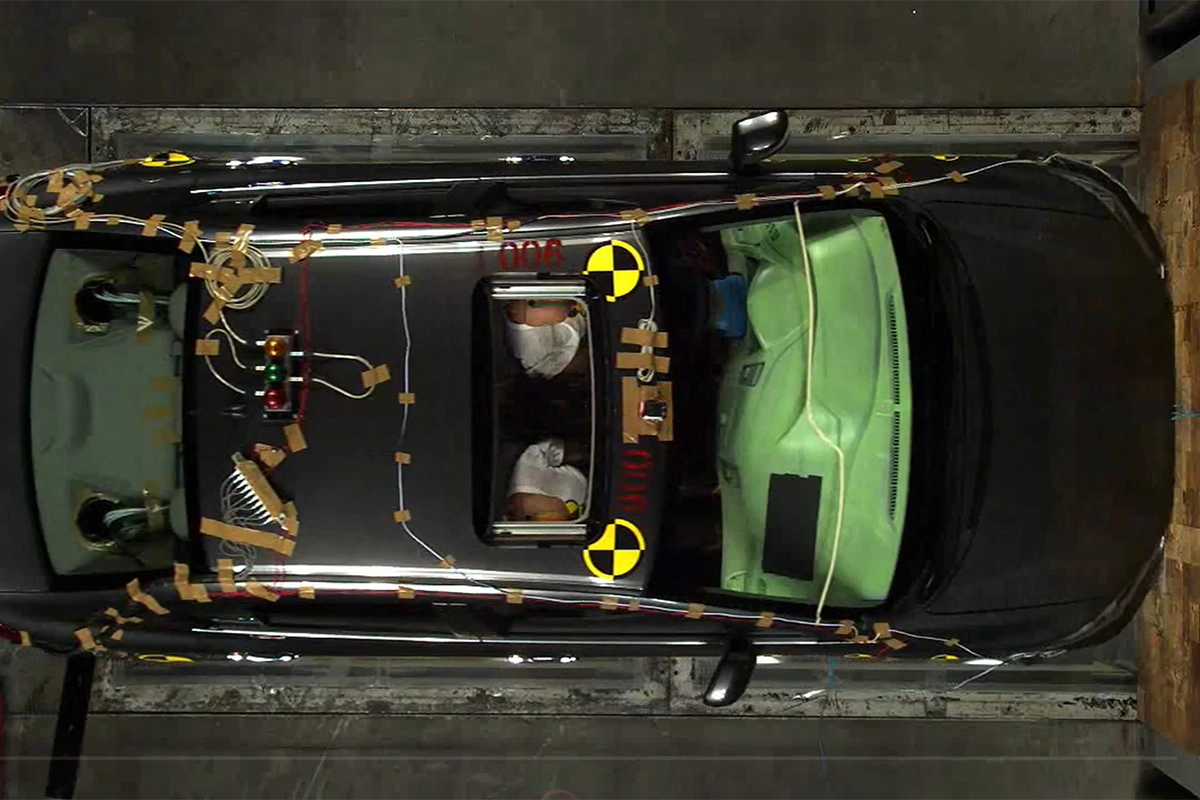
ルーフ強度試験機
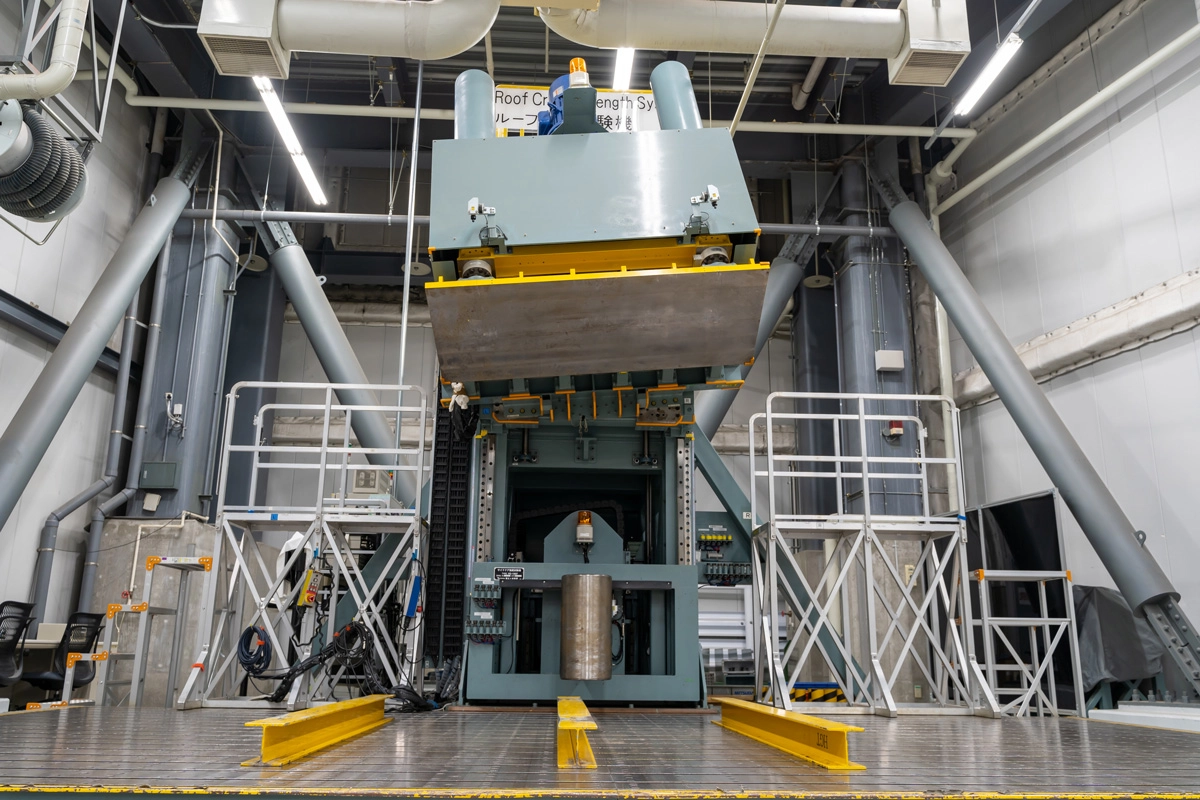
ルーフ強度テスト
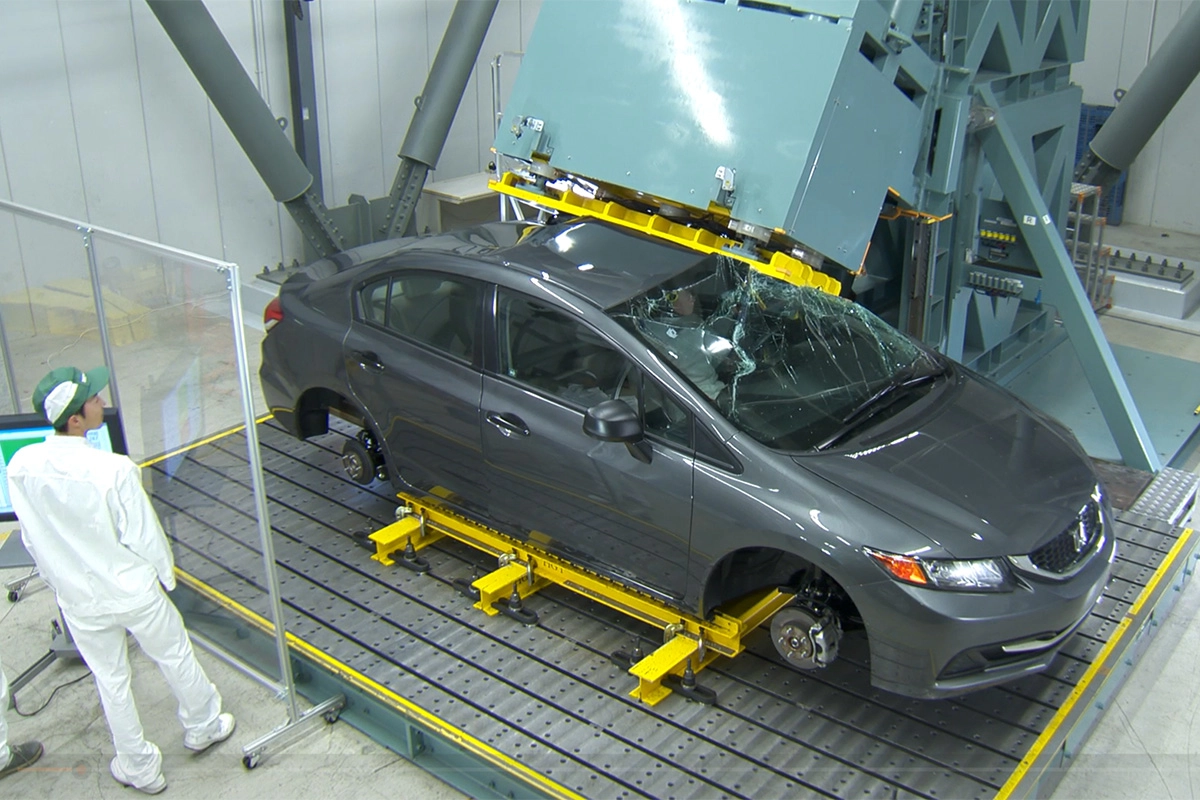
ピッチング付き油圧衝突シミュレーター
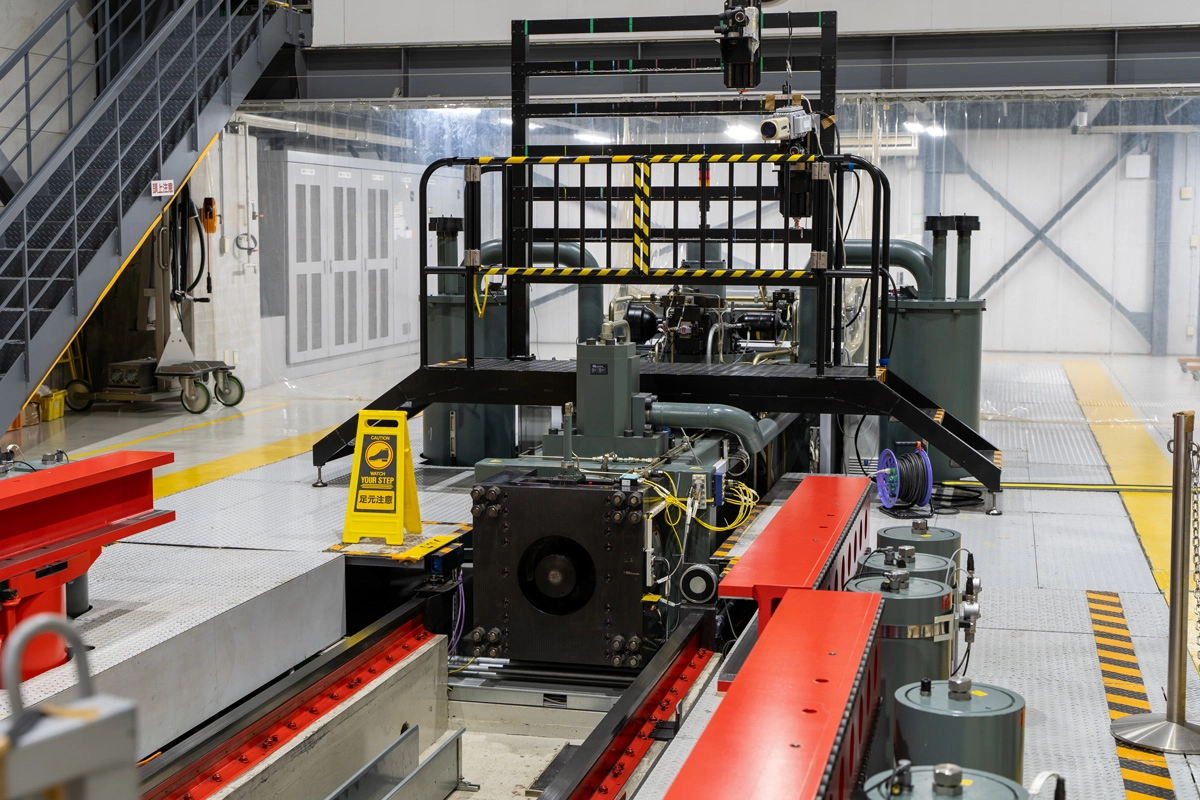
正面衝突試験場
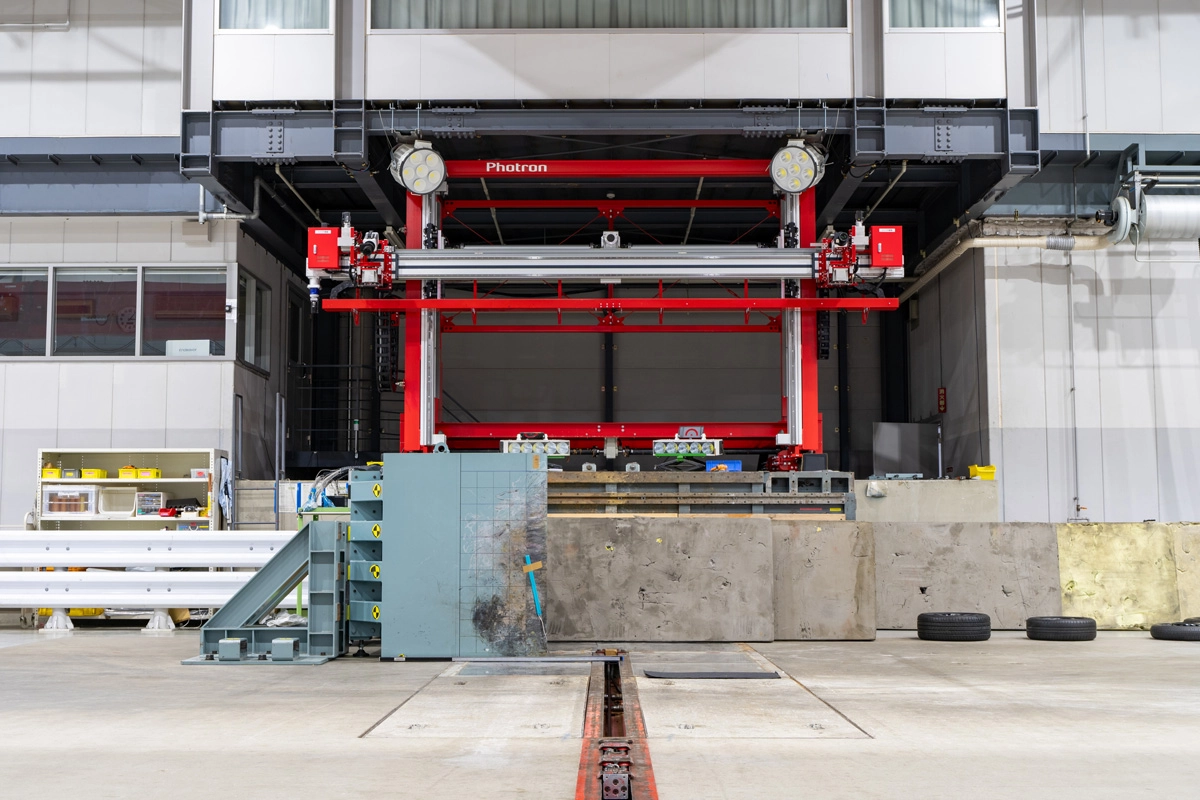
正面衝突テスト
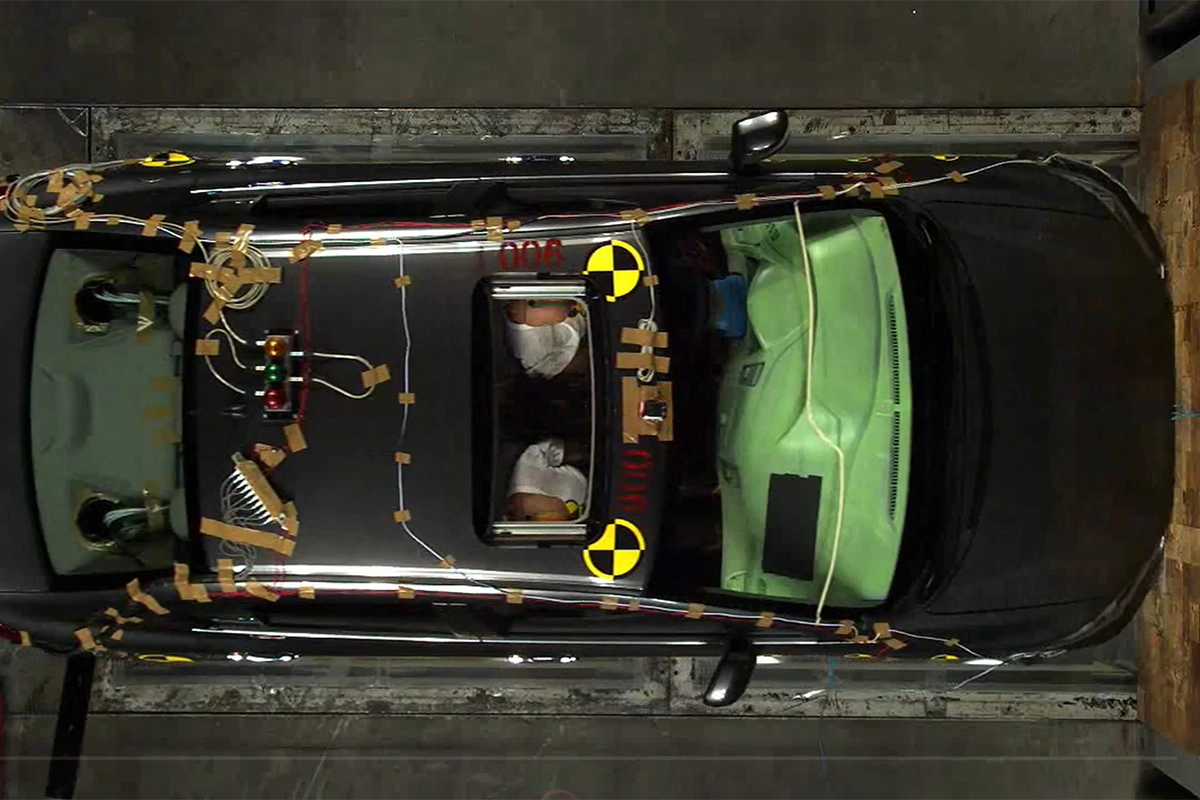

衝突試験用ダミー整備室
ダミー整備室では衝突テストで使うダミー人形の性能が規定内にあるかどうか確かめる検定や整備作業を行っている。ダミーは前面衝突や側面衝突などの衝突形態や、測定したい部位ごとに種類があり、さらに体格差や性別差、年齢差を考慮して種類を取りそろえている。最新のダミーは骨格の形状をより人体に近づけたうえでこれまでの荷重や加速度に加え、脳傷害に影響を与えると考えられている角加速度が計測できるようになっている。
ダミーは繰り返し使うのが基本だが、テスト3回に1回程度の頻度で検定を実施して、明確な異常が発生した場合や規定値外の場合は、部品交換などを行い整備する。ダミーは規定の性能を発生する温度幅が定められていることから、ダミー整備室は年間を通じて決められた温度・湿度の範囲内に管理している。

ダミーの調整
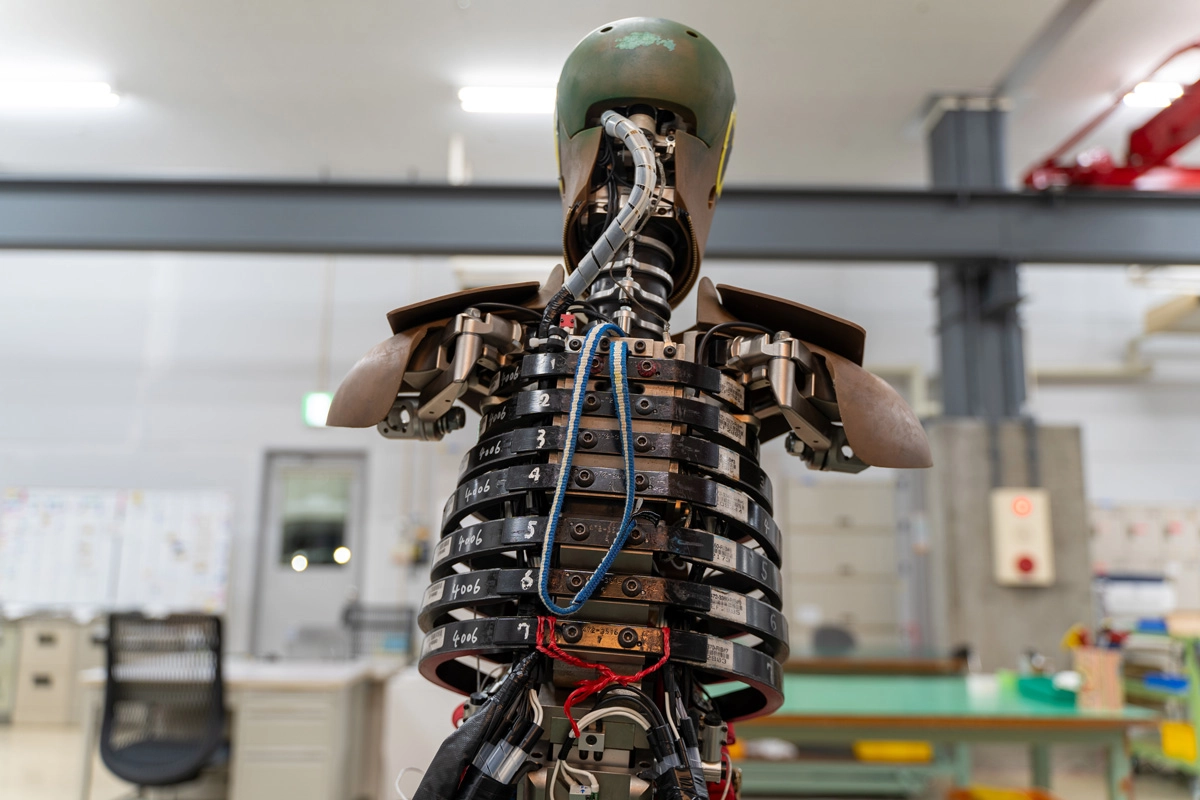
ダミー整備室
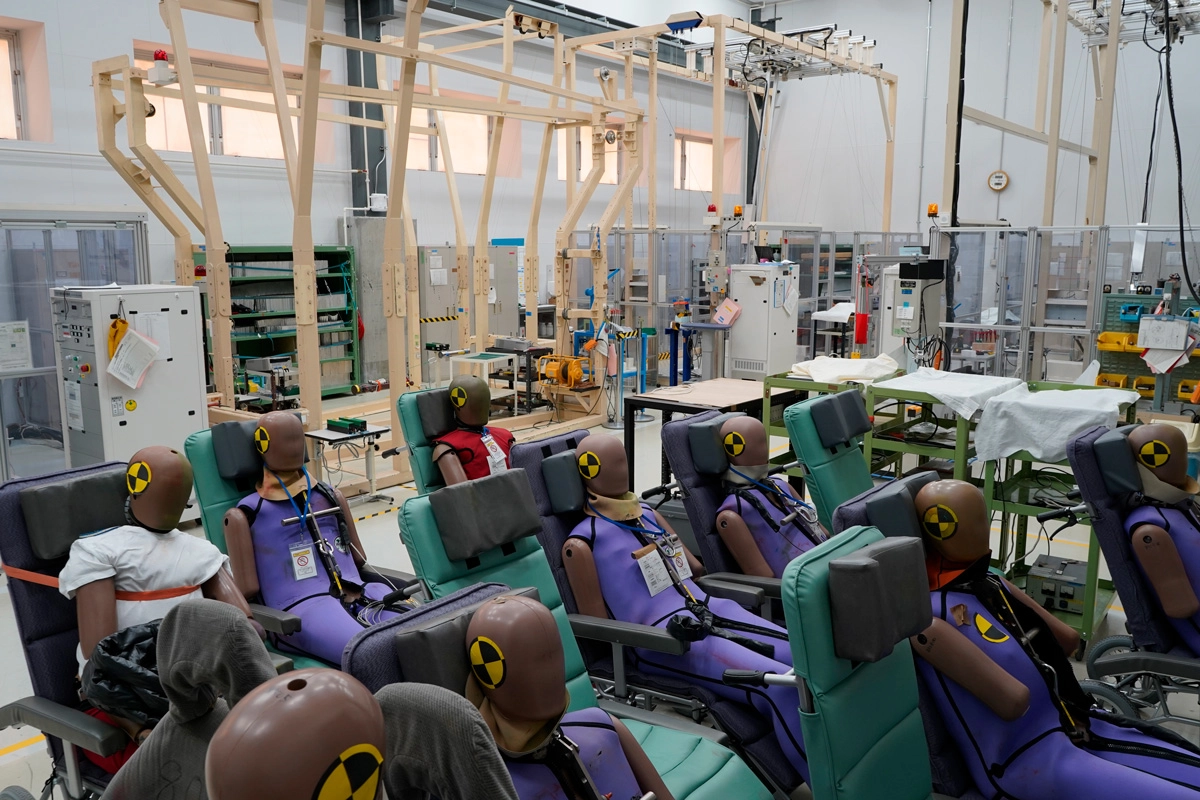
様々なダミー
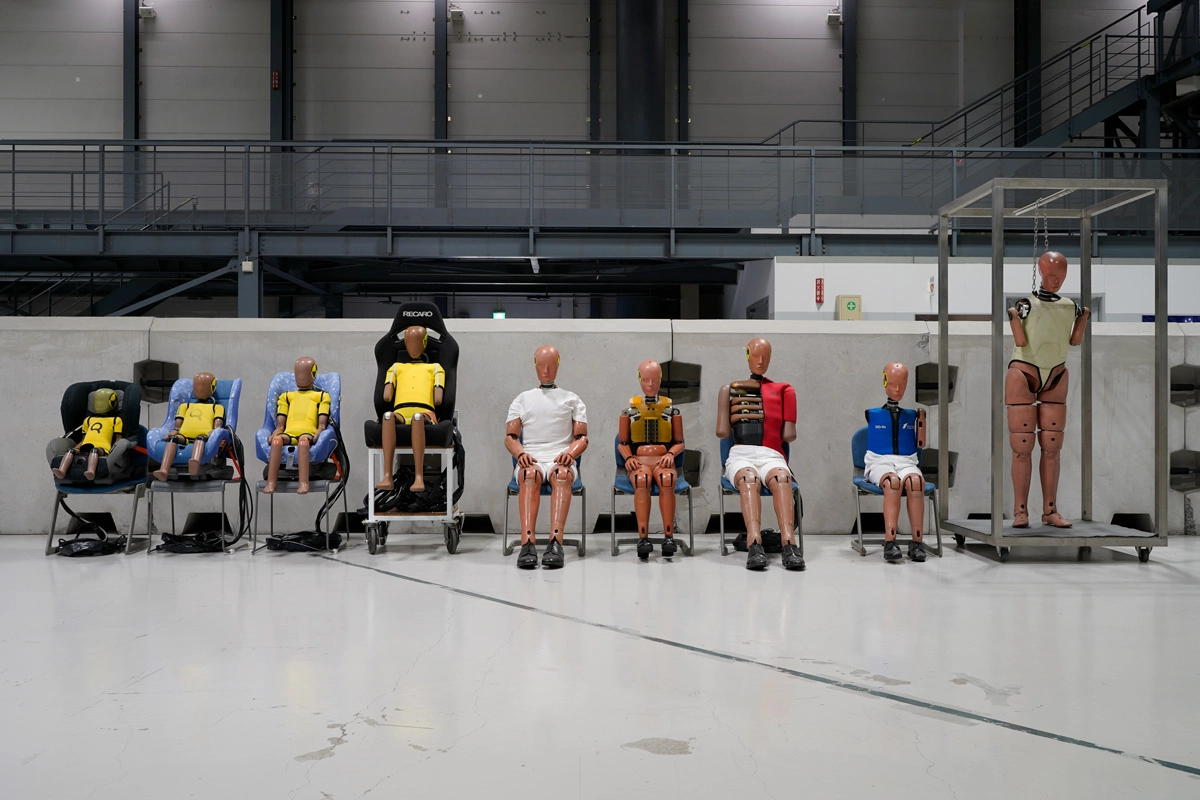
ダミーの調整
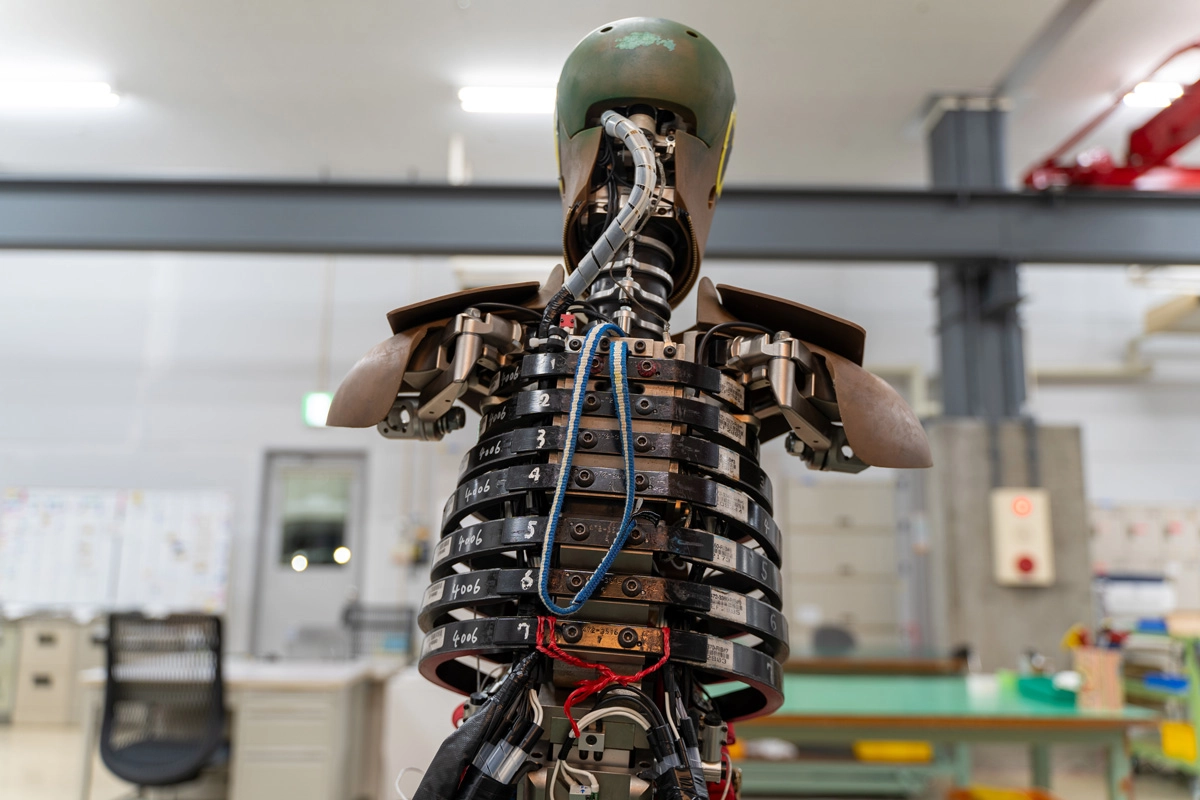
ダミー整備室
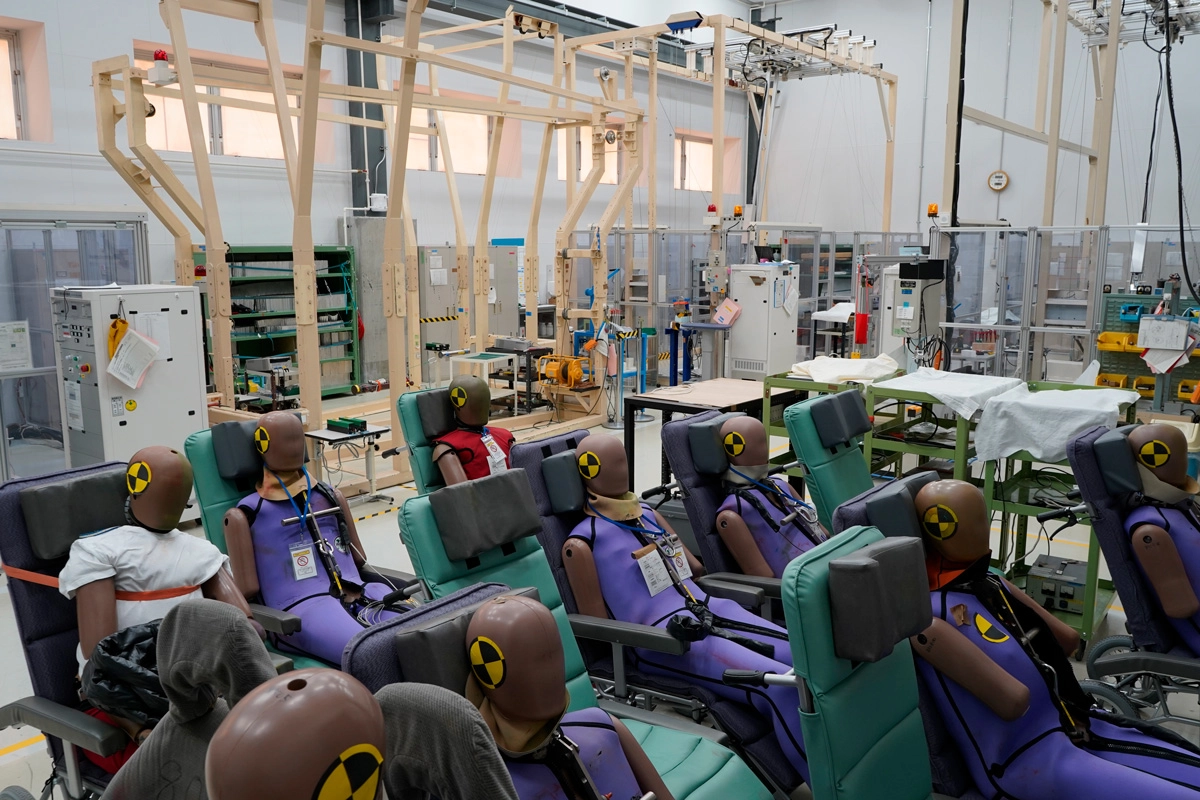
様々なダミー
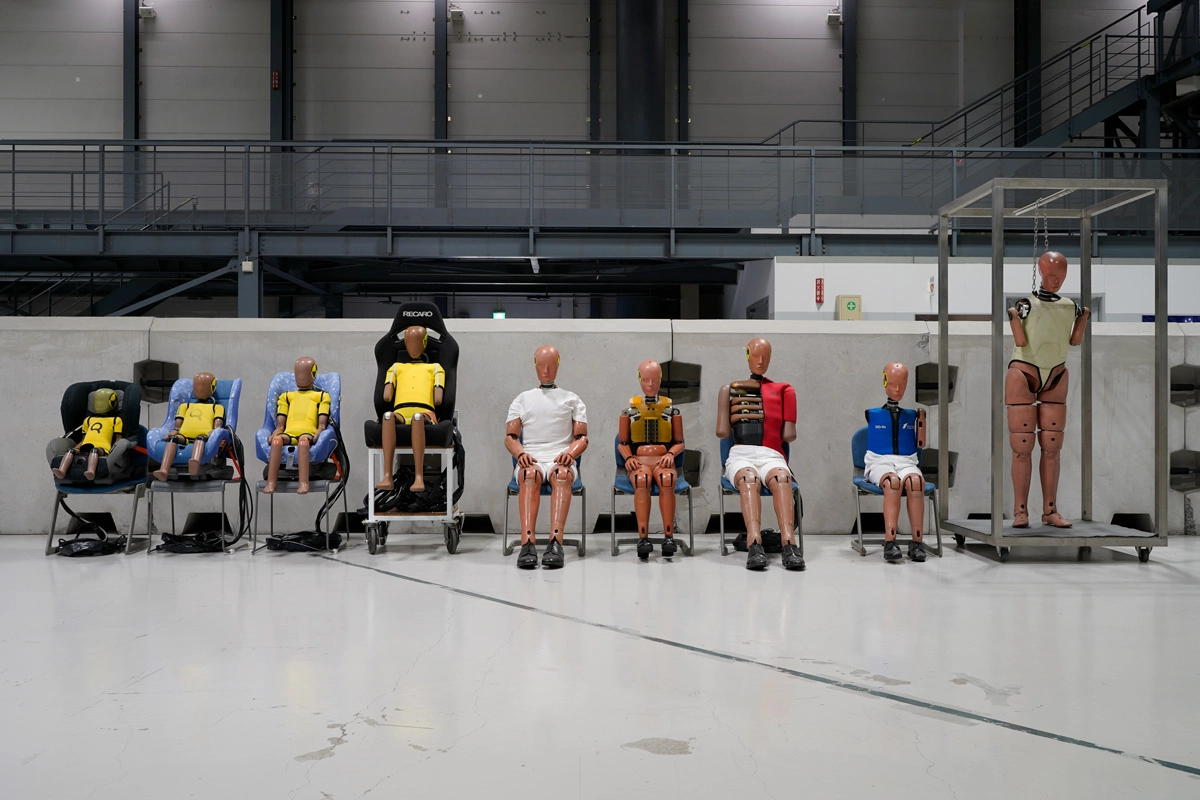
ダミーの調整
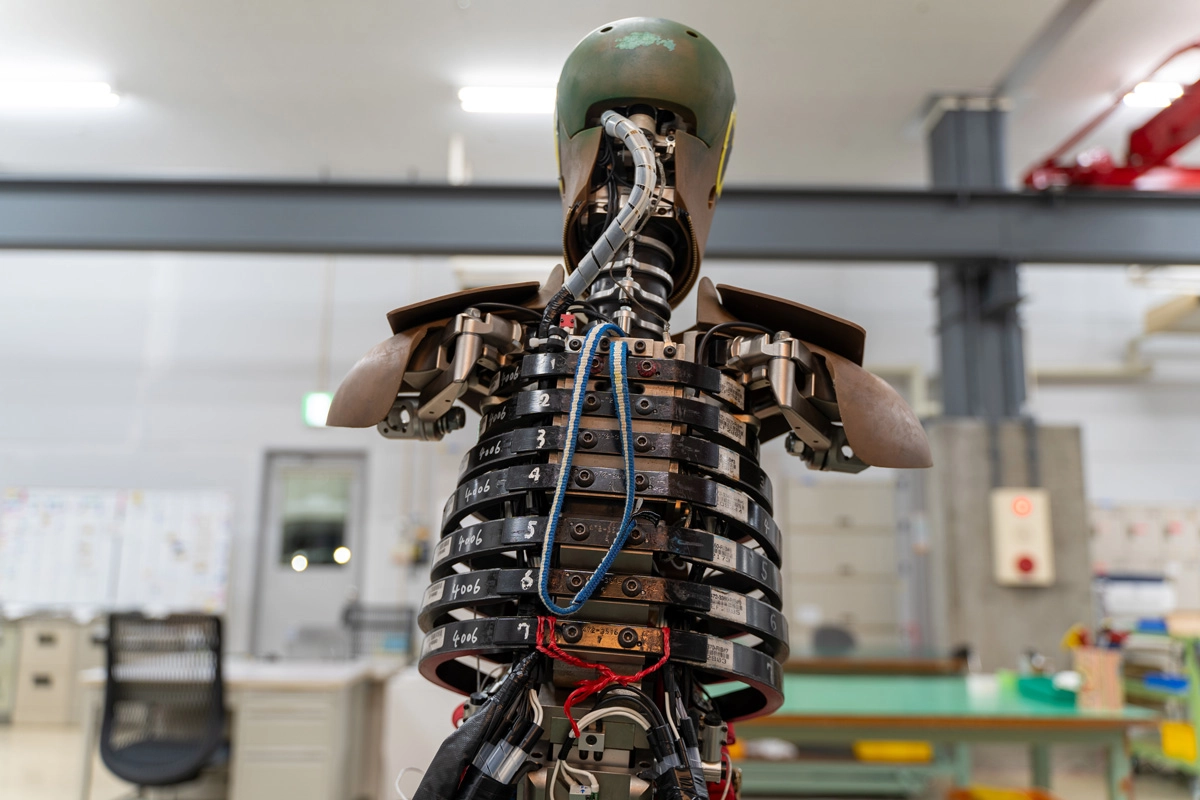

屋内全方位衝突実験施設の活用による技術
屋内全方位衝突実験施設の活用による成果のひとつが、現在すべてのHonda車に適用しているコンパティビリティ対応ボディーだ。骨格の形状や配置に工夫をこらすことにより面で衝突の衝撃を広く受け止めて骨格のすれ違いを防止。受けた衝撃は複数の経路に分散することで、衝突エネルギーを効果的に吸収。これらの技術により、大きなクルマと小さなクルマで衝撃吸収がほぼ同じになるようにした。
またHondaでは、「Safety for Everyone」の考えのもと、独自に歩行者ダミーを開発。歩行者傷害値の低減技術を研究しており、そのためのテストも行っている。代表的な活用事例が、ポップアップフードシステムだ。フロントバンパーに内蔵した圧力センサーが歩行者との接触を感知するとボンネットフードの後ろ側が持ち上がり、硬いエンジンなどとの間に空間を設けて歩行者の頭部に与える衝撃の緩和を補助する仕組みとなっている。
Hondaはこのように屋内全方位衝突実験施設を最大限活用し、現実の道路で起こりうるさまざまな事故形態をリアルに再現。数々の衝突テストで得られた知見と時代の要求に応じたアップデートを繰り返すことで、リアルワールドにおけるさらなる衝突安全性の向上に取り組んでいる。
INDEX
Hondaの研究開発施設
- 第1回 ものづくりはここから始まる「Hondaの研究開発」
- 第2回 道が製品を決める「栃木プルービンググラウンド」
- 第3回 道が製品を鍛える「鷹栖プルービンググラウンド」
- 第4回 空気を味方に、風を極める「実車風洞」
- 第5回 モビリティの核はここで鍛える「台上試験施設」
- 第6回 極限の環境でHondaを仕立てる「環境試験施設①」
- 第7回 極限の環境でHondaを仕立てる「環境試験施設②」
- 第8回 革新的なカタチをスピーディーに作る「金属3Dプリンター」
- 第9回 すべてはリアルで証明する「全方位衝突実験施設」
- 第10回 バーチャルが変える開発プロセス「XR検証施設」
- 第11回 自動運転に向けたバーチャルとリアルの融合「ドライビングシミュレーター」
関連コンテンツ
関連コンテンツ
テクノロジーHondaの研究開発施設すべてはリアルで証明する「全方位衝突実験施設」