安心と信頼を得るための部品供給
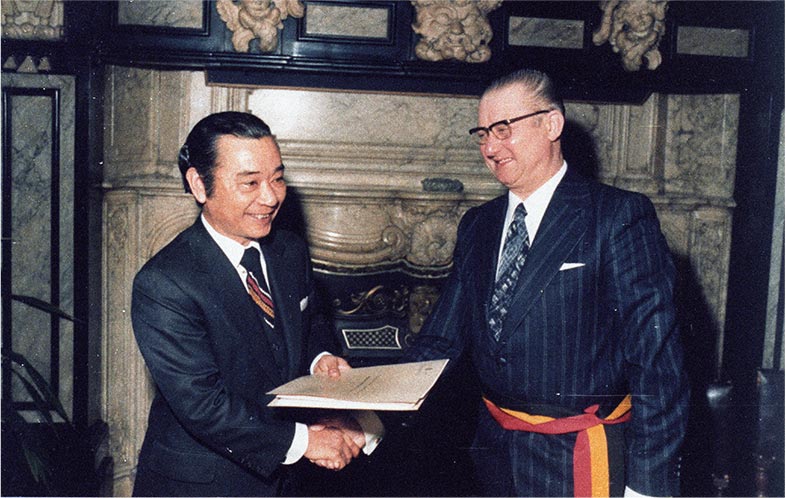
お客様の安心と信頼を得るためのサービスに必要不可欠な純正部品供給に対してもホンダは創業期から注力し、早く、適正価格でお届けする体制を構築してきた。
欧州では、1978年に設立されたホンダ・ヨーロッパ(以下、HE)が補修部品の欧州センターとしての機能を果たしていたが、1981年当時、欧州の各現地法人や販売店からHEに対して、部品の供給が遅い、欠品が多いなどの不満の声が上がっていた。そこでパーツ供給改善プロジェクトを発足させ、供給スピード、供給率の向上と情報ネットワークの見直しによる供給改善を図った。その後、二輪車・四輪車販売台数の飛躍的な増加に伴い、倉庫建設・拠点設立を展開しながら供給網を強化し翌日配送体制を確立した。
日本では、1987年7月に実施された部品部門に関するお客様の満足度調査において、供給スピードに対する評価が低かったことから、出荷元のパーツセンターから部品販売会社に供給する一次便と、部品販売会社経由で販売会社に届ける二次便の連動をスムーズに行うことによって納期の短縮および順守に取り組むこととなった。業界トップレベルの流通網を実現するために、1989年に部品販売会社からの受注に対して、二輪車部品は85%以上、四輪車部品は95%以上を24時間以内にお届けすることを目指し、二輪車は、1987年の73%が1989年に91%、四輪車は、同じく94%から98%となり目標を達成(ホンダ調べ)。北海道・青森・秋田の一部の地域などを除き、全国一律に24時間供給体制を確立した。
アジア大洋州においては、島しょ部が多く、道路整備も先進国と比較して進んでいないといった地理的な難しさがあるものの、当時、米州本部・欧州地域本部と比較して、アジア地域における部品供給機能が極端に弱いという実態を踏まえて、1996年にアジアパーツセンター(APC)プロジェクトを発足させた。そして、アジアにおける地域部品本部機能の強化とASEAN*310カ国の倉庫・管理システムの構築を行い、1998年の稼働開始時後からタイ国内で翌日配送体制をスタートさせている。米国では2007年に、部品の受け入れ・保管・出荷機能を持つ3つの親(ハブ)倉庫と、9つの地域子倉庫(パーツセンター)をベースとした供給網(3HUB・9PC)を整備することで、翌日配送体制を構築し、世界の主要地域で高位平準化した同一レベルの供給体制が完成した。同じく2007年に日本では、高い顧客満足度を業界トップレベルの効率で実現するという目標を掲げ鈴鹿物流センター(HBSL)を設立。物流拠点集約・集中・自前化と倉庫作業効率向上によって、15時30分までに受注した部品を翌日に販売店にお届けできるようになった。
日本からの輸出で始まった海外のお客様への部品供給は、現地生産の拡大に伴い現地調達・域内消費にとどまらず地域や国境を越えたグローバルな部品相互供給が必要となっていった。1996年に日本・欧州・北米・アジア大洋州による世界部品四極会議において地域間部品供給・価格ルールを制定し、翌1997年より四極間の部品相互供給が可能となった。四極会議はその後も定期的に開催され、地域間の供給ルール(供給年限・注文確定タイミング)やツール(グローバルトラッキングシステムやリターナブルクレート)を定めスムーズな地域間供給に貢献した。
3代目フィットから始まった中国を含むグローバル最適ソーシングの進展に連動し、補修部品は地域間での直送が進められることとなった。これまでの主要極以外の拠点(インド・中国・ベトナムなど)から世界の販売拠点へ直接供給されるグローバル部品が急激に増え、それらを安定的に調達し世界中へ供給するための輸出拠点および直送ルート整備が必要となった。新たな輸出拠点の部品供給体制を評価・支援するとともに、これまで主要現地法人間で結ばれていたルールを大幅改定し、全世界同一のシンプルかつ、より公平なビジネスルール「地域間ビジネスガイドライン」(グローバル供給・価格ガイドライン)を明確に設定した。2018年から2022年にかけて中国各合弁会社にも順次同一ルールを適用した結果、どの生産国からどの販売国へでも、お客様に確実に適正な価格で部品供給が可能となった。この地域間ビジネスガイドラインは、毎年のグローバル部品会議にて、その時々の環境変化に合わせて細かく改廃されており、いつの時代もパーツビジネスにおける明確な指針となっている。
一方で、供給網の強化に失敗した例もある。インドの部品事業は、ホンダの二輪車・四輪車・パワープロダクツの各事業会社が手がけてきたが、2006年に業務開始したホンダモーターインディアに集約することでコスト、物流体制の強化を図り、高品質な補修部品をタイムリーにお届けする体制の構築を目指していた。しかし、2010年に二輪車販売台数の爆発的増加を受け、部品倉庫の集約移転・システム変更対応を行った際、急激な環境変化に対処できず完全に倉庫機能がオーバーフローし、復旧に2年を要した。本来数年かかる供給網の整備・拠点設立の確実な成功には、現地法人の中期事業計画と連動した倉庫キャパシティや、物流経費に関するグローバル共通のKPI設定と定期的な点検による計画の精度アップが不可欠であることを学んだ。そこで、2016年より物流グローバル・ワーキング・グループ(GWG)を発足させ、各海外現地法人の倉庫保管能力を監視するとともに、地域の現場が主体となった物流効率の高位平準化活動を継続している。
グローバルで部品供給網を整備する一方、ビジネス拡大による新たな課題も出てきた。創業以来、お客様が製品を使用している間は、必要な補修部品を恒久的にお届けすることを約束してきたが、1990年代に入り、量産打ち切り後の旧型部品は増加の一途をたどり、お取引先が常時生産に応じる設備の維持が大きな負担になっていた。これを踏まえ、まず1990年に「ご相談パーツ制度」が導入された。これにより、一部の調達困難部品をあらかじめリスト化し、お客様から問い合わせがあった時点で納入にかかる時間や価格に関する情報をお伝えした上で受注を決定できるようになった。その後、20年以上前の部品が手に入るかなど他社動向実態を入念に調査した上で、1992年に生産年限*4が導入された。これによりお取引先は、生産台数に応じて規定で決められた必要な数の部品を納入すれば、その後金型・設備の廃却が可能となり、旧型部品生産の負担軽減に貢献した。
お取引先と同様、ホンダ内作部品についても、各量産工場における旧型部品の生産継続は限界を迎えており、受け皿が必要だった。特に、需要の大きい板金・バンパー部品を安定的に生産し世界中へ供給するための拠点が必要となり、全世界で旧型部品の集約生産体制の整備を徐々に進めていった。まず北アメリカ南部では1988年に地域の量産工場で増加する旧型内作部品の受け皿として、ホンダ・デ・メヒコ・エス・エー・デ・シー・ブイ(以下HDM、メキシコ)にて補修用板金・バンパーの旧型部品集約生産を開始。次いで欧州では1996年にホンダ・ベルギー・ファクトリー・エヌブイ(ベルギー)で、日本では1998年に八千代工業で補修用板金・バンパーの集約生産が始まった。2000年代に入るとアジアでの需要が急増し、2006年にアジア地域の受け皿としてホンダ初の補修専用板金工場となるアジア・パーツ・マニュファクチュアリング(以下APM、タイ)を設立。2010年にはホンダ・ターキー・エー・エス(以下HTR、トルコ)にて欧州地域分の旧型生産が開始され、各主要地域の旧型部品集約生産体制が整い、旧型内作部品の安定生産・供給体制が確立した。
その後、各地域の旧型部品集約生産体制は、災害発生時や工場閉鎖時などに、代替・補完供給を可能とするなど、さまざまな恩恵をこうむることになる。2011年のタイ洪水発生時には、APMが被災し4カ月間の稼働停止となったが、集約生産のノウハウを生かしHDM・八千代工業・HTRなど他の3拠点で直ちに代替生産・供給を行うことで、アジア地域やグローバルのお客様への部品供給の影響を最小限とした。また、2021年のホンダ・オブ・ザ・UKマニュファクチュアリング(HUM)・HTR閉鎖時にも、HTRで集約生産していた欧州へ供給する旧型板金部品をHDM・APMへ移管し、部品供給を継続することでお客様の修理に対する影響の最小化を図った。このグローバル体制は、今日もアフター市場への安定供給に寄与している。
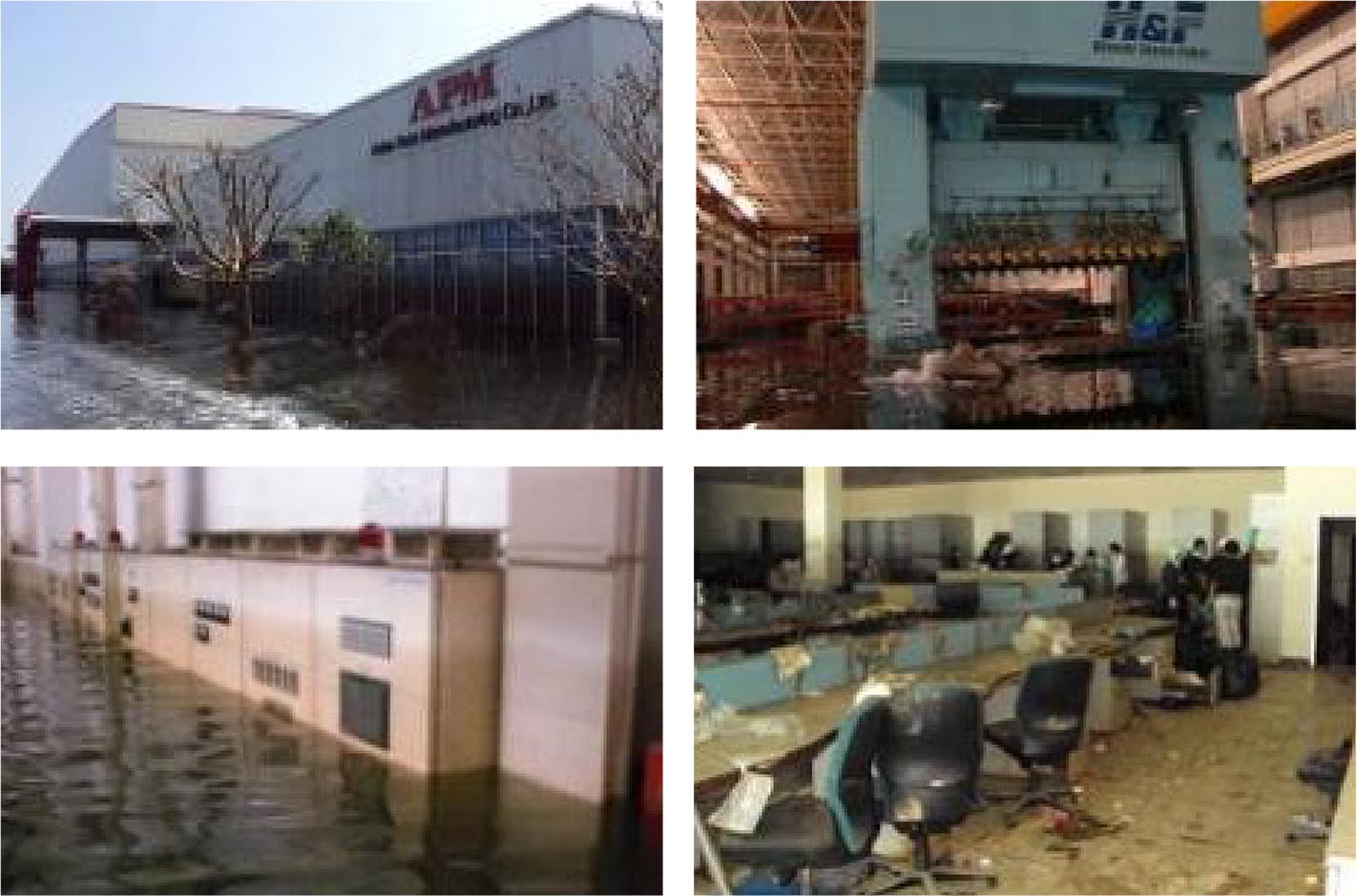
2011年のタイ洪水により水没したAPM
幅広いお客様のニーズに応えるための商品・サービス開発にも取り組んできた。ホンダの製品と同等の検査と管理によって品質保証されたホンダ純正オイルブランド「ULTRA」は、1959年の誕生以来、販売会社とともにお客様への訴求を続けてきた結果、日本や一部アジアのホンダ二輪車オーナーに定番のオイルとして親しまれている。これを皮切りに、ホンダ車にベストマッチの純正オイルを開発する動きが、グローバルで徐々に拡大していった。エンジンオイルのみならず他の油種も含めて日本側で開発し、地域側でお客様へのPRを行っている。
- :Association of South-East Asian Nations 東南アジア諸国連合
- :古い部品でも高頻度部品であれば継続して生産
先進技術で、期待を大きく超える「お客様満足」を目指す
お客様によってクルマの使い方は異なる。可能であるなら、お客様それぞれの使い方に合わせた最適なサービスを提供したい。この想いのもと、「一人ひとりに合わせた最適サービスの提供」の歴史は始まった。
2000年代の初頭には、オーナーズマニュアルの車載ディスプレイでの閲覧と、ディーラーに来店することなく、遠隔かつ自動でソフトウェアを更新する、といった構想はあったものの、デジタル対応に必要な技術やインフラが整わず実現できていなかった。その後、2010年代後半にはIT技術が飛躍的に進化。これにより、お客様の許可を得た上で、その許可をいただいたお客様ごとの走行中の車両情報が、より簡単に入手可能となり 「一人ひとりに合わせた最適サービスの提供」という想いがやっと現実のものとなり始めた。コネクテッドデータを活用したお客様のクルマの使用状態の見える化や、OTA(Over The Air)で来店せずにクルマのソフトウェアを最新化、デジタルオーナーズマニュアルの車載などの進化を続けている。
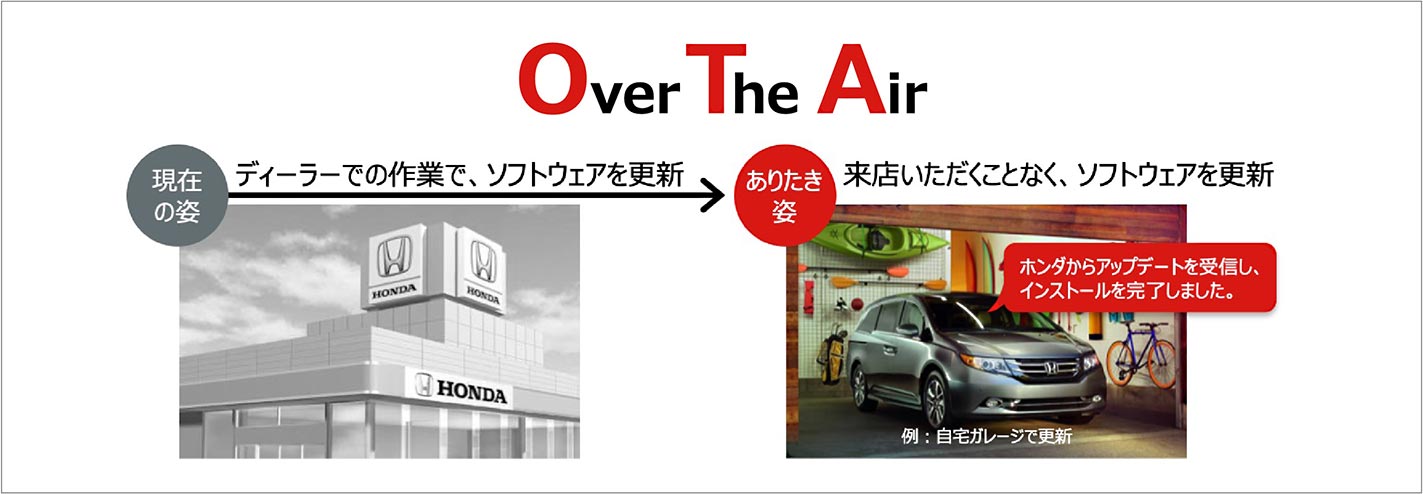
無線ネットワークを通じたソフトウェアのアップデート
一方、2000年代以降に車両の電子制御機構が飛躍的に拡大し、機構自体も複雑化したため、故障診断および修理を短時間で的確に実施することが困難になり、不具合再発のリスクが増大してきた。
それに対応するため、電装系の不具合を徹底的に分析し、
①ECUの自己診断機能を強化する
②自己診断できない事象の不具合発生時の制御情報を保存 することで不具合の再現性を向上する
という二つの戦略を立案し展開を開始した。
これまでの自己診断機能は、故障した際に故障コードDTC(Diagnostic Trouble Code)が表示されたとしても、その後、追加で診断が必要であり真の原因究明までに時間を要していた。しかし、ECUの自己診断機能を細分化することにより、検知した不具合1事象につき1つのDTCが設定され、販売店のサービススタッフによる診断時間が大幅に削減された。また、エンストや始動不良の症状については、時系列のECU情報の記録であるOBS(On Board Snap Shot)をECUのメモリーに残すことで、不具合発生時の制御状態が分かるようになった。
また、不具合発生時の制御情報の保存については、故障診断機を刷新することで大幅に診断機能を強化し、故障発生時の再現性および診断力を従来よりさらに向上させ、真の故障原因を突き止めやすくなり、修理時間の短縮につなげた。
これらを実現させるためにECUのメモリーを故障診断の再現性に使うことは、車両の性能向上にメモリーを活用したい開発側に理解し認めてもらう必要があり、導入は困難を極めた。
しかし、故障診断の再現性実現のためにメモリーを使うことがいかにお客様満足につながるのかを、設計部門へ粘り強く説明し、メモリー量の増加を協議し、実現していった。
また、記録された制御情報をもとに故障診断する上で鍵となる、詳細な設計情報を新たな高度診断サービス情報として積極的に販売店などに提供したことで、故障発生時に修理にかかる時間の短縮につながった。また、確実に、何が、どのように、なぜ起こったのかが分かるようになったことで、1回の来店で確実に直す一発修理率が向上した。これらにより、お客様の利便性改善や販売店の負荷軽減につながっている。
さらに、この活動で投入した新型故障診断機には、不具合車両から吸い上げた自己診断情報を、全世界の販売店とオンラインネットワークを介して日本のサービス部門が集め、設計部門にフィードバックするという機能も導入し、源流改善に貢献している。
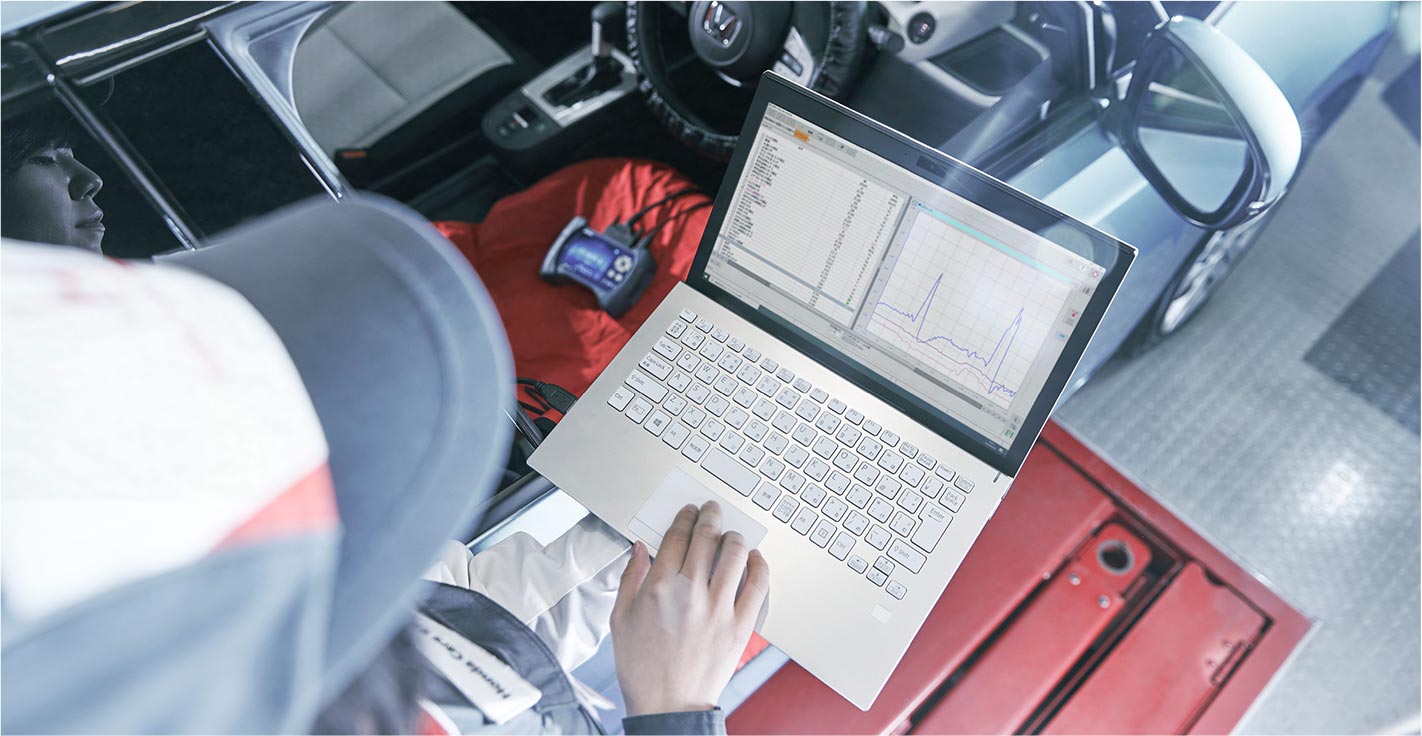
クルマに使われる先進技術に対応し、万全の点検・整備を行うための診断システム「i-HDS」
2020年発売の新型フィットから車両情報を収集することが容易になったが、サーバーに保存されたコネクテッドデータを取り出し分析できるのは、当初限られた品質部門の担当者だけだった。それを2022年度から、サービスの現場で有効的に使えるようにするため、コネクテッドデータの可視化機能を搭載したBI(Business Intelligence)ツールを開発し、市場で発生している問題が解決できるか否かを、サービス部門とSTC(本田技術工業(株)サービス技術センター)が連携し、検討を開始した。コネクテッドデータをサービス現場のどのような状況で活用できるかは2023年時点でまだトライアル中であるが、不具合(故障・事故・誤動作・誤操作)発生時に、クルマがどのような状態にあったかを見えるようにし、状況の正確な把握、分析が可能となってきた。さらに、不具合が発生し、DTC発生後の各運行ごとに故障が継続発生していたかどうかが確認できるようになった。
昨今、スマートフォンの普及・使用体験を通じて、ソフトウェアやアプリ内の情報更新を自分で行うことは日常的になっており、無線ネットワークを通じた車両搭載のソフトウェアのアップデートOTAニーズが非常に高くなっている。
OTAによるサービス展開は、北米で2018年モデルから導入を開始した。初めはエンターテインメント系のディスプレイオーディオとナビゲーションシステムから可能となり、サービス部門ではOTA管理システムと配信サーバーをつくり上げた。次に、適用するECUを増やしていくよう、2019年からサービス部門の担当者が開発部門に入り込み、研究所の開発テーマ「OTAによるソフトウェア更新システムの開発」の一員として共同研究に取り組んだ。そして、エンジンなど主要制御系ECUのOTA技法を開発して2023年モデルのアコードに適用した。
2023年モデルからの制御系システムのOTA開発においては、数万件のソフトウェア配信制御・ソフトウェアアップデート法規対応・ソフトウェアのダウンロードとインストール方法・ユーザーインターフェース設計など、多岐にわたる開発に取り組みサービス発案の特許も取得した。また、性能・品質面をより確実にして上市するために、サービス部門で車両量産前に半年を超える長期間かつ複数回にわたる現場での検証を、上市国である米国で行った結果、システムを完成させることができた。今後は不具合修正のためのOTAから、ソフトウェア更新による機能追加、セキュリティー向上など価値の拡大を目指し、関連部門と将来計画を立案、推進している。
サービス・部品に携わる部門として、創立以来ホンダフィロソフィーである「買う喜び」を世界中のお客様にお届けすることを目指し、お客様との接点である販売店のサービスの現場で最高のサービスを提供できるように活動してきた。この想いと活動の本質は今後も不変である。
しかしながら、ホンダが2050年に「カーボンニュートラル」「ホンダの二輪車・四輪車が関与する交通事故死者ゼロ」の実現を目指す上での事業環境変化、ならびに電動化に伴うお客様のニーズ多様化と価値観の劇的な変化が想定される。クルマの保有期間を担当するサービス・部品部門は、買っていただいた製品をお客様にいつまでも使い続けていただくために、新しいサービス価値の創造、さらに、そうして生んだサービスを、これまでの販売店を通じての提供に加え、デジタル技術をフル活用し個々のお客様に直接提供することにより、シームレスな関係構築を目指していく。そのためには、全てのお客様「一人ひとり」との接点が拡大し、感動体験を提供できるよう、新たな「使う喜び」の創造に向け邁進することが必要となる。
この目標達成に向け、デジタル技術を最大活用し、サービス・部品に携わるグローバルホンダの仲間との「連携」強化、ならびに社外とも積極的に協業し、「スピード」感を持って、変革にチャレンジしていく。
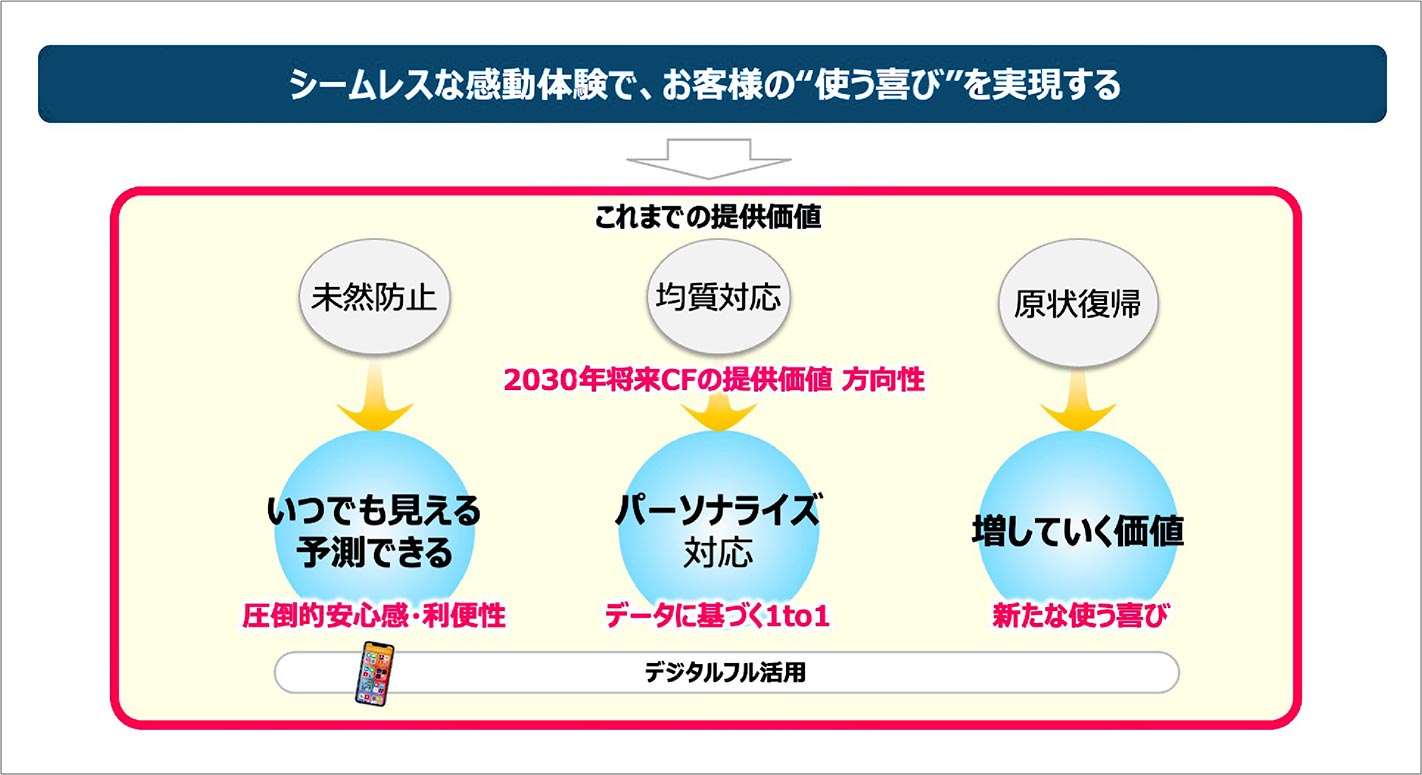
デジタル技術を活用し「お客様一人ひとり」とのシームレスな関係をつくりあげていく