市場変化に即応可能な、フレキシブル生産体質へ
「’01体改」の取り組み
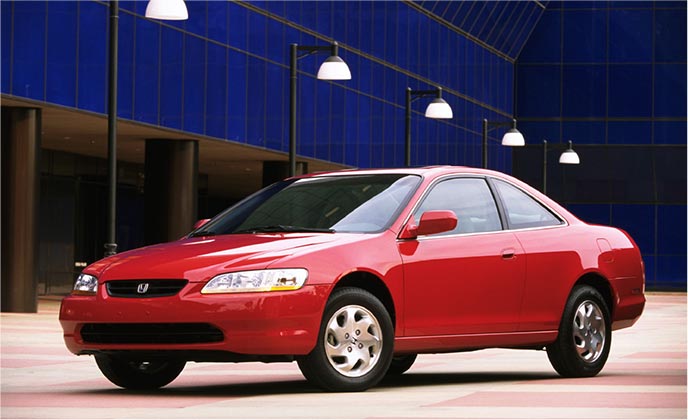
生産活動をグローバルに拡大していった1990年代、世界四地域体制を構築したホンダは、その一方で、工場ごとの生産設備の仕様や生産工程などの特性といった生産体質の違いにより、課題が生じてきた。日本においては、1990年代に入るとRV(レクリエーショナル・ビークル)やワンボックス車といったレジャー志向のクルマに人気が高まっていたが、ホンダはこうした機種を生産できる工場を有していなかった。 そのため、埼玉製作所狭山工場と鈴鹿製作所では大幅な改修を行い、狭山ではアコードのプラットフォームを基にしたオデッセイを、鈴鹿ではシビックのプラットフォームを基にしたCR-Vを生産するなど、既存の工場で対応したが、こうした大きな市場変化に追従する難しさが明らかになった。
海外拠点で生産する機種が埼玉生産機種か鈴鹿生産機種かによって、日本から支援するチームが違っていたため同じ海外拠点内でも埼玉チーム・鈴鹿チームが混在して支援をしていた。
そのため、同一ライン内でも埼玉方式、鈴鹿方式が混在していたのである。それに加えて、国内の工場では少しでも効率を上げるために生産機種に特化した独自の体質改善を実施してきた結果、工場ごとに異なるシステムやプロセスでの生産が定着。そのため、埼玉生産機種と鈴鹿生産機種を1つのラインで生産する海外拠点では双方のシステムやプロセスを備える必要が生じてしまっていた。
しかも、1990年代半ば以降、北米においては北米専用のアコードクーペ ワゴン・ACURA CL・オデッセイといった生産機種が増え、アジアではシティといった地域専用機種が生産されるようになるなど、生産システムやプロセスはさらに多様化していった。
このままでは新機種立ち上げのたびに多くの投資が必要となり、コスト競争力が低下するほか、増産時も拠点単独で対応せざるを得ず、ニーズへの追従が遅れ市場競争力も低下してしまう。こうしたことから、生産体質を大きく転換しなければホンダの将来はないと判断。グローバルでの生産体質改革に乗り出したのである。
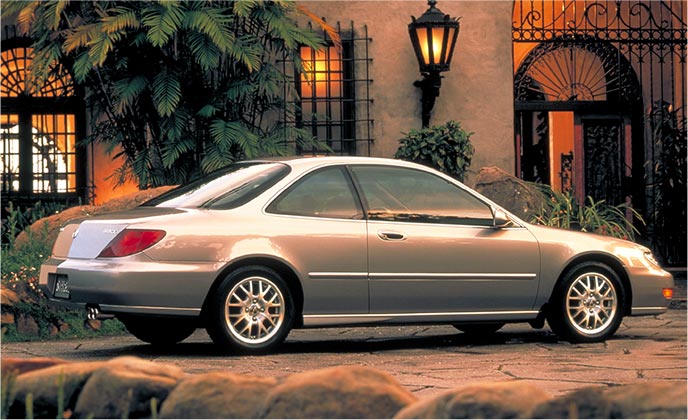
北米 ACURA CL
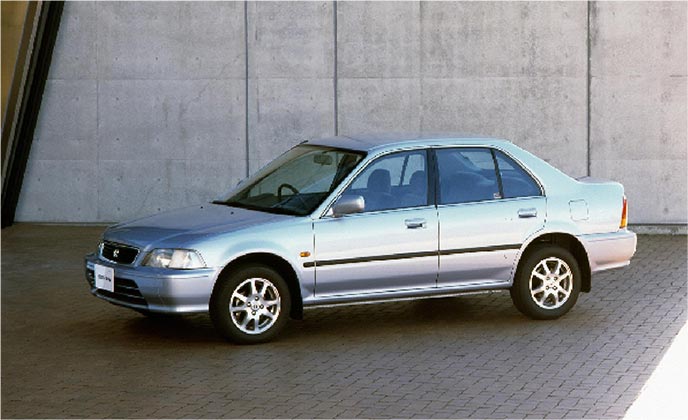
タイ シティ
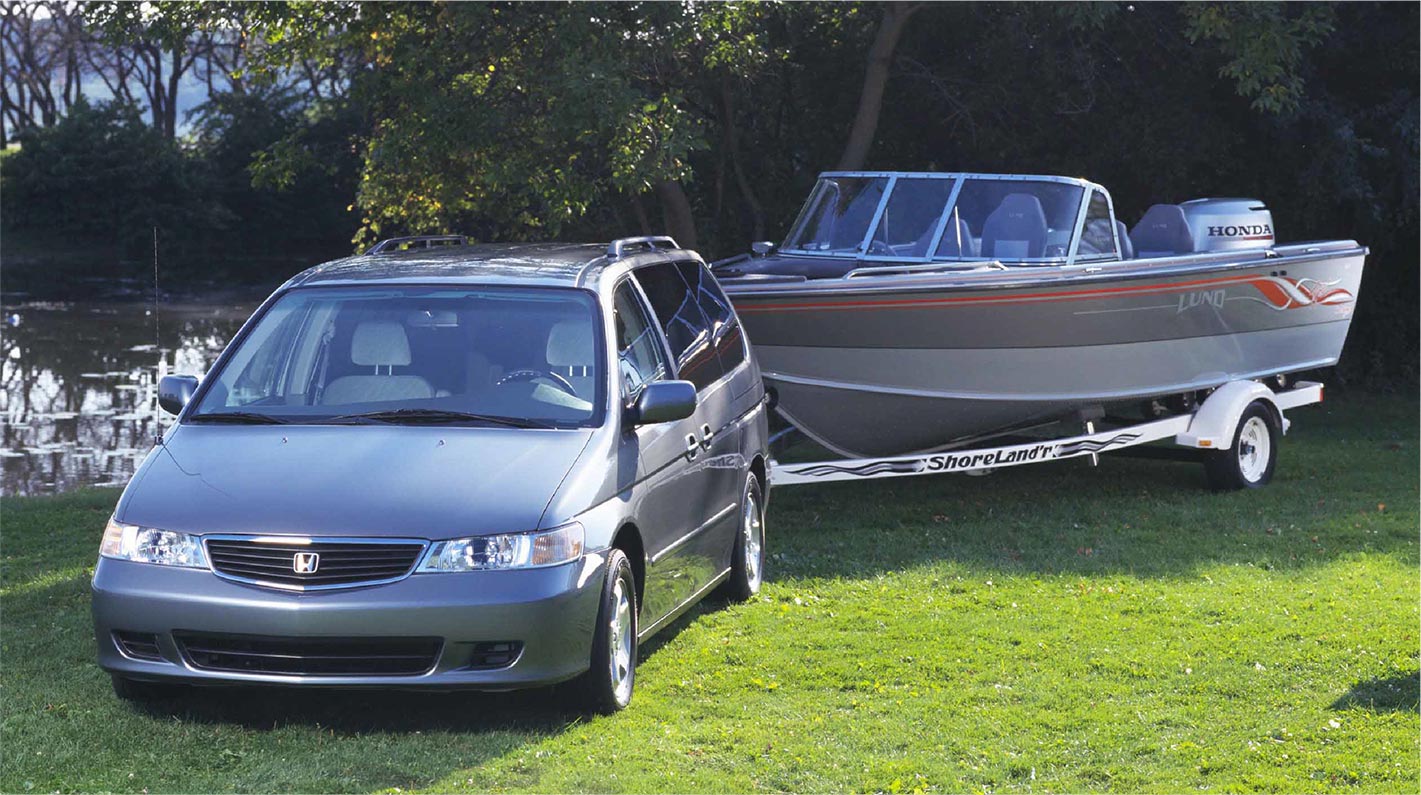
北米 オデッセイ
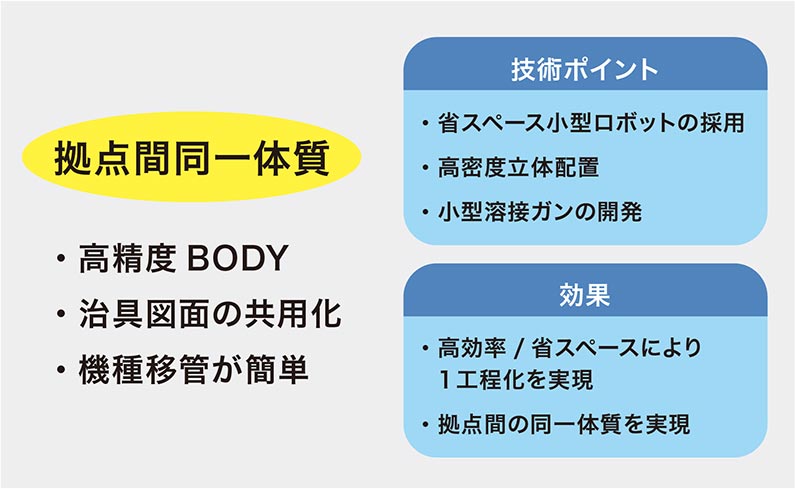
2001年、生産企画室と生産技術部門を担うホンダエンジニアリング(株)(EG)の合同プロジェクト、通称「’01体改」が発足した。プロジェクトの目的は、「軽少自在」な生産ラインを構築し、日本を含む各拠点へ水平展開すること。軽少自在とは、汎用性を大幅に高め、多機種に対応できるように生産設備の固定部分(機種ごとの専用部)を極力減らすことであり、世界同時立ち上げ、世界同一品質、投資10分の1を実現するというのが狙いだった。中でも特に改善を要したのが、重厚長大な設備を要する車体溶接プロセスだった。そこで、車体溶接ラインをターゲットに、次の3つの施策を軸にした大幅な体質改革を検討した。
①新機種リードタイム短縮
②内作コスト、投資、経費の削減
③四地域世界統一仕様
その中で、溶接ラインの主要工程であるSMGW(サブメイン総合溶接機)工程からサイドパネル(サブ)結合工程を分離する案が採用された。これは軽装備化(簡略化)、汎用化の実現のために高密度化したTT治具機能(固定スポット溶接装置と治具)を分離し、汎用性の高いロボット工程にするという手法であった。これ以降、治具の軽装備化が加速度的に進行していったのである。
国内生産現場に効果をもたらした
三現主義に基づく「ものづくり」への回帰
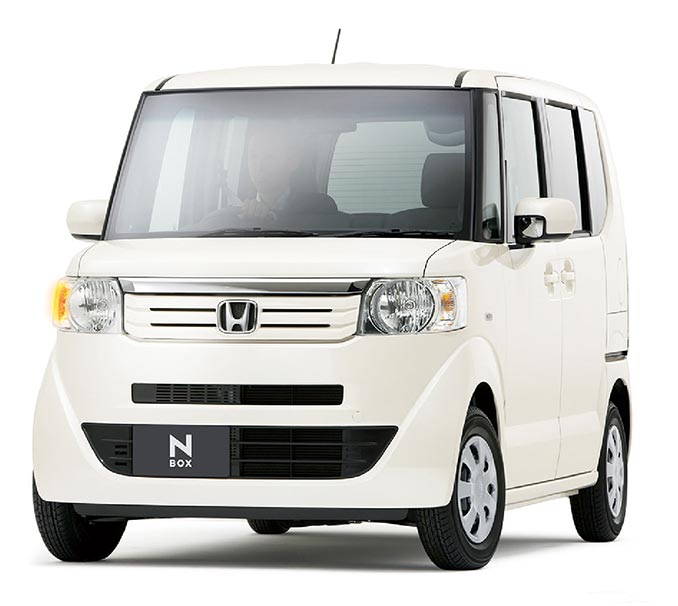
生産チームがフェイス・トゥ・フェイスで
プロジェクトを進めたN-BOX
2010年前後の世界経済はリーマンショックによって足踏み状態が続いており、日本ではそれに加えて、円高基調の為替動向が輸出競争力を厳しいものにしていた。ホンダの国内四輪事業については、国内生産能力を国内販売で自己完結することが重要な課題であった。国内の四輪車市場は縮小傾向にあるものの、その大半を軽・スモールクラスが占めており、特に軽乗用車の需要拡大が見込まれていた。軽を主力とするメーカーを中心に各社が熾烈な競争を繰り広げており、ホンダでは新たな軽乗用車、N-BOXの開発が急がれていた。
開発チームに当時の社長、伊東孝紳から上市を2カ月前倒しとの指示が出され、発売予定が2011年12月に繰り上がった。販売会社の社長たちから強い要請を受けてのことであった。そんな、上市に向けて追い込み状態にあった同年3月11日、東日本大震災が発生。栃木研究所が大きく被災した。
当時、新機種センターN-BOX責任者(E-PL)を務めていた轟木正則が振り返る。
「震災によって1カ月半くらい、すべての動きが止まってしまった。12月の立ち上げ予定は変更されずに、合計3カ月半くらいの時間が奪われてしまったんです」
奪われたのは時間だけではなかった。栃木研究所では試作車の製作も不可能な状態に陥っていた。そこで、N-BOXの生産を担当する鈴鹿製作所が数台の試作車をつくることになった。
「鈴鹿で試作車なんて今までつくったこともないですから、できるかどうか不安も相当ありましたが、研究所の状況を考えればやるしかない。もちろんまだ設備などはありませんし、エンジンもすべて手組みでした」(轟木)
だが、こうした新たな経験が、思わぬ効果をもたらすことになる。
「結果的に、通常より相当早い段階から実機に触れ、自分の手でつくることができた。それによって、つくり方がある程度『手の内に入る』というか、経験が積めたのは大きかったと思いますね」(轟木)
さらに、開発メンバーが作業不能となった栃木研究所から、鈴鹿製作所に設けられたサテライトオフィスに移ることになり、開発と生産が同じ現場で働くことで、これまでにない効果が生まれた。
当時、本田技術研究所四輪R&DセンターでN-BOXの開発責任者(LPL)を務めていた浅木泰昭は言う。
「距離が近いというメリットを、これほど痛感したことはありません。問題があると、いつもはメールや電話のやりとりで時間がかかっていましたが、現場で顔を合わせるだけで一瞬にして解決するんですから、フェイス・トゥ・フェイスのコミュニケーションの重要性を痛感しました」
こうして、直接的なコミュニケーションを図りながらプロジェクトを進めたことで開発速度が増し、N-BOXは予定通りの2011年12月に発売された。部門の垣根を越えて同じ現場・現物・現実を共有する、「三現主義」の大切さを改めて知ることとなったのである。
鈴鹿サテライトは、2012年4月に(株)本田技術研究所四輪R&Dセンター鈴鹿分室(HGT-S)へと発展した。研究所の一組織として、DEB部門(開発Development・生産Engineering・購買Buying)を鈴鹿のワンフロアに集約し、開発から購買・生産までを一貫して行う「軽QCDD展開」を発足。生産領域の品質(Quality)・コスト(Cost)・納期および調達(Delivery)と開発領域(Development)が一体となり、軽の製品化をスピーディーに展開する体制を目指す、通称「SKI(鈴鹿・軽・イノベーション)プロジェクト」がスタートし、N-BOXに続く軽自動車開発に、段階的に導入されていった。
「Made by Global Honda」のもと
海外拠点の四輪車生産体制を大改革
ホンダは創業以来、「需要のあるところで生産する」という理念のもと、世界の各地域に生産拠点を展開していった。この生産基本方針は、2000年代に入ると、「Made by Global Honda(世界最適生産)」へと発展。四輪車生産については「ホンダのグローバルネットワークを活用し、部品調達・生産を世界の最適な拠点で行い、最適な市場へ供給する」ことが明示された。また、世界のさらなる需要拡大や多様なニーズに応えるために、地域事業運営を日本・北米・欧州・アジア・南米・中国という六極体制へと発展させ、世界最適生産による各地域の市場ニーズに合わせた事業運営を進めていった。
そうした中で、生産領域においても「’01体改」を推進しながら、地域に最適な商品をタイムリーに供給していくために、現地開発・現地生産を加速させていった。しかし、こうした各拠点での多様なニーズへの対応が、2010年代半ばごろになると生産現場の混乱や事業効率の低下を招くこととなったのである。
各拠点で新機種の量産を立ち上げる際は、製品仕様・生産工程・生産設備に応じて「段確(段取り確認)」→「品確(品質確認)」→「量確(量産確認)」と呼ばれる段階を経ながら「品熟」(品質熟成)がなされていく。生産拠点を拡充していた当初は、「日本が1番国(最初の生産開始国)となって量産を立ち上げ、2番国(地域の生産拠点)への移行時に品熟のノウハウを水平展開することで品熟期間を短縮する」という流れであった。しかし、地域最適化によるグローバル機種の派生車や地域専用機種の増加によって、量産立ち上げの品熟工数が大幅に増し、従来の品熟プロセスでは対応が難しくなっていた。その結果、海外で新機種が計画通り立ち上がらず、ラインオフ後に加修(手直し)対応が必要となり、そのための費用やアソシエイトたちへの負担も増加してしまった。さらに、日本生産にない機種や仕様の立ち上げに対して、生産要件を品熟に反映できるスキルを持った日本からの支援メンバーの不足といった課題も発生し、人材育成も急務となった。
こうした課題を解決するために、ホンダは2019年、全社的な取り組みとして、開発効率や部品の共有化率を高める「ホンダアーキテクチャー」という開発手法を導入すると発表。これにより生産ラインでは、部品や装備の変更ごとに必要となる治具の組み換え作業が減り、地域間でのスピーディーでフレキシブルな生産補完が可能となることから、グローバル機種のシビック(2021年発売)の開発から採用されることになった。これにより生産領域は、製品仕様・生産工程・生産設備の標準化を実現すべく対策をスタートさせた。これは、日本の支援メンバー育成のために2017年から開始した、「グローバル新機種品質熟成スキル」向上活動の取り組みでもあった。
具体的な例としては、フロントまわりのボディー骨格の溶接構造を、各拠点に水平展開する際に統一化しやすいように、CAE(Computer Aided Engineering)解析データから導き出したバラつきが最も少ないシンプルな構造・仕様を構築。2番国への品熟情報伝達については、1番国の日本で展開する品熟内容を各拠点と共有できるようデータボックスを新設し、緊密なコミュニケーションによって各拠点の段取り状況の確認や現地の困りごとへの対応など、品熟への取り組みを展開した。
一方、地域専用機種については、現地アソシエイトの育成施策として、具体的な品質熟成マニュアルを構築し、北米の2カ所の生産拠点でトライアルを実施。マニュアルの有効性の検証と確認が完了したことで、日本を起点に北米5拠点・南米1拠点・アジア大洋州3拠点へ水平展開し、2023年以降の新機種の立ち上げに向けて統一の品熟体制を整えていった。
電動化を見据えたグローバル四輪車生産体制の見直しと、
グローバル製造技術の進化
2010年代後半になると、世界規模でクルマの電動化への動きが本格的に始まり、自動車業界は100年に一度といわれる大転換期を迎えた。ホンダはそれ以前より、四輪車を主軸に、二輪車、パワープロダクツのみならず、エネルギーも含めた電動化技術に取り組んできたが、今後ますます加速する電動車需要を見据え、「グローバルにおける生産配置と生産能力の適正化」という方針で、日本・米国・中国を軸に電動車に対応した四輪車生産体制づくりを進めることになった。一方、欧州については、電動車の強化が必要となる中で、欧州地域内での電動車の生産は、競争力などの観点から難しいと判断。「Made by Global Honda」の地域間での連携強化の考え方に基づき、欧州の環境規制と方向性が近い中国と商品ラインアップを共有するなど、グローバル生産リソースを活用した事業基盤の見直しを図ることとなった。
その結果として2019年2月に、HUMでの完成車生産を2021年中にシビックハッチバックの生産終了をもって終える方向であることが発表された。同日、トルコの四輪車生産工場であるホンダターキー・エー・エス(HTR)でのシビックセダンの生産も、2021年中に終了すると発表された。
2021年7月、HUM生産の最後のシビックがラインオフされた。HUMでは設立以来、シビックの生産が最も多く、約200万台を生産し、エンジン単体の生産は2020年時点で400万台を超えるなど欧州の重要な拠点を担ったが、35年にわたる生産活動に幕を下ろした。
また、日本では、埼玉製作所の狭山完成車工場を、今後の電動化に対応する最新の生産技術が備わる寄居完成車工場に集約することが2017年10月に発表され、2021年12月に埼玉製作所狭山工場は完成車の生産を終了。2021年6月にはパワートレインユニット製造部(栃木県真岡市)の閉鎖も決定され、2024年度中の閉鎖を目指して複数の生産拠点への業務の集約が進められている。
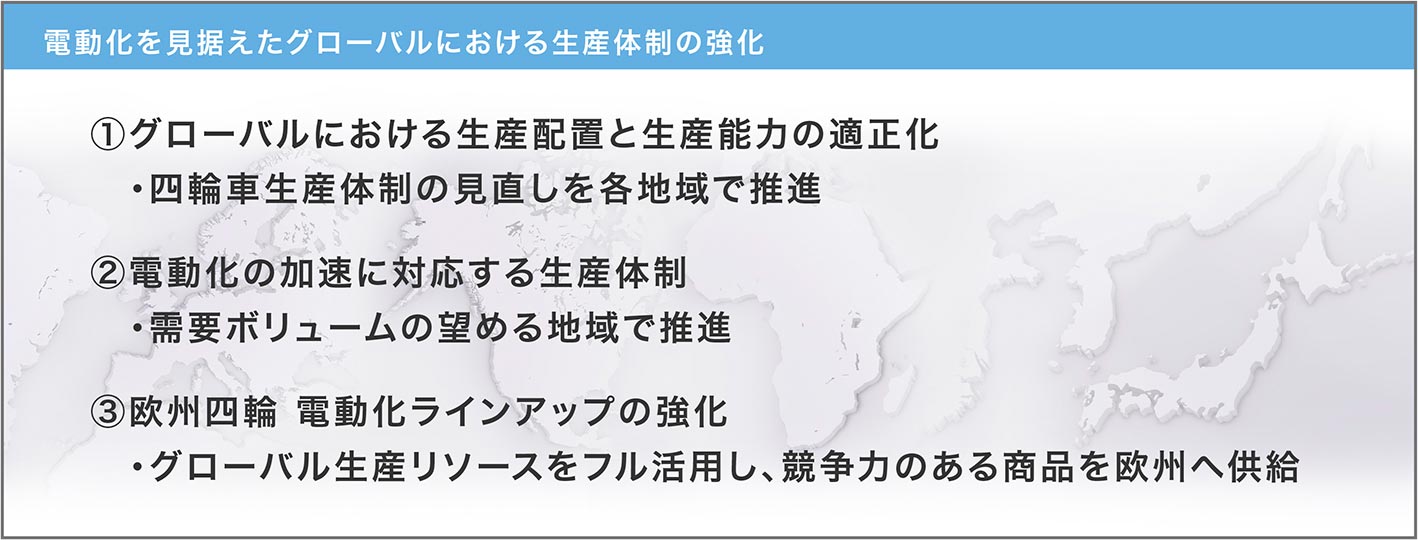
2020年には、本社組織の四輪事業運営体制が大きく見直された。営業(S)・生産(E)・開発(D)・購買(B)の各領域を四輪事業本部に統合した一体運営体制へと変更。戦略立案機能の強化、ならびに対他競争力の高いものづくり基盤を構築し、強い四輪事業の実現を狙いとした。
生産領域においては、グローバルでの生産品質の管理と高位平準化が重要となった。各拠点において、電動車をはじめ先進技術を搭載する四輪車の品質を担保した生産を行うために製造技術の確かさを実証し、生産が開始できるかどうかをDEB一体で検証すると同時に、競争力を高めるためにグローバル製造技術機能を導入することとした。
求められる製造技術機能については、世界標準で定めたプロセス・工程設計を基準とし、新機能のベースとなる生産技術・製造技術・品質技術については、製造DX技術を活用しながらマニュアル・ノウハウ集などに集約し、手順化していった。
そして、こうした電動車の高い品質や高知能化された安全機能を担保しながら安定生産を実現するための場として、2020年9月17日、寄居工場内に「グローバル製造技術棟」を設置。開発と生産が一体となってスピーディーに展開できるものづくりの取り組みが始まった。
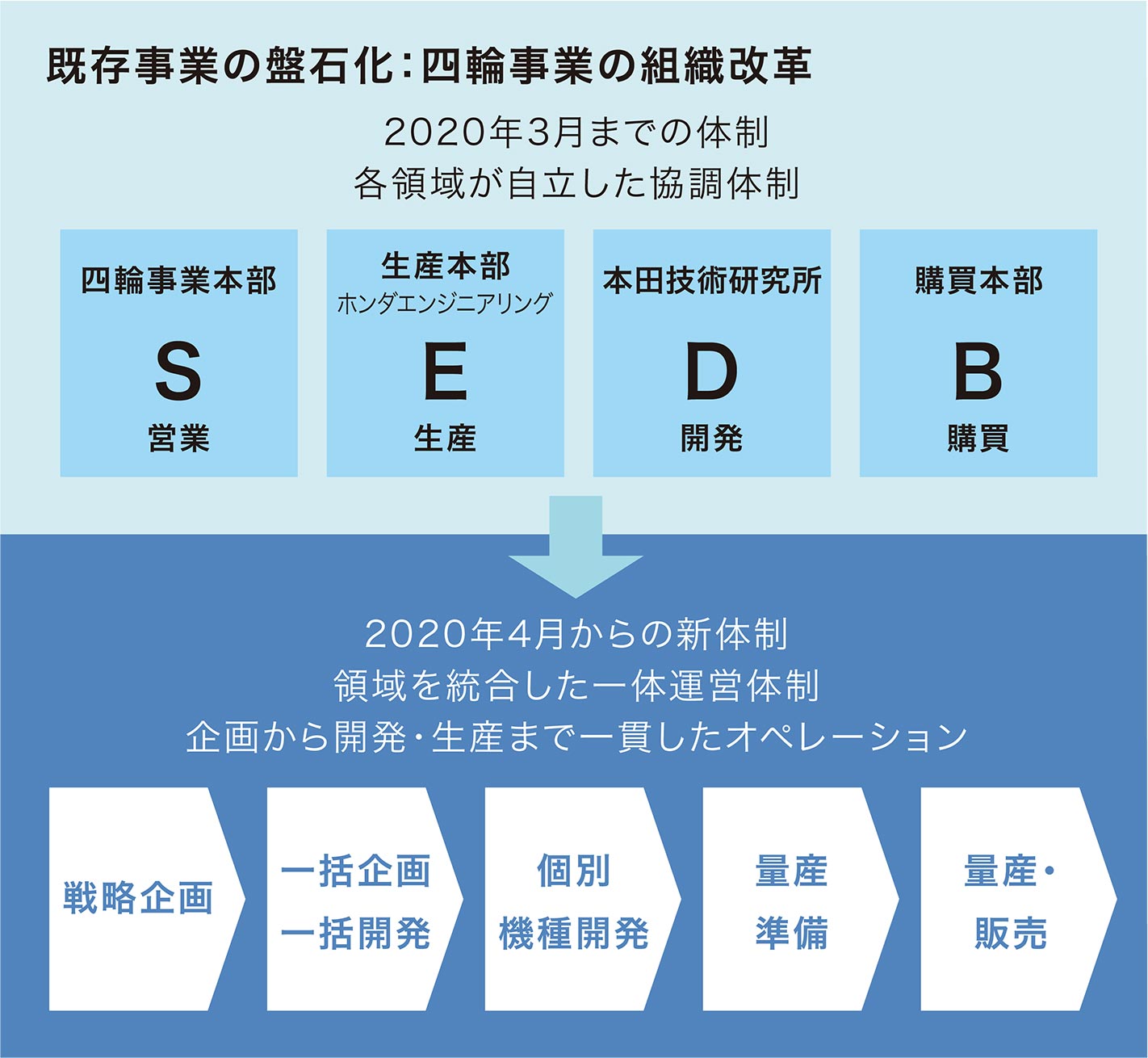
SEDBの協調体制から一体運営体制へ
最後の1台まで全力を尽くしたアソシエイトたち
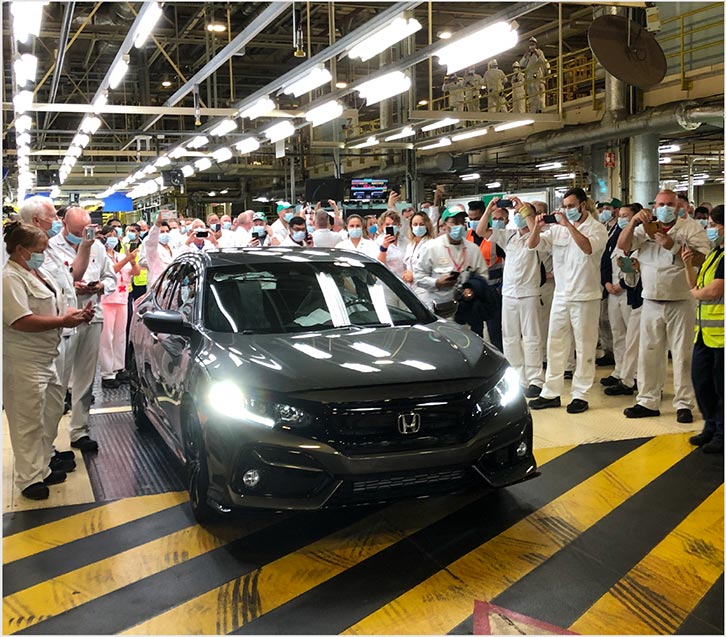
●HUMの工場閉鎖
2019年2月にHUMの生産活動終了が対外的に発表されると、HUMでは全従業員に対して八郷隆弘(当時、社長)・西本準(当時、HUM社長)のメッセージが配布され、労使協議がスタートした。
協議の状況は随時開示され、従業員から寄せられる質疑については随時フィードバックするなど、丁寧な対応を重ねた。すべての従業員が安心できるよう、退職保証や再就職サポートなどに努め、モチベーション維持のために、交流会や表彰といった社内イベントを実施するなど、生産終了まで業務に集中できる環境を保持していった。
対外発表から1年後の2020年2月に実施した「働く意欲・誇り・職場満足度」の従業員意識調査では、約8割が「HUMで働く誇り」を持ち、約7割が「最後までベストを尽くす」と回答。2021年7月の工場閉鎖までホンダブランドを守り、最後の1台まで誇りを持ってつくり続けた。
このようにHUMの生産活動に幕は降ろされたが、工場跡地の北東の端に記念樹を植えたホンダヘリテージパークを造園し、また、最後の主力モデルとなったシビックTYPE Rを大英自動車博物館に寄贈・展示、永遠にHUMのレガシーをイギリスの地に刻んだ。
社会が不安に包まれている今自分たちにできることを
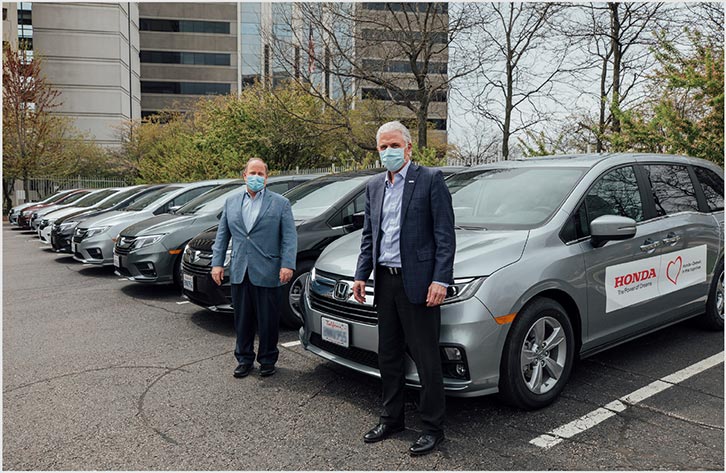
●コロナ禍での社会貢献活動
新型コロナウイルス感染症(COVID-19)の流行が拡大する中で、埼玉製作所狭山工場の従業員から感染者搬送車両をつくりたいとの提案があり、運転席と後部座席の間に仕切りを設置するなど運転者への感染対策を施した車両を、極めて短期間で開発。国内事業所でオデッセイやステップワゴンなどの搬送車が生産され、自治体へ提供された。
その後、各地の販売会社でも車両の仕立てを行い、地元自治体に提供。さらに、自治体で使用している車両に仕切り壁を設置するなどを含め、2020年4月からの提供開始以来、累計168台を26の都道府県に提供した。
また、この取り組みが動画投稿サイトで発信されると、米国ミシガン州とデトロイト市の関係者の目に留まり、その依頼を受けた当時のホンダ・リサーチ・アンド・ディベロップメント・アメリカ(後のホンダ・ディベロップメント・アンド・マニュファクチュアリング・オブ・アメリカHDMA)にて同様の取り組みが行われた。埼玉製作所狭山工場の製作者たちと連携を取りながら2週間という短期間で実現し、10台の車両がデトロイト市に貸与され感染者の搬送に役立てられた。
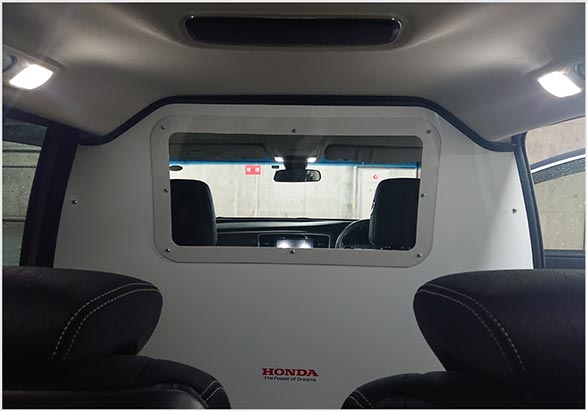

生産活動の進化は、その時代、その時々で
変えていくこと
ホンダの生産活動は、時代背景に合わせて事業の発展とともにその取り組み方を変えてきた。それは常に、今ある資源を有効活用し、品質を担保しながら、いかに効率よく競争力のある生産ができるか、お客様の期待を上回ることができるか、を追求し続けてきた歴史といえる。
執行役常務で四輪事業本部生産統括部長の大江健介は、ホンダの生産活動について次のように振り返った。
「その時代、その時々に合わせて、タイムリーに仕組み・体制・オペレーションを見直すことが不可欠でした。過去に縛られることなく、柔軟に変化させることで進化を続け、取り組みを通じて社是である『わたしたちは、地球的視野に立ち、世界中の顧客の満足のために、質の高い商品を適正な価格で提供することに全力を尽くす』ことを実践してきました」
そして大江は、今後の生産活動を進化させていく原動力は、ホンダで働く一人ひとりの意識にあると言う。
「存在を期待される企業であり続けるために、ホンダフィロソフィーの原点に立ち返り、『秒進分歩』で変わる時代にどう対応していくかを常に考え自分の仕事の課題や組織の課題に積極的に向き合い、解決に向けたチャレンジを続けていくことが重要です。私たちはこれまで、ものづくりのプロフェッショナルとして常に高い目標を掲げ、既成概念や常識を覆すような課題にも果敢に取り組んできました。その一人ひとりのすべての活動が、次世代のホンダの源泉であることは間違いありません。自動車業界の大転換期を迎え、製造業として発展してきたホンダが、ハードとソフト・サービスの融合で提供価値を高めるモビリティーカンパニーとサーキュラーエコノミーのキープレーヤーへと変革する、まさにはざまにいる今、『変わらないことがリスクである』と私たち一人ひとりが認識し、仕事のやり方を大胆に見直す。イノベーションはそこから起きるのです」