The Honda Super Handling Challenge Chapter 9
The Future of Super Handling (1): Four-Motor EVs
The Honda Super Handling Challenge Chapter 9

Honda established a youthful team of advanced development engineers to develop a four-motor Super Handling All-Wheel Drive (SH-AWD) electric vehicle (EV). In June 2015, they entered the car into the Pikes Peak International Hill Climb (PPIHC), held in Colorado, U.S.A., with the aim of verifying the effectiveness of four-motor torque vectoring.
Torque vectoring is a technology that creates driving torque differentials between the left and right wheels to generate a yaw moment around the center of gravity that helps the vehicle turn while stabilizing vehicle posture. This technology was put to practice use in 1996 with the addition of the Active Torque Transfer System (ATTS) to the Prelude. The ATTS system increased turning force through distribution of driving torque between the front left and right wheels.
Since that time, Honda has continued to evolve and apply the torque vectoring technology with each new generation. In 2004, it introduced SH-AWD, the world’s first system with a mechanical structure to freely control driving torque distribution between the front and rear wheels, and between the left and right rear wheels, to the Legend.
In 2014, it introduced Sport Hybrid SH-AWD, a three-motor hybrid system, to the Legend again. This system enabled advanced torque vectoring using an engine and motor in the front coupled with a Twin Motor Unit (TMU) mounted in the rear. Then in 2016, it used Sport Hybrid SH-AWD on the second-generation NSX, but this time with the engine and motor mounted midship to drive the rear wheels and the TMU mounted in the front. Using motor control to create driving torque differentials, the system offered light handling for turning freely in a range of driving scenarios.
The four-motor SH-AWD EV is an extension of this technology. Both the Legend and NSX are mainly engine-powered cars, driven from the front or rear, whereas the four-motor SH-AWD EV is powered by high-response, highly controllable motors in both the front and rear. The aim of this car was to confirm the effectiveness of using four motors to achieve the ultimate torque vectoring.
In 2012, around the time that development started, global penetration of EVs was not at the levels seen today. At the time, there were only a few fast chargers available at Honda’s R&D facilities as well. In February 2016, Honda announced its goal of replacing two-thirds of its automobile sales with zero-emission vehicles, including plug-in hybrids, hybrids, fuel cell vehicles (FCVs), and battery electric vehicles (BEVs), by around 2030. Then in April 2023, it announced plans to produce more than 2 million EVs globally each year by 2030.
Electric SH-AWD with Precision All-Wheel Steer (Advanced Development Vehicle)

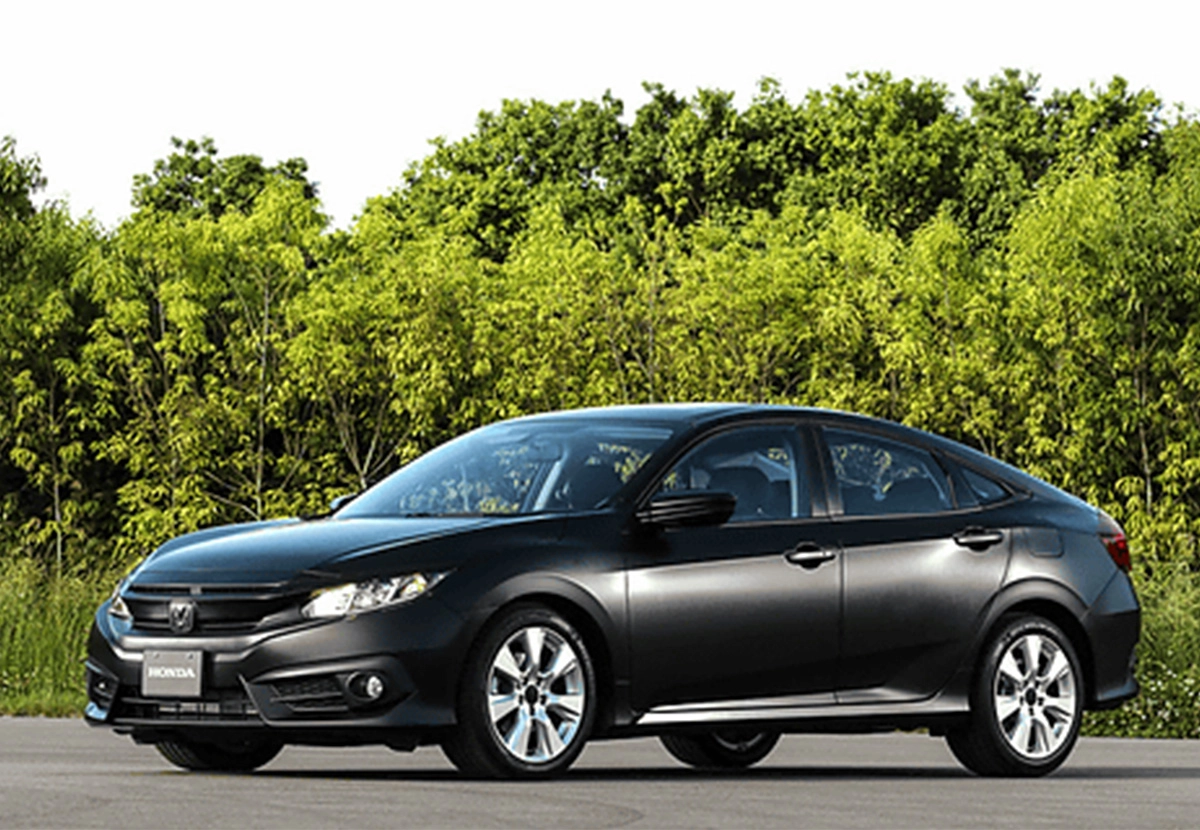






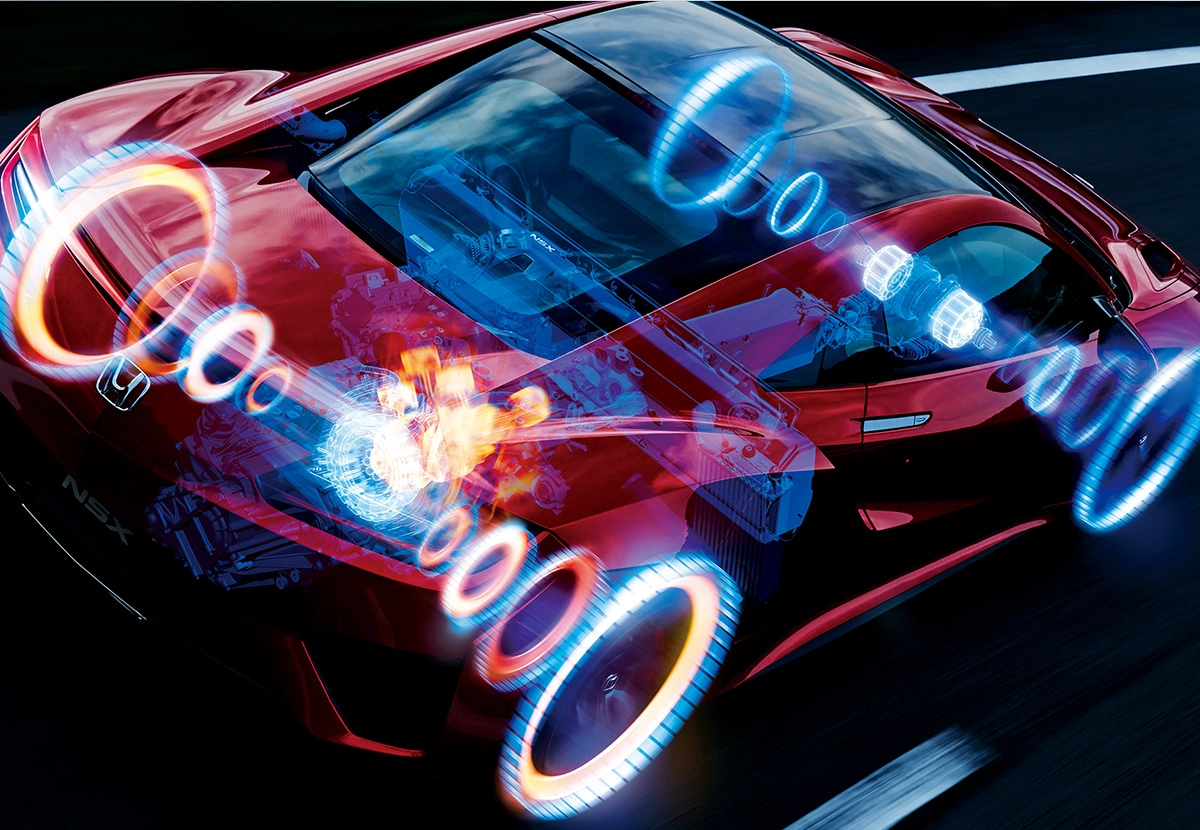
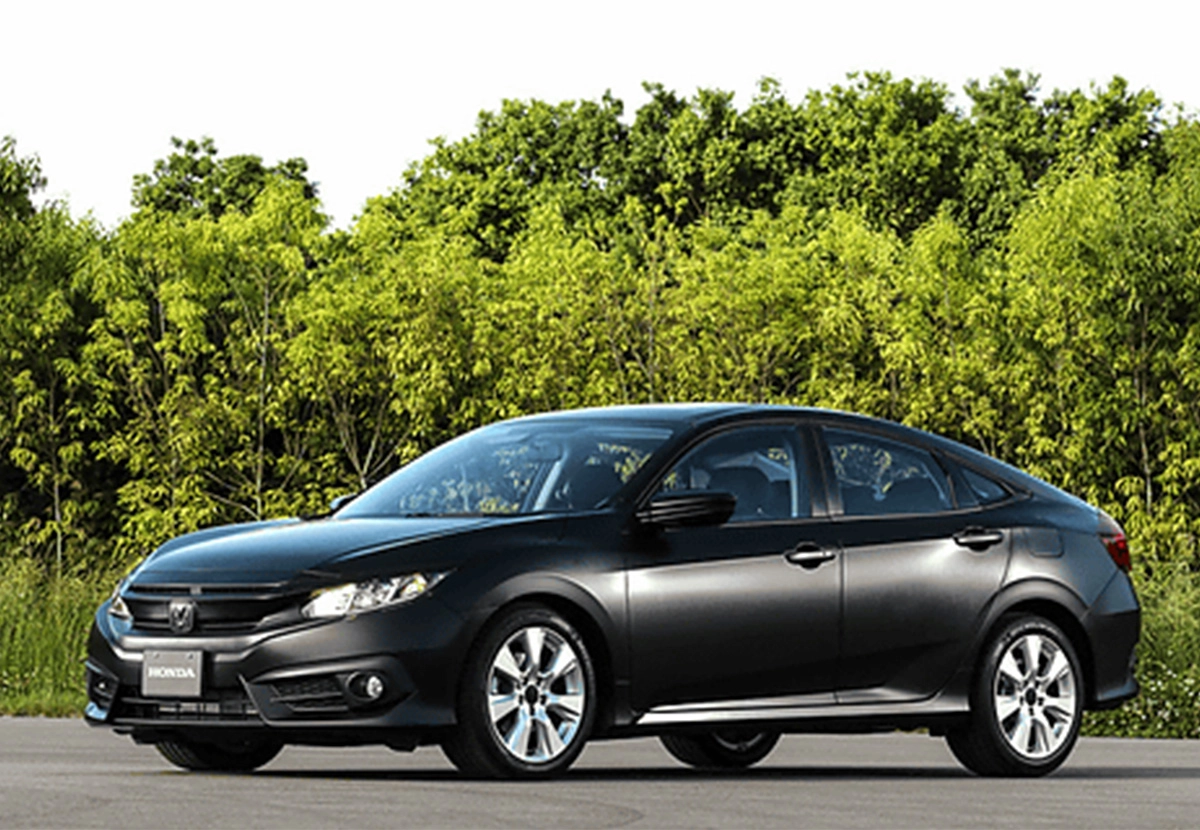






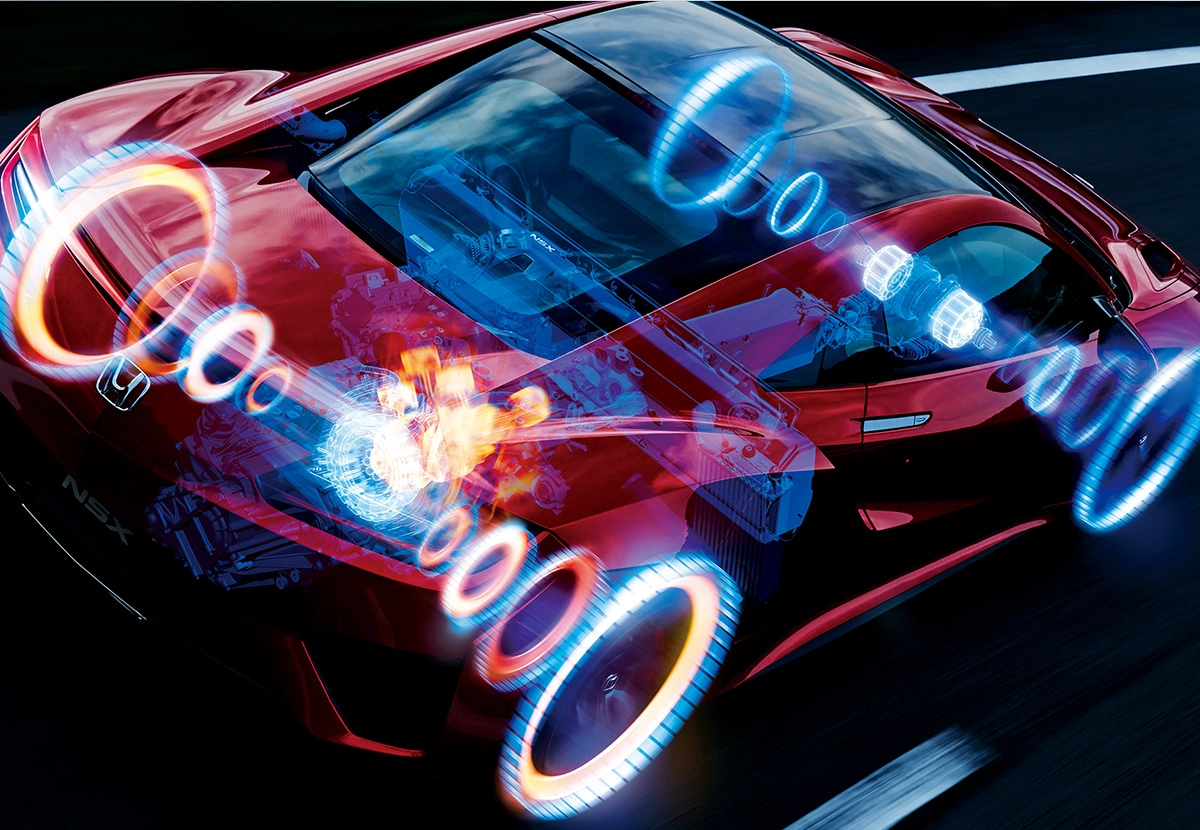
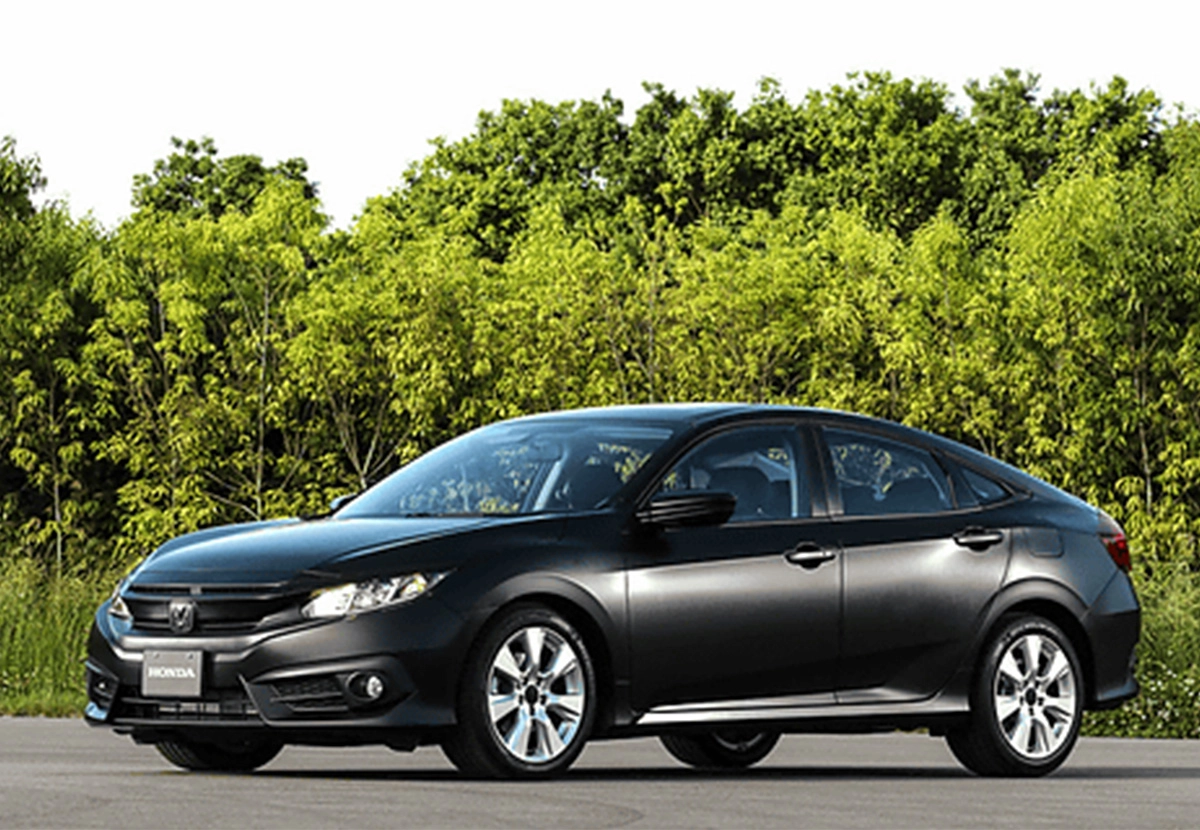

Development of the SH-AWD EV started from the belief that torque vectoring and EVs would certainly intersect at some point in the future. The development team felt the affinity of electrification to the evolution of torque vectoring. When trying to control driving torque using an engine, the first requirement is to control the volume of air fed to the cylinders. The process begins with ECU signals triggering throttle movement, resulting in movement of air with an appropriate level of inertia, the air entering the cylinders during the intake stroke, being compressed while mixing with the fuel, and then being ignited by the spark plugs. The process continues with the expansion stroke converting internal cylinder pressure to rotational movement of the crankshaft, and finally torque is generated.
When using a motor, on the other hand, the entire process consists of ECU signals triggering the motor to generate the required amount of torque, with a response time of one-thousandth of a second. With engines, there are physical limits to how much this responsiveness can be improved, while the process never goes like the simulation. Motors, on the other hand, operate just like the simulation in terms of both driving and braking. The idea of using four motors, one for each wheel, was that all wheels could be controlled freely and the ultimate torque vectoring could be achieved.
Pikes Peak International Hill Climb (PPIHC) Course Map
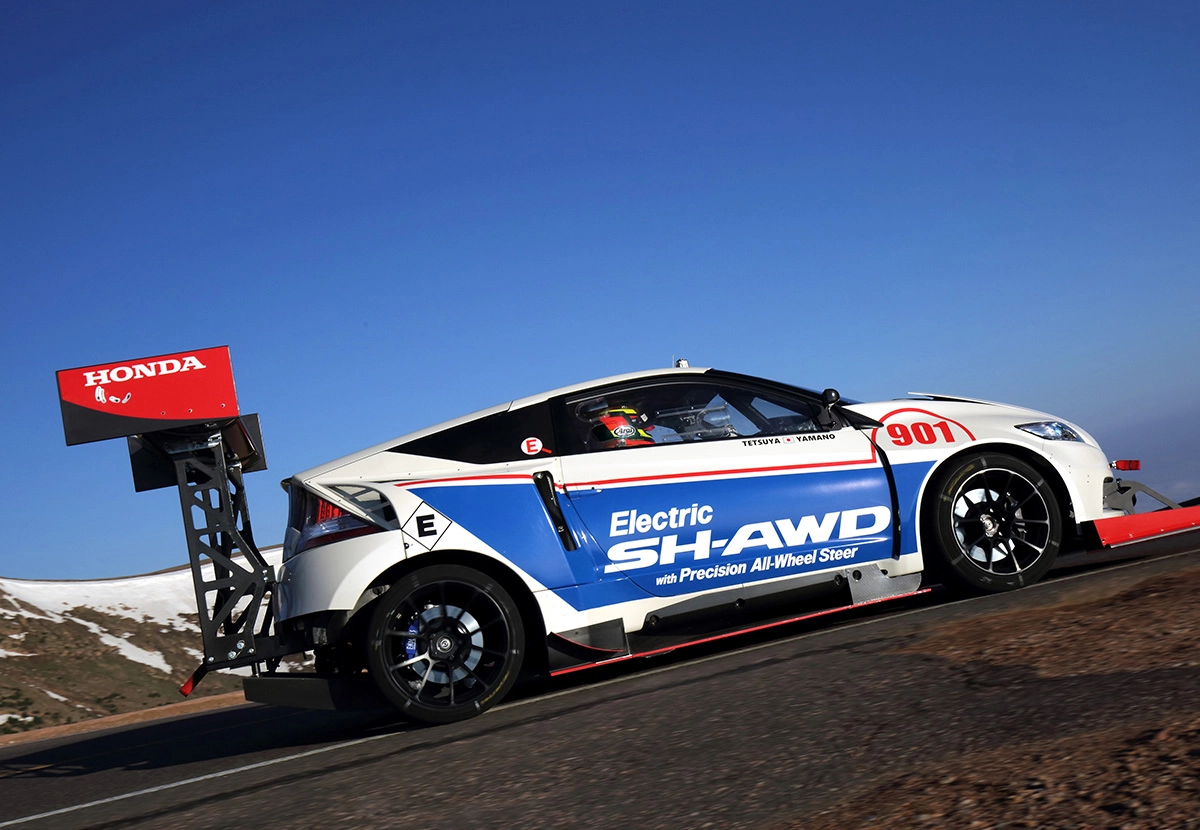
Summiting Pikes Peak in the Rocky Mountains, the PPIHC was held for the first time in 1916. Starting at an altitude of 2,862 m, the hill climb covers a distance of about 20 km until the finish line at 4,301 m, with participants racing against the clock around 156 corners. Drivers can experience sunny weather at the start, but changing to falling snow at the finish line situated above the tree line. The closer to the finish line that they get, the lower the air density becomes, which reduces engine output by about 40%.
EV output, on the other hand, is not affected by drops in air density. But with harsh changes in temperature throughout the course, and the continuous demand for high current flows, battery temperature management becomes important. In addition to verifying the effectiveness of torque vectoring, the team treated the race as an opportunity to gather useful data.
Electric SH-AWD with Precision All-Wheel Steer (CR-Z-based Racing Car)
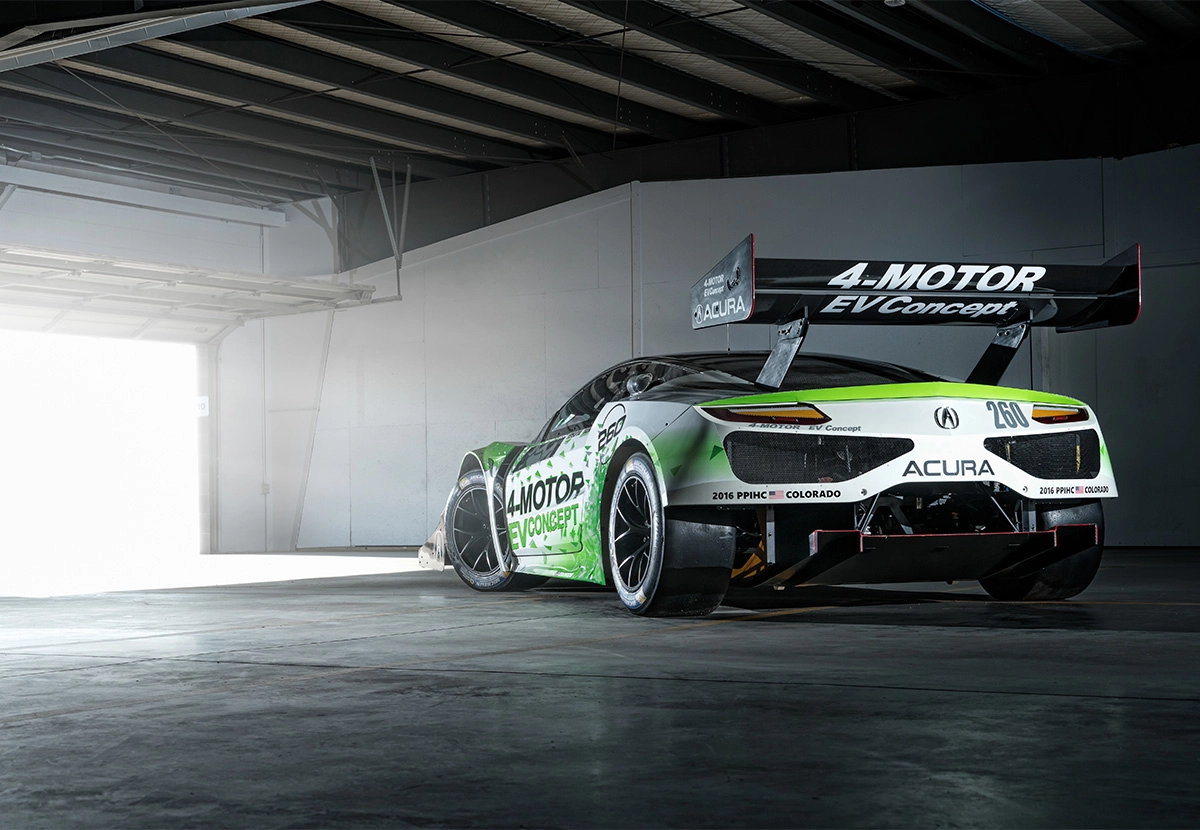
The CR-Z was chosen as the base for the car Honda entered into the PPIHC because it had space for mounting a battery in place of the rear seat to improve safety in the event of a rollover or other accident, and because a sports cars base was preferable. The reason that four motors were used is that costs could be maintained at a more reasonable level than if a large motor had to be newly developed, and consequently because they provided more power for torque vectoring. So rather than two birds with one stone, Honda’s approach was more “three birds with one stone.”
With the second-generation NSX not yet launched at the time, the team took the system from the Legend, which had the TMU mounted in the rear, and mounted it in the front as well as the rear on this car. The TMUs each comprised two motors, planetary reduction gear mechanisms, one-way clutch, and brake. Their basic structure was copied from the Legend as well due to the development concept of using mass production parts directly on the PPIHC racing car. A direct-coupled clutch was also employed for efficiency.
The team also installed Precision All-Wheel Steer (P-AWS), a rear toe control system from the front-wheel-drive Acura RLX in the North American market. The P-AWS system replaced the rear suspension toe control arm with an electronic telescopic actuator to steer the left and right rear wheels independently. A lithium-ion battery was also installed behind the front seat.
The PPIHC is contested by a variety of vehicle classes. In the 2015 event, the overall victor in the modified EV class (unlimited EV division) completed the run in a time of 9 minutes 7 seconds. The Honda team named its car “Electric SH-AWD with Precision All-Wheel Steer,” with the purpose of entry being to verify the effectiveness of torque vectoring in harsh environments, rather than to achieve the fastest time. With neither power nor ranking being the goal, they chose to enter the Exhibition Class (mass production prototype), and set a target time of 10 minutes 30 seconds.
Pikes Peak International Hill Climb (PPIHC) Classes and Target

The fundamental principle of torque vectoring control is that applying a greater torque to an outer wheel than to an inner wheel generates a yaw moment toward the inside of the turn, around the center of gravity, that achieves outstanding steering response. After conducting research, Honda’s development team found this control technology to be effective when used on the rear axle, but that when used on the front axle, it tended to pull the steering and create an uncomfortable vehicle behavior for the driver.
It also found that when a greater torque was applied to the outer front wheel than to the inner front wheel, it pulled the steering and then sometimes created a tendency to understeer. To counter this, a larger torque was applied to the inner front wheel than to the outer front wheel to generate a restoring moment, and that brought vehicle behavior back to stability. Rather than applying uniform control in all situations, they were able to switch between settings, depending on the driving situation, according to various vehicle information, including steering angle, gas pedal position, vehicle speed, lateral G-forces, and yaw rate.
In the lead-up to the actual PPIHC race, the development team repeatedly test drove the racing car in Japan to adjust the control to the driver’s preferences. The result was a system that could be adjusted toward more responsive steering if preferred, or toward more stable steering if that was the driver’s preference. The ability to use control technology to tailor vehicle behavior to a driver’s preferences was not only a characteristic of the four-motor SH-AWD EV, but an example of putting that characteristic to full use as well. At Pikes Peak as well, the team tested the system vigorously to analyze each driving situation, from tight cornering to stretches where the cliffs closed in, to ascertain the optimal controls ahead of the race.
SH-SH-AWD TMU Setting Comparison

On the day, Honda’s racing car recorded a time of 10 minutes 23.829 seconds. Rather than bettering the preliminary simulation times, which it did, the main achievement was successful implementation of independent motor-based torque vectoring on all four wheels, while maintaining natural vehicle behavior that did not feel uncomfortable for the driver.
At Honda’s first attempt at the PPIHC in 2015, it was able to confirm the effectiveness of torque vectoring, as its primary focus, in line with simulations. The results showed yet again the future potential of four-motor EVs helping to create a car that moves as expected even with a simple configuration.
Race Day Photos



















The Honda Super Handling Challenge
- Chapter 1 Honda Four-Wheel Steering System (4WS) Technology – 1987
- Chapter 2 Active Torque Transfer System (ATTS) Technology – 1996
- Chapter 3 Variable Gear Ratio Steering (VGS) Technology – 2000
- Chapter 4 Super Handling All-Wheel Drive™ (SH-AWD®) Technology – 2004
- Chapter 5 Rear Toe Control System: Precision All-Wheel Steer Technology – 2012
- Chapter 6 Legend’s Sport Hybrid SH-AWD® Technology, a Three-Motor Hybrid System – 2014
- Chapter 7 NSX’s Sport Hybrid SH-AWD® Technology, a Three-Motor Hybrid System – 2015
- Chapter 8 Honda’s Concept of Dynamic Performance
- Chapter 9 The Future of Super Handling (1): Four-Motor EVs
- Chapter 10 The Future of Super Handling (2): Four-Motor EVs
TechnologyHonda Super HandlingThe Future of Super Handling (1): Four-Motor EVs