The Honda Super Handling Challenge Chapter 2
Active Torque Transfer System (ATTS) Technology – 1996
The Honda Super Handling Challenge Chapter 2
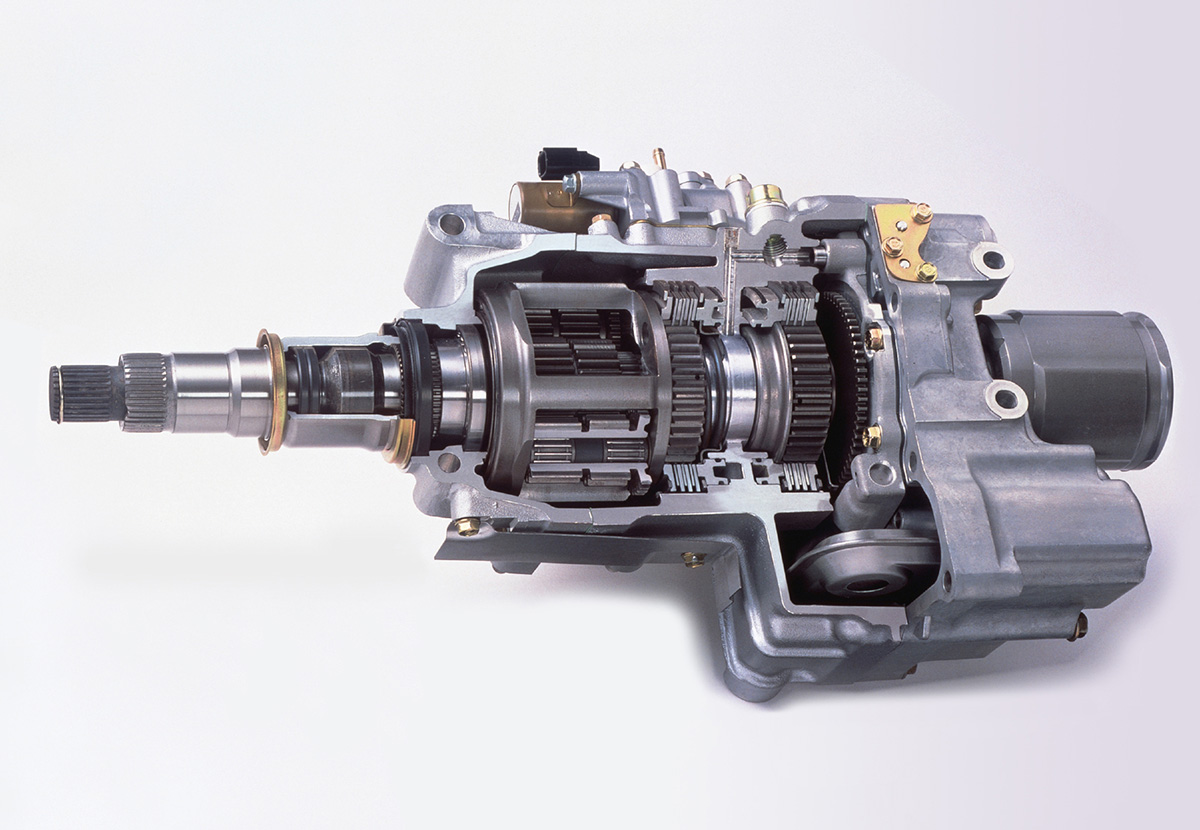
Honda developed the Active Torque Transfer System (ATTS), which achieves excellent turning performance by distributing torque between the left and right wheels in front-wheel drive vehicles, and first applied the technology to the Prelude Type S which went on sale on November 8, 1996. The ATTS distributes different amounts of torque to the left and right wheels depending on the turning conditions, in contrast to conventional systems which could only provide equal torque to both driving wheels.
Prelude – 1996
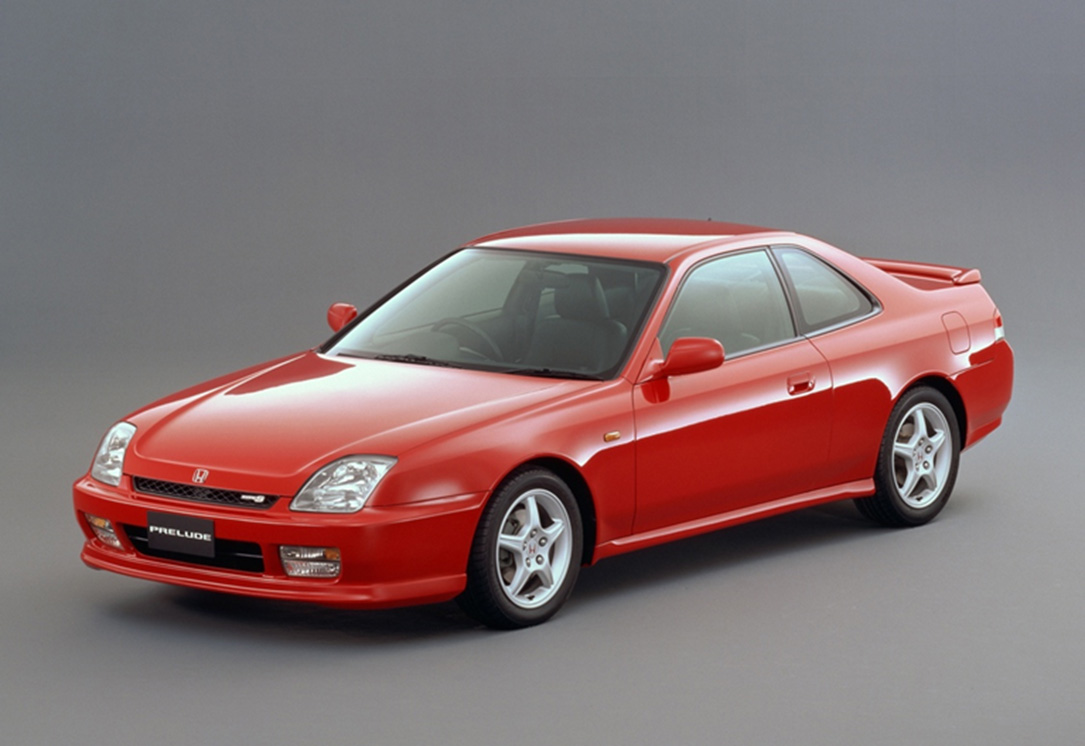
A car typically turns by changing the direction of its tires through steering operation. The torque generated by the engine is used only for driving and is always equally distributed to the left and right tires. With ATTS, depending on the turning condition, less torque is distributed to the inner tire and more torque is distributed to the outer tire while turning. This uneven distribution of the torque creates an effect that facilitates turning by steering. This is the same principle as turning a rowboat by rowing the outside oar harder and increasing the force on the outside of the turn.
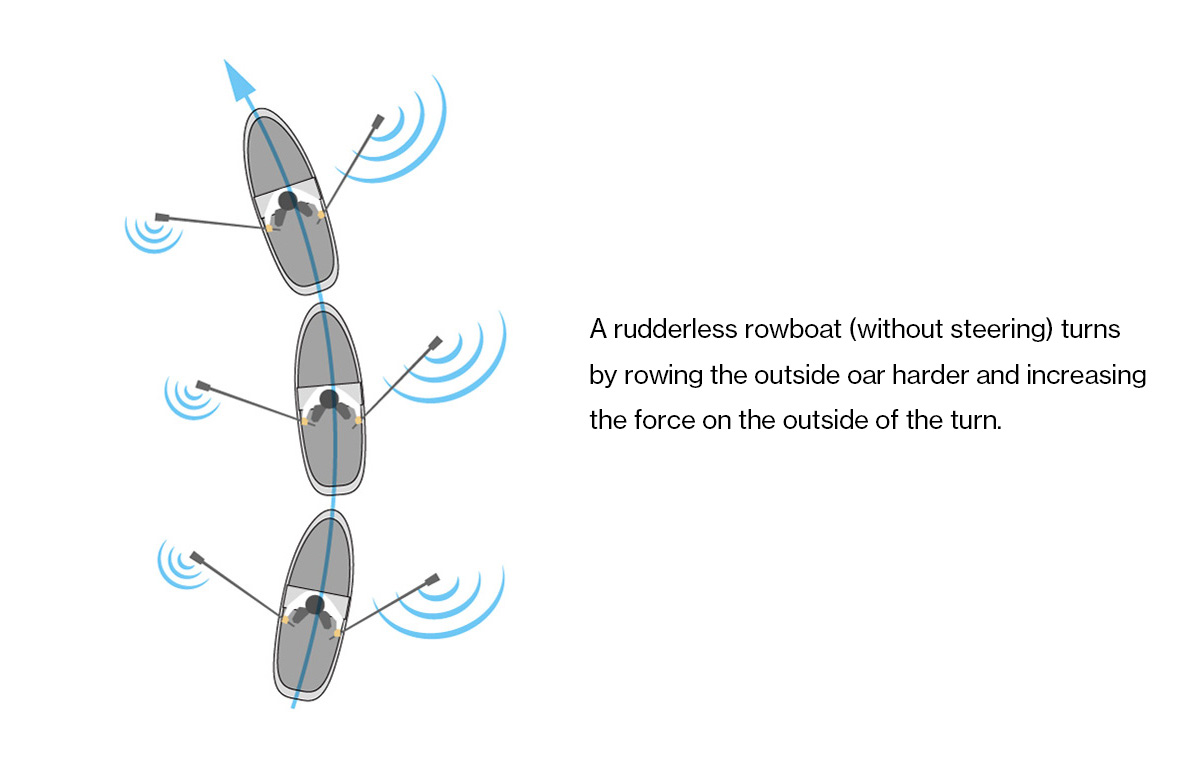
The Legend, which went on sale in October 2004, was equipped with the world's first Super Handling All Wheel Drive (SH-AWD) system. The Legend's SH-AWD generates an inward yaw moment by transmitting greater driving torque to the driven (rear) outer tire than to the inner tire when turning. Although there is a difference between the drive and driven tires, the concept of actively controlling the yaw moment was the same. In other words, ATTS was already demonstrating the concept that would later lead to the SH-AWD.
The ATTS concept came from the idea that new vehicle characteristics could be realized by replacing four-wheel-drive (4WD), which distributes driving torque between the front and rear tires, with torque vectoring to left and right tires. The principle of left-right driving torque distribution was reproduced by converting a 1987 4WD Civic Shuttle into a one-wheel-drive vehicle, with torque going only to the rear-right tire. The development team drove this car on a test course at the Tochigi R&D Center and confirmed the exhilarating turning feel resulting from the generation of a yaw moment.
By 1989, the technical viability of the system had been established, and development was underway to apply ATTS to 4WD vehicles. However, the opportunity for commercialization came first with front-wheel-drive (FWD) vehicles. This was the 1996 Prelude. The commercialization of the ATTS unit was based on repeated studies, which led to a layout combining parallel twin-shaft and hydraulic CVT (concept), a parallel triple-shaft (concept), a parallel twin-shaft (prototype), a double pinion and double planetary (prototype), and finally to a triple pinion and triple planetary system.
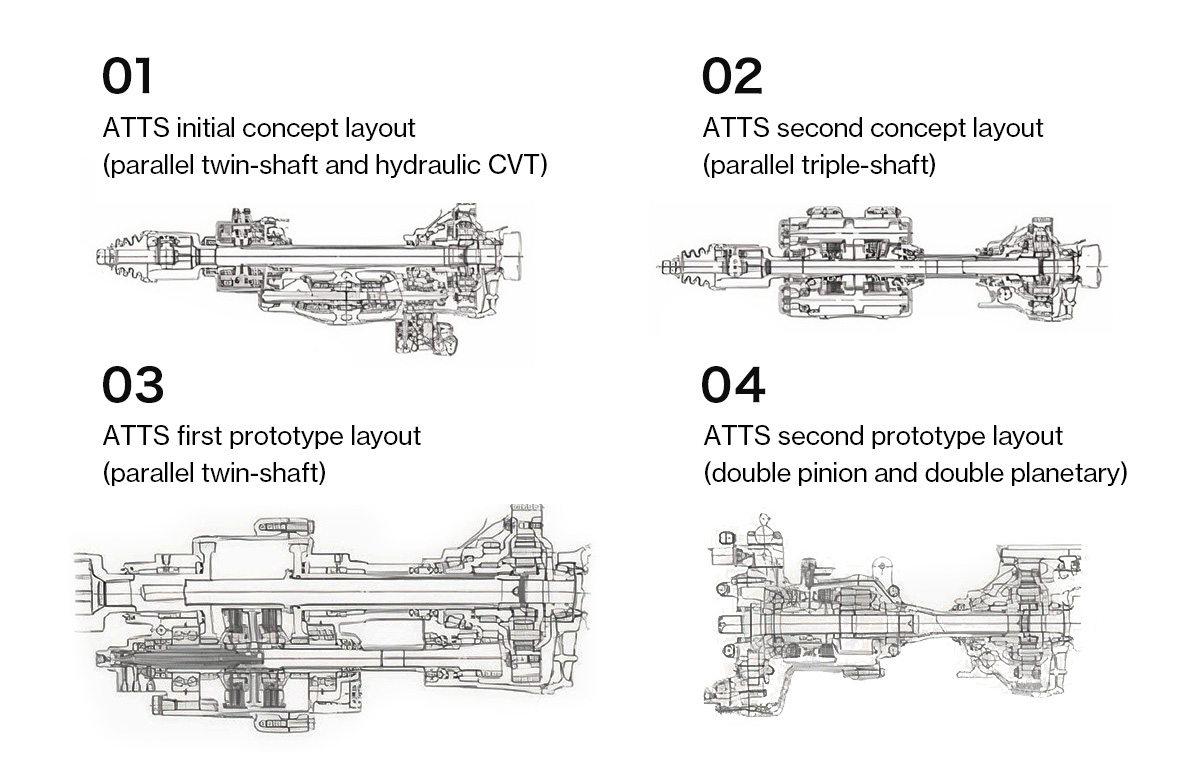
The Prelude was equipped with an ATTS unit that consisted of 1) a triple planetary gear assembly that distributes the driving torque from the differential gear, 2) left and right multi-disc wet clutches and 3) a hydraulic control unit. The torque distributed to the left and right from the differential gear is transmitted to the ATTS unit via two concentric overlapping shafts. The outer concentric circle is the rotational shaft of the right tire, and the torque is transmitted from right to left via the differential gear case. The inner concentric circle connects directly from the differential gear to the left tire. The carrier shaft of the planetary gear is connected to the right-turning clutch, and the leftmost gear of the triple pinion is connected to the left-turning clutch.
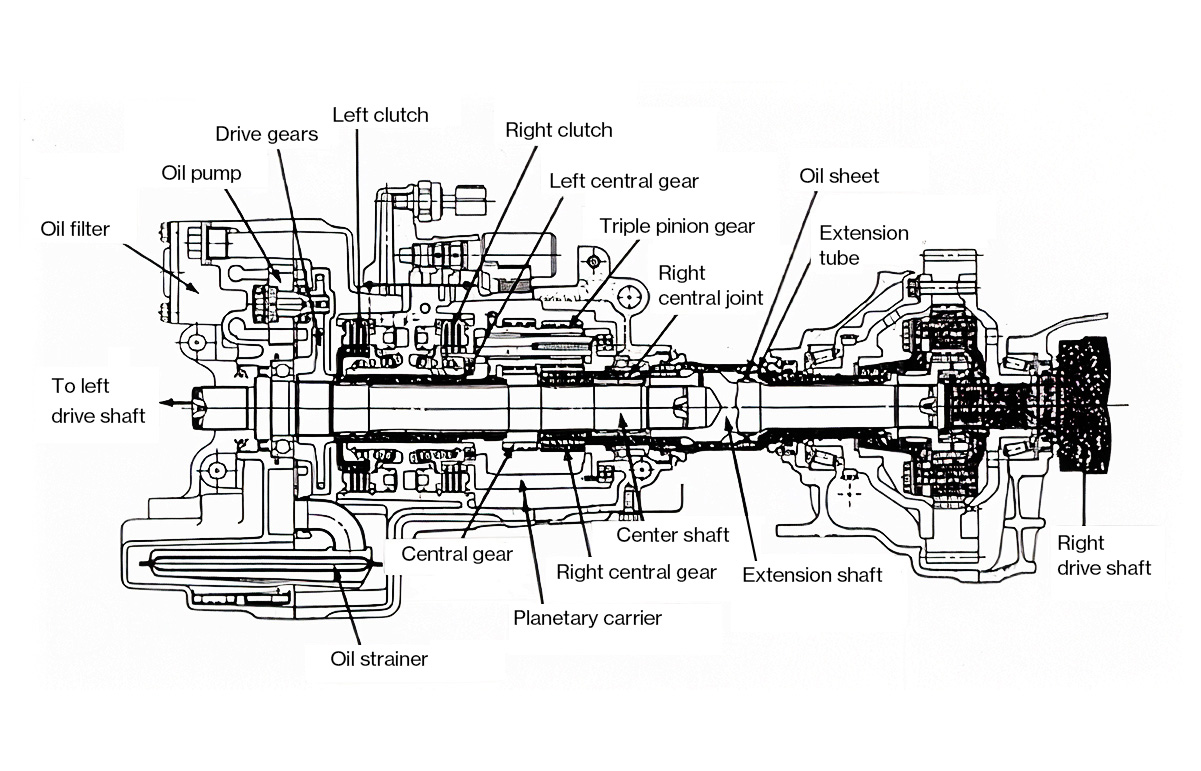
As with the principle of a rowboat turning, in order to control the yaw moment with the right-left distribution of the driving torque, the outer tires must turn faster than the inner tires. To achieve this, a speed-boosting mechanism is necessary. A speed-boosting mechanism using triple-pinion planetary gears is used to raise the speed of the inner tire above that of the outer tire, and by connecting the clutch, driving torque is generated in the outer tire and braking force is generated in the inner tire to make rotation of the outer tire greater than the inner tire.
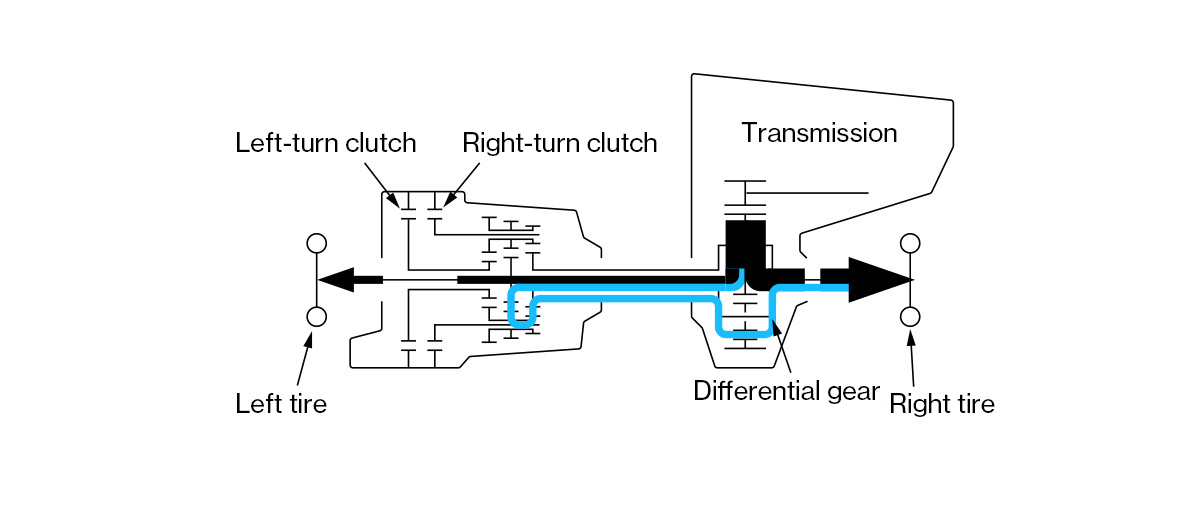
Turning left
When turning left, the driving torque is transmitted as follows. When the left-turn clutch decelerates and is locked, left wheel torque split by the differential gear is transmitted to the left sun gear, to the triple pinion gear, to the right sun gear, to the differential gear case, and to the right wheel axle, increasing the driving torque of the right tire.

Turning right
When the right-turn clutch decelerates and is locked, right wheel torque split by the differential gear is transmitted to the differential gear case, right sun gear, to the triple pinion gear, to the left sun gear and to the left wheel axle, increasing the driving torque of the left tire.
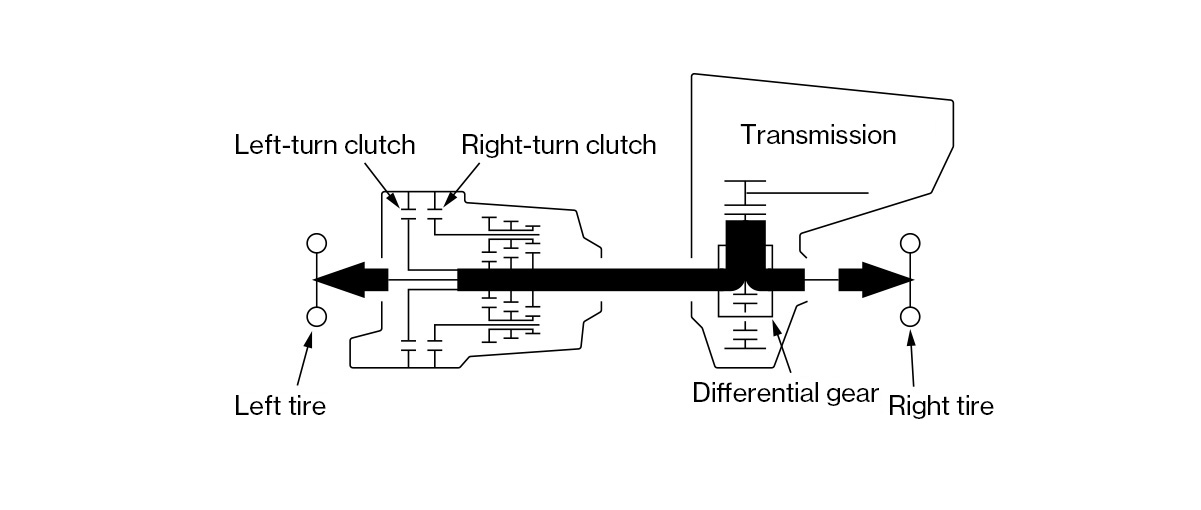
Driving straight
The neither of turning clutches is engaged, and driving torque is transmitted from the engine to the transmission, to the differential gear and to the left and right tires equally.
Since ATTS is set to actively overdrive the outer tire by around 15% compared to the inner tire, when the clutch decelerates and locks during a turn, the outer tire will be overdriven by approximately 15% compared to the inner tire. This makes controlling of left-right torque distribution possible within a range of 1.15 or less for the ratio of the tire trajectories of the left and right tires while turning. Assuming the tread of the vehicle is 1.5m, this means that the ATTS is effective in turning with an inner tire turning radius of 10m or more. In addition, by adjusting the degree of gear engagement with the multi-disc clutch, the drive torque distribution ratio can be freely controlled up to 80:20 (outer wheel: inner wheel).
The multi-disc clutch, which distributes the driving torque to the left and right tires in accordance with the turning conditions during acceleration, is controlled by the torque vectoring ECU. The basis of the control is the feed-forward control, where the amount of control is determined by the amount of the accelerator pedal depression and steering angle, as well as the turning condition calculated from vehicle speed and lateral acceleration, additionally with feedback from the yaw rate sensor.
Specifically, drive torque is calculated based on 1) the engine torque which is based on the engine data such as engine speed and negative intake pressure, 2) engine speed and 3) gear ratio calculated from the front tire speed. Moreover, the ever-changing front/rear acceleration is estimated from the drive torque. At the same time, the lateral acceleration is calculated from the rear tire speed and steering angle, and the amount of turning is determined by comparing it to the actual acceleration. Furthermore, the target hydraulic pressure for the clutches within the ATTS unit is determined by calculating the amounts of torque distributed to left and right tires based on the front/rear acceleration and the amount of turning. To improve control accuracy, the yaw rate detected by the yaw rate sensor is fed back to stabilize vehicle behavior.
Generally, when a vehicle accelerates while turning, turning force decreases because tire grip is used for acceleration, resulting in a tendency toward understeer. Deceleration allows the tires to use their grip on the turning side, which reduces the degree of understeer. In other words, the vehicle behaves differently depending on whether the driver accelerates or decelerates by operating the accelerator pedal. Calculations and tests have shown that ATTS increases the restoring moment to bring the vehicle back to a straight line when accelerating, and decreases it when decelerating. ATTS acts to reduce the change in vehicle attitude during acceleration and deceleration caused by the driver's accelerator pedal operation.
Trajectory when accelerator is released while turning
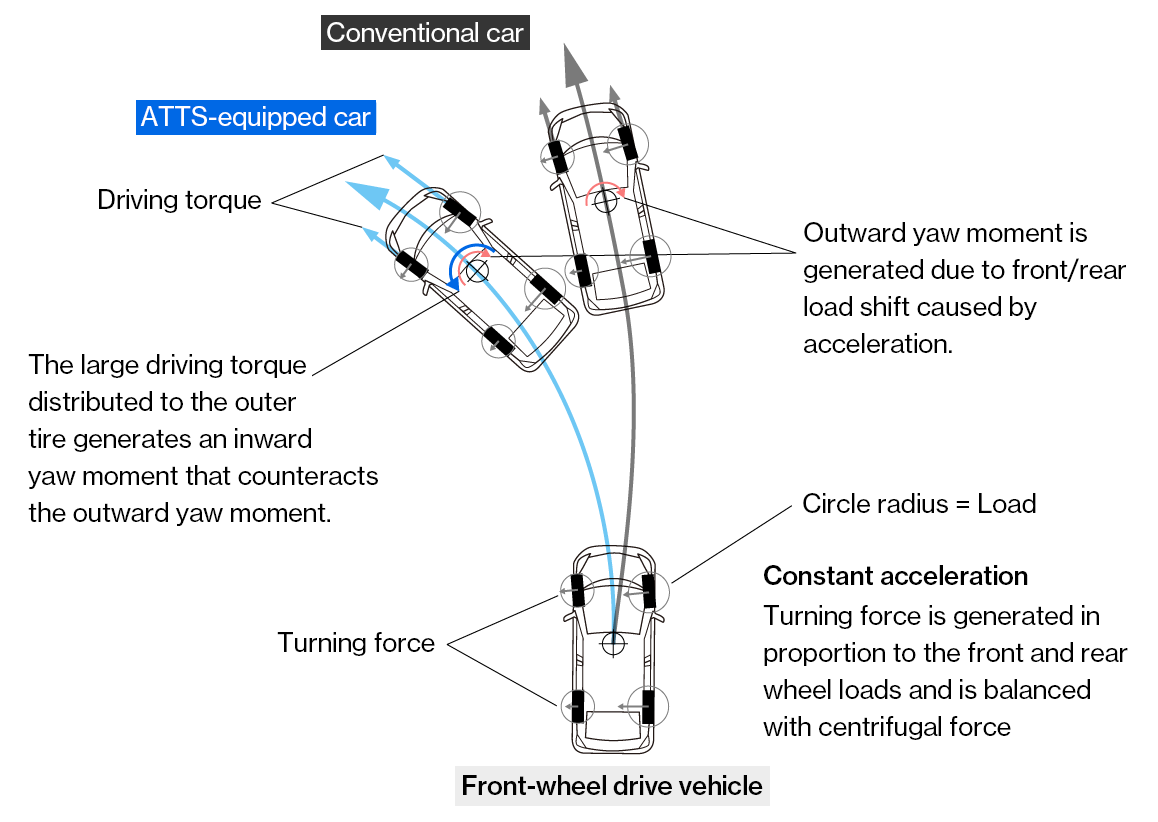
ATTS generates a yaw moment by transferring more driving torque to the outer tire during acceleration in a turn, which has the effect of helping the vehicle to turn. In addition, it also effectively brings out the performance of the front tires. When turning, the ground load on the outer tire increases and the ground load on the inner tire decreases. In a regular front-wheel drive vehicle, the driving torque is distributed equally to the left and right tires, so the grip of the tires is used to drive the inner tire, which cannot be fully used for turning.
With ATTS, the driving torque is distributed to the left and right tires in accordance with their capabilities, allowing the tires to be used effectively when turning, and the total turning force of the left and right tires is greater than that of a normal front-wheel drive vehicle. In addition to the generation of yaw moment, the effective utilization of the capabilities of the left and right tires reduces the understeer during acceleration.
As understeer is reduced by ATTS, the steering angle and tire slip angle are also reduced. As a result, wear on the outer tire increases slightly, but decreases on the inner tire, and overall tire wear is reduced, as confirmed by actual driving wear tests.
Honda developed a dedicated front suspension for ATTS. When different amount of drive torques are applied to the left and right tires by ATTS, the difference between the left and right torque acts to turn inward around the kingpin (center axis of rotation), and as the drive torque of the outer tire becomes greater than that of the inner tire, generating the torque steer in the direction of steering.
To eliminate this torque steer, it is necessary to reduce the kingpin offset of the suspension. With the Prelude's double wishbone suspension, the torque steer was reduced by adopting the double joint to the lower link, which enables the virtual kingpin to be set at a different position from the actual ball joint position.
Tire grip increases in proportion to vertical load. When turning, the load on the outer tires increases and the load on the inner tires decreases. ATTS, which increases the load for the outer tires with increased grip, is a logical control, and a technology that enables Honda to create cars that feel like they are behaving at the will of the driver.
TechnologyHonda Super HandlingActive Torque Transfer System (ATTS) Technology – 1996