To Remain the World’s No.1
Kumamoto Factory, Honda’s Global Core Factory
The Kumamoto Factory plays an important role as Honda’s core global motorcycle plant while producing mainly FUN models. General Manager (as of 2023) Masaki Shimazoe looked back on the past.
“I think around 2000 was our new beginning. At the time we planned to triple our annual global production and sales of 5 million units by 2010, and created the ‘500,000 units per pack’ factory standard and made it our global standard. One line can produce 500,000 units, so we worked at a considerable pace to build 20 new lines within 10 years.”
Initially, the Kumamoto Factory produced FUN models in “500,000 units per pack,” while the Hamamatsu Factory produced models with complex specifications. In 2008, the two bases were consolidated into Kumamoto. Meanwhile, there was also the problem of Chinese copies.
“In Hamamatsu, we were doing PDI (pre-delivery inspection) on Todays sent from Sundiro Honda in China. We had tremendous cost competitiveness, but I think it was a tough battle to bring the quality to a level acceptable to Japanese users.” (Shimazoe)
By 2010, Honda was promoting the independence of its overseas plants and the localization of SEDBQ*3 while expanding the global production and sales target from 15 million units to 20 million units by 2020. Even if all production bases became independent and each promoted product manufacturing tailored to regional characteristics, the quality and reliability of the Honda brand could not be compromised.
“One of the methods to achieve unification and uniformity was to prepare a technical catalog of manufacturing technologies and make this catalog globally available. Another was to share jig information. For example, when a jig diagram drawn by TH was to be used by Honda Vietnam (HVN), it could only be passed on through Honda’s technical support, which was time-consuming and labor-intensive. This was inefficient, so the bases signed agreements so that information could be mutually complementary and shared. We also struggled with the development of a common platform. For example, Vietnam, Thailand, and Indonesia produce the same global model, but sometimes the appearance is the same, and sometimes it is changed according to regional preferences, so there are small differences in design on the production line, making it difficult to create common specifications. I believe that it is Honda’s strength and characteristic to fit these differences in the field and in the actual product.” (Shimazoe)
- S: sales, E: engineering/production, D: development, B: buying/purchasing, Q: quality
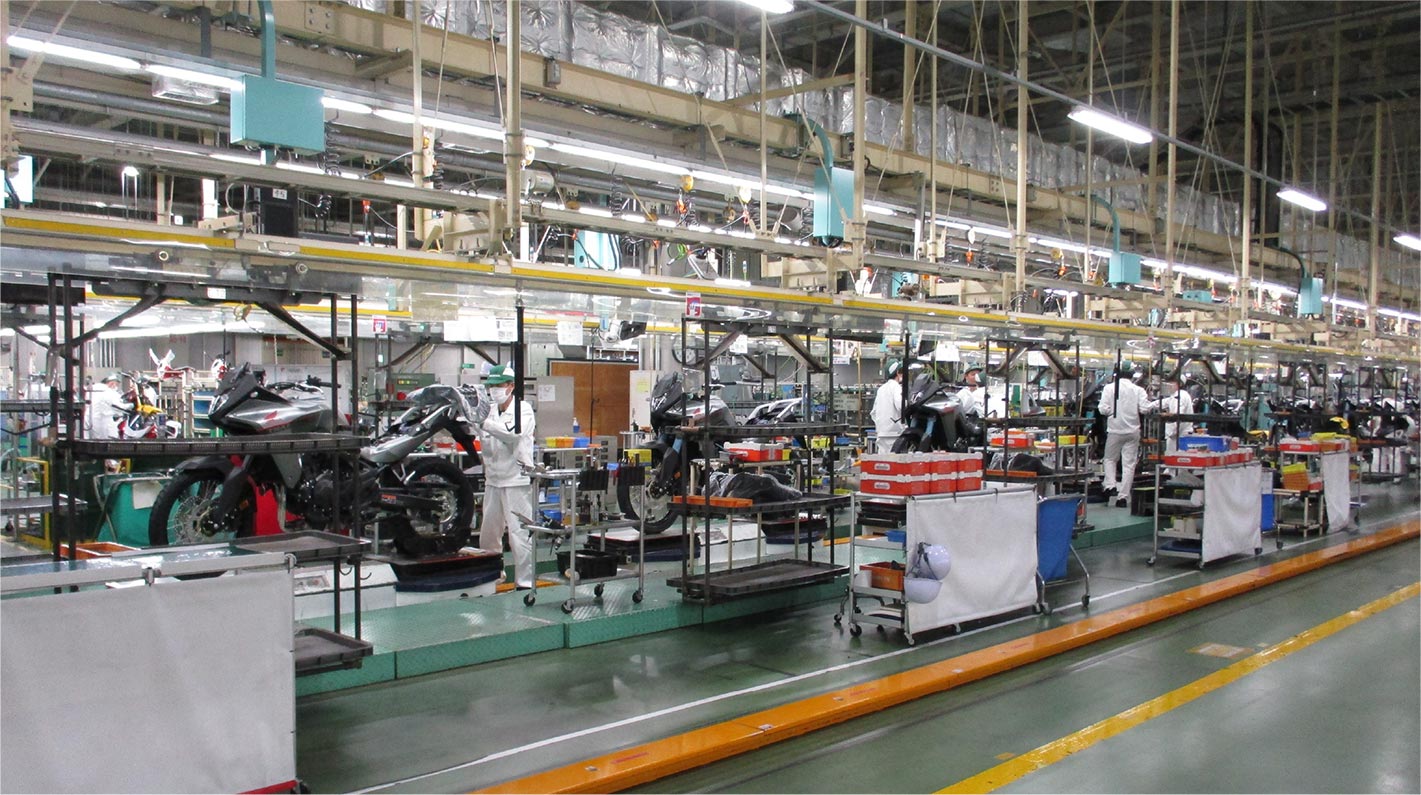
Kumamoto Factory acts as Honda’s global motorcycle core factory.
Kumamoto Factory’s Craftsmanship Spirit Creates Admiration
Honda’s strength at the production site is, in a sense, the spirit of craftsmanship. Honda not only pursues high efficiency and precision, but also produces top-end models that users adore, and has demonstrated its pride and determination as the world’s number one motorcycle manufacturer. The best example of this is the RC213V-S, launched in 2015. It was an unprecedented move to sell a street-legal version of the RC213V MotoGP factory bike.
“This was new to the Kumamoto factory, so we decided to produce it in a ‘show process.’ Since the manufacturing process was completely different from that of mass-produced models, and the people on site had to work very hard to bring it to fruition, we thought it would be a good idea to have everyone see the process. We decided that the best way to do this was to have visitors watch as the engineers worked, so we set up an assembly booth. We wanted to make it attractive, rather than just a work process,” recalls Tadayuki Watanabe, who planned the RC213V-S mass production project.
The challenge was procuring the necessary parts and securing the human resources to assemble them. Convincing the prototype manufacturer to accept the production of special parts that could be considered prototypes in terms of mass production was a challenge, but so was the management of the parts that were delivered.
“The prototype manufacturer was so helpful, they told us they would only make a certain number, and would never do this again. Deliveries were hectic, depending on whether they were delivered in batches or in complete instalments, so we had to figure out how to manage and deliver the parts. The factory management in Kumamoto had its hands full with mass production, so I had no choice but to do it myself.” (Watanabe)
Task members were selected from among the associates working at each site. For example, even for a single weld, joint surfaces were manually sanded and adjusted, and welding was only conducted after the surfaces had been properly prepared. On top of this, the welding beads were required to be 1 mm apart.
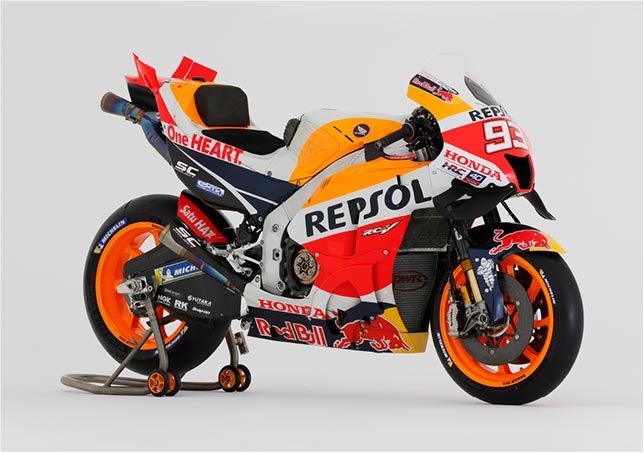
“I wanted to show people the hard work by the task members. From my own experience, I think the efforts of the young welders must have been amazing. The experience must have given them confidence and made them proud of their work. The power of young people is tremendous, and I felt that this will become Kumamoto’s potential.” (Watanabe)
For production, the plan was to complete each task precisely, one unit per day. This included the “attractive process” concept. The work, including adjustments, was all done by hand, as the bike had to reproduce the same high level of assembly precision as a MotoGP machine. Watanabe said, “For us at Honda, that is our origin.”
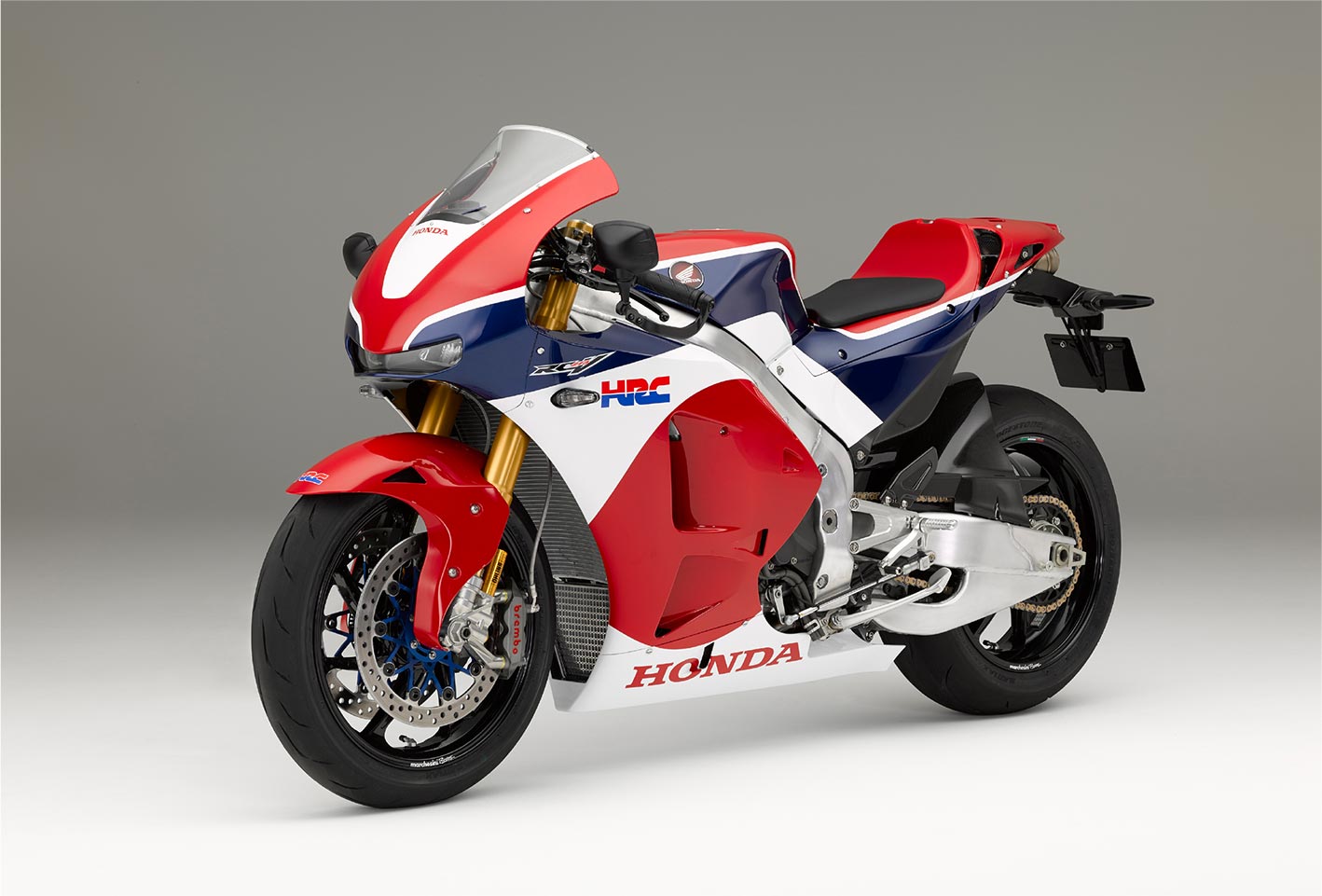
The RC213V-S, a mass production model of the RC213V MotoGP machine, was entirely hand-assembled at Kumamoto Factory.
Although Times Change, the “Three Reality Principle“
is Practiced
As of 2023, Kumamoto does not draw a line between development and production, but rather conducts its business as unified DEB. A Kumamoto branch of R&D has been established within the Kumamoto Factory, and they are working together as one to solve problems. In Japan, organizations are often subdivided for departmental optimization, and while a high level of specialization is an advantage, the slow time efficiency of interdepartmental coordination is often a disadvantage.
“We wanted to solve this problem and speed up the process. In order to establish technologies in Kumamoto, the core factory, and to spread them to the rest of the world, it was essential for the Japanese side to be unified.” (Shimazoe)
When Shimazoe became the General Manager of Kumamoto, he kept on saying, “As the core factory, it is not enough to just go to other factories to provide support. Use overseas parts.” One reason was to hedge foreign exchange from a managerial standpoint (using overseas parts would make parts cheaper even if the yen appreciated), and the other was to make associates aware of the quality of parts made by overseas bases.
“If we were to take responsibility for the quality of the parts, we would take our work more seriously. If we need to go and hear the customers for ourselves, we need to ride our own products. A dealer in Thailand once told me, ‘Honda is different from other manufacturers. Japanese people come to us immediately.’ If you are not satisfied, keep at it until you are. This is what we call the ‘Three Reality Principle’, where the people on the front line understand the situation, say, ‘Okay, let's do it,’ and then take action to get closer to the solution. I believe this is the only way we can win.” (Shimazoe)
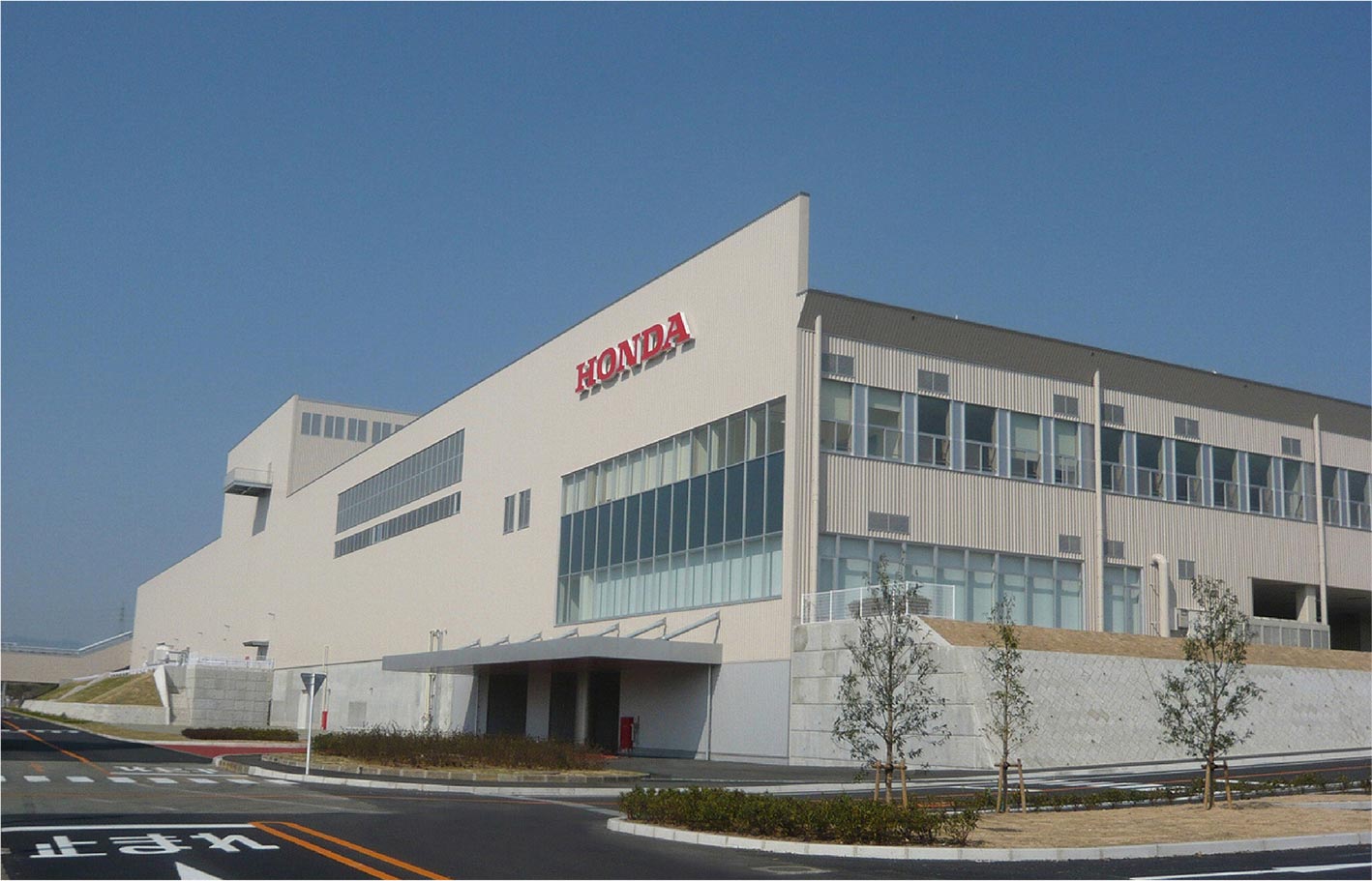
Kumamoto Factory
Pride in Monozukuri “RC30 Refresh Plan”
In 2020, Motorcycle Operations opened the Motorcycle Refresh Center at the Kumamoto Factory to implement the “VFR750 R
This is a technical service to restore RC30s released in 1987, and includes the sale of approximately 150 parts close to the original specifications, which were previously difficult to obtain, and restoration work by seasoned engineers at the Kumamoto Factory.
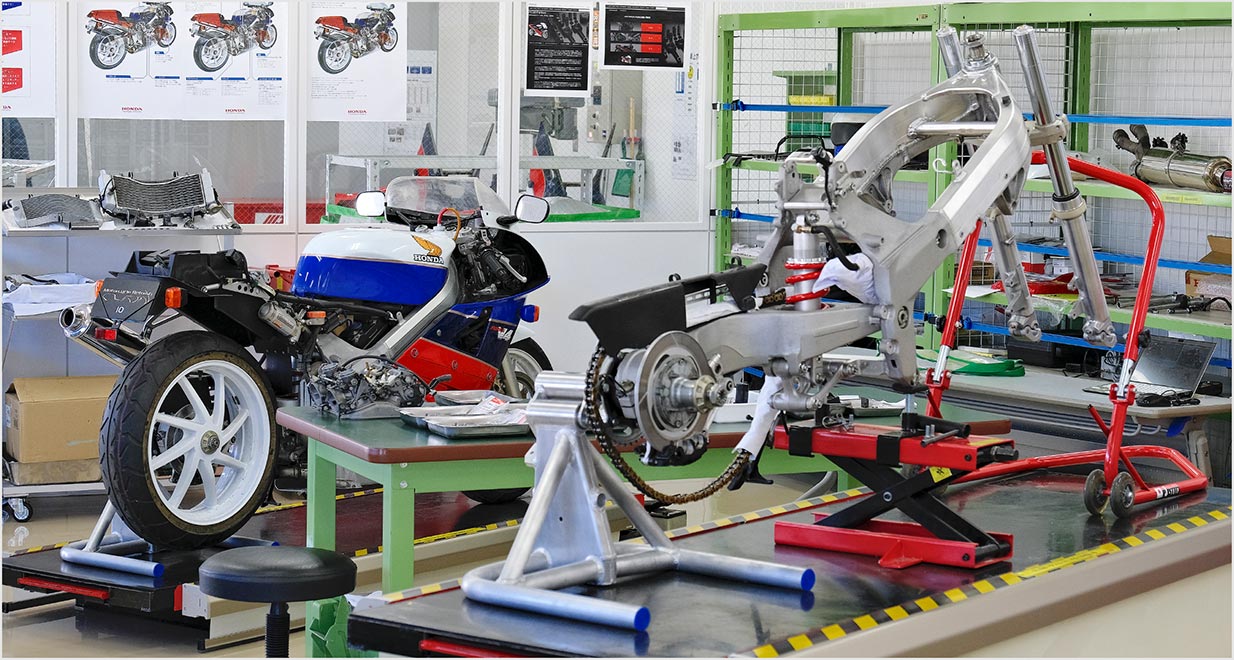