“Creating What Does Not Exist”
- Human-centric Safety Technology
In the mid-1990s, Honda R&D’s associates involved in safety technology were developing a policy that when considering automobile safety in the 21st century, crash safety should be tackled in a more realistic (real world) context.
The associates who had been studying the actual state of traffic accidents from early on, had noticed that collisions between cars or between cars and pedestrians accounted for a large percentage of accident fatalities. They had a rough idea of how collision-safety bodies for cars would evolve. If so, they decided, they should focus on and deal with the two greatest causes of accident fatalities in the real world.
Although pedestrian accidents accounted for a large percentage of traffic accidents in Japan, no serious measures had been taken with the vehicles. Honda believed it was necessary to tackle this problem head-on, and began full-scale research on pedestrian protection in 1988. Based on a detailed analysis of actual accidents, the team investigated which part of the car hit which part of the pedestrian, and found that the most likely cause of death was head and face trauma, accounting for 63% of fatalities, while the hood, fenders, and upper dashboard were the most frequent contact points, accounting for 80% of all accidents. Honda decided to place the highest priority on head protection by the front of the vehicle body, but to do so, it was necessary to determine the position and speed at which the head was struck by the vehicle.
At the time, there were no crash test pedestrian dummies, and tests were conducted using modified crash test occupant dummies. In order to confirm the accuracy of the test, Honda undertook an analysis of how injuries occurred and found that there was a discrepancy with the previous data.
“Pedestrian Protection Must Begin with the Creation of Pedestrian Dummies”
Not setting regulations as the standard, and creating what does not yet exist. This was the Honda way. The decision was made to develop a pedestrian dummy in order to conduct tests more closely resembling real world accident conditions. The first task was to make the dummy’s behavior closer to that of a human body in case of a collision. A simulated dummy was developed using publicly available human anatomical data. It was a simple model, consisting of an elliptical rigid body with jointed limbs, but Honda succeeded in high-accuracy reproduction of the behavior of the human body by ensuring joint characteristics data was close to a human’s characteristics. This knowledge was then reflected in the actual dummy. After applying deformable components to the legs, adding spinal joints, and further reviewing the joint characteristics, the world’s first crash test pedestrian dummy, POLAR, was completed in 1998.
Using POLAR for crash tests, Honda developed a car body structure that reduced pedestrian injuries. Pedestrian-Injury mitigation technology was applied to the HR-V, which was launched in September 1998, and its application was gradually expanded. The pedestrian dummy was also evolved to more closely resemble human characteristics in order to improve its ability to evaluate injury data as well as behavior, and the data measurement points were expanded. Until then, the sensors built into the dummies were connected by wire to an external data collection device, which affected the behavior of the dummies. POLAR II was developed in 2000 with a built-in data collection.
In response to the increasing number of vehicles with high bumpers, such as minivans and SUVs, Honda analyzed the latest pedestrian accident data and found that injuries to the waist and thighs were becoming more common. These areas on the crash dummy was replaced with a flexible structure. With improved fracture simulation accuracy, Honda announced POLAR Il in 2008. This was a major contribution to the evolution of pedestrian protection in automobiles.
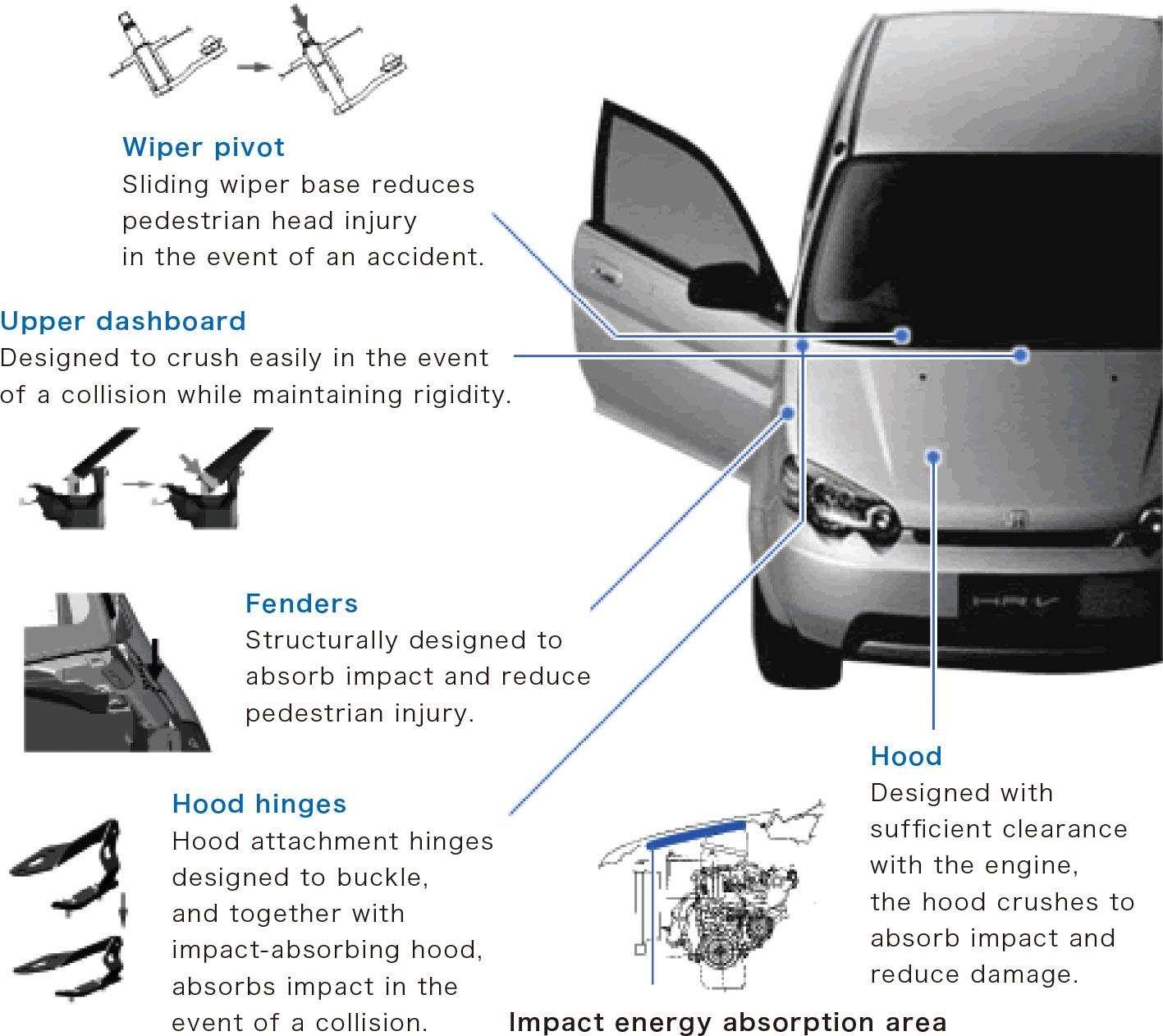
Pedestrian Injury Reduction Body developed through crash tests with POLAR pedestrian dummy
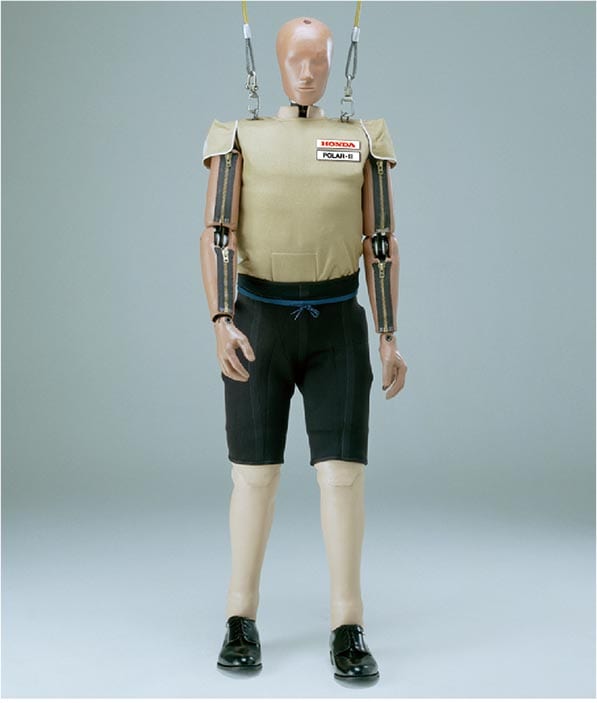
POLAR III, third generation POLAR pedestrian dummy
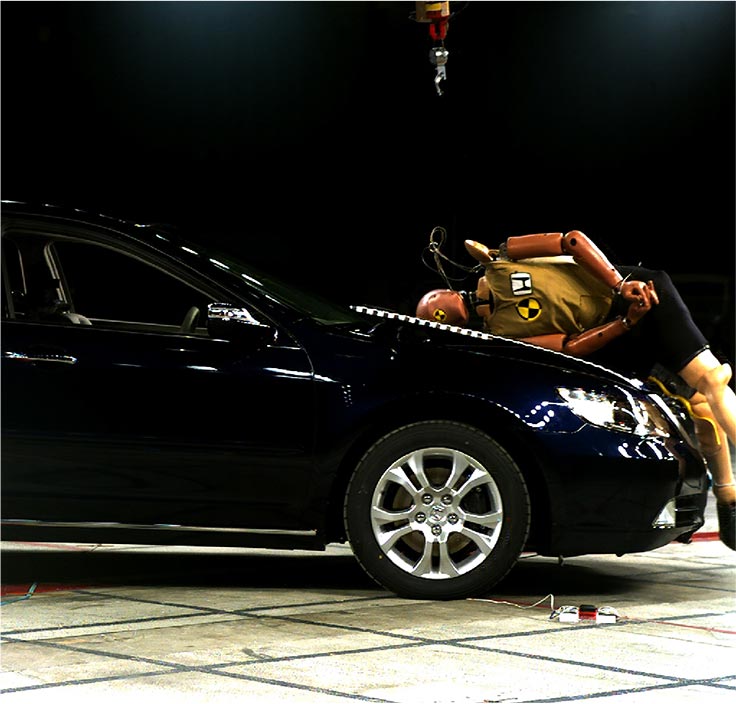
Crash test using pedestrian dummy
Meanwhile, Honda was also creating its own technology for body collision safety performance. Having experienced the so-called “second traffic war” in the late 1980s and early 1990s, Japan began applying frontal collision regulations in 1994, and in the following year established J-NCAP (Japan New Car Assessment Program), which evaluates safety under stricter conditions than the law. In 1998, Europe introduced a unified standard, but the different testing methods in Japan, the U.S., and Europe affected the development and evaluation of automobiles.
The rigid barrier (non-deforming) front full-wrap collision method used by the U.S. and Japan was suitable for evaluating seat belts and airbags. Since it was necessary to suppress the impact to the occupants by crushing the front part of the vehicle to absorb collision energy, a relatively low body rigidity was advantageous. On the other hand, Europe evaluated deformable barriers in frontal offset collisions, with the main focus on securing the occupants’ survival zone. Because of the offset, or one-sided impact and high input load, the development tended to stiffen the car’s body. In other words, there were two standards: one was to soften the body and the other was to stiffen it.
Honda believed that in order to save the occupants in the real world, both of these characteristics needed to be achieved at a core level. Honda then worked to mathematically verify a “new concept for occupant deceleration control in the event of a collision” and to realize the technology. The new concept was characterized by controlling G-force (acceleration) during a collision in three major stages. In the initial stage, when occupants are not yet subjected to a large G-force, the vehicle body generates a high degree of deceleration to absorb energy. Then, at the stage when G-force begins to be applied to the occupants, vehicle body deceleration is kept low to prevent an increase in the occupants’ G-force. Finally, a constant deceleration is generated to effectively prevent cabin deformation. This enables the cabin to be protected and survival zone to be secured while reducing occupant injury. Honda termed this collision-safe body that introduced this concept, together with the new airbag system and pedestrian injury mitigation body, Honda “G-Control” safety technology.
Honda believes there are no points where safety begins and ends. Always keeping ahead of the real world, Honda noticed that the rapid increase in the number of tall SUVs and minivans was causing more and more small cars to suffer serious damage. It could not remain in a fixed barrier forever. To get closer to the real world, Honda believed it was necessary to develop technologies for so-called compatibility (coexistence*1), based on the premise that cars of different sizes and weights collide with each other. Since the mid-1980s, Honda had been conducting crash tests between cars at the Japan Automobile Research Institute (JARI) and overseas facilities, but these were mainly for the purpose of verifying the accuracy of airbags. Honda began conducting car-to-car crash tests under the new compatibility concept, but JARI was inconvenient as it was the only testing facility in Japan at the time. Depending on how crowded the testing facility was, tests could not be conducted for several months, and Tsukuba, where JARI was located, was too far away from Honda’s development base to reflect test results promptly. Honda’s tradition was to “do it today, do it now” if something needed fixing.
Furthermore, only a limited number of developers would be able to see the actual crash if it were done at a distance. This went against Honda’s emphasis on its “Three Realities” Principle, to share the same work, hardware, and realities.
”We want all our engineers who develop Honda cars to see the reality of a crash happening in the real world.”
The development team appealed to upper management for the necessity of its own experimental facility, and after receiving approval, construction was hastily begun. In March 2000, the world’s first indoor omni-directional crash test facility, known as Building 67, was completed. The vast 40,000-square-meter crash test space, equivalent to the area of Tokyo Dome, did not have a single pillar to support the roof. This was done to ensure that the pillars would not restrict the experiments and to facilitate the reproduction of various types of collisions. Tests could be conducted indoors so as not be affected by weather conditions, and to create a comfortable environment for testing in both summer and winter. This was based on the Honda philosophy of “respect for people.”
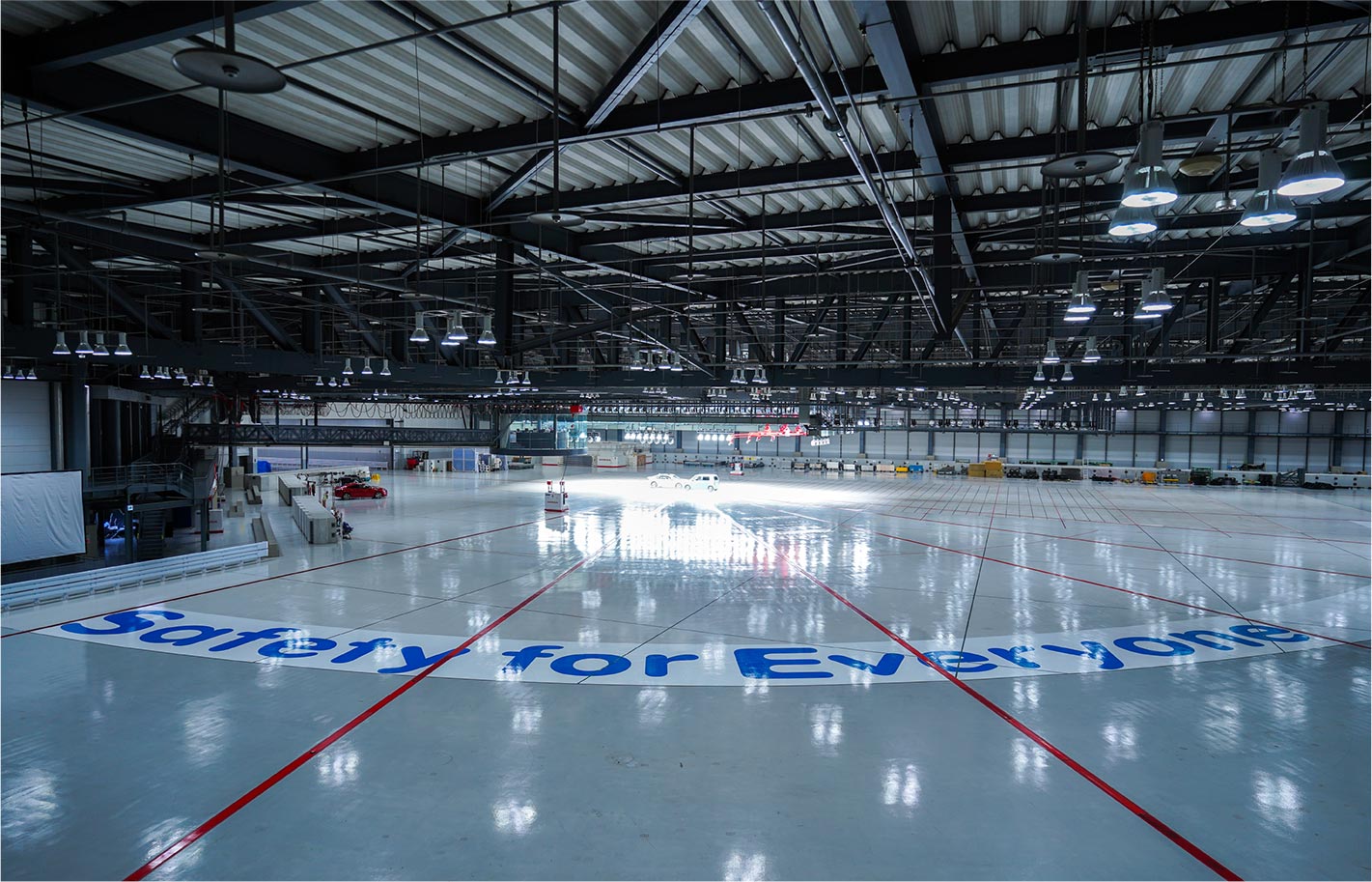
Indoor omni-directional collision test facility for real-world collision tests
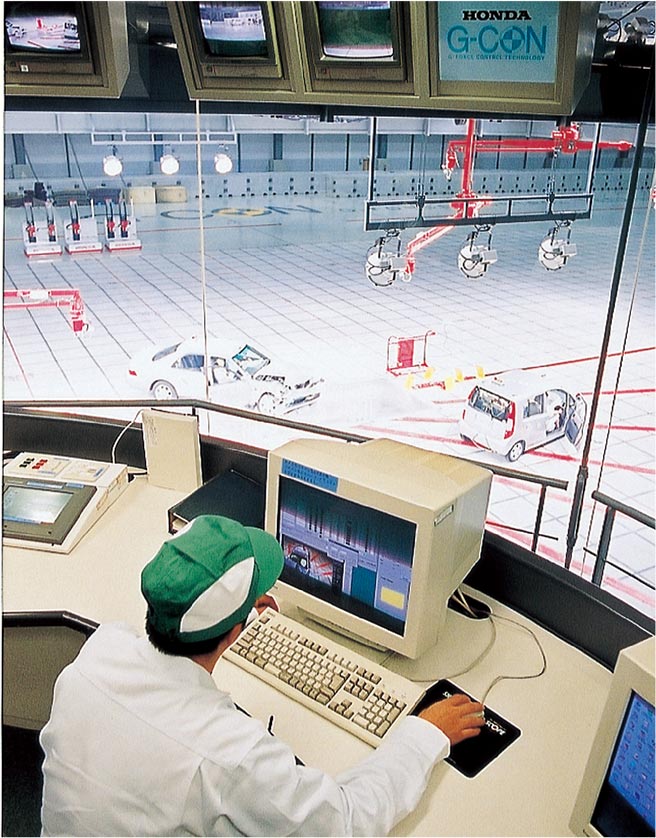
After the completion of Building 67, research begun by conducting collision tests between vehicles of different sizes, and it was found that the shock-absorbing structures of large and small vehicles were not in line with each other. Designed to align shock-absorbing areas of both types of vehicle and disperse impact to improve self-protection and reducing damage to other vehicles, Honda developed a new compatibility body design which was adopted for the first time in the Life mini-car launched in September 2003. The compatibility body, which was developed through crash tests, was an achievement of Building 67 and one of Honda’s answers to real-world safety.
- Aligning shock-absorbing areas of vehicle with differing weights and structures
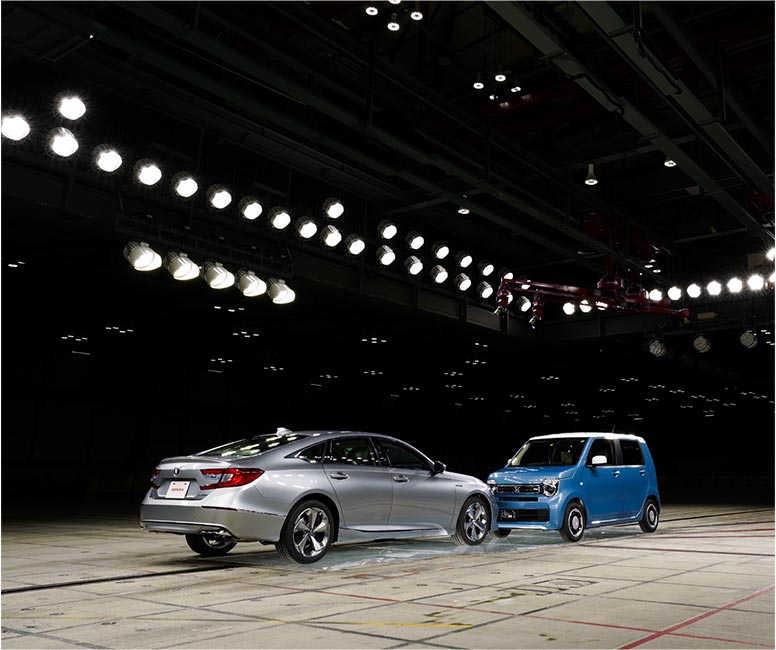
Collision test between large and small vehicles
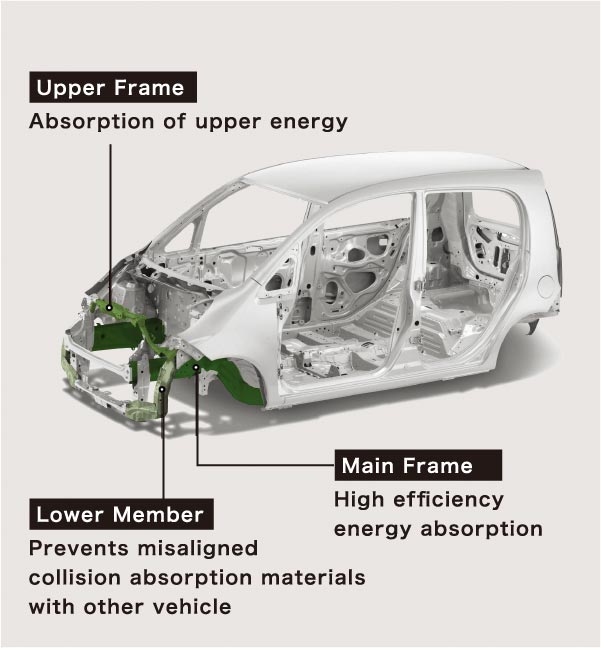
Life’s compatibility body
Toward a Collision-free Society
Honda began researching radar, including inter-vehicular distance control, more than 50 years ago in 1971. This research led to the development of a method of communicating warnings by the weight of the accelerator pedal rather than sound, a radar braking system that activates the brakes in an emergency, and Honda’s original Adaptive Cruise Control (ACC). In 1995, after 20 years of its first phase of the Advanced Safety Vehicle (ASV) development, Honda indicated its findings at an ASV announcement, and began research towards introducing Collision Mitigation Brake System (CBM), designed to help avoid rear-end collisions, which account for about 30% of traffic fatalities and injuries, and mitigate the damage they cause. In 2003, after researching ASV-2 since 1996, the world's first CMS was introduced alongside the E-pretensioner system, linked to the CMS to provide a sensory warning and occupant restraint, with the Inspire.
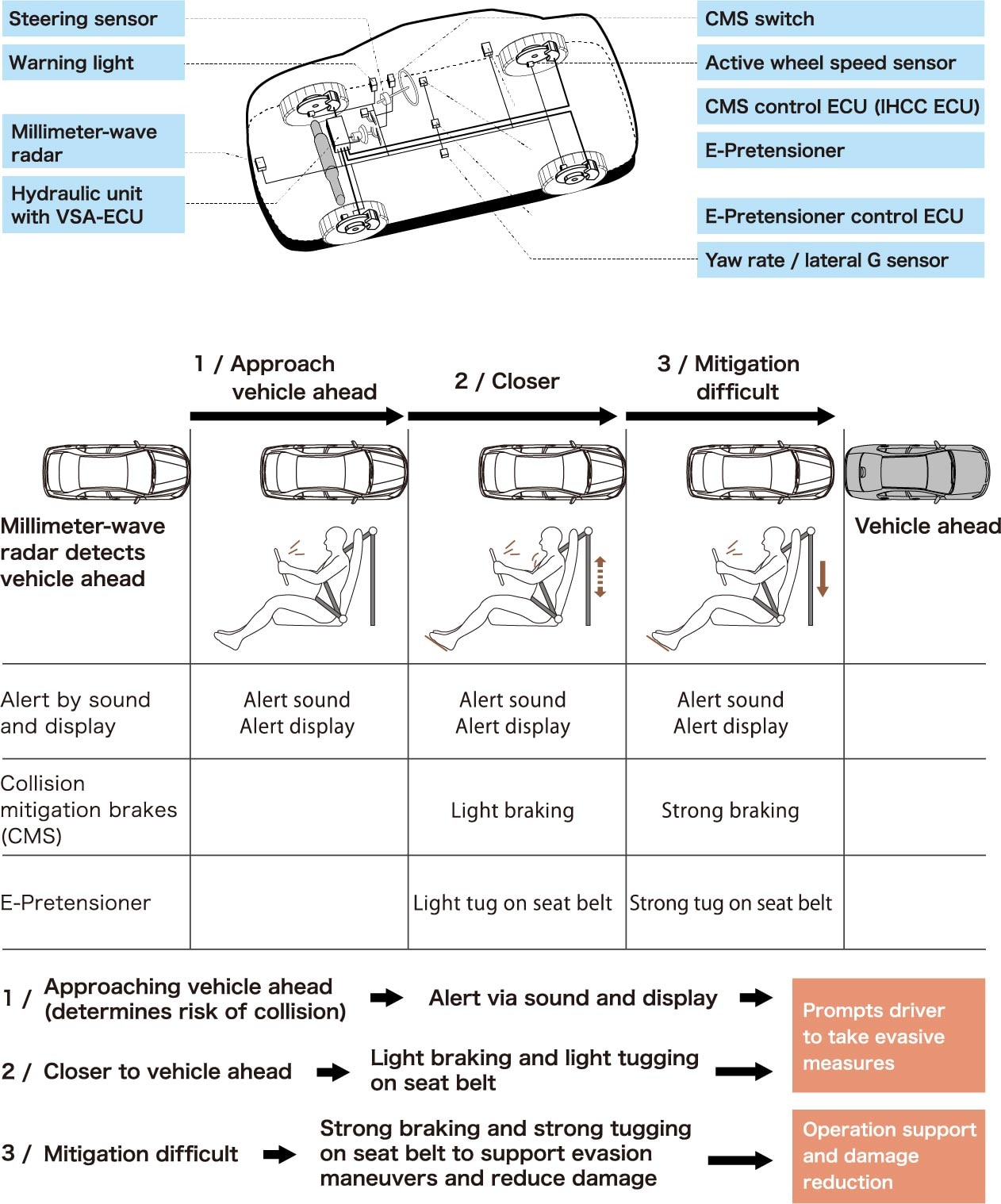
CMS+E-Pretensioner belt system and operation
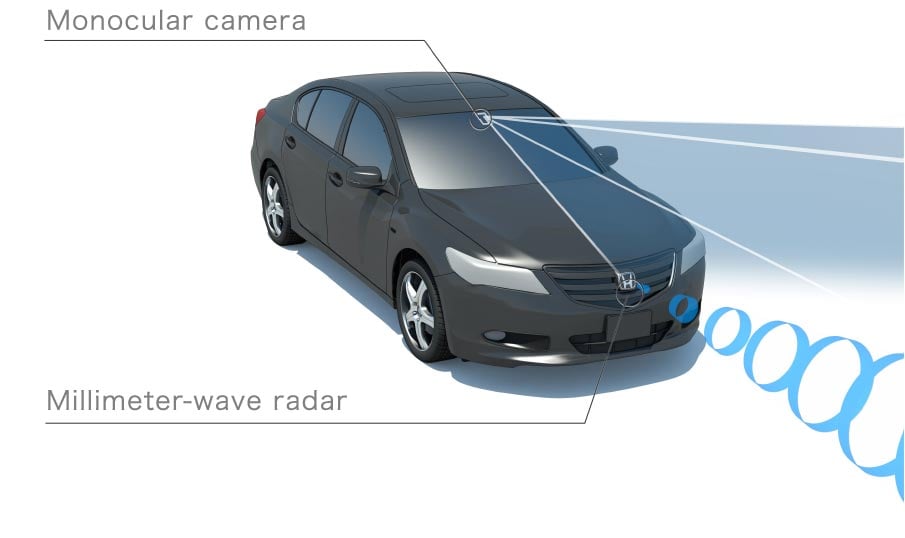
At the time, there was an atmosphere of uncertainty within Honda R&D as to whether the technology was truly valuable, but as soon as the Inspire was launched, it received coverage not only from automobile magazines but also from economic and scientific journals. As it became clear that other companies were following suit, Honda R&D realized that the technology was so advanced, its value was difficult to grasp even within the company.
Although CMS allowed Honda to demonstrate its response to rear-end collisions, it was yet unable to provide a realistic solution to intersection accidents, which had a similar probability to occur, and head-on collisions, which had a high rate of serious injury.
Aiming to support accident avoidance, Honda continued to develop safety technologies. By 2004, it had developed the world’s first intelligent night vision system to help drivers spot pedestrians in front of them at night, and continued to evolve Lane Keep and Lane Departure Warning System (LVDS), and Adaptive Cruise Control with Low Speed Follow, which was already in development with ASV-2.
In October 2014, Honda introduced Honda SENSING, an advanced safety driving assist system that supports safe and comfortable driving and accident avoidance by using millimeter-wave radar and a monocular camera to recognize conditions ahead of the vehicle, coordinating braking and steering control. In Japan, the application of this technology was gradually expanded starting with the Odyssey launched in 2015.
Since then, Honda continued to evolve Honda SENSING, and anticipating automated driving in the future, launched the Legend equipped with Honda SENSING Elite, achieving Level 3 automated driving, in 2021. Traffic Jam Pilot enables the driver to operate the navigation system, such as watching TV or DVD on the navigation screen and searching for destinations, while the vehicle drives hands-off in traffic jams, reducing driver fatigue and stress*2.
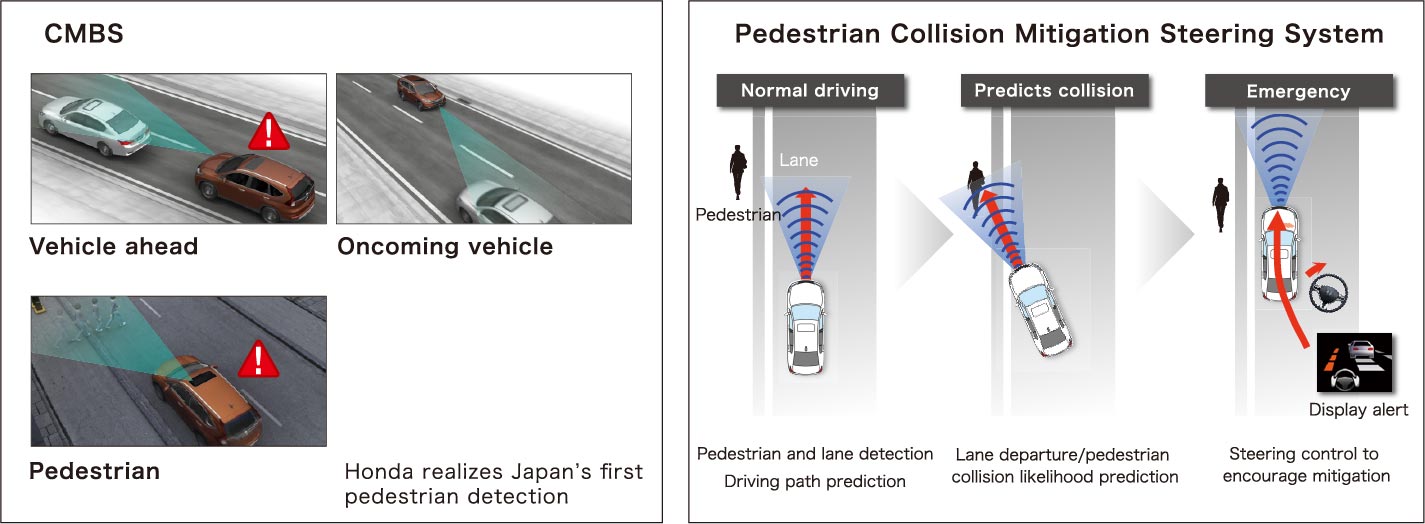
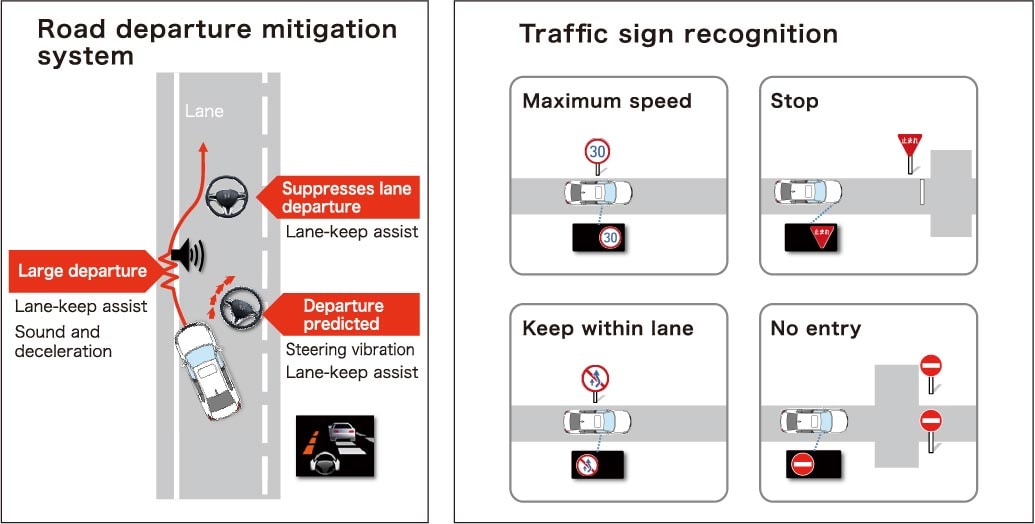
Honda SENSING
major features: CMBS,
Pedestrian Collision
Mitigation Steering System,
Road Departure Mitigation
System, Traffic Sign
Recognition System
In November of the same year, Honda unveiled to the world the advanced safety technologies it was developing to realize a society in which all traffic participants are free from the risk of traffic accidents, and can move freely with peace of mind. Through the world’s first intelligent driving support technology using artificial intelligence (Al) that can reduce driving errors and risks and guide drivers to safe and secure driving according to the abilities and conditions of each individual, and safety and security network technology supports the prediction and avoidance of risks before an accident occurs by connecting all traffic participants (people and mobility) via communications, will contribute to Honda’s announced goal of achieving “zero traffic collision fatalities” involving Honda motorcycles and automobiles worldwide by 2050.
Honda aims to realize a society without accidents. To this end, Honda aims to deploy Honda SENSING 360, an omni-directional safe driving support system that covers blind spots around the vehicle to help drivers avoid traffic accidents and reduce their driving burden, with motorcycle detection and other advanced driving support systems aimed at safety and security, to all of its automobiles worldwide by 2030. Honda will continue the challenge of evolving ADAS (Advanced Driver Assistance System) functions to provide safety and peace of mind.
In addition, Honda will continue to expand its motorcycle safety technologies, strengthen its safe driving promotion activities, which it has been involved in since 1970, and develop Honda Safety EdTech, an online traffic safety education system, aiming to halve the number of traffic accident fatalities involving Honda motorcycles and automobiles worldwide by 2030, and achieve zero traffic accident fatalities by 2050 through early establishment of future safety technologies. Honda will continue to work relentlessly to realize its fundamental safety philosophy of “Safety for Everyone.”
- Conditional automated driving (limited area). “Automated driving” as defined by the Japanese government (in accordance with SAE). Under certain conditions, the system monitors surrounding traffic conditions and takes over driving operations. If the system deviates from the operable conditions, it is required to issue an alarm and immediately allow the driver to take over.
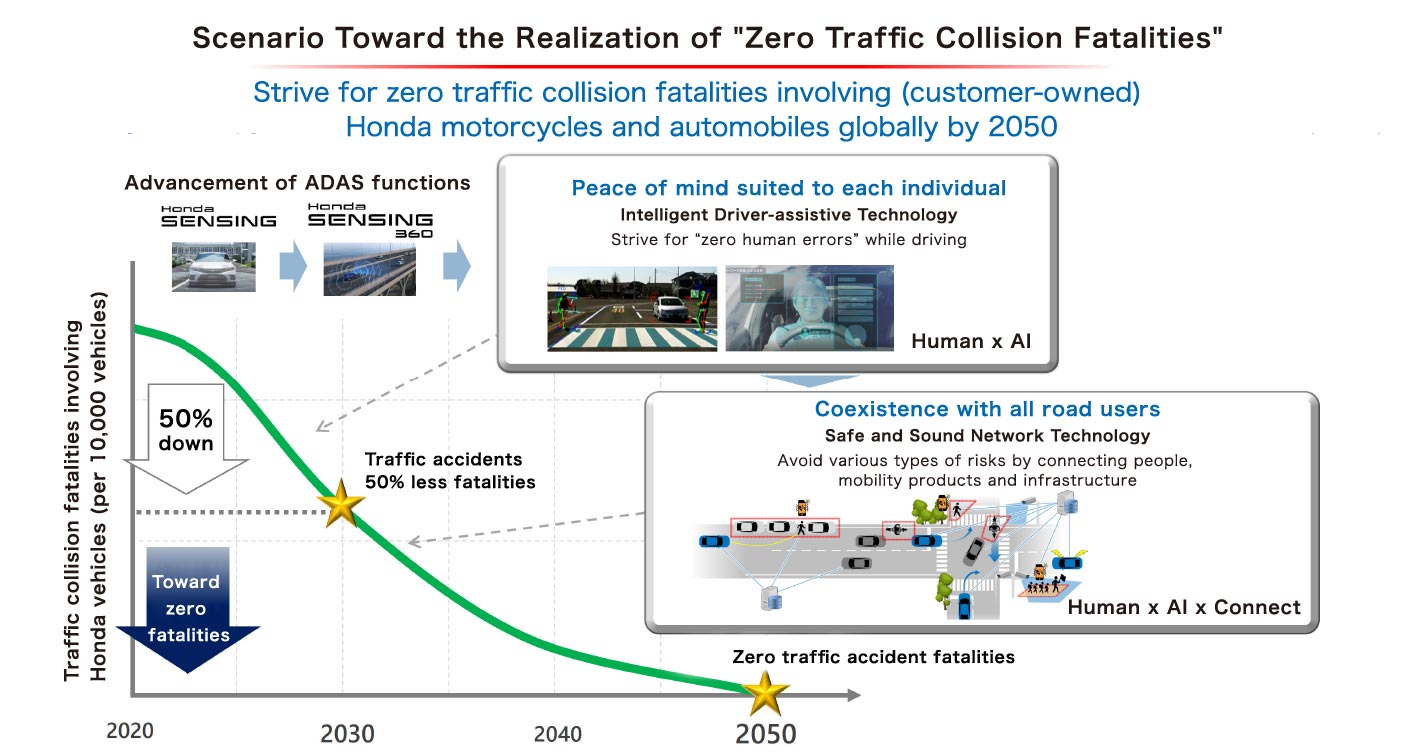
Scenario Toward the Realization of "Zero Traffic Collision Fatalities"
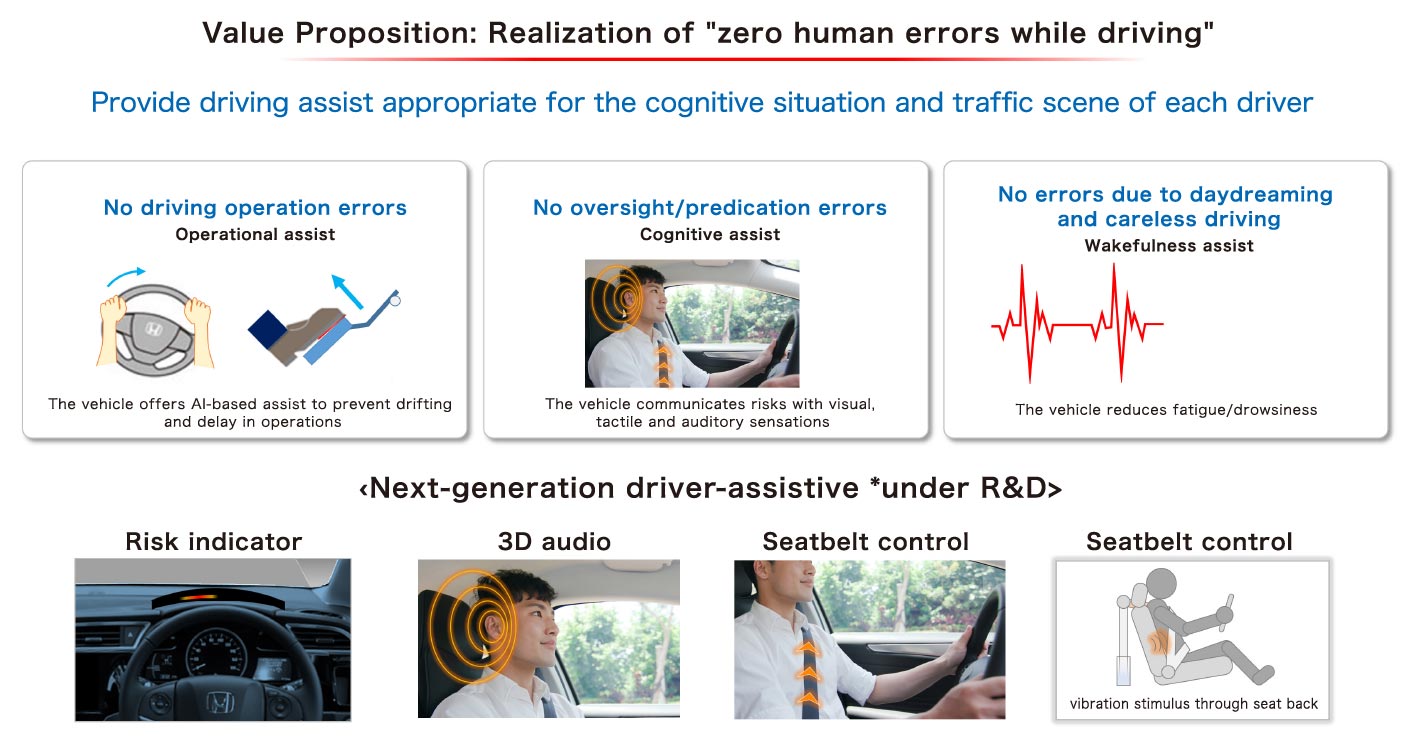
Intelligent Driver-assistive Technology : Value Proposition
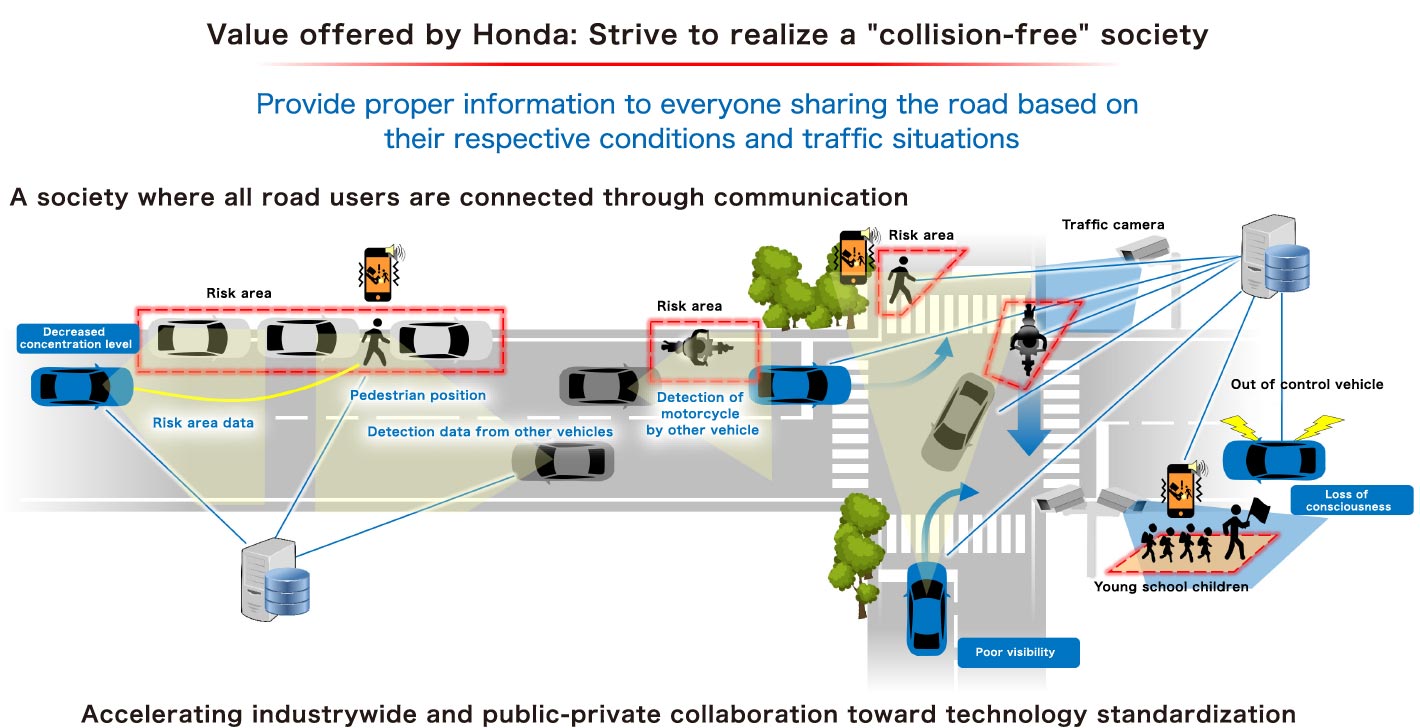
Safe and Sound Network Technology