The Goal Was Set to Create the World’s Best EV
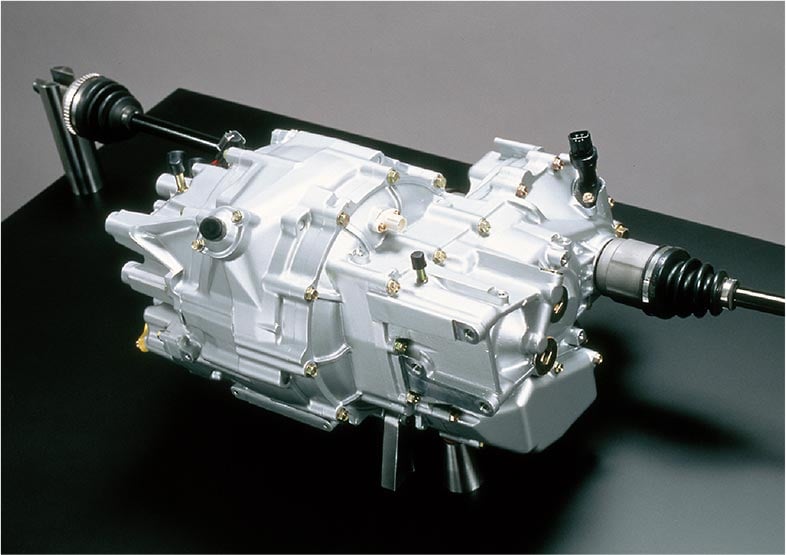
During the fundamental research phase of the project, one-by-one, the team mastered the essential technologies necessary to build an EV [Appendix 1].
There still was some time before the Zero-Emissions Vehicle (ZEV) Program would take effect in 1998, so Honda continued its pursuit of an original EV that would stand out from EVs of other automakers which were already in the EV market.
The team decided to independently develop and produce the motor and control unit, and chose to adopt a brushless DC motor, which was an unusual choice for large motors at the time. Shigeru Suzuki explained: “The results of our simulations suggested that this [brushless DC motor] would be the most efficient motor for EVs, so we concentrated our efforts on it and thoroughly increased its efficiency.”
Most EV manufacturers at the time were using standard induction motors; however it was essential to adopt a motor with the highest efficiency to realize an EV with higher performance.
Moreover, as the EV motor and control unit were equivalent to the engine of gasoline-powered vehicles, Honda definitely wanted to develop and establish its own original technologies, foreseeing the future when such technologies become the core technologies of Honda.
The first brushless DC motor the team created performed well beyond their expectations, and this motor was later perfected as a high-performance EV motor after several years of trial and error.
With the motor technology finally in hand, the team had mastered virtually all essential technologies to build an EV and, thus, in June 1992, the project moved on to the development of a production model.
Top management directed the team to “create the world’s best EV” by pursuing two characteristic features for this completely new mobility product – it had to express a clean, quiet, and smooth ride at the level beyond what existing cars could offer, and it had to be innovative.
Real-World Test Driving Totaled 130,000 km (80,000 miles)
By the start of the development of the production model, the project team had mastered virtually all essential EV technologies, however the only test vehicle the team had at this time was the Civic Shuttle converted into an EV with the range of only about 40 to 50 km (25 to 31 miles).
In addition, the team didn’t have any clear prospect for equipping the vehicle with enhanced collision safety technologies that would address the vehicle weight increase due to the addition of battery weight. In other words, the team still needed to conduct a lot more intensive research to put its EV into practical use.
As the first step, for the purpose of further refining the concept of the EV Honda was striving to create, the team decided to build a new prototype called the EX-V and exhibit it at the 1993 Tokyo Motor Show.
At the same time, in order to obtain usage data in the real-world environment, Honda decided to contract with a power company in California to jointly conduct road testing of its EVs for two years, starting in 1994.
Kenji Matsumoto, then the project leader of development of the production model, explained Honda’s thoughts behind this testing in the U.S.: “Honda had a strong presence in the U.S. And in terms of market share by state, Honda ranked first in California. If people there are being affected by environmental issues, we felt that Honda should be there to contribute.”
Based on this belief, Honda identified California as the main market for its new EV, and thus conducted the testing there.
The CUV-4 test vehicle was built by converting the Civic. For use in long-term road testing, it was important to take all possible measures to ensure electrical safety.
A number of safety concerns the team needed to address included: how to address possible electrical leakage in the event of a collision; how to deal with floods; how to ensure safety in case the abnormal generation, ignition and explosion of hydrogen occurs with the vehicle’s NiMH battery due to a malfunction or defect of the charging parts on the EV. These issues were resolved one-by-one by confirming the effectiveness of the relevant safety measures in environments replicating possible problematic situations identified by the team, such as when the battery box was immersed in salt water, or deliberately being ignited and exploded. After installing sufficient safety features, the EV was ready in its basic form.
Matsumoto explained: “After making changes to some of the hardware settings and complying with all applicable laws and regulations in Japan and the U.S., we took the EV out for road testing.”[Appendix 2]
Despite such rigorous preparation, the road tests revealed another unexpected problem:
Unlike the result of simulation-based testing, the lead-acid battery on the vehicle rapidly deteriorated when the vehicle was left undriven for a week or two in the summer heat. This finding suggested that it would be necessary to switch from a lead-acid battery to a nickel-metal hydride (NiMH) battery, which is less susceptible to changes in ambient air temperature and the operating environment. Fortunately, there was no need to panic because Honda had already started working with a battery manufacturer to develop a new NiMH battery.
During this 2-year real-world testing in the U.S., a total of 10 units of Honda EVs, including the test vehicles provided by both Honda Research of America (HRA) (later Honda R&D North America
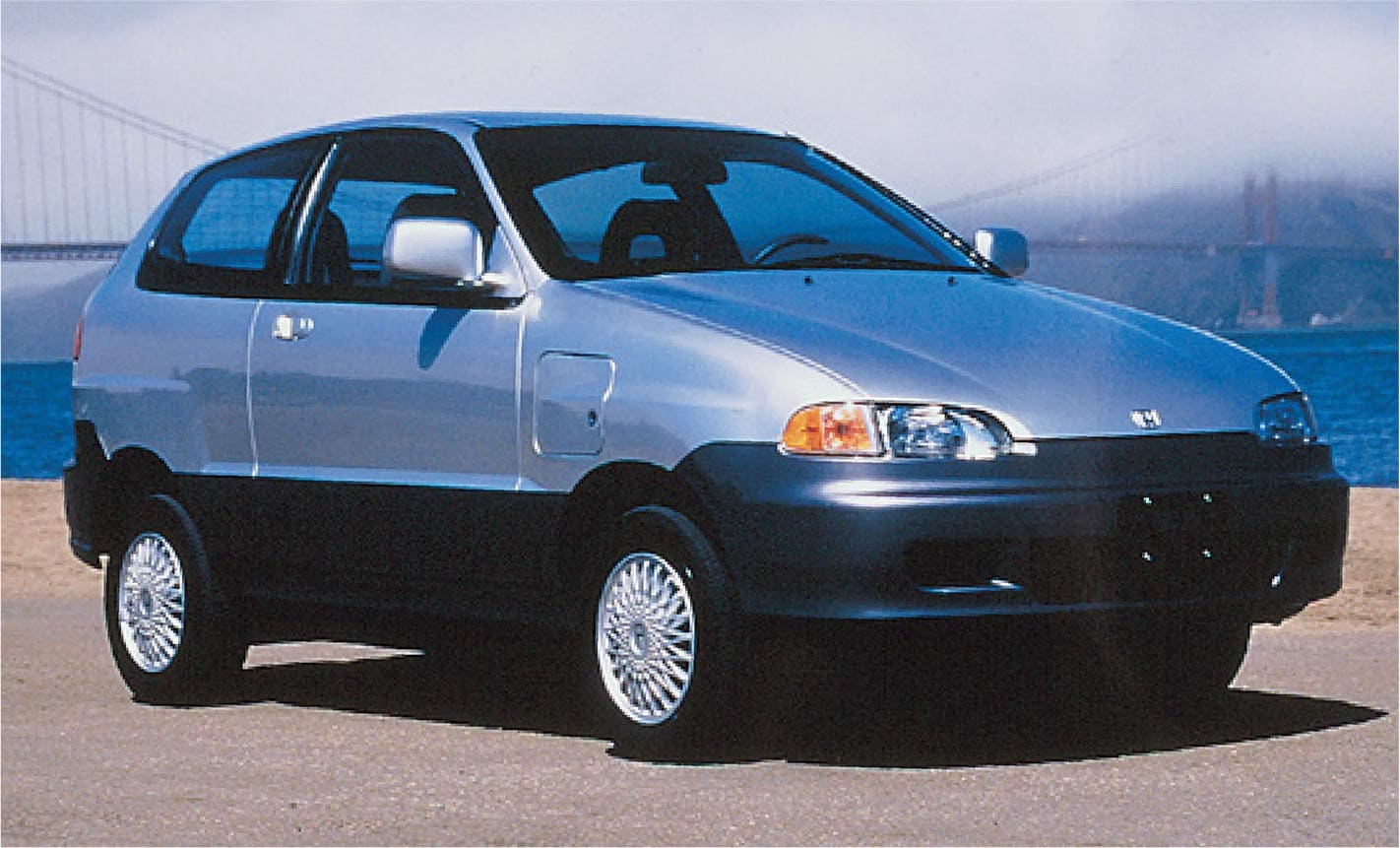
CUV-4, a real-world test vehicle with a total driving distance of 80,000 miles (130,000 km)
Foundations of Honda’s Electrification Technology
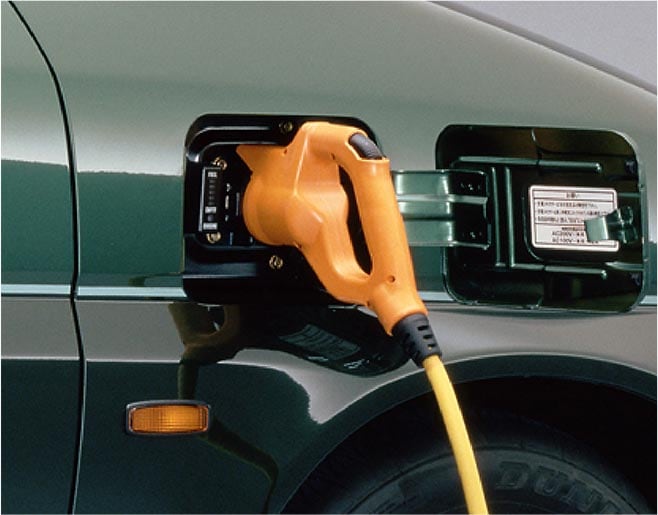
The first prototype of a production EV was completed in December 1995.
Matsumoto recalled: “We struggled to create a body design that would convey the unique nature of an EV. That said, we only considered introducing our EV to market with an exclusive body, not a modification of an existing model. That was not only because we had such a strong emotional attachment to the vehicle, but also we knew that if we even mention modifying an existing vehicle, top management would get upset and tell us, ‘What are you, insane?’”
Creating an exclusive body design would tend to be costly, and the EV development at that time was predicated on small-volume production. However, the product development division and the production engineering division worked as one to assess and mature product quality as early as possible, then adopted permanent dies*6 for major components even from the first production lots of this prototype vehicle.
The first prototype of the production model was produced by leveraging the collective strengths of Honda, including Honda Engineering, which manufactured the motor, and the Takanezawa Plant of Tochigi Factory, which produced the body and later was put in charge of mass production of this model.
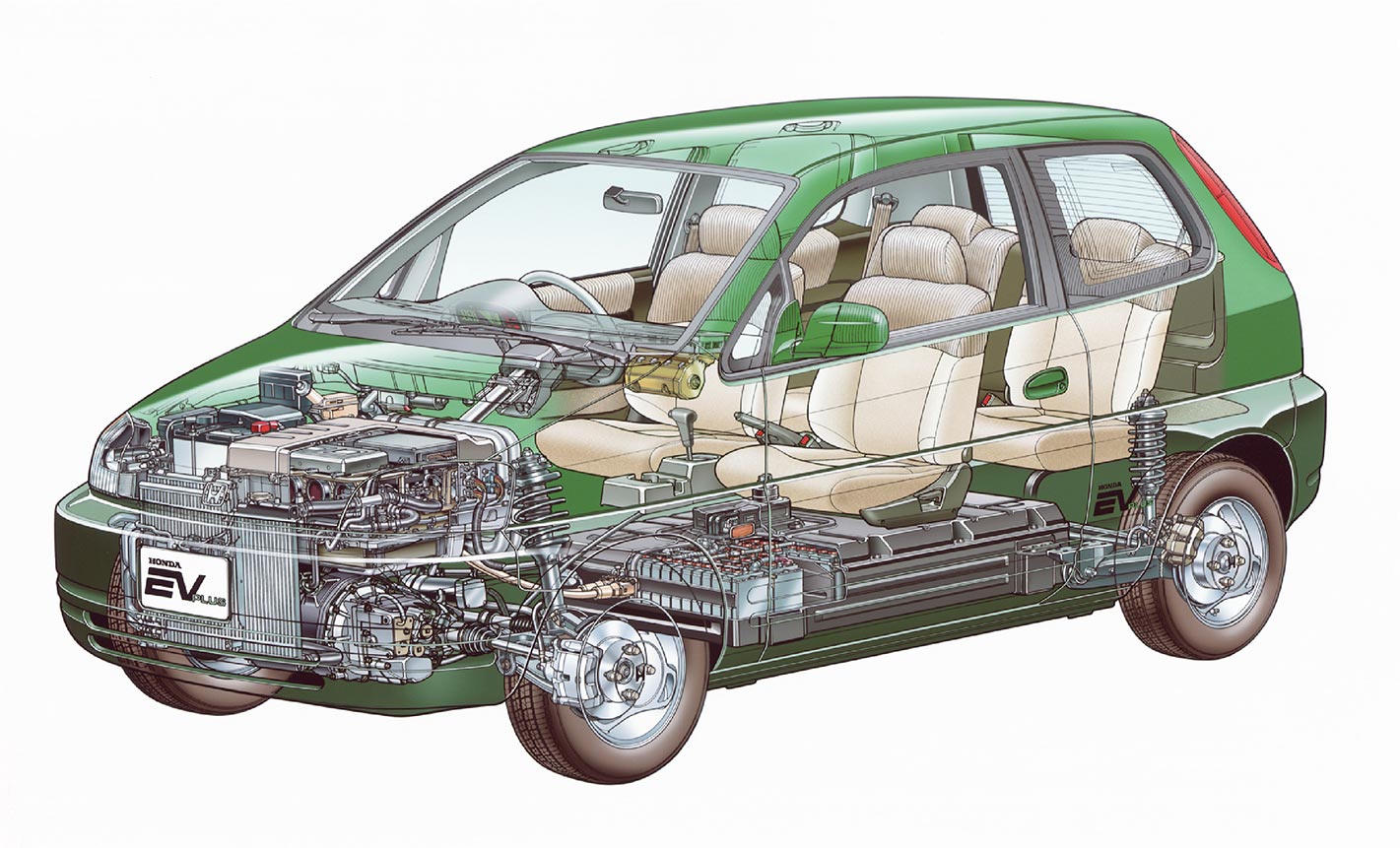
Perspective view of HONDA EV Plus
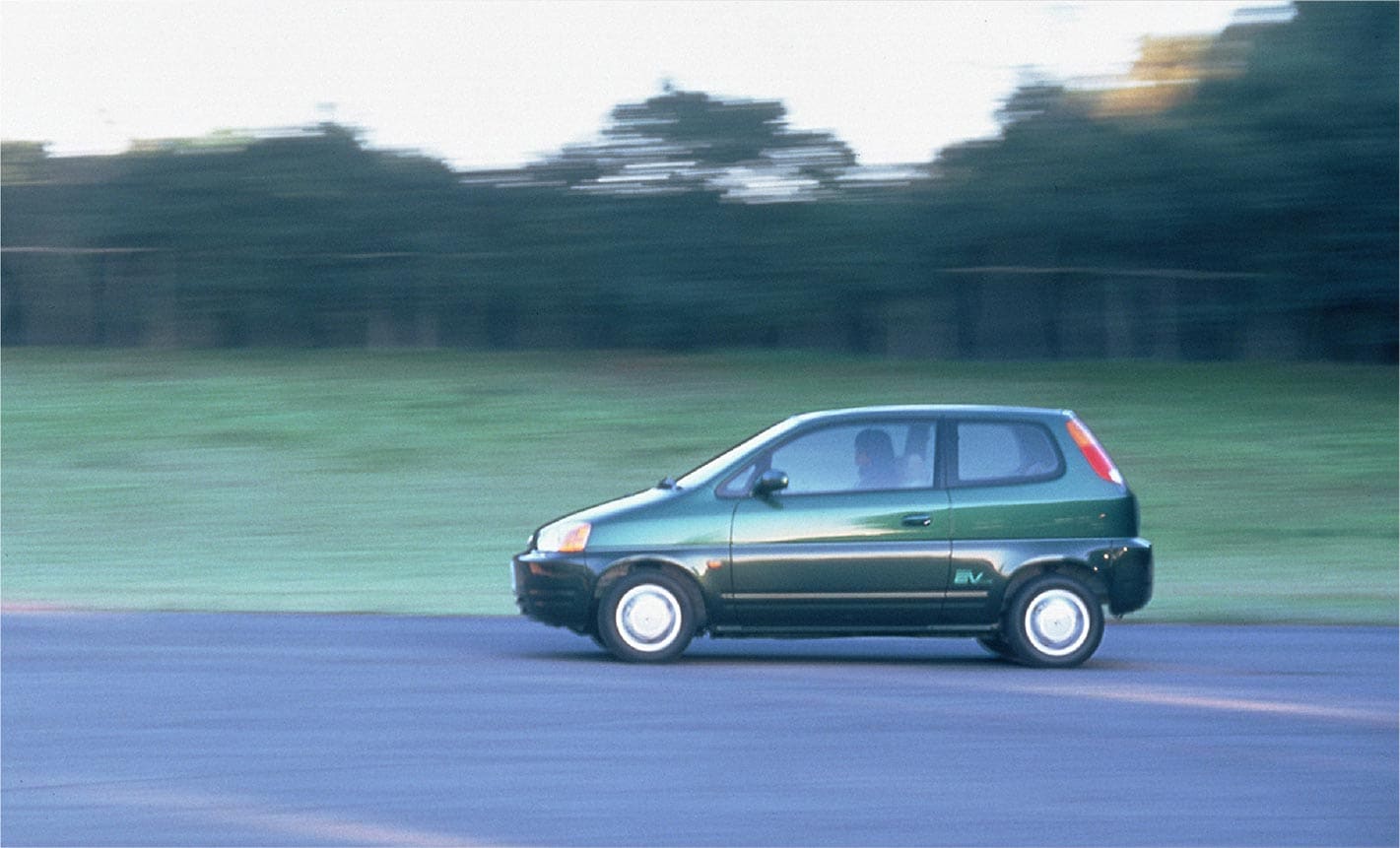
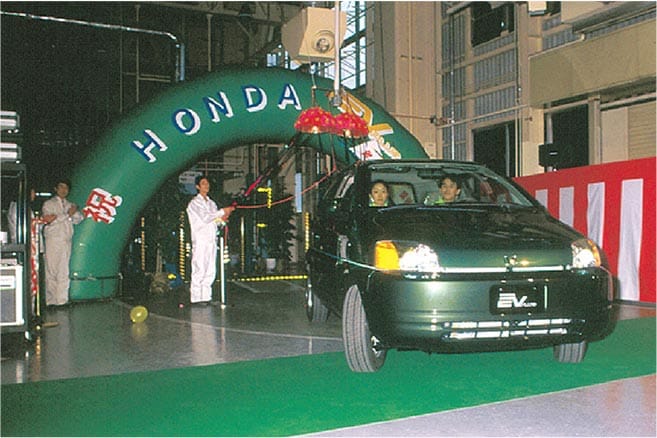
In January 1996, Nobuhiko Kawamoto, then the President of Honda, test-drove the newly produced prototype and made an immediate decision: “It’s a go. Let’s do it!”
Following a green light from Kawamoto, Hiroyuki Yoshino, then the Vice President of Honda, gave the instruction to the team: “Once it’s ready, make a technology announcement immediately. And do it simultaneously in both Japan and the U.S.”
The prototype had just been produced. Although it demonstrated sufficient driving performance on a test course, there was still some uncertainty as to whether the production model would be perfected as the team intended.
The development team members immediately and desperately ironed out the final details. In April 1996, simultaneously in Japan and the U.S., Honda held a technology briefing on the Honda EV Plus, a full-fledged and practical EV that fully incorporated both Honda’s passenger vehicle technologies and cutting-edge EV technologies.
A year later, in April 1997, after extensive technology verifications through a number of public road tests and internal and external product monitoring, Honda held a line-off ceremony to commemorate the production of the first unit of Honda EV Plus.
When the first unit of EV Plus driven by a Honda associate passed in front of the audience attending the ceremony, it was showered with flashes from a number of press cameras, marking the moment when the foundation was laid for Honda’s continued pursuit of electrification technologies.
The development leader Kenji Matsumoto, who successfully completed the mission to deliver Honda’s first EV product to customers, quickly shifted his thoughts toward the further advancement of EV technologies: “We still have a lot of work to do, including the improvement of battery performance. Yet, on the other hand, there are more and more people who are willing to do what they can to contribute to environmental protection efforts, such as installing solar panels on the roofs of their homes regardless of the expense. Schools are also being proactive in educating their students about environmental issues. So, when these children reach the age to start buying cars, in five to ten years, all cars must come with environmental and safety features as standard equipment. I can definitely sense that the era of electric vehicles is well on its way.”
In 1999, two years after the launch of the EV Plus, Honda launched its first hybrid car, the Insight. Then, in 2002, Honda began lease sales of the Honda FCX fuel cell vehicle by making the first customer deliveries to the Japanese government’s Cabinet Office and to the City of Los Angeles in the U.S. on the same day. “The FCX also was the world’s first fuel cell vehicle to obtain U.S. government approval for commercialization.”
The foresight Matsumoto had more than 20 years ago had become a reality. It all started with the first, four-member EV project team which began laying the foundation of Honda electrification technologies.
Matsumoto had an unforgettable experience as the development leader of the EV Plus. In the course of conducting survey interviews with prospective customers in the U.S., which took place in parallel with the road testing, he met so many American consumers who expressed deep understanding toward environmental conservation.
“I can’t tell you how much courage it gave me and my team to know there are people out there who would relate to and support environmental initiatives Honda was taking through the development of the EV. Even now, I remember the words we were told in the U.S.: ‘This car is right for me. I’m doing the right thing.’”
- Dies/molds on which permanent treatment is applied. Such dies/molds are usually introduced during mass production to correct defects and other issues in parts production.
[Appendix 1] Essential technologies needed for EVs
- (1) New technologies and systems required to change the power source of the vehicle
- Drive motor
- EV Battery (rechargeable battery)
- Motor controller
- Air conditioning system
- Electric power steering system
- 12V battery charge
- Brake system
- Regenerative control system
- Total control system
- (2) Performance needed for regulatory compliance
- Collision safety performance (accommodating the vehicle weight increase)
- Defroster performance
- (3) Additional EV-exclusive technologies
- Charging system
- Electrical safety system
- Heating system
- Radio wave (electromagnetic wave) interference management
[Appendix 2] Examples of modifications made to hardware specifications
- (1) Total voltage changed from 240V to 288V
- (2) Motor output changed from 40kW to 49kW
- (3) Transmission changed from the torque-converterless 3-speed automatic
transmission to the first gear fixed ratio reduction transmission (fixed-ratio gearbox). - (4) Battery changed from lead-acid battery to nickel-metal hydride (NiMH) battery.
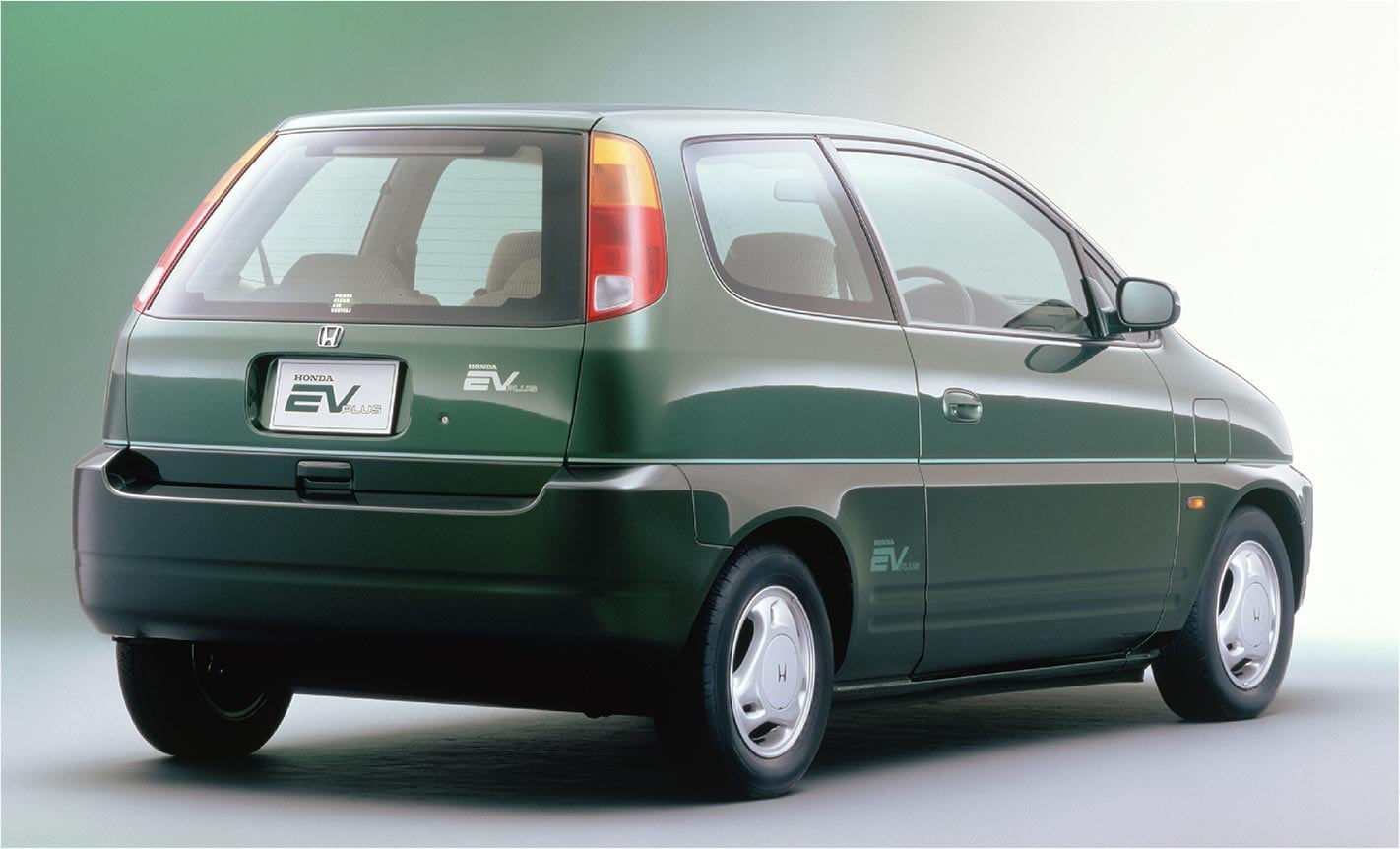
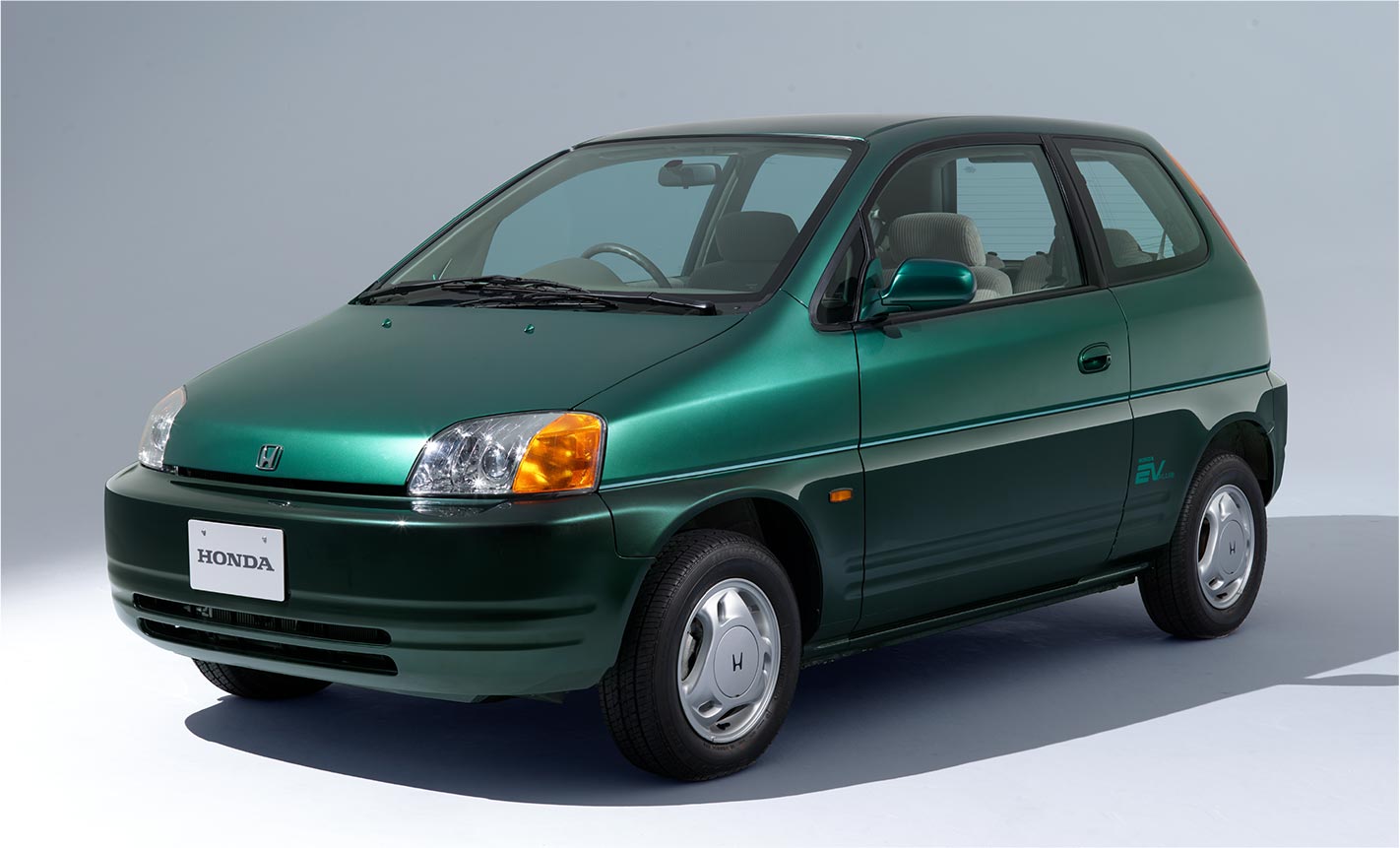