Cub Stories
What does it mean to ‘make things you can hold in your hand’?
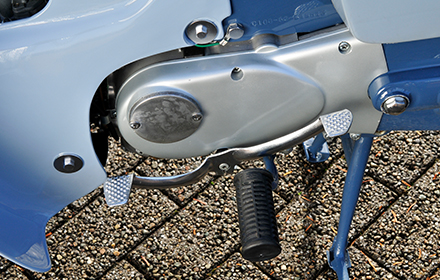
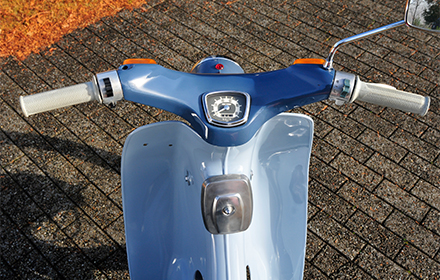
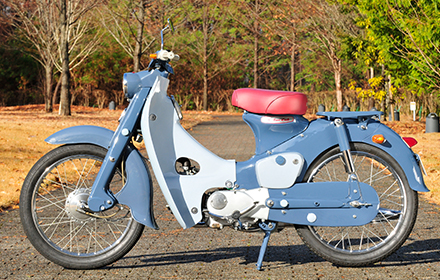
Three experimental bikes were made to test out eight clutch prototypes, leading to the finalization of the automatic centrifugal clutch that became one of the hallmarks of the Super Cub, and one of its biggest features. Its easy operation freed up the left hand, making it revolutionary among motorcycles while also bringing management and rank-and-file employees closer together. Immersing themselves in the problems at hand, gathering together individual ideas while promoting a shared consciousness, and moving forward selection of the best proposals by sifting out the bad and keeping the good. This was the corporate culture of the young Honda Motor Company only 10 years after its establishment, and it is no exaggeration that this style of doing business underlies what Honda is today.
As the project progressed through engine, transmission and chassis design, body design began in April.
Kimura — “The Old Man always said, ‘Create things you can hold in your hand.’ At first, I couldn’t quite grasp the correct meaning of these words, thinking this was probably some local saying from around Shizuoka, which was where he grew up. I asked Kawashima (Kiyoshi Kawashima, later to become Honda’s second president) in the Engine Design department to tell me what it meant, since I knew he was from the same Hamamatsu area as the Old Man. He told me, ‘It means that we should make small things that can be held in your hands or body.’ In other words, we should make a compact bike that anybody can operate with ease.”
In giving form to the design, something Soichiro Honda was really concerned with was the size of the tires. What was the appropriate tire size that could most effectively give motion to the new engine so that it could provide stable power at even low speeds? The chassis would be determined by tire size, which would subsequently lead to the most important “thing that can fit in your hand” size and proportions made to fit the average Japanese rider./p>
Kimura — “The tire team was doing research on smaller-diameter wheels, and they found that the ideal outer tire diameter was 21 inches (533mm). Although many mopeds in Europe were between 24 and 26 inches (610 – 660mm), which was similar to the outer diameter of bicycle tires, they said that if you took into consideration the size of the average Japanese user, the most appropriate size that could ensure easy mounting and dismounting, and provide good footing and excellent riding performance would be 21 inches. Therefore, we focused on a smaller tire that was 2.25 inches in thickness mounted on a 17-inch diameter rim. In the case of this 2.25–17 tire, I thought the outer diameter would be a bit over 54.5 centimeters.
“By that point in time, a wooden model of the engine had arrived, and since its transmission and centrifugal clutch were integrated into the whole, it was quite large at about 450mm long and 124mm wide. Drawing up two 2.25–17 tires and positioning them for a wheelbase of about 1,200mm, I drew in a large straddling space with the engine placed low and horizontally, and it all fit neatly together with very little waste. After that, I figured the approximate position of the handlebars, and when I sketched them in on the drawing, the resulting shape closely resembled the Super Cub. In other words, the size of the tires gave birth to the Super Cub’s style.”
However, no 2.25-17 inch tires were being produced in Japan at the time, and since no product like that existed, no life-sized tires could be found to use on the mockup. In this situation it was impossible to visualize the complete structure. The design staff took great pains to find a solution, going so far as to cut a section out of a pair of existing 18-inch tires and sewing the ends together to achieve the desired dimensions, reducing their inner diameters to 17 inches. It was the tires then that became critical for making the mockup, as well as for future mass production.
What doesn’t exist, doesn’t exist. The birth pains of development
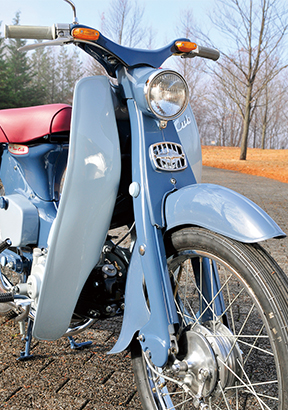
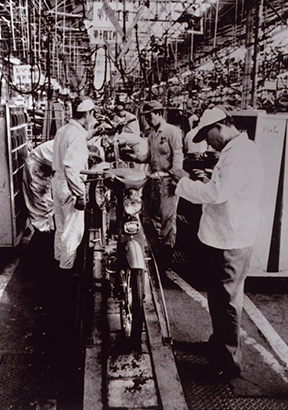
Although initially produced at the Yamato Plant in Saitama Pref. (photo), the Suzuka Factory was soon built to cope with booming demand.
Chassis designer Yoshiro Harada — “Even big manufacturers don’t create new standards for just one model of bike. After a string of refusals, we were at a complete loss about what to do. Then at last a small tire maker showed up and told us they could take on the job.”
From its earliest stages of trial production, Honda has always stuck to ‘realist principles.’ Even for tires, they usually employ a technique of applying the same size and shape of tire as is already being used on an existing bike.
No design study drawings were used in the Super Cub’s design development. Instead of winnowing down its design from a heap of design ideas and drawings strewn across a desk, Soichiro and his staff would dive right in, applying their thoughts and actions to building a prototype from an image that had seemingly taken root among them.
Kimura — “It was the Old Man’s belief that to get to the truth of the matter we had to build a clay model of the same size and scale as the real bike. That is to say, by using things that closely resembled the real product. With a clay model, investigations could instantly be made in three and four dimensions, eliminating the necessity of making calculations or doing trial production runs. Moreover, everybody involved could understand what they were seeing on the spot. In reality, I didn’t understand motorcycles very well when I started working on the clay model for the Super Cub. The Old Man came and started hacking away on the front fairing to narrow its width, saying, “The wind comes in like this and moves over it like that.” However, soon after he got started, the metallic net making up the core of the model became exposed and cut his finger, “Ouch!” Since he was still hard at work cutting down the model in spite of his injury, I ran to the clinic to get a band-aid for him.”
"Always bet on new product ideas and confront challenging problems. The job may be a struggle, but any pain is short-lived compared to the potential for success." Episodes like this were infused with the passion of the founder, who wanted to give life to his own dreams while lifting up his employees. The staff who followed his lead often faced great difficulties, but they must have also felt that they were responding to accelerating new dimensions in design. Soichiro was often heard to say that design is the key to creating industrial products that can give each consumer the greatest satisfaction.
Kimura — “Take the front fork design as an example. Many years earlier I saw a scene in the Disney movie ‘Bambi’ in which Bambi was running at full speed, then stretched out his forelegs to quickly stop and stand firm. That short scene stuck in my mind, and I used that image in creating the shape of the Super Cub’s front fork.
“One more thing that I can point to with pride is the wing-shaped pressed steel handlebars. This was an original Honda design that no other makers had. To tell the truth, while the Super Cub was still in its development stages, I was also working with the Benly development project and had already designed the Benly’s pressed steel handlebars. Therefore, although the Super Cub’s handlebars were first made of conventional steel tube, I strongly insisted on using the pressed steel handlebars, and won the approval of everyone concerned by showing how well it worked on the Benly.”
While the gist of the design was thus being established, another part worthy of special mention—and one of the Super Cub’s most distinctive and eye-catching features—is the use of totally new polyethylene resin in the creation of its front fender and leg shields. This new material also made the bodywork remarkably light compared to FRP (fiber-reinforced plastic). Additionally, polyethylene’s more pliable properties made it almost unbreakable, while giving the body parts a remarkably warm texture.
Kimura — “Since the plastic parts had a softer quality, I changed the colors to create a combination that exuded both softness and brightness. I called these the colors of the sea and the sky, as they’re colors that are familiar to and popular with most Japanese. Since the Super Cub was designed to be a vehicle for the masses, I wanted to use familiar colors rather than fancy shades. As an accent, we made the seat a reddish purple color. In those days, the Old Man used to wear a red shirt and drive a red sports car, which gave me a hint. Then I recalled a scene I saw in the movie ‘Summertime’ starring Katharine Hepburn, in which a piece of Italian Venetian glass glistens with a purplish deep red hue in the light. This made me think that if the seat were a slightly bluish red, then it would perfectly complement the blue of the body.”
As for the polyethylene used to make the body parts, the specialty makers of the time had never processed such large molded parts. So in order to get Honda to outsource the production of the parts to them, they agreed to the condition that Honda would provide the molds. Could this have been because not only Honda itself but also the subcontractors were eager to create an innovative new motorcycle that the world had never seen before?
Kimura — “Even if we made somewhat unreasonable requests, they always accepted without the slightest look of annoyance. If I said, ‘Please take care of this,’ they’d just reply ‘Okay, no problem.’ Everybody cooperated with each other in this way. The Old Man used to say, ‘Everybody’s got to think carefully.’ The Super Cub was truly a bike developed as a result of ‘everybody’ working together.
“Although the R&D team tried everything they could until the Super Cub was safely delivered to the customers, the production and sales teams and outside contractors who made the pressed steel parts, resin parts and seats understood our feelings and made extraordinary efforts together. I’m convinced that good products can never be made by the research and development alone.”