Hondaの研究開発施設 第5回
Hondaの研究開発施設 第5回
2024.11.25
モビリティの核はここで鍛える「台上試験施設」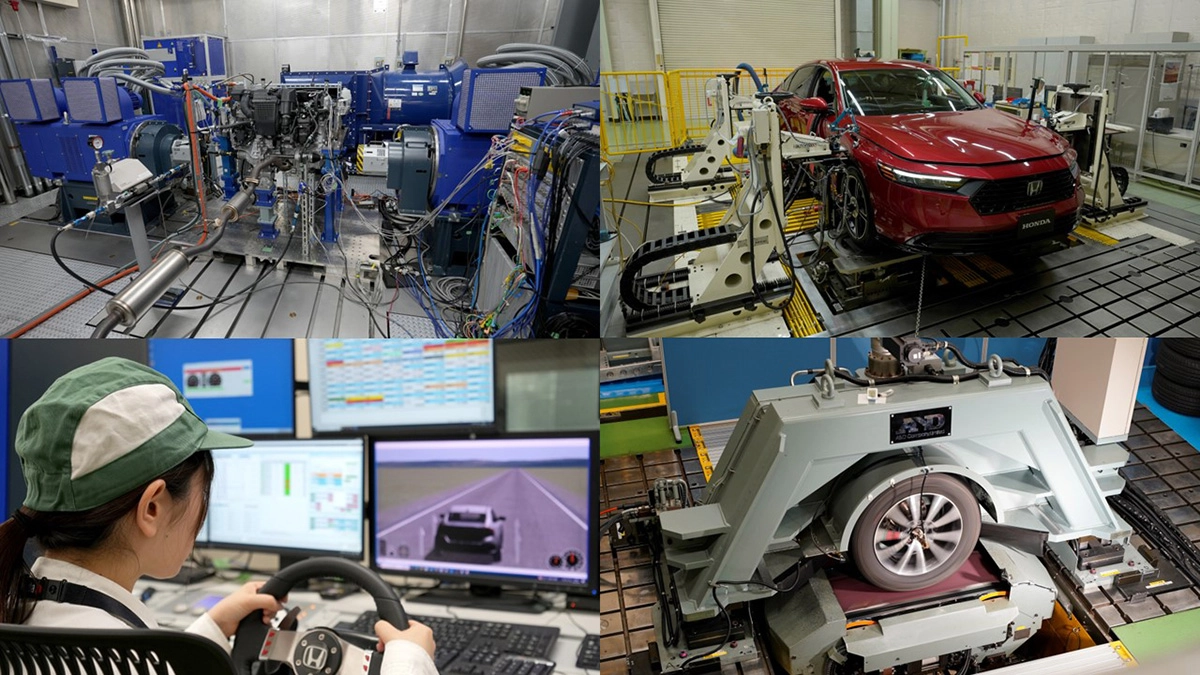
ベンチやテスターでクルマの本質を知る
クルマを効率的に開発するためには、クルマを構成する部品やシステムの特性を知ることが重要である。クルマになった状態では相互に影響する領域が複雑に絡み合うため、改善のポイントや課題解決の糸口に到達するのが難しくなるからだ。ハイブリッドシステムはエンジンやモーター、インバーターなどの部品で構成されており、サスペンションはタイヤやダンパー、コイルスプリングなどで構成されている。
それら部品やシステムの特性を計測する装置がベンチやテスターだ。これらで部品単体やシステムの特性を数値化し、設計にフィードバックする。設計側はベンチやテスターで得られた数値を参考に、目標性能を達成すべくシミュレーションを行ない、最終的には実車で評価する。
部品やシステムの素性を高い分解能で数値化しておくと、シミュレーションの精度が上がり、目標に到達するまでの手戻りが少なくなって効率が上がる。実走テストでは天候や気温など外乱の影響を受けるが、ベンチやテスターの試験施設は任意の環境で繰り返し計測できる。そのため、より良い製品をタイミングよく、かつリーズナブルな価格で提供できるようになる。Hondaのクルマは以下に紹介するベンチやテスターによる基礎データの計測やセッティングにより、鍛え上げられていく。
パワートレーン(ハイブリッドシステム)テストベンチ
Hondaのハイブリッドシステムe:HEV(イー・エイチイーブイ)は、2モーター内蔵電気式CVTとエンジン、パワーコントロールユニット(PCU)、バッテリーパックで構成される。このうち、2モーター内蔵電気式CVTとエンジン、PCUを抜き出して台上計測装置に据え付けたのがパワートレーンテストベンチだ。このベンチでは定常状態だけでなく過渡状態の測定も行なう。各部品の状態を詳しく計測するために、台上のユニットにはセンサー類を追加。エンジンはエンジン単体のベンチ、モーターはモーター単体のベンチで詳細な計測を行ない、得られた情報は相互に補完して開発に生かす。
e:HEVの代表的な走行モードは、バッテリーに蓄えた電力のみで走行用モーターを駆動するEVモード、エンジンの力で発電した電力にバッテリーからの電力を加えて走行用モーターを駆動するハイブリッドモード、クラッチをつないでエンジンの力を直接タイヤに伝えて駆動するエンジンモードがある。
e:HEVは日常のほとんどをモーターで走行し、効率がモーターよりもエンジンのほうが高い高速クルーズなどではエンジンモードで走行する。さまざまなモードをシーンに応じて使い分けるのが特徴だ。どのシーンでどのモードを選択するのが最も効率がいいのか。その検証を行なうのが、パワートレーンテストベンチの役割のひとつ。計測で確認した振る舞いを設計にフィードバックする。
EVモードからハイブリッドモード、ハイブリッドモードからエンジンモードに遷移する際には違和感なくなめらかに移行させたい。どのように制御をセッティングするとスムーズに遷移し、気持ち良く走れるようになるのか。セッティングをさまざまに振り、評価するのもこのベンチの役割である。

コントロール室
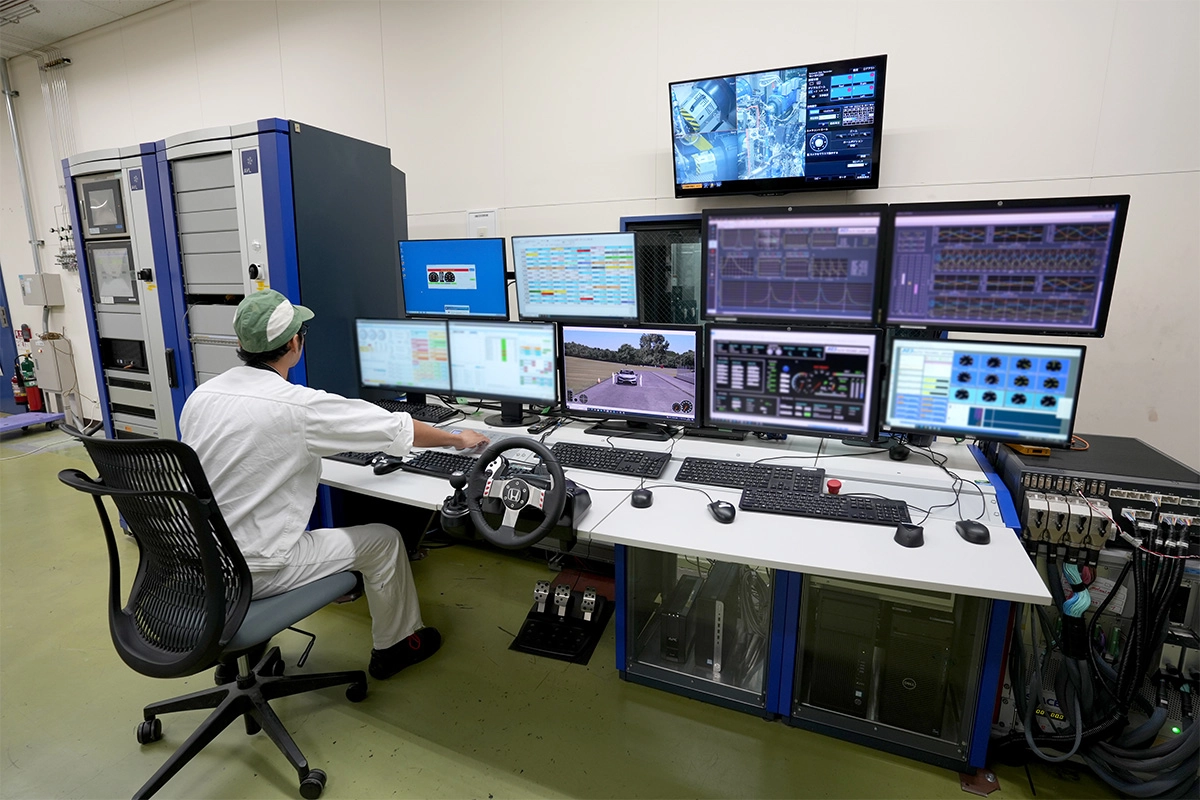
パワートレーンテストベンチ
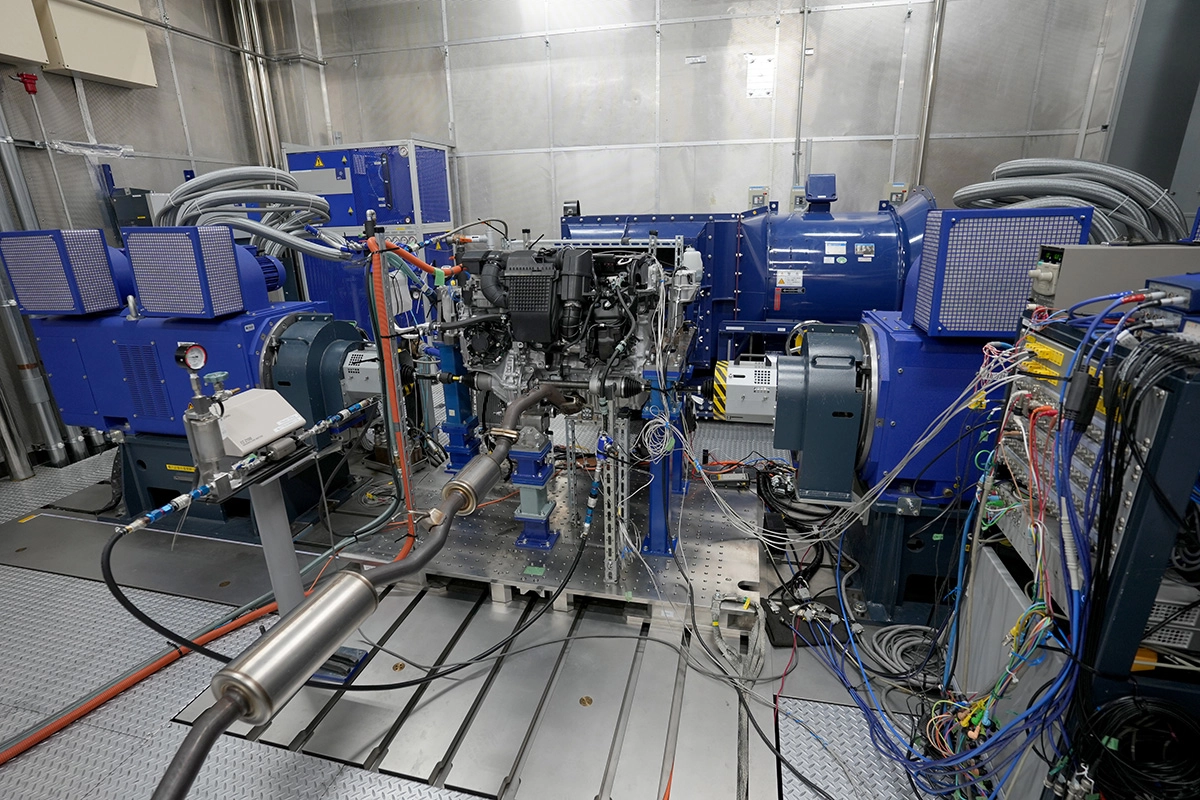
パワートレーンテストベンチ
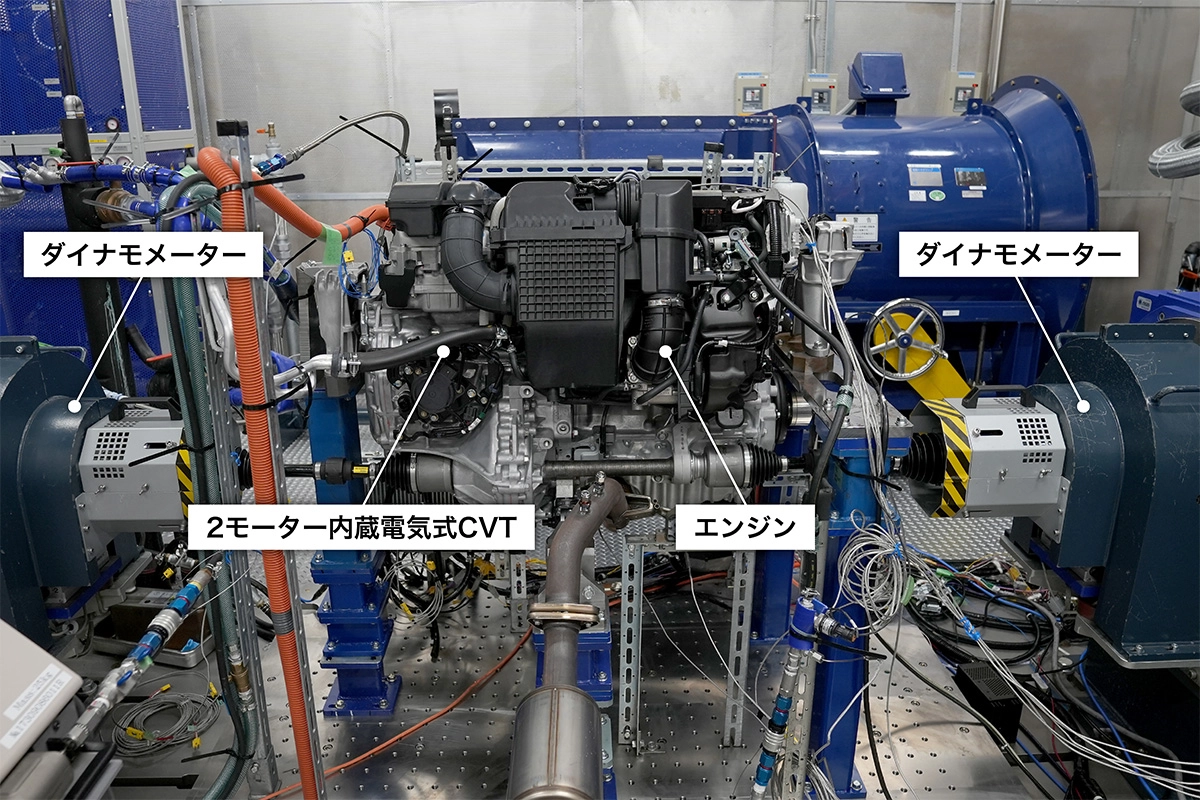
システム構成図
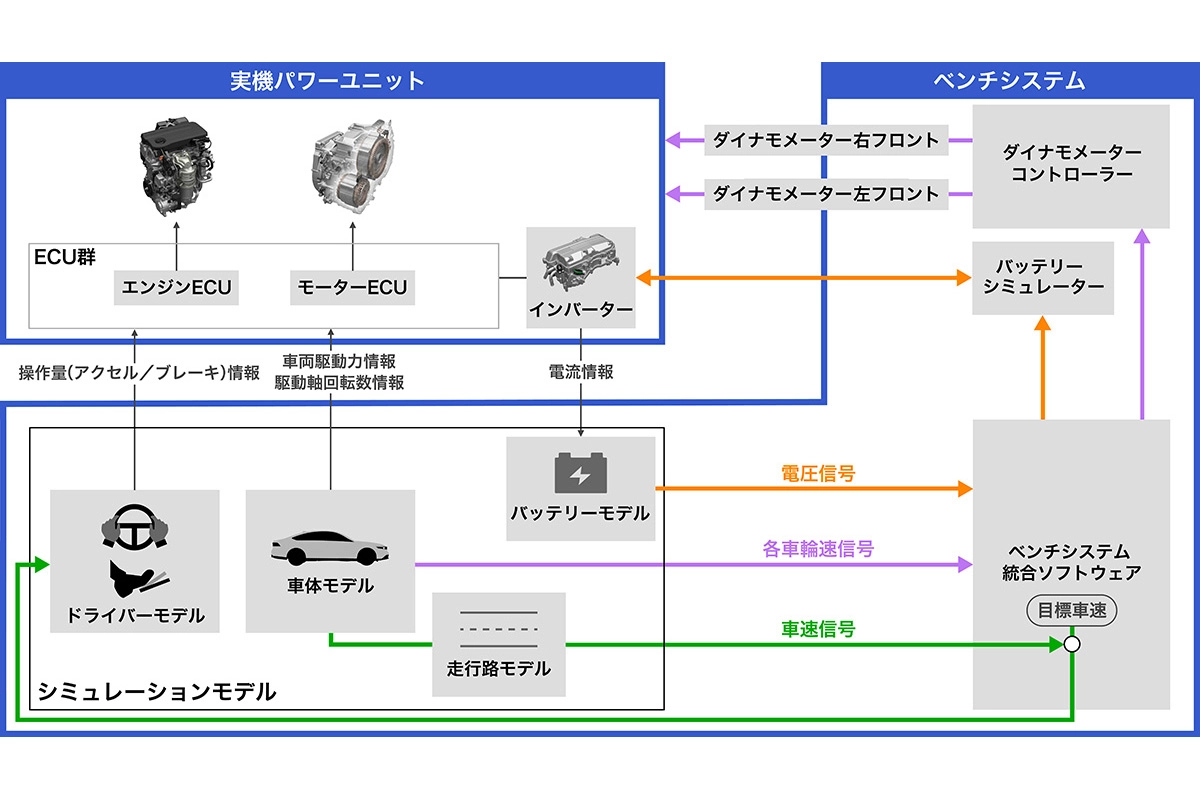
コントロール室
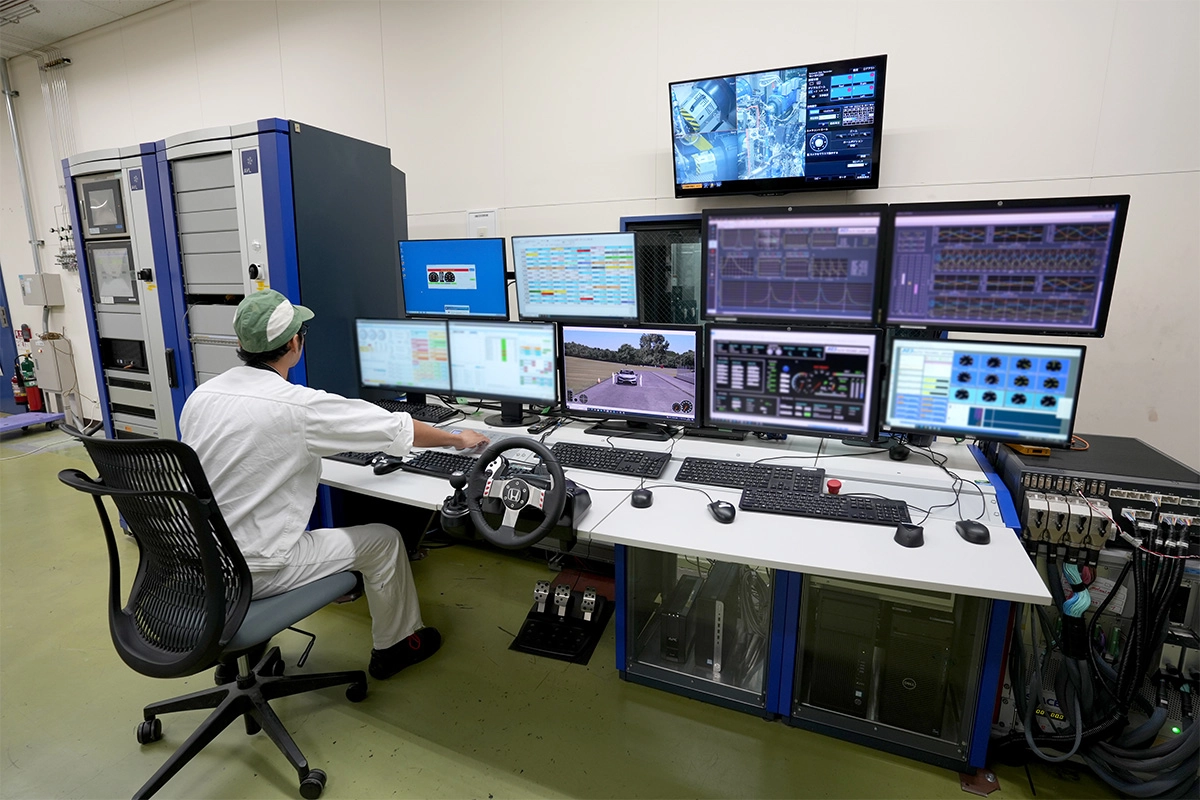
パワートレーンテストベンチ
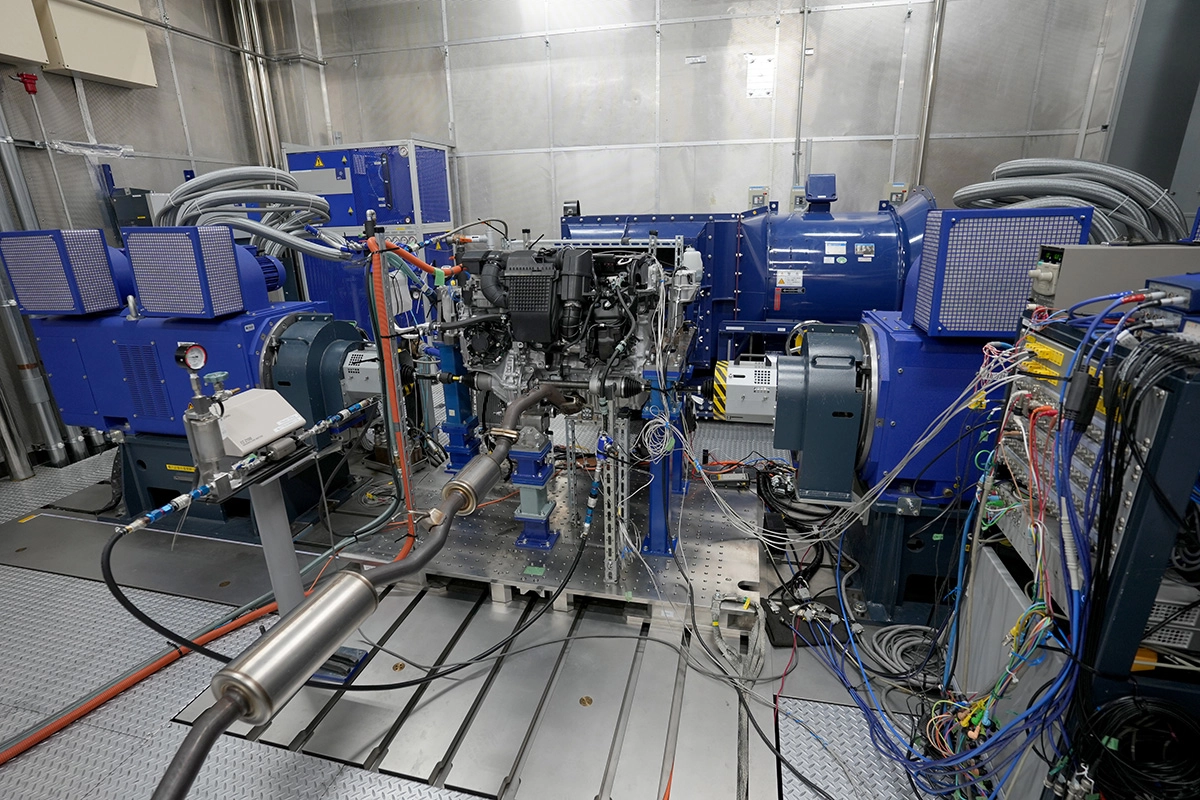
パワートレーンテストベンチ
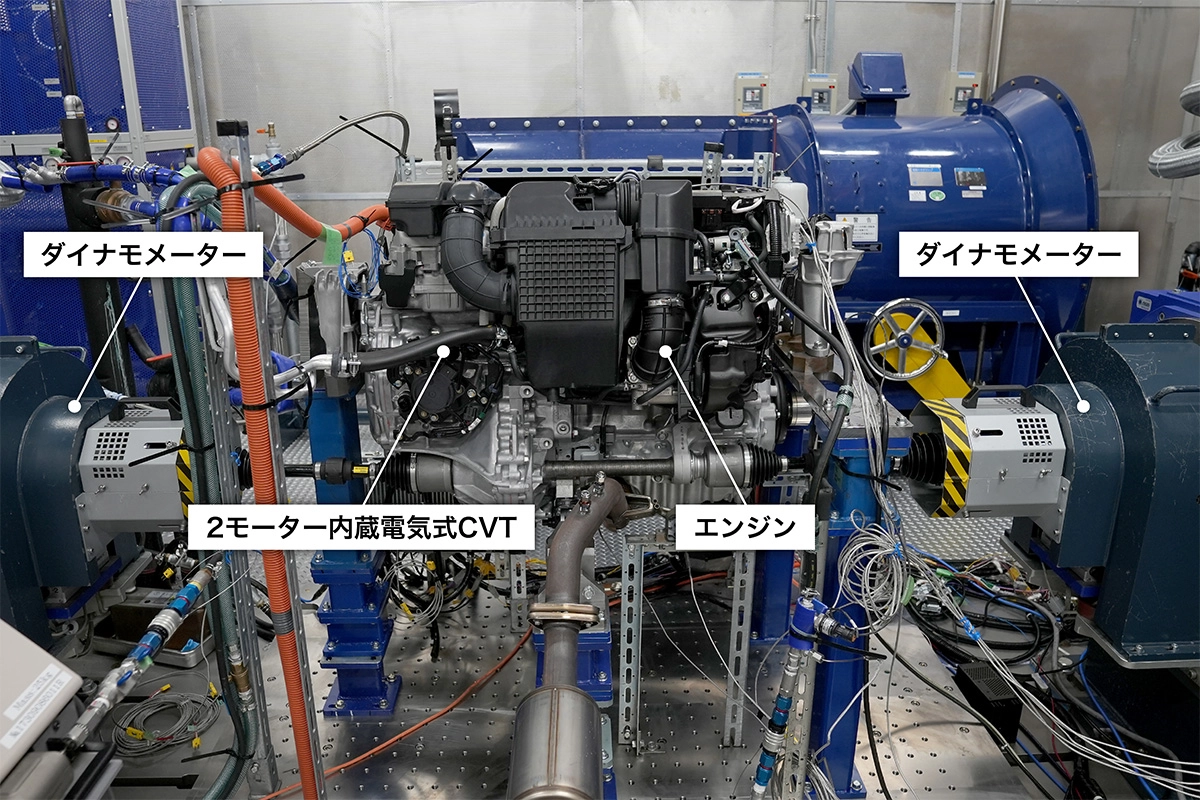
システム構成図
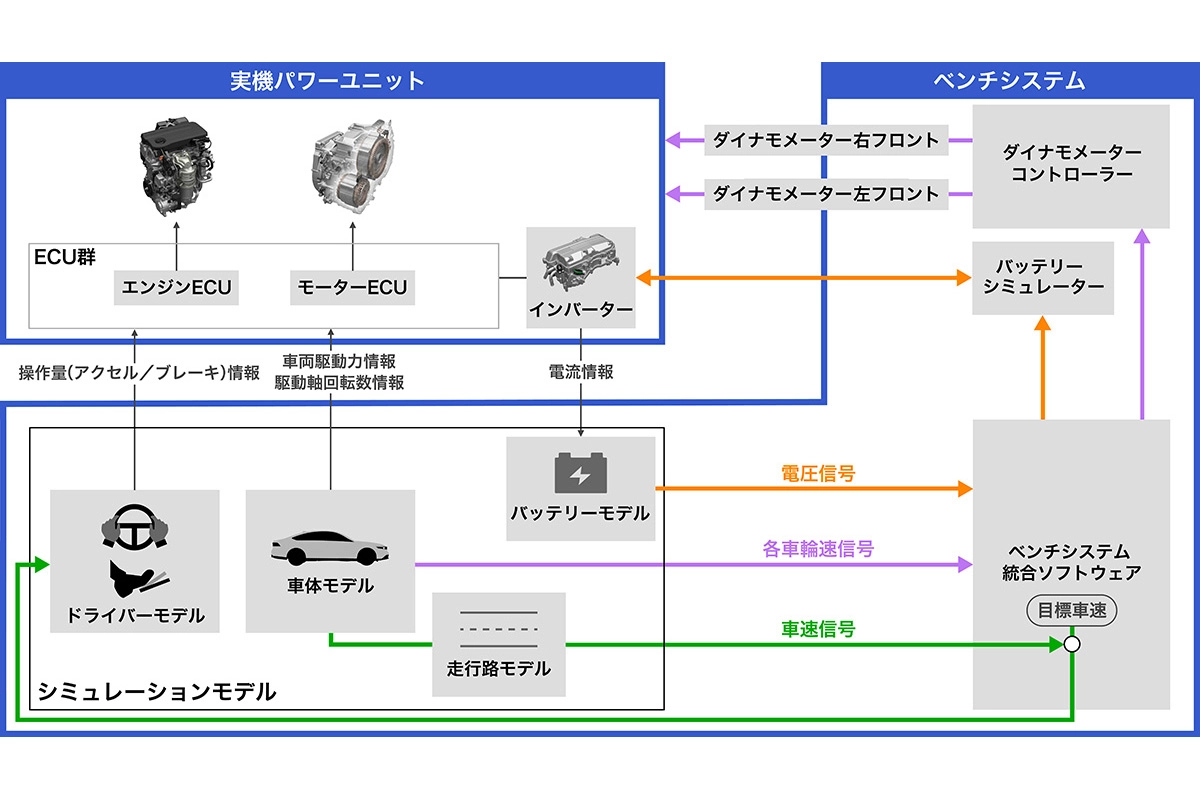
コントロール室
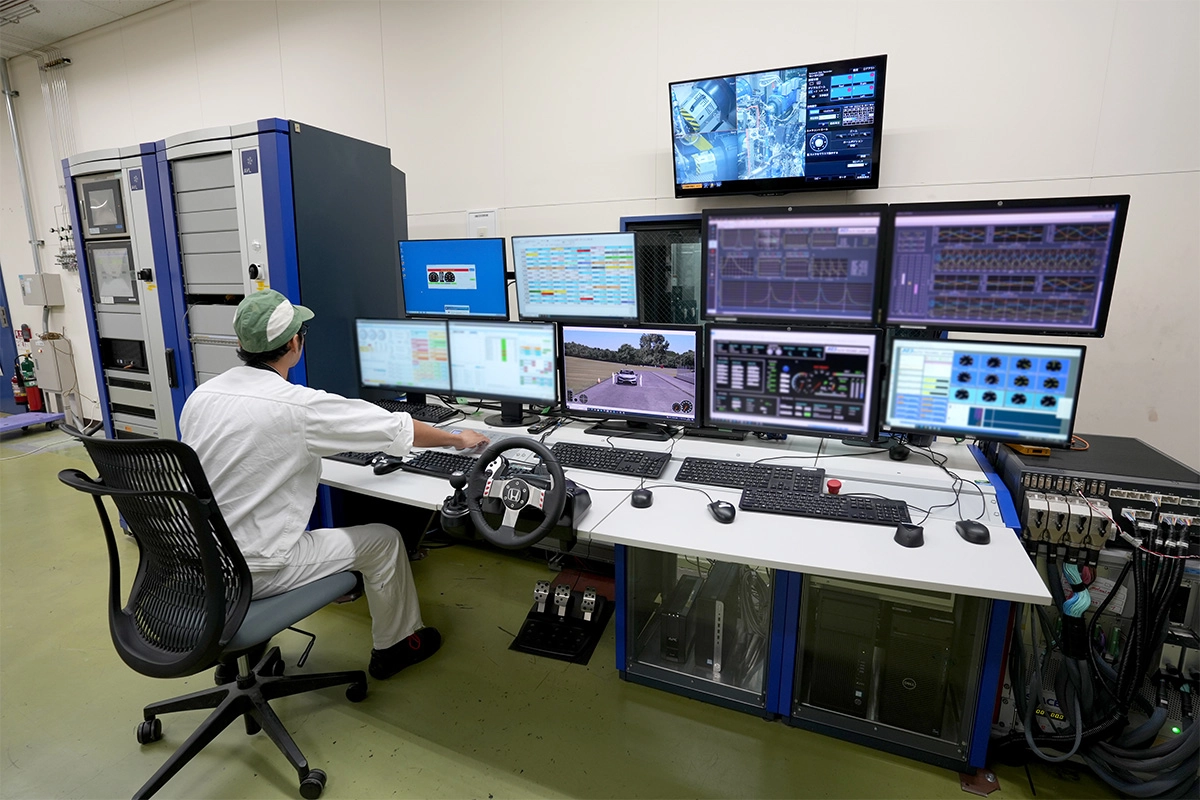

実走テストに比べ、短時間で繰り返し評価できるのがベンチテストのメリットだ。また、実走では気温や風の強さなど、外乱による影響を受けるため、データがばらつきがち。ベンチでは風や天候の影響を受けず、温度を一定の範囲でコントロールすることができる。いつも同じ温度、あるいは狙った温度に制御して計測できるのもベンチテストのメリットだ。
実車で搭載しているバッテリーパックをベンチ室に持ち込んでテストすることも可能だが、テストの効率を考え、設備で代用している。別室に直流電流を供給する電源があり、バッテリーシミュレーターによりバッテリーパックの振る舞いを再現させる。満充電の状態を再現することも可能だし、残量が少ない状態を再現することも可能。また、劣化したバッテリーの状態を再現することも可能で、さまざまな条件で評価することができる。
テストの無人化に対応しているのも、パワートレーンテストベンチの特徴。設備的には24時間無人試験も可能だ。一方で、人が集まって耳をそばだてるケースもある。コントロール室にはアクセルペダルが置かれている。本来は操作盤のダイヤルがアクセル代わりを務める。一部機種のe:HEVに適用したリニアシフトコントロールの開発では、アクセルペダルを踏んだときの、車速の伸びとシンクロしたエンジン回転数の段階的な変化を少しでもリアルな条件とそろえたいと、あえてペダルを用意し操作した。現場、現物、現実を見て物事を判断するHondaの三現主義を体現する部分である。
人の操作による評価の様子
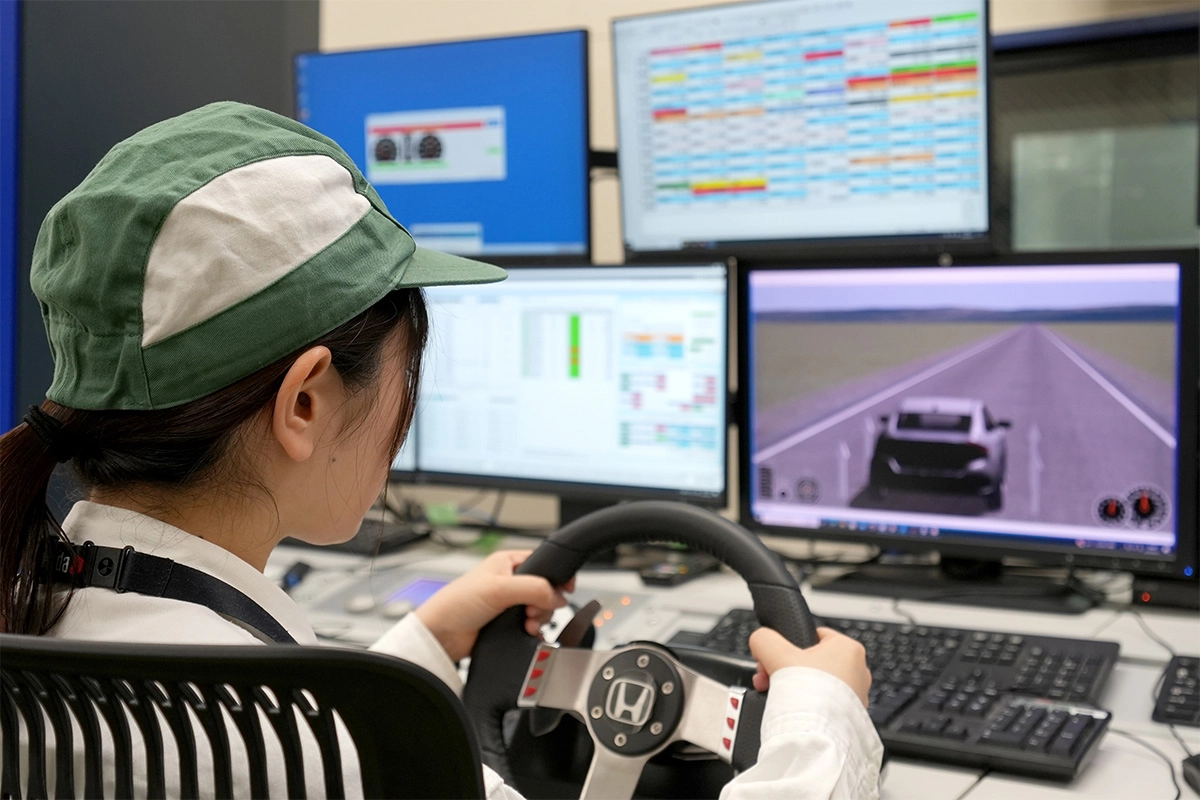
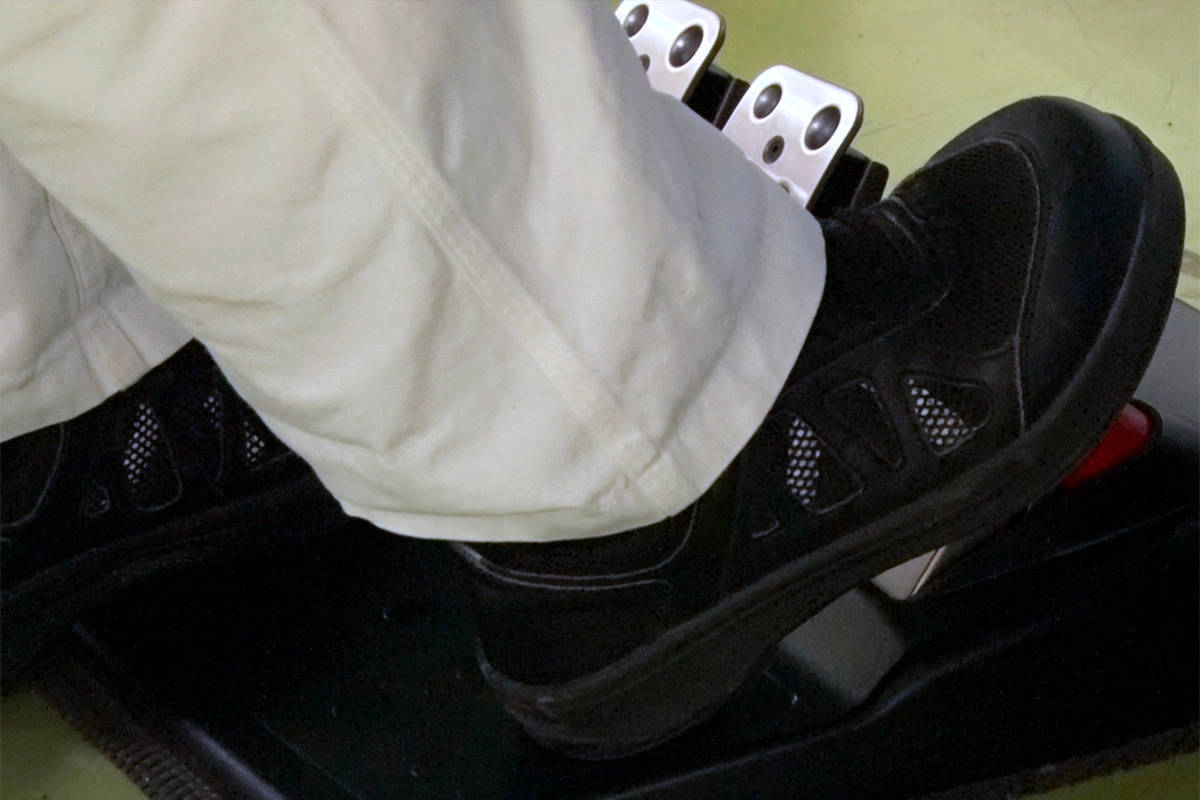
モーター性能ベンチ
ハイブリッドシステムやEV(電気自動車)に搭載するモーターの基礎データをとる試験装置がモーター性能ベンチだ。モーター性能ベンチでの計測で得られたデータを、電磁鋼板を積層したローターに埋め込む磁石の配置や電磁鋼板の枚数をどうするか、ローターとステーターの距離をどうするかなど、最終的に完成車に搭載される際の出力/トルク、電費など、性能や効率に影響を与えるモーターの諸元(スペック)決めに反映する。
ベンチ室の中に箱治具と呼ぶケースが設置されており、中に試験するモーターが入っている。ローターがきちんと回っているかを確認したり、モーターを冷却する油の流れを確認したりするため、一部は内部が目視できる状態になっている。ローターや、ローターに埋め込んだ磁石、ステーターの巻線、油などは、センサーで温度を計測する。計測時に耐熱限界を超えないよう監視するためと、基礎データを収集するためだ。試験では駆動と回生を繰り返したりして計測し、出力やトルク、効率を算出する。
バッテリーの直流電流を交流電流に変換するインバーターは、シミュレーターを使う場合もあるが、車載しているものを使う場合もある。ノイズの状態やその影響など、インバーターとモーターを組み合わせた際に起きる事象を確認するためだ。
実車ではスペースの制約などから付けられないセンサーが付けられるのも、モーターベンチのメリットだ。また、実車で適用するオペレーションの範囲を超えて、自由に回転数を設定したり、温度を振ったりするなど、さまざまな条件で試験ができるのもベンチテストのメリットである。実際の運転状況の再現だけでなく、限界領域の見極めも行なうことができる。また、実車テストで発生した、走る・曲がる・止まる動作の違和感となる現象の原因解析に利用することもある。
モーターの効率は一般的に90%以上あり、40%程度のエンジンの熱効率よりはるかに高い。残る損失は10%程度のため、わずかな違いが効率を大きく左右する。そのため、モーター性能ベンチでは、小さな事象をどれだけ正確に計測できるかが重要。トルクは1Nm未満まで正確に計測できるし、電気的な応答を把握するために必要な時間軸での微細な事象を正確に捉えるよう整備している。ドライバーの意志に忠実に呼応する加減速を生み出すことができるのは、このように高い分解能で計測を行なっているからだ。
モーター性能ベンチでモーターの基礎データを収集した後は、冷却テストや耐久テスト、システムテストなど開発の後段階のテストに移っていく。Hondaのモーターが高い性能と耐久性を担保しているのは、技術を手の内化しつつ、基礎データをきっちり取り、最終的には人の目で確認して品質を担保しているから。オシロスコープに流れる波形を眺めていると見えてくるものがあり、それが現象解析に結びつくことがある。設備は効率を向上させる手段であり、正しく評価したいから設備にこだわる。しかし、開発を行なうのはあくまでも“人”だと意識し、こだわりをもって測定に取り組んでいる。

オシロスコープ
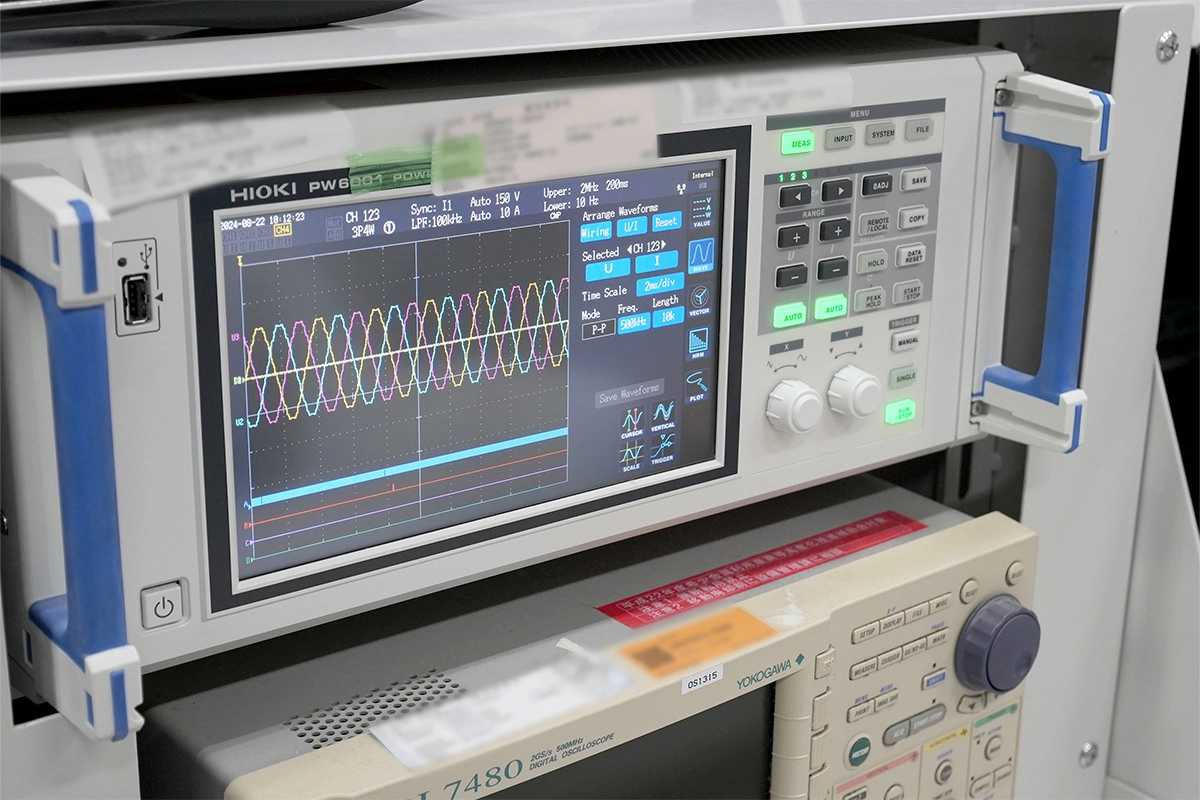
モーター性能ベンチ
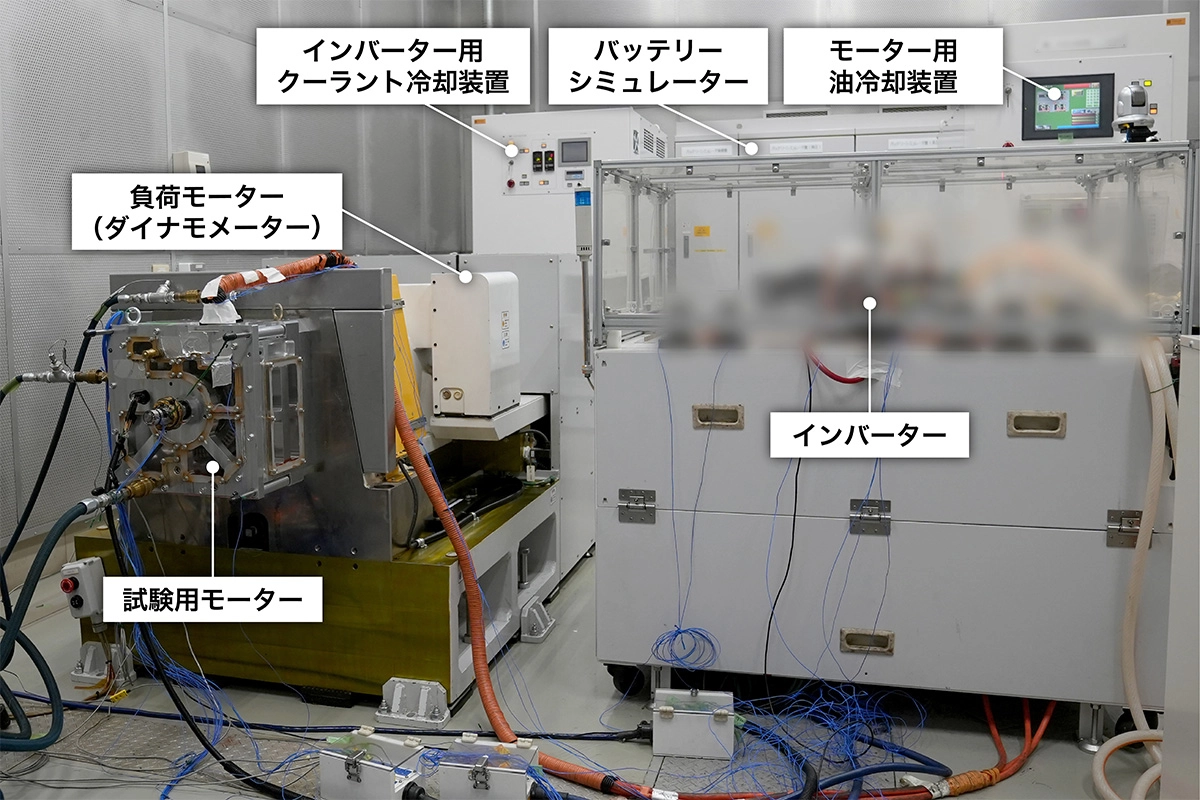
モーター性能ベンチ
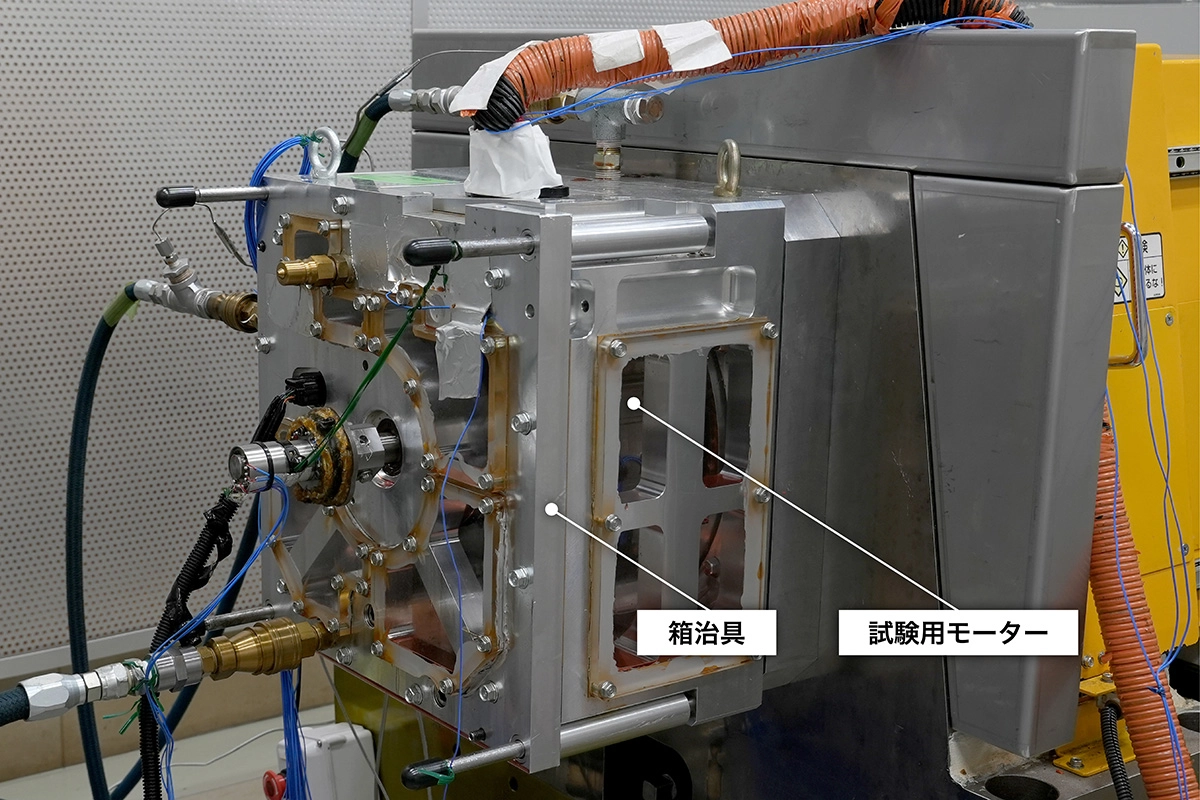
システム構成図
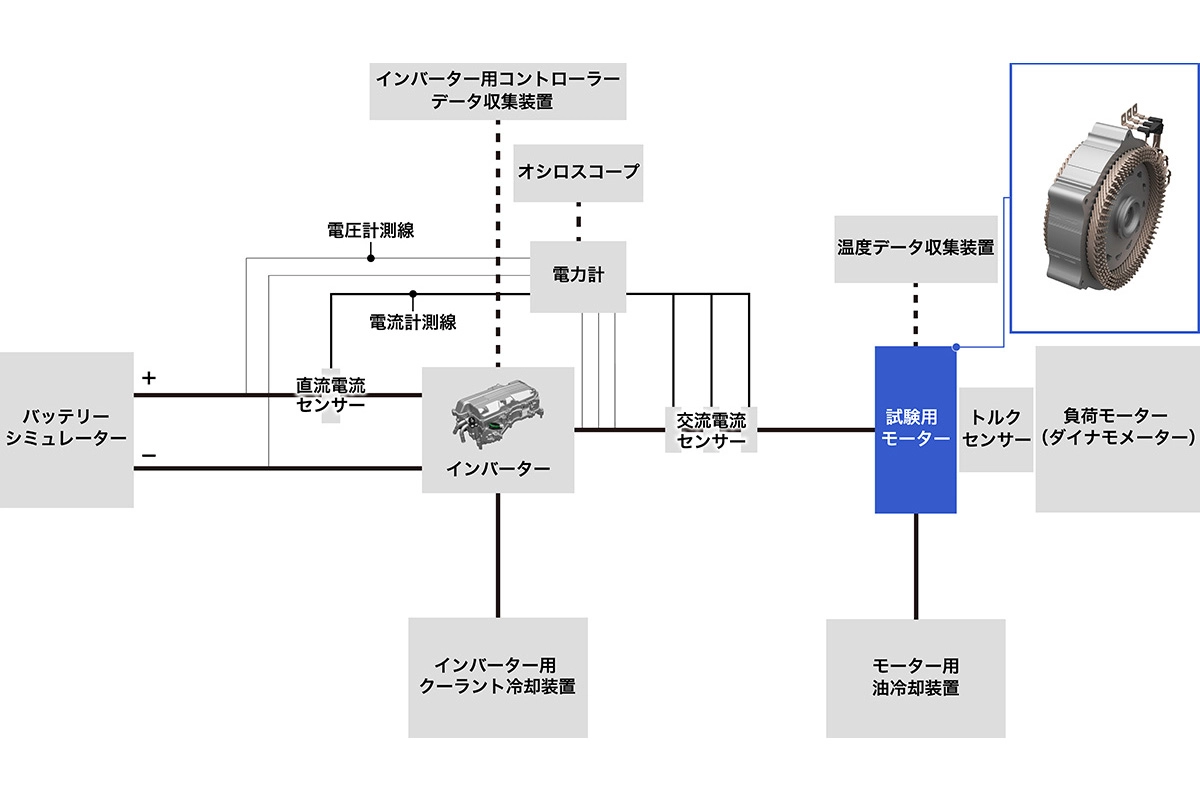
コントロール室
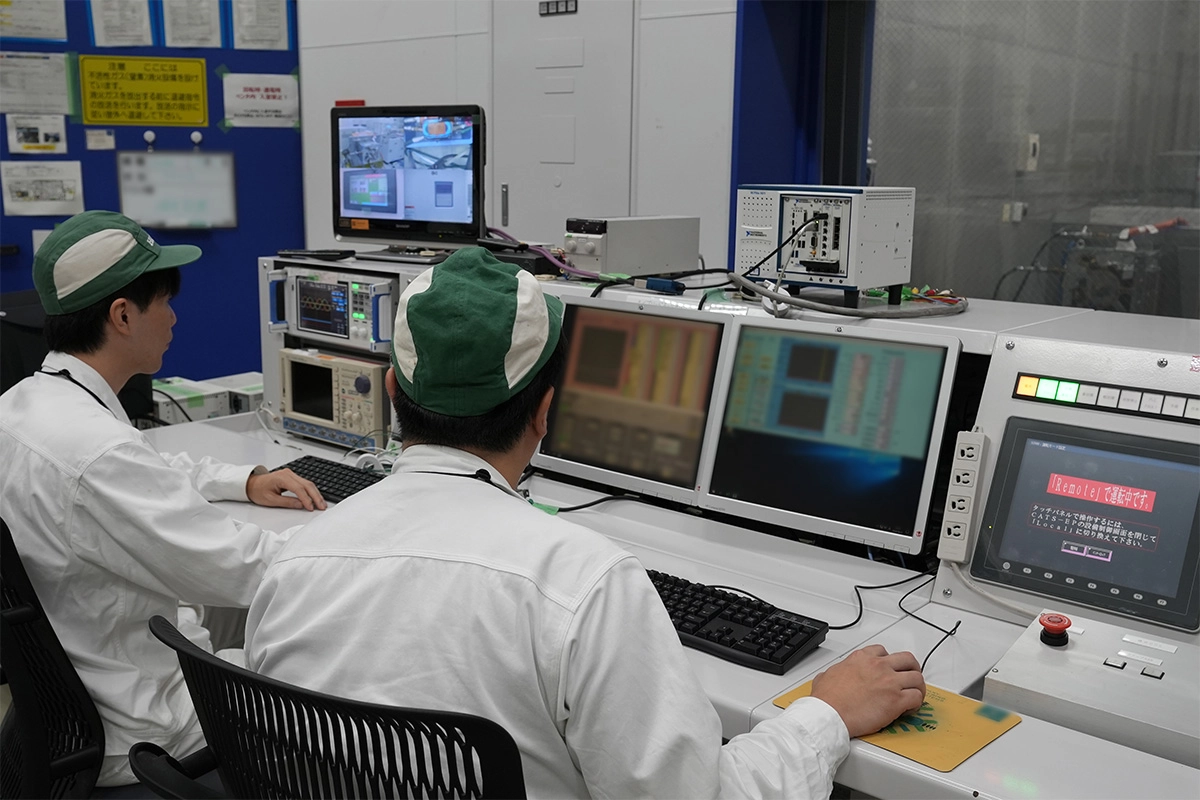
オシロスコープ
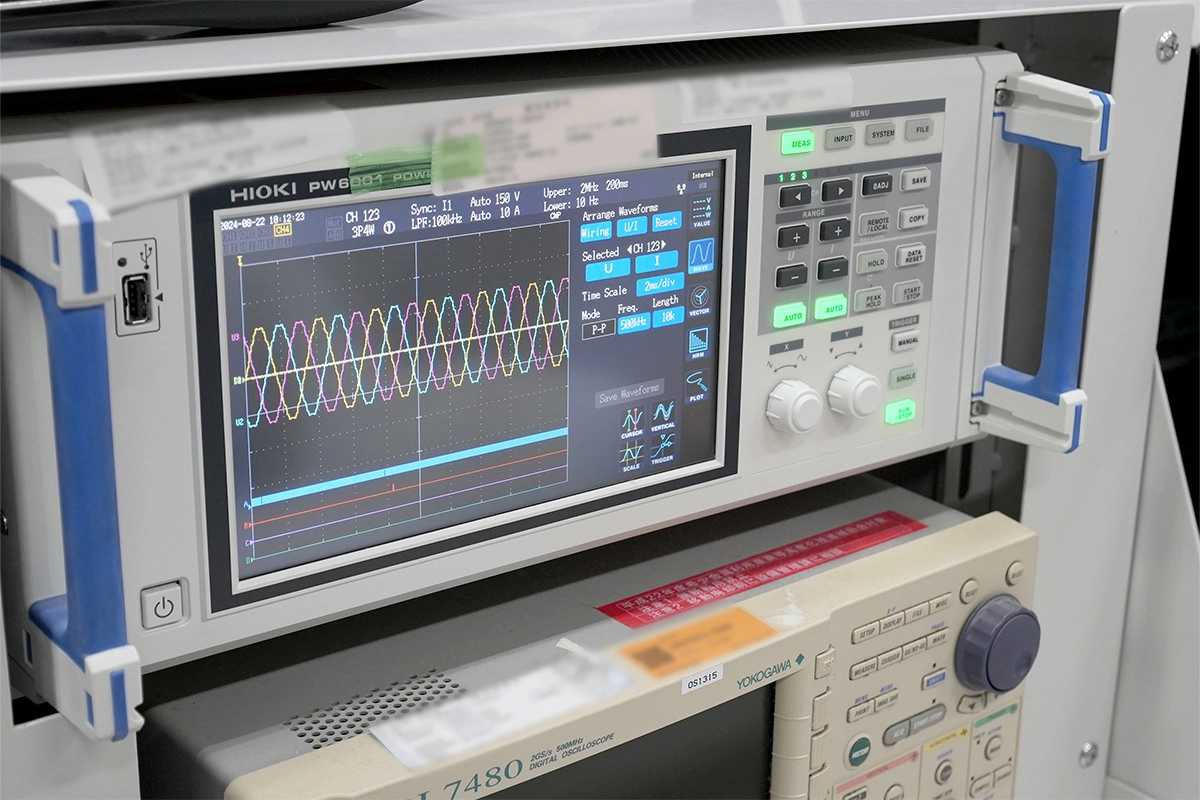
モーター性能ベンチ
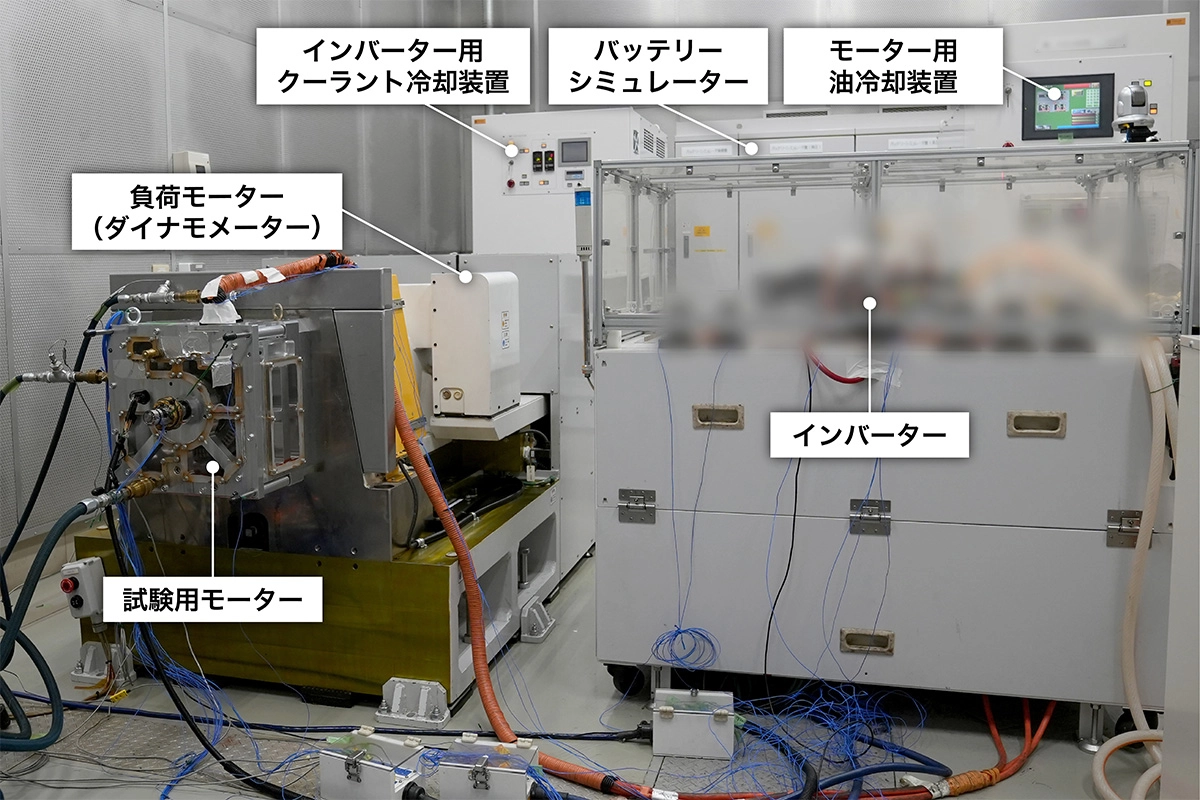
モーター性能ベンチ
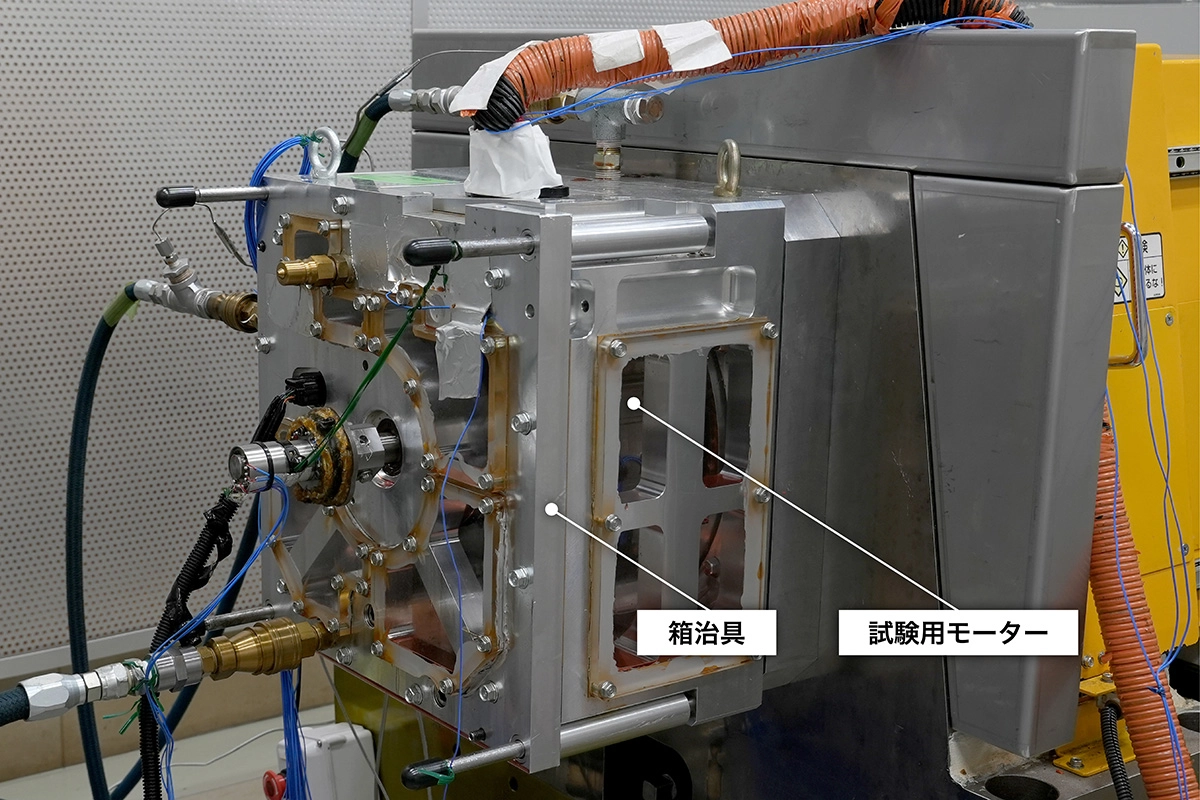
システム構成図
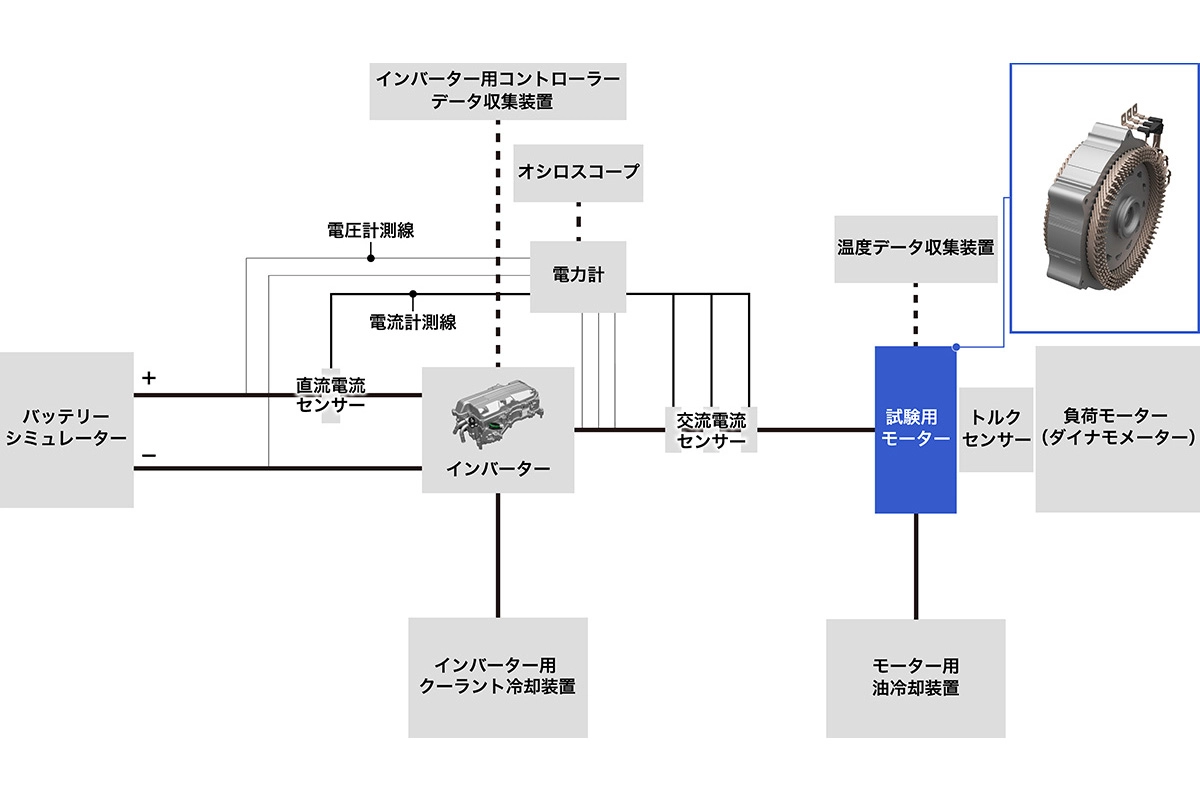
コントロール室
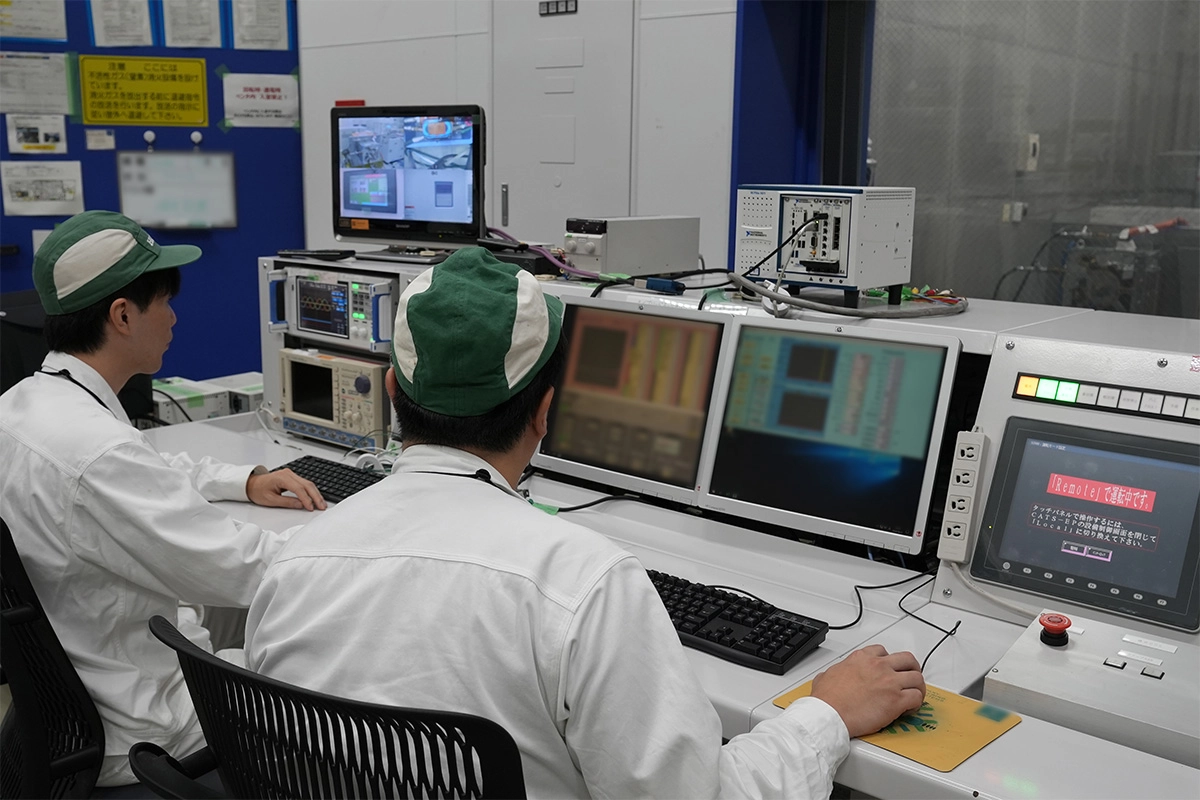
オシロスコープ
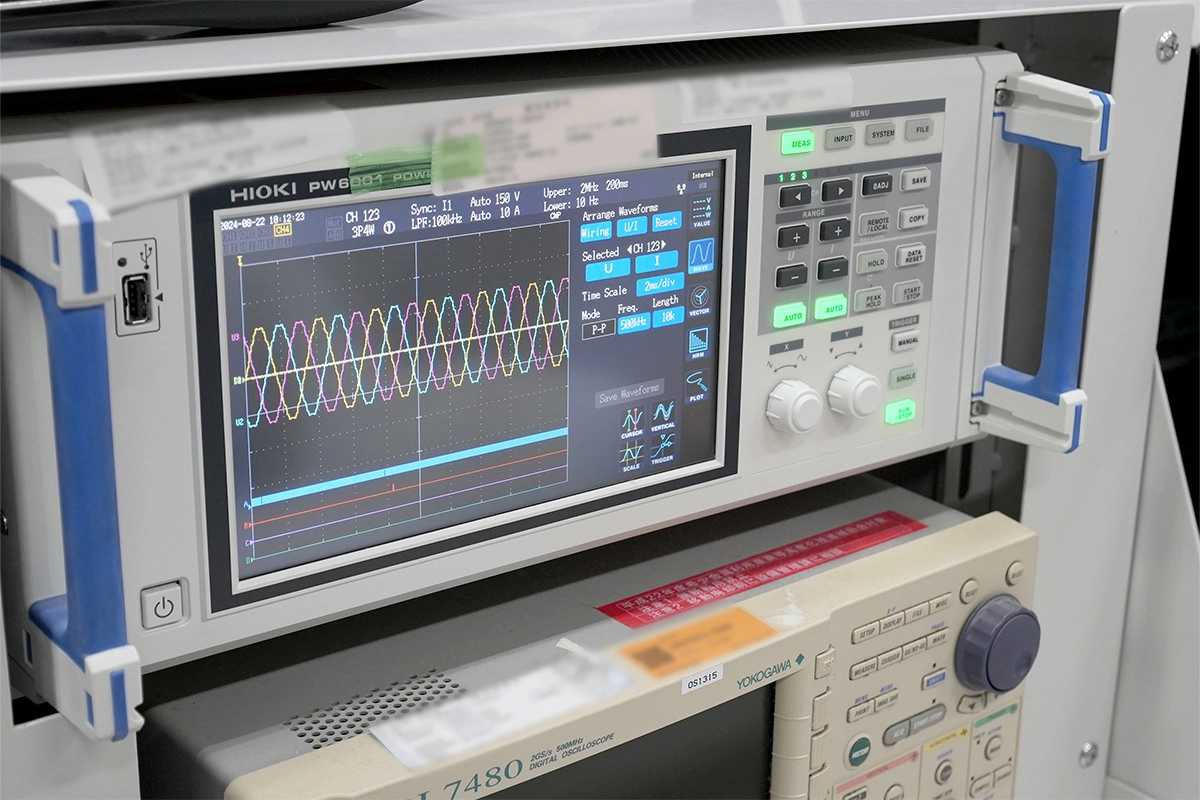

モーター極低速回転ベンチ
モーターは回転部分のローターと、その外側にある固定部分のステーターで構成されている。電流を流すと、ローターの永久磁石がステーターの電磁石に近づいた際にトルクが高くなり、離れるとトルクが下がる。ローターの永久磁石の極数や配置とステーターの電磁石の極数の組み合わせなどによって、トルクに脈動(脈を打つような振幅)が生じる。この脈動をトルクリップルと呼ぶ。
一般的な電気モーターのトルクリップルは最大トルクに対して10~15%の範囲で生じる。例えば、急な上り勾配で停止した際に、ローターとステーターの位相がちょうどトルクの谷の位置で止まる場合が考えられる。こうした状況でも発進時に不安を抱かせずに済むトルクを発生できるかを評価することも、このベンチで行なう。また、測定して得た基礎データをもとにトルクリップルの幅を一般的なモーターよりも小さくするようなアイデアを設計側にフィードバックしたりもする。
トルクリップルはモーターが発する音の原因にもなる。出てしまう音を車体側で抑えるのではなく、源流で断つべく、担当部署が誇りを持って試験に携わっている。モーターを極低回転で回さないと検出できないデータを精密に捉えることで、静粛性の高いモーターの開発に貢献している。
モーターを高速で回転させるとトルクが平均化されてしまうため、極低速で回転させてトルクリップルを計測したい。低回転にするほど、トルクの変動を精密に捉えることができるからだ。それを実現するのが、モーター極低速回転ベンチである。このベンチでは1rpm以下の極低速で回転させることもできるし、極数に応じて位相ごとに止めながら計測することも可能だ。
モーター極低速回転ベンチでは、設計どおりのトルクリップルになっているかどうかを確認するのが基本。Hondaのすべての台上試験施設に共通しているが、試験の運用に携わる技術者は単に試験を行なうのではなく、最終製品を意識しながら試験の現場で現物と現実を確認し、現実を知る技術者の立場から設計側と対等に情報交換を行なっている。
試験用モーター
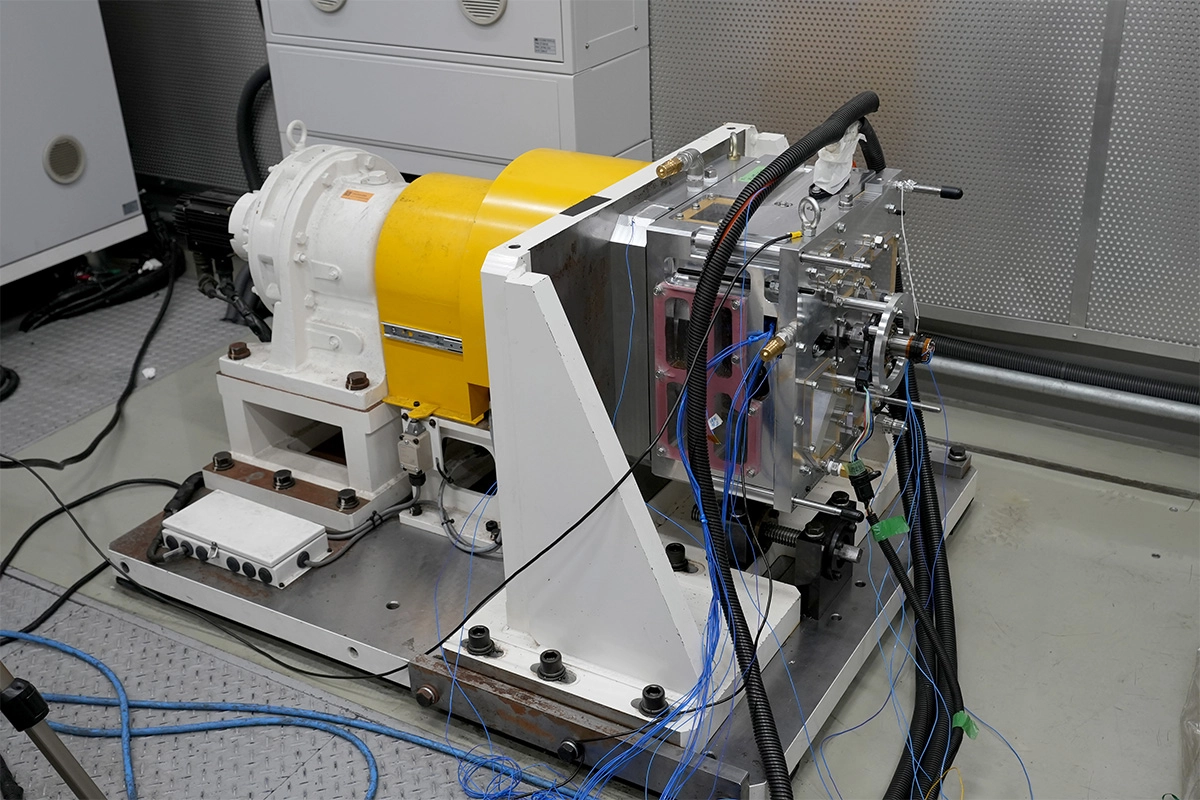
コントロール室
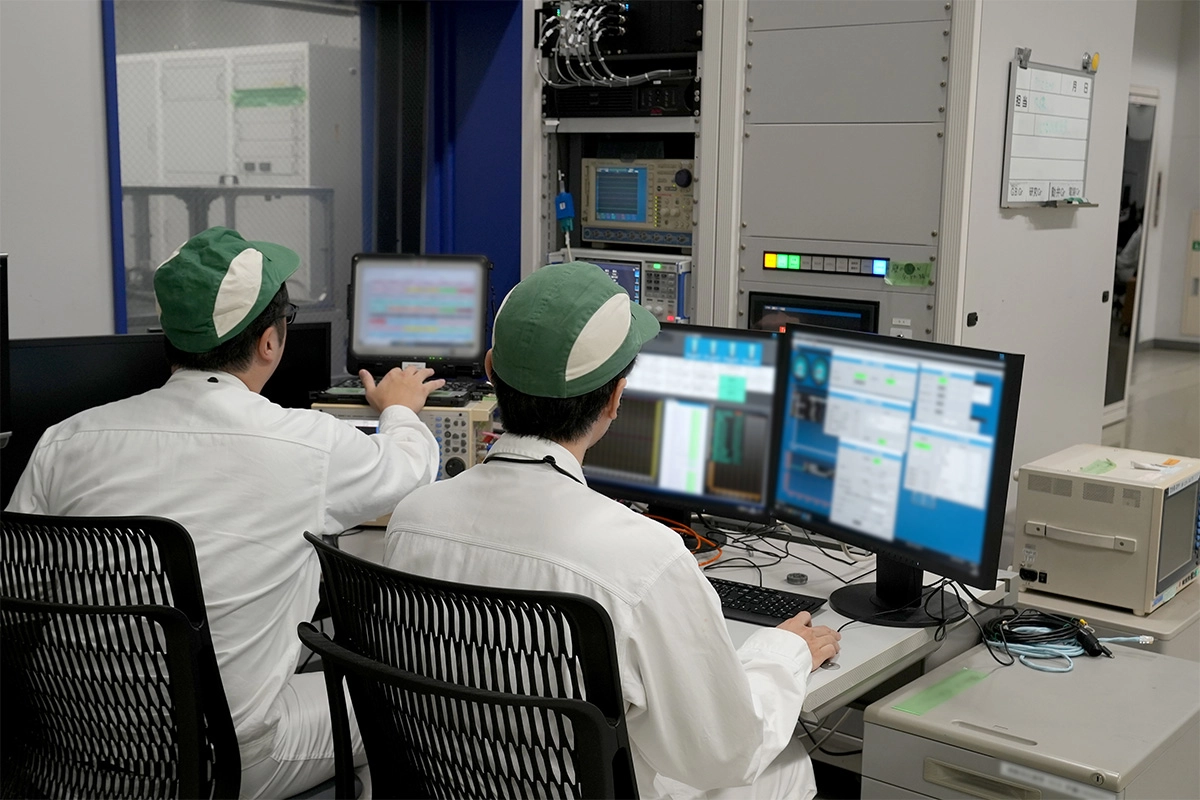
ドライブユニット/モーター単体NVベンチ
ハイブリッドシステムの場合は発電用モーターと走行用モーターを動力伝達機構と組み合わせてケースに収めたドライブユニットの状態、EVの場合は走行用モーターと減速機構を組み合わせてケースに収めた状態で騒音(Noise)と振動(Vibration)を計測するのが、ドライブユニットNVベンチだ。部品単体ではなくドライブユニットになった状態で発する音や振動の発生源を特定し、それを効率的に低減する開発に貢献するのが、このベンチの役割である。
一方、モーター単体の振動と騒音を計測するのがモーター単体NVベンチだ。ドライブユニットNVベンチの測定データと合わせ、目標とする室内音に向けて開発を進めていく。両ベンチとも計測は音が反響しないよう吸音材で囲んだ無響室で行なう。ドライブユニットNVベンチではドライブユニットを音響測定治具で囲み、測定対象物から決まった位置に複数のマイクを配置してユニットが発する音圧を測定。音響パワー(音響エネルギーの総量)の指標を用いて評価する。
NVは低周波と高周波に分類し、測定している。低周波は固体伝搬音と言い換えることができ、金属製ケースなどの固体を伝わった振動が空気を振動させて伝わる音。測定対象物にGセンサーを取り付けて測定する。一方、高周波は空気を振動させて伝わる空気伝搬音を指し、音響測定治具で測定する。
完成車の状態で室内音を何デシベル以下にするという目標が決まると、そこから固体伝搬音と空気伝搬音の数値目標が算出される。ドライブユニットNVベンチで固体伝搬音と空気伝搬音を測定し、設計と実機のコリレーション(相関関係の確認と分析)を行なう。目標を達成できそうにないからといって、車体側に吸音や遮音などの対策を押し付けるようなことはしない。経験の積み重ねで蓄積した知見を生かし、「自分たちのところで良くする」「こだわりを持っているからこそ、いい製品になる」という信念で計測に取り組んでいる。
無響室
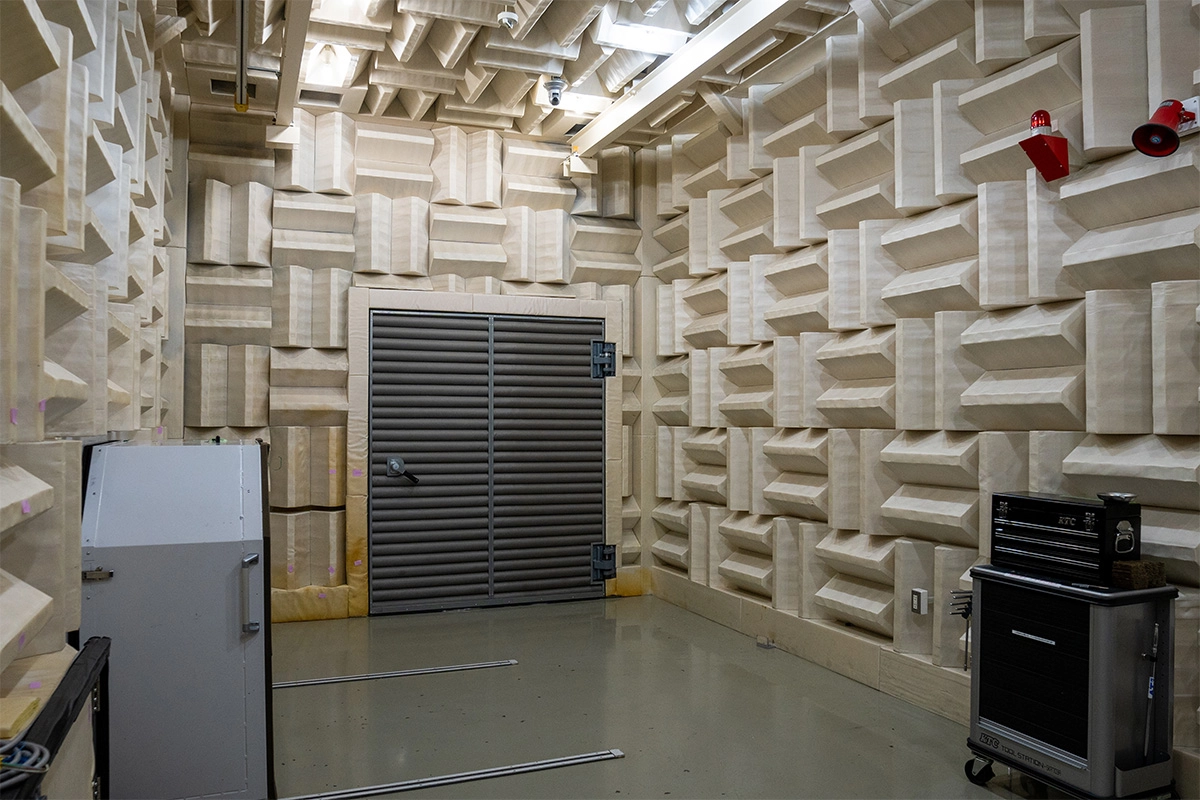
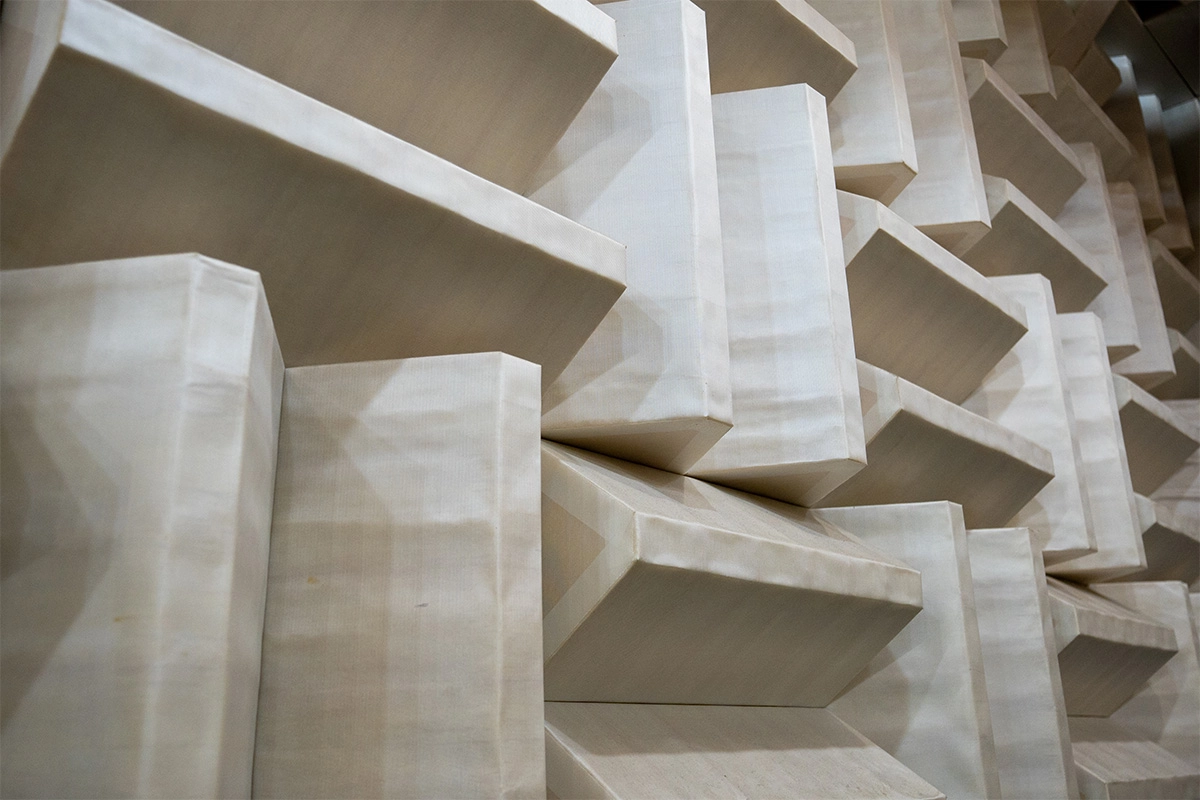
単気筒性能エンジンベンチ
実際のエンジンの1気筒分だけを切り出したのが、単気筒性能エンジンベンチである。エンジン開発の最初の段階で、燃焼諸元を決める。燃焼諸元とは、吸気系であれば吸気管の径や長さ、チャンバーの容量、吸気ポートの三次元形状に吸気バルブの径や形状、カムプロファイルなどが該当する。燃焼室ではその形状や圧縮比、ピストンの形状、インジェクターの配置、点火プラグの仕様などが該当。各部品の機能や相互作用を考慮し、仕様を決めていく。単気筒性能エンジンベンチで行なう試験で得られるデータは、エンジンのキャラクターを決める際に重要な役割を担う。
単気筒性能エンジンベンチで燃焼を詳細に評価することにより、燃焼諸元を早期かつ確実に決定し、開発の後工程で行う各種機能検証を手戻りなく行なうことができる。目には見えないエンジン内部の燃焼状態を精密な圧力計測により、圧力の微小な変化から見える化し、燃焼状態を把握・解析。計測結果を設計にフィードバックし、仕様検討を推進する。その結果、目標性能を満足する燃焼諸元が開発初期に確実に決定できるようになる。
4気筒などの多気筒エンジンでは、気筒ごとのばらつきや気筒同士の相互作用など、燃焼に対する外乱が多く、燃焼解析の精度が低下する。一方、1気筒を切り出した単気筒エンジンでは、純粋に燃焼に焦点を当てた解析・検証が可能になる。また、エンジンの取り回し自由度が高いため、多気筒エンジンでは装着できないセンサーの装着が可能だ。単気筒では部品交換作業の工数・費用の削減にもつながり、高効率な開発が実現できる。
装置の見た目はまさに、エンジンを1気筒分切り出した格好だ。単気筒特有の吸気の脈動が生じないよう、容量の大きな球形のサージタンクを設置。排気側は反射波の影響を受けないようチャンバーを設置し、純粋に燃焼に焦点を当てた計測ができるよう環境を整えている。
また、大気圧の影響を排除するため、吸気圧力を一定に保つ装置を設計・製作し設置している。排気エミッション規制の強化にともない、低温条件でのエミッション低減が厳しくなる傾向だ。このトレンドに対応するため、冷却水と吸気を冷却する専用の低温装置を設計し設置した。
4気筒エンジンの場合は1番、4番気筒と2番、3番気筒が180度の位相で上下するため、エンジン全体ではピストンの往復運動による回転1次の慣性力が釣り合う。ところが単気筒の場合は慣性力を打ち消す気筒が存在しないため、単気筒エンジン特有の振動設計が必要となり、従来は低回転における燃費評価での活用に留まり、高回転出力は評価してこなかった。一方で、モータースポーツの開発拠点であるHRC SakuraではF1の単気筒エンジンで10,000rpmをゆうに超える高回転で運用している。そこで、Sakuraの施設を参考に台上試験施設側で知恵を絞り、量産用単気筒性能エンジンでも高回転化を実現。その結果、単気筒でも全開出力が評価できるようになった。
ある諸元を変えると、それに関連する事象が影響を受け、燃焼状態量が変わる。CAE(コンピューターを活用した設計および解析)を中心に選定した、目標性能を満足する燃焼諸元を実機で検証するのが単気筒性能エンジンベンチの役割。並行し、計測したデータから燃焼状態量の変化を紐解く解析を行ない、CAEの精度向上にも役立てている。

コントロール室
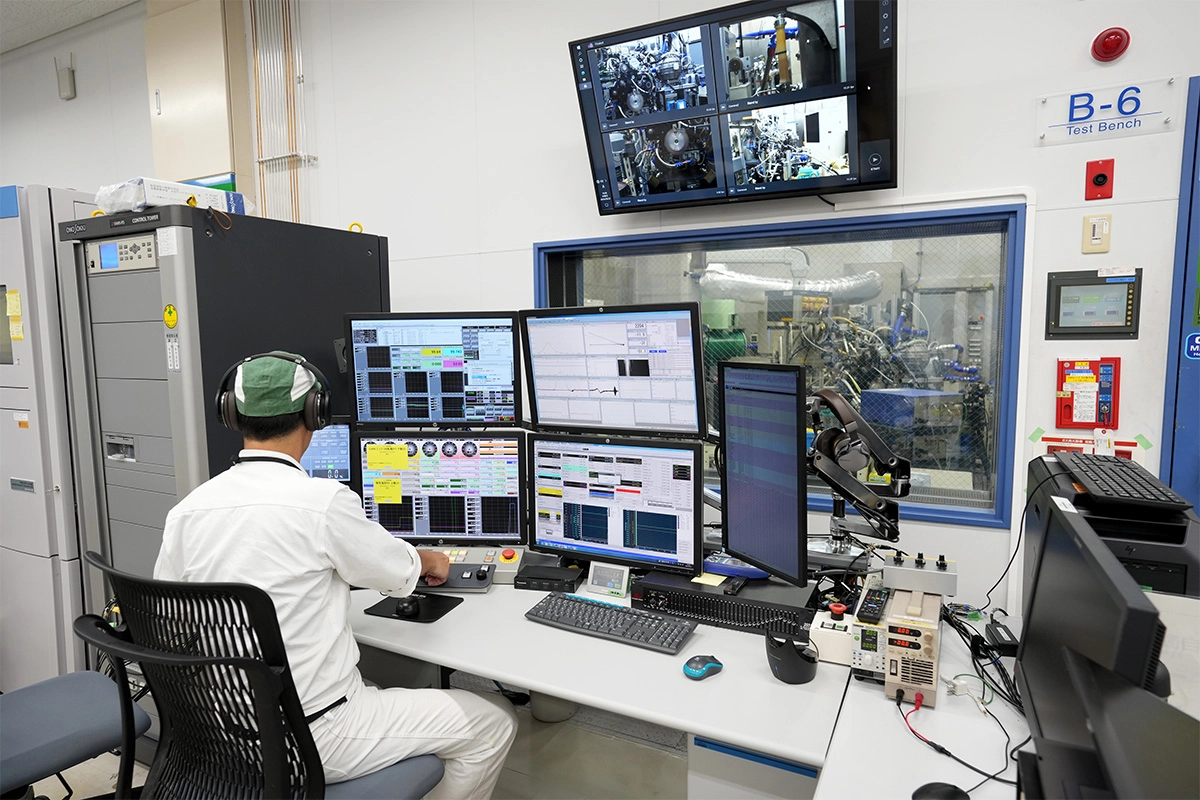
単気筒性能エンジンベンチ
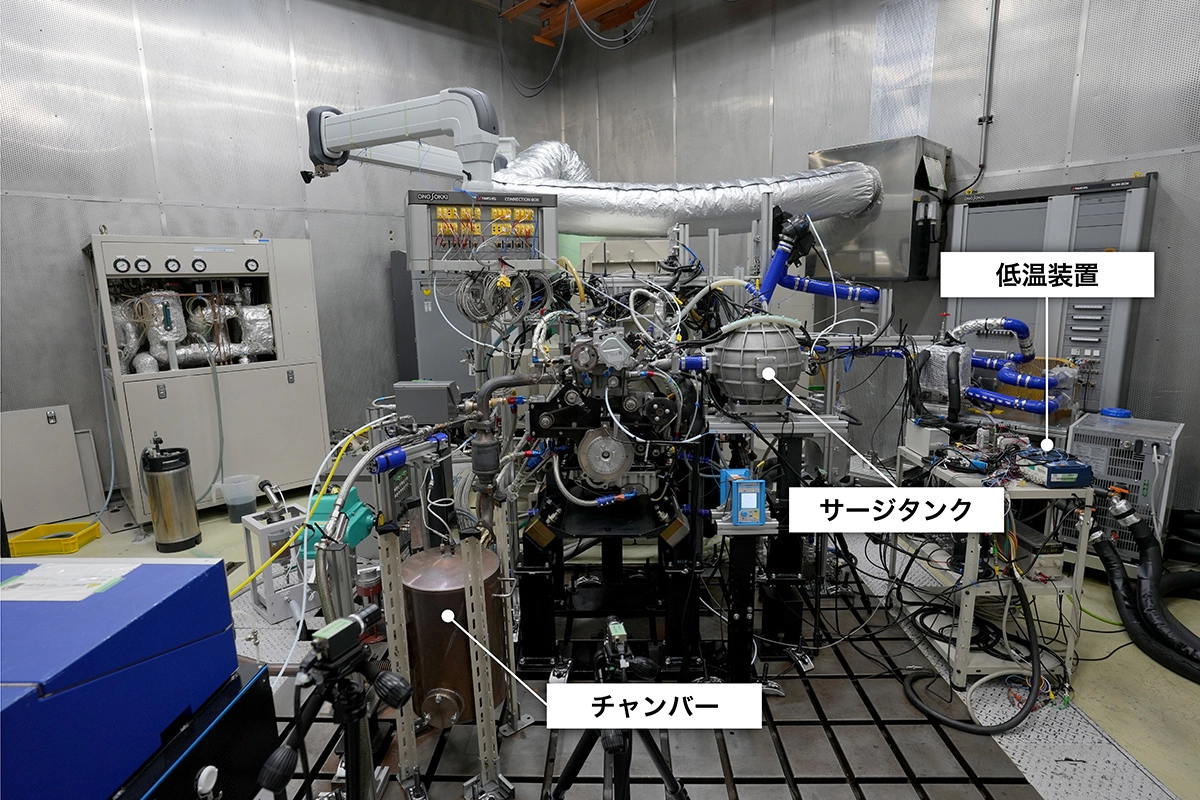
単気筒性能エンジンベンチ
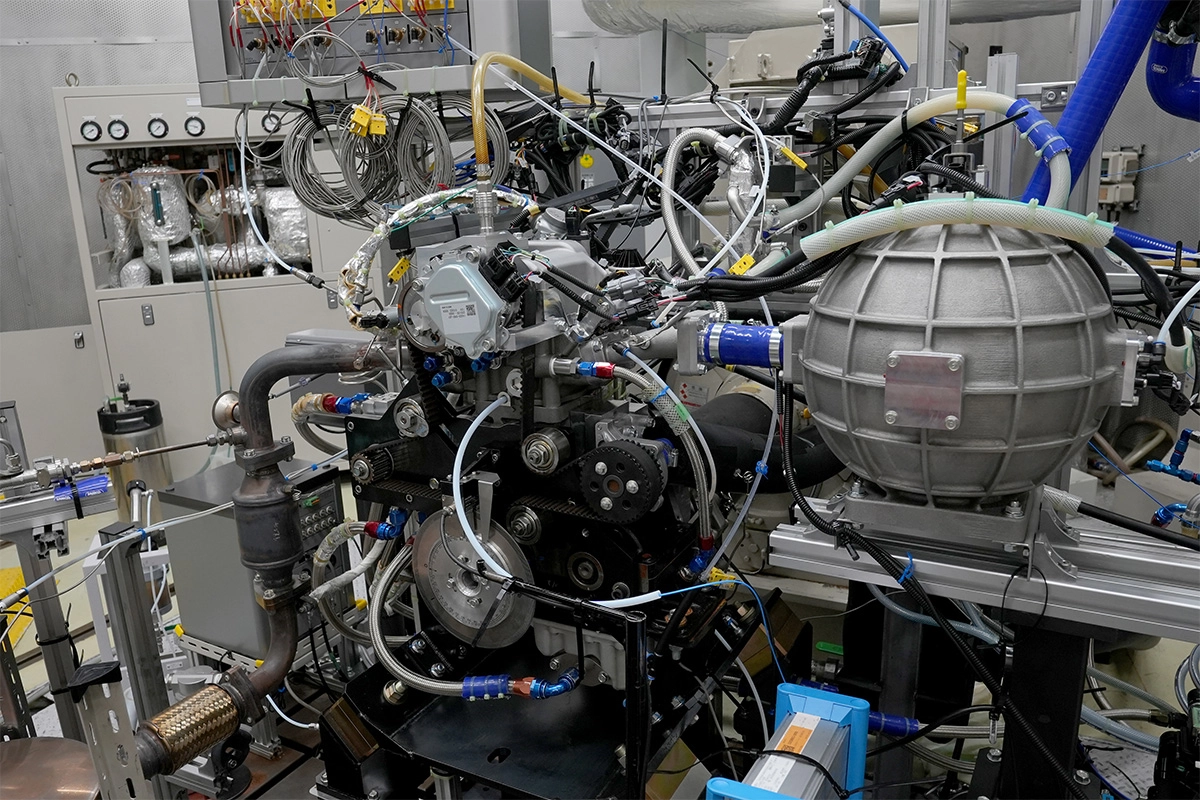
コントロール室
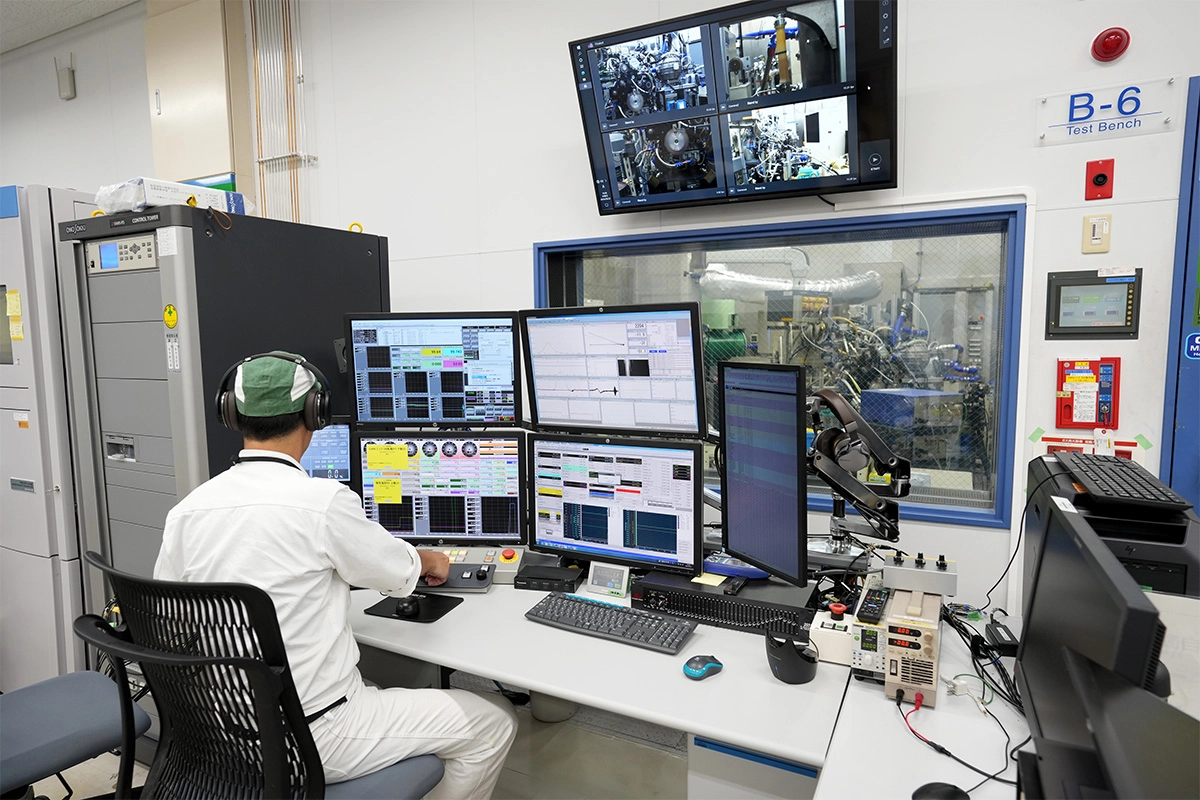
単気筒性能エンジンベンチ
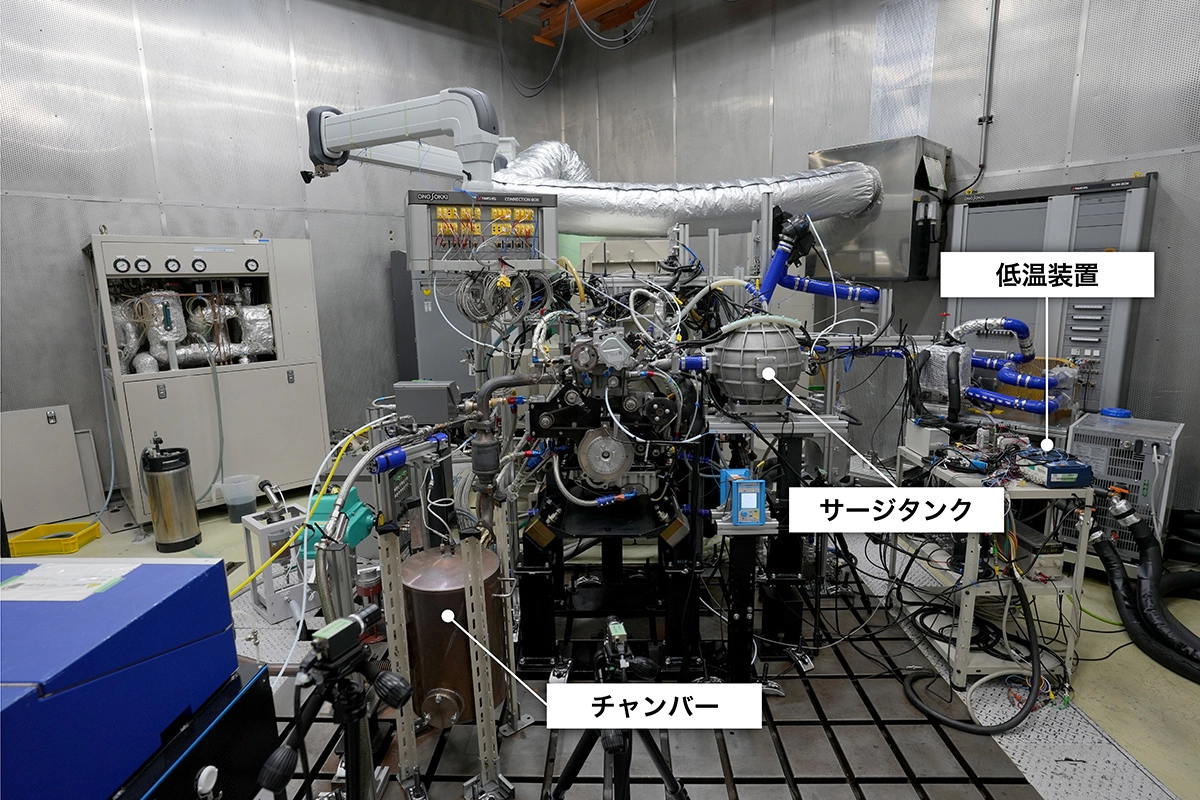
単気筒性能エンジンベンチ
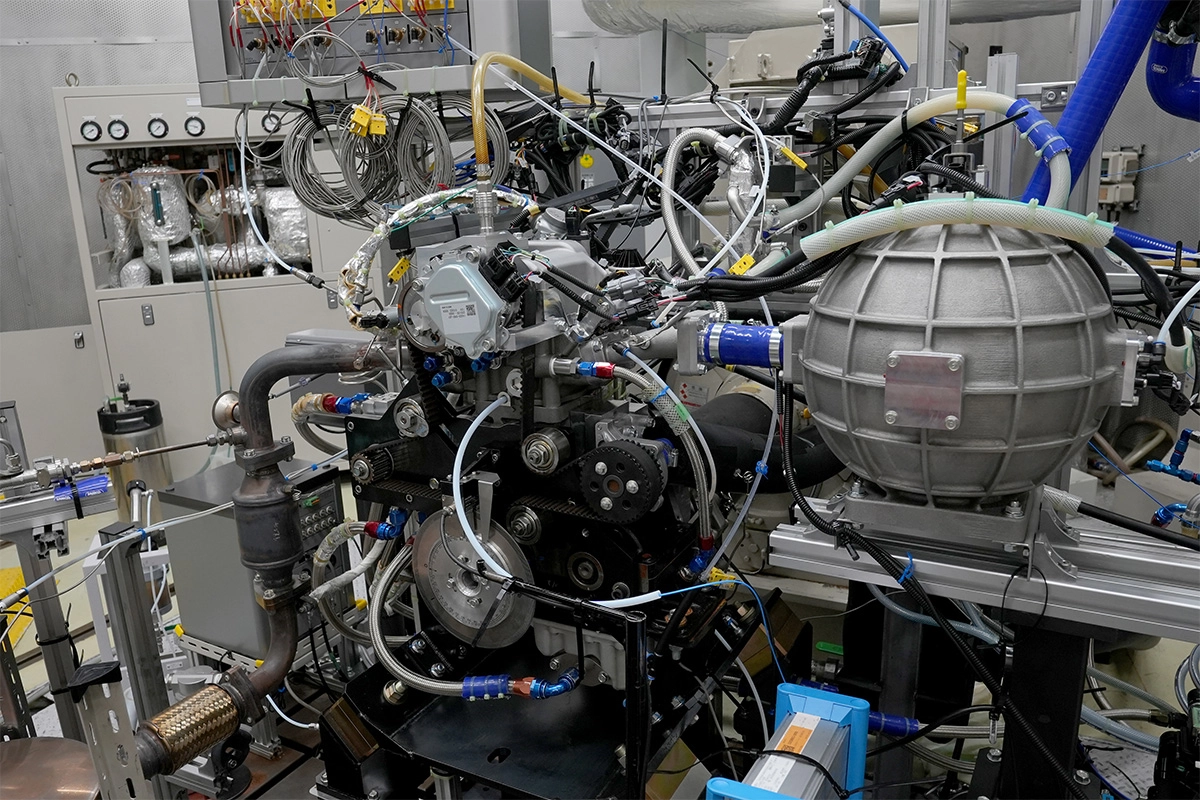
コントロール室
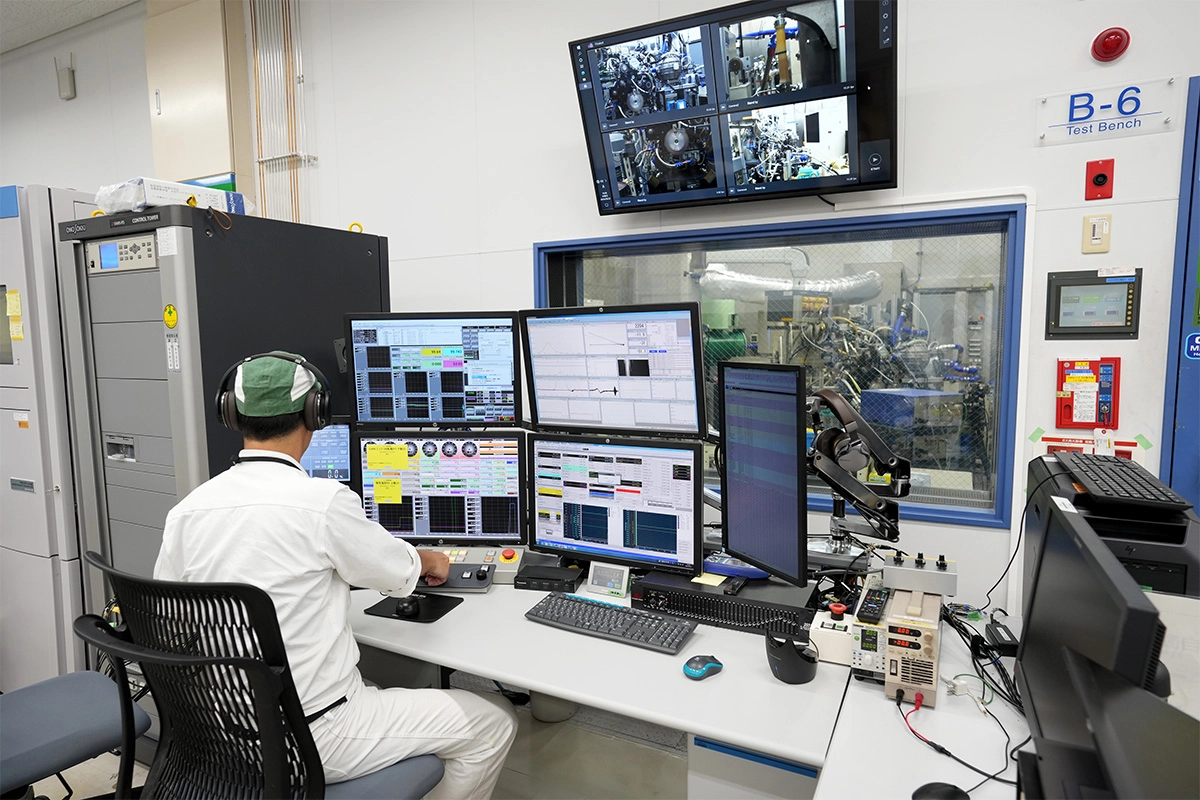

単気筒可視化エンジンベンチ
通常は外から見えない燃焼を目に見える状態にする装置が単気筒可視化エンジンベンチだ。CAEや単気筒性能エンジンベンチで基本諸元を絞り込んだ後、燃焼が狙いとおりになっているかどうかを検証するために単気筒可視化エンジンベンチを用いる。燃料の噴霧や混合気の流動、あるいは燃焼を実際に人の目で見て理解を深め、効率のいい燃焼開発につなげるのがこの装置の狙いだ。
試験室には特別に製作された単気筒可視化エンジンが床に固定されている。シリンダー部は耐熱温度の高い石英ガラスでできており、内部が透けて見える状態。シリンダー内の様子を撮影する高速度カメラが、シリンダー全体と壁面付着の様子を狙える位置に設置できるようになっている。また、点火後に火炎が燃え広がる様子を燃焼室の下から捉えられるよう、石英ガラス製のピストンも用意している。
高速度カメラは通常1万コマ/秒で撮影。エンジン筒内で起きる現象をスローモーションで撮影し、後でじっくり観察することで事象解明を行なう。燃料を筒内に直接噴射する直噴エンジンの場合、近年はシリンダー壁面に付着した燃料がクランクケース内に混入して潤滑油と混ざるダイリューション(希薄化)が課題となっている。ダイリューションが起きると潤滑油の性能が低下して軸受などの損傷につながる可能性がある。この事象を回避するために燃料の壁面付着を減らしたい。可視化によるダイリューションの事象解明は、この装置の代表的な用途のひとつだ。

コントロール室
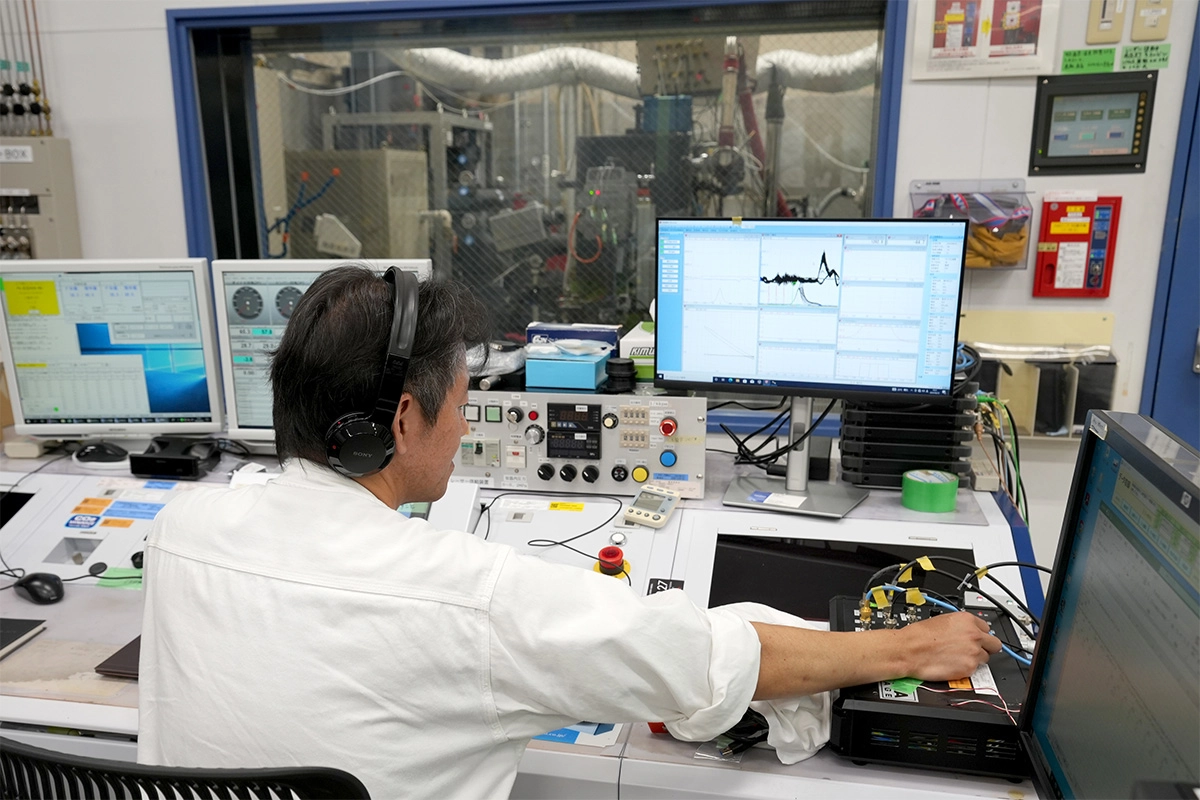
単気筒可視化エンジンベンチ
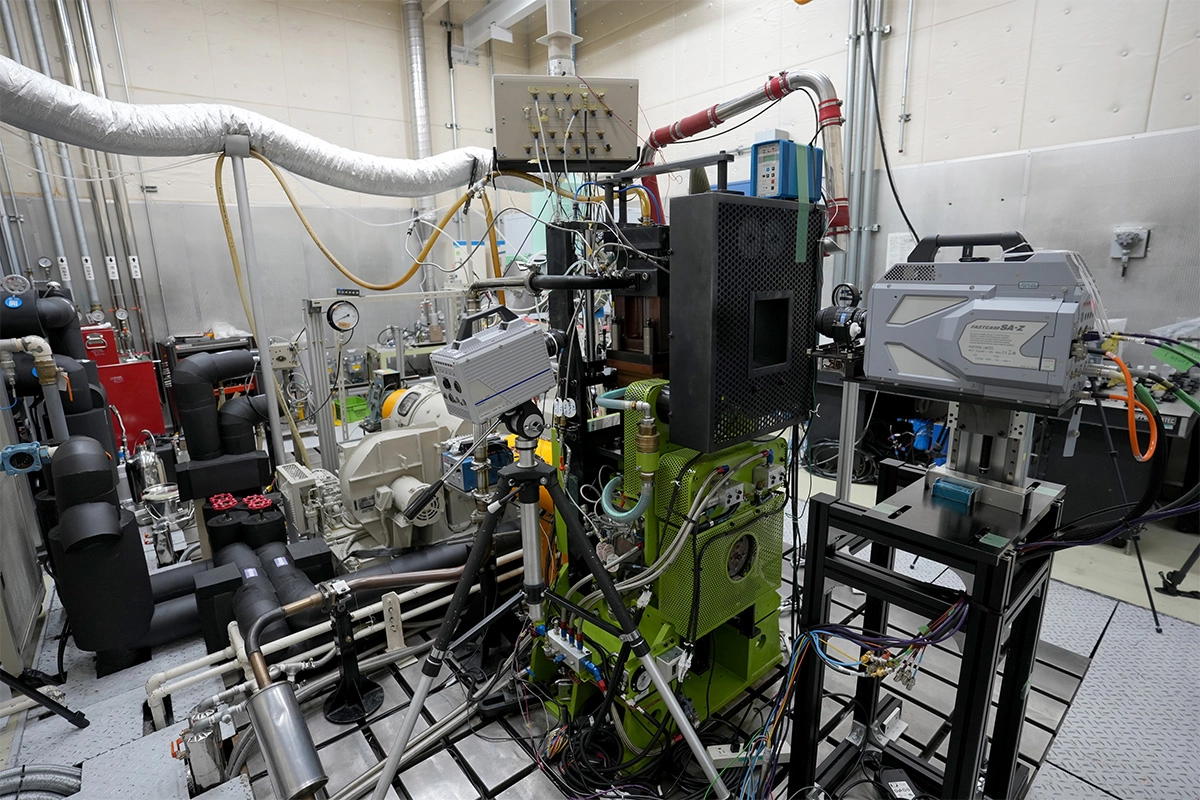
単気筒可視化エンジンベンチ
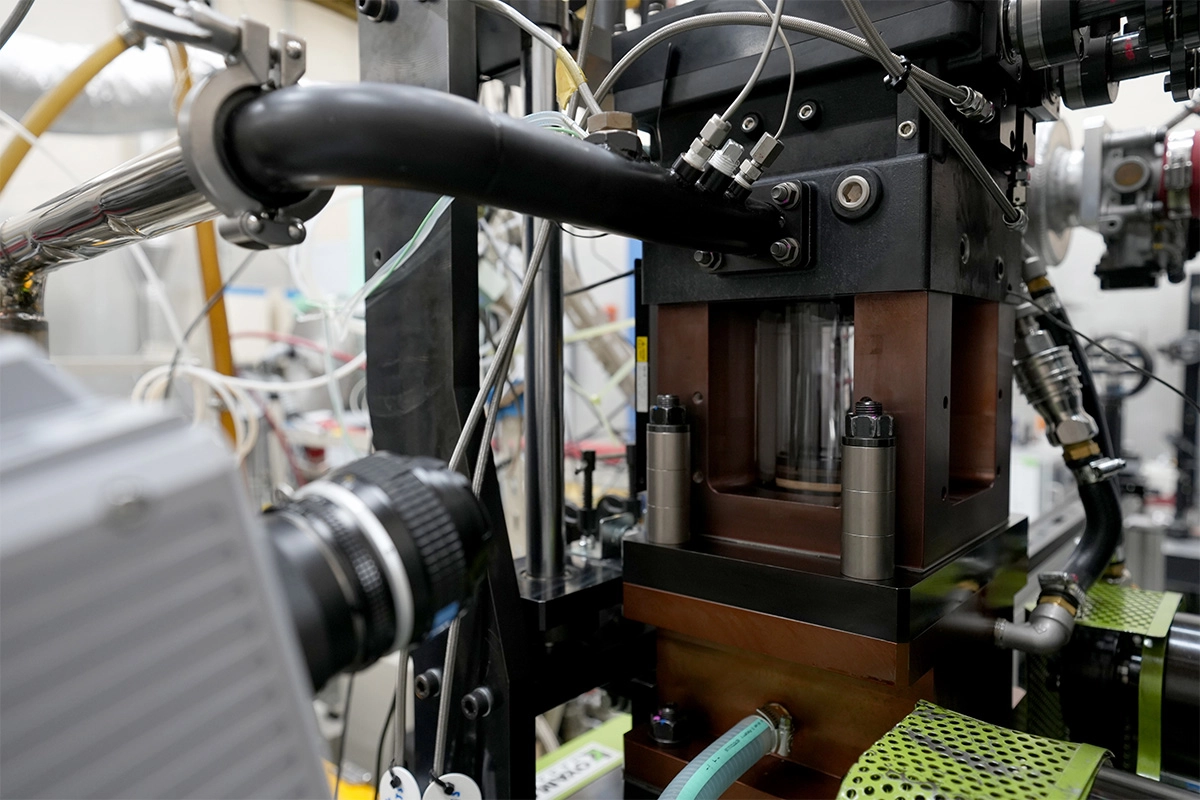
シリンダー壁面に向かってくる燃料の噴霧やシリンダー壁面に付着する燃料の様子を捉えるカメラ
単気筒可視化エンジンベンチ
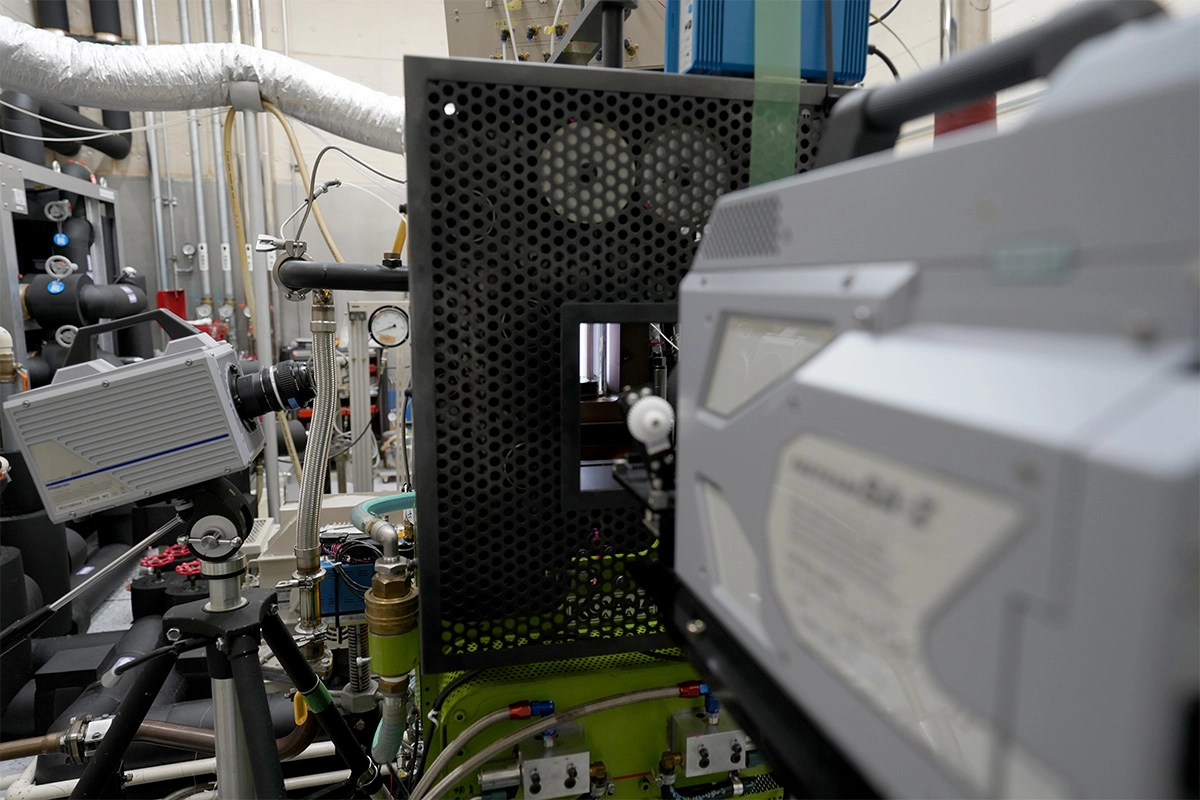
燃料の噴霧や火炎が燃え広がるシリンダー全体の様子を捉えるカメラ
コントロール室
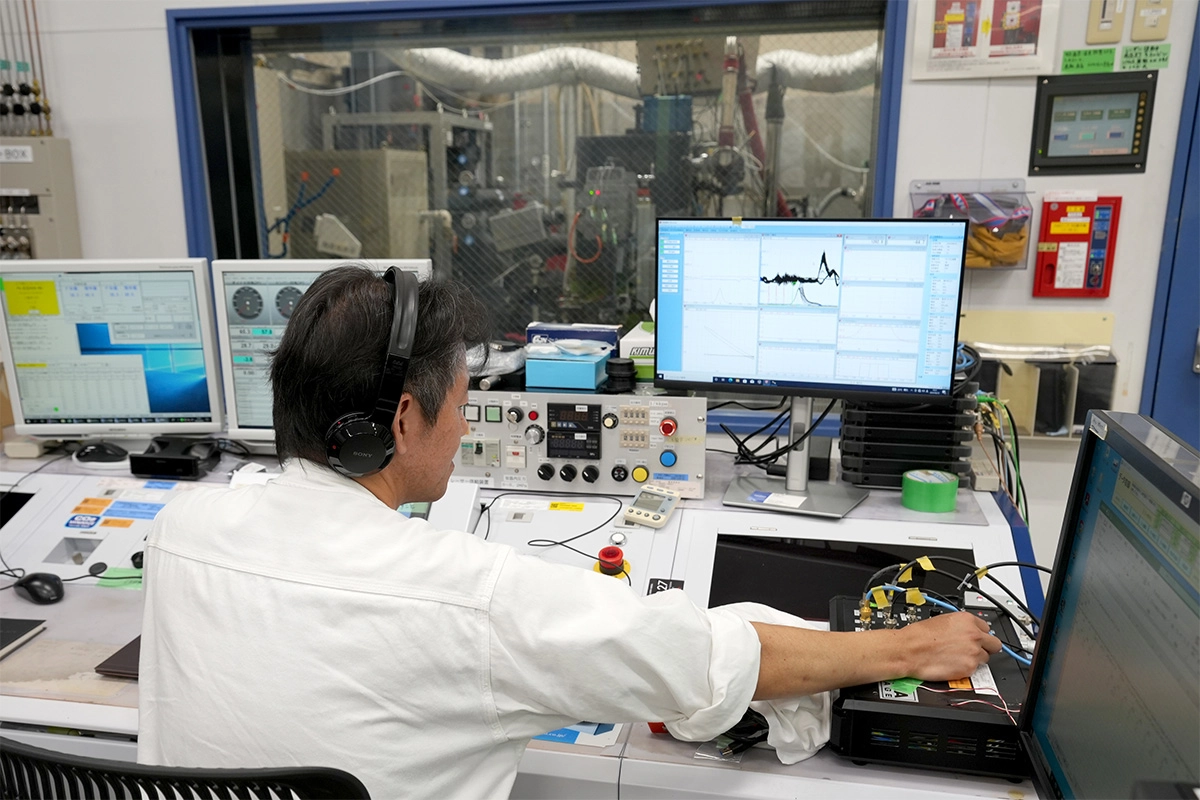
単気筒可視化エンジンベンチ
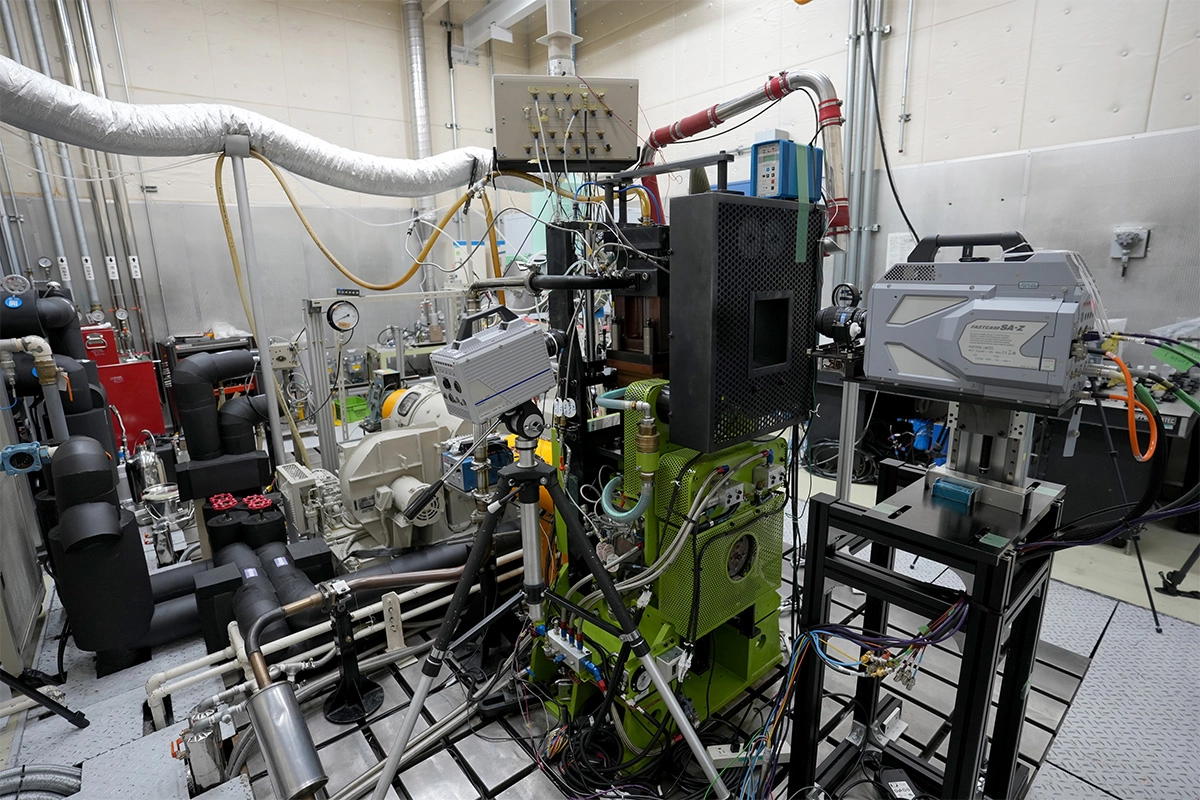
単気筒可視化エンジンベンチ
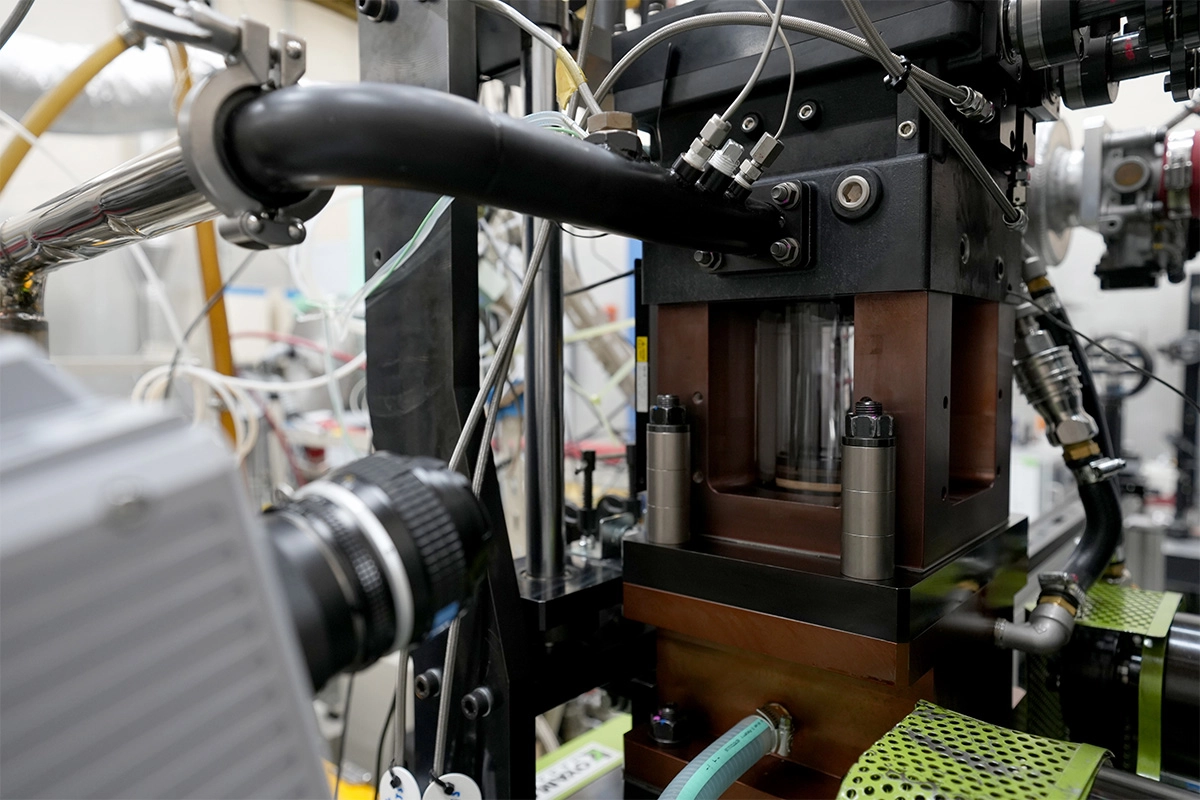
シリンダー壁面に向かってくる燃料の噴霧やシリンダー壁面に付着する燃料の様子を捉えるカメラ
単気筒可視化エンジンベンチ
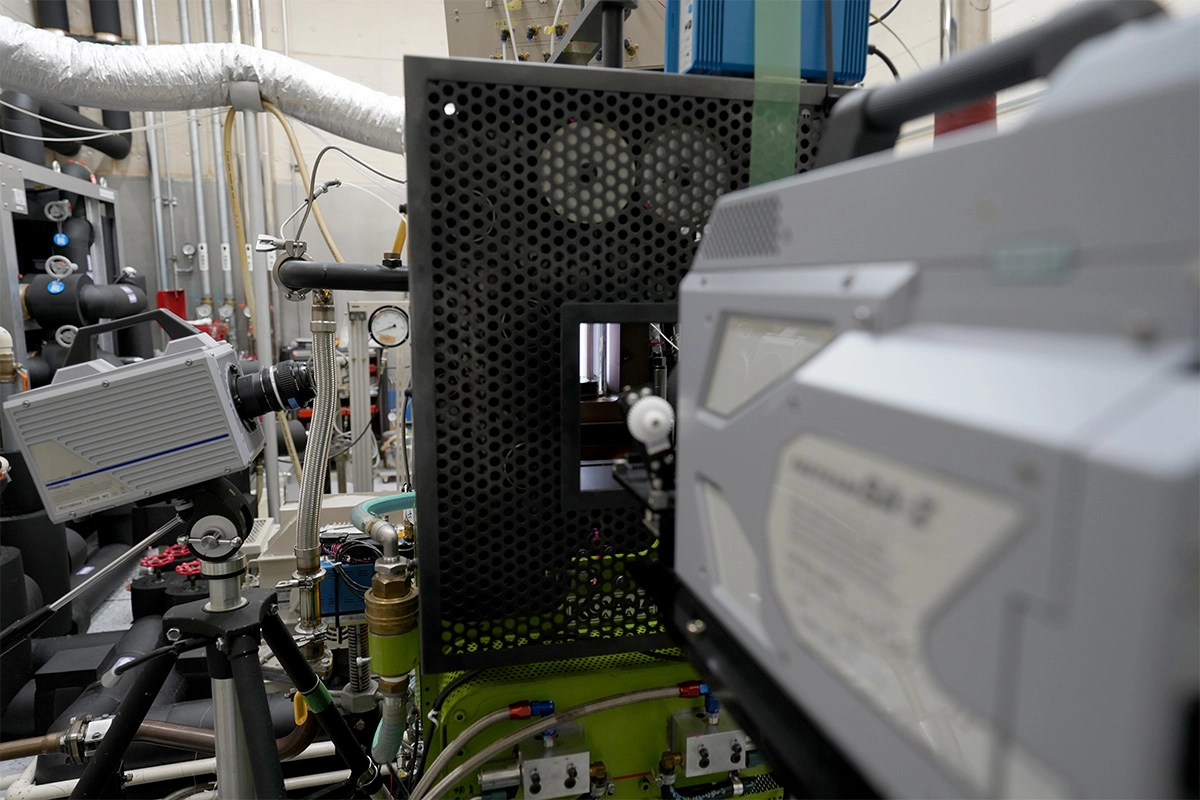
燃料の噴霧や火炎が燃え広がるシリンダー全体の様子を捉えるカメラ
コントロール室
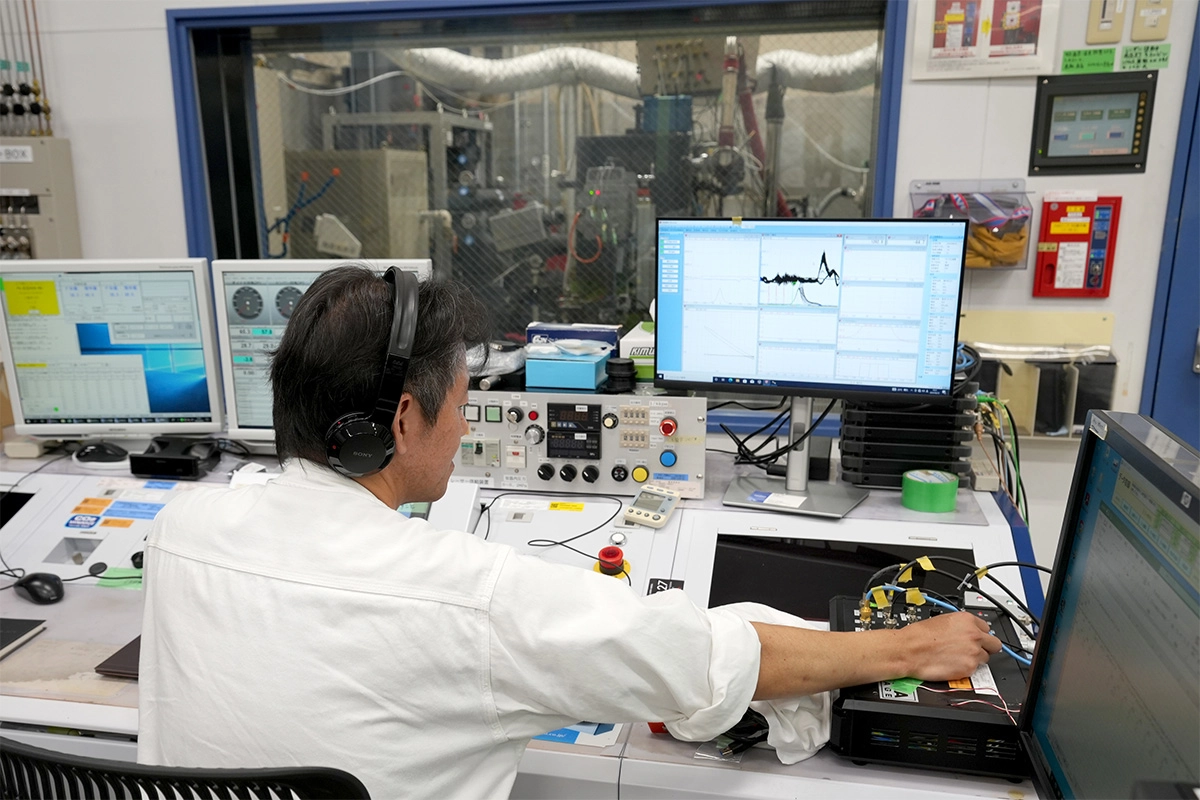

ボア、ストロークなどの諸元は実機とまったく同じにできる。ピストン冠面は交換が可能。ポート形状やインジェクターの位置も変更可能。燃料の噴射圧は調整の幅を持たせており、過給を再現することもできる。水温が低いと壁面に付着した燃料が気化せず、すすが形成される。試験室にはエンジン冷却水の冷却装置が設置してあり、水温0℃などの低温条件でテストできるようになっている。エミッションの低減に結びつく事象解明も、単気筒可視化エンジンベンチの役割のひとつだ。
計測で得られたデータは、シミュレーションで検討したとおりになっているかどうかの検証にも用いる。技術者がシミュレーションの結果から頭に思い描いていた事象が実際にそのとおりなのかどうか、可視化画像を見ると一目瞭然のため、認識合わせに役立っている。
高速度カメラによる撮影は可視化技術のひとつであり、吸気行程、圧縮行程、膨張行程、排気行程の各工程で起きる筒内現象に応じ、PIV※1(粒子画像流速測定法)やシャドウグラフ法※2など、最適な手法を用いて可視化を行なっている。
※1 Particle Image
Velocimetryの略。トレーサ粒子を混入した吸気にレーザーシートを照射し、粒子画像の移動から吸気の速度と方向を求める可視化手法。
※2 光源とスクリーンを用い、混合気の濃度の変化を可視化する手法。
燃料の噴霧や火炎が燃え拡がる様子(スローモーション映像)
タイヤフォース&モーメント計測試験機
車両の運動性能を語る上で欠かせないのが、タイヤ性能だ。クルマが地面に接地しているのはタイヤのみ。どんなに高性能なパワーユニットや車体を開発しても、タイヤの力を超える運動性能を出すことはできない。このため、タイヤの力を知ることが大切。タイヤフォース&モーメント計測試験機は車両設計の基本である“タイヤを知る”ための装置だ。
コーナリングやブレーキングなど、走行中のタイヤが遭遇するさまざまなシーンを台上で再現し、各シーンでタイヤが発生するフォース(力)とモーメント(軸まわりの回転運動)、いわゆる六分力を計測するのがタイヤフォース&モーメント計測試験機だ。いわばタイヤの運動能力テストを行なう装置と言える。完成車の基本特性を決めるにあたり、その基礎となるデータをここで収集。開発の初期段階でタイヤに関する詳細な特性が得られるため、開発プロセスにおける手戻りが減ると同時に性能の引き上げにつながり、完成車をタイムリーにお客様に届けられるようになる。
タイヤの特性を計測し数値化するのがこの装置の役割で、コンピューターの中でシミュレーションを行なうためのタイヤモデルを作ることが目的の一つ。近年の車両開発では開発効率化の観点から、ドライビングシミュレーターを活用している。ドライビングシミュレーターには、タイヤの振る舞いを数値化したタイヤモデルが欠かせない。タイヤモデル作りに必要なデータを得るために、タイヤフォース&モーメント計測試験機は重要な試験機といえる。
タイヤはホイールに組み込んだ状態で装置に固定し、スチール製ベルトの上を転がる。ベルトは円筒状だが、実際の路面と同様の平坦な状況を再現するために、円筒状のベルトを2つのドラムで引っ張っている。タイヤの荷重に対してベルトが平坦な状態を維持できるように、平坦部の下にはエアベアリングを設置している。片側のドラムでベルトを回転させ、常用速度でのタイヤの6分力を計測する。
タイヤは荒れた路面のようなアンジュレーションがあるとタイヤ発生力が減る。これはタイヤがヒステリシス特性を持つため荷重抜けのような事象が発生するためだ。このような事象を再現するために、一般的にはタイヤ側を上下加振する方法が用いられるが、センサー類も一緒に加振されてしまうため、計測が困難になる場合がある。Hondaの試験機はタイヤにベルト側(路面側)から上下加振入力できるようにしており、アンジュレーション乗り越え時のような事象も詳細に把握することが可能。この機能を生かしサスペンションダンバーの特性検討にも活用している。
一方で、パーキングアシストのような極低速域の事象をシミュレーションするためのタイヤ特性計測も行なう。極低速域では常用域とはタイヤの特性が大きく異なるため、専用の計測を行なうことで、極低速域も表現できるタイヤモデルの作成を可能としている。
シミュレーションの走行条件に合わせて、適切なタイヤモデルを作る必要があるため、タイヤモデルの高機能化に合わせて計測モードも開発しており、その開発に合わせ、試験機も進化させている。
実際の車両もタイヤが無ければ走れないが、バーチャル空間でもタイヤモデルが無ければ、車両は走れない。モノづくりがバーチャル開発へ推移していくのに応じて、タイヤの特性試験機の役割はますます増していくことになる。

コントロール室
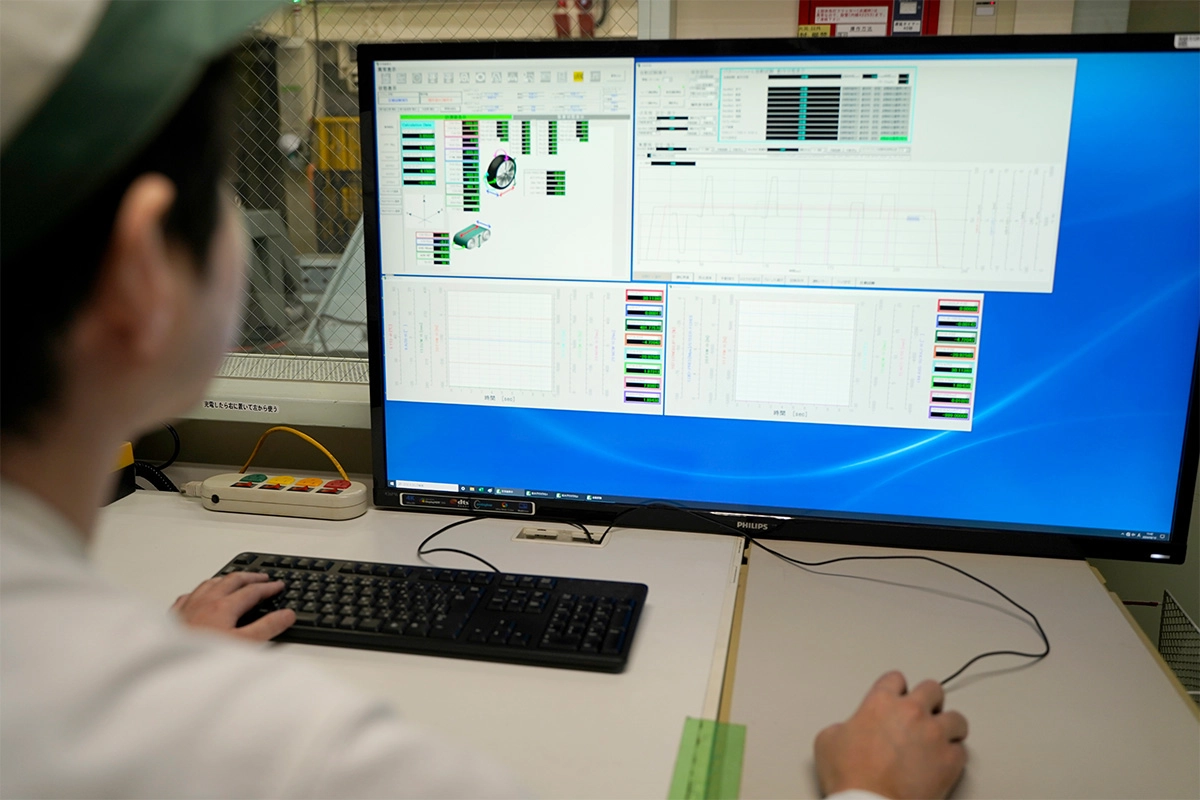
タイヤフォース&モーメント計測試験機
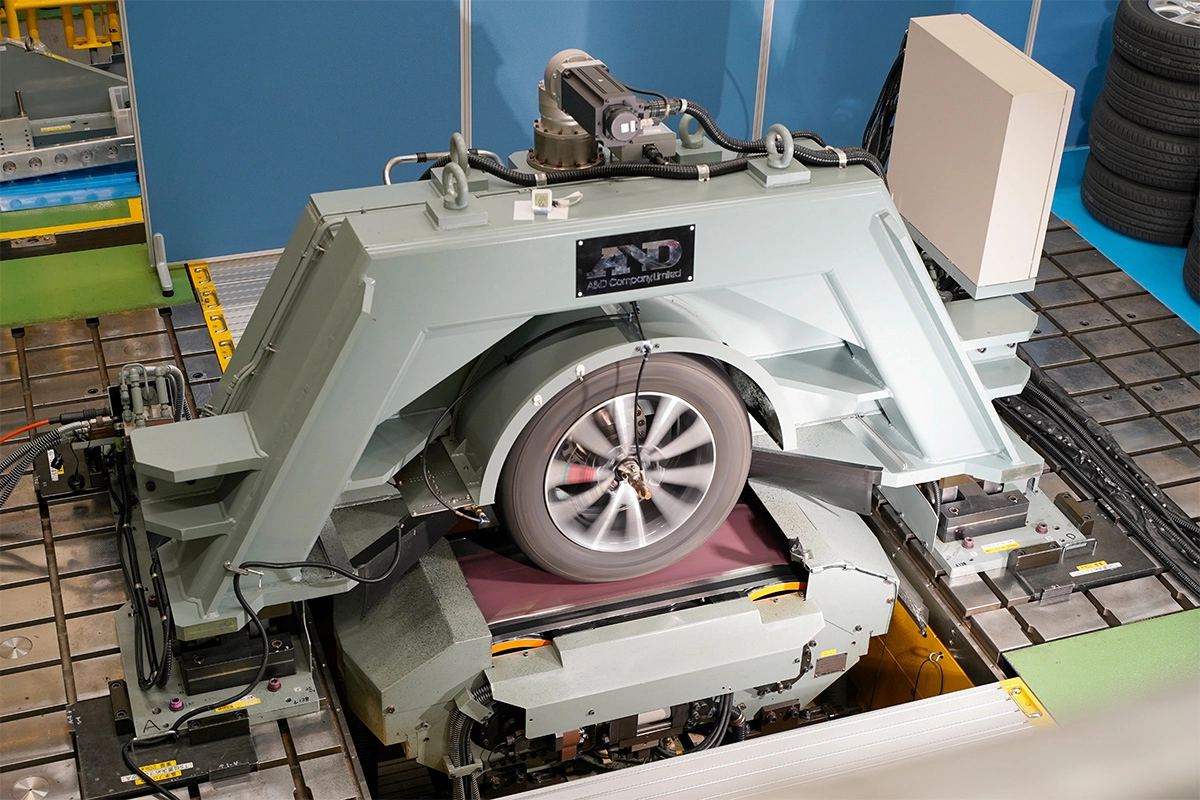
タイヤフォース&モーメント計測試験機
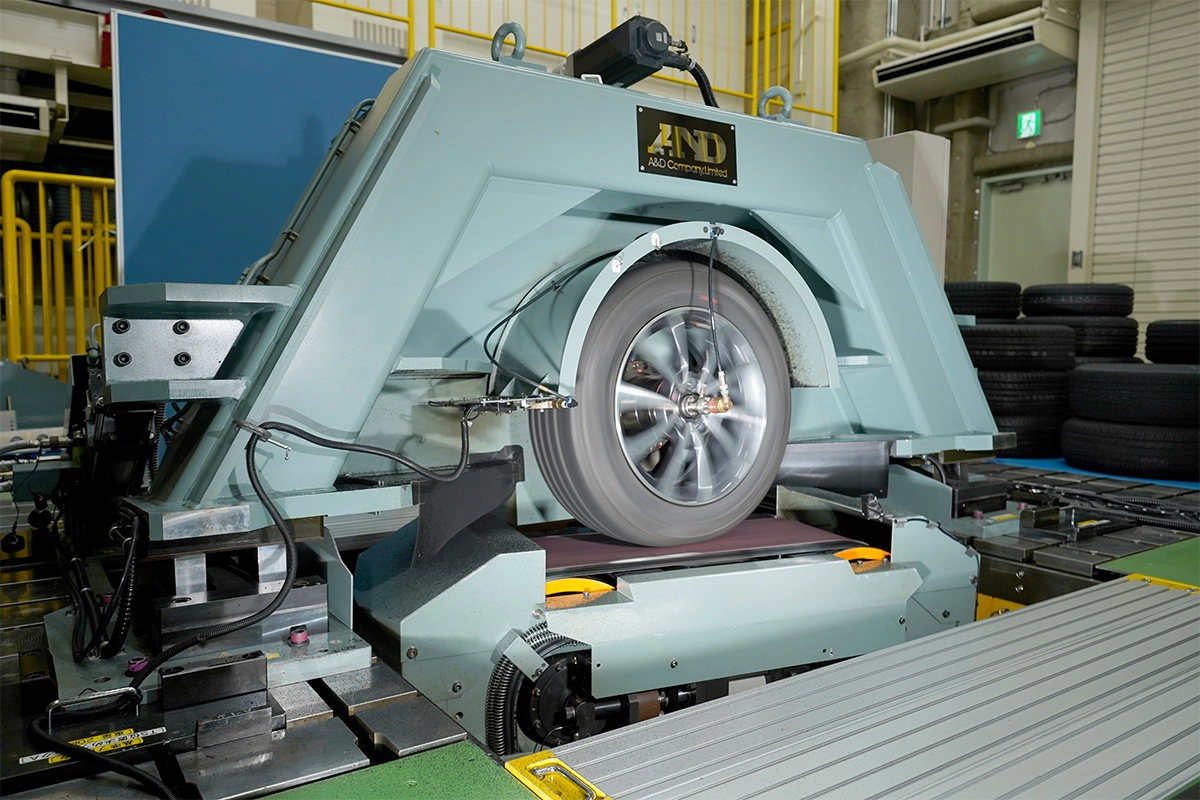
コントロール室
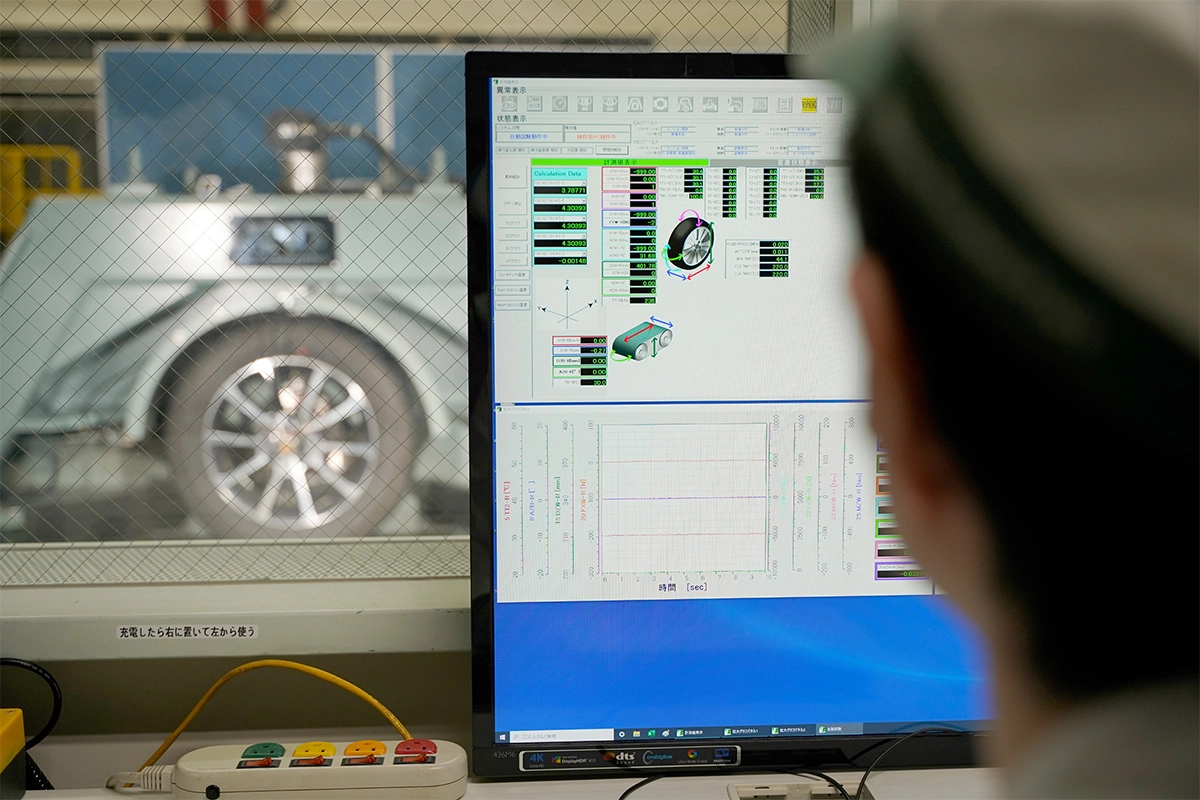
コントロール室
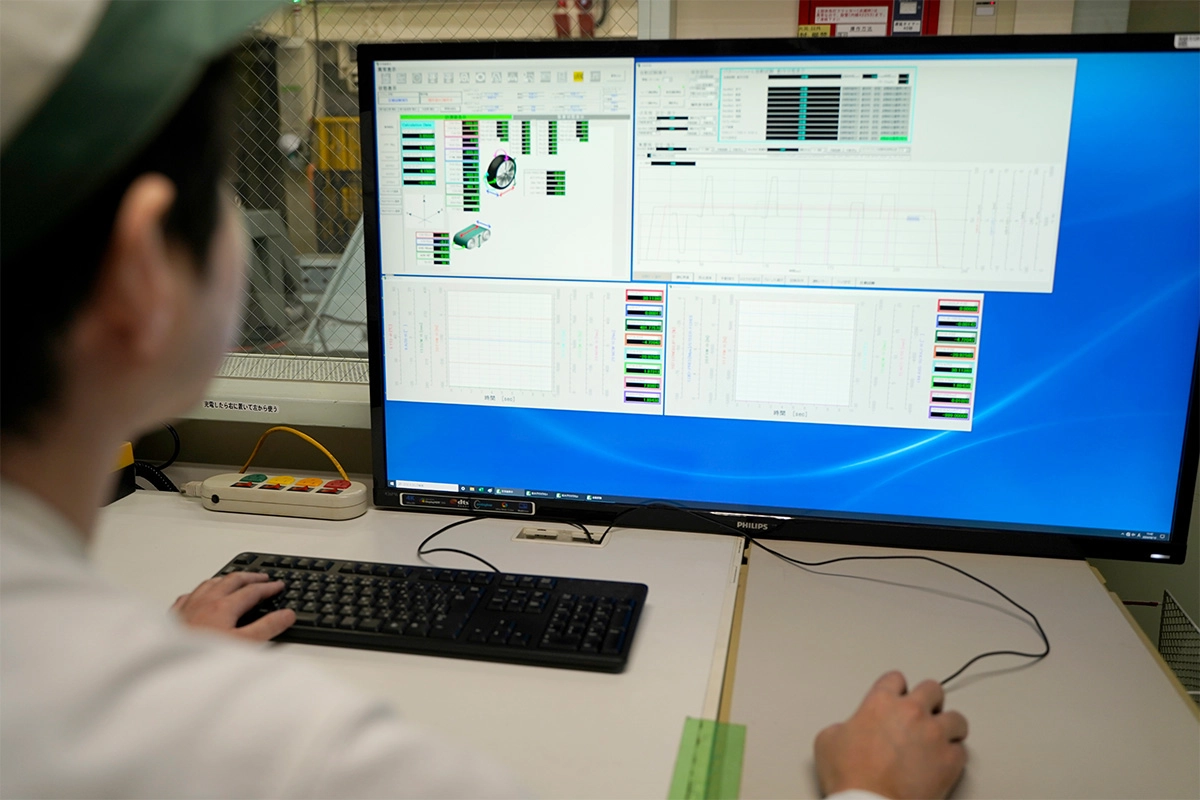
タイヤフォース&モーメント計測試験機
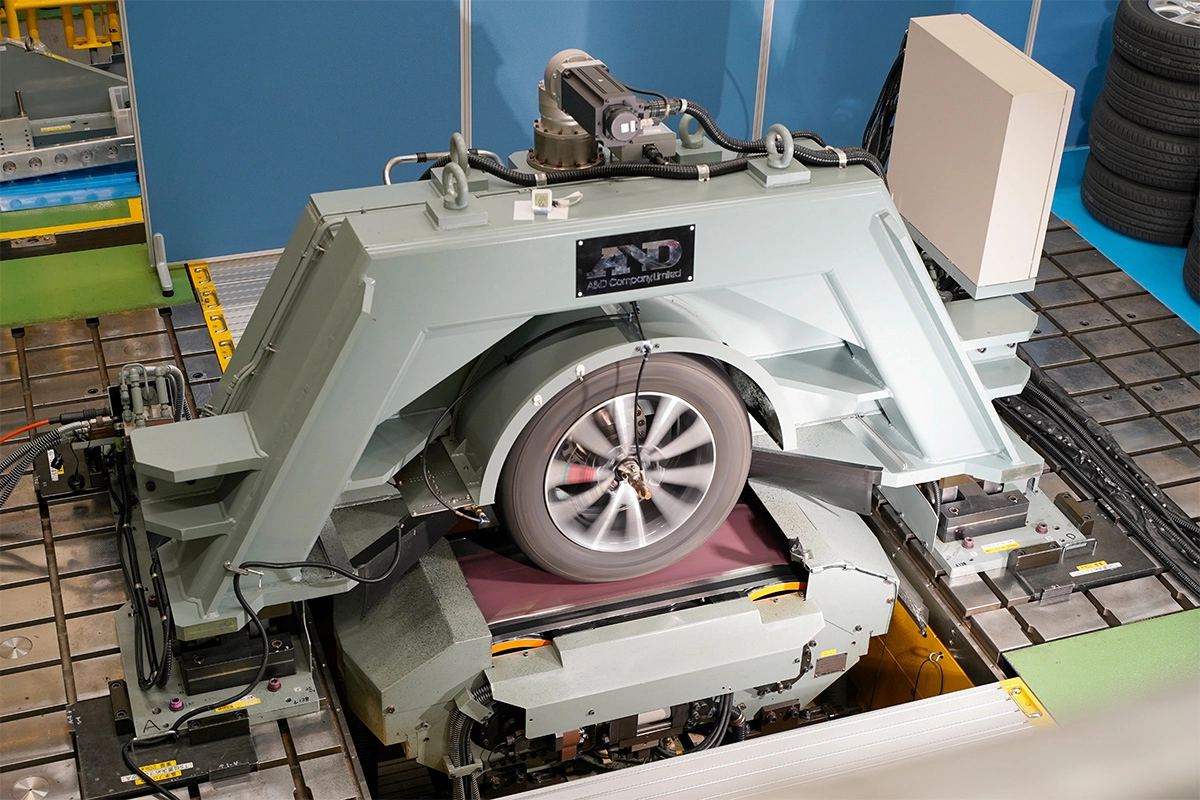
タイヤフォース&モーメント計測試験機
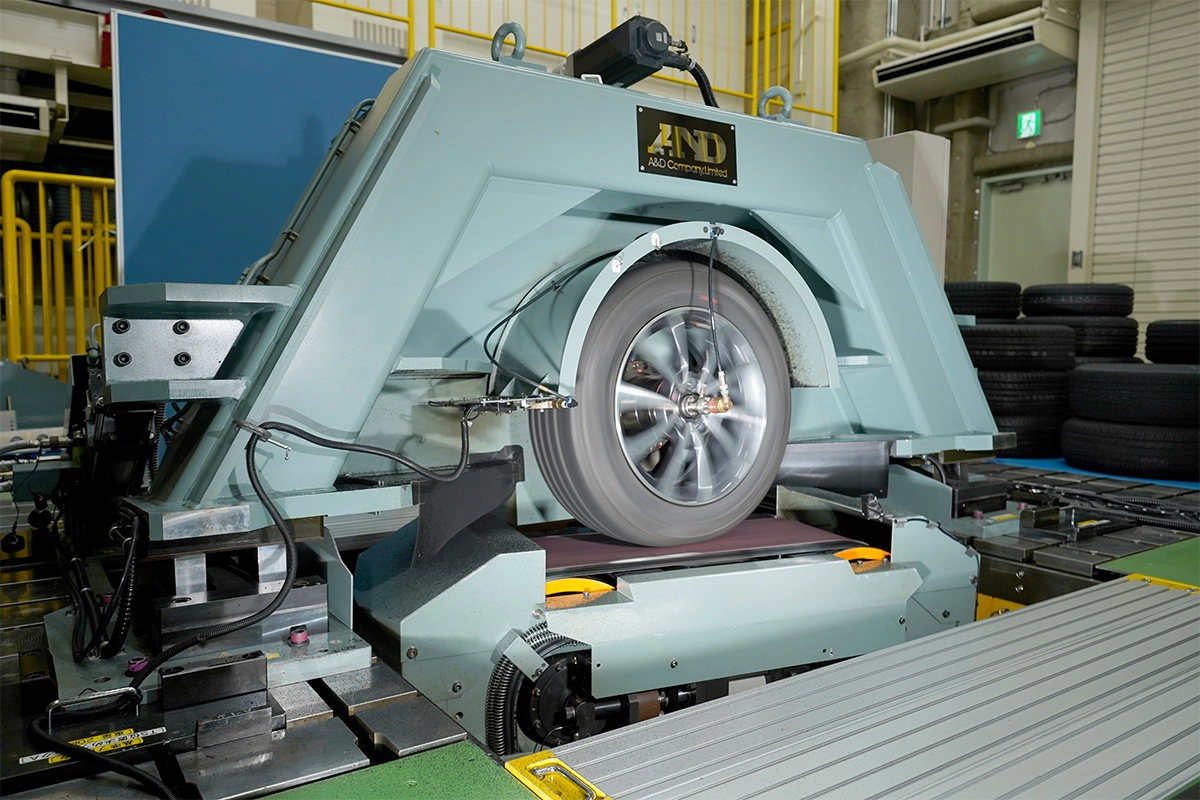
コントロール室
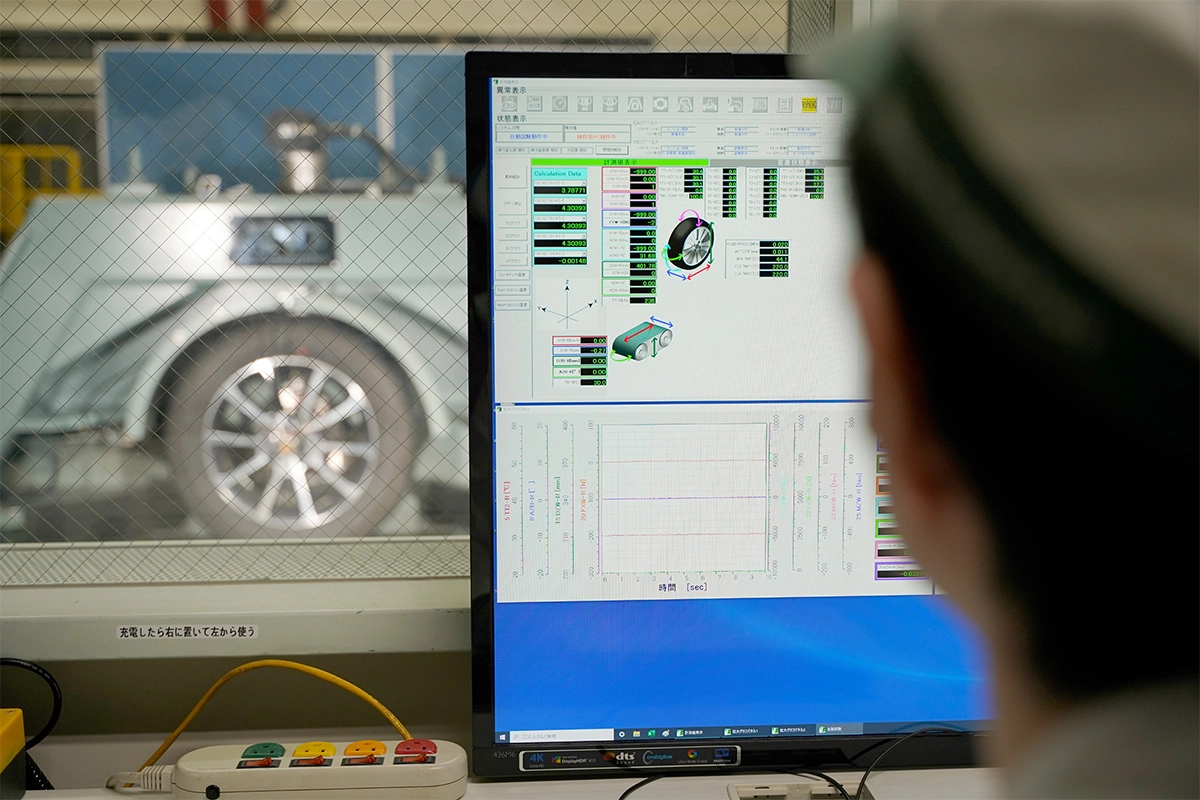
コントロール室
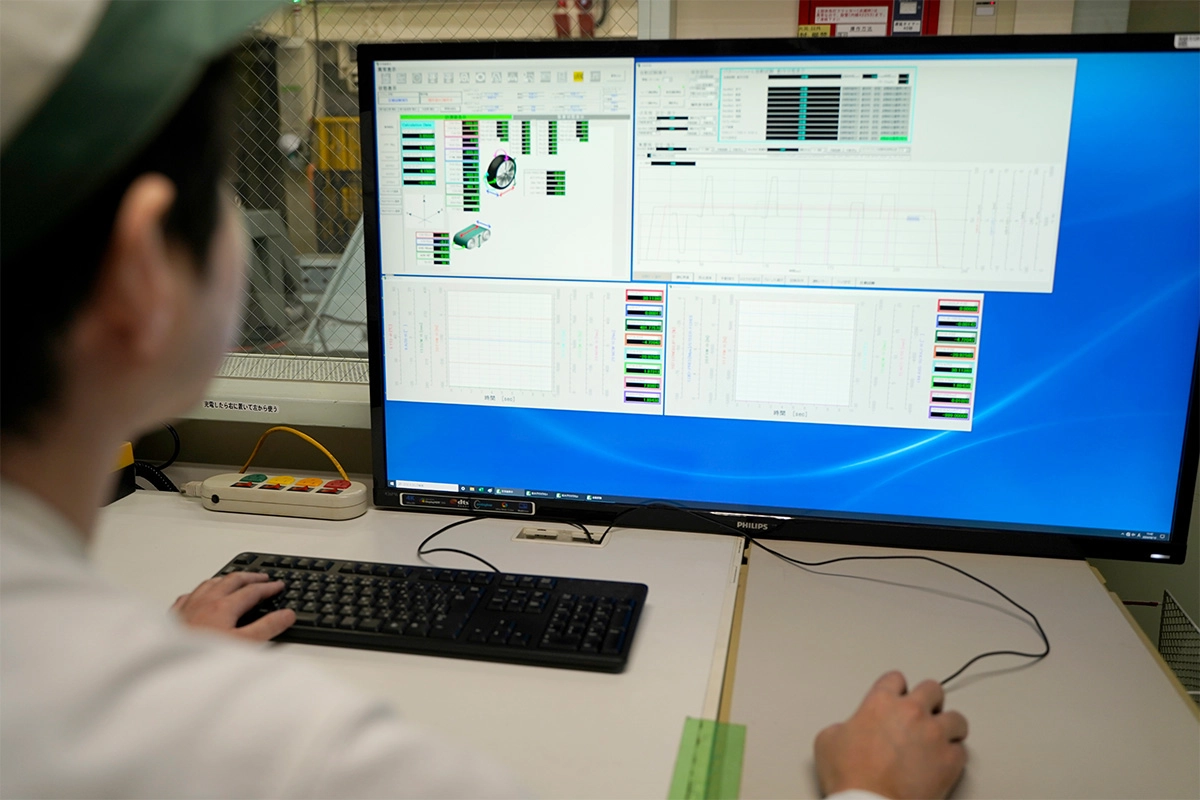

サスペンションテスター
サスペンションのキネマティクス(幾何学的特性)やコンプライアンス(ブッシュやアーム/リンク類の弾性変形)による特性を計測するのが、サスペンションテスターである。“キネマティクス”と“コンプライアンス”の頭文字をとって、K&C試験機とも呼ばれている。サスペンションの特性を計測・評価し、シミュレーションに適用することで、Hondaが目指す走りの質を高めることがこの装置の役割である。
サスペンションの特性は計算で予測することができるが、実車で必ずしも計算どおりの動きをしているとは限らない。実車で起こるさまざまな事象を解析・予測するために、サスペンションテスターでは機械としての基本的な特性の評価・分析を行ない、さらにシミュレーションソフトと連携することでより詳細な性能予測を可能としている。
装置の概要は以下のとおり。ジャッキアップポイントを利用して試験車両を設備に固定し、ステアリングに取り付けられた操舵アクチュエーター、およびタイヤ接地面の負荷入力テーブルの動作によって走行中のドライバーのステアリング操作やタイヤと路面の間に働く力を再現することで、サスペンションの特性を計測する。
大きな入力を与えた状態でもサスペンション特性を正確に評価するため、レーザー変位計によってボディの変形やずれを補正している。キャンバーやトーなどの角度は100分の1度レベルでの計測が求められ、ボディのわずかな変位も無視できないからだ。裏を返せば、人はそれだけ微小な変化を感じとるため、高い分解能で計測する必要があるということだ。

コントロール室
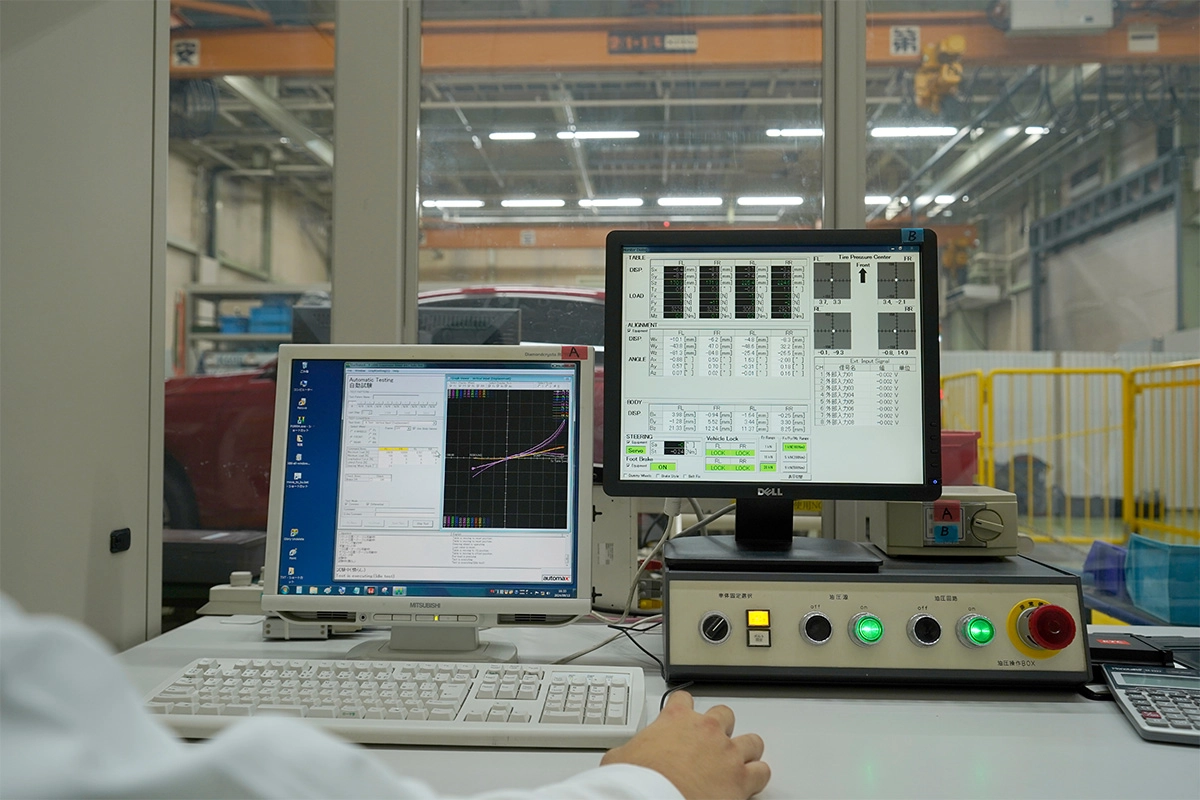
サスペンションテスター
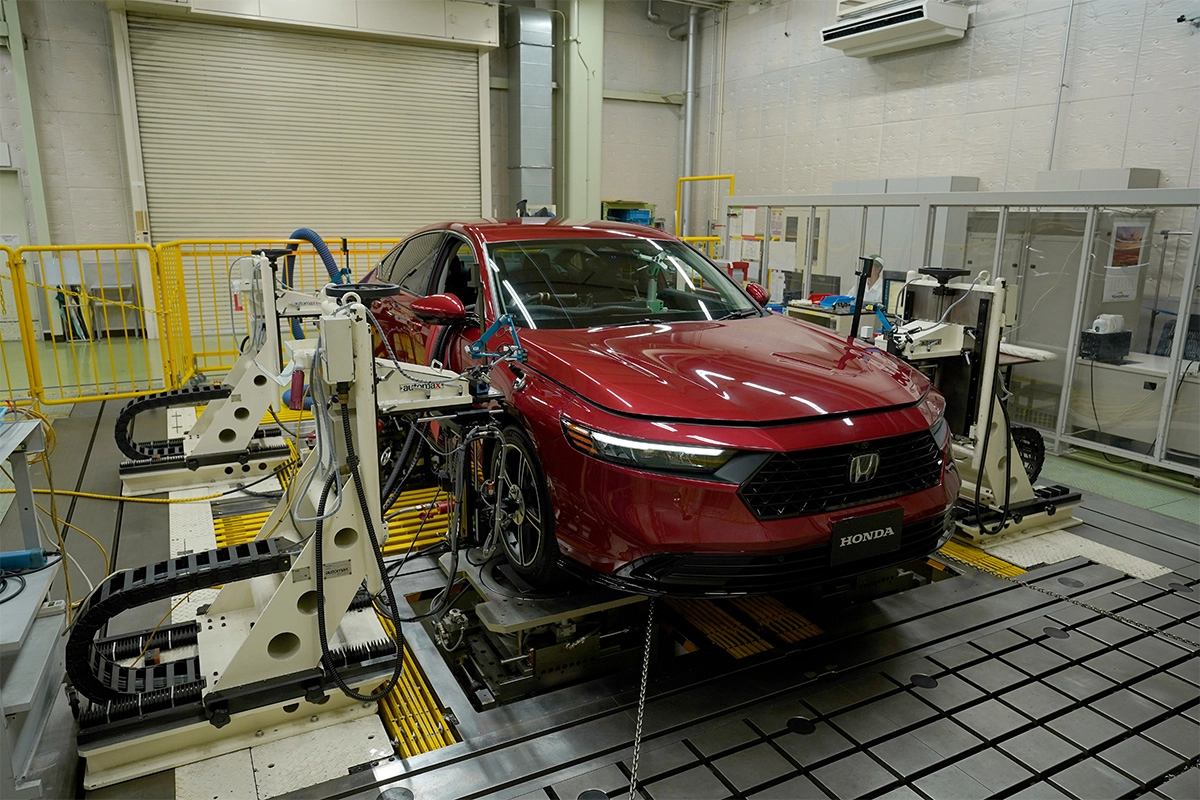
サスペンションテスター
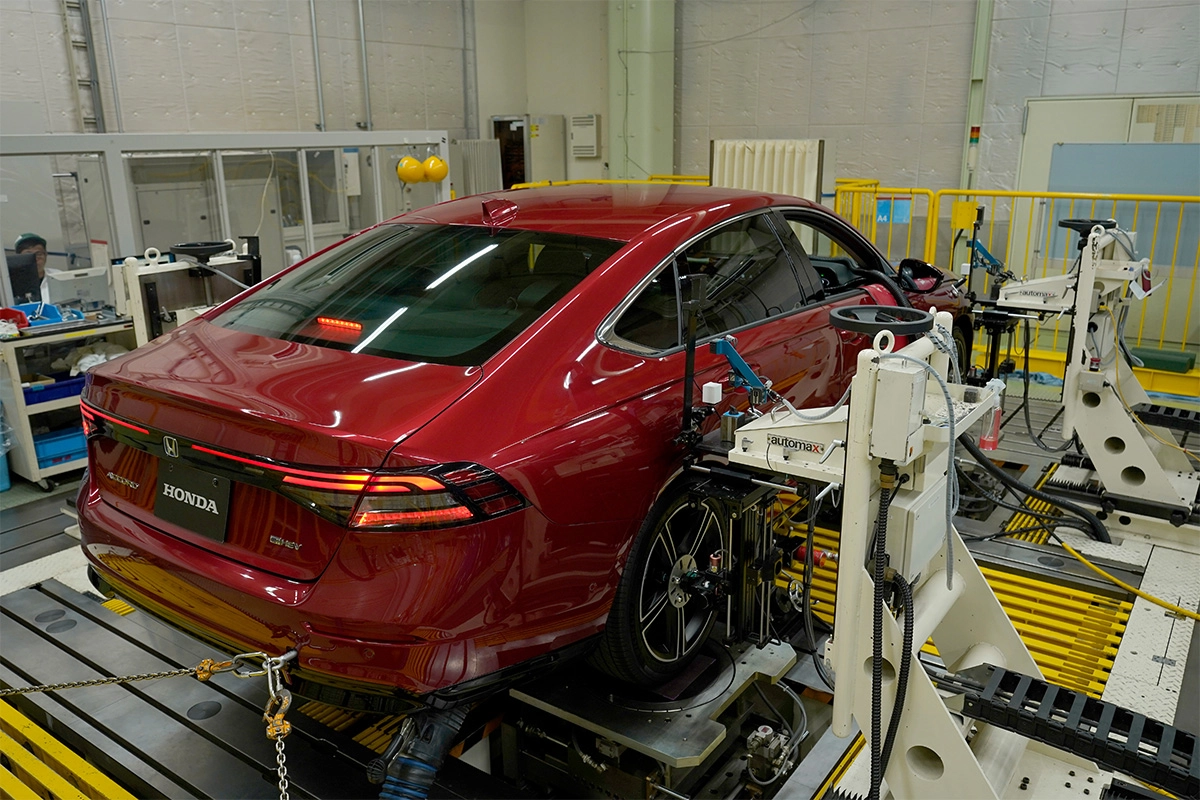
サスペンションテスター
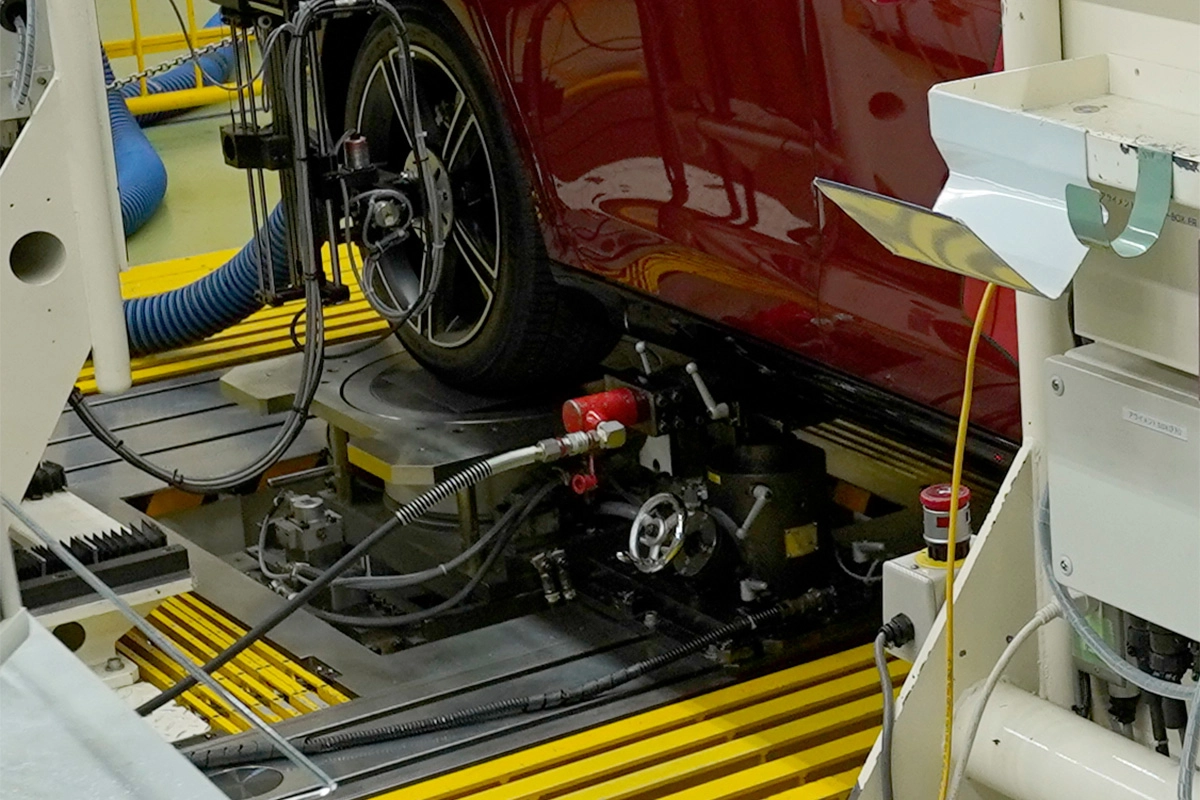
ジャッキアップポイントを利用して試験車両を設備に固定している様子
サスペンションテスター
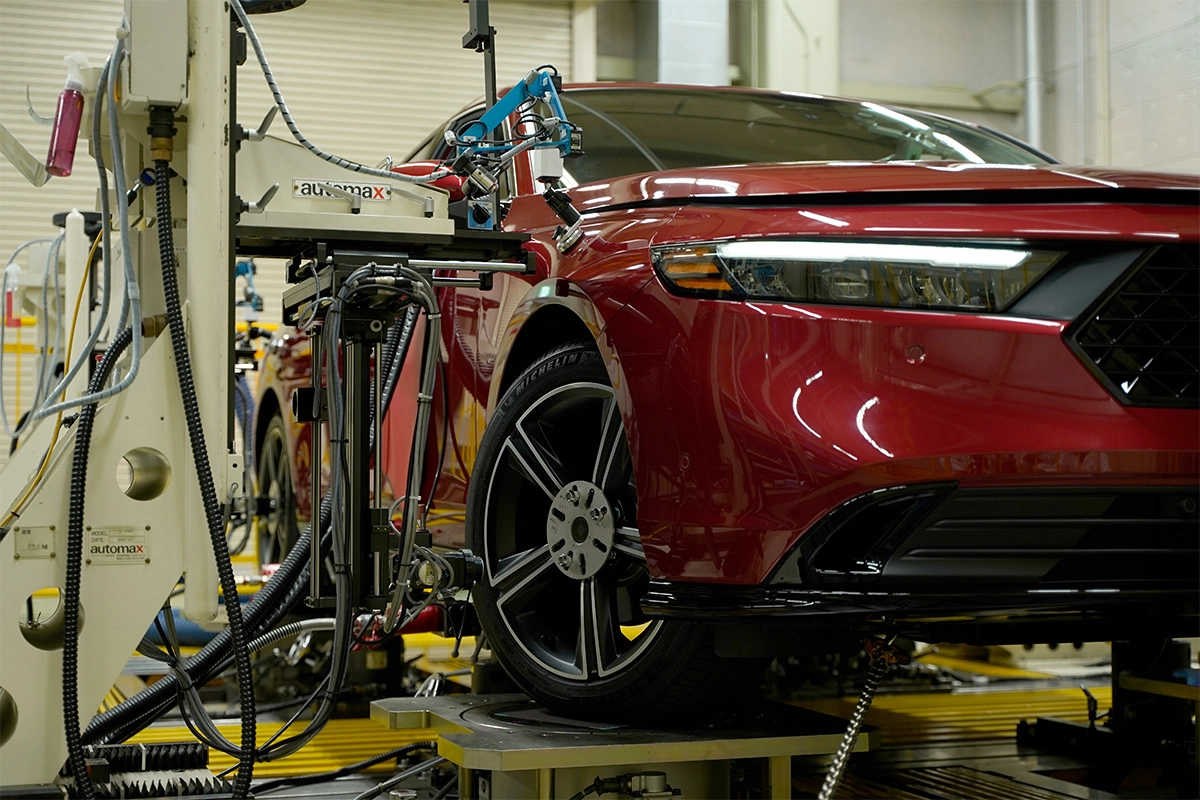
サスペンションテスター
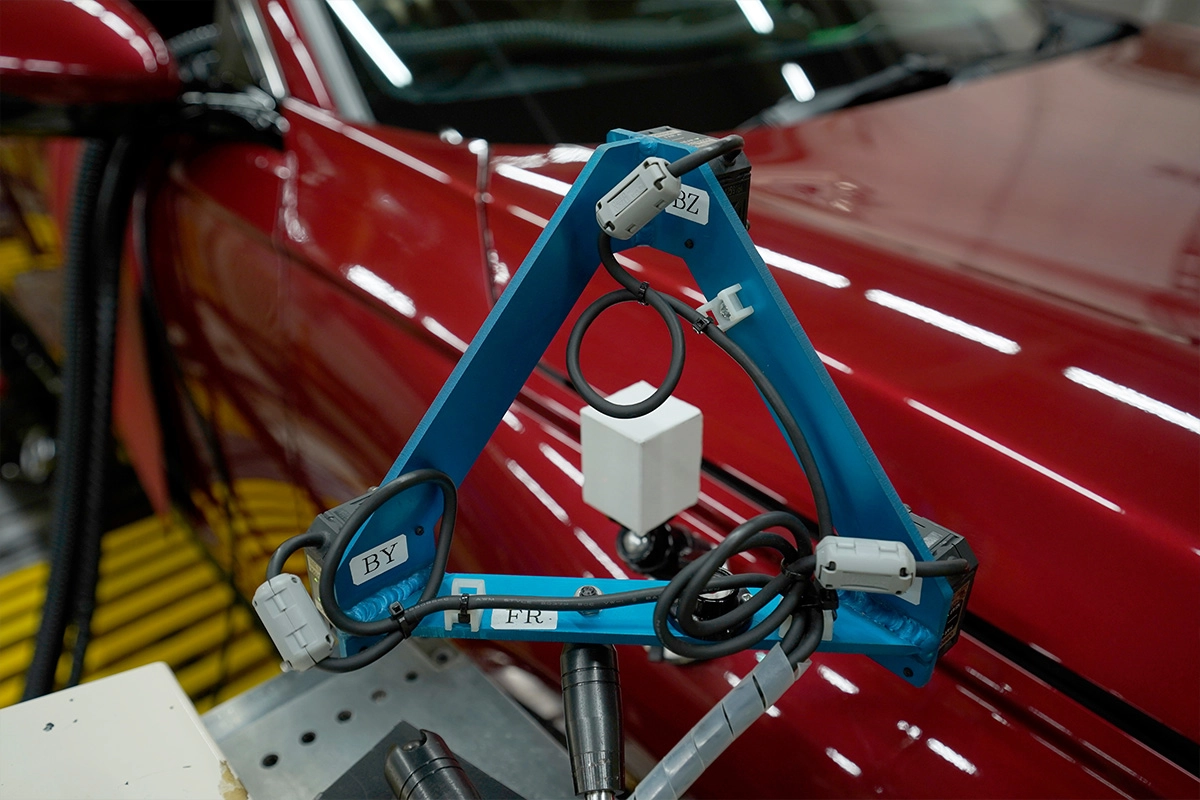
レーザー変位計
サスペンションテスター
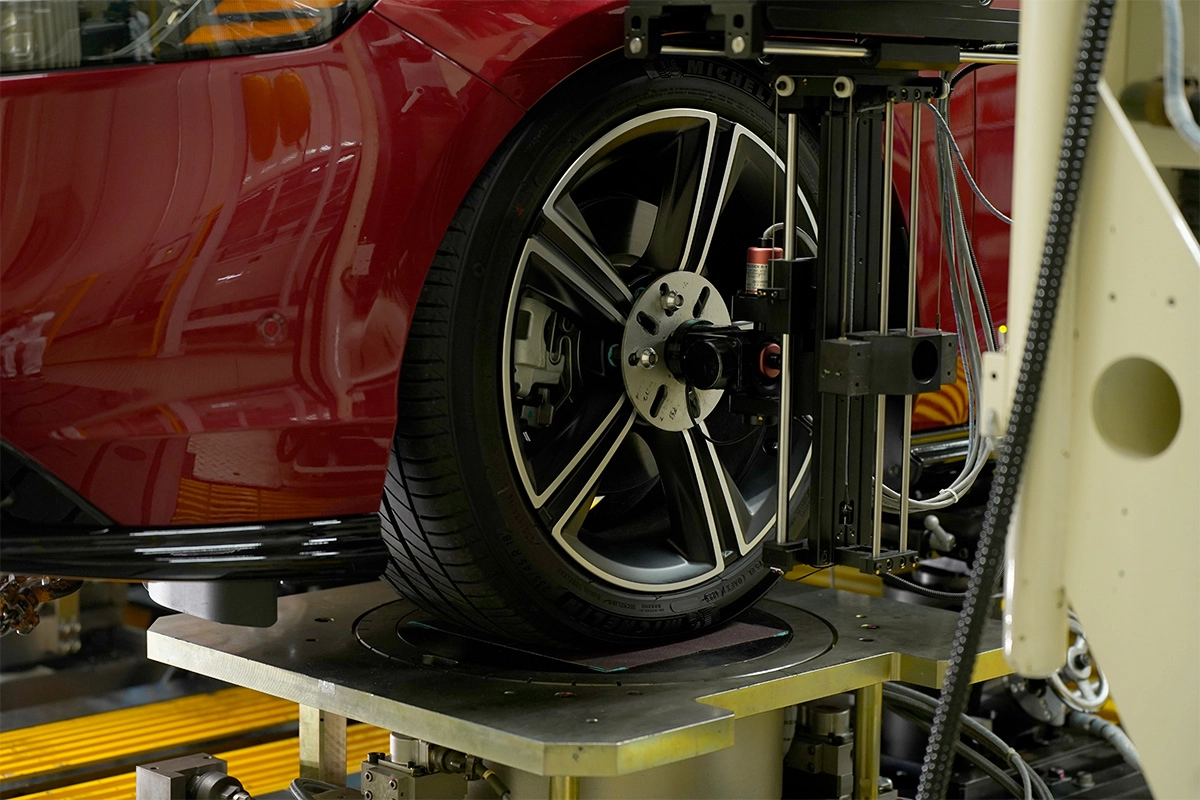
サスペンションテスター
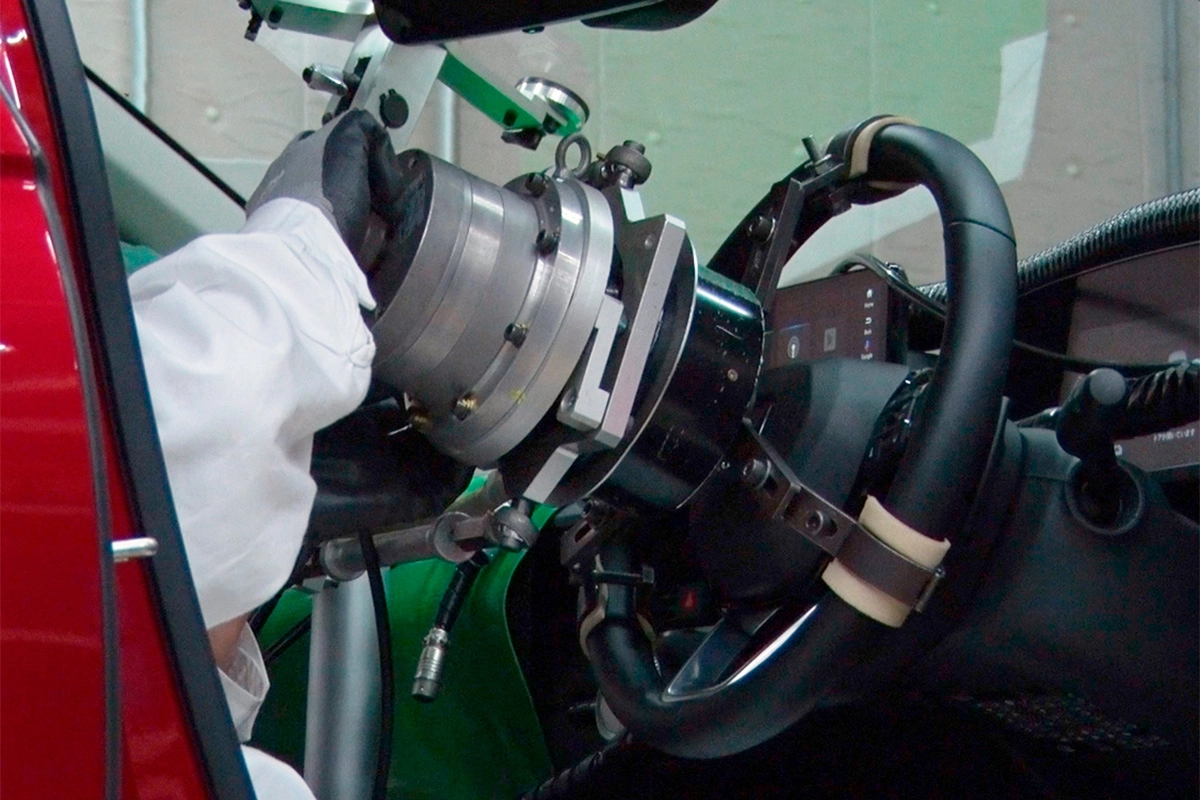
操舵アクチュエーターを取り付けている様子
コントロール室
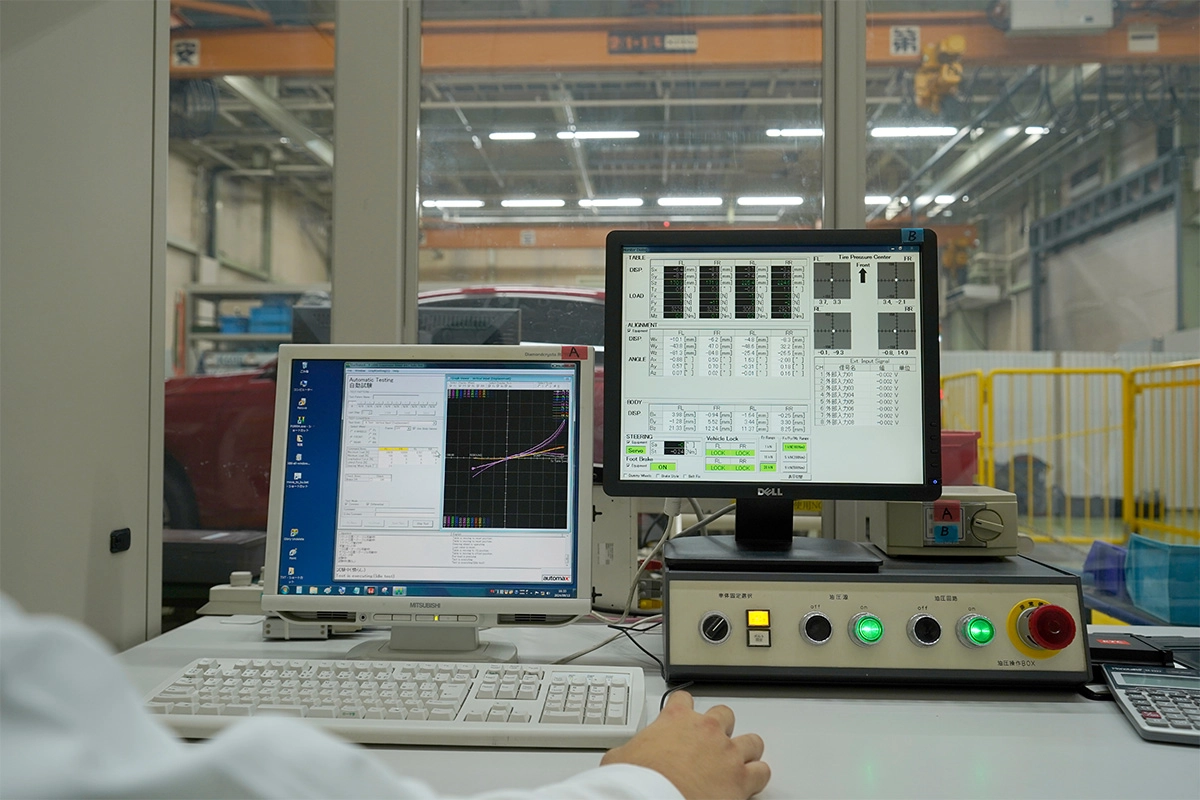
サスペンションテスター
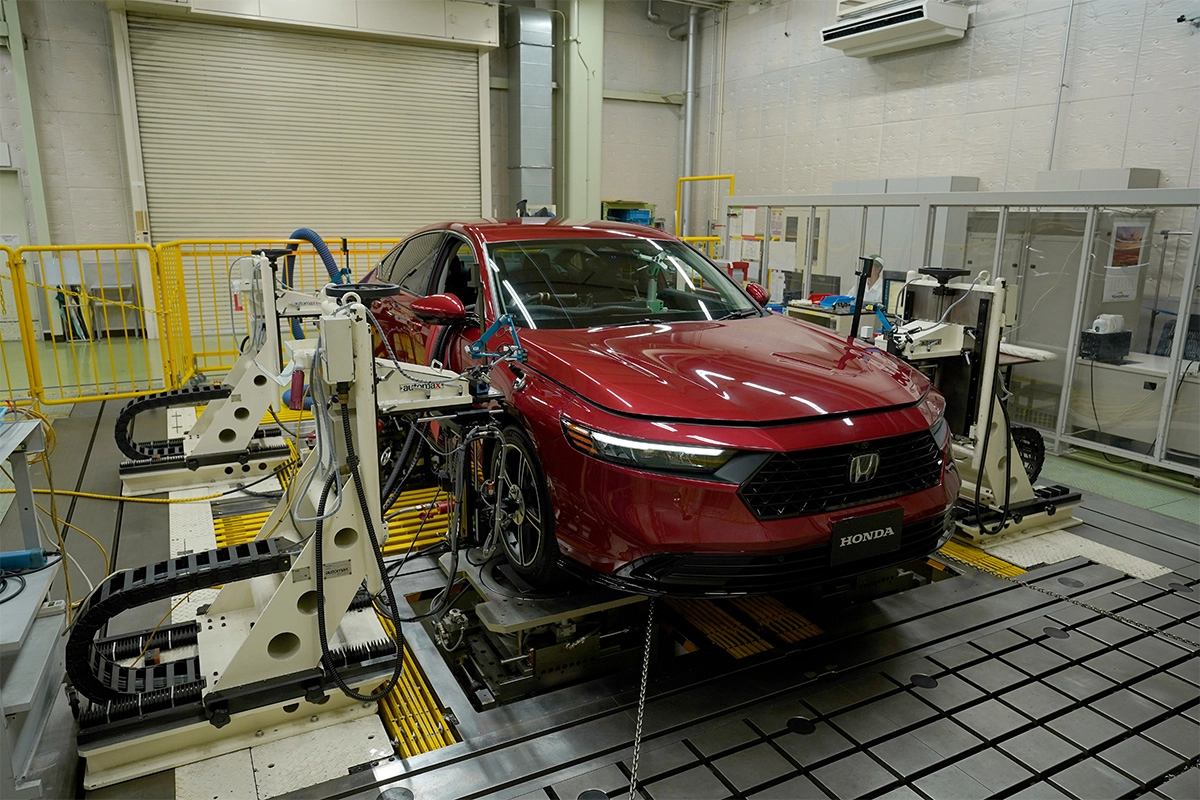
サスペンションテスター
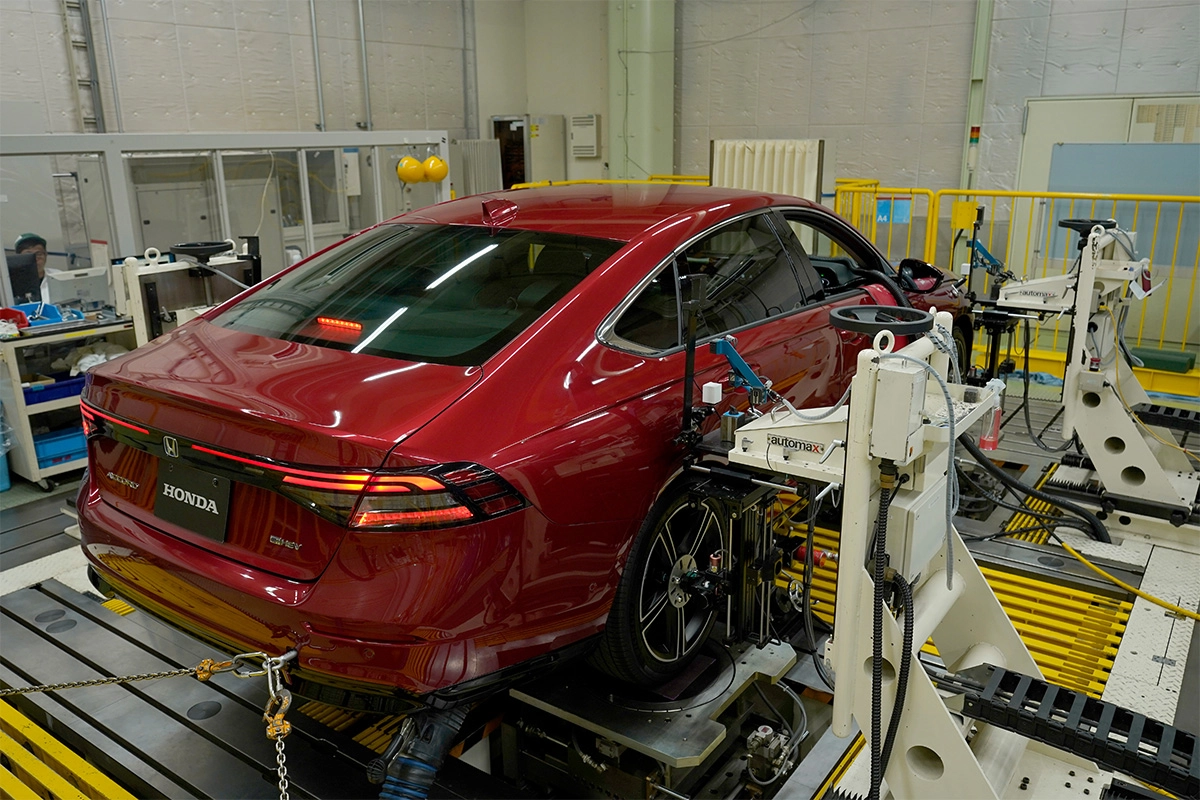
サスペンションテスター
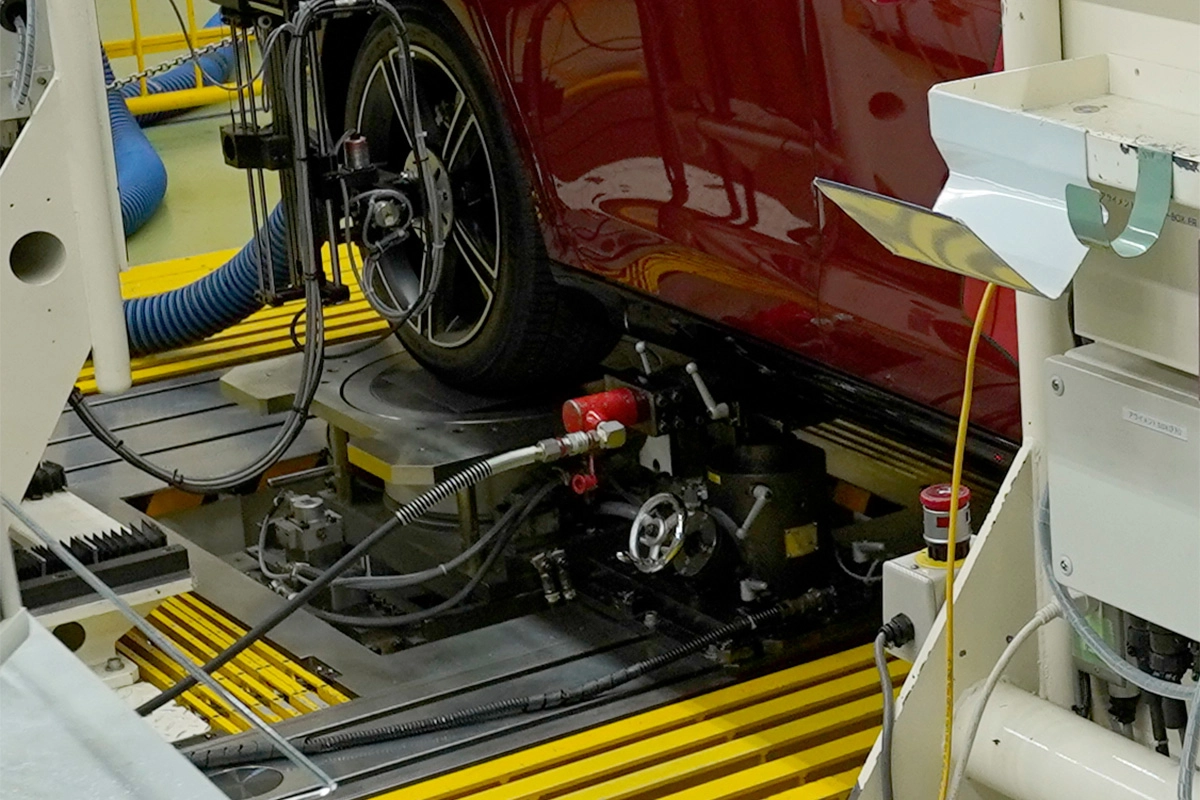
ジャッキアップポイントを利用して試験車両を設備に固定している様子
サスペンションテスター
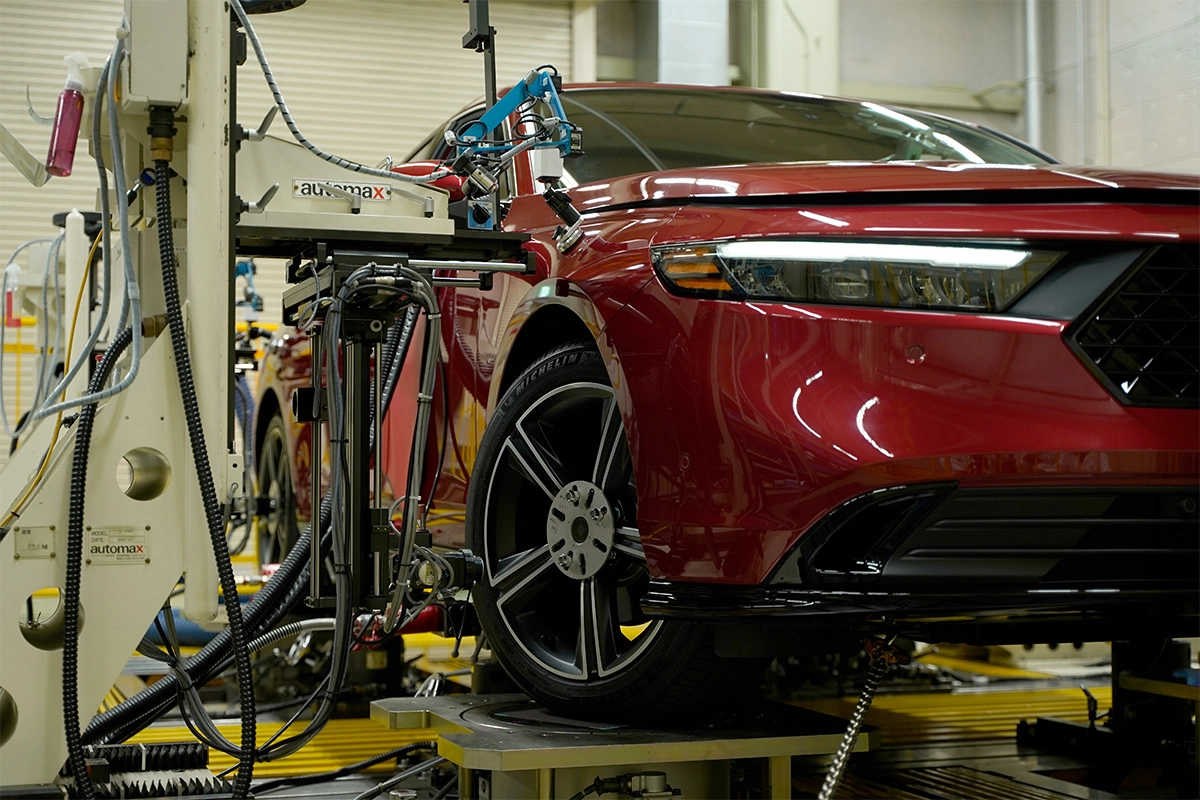
サスペンションテスター
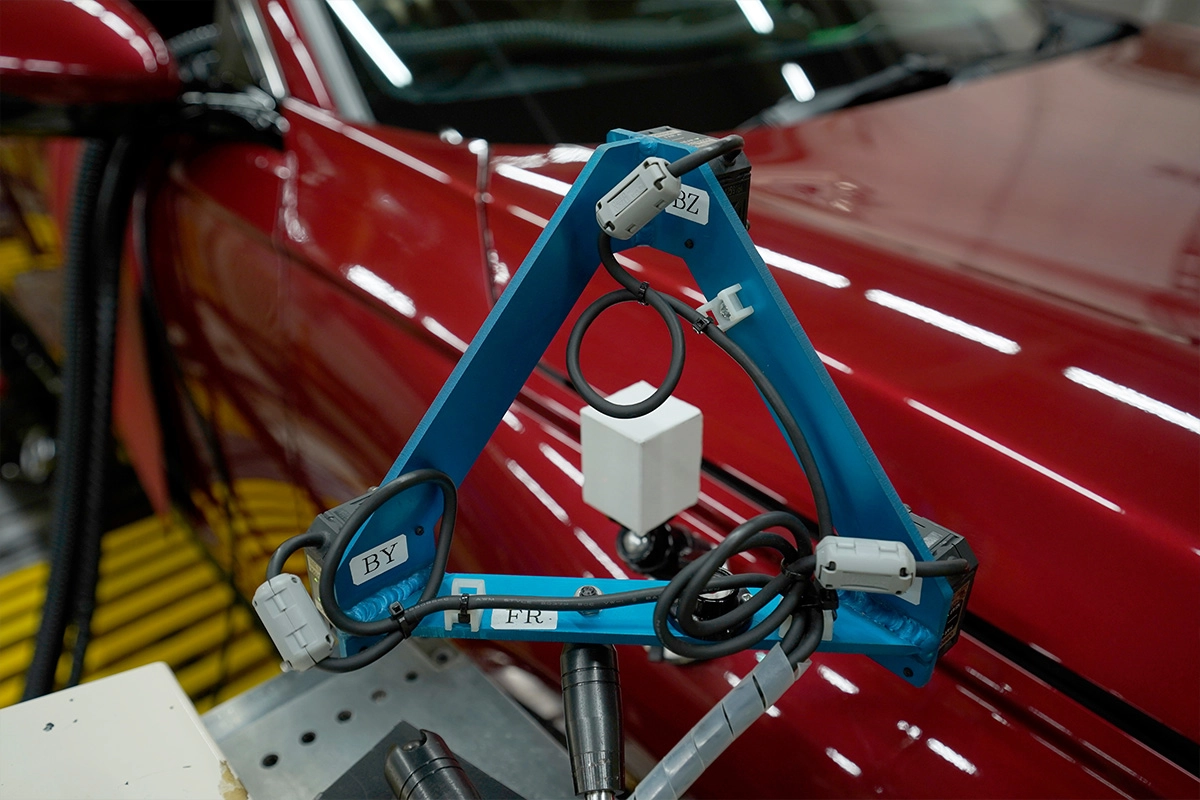
レーザー変位計
サスペンションテスター
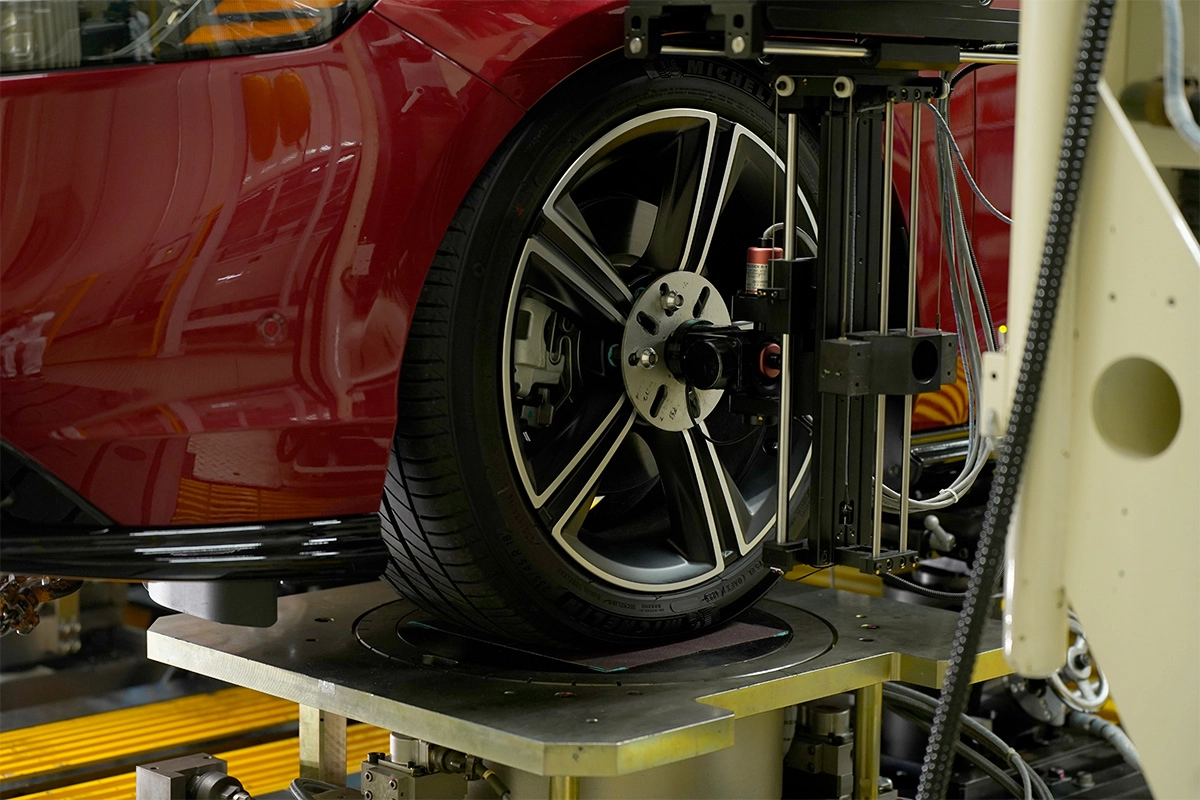
サスペンションテスター
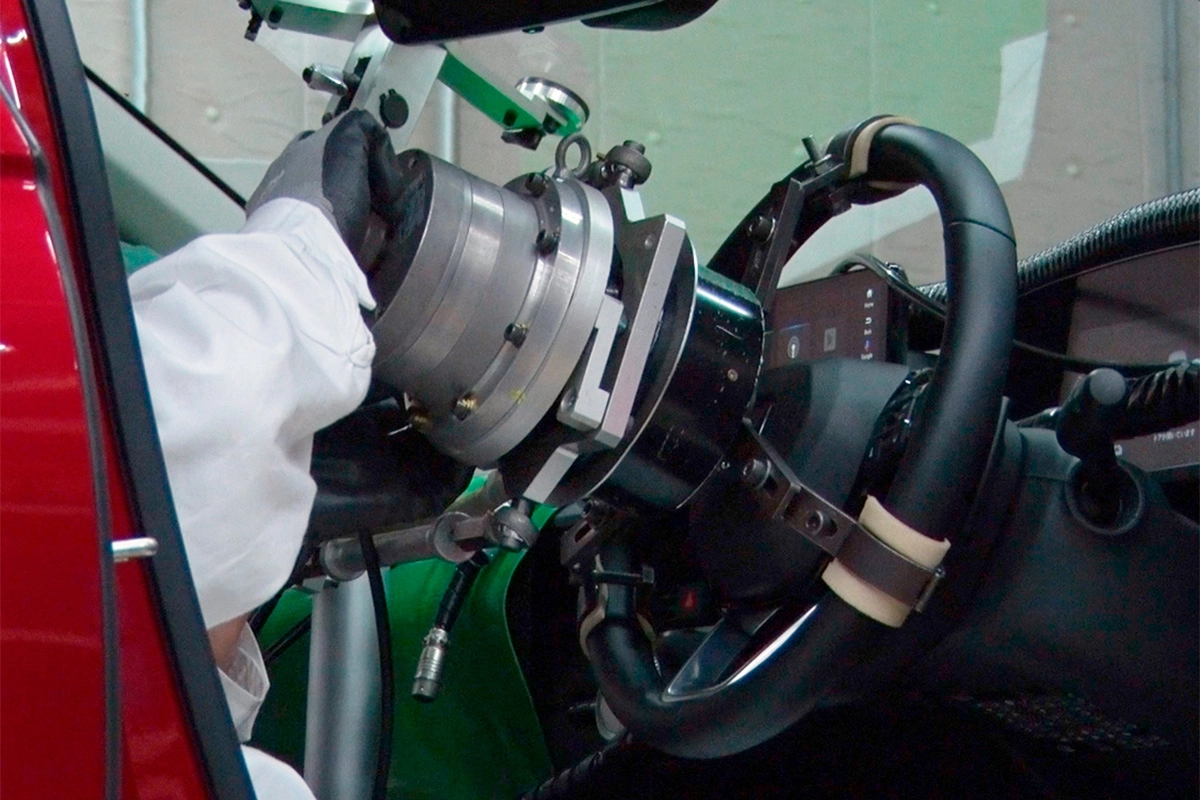
操舵アクチュエーターを取り付けている様子
コントロール室
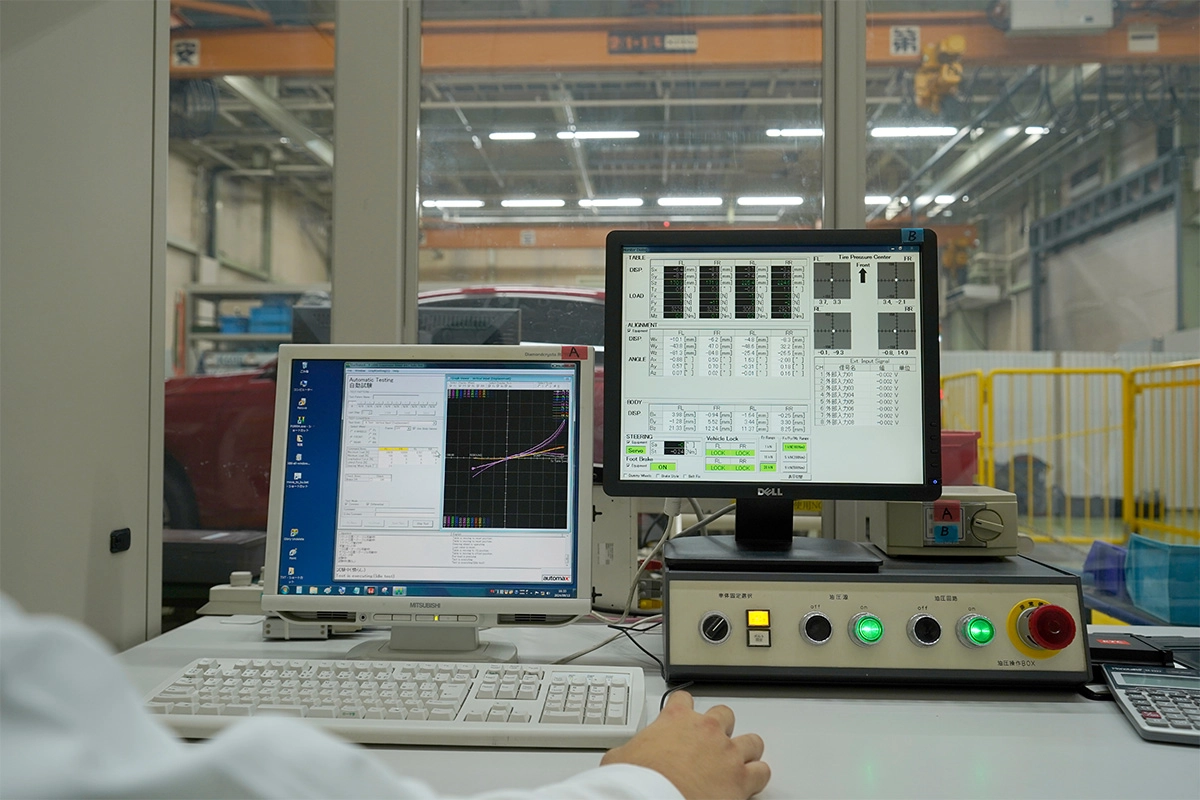

今日においては運転支援や自動運転など、シミュレーションを高度に活用した開発がより重要となっており、精度の高い計測データが活用されている。またハードウェア開発の高効率化に向けて、車体を必要としないサスペンション単体での評価にも取り組んでいる。
クルマは大量生産の工業製品の代表格でありながら、人の感性に触れる特殊な工業製品でもある。開発効率を高めて早くお客様のもとに届けたい一方で、Hondaとして感性に訴えるハンドリングや乗り味を届けたい思いがある。そのためには最大限にサスペンションの性能を引き出す必要があり、そこにサスペンションテスターの存在価値がある。
INDEX
Hondaの研究開発施設
- 第1回 ものづくりはここから始まる「Hondaの研究開発」
- 第2回 道が製品を決める「栃木プルービンググラウンド」
- 第3回 道が製品を鍛える「鷹栖プルービンググラウンド」
- 第4回 空気を味方に、風を極める「実車風洞」
- 第5回 モビリティの核はここで鍛える「台上試験施設」
- 第6回 極限の環境でHondaを仕立てる「環境試験施設①」
- 第7回 極限の環境でHondaを仕立てる「環境試験施設②」
- 第8回 革新的なカタチをスピーディーに作る「金属3Dプリンター」
- 第9回 すべてはリアルで証明する「全方位衝突実験施設」
- 第10回 バーチャルが変える開発プロセス「XR検証施設」
- 第11回 自動運転に向けたバーチャルとリアルの融合「ドライビングシミュレーター」
関連コンテンツ
関連コンテンツ
テクノロジーHondaの研究開発施設モビリティの核はここで鍛える「台上試験施設」