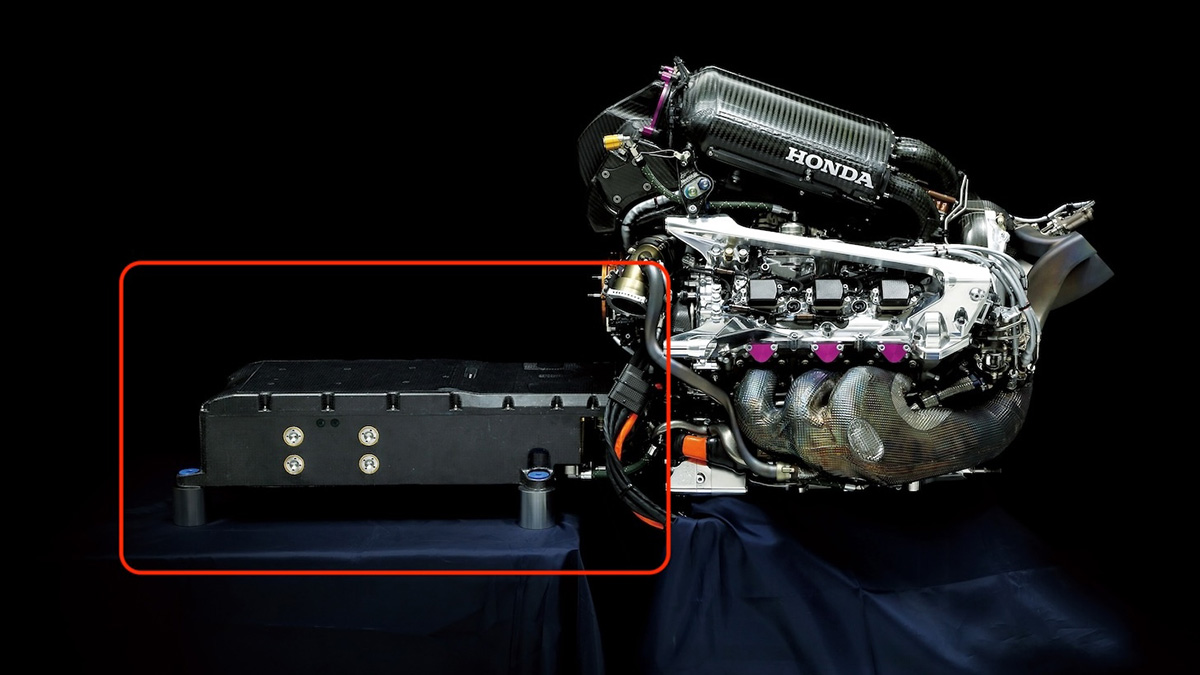
Honda's ESS
Batteries store electrical energy generated by the MGU-K kinetic energy recovery system and MGU-H heat energy recovery system. In F1 regulations, this is referred to as the Energy Store (ES), which covers the full system of battery cells and peripheral devices such as the inverter.
Regulations specify a maximum voltage of 1,000 V for the ES. Installation is also covered by regulations to ensure safety, with rules stipulating that it must be located within the survival cell. Therefore, the ES is situated behind the driver’s seat and below the fuel tank. With a change of regulations in 2018, it was required to have a minimum volume of 22 L and minimum weight of 30.6 kg. As explained below, the ES developed by Honda was designed specifically to these specifications. Incidentally, another change of regulations introduced in 2022 increased minimum weight to 31.0 kg (accompanying an increase in total power unit minimum weight from 150 to 151 kg).
When developing its own F1 regulation ES, Honda uses the abbreviation ESS, meaning “energy storage system.” In addition to the battery cells that store electrical energy, the ESS refers to a single package containing the other related units, including the inverter, DC-DC converter, and battery management system (BMS).
When it started participating in the F1 as a power unit supplier in 2015, Honda jointly developed an ESS with its partner McLaren. ESS assembly was performed by the McLaren team. Deciding to start insourcing the ESS technologies that play an important role in terms of on-track performance, Honda gradually moved ESS development and assembly functions in-house from 2016. By the time it started partnering with Scuderia Toro Rosso as a power unit supplier in 2018, it had fully shifted to an in-house development and assembly system. From logistical and other perspectives, the Honda Racing Development (HRD) site in the UK for development and assembly was located at Milton Keynes where the factory of Red Bull, to which Honda supplied power units from 2019, was also located.
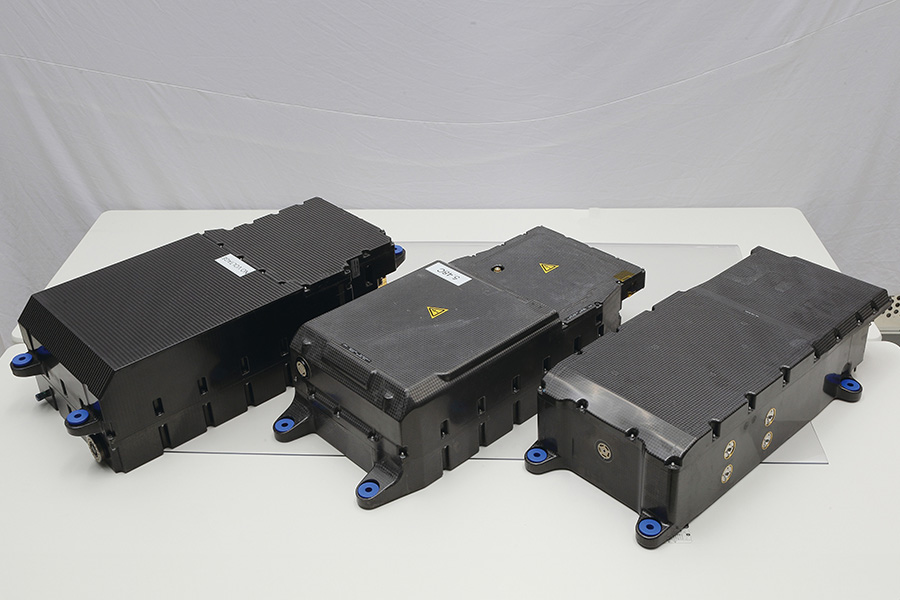
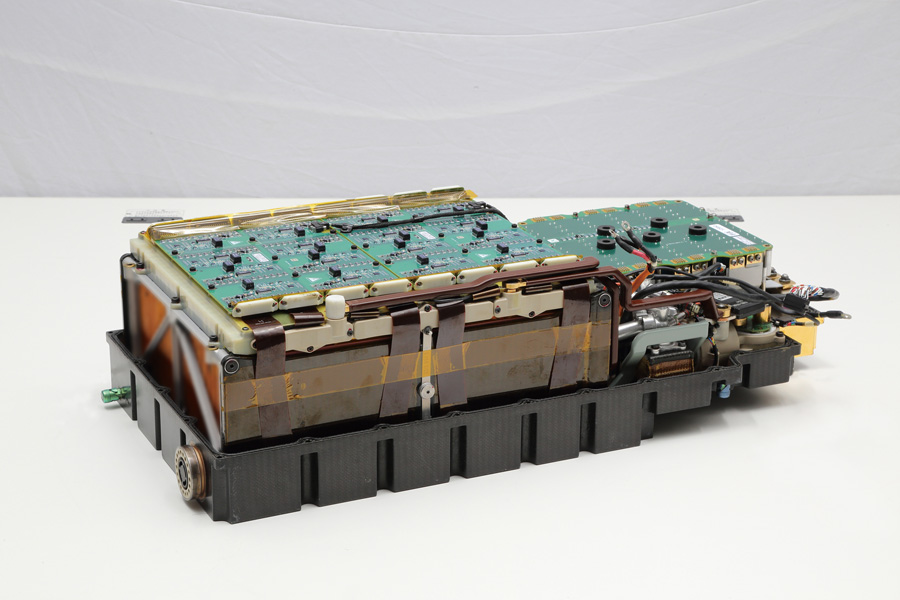
When developing the 2016 ESS, Honda focused on improving reliability and reducing weight. In 2017, it worked on optimizing the battery cells and on reducing both size and weight. While changing partner in 2018, and adding an additional team partner in 2019, it basically maintained the same specifications for those years, while focusing on improving reliability.
When developing the 2020 ESS, Honda again worked on reducing size and weight and increasing output. At the Belgian Grand Prix, the 12th round of the 2021 season, it introduced an ESS with even higher output.
Carbon nanotubes (CNTs), the key technology for further increasing output
As already explained, ESS development was conducted in the United Kingdom, but being unable to find a local supplier to manufacture the materials that represent a key technology for further increasing output, Honda decided to develop the ESS with the support of a Japanese supplier. The key technology in question was carbon nanotubes (CNTs). Battery cell electrodes containing carbon particles, and electricity flows through these particles.
By filling the spaces between carbon particles with the nanometer-sized, tube-shaped CNTs (with a diameter of one millionth of a millimeter, or 10-9 m), it is possible to achieve low resistance and enable electricity to flow more freely. However, rather than just mixing the CNTs with the carbon particles, this technology provided the knowhow needed to optimize the process, including the mixing method, thickness, and coating method for applying a thin layer of active material to the electrodes.
Battery cells also employ separators that prevent internal short circuits while allowing the transmission of lithium ions between the anode and the cathode, and the thinner those separators can be made, the lower the resistance and the higher the output. If efforts are too aggressive at this time, on the other hand, the risk of internal short circuits increases. When developing a new ESS for the 12th round of the 2021 season, Honda was able to make these separators thinner while maintaining reliability by optimizing the material characteristics.
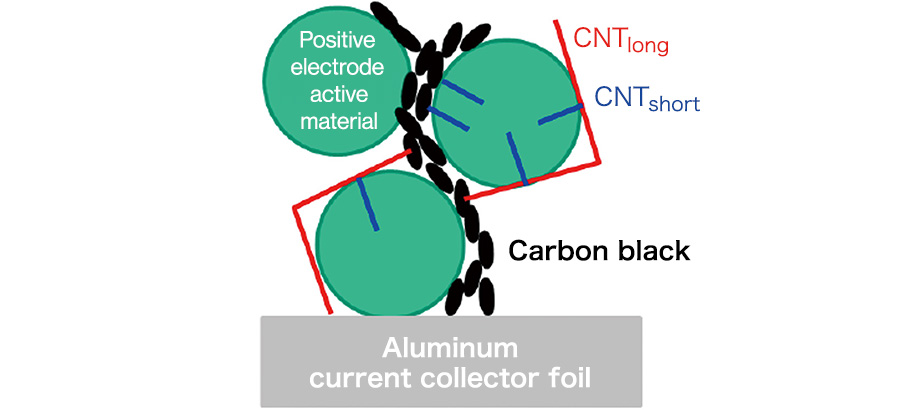
New EES developed by Honda
Honda’s newest ESS, fully developed in-house, has remarkably lower loss, during times of high current flow in particular, compared to ESSs of the past due to its lower resistance. From a different perspective, this means it provides an increased level of usable energy. And with greater resistance to deterioration compared to older ESSs, with a minimal drop in output, the greater the distance traveled, the greater the difference in performance between the new and old ESSs.
Due to higher efficiency and lower loss in the new ESS, the MGU-K and MGU-H can be deployed for a longer period of time on the drive side compared to previous ESSs, even if energy recovery levels are the same. (Deployment refers to the assist focused on in mass production development, while harvesting is a term sometimes used by Honda and others, when developing F1 power units, for the recovery of energy.) The volumetric output density (W/kg) of the new ESS introduced in the 12th round of the 2021 season is 1.3 times greater than that of the ESS used in 2020 and 2021 seasons. Using the 2015 ESS as the base, the 2021 ESS is 26% smaller and 15% lighter, which contributes greatly from the perspectives of energy management and optimizing vehicle driving performance.
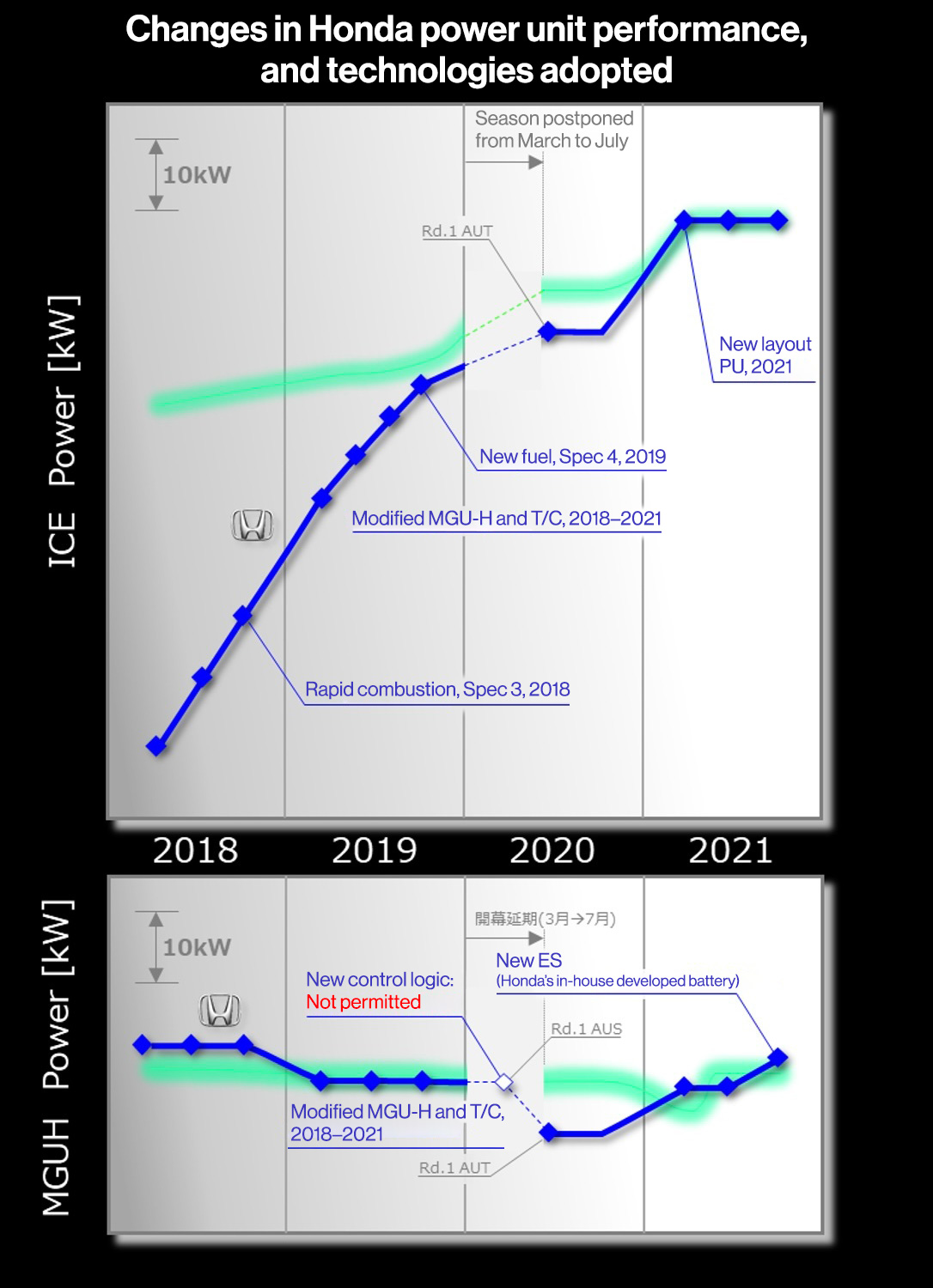
Control technology since the 2014 season
Maximum fuel flow rate has been regulated for F1 cars since the 2014 season. The maximum fuel amount that can be used during races has also been regulated. Development, therefore, has needed to focus on efficiently converting the limited energy available in fuel into engine output (Evolution of the V6 Power Unit, Evolution of Technologies Boasting the Ultimate Combustion Efficiency). On the other hand, selective use of the MGU-K and MGU-H depending on the driving situation can greatly influence on-track performance, so the development of energy management systems is important.
Restricted to a maximum output of 120 kW, the MGU-K is allowed to send up to 2 MJ of recovered energy per lap to the ES, and the ES is allowed to send up to 4 MJ of assist (deployment energy) per lap to the MGU-K. Therefore, only 2 MJ of energy per lap is available for use if relying solely on recovered energy from the MGU-K.
The basic idea is that the MGU-H is used to make up the shortfall. MGU-H output, and the amount of assist energy recovered and used for power per lap, are not regulated, so there are no setting restrictions. However, the MGU-H recovers heat energy from the exhaust gas. This creates a trade-off whereby focusing on engine output leads to less heat energy available for the MGU-H and less energy recovery, whereas focusing too heavily on MGU-H energy recovery leads to lower engine output.
The challenge has become how to determine the balance between engine output and MGU-H energy recovery that produces the best performance on the track. With qualifying rounds not requiring much thought to be given to this energy balance, and actual races applying restrictions, the ongoing focus of development has been to find the optimal use of energy for each scenario. Energy management under race conditions treats each course as a series of segments, with MGU-K deployment being allocated according to the characteristics of each segment. (In segments where the energy balance is more sensitive, MGU-K assist is prioritized.)
Looking at MGU-K and MGU-H usage by driving situation, the MGU-K is fully used during deceleration to recover kinetic energy, while the MGU-H is used to recover energy at the same time. What this specifically means is that exhaust temperature is intentionally allowed to increase when off-throttle to allow recovery of the heat energy from the exhaust gas and storage in the ES. The team developing this control technology have termed it Additional Harvest Power, or AHP.
Under partial throttle when starting to exit a corner, a different control technology called partial recovery is employed. It is used to generate electricity by diverting excess output to the MGU-K after the engine generates enough output to meet the driver’s needs. Both AHP and partial recovery consume extra fuel, but this control technology was planned and implemented because increasing energy recovery and storing it in the ES to increase the amount of energy used for MGU-K assist achieves a greater performance gain than what could be achieved through fuel consumption alone.
It is known that minimizing the time to reach maximum speed on straights is a highly effective way to reduce lap times. Therefore, to increase the maximum acceleration power when first hitting full acceleration on straights, while fully deploying MGU-K assist, MGU-H assist is also fully deployed to rapidly increase boost pressure. This means that the MGU-H is used in the same way as an electric compressor.
Then, toward the middle of the straights, MGU-H mode switches while MGU-K remains in full assist mode, with the MGU-H recovering excess exhaust energy. Toward the end of straights, which have less of an impact on lap times, MGU-K assist is discontinued and MGU-H energy recovery only is employed to restore ES charge levels.
During situations that require greater power, such as the race start and when overtaking, e-boost is used. Normally, the waste gate is closed to enable full use of the MGU-H for recovering energy from the exhaust gas. At race starts and when overtaking, on the other hand, the waste gate is opened to lower exhaust pressure, reduce pumping loss, and increase engine output. At the same time, the MGU-H is used to provide assist and help with turbocharger work. The MGU-K is also switched to full output to achieve maximum output generation from the system.
Extra Harvest/Extra Deploy is a control technology fully implemented from the middle of the 2018 season. The maximum amount of energy that can be sent directly from the MGU-K to the ES is 2 MJ per lap, so rather than sending any recovered energy over 2 MJ to the ES, that energy is sent to the MGU-H, which has no restrictions on energy exchanged with the ES. After being used for only a moment to assist the MGU-H, the inertial energy from the rotor is then immediately recovered. Through continuous repetition of this assist-to-recovery cycle at a frequency of 20 Hz or less, the recovered energy is sent to the ES. This is known as Extra Harvest.
Although the efficiency of energy recovery via the MGU-H is less than direct energy recovery by the MGU-K, total energy recovery of the system is increased, leading to increased MGU-K assist time and therefore gains in terms of lap times. Lap time gains have been confirmed at 0.1 to 0.2 seconds on the Hungarian Grand Prix circuit (Hungaroring) and around 0.4 seconds on the Belgian Grand Prix circuit (Spa-Francorchamps), so the control technology has a significant effect.
Extra Deploy is like Extra Harvest, but the energy flow is reversed. Because the amount of energy allowed to be sent from the ES to the MGU-K is limited to 4 MJ per lap, energy over this maximum is sent to the MGU-H where it accelerates the rotor for a moment only and then recovers the inertial energy from the rotor. The electrical energy generated as a result is sent directly to the MGU-K as a way of legally exceeding the 4 MJ of energy allowed to assist the MGU-K. Use of this Extra Deploy control technology is expected to achieve lap time gains of 0.2 to 0.3 seconds.
The pursuit of higher efficiency for the various components of the power unit, while working to reduce size and weight, are both important. However, of utmost importance is the pursuit of speed through optimization of energy management to achieve efficient recovery and efficient use of energy. Ever since Honda started participating in the F1, it has continually worked to evolve its energy management technologies and to refine technologies that efficiently convert limited amounts of energy into speed.