Honda 0 Series is the culmination of Honda’s new approach to EV development, “Thin, Light, and Wise.”, aiming to minimize the battery size while providing sufficient cruising range and a nimble driving experience that transcends the existing image of EVs. New value creation requires unprecedented production technologies.
Engineers involved in four core production technologies shared their passion at Honda 0 Tech Meeting 2024, held in August 2024.
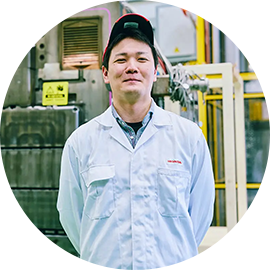
PU Plasticity Engineering, PU Production Engineering Department View More Close Minoru Ichikawa
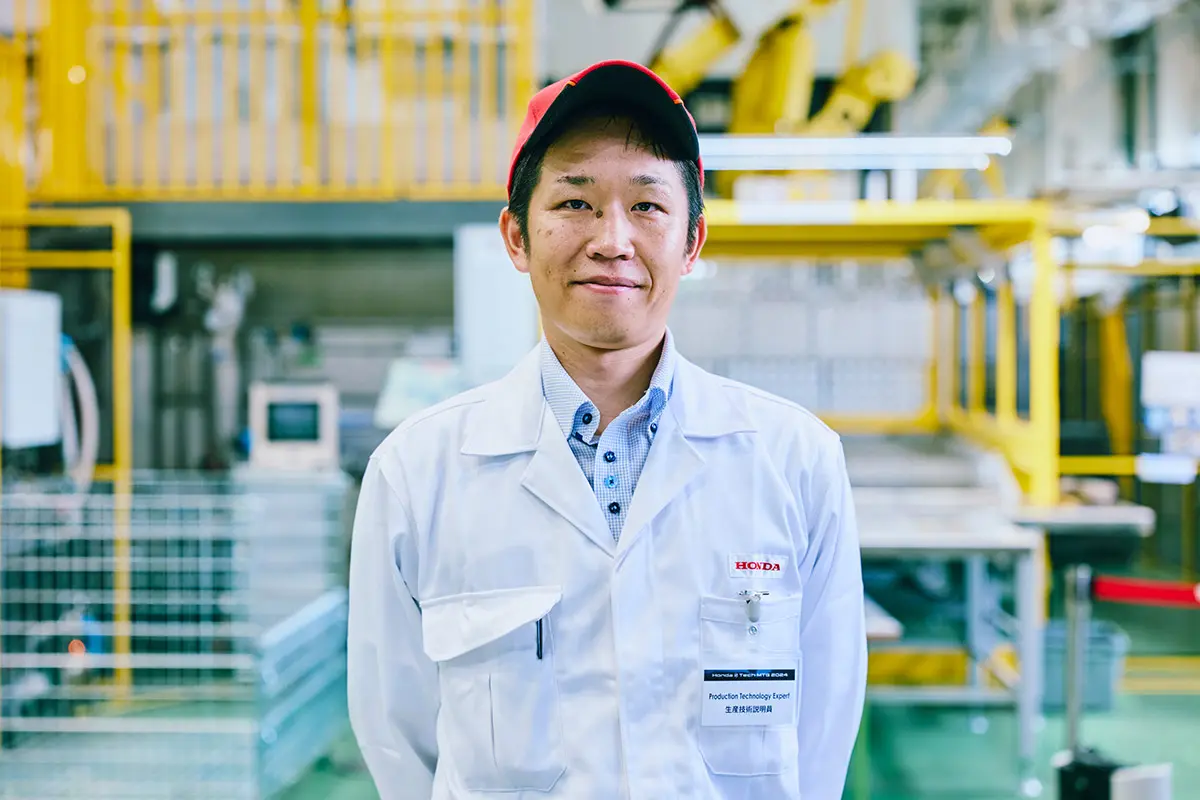
PU Equipment Engineering, PU Production Engineering Department View More Close Atsushi Yoshida
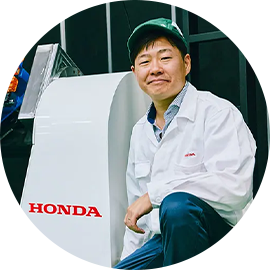
Body Equipment Engineering, Body Production Engineering Department View More Close Rikki Ito
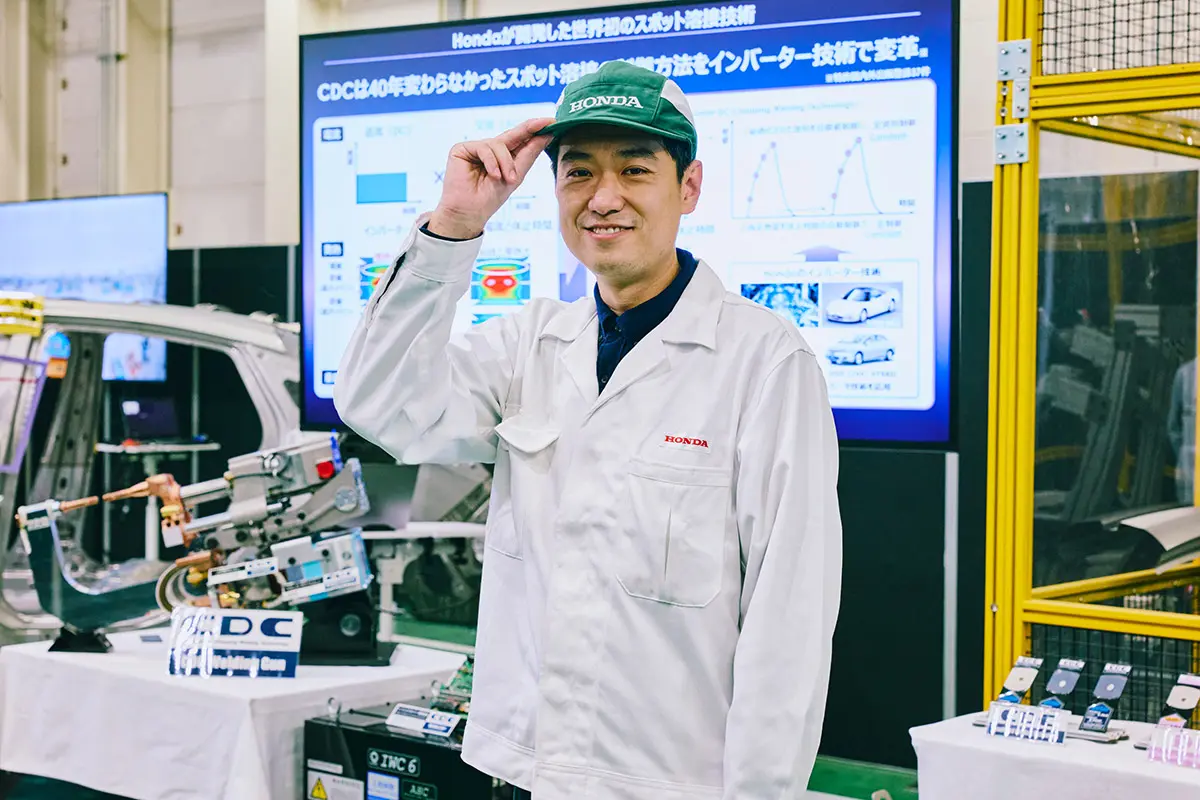
Body Equipment Engineering, Body Production Engineering Department View More Close Xihao Tan
Megacasting, a New Production Method for Cars
Megacasting is a technology for molding large cast parts. This technology is indispensable to the “Thin” and “Light” aspects of the Honda 0 Series, by achieving a highly strong battery case through molding as one piece and eliminating seams.
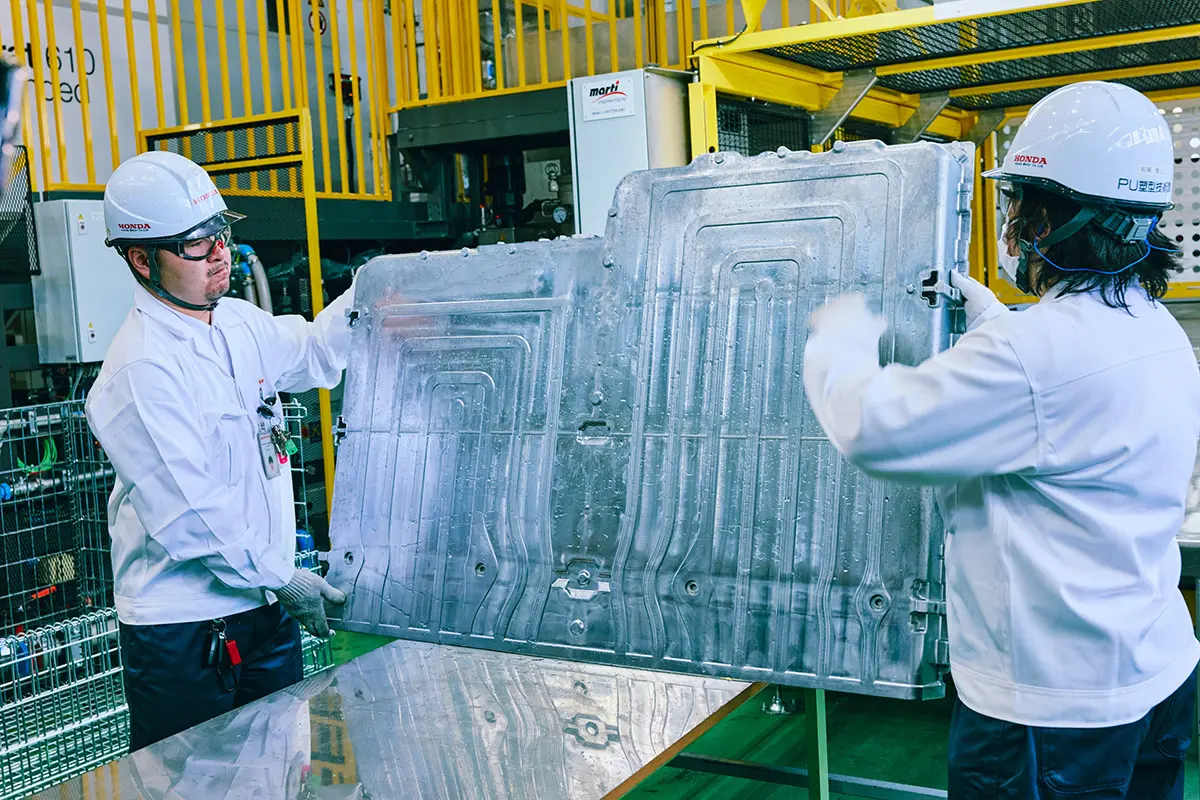
Large-scale casting is a technology that has recently attracted attention. In order to meet the challenge of “Wise” manufacturing, one of the key aspects of the Honda 0 Series, the battery case is cast in sections and joined together. The battery case and ancillary parts, which generally consists of more than 60 parts, are reduced to only 5 parts, making it possible to produce a high-quality, thin, and light casing. By selecting the appropriate size equipment, megacasting also enables smart manufacturing with low costs.
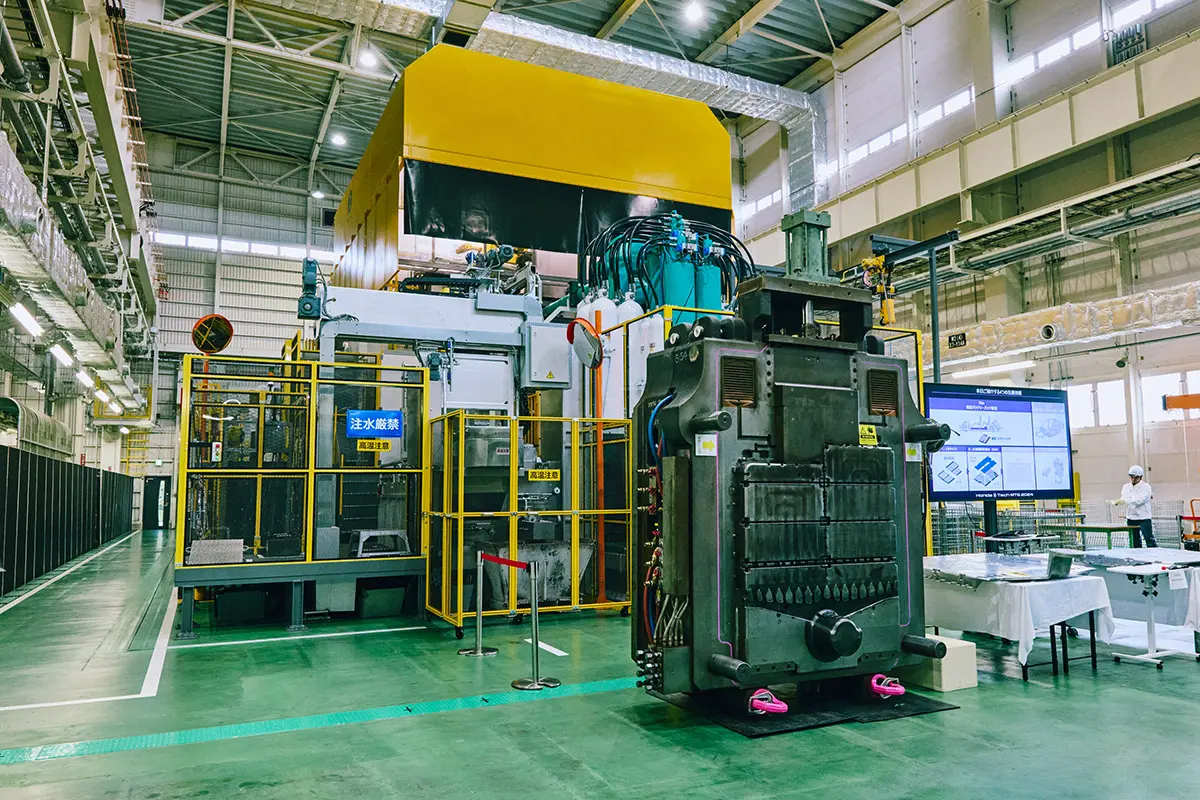
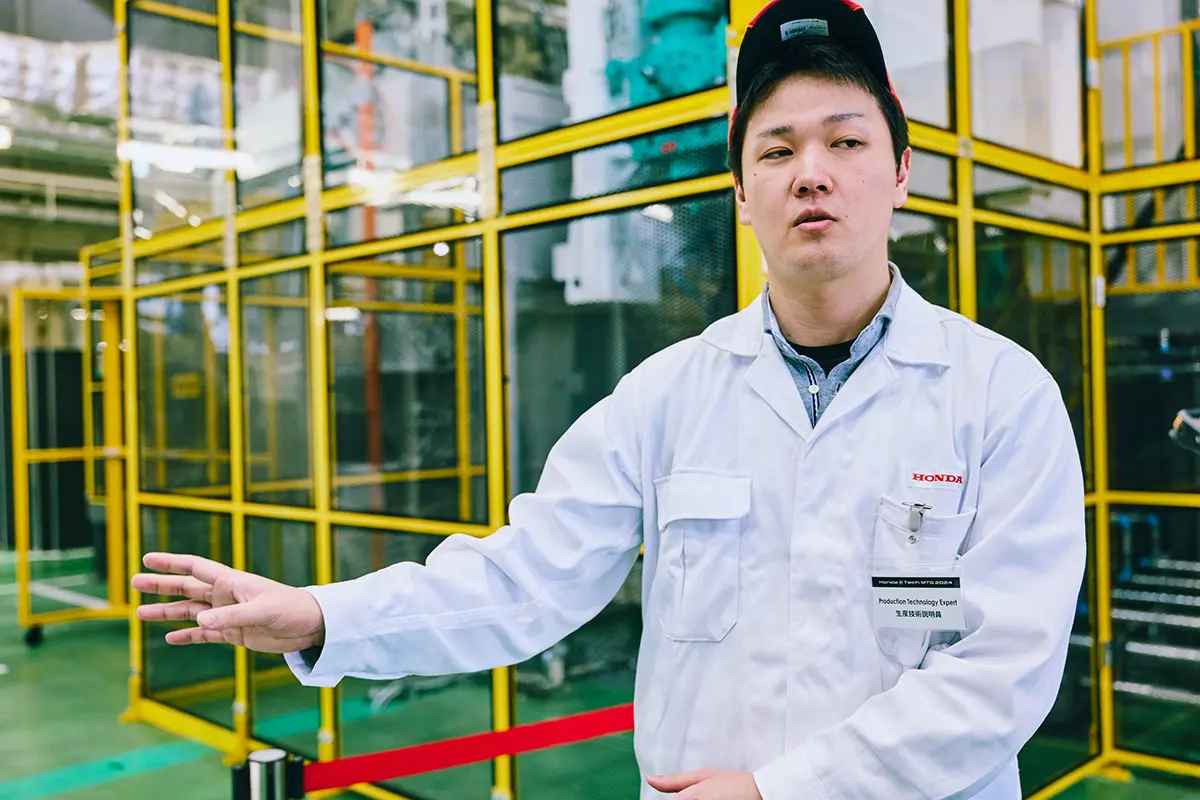
3D Friction Stir Welding (FSW) to Ensure Strength and Airtightness
3D Friction Stir Welding (FSW) is applied to two processes in the manufacturing of battery cases. The first is the process of joining parts made by megacasting to form the case enclosure, and the second is the process of joining the water jacket cover, which is necessary to provide the battery with cooling. This technology uses only the frictional heat between the rotating rod-shaped tool and the joint to soften and join the aluminum parts. As there is less damage to the base material from heat than with conventional welding, joints can easily be maintained at a high quality, making the entire battery case thinner and lighter while ensuring joint strength and airtightness.
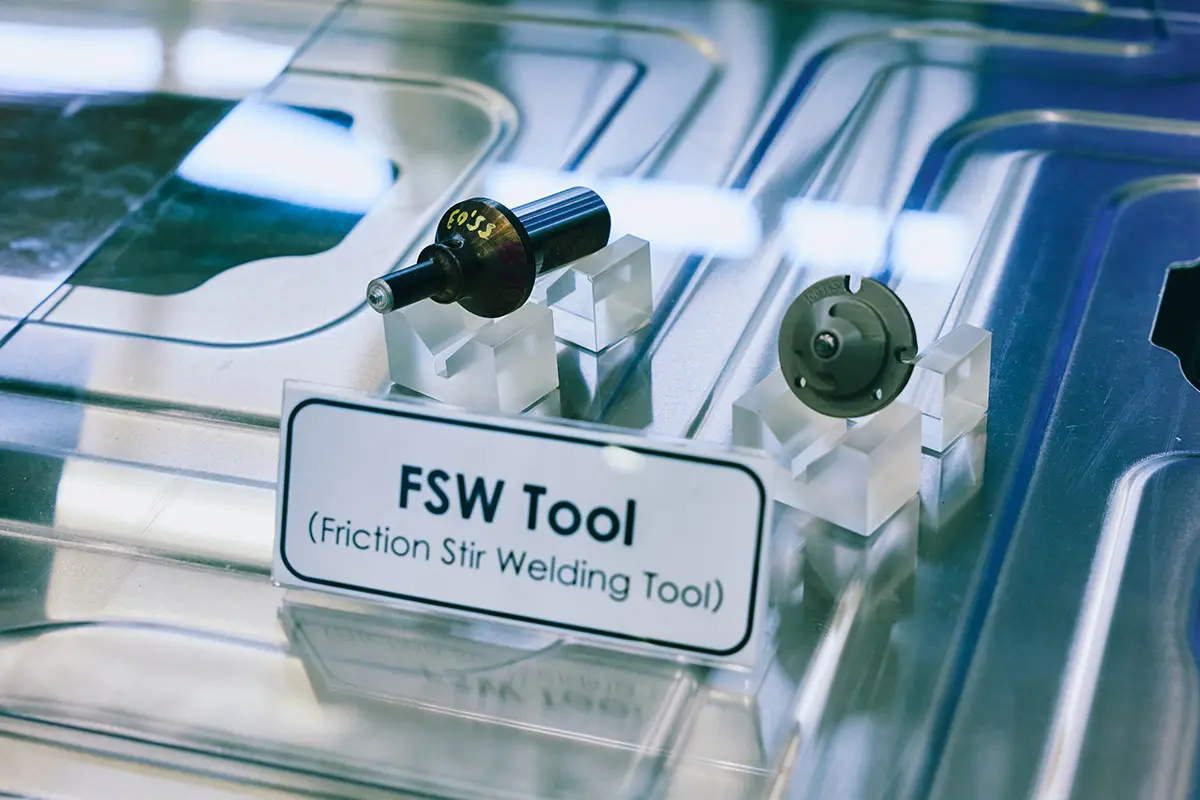
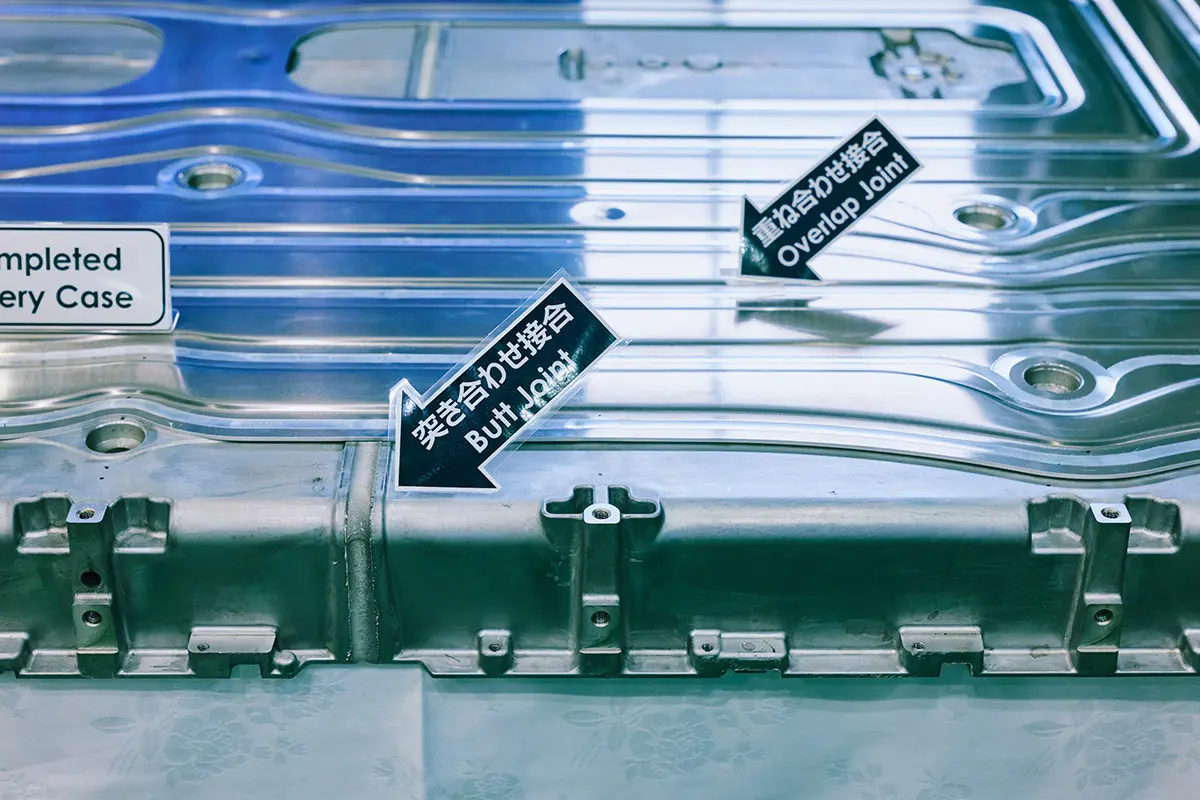
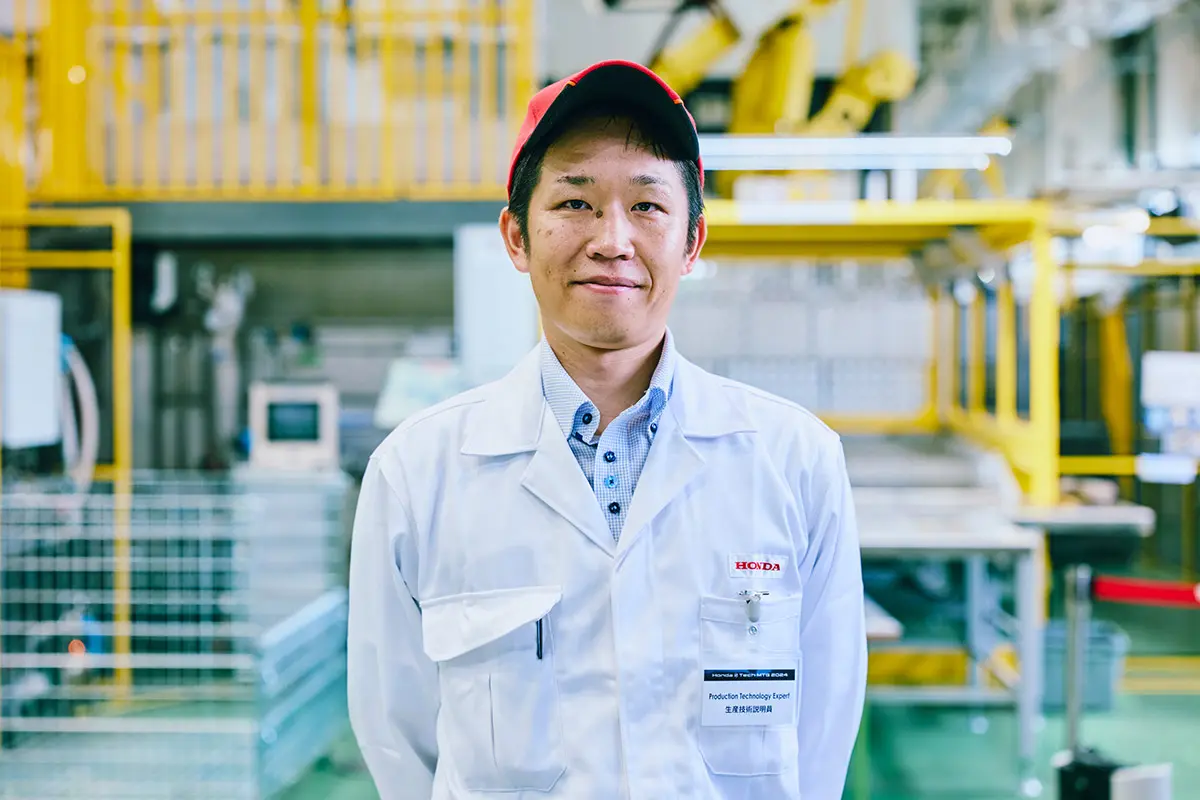
With battery case manufacturing, we focused on shortening the processes. By setting the joining conditions according to characteristics such as strength that vary by material and optimizing tool movements and other factors according to the shape of the joints, we were able to stabilize the quality of the joints while minimizing the amount of pre-processing required. Although FSW is common, Honda’s ability to apply technologies across the engine manufacturing process allows us to deliver products with a good overall balance as a product.
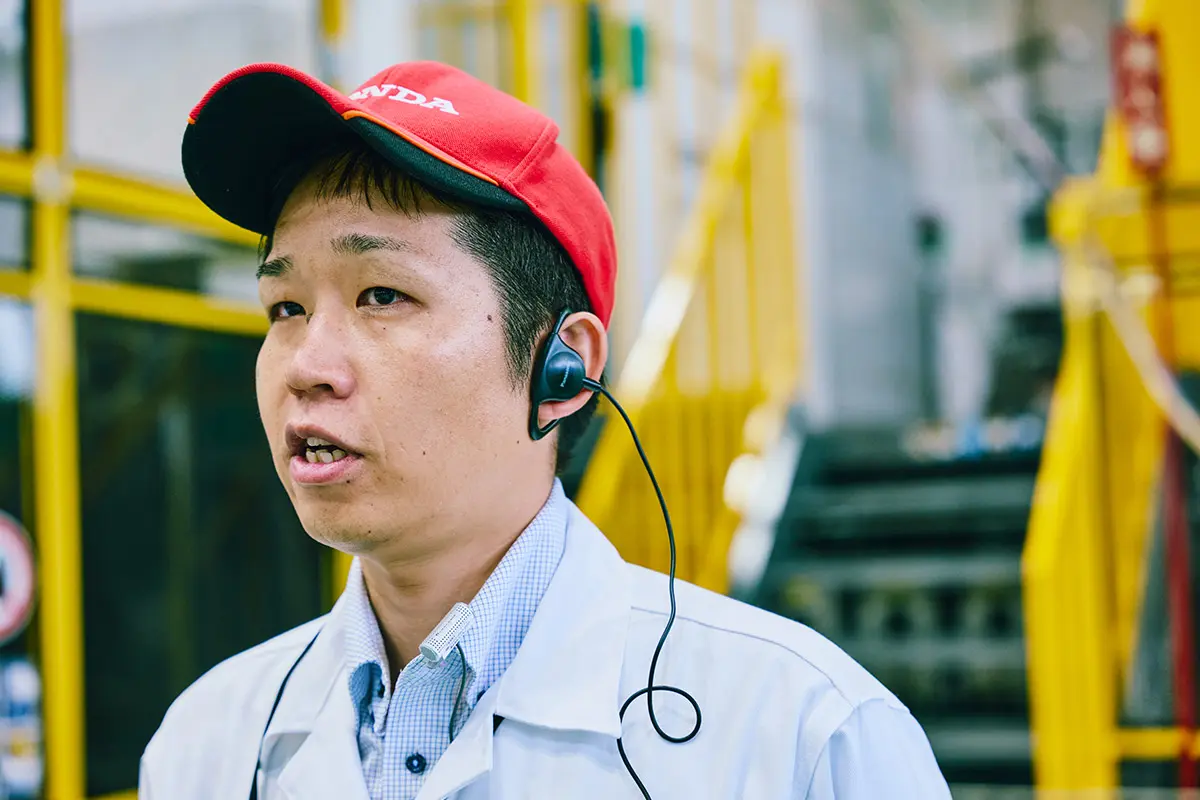
Flex-cell Production System, the Starting Point for Change in Production Methods
In contrast to a production line system, in which processes are divided and progress at a fixed pace with assembly by multiple workers, all assembly is performed by one person in a fixed location with the cell production system. This method is usually applied to processing lines, by Honda has incorporated the flex-cell production system, where parts are supplied by unmanned automatic guided vehicles (AGVs) for efficient assembly, in the assembly of Honda 0 series batteries.
This revolutionary production system avoids stoppages of the entire line by arranging multiple identical facilities in parallel, stabilizes production volume, improves production efficiency by eliminating waiting time for product transfer, and realizes more efficient capital investment. Furthermore, it can accommodate future changes and evolution of production lines.
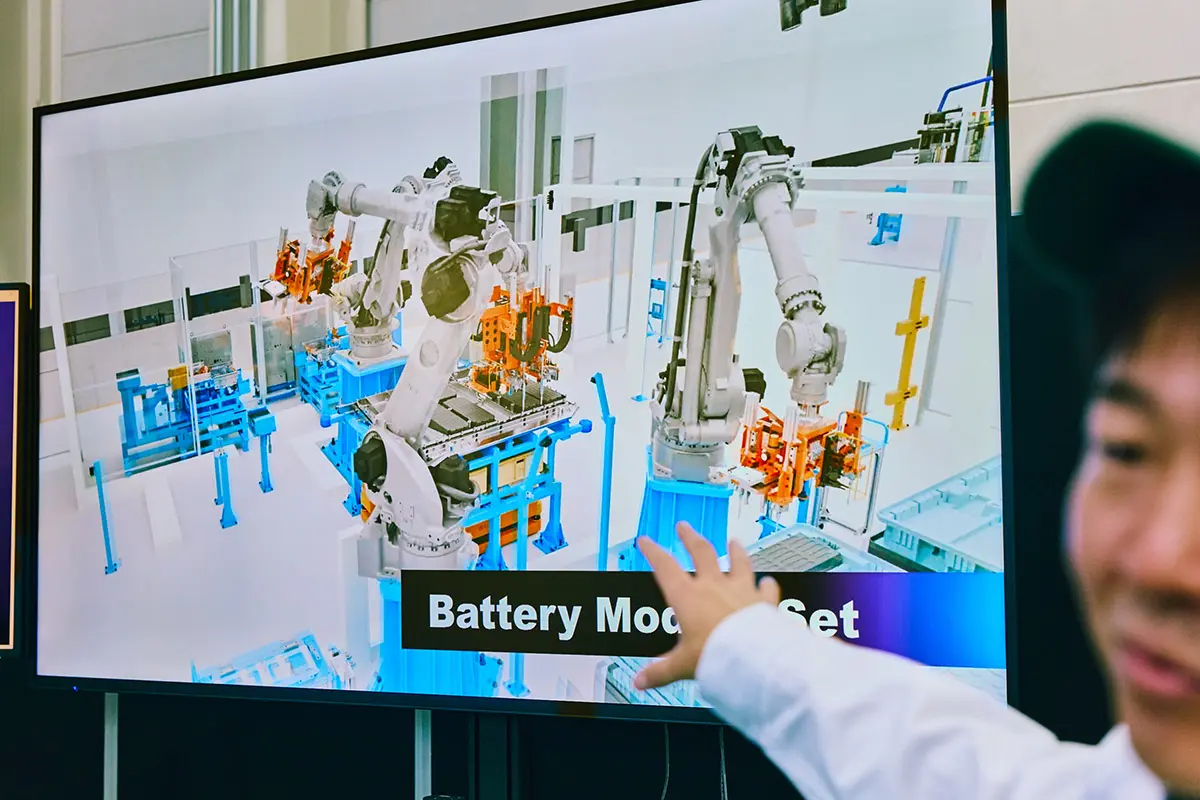
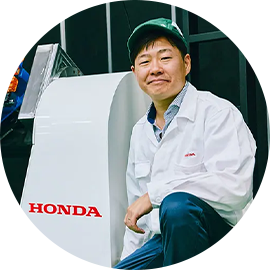
Since each process has to be connected in order to build a flex-cell production system, communication among the members was the most difficult aspect of the project. We were able to realize this system by building good human relationships, including with associates in North America, and by persistent discussions with each other as Honda engineers with pride. I believe people are Honda’s greatest assets.
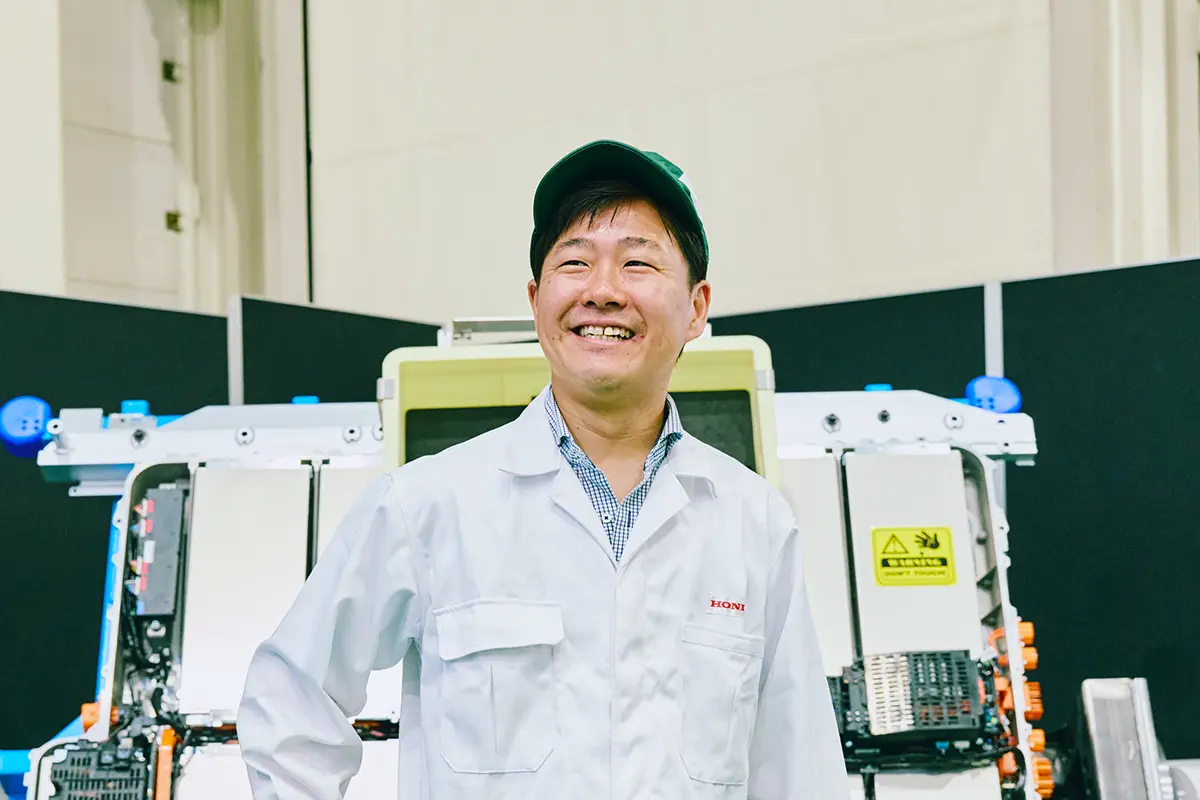
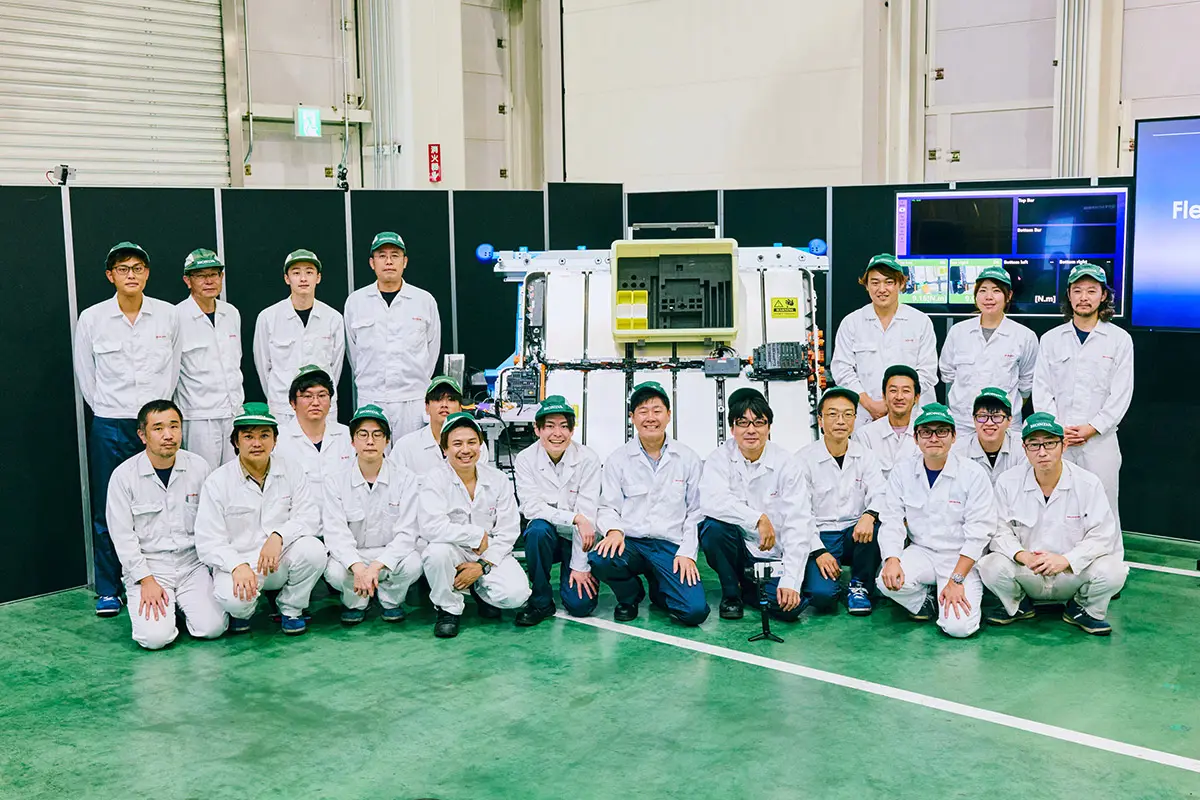
World’s First CDC Joining that Reduces Body Frame Weight
When joining body parts, it has been difficult to join ultra-high tensile strength steel plates and decorative exterior plates (thin soft steel plates) using conventional spot welding due to spatter*1 and loss of strength occurring due to the difference in thickness and materials.
To address this problem, Honda developed the world’s first Constant DC Chopping (CDC) welding technology with which the inverter*2-controlled current is used for welding. This technology is the result of applying Honda’s wealth of know-how on inverter control, including inverter design and reliability technology for hybrid systems, clean waveform AC generators, and the world’s first welding machine for joining the all-aluminum body of the first-generation NSX. Conventional spot welding could not be used with light and strong materials, leading to an increase in the weight of body components, while CDC welding technology has improved material efficiency and weight reduction.
1 Metal particles hardened by molten metal scattering during welding
2 Device that converts DC to AC current
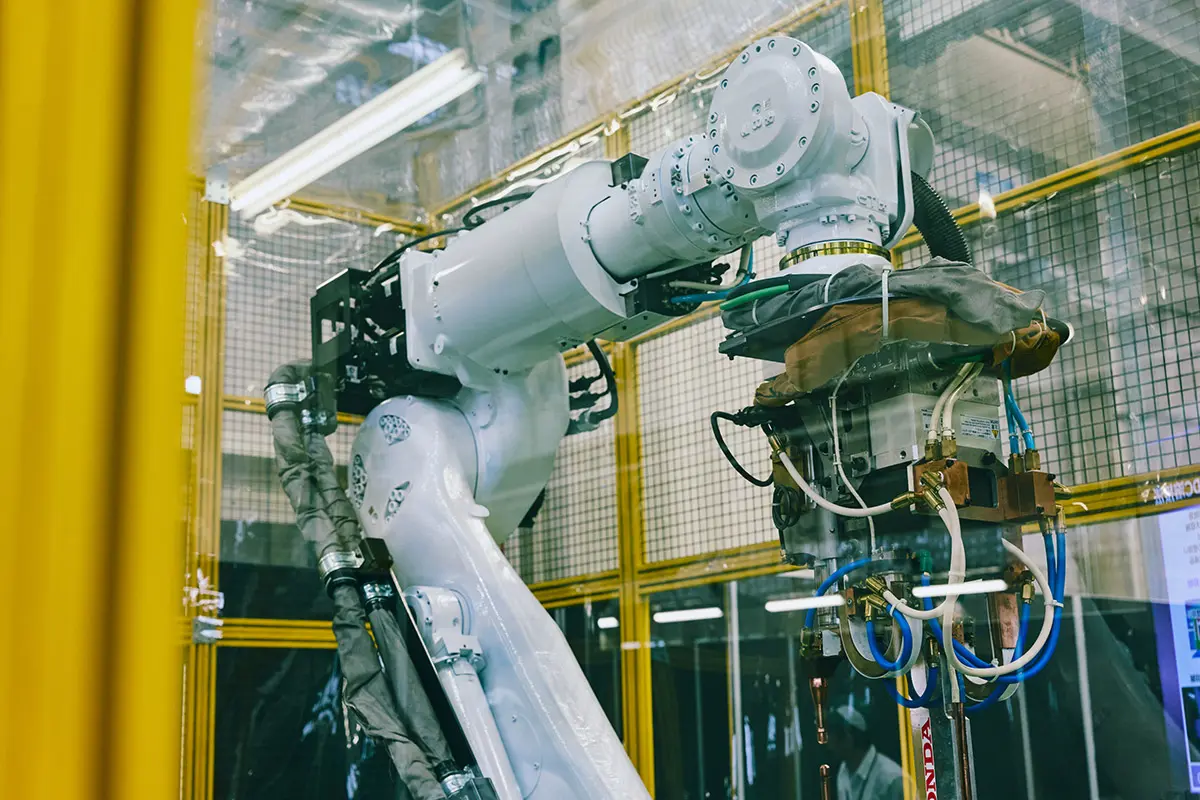
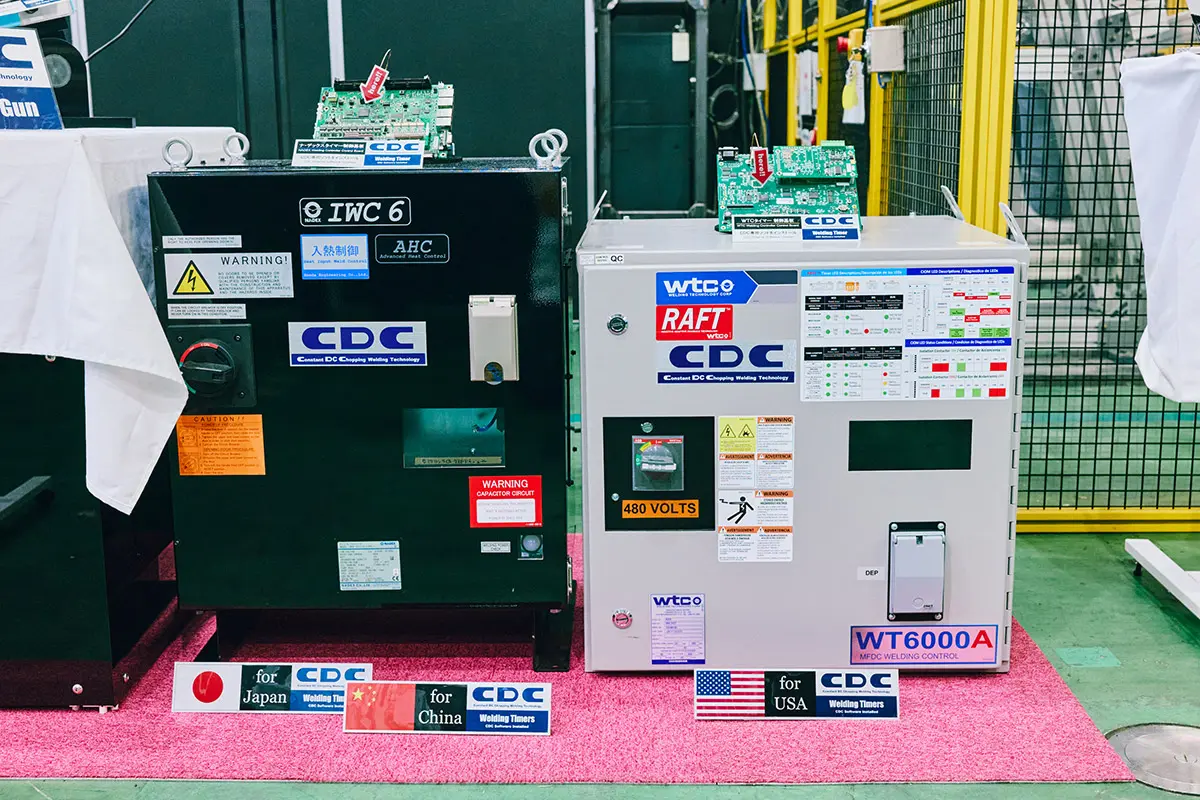
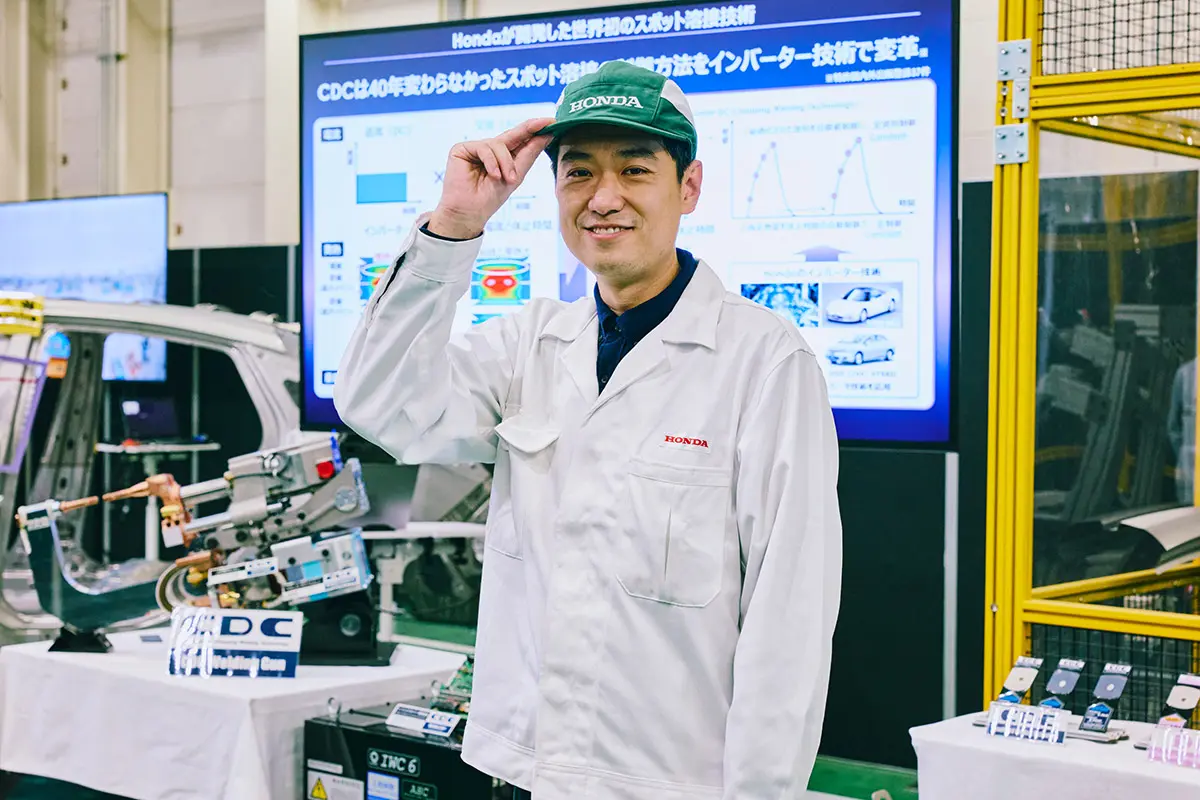
At first, welding machine manufacturers said this technology was impossible, because of its very short time control of approximately 10 microseconds. But “if it doesn’t exist, we make it,” is Honda’s way. We did not give up, but worked out how to make it real. I want to expand the use of this technology we have established within Honda to the smooth startup of mass production.
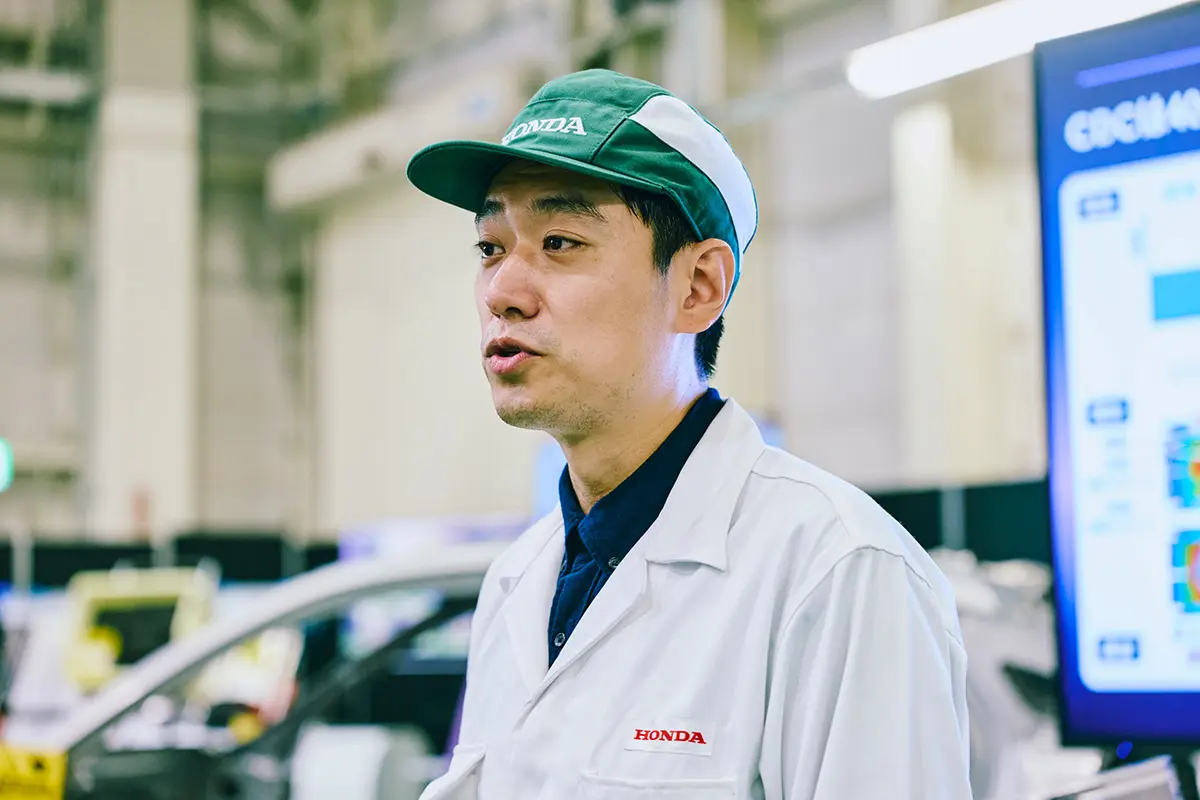
Honda’s Passion on Car Manufacturing Described at Honda 0 Tech Meeting 2024
The engineers shared insights and takeaways from the exchange of opinions and feedback with the participants of Honda 0 Tech Meeting 2024.
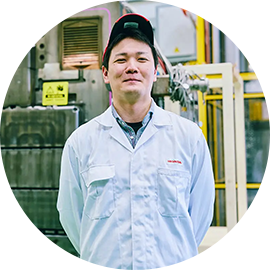
I was asked “Why megacasting, and not gigacasting.” Bigger is not necessarily better, and Honda feels that gigacasting faces challenges, such as difficulty in ensuring dimensional accuracy, high power consumption, large capital investment, and difficulty in transportation and repair due to the large size of its parts. In the spirit of Honda, which sets its own strict standards and develops its own manufacturing machinery and systems, we want to expand the application of megacasting to body parts in the future, and further contribute to Honda’s carbon neutrality efforts as its production division.
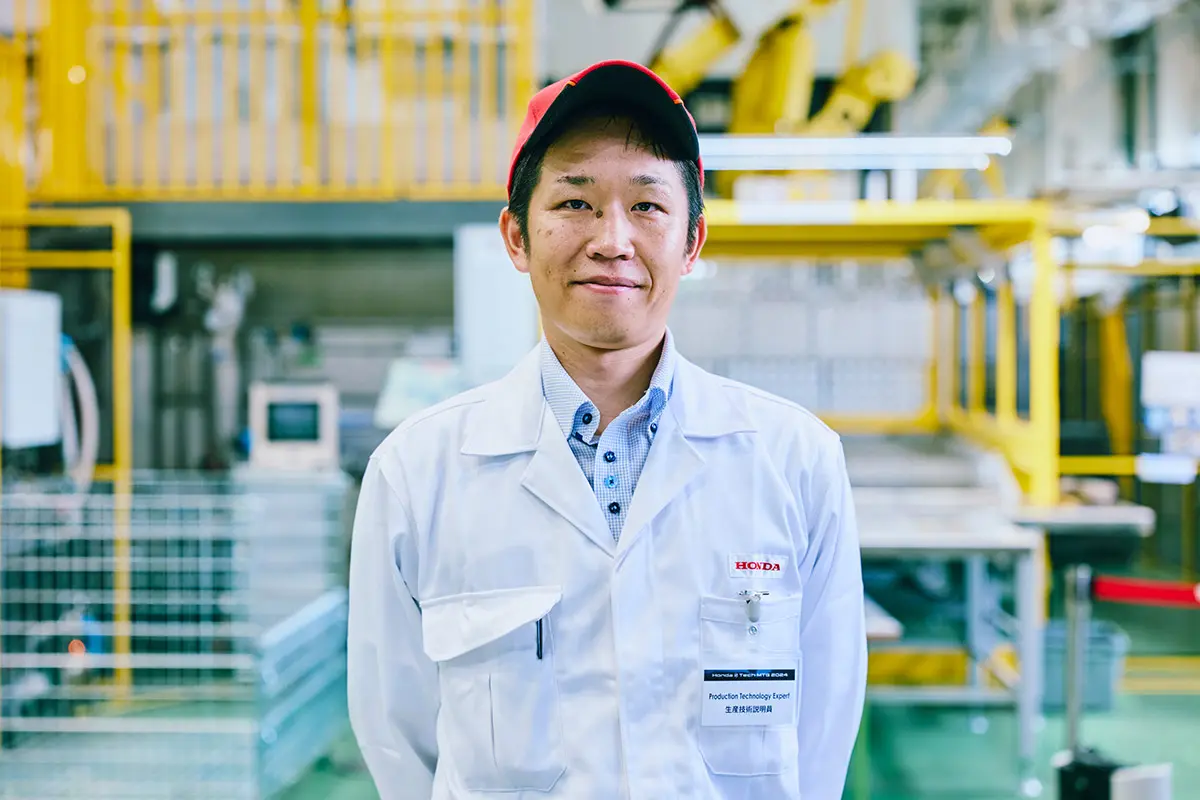
We have been given approval on the importance of keeping the technology in-house as we move forward with shortening processes. Honda 0 Series battery cases must first start up and enter production without issue, but then we aim to expand application to components such as body frame parts, by utilizing the knowledge and know-how we have gained. We believe that FSW is an important way to increase the flexibility and productivity of our products.
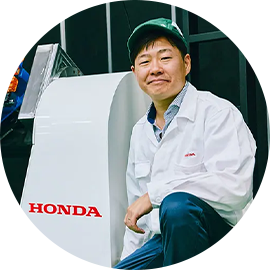
We expect that EV battery systems will change in many ways in the future, and we have received positive feedback on how to expand our flex-cell production system around the world after its introduction. We believe that realizing the flex-cell production system is one test cleared, and an important starting point for our production division to keep up with future Honda vehicles, which will continue to change and evolve.
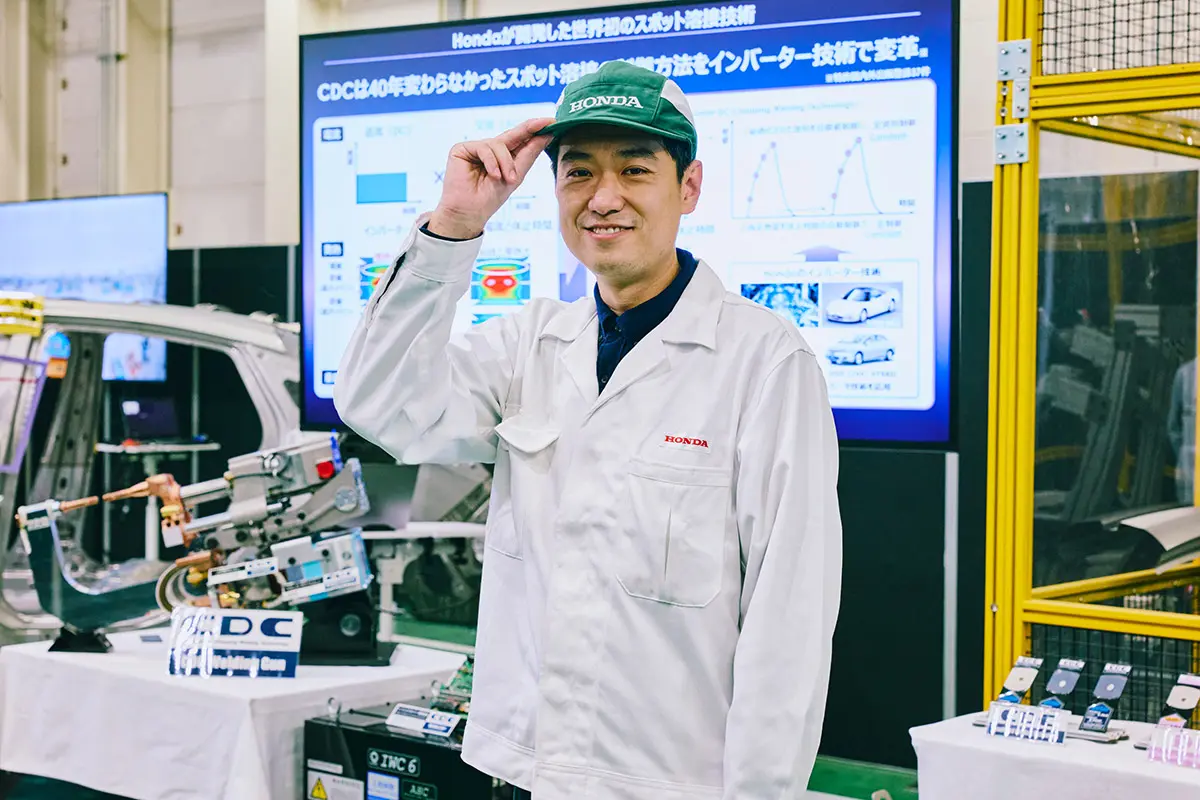
We received many comments that this is a very unique technology. It can be considered “Wise” technology because it can be implemented simply by replacing the welding gun and software in existing spot welding machines. We hope to utilize the know-how we have accumulated through the launch of the Honda 0 Series, and to apply this technology at Honda plants around the world to make Honda vehicles more and more “Thin” and “Light.”
<Related Articles>
Index
In order to cast parts that are larger than conventional parts, high mold clamping force is required to prevent the mold from opening when molten aluminum is poured in and pressure is applied. In preparation for Honda 0 series production, Honda introduced an appropriately-sized 6,000-ton large-scale casting machine for the first time in Japan to enhance manufacturing quality, and is now working to realize high-quality thin large-sized parts by applying its ingenuity and know-how accumulated through its casting technologies.