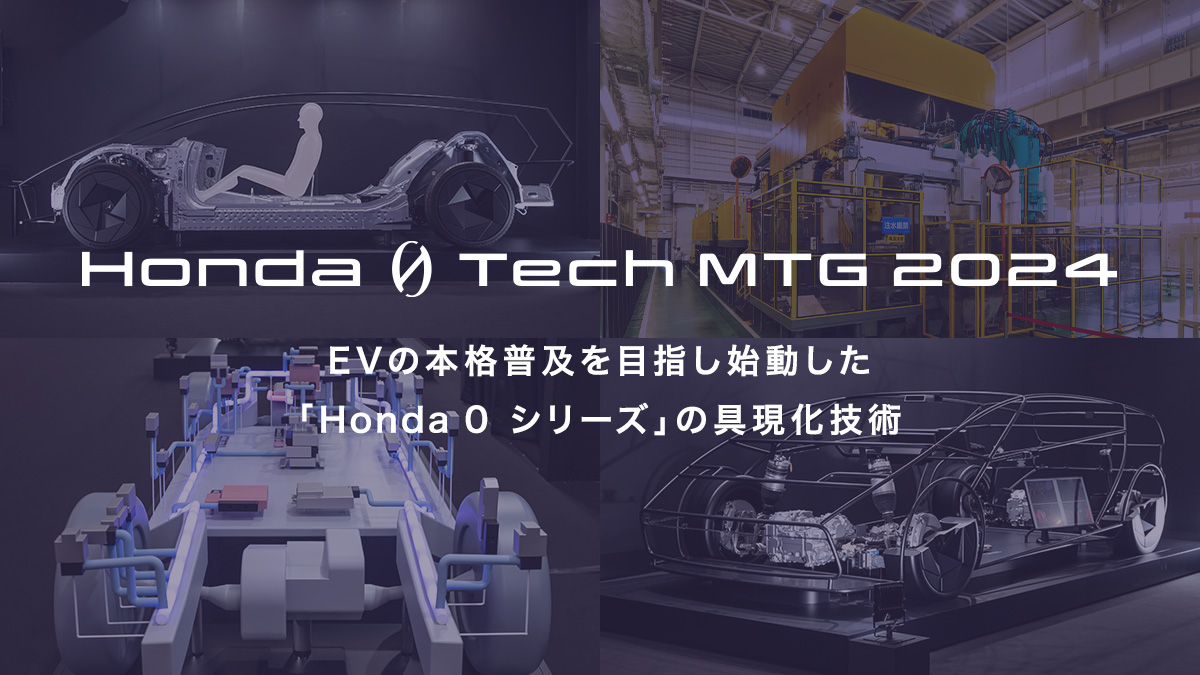
“Thin, Light”を可能にする生産技術
まったく新しいEV価値を持つ「Honda 0シリーズ」。その具現化を可能にしたのが、“Thin, Light” 「薄く、軽く」を成立させるための生産技術です。HondaはEVの本格的な普及期に向けて、従来のEVの概念を一新する薄型バッテリーパックの製造技術と、従来のレベルを超えた軽量ボディー骨格の成形・溶接技術を確立しました。

薄型バッテリーパック生産技術①<メガキャスト鋳造>
Hondaの国内工場に初導入した6,000トンクラスの大型鋳造機
薄型バッテリーパックはアルミケースの中に電池を敷き詰めた構造になっています。
従来のバッテリーパックのケースはおおよそ60点以上の部品を組み合せていました。これに対し「Honda 0シリーズ」では革新的なアルミ鋳造技術と接合・締結技術を確立し、適切なサイズで3点に集約した部品で構成されるケースを実現しています。

メガキャスト(6,000トン)による分割鋳造を採用することで、バッテリーパックの多様な仕様に応じたケースの作り分けを可能にしました。ギガキャスト(10,000トン)鋳造の場合は一体鋳造が可能ですが、中型モデル用や大型モデル用といった個別に作る必要があります。メガキャストでは共通部を作り部品点数を抑えることで、適切なサイズで製造コストを抑えた高効率な製造を可能にしています。

アルミ鋳造技術において、バッテリーケースの場合はエンジン車のトランスミッションケースに比べて薄型で大物の部品になるため、高品質を徹底的に追求しました。これまでエンジン車の量産を通じて改善・改良を重ねてきた鋳造技術のノウハウを活かし、バッテリーケースの高水準の内部品質と寸法精度を実現するために、3つの鋳造技術を確立しています。


①減圧鋳造技術
溶けたアルミを金型に流し込む際には、空気やガスの巻き込む量を減らす必要があるため、金型の構成部品の隙間から空気が入り込む箇所に、エンジン製造で培った特許取得のシール構造を採用。金型内を密閉することで高品質な鋳造を実現しています。

②金型温度調整鋳造技術
溶けたアルミを流し込む際に金型の隅々までしっかりと流し込むために、金型の温度を高過ぎず、低すぎない温度に調整することで、高品質な鋳造を実現しています。

③トリムと矯正を1工程化
鋳造後の水没(冷却)による収縮で生じる変形に対し、従来はトリム→矯正の2工程をショートプロセス化。 1工程で同時に行うことで、より高い寸法精度を実現しています。

バッテリーパックのアルミケースで確立したメガキャスト鋳造技術は、将来的にはアルミボディー骨格の部品製造などに適用拡大していきます。

薄型バッテリーパック生産技術②<3D摩擦攪拌接合(FSW)>
FSW:Friction Stir Welding
バッテリーケースの接合には、メガキャスト鋳造で作られた2つの部品を接合(突き合わせ接合)してケース本体を製作する工程と、そのケース本体にウォータージャケットカバーを接合(重ね合わせ接合)してバッテリー冷却回路を作る工程という、2つの工程に3D摩擦攪拌接合(FSW)を採用しています。

FSWは金属を溶かすことなく接合する技術です。回転するツールをワークに押し付け、その際に発生する摩擦熱でアルミを撹拌し、接合を行います。一般的なアーク溶接と比べて入熱量が少ないため変形を抑えることができ、接合部内部に欠陥が生じないことから、連続接合でも気密性や強度の高い接合を実現できるため、この製法を適用しました。
Hondaでは長年にわたりこの接合技術を活用してきた実績があり、2000年にはオフロード専用四輪バギーのアルミホイール、2012年には四輪量産車の骨格部品において、スチールとアルミの接合に世界で初めて採用しています。


接合工程においてもプロセスの短縮を図る新たな製法を開発しました。従来のFSWでは、接合する部品同士の段差や隙間、素材表面のうねりに対して、機械加工を施してから接合を行っていました。今回は、メガキャスト鋳造技術による部品の高精度化に加え、突合せ面以外に機械加工を施すことなく、アルミ部品の素材面に直接FSWを施せる治具やツールを具現化。これにより、機械加工の3工程を省略しショートプロセスで高品質な接合を実現しました。

①突き合わせ接合
バッテリーケースの2つの部品を接合する突き合わせ接合では、まず、2つのワークをクランプする際に、アイロンがけの要領で中心から外側へ順にクランプし、2部品の接合ラインを合わせます。続いて、クランプ部に生じるわずかな段差や隙間には、広い入熱範囲を持つ回転ショルダータイプのツールを使用し、それらを埋める効果を持たせています。平坦部は約3°の前進角をつけて接合しますが、R部も同じ前進角で接合するとショルダーの当たり方が変わり、入熱量が不足することがあります。そのため、前進角をきめ細かくコントロールし、入熱量を安定させることで、高い接合品質を実現しています。


②重ね合わせ接合
ウォータージャケットカバーの重ね合わせ接合では、接合前のバッテリーケース本体表面に約2mmのうねりがあるため、固定ショルダータイプのツールを使用してワークを押さえつけ、ケースとウォータージャケットカバーの接合面の隙間をなくして接合します。このツールは追従性が高く、ウォータージャケットカバーの接合面を確実に抑え込むことができるため、隙間が原因で発生しやすいバリがほとんど生じず、長い接合ラインで安定した接合を実現できました。

薄型バッテリーパック生産技術③<フレックスセル生産システム>
Hondaはこれまで、生産の自動化や工程の効率化などに取り組み、さまざまな技術開発によって高効率な生産ラインを構築してきました。2013年に稼働した寄居完成車工場では、多様な機種が混流するなかで、重量物や高精度な組付けが求められる組立作業の自動化を導入する事で高速で高効率な生産ラインを実現。2016年にはプラチンブリ工場に、通常のライン生産方式とは異なり、作業者が広い範囲の工程を受け持ち、複数部品の組み付けを行うセル生産方式の生産ユニットをメインラインに組み込んで流動させた、世界初となる「ARCライン*」を導入。生産効率を大幅に向上させました。
*Assembly Revolution Cell
埼玉製作所寄居完成車工場 / ホンダオートモービル(タイランド)カンパニー・リミテッド プラチンブリ工場
一方で現在は、EVシフトはかなり進んできたものの、売れ筋への変化追従や製造業における労働人口の減少という課題もあります。
こうした時代の流れに対してよりフレキシブルに対応していくために、Hondaはこれまで培ってきた生産技術を基盤に、生産として更にフレキシブルな構えができるプロセスとして、いっそう進化した生産システム「フレックスセル生産システム」を構築しました。

フレックスセル生産システムとは
従来のラインプロセスは、生産量の変化や製品仕様の変化に追従するために、稼働を停止させ、ライン全体の改造・移設をした後に生産を再開する必要がありました。この方法はラインの安定稼働に時間を要し、生産効率を下げてしまう原因でもありました。また、直列ラインであるが故に1つの装置が停止すると生産ラインも停止してしまい、生産量が低下するという事実もありました。

そうしたなかでHondaが導き出したのが、生産性と柔軟性を両立させるためにセル生産を全面的に取り入れるという生産方式です。このフレックスセル生産システムを導入することで、生産活動を維持しながら増産や仕様変更に応じて必要な部分にセルを追加するなどしてスムーズに対応することで、需要への追従性を高めていきます。また、自動化率を引き上げても、安定した稼働率を維持することが可能となります。

薄型バッテリーパックの組み立てラインでは、自動化セルゾーンと作業者セルゾーンに分かれており、部品などの搬送はAGV(無人搬送車)がすべて担います。AGVが物流エリアとそれらのゾーンの経路を自在につなぐことによってフレキシブルな生産に対応します。
フレックスセル生産システムの大きな特徴は、まずは少量生産から始まり、市場のニーズに合わせてセルを加えていくことで生産量を増やすことができます。また、セルを組み替えることで、工場のレイアウト制約に縛られずに生産ラインを構築することが可能となります。

フレックスセル生産システムを支えるデジタル&知能化技術
フレックスセル生産システムはセルを増加させていくことで、問題が生じてしまうことが考えられます。「搬送経路の複雑化」と「セルの組み合わせパターンの複雑化」です。こうした問題の発生を防ぐために、デジタル化や知能化技術によるがVC*が不可欠となります。
* Virtual Commissioning

①デジタルツインシステム
セルの増加や組み替えは容易に対応できる一方で、それによって搬送経路が複雑化します。AGVの台数や分岐点が多くなるため、事前のシミュレーションで実際の現場に則したより精度の高い検証が必要です。これを解決するのがデジタルツインシステムです。
デジタル空間と現実世界が一致していることが事前に確認できるため、生産準備段階で搬送経路のソフトウェアの完成度を圧倒的に高めることができます。


②デジタルツールの活用
セルの組み合わせパターンの複雑化という問題については、生産量が低下した場合、従来の直列ラインでは特定しやすかったものが、組み合わせが複雑化してしまうことで、どのセルが原因なのか特定しづらくなりかねません。そこでデジタルツールを活用し、問題が発生する条件の共通点を検出します。

次に、検出した結果を解析。あるプロセスの特定のセルで生産したことが共通点となり、そのセルを重点的にチェックしていきます。このようにデジタルツールの活用によって原因究明の大幅な時間短縮を実現することで、ライン全体の安定稼働につなげています。
③知能化技術の活用
さらなる効率化を目指し、AGVの経路指示システムに知能化技術を活用することも予定しています。ライン全体の稼働データが集まった段階で知能化技術を導入。AGVの混雑状況、各設備の稼働状況、人による作業時間のばらつきなどを考慮し、ライン全体を把握しながらAGVの経路をリアルタイムに最適化することで、よりいっそうの安定稼働、生産能力の向上につなげていきます。

④知能化技術を用いた品質保証
バッテリーパックの組み立てにおいては、特に確実な作業による品質保証が求められます。従来は人による組み立てを、人が品質保証していました。これに対し、作業者が装着するカメラなどで組み立て作業を認識させることによって、品質保証はデジタルツールが担います。これにより作業者の精神的な負担を軽減するとともに、品質保証を大前提に、さらなる効率化を図ることもできます。

Hondaではこのようなデジタルツールを「Honda 0シリーズ」を皮切りに順次展開していく予定です。
薄型バッテリーパック組み立てライン「フレックスセル生産システム」
軽量ボディー骨格溶接技術<CDC溶接>
CDC:Constant DC Chopping
CDC溶接とは従来では不可能だった超ハイテンを含む3枚重ねの接合を可能とする、世界初のインバーター技術を応用したスポット溶接技術です。
ボディー骨格に求められる対衝突性能において、EVの場合はバッテリーがフロア全面に搭載されるため、乗員保護とバッテリー保護がキャビン骨格に対してより厳しく求められます。センターピラーを例にとると、外板の薄板軟鋼と、強度を受け持つ内部の厚板(超ハイテン材)からなる3枚重ね構造となっており、この、薄・厚・厚というハイテン材を含む異なる板厚の組み合わせが、溶接を非常に難しくしています。しかもEVの航続距離を向上させるために、軽量化も達成しなければなりません。

ではどのように高強度化と軽量化を両立させるのか。
下の図は、縦軸に車体強度、横軸に車体重量を示しています。従来の成行き構造に対して、CDC溶接はより高ハイテンの厚板を溶接できるようになり、材料そのものの強度が上がります。それに伴い使用する材料が削減され、軽量化と高強度化の両立が可能になります。強度がさらに必要な部位では、ハイテン材の板厚をより増した溶接が可能です。どちらも板組みも従来の技術では溶接ができませんでした。

現在、量産車の骨格溶接で主流となっているのは直流(DC)溶接で、ロボットがこの溶接ガンを把持し、先端の電極で溶接箇所を挟み、約1万アンペアほどの電流を流すことで板を発熱させ溶接します。

このDC方式は、インバーター制御により溶接ガンを軽く小さくすることができ、ロボットへの搭載や自動化を可能にするなど、Hondaは長年にわたり進化・改良を重ねながら採用してきました。
しかし近年は、材料の進化に伴い厚板のハイテン化が進むと、厚板は発熱しやすくスパッタ(溶接時に溶融金属が飛散して固まった金属粒)が発生して強度の低下を招き、薄板は反対に発熱しにくく溶接不足となる、という課題が顕在化してきました。
一方、AC(交流)方式は古くからある溶接方法で、重量が非常に重いため自動化が困難とされていますが、高いピーク電流により薄板側で発熱が促され、休止時間により厚板側の発熱が抑制されやすい特性を持っています。
そこで、Hondaの多様なインバーター技術を応用し、小型軽量でありながら高いピーク電流と休止時間を確保する波形制御を実現したのがCDC溶接です。
●高いピーク電流をもつ最適化された波形を目標値制御することでコンスタント(一定)に保つ技術
●休止時間を自動で制御することで指定の熱量をコンスタント(一定)に保つ技術
この2つの着想技術から「CDC」(コンスタントDCチョッピング)と名付けました。
Hondaは世界初のインバーター技術を応用したスポット溶接を実現したことで、スポット溶接の制御方法を革新的に進化させました。

さらにCDCの大きなメリットは、既存のロボットにガン交換とソフトの追加で対応できる点で、大掛かりな改修工事をすることなく量産導入が可能です。溶接ガンのトランスの高出力化、電流センサーの追加、そして既存の溶接コントローラーにCDCソフトをインストールすることで対応が可能。CDCは従来手法のDC溶接とAC溶接それぞれの良いところを高次元で成立させた、理想とも言える新しい溶接技術です。

CDC溶接のメカニズム
従来のDC溶接では単調に鉄の溶融池が拡大します。そのため溶融池の壁が薄く、決壊してスパッタが発生します。一方、CDC溶接ではパルスにより溶融池が拡大・収縮を繰り返して厚い壁を効果的に作るため、スパッタを抑制します。また、高いピーク電流によりDC溶接では存在しなかった、薄厚間の広範囲の発熱部位を形成します。この薄厚間の溶接と厚板間のスパッタ抑制という背反要素を両立させたスポット溶接技術がCDCになります。

CDC接合技術 デモンストレーション1
CDC接合技術 デモンストレーション2
Hondaは今後、CDC溶接技術をさまざまなEV開発に展開していくことはもちろん、エンジン車・ハイブリッド車へと全領域に適用を拡大していきます。
