The VTEC Engine / 1989
Variable Valve Timing for Power and Fuel Economy
In order to develop its next generation of engines for the mainstream market, Honda's NCE (New Concept Engine) program was launched in March 1984. Specific targets identified through the program included high torque in both the low- and high-rpm ranges and dramatic increases in horsepower per liter. The program was a success, resulting in a series that included the DOHC engine found in the 1985 Civic and Integra, and the SOHC center-plug engine in the 1987 City.
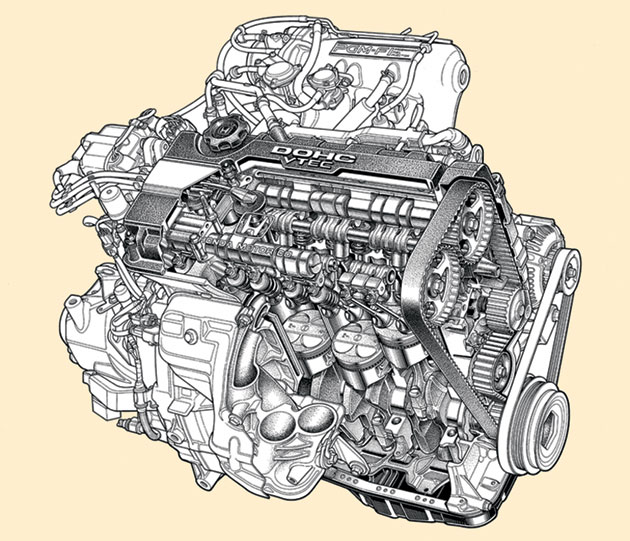
The structure of Honda's VTEC engine, the ultimate expression of an original concept
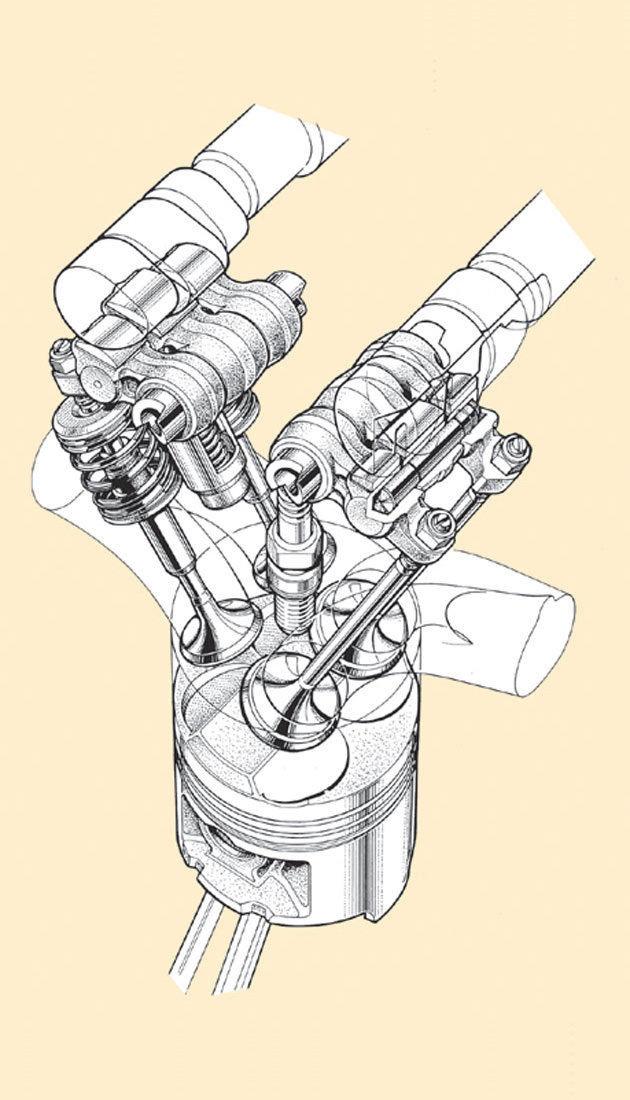
The DOHC/VTEC mechanism with a set of three cam followers and rocker arms on both the intake side and exhaust side. A wide torque band is achieved through the speed-sensitive switching of cam hills.
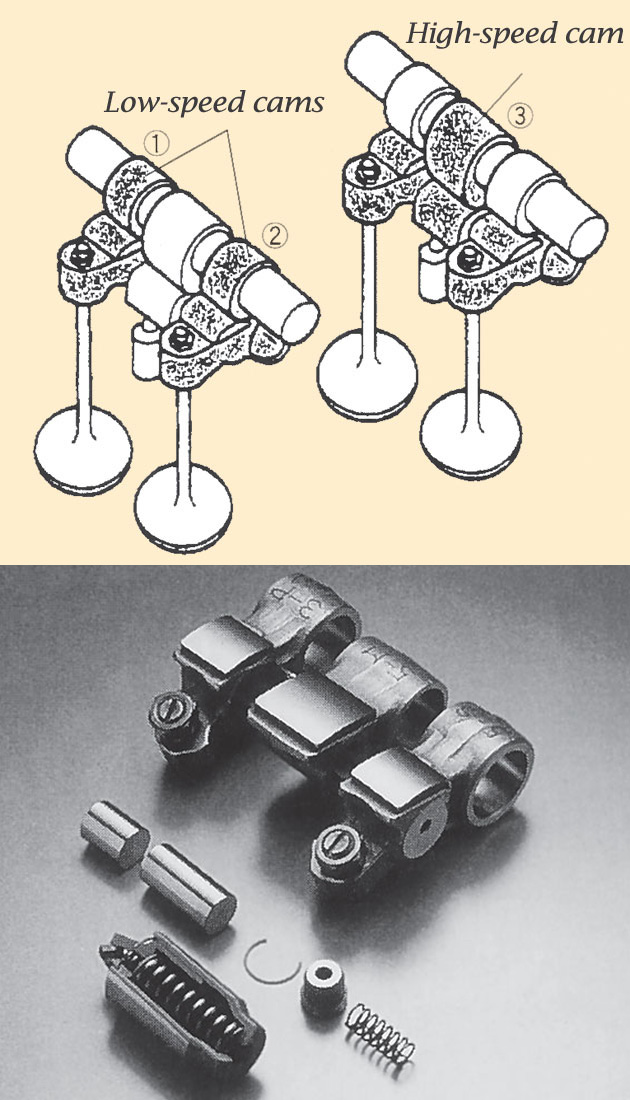
The two low-speed cam followers and one high-speed cam follower form the basis of VTEC technology
Ikuo Kajitani, who was employed in the First Design Dept at Honda's Tochigi R&D Center, was involved in the development of these four-valve engines. Through his experience in engine design, Kajitani had become convinced that Honda's next engine should offer a mechanism that could alter the timing of the valves.
"Characteristically," Kajitani said, "four-valve engines are known as high-revving, high-output machines. And for that reason we knew it would be quite difficult to achieve low-end performance if the engine's displacement were too small."
Problems certainly arose during the process of development. A reduction in the valve's interior angle, attempted in order to increase low-end torque, resulted in a broken timing belt and valve spring as the unit reached the upper range of revolutions. To address the problem, the development staff put in uncounted hours studying how to balance these two critical areas of engine performance. They knew they had already succeeded with their DOHC and SOHC powerplants, but to develop a new unit that would outperform its predecessors they would have to bridge the gap between the low end and the upper limit.
One group already had examined the idea of switchable valve timing. In January 1983, a year before the NCE program began, a research team was formed to study the mechanism as a means of enhancing fuel economy. Even though by the end of 1982 Honda engines were already capable of a world-beating 50 miles per gallon (mpg), there would be an effort to improve.
A possibility was thus identified through the study of a new valve mechanism. Specifically, it was believed that the installation of a new set of cam followers and rocker arms for high-speed operation on the intake and exhaust sides would help, along with the switching of cam hills according to engine speed. This was to be their solution to higher engine efficiency.
This was the so-called "valve stopping + variable valve timing" mechanism employed in the NCE program. As a core technology for Honda's proposed new line of engines, the mechanism then underwent a program of study and refinement under the careful supervision of Honda's research staff. Eventually the mechanism evolved into Honda's VTEC (Variable Valve Timing & Lift Electronic Control System) engine. Launched via the 1989 Integra, this innovative technology surprised the world with a new level of performance from a compact, fuel-efficient engine.
Designing a Dream: A Hundred Horses per Liter
"Find a new technology to lead the next generation of Honda engines." This was the directive issued by the top management at Honda R&D, and in response a project was proposed to expand the variable valve-timing approach. Since it had originally been created to improve fuel economy, the engineering staff's new assignment would be to combine outstanding mileage with impressive output across the entire powerband.
This proposal was approved as a D-development project, and was instituted in November 1986. The objective was to develop a new engine for the 1989 Integra.
Kajitani, serving as LPL of the engine development project, was excited about the new opportunity. He knew that working on VTEC technology would not merely solve many problems he had experienced in development of the DOHC and SOHC engines, but would play a major role in the creation of future powerplant designs.
Kajitani believed the specification for Honda's new engine - 90 horsepower per liter, or 140 in all from a 1.6-liter unit - was not really reflective of the 1990s approach. After all, the DOHC engine already produced 130 horsepower, but the new engine would only have ten more than that. He knew it just was not enough. Then, as if to read Kajitani's mind, Nobuhiko Kawamoto, then president of Honda R&D made a thoughtful suggestion:
"Why don't you raise your target to 100 horsepower per liter?" he asked.
It had always been thought that a normally aspirated engine could not be made to produce 100 horsepower per liter. But Kajitani could see in Kawamoto the passionate vision of an engineer, and he felt inspired by such a straightforward proposal. Of course, he knew it would mean 160 horsepower from only 1.6 liters, at a maximum of 8,000 rpm.
"I understand," Kajitani replied. "We'll make that our goal." Though he was by no means certain such a thing could be done, he certainly had the energy to try. Kajitani knew that in order to embark upon a challenging path, they must set their goals high.
An Open Invitation to Participate
It was decidedly easier to set the goal than to convey it to the development staff. When Kajitani sat down with his associates and gave them the news, he was immediately swept back by a barrage of questions.
For example, the target 8,000 rpm was almost 20 percent higher than the maximum output of 6,800 rpm achieved by current 1.6-liter DOHC engines. Moreover, the inertial force upon various engine parts would increase by 40 percent. Naturally, the engine would be subject to considerably higher loads due to its increased interior heat. Therefore, to reduce inertial mass under such high revolutions, the weight of each part would have to be reduced. At the same time, it was obvious that doing so would result in lower rigidity, causing problems in durability and reliability. No one knew how to achieve the goal or what approach they should take. A big debate was started within the team as to whether the goal was even reachable.
It was a natural reaction, of course. They were told to develop a dream engine like nothing they had ever seen before. To achieve it, they would have to enter a new realm of technology. "The more you know, the farther you can see," said Kajitani.
"The team members couldn't forget their fears, as long as there was the possibility that they might fail."
Discussions were held day after day for three straight months. One day, Kajitani decided they had had enough of such discussions, and so gathered his team for an announcement.
Though each team member was interested, the team as a whole needed a push before it could accept the challenge and reach for a new level. Kajitani announced his decision to give that push. He knew that timing would be crucial to the direction of such a large group. Accordingly, he gave them ample time to express their opinions. Eventually, the discussions served to align all vectors in a single direction. When Kajitani finally addressed the engineering staff, he was able to do so knowing that each of them had the burning desire to create the world's best engine.
"I have decided I'm going to try," he said, speaking to the group of more than 100 engineers. "It's an important project, but you don't have to participate if you don't want to." No one came forward to say he was leaving the project, for despite the fears and doubts it was the kind of project no engineer could refuse.
Discerning Genuine Technologies
It all began in the planning stage, wherein the team identified approximately thirty new mechanisms and technologies they would need to introduce in order to secure a stable VTEC system. These included a valve-operating system with a hydraulic timing selector pin, a small hydraulic tappet mechanism built into the rocker arm, and weight-reduction techniques to achieve higher revolutions and output. However, time and resources were limited, and it would be nearly impossible to achieve all of their objectives. As a matter of efficiency, priority items were selected with an emphasis on satisfying the engine's product requirements. For the items selected, detailed specifications were set and technological feasibilities examined.
During the selection process, the team came across technologies they believed were unnecessary in meeting the target requirements, along with unverifiable technologies which, if found to be flawed, could affect the VTEC mechanism itself. For advice the development team arranged a consultation meeting with members of the evaluation committee, whereupon the development team listed items they had originally wanted to adopt but now wished to cancel.
The discussions produced no results, since both sides refused to give up any ground. Kajitani was not certain which technologies should be used and which should be set aside. He kept asking himself, "Is this technology genuine?" That was exactly what Kawamoto would say.
"When I wasn't sure whether to introduce a new technology, Mr. Kawamoto would ask me if the technology was genuine. If I could honestly answer 'Yes,' he'd say, 'Okay, then do it.' When he asked me if it was 'genuine' or not, I was confused about what to say. After all, sometimes it's difficult to tell what's genuine and what isn't. Personally, I thought of a technology as genuine if it had been in the market around for ten years, but Mr. Kawamoto had a different definition. Even so, a technology that's been for around ten years is one that's accepted by society. In that sense, there shouldn't be any problem adopting such a technology to all models."
Several consultation meetings were held, some of them deep into the night, and at last the committee members accepted the development team's request. Such difficulties were commensurate with the scope of their proposed achievement. The difficulties the team endured through its discussions with the committee helped bring the VTEC engine to life.
Pursuing Excellence Through Trial and Error
The start of development meant, of course, that the team would begin facing the first of many anticipated challenges. There was often fear in Kajitani's mind, as well. "I thought we might not be able to achieve it because the goal was too high," he said, recalling the many travails of project development.
It was quite difficult, for example, to balance the valve-timing lift against the load placed on the timing belt, which would increase at high engine speeds due to the spring and other factors. Although it was a problem needing a solution in order to achieve the target output, such an answer would not be easy to find. To make matters worse, they found that the low-speed single-valve timing system was not applicable because it had been patented by another company. After examining numerous countermeasures through laborious trial and error, the team decided to change the entire specification surrounding the valve operating system. Subsequently, they introduced the combination valve-timing system after reviewing the valve diameter, lift and port shape, and identifying settings to ensure sufficient output. Further, they created a lightweight driven pulley using high-density, high-strength sintered alloy, and modified its shape for reduced thickness. This resulted in a 10 percent lower moment of inertia. Through these efforts the team satisfied the requirement for timing-belt load while achieving its output objective.
Output across the full rev range was increased by widening the diameter of the intake valve from the conventional DOHC engine from 30 mm to 33 mm. Also, the team adopted valve timing and lift settings that were comparable to Honda racing engines in order to enhance volumetric efficiency. The improved output resulting from that technique actually served to improve performance at high speeds. Additionally, measures were taken to reduce intake resistance. At last, the goal was reached, with a full 160 horsepower at 7,600 rpm and a redline of 8,000.
Low-speed torque, an initial project objective, was obtained by changing the low-speed cam's setting from the traditional 35 degrees to 20/30 degrees ABDC (after bottom dead-center). This permitted the intake valve to close early, drastically improving the engine's volumetric efficiency. Since the engine now had higher efficiency at low speeds of operation, a broader torque band could be realized.
The implementation of new materials was certainly a factor in the successful application of these technologies. For example, since the VTEC engine's three cam followers must be positioned in a single bore, the camshaft offers relatively limited cam width. Therefore, the shaft must be designed to withstand high surface pressures. To achieve this, the team developed a new camshaft of cast steel. The shaft was made of new high-carbon, high-chrome cast steel alloy, which was given a combination of heat and surface treatments. As a result the unit's extreme rigidity increased its critical surface pressure by as much as 40 percent.
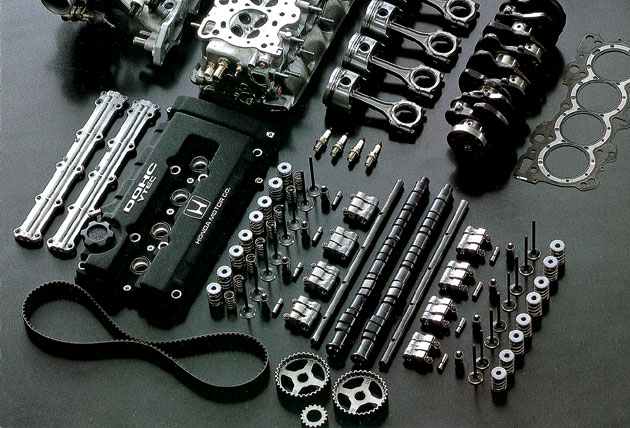
The VTEC engine parts used around the head. Each part was made lighter and more rigid in order to increase output and withstand greater loads at high engine speeds.
The exhaust valve, too, employed a newly developed material made of a nickel-based, extremely heat-resistant steel combined with molybdenum, titanium, and tungsten. Accordingly, its heat resistance was increased by 30 percent. Moreover, the larger diameter of the valve's umbrella section and its reduced stem thickness produced a drop in weight of nearly 20 percent. These ideas and effort gradually shaped a reliable VTEC engine.
Applying the Technology to All Honda Models
The VTEC engine had finally revealed its complete performance profile. However, the success of D-development only meant the start of a critical phase. In order to ensure absolute reliability in mass production and introduce the engine to the market with confidence, the team had to guarantee the functions of all mechanisms and parts. In addition to a significant responsibility for product reliability, the team had special expectations regarding the VTEC engine. Said Kajitani, "We all shared the determination to apply these technologies to every Honda model."
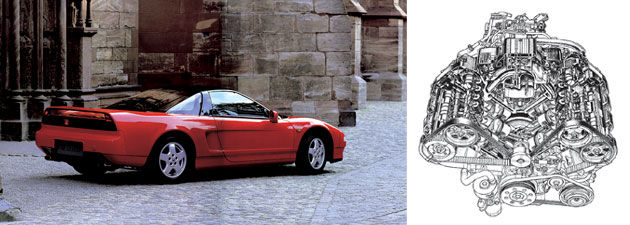
The V6 3.0-liter DOHC/VTEC engine powering Honda's flagship NSX sportscar
The team's view of it was that VTEC technology shouldn't be limited to the Integra alone but further improved it could be adapted to Honda's future model developments. As such, the initial specification would have to meet customer expectations. In fact, the team had gone through a repeated process of trial and error designed to eliminate all possible problems, however minor they might have been. Actually, at the onset of engine development their greatest concern was the assurance of engine functions. They knew how difficult it would be to guarantee a complex switching mechanism.
For example, the selector pin had a thickness of only 10 mm, so its operation was affected by wear of just several microns. So, in many cases the more delicate the task the more worrisome it was.
"That's why we so thoroughly carried out our malicious tests," said Kajitani. "We were very near the point of overdoing it."
A malicious test is one designed to verify a mechanism's reliability and performance by subjecting it to conditions far in excess of those anticipated during actual vehicle operation. In case of VTEC, numerous tests were repeatedly carried out for all parts, including the timing belt, camshaft, rocker arm and selector pin, to meet the target switching performance of 400,000 events. The team even analyzed the effect of changing loads on the control of low- and high-speed valve timing. Fail-safe*1 measures were further incorporated in the hydraulics and electrical systems. In this way the development staff not only eliminated its initial fears but achieved a degree of reliability that was well beyond the target value.
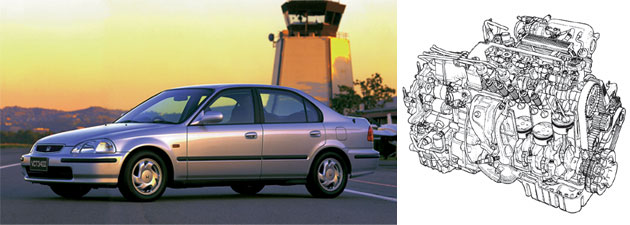
The 1996 Civic equipped with the 1.5-liter, three-stage SOHC/VTEC engine
Note
*1: Fail-safe feature: An auxiliary device or system is used to ensure continued operation in the event that a system failure occurs.
The Confidence Needed to Innovate
Honda's new Integra, equipped with the DOHC/VTEC engine, was introduced to the market in April 1989. The VTEC technology drew considerable praise as the world's first valve mechanism capable of simultaneously changing the valve timing and lift on the intake and exhaust sides. In addition to its impressive output and high-revving energy, the VTEC powerplant boasted superior perform-ance at the low end-including a smooth idle and easy starting-along with better fuel economy. It was truly a "dream engine" - a completely new driving experience for motoring enthusiasts around the globe.
"Everyone of us had pledged to do his utmost to create a world-class engine," Kajitani said. "We were confident that variable valve-timing technology would be the next big thing. After all, we had overcome the challenges of development and testing because we knew that only our very best effort would establish this technology.
The DOHC/VTEC engine was subsequently adapted for use in the NSX, Accord and Civic. Following the SOHC/VTEC engine, and then the VTEC-E in 1991, this technology evolved into the three-stage VTEC engine introduced in 1995, which demonstrated an even greater degree of efficiency in output control.
Accordingly, the VTEC powerplant is now a genuine technology in every sense of the term. This is a benefit shared by the entire Honda organization worldwide, thanks to the dedicated efforts of a talented and courageous development staff.