The Airbag System / 1987
A Project in Search of Direction
A platform car carrying a test dummy begins moving, quickly reaching a speed of 30 miles (48 kilometers) per hour as a small crowd of staff people watch in eager anticipation. Then comes the moment, with a thunderous "Bang!" The onlookers could see the dummy sway in its seat; moreover, the impact was so great that even those standing at a distance could feel it.
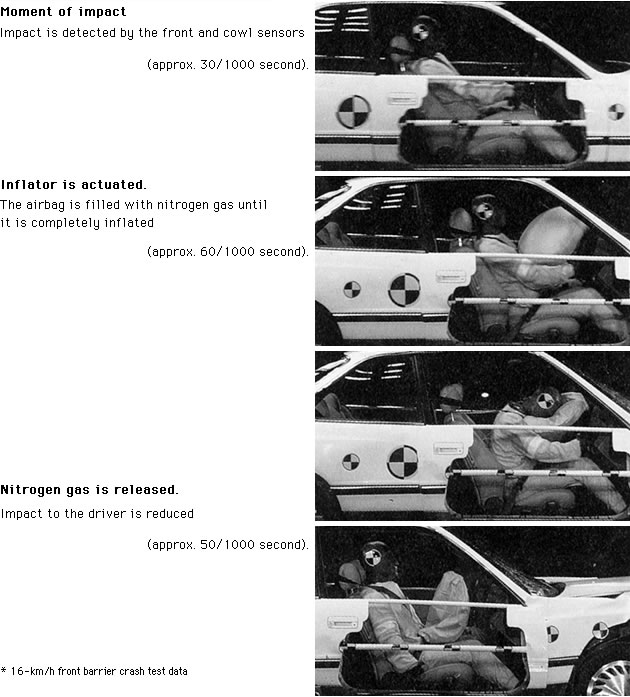
"Okay," someone says, affecting a tone of confidence. "We must have done it right this time." However, that person's hopes are quickly shattered when it is found the dummy had plunged forward before the airbag inflated.
It was always the same: They could not seem to inflate the bag within the target space of time. Of course, that particular window was only a fraction of a second, 0.003 sec. to be exact. The development staff had already experienced this failure a great number of times. Every test started with the highest hopes, only to end in disappointment as the test staff realized they had not achieved the correct timing for inflation. However, no one had the luxury of feeling down about it. They knew that if they couldn't leap this hurdle, no one could.
The year was 1975, and Honda had just begun an independent development project for an airbag system. One day Motohiro Okada, manager of the project, handed a notebook to Kiyoshi Honda (no relation to Soichiro Honda), a member of the development team. "Read this information," Okada said. But the book was nearly empty, except for a single remark about a test procedure designed to measure the sound of a "bang"; the sound an airbag makes at the instant of inflation. Since they had no development partner to rely upon, the staff had to start by groping in the dark for any available clue.
It seemed the moment was right for Honda to develop an airbag system. Ever since a 1970 review by the United States Congress there had been ongoing debates as to whether the automakers should be required to equip their passenger cars with passive restraint systems. Such systems would have included passive seatbelts, airbags and other devices that don't require an intentional action by the user in order to be deployed. Ford and GM had already carried out fleet tests in 1972 and 1973, respectively, and it was simply no longer possible to sell cars to the consuming public while claiming to the authorities that safety was a hindrance to production and marketing.
Honda, in order to develop its own airbag system, had decided to employ the "concurrent implementation of heterogeneous projects." Specifically, two teams would be formed, competing against one another with independently contrived airbag mechanisms. In Honda's case, one was based on an outside-air induction system, while the other relied solely on a charge of gas. Although both types had cleared the first hurdle with sufficient amounts of inflation, the gas-only system was ultimately chosen due to its simpler mechanism.
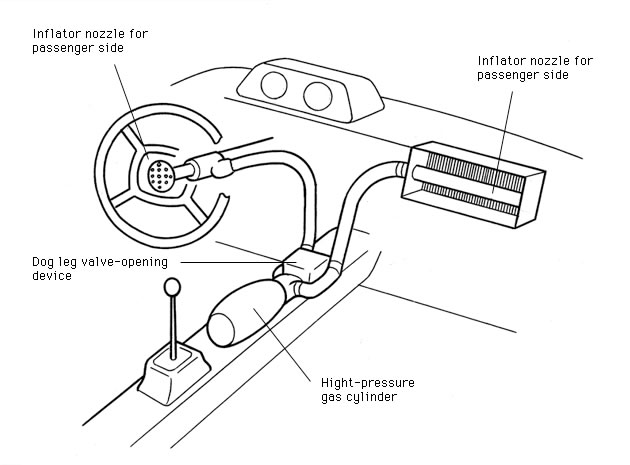
A gas-only dual-airbag configuration covering both the driver and front passenger. The system is linked to a 1500 cc cylinder filled with gas compressed to 400 barometric pressures.
According to the results of their crash tests, the team decided they had to increase the efficiency of gas blow-out. Therefore, the gas cylinder's pressure setting was increased to 400 barometric pressures. At that level, whatever knowledge they had would no longer apply. The staff had to think for themselves and try out each idea on their own.
"The creation of a new technology means there's no one else who has the information you want," said Kiyoshi. Honda. "We could consult experts in related fields, but to put all the pieces together in a complete system was another thing entirely."
The journey was an ongoing succession of obstacles. So, whenever the development staff hit a wall, they would go to experts in the field and learn from them. They would correct drawings, and often weld parts and work sheet metal themselves. Through these efforts, the crash speed gradually increased to 35 miles per hour. At the third evaluation meeting held in January 1979, the team finally succeeded in inflating the bag in time.
Not Ready for Production - The Decision to Give Up
The gas-only system turned out to be a fairly large device, once it was completed. However, in the development stage the most important task was to verify functions, so there was no time to worry about the amount of space it occupied. In addition to its functionality, there were several problems to be addressed, such as the danger of carrying a gas cylinder under 400 barometric pressure, the reliability of the valve-opening device, and thick, hard piping. As long as these problems went unresolved, there was no way the system could ever be employed in mass production.
The team therefore changed its direction in September 1979, focusing on a system with a practical specification suitable for mass production vehicles. Specifically, they began developing a mechanism for powder-actuated inflation that would generate gas via the combustion of gunpowder.
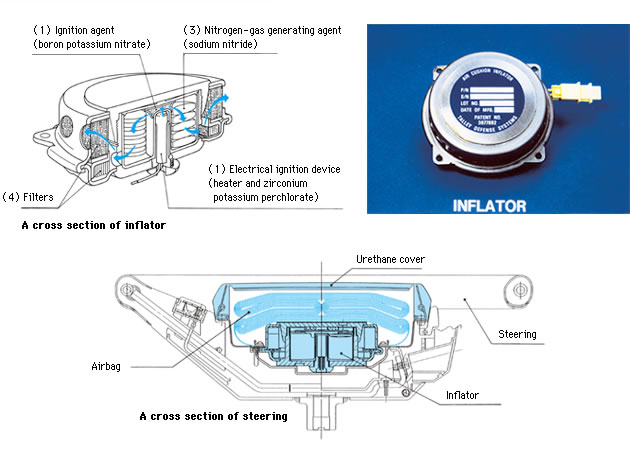
The powder-actuated inflator that provided a significant boost toward a production-ready system
That stage of development did not go as smoothly as they had hoped. With the powder-actuated system there would be higher gas temperatures, meaning that the bag would inflate more readily. However, the bag could not provide sufficient passenger protection. The reason for that was, the high-temperature gas created through powder actuation was naturally subject to higher molecular activity. In other words, the powder-actuated system could inflate the bag with fewer molecules, but it offered less protection compared to the gas system. Eventually the problem was solved by increasing the dimensions of the bag and choosing a more powerful inflator. However, the solutions didn't come without an exhaustive process of trial and error.
The development team finally completed a mass-production airbag system in 1982, seven years after the project began. The final hurdle was an evaluation meeting, the intent of which was to approve the system for manufacturing. However, a surprising proposal was made by Hideo Takeda, who had succeeded Okada as the second project manager.
"I don't think we should introduce the system yet, because consumers in general are still unfamiliar with the airbag itself," said Okada.
Airbags are critical components that affect passenger safety, so Honda could not be too cautious about the introduction. There was concern that the airbag might be misused by those who were not familiar with its intended use. Also, should there be any malfunction or defect, the user would suffer serious consequences. Although Okada was confident in the system's performance, he was still reluctant to make it the first airbag system. Perhaps there was some doubt concerning its performance, from the standpoint of engineering. After all, absolute reliability was the essence of the airbag system.
Learning from NASA
The development team was reorganized under a new objective at the end of 1982. Their goal was now to enhance the reliability of the airbag system so that it could be produced as an SRS (supplemental restraint system), meaning one supplementing the function of seatbelts. Thus the team was reduced from over ten to four, with Saburo Kobayashi acting as the third project manager. However, the team remained every bit as enthusiastic as before.
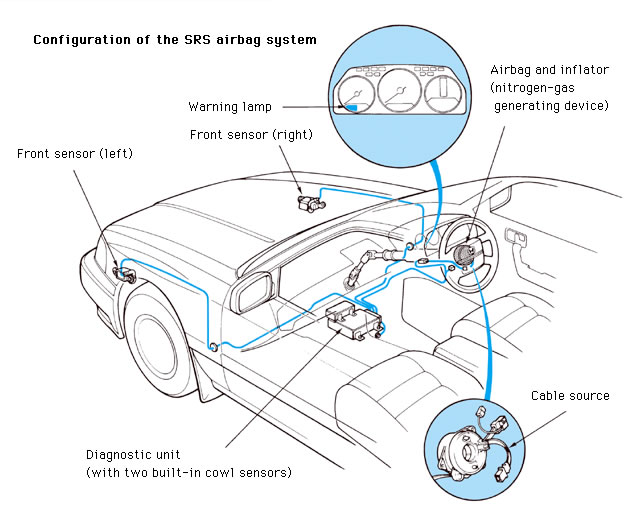
"We had acquired the basic technologies and established the necessary functions," recalled K. Honda. "We simply needed to ensure productivity and reliability. This time we were determined to make it into a product."
The establishment of a truly reliable system, however, would prove more difficult than developing the mechanism itself. This was because the airbag system was a one-shot device. In other words, it was not possible to test each system in order to ensure that it would function properly.
Therefore, the team turned to one of the world's great experts in reliability, NASA (the U.S. National Aeronautics and Space Administration) to study the techniques used in their own development programs. In September 1983, the team visited the McDonnell Douglas Aerospace Center (MDAC), where they learned many techniques and concepts having direct relationships to reliability. The FTA (fault tree analysis) method was one such method, and it really opened their eyes. The essence of FTA is to define a goal and identify factors that prevent the achievement of that goal. After that, one must calculate the probability of failure for each problem phenomenon, along with the total probability of failure.
The Honda team would, for example, start by defining the role of the airbag – to protect the passenger by inflating properly in the event the car is involved in a crash. Next, they would identify the phenomena that prevent the airbag from fulfilling its duty, such as improper inflation. Then, the factors causing the phenomenon are identified. These may include a defective sensor system or the malfunctioning of the module containing the bag. Eventually, the problem phenomenon is traced down to a single part. Next, the entire analytical process is repeated, and the failure probability of each phenomenon is calculated. Based on the results, the team would devise preventive measures for such phenomena demonstrating lower reliability, until the total of failure probabilities reaches the target. A key point in conducting an FTA is to start with a very general concept before going into the airbag's specific failures. In other words, think of the car's role in society and what can happen when a car is involved in an accident. A general concept such as this reveals the importance of thinking of the other party involved in the accident. Moreover, airbag failure can't be explained through a single definition: the airbag can fail in a variety of different ways. Therefore, identifying the outlying conditions and categorizing them into pertinent groups can result in appropriate solutions.
"At first we didn't see why we had to go through such a cumbersome process," recalled K. Honda. "However, we gradually came to understand the significance of FTA as we performed the analysis ourselves, based on examples from the MDAC staff."
The development staff also studied the FMEA (failure mode and effect analysis) method. In many ways the opposite of FTA, FMEA is used to analyze what effect is given to the target system when a single part fails. Through such techniques the staff found a clear direction as to how they should improve their system's reliability. They also received much helpful advice from the MDAC staff, including the importance of a simple design and clearly defined goal, the listing of possible methods with which to achieve the goal, and the identification of problems accompanying each method. That experience taught the Honda team that there was no easy way to achieve its goal of absolute reliability.
Raising the Target - One More Digit
The MDAC's methods of analysis helped the development team increase the reliability of its airbag system to the original target of five 9s, or 99.999 percent. This number indicates that the system would fail only once every 100,000 events. Considering that the probability of failure required to launch a space rocket was 99.9 percent, Honda's figure was regarded as infinitely closer to zero. This gave the team members a great feeling of confidence. With reliability data in hand showing five 9s, the team was ready for its November 1983 evaluation meeting. Contrary to their expectations, however, the team faced a new hurdle when Honda R&D's Executive Vice President Tadashi Kume commented after listening to their presentation.
"Reliability is the critical key in an airbag system's success," Kume said. "Raise the reliability target another digit." Obviously, Kume wished to enhance the system's reliability by reducing the failure probability to six 9s or 99.9999 percent, meaning once every million times. Yet, there was a simple logic in that. One failure in every hundred thousand times could be interpreted as one car with a defective system in every hundred thousand cars. Given the volume of cars Honda was selling, the system failing in one car out of every hundred thousand was simply unacceptable.
"That's easy for you to say, Kiyoshi." Honda thought. But he was also thinking that maybe he should feel the way Kume did concerning the number. "Six 9s is only a number on paper. We don't know if our system could achieve that level of reliability, no matter how hard we try. But unless the research to improve reliability requires too much money and pushes the cost out of range, and if what's required is to wrack our brains for ideas and solve the obstacles standing in our way, we must keep on trying as long as there is a possibility."
Ideas are themselves the reward for any worthwhile endeavor, and as if to prove Honda's commitment the effort to achieve 99.9999 percent reliability brought forth a wave of possible solutions.
The Challenge to Achieve Six 9s
The overall system was reviewed again by the development team. Since they were starting at 99.999 percent, however one more digit meant quite a lot. Accordingly, their work would require accuracy and persistence.
The initial task was to minimize the number of SFPs, or single failure points. SFP is a failure mode in which the system is affected by a single failure. For example, the airbag system is connected to four impact-detection sensors: two at the front and two at rear of the vehicle. To prevent a fatal failure from occurring even when one of these sensors failed, the sensors were connected in parallel-to-serial wiring. Using the FTA charts pasted on the walls, the staff marked the position of each SFP in red. There were so many SFPs that it looked as if the walls had been spattered in blood.
One problem identified through that process was the possibility of electrical contact failure at the slip ring. The ring, used to provide an electrical connection between the steering wheel and steering column, was subject to malfunctioning due to deposits of dust and chattering*1 from excessive vibration. Although the possibility was very slim - a mere fraction of a second when the ring's chattering may coincide with the timing of the sensor actuation - the team could not afford to ignore the problem. To eliminate the concern, the team designed a reel of spiraling cable, so that a constant flow of current could be realized.
The team then examined the reliability of slip rings, comparing the original specification and countermeasure specification in order to decide whether to adopt the new design. Both versions, however, showed similar levels of reliability. The final decision to adopt the new specification was made based on the concept of emotional confidence - reliability that cannot be expressed by a value. When an electrical contact was examined in light of emotional reliability, there was nothing more reliable than a contact that could be in the current-carrying condition all the time.
Factory assembly was also considered in the designing of the new cable reel. There was a possibility that the cable could be cut upon turning the steering wheel, if the reel wasn't mounted in the center. To solve the problem, an automatic centering mechanism was devised to allow easy assembly of the reel without affecting its reliability. The team members made frequent trips to the factory, checking the effectiveness in the trial assembly process and reflecting the findings in their FTA chart. They also carried out a number of crash tests by assuming various conditions the car would encounter during actual driving, in order to see how the sensors and airbag would function in real situations. Every possible scenario was simulated. For example, sensor performance was verified in situations where the car ran over a side curb or crashed into a truck and slid into the space below the truck's platform. It was all a matter of achieving their new target: six 9s.
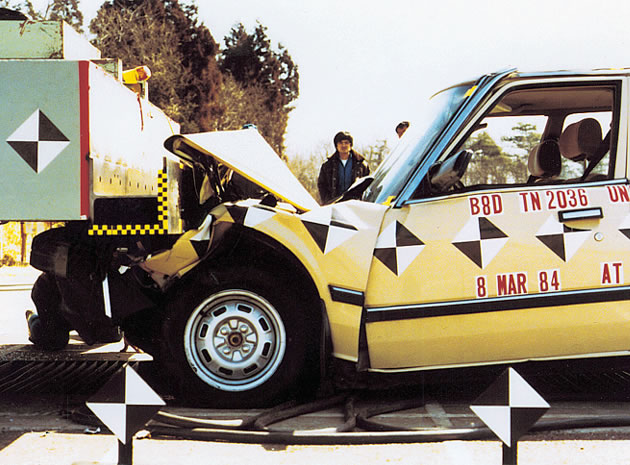
A crash test evaluting the airbag function when the car ran over a side curb (Photograph courtesy of Kiyoshi Honda)
Note:
*1 This term normally refers to a type of mechanical noise. However, in this case it means failure in the electrical contact resulting from vibration.
A Traceability System Enhances Reliability
The effort to improve reliability was in its final stage in the spring of 1986. To confirm reliability during actual use, the second fleet test was carried out using 100 Legends produced on the factory line.
Each of these cars was equipped with a device to measure changes in the system's electrical resistance. Based on the resultant data, the team then examined how the electrical characteristic would change depending on the usage of the car, the season or day/night temperature differences, and how such electrical changes would affect the system. The results verified the reliability they had achieved. The test fleet of Legends proved highly effective in improving reliability. It was the traceability system, or bar-coding of every part used in the system that allowed the production staff to identify which part had been installed on what car.
With this system, the affected cars could be immediately identified and appropriate actions taken, should an error be found in a part or mount in the airbag system after it was sold.
In fact, when a defect was found in a production lot of inflators in 1990, the affected cars were quickly identified via the traceability system and the defective parts were replaced within a matter of days. The cost of replacing the parts for the affected twelve cars in Japan was 800,000 yen. Had it not been for the traceability system, the company would have had to check all 500,000 vehicles sold, causing a considerable inconvenience to many Honda customers.
Once the fleet test had confirmed the target reliability level, Japan got its first airbag system in the Legend in September 1987. It was a dozen years after development began, way back in 1975. It is no surprise in retrospect, but more customers than initially expected were choosing to go with the airbag system. Today, airbags have become standard equipment. This could not have occurred without the diligence of a development staff that worked to achieve the absolute limit of reliability.
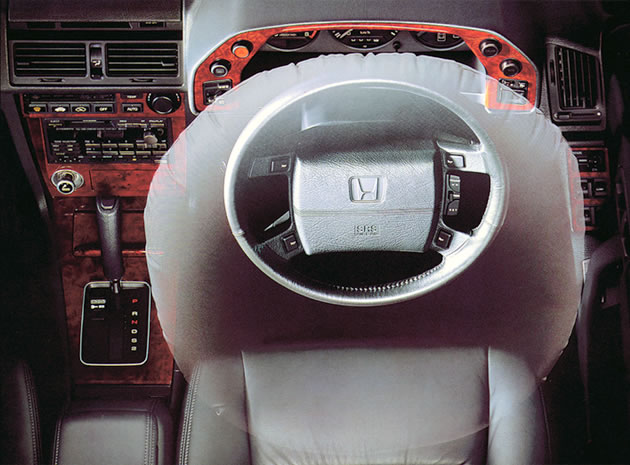
Japan's first driver-side airbag system. It was featured in the Legend.
Numbers alone cannot truly express the notion of reliability. It is affected by various elements relating to conditions of production, the target system or its parts, and the environments to which they are ultimately subjected. Therefore, the determination of Honda's development staff made all the difference. It was they who examined all these elements, and it was their hard work that resulted in a new technology.
"We faced many obstacles during development," said Kiyoshi. Honda, looking back at that period. "As soon as we overcame one hurdle, we'd find ourselves facing another. But what we experienced was a series of joyous events, not painful ones. Of course, we had to learn many things in different areas of technical discipline. We studied theories of gunpowder combustion and high-molecular materials. We even prepared a patent-application document concerning chemical-related issues. Although I hated all those statistics, I had no choice but to study it. After all, once you begin developing a technology that no one in the world knows anything about, you soon realize you have only yourself to depend on."