Steering Angle Sensing Four-Wheel Steering System (4WS) / 1987
Can We Utilize the Rear Wheels of FF Cars?
The 1960s were a decade of dramatic progress in science and engineering. In space, NASA's Apollo missions fostered boundless dreams and aspirations, as man took his first glorious steps upon the surface of the moon. And on Earth, people were beginning to see visions of an ever-advancing automotive technology. It all meant the promise of a bright future.
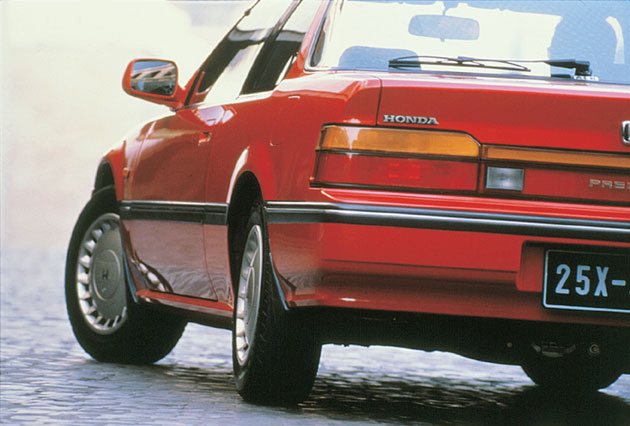
The 1987 Prelude, featuring the world's first steering angle sensing 4WS
The rapid popularization of automobiles in the 1960s backlashed in the 1970s, however. Various problems began to emerge, from environmental pollution and traffic congestion to growing numbers of traffic accidents and recalls of defective vehicles. In response to public concerns, significant efforts were made to address these problems. The ESV (Experimental Safety Vehicle) program, led by NHTSA (National Highway Traffic Safety Administration, a U.S. agency), was one such effort.
The ESV's objective was to conduct a fundamental review of automobile safety, with the intention of lowering the rising tide of traffic accidents. It was a matter of global consensus, with automobile manufacturers around the world joining the program. With its automobile operations finally getting on track, Honda decided to participate in the program as well, though on a semi-official level. As a result, research was begun on an experimental safety vehicle.
Automotive safety generally falls into two categories: "Collision avoidance" and "active safety." Honda's themes of research were explored from the perspective of enhanced active safety in the areas of maneuverability, stability and dynamic performance. In other words, the research aimed at developing responsive vehicles that could more easily avoid obstacles and, when necessary, come to a quick, complete stop. It was this research effort that ultimately laid the foundation for subsequent evolutionary developments in power steering. Another of the possibilities examined through Honda's research was a hydraulic suspension system designed to prevent centrifugal force from affecting the driver.
The assurance of active safety, which was the main target of the research, meant that Honda would have to identify fundamentally effective mechanisms in order to achieve better dynamic performance. At the end of 1977, Honda held a brainstorming session in the hope of returning to the basics through a review of fundamental vehicle structures. This brainstorming session gave birth to the concept of a 4-wheel steering (4WS) system.
Honda vehicles were at the time essentially front-engine, front-wheel-drive (FF) models. In an FF vehicle the rear wheels play a relatively minor role, since the front wheels perform around 80 percent of the steering, driving and braking. Compared to the front wheels, the rear wheels are merely in place as a means of support, ensuring that the car moves ahead in a straight and predictable fashion.
The brainstorming session produced certain discussions that led to an interesting fact: although there were cars with four-wheel brake systems and four-wheel drive, steering control was universally given to the front wheels. Naturally, they wondered if they could utilize the idle rear wheels to provide some steering function. With that, an initial concept was defined. The fact that only Honda had vehicles of FF specification made the idea all the more intriguing. If the rear wheels could be employed in a way that provided some steering control, dynamic performance would improve significantly. The research engineers began to ponder that question, and as they did their desire for a new challenge was awakened.
Ideas Become a Theoretical Model
At the Sixth Research Block of the Wako R&D Center, Shoichi Sano and Osamu Furukawa were deep in discussion as to how they should approach the concept identified in the brainstorming session.
The idea, after all, had not yet been approved as an official project theme, so the financial and human resources available to them were quite limited. Moreover, several projects were running concurrently at the time, making a proper development team even harder to come by. Data, too, was hardly sufficient, given the uniqueness of such a concept. For example, although they wanted to modify existing models in order to construct test cars, they didn't even know whether the front and rear wheels should turn in the same direction or in opposite directions. There were so many questions, due to the fact that a steering system based on four wheels would allow considerable flexibility in control. The key question was where to start.
Sano and Furukawa decided to build a theoretical model for the four-wheel steering system, believing it would help define the fundamental concept before the actual research started.
"It was interesting just mulling over ideas in my head, simply because it was such a new system," Furukawa recalled. "Nobody had ever driven a car with such a system before. I had fun just imagining myself driving it. I have to admit, it was something of an obsession. I was always thinking about the 4WS system, even when I wasn't working."
The theoretical model created at this stage eventually led the pair to the basic mechanisms, providing a dramatic motivation in the development of the 4WS system.
Four-wheel steering, however, wasn't an unknown concept.
Daimler-Benz had already developed four-wheel drive, four-wheel steering vehicles for the Forest Service. Their rear wheels were designed to turn in the opposite direction to the front wheels so that the vehicle could make sharp turns along narrow mountain roads. However, the specification had yet to be adapted for use in mass-production units. Even though it was effective in mountain driving, maneuverability was less than perfect elsewhere. Consequently, these cars occasionally had stability problems while being driven on Germany's famed Autobahn.
A special committee under Japan's Ministry of Transport once examined the merits of a vehicle whose rear wheels could turn in the direction opposite that of the front wheels, as part of discussions regarding the safety of large trucks. There was mounting public concern at the time regarding the danger of transport vehicles, particularly in instances where wide left turns were called for. The committee, too, concluded that a vehicle with four-wheel steering would be less stable at high speeds.
Furukawa's theoretical model substantiated these concerns, concurrently defining a direction as to how Honda should proceed. The fundamental principle identified by his model was that the front and rear wheels should turn in the same direction at high speeds and opposite directions at low speeds.
"We used figures to express an ideal car," Furukawa said. "It was one that could make quick, sharp turns, for which we made the proper calculations. And this was the answer we came up with."
The ideal control method for the four wheels was examined from a broader perspective, and those findings were then reflected in a concrete, theoretical model. This approach successfully outlined a 4WS system that was unlike anything before it. The principle mechanism won a basic patent in 1978, which further propelled Honda's development of the 4WS system.
The Test Car: From Theory to Reality
Another group outside Honda was studying a similar system at the time Honda had begun its research into 4WS. Oguchi's laboratory at Shibaura Institute of Technology, led by then assistant professor Oguchi was examining a steering-control system that would allow the front and rear wheels to move independently, thus moderating the negative effects of understeer and oversteer. Honda knew about Oguchi's research group, since the company had earlier commissioned studies on maneuverability and stability in mini cars. When Sano and Furukawa learned that the group was conducting research under a similar theme, they proposed that the two join forces. With that, the two-man development team gained a significant measure of support.
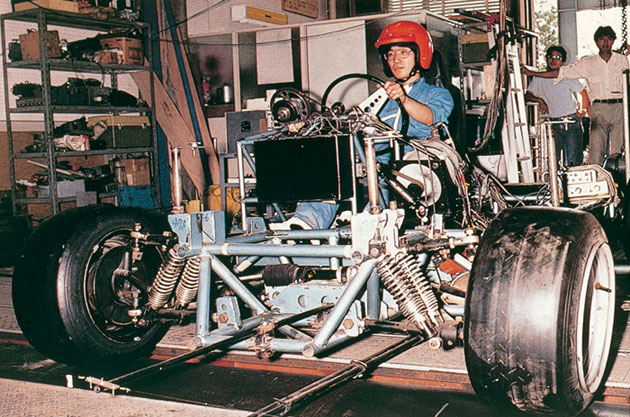
Test equipment in Oguchi's laboratory at Shibaura Institute of Technology. The development team's research made real progress, thanks to the drum-type bench tester.
A key benefit of the joint research was the drum-type bench tester installed in Oguchi's laboratory. It was a device made of two drums placed in parallel at the front and back. A test car made of pipe frames was placed on top of the tester. The tester could evaluate maneuverability and stability under various conditions by changing the gearbox setting in order to obtain the desired steering ratios for the front and rear wheels. With this device Sano and Furukawa could substantiate their theory through the collection of quantifiable data. They also acquired other data, including an optimal steering ratio for the rear wheels. This proved very useful when filing the patent application for their aforementioned technology.
The two partners made rapid progress, and soon they were ready to test an actual vehicle. In April 1981, the first drive test was carried out on the west course at Suzuka Circuit. The test car was built from two Accords whose front sections were cut off and welded together to make one vehicle. The link mechanism that interconnected the front and rear steering mechanisms came courtesy of Oguchi and his students, who had fashioned it by hand.
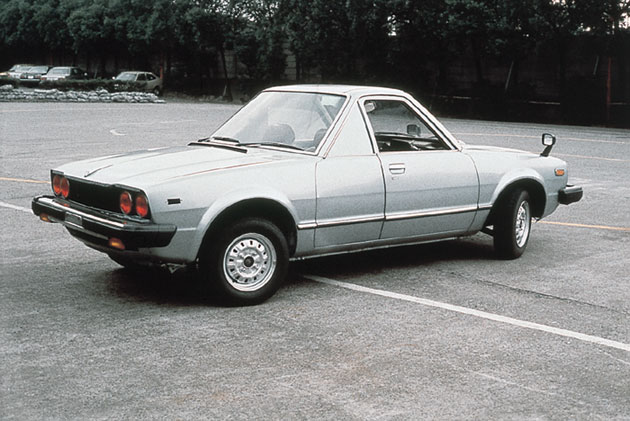
The 4WS test car created by fusing the front sections of two Accords. Putting together two front sections, instead of modifying one complete vehicle to four-wheel steering specifications, greatly enhanced the progress of development.
"We had a good feeling about the outcome," Furukawa said. "Still, it was our first attempt, so we were very anxious to see what would happen."
Happily, the test results obliterated any concerns they might have had. The test car demonstrated a level of dynamic performance that far exceeded their expectations, in the process transforming a mere theory into reality. And given such a positive outcome, it was now possible for a formal 4WS development project to get under way.
The Shift from Speed to Steering Angle
The control mechanism created through the joint effort, which turned the front and rear wheels in the same direction at high speeds but in opposing directions at low speeds, was initially conceived as a "speed-linked 4WS system" - a control mechanism directly dependent on the speed of the vehicle. However, it required a gear-ratio control in order to successively link the wheel-turning actions in two different directions. Accordingly, a new mechanism had to be developed by combining an electronic control device and variable gear-ratio mechanism.
The layout of such a system would prove to be a difficult, but not impossible challenge. However, excessive complexity could result in problems during production, that would be reflected in the market. Therefore, further discussions were held in order to simplify the system. Eventually, the review process led to a theoretical shift in linking the control function to the angle of steering rather than the vehicle's speed. This became the starting point for a "steering-angle sensing 4WS," which would control the rear wheels in accordance with how much the steering wheel was turned.
This is easier to understand by imagining what one does when driving a car. When changing lanes on a highway, the steering wheel is turned only slightly. However, there are situations in which the steering wheel must be turned considerably more, such as when parking the vehicle in a garage. In view of enhanced dynamic performance, the front and rear wheels should turn in the same direction at high speeds and in opposite directions at low speeds. But when steering angles are applied to this principle, the front and rear wheels should turn in the same direction at smaller angles but opposite directions when greater angles are applied.
Honda had, in fact, already included this concept in a patent the company obtained in 1978. However, it all became a reality with the development of a new crank mechanism, which was designed to turn the wheels in the same direction initially but in opposite directions after a certain point. For example, when the steering wheel was turned to a large angle, the wheels would turn in the same direction for a brief moment after the steering wheel starts to rotate. Then, as the angle of steering increased, the rear wheels would turn toward the opposite direction. One problem had to be resolved, though, in order that the mechanism could be utilized. With a single crank mechanism, the wheels could only be turned at certain instances, regardless of whether the front and/or rear wheels were turning in the same or opposite directions. With the car traveling at high speed, the desired control could be achieved with the rear wheels turned just one or two degrees at most in crank angle. On the other hand, an offset of approximately five degrees would provide more effective control during low-speed maneuvers. In that regard it would not make sense to use only one crank. Therefore, it was decided that the combination of two cranks would overcome the drawback. This led to the development of a simple mechanical system that would not rely on an electronic control device or other such complexities.
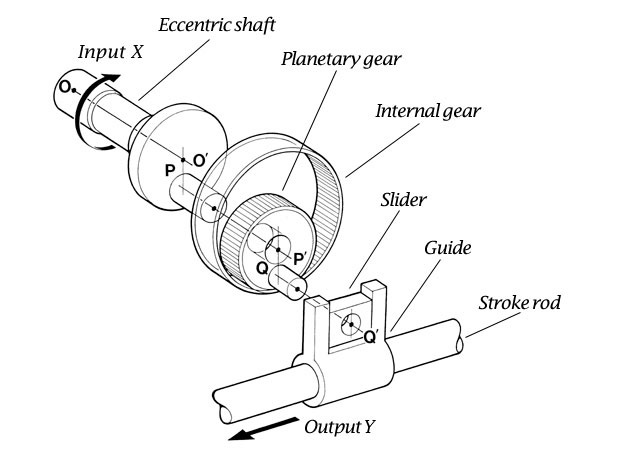
The operating mechanism of the rear steering gearbox, which connects two crank mechanisms at different phases using a planetary gear
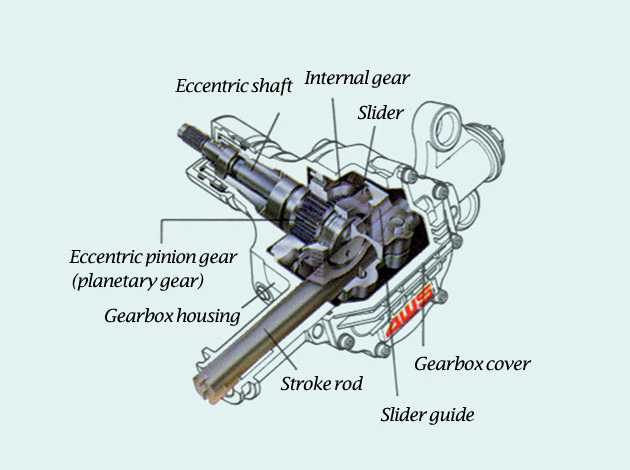
The rear steering gearbox used in the 1988 Prelude
High scores were given to the complete 4WS system at its initial evaluation. Even Tadashi Kume, then the president of Honda R&D, was impressed by its simplicity and effectiveness. The achievement was the fruit of hard work by the development staff, who at each occurrence of difficulties used a calm, analytical approach in order that the project could move forward. Simplicity was their byword, and in all respects the 4WS system satisfied that.
The New Concept: A Hard Thing to Promote
It is only human nature that people are suspicious and skeptical of things they do not fully understand. This was certainly true of Honda's 4WS system, which would be a challenge to sell in the marketplace. Compounding the problem was that four-wheel steering control is very complex, making the benefits difficult to understand simply by describing the specifications. It would be hard for anyone to understand just how much the maneuverability and stability have improved without actually driving the car and experiencing its effect. When basic research began, there were as many doubters in the company as there were believers. Some expressed their doubts in an outright fashion, saying that the rear wheels should not turn and that using them for steering control could never work. But as the 4WS development project progressed, moving toward the D-development stage, Furukawa, the newly appointed LPL, had to think of ways to promote confidence in the new system.
Problems were nevertheless manifested in the D-development stage that the team hadn't even imagined during the R-development phase.
For instance, the 4WS system would need long link shafts, but those wouldn't fit on the production line because all extraneous space along the line had been eliminated for maximum efficiency. Suspension alignment, too, became an area of concern. With a conventional vehicle, the alignment process simply requires that the front wheels be adjusted against a fixed reference point - the rear wheels. But in a car equipped with a four-wheel steering system the body would have to serve as the reference, necessitating changes in the equipment and process used.
Regardless of any possible benefits it might offer, a technology can not be applied to products if it requires an excessive investment, since that will only force the cost of those products higher. To solve the problem, the factory had to work hard to find ways of controlling costs.
Furukawa knew he had to do something to alleviate the sense of doubt that was becoming prevalent among the factory personnel and other staff. So, while working to solve the problems at hand, he decided to give his colleagues an opportunity to drive the car themselves. After all, it was the only way for them to experience the sensation of a 4WS system, and the only way to understand its potential impact.
Furukawa formed a 4WS promotional committee so that test drives could be arranged for factory and service personnel. It was through such tests that the people who would actually produce the final product came to perceive it as an entirely new level of dynamic performance. In fact, the test drives not only facilitated communication among all involved, they also sparked enthusiasm about Honda's exciting new technology.
Eventually, the associated staff people at Honda's overseas offices, along with journalists and officials from certifying agencies, were invited to try the system, thus nurturing an accurate understanding of 4WS.
Malicious Tests and Local Adaptability Tests
Exhaustive studies were carried out to identify and eliminate the problems that might occur in the marketplace. Even though the cars were to be driven by different users in different ways, it would be impossible to predict every condition the vehicle would encounter. In other words, it was possible that problems could occur outside the context of what the design engineers had anticipated. To minimize that possibility, trial tests were conducted in various practical settings.
A series of "malicious tests" was devised, so named because the test conditions were set to simulate overly adverse situations that were unlikely to occur during normal use. For example, one test examined whether the steering function would work when the driver started the engine and turned the steering wheel without knowing that one of the rear wheels was caught in a ditch only as wide as the wheel's rim. Another test would determine whether the system would break down during operation if the car was used in a cold climate such as Hokkaido's, with the rear wheels frozen under a mantle of snow. Numerous other scenarios were considered, during which all system functions were verified in detail.
The development team even held a number of local-adaptability tests in Europe, along with test drives for personnel at Honda's overseas offices. These helped identify problems during actual driving, as well as driver responses to them. This had all been designed to incorporate user feedback into solutions that would further enhance the system's performance. Of course, there were a few mishaps. During one test drive, a driver who was overly confident in the system approached a corner at excessively high speed and smashed right through the guardrail. Nevertheless, marks for the system were very high and every office in Europe gave it a "thumbs-up." The results couldn't have been more satisfying.
The world was now ready for another first. In April 1987, Honda's unique steering angle sensing 4WS debuted in the form of a stunning new, high-performance Prelude. The system had indeed opened doors to an entirely new perception of automotive possibility.
The Importance of a Challenge
Over a ten year period, Honda's new 4WS system had evolved from the basis of a casual comment - a simple idea - to the production of a car that would set a new standard in handling and dynamic performance. Yet, the reason for Honda's technical leadership was equally simple: Use a theoretical model to identify the fundamental principle of operation. Once that was achieved, the other aspects of development would follow suit. And in that regard the final outcome was truly an extension of the original idea.
"We were able to define what we could achieve by turning the rear wheels," Furukawa said, "and that understanding proved to be a real boost. Once we had the concept, we only needed to embody it by experimenting with ideas and solving problems."
The theoretical model's significance is reflected in the fact that it is now a popular method among researchers. Simple in form yet applicable to the most advanced theory of control, the model has been used in various studies, including those leading to today's suspension-control technologies and active, left/right braking systems. In that regard, Honda's development of 4WS became the foundation for many subsequent theories of automotive control.
"It was the desire to bring what we believed to the world, and to see it accepted by users," Furukawa explained. "That's the thing that made our R&D process work."
The act of innovating, then, stemmed from the search for ideas the development team could use to realize a goal. Each time they encountered a problem, they had to stop and find a solution. They knew that failures would occur despite their efficiency in seeking the target - that was simply the price of success. Ultimately the technology they had so diligently endeavored to achieve became a product, and it was well received in the market. It was a real benefit to their confidence as engineers.
"When the 4WS system was in development," Furukawa said, "I truly believed that I was creating a technology. But when I look back at it now, perhaps it was the 4WS technology that was nurturing me."
Honda's 4WS system undeniably established a new standard in driving performance, but without a doubt it did something more. It brought creative minds together in a solution that would one day benefit the automotive world.