Establishing Honda of America Manufacturing / 1980
Gaining an Edge in the Global Competition
Honda found itself surrounded by an atmosphere of upheaval in the 1970s, both in Japan and abroad.
Yet, that situation had actually arisen much earlier-in the mid-1960s when, along with advancing industrialization and motorization, air pollution had become a serious social issue. The Clean Air Act of 1970 passed by the U.S. Congress resulted in even stricter regulations regarding tailpipe emissions. Moreover, the Clean Air Act had influenced the Japanese government to tighten its own policies.
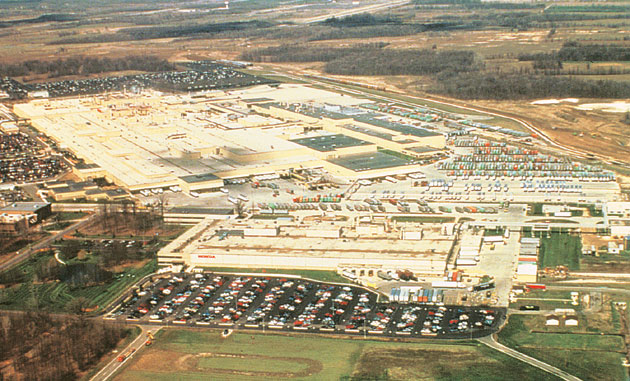
A view of the entire HAM plant at Marysville, Ohio, in the American Midwest. The building at the front is a motorcycle plant, which began operating in September 1979. The auto plant is in the rear.
Accordingly, auto manufacturers had to comply with such demands, and with no time to waste. Company President Soichiro Honda put out a call to action on behalf of researchers at the R&D Center, saying, "This allows latecomers like us to line up at the same starting line as our rivals." His encouragement extended to all Honda associates. "Now is the chance," he said, emphasizing his view of the matter in several issues of the Honda Company Newsletter.
In August 1971, the U.S. government announced its policy in protection of the dollar. This was the result of a shift in the yen toward the floating-exchange-rate system, which had prompted the actual value of the yen to rise, bringing about a crash in the Japanese stock market.
At Honda, where exports to the U.S. and other countries made up 60 percent of total revenues, the impact was tremendous.
"We must use new ideas to change our way of doing business," stated Executive Vice-President Takeo Fujisawa in the September 7, 1971, issue of Nihon Keizai Shimbun. "Otherwise, we’ll continue to feel the impact of outside forces. In fact, we’re already having difficulties with our conventional method of rapidly increasing the number of exports by employing technologies, mass-producing and streamlining. We have to come up with a newer, more suitable method."
The New Honda Plan (NHP), proposed by the senior managing director Kiyoshi Kawashima, was implemented in April 1972 as a company-wide effort to build a corporate structure that would allow rapid response to changing situations in a flexible manner. The "Global Production Strategy," was one such project promoted to all corporate divisions.
Kiyoshi Kawashima assumed the post of company president in October 1973, effectively replacing Honda founders Soichiro Honda and Takeo Fujisawa. Immediately afterward, another incident took place that rocked the global economy to its very foundation: the first oil crisis, triggered by the war in the Middle East. However, it was more than a direct hit to business. It also gave rise to serious questions concerning the entire global population. The oil crisis was an especially heavy blow to the Japanese economy, which, despite almost 100 percent dependence on foreign petroleum, had been riding a wave of high economic growth. The oil crisis, however, served as an opportunity for Honda to establish the idea of decentralizing its manufacturing bases and becoming even more global. Indeed, it led the company to give serious consideration to the creation of a system that could offer a steady supply of products without being affected by changes in global dynamics.
At the same time, Honda had a long-standing policy to build products in the market where they are sold. Through this policy, Honda also can contribute to the local community through employment and paying taxes. The policy is based on Honda’s corporate philosophy of "The Tree Joys" - the "joy of buying", the "joy of selling" and the "joy of creating." To realize this policy, the NHP Global Production Strategy Project team began analyzing the possibility of local motorcycle production in the U.S. - the biggest single Honda market in the world.
Therefore, a feasibility study was conducted in the fall of 1974, at the request of Kiyoshi Kawashima. There were feasibility study tours of American manufacturing plants, and cost comparisons between the importation of completed cars and local manufacturing. However, it was a big question whether such products manufactured in the U.S. would possess the same quality as those built in Japan, as was the issue of profitability.
"Okay, I understand," said Kiyoshi Kawashima. "Let me hold onto this project for the time being. But keep the research data handy so that it can be used whenever the need arises." He then decided to forego the manufacture of motorcycles in the U.S., ending the NHP’s study. However, he could not seem to forget the idea of establishing a manufacturing base in the U.S. that would allow motorcycles to be made locally.
Believing that one-way exports would not last indefinitely and that thinking in terms of profit only would never allow him to make up his mind, Kawashima decided he should weigh such a decision with great care.
Local Feasibility Study Begins Anew
Export of the Civic began to the U.S. and the rest of the world in1973, having debuted in Japan the previous year. That model was equipped with the CVCC engine, the first powerplant developed by an auto manufacturer that passed the strict emissions standards of the U.S. Clean Air Act. Accordingly, the Civic was a hit with the public, boasting great fuel efficiency and considerably cleaner exhaust than any car before it. In Japan, the car won the Car of the Year Award three straight years, beginning in 1973, while in the U.S., it ranked first in a fuel economy test conducted by the EPA (Environmental Protection Agency) in 1974, winning praise around the world. There was indeed a great demand for the Civic as a small yet eminently practical car for the domestic and foreign markets, particularly with its arrival on the heels of the first oil crisis.
It was not easy to satisfy demand and, as a result, both the Suzuka and Saitama Factories had to manufacture Civics at full capacity every day. The Board of Directors even discussed the possibility of expanding Suzuka with a second automobile production line in order to provide for another surge in Civic sales. Yet, Kiyoshi Kawashima was not quite ready for such a thing.
"It’s true that the Civic is selling well," he said. "However, it would be virtually impossible for Honda, given the current conditions, to immediately enhance its domestic sales strength to meet the increased production requirement. Moreover, we’d have to consider the cost that would accompany an expansion in the production line. But Honda’s auto business is finally bearing fruit, thanks to the Civic. And since it is a budding business, we shouldn’t assume we’re ready to charge into competition with the other Japanese manufacturers, either in terms of sales or capital. So, rather than compete domestically to no avail, I would like to use this opportunity to take a chance in America, the world’s largest market. I would like to build a motorcycle factory and eventually an automobile factory in the United States, where no [Japanese auto manufacturer] has yet done so."
The proposed plan to add a second line for car production at Suzuka Factory was thus put on hold, at the insistence of Kiyoshi Kawashima. Instead, the company’s decision-makers began taking another look at a possible U.S. manufacturing base. "Recent study has concluded that a Honda factory in the U.S. would have a hard time making a profit through the manufacture of motorcycles alone," Kiyoshi Kawashima said. "However, now that the Civic has begun to sell in America, I wonder if we might have a possibility there."
It was at this time that Masami Suzuki, then the managing director, was instructed to conduct another feasibility study. However, concurrently, he was busy supervising the overseas manufacture of automobiles and unit sales of CVCC engines. Having licensed CVCC technologies, Suzuki had established a number of solid contacts among automakers in Japan and elsewhere.
"Let’s find out again what we can do in the States," said Suzuki in November 1975. Immediately, he began organizing a study group with which to explore the concept of car production in America.
The Eve of Honda’s American Expansion
Honda’s impending full-scale exportation of Civic cars and CVCC engines to the U.S. was to occur at a time in which the American auto industry was suffering the effects of the first oil crisis, which had made consumers wary of the cumbersome "gas guzzlers" being offered by Detroit. In fact, the U.S. makers still had no consensus concerning a technology that would meet the requirements of the Clean Air Act. It had not yet developed reasonably priced economy cars, leaving that segment of the market open to European and Japanese models, which gradually began populating the country. In the meantime, the American factories began trimming back their operations, laying off increased numbers of employees.
The American expansion of Civic sales would therefore necessitate a larger number of dealerships. Increasing the number of imported cars - Civics, in particular - would require countermeasures against the future import regulations that would likely be imposed.
Thus, Honda President Kiyoshi Kawashima’s goal - the manufacture of automobiles in the U.S. - agreed with the realities of an entire economy, society, and auto industry. He knew the key to Honda’s continued growth was to pursue the potential of local production in America.
Suzuki left Japan in January 1976, flying to the U.S. in order to accomplish his mission. Following an exchange of opinions with Hirofumi Nakamura, the general manager of American Honda Motor Co., he held talks with American managers, seeking their comments regarding the manufacture of automobiles stateside. Based on their own rather unpleasant experiences with the intrinsic quality problems of contemporary American-made cars, though, the U.S. managers did not agree that it would be a good idea for Honda to do so. Actually, they all said that "rather than think of doing something so difficult, we should send more and more cars from Japan while the Civic is riding high in sales." Accordingly, the conclusion drawn from the discussion was to study the feasibility of U.S. manufacturing, with emphasis on the achievement of consistently high quality levels:
1) What type of management structure would enable the production of quality cars?
2) What type of location should we choose in order to secure an environment in which cars of outstanding quality could be produced?
The spring of 1976 found Suzuki in the midst of sales negotiations with Ford regarding CVCC engine units. Lee Iacocca, president of Ford Motor Company, had much to say in praise of the Accord, which Honda had just begun selling in the U.S., albeit in limited numbers.
"I drive [an Accord] myself on the commute to work," Iacocca said, expressing a desire for those engines to be supplied to Ford. "You have my congratulations for making such a wonderful car."
The negotiator from Ford also assured Suzuki that if Ford were to come up with a manufacturing plan for Accords, then annual sales of 600,000 units, including station wagons, could easily be achieved.
Suzuki in turn said he was studying the possible manufacture of cars in the U.S., and asked for permission to tour Ford’s main plants. Iacocca promptly introduced him to Ford’s vice-president in charge of production, and that same day, they had a discussion. The vice president then referred Suzuki to the most highly rated facility among the many that Ford operated. Significantly, that evaluation was based mostly on the quality of its employees. Therefore, following that meeting he visited the plant, in which the methods of communication between the management and production crew were well established. Suzuki was impressed, but he also knew the plant would present certain limitations in terms of knockdown production.
The knockdown system was in fact a prominent part of American auto manufacturing, in which the main car assemblies were transported via railroad from Detroit, Michigan. The manufacturing systems made use of multiple-variety, small-volume production, employing buildings and facilities that had long since reached their maximum depreciation.
At the same time, Honda Engineering (EG) was becoming increasingly confident in its manufacturing technologies, which featured welding machines and robots for reduced presswork and a dramatic integration of welding processes. Through this system, beginning with a stamping process that boasted a technology for the rapid changeover of dies and cutting heads, Honda was already at the point at which real cost-performance could be achieved using a sensible scale of production.
Suzuki’s tour of the Ford plant therefore facilitated a clearer perspective of what hardware should be brought to the U.S., i. e., the types of cars that should be made and what Honda should do in terms of production. In fact, he was starting to think that Honda was competent enough to manufacture cars in America, the fabled Land of the Automobile.
In his travels across the U.S., Suzuki was keenly aware of how those involved in service industries, including hotels and restaurants, could offer such sophistication of hospitality. He could not dismiss the fact that America’s true greatness was to be found in the friendliness and cheerfulness of its people, and in the inherent pleasures of that environment.
Therefore, he knew it was not a matter of people intentionally producing bad cars. Rather, it was because the management systems deprived workers of their natural motivation to excel. The auto factories themselves were no exception.
Suzuki also became aware of the differences in environments and lifestyles he had observed among the different regions of the country. He knew he had to consider such factors when choosing a site for plant construction.
Honda to Build a Motorcycle Plant in Ohio
Formed in December 1975 to determine the feasibility of U.S. automobile manufacturing, the group now began to focus on the following two requirements:
1) The cost of manufacturing automobiles must be plausible when compared to the price of Japanese-made cars sold in the U.S.
2) Quality must be secured on a level equal to those completed in Japan.
In May 1976, the Joint Meeting of Senior Managing Directors endorsed the commissioning of an American consulting firm to research automobile production in the U.S. Requirements for the plant location study were presented, calling for a place in which 100,000 Civics and Accords could be produced annually and transported via truck lines or railroads.
A midterm report was presented by a consulting firm in October 1976. Several cities in Ohio and Tennessee were named as specific candidates, based on their intrinsic economies. The final report came at the end of the year, when many candidate locations centering around Columbus, Ohio, were proposed. However, it would not be easy to find a site that answered all of Honda’s requirements.
Then, in February 1977, the company asked a university research institute to examine the quality of the labor force, for the purpose of verifying previous data. According to that report, it was confirmed that the region from Ohio to Kentucky had a low rate of job turnover, along with highly motivated workers. However, no specific location was identified as an optimal candidate.
The requirements for the location of a plant were that it be on a level lot covering between 100 and 200 acres (approximately two million square meters), that it offer access to expressways and railroads, and that a high-quality labor force be available.
The results of the location study and research concerning labor quality brought Ohio further into focus, at which time the project was enhanced with additional personnel. Meanwhile Suzuki and others began a quest for new information, touring more than fifty sites throughout the state. That search, however, went without a satisfactory result.
Therefore, finally it was decided that a meeting with the governor of Ohio was the only way to pull out of the situation. Suzuki requested an appointment in July 1977, after a considerable period of deliberation.
"I visited the governor, determined to give up on Ohio," Suzuki recalled, "if none of the locations the state had recommended could prove sufficient."
Governor James Rhodes, upon hearing that Honda had focused on his state as the final candidate for plant construction, welcomed the project members with open arms. New locations were immediately cited as candidates, and a tour itinerary was arranged.
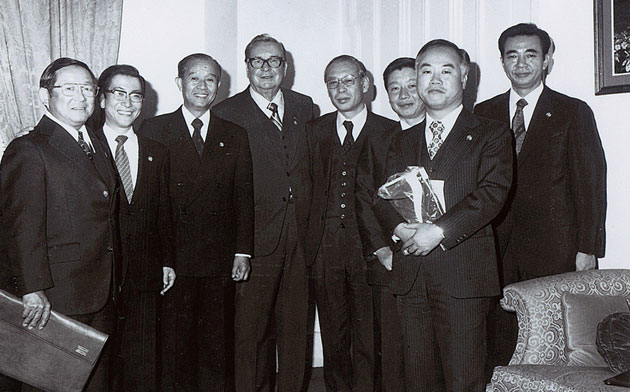
Attending the news conference were, from left, Matt Matsuoka, Kiyoshi Ikemi, Kihachiro Kawashima, Governor James Rhodes, Masami Suzuki, Koichiro Yoshizawa, Shigeyoshi Yoshida, and Kazuo Nakagawa (Photo courtesy of Mr. Masami Suzuki)
The following day Jim Dark, chief of Ohio’s Economic Development Bureau, took the three project members - Suzuki, Kazuo Nakagawa (managing director in charge of overseas production), and Shigeyoshi Yoshida (president of HIT*1 - on a tour of industrial suburbs in a state-owned airplane. Following the tour, they stopped by the state-run Transportation Research Center (TRC).
The center was a large proving ground boasting a number of different test facilities, among which was a 7.5 miles (12 km) oval course. It was used by makers of cars, trucks, and auto parts, as well as by government organizations and research groups. There the topic of conversation turned to employment, with people from TRC saying that many people in the area were industrious and that a large number of quality workers would be available. Indeed, Suzuki, Nakagawa, and Yoshida saw for themselves how hard the young female test riders were working at the center, they knew it would be a good idea to research the area further.
Suzuki asked, "Is there a site around here that would be appropriate for industrial use?" In response, Dark showed them a lot immediately east of the TRC. It was about 200 acres in size, and there was a main highway nearby. It even had a nearby railroad track, although it was no longer in use. Restoration of the railroad would allow the transport of completed automobiles and associated parts, and soon it was evident that this location fulfilled all the requirements for the manufacture of automobiles.
That evening, the three men reexamined some of the locations they had toured, agreeing unanimously on the lot next to TRC. The following day, they visited Governor Rhodes, telling him they wished to acquire the property.
Mr. Rhodes replied, "Then, the state will provide you the lot for free." "Oh, no, we can’t accept that," said Suzuki, acting as Honda’s official representative. "We would like to purchase the land at its fair market price."
It was decided that the plant would begin on a small scale, through the production of motorcycles. Then, once the new plant had become proficient in that process, they could apply it to the production of cars.
"Although I didn’t see the location myself," Kiyoshi Kawashima recalled, "I made my choice [to build a plant there], because it was the result of a thoroughly considered decision by my trusted colleagues."
Honda signed an agreement with the State of Ohio in October 1977, simultaneously announcing in Japan and the U.S. that it planned to build a motorcycle plant. The total amount of investment was to be $25 million, which was then equal to approximately 6.5 billion yen. The agreement entailed the acquisition of 214 acres of land for the construction of a facility capable of producing 60,000 large motorcycles a year via a single workshift employing between 300 to 500 people. Production was to begin in 1979, two years down the road. It was also announced that when motorcycle production was well underway and requirements such as the understanding of the local community had been met, Honda intended to manufacture automobiles in a facility adjacent to the motorcycle plant.
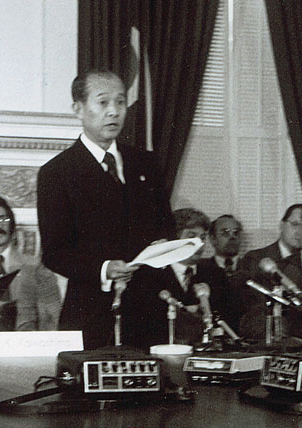
Executive Vice President Kihachiro Kawashima made an announcement on October 11, 1977, regarding the building of a Honda motorcycle factory in the Midwestern U.S. state of Ohio.
Note:
*1 HIT (Honda International Trading Corp.), financed and established by American Honda in September 1972, engages in the trading business.
The Honda Philosophy at Work in the U.S.
The new corporation, Honda of America Manufacturing (HAM), was established in February 1978 for the purpose of producing motorcycles. The operational setup was based on the idea that the profits American customers provide Honda should be reinvested in America, rather than taken back to Japan. This would allow the company to expand its activities internationally, while becoming more thoroughly engrained in the American cultural fabric. Therefore, 80 percent of the initial capital was financed by American Honda, while the remaining 20 percent was financed by Honda Motor of Japan. As of the late 1990s, American Honda’s investment in HAM had reached about 97.6 percent.
The announcement to build a motorcycle plant brought about full-scale preparations both in Japan and the U.S., in order to build the plant and establish an infrastructure. HAM President Kazuo Nakagawa, who was to direct U.S. manufacturing operations, led the others in establishing a context for corporate activity.
The manufacture of motorcycles in the U.S. was to require nearly twice the funding and labor force used in Japan. Accordingly, discussions turned toward the question of what should be done to manage profitable U.S. operations, considering the limited profit margin inherent in motorcycle production. The conclusion drawn by Nakagawa and his colleagues was that Honda’s top priority in corporate activity was to provide high-quality products that would ensure the satisfaction of Honda customers.
To start activities in Ohio and take root in the local community, Honda officials decided it was necessary to provide an understanding of Honda throughout the local community, which they would achieve by clearly stating the company’s goals and strategy to begin operations. Moreover, in hiring Americans, despite the many cultural differences between Japan and America was important that Honda reveal its objectives in order to win the understanding and full cooperation of every new associate. To that end, Honda needed to organize its own thoughts concerning such hirings.
Considerable debate ensued, after which it was decided that no HAM employee would be described via the term "worker" or other such words as commonly used in the U.S. Instead, they were to be called "associates," meaning members of a team working on behalf of a common goal. Additionally, Honda had to settle basic issues such as wage structure and job rotation. In America, wages were generally paid according to the type of job one held, but this was not to be the case at HAM. For any job position, the job description included responsibility for product quality. The names of job positions and supervisors were newly established to encourage associates to gain a sense of pride in their work, and thereby function as a team. At the plant, a flat wage rate was adopted based on the job-rotation system.
Honda first hired American managers who would oversee plant operations. Then, after HAM’s corporate concept had been thoroughly explained to them, the company would hire general associates for engagement in motorcycle production.
Despite not having advertised its job openings in the area newspapers, the applicants came in droves - more than 3,000 in all. "The unemployment rate was definitely high at the time," recalled Nakagawa, "but just hearing the name Honda prompted a great many people to apply for jobs. It really dawned on me then that the good image Honda had built through its products and sales was taking root in America."
HAM’s Executive Vice-President Shigeyoshi Yoshida and Manager of General Affairs Kunio Iwamoto led the hiring operation, explaining Honda’s goals for U.S. manufacturing, operation policy, philosophy, and work regulations to each applicant. Hiring was conducted under the strict policy that all members of the selection committee had to agree on personnel selections. As a result, only fifty people were hired, none of whom had ever been involved in the manufacturing of motorcycles. To Honda, it was more important that there was a passion for work rather than direct experience with motorcycle construction. It was passion, they believed, that would lead to a more rapid assimilation of Honda’s philosophy and operational outlook.
"Sometimes we’d find resistance to certain ideas," Iwamoto recalled, "such as when associates would say, ‘Don’t make us wear these white work clothes. It’s unheard of in America to have all employees wear white.’ But when we explained to them that white workclothes were designed with hidden buttons to keep them from scratching the products, and that white clothes would call attention to stains, helping promote cleanliness (when engaged in manufacturing activities), most of them understood and accepted it."
Furthermore, HAM followed Honda’s basic philosophy of not using a preferential management system, which was common at American manufacturing plants. Reflecting this approach, the cafeteria was designed for everyone to eat together at once. Parking spaces were provided on a first-come, first-served basis. Thus, HAM came up with its own system of associate benefits and welfare. In 1984, Scott Whitlock and Susan Insley, attorneys from a local law firm, joined HAM in the areas of administration and public and community relations and became instrumental in establishing the corporate system, and teaching and implementing Honda philosophy among the associates at HAM. Later Whitlock moved to auto operations and was promoted to executive vice president and Insley to vice president and general manager of the Anna Engine Plant. In 1995, both of them resigned and returned to private practice.
HAM’s Flagship Motorcycle
Opinions varied widely concerning which model should be manufactured at HAM.
Considering the fact that large motorcycles had long dominated the American market, the most desirable model for production was the Gold Wing GL1000, a flagship bike built by Saitama Factory’s Sayama Plant and exported to the U.S. It was therefore decided that production of the Gold Wing would be discontinued in Japan and transferred to HAM, which would be its exclusive maker.
The Gold Wing GL1000, however, had many parts and would be quite difficult for the associates at HAM to assemble, given that it would be their first opportunity to produce a motorcycle. It was also very possible that a skilled labor force would be required in order to achieve the promised level of product quality. Therefore, it was decided that manufacturing operations would begin with the CR250R, a motocross bike having a much smaller number of parts than the larger, more complicated GL1000. The operation would then shift gradually to production of the Gold Wing.
Japanese engineers began arriving in Ohio in 1979. They decided to disperse throughout the area in order to integrate as residents of the regional community. Yet, this was to prose considerable difficulty for the Japanese staff and their families, including problems with the English language. However, it was Honda’s attitude toward assimilation that became the foundation of HAM’s acceptance as a member of the local community.
The associates at HAM began their training in motorcycle production under the tutelage of the Japanese engineers, who handled the areas of technical orientation without interpreters. Key words and gestures were repeatedly used to convey the importance of quality control, which was considered the single most important element in the entire manufacturing operation. It was a process that inspired the enthusiasm of HAM’s Japanese instructors. The American managers meanwhile were sent to Japan so that they could acquire essential knowledge about Honda’s manufacturing processes. For welding operations requiring special techniques, associates were sent to a vocational training school in Ohio to learn the basics, after which they were sent to Japan for two weeks of on-the-job training. Training was also ongoing for other critical production tasks. In order to prepare for actual plant operations other issues, including the shipment of parts from Sayama Plant, were considered from various perspectives. This extended to the tiniest details, such as what types of parts should be packed into sets, and in which quantities, in order to ensure product quality and production control.
The first CR250R produced at HAM rolled off the production line on September 10, 1979, thanks to a process that had indeed secured production quality as the number one goal. Honda had even promoted a "discover and report" system, in which the associates were encouraged to report any defects in order to prevent such problems from carrying on to subsequent processes.
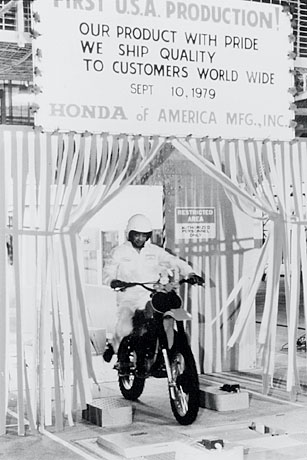
The CR250R, first of Honda’s motorcycles to be produced at HAM, rolled off the production line on September 10, 1979. Shown aboard the bike is Kazuo Nakagawa, HAM’s inaugural president.
Honda also asked its parts suppliers to be careful when handling their product for delivery. When parts did not meet Honda’s strict requirements for quality, the company would work with the vendor to resolve the problem. It was thus that HAM’s manufacturing operation gradually got under way. And, April 1980, the Gold Wing GL1100, a highly anticipated new model, was being assembled by the associates at Honda’s new Ohio plant.
Setting the Stage for Car Production
A drastic increase in the standard price of crude oil was set at the OPEC meeting in June 1979, triggering a second oil crisis. This in turn hastened the world’s attention toward energy conservation, nowhere more so than in the United States, where the car market had for years been dominated by large cars. The U.S. had suddenly found that fuel-efficient cars could be attractive, practical, and fun. It was an enticing new concept.
January 1980 found Honda announcing its plan to build an auto production facility on a lot next to the motorcycle plant at HAM, thus becoming the first Japanese auto manufacturer to produce cars in the U.S. That plan involved the investment of an additional $250 million to build a plant with a production capacity of nearly 150,000 cars. Two thousand new employees were to be hired, and manufacturing was slated to begin two years down the road.
Honda’s announcement was a breath of fresh air amid the growing trade friction between Japan and America, in which the exportation of Japanese cars to the U.S. was the greatest factor. The move was welcomed by both governments. Moreover, the media praised the fact that the company had voluntarily worked out a plan to manufacture cars in the States before the issue of trade friction had become public knowledge.
The engineering staff at EG, working with the assumption that auto production at HAM would yield 600 cars a day, developed a welding machine that integrated several processes. Steel sheets were shipped from the U.S. in order that the new machine could be validated using the proper type of material.
Auto production in the United States was taking shape when, in December 1979, Honda signed a licensing agreement with British Leyland Ltd. (BL), the respected British auto manufacturer. This was to be Honda’s first step toward European car production. Thus, Honda could apply its experience with BL to the strategies for auto production at HAM, especially with regard to production facilities and overseas engine/transmission shipments. This, together with the expertise obtained through motorcycle manufacturing at HAM, would give Honda an excellent start in automobile production in America.
It was increasingly seen as a real possibility that Honda would make it in America. The actual production of the company’s first U.S.- produced car was close at hand.
The Mission: Build an Even Better Accord!
Construction of the HAM automobile plant began in December 1980. To prove that Honda was building a plant that truly would be rooted in the American community, Honda actively employed manufacturing equipment that was made or sold locally, and decided on a basic policy to manufacture cars using American-made raw materials such as sheet steel, plastic, and paint. This was a challenging task at the time, since given the differences in Japanese and American standards, there was a considerable risk of diminished quality. In fact, many believed that HAM would not be able to produce cars that were of the same quality as their Japanese-made counterparts. This was a critical point, for if any public perception were to arise that HAM-produced Accords were lacking in quality it would be hard to erase. There would be no excuse for mistakes involving quality control.
A system of mutual support was established with Saitama Factory’s Sayama Plant as the "mother plant" in Japan, so that both locations could ensure timely responses to all car-production requirements. Additionally, the R&D Center provided invaluable support in dealing with raw materials and parts specifications. To facilitate the successful launch of American operations, HAM’s Executive Vice President Hiroshi Hayano was to direct the start-up, while in Japan Saitama’s General Manager Takeru Mizoguchi led the support effort.
"I sent about 300 people, including the best experts and veteran associates, from Sayama to help out at HAM," Mizoguchi said, recalling the intense period of preparation. Inspections of mass-production performance at the HAM plant went forward at a rapid pace, and whenever defective parts were found, their cause was corrected in collaboration with the associated parts manufacturer. The staff from Japan worked with unfamiliar American equipment, making technical improvements with the help of American manufacturers in order to achieve consistent quality in mass production.
Many associates who had gained experience in motorcycle production were in fact transferred to the new auto plant, demonstrating impressive leadership abilities on behalf of the newly hired associates.
HAM’s first Accord rolled off the production line on November 1, 1982, achieving the promised quality in Production. In time, the number of cars the plant was producing increased, making way for full-scale output. That occurred a year-and-a-half after start-up, via the shift to a double workshift system for the production of 600 cars daily. Later a second production line was established, becoming operational in April 1986. Eventually, HAM was on a schedule of 300,000 units per year, shipping cars overseas for sale in Japan and other countries around the world.
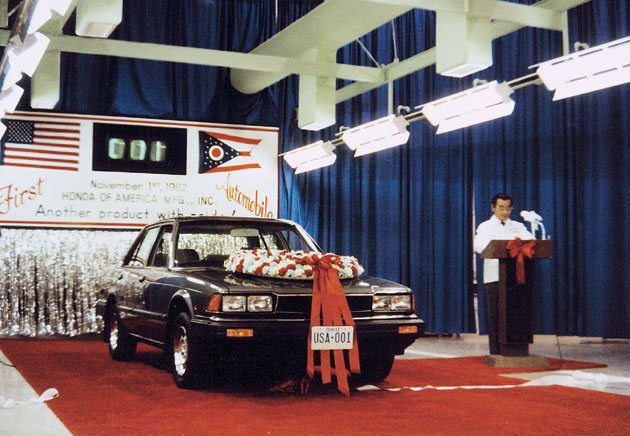
HAM’s first Accord left the production line on November 1, 1982. On the right is Kiyoshi Kawashima, proclaiming that the Japanese car-production facility built on American soil had rolled out its first vehicle. The car is now exhibited at the Henry Ford Museum, in Dearborn, Michigan.
"Many people were worried about whether Honda could really produce good cars in the U.S.," Nakagawa said. "So, it was helpful that we challenged the situation by creating a plant with a safe, cheerful, quality-oriented environment. Also, the many Japanese staff stationed in Ohio and those visiting from Japan did a wonderful job teaching our associates about Honda’s philosophy and technologies. I once heard that Mr. Kawashima said in Japan, ‘Ohio is the lifeline of Honda.’ His words became our driving force, inspiring us to achieve our goals no matter how difficult they might have been."
Kawashima recalled, "If we had failed in the American market, Honda would have lost its biggest market. That, of course, world have had very serious consequences. So, in that sense I believed that Ohio truly was Honda’s lifeline."
North American Manufacturing Expands
Coinciding with Honda’s effort to expand its manufacturing operations, the company also promoted an increase in the percentage of locally procured parts (local-content). Such an increase would enable timely manufacturing operations while contributing to the community through the creation of jobs at Honda’s American parts suppliers. Moreover, at a time when the yen was rapidly growing in strength, it had the effect of reducing fluctuations in the exchange rate by switching from the exportation of parts from Japan.
An increase in local-content, though, meant that local manufactures had to produce parts that met Honda’s specifications and stringent quality requirements. This entailed a significant amount of work. Through negotiations with American parts manufacturers, Honda worked to increase the number of associate suppliers who could promise to meet Honda’s requirements, and established parts makers in the U.S. with the help of Japanese parts makers, thereby creating a system for the supply of local parts.
BPI*1 was established on a lot next to HAM in November 1981, while in May 1984, KTH*2 was established. Many other parts makers were later established in the U.S., fulfilling the need for reliable, high-quality parts supplies.
Honda announced in October 1983 that it would build the Anna Engine Plant, a dedicated manufacturing facility. Then, in July 1985, the Anna Plant began producing Motorcycle engines. This plant was built with the goal of establishing an auto manufacturing base in Canada (Honda of Canada Manufacturing), with Anna assuming the role of engine provider. Therefore, concurrent with the manufacture of Honda cars in the U.S. and Canada, the production of automobile engines got under way at Anna It was September 1986.
Notes:
*1 BPI (Bellemar Parts Industries, Inc.), jointly financed and established by American Honda, Tokyo Sheet and Mie R&D in November 1981, manufactures exhaust pipes, brake pipes, and door sashes.
*2 KTH (KTH Parts Industries, Inc.), jointly financed and established by American Honda, Kikuchi Press, Hirata Press, Takao Metals, and Hongo Manufacturing in May 1984-manufactures press parts and welding parts for automobiles. (Names are as of the company's founding.)
American Development and Manufacturing Operations Grow
Honda established the HG-O (HG-Ohio Office) in July 1979 for providing technical consulting services to HAM and supporting the development of locally procured parts. Then, in April 1981, it became HRA-O (Honda Research of America, Ohio Office), whereupon it began its support of enhanced motorcycle quality and the development of Accord parts for local procurement.
In September 1984, as part of a system designed to facilitate autonomous operation, Honda Research of America was renamed as Honda R&D North America (HRA).
Furthermore, in May 1985, a branch office of EG was set up at HAM, and in April 1988, the office was incorporated as a local corporation Honda Engineering North America, Inc (EGA).
HAM added the production of Civics in July 1986. By December 1989, a second automobile plant (East Liberty Plant) began operating nearby.
Honda announced its Five-Part Strategy in September 1987, aiming toward further improvements in its North American corporate activities. This would involve the expansion of development and production in the U.S., as well as plants for exportation. Moreover, the strategy cited the goal of raising the local-content percentage from 60 percent to 75 percent by 1991.
HAM has since become Honda’s largest manufacturing base, producing 695,000 completed motorcycles and automobiles and 900,000 engines yearly using North American globally-sourced parts, with the support of more than 10,000 associates. In fact, using both domestic and globally-sourced parts the local-content of HAM’s completed vehicles has reached more than 90percent by traditional measures.
An Accord developed at HRA especially for North American market was manufactured at HAM in 1977. It was the fruit of teamwork comprising design, development, manufacturing, and sales systems in North America, quite independent of Honda in Japan. Thus, the new Accord had become an American car, and was embraced by people throughout the U.S.