The E300 Portable Generator / 1965
Convenient and Easy-to-Use Portable Generator
Spurred by the success of recent marketing efforts of its tillers and outboard marine engines, Honda's Power Products Division began in 1963 searching for ways to expand its lineup of generator products. Electrical appliances were coming into general household use, and leisure activities were enjoying increased popularity. Thus, there was an emerging need for portable generators, and it was widely anticipated that Japan's manufacturers would develop products in response to consumer demand.
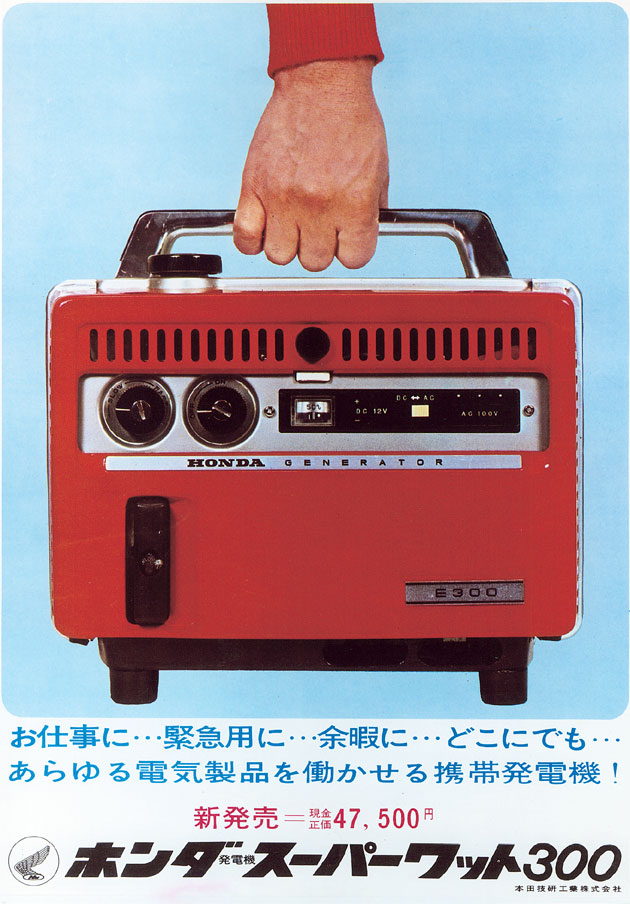
The brochure for the E300 introduced in January 1965. As the picture shows, the generator could be carried with one hand.
Honda had earlier developed a compact portable generator, the E40, by anticipating the future demand for products of that type. This lightweight, portable unit had the benefit of a soundproof housing and numerous other technical innovations. Even so, the E40 never made it to the market. The timing simply was not right, so mass production would not have been an economically sound move.
The new E300, however, was based on the expertise that Honda had acquired through its work on the previous unit. It was the ideal concept for a generator, combining 300-watt output with quiet and easy-to-use operation in a compact enclosure.
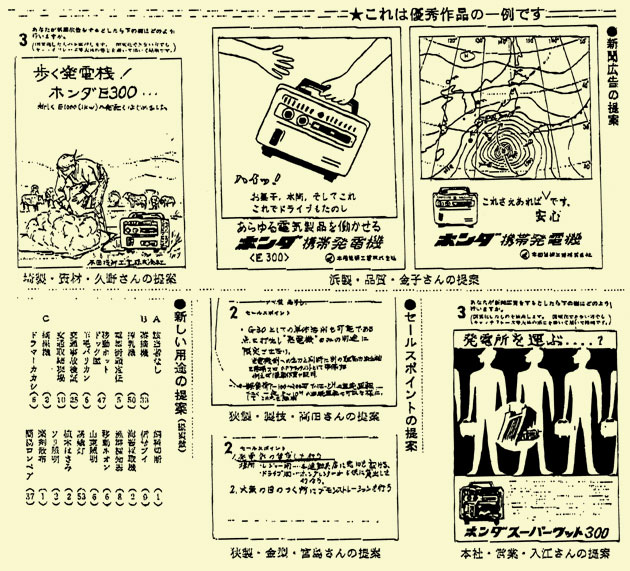
When the E300 was released, the employees were invited to send in ideas for the generator's application and newspaper ad. The most outstanding entries were published in the Honda company Newsletter (No. 116, issued in April 1966).
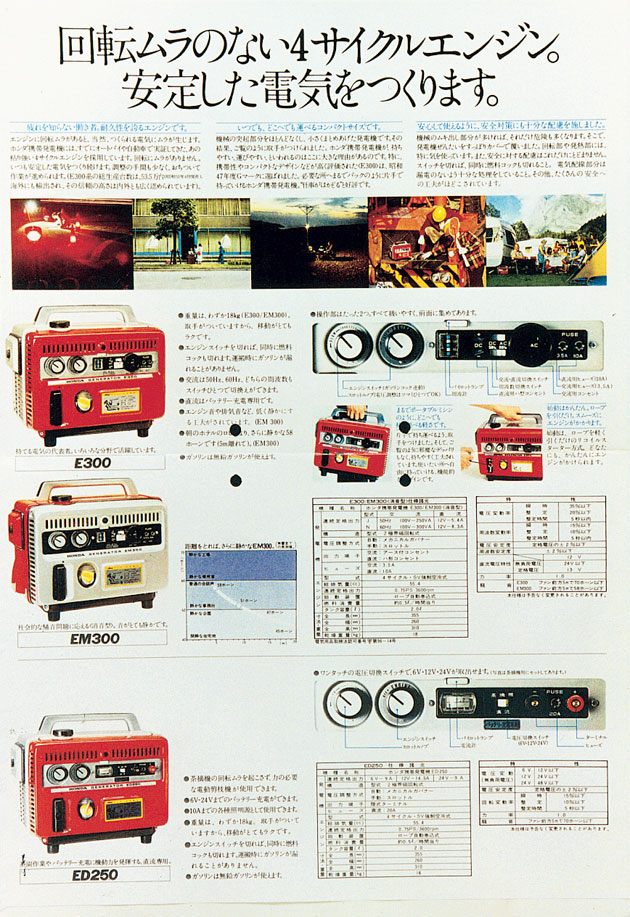
A brochure listing the specifications and features of the E300, EM300, and ED250
The Challenge of a Reduced Engine Size
Mikio Koyama, a member of the Engineering Design Department and also the general secretary of the Labor Union, was assigned to the E300 project in October 1963 to develop its engine and functional units. As the lone member of the project, he began to challenge the development of a portable generator going through every working process from designing to managing the prototype fabrication.
Koyama first had to reduce the size of the generator's engine, a hurdle he overcame by adopting a side-valve design with a displacement of just 50 cc. However, there was also the problem of space layout. Because the output side of the crankshaft was to be taken up by the generator component, all engine-control functions would have to be accommodated within the limited room available at the opposite side of the unit. Accordingly, the magnet rotor had to be attached to the rotational axis. This meant that all the necessary parts had to be attached to a single axis, including the rotation-control governor used to maintain constant r.p.m. and the recoil starter. The positional review of components also included the muffler, ignition coil, and cooling fan. The key was to combine these parts within a small space, yet ensure maximum efficiency in operation.
Put through the Wringer of a Prototyping Expert
Koyama endured considerable hardship in the E300 project, since he was already busy with his commitments to the union. He simply was not able to devote all his time to the product's development. Therefore, even though he had managed to complete the drawings, he had no idea how a prototype could be built. The employees involved in prototype construction, though, were to prove invaluable in that regard.
The fact that he was doing all the work himself meant that Koyama often encountered difficulties in the transformation from design to prototype. The occasional error in calculated values or drawing specifications meant that much of the work had to be redone. For example, a craftsman, an expert in wooden pattern crafting, encountered a crankcase draft angle of 1/50, which Koyama had specified in his drawing. The expert immediately pointed the discrepancy out to his colleague, saying they could never make a sand model casting with that angle. However, when Koyama argued against the expert advice based on what he would later describe as "youthful folly or an amateurish idea," it only infuriated the veteran. "You don't know anything about casting," he shouted, and proceeded to spend an entire day correcting just about everything in the drawing. He even took it upon himself to teach Koyama the theories of casting and specification methods on design drawings using wooden patterns.
It was thus an emotional moment when Koyama, with prototype engine completed, took the unit to the bench and submitted it for performance testing.
"I still remember the excitement I felt when the engine was fired up," recalled Koyama.
A Standoff with Soichiro Honda
One day, while he was going through the usual struggles with his drawing, Koyama began to sense the presence of someone watching him from behind. Slowly, he turned around and found Soichiro Honda standing there. To his surprise, though, Mr. Honda suddenly reached for the drawing, stripped it off of the design table, and threw it into the wastebasket. Koyama was so upset he was unable to say anything. A moment of complete silence followed, after which Mr. Honda said, "Why do you have to make the crankcase so big? Didn't you even consider that you could reduce the volume by not placing the bolts inside but simply allow them to be exposed? And how did you come up with such a long crankshaft for such a small engine? Make it a split-type instead." Then Soichiro turned and left, having pointed out two fundamental flaws in the young engineer's design.
However, there was a reason for the bolt design. Since there was no external appearance thought out yet, Koyama had to focus on giving the exposed section of the engine a decent look. To that end, he had designed the crankcase shape so that the tightening bolts would not be exposed. With regard to the long crankshaft, though, Koyama himself had acknowledged the effectiveness of a split-type, cantilevered design in terms of cost and productivity. Moreover, in that design, the connecting rod could be integrated. When he actually tested the crankshaft, though, the basic problems in engineering began to show up, including deflection and a tapping noise. Even the long process of trial and error seemed inadequate to resolve these issues, and weaknesses in Koyama's design dogged him all the way to the eve of mass production.
Refining the Layout in Just Three Months
Hiroyuki Hatakeyama was assigned to the E300's design in the spring of 1964, moving over from his position in charge of tiller development. He quickly began working on a concept, completing the drawing in a very short time. "I think it took me about three months to finish the layout," Hatakeyama recalled. Considering the essence of "portability," the first image that came to Hatakeyama's mind was that of a briefcase.
This concept, however, was found to be impractical, since the carrying position and operating position are completely reversed, which would cause problems in the fuel-supply system and other functions. Soon, he began working with Masahiro Sato of the Design Studio, and gradually set his mind on a shape. The new, cube-like configuration of the E300 generator was a radical departure from product designs of the period.
"We conducted some market studies, but we found virtually no products of that type," recalled Hatakeyama. "So, there was no competition, nor were there any particular guidelines we could follow. For these reasons, we could work on our design based on free, unrestricted thinking. At that time, we didn't have the current SED system or the means to conduct accurate market analysis as we do today. Nevertheless, we were convinced that it was the right shape, believing that a good product would always sell.
Soichiro Honda's Proposal with Young Female Users in Mind
Soichiro Honda, too, had a strong attachment to the portable generator, and in his enthusiasm for the project, he showered Hatakeyama with requests: "Don't ignore the bottom section. You must pay equal attention to areas that are not exposed." "Give it a warm, accessible look, so that everyone will have a sense of ease." "Reduce the operating sound and minimize vibration." Some of his requests, Hatakeyama recalled, were quite specific.
"Mr. Honda came up with new ideas one after another," said Hatakeyama. "He had a keen interest in the product. We could really sense that he wanted to compete with Honda's rivals by creating something that was new and original."
When at last he saw the completed cubic design, Mr. Honda pointed out that the handle was too long. He suggested that the handle be shortened so that when the generator was carried by a man and a woman, their hands would touch one another. It was shrewd advice, taking into account the user's sensitivities, particularly those of young women. Unfortunately, though, shortening the handle was found to be impractical due to structural limitations inherent in the assurance of fuel supply.
As for the design, consideration was given to small details in order to emphasize the product's "gentle image and ease of use." For example, a round knob design was adopted for all switches. The integrated control that served as both a switch and fuel cock looked exactly like the volume knob of a radio. As for the screws, ideas were incorporated to conceal the head section as much as possible. Throughout its design the project team faithfully reflected the advice given by Mr. Honda, who wanted to minimize mechanical elements and convey an easy-to-use image.
Walls that Stood in the Way of Final Specifications
Eventually, the prototype stage was completed, and a new team was formed in order to finalize the E300's specifications. Personnel from the Design Studio, Engineering Design, and Testing departments of Honda R&D, as well as from Production Engineering at Hamamatsu Factory, began working together to prepare for mass production.
However, the team found itself up against unexpected difficulties. In particular, the team members acknowledged three major problems blocking their way: these were related to the split-type crankshaft, maintenance-free continuous operation and reactor.
The team found, however, that the problem of a tapping noise in the split-type crankshaft could not be solved until mass production was under way. Consequently, the shaft had to be changed to a single-piece type during production. The goal of maintenance-free continuous operation was hindered by decreased output resulting from carbon deposits in the combustion chamber. To obtain approval for mass production, the requirement of 300 hours of maintenance-free, continuous operation had to be met. The team cleared that hurdle by increasing the bore size from 50 cc to 55 cc and adopting a squish-type cylinder head.
The reactor used to maintain constant voltage was the source of a problem in the generator section. The problem was a rather complicated one caused by the resinous material used as the core of the coil in the constant-voltage device. The coil would break when the resin was subjected to heat, ultimately leading to product failure. To tackle this problem, a group of production engineering personnel (electrical specialists) from Hamamatsu Factory, including Michiharu Kitamura, an electrical engineer, worked with Koyama in coordinating the matter with the manufacturer in charge of the generator section. Finally, the problem was solved through the adoption of injection resin with a lower threshold of thermosetting.
The mass-production drawing was eventually sent to Hamamatsu Factory, after which not a day went by without the project team struggling to solve problems. On the day that mass production began, Koyama said to himself, "We've finally made it."
Koyama also acknowledged that the new generator would not have seen the light of day without the teamwork of the various staff members, who with their wide-ranging expertise devoted their knowledge and energy to the project.
The Birth of the E300, a New Generator for the World
Honda introduced its innovative E300 portable generator in January 1965, promoting it as a product that could be carried with one hand.
"We were confident of its value as a portable, general-purpose generator," Hatakeyama recalled. "But when I was asked what the generator was for, I could only make some general remark that it was 'useful in a wide range of applications.' In other words, it wasn't necessarily a product that was developed with clearly defined target users in mind." Contrary to any doubts he might have had, though, demand for the E300 grew at an astounding rate. The key factor in that was the widespread use of generators for lighting the stalls at local festivals and fairs held across the country.
"All the people involved in the product-those in production as well as in sales-rushed headlong into this new and challenging field," Hatakeyama said. "The E300 benefited from the unexpected results of their efforts."
The E300 soon expanded its market overseas, showing its winning ways as a compact, easy-to-use generator for wide-ranging applications. Domestic sales also grew, thanks to the success of a unique TV commercial produced by the Sales Promotion Division. Ultimately, the E300 became the best-selling unit among all Honda power products, recording cumulative sales of 500,000 units. Moreover, that basic concept, which gave rise to the subsequent Denta series generators, is evident in contemporary Honda models.
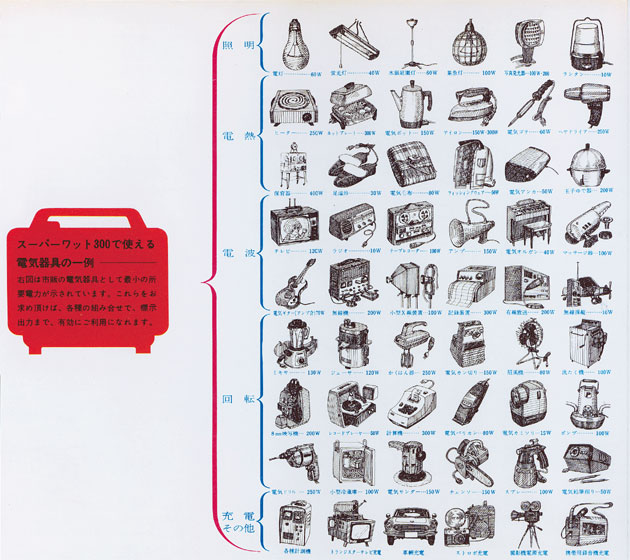
The initial product brochure introducing sample electrical appliances that could be used with the E300 generator
"In developing the E300," said Koyama, "I was able to apply everything I had learned through my previous experience. It was also a project in which I came to understand everything I needed to know, including how to approach product development, what we should look for in the design process and how to conduct tests effectively. Overall, the experience helped me in every motorcycle or automobile project I was later to become involved in. Today, the E300 is a familiar product around the world, being used by people in various ways. Knowing that, I cannot help but realize how lucky I was to be able to play a part in the development of such a great product."