Honda’s R&D Facilities Chapter 6
Environmental Testing Facilities (1): Fine-Tuning Honda Products in Extreme
Environments
Honda’s R&D Facilities Chapter 6
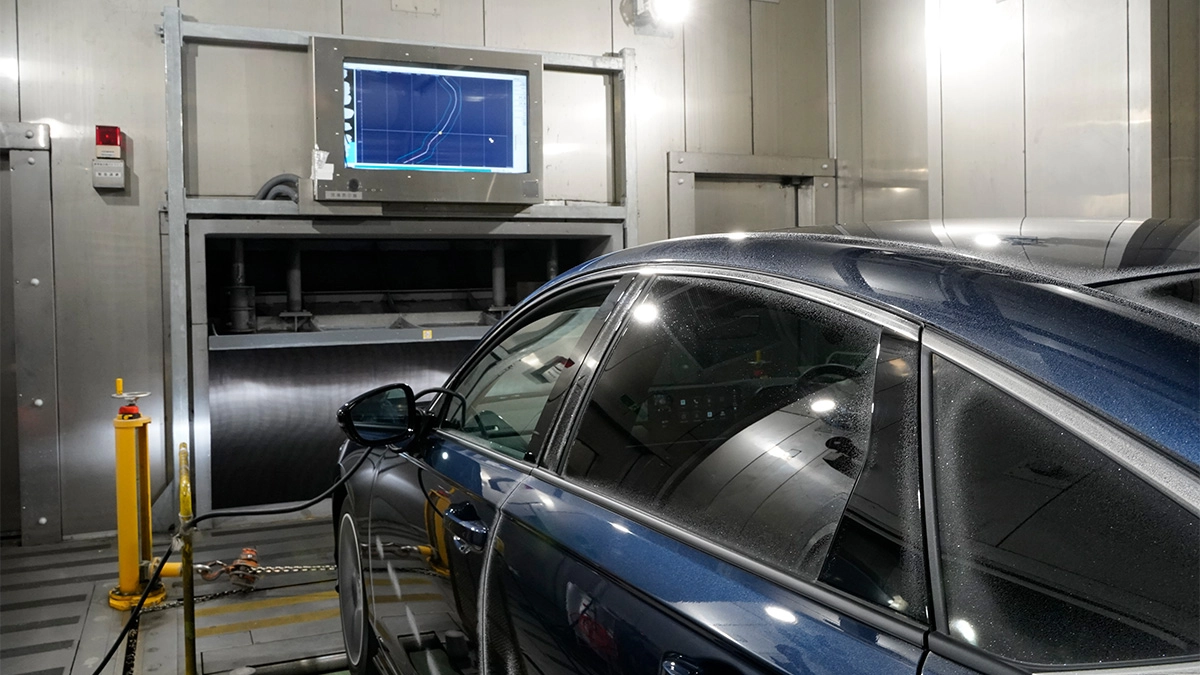
Artificially Recreated Harsh Environments Increase Development Density
Honda vehicles are driven in various regions all over the world. In some places, the temperature drops below minus 20 degrees Celsius in winter. Some areas reach altitudes above 3,000 meters. On-location field testing to confirm that vehicles perform as intended is essential for ensuring that Honda users can feel reassured about driving in such harsh environments. However, it takes time and costs money to send people and items to far-off places, and there is no guarantee that the desired conditions will eventuate even if those expeditions are undertaken. When Mother Nature is part of the equation, there is only so much that can be achieved within the development timeframe.
Honda facilities that artificially recreate the low temperatures of cold-weather regions and the low air pressure of regions situated at elevated altitudes are a low-temperature noise and vibration test bench, and a negative-pressure, low-temperature climatic chassis dynamometer. Both are located at the main center for four-wheeled vehicle development in Tochigi. Basic performance parameters are checked and fine-tuned here throughout the year. This increases development density while also reducing the burden of field tests, leading to higher development efficiency and enhanced marketability.
Low-Temperature Engine NV Test Bench
A low-temperature engine NV test bench measures engine noise and vibrations in an artificially recreated cold-weather climate. Not only can it cool the room to extremely low temperatures below minus 20 degrees Celsius, but it also cools coolants, lubricants, and fuel to extremely low temperatures to create the same kind of environment as the cold-weather regions where vehicles are actually driven. Repeated testing in an artificially recreated low-temperature environment reduces the burden of on-location field testing and improves development efficiency, enabling delivery to customers of products of higher quality.
Metals characteristically contract as the temperature falls. The clearance between parts, such as pistons and cylinder liners, increases as a result, sometimes making the engine produce a different sound when started at low temperature compared to after it has warmed up. Lubricant, which becomes more fluid as the engine warms up, is more viscous at low temperatures and this also influences noise. Metallic rattling, for example, may sound more pronounced.
Honda wants customers to ride its vehicles without being bothered by noise at normal or low temperatures. The development team used to seek out low-temperature environments in which to evaluate noise and vibrations in low-temperature conditions, venturing in winter to gruelingly cold regions and in summer to cold regions of the southern hemisphere, where the seasons were the opposite to Japan. Although field tests are still undertaken today to verify how actual products fare in the real world, the natural world complicates the ability to reproduce the right conditions. Field tests, while a necessary task, cannot be considered efficient.
For example, when undertaking cold start field tests on location, it may be that only one test can be carried out each day. This is because performing a test warms up the engine and testing requires precise reconstruction of the right conditions—the whole engine, including coolant and lubricant, completely cooled. It might take until the following morning for the engine to cool completely, and even then, there is no guarantee the desired temperature conditions will be achieved.
The low-temperature engine NV test bench controls the temperature to achieve the desired conditions, enabling repeated evaluation at short intervals. As the necessary improvements are identified, they can be completed on-site within the Tochigi R&D facility. This allows a speedy turnaround for repeat testing as it eliminates the process, required with field tests, of taking the engine back to the R&D center in Japan for adjustments before returning to the location for further testing. The ability to conduct repeated testing under the same conditions, without being affected by the climate or other outside interference, also opens up potential for additional discoveries and reduces the chance of overlooking issues. These, too, make the low-temperature engine NV test bench worthwhile.
Not only does the low-temperature engine NV test bench use a refrigeration
unit to recreate low-temperature environments, but it also has a heater for
simulating the warm-up speed of an actual vehicle operating in low
temperatures.
To measure noise with high precision, an anechoic chamber
is used. While noise and vibrations are generally measured with a
microphones and G sensors, Honda also makes sure to check these parameters
with the human ear rather than rely solely on recorded data to make
evaluation judgments. Data is checked to ensure phenomena perceived by human
ears have been picked up, and the phenomena are analyzed. Evaluation is
repeated until the targets are reached. On-location field tests are
conducted at the end for confirmation.
The low-temperature engine NV test bench is used for not only measuring noise and vibrations in whole engines, but also component testing. For example, an assembly of just the cylinder block and head might be gradually cooled to see how the cylinder bore deforms as the temperature falls, and to measure those deformations in close detail. Deformation is also measured as the engine warms during the warm-up process. Understanding how deformation occurs with temperature changes is a way of analyzing the mechanisms behind noise generation. Conducting such component tests with varying scope leads to an accumulation of base data that can be reconciled with computer-aided engineering (CAE; design and analysis using computers) to enhance the accuracy of calculations.
In the low-temperature engine NV test bench, we have an example of how equipment progress is linked to technological progress. The ability to faithfully recreate low-temperature environments within the test bench chamber combines with advancements in measuring technology to enable observation of phenomena in finer detail than was previously possible, as well as faster, more suitable action addressing noise and vibration issues. This helps to enhance the marketability of Honda four-wheeled vehicles.

Main Refrigeration Unit
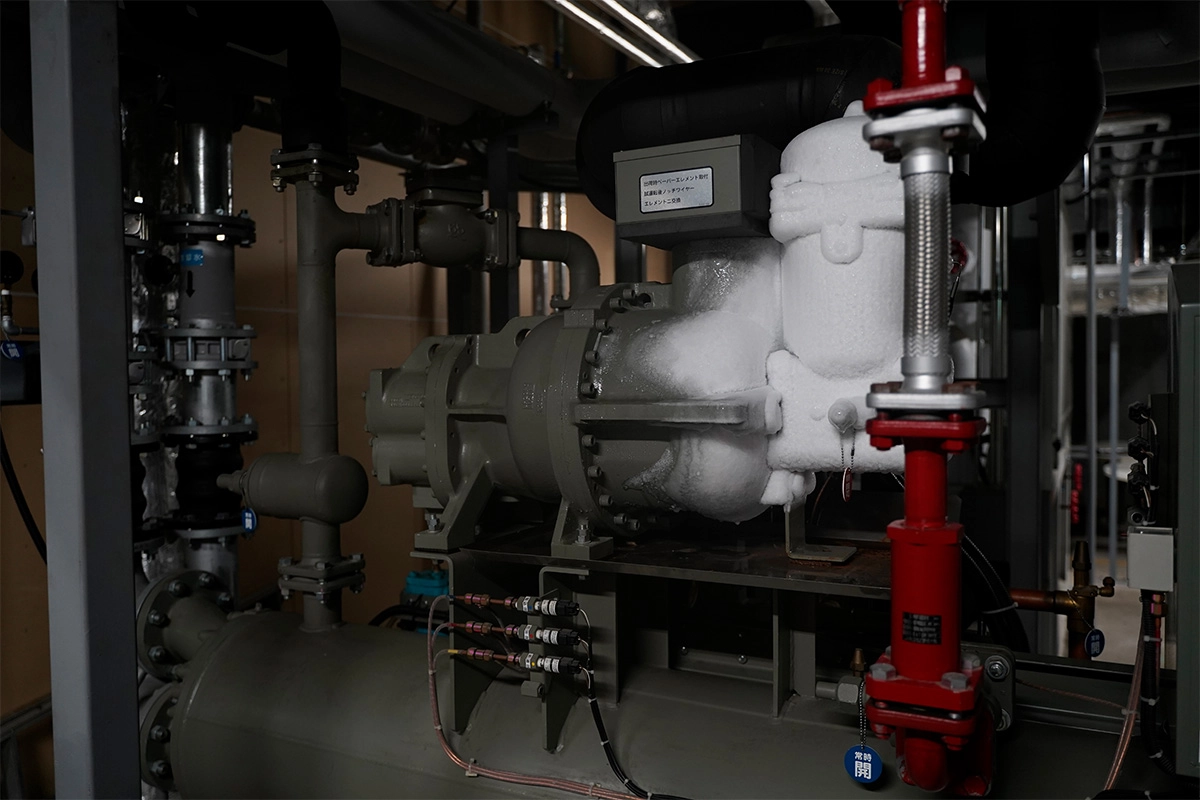
Low-Temperature Engine NV Test Bench
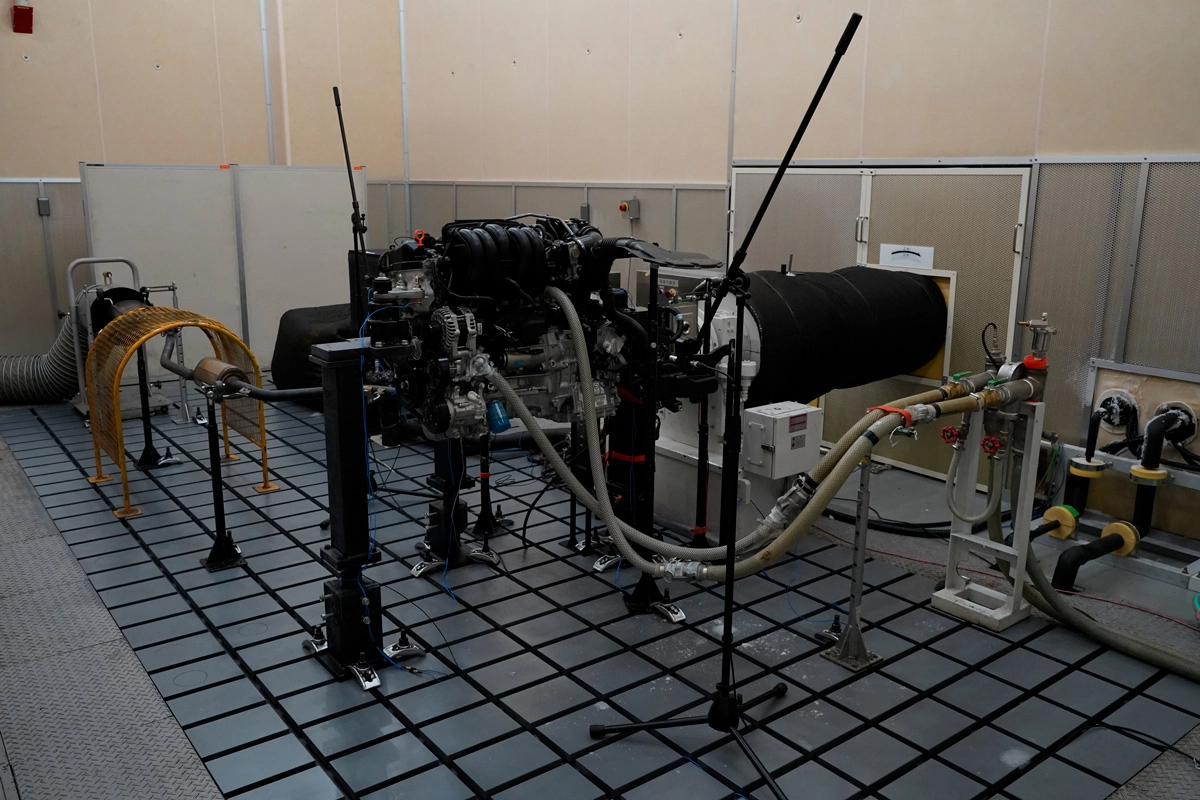
G sensors and Microphone
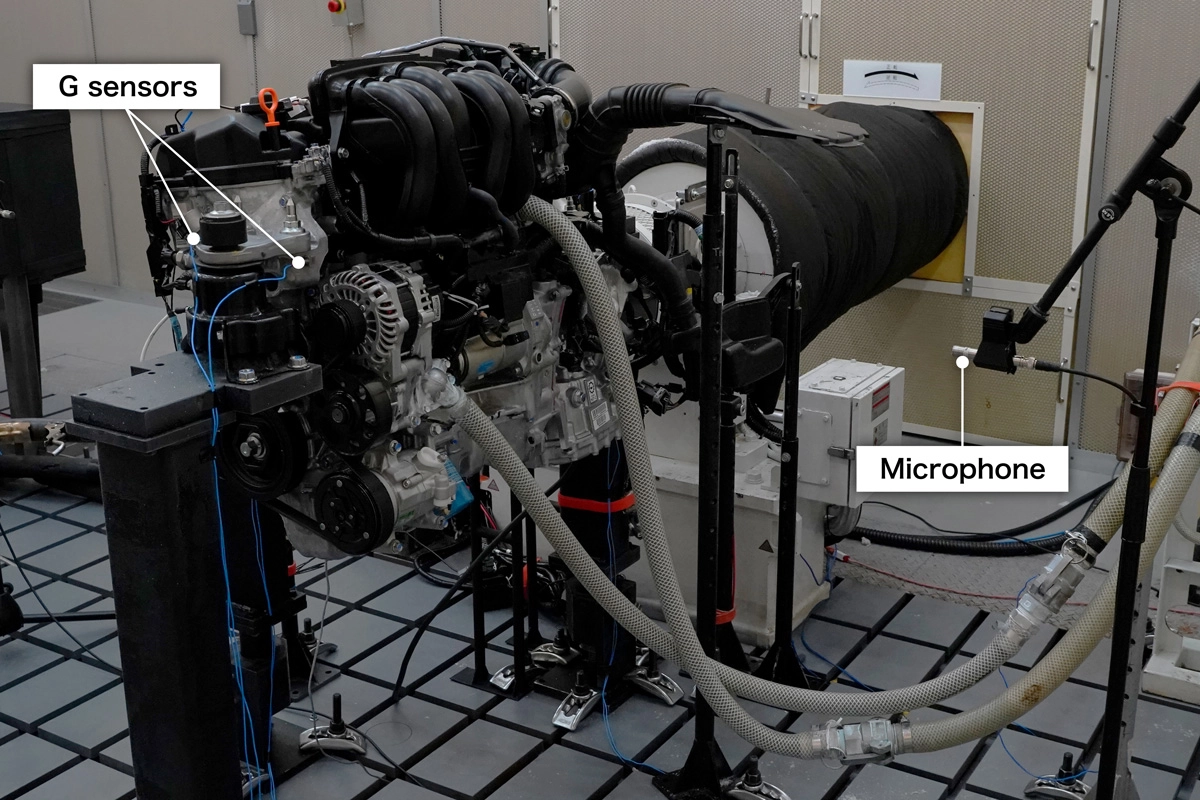
Control Room
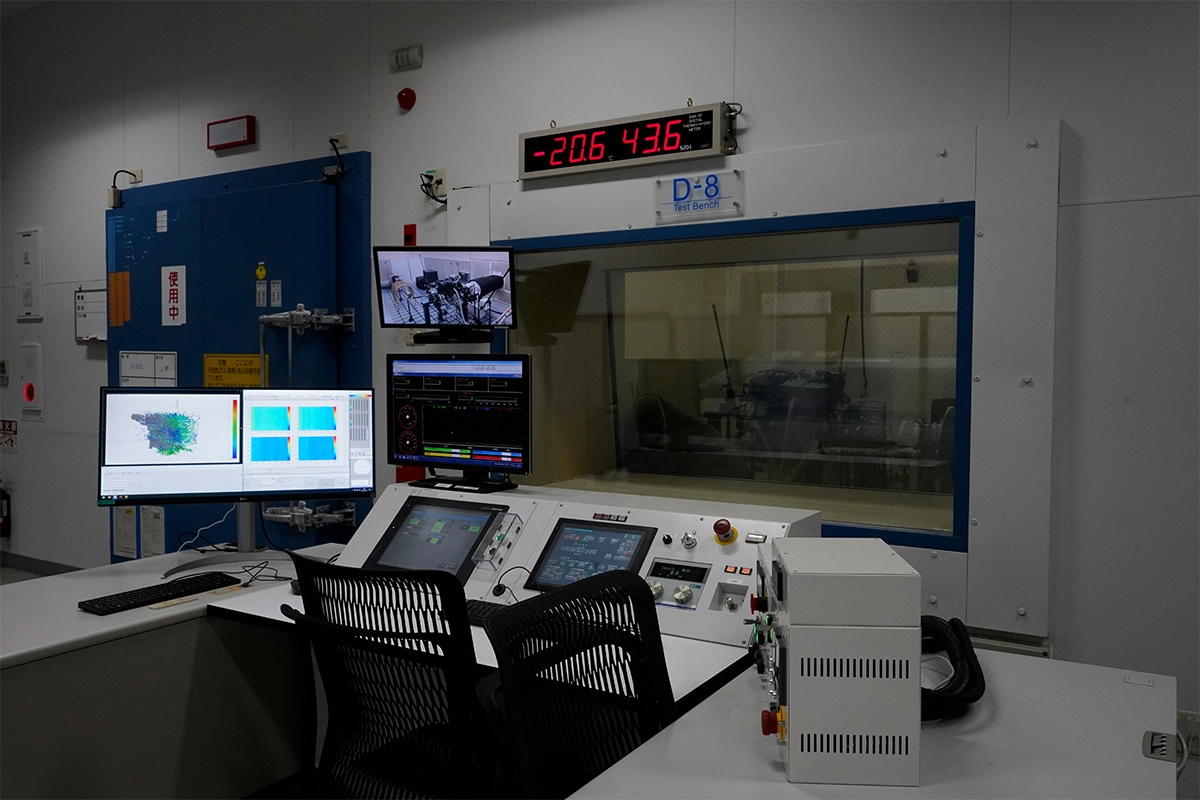
Main Refrigeration Unit
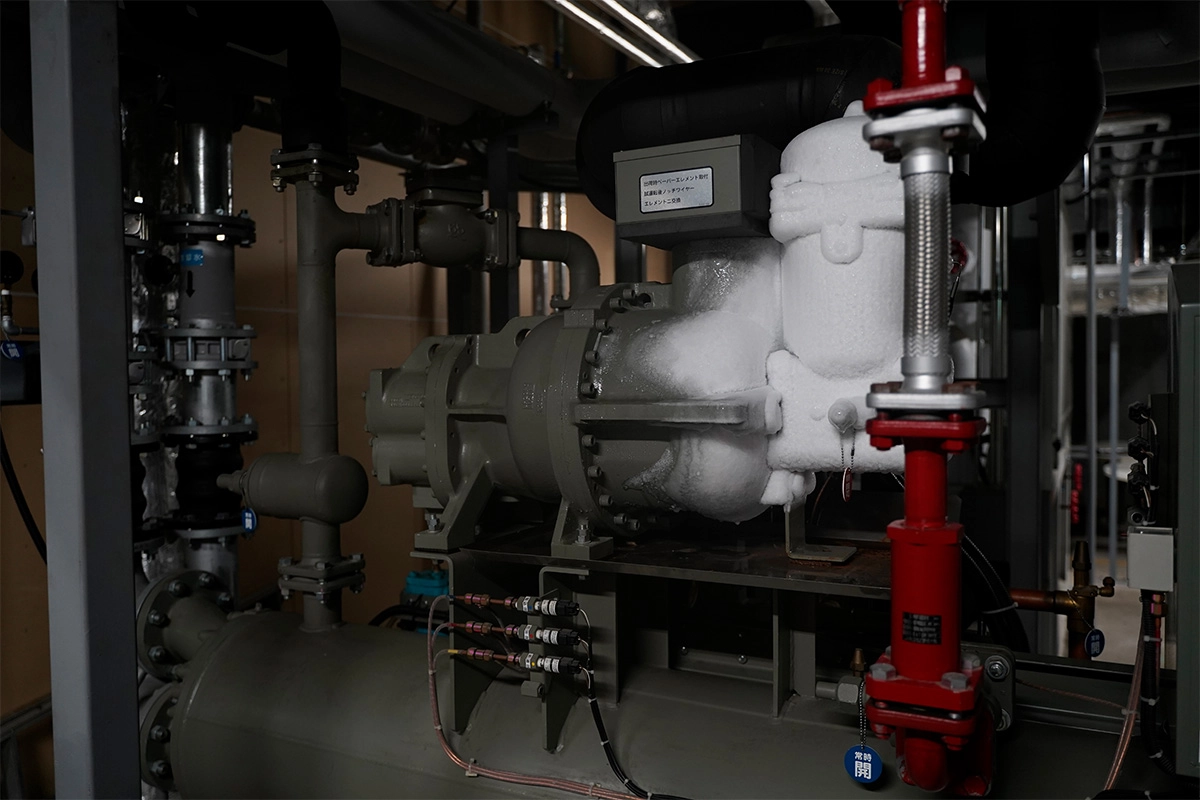
Low-Temperature Engine NV Test Bench
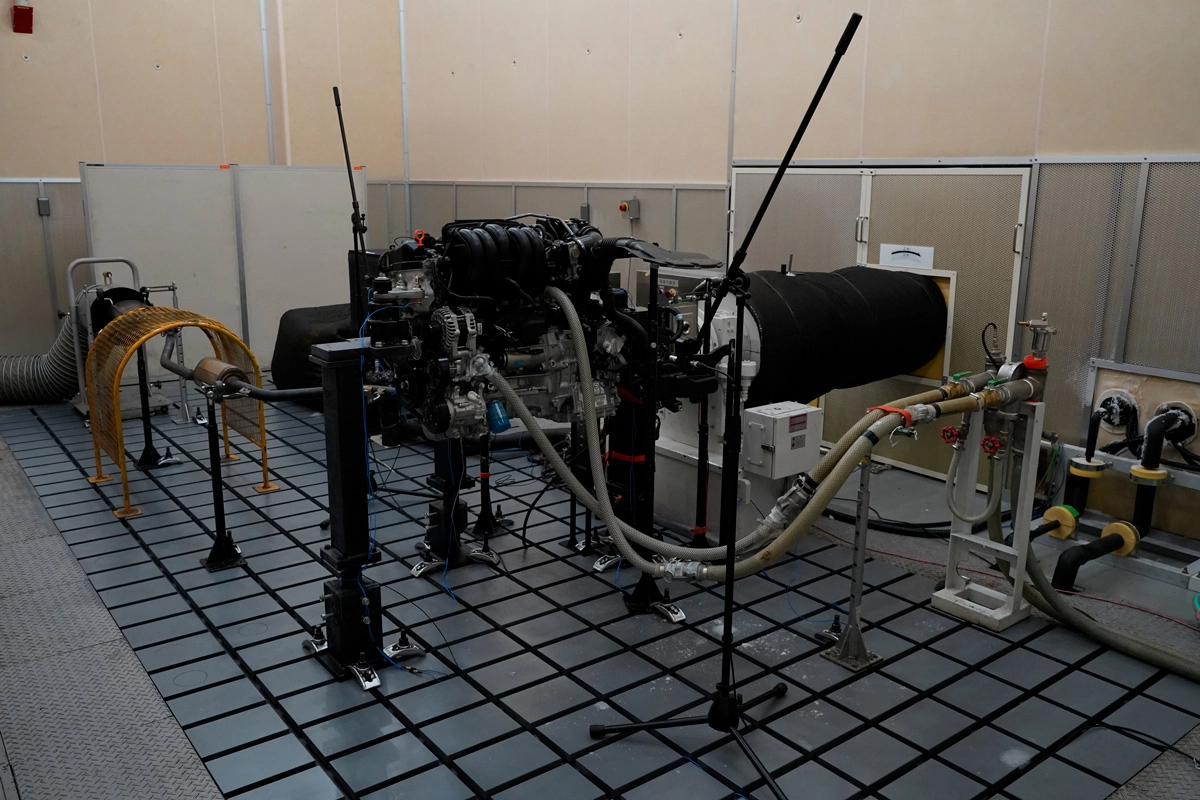
G sensors and Microphone
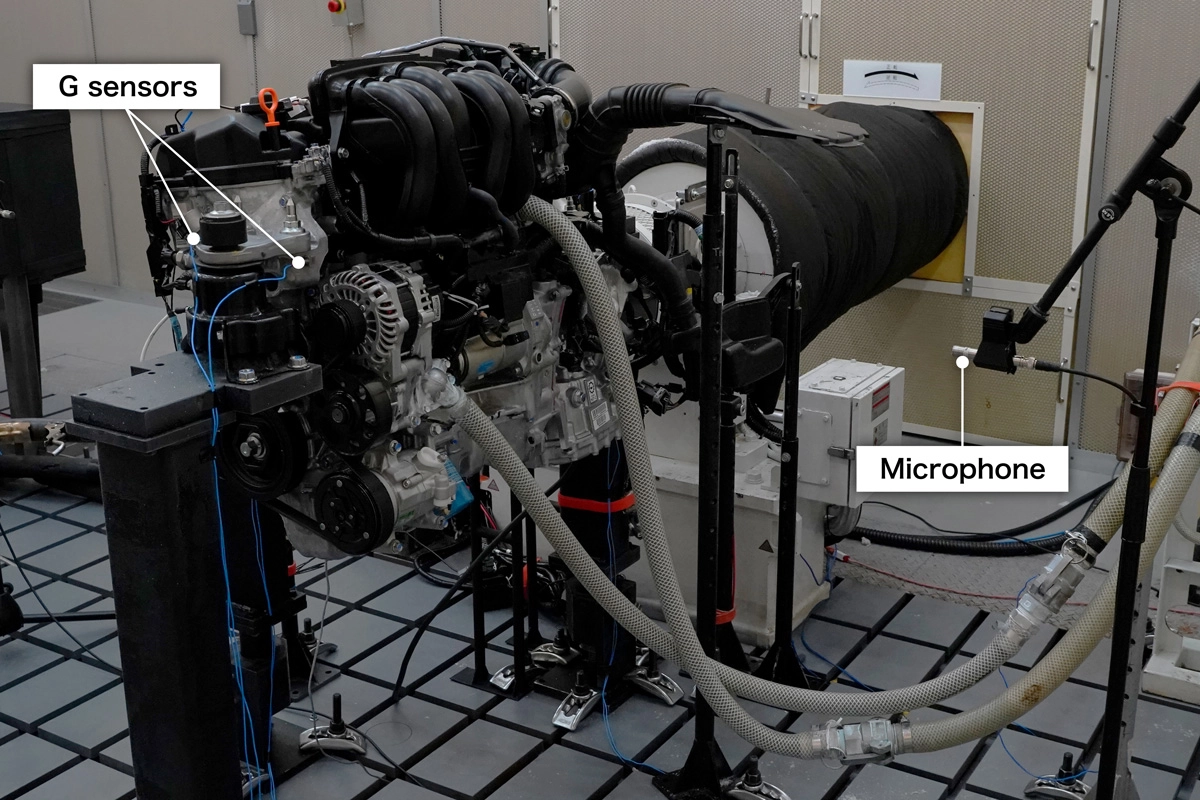
Control Room
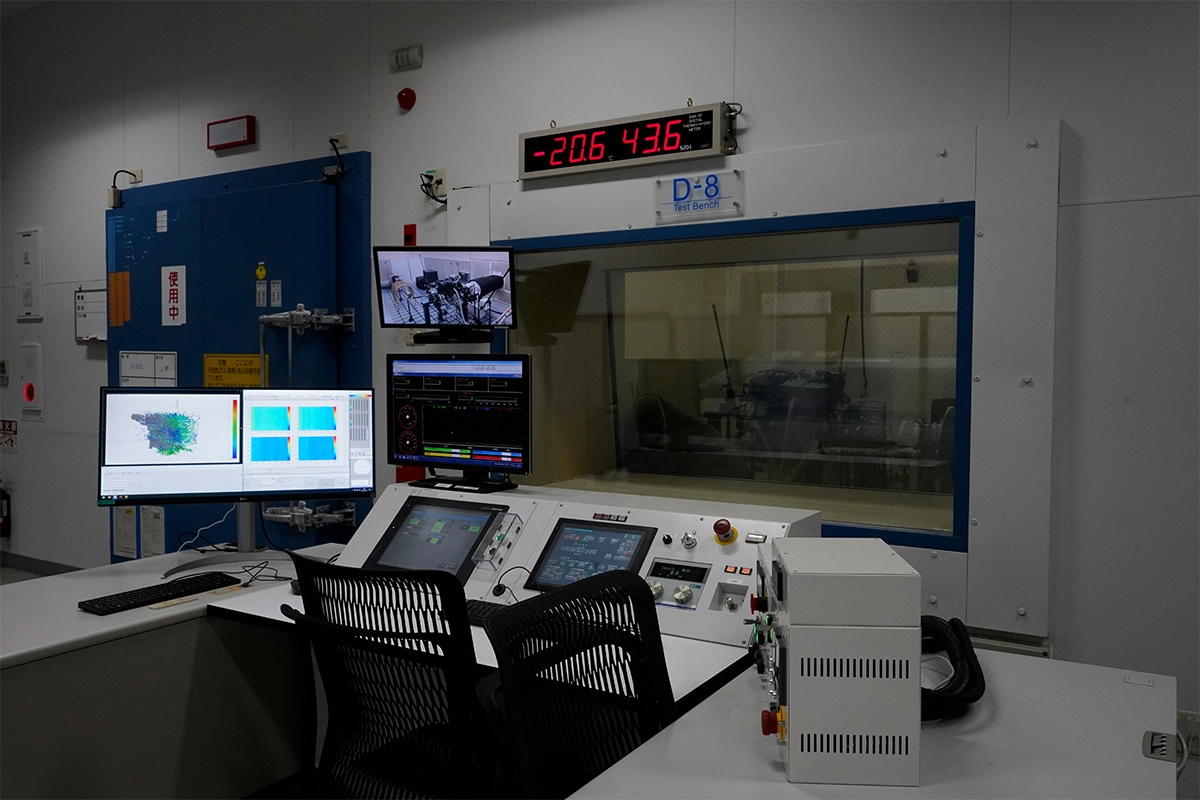
Main Refrigeration Unit
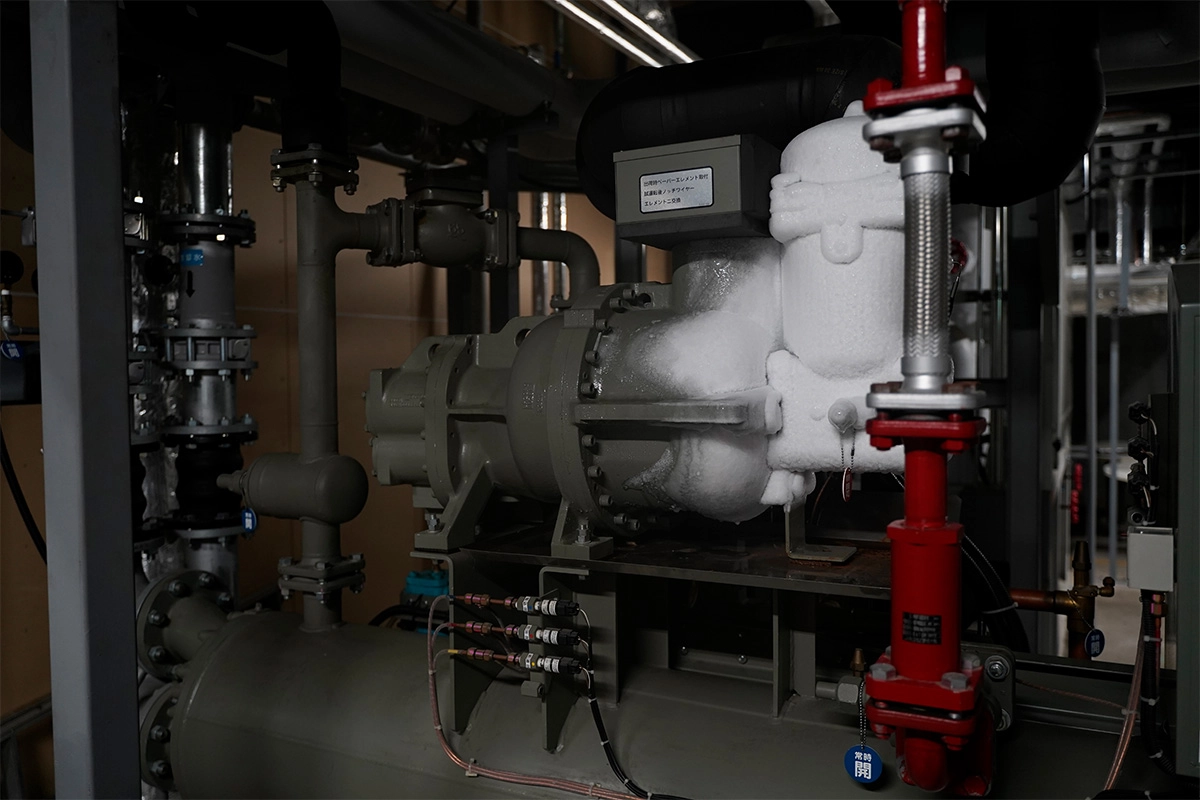

Negative-Pressure, Low-Temperature Climatic Chassis Dynamometer
A negative-pressure, low-temperature emissions-testing climatic chassis dynamometer, or dyno, is a facility used to test vehicles in a simulation of actual driving within a recreated high-altitude environment with thinner air and the resulting cooler temperatures. Honda vehicles are used at such high altitudes where the temperature and air pressure are low. The role of this facility, in ensuring that users can feel reassured about driving even in harsh environments, is to observe the driving performance and exhaust emissions of both engine-powered vehicles and vehicles with hybrid systems atop a chassis dynamometer (equipment for measuring the power output of a vehicle via rollers).
Air is required for engine combustion. As air pressure drops with increasing altitude, the density of the air falls, causing a decrease in engine output proportional to the drop in air density. One role of this facility is to check that the engine, or hybrid system, is functioning as intended, properly controlled based on information detected by sensors.
In a worst case scenario, the failure of an engine to start in a harsh high-altitude environment, where both air pressure and temperature are low, could be life-threatening. Checking startability in low-pressure, low-temperature environments is therefore an important evaluation parameter. Engines are also evaluated from a drivability perspective to determine whether they operate as intended during operations that drivers undertake every day, such as acceleration, deceleration, and cruising. In elevated areas, drivability can sometimes differ from low-lying terrain due to diminished engine torque. And in low-temperature environments, road surfaces are sometimes slippery, as they might freeze over. Slight, unintentional changes in vehicle behavior can unsettle drivers. Honda undertakes measurements and evaluation with close attention to detail to ensure that users can feel reassured about driving even in these conditions.
Because the negative-pressure, low-temperature emissions-testing chassis dynamometer creates low-pressure conditions by removing air from the room, it is of sturdy construction, designed to withstand relatively high pressure from the outside. Inside the Test Chamber, alongside the dyno on which the vehicle is loaded, there is also space for one vehicle where it can be tested or wait on standby. If only start-up and conditions during idling are being checked, this space can be used. The test vehicle upon the dyno is subjected to an airflow corresponding to the vehicle speed. This simulates wind created by motion, enabling testing under the same conditions as a vehicle on the road.
Adjacent to the Test Chamber is a Soak Chamber. Here, vehicles are sufficiently cooled prior to testing . While low-temperature conditions can be simulated in the Test Chamber, accurate data will not be collected if the vehicle itself is still at a normal temperature. Time is therefore taken to cool the vehicle to its very core. Parameters that need to be verified in relation to faults and issues more likely to arise in low-pressure or low-temperature environments are established in advance based on know-how gained from past experience. Every effort is made to ensure that the vehicle will not break down even when the demands placed on it are severe.
Working in low air pressure and low temperatures can be a huge strain on the human body. Workers enter the room housing the dyno only after acclimatizing their bodies to the low pressure inside a Decompression Chamber. After completing their tasks within a limited timeframe, the workers enter a Recompression Chamber, where they gradually increase the atmospheric pressure to acclimatize their bodies before returning to the Control Room side of the facility. In case something goes wrong, there are always at least two people on either side—two workers on the dyno side and two operators in the Control Room.
While the negative-pressure, low-temperature emissions-testing dyno can simulate the conditions of elevated areas in order to establish engine and hybrid system settings for low-pressure and low-temperature environments, Honda fully understands that this is not enough. Ultimately, vehicles must also undergo on-location field testing. This is because there are always scenarios that cannot be checked except in the real world. But the burden of field testing is without question lighter now that basic settings are established using the negative-pressure, low-temperature emissions-testing dyno than when most of the checking had to be done on location. Higher development density is contributing to both quality improvements and enhanced product marketability.

Control Room
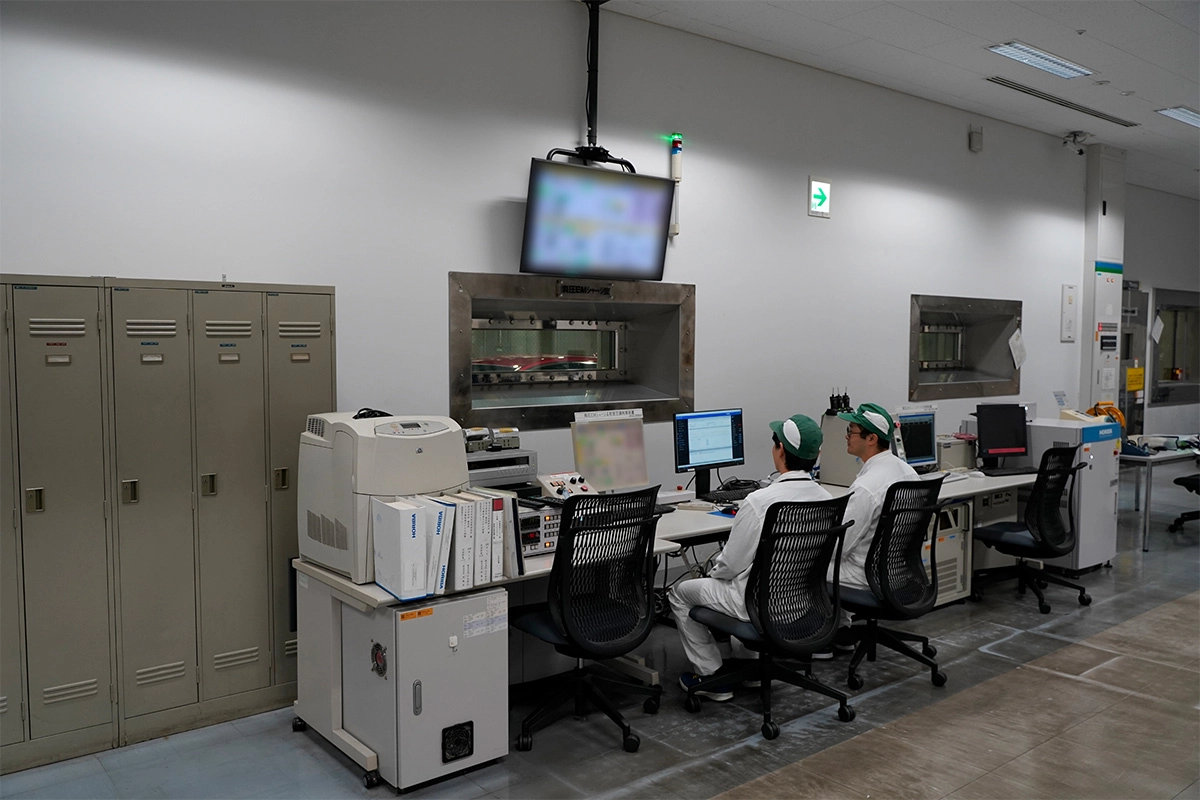
Layout of the Negative-Pressure, Low-Temperature Climatic Chassis Dynamometer
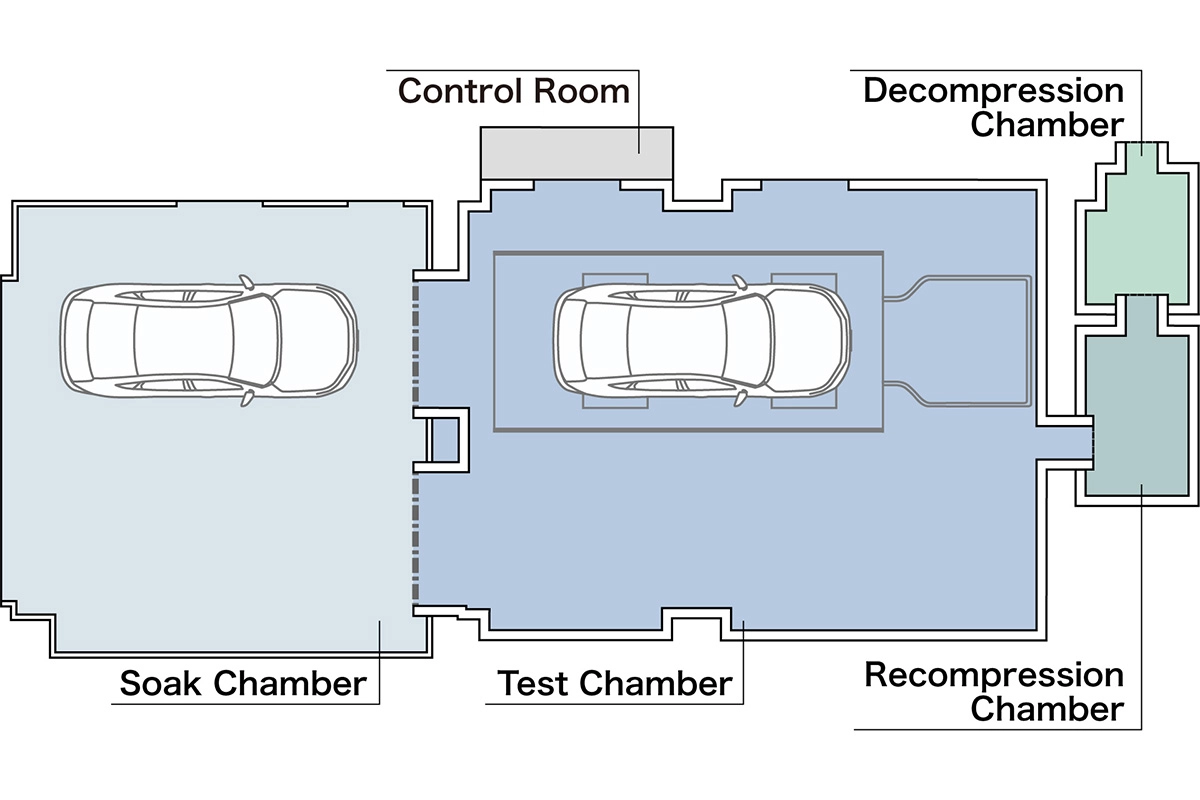
Test Chamber
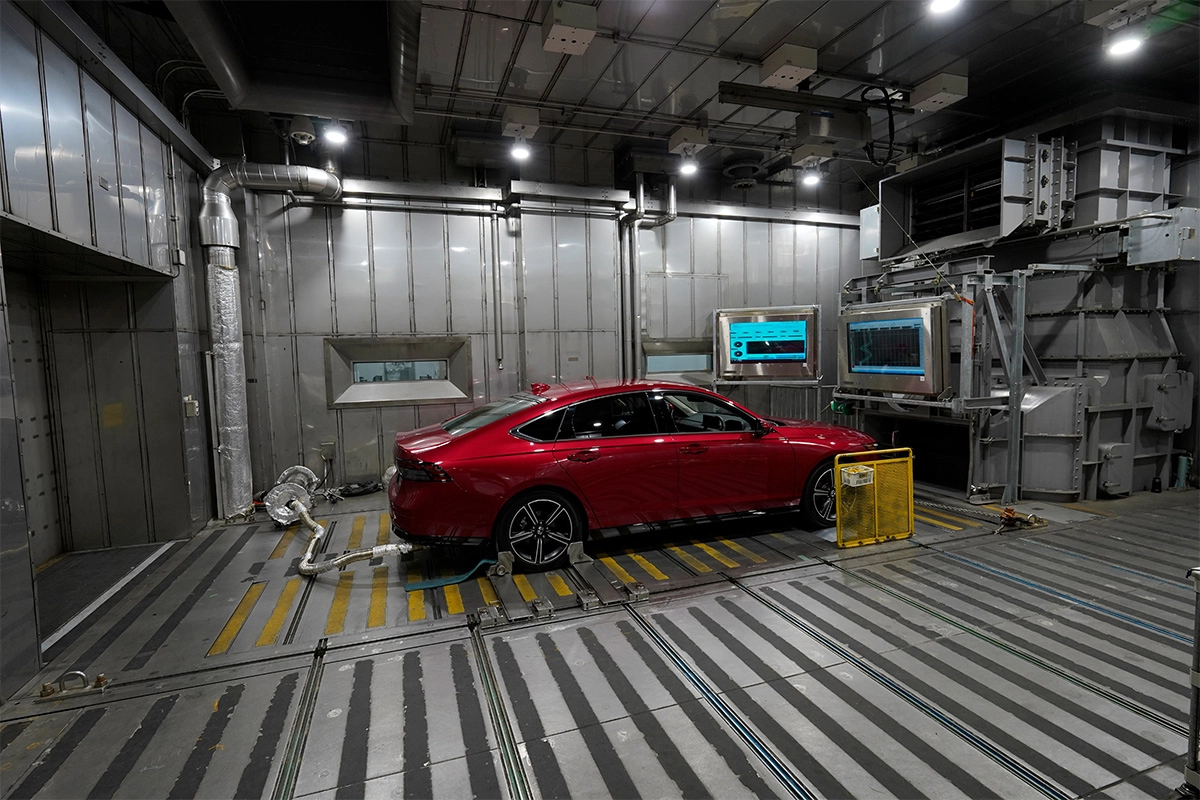
Soak Chamber
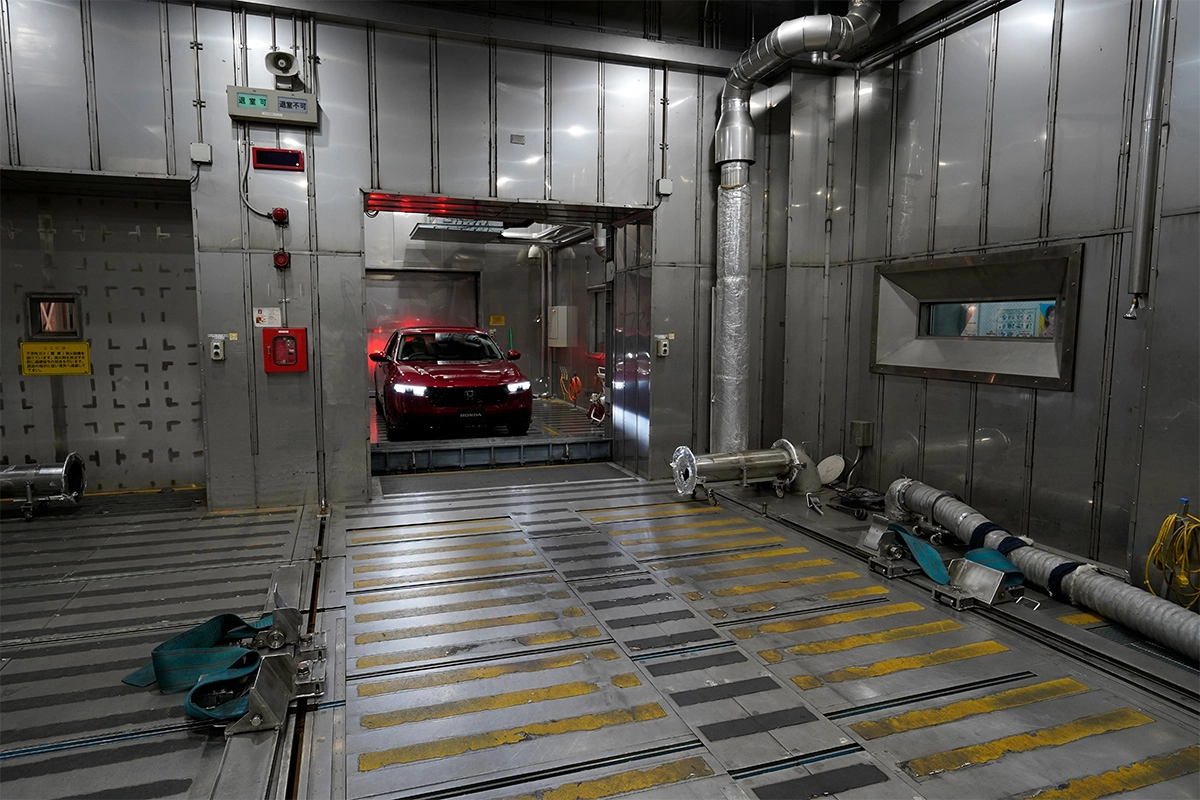
Decompression Chamber
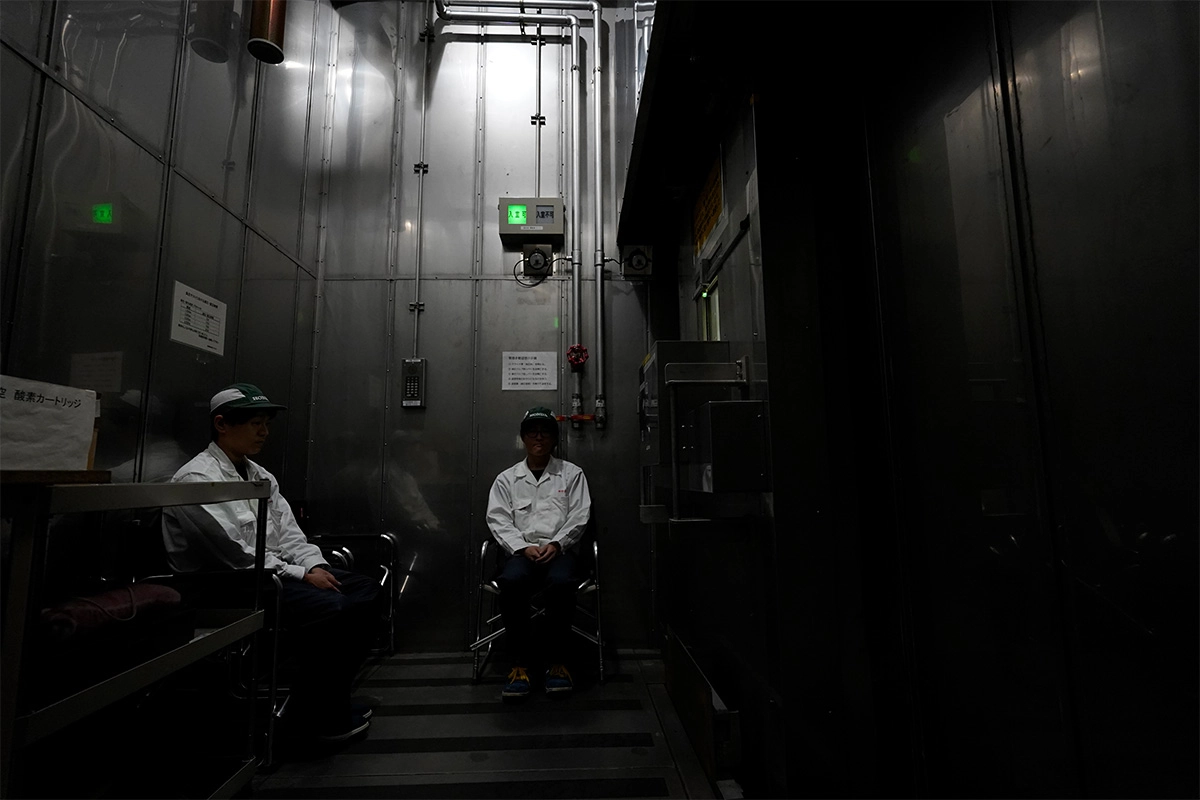
Pressure Gauge
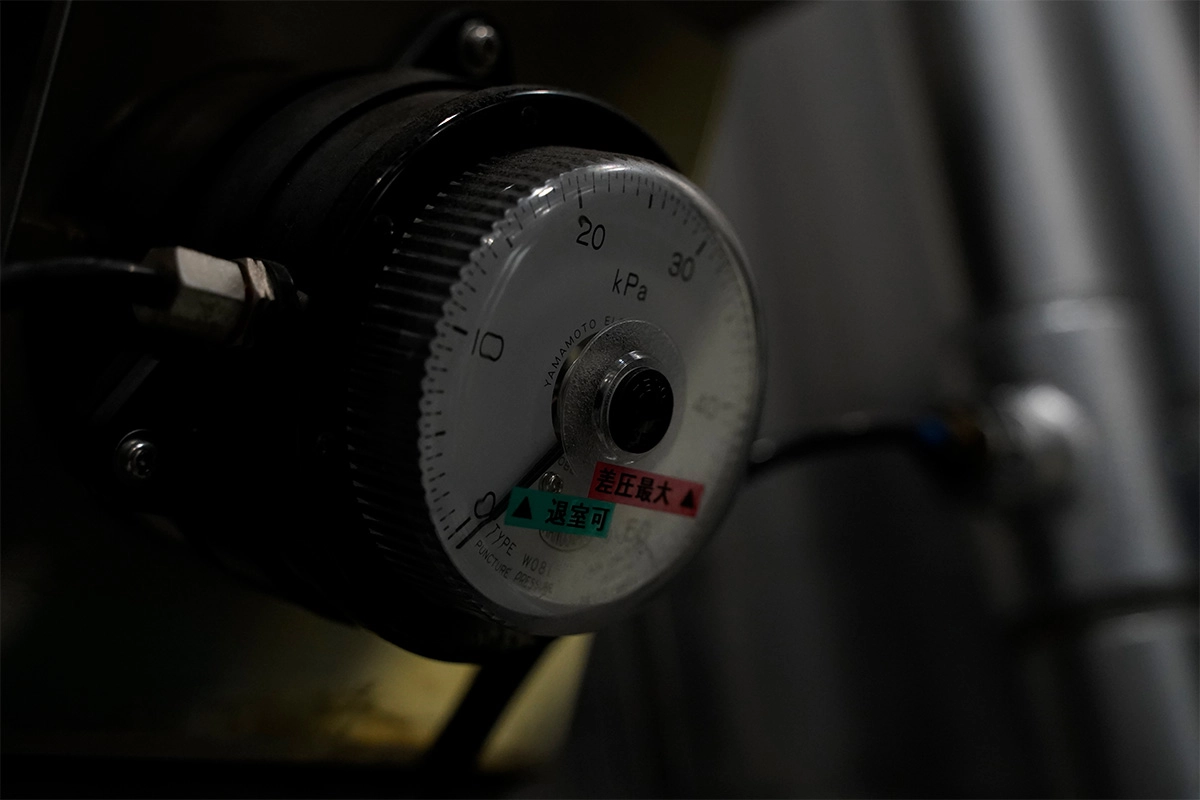
Control Room
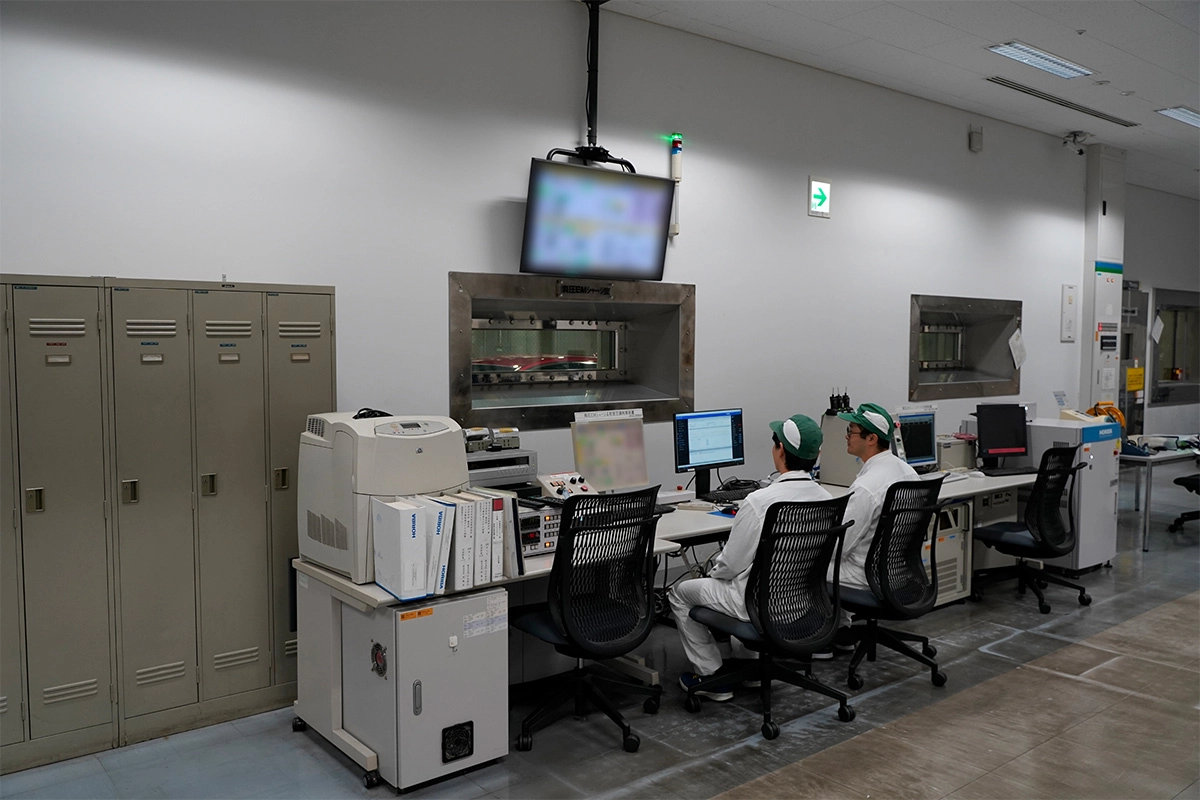
Layout of the Negative-Pressure, Low-Temperature Climatic Chassis Dynamometer
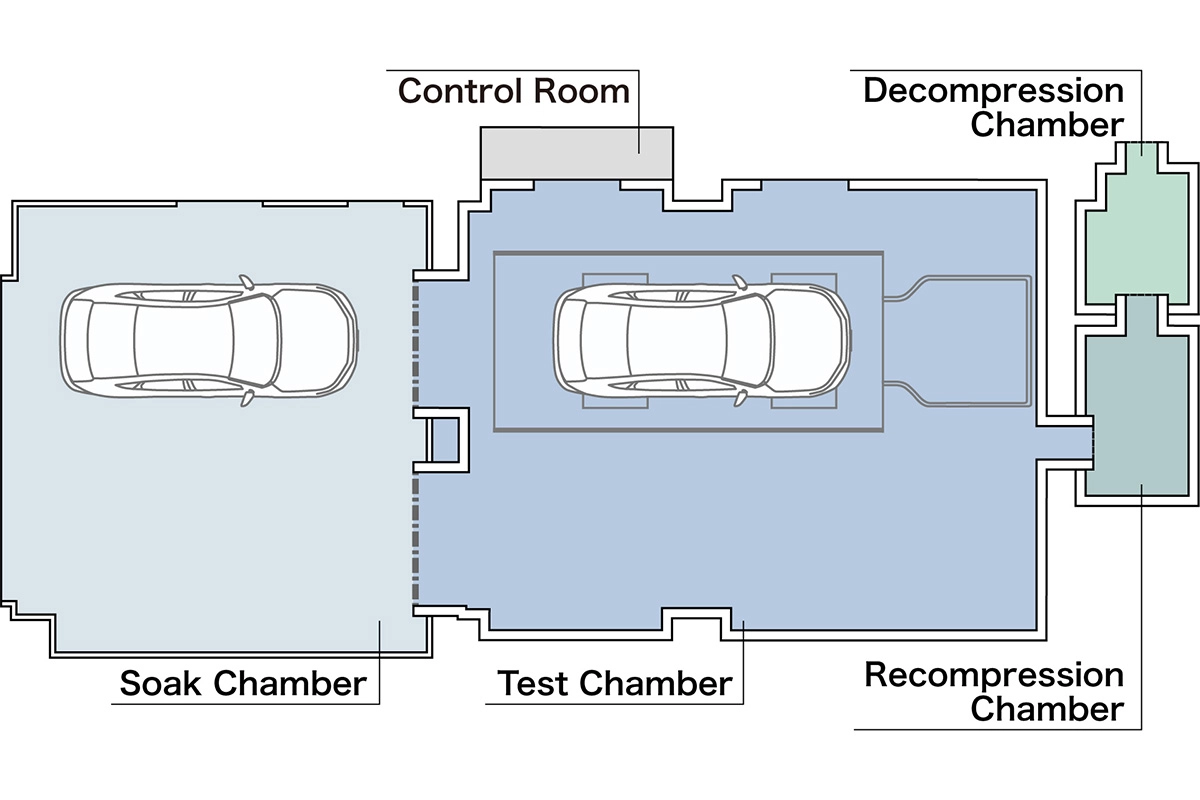
Test Chamber
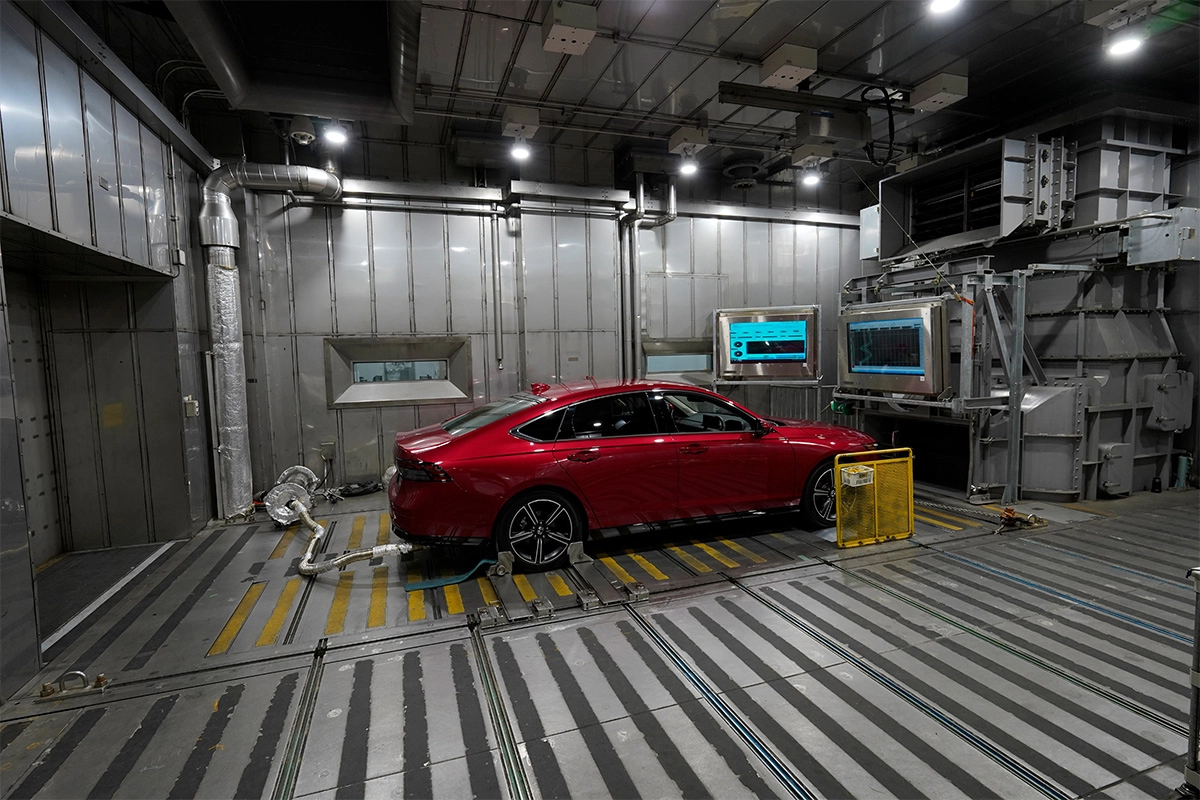
Soak Chamber
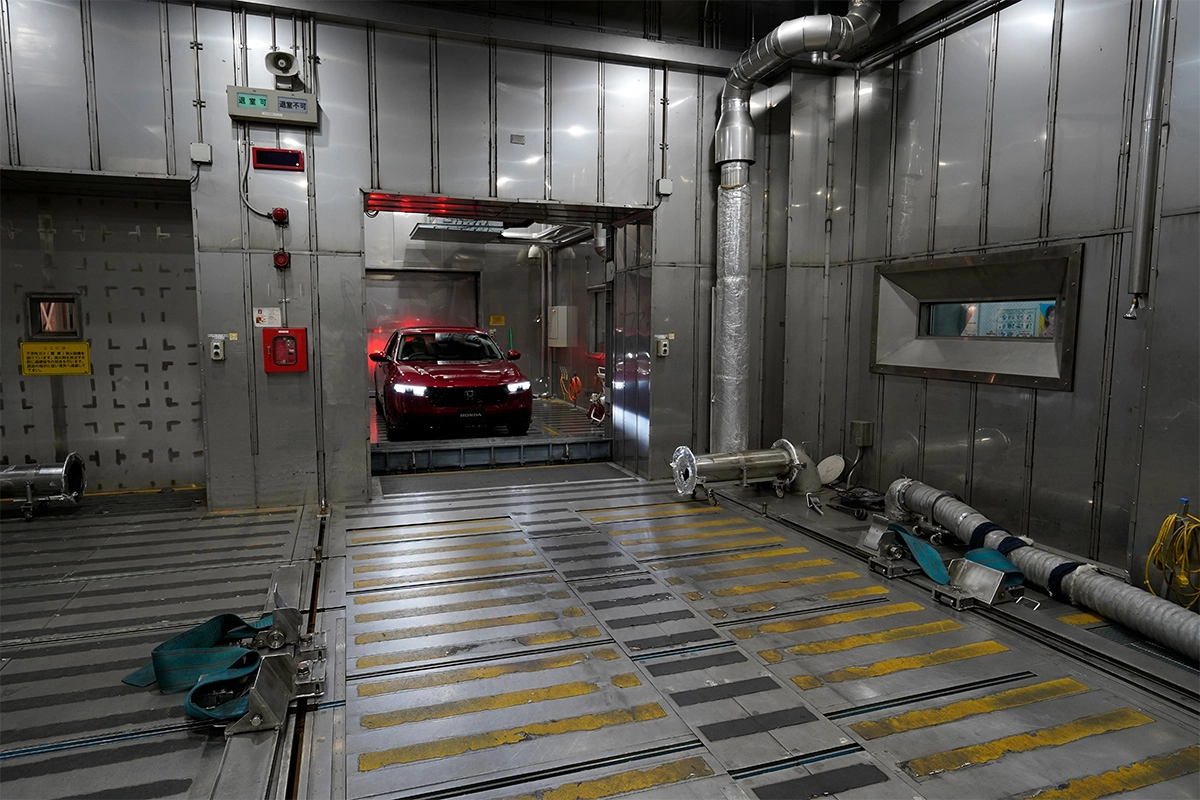
Decompression Chamber
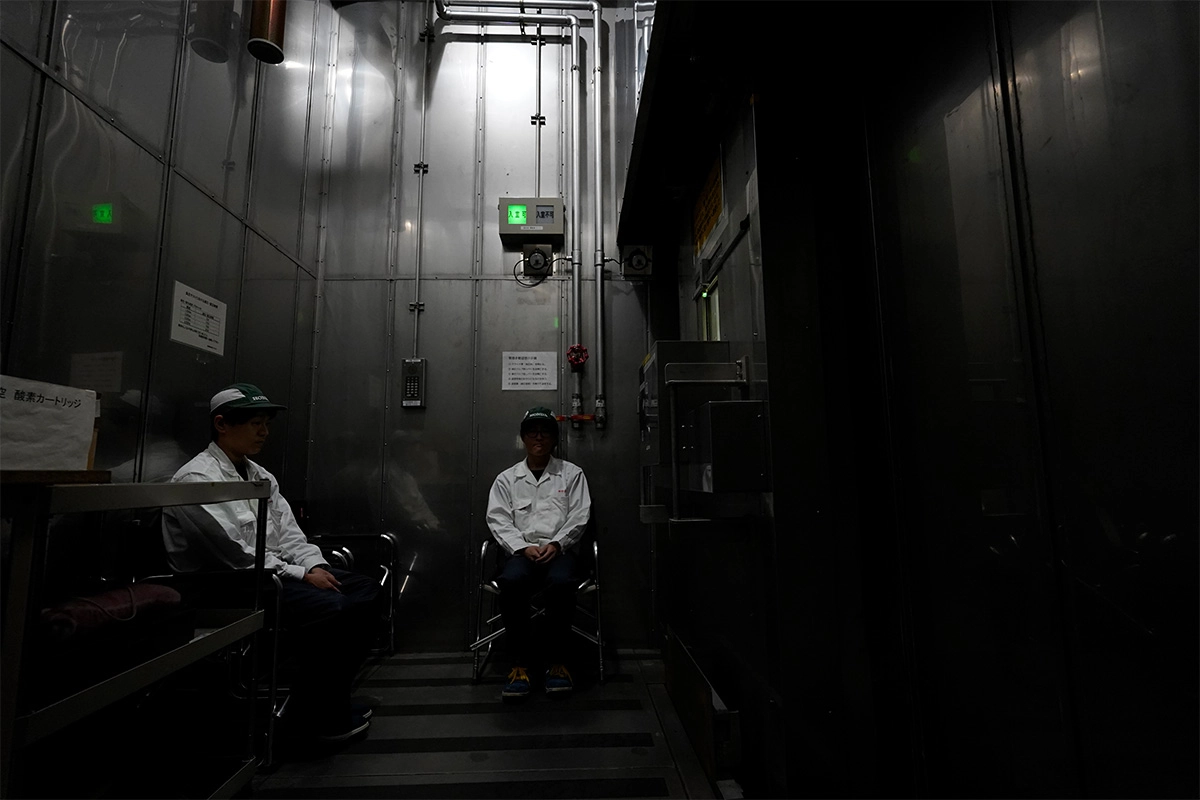
Pressure Gauge
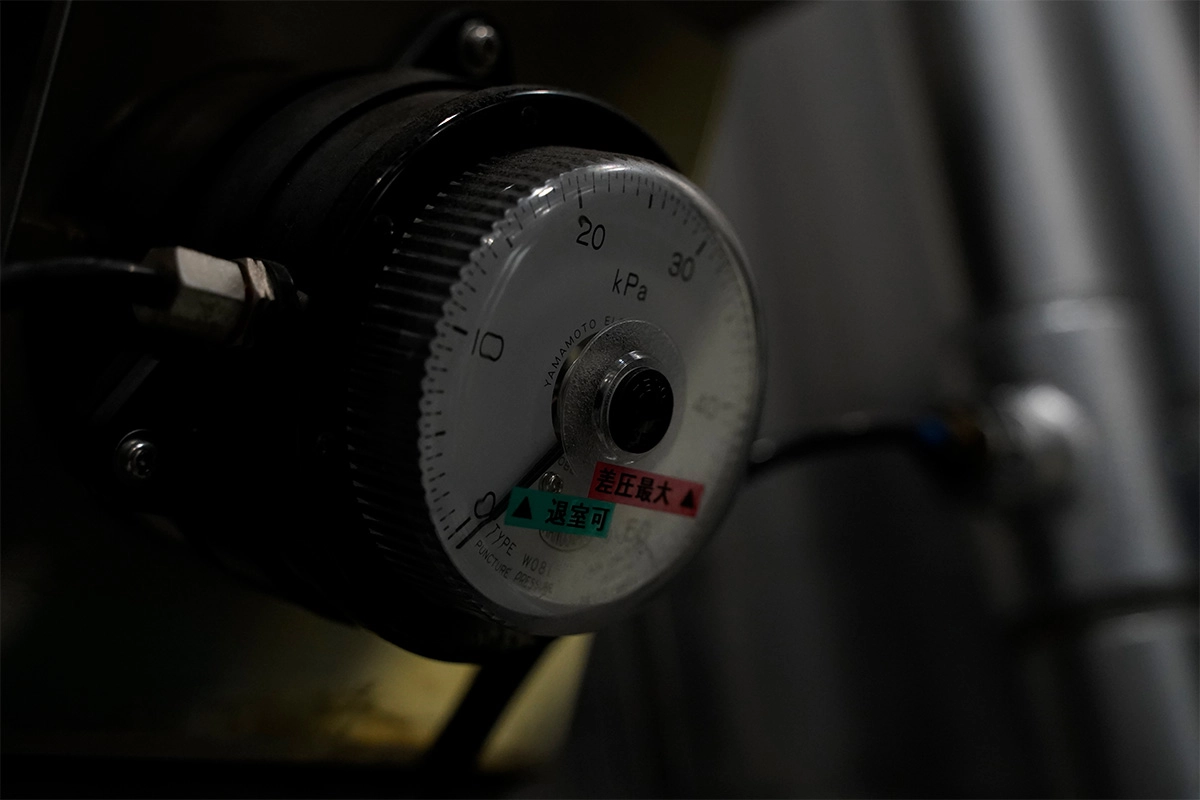
Control Room
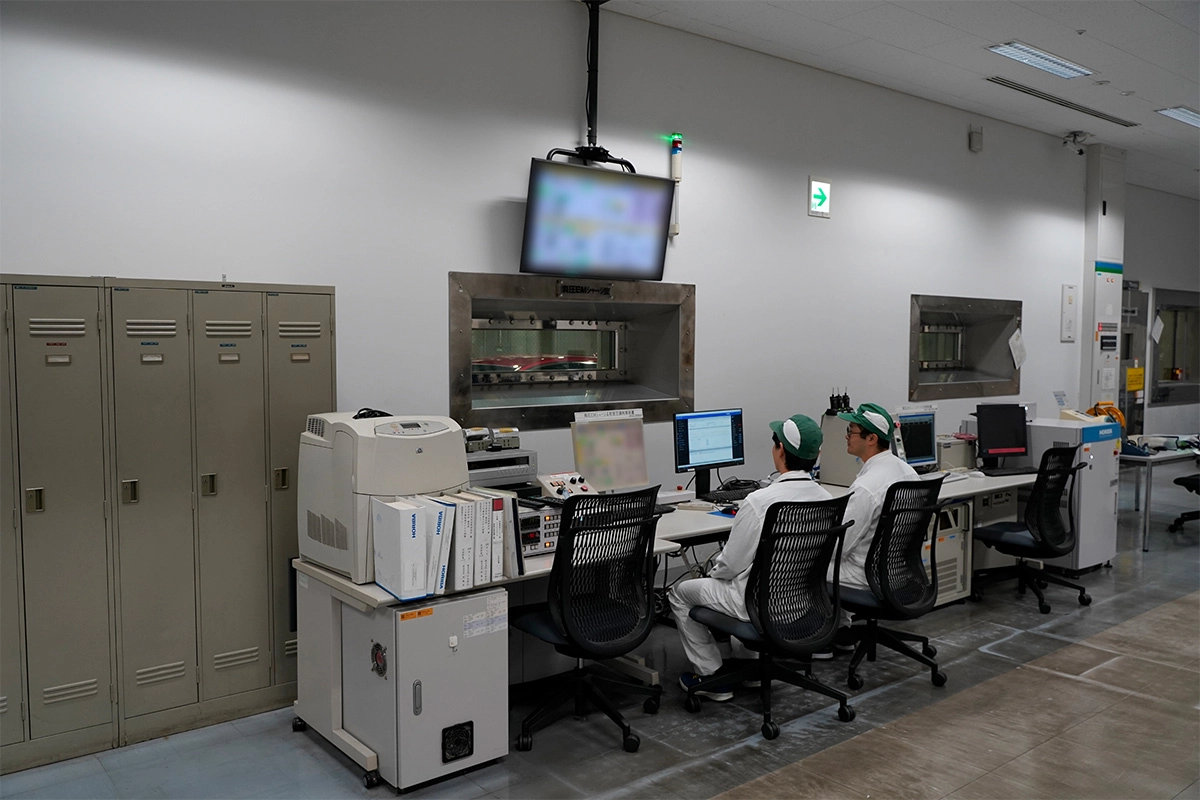

INDEX
Honda’s R&D Facilities
- Chapter 1 Honda’s R&D Facilities: Manufacturing Starts Here
- Chapter 2 Tochigi Proving Ground: The Road Decides the Product
- Chapter 3 Takasu Proving Ground: The Road Refines the Product
- Chapter 4 Full-Scale Wind Tunnel: Mastering the Wind with the Air as Our Ally
- Chapter 5 Bench Test Facilities: Forging the Core of Mobility
- Chapter 6 Environmental Testing Facilities (1): Fine-Tuning Honda Products in Extreme Environments
- Chapter 7 Environmental Test Facility (2): Tailoring Honda Products in Extreme Environments
- Chapter 8 3D Metal Printing: Speedy Creation of Innovative Shapes
- Chapter 9 Omni-Directional Collision Test Facility: Real-World Certification for Everything
- Chapter 10 XR Verification Facility: Virtual Reality Changing the Development Process
- Chapter 11 Driving Simulator: Fusing the Virtual and Physical Worlds for Automated Driving
TechnologyHonda’s R&D FacilitiesEnvironmental Testing Facilities (1): Fine-Tuning Honda Products in Extreme Environments