Honda’s R&D Facilities Chapter 5
Bench Test Facilities: Refining the Core of Vehicle Performance
Honda’s R&D Facilities Chapter 5
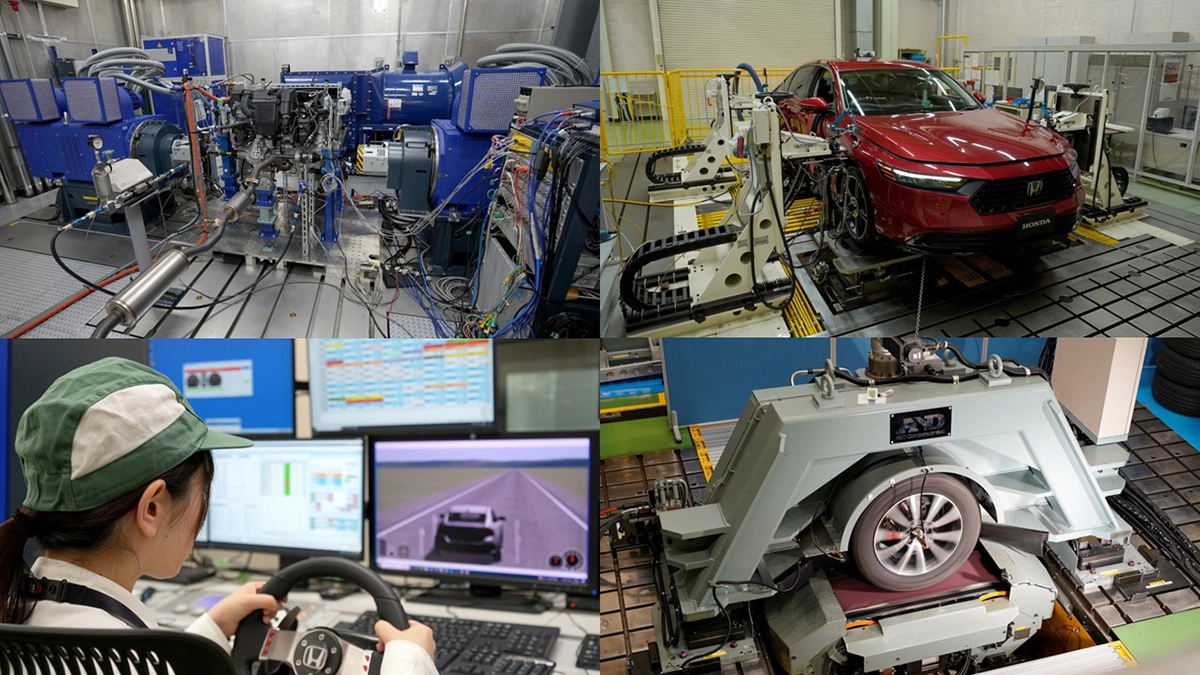
Understanding the Essentials of Vehicle Performance Through Bench Test Facilities
In order to develop vehicles efficiently, it is important to understand the characteristics of the parts and systems that make up the car. This is because the components and its characteristics influence each other, and it makes it difficult to identify the points for improvement or find the solutions to issues. Hybrid systems consist of parts such as engines, motors, and inverters, while suspensions are made up of tires, dampers, coil springs, and other parts.
Bench test facilities evaluate the characteristics of these parts and systems. They quantify the characteristics of individual parts and systems, feeding the result back into the design process. The design team uses the numerical data obtained from benches and testers to run simulations to achieve target performance. And evaluate actual vehicle performance again, ultimately evaluating the results in actual vehicles.
When the properties of parts and systems are quantified at high resolution, simulation accuracy improves, revise work will be reduced, and the target will be achieved efficiently. While actual road tests are affected by external disturbances such as weather and temperature, bench and tester facilities enable repeated measurements under controlled conditions. This makes it possible to deliver better products to the customer quickly with reasonable prices. Honda's cars are refined through the fundamental measurements and setting using the bench test facilities introduced below.
Powertrain (Hybrid System) Test Bench
Honda's e:HEV hybrid system consists of a traction motor, a generator motor, an engine, a Power Control Unit (PCU), and a battery pack. The powertrain test bench is where the traction motor, the generator motor, the engine, and the PCU are extracted and mounted on a test measurement apparatus. This bench conducts measurements not only in steady-state, but also in transient conditions. Additional sensors are installed on the bench-mounted units to measure part conditions in detail. Engines undergo detailed measurements on dedicated engine benches, while motors are tested on dedicated motor benches, with the information obtained from each complementing the other in development.
The representative driving modes of the e:HEV include EV drive mode, which drives the traction motor using only power stored in the battery; Hybrid drive mode, which drives the traction motor using power generated by the engine combined with power from the battery; and Engine drive mode, which directly transmits engine power to the tires through an engaged clutch.
The e:HEV operates primarily on motor power in daily use, switching to Engine mode for situations such as high-speed cruising where engine efficiency exceeds motor efficiency. A key characteristic is how it selectively uses different modes depending on the situation. One role of the powertrain test bench is to verify which mode is most efficient in which situation. The behavior confirmed through measurements is fed back into the design process.
When transitioning from EV mode to Hybrid mode, or from Hybrid mode to Engine mode, the aim is to achieve smooth transitions that feel natural to occupants. Another role of this bench is to evaluate various control settings to determine how to achieve smooth transitions that enable satisfying driving performance.

Control Room
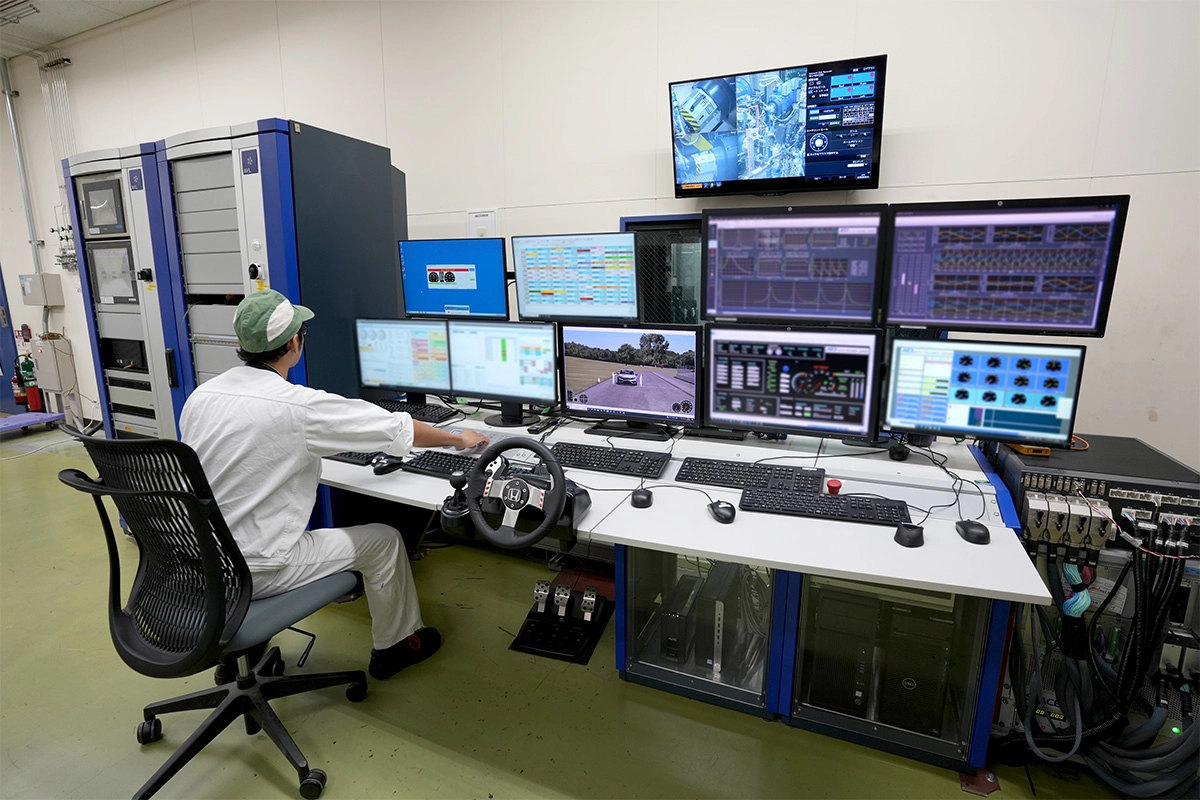
Powertrain Test Bench
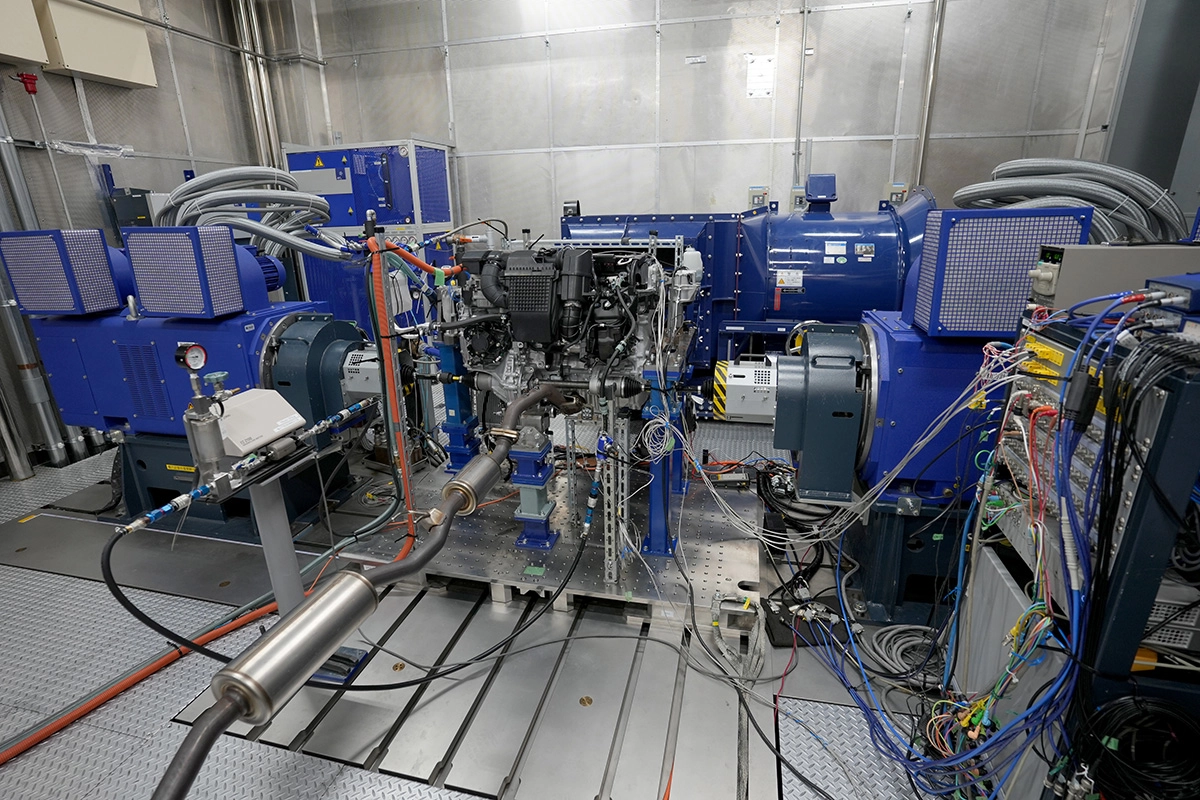
Powertrain Test Bench
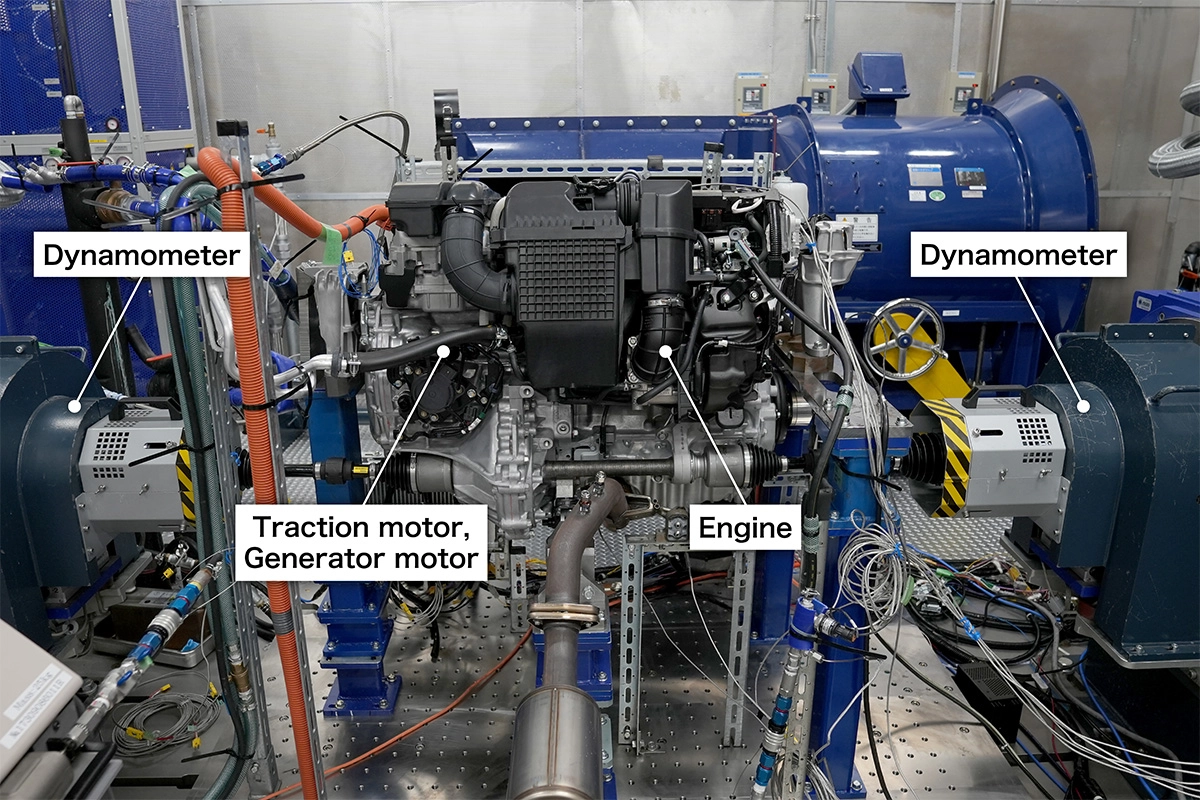
System Configuration Diagram
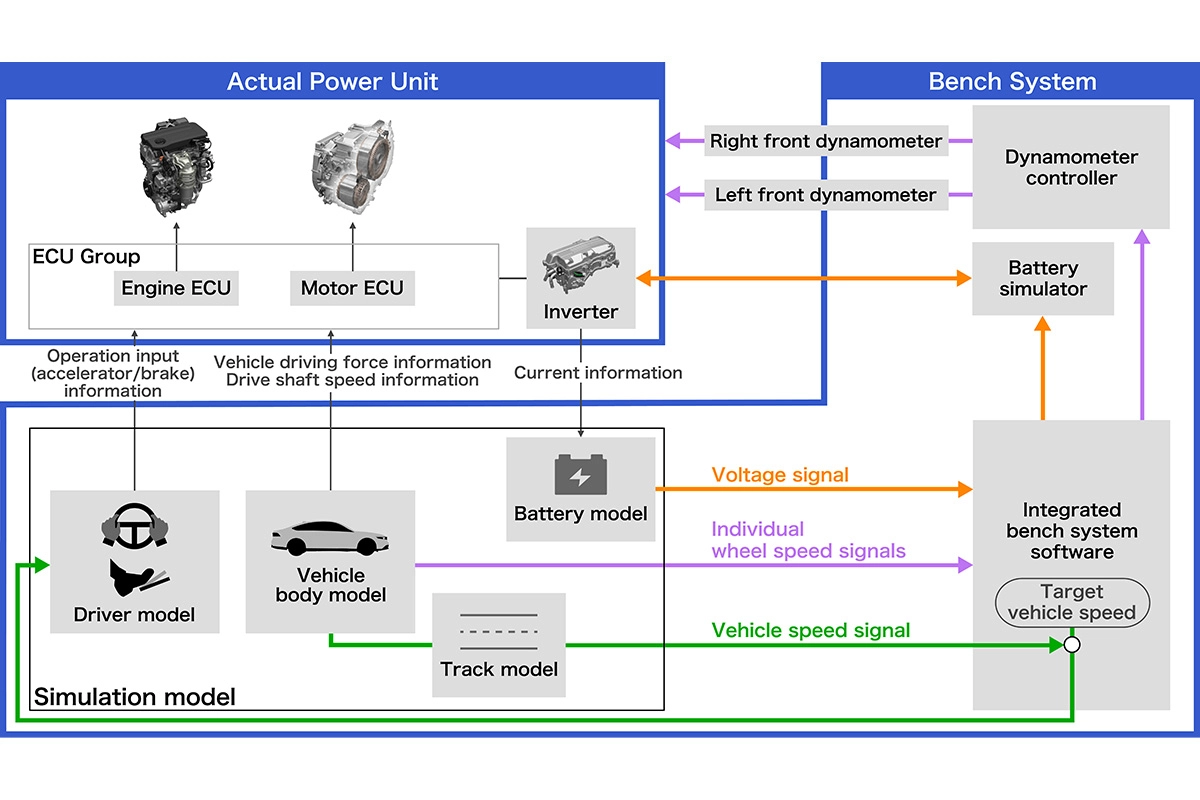
Control Room
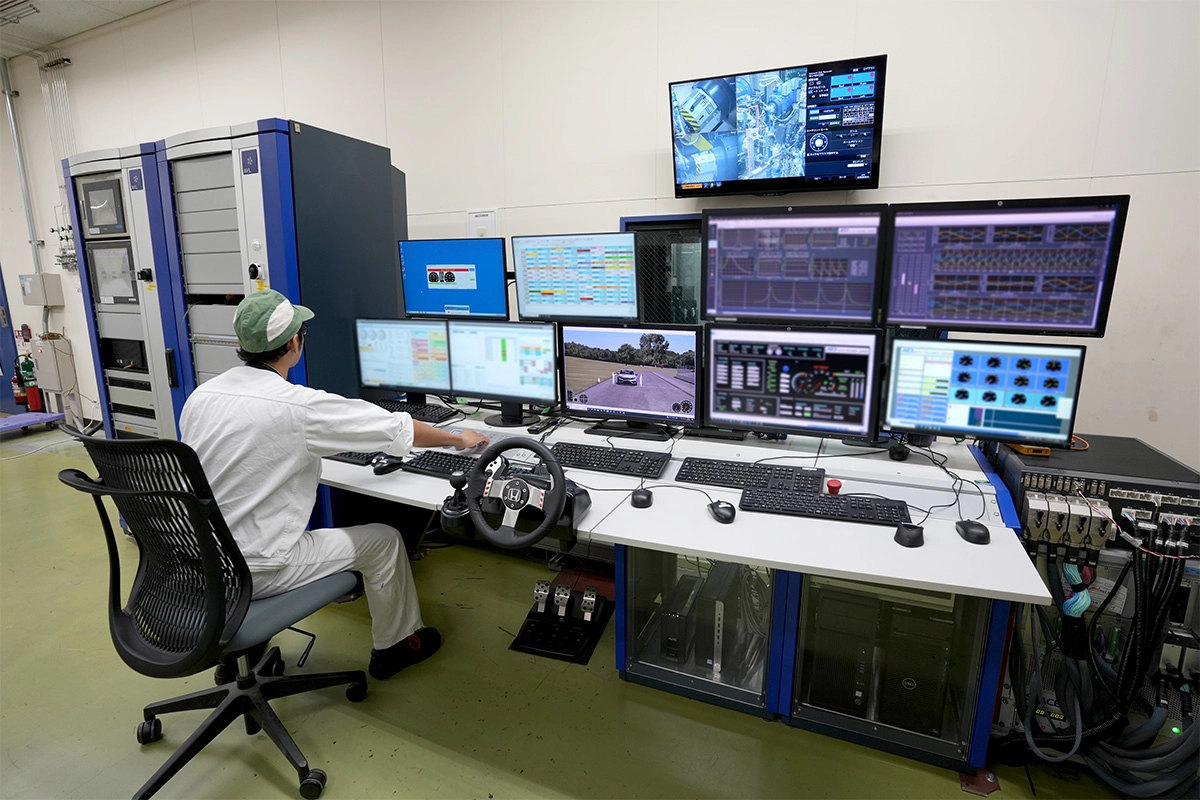
Powertrain Test Bench
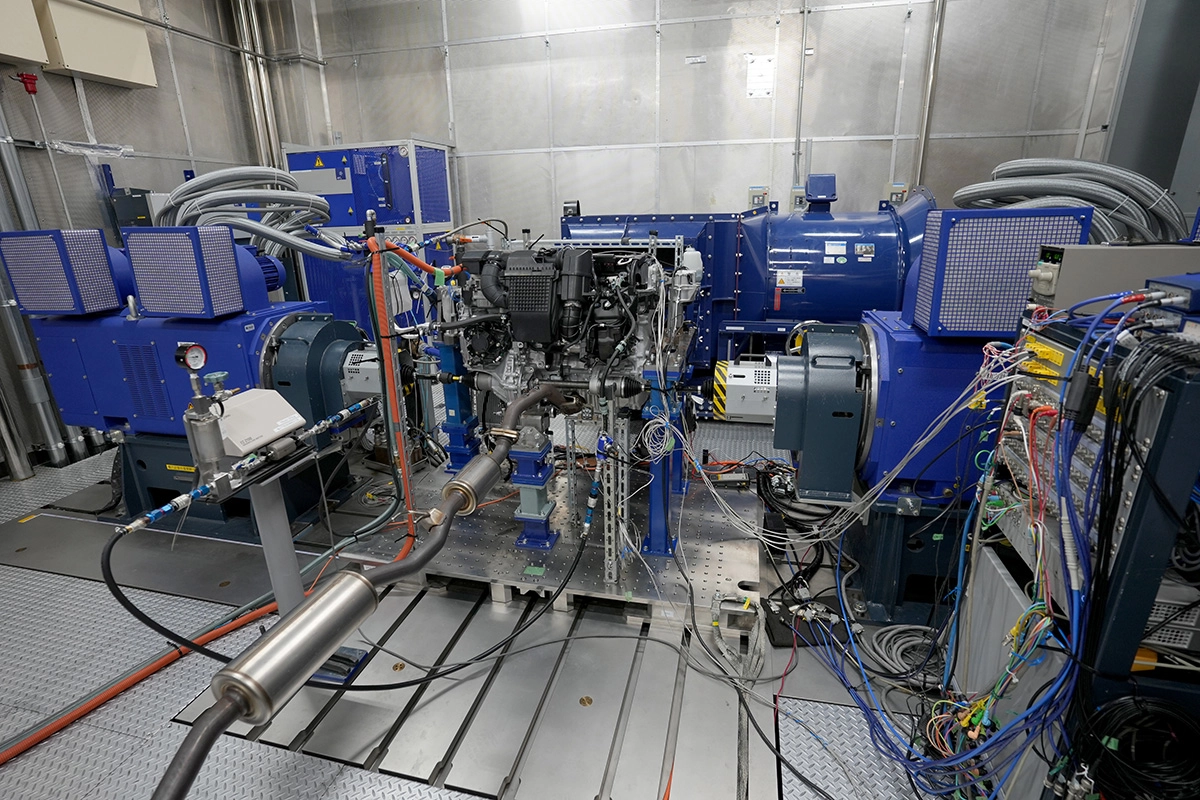
Powertrain Test Bench
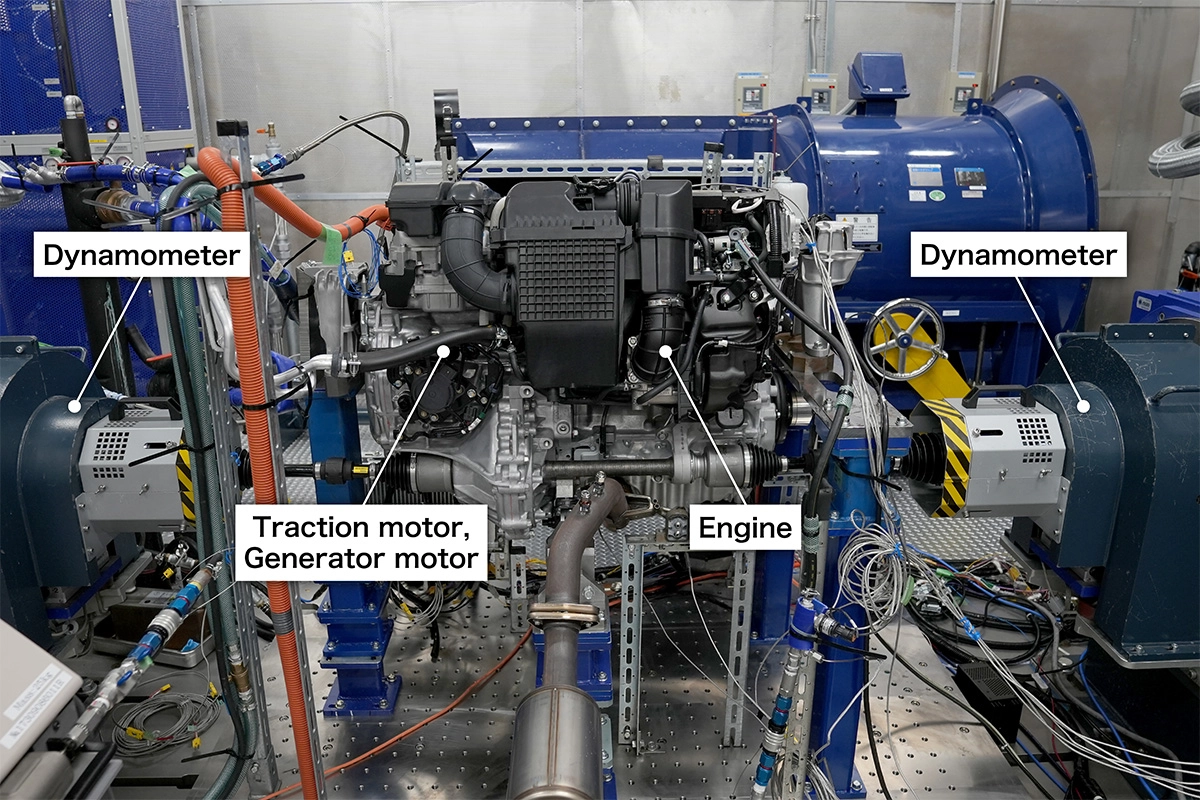
System Configuration Diagram
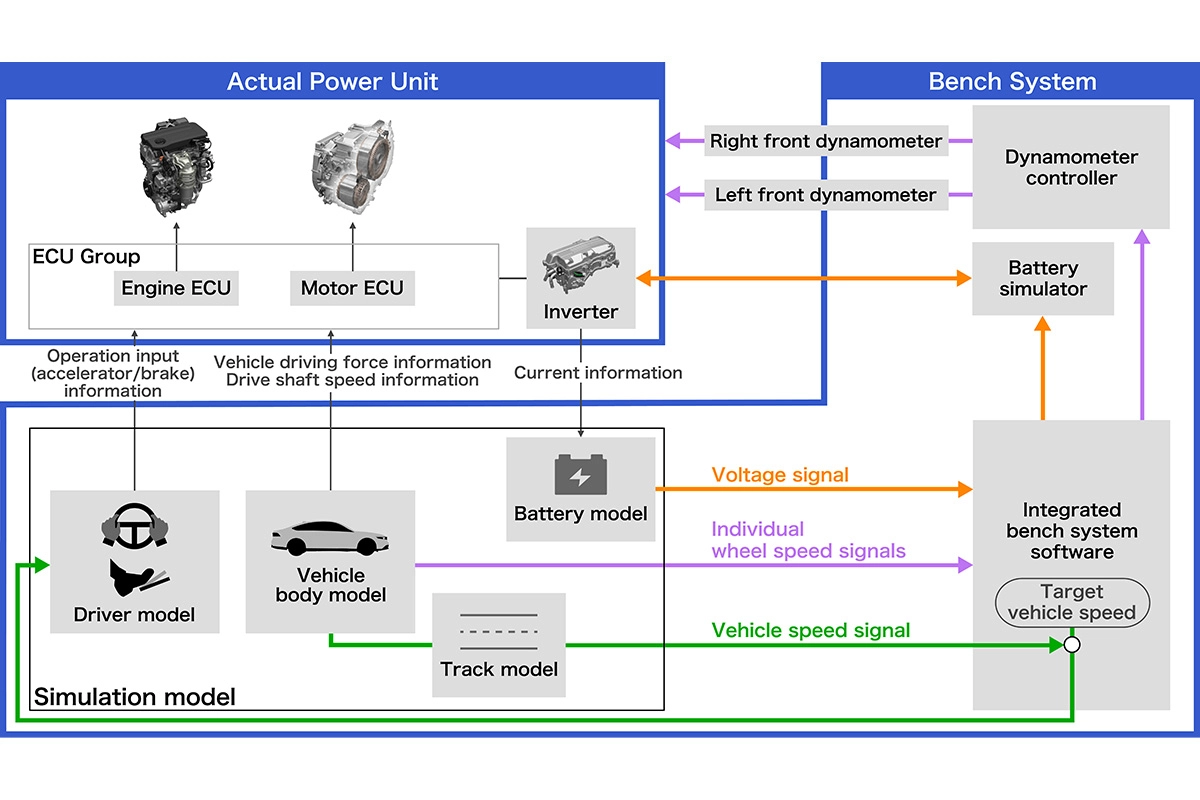
Control Room
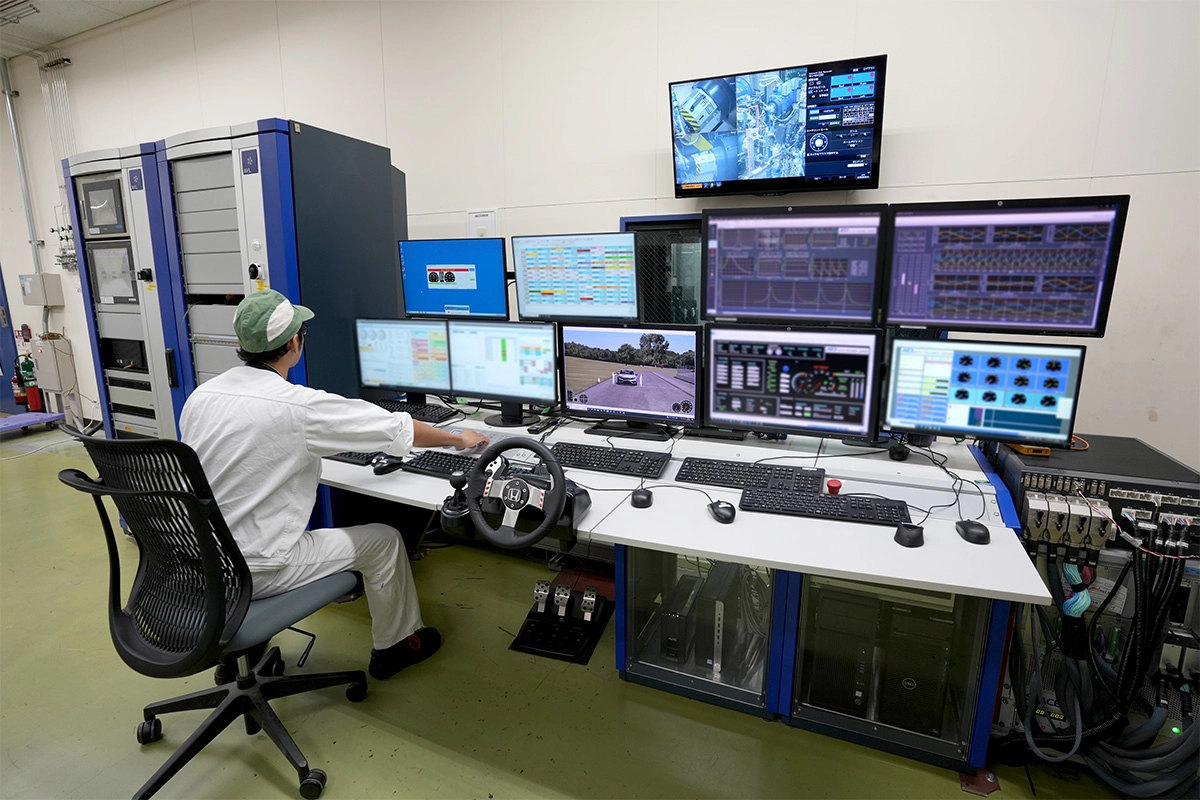

Compared to actual road tests, bench testing offers the advantage of enabling repeated evaluations in a shorter time. Additionally, data from actual road tests tends to vary due to external disturbances such as air temperature and wind strength. On a test bench, measurements are not affected by wind or weather, and temperature can be controlled within specific ranges. Another advantage of bench testing is the ability to take measurements while maintaining constant temperatures or controlling them to targeted levels.
While it is possible to bring the battery pack from an actual vehicle into the bench room for testing, equipment substitution is used for greater testing efficiency. A direct current power supply is located in a separate room, and a battery simulator reproduces battery pack behavior. It can simulate conditions such as a fully charged state or a low charge state. It can also simulate deteriorated battery conditions, enabling evaluation under various conditions.
Another characteristic of the powertrain test bench is its capability for unattended testing. The facilities enable 24-hour unattended testing. However, there are also cases where people gather to listen carefully. An accelerator pedal is placed in the control room. Normally, a dial on the control panel serves as the accelerator. During development of the Linear Shift Control applied to certain e:HEV models, an actual pedal was intentionally installed and used to align conditions as realistically as possible when checking the gradual changes in engine speed synchronized with vehicle speed acceleration during pedal operation. This embodies Honda's Three Reality Principle of making decisions based on going to the actual place, knowing the actual situation, and being realistic.
Evaluation Through Human Operation
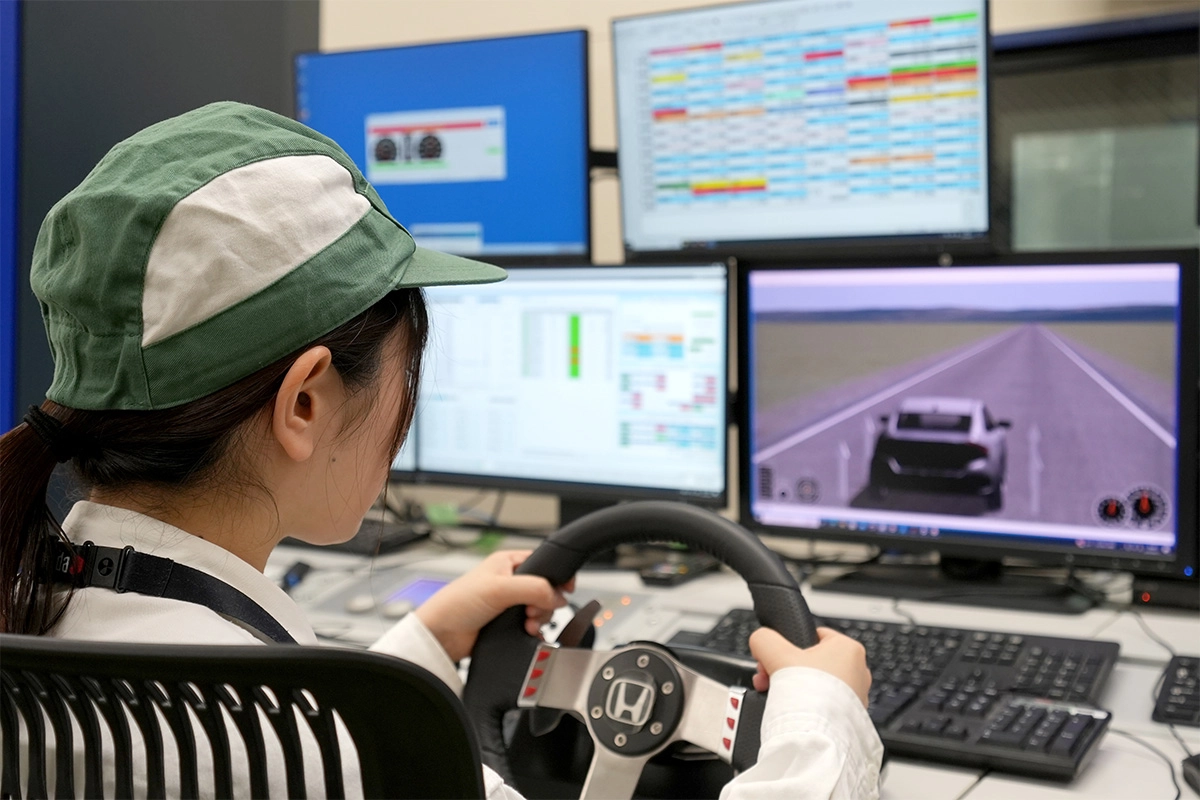
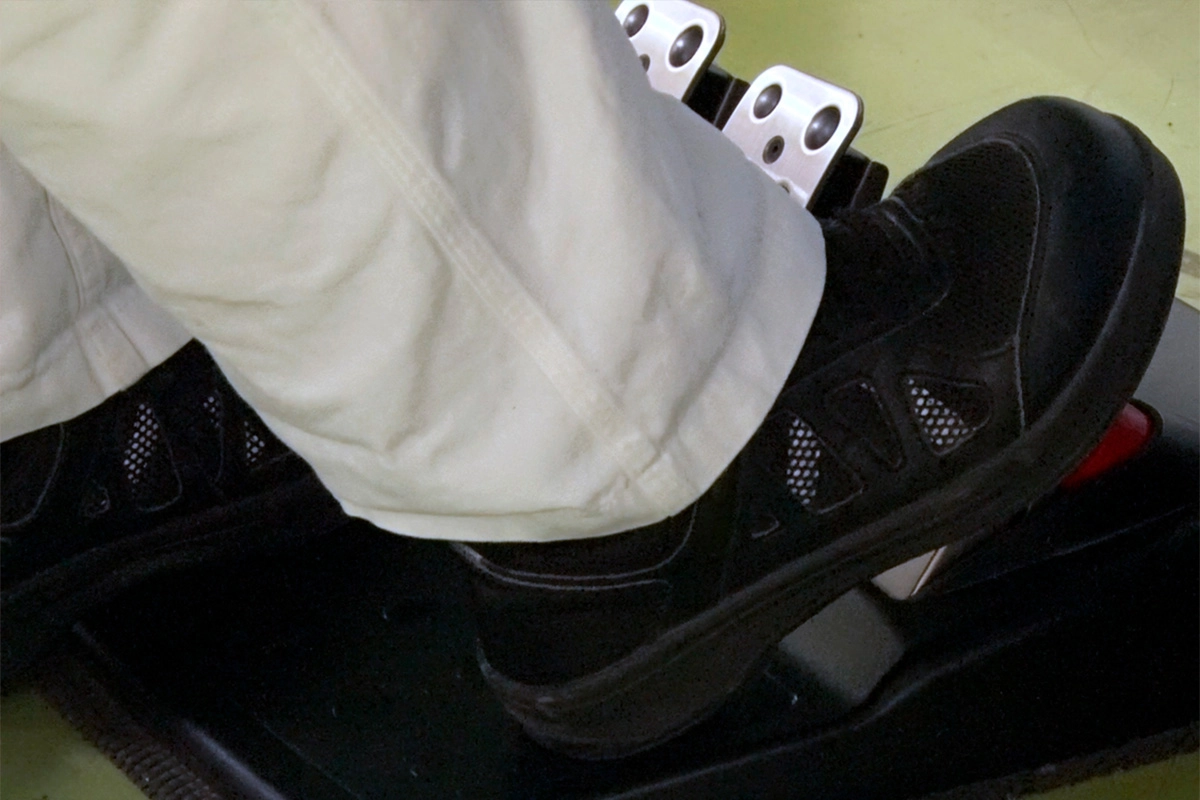
Motor Performance Bench
The motor performance bench is a testing apparatus used to collect basic data on motors installed in hybrid systems and battery electric vehicles (BEVs). Data obtained from motor performance bench measurements influences motor specifications that affect performance and efficiency when installed in the final vehicle. These specifications include factors such as magnet placement in rotors made of laminated electromagnetic steel sheets, the number of electromagnetic steel sheets to use, and the distance between rotor and stator, which ultimately affect output/torque and electricity efficiency.
A case called a test box is installed in the bench room, and it contains the motor being tested. Parts of the case allow inspection of the interior to confirm proper rotor rotation and check the flow of oil cooling the motor. Sensors measure the temperature of components including the rotor, magnets embedded in the rotor, stator windings, and oil. This is both to ensure that measurements do not exceed heat resistance limits and to collect basic data. Testing involves repeated measurements during driving and recovery to calculate output, torque, and efficiency.
The inverter that converts direct current from the battery to alternating current sometimes uses a simulator, but in other cases uses the actual vehicle-mounted unit. This enables verification of phenomena that occur when combining the inverter and motor, such as noise conditions and their effects.
Another advantage of the motor bench is the ability to install sensors that cannot be mounted on actual vehicles due to space constraints. An additional benefit of bench testing is the ability to conduct tests under various conditions beyond the operational range used in actual vehicles, such as freely setting rotation speeds and varying temperatures. This enables not only reproduction of actual driving conditions, but also determination of operational limits. The bench is also sometimes used to analyze the causes of phenomena that create discomfort in driving, turning, and stopping operations detected during actual vehicle testing.
Motor efficiency is typically at 90% or above, which is significantly higher than engine thermal efficiency, which is around 40%. With losses accounting for only about 10%, small differences can greatly affect efficiency. Therefore, the ability to accurately measure minute phenomena is critical on the motor performance bench. Torque can be measured accurately down to less than 1 Nm, and the equipment is set up to precisely capture microscopic events on the time axis necessary for understanding electrical responses. This high-resolution measurement enables acceleration and deceleration that faithfully responds to driver intent.
After collecting basic motor data on the motor performance bench, development progresses to later stage testing that includes cooling tests, durability tests, and system tests. Honda is able to ensure high performance and durability in its motors by internalizing technologies, meticulously collecting basic data, and ultimately guaranteeing quality through human verification. Observing waveforms on the oscilloscope can reveal insights that lead to phenomenon analysis. Equipment serves as a means to improve efficiency, and Honda's dedication to equipment stems from the desire for accurate evaluation. However, development is carried out with the awareness that responsibility ultimately lies with people, and measurements are conducted with an unwavering commitment to quality.

Oscilloscope

Motor Performance Bench
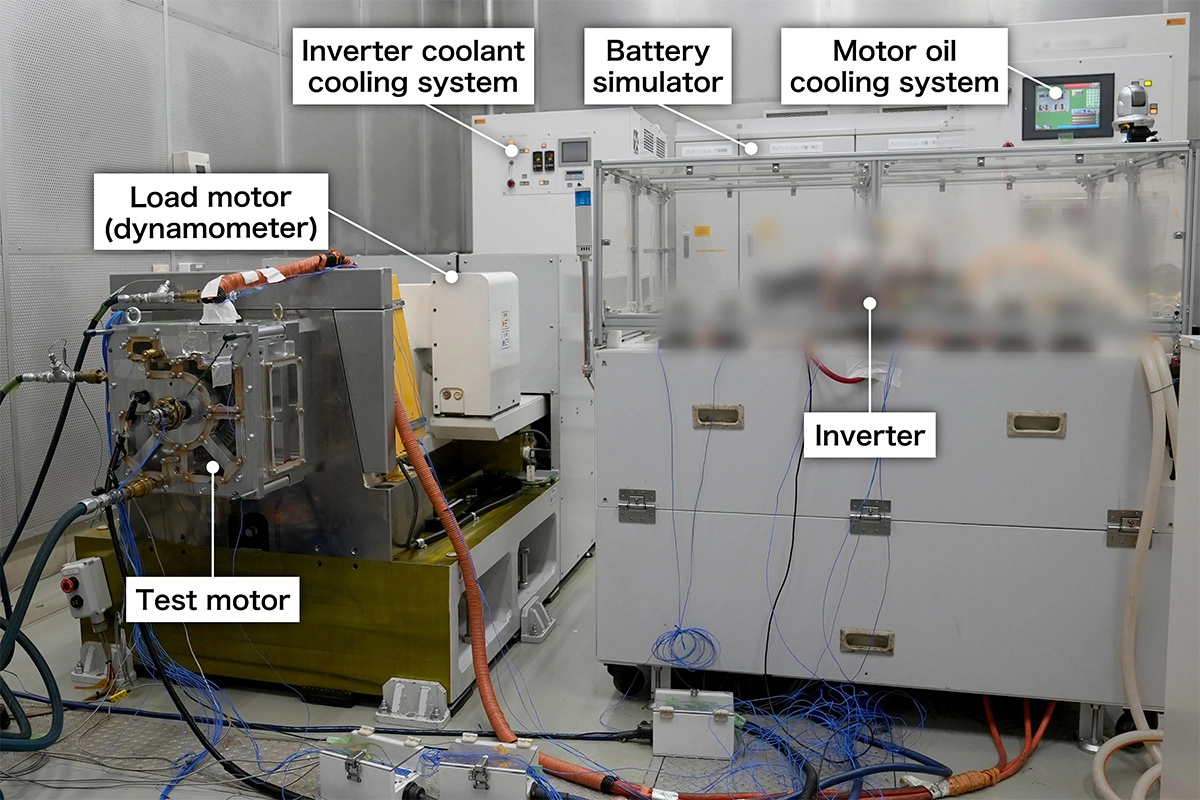
Motor Performance Bench
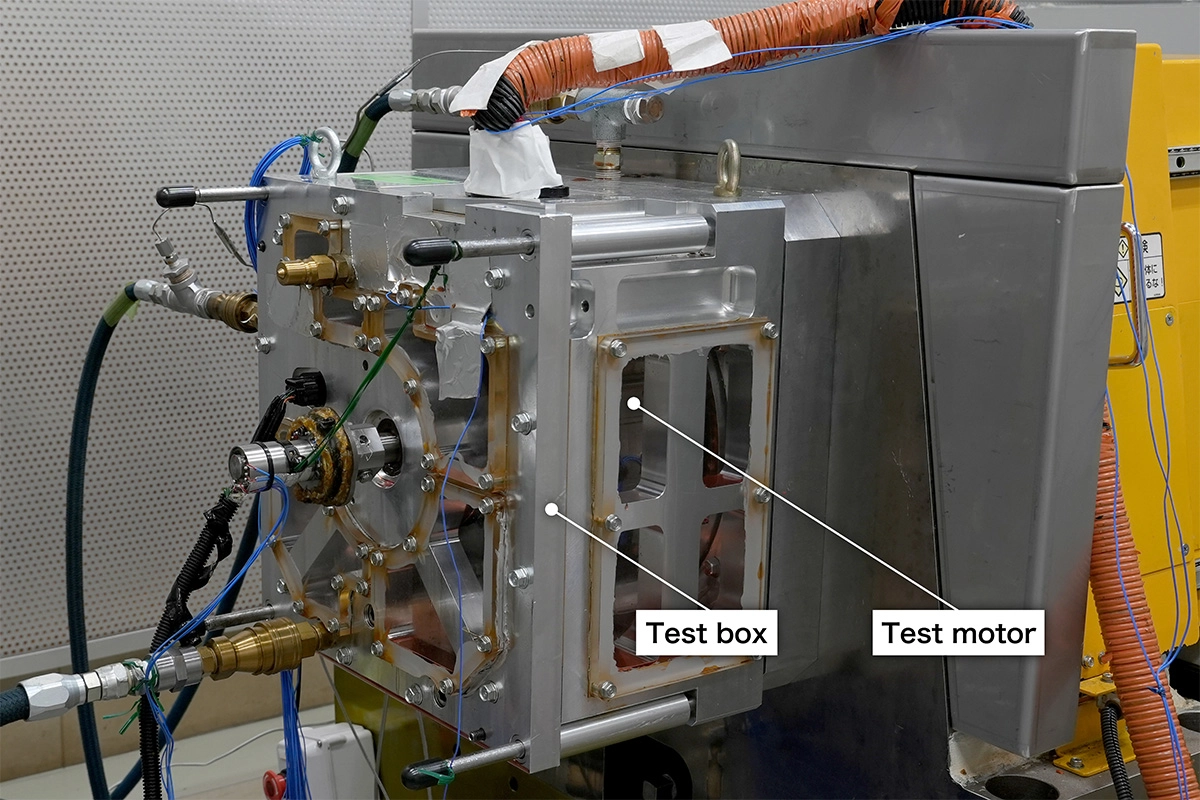
System Configuration Diagram
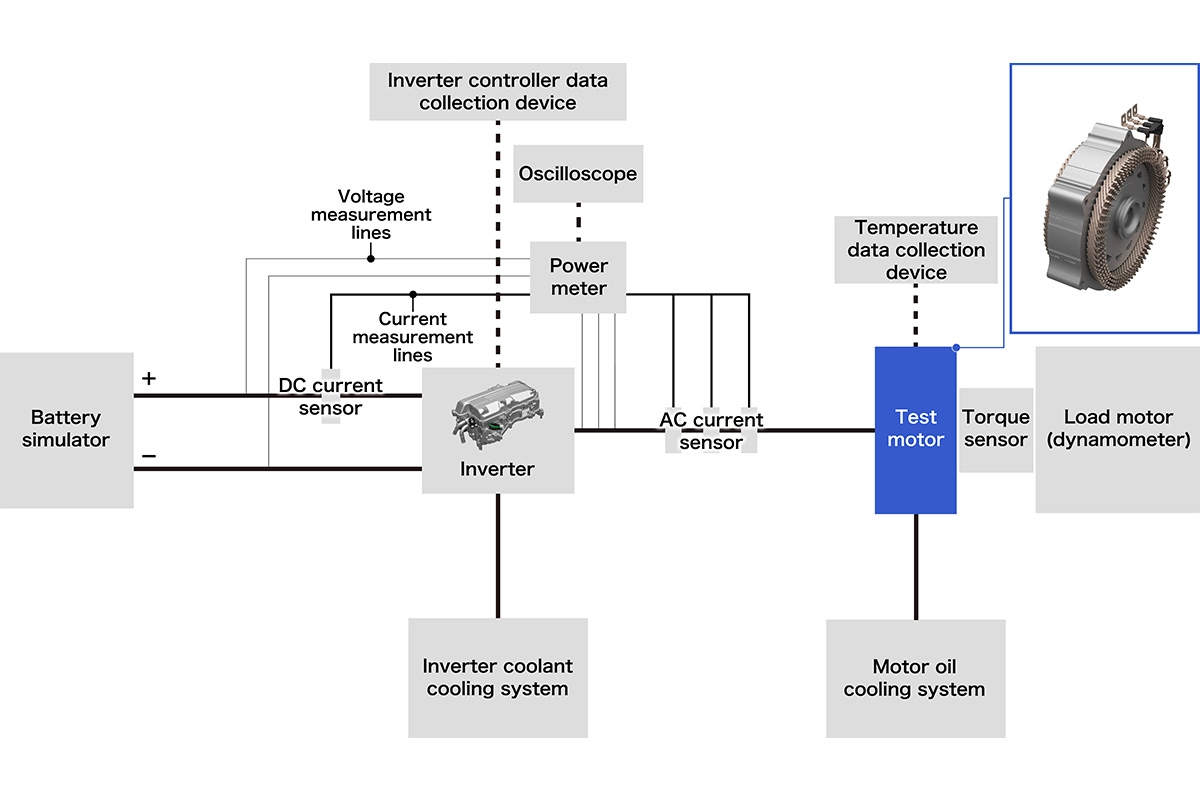
Control Room
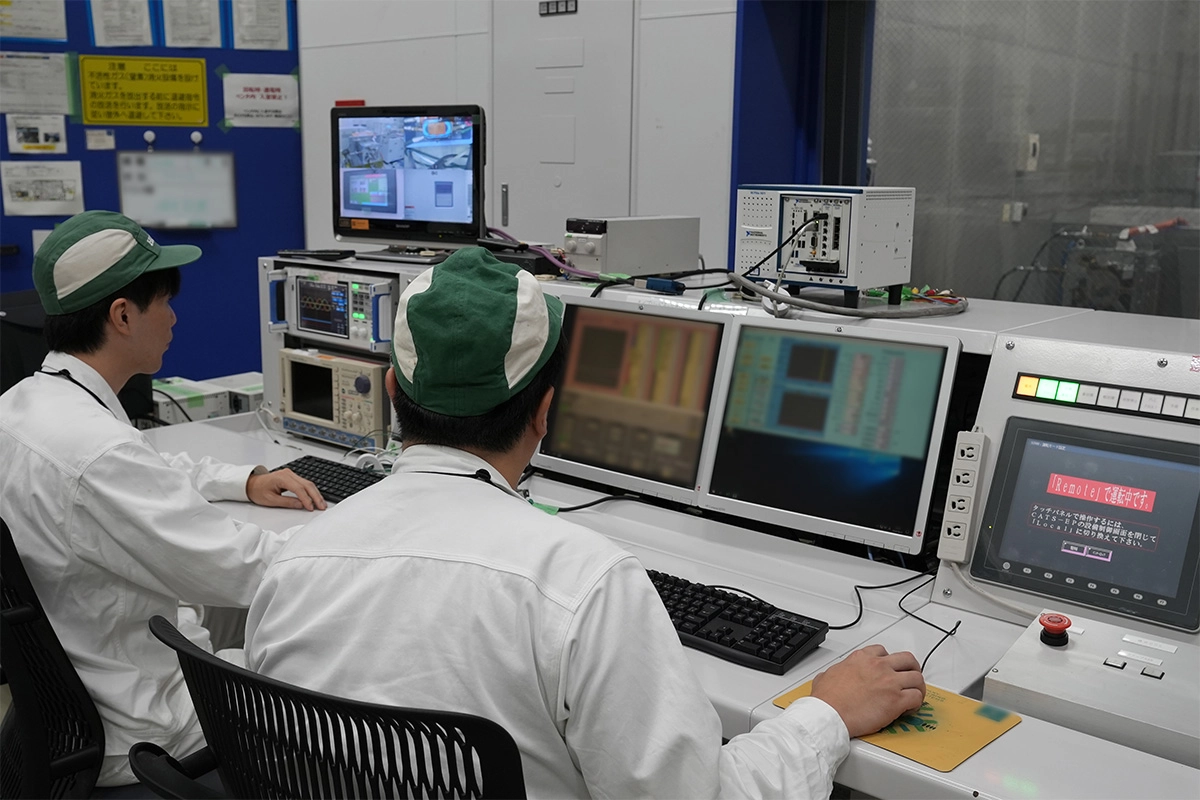
Oscilloscope

Motor Performance Bench
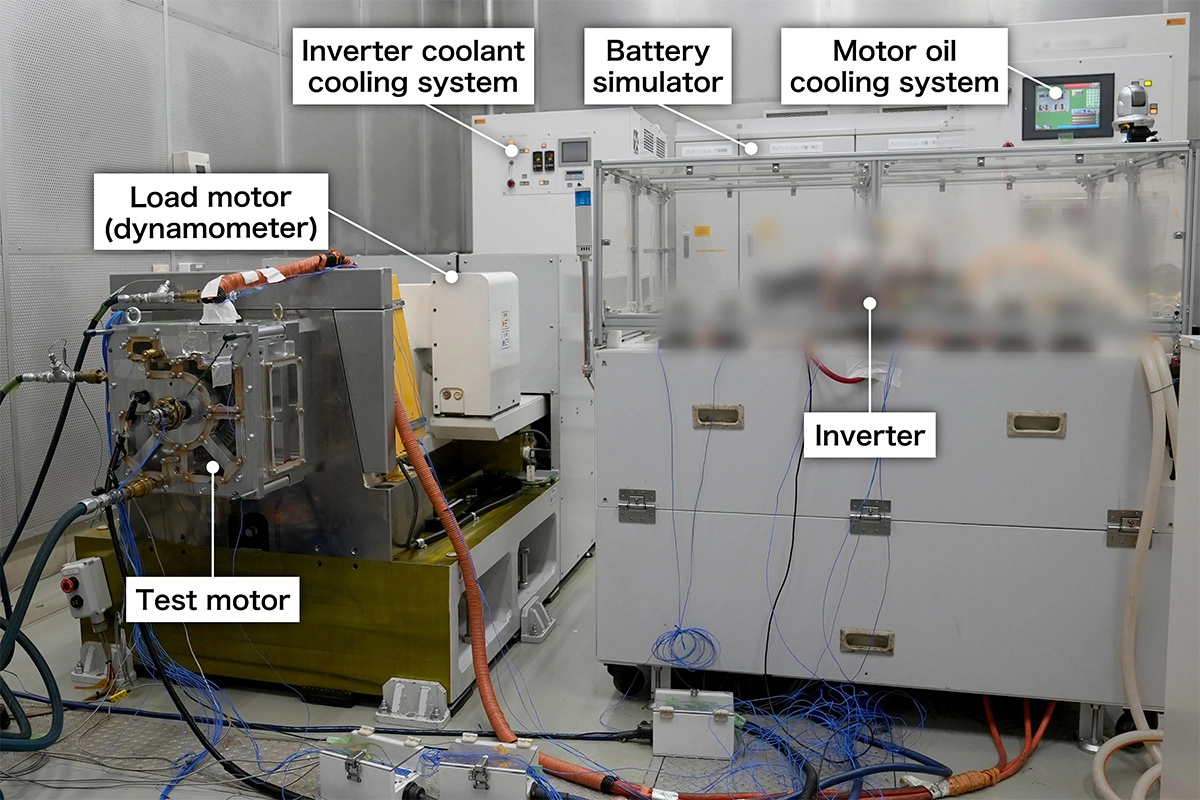
Motor Performance Bench
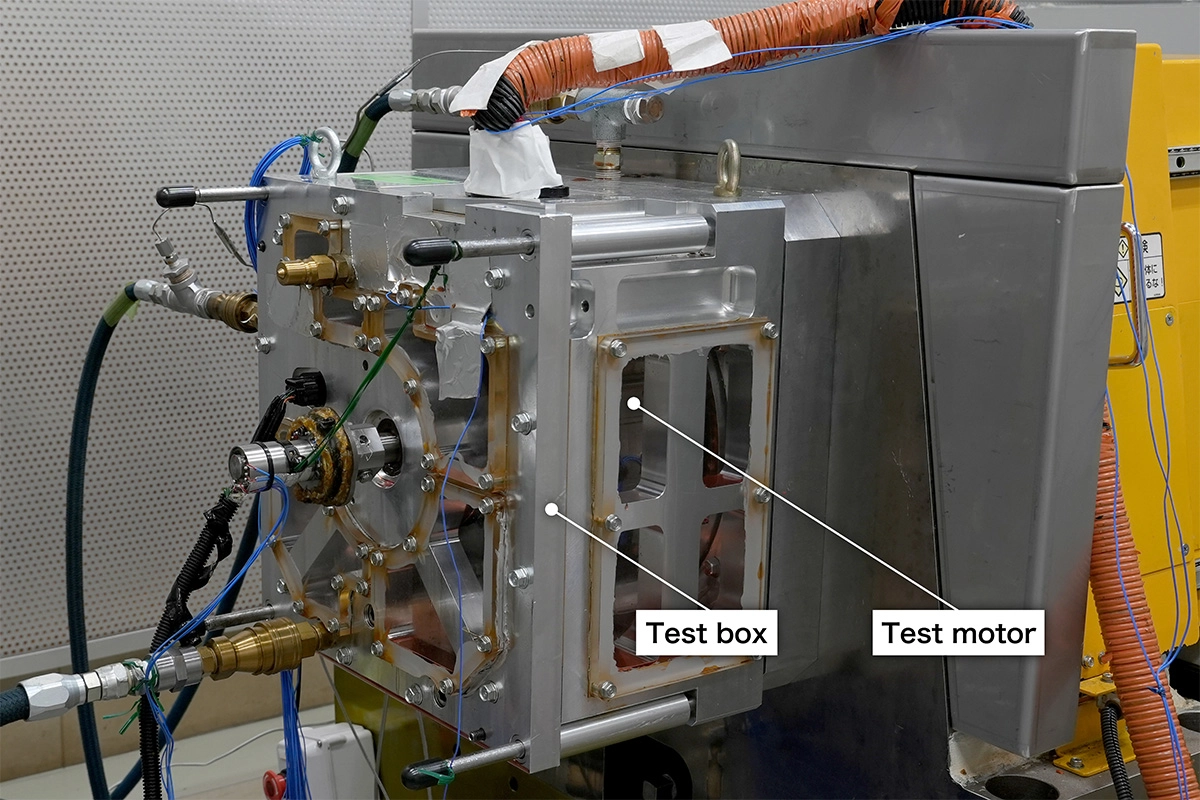
System Configuration Diagram
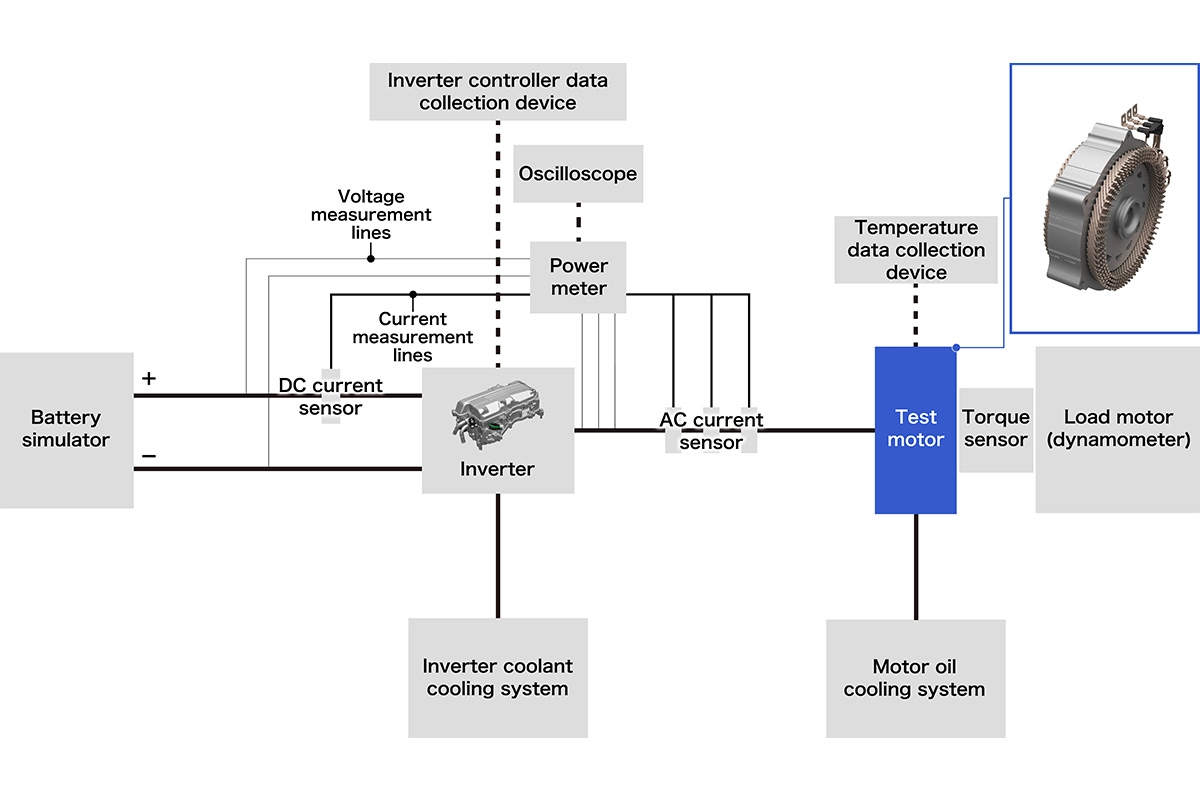
Control Room
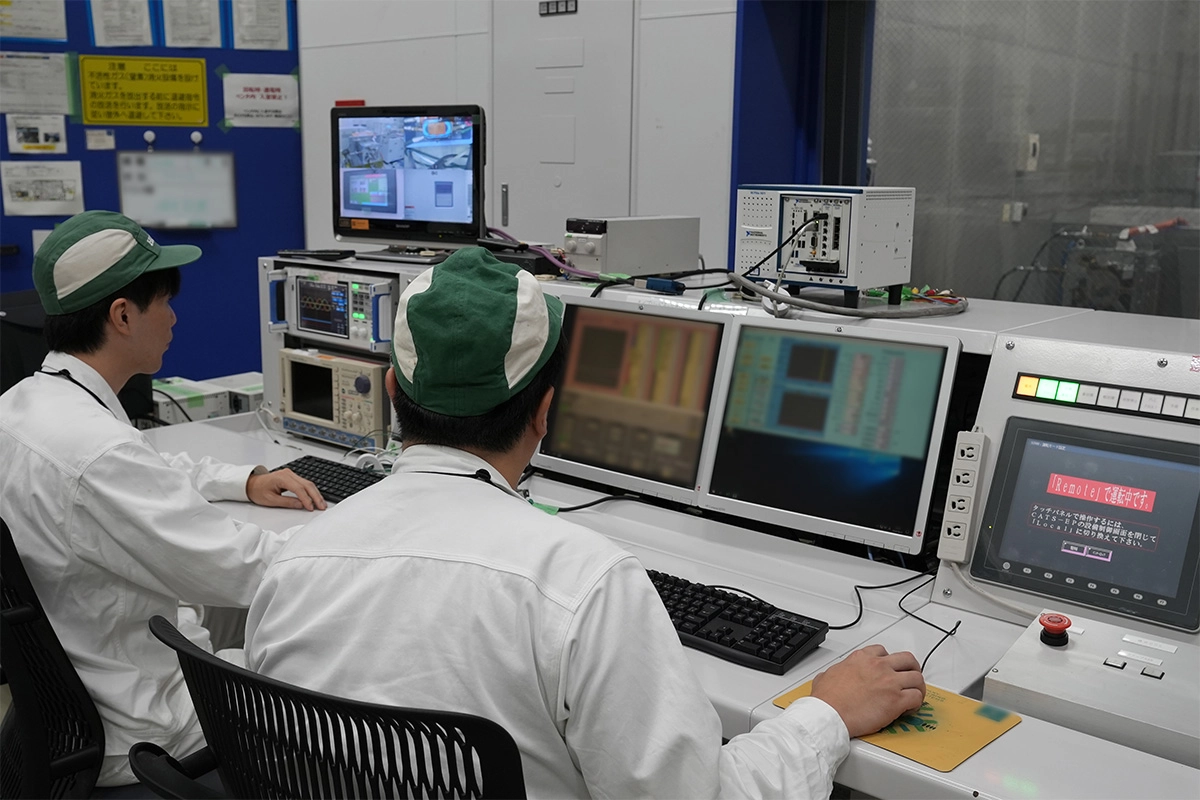
Oscilloscope


Very-low-speed Rotation Motor Bench
A motor consists of a rotating rotor and a fixed stator on the outside. When current flows, torque increases when the rotor's permanent magnets approach the stator's electromagnets, and decreases when they move apart. Torque pulsation (amplitude similar to a pulse) occurs based on factors such as the combination of the number and arrangement of poles in the rotor's permanent magnets and the number of poles in the stator's electromagnets. This pulsation is called torque ripple.
In typical electric motors, torque ripple occurs within a range of 10-15% of maximum torque. For example, when stopping on a steep uphill grade, the rotor and stator phases might stop at a position corresponding to a torque valley. This bench is used to evaluate whether sufficient torque can be generated to prevent anxiety when starting from such situations. The basic data obtained from measurements is also fed back to the design team to develop ideas for reducing torque ripple amplitude below that of conventional motors.
Torque ripple can also cause motor noise. Rather than suppressing the resulting sound through the vehicle body, the responsible department conducts testing with pride, aiming to eliminate the noise at its source. By precisely capturing data that can only be detected when rotating motors at very-low speeds, they contribute to the development of motors with a superior level of quietness.
When motors rotate at high speeds, torque becomes averaged, so torque ripple should be measured at very-low speeds. This is because the lower the rotation speed, the more precisely torque fluctuations can be captured. The very-low speed rotation motor bench makes this possible. This bench can rotate motors at very-low speeds at or below 1 rpm and can also perform measurements while stopping at each phase according to the number of poles.
The basic function of the very-low speed rotation motor bench is to verify whether torque ripple matches design specifications. As is true for all Honda bench testing facilities, the engineers involved in test operations do not simply conduct tests. They verify actual situations with actual products at the test site while keeping the final product in mind, and exchange information with the design team as equals from their position as engineers who understand real-world conditions.
Test motor
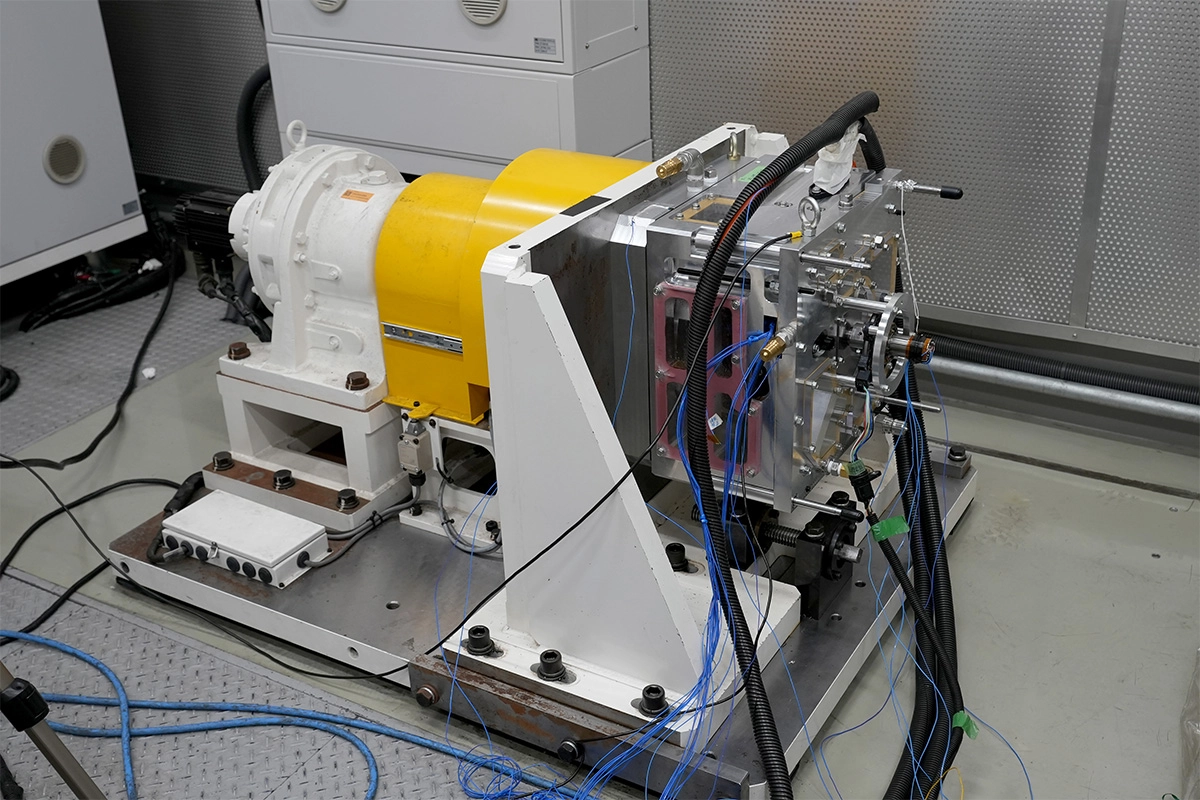
Control Room
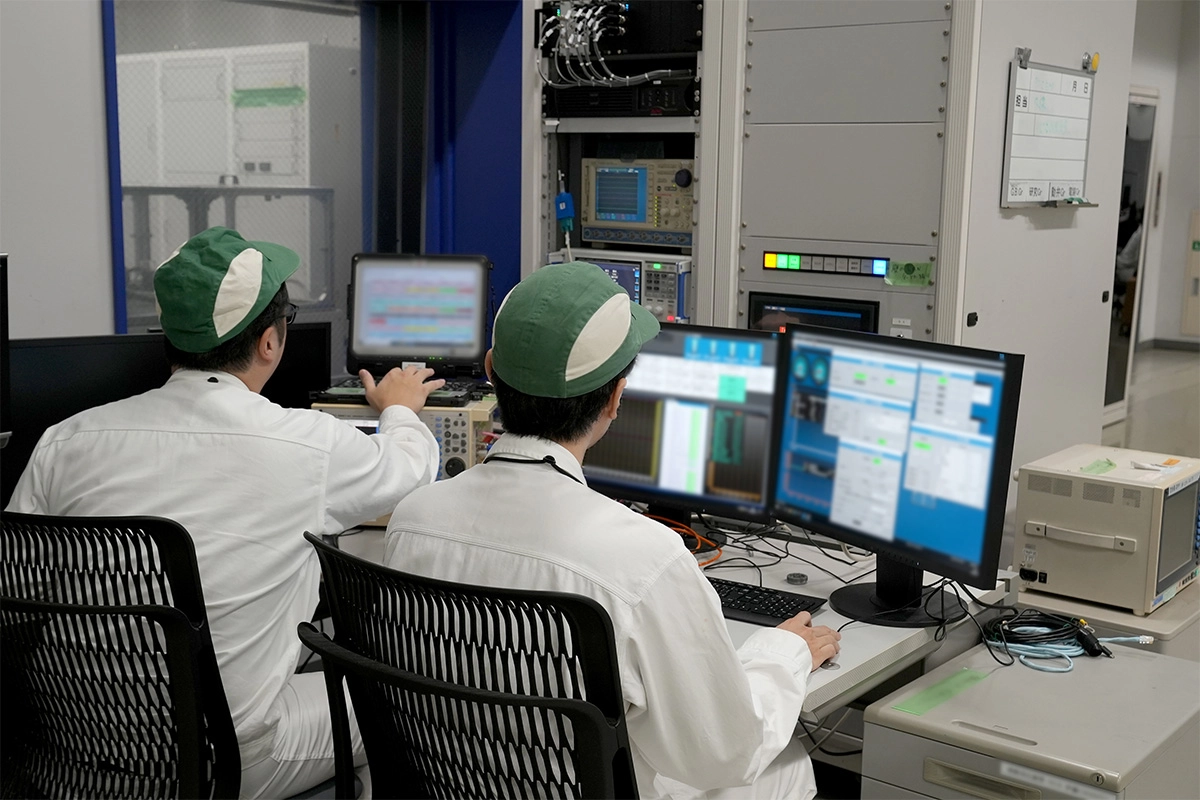
Drive Unit/Standalone Motor NV Bench
The drive unit NV bench measures the noise and vibration of drive units, which consist of either a generator motor and traction motor combined with a power transmission mechanism and housed in a case for hybrid systems, or a traction motor combined with a reduction mechanism and housed in a case for BEVs. This bench's role is to contribute to development by identifying and efficiently reducing sources of noise and vibration emitted due to assembly as a drive unit rather than as individual parts.
The standalone motor NV bench, on the other hand, measures the vibration and noise of individual motors. Together with measurement data from the drive unit NV bench, this advances development toward targeted interior sound levels. Both benches conduct measurements in anechoic chambers surrounded by sound-absorbing materials to prevent echo. On the drive unit NV bench, the drive unit is enclosed in an acoustic measurement jig, with multiple microphones placed at predetermined positions from the test object to measure the sound pressure emitted by the unit. The evaluation uses sound power level as an index to measure total acoustic energy.
NV is classified and measured as low and high frequencies. Low frequencies can be described as structure-borne sound, which is sound transmitted through vibrations of solid objects such as metal cases that then vibrate the air. This is measured by attaching G-sensors to the test object. High frequencies, on the other hand, refer to airborne sound transmitted through air vibration and are measured using acoustic measurement jigs.
Once a target is set for interior sound levels below a certain number of decibels in the completed vehicle, numerical targets for structure-borne and airborne sound are calculated from this. The drive unit NV bench measures structure-borne and airborne sound to investigate the correlation (verification and analysis of relationships) between design and actual hardware. Even when targets appear difficult to achieve, countermeasures such as sound absorption or insulation are not simply imposed upon the vehicle body side. Measurements are conducted based on the belief that we must make improvements ourselves and that dedication leads to better products, utilizing knowledge accumulated through years of experience.
Anechoic Chamber
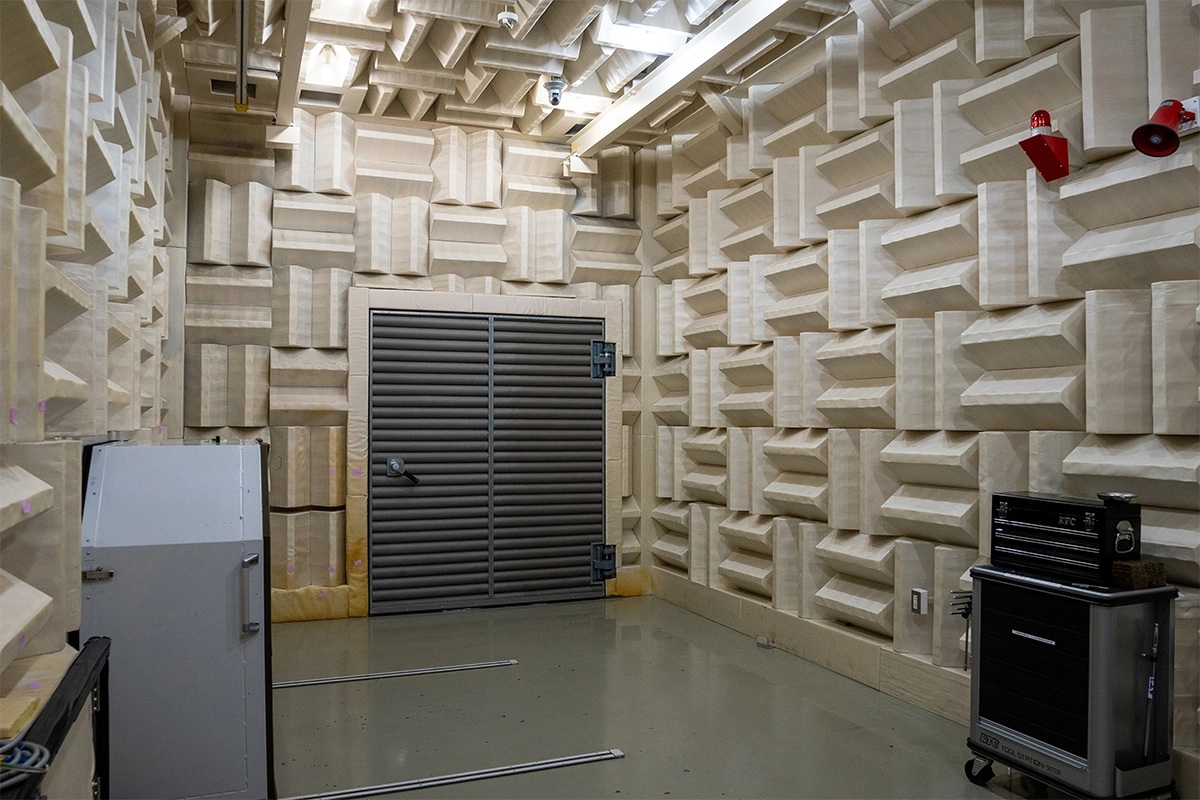
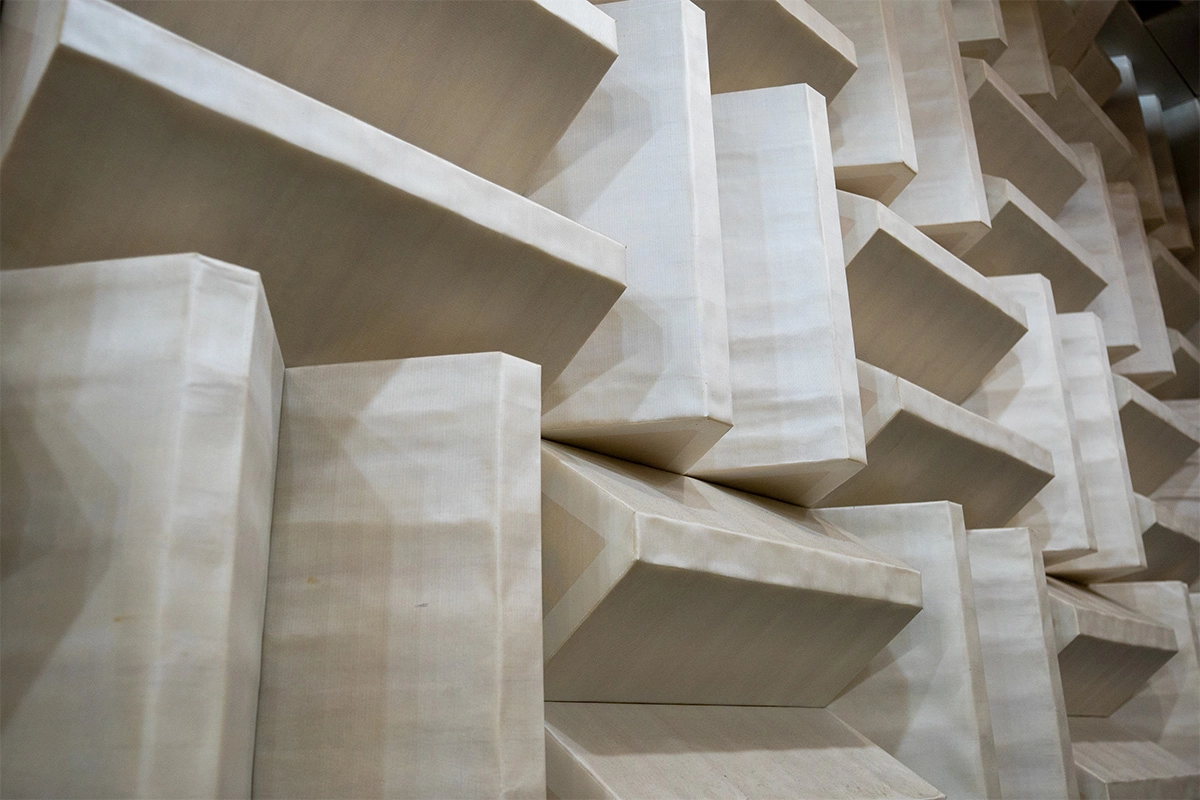
Single-cylinder Performance Engine Bench
The single-cylinder performance engine is an engine that consists of only one cylinder from an actual engine. Combustion specifications are determined using this facility in the initial stage of engine development. Combustion specifications include intake pipe diameter and length, chamber volume, three-dimensional intake port geometry, intake valve diameter and shape, and cam profile, etc. for the intake system, and detail geometry of combustion chamber and piston, compression ratio, the specifications of Injector and spark plug, etc. for in-cylinder. Specifications are determined while considering the functions and interactions between the parts. Data obtained from single-cylinder performance engine bench testing plays a crucial role in determining engine character.
Detailed evaluation of combustion on the single-cylinder performance engine bench enables early and reliable determination of combustion specifications, allowing various function verifications in later development stages to proceed without reworking. The invisible combustion state inside the engine is visualized through minute pressure changes captured by precise pressure measurements, enabling understanding and analysis of combustion conditions. The measurement results are fed back into the engine design, and specification reviews are promoted. As a result, combustion specifications that satisfy target performance can be reliably determined in the early stages of development.
In multi-cylinder engines such as four-cylinder engines, combustion analysis precision decreases due to multiple disturbances affecting combustion, such as variations between cylinders and cylinder interactions. By contrast, a single-cylinder engine enables analysis and verification focused purely on combustion. Additionally, greater engine handling flexibility allows installation of sensors that cannot be mounted on multi-cylinder engines. Using a single cylinder also reduces parts replacement labor and costs, enabling more efficient development.
The equipment literally looks like one cylinder cut out from the actual engine. A large spherical surge tank is installed to prevent the intake pulsation unique to single cylinders. And on the exhaust side, a chamber is installed to prevent the effects of reflected waves. Creating an environment that enables measurements focused purely on combustion.
Furthermore, equipment designed and manufactured to maintain constant intake pressure is installed to eliminate the effects of atmospheric pressure. With increasingly stringent exhaust emission regulations, the requirements for emission reduction under low-temperature conditions are becoming stricter. To address this trend, a low-temperature system for cooling both the coolant and intake air was designed and installed.
In the case of a four-cylinder engine, the first and fourth cylinders and the second and third cylinders are arranged in a 180-degree phase, so the inertia force of the first-order rotation caused by the reciprocating motion of the pistons is balanced throughout the engine. However, single-cylinder engines have no cylinders to cancel out inertial forces, requiring vibration design specific to single-cylinder engines. Therefor traditionally, it has only been used to evaluate fuel efficiency at low speeds, and high speed output has not been evaluated. On the other hand, at HRC Sakura, the development base for motor sports, single-cylinder engines for Fomula1 cars are operated at high speeds of over 10,000 rpm. Drawing inspiration from Sakura's facilities, the single-cylinder engines are updated and achieve high-speed operation. As a result, full-throttle output can be evaluated even on single cylinders.
When certain specifications are changed, related phenomena are affected, changing combustion state quantities. The role of the single-cylinder performance engine bench is to verify combustion specifications that satisfy the target performance, which have been selected mainly using CAE (computer-aided design and analysis), on an actual engine. In addition, changes in combustion state quantities are analyzed from the measured data, which is also used to improve the accuracy of CAE.

Control Room
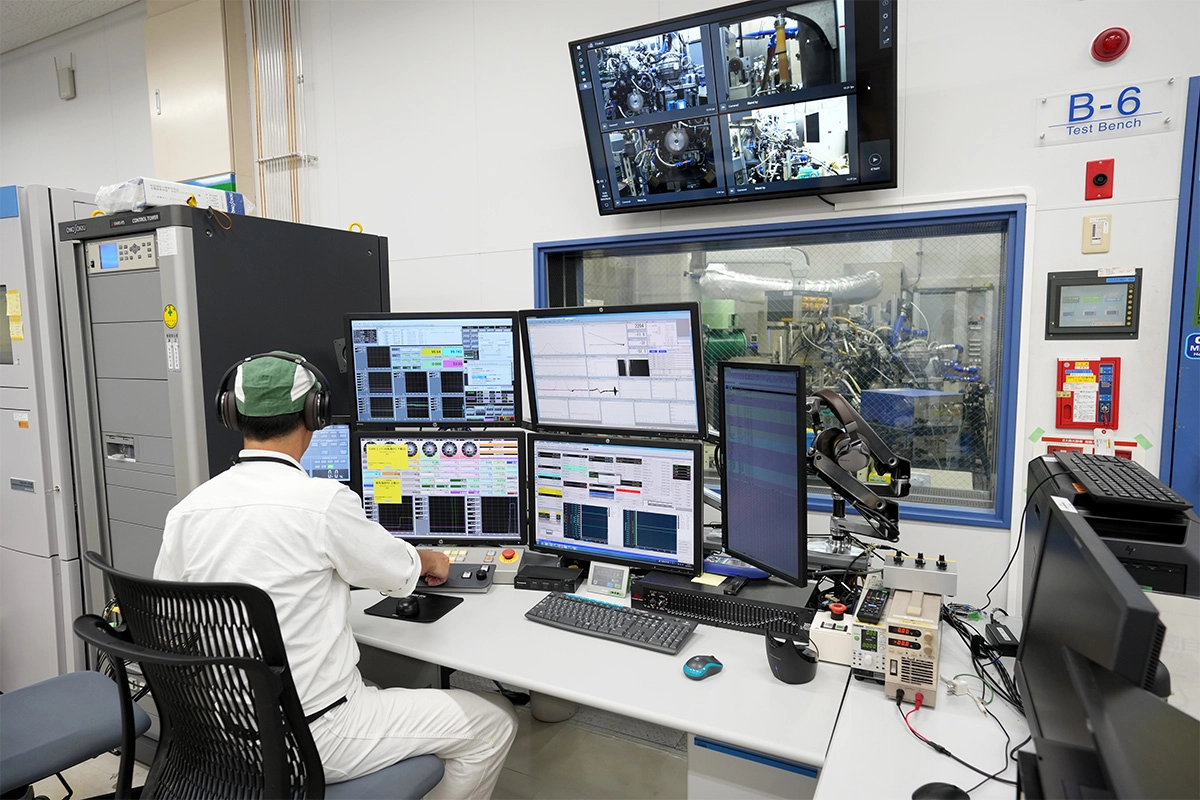
Single-cylinder Performance Engine Bench
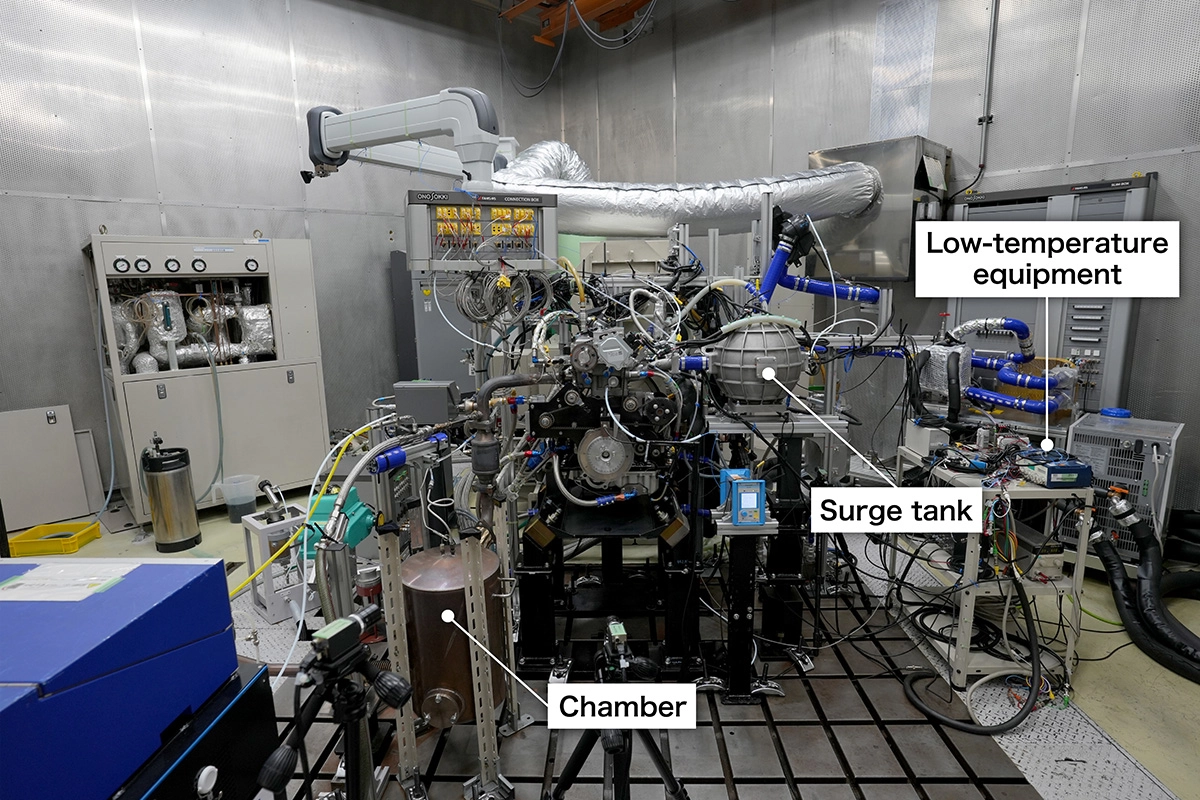
Single-cylinder Performance Engine Bench
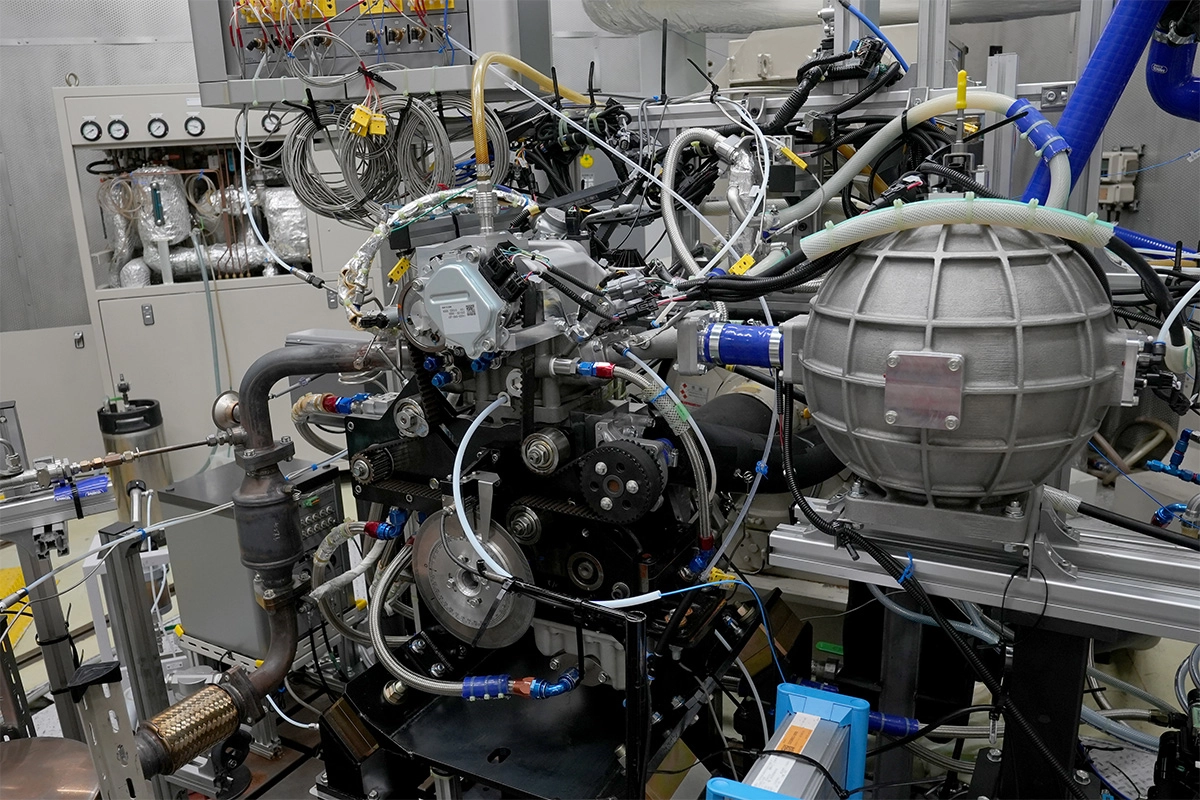
Control Room
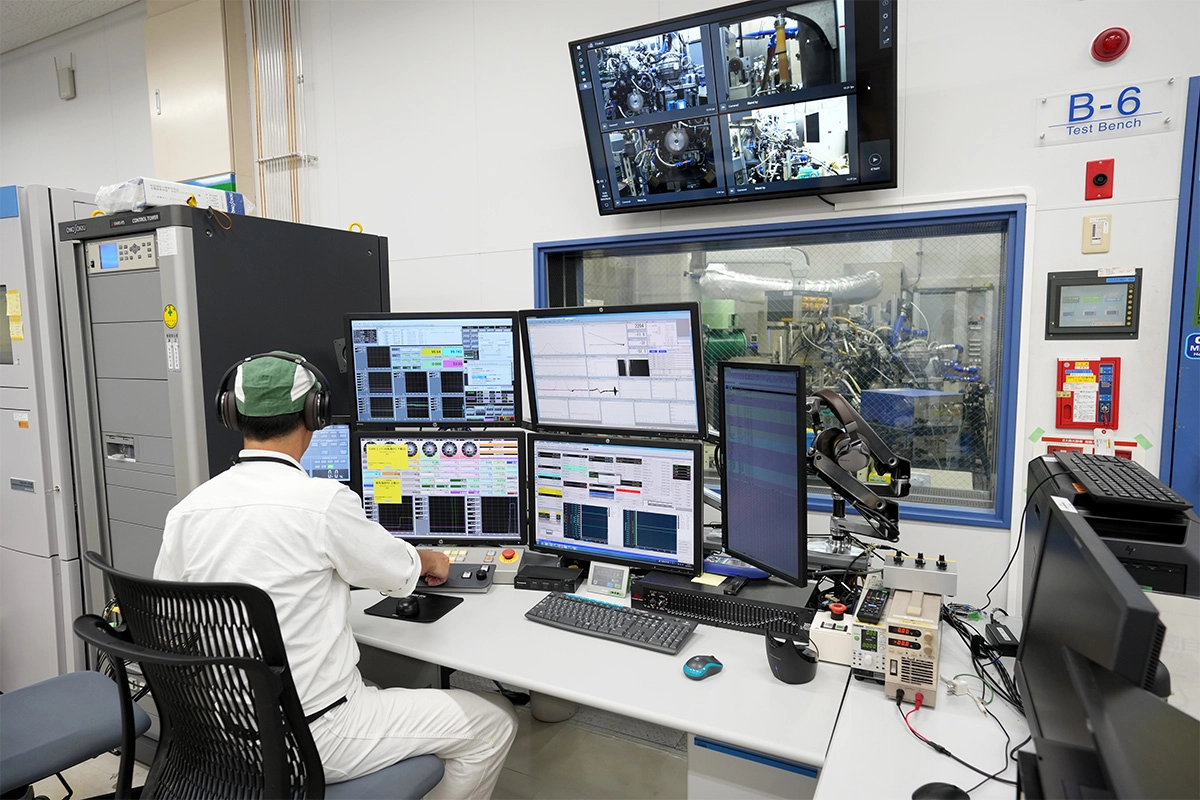
Single-cylinder Performance Engine Bench
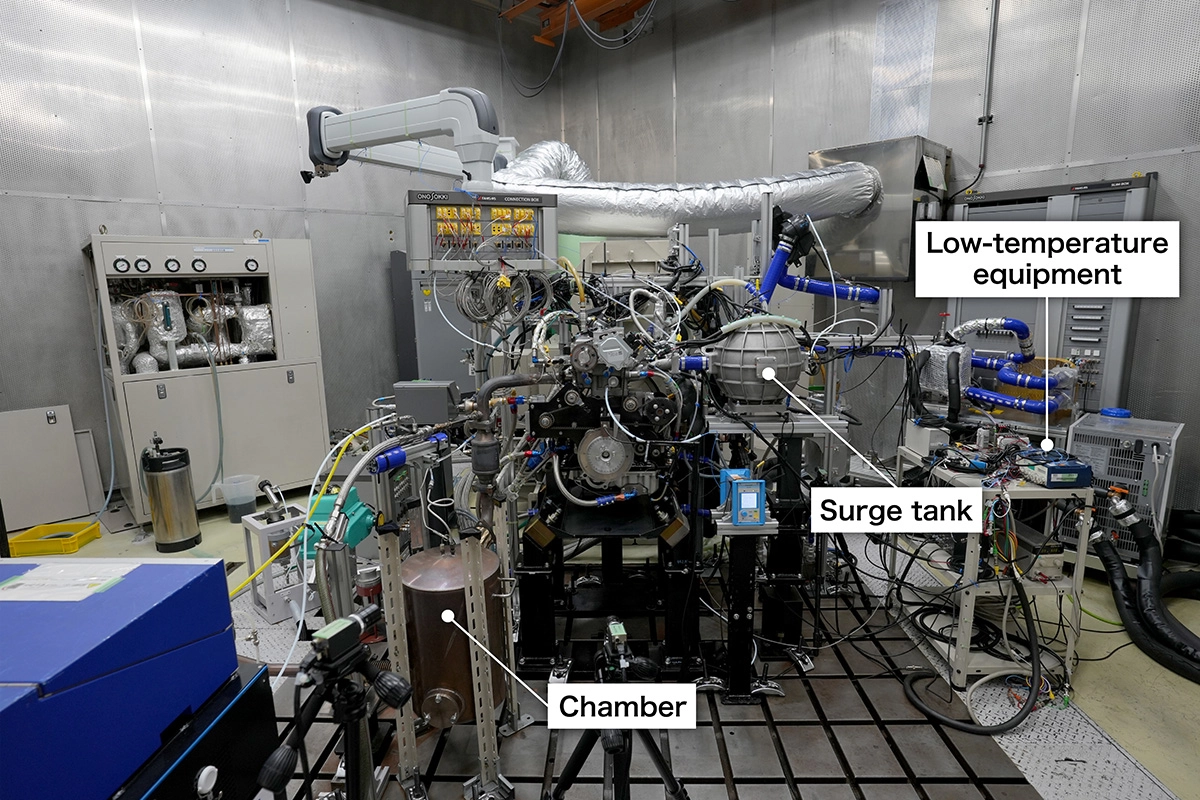
Single-cylinder Performance Engine Bench
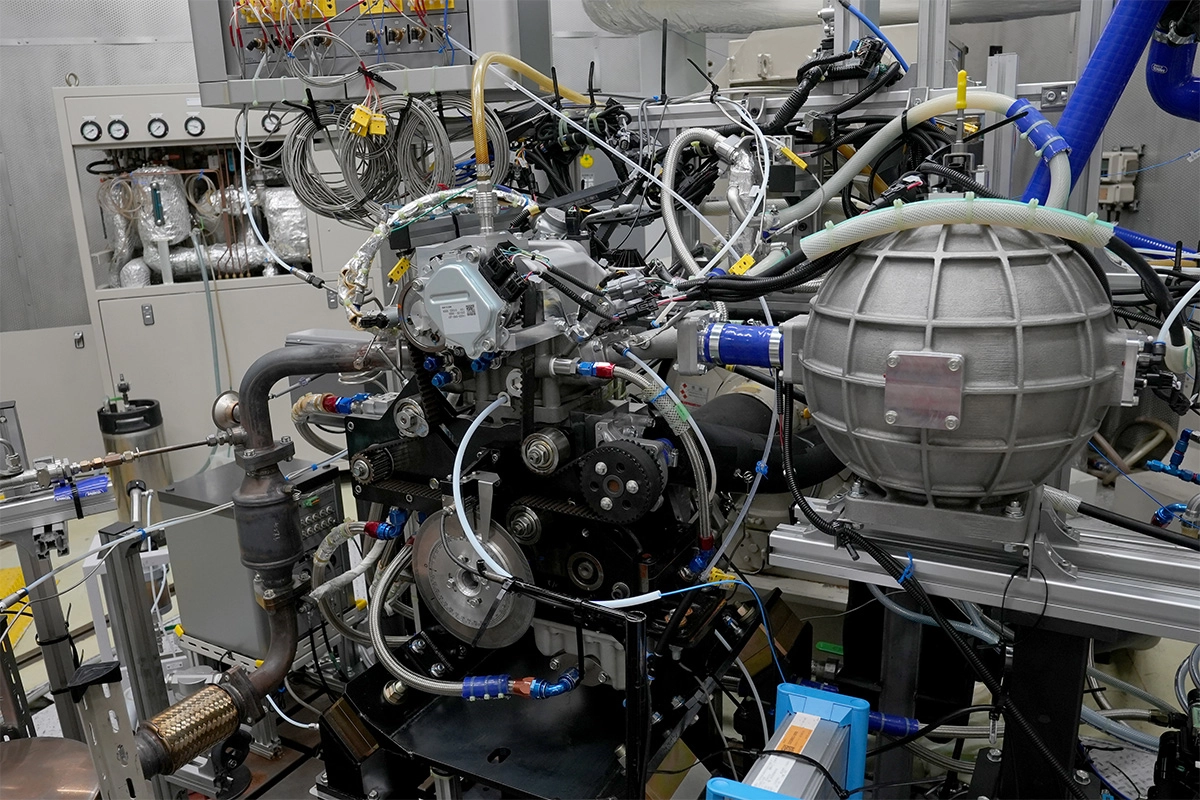
Control Room
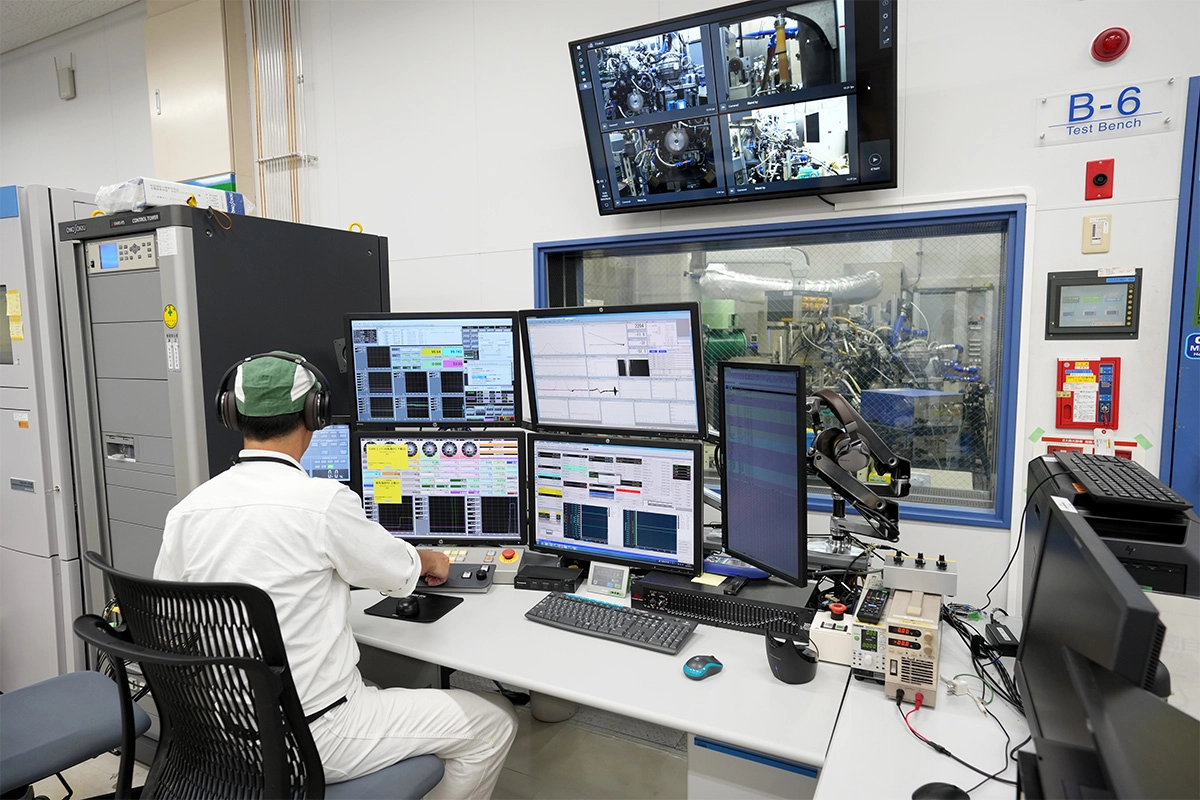

Optical Single-cylinder Engine Bench
The optical single-cylinder engine bench is equipment that makes combustion, normally invisible from outside, visible. After studying the main specifications performed by CAE and single-cylinder performance engine bench testing, the optical single-cylinder engine bench is used to verify the parameters of combustion design. The aim of this equipment is to realize the more efficient engine combustion development due to understanding of detail phenomena, which is fuel spray behavior, in-cylinder charge motion and combustion condition etc., through the engine engineer’s “eyes (point of view)”.
A specially manufactured optical single-cylinder engine is fixed to the floor of the test room. The cylinder liner is made of quartz glass with high heat resistance, allowing visibility of the in-cylinder. High-speed cameras can be set to capture both the entire cylinder and fuel adhesion on inside wall of cylinder liner. Additionally, a piston equipped with a quartz window is available to capture the spread of flames from below the combustion chamber after ignition.
The high-speed cameras are typically operated at 10,000 frames per second. High speed phenomena occurring inside the engine cylinder are captured as images and carefully observed later for phenomenon analysis. In direct injection engines that inject fuel directly into the cylinder, oil dilution—where fuel adhering to cylinder liner mixes with lubricating oil in the crankcase—has become a recent challenge. When oil dilution occurs, lubricating oil performance decreases, potentially leading to damage of the bearings and other parts. To avoid this phenomenon, reducing the adhesion of fuel to cylinder liner is ideal. Visualization-based analysis of dilution is one of the primary applications of this equipment.

Control Room
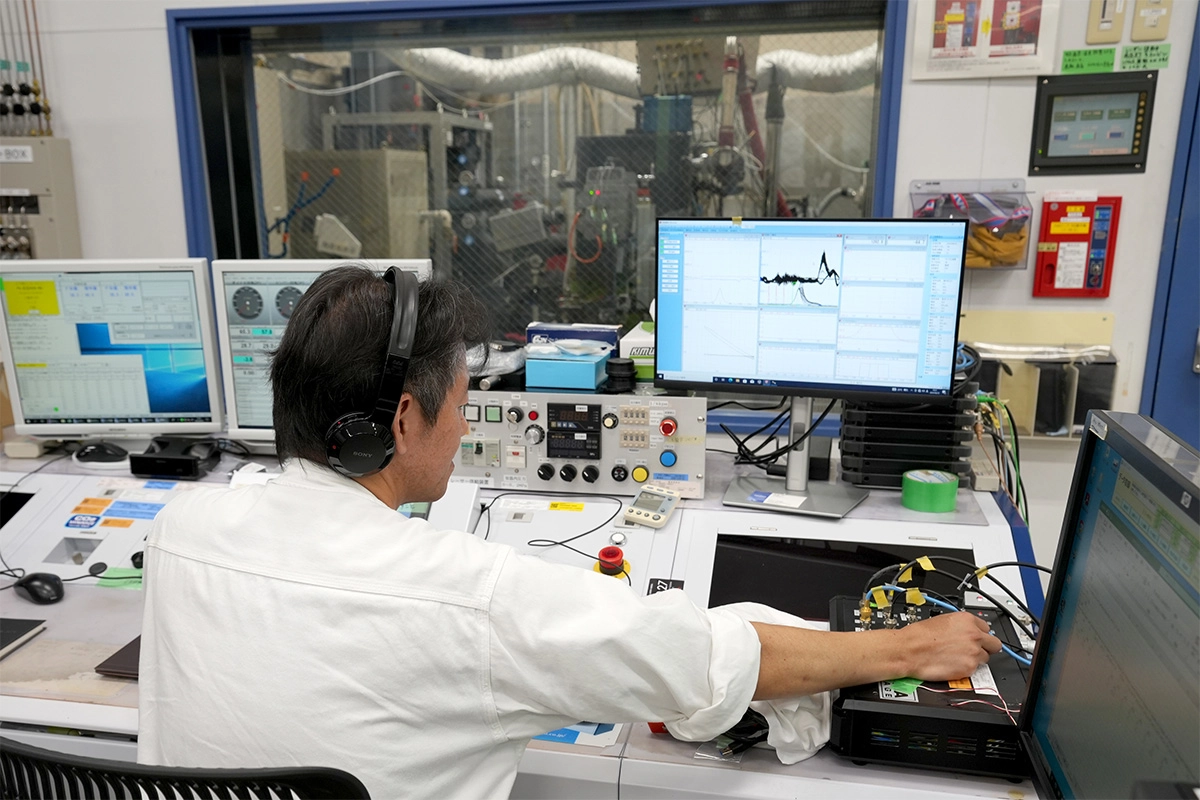
Optical Single-cylinder Engine Bench
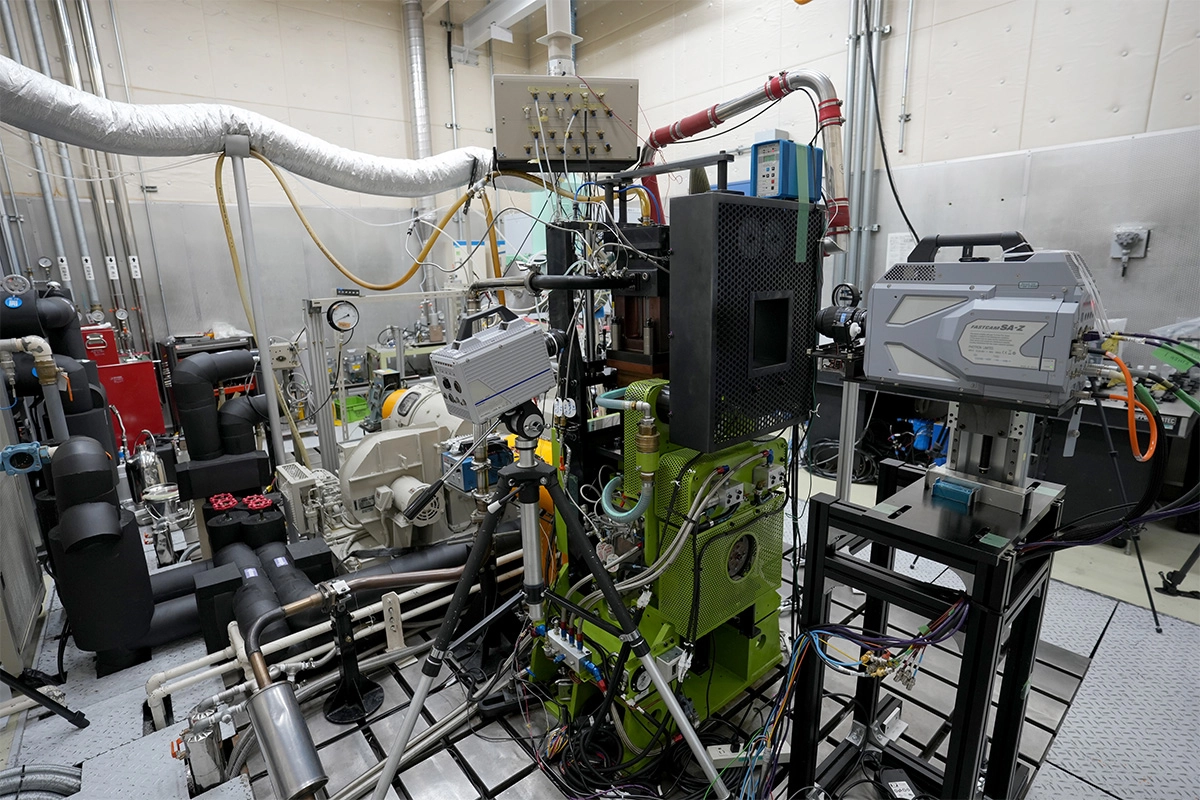
Optical Single-cylinder Engine Bench
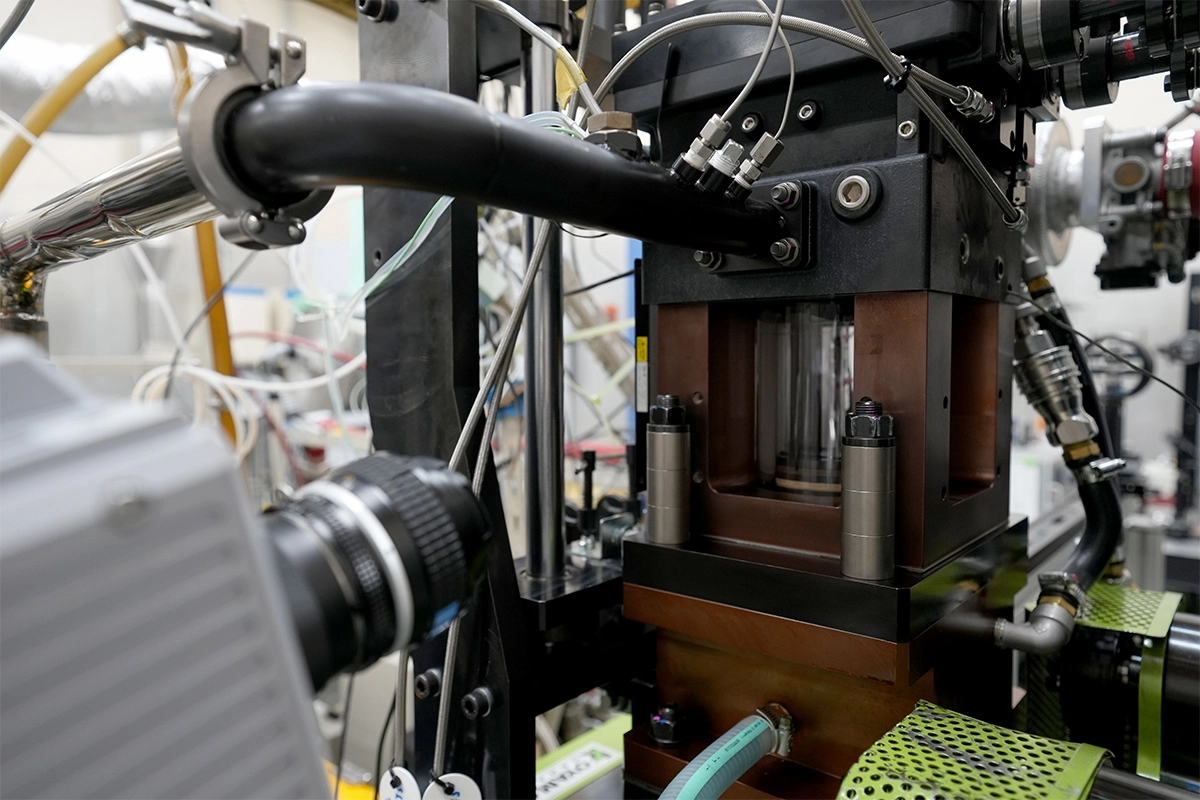
Camera capturing fuel spray directed at inside wall of cylinder liner and fuel adhesion to inside wall of cylinder liner
Optical Single-cylinder Engine Bench
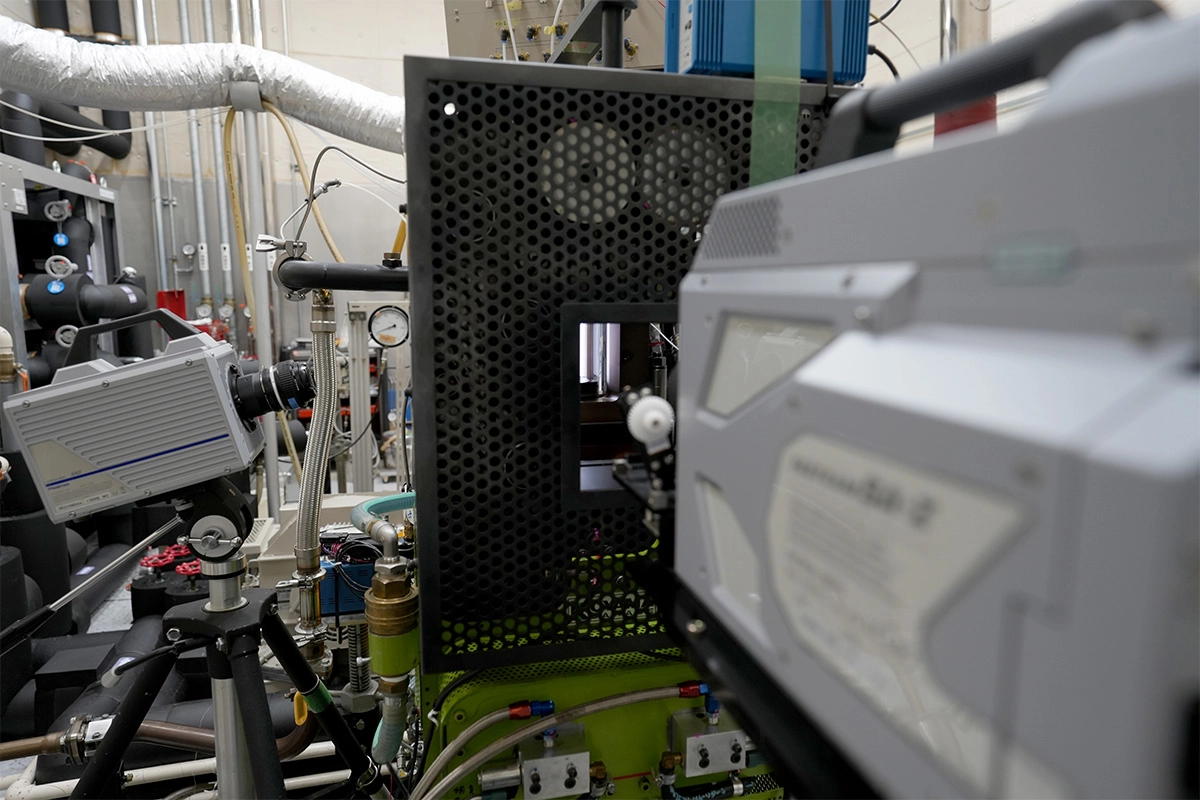
Camera capturing overall view of cylinder showing fuel spray and flame propagation
Control Room
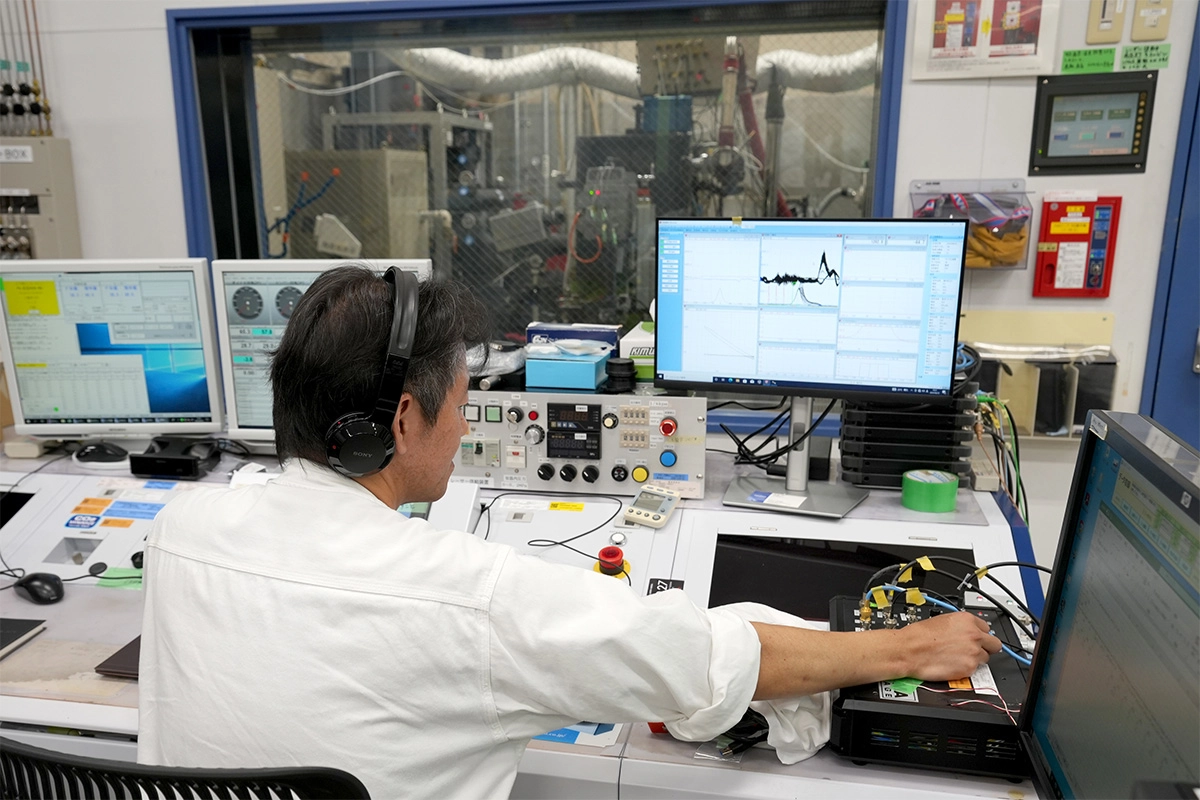
Optical Single-cylinder Engine Bench
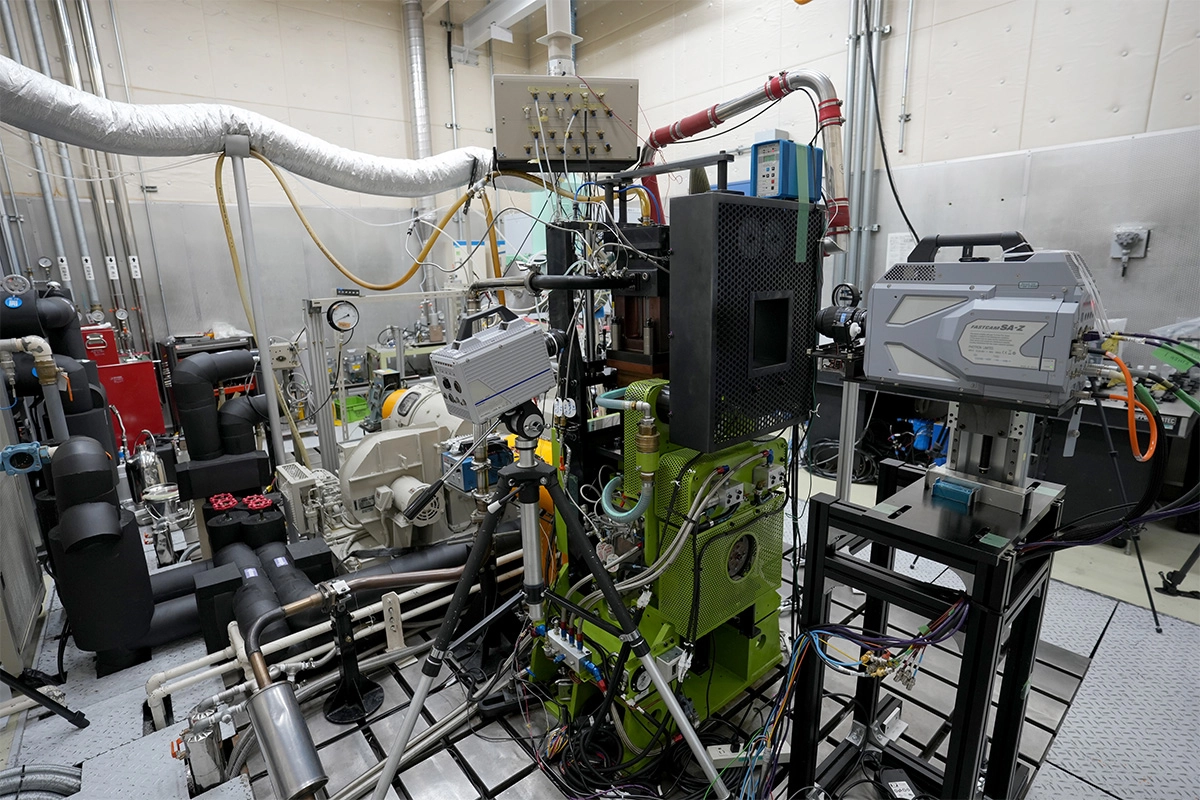
Optical Single-cylinder Engine Bench
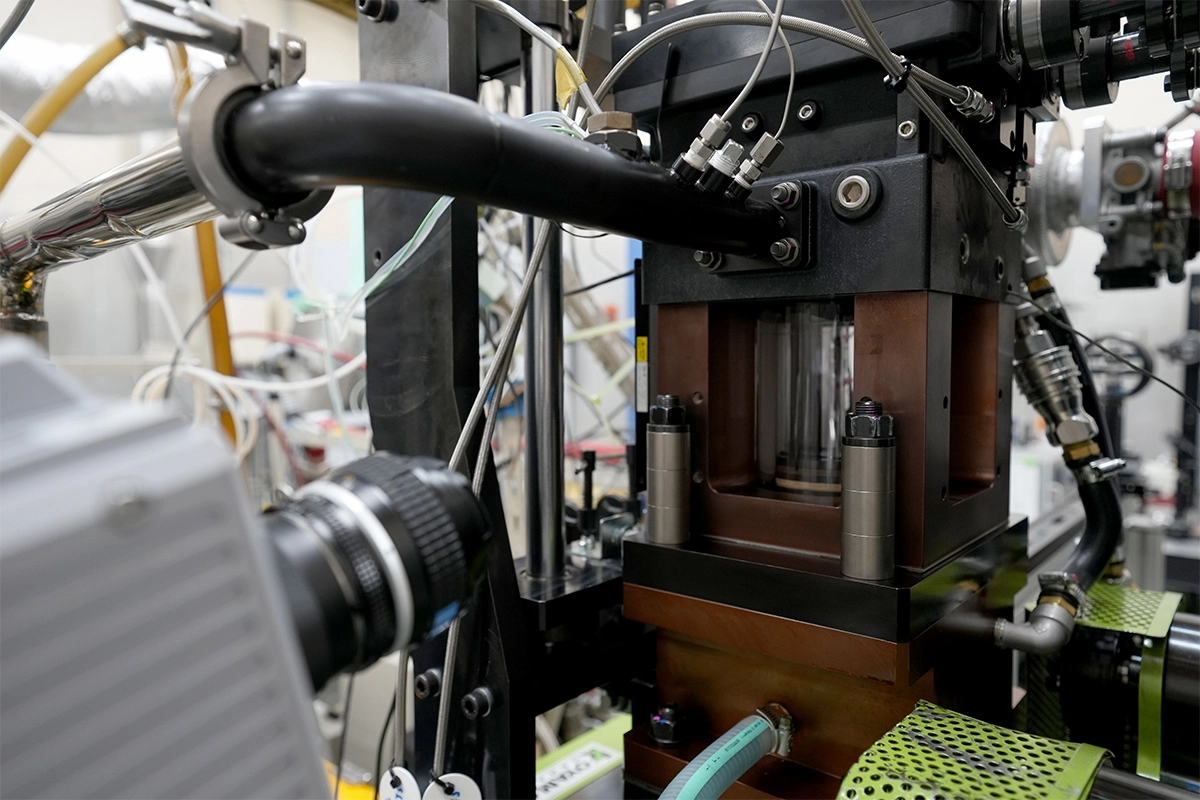
Camera capturing fuel spray directed at inside wall of cylinder liner and fuel adhesion to inside wall of cylinder liner
Optical Single-cylinder Engine Bench
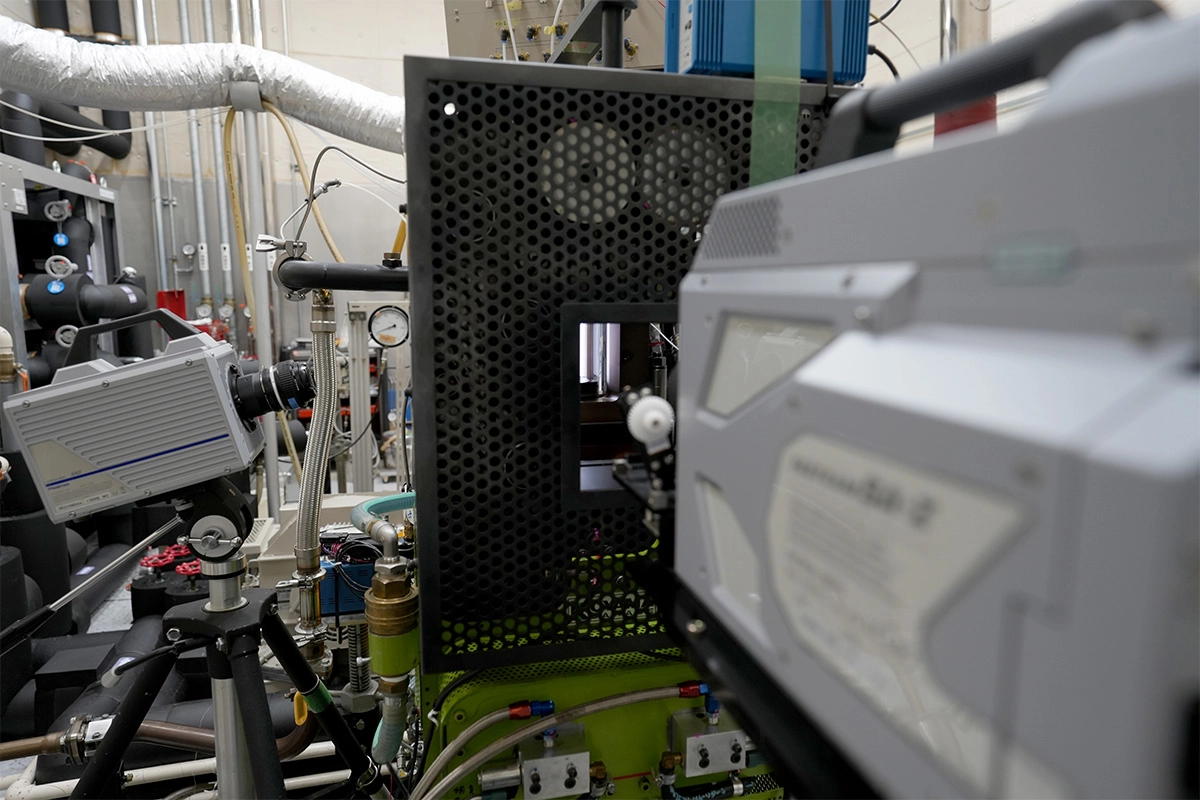
Camera capturing overall view of cylinder showing fuel spray and flame propagation
Control Room
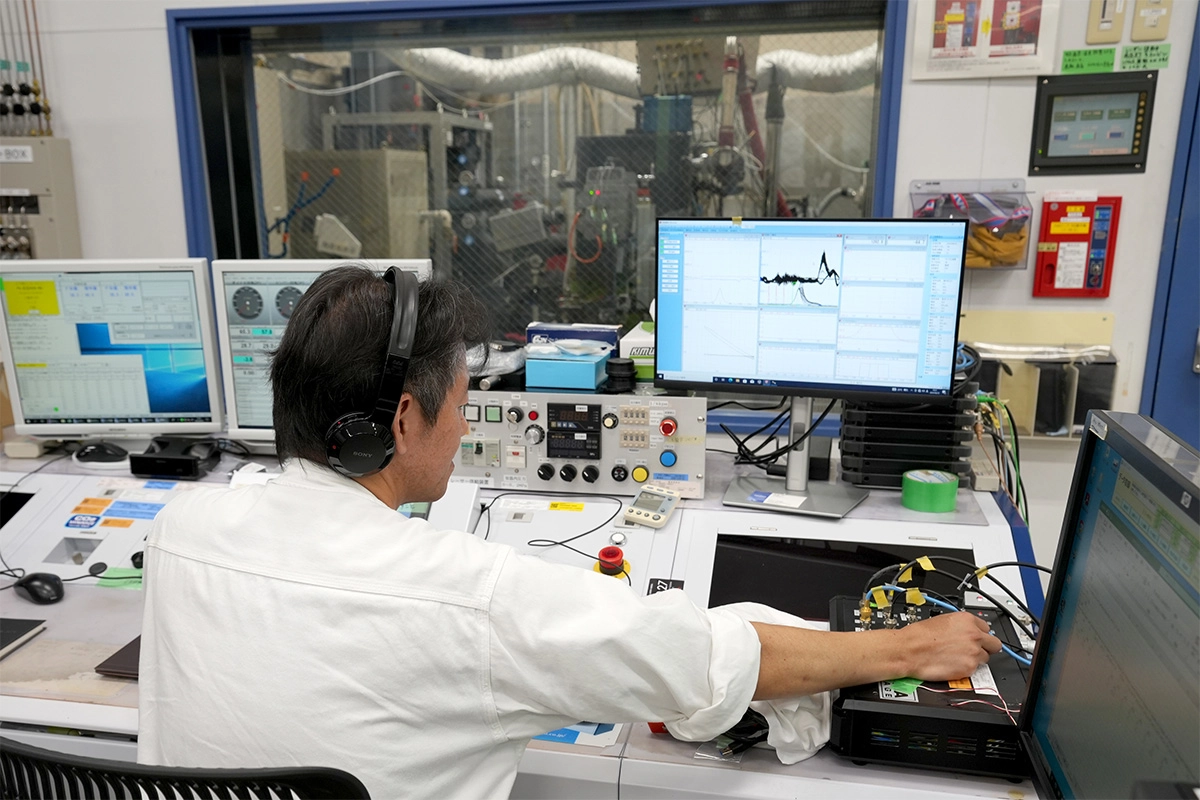

Specifications, such as for bore and stroke, can be made exactly the same as metal multi-cylinder engines. The piston crown surface is interchangeable. Intake port shapes and injector positions can be modified as well. Fuel injection pressure can be adjusted across a range and it is possible to recreate turbocharging conditions by external supercharging equipment. When water temperature is low, fuel adhering to cylinder liner does not vaporize, leading to soot formation. The test room is equipped with engine coolant cooling equipment, enabling testing under low-temperature conditions such as 0°C water temperature. Clarifying the phenomena that lead to a reduction in emissions is also one of the roles of the optical single-cylinder engine bench.
Data obtained from optical measurements is also used to verify the parameters of combustion design studied by computer simulation. The optical measurement images make it immediately apparent whether phenomena that engineers envisioned based on simulation results actually occur as expected, which helps to align understanding.
High-speed camera photography is one optical measurement technique, and optical measurement is carried out using optimal methods for each phase of phenomena occurring inside the cylinder during intake, compression, expansion, and exhaust strokes, such as Particle Image Velocimetry (PIV)*1 and the shadowgraph method*2.
*1 An optical measurement method that determines in-cylinder flow
velocity and direction from the movement of particle images which
obtained by irradiating a laser sheet in intake air mixed with tracer
particles.
*2 An optical measurement method that detects the density graduation of
air-fuel mixture a light source and screen.
Fuel Spray and Flame Propagation (Slow-motion video)
Tire Force and Moment Measurement Machine
Tire performance is essential when discussing vehicle dynamic performance. Tires are the only points of contact between a car and the ground. No matter how high-performance the power unit or chassis might be, dynamic performance cannot exceed the capabilities of the tires. Therefore, understanding tire characteristic is very important for dynamic performance. The tire force and moment measurement machine is the facility for understanding tires—a fundamental aspect of vehicle dynamic performance design.
The tire force and moment measurement machine reproduces various scenarios that tires encounter while driving, such as cornering and braking, on a test bench. It measures the forces and moments (rotational motion around axes), known as the six force components, generated by tires in each scenario. In other words, this facility evaluates the performance of the tires. The characteristic measured here will be the fundamental information for dynamic performance design. Early acquisition of the tire characteristics helps to enhance vehicle performance, and also it reduces revise work during development. That’s the key to deliver our product to the customers early.
The purpose of this facility is to create the tire models for simulation by measuring tire characteristics. A driving simulator is often used in recent vehicle development for efficiency, and it requires tire models that can reproduce the behavior of the tire correctly. Facility to acquire the characteristics to create precise tire models.
The tire, assembled with a wheel, is attached to the machine and rolls on a steel belt. The road surface is reproduced by the cylindrical belt pulled by two drums. Air bearings are installed beneath the flat section to maintain the belt's flatness against tire loads. One drum drives the belt and measures the tire forces and moments at the axle at normal speed.
Tire force will be reduced when it encounters the undulations because of its hysteresis characteristic. To reproduce this phenomena, Honda’s facility can excite the tire vertically from the contact patch side while most of the similar facility excite from the axle side. This feature improves the measurement accuracy and enables phenomena to be understood such as when traversing undulations in detail. Taking advantage of this capability, this facility is also used to study suspension damper characteristics.
The facility also measures tire characteristics for simulating very-low-speed phenomena such as parking assist. Since tire characteristics at very-low speeds differ significantly from those at normal speeds, specific test modes are taken to enable creation of tire models that can also express very-low-speed behavior.
Since tire models must be created to match simulation driving conditions, measurement modes are being developed in line with the advancement of tire model functionality, and the test facility is evolving alongside this development.
Just as actual vehicles cannot run without tires, vehicles cannot run in virtual space without tire models. As manufacturing shifts toward virtual development, the role of tire characteristic testing machines will become increasingly important.

Control Room
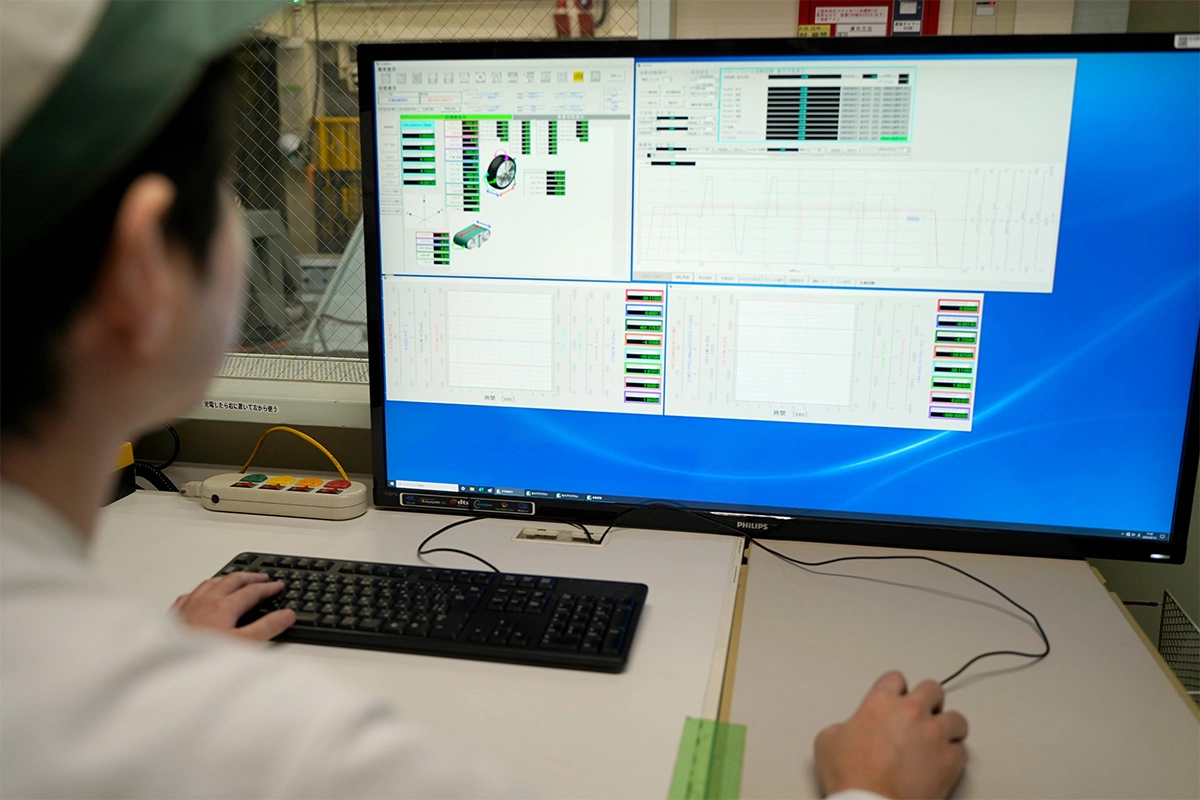
Tire Force and Moment Measurement Machine
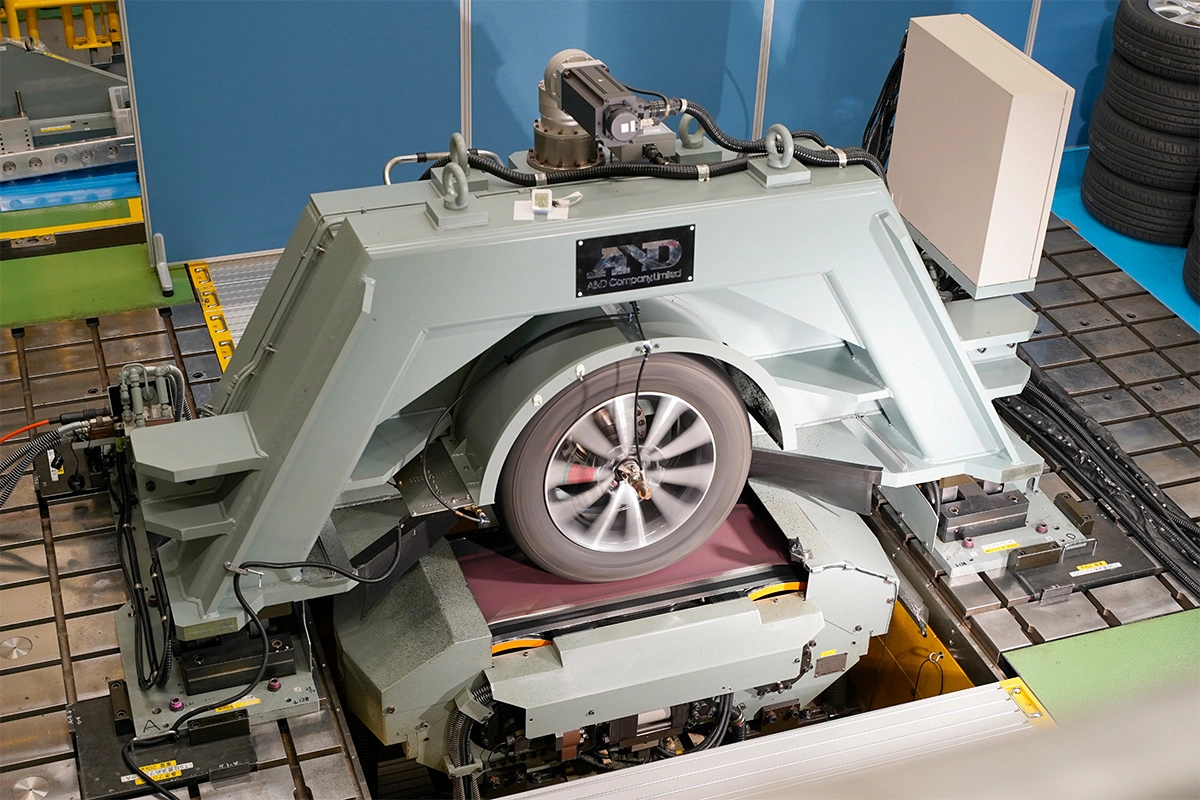
Tire Force and Moment Measurement Machine
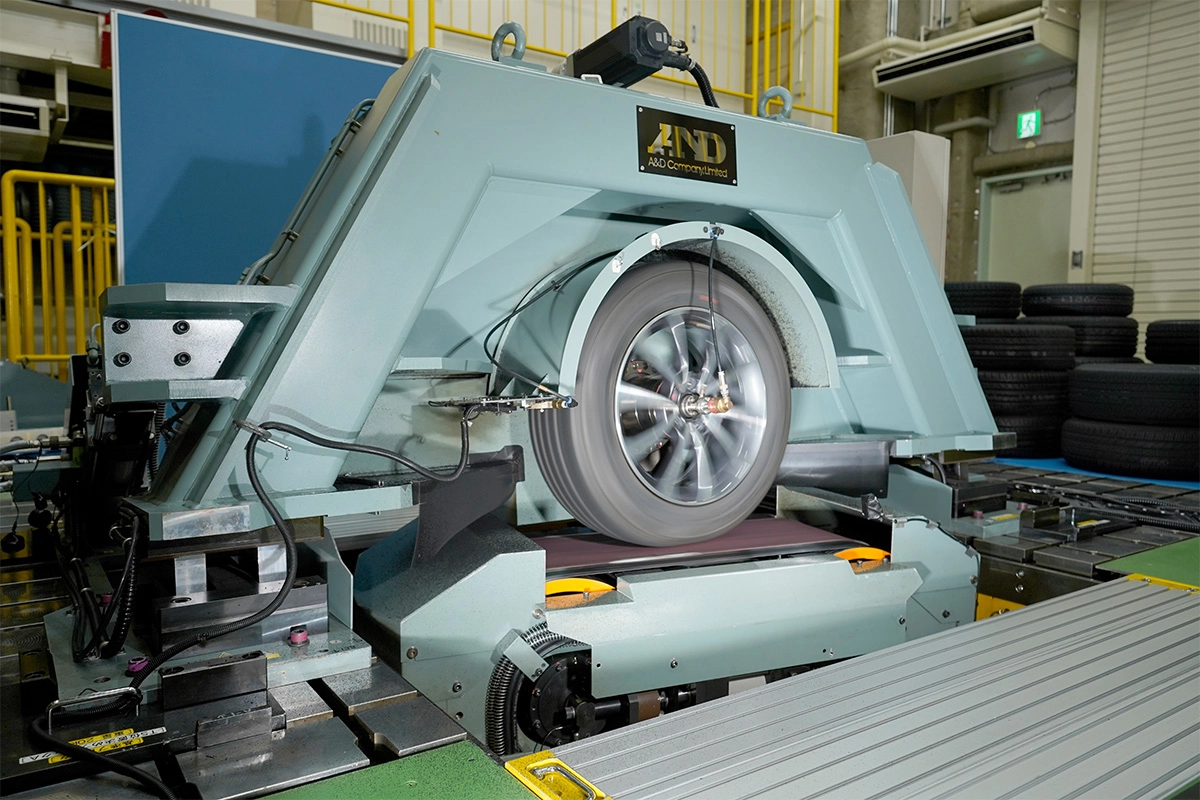
Control Room
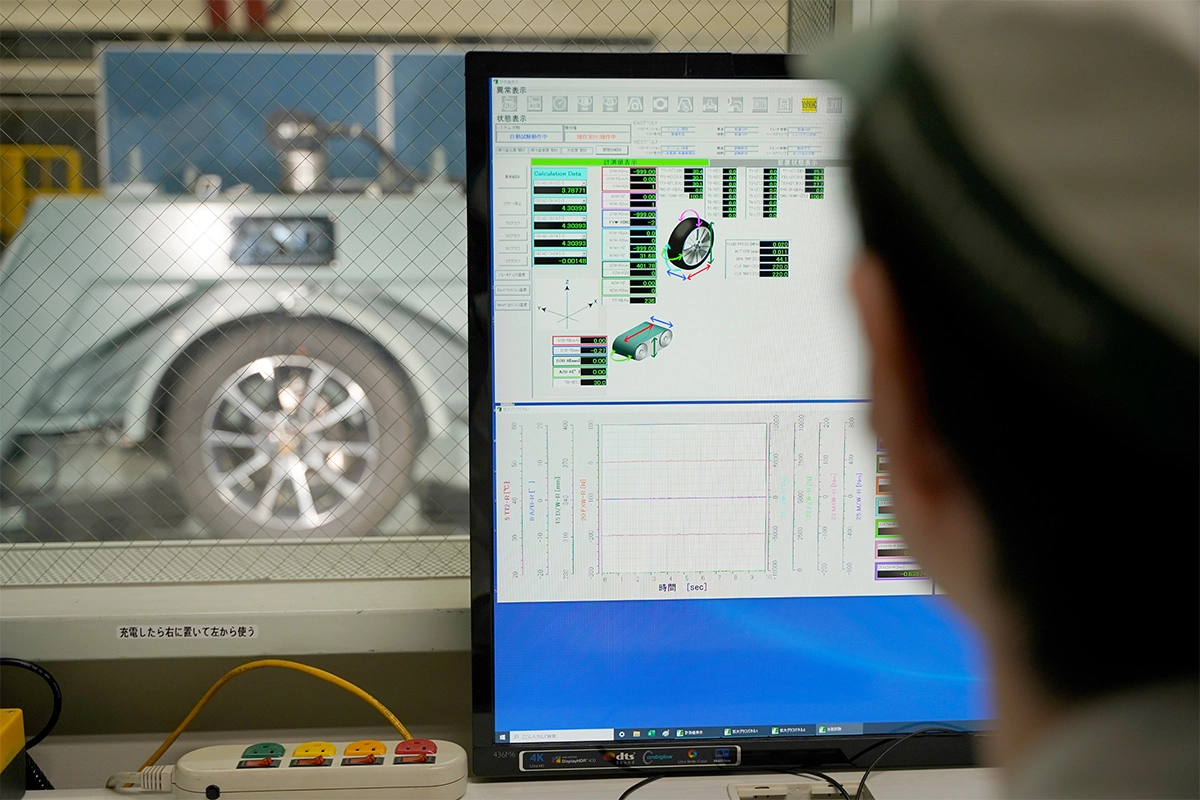
Control Room
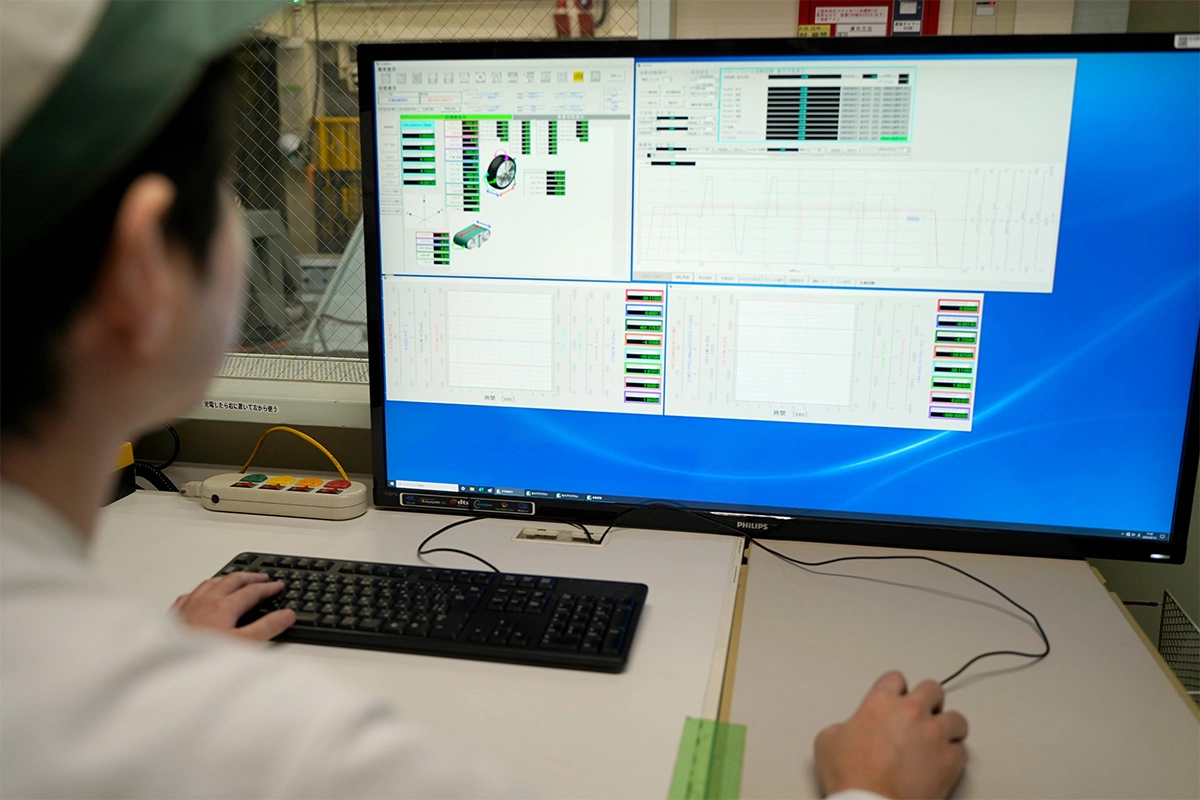
Tire Force and Moment Measurement Machine
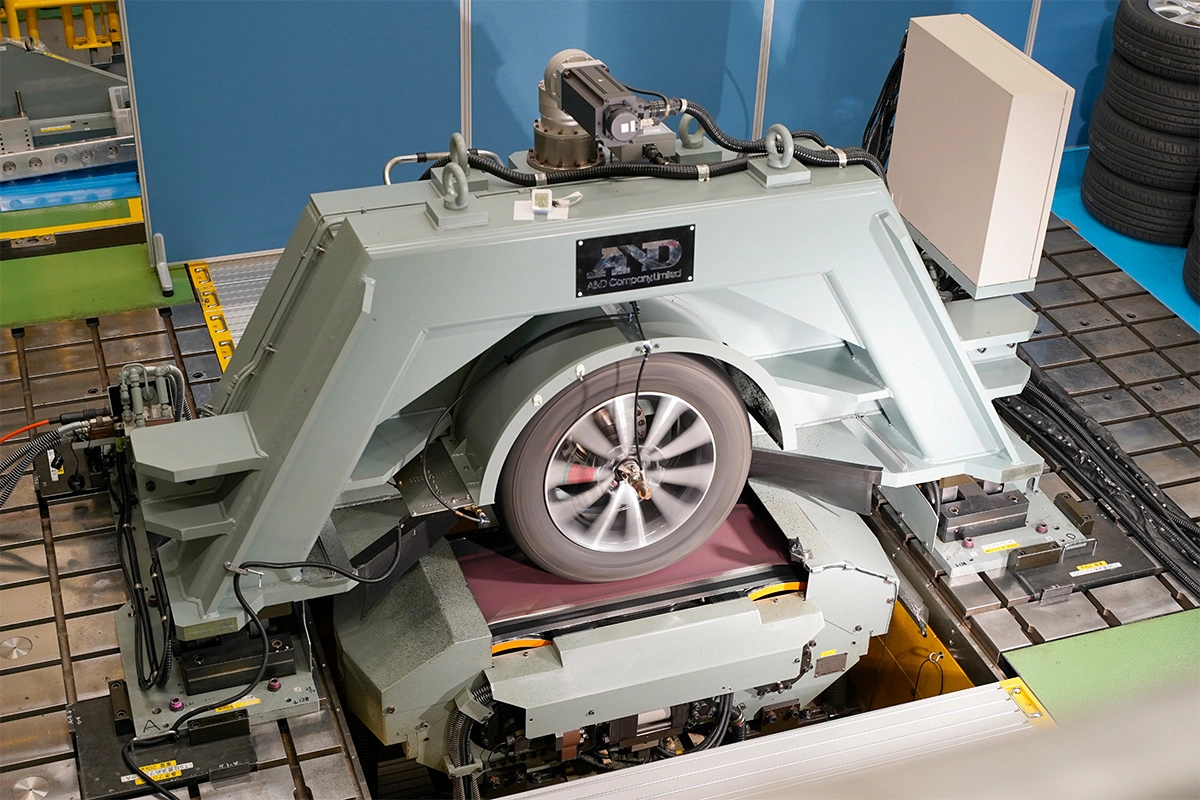
Tire Force and Moment Measurement Machine
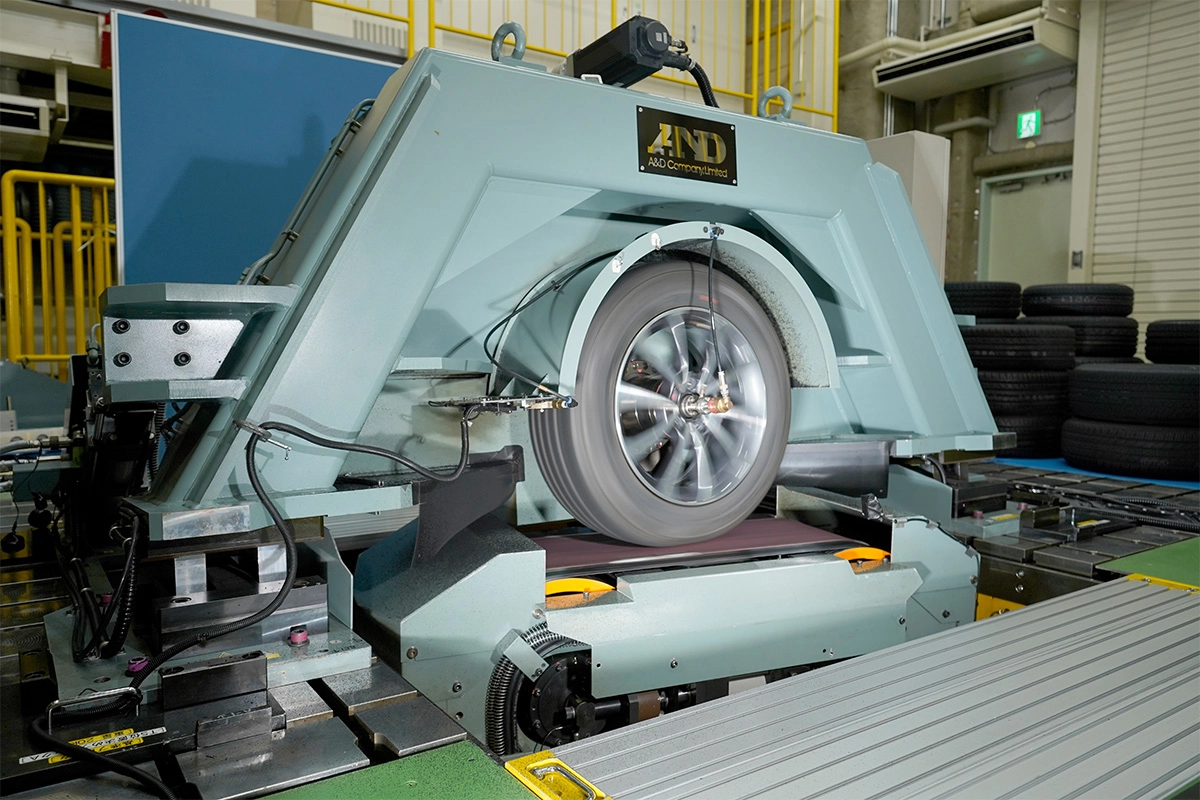
Control Room
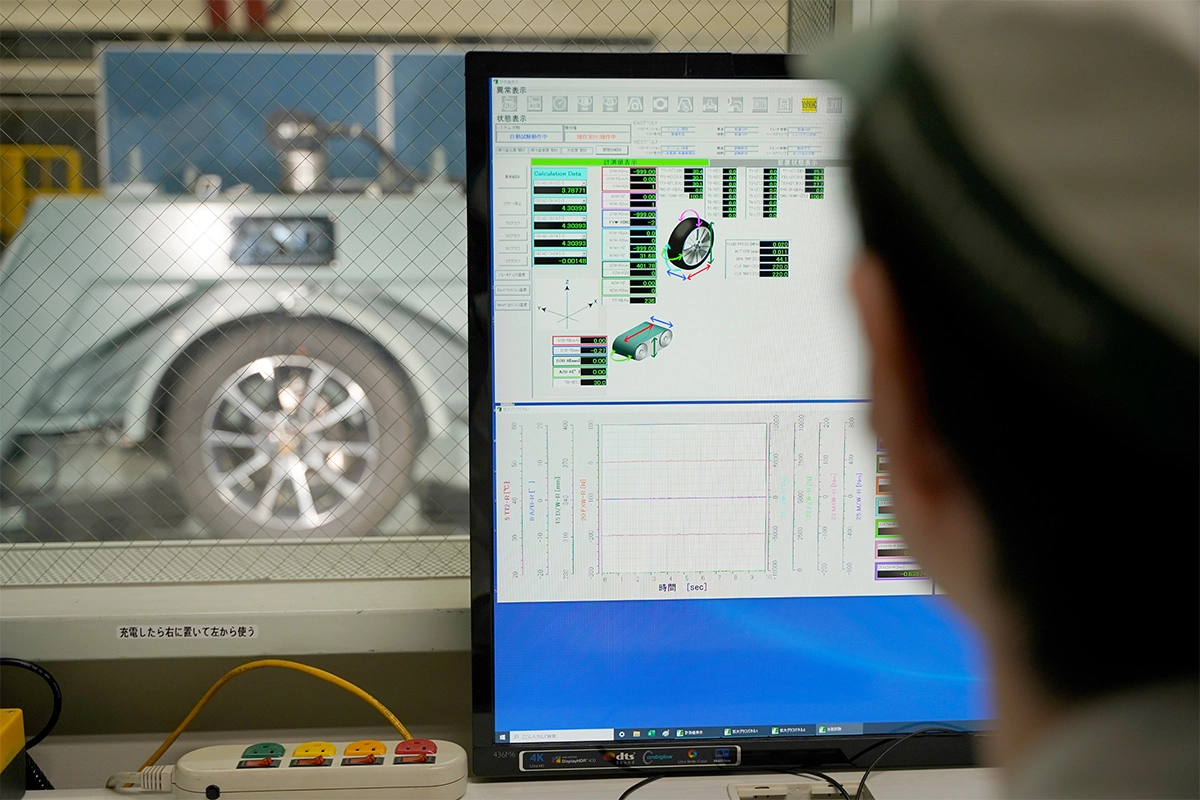
Control Room
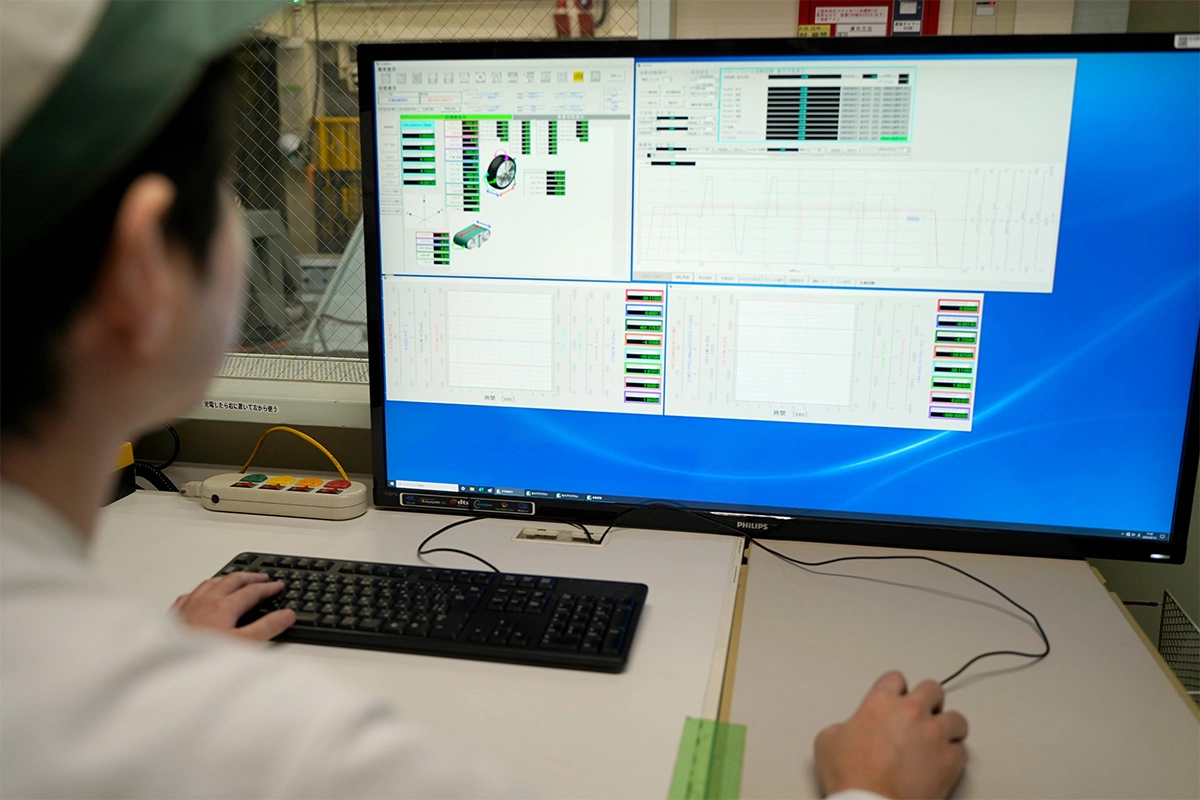

Suspension Tester
The suspension tester measures suspension characteristics, including kinematics (geometric characteristics) and compliance (elastic deformation of bushings, arms, and links). It is also called the Kinematics & Compliance (K&C) testing machine. This facility’s role is to enhance the vehicle dynamic performance that Honda aims for by measuring and evaluating suspension characteristics combined with simulations.
While suspension characteristics can be predicted through calculations, sometimes vehicles don’t behave as predicted in calculations. To analyze and predict various phenomena that occur in actual vehicles, the suspension tester evaluates and analyzes fundamental suspension characteristics, and enables more detailed performance prediction combined with simulation software.
The equipment overview is as follows. The test vehicle is fixed to the facility using the jacking points, and suspension characteristics are measured by reproducing the steering inputs made by a driver while driving, as well as forces at the tire contact patch, through the operation of a steering actuator attached to the steering system and load input tables at the tire contact surfaces.
Laser displacement sensors correct for body deformation and displacement to enable accurate evaluation of suspension characteristics even under large inputs. Angles such as camber and toe must be measured to within one-hundredth of a degree because even slight displacement of the body cannot be ignored. In other words, high-resolution measurement is necessary because humans can detect differences as minute as this.

Control Room
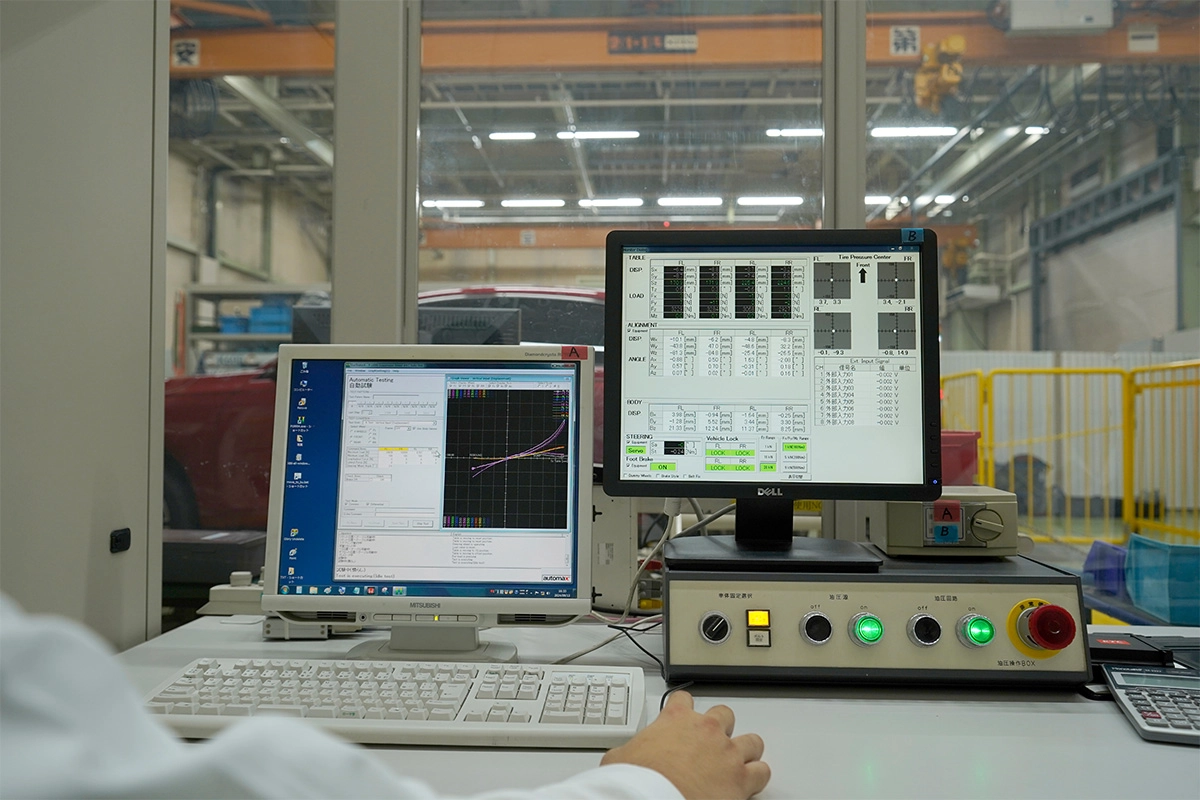
Suspension Tester
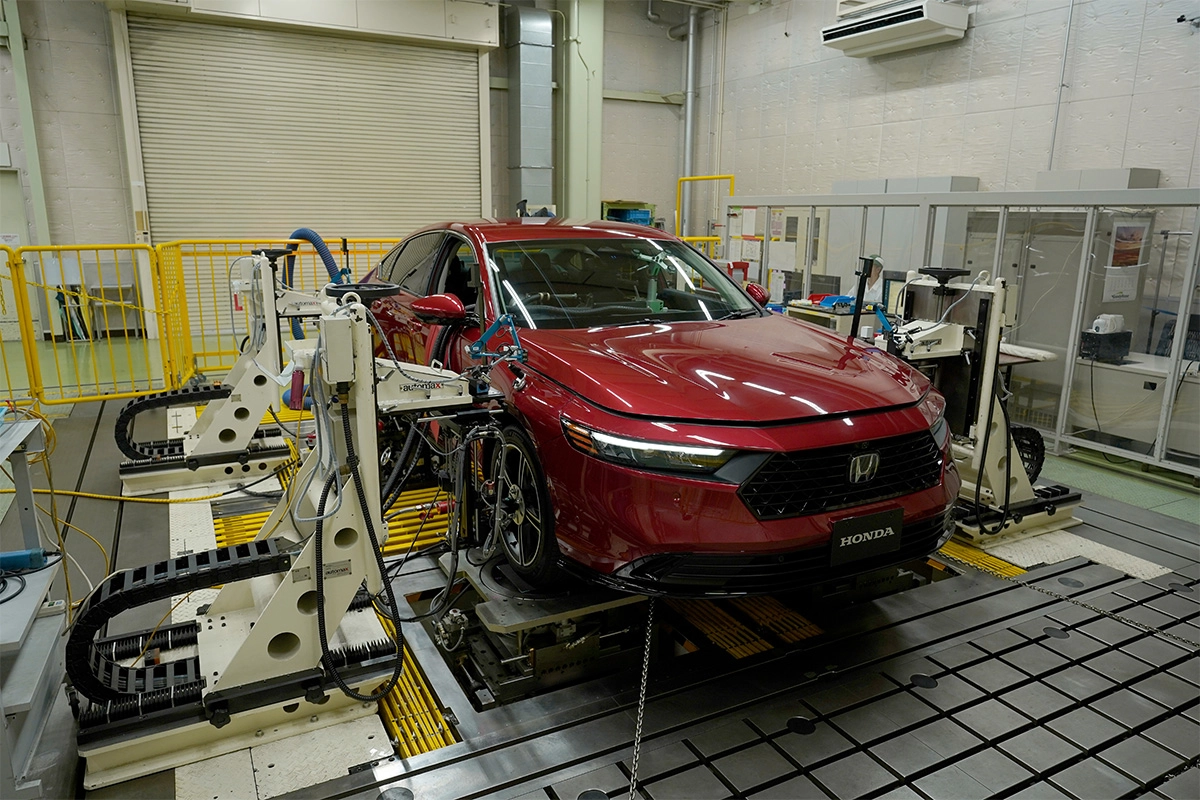
Suspension Tester
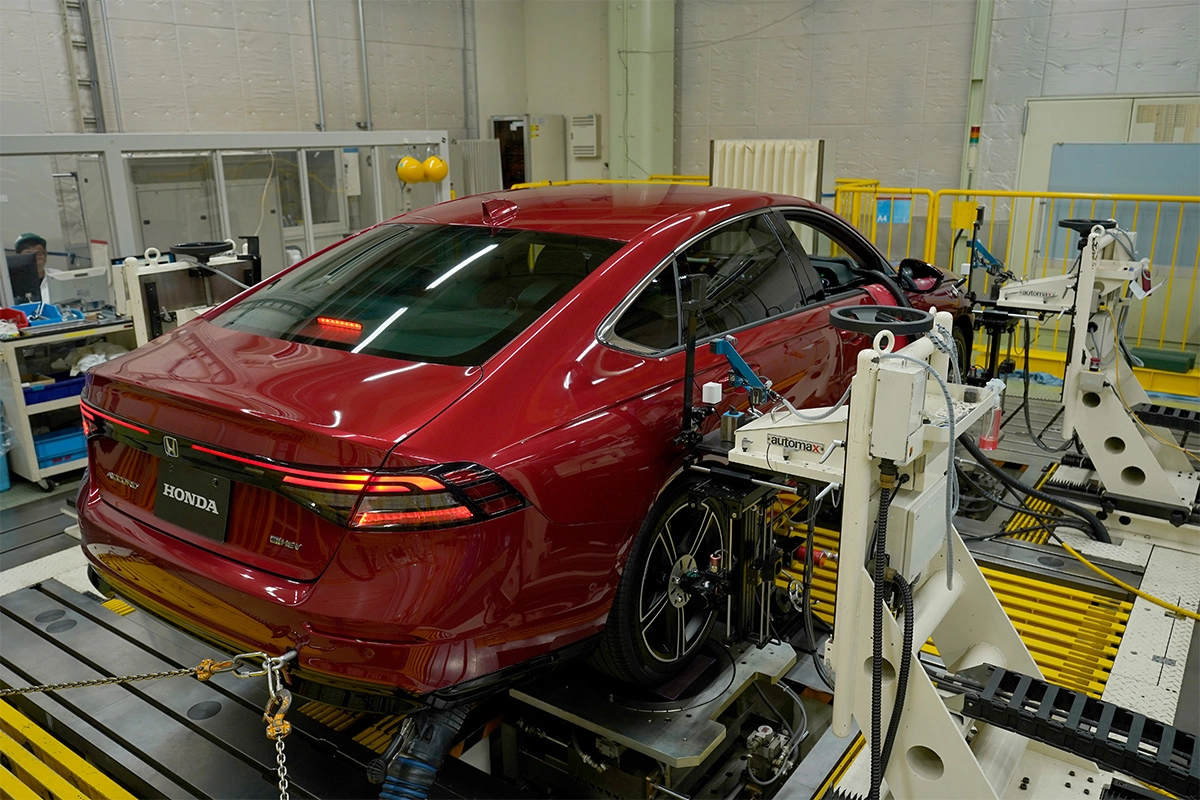
Suspension Tester
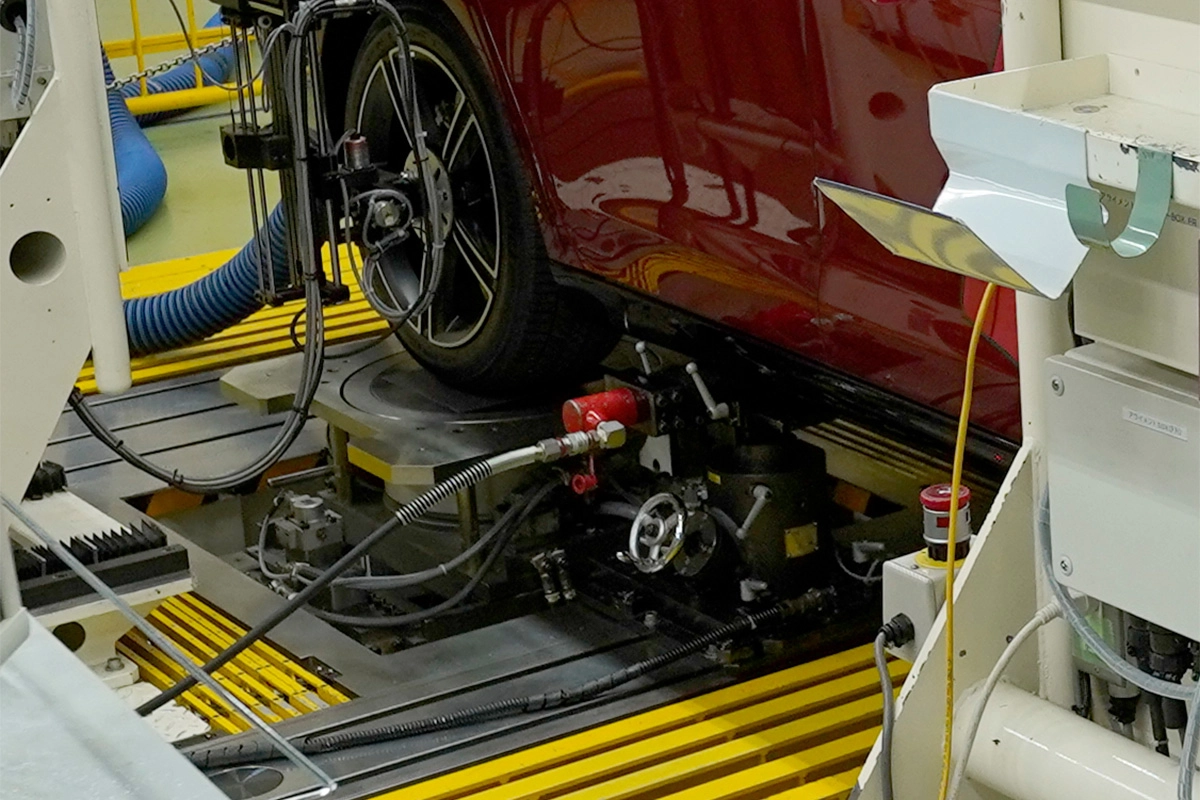
Test vehicle fixed to facility using jacking points
Suspension Tester
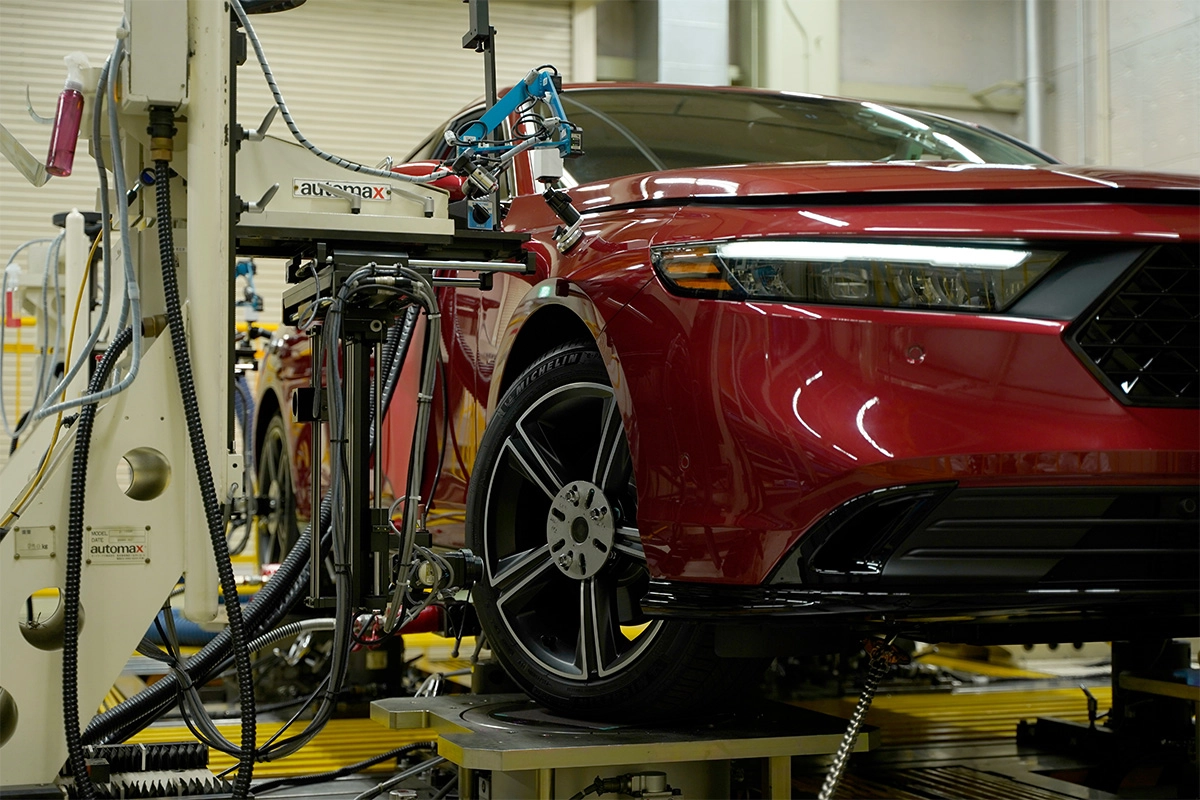
Suspension Tester
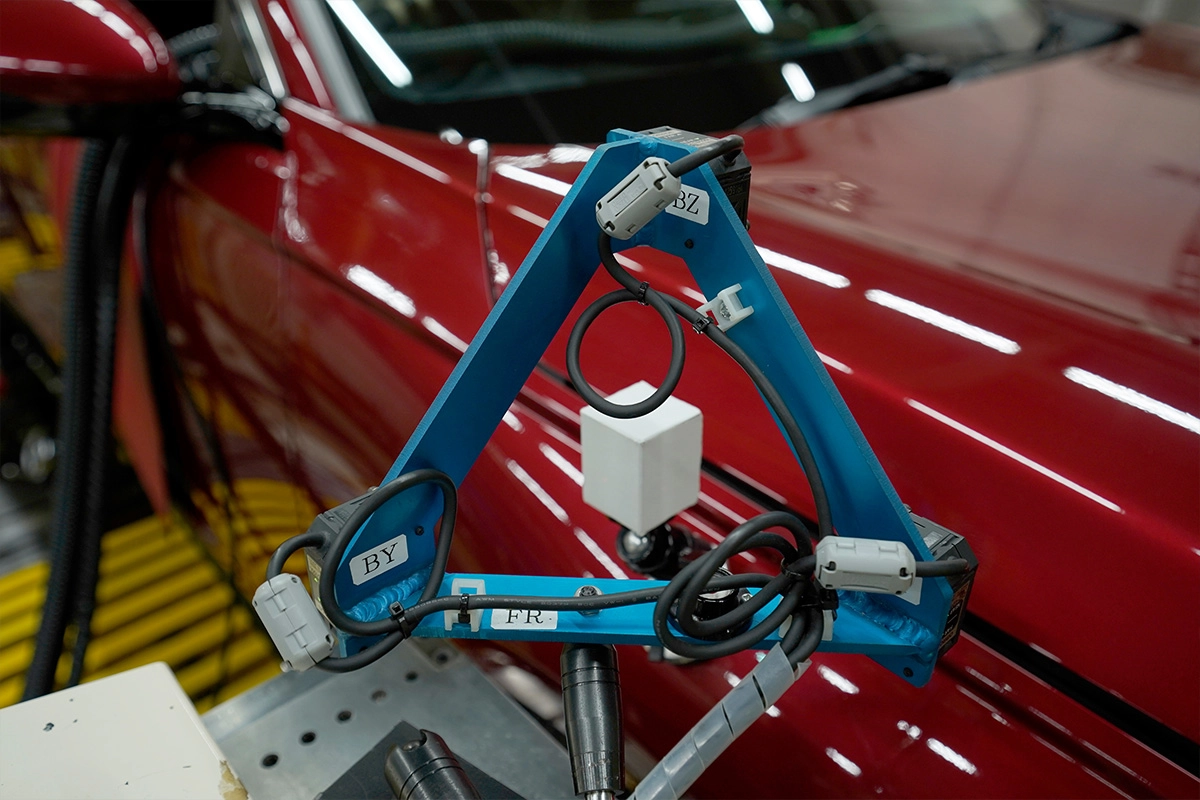
Laser displacement sensors
Suspension Tester
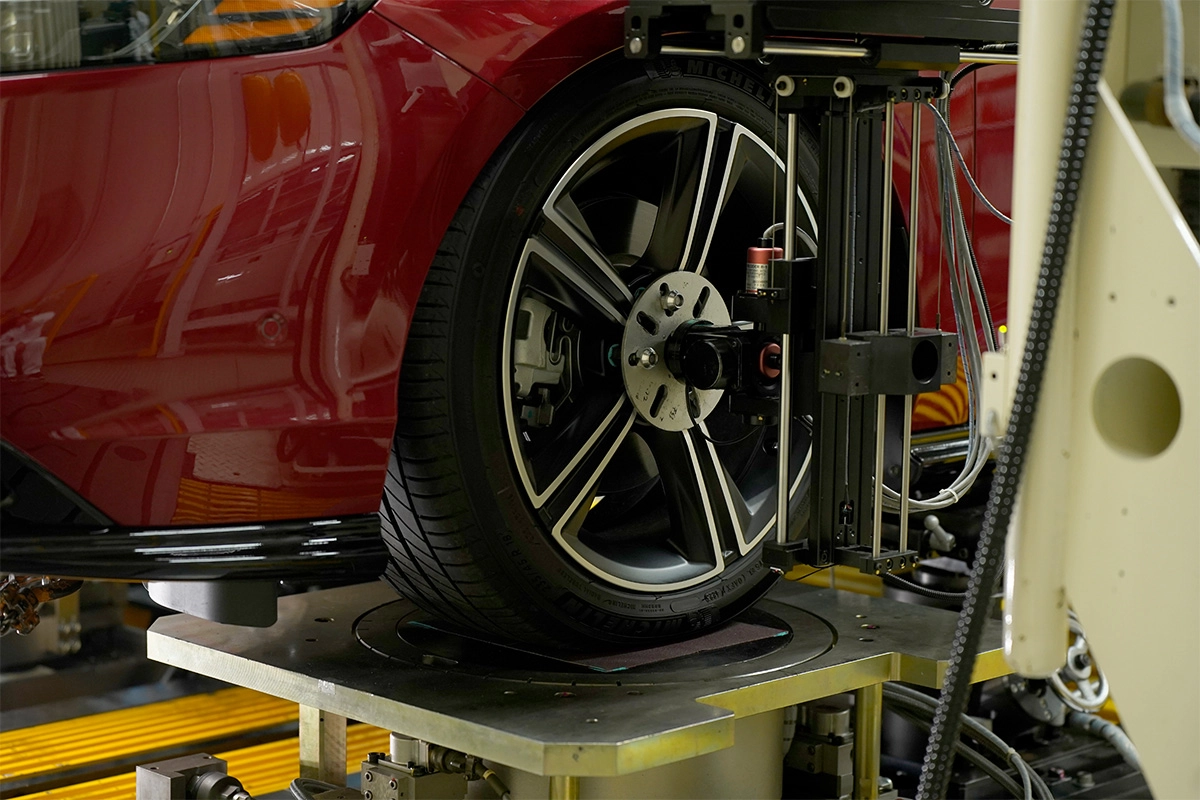
Suspension Tester
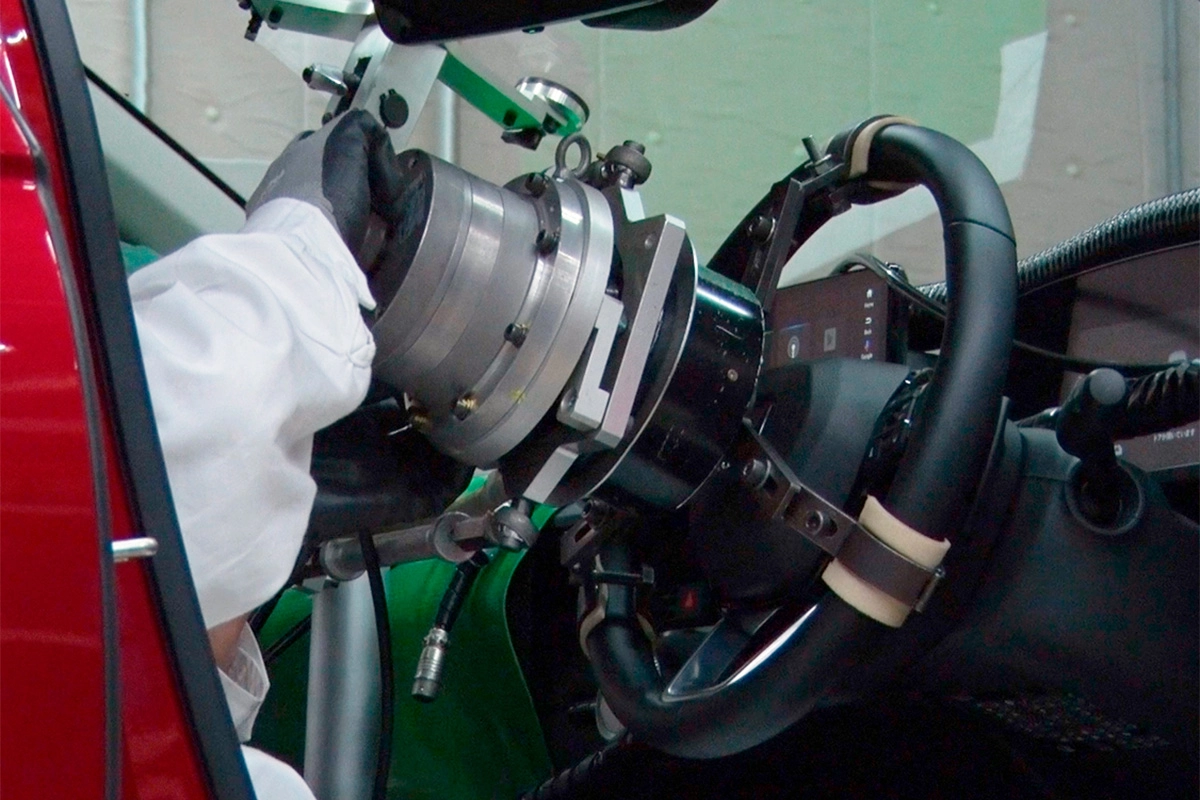
View of steering actuator installation
Control Room
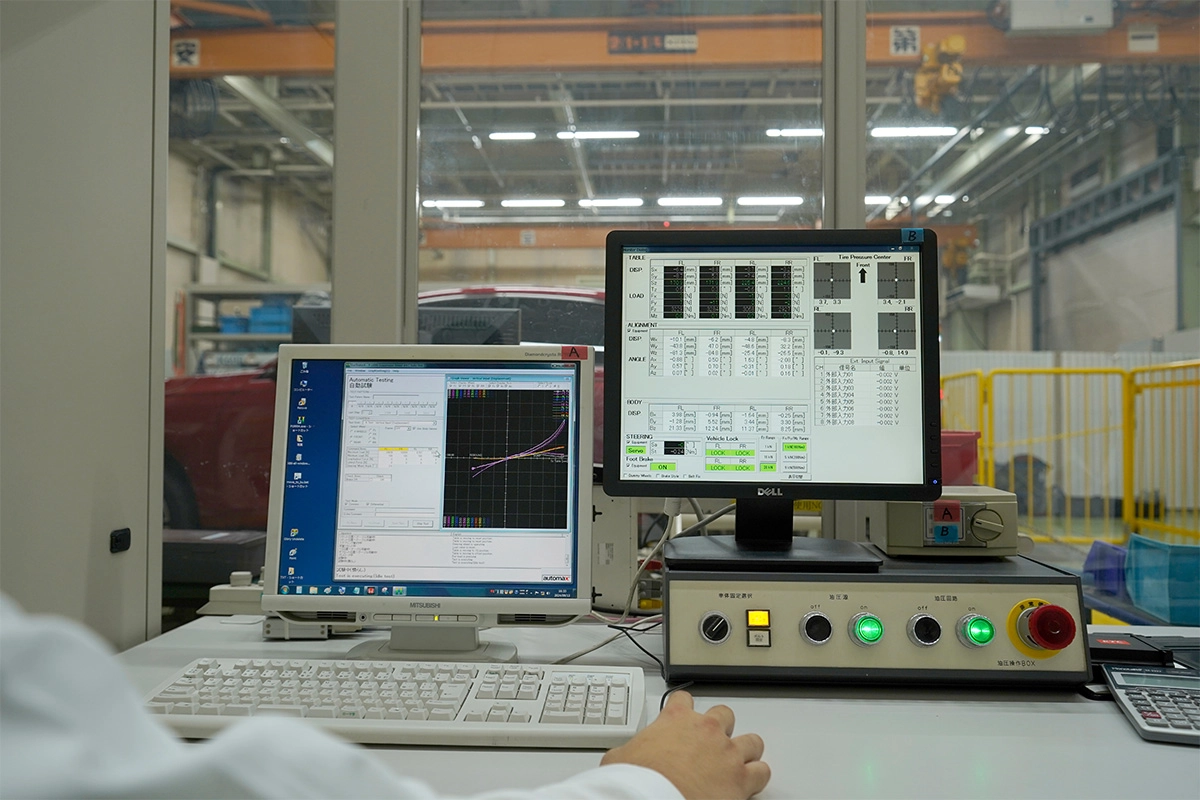
Suspension Tester
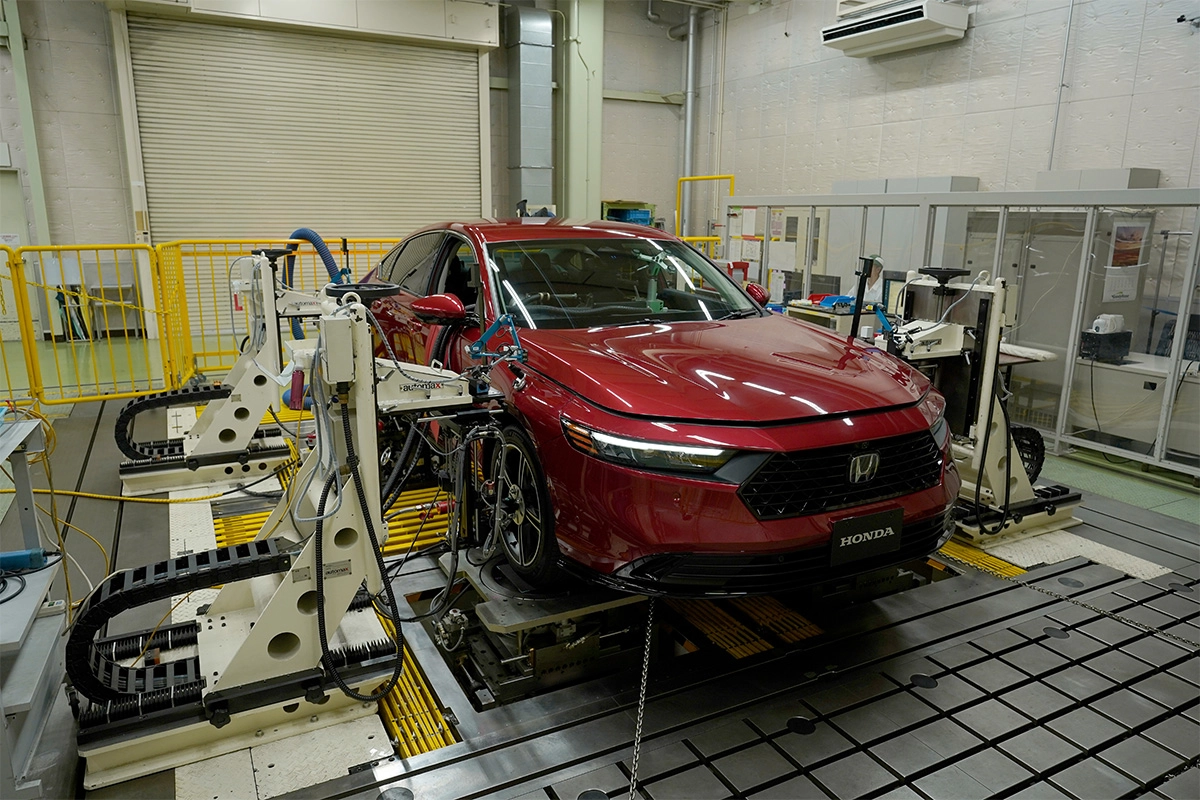
Suspension Tester
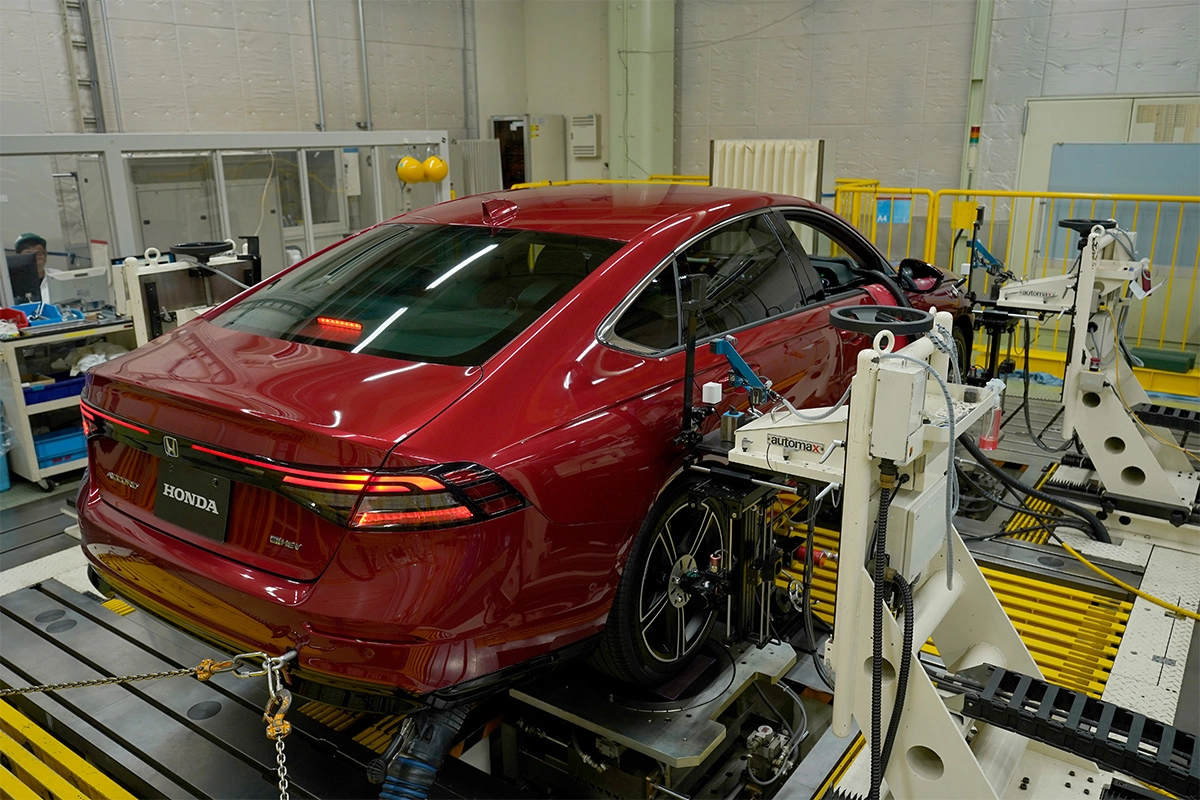
Suspension Tester
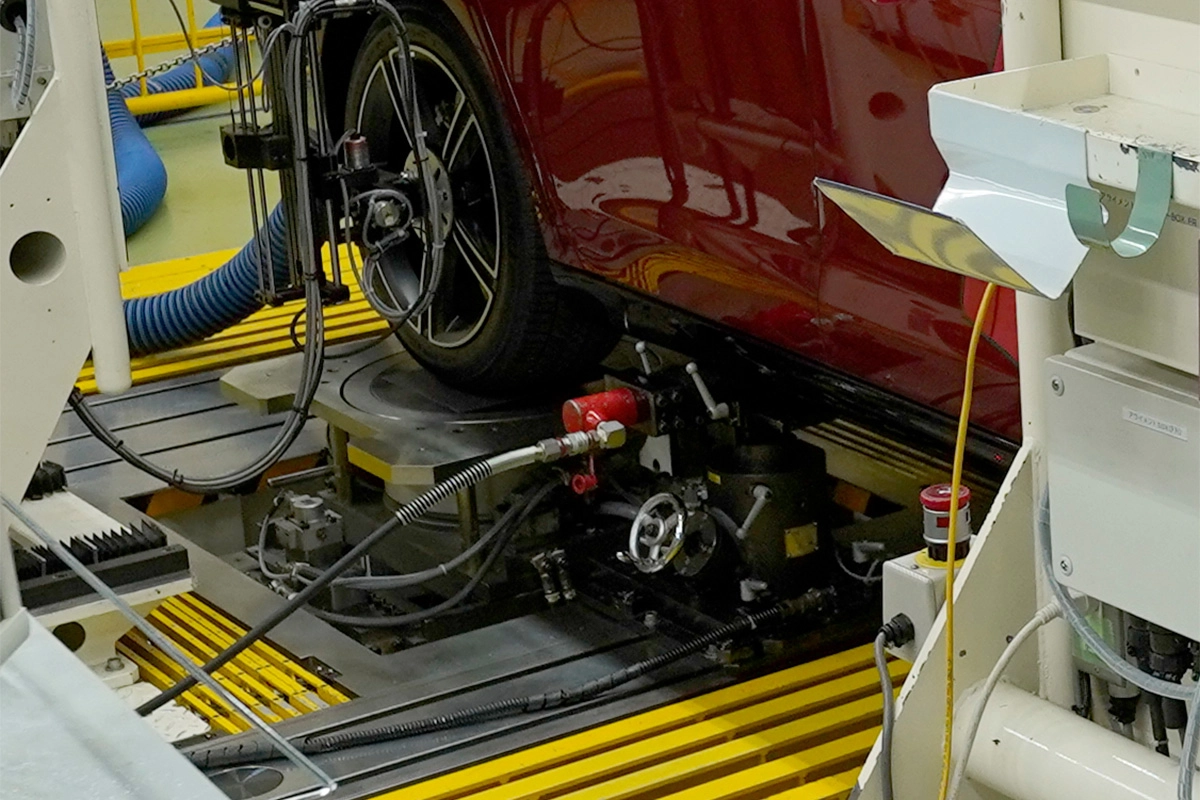
Test vehicle fixed to facility using jacking points
Suspension Tester
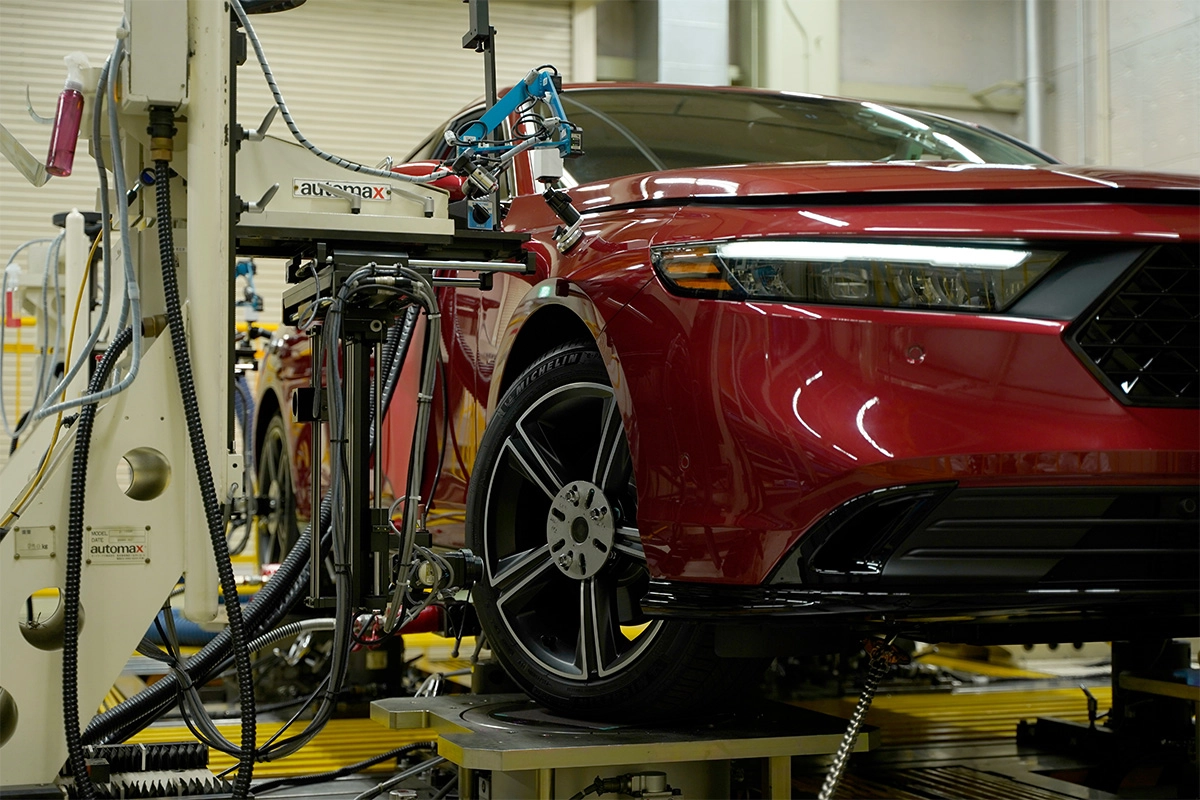
Suspension Tester
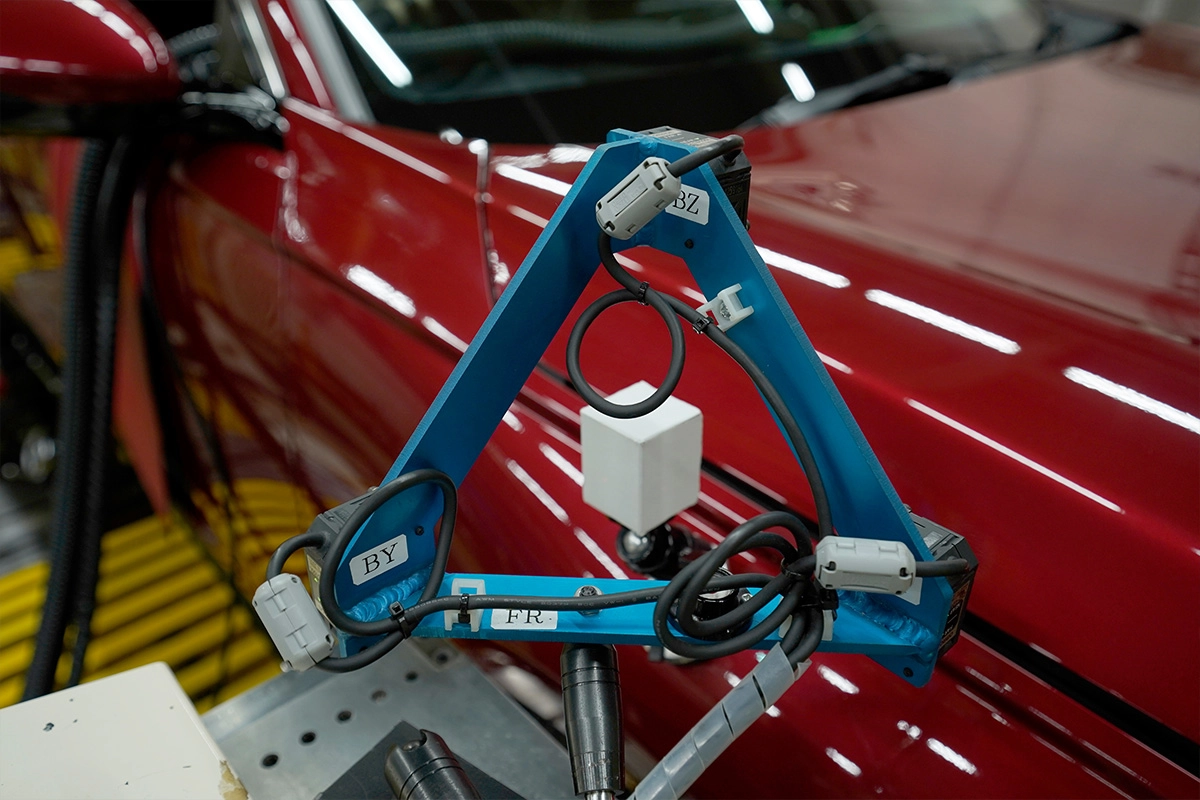
Laser displacement sensors
Suspension Tester
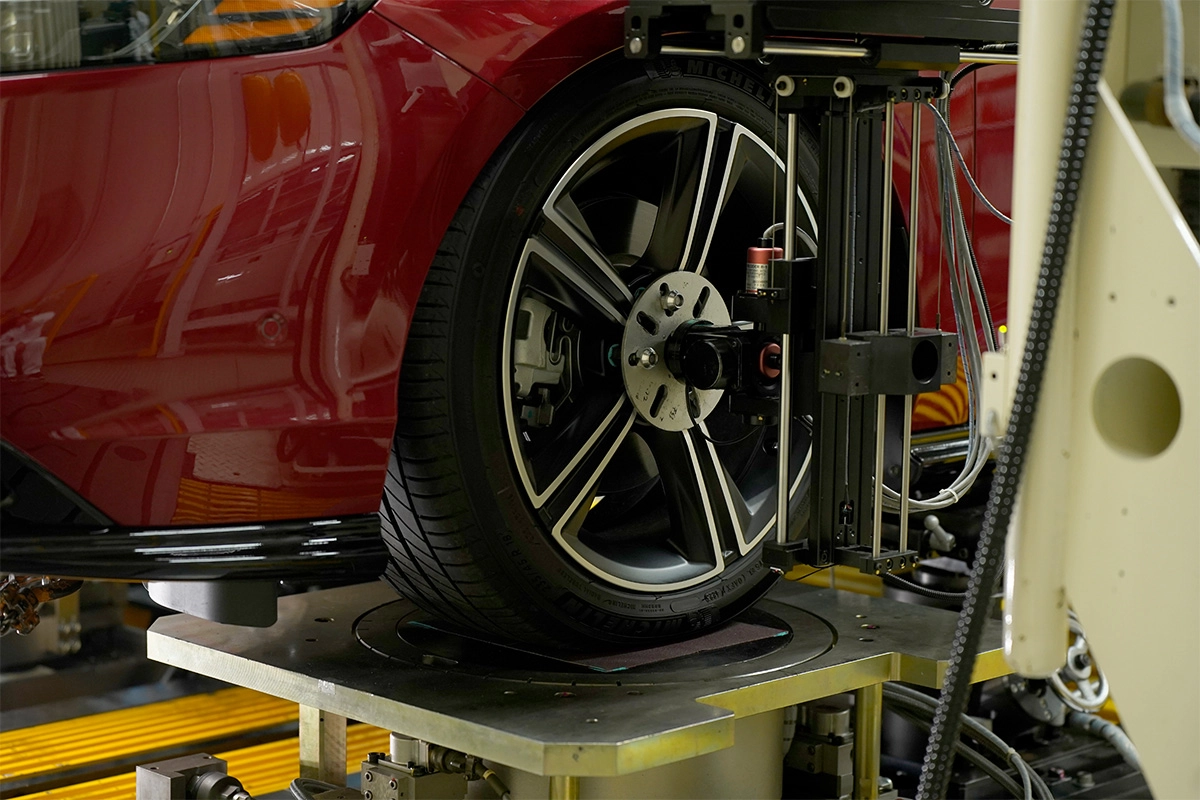
Suspension Tester
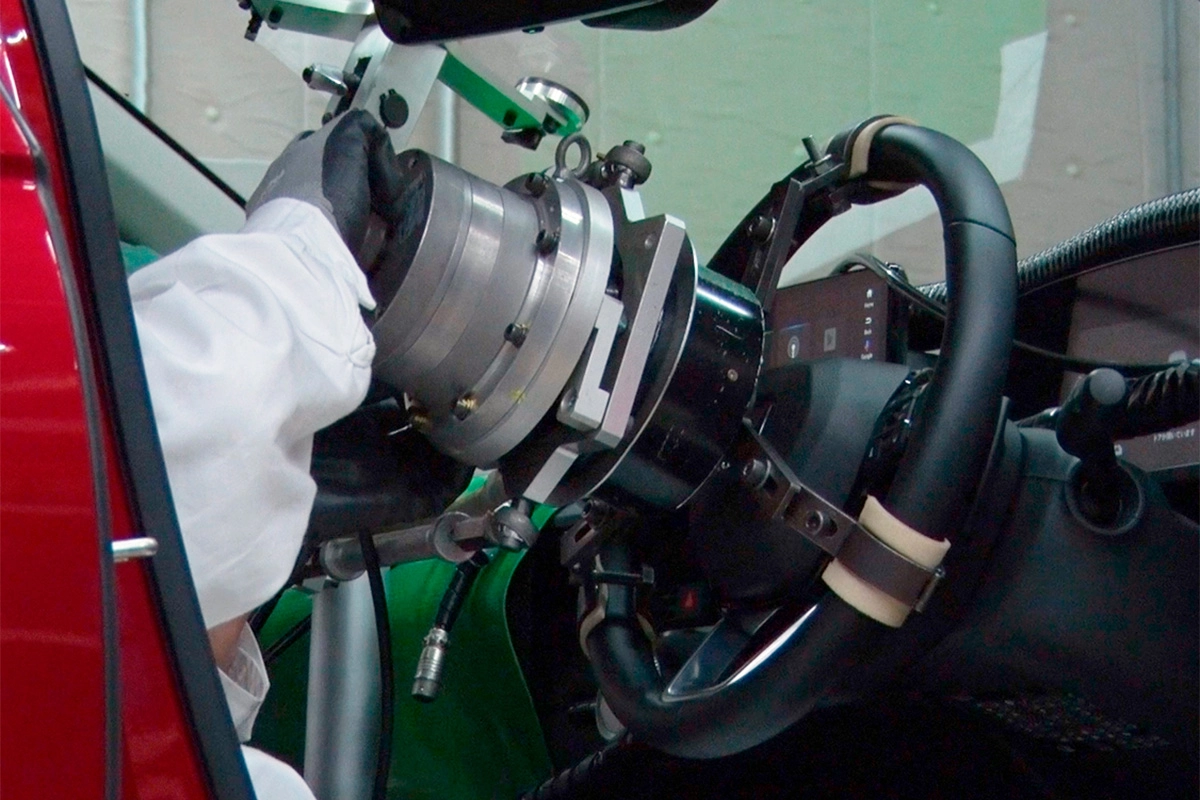
View of steering actuator installation
Control Room
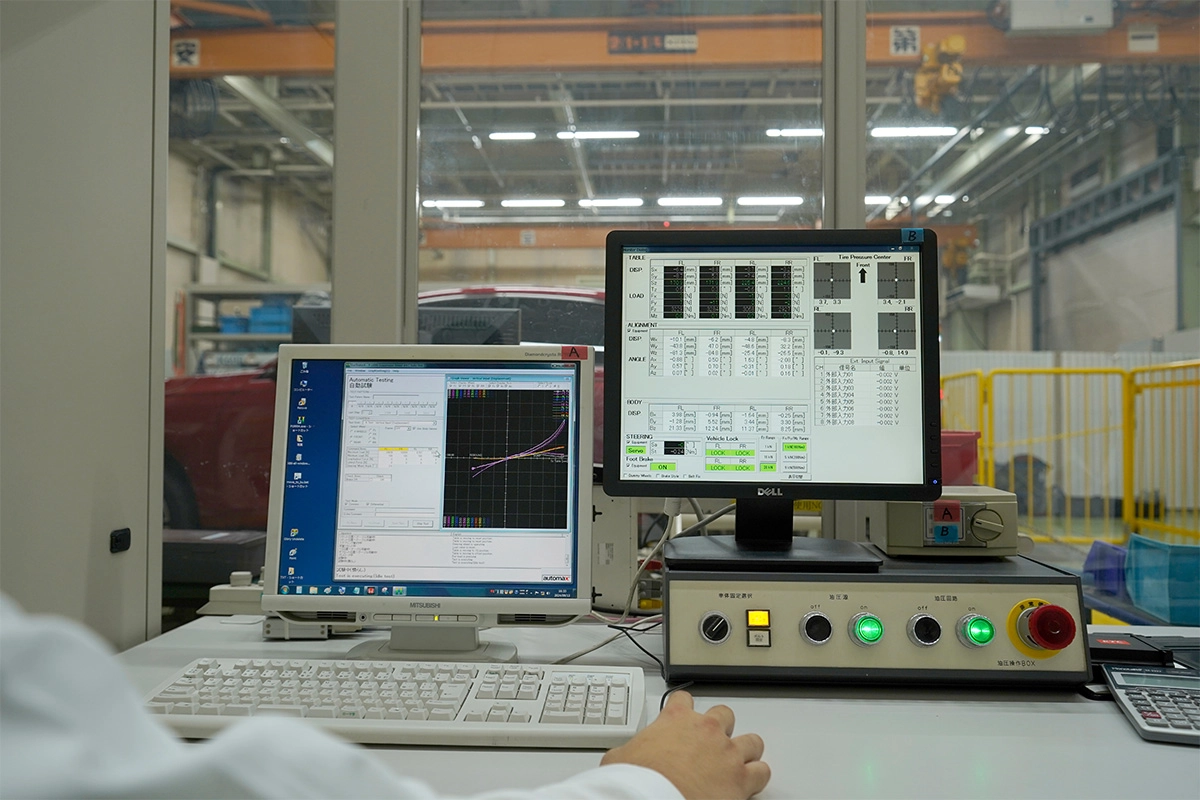

Today, simulation becomes much more important with recent AD/ADAS demand and the accuracy of the models, and data needs to be more precise accordingly. Additionally, the method to evaluate suspension characteristic without the vehicle body is being prepared to enhance development efficiency.
While cars are the quintessential mass-produced industrial product, they are also a special product that affects people's senses. Although there is a wish to enhance development efficiency to deliver products to customers quickly, Honda also wants to deliver handling and ride performance that appeal to the senses. This requires maximizing suspension performance, which is where the suspension tester demonstrates its value.
INDEX
Honda’s R&D Facilities
- Chapter 1 Honda’s R&D Facilities: Manufacturing Starts Here
- Chapter 2 Tochigi Proving Ground: The Road Decides the Product
- Chapter 3 Takasu Proving Ground: The Road Refines the Product
- Chapter 4 Full-Scale Wind Tunnel: Mastering the Wind with the Air as Our Ally
- Chapter 5 Bench Test Facilities: Forging the Core of Mobility
- Chapter 6 Environmental Testing Facilities (1): Fine-Tuning Honda Products in Extreme Environments
- Chapter 7 Environmental Test Facility (2): Tailoring Honda Products in Extreme Environments
- Chapter 8 3D Metal Printing: Speedy Creation of Innovative Shapes
- Chapter 9 Omni-Directional Collision Test Facility: Real-World Certification for Everything
- Chapter 10 XR Verification Facility: Virtual Reality Changing the Development Process
- Chapter 11 Driving Simulator: Fusing the Virtual and Physical Worlds for Automated Driving
TechnologyHonda’s R&D FacilitiesBench Test Facilities: Refining the Core of Vehicle Performance