The Honda Super Handling Challenge Chapter 10
The Future of Super Handling (2): Four-Motor EVs
The Honda Super Handling Challenge Chapter 10

In 2015, Honda participated in the Pikes Peak International Hill Climb (PPIHC) with a four-motor electric vehicle, based on the CR-Z, that it named “Electric SH-AWD with Precision All-Wheel Steer.” Although the development team, comprised mainly of young engineers, split up after the race, it reformed again with young engineers for a short period of intensive development ahead of participation in the 2016 PPIHC.
As in 2015, the purpose of participating in the PPIHC was to confirm the effectiveness of torque vectoring achieved through freely controlled motors on each wheel. The base vehicle for the 2016 race was the second-generation NSX. Development of a dedicated racing car would also have been within the rules, but Honda was committed to competing with a model shaped like a mass-production car. It therefore chose to use the second-generation NSX, which was introduced to the North American market in 2015 (and later introduced to Japan in August 2016). The body was made of carbon fiber reinforced plastic (CFRP), with dimensions based on the external panels of the mass-production NSX and modified in a number of ways, including fenders that protruded slightly.
First Model Developed for the 2016 PPIHC

























In compliance with PPIHC regulations, the frame was constructed of steel tubing, with specifications completely different from the mass-production NSX, which used a multi-material space frame with a focus on aluminum extrusions. The front- and rear-mounted Twin Motor Units (TMUs) were the same as on the car used in 2015, but newly developed for the 2016 model instead of the mass-production TMUs from the 2015 model.
Layout

In line with the concept of focusing on commonality, the 2015 model was based on the mass-production CR-Z and its various components were based on mass-production parts. For this reason, Honda narrowed the focus for the PPIHC, not to prioritizing the fastest time, but to verifying the effectiveness of torque vectoring.
While they chose to enter the Exhibition Class (mass production prototype) in 2015, they changed to the Modified EV Class (unlimited EV division) in 2016. The goal in 2016 became to win against EVs developed for racing, with a model shaped like a mass-production car, and to better the fastest time in the class the previous year by finishing in less than nine minutes. Compared to its finish time of 10 minutes 23.829 seconds in the Exhibition Class in 2015, this meant a dramatic increase in performance was needed.
The aim was to develop a car with around twice the maximum system output as the previous year. The TMUs used on Sport Hybrid SH-AWD-equipped Legend and NSX models had motor output shafts extending to the planetary reduction gear mechanisms located at the center of the vehicles, with the drive shafts going in the opposite direction within the hollow output shafts.
The configuration was changed for the “4-Motor EV Concept,” which made its appearance at the 2016 PPIHC, with output shafts moved to the outside of the motors and a parallel shaft arrangement used for reduction instead of planetary gears. This enabled use of drive shafts with a greater diameter to provide higher rigidity, and it enabled the heavy motors to be mounted at a lower position, in expectation of a favorable impact on vehicle driving performance. With the experience of having competed in 2015, Honda was also able to optimize the number of motor windings and poles with consideration given to factors such as balancing output and heat generation.
Although the 2015 model was equipped with Precision All-Wheel Steer (P-AWS), to enable independent steering of the left and right rear wheels, this was not used on the 2016 model to enable a narrowed focus on functional verification of four-motor torque vectoring.
The following illustrations describe examples of torque vectoring control based on information such as steering angle, gas pedal position, vehicle speed, lateral G-forces, and yaw rate.
2016 Model Four-Motor EV Torque Vectoring Control











Starting at an altitude of 2,862 m, the hill climb at Pikes Peak in Colorado, U.S.A., covers a distance of about 20 km until the finish line at 4,301 m, with participants racing against the clock around 156 corners. Celebrating the 100th anniversary of the PPIHC, 100 cars competed across eight classes in 2016.
Racing in the Modified EV Class, the 4-Motor EV Concept finished the final in a time of 9 minutes 6.0 seconds, coming in second place in its class and third place overall. Although missing the goal of finishing in less than nine minutes, the car did confirm the expected performance. Comparing performance against its more powerful competitors around the tight corners, corner exit profiles showed that Honda’s car accelerated out of corners faster than the others, thereby confirming the effectiveness of torque vectoring.
While torque vectoring also had value in terms of speed, the more important achievement was that the car behaved as expected and did not feel uncomfortable for the driver. An ideal car can deliver this performance at a high level. For example, cars might behave as expected on dry paved roads but not on slippery road surfaces. The car has to turn when the steering wheel is turned, and accelerate when the gas pedal is pressed. To stop when stepping on the brake. We take it for granted that a car does these things, but it has to do them regardless of the road conditions. This alleviates stress and allows the driver to drive with confidence.
High repeatability is important as well. If the car does not turn as expected, or stop as expected, it has to be driven with an additional margin for error. It is important that the car always behaves the same way even if the conditions change or outside disturbances are introduced.
2016 PPIHC Race Car Photos






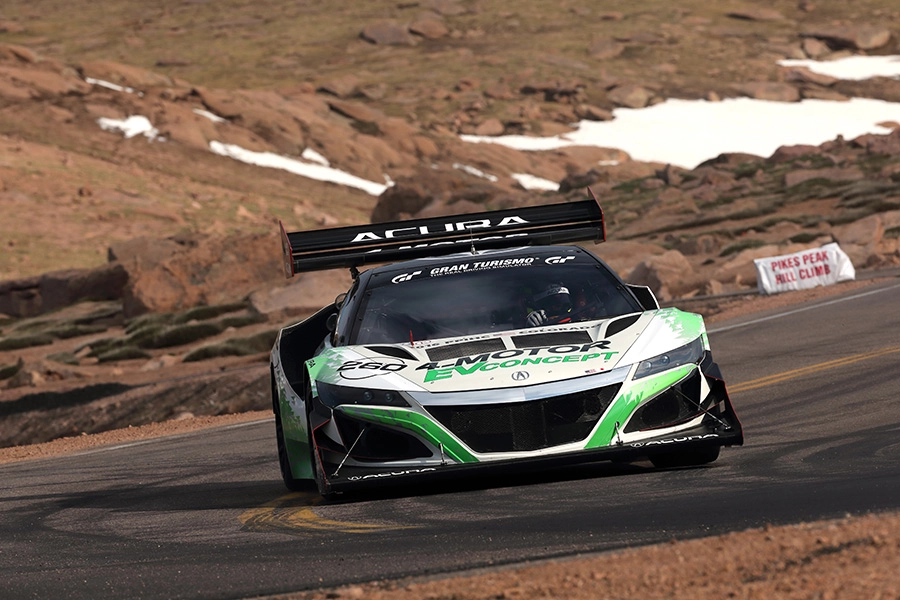







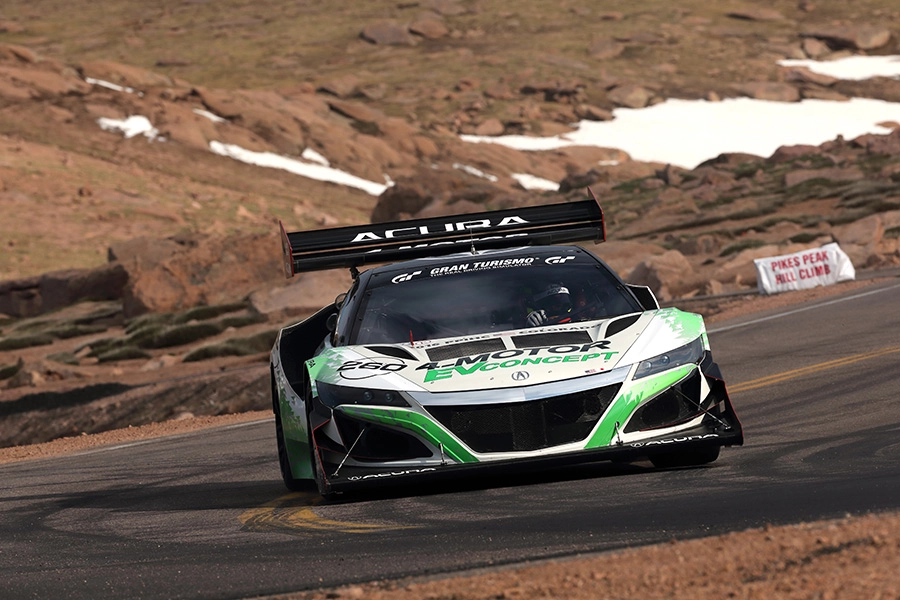




Honda has been refining its four-motor torque vectoring technology to achieve this level of driving performance. By competing in the time trials, on a cliff-side course without guardrails and in a harsh environment with dramatic changes in air temperature, air pressure, and weather, it was able to verify technologies in a car that acted as expected and at the will of the driver. The race also enabled Honda to collect valuable data that will take it to the next level. As the first to start developing a four-motor EV, Honda proved the effectiveness of its system at the PPIHC.
However, there is no end to the development of Super Handling technologies, including torque vectoring, that allow the driver to enjoy at-will handling of the car. With an ongoing focus on refining human-centric technologies, Honda’s goal will always be to develop technologies that enhance the joy of mobility.
The Honda Super Handling Challenge
- Chapter 1 Honda Four-Wheel Steering System (4WS) Technology – 1987
- Chapter 2 Active Torque Transfer System (ATTS) Technology – 1996
- Chapter 3 Variable Gear Ratio Steering (VGS) Technology – 2000
- Chapter 4 Super Handling All-Wheel Drive™ (SH-AWD®) Technology – 2004
- Chapter 5 Rear Toe Control System: Precision All-Wheel Steer Technology – 2012
- Chapter 6 Legend’s Sport Hybrid SH-AWD® Technology, a Three-Motor Hybrid System – 2014
- Chapter 7 NSX’s Sport Hybrid SH-AWD® Technology, a Three-Motor Hybrid System – 2015
- Chapter 8 Honda’s Concept of Dynamic Performance
- Chapter 9 The Future of Super Handling (1): Four-Motor EVs
- Chapter 10 The Future of Super Handling (2): Four-Motor EVs
TechnologyHonda Super HandlingThe Future of Super Handling (2): Four-Motor EVs