The Honda Super Handling Challenge Chapter 6
Legend’s Sport Hybrid SH-AWD® Technology, a Three-Motor Hybrid System – 2014
The Honda Super Handling Challenge Chapter 6
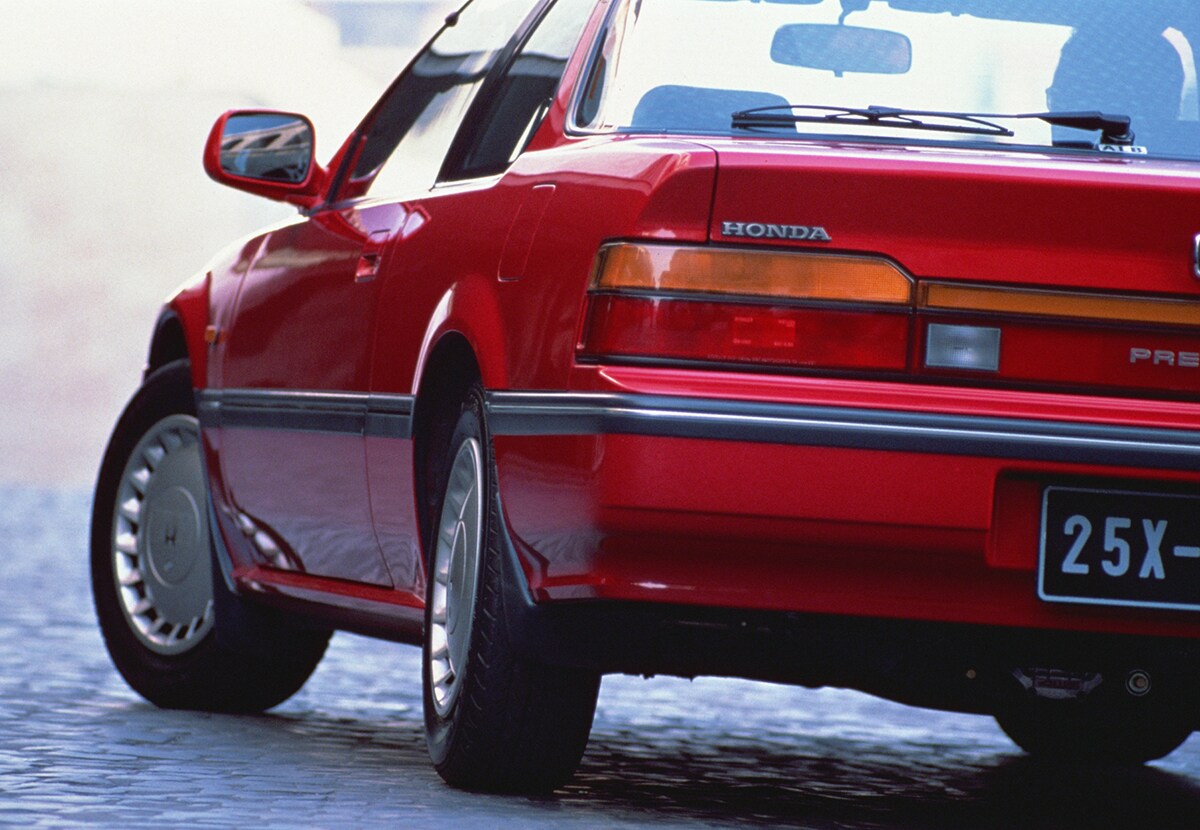
Ever since Honda began producing cars, it has chosen and implemented the most appropriate systems for the times, continually developing new technologies and creating cars that perform at the will of the driver. Following four-wheel steering (4WS) in 1987, the Active Torque Transfer System (ATTS) in 1996, and Variable Gear Ratio Steering (VGS) in 2000, Honda developed the world’s first Super Handling All-Wheel Drive (SH-AWD) system with the ability to freely control torque distribution between the front and rear wheels, and between the left and right rear wheels, in 2004 and debuted the technology on the fourth-generation Legend.
The SH-AWD system was designed to improve the dynamic performance of cars by utilizing driving torque to increase not only driving performance, but turning performance as well. The technology uses torque vectoring to create a torque differential between the left and right wheels. By applying greater driving torque to the outer wheel than to the inner wheel when accelerating in a turn, a yaw moment is generated around the center of gravity, which has the effect of helping the vehicle to turn.
With the SH-AWD system, the rear drive unit is driven by power transmitted from the engine via the transfer mechanism. Because of this, torque vectoring was effective when accelerating in a turn if the engine was producing sufficient torque, but it had limited effectiveness in normal driving scenarios.
In 2012, Honda unveiled the Sport Hybrid SH-AWD, a three-motor hybrid system, for the first time at Honda Meeting 2012, its technology event for members of the press. Its strategy behind building out the Sport Hybrid range, which includes the one-motor Intelligent Dual Clutch Drive (i-DCD) hybrid used in the Fit and the two-motor Intelligent Multi-Mode Drive (i-MMD) hybrid used in the Accord, was to establish different hybrid systems for different applications.
Sport Hybrid SH-AWD was used for the first time on the fifth-generation Legend announced on November 10, 2014. Then in 2016, it was used on the second-generation NSX, with a midship layout, as a technology bringing new fun to driving.
The Sport Hybrid SH-AWD system used on the Legend is equipped with two rear-mounted motors that enable highly responsive torque vectoring to the left and right rear wheels regardless of the level of driving torque generated by the front-mounted engine. In this way, the previously-limited torque vectoring effect has been expanded in the SH-AWD system, making it effective in normal driving scenarios as well. It has greatly expanded the “at will” control of the car, ensuring the car moves as expected for reassuring turning performance.
Sport Hybrid SH-AWD system configuration diagram (Legend photographed)
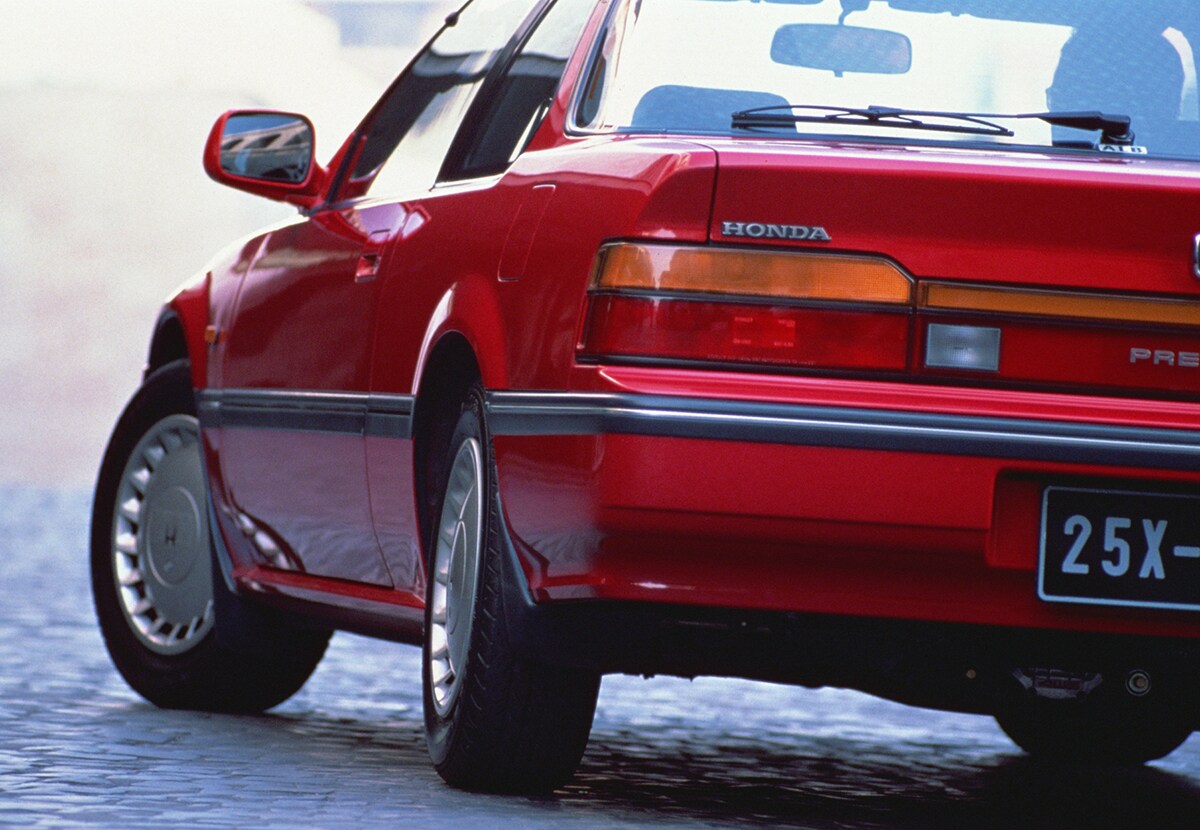
Sport Hybrid SH-AWD system configuration and layout are explained below.
● 3.5-liter V6 direct-injection i-VTEC engine mounted in the front, combined with a 7-speed dual clutch transmission with built-in high-output motor (max. output of 35 kW at 3,000 rpm, and max. torque of 148 Nm at 500–2,000 rpm)
● Power Drive Unit (PDU), located within the center console, to optimally control each motor
● Intelligent Power Unit (IPU), with built-in high-capacity lithium-ion battery, mounted in the rear
● Twin Motor Unit (TMU), enabling torque vectoring to the left and right rear wheels, mounted within the rear sub frame
Designed for compact storage within the rear sub frame, the TMU comprises two newly developed motors with dramatically reduced torque fluctuations (ripple) when rotating, planetary reduction gear mechanisms, one-way clutch, and brake. While compact, the new motors are able to deliver high output and high torque (max. per-motor output of 27 kW at 4,000 rpm, and max. per-motor torque of 73 Nm at 0–2,000 rpm) using high-performance magnets and high-efficiency electromagnetic steel sheets.
TMU system configuration diagram
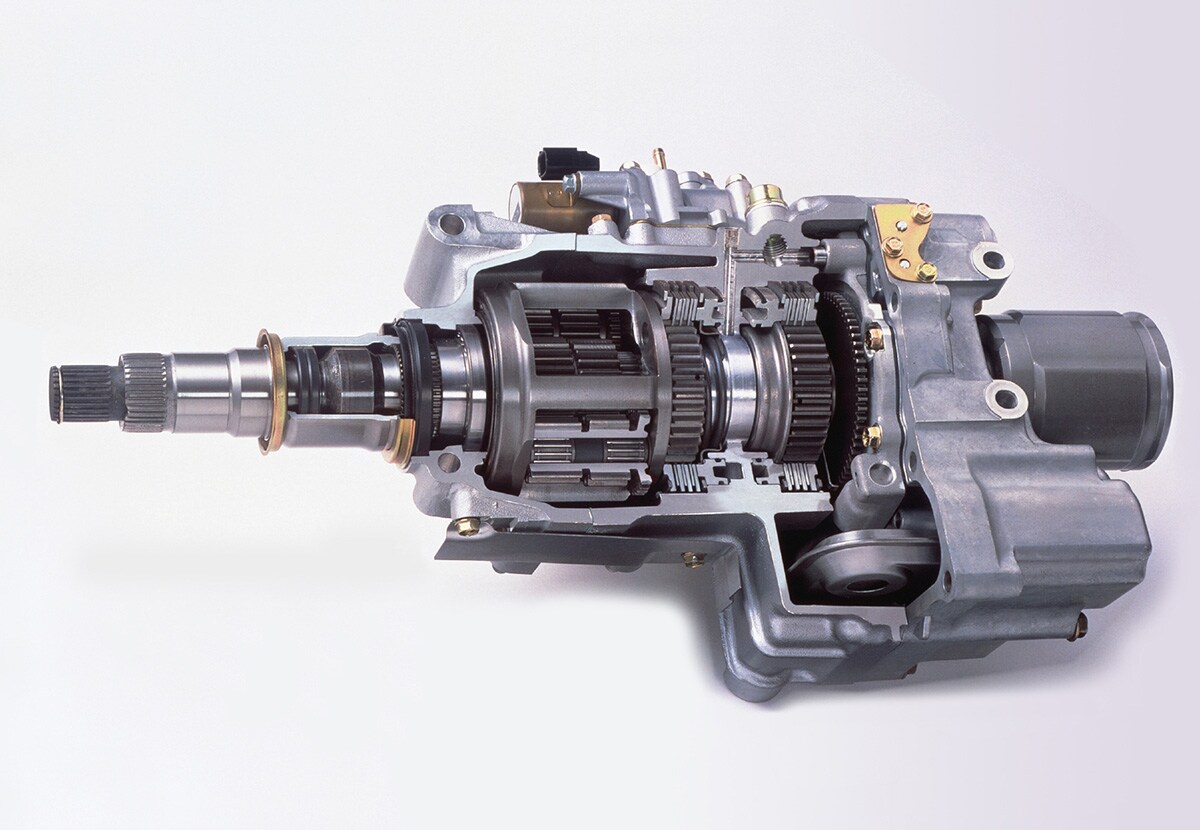
The planetary gear-based reduction gear mechanisms built in to the motors comprise a sun gear directly connected to the motor shaft, three double-pinion gears that mesh with the sun gear, a planetary carrier that supports the double-pinion gears, and an outer ring gear. They reduce motor speed by roughly one-tenth while increasing torque roughly tenfold to drive the wheels.
The brake is used to lock or release the ring gear. The one-way clutch restricts reaction force, acting on the planetary reduction gear mechanism's ring gear, to the traveling direction only, which reduces brake load (and contributes to energy efficiency).
Torque is transmitted in the following manner.
1. The motor rotates the sun gear.
2. The sun gear rotates the double-pinion gears.
3. The double-pinion gears rotate the planetary carrier because the ring gear is fixed.
4. The planetary carrier rotates the wheel via the axle shaft and drive shaft.
Planetary reduction gear mechanism configuration diagram
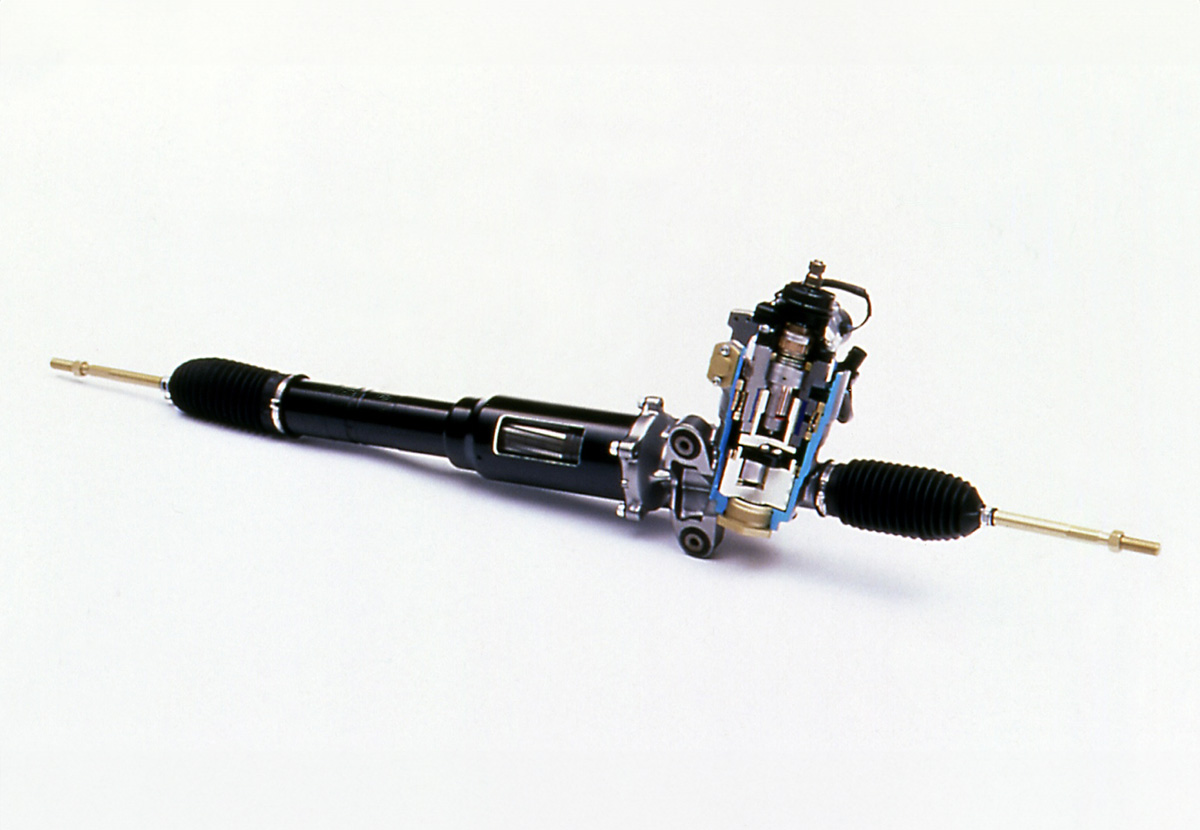
TMU in operation (video)
The TMU employs a brake to lock the ring gears in place to efficiently transmit motor torque to the drive shaft. On the other hand, when the ring gears are fixed, there is a risk of the motors exceeding their allowable maximum rpm at high speeds due to the proportional relationship between the rotational speed of the motors and wheels. For this reason, the ring gears are released by the brake at high speeds, making them freely rotatable, to protect the motors by allowing them to rotate without being affected by wheel speed.
The TMU’s two motors independently control driving torque to the left and right rear wheels without relying on engine torque or front wheel driving torque. They can also be used for torque vectoring during deceleration by controlling motor resistance during regenerative deceleration. Furthermore, by applying positive torque to the outside wheel and negative torque to the inside wheel, the system generates a higher yaw moment toward the inside of the turn than is possible with the conventional SH-AWD system.
Torque vectoring illustration
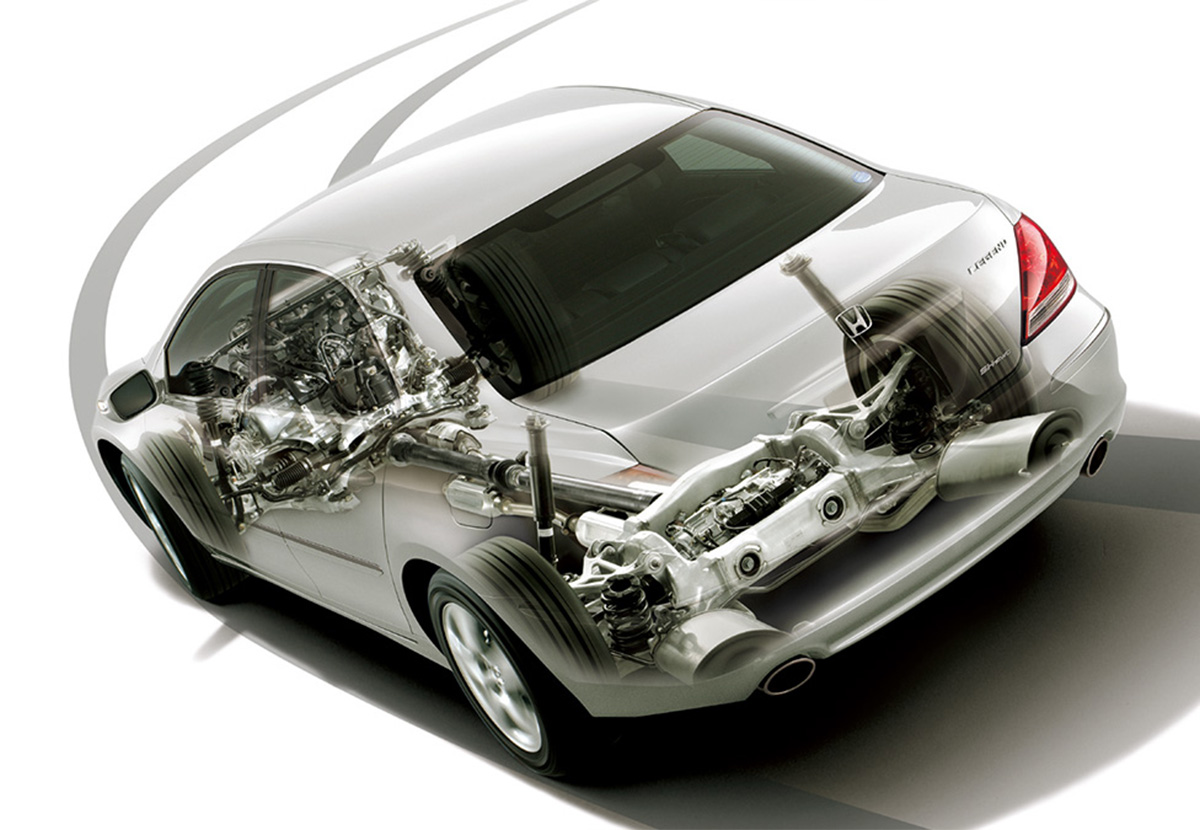

When a car enters a corner with initial braking and then exits it, negative torque (regenerative braking mode) is applied to the left and right rear wheels during the turn-in phase of the corner (decelerating in turn). The system applies a greater negative torque to the inside wheel than to the outside wheel to generate a yaw moment toward the inside of the turn, which achieves outstanding steering response even when braking into the corner.
In the corner, positive torque is then applied to the outside rear wheel and negative torque is applied to the inside rear wheel to generate a larger yaw moment toward the inside of the turn. This delivers outstanding line tracing performance even in sharp corners.
When exiting the corner, the system applies positive torque to both rear wheels to deliver powerful acceleration. With greater torque applied to the outer wheel than to the inner wheel, distribution of torque is optimized to the corner, which improves stability.
When debuted on the fourth-generation Legend in 2004, the SH-AWD system distributed engine driving torque between the front and rear wheels, and also between the left and right rear wheels. It was effective in improving line tracing performance when accelerating in turns, and in creating a sense of all four wheels tightly turning together. For this reason, it’s selling point was the considerable effect that could be felt mainly when driving on winding country roads. With the development of Sport Hybrid SH-AWD, on the other hand, which debuted advanced motor-based torque vectoring on the fifth-generation Legend in 2014, the goals were redefined to include the following five “normal driving” scenarios in addition to winding country roads, with the control technology being developed to achieve the desired effects.
● Improved maneuverability when turning left or right at intersections (generation of yaw moment in the turning direction)
● Agile and smooth turn-in characteristics when turning to enter traffic on an expressway after passing through the toll booth (generation of yaw moment in the turning direction)
● Reassuring high-speed stability when changing lanes on an expressway (generation of yaw moment in the turning suppression direction)
● Smooth and tolerant at-limit behavior when undertaking emergency avoidance measures (generation of yaw moment in the turning suppression direction)
● Reassuring handling stability on snow-covered roads regardless of road condition (selectable control for low-mu road surfaces)
The core of Sport Hybrid SH-AWD is feedforward control, which achieves vehicle behavior that is both highly responsive and faithful to the driver’s intention. However, relying on feedforward control only can result in reduced control performance due to changes in vehicle characteristics or road conditions, so the control configuration also includes feedback control to ensure stability.
Feedforward control is used to determine distribution of driving torque between front and rear wheels, and between the left and right rear wheels, in line with the driver’s intentions (steering wheel and gas pedal operation) and the degree of turning (lateral acceleration). Front/rear driving torque distribution control adjusts the amount of torque distributed to the rear wheels in line with the driver’s acceleration intention and the degree of turning. The goal is to equalize loads across the front and rear wheels in response to rearward load-shift under acceleration and steering-related lateral forces applied to front wheels.
Similarly, left/right driving torque distribution control determines driving torque for the left and right rear wheels by calculating additional yaw moment required in accordance with the driver’s intentions and degree of turning. The Sport Hybrid SH-AWD system is able to generate yaw moment from the TMU without relying on engine torque, demonstrating the effect of torque vectoring in normal driving scenarios that use comparatively less acceleration.
Utilizing these characteristics, the basic control generates a large turning yaw moment to increase response gain in low-speed scenarios, where response gain in response to steering is low, depending on vehicle speed and steering wheel angle. On the other hand, in high-speed scenarios, where the response gain is high, yaw moment is generated in the turning suppression direction to achieve vehicle stability.
Determining whether to generate a (positive) turning yaw moment or a (negative) turning suppression yaw moment based only on vehicle speed can make vehicle occupants uncomfortable. For this reason, gas pedal position and lateral speed are used together with vehicle speed to determine switching between positive and negative yaw moments to give a more natural feeling to operation.
Differential control has also been added to issue control instructions according to the speed at which steering wheel angle and gas pedal position are changed. This improves the initial yaw rate response to steering and improves control of vehicle posture when pressing the gas pedal, and has achieved more direct and agile vehicle movement in line with driver operation.
The purpose of feedback control is mainly to improve stability in relation to changes in vehicle characteristics, including by improving transient stability during emergency steering operation and suppressing excessive tuck-in. Therefore, the TMU not only generates yaw moment in the more stable direction (turning suppression), but it also increases torque distribution to the front wheels to suppress rear wheel skidding, which achieves a more stable vehicle behavior.
Sport Hybrid SH-AWD comes with more refined versions of these controls to demonstrate its effectiveness not only in the tight turning performance on winding roads that the original SH-AWD was aimed at, but also in the goals of the five normal driving scenarios above. The result is a technology that contributes to agile and reassuring driving performance in a wide variety of driving scenarios.
Sport Hybrid SH-AWD (promotional video, 2014)
The Honda Super Handling Challenge
- Chapter 1 Honda Four-Wheel Steering System (4WS) Technology – 1987
- Chapter 2 Active Torque Transfer System (ATTS) Technology – 1996
- Chapter 3 Variable Gear Ratio Steering (VGS) Technology – 2000
- Chapter 4 Super Handling All-Wheel Drive™ (SH-AWD®) Technology – 2004
- Chapter 5 Rear Toe Control System: Precision All-Wheel Steer Technology – 2012
- Chapter 6 Legend’s Sport Hybrid SH-AWD® Technology, a Three-Motor Hybrid System – 2014
- Chapter 7 NSX’s Sport Hybrid SH-AWD® Technology, a Three-Motor Hybrid System – 2015
- Chapter 8 Honda’s Concept of Dynamic Performance
- Chapter 9 The Future of Super Handling (1): Four-Motor EVs
- Chapter 10 The Future of Super Handling (2): Four-Motor EVs
TechnologyHonda Super HandlingLegend’s Sport Hybrid SH-AWD® Technology, a Three-Motor Hybrid System – 2014