The Honda Super Handling Challenge Chapter 1
Honda Four-Wheel Steering System (Honda 4WS) Technology – 1987
The Honda Super Handling Challenge Chapter 1
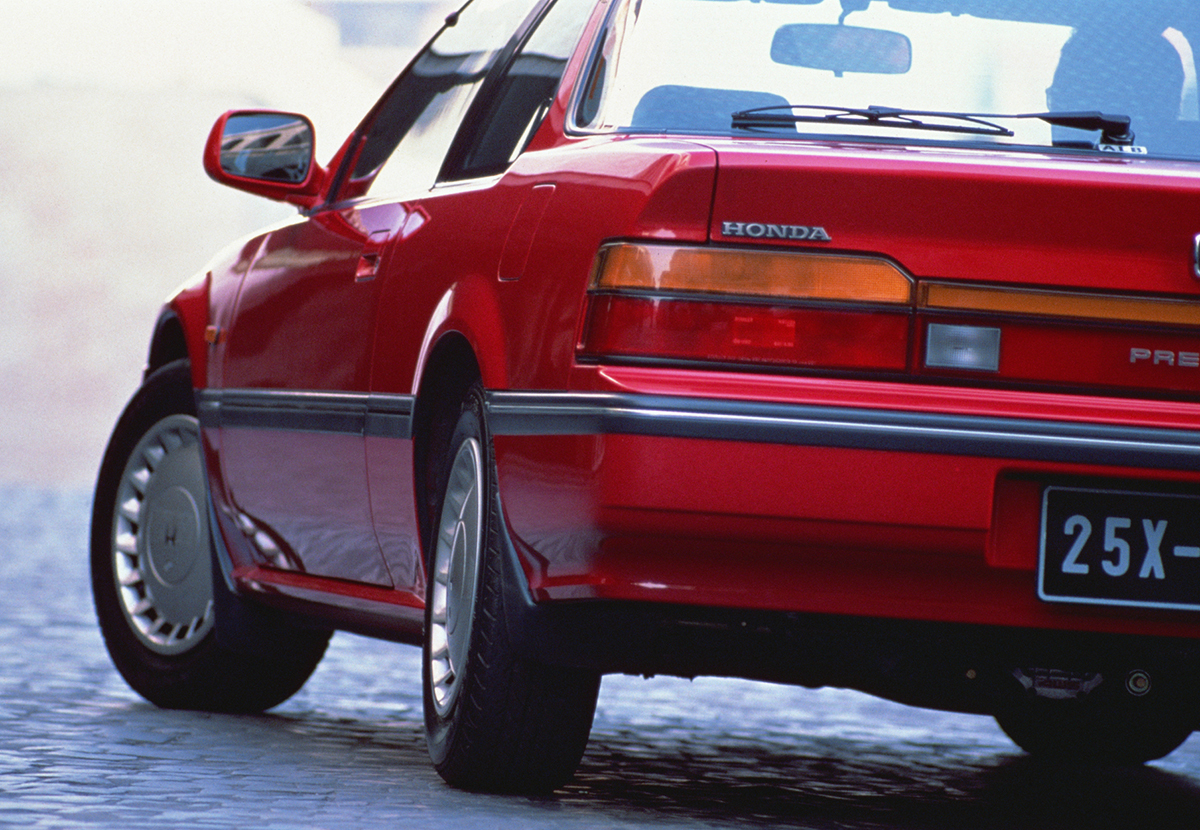
Four-wheel steering (4WS) is a system that steers the vehicle using not only the front wheels, but the rear wheels, as well. In 1987, Honda introduced the world’s first steering angle sensing 4WS system in the Prelude. At the time of the launch, the name of the technology was Steering Angle Sensing Honda Four-Wheel Steering System (Honda 4WS).
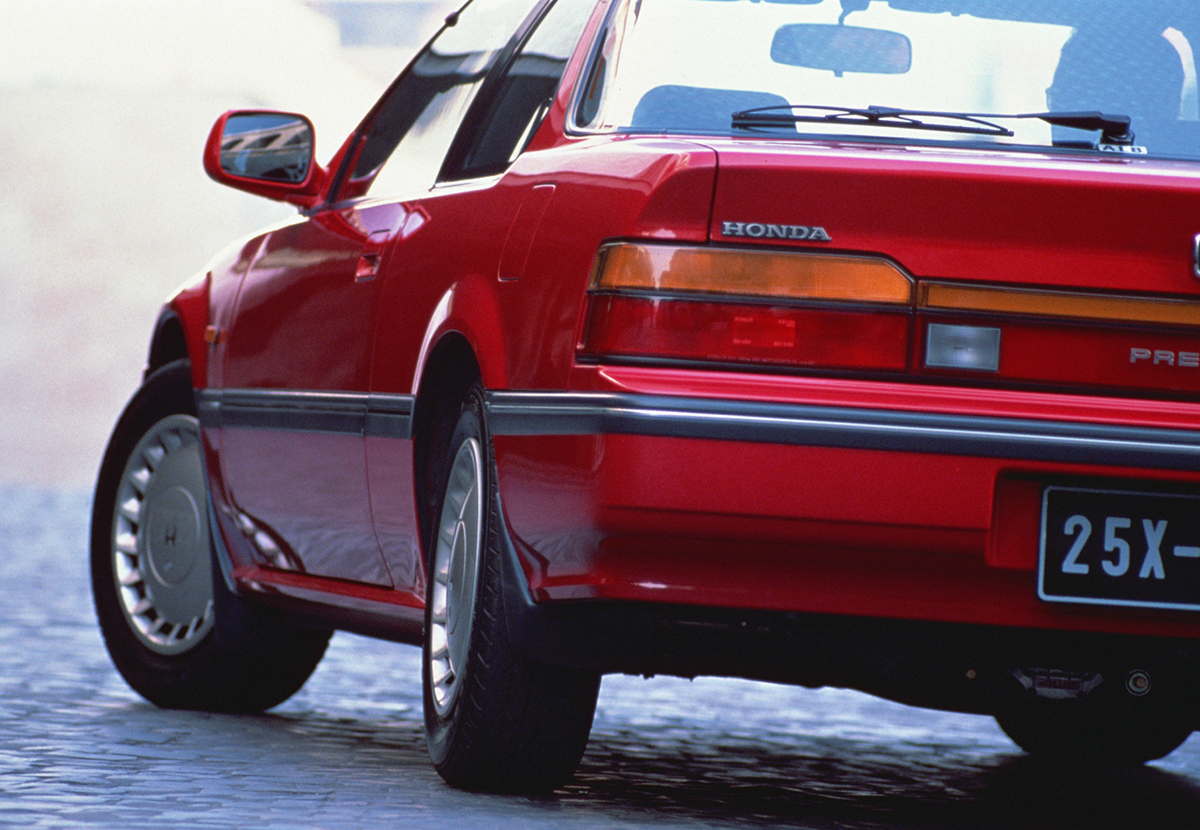
Honda 4WS is a mechanical system that steers the front and rear wheels in the same direction (in phase) or opposite directions (reverse phase) depending on the steering angle. At high speeds, steering angles are typically small, such as when changing lanes, so the rear wheels are turned in the same direction as the front wheels. When greater maneuverability is desired while driving at low speeds, such as on narrow roads or parking the vehicle in a garage, the steering angle would be large, so the rear wheels are turned in the opposite direction to the front wheels. This system achieves both agile and stable maneuvering characteristics and a small turning radius.
The development of Honda 4WS began with the goal of improving active safety. In the 1970s, the National Highway Traffic Safety Administration (NHTSA) in the U.S. proposed the Experimental Safety Vehicle (ESV) program. NHTSA’s goal was to address the issue of the continuing rise of traffic collisions from the perspectives of passive safety (collision mitigation and active safety (collision avoidance).
Honda decided to participate in this ESV program, but at the time, Honda was only producing mini-vehicles (Japanese kei-cars) and was in the process of planning and prototyping for the production of compact cars. It was obvious that implementing measures to improve passive safety in compact cars would lead to a significant increase in vehicle weight and a reduction in interior space, which would undermine the economical efficiency that is the strong point of compact cars. Therefore, Honda decided to focus on improving active safety and to pursue research on technologies to improve maneuverability, stability and dynamic performance.
The 4WS system was the result of many studies. It was known in theory that reducing the response delay of the vehicle’s lateral movement would be effective in improving collision avoidance performance. By controlling the rear and front wheels simultaneously with a 4WS system, the vehicle would change its course without delay in response to the driver’s steering wheel operation. As a result, collision avoidance performance and, thus, overall safety would be enhanced.
The development of Honda 4WS began in 1977. First, the team set out to build a theoretical model of four-wheel steering, and came to the conclusion that the rear wheels should be turned in the same direction as the front wheels at high speeds, and in the opposite direction at low speeds. In 1978, Honda filed for a basic patent and, in 1979, presented an academic paper at the ESV International Conference. In 1981, a test car was built by joining the front halves of two first-generation Accords. Testing of this car on the west course of the Suzuka Circuit proved the theory correct.
Honda initially considered a speed-linked 4WS system, in which the rear wheels turn in the same direction as the front wheels at high speeds and in the opposite direction at low speeds. However, it was pointed out that this system would be too complex to be marketable, so a simpler, steering angle sensing mechanism was considered and adopted. Under normal conditions while driving along a road, the steering angle is small. On the other hand, when parking in a garage or making a U-turn, the vehicle is driven at a low speed. By turning the rear wheels in the same direction as the front wheels at small steering angles and in the opposite direction at large steering angles, the desired functionality is achieved.
With conventional 2WS, only front wheels change direction when the steering wheel is turned. When the steering wheel is turned while the vehicle is moving, the front tires rotate while slipping sideways, creating a slip angle between the tire surface and the direction of travel, which generates cornering force, the lateral force at right angles to the direction of travel. When cornering force is generated, the vehicle changes its direction of travel, which generates a yaw moment around the vehicle's center of gravity. This also generates a sideslip angle on the rear tires, which generates cornering force supporting the vehicle's turning motion.
With 4WS, the rear wheels simultaneously turn in the same direction as the front wheels, generating cornering force in the rear tires with greater responsiveness than 2WS, which makes the vehicle's turning motion smoother. Reducing the yaw moment to be generated while turning is also technically possible, leading to improved stability.
Honda announced the Honda 4WS technology in October 1986, and in the following year, launched the Prelude, with the steering angle sensing Honda 4WS as optional. This system consisted of two steering gearbox sub-systems (front and rear) mechanically connected by a center shaft. Initially, a single-crank mechanism was considered, but it would only allow steering of the front and rear wheels at the same angles (both in-phase and reverse-phase). If the steering angle is set for high speeds (smaller angles), the steering angle at low speeds (reverse phase) would also be smaller, reducing the effectiveness of the system.
4WS System
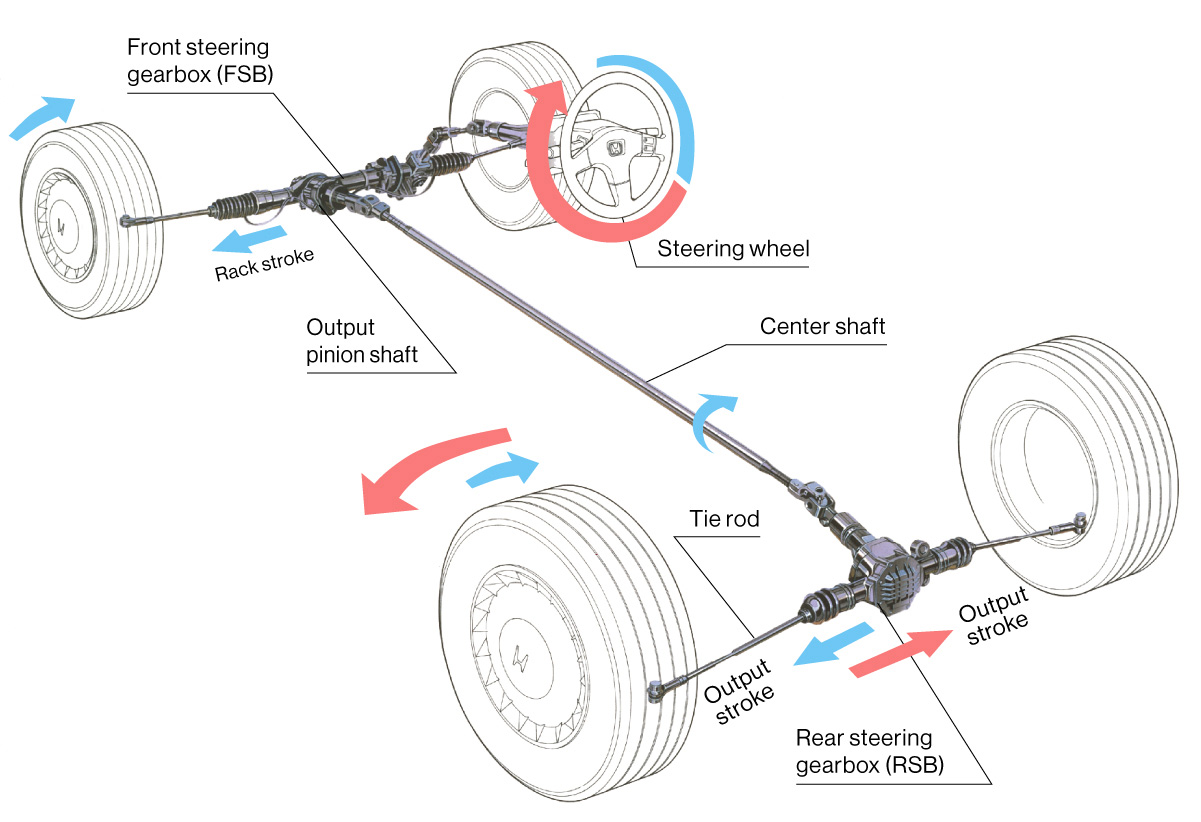
This problem was solved by incorporating a double-crank system (which combines two crank mechanisms), where small steering angle resulted in small in-phase rear wheel steering, and large steering angle resulted in large, reverse-phase turning.
The front steering gearbox is a typical rack-and-pinion system. When the steering wheel is turned, the steering shaft rotates, and the pinion gear attached to the end transmits force and moves the rack (a long, thin, geared plate), changing the direction of the front wheels through tie rods attached to the end of the rack. The horizontal movement of the rack is transmitted to the output pinion shaft and converted into rotational motion, which is transmitted through the center shaft under the floor to the rear steering gearbox.
The rear steering gearbox consists of an eccentric shaft, planetary gear, internal gear, slider, guide, and stroke rod. Input from the center shaft rotates the eccentric shaft, which functions as the first crank. The planetary gear attached to the eccentric shaft meshes with the internal gear fixed in the gearbox. The planetary gear, which receives power from the eccentric shaft, rotates in the opposite direction while revolving around the internal gear. The planetary gear, which functions as the second crank, also has an eccentric shaft, which moves by combining the two motions of rotation and revolution. The slider and guide absorb the vertical movement of the planetary gear eccentric shaft and transmit only the horizontal movement to the stroke rod. The rear wheels are steered via the tie rods.
The Prelude’s lock-to-lock was set to 2.5 turns of the steering wheel. In terms of steering wheel angle, this is 900 degrees, or 450 degrees from the center (neutral) position. For the front steering, the inner tire turns slightly more than the outer tire to a maximum angle of around 35 degrees (both inner and outer tires).
Rear Steering Gearbox Structure

Rear wheel steering characteristics can be fine-tuned by setting the shaft eccentricity of the eccentric and planetary gear shafts, and the gear ratio between planetary and internal gears. In the case of the Prelude, the maximum rear wheel angle is 120 degrees. But with small steering wheel angles up to 10 degrees, the rear wheel angle approaches 1.5 degrees, and as the steering wheel angle increases further, the responsive angle of the rear decreases. At a steering angle of 230 degrees (a front wheel angle of less than 20 degrees), the rear wheel angle becomes 0 degrees.
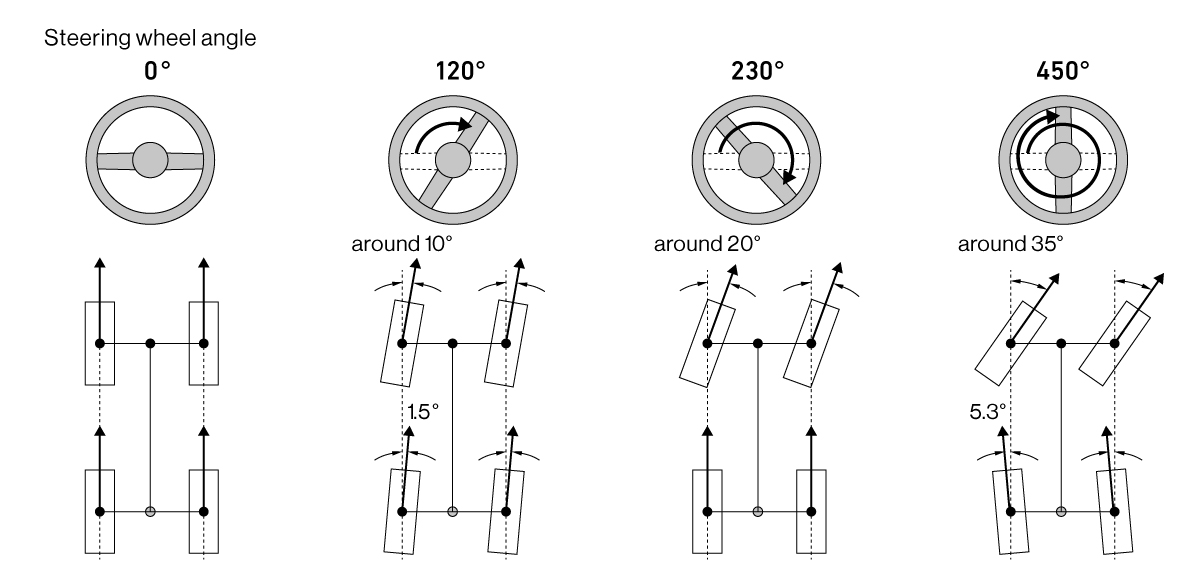
As the steering wheel is turned beyond 230 degrees, the rear wheels begin to turn in a reverse phase. When the steering wheel is turned 450 degrees (front wheel angle of around 35 degrees), the rear wheels turn to a maximum angle of 5.3 degrees. Compared to the minimum turning radius of the Prelude 2WS, which is 5.3m, the 4WS version realized a radius of 4.8 m (0.5m smaller), greatly improving the vehicle’s turning radius.
Focusing on how the rear steering gearbox works, when the steering wheel is turned from the neutral position to the right, while the angles are small the stroke rod moves to the left in order to turn the rear wheels to the right, in the same phase as the front. As the angle increases, the rear wheel angle returns to a neutral position, and then begins to turn to the left, in the opposite direction of the front wheels.
Although the development began to enhance active safety, steering angle sensing 4WS achieved steering response characteristics that could not be achieved with a conventional front-wheel steering system, demonstrating great potential for improving handling, an area Honda has consistently pursued.
The Honda Super Handling Challenge
- Chapter 1 Honda Four-Wheel Steering System (4WS) Technology – 1987
- Chapter 2 Active Torque Transfer System (ATTS) Technology – 1996
- Chapter 3 Variable Gear Ratio Steering (VGS) Technology – 2000
- Chapter 4 Super Handling All-Wheel Drive™ (SH-AWD®) Technology – 2004
- Chapter 5 Rear Toe Control System: Precision All-Wheel Steer Technology – 2012
- Chapter 6 Legend’s Sport Hybrid SH-AWD® Technology, a Three-Motor Hybrid System – 2014
- Chapter 7 NSX’s Sport Hybrid SH-AWD® Technology, a Three-Motor Hybrid System – 2015
- Chapter 8 Honda’s Concept of Dynamic Performance
- Chapter 9 The Future of Super Handling (1): Four-Motor EVs
- Chapter 10 The Future of Super Handling (2): Four-Motor EVs
TechnologyHonda Super HandlingHonda Four-Wheel Steering System (Honda 4WS) Technology – 1987