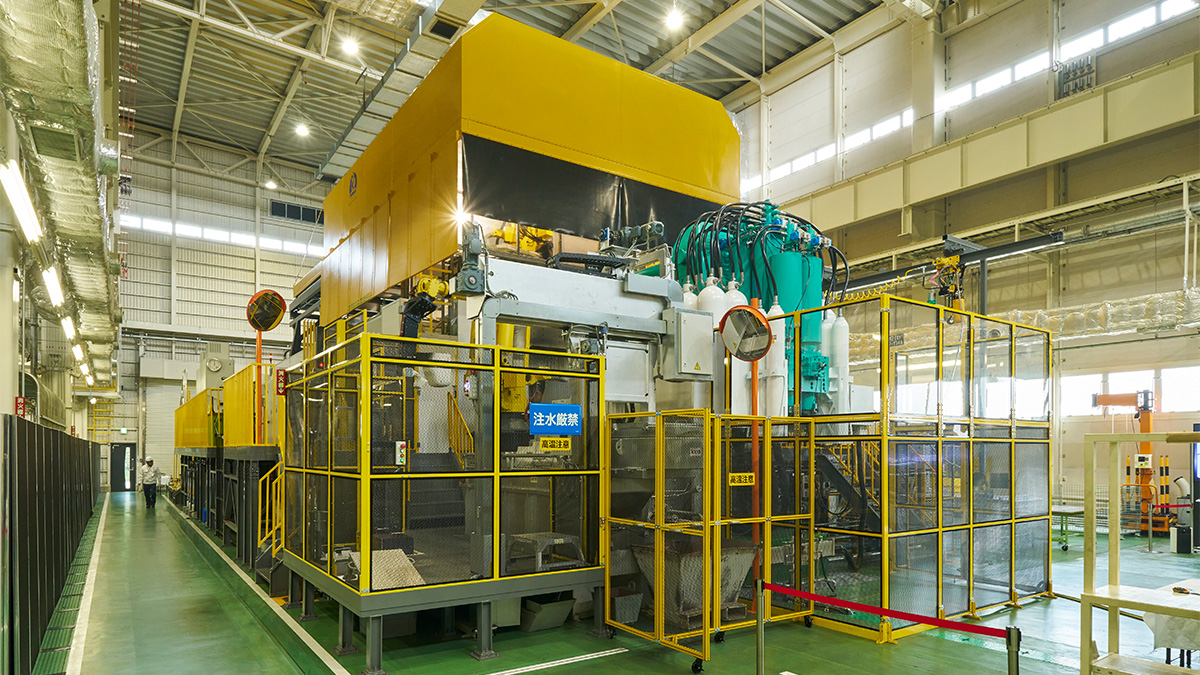
Production technologies that enable “Thin, Light”
The “Honda 0 Series” has entirely new EV value. This was made possible by cutting-edge production technologies that have realized “Thin, Light.”
Honda has developed manufacturing technology for thin battery packs that will revolutionize the traditional concept of EVs, as well as for forming and welding technology for lightweight body frames that surpass conventional levels, toward the period of EV popularization.
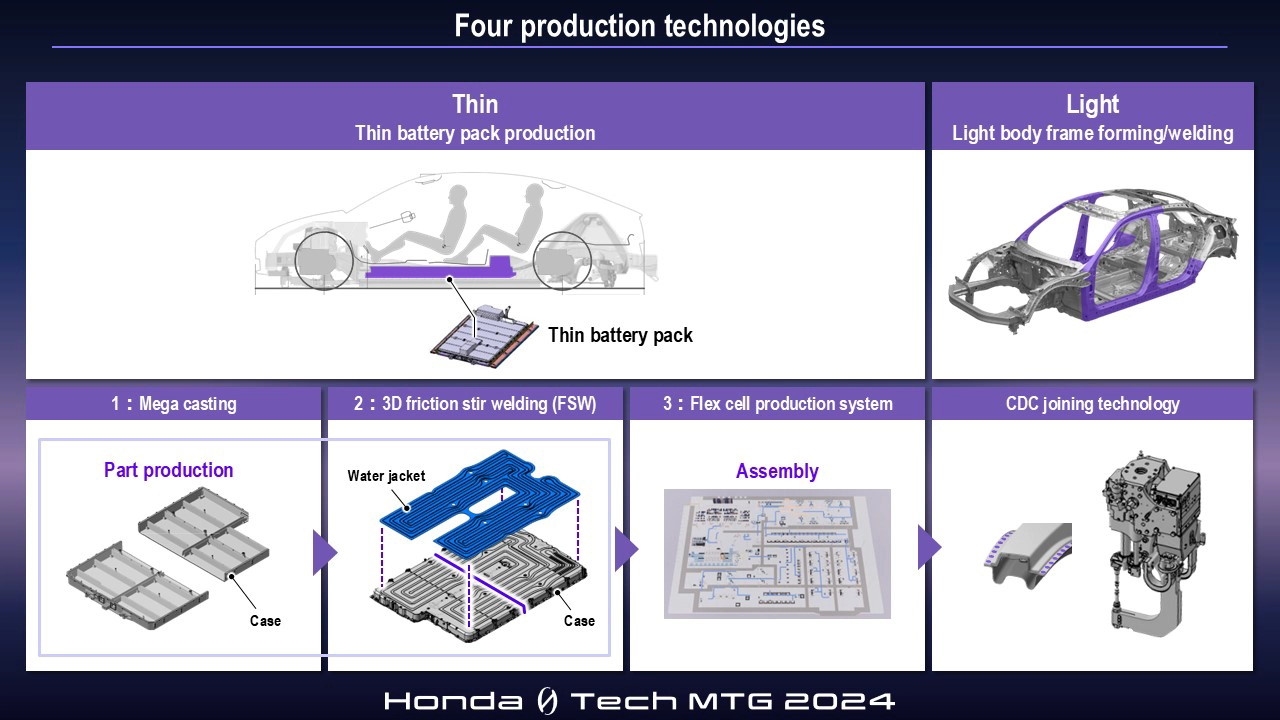
Thin battery pack production technology (1) <Mega-casting>
The first 6000-ton large casting machine that was introduced in a Honda plant in Japan
A thin battery pack is structured so that batteries are laid flat side-by-side in an aluminum case.
A conventional battery pack case is comprised of around 60 parts or more. For “Honda 0 series,” we have implemented a case comprised of three consolidated parts in appropriate sizes by establishing innovative technologies for aluminum casting, joining, and fastening.
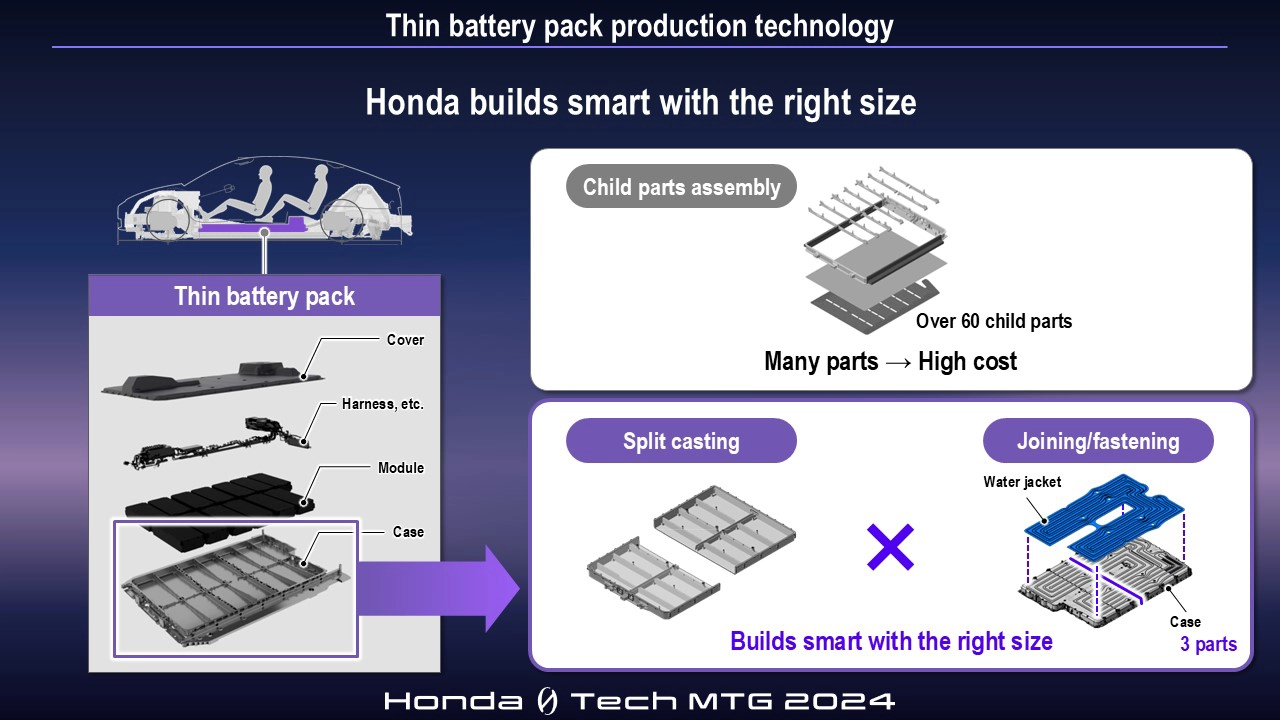
Using split casting by mega-casting (6,000 tons) has allowed different cases to be manufactured based on the various battery pack specifications. Giga-casting (10,000 tons) allows monobloc casting, which requires individual cases to be made such as for medium-size and large-size models. Mega-casting allows highly efficient, low-cost manufacturing by making common parts to reduce the number of parts in appropriate sizes.
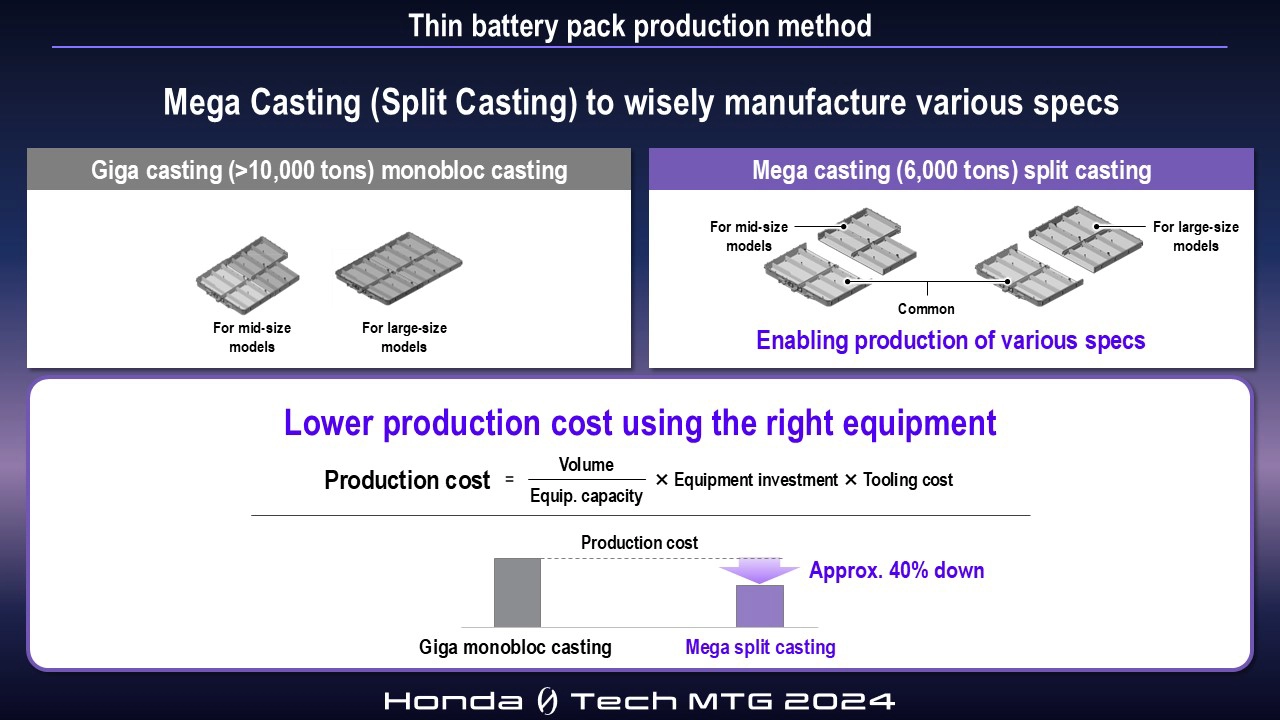
From the aluminum casting technology perspective, since the battery case is a thin and large part compared with the transmission case of an engine vehicle, high quality has been pursued intensively. By taking advantage of our expertise in casting technologies that have been modified and improved through the mass production of engine vehicles, we have established three casting technologies to achieve high-level internal quality and dimensional accuracy of the battery cases.
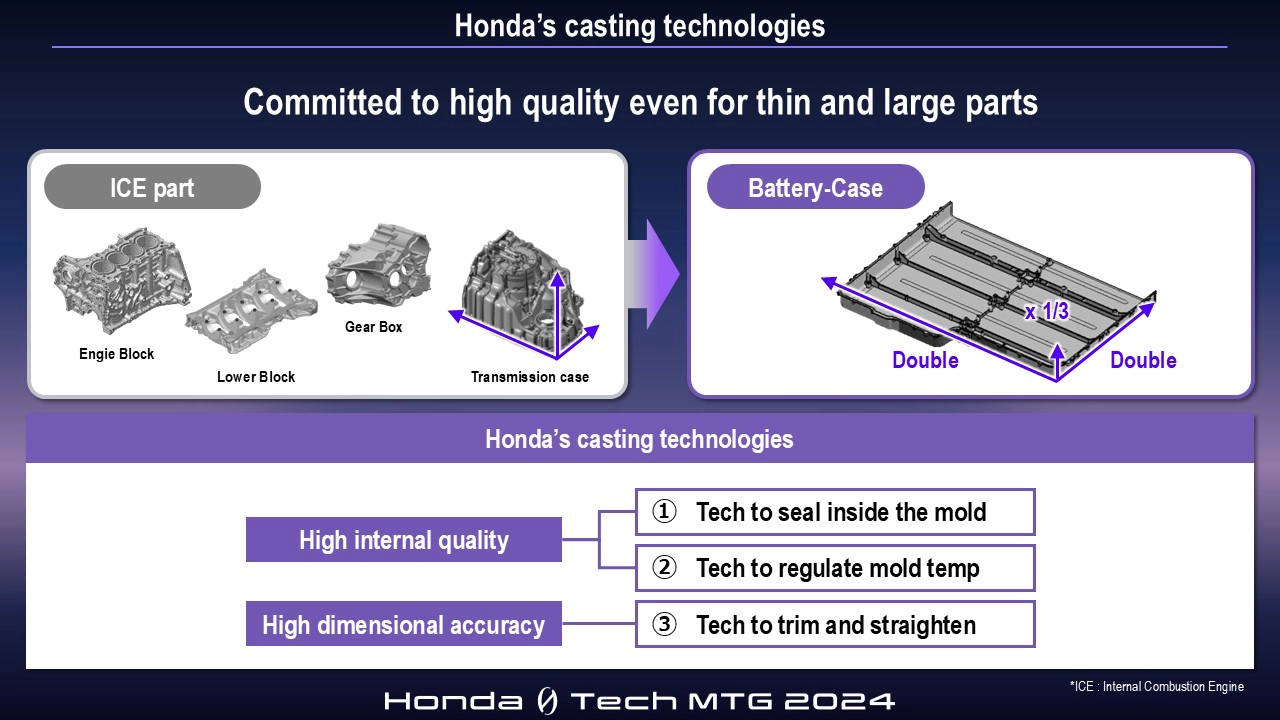
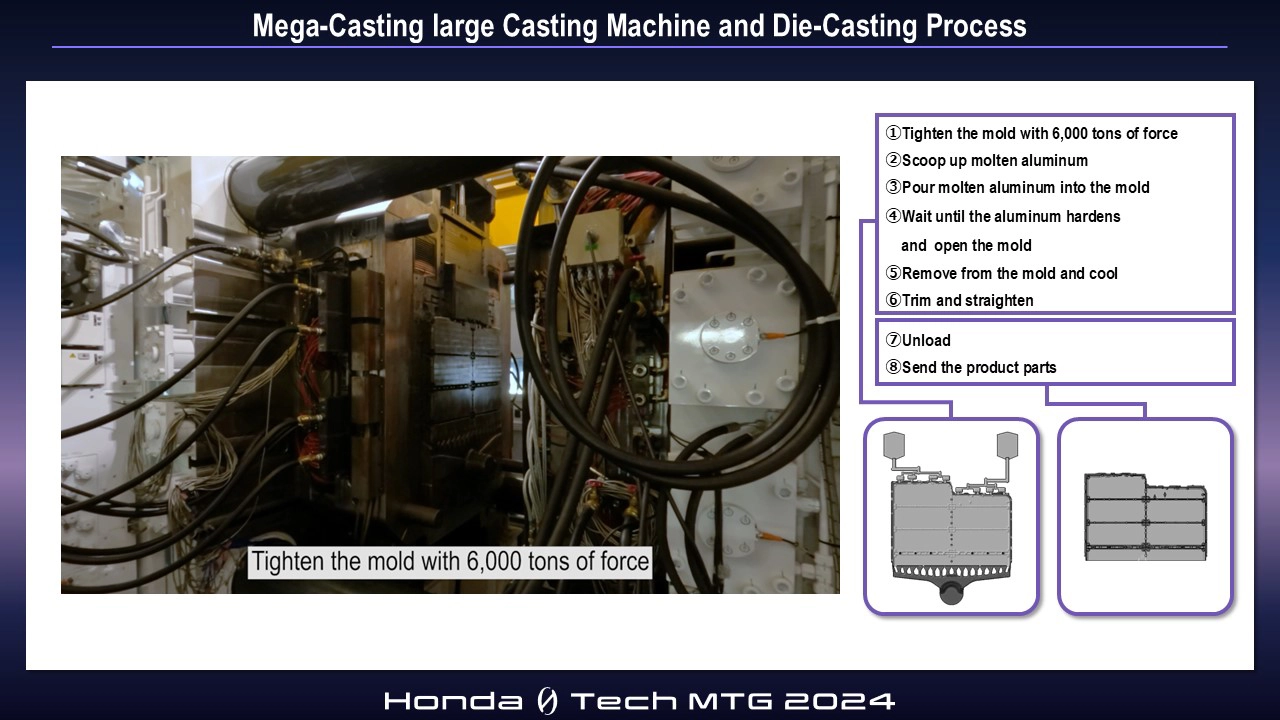
(1) Vacuum casting technology
When molten aluminum is poured into the mold, air and gases entering it need to be reduced. Thus, gaps between mold components through which air might enter are sealed based on our patented sealing technology that has been cultivated through engine manufacturing. By sealing the mold, high-quality casting is achieved.
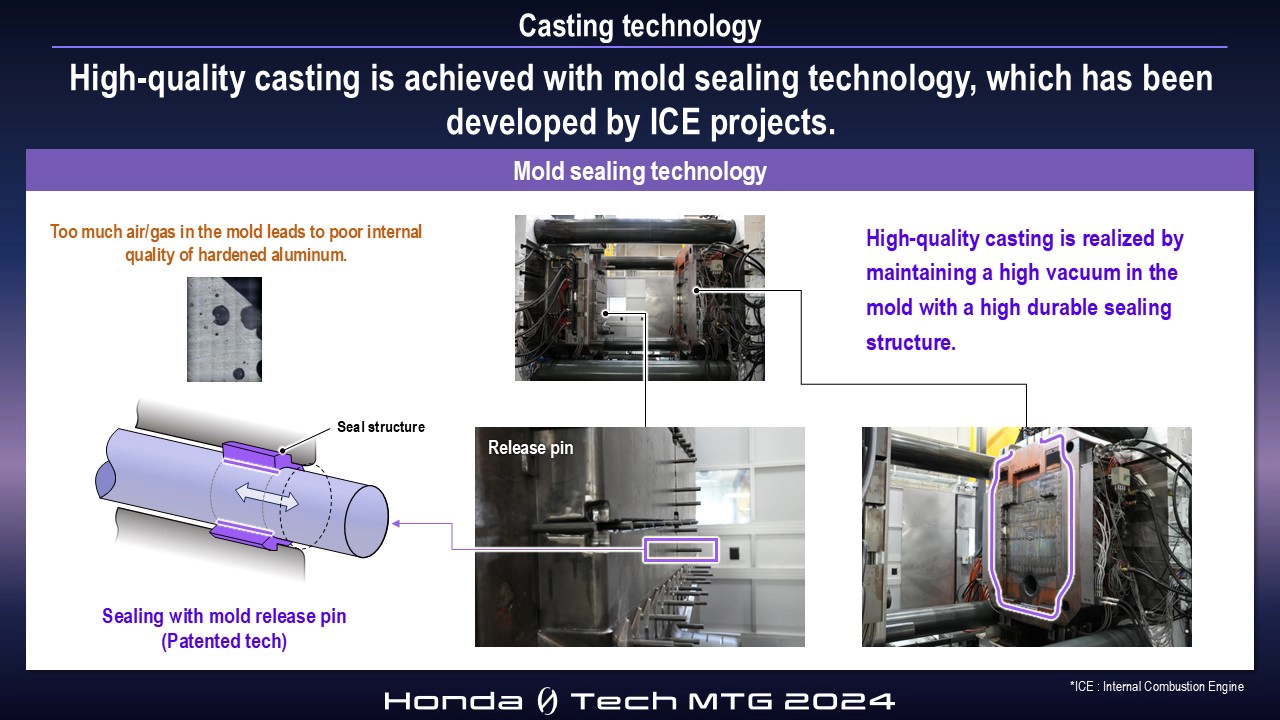
(2) Casting technology to regulate mold temperature
This technology adjusts the mold temperature within an appropriate range to ensure that molten aluminum is poured into every corner of the mold, resulting in high-quality casting.
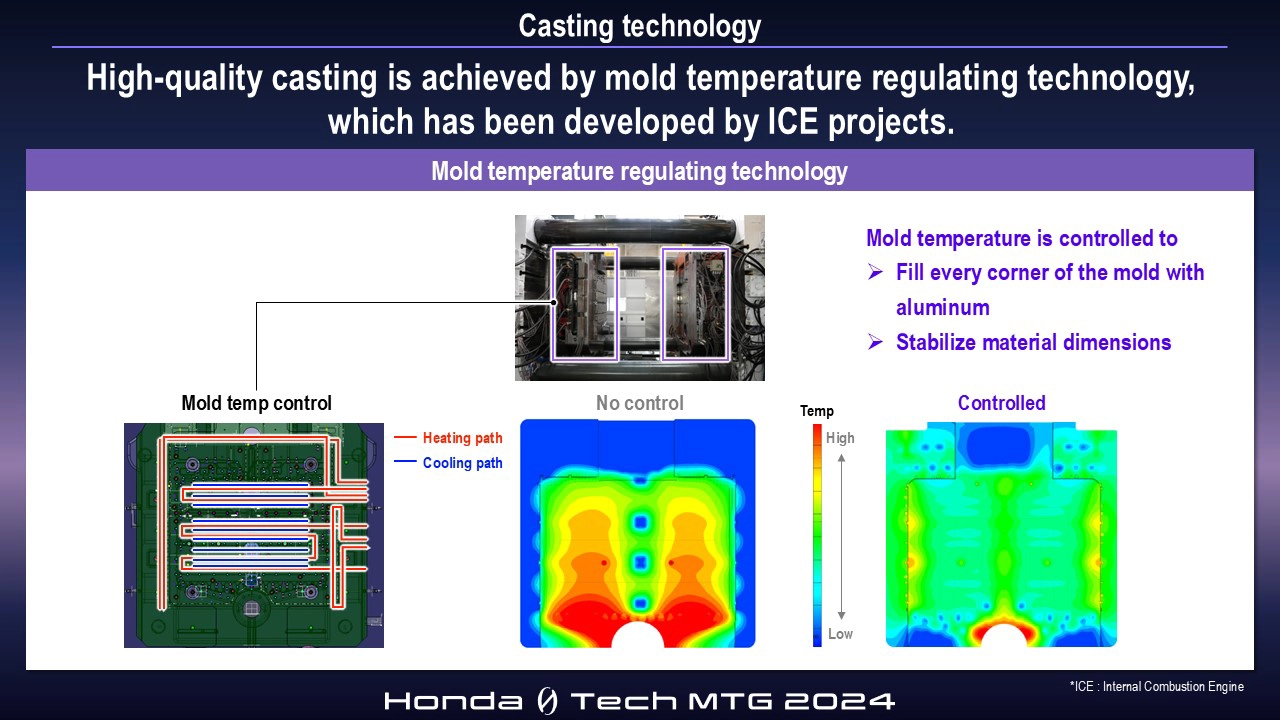
(3) Technology to trim and straighten in a single process
For deformation due to shrinkage caused by cooling (dipping into water) after casting, this technology has combined two conventional processes of trimming and straightening into a short process. Performing the operations simultaneously in one process has allowed high dimensional accuracy.
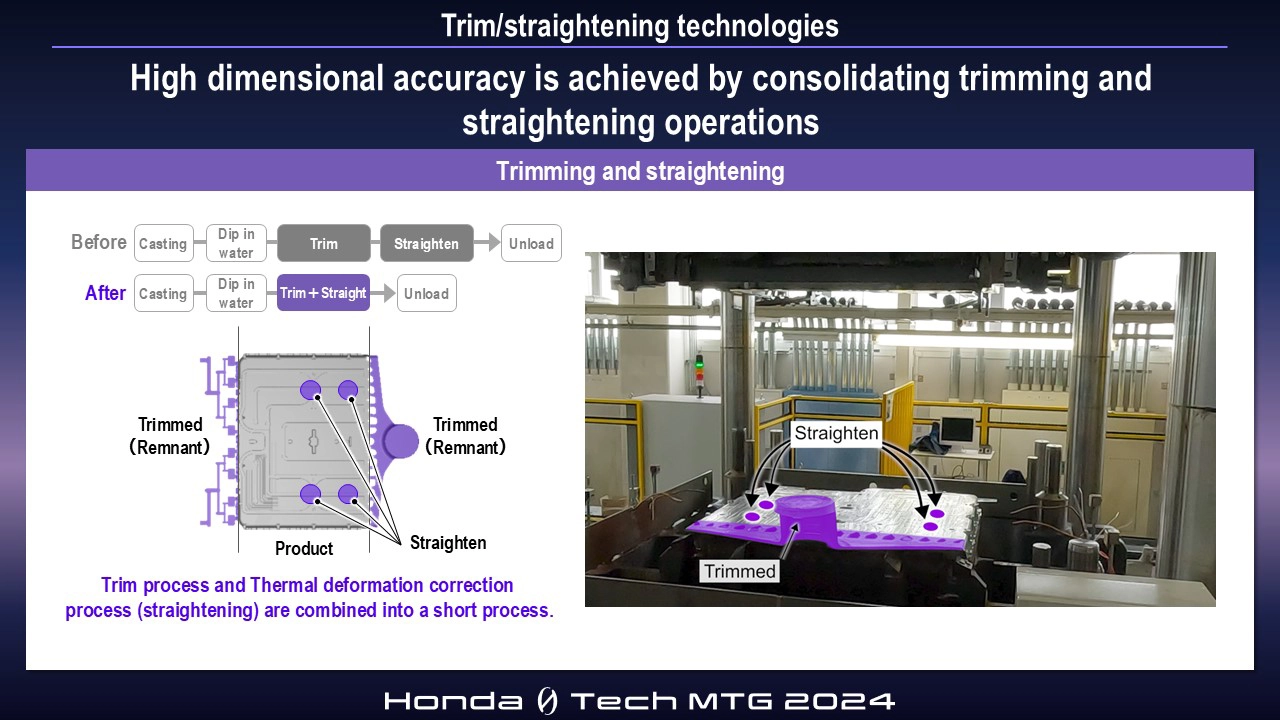
Mega-casting technology established to produce battery pack aluminum cases will be applied to other areas such as production of aluminum body frame parts in the future.
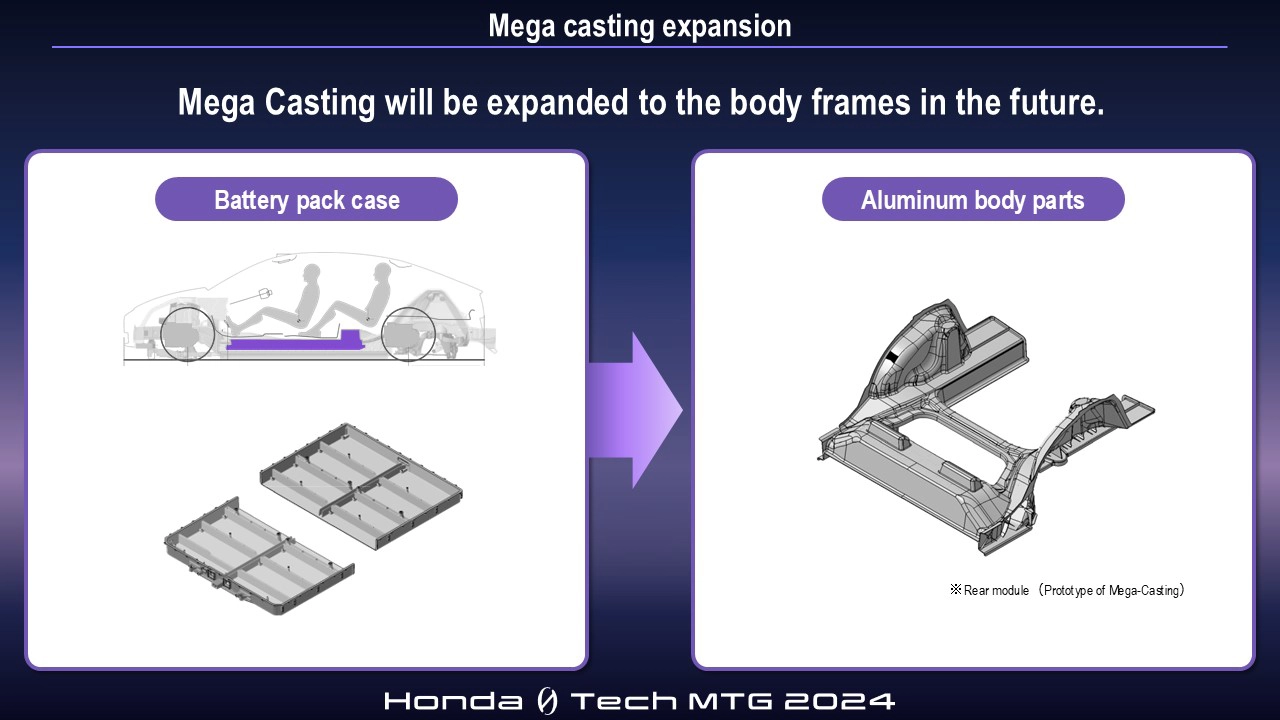
Thin battery pack production technology (2) <3D Friction Stir Welding (FSW)>
FSW:Friction Stir Welding
To join parts of a battery case, 3D FSW (Friction Stir Welding) is used in two processes: A process of joining two cast parts made by mega-casting to form the main body of the case (butt joint), and another process of joining a water jacket cover with the case body (overlap joint) to form a battery cooling water circuit.
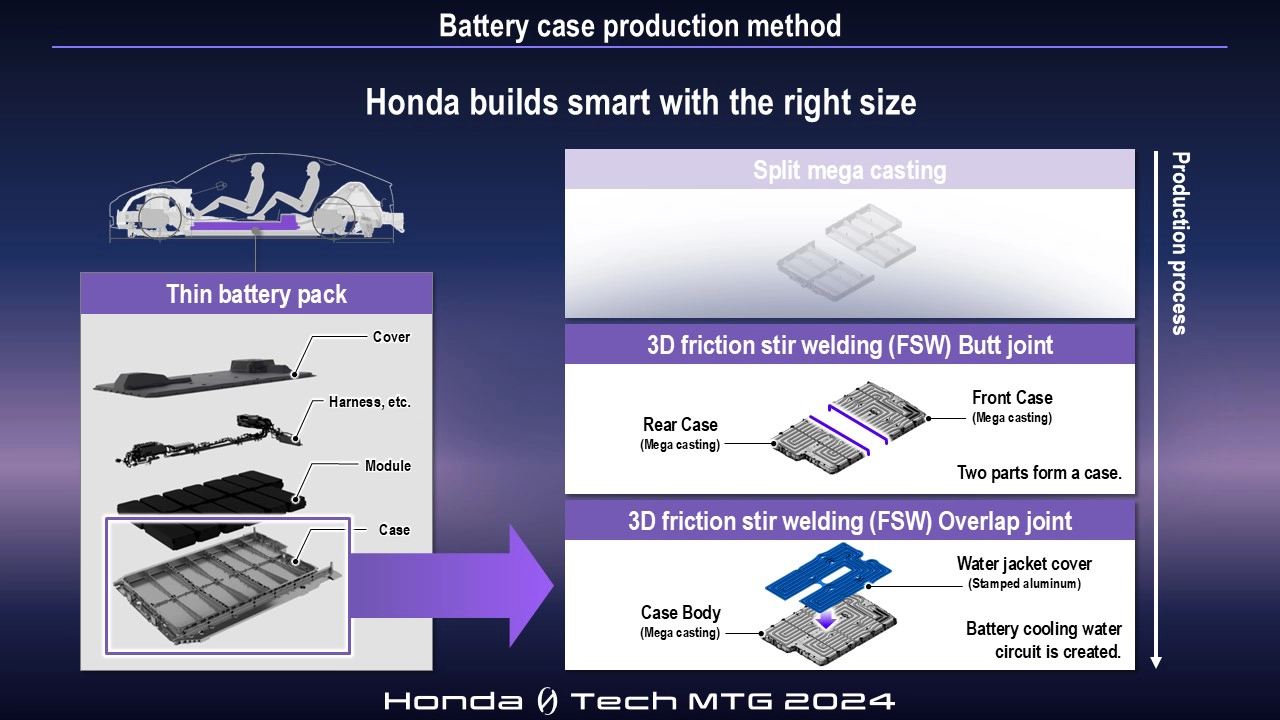
FSW is a technique that joins metal materials without melting the metal. A rotating tool is pressed against the workpiece and the frictional heat generated stirs the aluminum to join materials. Compared with generally used arc welding, FSW uses significantly less heat, which minimizes distortion of the material and generates no internal defects, allowing continuous joining with high airtightness and strength. So, we use this method.
Honda has been using this joining technology for many years: In 2000, it was applied to the aluminum wheels of off-road four-wheelers, and in 2012, it was used for the first time in the world to join steel and aluminum materials for structural parts of mass-produced vehicles.
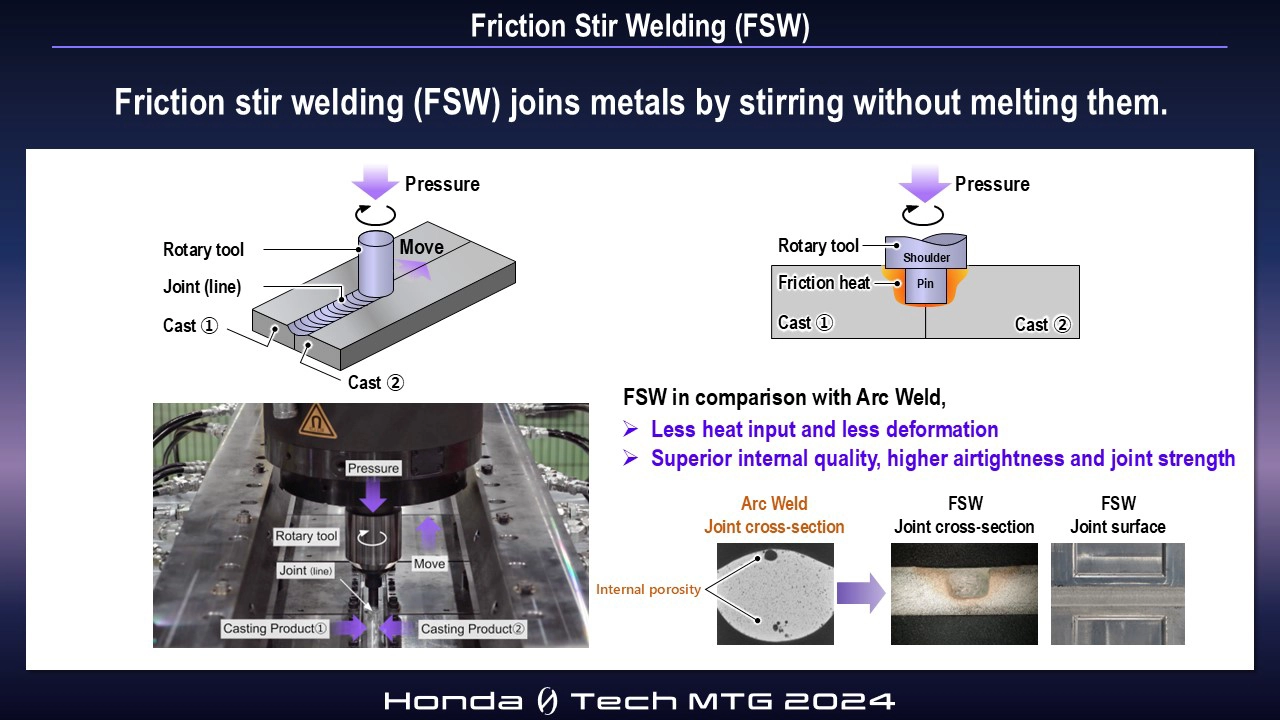
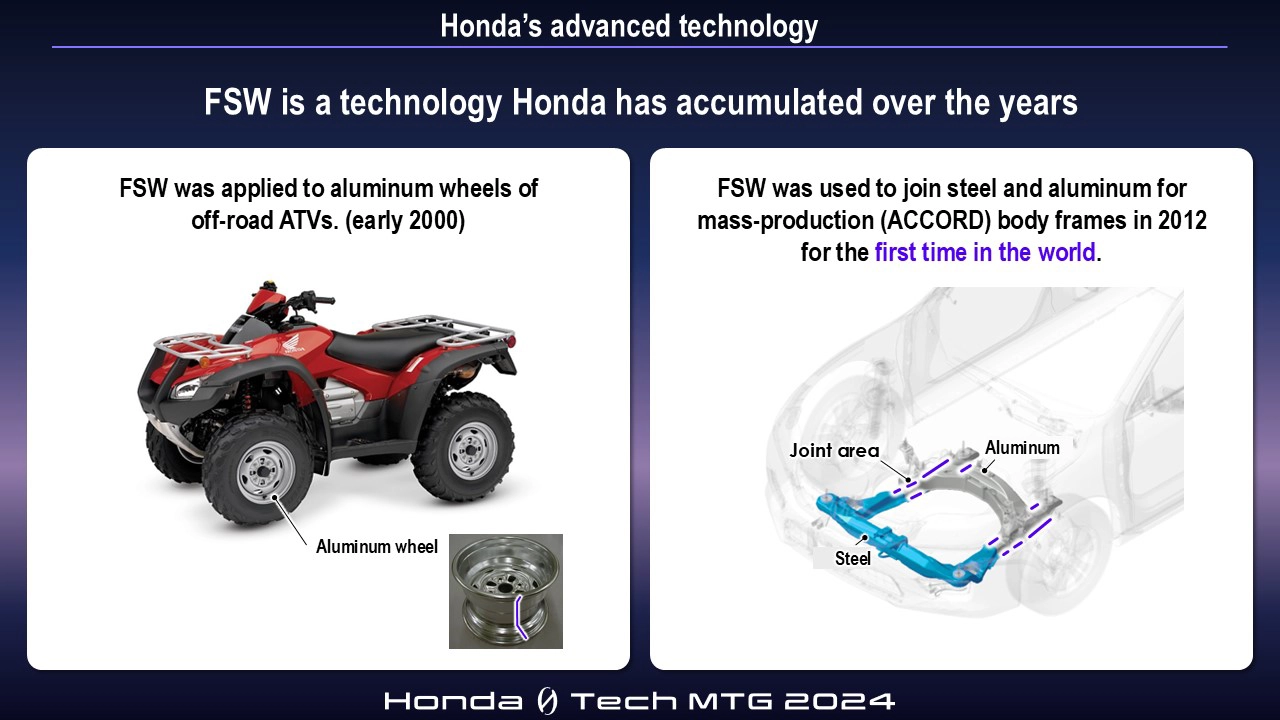
We have developed a new method to shorten the joining process as well. In conventional FSW, machining is required before joining steps to cope with gaps and misalignment between parts to be joined and waviness on material surfaces. This time, in addition to the higher precision of parts given by the mega-casting technology, we have developed jigs and tools that can apply FSW directly on the material surface of aluminum parts without performing machining processes except on butt surfaces. This has allowed three machining processes to be omitted, providing high-quality joining in a short process.
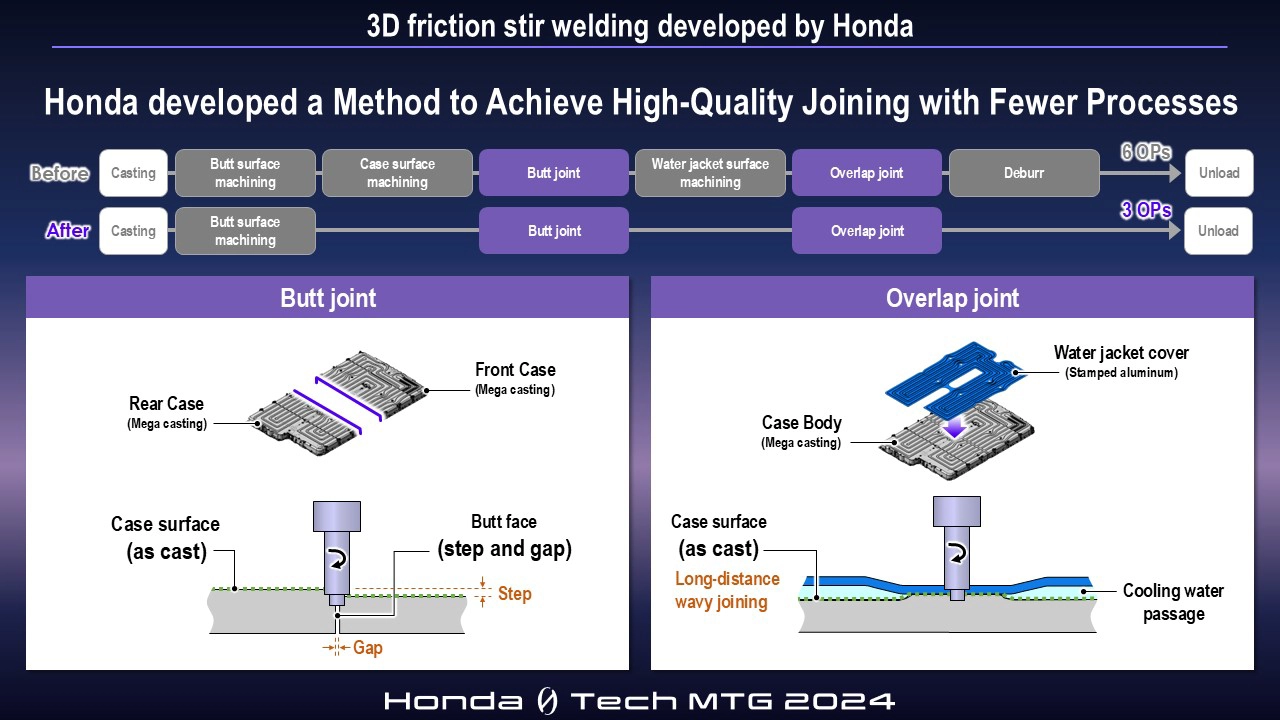
(1) Butt joint
In a butt joint process to join two parts of the battery case, clamping of the two workpieces is performed from the center outwards just like ironing to fit the joint lines of the two parts with each other. For any slight gaps or misalignment that may occur during clamping, a rotary shoulder tool with a large heat input range is used to effectively fill such gaps. Flat parts are joined at an advance angle of about 3 degrees, however, using the same advance angle for R sections may change the contact pattern of the shoulder, which may lead to insufficient heat input. So, by finely adjusting the advance angle to stabilize the heat input, high joint quality is obtained.

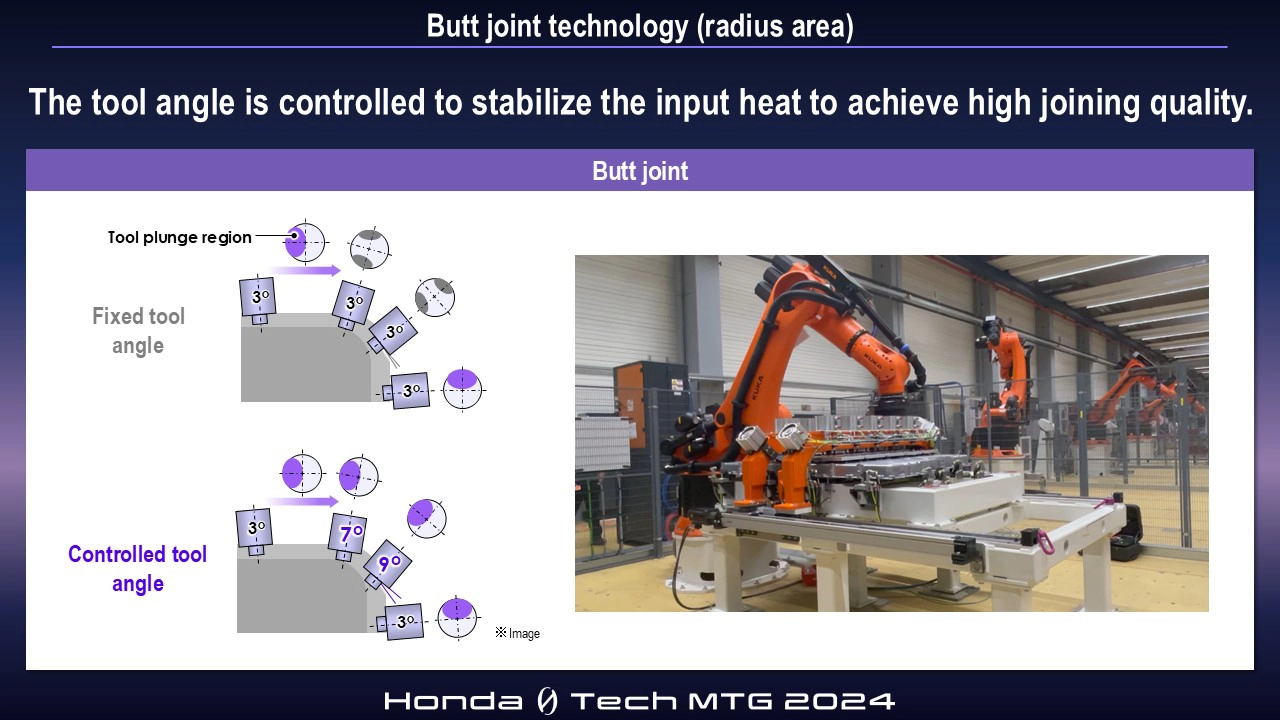
(2) Overlap joint
In an overlap joint process to join the water jacket cover, since the surface of the case has a waviness of about 2 mm before being joined, we use a fixed shoulder tool, which presses down on the workpiece effectively to close the gap between the case and the water jacket cover to join the parts. This tool has high trackability and can press down on the joint surface of the water jacket cover firmly. As a result, burrs, which are likely to be generated due to gaps, are significantly reduced, allowing joining to be stably performed over a long joining line.

Thin battery pack production technology (3) <Flexcell Production System>
Honda has worked on the automation of production and streamlining of the processes, building highly efficient production lines through various technological developments. The Yorii Automobile Plant, which started its operation in 2013 and manufactures various models in a mixed way, has introduced automation technology for handling heavy parts and high-precision assembly and implemented a high-speed, highly efficient production line. Furthermore, in 2016, instead of the usual line production system, we introduced the world's first “ARC line*” that has incorporated cell production units, where workers are responsible for a wide range of processes and assemble multiple parts, into the main line and flowed them there. With this, we have greatly improved production efficiency.
* Assembly Revolution Cell
Saitama Factory Yorii Automobile Plant/Honda Automobile (Thailand) Co., Ltd. Prachinburi Plant
On the other hand, although the shift to EVs has made considerable progress, we face issues of how we keep pace with changes in top-sellers and decline in labor force population in the manufacturing industry.
To cope with such a trend in times more flexibly, we have built a further advanced production system “Flexcell production system” as a process that allows us to be more flexible in our production based on production technologies Honda has cultivated up to now.
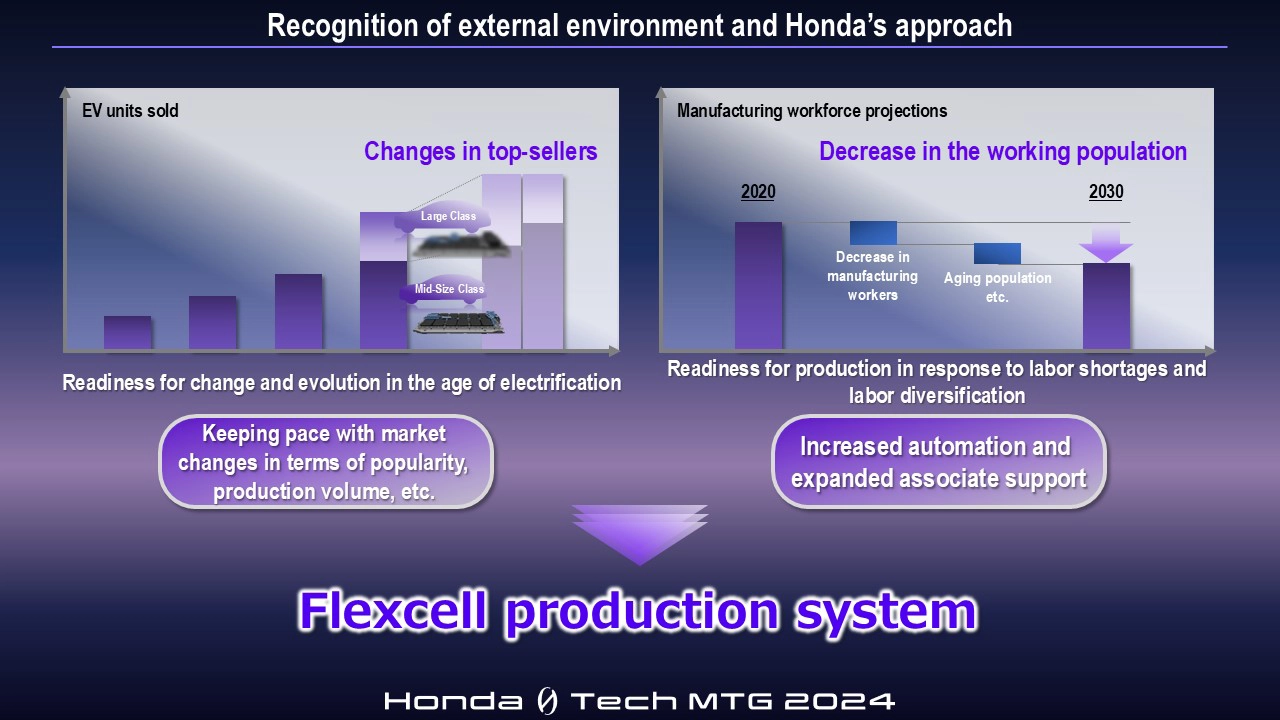
Flexcell Production System
To keep pace with changes in production volume and product specifications, the conventional line process required us to stop the operation, modify or relocate the line, and then resume production. This method took time before stable line operation was reached, reducing production efficiency. And in a serial production line, the whole production line is stopped even when a single device stops, reducing production volume.
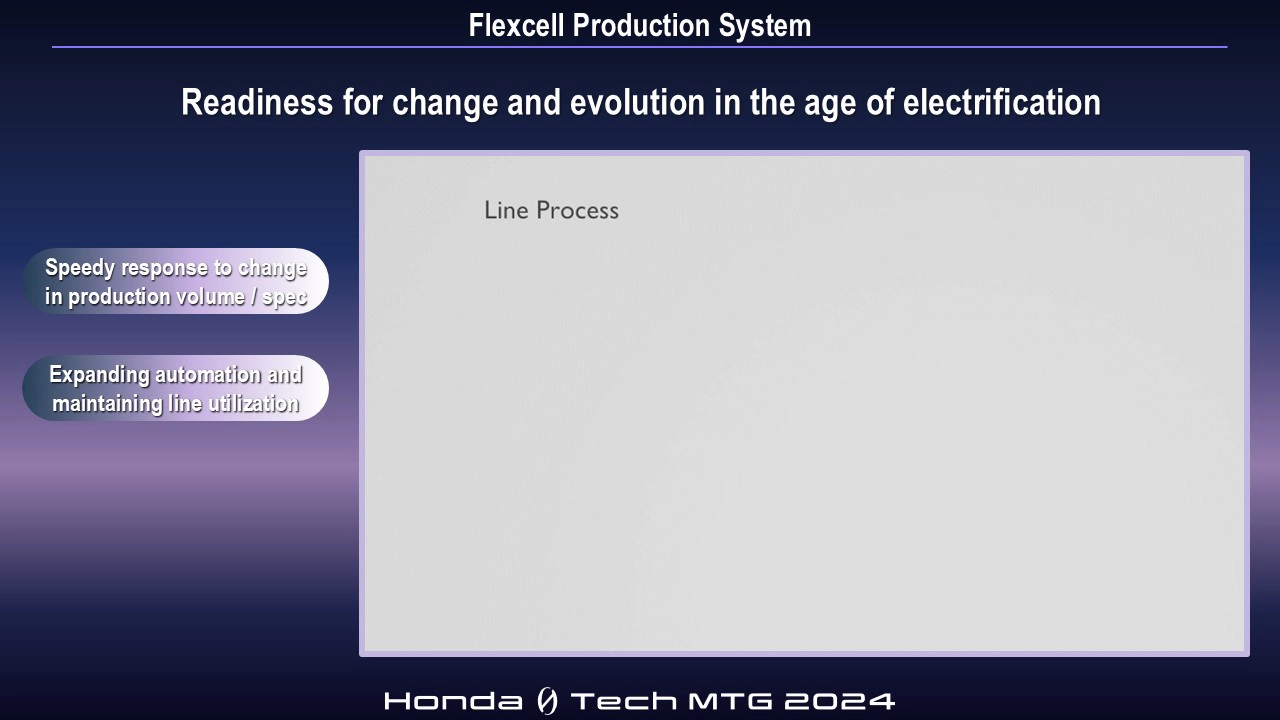
One answer we have come up with to address such issues is a production system that has fully incorporated cell production, which allows us to be both productive and flexible. With the introduction of the Flexcell production system, we can smoothly respond to changes in production volume and specifications by adding or rearranging cells for necessary areas while maintaining production activities, thereby improving our capability to keep up with the demand. In addition, it is possible to maintain a stable utilization rate even when the automation rate is increased.
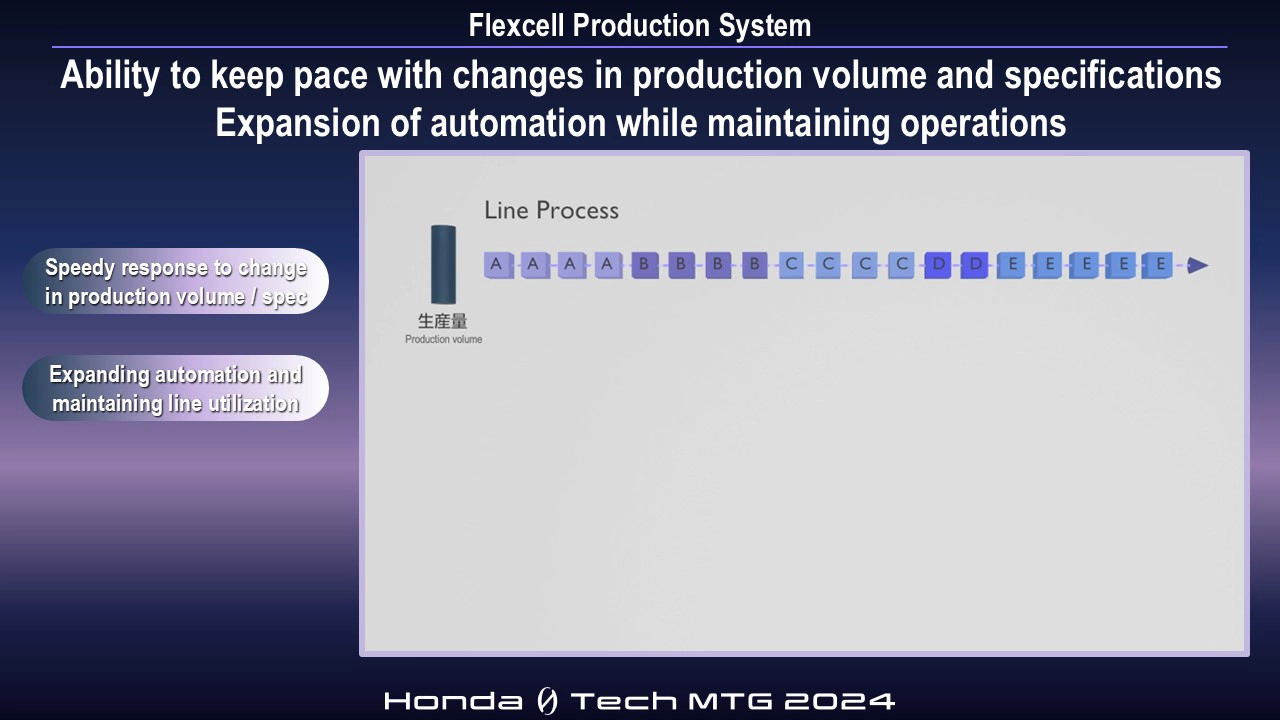
A thin battery pack assembly line is divided into an Automation Cell Zone and a Manual Cell Zone, and parts are conveyed completely by AGVs (Automatic Guided Vehicles). AGVs connecting the logistics area and such zones in a flexible manner support flexible production.
A notable feature of the Flexcell production system is that it can start with a low volume production and increase the production volume by adding cells depending on the market needs. In addition, by rearranging cells, a production line can be built without being restricted by the plant layout.
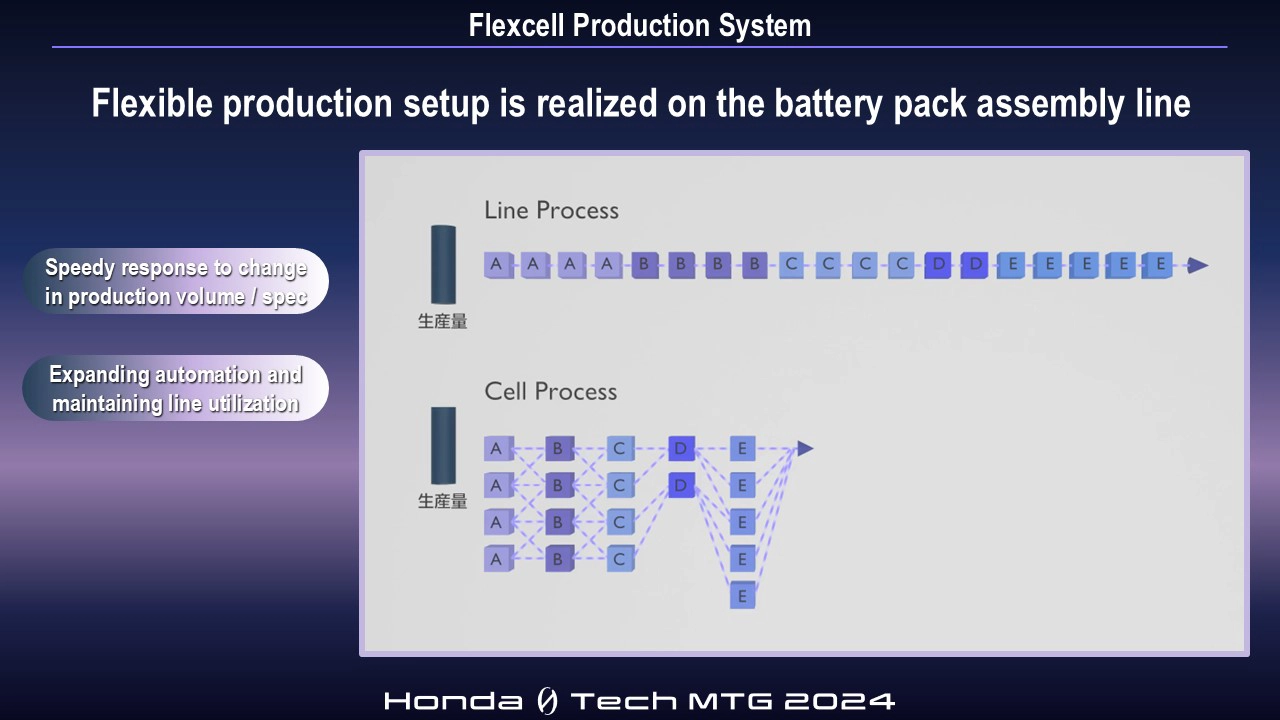
Digital and intelligent technologies that support Flexcell production system
The Flexcell production system may cause problems as cells increase. They are “complexity of transport routes” and “complexity of cell combination patterns.” To avoid such problems from arising, VC* based on digital and intelligent technologies is essential.
*Virtual Commissioning
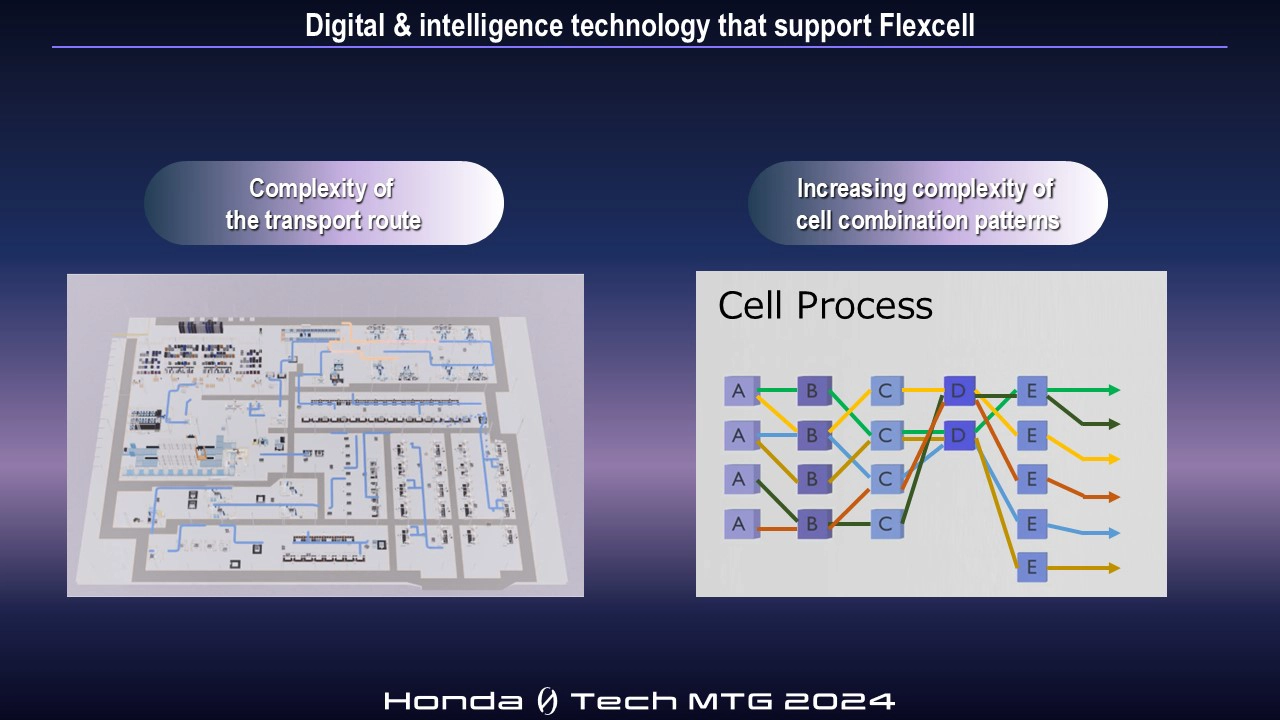
(1) Digital twin system
Cells can be added and rearranged easily, which in turn makes transport routes more complex. As the numbers of AGVs and junction points increase, more accurate verification through in advance simulation is required to reflect the actual field conditions. This issue can be solved by the digital twin system.
Since it can be verified in advance that the digital space is consistent with the real world, the completeness of the software on conveyance routes can be drastically increased in the production preparation stage.
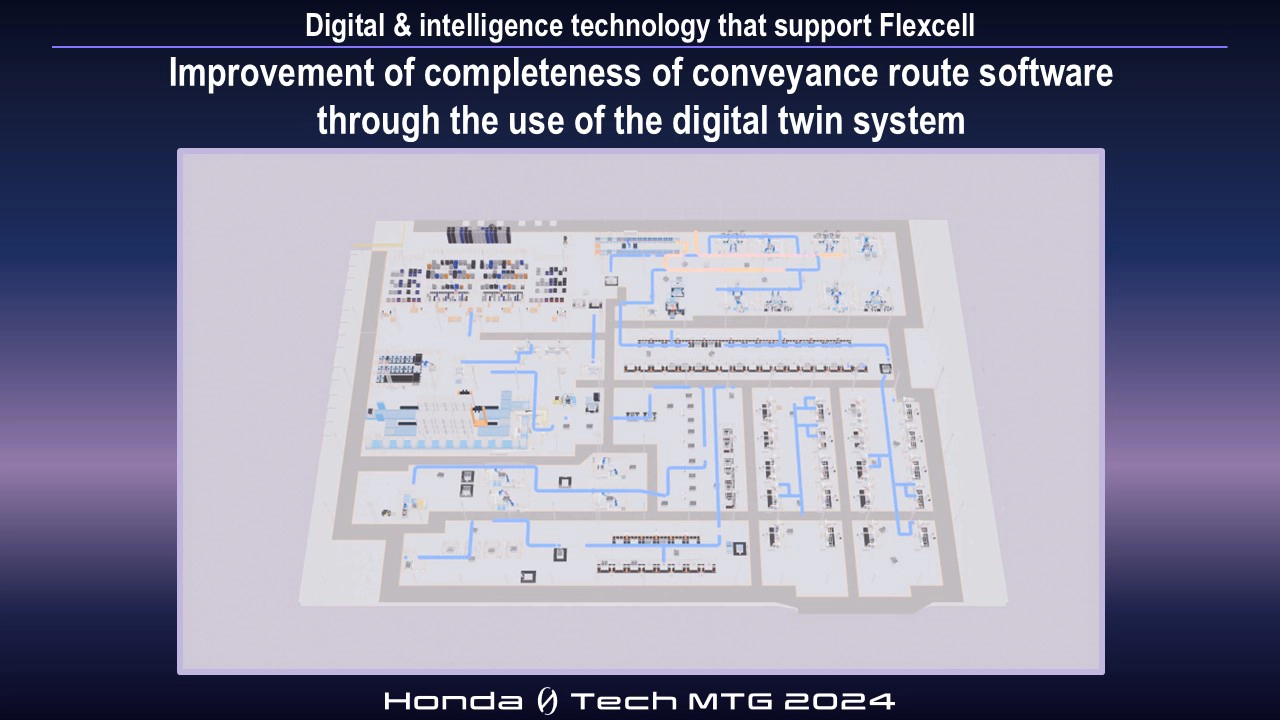
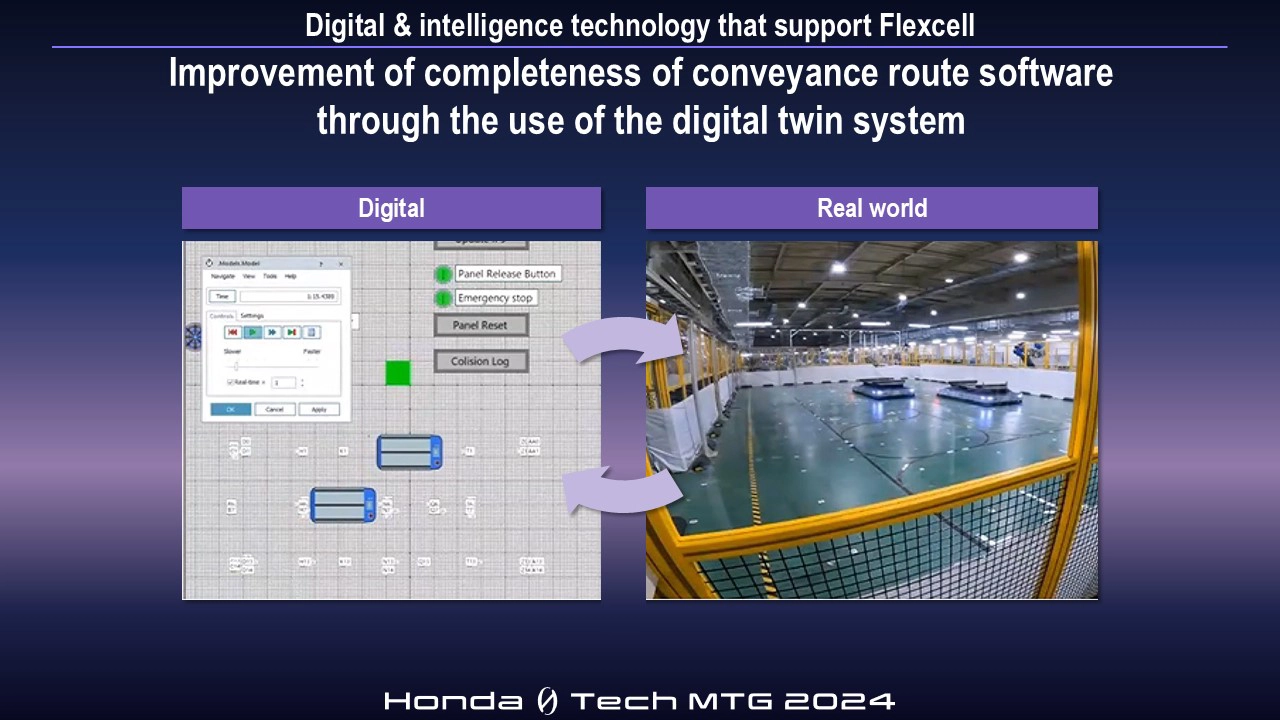
(2) Using digital tools
The complexity of cell combination patterns may create an issue that in the case of a production volume decrease, identifying which cell has caused the drop might be difficult compared with a conventional serial line where identification is easy. So, we use digital tools to detect common points among conditions under which problems arise.
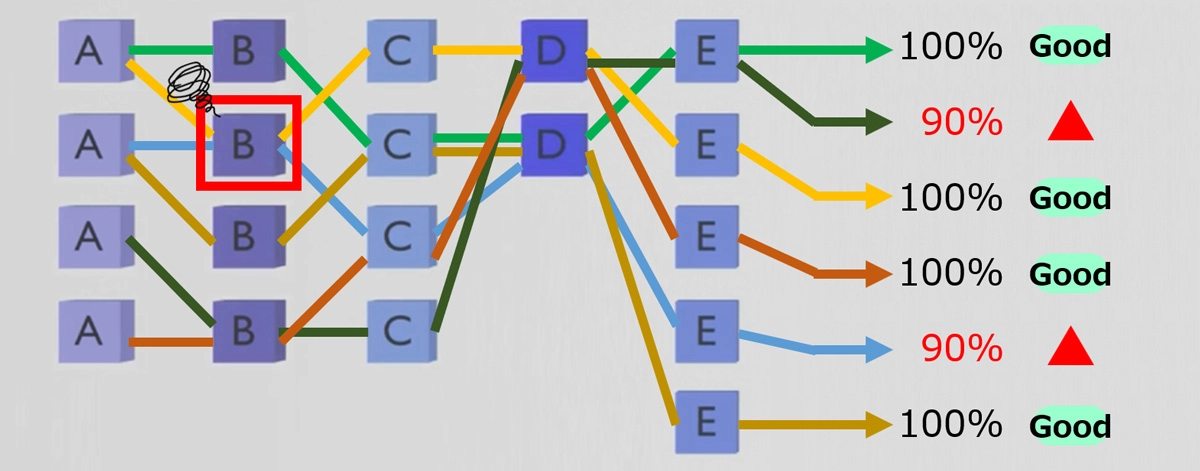
Then, detection results are analyzed. When a common point is a specific cell in a process used for production, the cell is intensively checked. In this way, using digital tools drastically reduces time for cause investigation, leading to the stable operation of the entire line.
(3) Using intelligent technology
For higher efficiency, we plan to incorporate intelligent technology into our AGV guidance system. The intelligent technology will be deployed when the operation data of the whole line has been collected. It will optimize AGV routing in real time by considering such conditions as AGV congestion, each equipment's run-rate and human-related work time variation, leading to more stable production line operation and increased production capability.
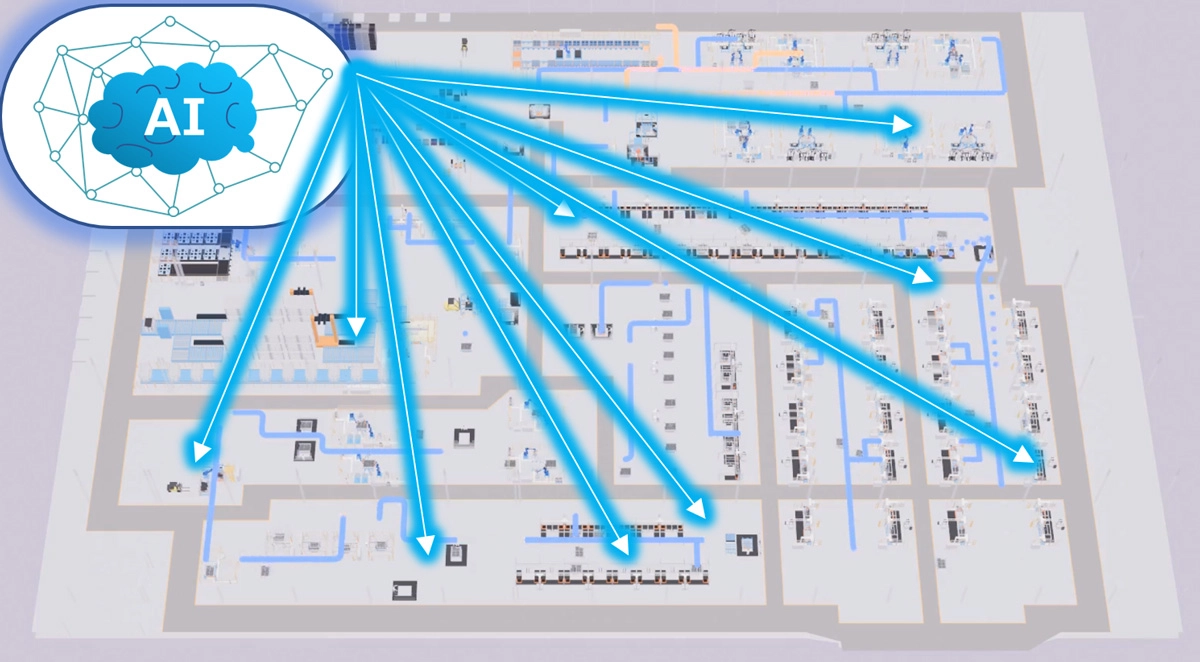
(4) Quality assurance using intelligent technology
In assembling battery packs, quality assurance through securely conducted work is especially required. So far, quality of assembling by human workers has been assured by human associates. Now, by having cameras worn by associates that recognize the assembling work, digital tools assume the quality assurance role. This reduces the mental burden on associates and further improves efficiency while the quality is assured.
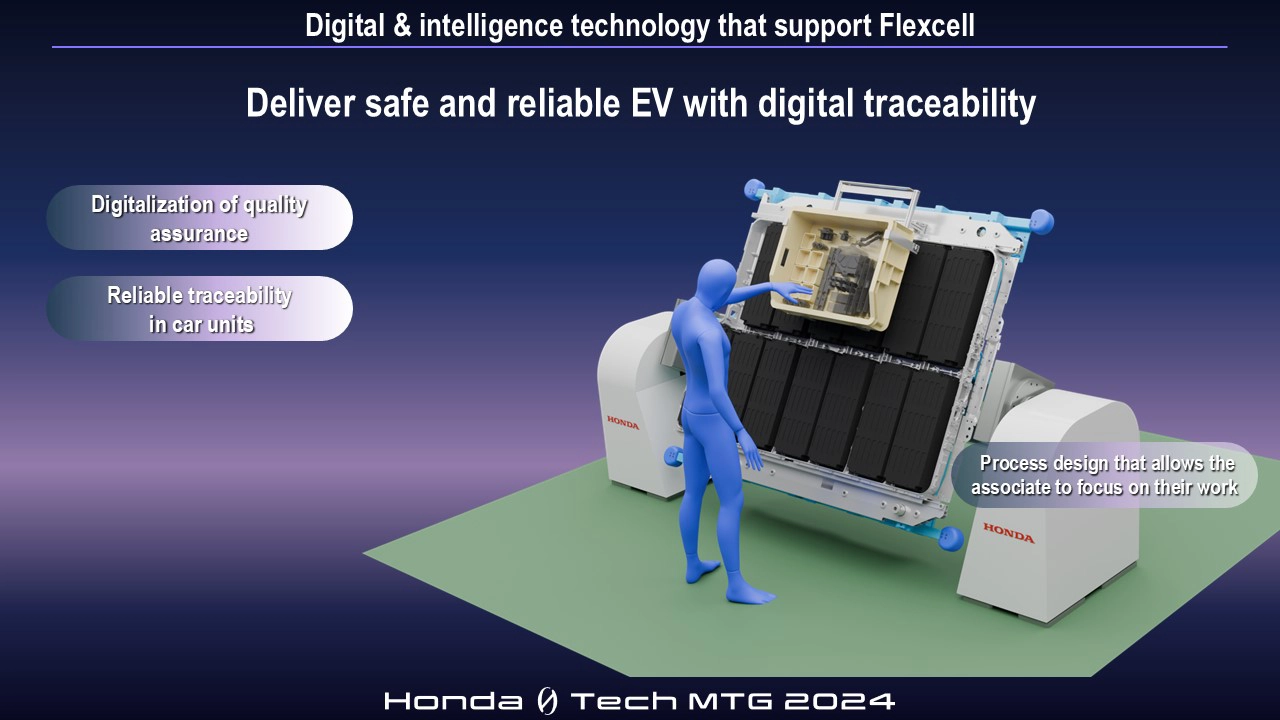
Honda plans to roll out such digital tools starting with our “Honda 0 series.”
Thin battery pack assembly line “Flexcell production system”
Lightweight body frame welding technology <CDC welding>
CDC: Constant DC Chopping
CDC welding is the world-first spot welding technology that has applied inverter technology to allow three layered sheets including ultra-high tensile steel materials to be joined, which has not been possible to date.
In the collision resistance performance required for the body frame, since the battery is mounted on the entire floor of the BEV, the cabin frame is required to protect the occupants and battery more stringently. Take a center pillar, for example. It is structured by stacking three steel sheets, consisting of a thin sheet of mild steel that determines the design and thick sheets of ultra-high tensile steel that take care of the strength, and this combination of thick and thin sheets makes welding extremely difficult. Moreover, light-weighting must be achieved to increase the cruising range of the BEV.
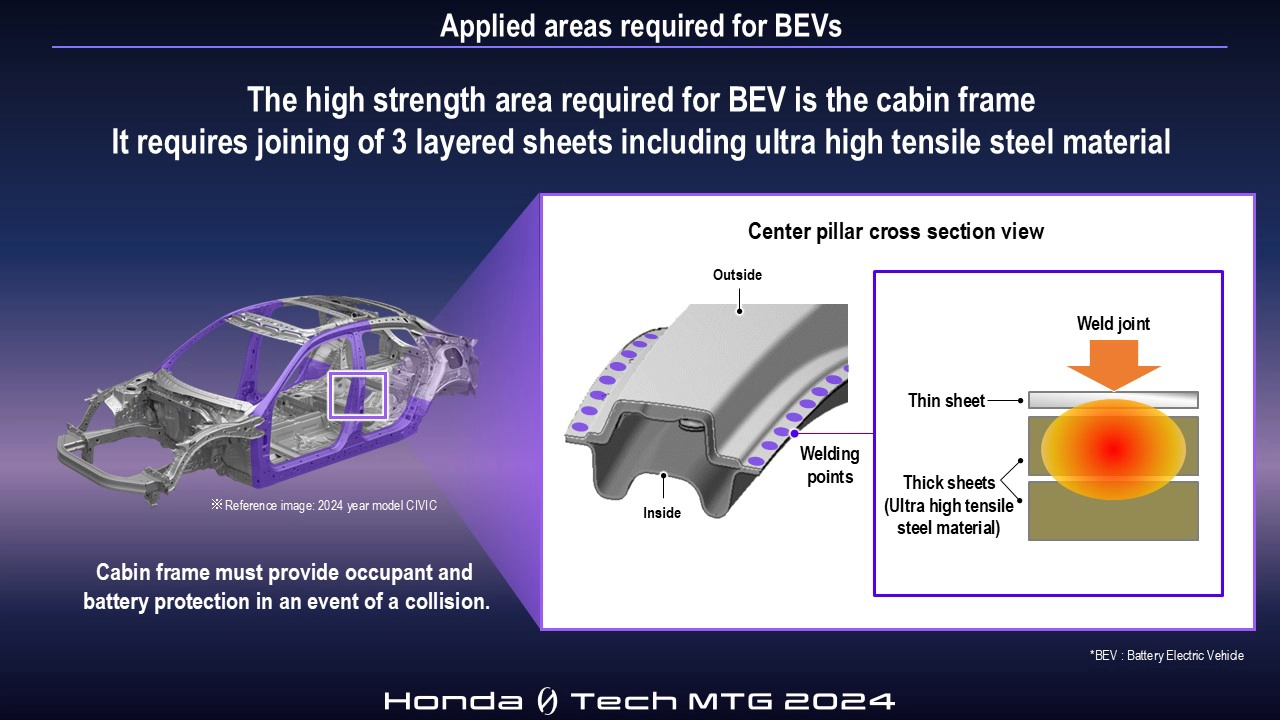
So, how do we achieve high strength and light weight at the same time?
In the figure below, the vertical axis shows body strength, and the horizontal axis shows body weight. In contrast with a conventional structure, CDC welding allows higher tensile thick sheets to be welded, increasing the strength of the materials themselves. Materials used are reduced accordingly, achieving light weight and high strength. For areas that require higher strength, thicker high tensile sheets can be welded. Both sheet combinations cannot be welded using conventional techniques.
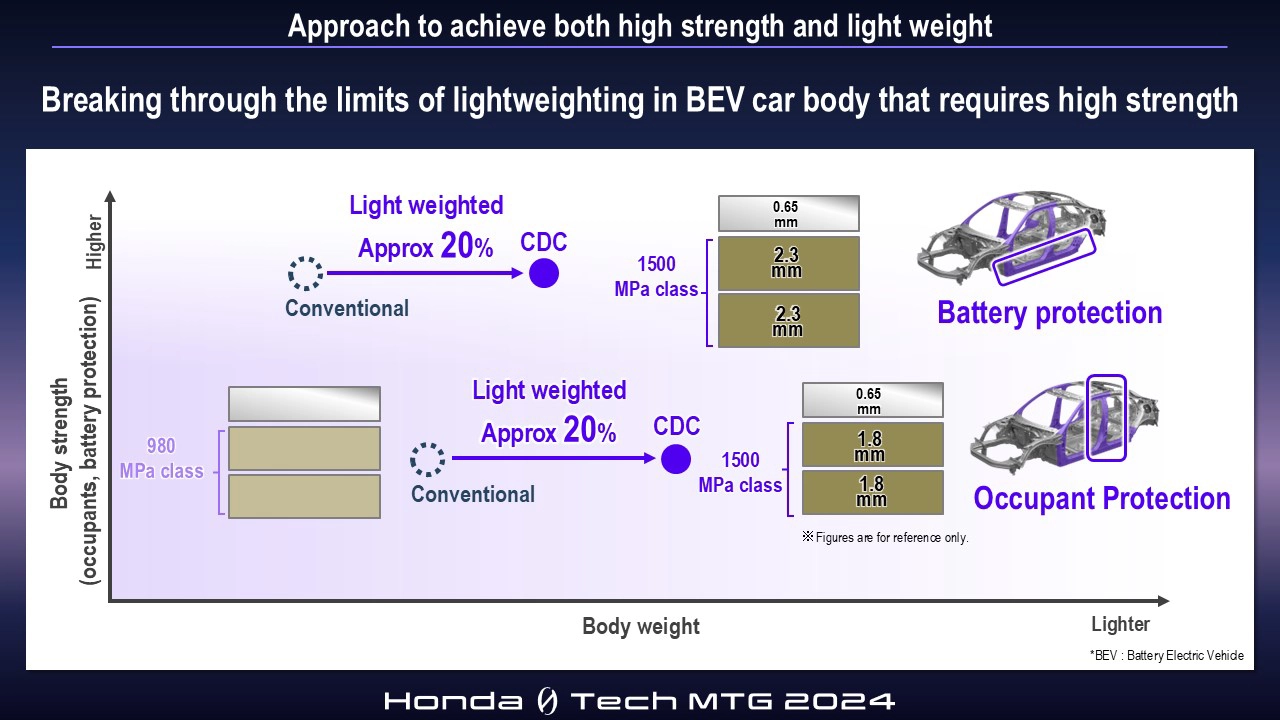
Currently, frame welding for mass-produced vehicles mainly uses DC (direct current) spot welding, where a robot holds this welding gun, clamps a welding point with electrodes at the tip, and generates heat by passing a direct current of about 10,000 amperes to weld.
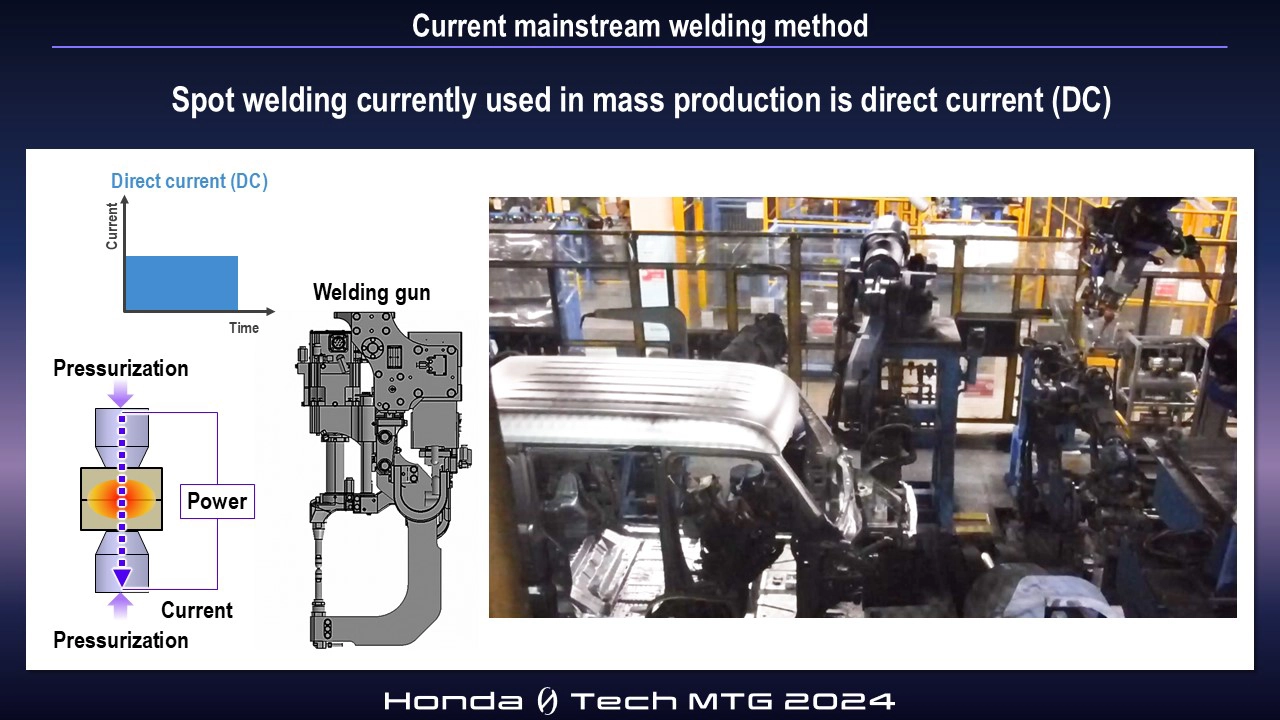
This DC spot welding allows the welding gun to be mounted on a robot and automated since it can be made light and small with inverter control, and Honda has been using DC spot welding for many years, continuing evolving and improving it
In recent years, however, issues have become apparent that spatters (metal particles made of melted metal at welding scattered and solidified) generated on thick sheets due to their tendency to generate heat cause lower strength, while weak heat generation on thin sheets causes insufficient welding.
On the other hand, AC (alternating current) welding has been around for a long time and its extremely heavy weight is believed to make it difficult to be automated, but its high peak current generates more heat on thin sheets and its pause time suppresses heat generation on thick sheets
Now, CDC welding is a method that has implemented waveform control to secure high peak current and pause time in a compact and light-weight manner by applying Honda’s various inverter technologies.
● A technology that maintains an optimized waveform with a high peak current in a constant manner by controlling target values
● A technology that keeps a specified amount of heat constant by automatically controlling the pause time
From these two invented technologies, we have named this method “CDC” (Constant DC Chopping).
Honda has revolutionized the way spot welding is controlled by implementing the world’s first method that has applied our inverter technology.
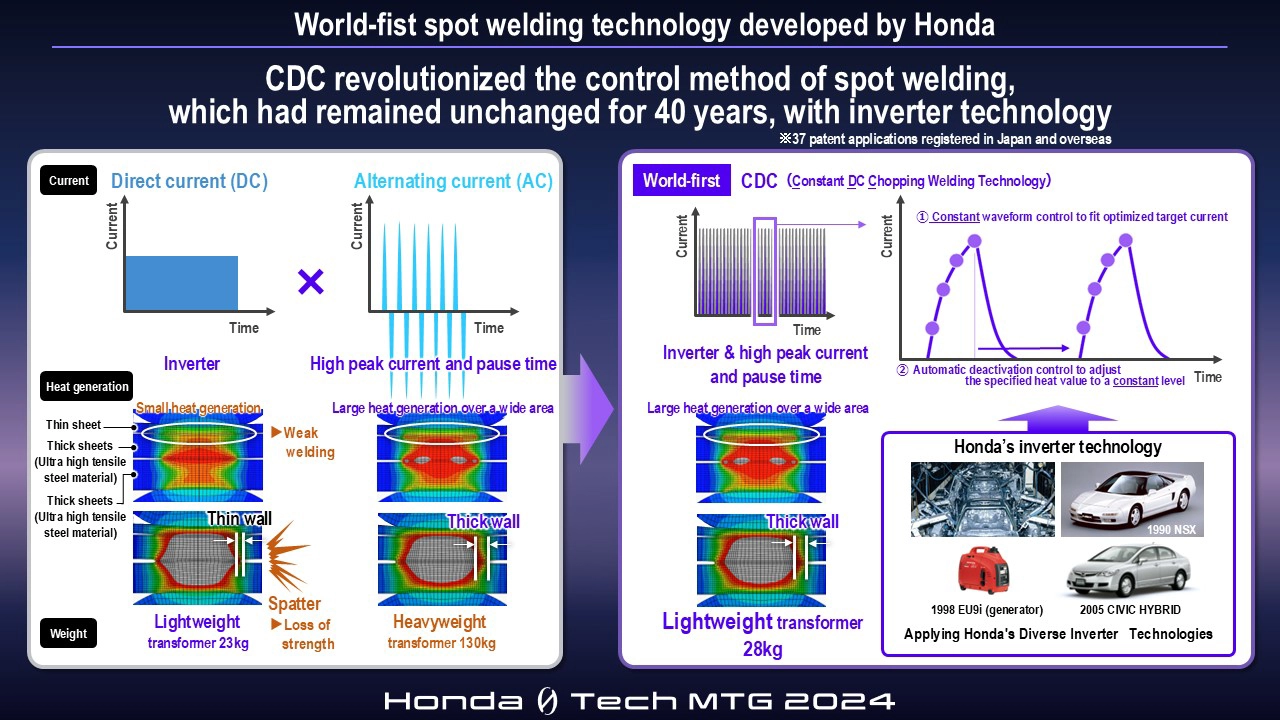
Another significant advantage of CDC is that it can be implemented by replacing guns and adding software to allow it to be introduced into mass production without requiring large-scale modification. It can be introduced by increasing the power output of the welding gun transformer, adding a current sensor, and installing CDC software into the existing welding controller. CDC can be said to be an ideal new welding technology that features advantages of both conventional DC and AC welding methods.
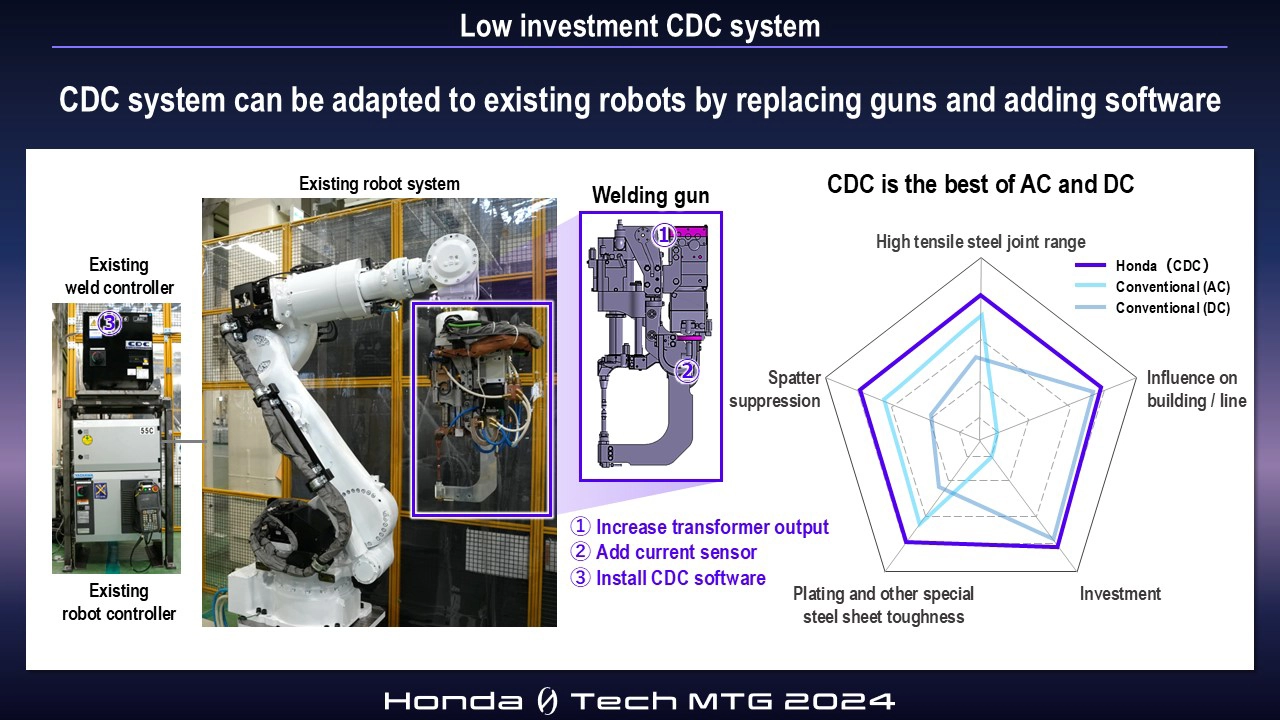
CDC welding mechanism
In conventional DC welding, the iron molten pool expands monotonically. This causes the walls of the molten pool to be thin and break down easily, generating spatters. On the other hand, in CDC welding, the pulses cause the molten pool to repeatedly expand and contract, creating thick walls effectively and suppressing spatters. The high peak current forms a large heat generating area between thin and thick sheets, which does not exist with DC welding. CDC is the spot-welding technology that has combined these two opposing factors: welding between thin and thick sheets and spatter suppression between thick sheets.
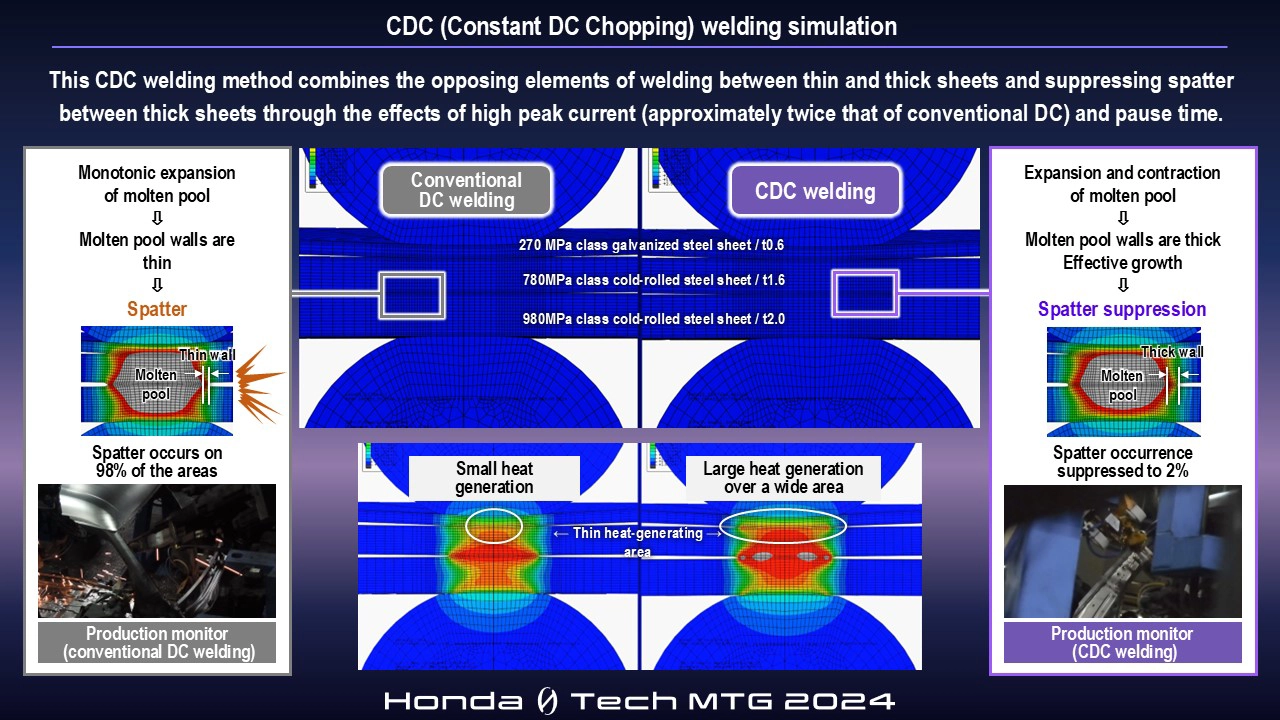
CDC joining technology demonstration 1
CDC joining technology demonstration 2
Honda will expand the deployment of CDC welding technology not only to the development of BEVs, but also to all areas including engine and hybrid electric vehicles.
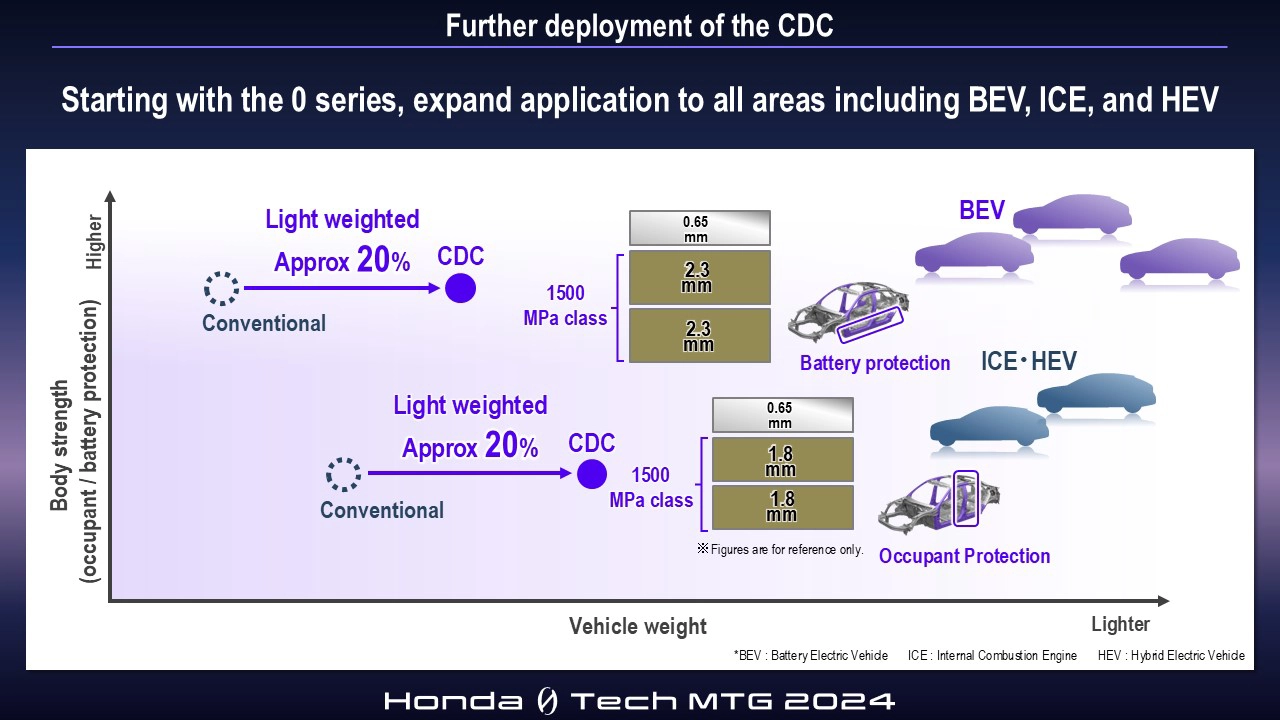