Electrified Power Unit eGX
GXE2.0H (Integrated) / GXE2.0S (Separated)
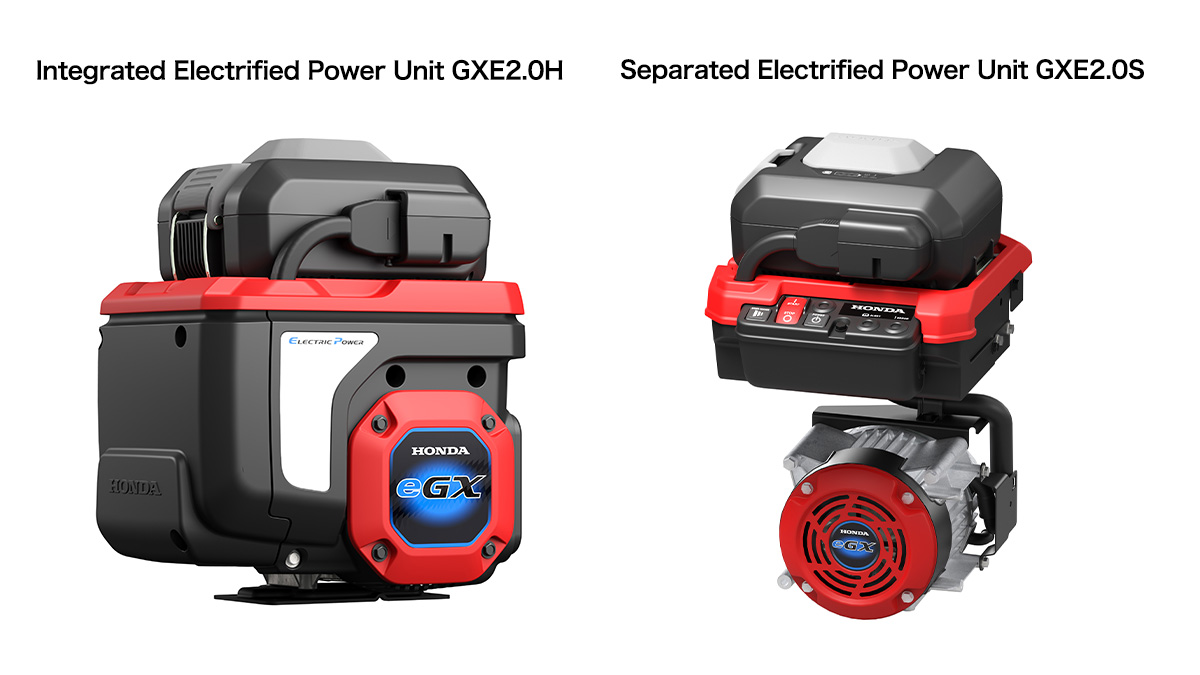
Electrifying the 2kW class GX Engine
Aiming to lead the world trend in electrification, Honda is working on electrifying a wide range of products. One example is the eGX electrified power unit, an electric version of Honda's GX series of general-purpose engines, popular since launch in 1983 over 40 years ago thanks to its excellent reliability.
Compared to 1kW-class power units for light-duty work such as brush-cutters and walk-behind lawnmowers, the eGX realizes the commercialization of 2kW-class power for heavy-duty work equipment such as construction machinery which had yet to be electrically powered due to severe operating environments. By electrifying the large-capacity class power unit, Honda aimed to contribute to the environment by reducing exhaust gas emissions from general-purpose engines, and to protect operators by reducing vibration.
About general-purpose engines / GX engines
General-purpose engines are engines manufactured for use in various types of work equipment. Honda introduced its first general-purpose engine in 1953, which was continually improved. As a result, in 1983 Honda launched the GX engine, revolutionizing general-purpose engines. At the time, side-valve (SV) engines were commonly used in general-purpose engines. To vastly improve high-output, low fuel consumption, durability, quietness and high reliability, overhead valve (OHV) mechanisms were promising, but were difficult to make compact and had too many components. The GX engine overcame these problems and was introduced as a compact, high-performance general-purpose engine with an OHV mechanism. Since then, the GX engine has powered a wide variety of work equipment around the world, and has continued to evolve and gain high reliability.
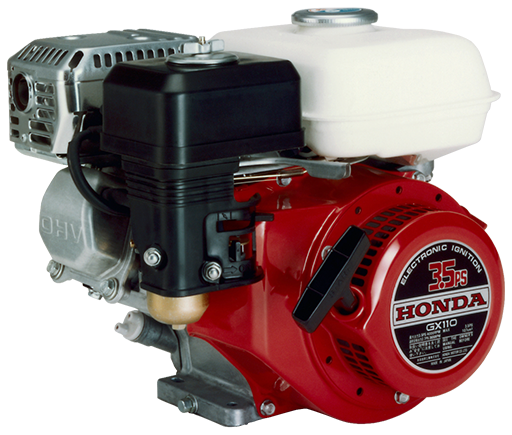
GX110 launched in 1983
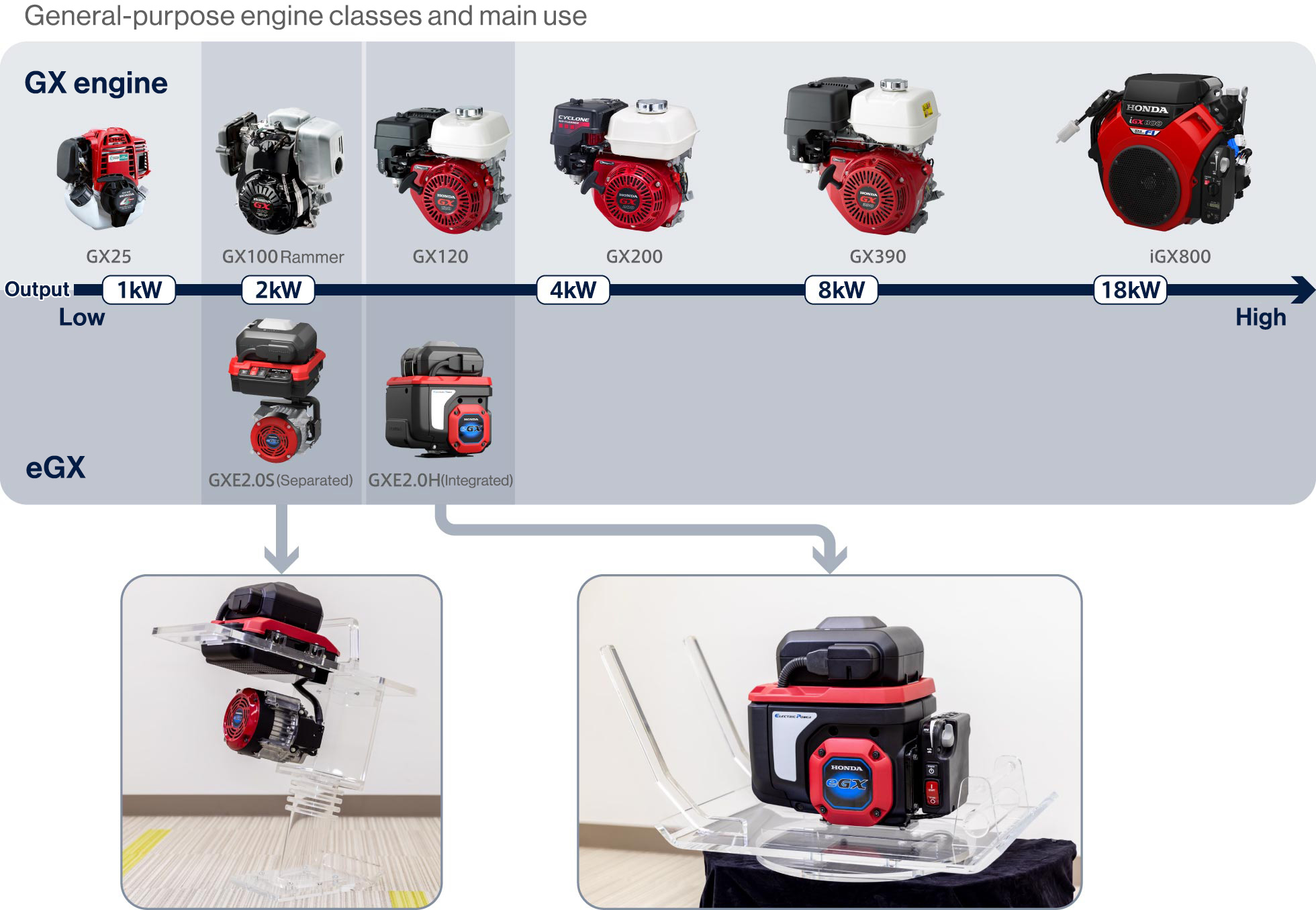
eGX mounted on construction machinery rammers (left) and plate compactors (right) seen at construction sites (acrylic models)
Durability Tests on Construction Machinery Subjected to Severe Loads of Tens of Gs
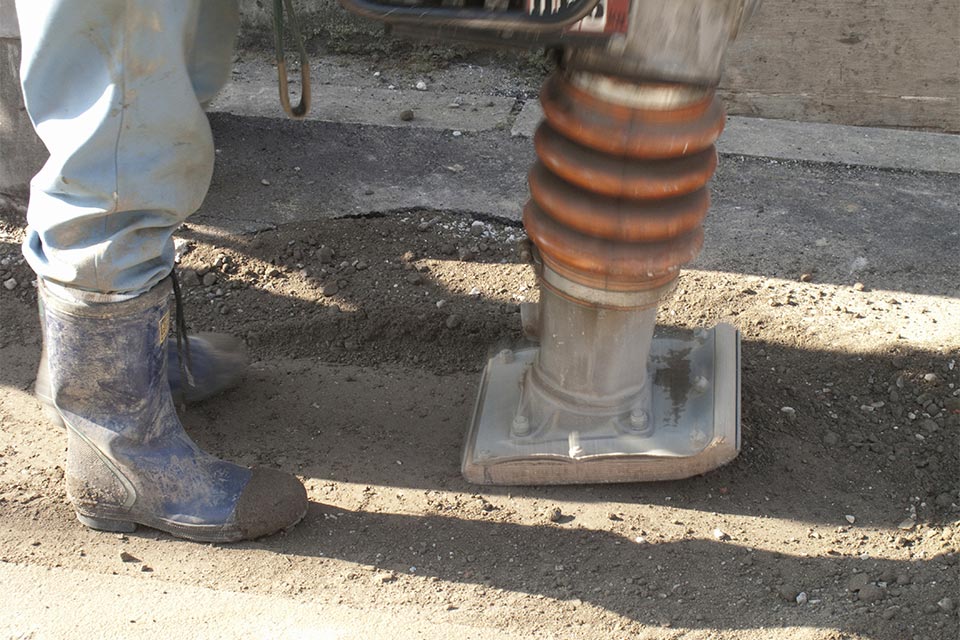
Rammers compact surfaces using impact, with a reaction causing the same amount of impact to the operator
Equipment used at construction sites, such as rammers and plate compactors, which compact the ground using impact, are subjected to a reaction force that pushes the ground, sometimes up to several tens of Gs, back into the machine. Unlike engines, the eGX is an electrified power unit that requires no oil lubrication and is equipped with precision control electronics. Various efforts have been made to have the same durability as the GX engine by introducing shaft support design, increased rigidity of motor components, and vibration isolation with rubber mounts for the battery and control system.
Attention to Design that Looks and Feels Secure and Compact to the Touch
The GX engine is a long selling power product model. To describe the reliability of its design cultivated over decades, the new eGX employs a horizontal base design that appears stable and level with the ground. In addition, red casing around the center shaft with an engine icon, doubling-up as a maintenance hatch, express a sense of security and that the eGX is the successor to the GX engine.
In addition, since workers often touch construction equipment, a rounded design helps keep operators from hurting themselves.
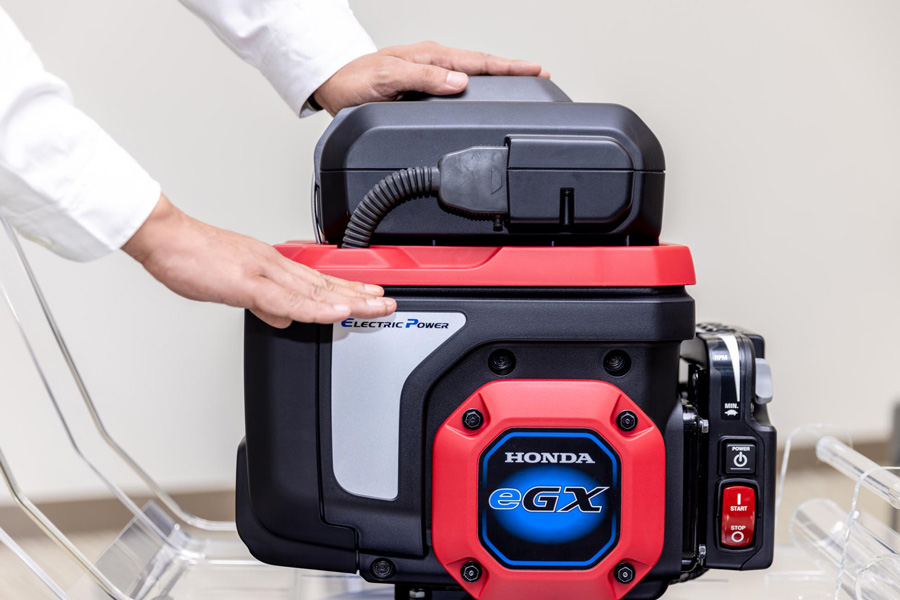
Horizontal base design without edges ensures rigidity while also being safe to handle as it is round.
Two-stage Cooling with Fan Inside Motor
The eGX is equipped with precision electronics, requiring more cooling than equivalent engines. While engines can tolerate temperatures up to about 150°C, motors must be used at 80–100°C or lower to prevent damage to the semiconductors on the electronic boards that make up the sensors inside the motor, the motor driver power unit, the battery control system, and other components. Honda’s solution was a two-stage cooling structure, placing a fan inside the motor to convect internal air, which is sent to the outer aluminum motor housing, which in turn is cooled by an external fan. Although the structure is complex, this system was selected to enable the electrified power unit to be used in harsh conditions. The motors are manufactured in-house, demonstrating how Honda is committed to this technology.
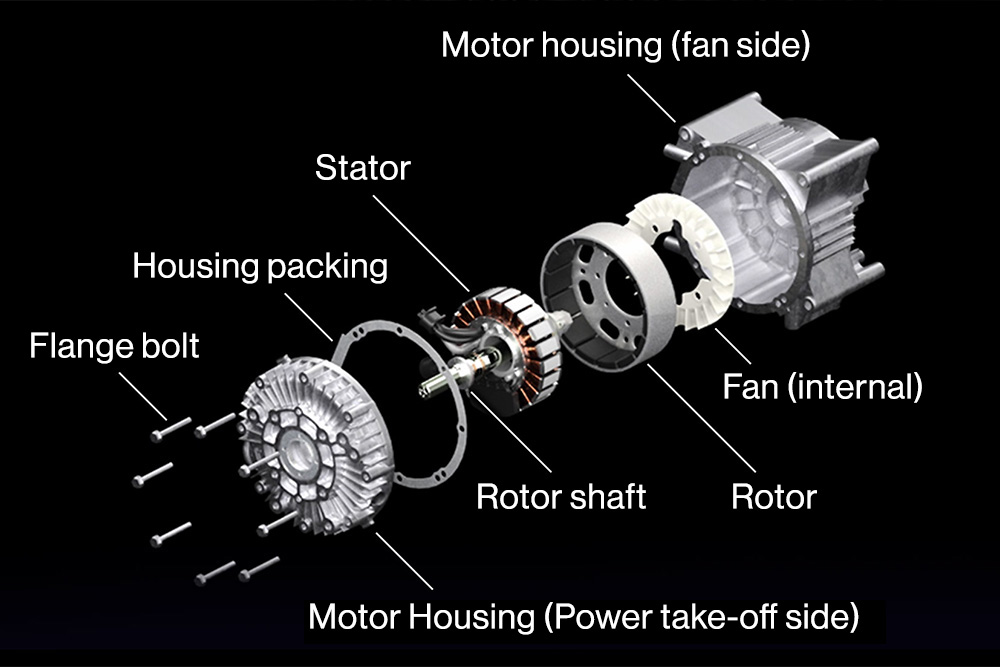
To the right of the stator where the coil is wound is a bowl-shaped rotor. To the right of the rotor is the inner fan. The outer fan is not depicted. On the far right is the finned aluminum motor housing.
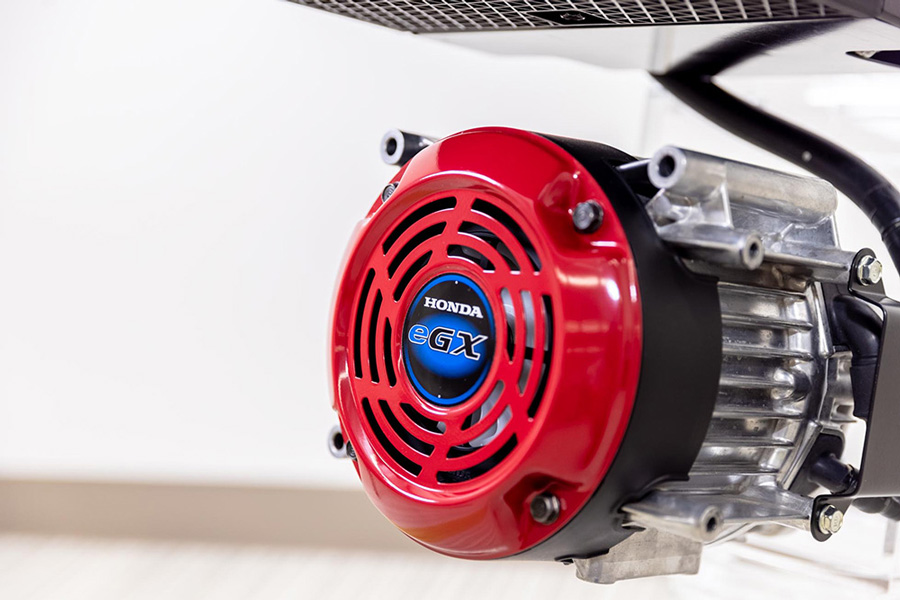
eGX (separated). External fan can be seen through the red mesh. The aluminum motor housing has cooling fins.
The Battery Area Has Ingenuity
Most electrified products house the battery either inside the device itself, or in a protective casing. The eGX’s battery is strong enough to withstand being dropped standalone from a height of more than 10 meters, so it is mounted without a protective casing. This eliminates the space needed to open the case lid, allowing the eGX’s battery to be mounted on top of the motor, similar to the gasoline tank mounted on top of the GX engine. The battery can be replaced from the top, as easy as refueling the GX. Furthermore, the rounded edges create a compact layout, allowing the eGX to be mounted as easily as the GX engines. Testing has verified that it is resistant to salt water based on water and dust resistant standards of certification organizations..
The battery consists of lithium-ion cells stacked in a square bale shape, surrounded by air channels for cooling, which is essential as lithium-ion batteries cannot be recharged unless they are below a certain temperature, and rapid recharging is impossible without cooling.
Since completely sealed batteries take more than two hours to cool, the eGX has an air vent at the bottom of the battery to allow cooling air to flow inside, reducing cooling time to around 10 minutes, and allowing it to be charged to 80% capacity in an hour. The eGX has the capacity to be operated for 30 minutes to an hour, so three batteries are enough for uninterrupted eGX operation. The eGX could operate for a longer time by increasing battery capacity, but this would increase weight and cost, therefore it was made purposely to be used while replacing multiple batteries.
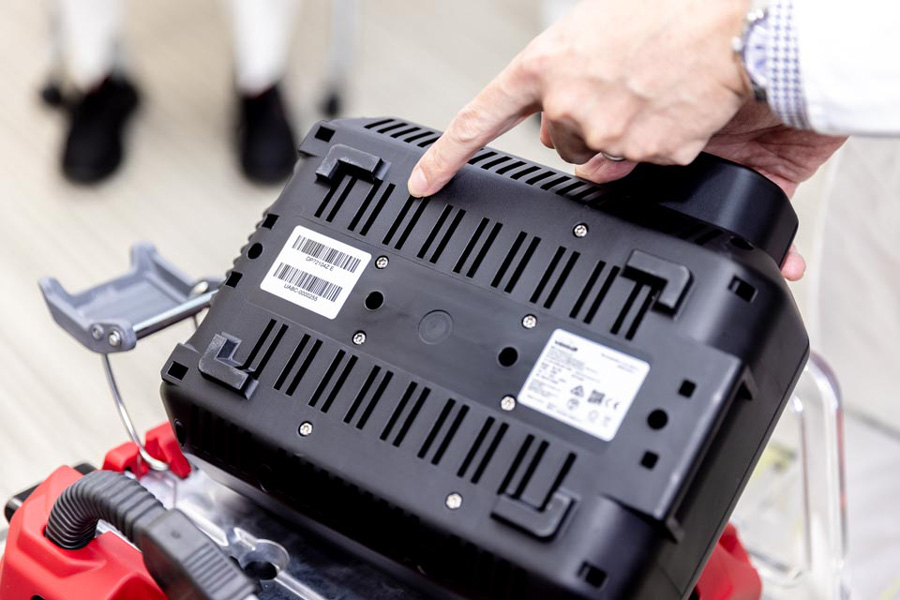
Slits below allow air to cool the battery, reducing the battery temperature sufficiently for quick charging within 10 minutes
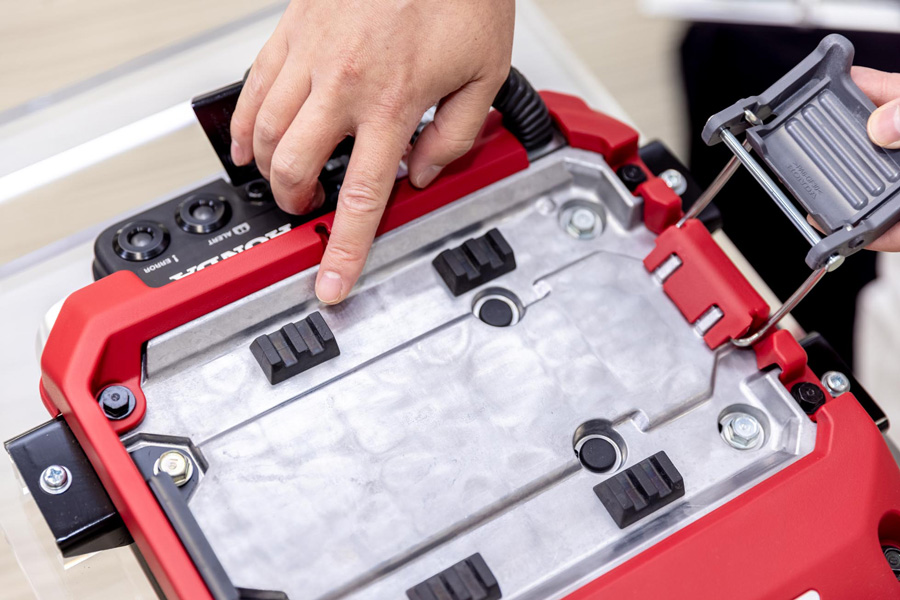
Battery supports have cushioning that is not too hard or soft, to absorb shock while firmly securing the battery
Possibility of New Needs Through Electrification
The first thing the user is surprised by using the eGX, is how easy it is to start with just a push of a button, and how quiet it is because it is powered by a motor. The eGX is easy to operate, without the hassles of maintenance and dirty hands from filling up the gas tank and changing the oil and air cleaner. The advantages of using an electrified power unit go further. Construction work on condominiums and buildings is often done during the day and at night, therefore, some work cannot be done at night due to noise considerations for the neighborhood, which potentially affects construction schedules.. By using quiet, electrified work equipment, this work can be done at night or early in the morning, leading to a shorter construction time.
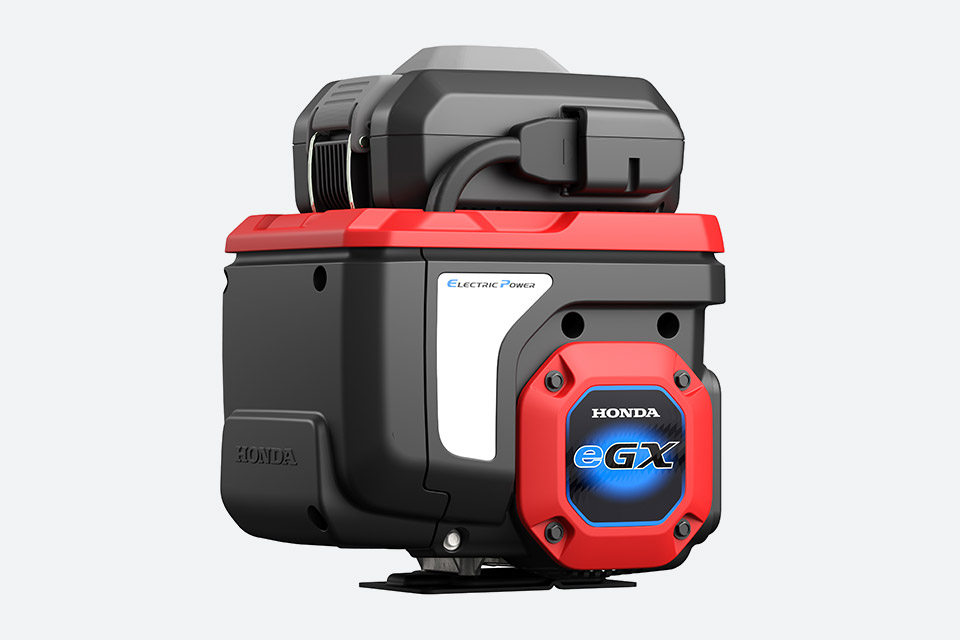
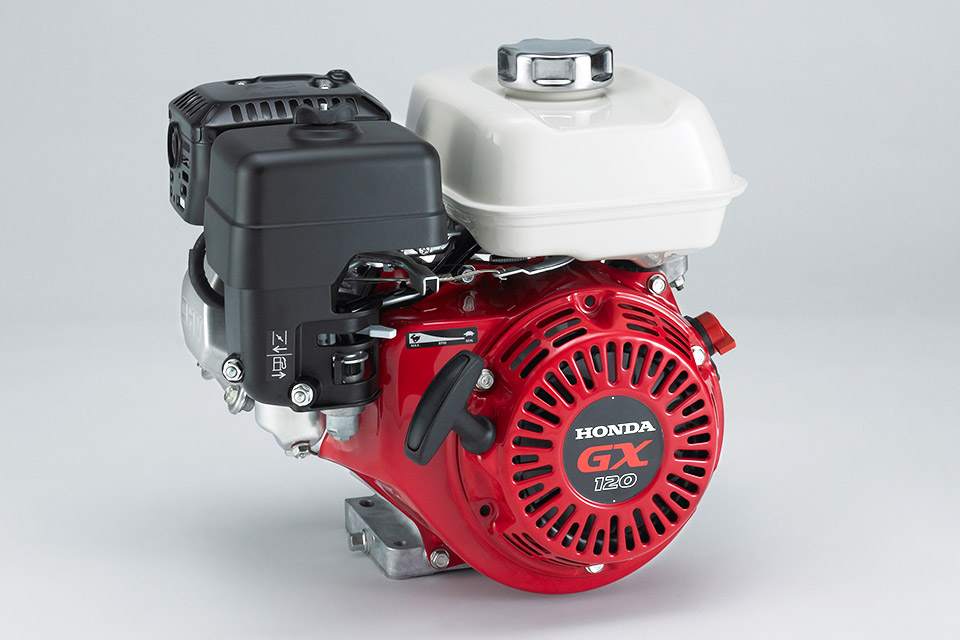
The eGX electrified power unit (left) and the GX120 general-purpose engine (right). Electrified power units are expected to become the mainstream power unit for construction machinery in the not-too-distant future.
The ease of use and maintenance-free advantages of electrified power units may also lead to new needs for work machines that were previously unimaginable, or replacing work done by hand that is too troublesome. With the growing momentum for carbon-free products and environmental regulations in various countries, Honda believes that there will come a time when it will not be able to provide engines. At that time, electrified power units will be installed instead. Starting with the 2kW eGX, Honda will further accelerate electrification.
GX Engine / eGX Electrified Power Unit Starting Procedure, Quietness and Vibration Comparison
Video comparing GX engine and eGX starting procedures, quietness and vibration. The eGX electrified power unit was designed to be easy to start, quiet and low-vibration.
INDEX
TechnologyElectrified Power Unit eGX GXE2.0H (Integrated) / GXE2.0S (Separated)