The Car Navigation System / 1981
Behind the Success of the CVCC Engine
The automobile, according to a well-known joke in Japan, is "a third-class machine." But the logic of such a statement is not without some truth, however, since the car is utterly dependent on human control. A car cannot move unless the driver tells it to do so. Moreover, people must undergo twenty to thirty hours of training before they are able to operate a car safely. Therefore, in essence the joke is saying that no other machine demands such a degree of human attention. However, it also infers that there is some other potential direction in automotive technology, which is in a way quite true. The world had finally come to believe, and indeed expect, that the car could function in a more intuitive, intelligent manner.
The automotive industry experienced rapid progress during the 1970s, especially in terms of electronics technology. A major factor in that progress were the emission-control regulations, which were getting more stringent with each passing year. Many car makers were busy attempting to use electronics to resolve the issues that were keeping them out of conformance with the requirements. Ultimately, though, the industry's electronics control technologies were applied to a broad range of automotive components, including transmissions and meters, thus creating a new field of endeavor known as "car electronics."
Throughout this period, Honda was actively engaged in the development of its newest engine concept, the CVCC. The reason for this was simple: Honda knew its CVCC engine would meet the requirements of the Clean Air Act of 1970, a bill enacted by the U.S. Congress. Indeed, the new powerplant was a surprise to the entire auto industry, demonstrating the high standard of refinement that Honda's engine development technologies had achieved.
The field of car electronics was moving forward, however, leaving Honda behind. While Honda had successfully developed a very efficient, clean-running engine that short detour had distracted Honda R&D from other pressing needs for the immediate future. Therefore, in 1976, Katsutoshi Tagami, who was in charge of portable generator developments for power products, was called by Honda R&D Center's Senior Managing Director Tadashi Kume, who said, "I want you to take charge of electrical equipment for automobiles."
Tagami was given the order to run the Eighth Research Block, more commonly known as the Electrical Equipment Research Group. Tagami, who had never before considered having any involvement in cars, was thoroughly surprised.
"Your role," Kume explained, "is to bring us up to the level of other manufacturers and eventually get a step ahead of them."
Kume, having seen the astounding progress the industry had made with regard to electronics technologies, was seriously concerned about the company's ability to compete in that regard. He knew electronics technology was becoming an integral part of engine development.
The development of electrical equipment at Honda had always been left to outside specialists who could manufacturer and supply the required parts. Accordingly, the outside development of such engine systems would require that all of Honda's engine specifications be disclosed to the suppliers. This was clearly unacceptable to Honda, whose business was founded on engine technology. Kume's wish to "get one step ahead of them" reflected his determination to resolve the matter.
Creating a Progressive Strategy
Tagami was resolute: "The things to which we are passionately committed demand an environment where we have the freedom to work, without unnecessary restrictions. If we let go of our engines, Honda will cease to be. Accordingly, the protection of our engines - indeed, the company itself - means we must have our own car-electronics technology."
Determined to make it happen, Tagami began developing a comprehensive strategy for engine electronics. He wanted an overall picture as to what technological advancement Honda had to achieve and how, in order for the company to gain a foothold in that area of endeavor. A hastily drawn-up strategy spelled out the future direction of cars, in tandem evolution with electronics technology. The key phrase for this was "intelligent automobile."
The strategy made use of a basic outline, as follows: Progress in electronics technology would facilitate the control of engines and transmissions, leading to automatic cruise control. Automation would further advance to the area of steering control. Eventually, the driver would be able to input a destination on the map, at which the car would automatically select the optimal route and take him there. The ultimate goal of development would be a fully automated car that could drive itself.
Kume called his concept ACE, for "Automatically Adaptive and Creative Electronically Controlled System." It was a concept that would eventually result in the development of PGM-F1 systems and anti-lock braking systems.
Travel route guidance was one of the features outlined in the ACE strategy, However, it did not foresee the sophisticated systems of navigation with which Honda is now familiar. To take the concept to that level would require further study, many new ideas and a great deal of effort.
A Gas-rate Gyro Comprising Just Eight Parts
Kume had a chance to visit a training site used by Japan's Self-defense Force. Watching a group of tanks rumble across very rough terrain, Kume suddenly noticed their gun barrels. Regardless of the attitude of the tank itself, the barrel was able to maintain constant aim with respect to its target. Kume, who was later told that the barrel was controlled by a gyroscope*1, thought of adapting that technology for use in cars. Upon returning to the R&D Center, he gave the order to study gyroscopics.
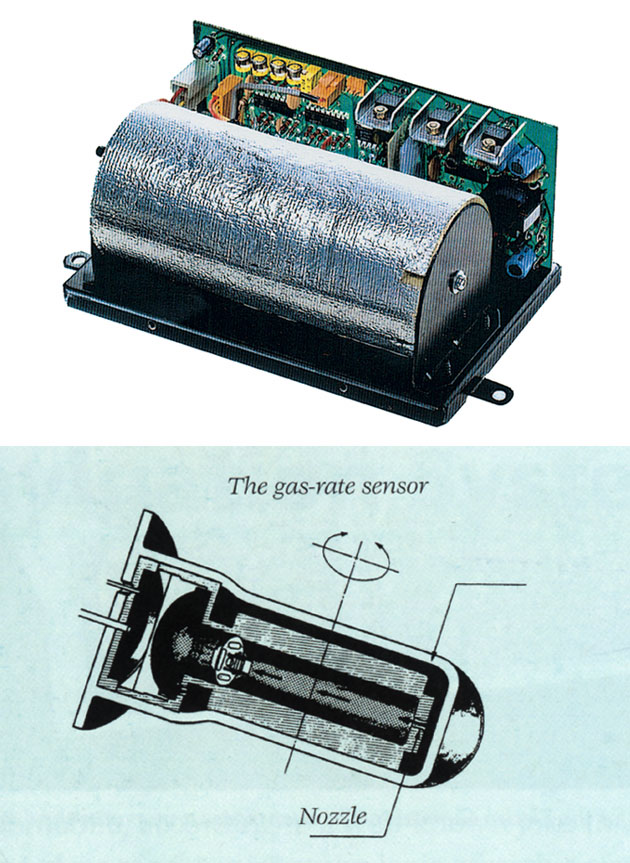
The gas-rate gyro that led to the development of a practical navigation system for cars
Having heard of Kume's idea, Tagami believed the technology could be applied to suspensions, but that notion was dispelled when he got hold of a gyroscope and disassembled it. Not only was a gyro a result of precision engineering, it had more than 200 parts. Obviously, it was something that could be adapted to mass-produced cars. However, some new form of technology was needed in order that Tagami's electrical/electronics strategy might come to life. Tagami persisted choosing not to give up on the gyroscope, leading him to the gas-rate gyro.
The gas-rate gyro works by using the inertial force of gas to move straight, employing helium ejected from a nozzle and blown onto two heated wires. The unit determines directional changes by sensing the temperature differences between the two wires. Therefore, this type of gyro, which employed just eight parts, was a very appealing candidate. However, it was not very accurate, and the zero point was often impossible to locate precisely. It was a problem for the development staff, but further study nevertheless identified certain benefits. As a result, the staff continued its research, hoping to develop a system that would offer reliable control, although within a limited range, along with constant zero correction.
The team's research in gyroscopics took a new turn in 1977, when a staff member proposed that the system might be utilized for travel-route guidance. The suggestion was that the gyro's direction-sensing function could be used to guide a car if zero was constantly adjusted to the target road.
The team began experimenting immediately. First, a map was drawn on a transparent sheet, then the target route was traced using a black, felt-tip marker. The objective of their experiment was to confirm whether the sensor could follow the route and guide the car. In fact, their initial results were highly encouraging. Subsequent experiments examined a more advanced idea, attempting to determine whether the sensor could pinpoint its own location according to road patterns and the car's direction of travel. This indeed became the starting point for important research, eventually leading to the world's first automotive navigation system: the Honda Electro Gyrocator.
Note:
*1 Gyroscope: A device consisting of a Spinning wheel mounted on a base so that it can rotate freely in the three axes.
Gyrocator Development: A Path Strewn with Difficulties
The concept had been defined, but many problems had yet to be resolved. The most troublesome of these was the gas-rate gyro's lack of accuracy. To make the system truly practical, it would have to be improved and stabilized, especially with regard to the zero point.
The research team had used trial and error to produce various improvements in the system's eight basic parts. Among these was the discovery that fluctuating performance was the result of variations in ambient temperature, resulting in the use of a special chamber to control temperature and ensure consistency. Meanwhile, Tagami was looking for a supplier to produce a stable-running gas-rate gyro, since doing so would require a high level of vacuum technology in order to increase the purity of the helium gas used.
Tagami was leading development of a new technology, with great uncertainty as to whether it would become an actual product. Therefore, suppliers were understandably hesitant. After many rejections, Tagami's only hope was the headlight manufacturer Stanley Electric, which had superior vacuum technology. He visited the company's research center every day and pleaded for support, and finally the director agreed.
"I think that as an engineer he could relate to our passion for the creation of something new," Tagami said. "He gave us support by standing up to objections within the company. In fact, he really saved our lives."
Stanley and Honda thus began a collaborative effort to make the gas-rate gyro more consistent and accurate. That would not be an easy task, though. Later, the extent of that challenge became evident when the initial mass-production data showed a yield of only one in ten units.
Could the Map Be Wrong?
Some hurdles encountered by the research team had not been expected at all. For example, while the accuracy of the gas-rate gyro had improved and the system could at last be road-tested, one problem cropped up during that process. At the evaluation test, Tagami drove the car carrying Kume and Nobuhiko Kawamoto, then an assistant general manager at the R&D Center. The car had gone over the same route several times, but each time it deviated from the course at the same point. For the longest time they could not understand why. It has long since become a joke, but for a time they seriously considered whether there might be a secret military facility nearby. They even conducted a study with a field-intensity measuring device. However, all their efforts to identify the cause simply failed. Then, after every viable possibility had been considered, the team came to think the map could be wrong.
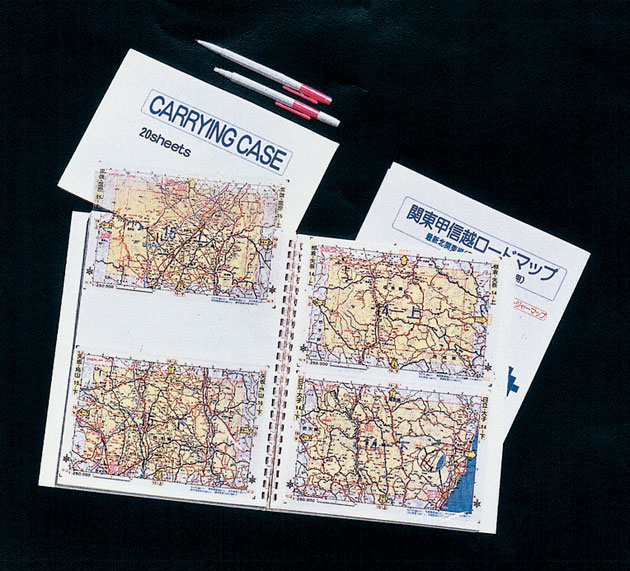
Map films for the Electro Gyrocator. The user places a map over the CRT.
The company that had sold them the map was contacted. It was then that the team learned about the general inaccuracy of cartographic representations.
For example, on a map of a 1:100,000 scale, a road of 10 meters wide is shown via a line only 0.1 mm thick. However, in an area where many roads run close together, a number of thin lines will necessarily overlap, making the map difficult to read. In such a case the roads are shown by ignoring actual distances to a certain degree. This practice, called "deformation," has long been common in cartography.
It was eventually decided that maps would be created specifically for the experimental system. However, the team was forced to make a detour because of this incident.
The Final Test: From Suzuka to Tokyo
A final evaluation was held at the beginning of 1981, the requirement of which was that the system could send Kume from a meeting of automobile dealers in Suzuka back to his house in Tokyo. Once Kume had circled the location of his house on the map, the car left Suzuka at six o'clock in the morning. Of course, Tagami did not know the exact location of Kume's house. They simply headed for their destination, getting on and off the expressways according to directions given by Kume. By the time they reached Tokyo, it was already after seven in the evening.
The decisive moment was drawing near. Tagami was watching with eager anticipation as the indicator on the CRT got closer to the circle. Finally, he stopped the car.
"I believe your house is around here," said Tagami.
After a moment's silence, Kume replied, "Okay, you passed the test. My house is right over there."
The words resounded in Tagami's mind, as if to reward him for the completion of such a long and arduous journey.
It was the birth of the first navigation system ever developed for use in a car. In August 1981, the Honda Electro Gyrocator was introduced as a dealer option for the second-generation Accord. The new system was not just a shock to the automotive industry; it sent the electrical equipment makers running. The strategy that had anticipated the future of technology, together with an uncompromising effort to create a reliable gyro and dedicated maps, had led to a new era in automotive capability.
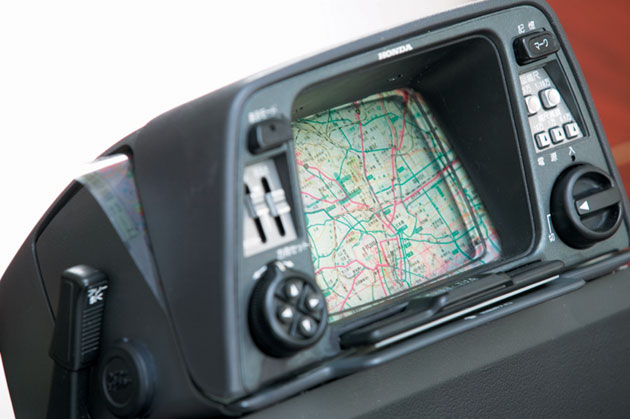
Honda's Electro Gyrocator - the world's first navigation system for use in a car
The Challenge of Digitization
The development of next-generation navigation systems was initiated in January 1982, five months after the release of the Gyrocator. Three concurrent sub-projects were started under the main development theme, the objectives of which were as follows:
[1] Develop an analog map-based navigation system as an advanced version of the Gyrocator (generation 1.5).
[2] Develop a fully automated system that uses com puter and digital maps to perform automatic map matching (second generation).
[3] Study the technology of optical-fiber gyroscopics.
Honda had decided to run three projects concurrently in order to ensure its dominance in the field of navigation, especially with respect to other manufacturers. However, what would pave the way for Honda's future was the project dedicated to digital map navigation.
Yukinobu Nakamura, who had proposed systems using digital maps, was appointed the project's LPL (Large Project Leader). Outlined in his mind was a direction that would transform the analog system to the digital format. In fact, beginning in about 1980 Nakamura had briefly studied on a company scholarship at the Electronics Engineering Research Laboratory of the Industrial Engineering Institute, an organization operating under the Ministry of International Trade and Industry located in Tsukuba Gakuen City, Ibaragi Prefecture. During his study of optical-fiber gyro technology there, Nakamura had conceived the idea of a digital, map-based navigation system.
The major difference between an analog map system and its digital counterpart is that the latter employs a function known as "map matching." It is a technology whereby the system uses digitized map information to compare the car's actual direction of travel to road patterns, thus determining the current position with a higher degree of accuracy. Although the technology itself was developed over a course of several phases by multiple companies, it was Honda that eventually got hold of the basic technological patents, including the map-matching technology and know-how in digital map creation, including partition storage, composite display, smooth scrolling of the screen, etc. Because of this, the company was able to pioneer digital map technology as we know it today.
"A System That Cannot Lie"
The process of development was never easy, and there were many turns in the road. One major obstacle was the lack of appropriate media for data storage. When Honda first digitized maps, there was no media in the world that could store such vast amounts of data. After all, this was a time when standards for the compact disc were being established, and Honda's tests were using 8-inch floppy disks. The volume of data was so huge that to store the information from maps comprising all of Japan would require several hundred disks.
Another obstacle was Honda's uncompromising stance toward the development of next-generation navigation systems. For both digital and analog systems, the development team had been asked to take the performance to the absolute limit. Kawamoto, who had earlier been promoted to vice-president at Honda R&D, often instructed his staff to "please develop a system that cannot lie."
A system that does not lie obviously means an infallible one. For example, a calculator that could not compute the correct results would not sell. The same logic applies to navigation systems. Customers wanted perfect systems, so the development staff faced tremendous pressure. In those days, Nakamura would often have dreams about evaluation tests, and in those dreams the car would deviate farther and farther away from the target route, right in front of Kawamoto. He would panic, only to wake up and find it was a dream. It was sheer torture for him.
Analog to Digital: A Three-year Detour Leads to the Goal
The development of Honda's analog map navigation system, which was scheduled to finish before the digital system, was still struggling along in 1983. Following the abandonment of an initial plan of using laser discs to store map data due to difficulties with the company's joint development partner, the team had adopted microfilm as an alternative. However, that system made it difficult to change maps automatically, which was a system requirement. Fortunately, an improved situation in 1984 allowed Honda to resume the joint development of laser discs. Therefore, to compensate for the delay, Honda directed the majority of its development effort to the analog map navigation system. Development of the digital system was temporarily suspended when Nakamura was appointed LPL in charge of the analog project.
However, progress in digital technology would not stop simply because Honda had turned its attention to analog. In 1985, for example, the U.S. company ETAK introduced its own digital map navigation system. Although the system's effective range - the area of geographical coverage - was limited, the announcement was a dour one for Nakamura and his staff. Therefore, ultimately the development of a practical analog system was shelved. The staff experienced indescribable feelings of disappointment.
The development of the digital map navigation system resumed in 1987, following a three-year hiatus. However, obviously there was no time to lose. To create a practical system as soon as possible, the map-matching function was simplified to provide main-road navigation only. However, the high-precision gyro and advanced map-matching mechanism were combined to ensure the performance of the map-matching function even in the event the car was driven off the map.
In March 1988, the development project, which had been carried out independently by the Basic R&D Center (HGF), became a joint project with Tochigi R&D Center (HGT). Thus completed, the system made its official debut in the second-generation, 1990 Legend. This was in the end an ample reward for the development team, which through perseverance and constant dedication to a goal had produced a real and lasting innovation.
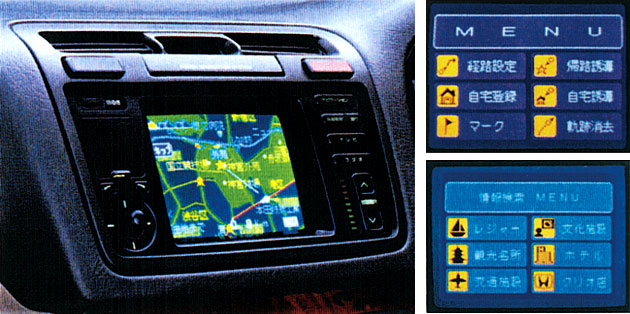
The second-generation NAVI, employing digital map technology. Honda holds patents for most of the basic technologies, including the CD-ROM maps, map-matching technology and map-partitioning storage system.
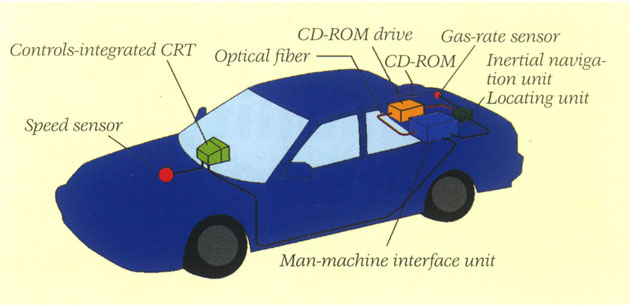
A layout drawing of the second-generation NAVI