世界No.1であり続けるために。
グローバルマザー工場・熊本製作所
熊本製作所はFUNモデルを中心とした生産を行いつつ、グローバルに向けた二輪車のマザー工場として重要な役割を果たしている。所長(2023年現在)の島添正規がこれまでを振り返る。
「2000年ごろがわれわれの新たなスタートだったと思う。当時、合計で年間500万台の世界生産販売を2010年までに3倍にする計画で、「50万台1パック」の工場規格をつくってグローバルスタンダードにした。1本で50万台だから、新たに20本のラインをつくる、これを10年でやるべく相当のスピードで進めた」
当初は、大量生産向け「50万台1パック」に対し、熊本製作所がFUNモデル、仕様が複雑なモデルは浜松製作所が担当したが、2008年に二輪拠点は熊本に集約。その間には中国のコピー車問題もあった。
「浜松では、中国の新大洲ホンダから送られてきたトゥデイのPDI(出荷前検査)をやっていた。ものすごいコスト競争力があったが、品質については日本のユーザーに受け入れられる品質に持っていくのはかなり厳しい戦いだったと思う」(島添)
2010年には、2020年までに世界生産販売目標を1,500万台から2,000万台へと拡大しつつ、海外工場の自立化、SEDBQ*3の現地化を推進した。全部が独立してそれぞれが地域特性に合わせた製品づくりを進めても、ホンダブランドとしての品質や信頼性が損なわれてはならない。
「統一・均一化を図るための手法の一つは、製造技術に関しては技術カタログをしっかりと整え、これをまずグローバルに公開にした。もう一つは治具情報の共有。例えばTHの描いた治具図をホンダ・ベトナム(HVN)が使うような場合、いったんはホンダの技術支援担当を通じてしか渡せなかったため、毎回手間と時間がかかる。それでは効率が悪いので、情報を相互補完し共有できるよう拠点間契約を締結している。共通プラットフォームの開発でも苦心した。例えば、ベトナム・タイ・インドネシアは同じグローバルモデルをつくるが、その外観が一緒の時もあれば、地域の好みで変える場合もあるので、生産ラインにちょっとした設計の違いがありなかなか共通仕様にしにくい。そこをしっかりと現場・現物でフィットさせるのが、ホンダの力でありホンダの特徴だと思っている」(島添)
- : S販売・E生産・D開発・B購買・Q品質
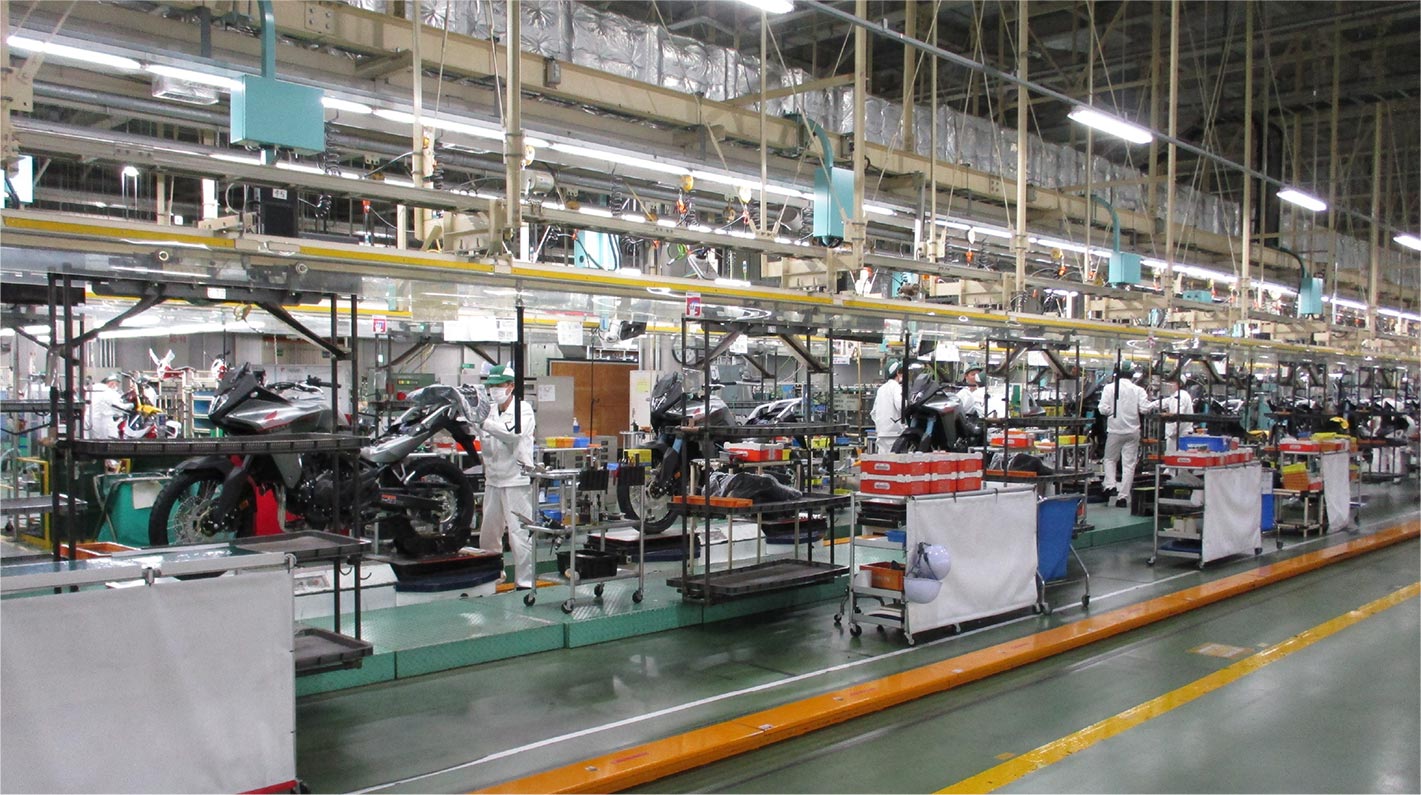
二輪車のグローバルマザー工場としての役割を担う熊本製作所
熊本製作所の職人魂、憧れをつくる
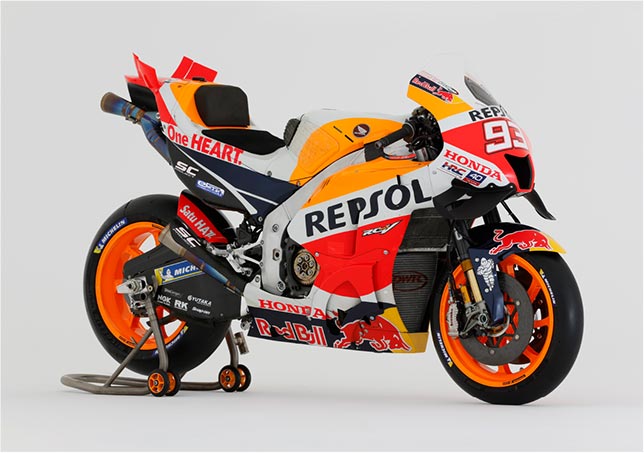
生産現場でホンダが得意とする現場力は、いってみれば職人魂のようなものだ。そこでは高効率と正確さを追い求めるだけではなく、ユーザーの憧れるトップエンドモデルも生み出して、世界中に二輪車ナンバーワンメーカーの意地と誇りをアピールしてきた。その最たるものは、2015年に上市されたRC213V-Sだろう。それは、ファクトリーMotoGPマシンRC213V公道バージョンを販売するという前代未聞の施策だった。
「熊本としても普通は経験のできない仕事だったので、その製造を『見せる工程』で行うことになった。量産モデルとは全く違うつくり方のため、現場の人たちがすごく努力して形にするものだから、やはりみんなに見てもらうおうと。それなら、目の前で見てもらうのが一番良いと、組み立てブースを設定した。それも『見せる』ではなく、『魅せる』にしたかった」と、RC213V-Sの量産化プロジェクトを企画した渡辺忠幸は振り返る。
課題は、必要な部品の調達と、それを組み上げていく人材の確保だった。量産品からみれば試作品ともいえる、特殊な部品の生産を引き受けてもらうために試作メーカーを説得することも大変だったが、納入された部品の管理でも苦労した。
「この数しかつくらない、もう二度とやらないというくらい、試作メーカーさんも骨を折ってくれた。納入も先方の都合で一括搬入か、分割搬入か、バラバラだったから、それをどうやって管理して払い出していくか。熊本の工場管理は量産で手一杯だったから、自分でやるしかなかった」(渡辺)
人材は、各現場で働いているメンバーの中から選出した。例えば、溶接一つとっても接合面の合わせは手作業で削って調整し、きちんと面出ししてから溶接していったのだが、そのビードは1ミリ間隔という基準が求められていたという。
「そこは携わった工程者の努力というものであり、そういうところを見せたかった。自分の経験からみると、溶接を担当した若いメンバーの取り組みはすごいものがあっただろうと思う。その経験で自信がついただろうし、自分の仕事に対して誇りが持てるのではないだろうか。若い人たちのパワーはすさまじいものがあるし、それが熊本のポテンシャルになっていくのだと感じた」(渡辺)
生産をするにあたっては、きっちり一つ一つ仕事を終わらせていくという考え方の下、1日1台という計画だった。その中には、「魅せる工程」のコンセプトも含まれている。ここでは、MotoGPマシン同等の高度な組み立て精度の再現性が求められたので、調整も含めて作業は全て手組みだった。「われわれホンダの人間としては、それが原点だと思っている」と渡辺は言う。
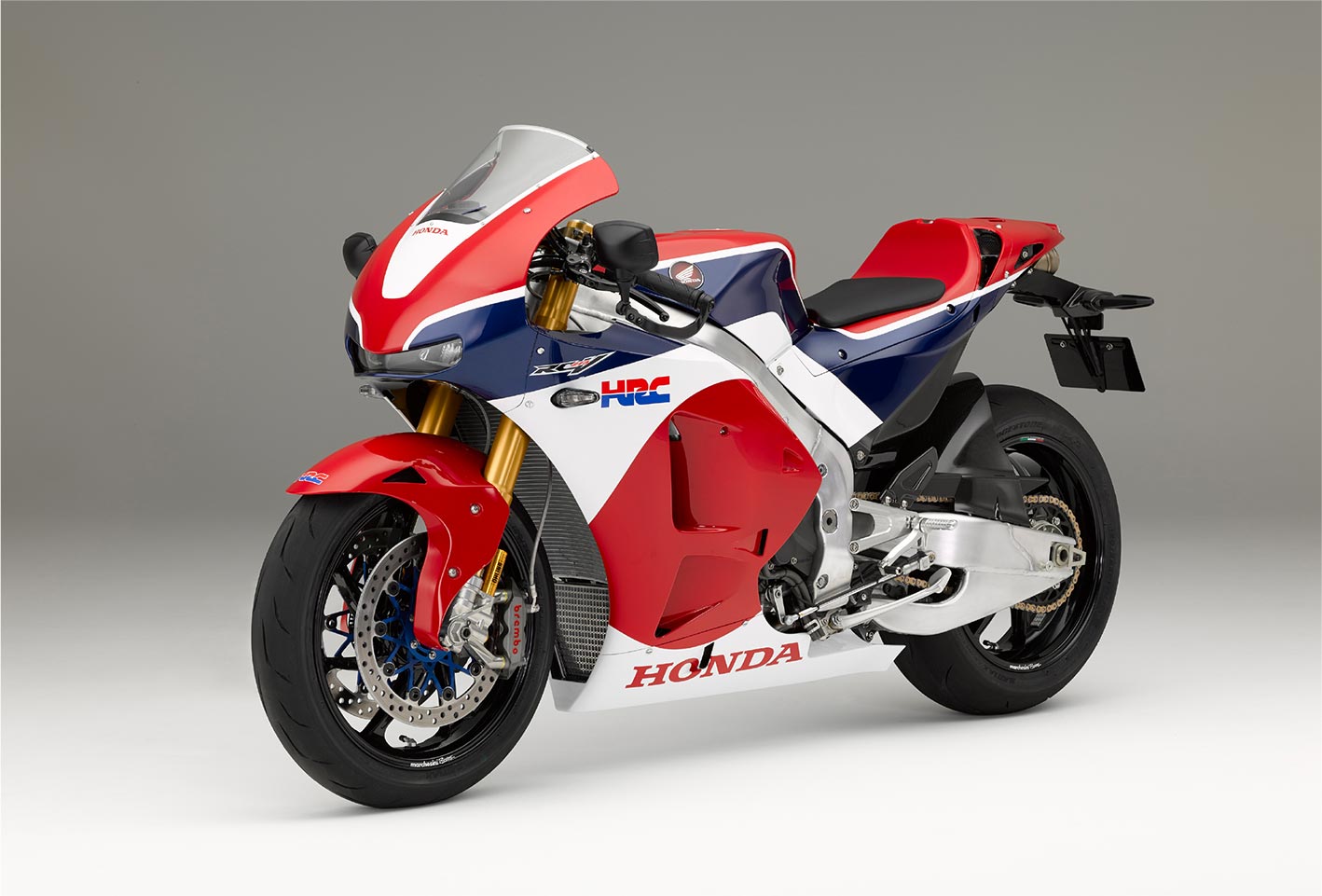
熊本製作所で作業を全て手組みで行った、MotoGPマシン RC213Vの量産モデルRC213V-S
時代は変わっても変わらないもの、三現主義の実践
2023年現在、熊本では開発と生産に線を引かず、DEB一体で事業を進めている。製作所内には開発部門の熊本分室が設置され、一丸となって課題解決に取り組んでいる。日本では部門最適で組織が細分化されていることが多いが、高度な専門性はメリットとしてある反面、各部門間協調における時間効率の遅さはデメリットとなる場合が多い。
「そこを解決してスピードを上げたかった。マザーである熊本で技術を確立し世界中に展開するには、日本側が一枚岩であることが不可欠だ」(島添)
島添は熊本の所長になった際に「マザー工場としてただ現地に支援に行くだけではダメだ。海外部品を使え」と言い続けたという。一つは経営的な観点で為替ヘッジをすること(海外部品を使えば円高になっても部品は安くなる)、もう一つは海外拠点がつくっている部品の品質を全員に認識させることだった。
「それを自分たちの責任として市場に出すとなれば、より本気で取り組むようになると考えたからだ。必要とあらば、現場に行ってお客様の話を直接聞き、自分で商品に乗ることも厭わない姿勢も大事だ。タイの販売店関係者が『ホンダだけはすぐ日本人が来る。他のメーカーとは違う』と驚いたこともあるが、納得がいかないなら、納得がいくまで確認することだ。それが、われわれが言っている三現主義であり、現場の者たちが状況を理解して『よし、やるぞ』と言って、どんどん手を上げて、一歩、二歩と行動に結びつけていく。それでやっていくしかわれわれに勝ち目はないと思っている」(島添)
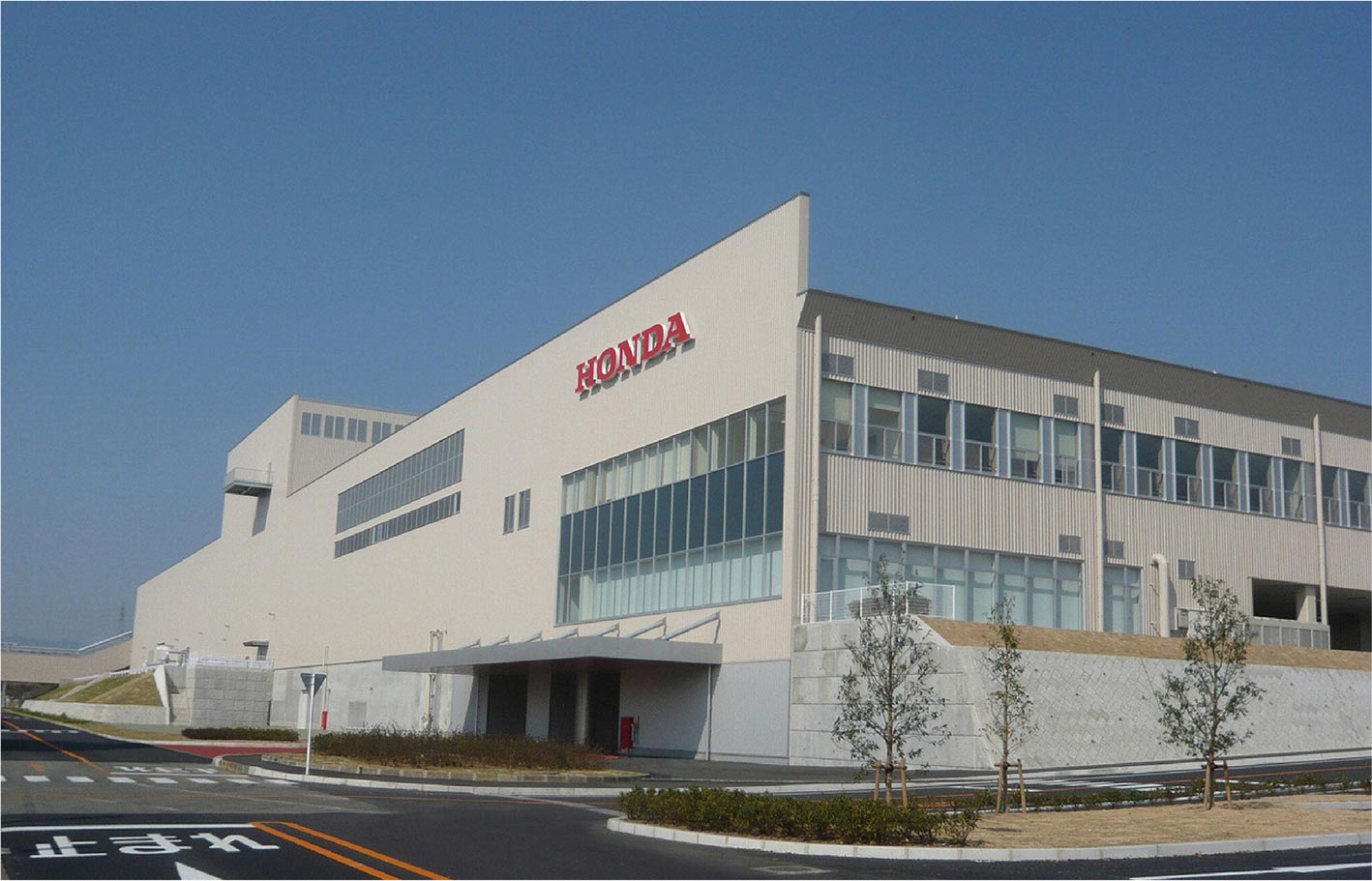
熊本製作所
ものづくりの誇りを込めた「RC30リフレッシュプラン」
2020年、二輪事業本部は熊本製作所に「VFR750R〈RC30〉リフレッシュプラン」を実行するためのモーターサイクルリフレッシュセンターを開設しサービスの提供を開始した。
これは1987年に発売されたRC30のコンディションを回復するための技術サービスであり、これまで入手が困難だったオリジナルスペックに近いパーツ約150点の販売や、熊本製作所内でのベテランエンジニアによるレストア作業を行うものである。
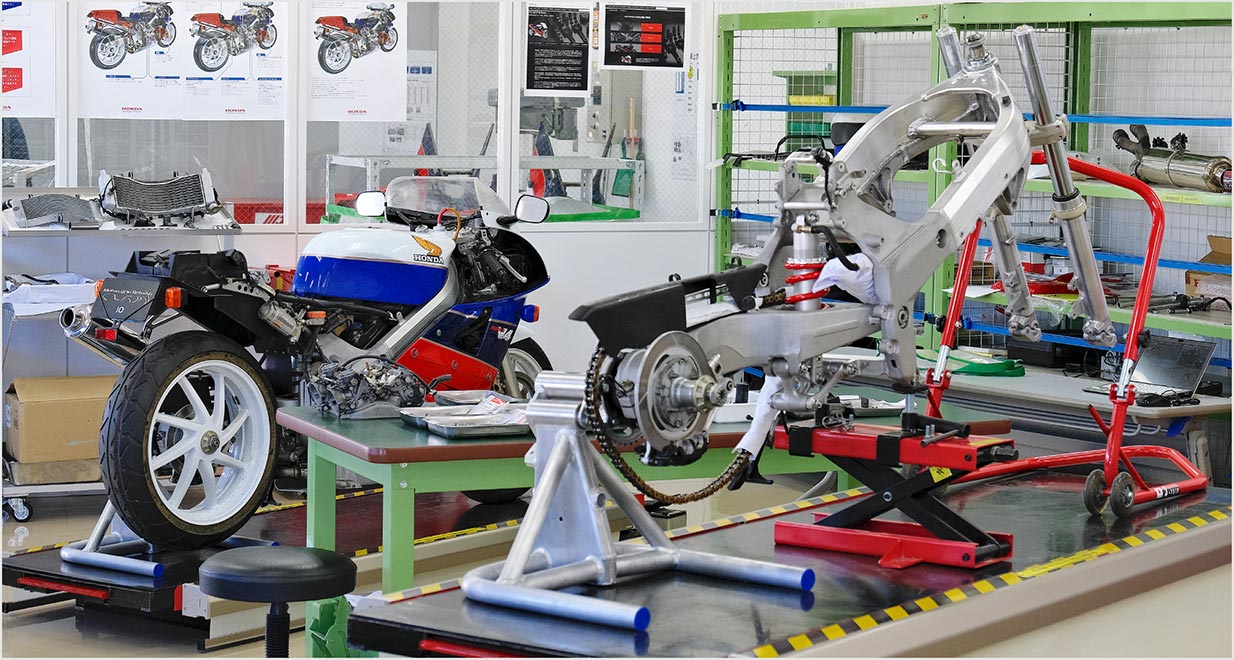