“Thin, Light, and Wise.(薄く、軽く、賢く)”という新たなEV開発アプローチにより、バッテリー搭載量を最小限にしながら、充分な航続距離と同時に、EVの既存イメージを超えた軽快な走りの実現も目指す「Honda 0シリーズ」。新価値創造には、生産技術にもこれまでにないものが必要となります。
2024年10月に開催された「Honda 0 Tech Meeting 2024」の現地で、核となる4つの生産技術に携わる担当者たちに想いを聞きました。
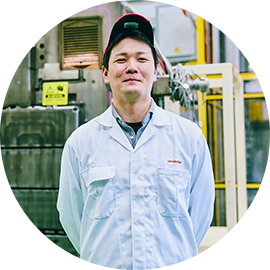
PU生産技術部 PU塑型技術課 もっと見る 閉じる 市川 稔
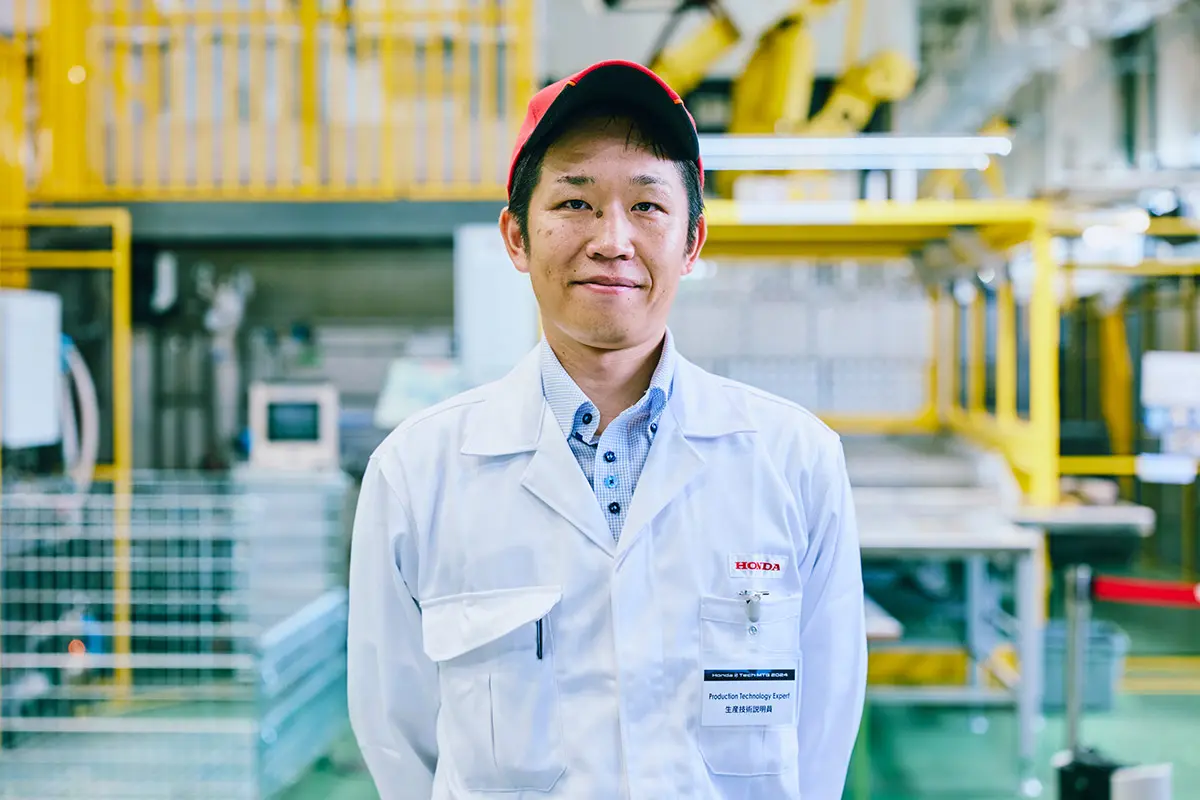
PU生産技術部 PU設備技術課 もっと見る 閉じる 吉田 篤史
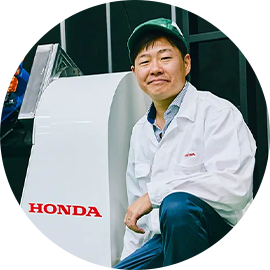
車体生産技術部 車体設備技術課 もっと見る 閉じる 伊藤 律規
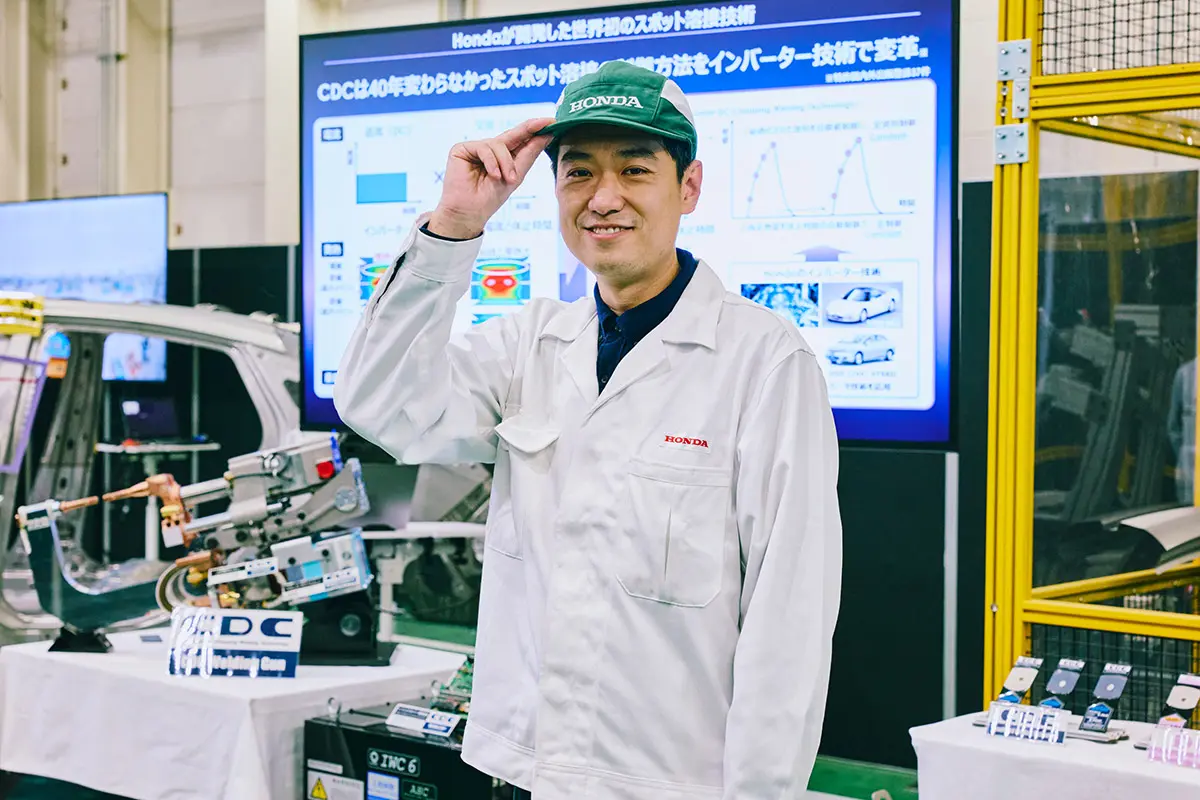
車体生産技術部 車体設備技術課 もっと見る 閉じる 譚 錫昊
クルマの新しい生産方法となるメガキャスト鋳造
メガキャスト鋳造とは、従来より大きな鋳造部品を一体成形するための技術です。バッテリーケースを一体成形することにより継ぎ目がなくなり高い強度を維持する、「Honda 0シリーズ」の“Thin”(薄く)、“Light”(軽く)実現に欠かせない技術です。
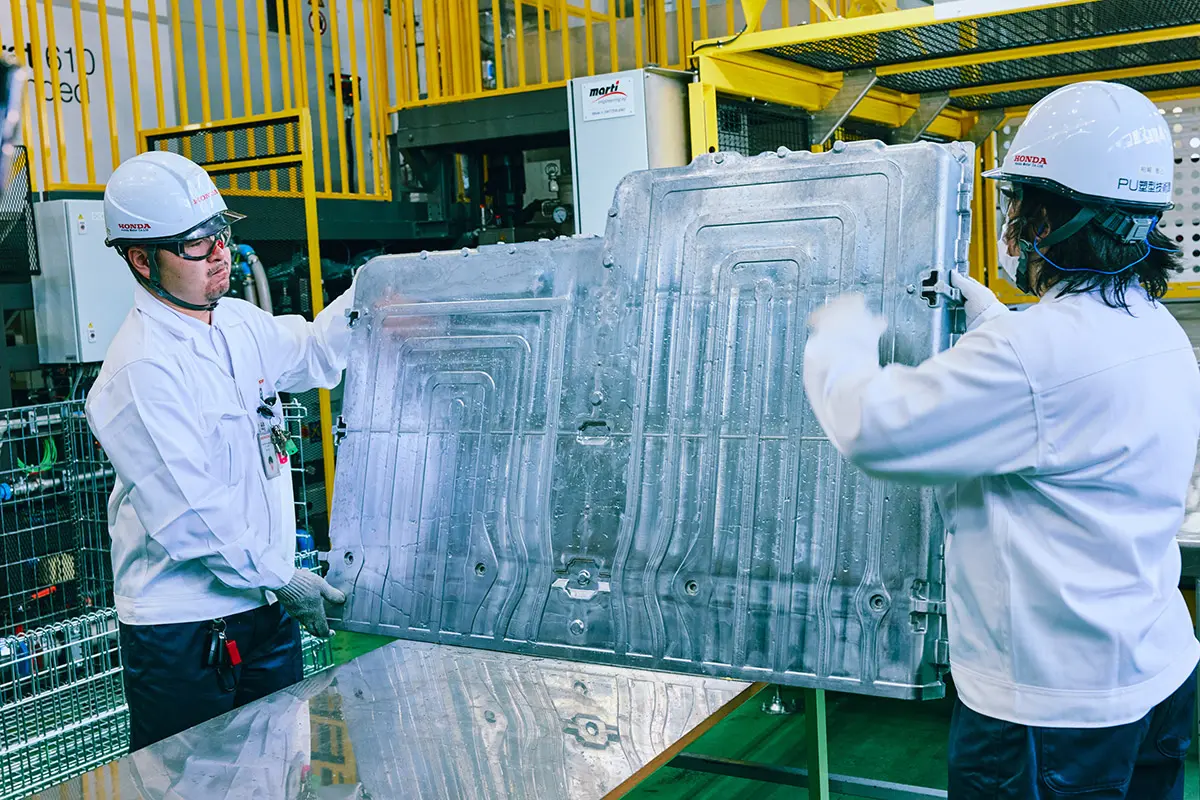
大型鋳造は最近注目されている技術ですが、Honda 0シリーズのテーマのひとつでもある“Wise”、すなわち賢くつくることに挑むという想いから、バッテリーケースを分割鋳造し、接合締結するという作りを採用しています。一般的には部品点数が60を超えるバッテリーケースと付帯部分をわずか5つの部品で高品質に、薄く、軽くつくることを実現しました。メガキャストでは適切なサイズの設備を選ぶことで、製造コストを抑えた賢いものづくりも可能にします。
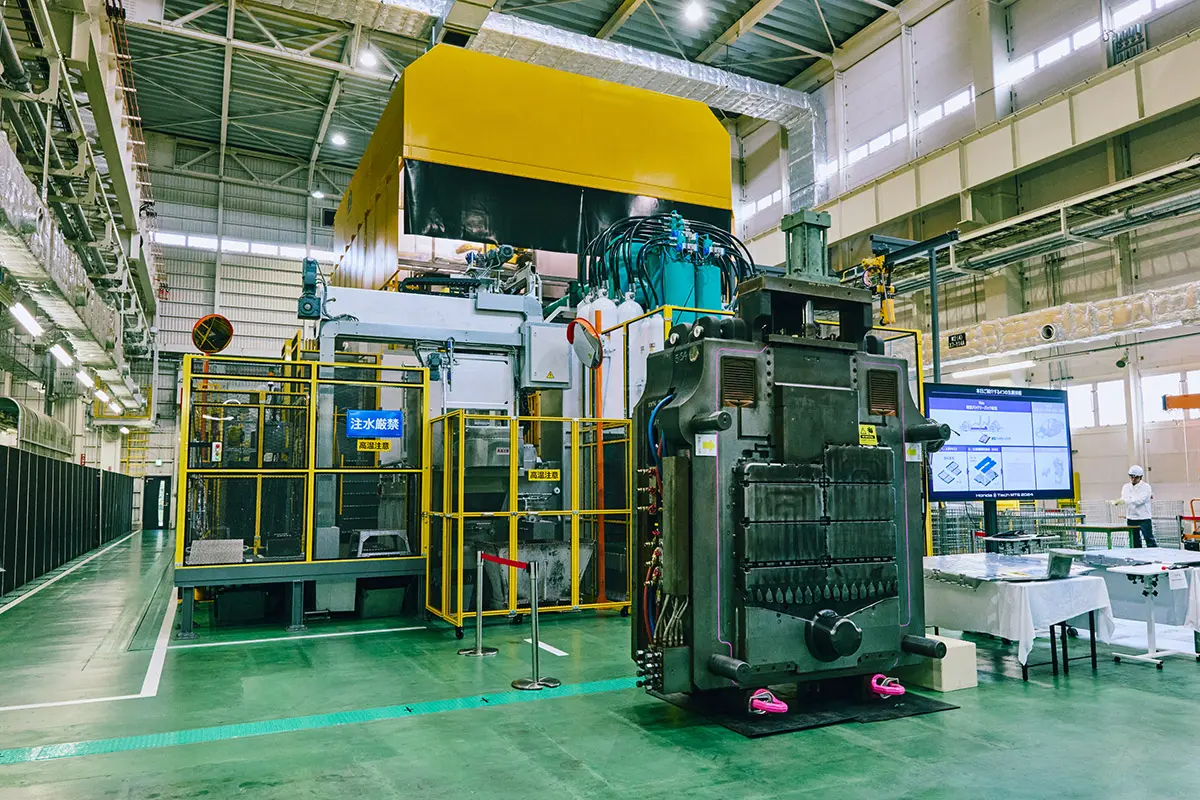
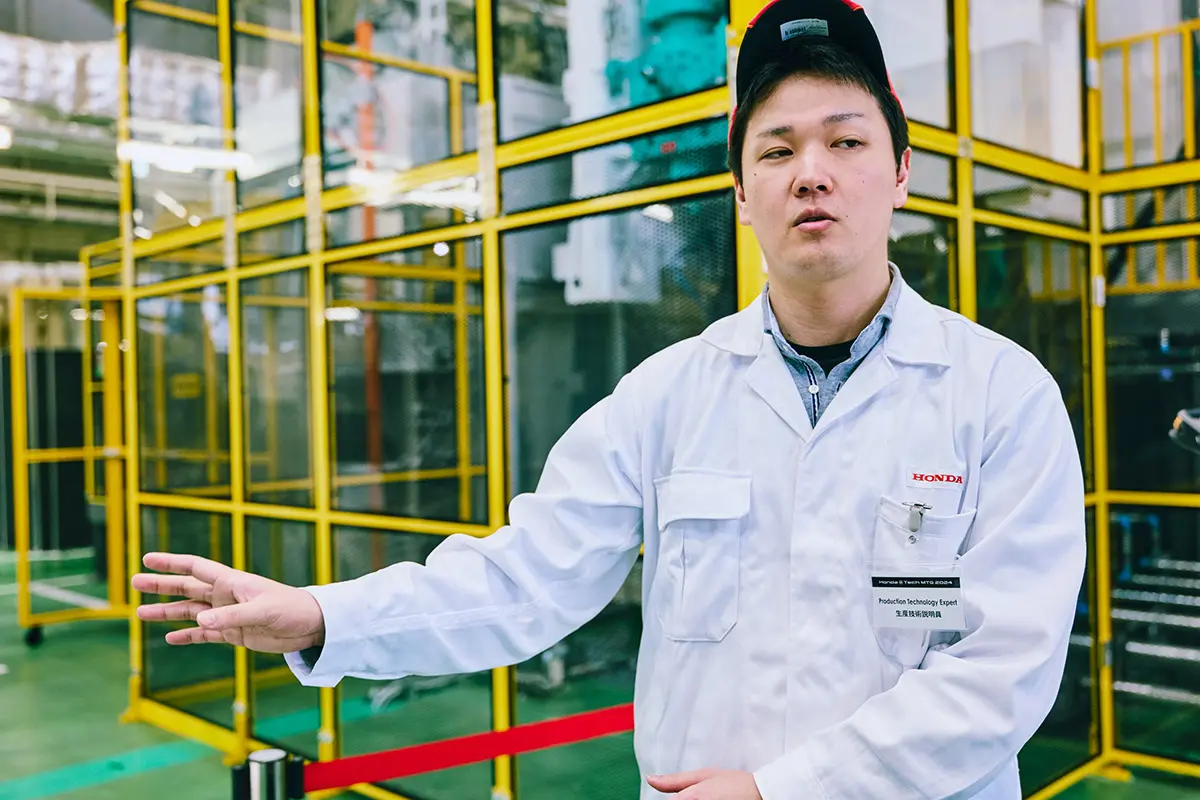
強度と気密性を確保する3D摩擦攪拌接合(FSW)
バッテリーケースの製造において、2つの工程に「3D摩擦攪拌接合(FSW=Friction Stir Welding)」を適用しています。1つ目はメガキャストでつくった部品同士を接合し、ケース本体をつくる工程、2つ目はバッテリーに冷却機能を持たせるために必要となるウォータージャケットカバーをケース本体に接合する工程です。この技術は、突起のある円筒状のツールを回転させ、接合部との摩擦熱だけでアルミを軟化させて接合します。そのため、従来の溶接よりも熱による母材のダメージが少なく、接合部の品質を高く保ちやすいので、接合強度と気密性を確保しつつも、バッテリーケース全体を薄く、軽くつくることができます。
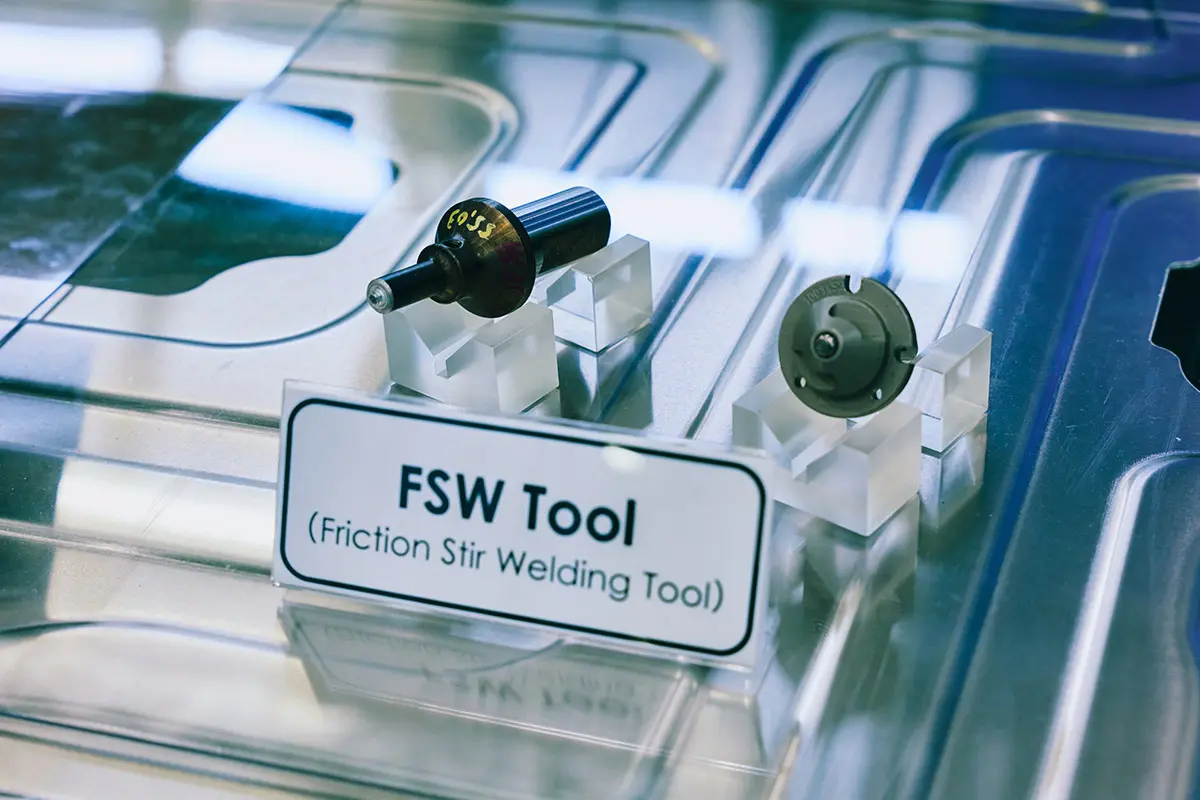
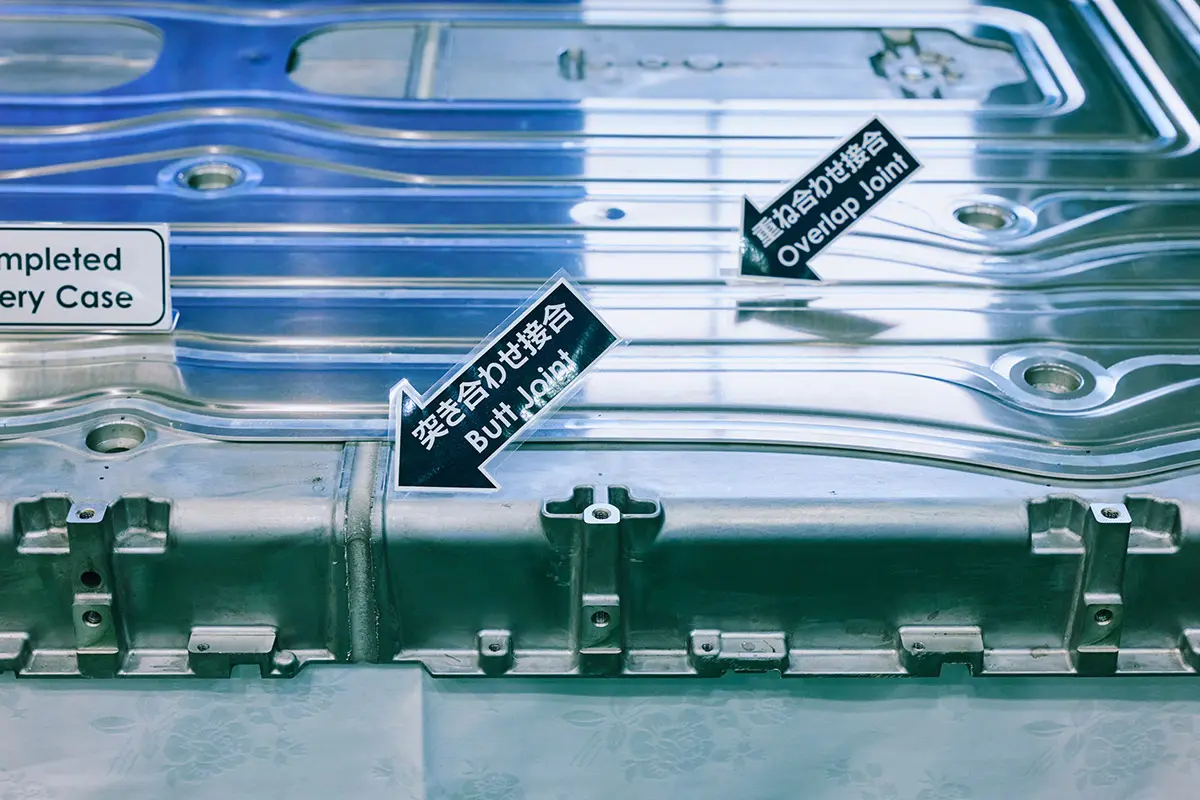
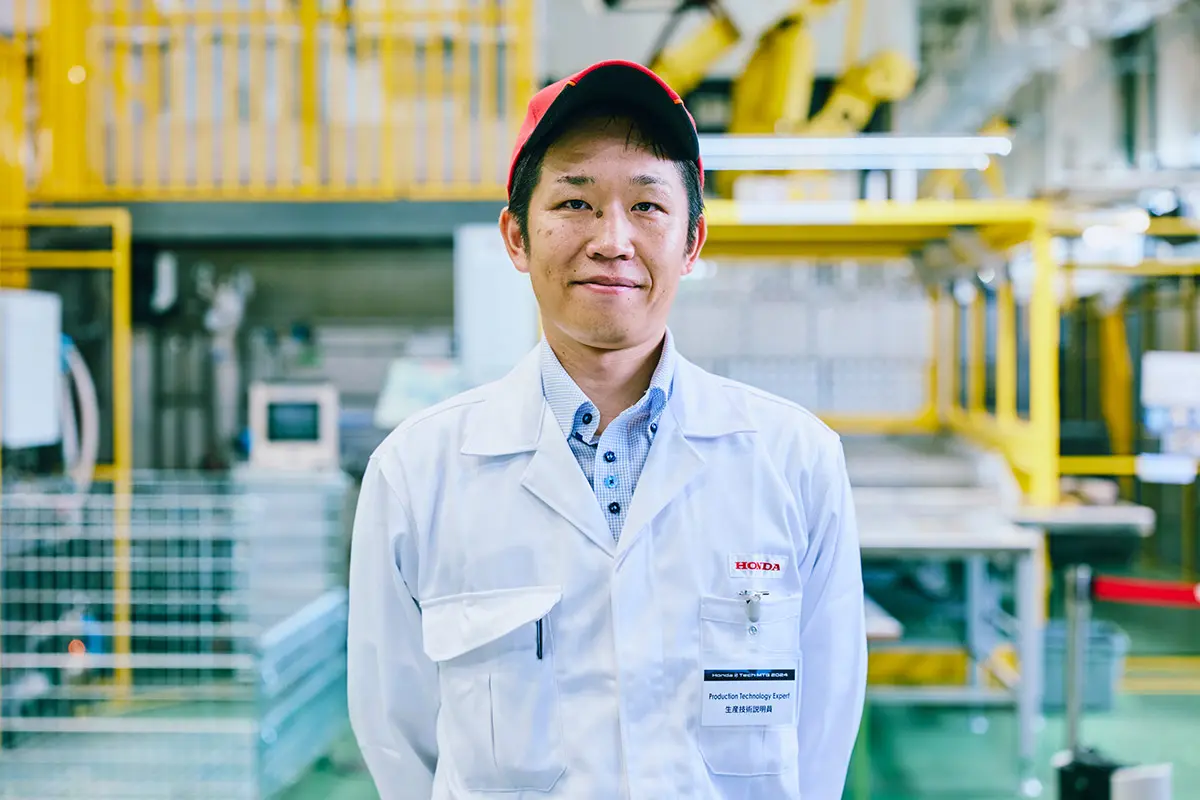
今回のバッテリーケース製造ではショートプロセス化にこだわりました。材料によって異なる強度などの特性に合わせた接合条件の設定や、接合箇所の形状に合わせてツールの動きなどを最適化することで、前加工を必要最小限にしながら、接合部の品質の安定化を実現しました。FSW自体は一般的ですが、その工程だけでなく生産プロセス全体で連携できるHondaの強みがあるからこそ、製品としてトータルバランスがよいものを世に送り出すことができると考えています。
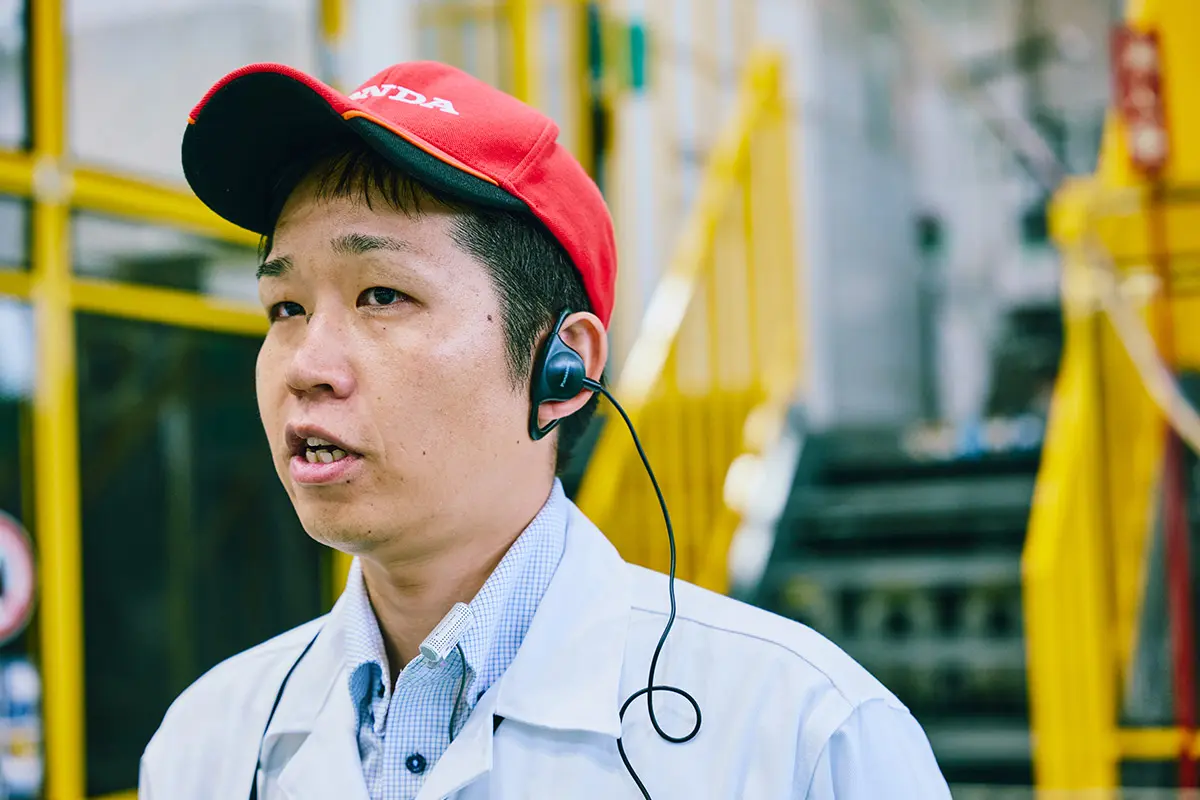
今後の生産方式の変化の起点となるフレックスセル生産方式
工程を分割して一定時間で流し、複数人で組み立てるライン生産方式に対し、1人が固定した場所ですべての組み立てを行うのがセル生産方式。従来は加工ラインなどで使われる方式ですが、無人搬送車(AGV)で部品を供給し、効率的な組み立てを行う「フレックスセル生産方式」をHonda 0シリーズのバッテリー組み立てに導入しました。
同一設備を複数並列に配置することでライン全体が止まることを避けられ、生産量を安定させ、製品が移動する待ち時間解消による生産効率の向上、設備投資の効率化を叶える画期的な生産システムで、今後の生産ラインの変化や進化にも対応できます。
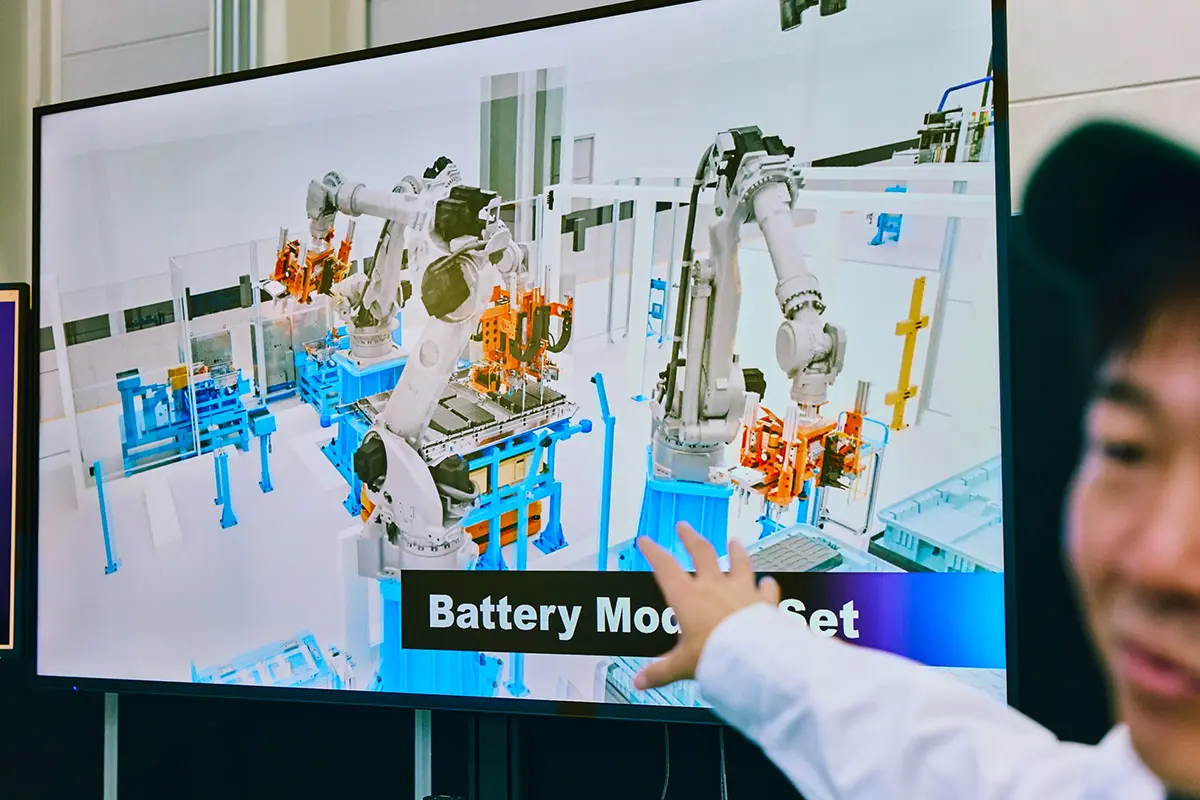
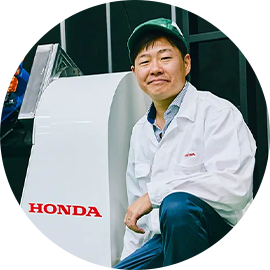
フレックスセル生産方式の構築には各工程プロセスを繋げていく必要があるため、「メンバー同士のコミュニケーション」が一番大変でした。北米メンバーも含めてよい人間関係を構築した上で、それぞれHonda技術者としてプライドを持ち、諦めずに議論しながら、実現に繋げることができました。そうした「人」がHondaの財産なのだと実感します。
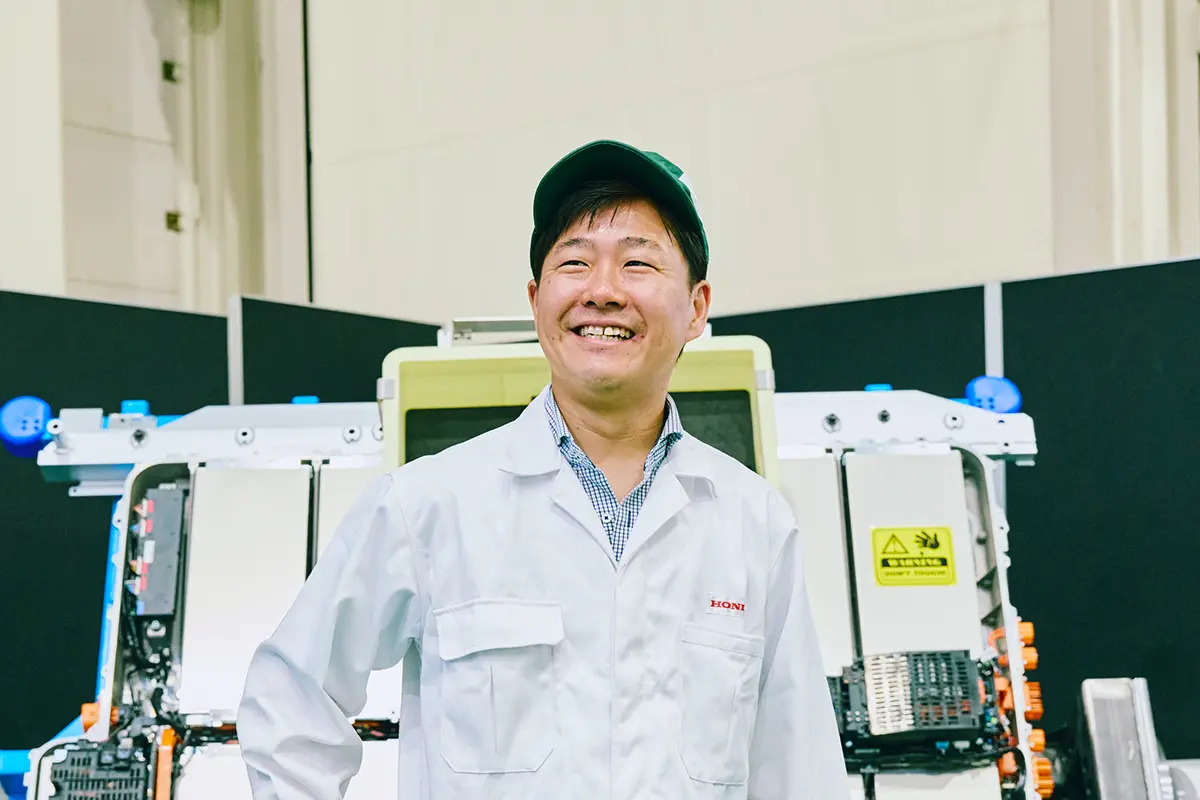
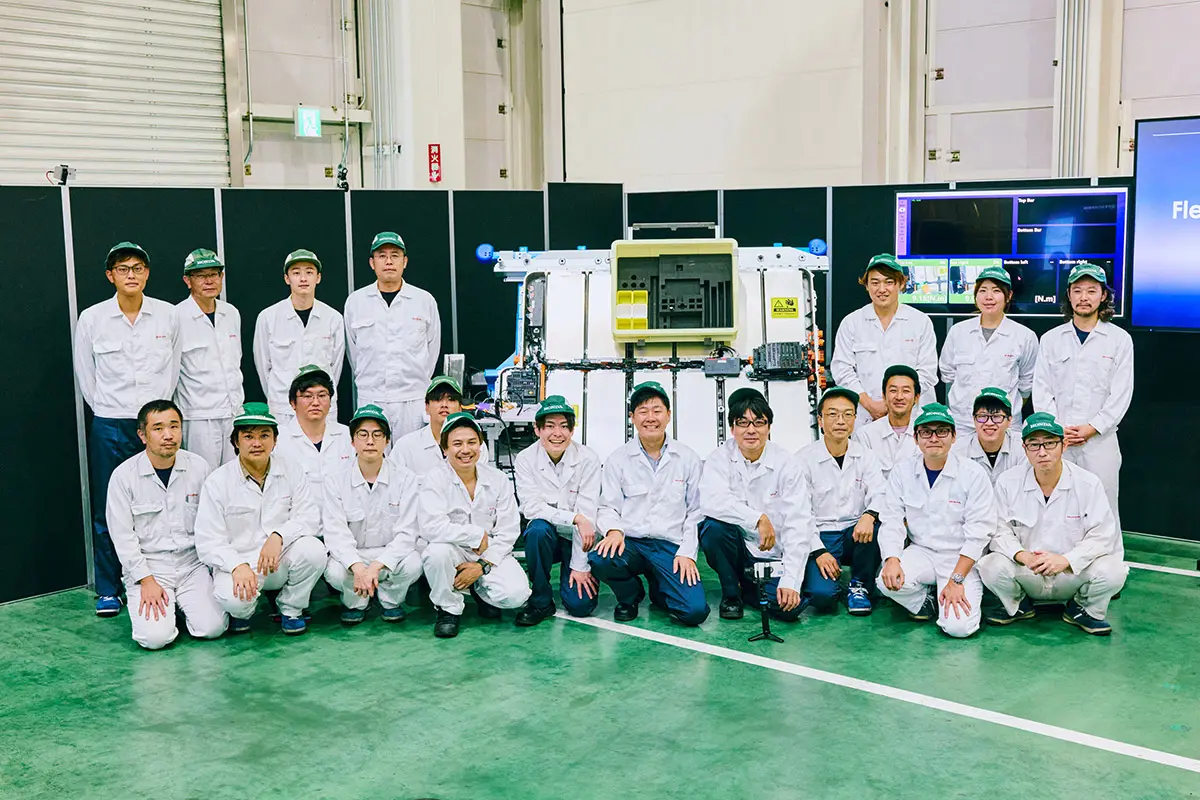
ボディーそのものを軽量化する世界初のCDC溶接
ボディー部材を接合する際、超ハイテン(超高張力鋼板)と呼ばれる強度材料とデザイン外板(薄板軟鋼)を従来のスポット溶接で接合しようとすると、厚み・素材の違いによるスパッタ(※1)の発生と強度不足が同時に起こり、接合が困難でした。
そこでHondaは、溶接に使う電流をインバーター(※2)で適切に制御する、世界初のCDC溶接技術(CDC=Constant DC Chopping)をつくり上げました。ハイブリッドシステムのインバーター設計・信頼性技術や美しい波形の交流電気を出力する発電機、初代NSXの世界初のオールアルミボディーを接合する溶接機など、これまでにHondaが蓄積したインバーター制御のノウハウを応用したものです。従来のスポット溶接では軽く強度の高い材料を使用できず、ボディー部材の重量増につながっていましたが、CDC溶接技術により材料効率向上と軽量化を実現しました。
※1 溶接時に溶融金属が飛散して固まった金属粒
※2 直流電流を交流電流に変換する装置
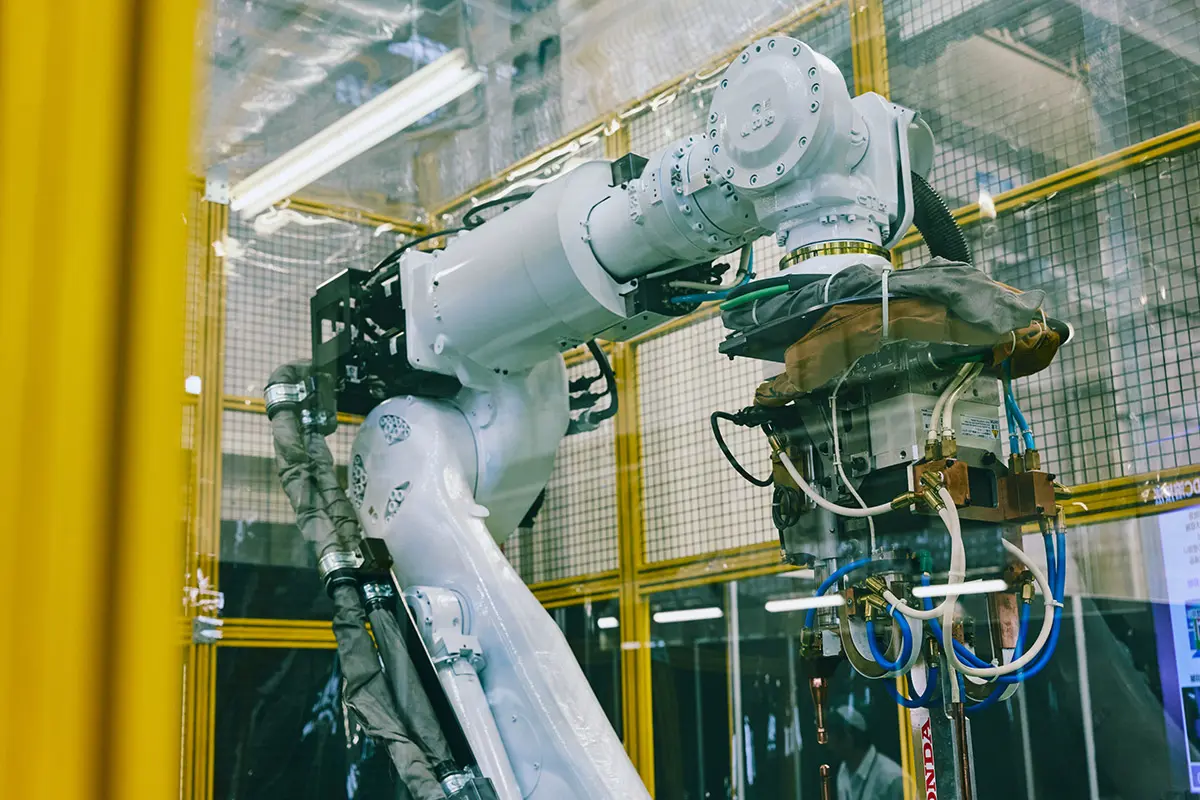
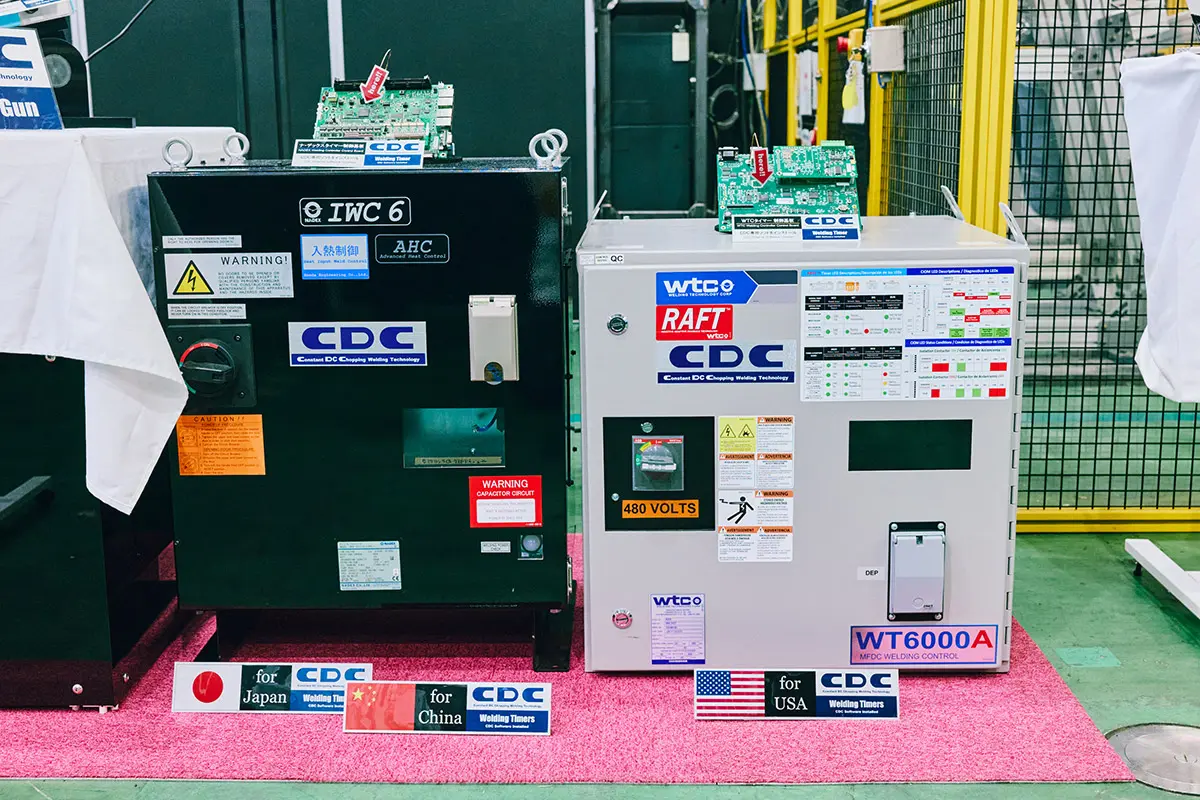
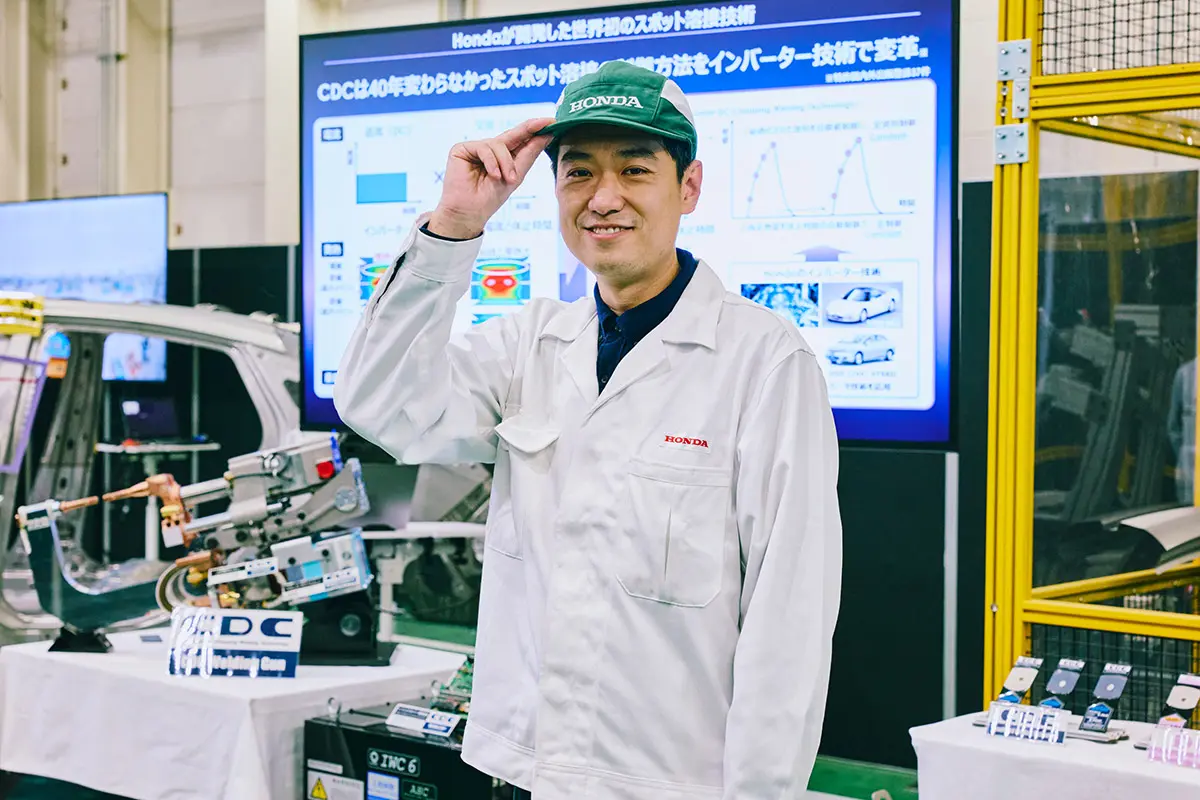
この技術は、約10マイクロ秒というとても短い時間制御のため、はじめは溶接機メーカーからも不可能と言われました。しかし、「ないものはつくる」のがHonda。簡単にあきらめるのではなく、「どうすればできるか」に挑み、実現しました。Honda内部で確立した技術を量産に向けて安定立上げに繋げていきたいと思っています。
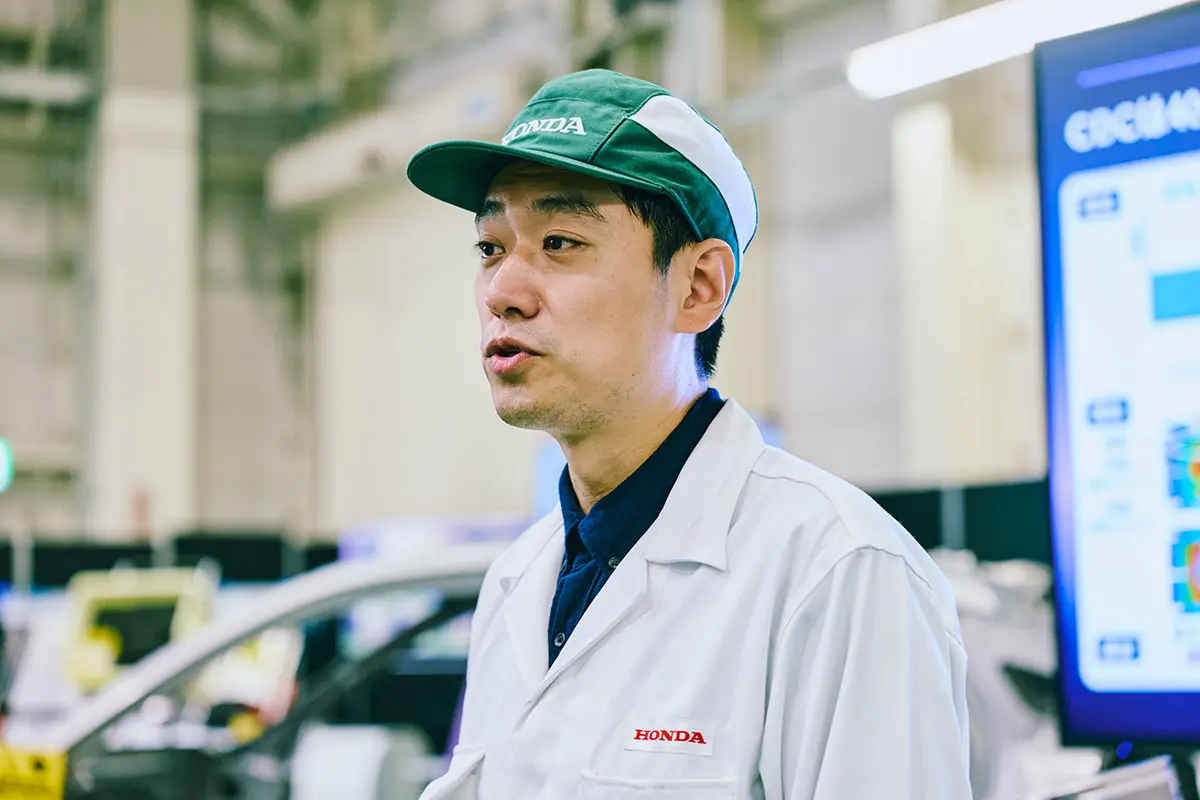
Honda 0 Tech Meeting 2024を経て語る「Hondaのクルマづくりへの想い」
最後に、Honda 0 Tech Meeting 2024の参加者との意見交換や反響を受けて得られた気づきや収穫について伺いました。
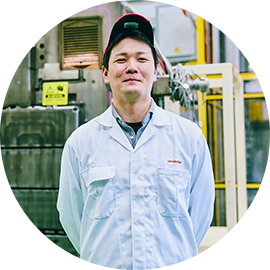
なぜ「ギガ」ではなく「メガ」なのかという質問がありました。大きければ良いということではなく、Hondaとしては、ギガキャストは寸法精度確保の難しさや製造時の消費電力の多さ、設備投資の大きさ、大型部品ゆえに運搬の難しさや修理が困難であるといった課題を感じています。自ら厳しい基準を設け、製造する機械やシステムまでを自前で開発するHondaの精神のもと、今後はメガキャスト鋳造の適用範囲をボディー部品にまで広げ、Hondaのカーボンニュートラルの取り組みに生産部門としてさらに貢献していきたいと思っています。
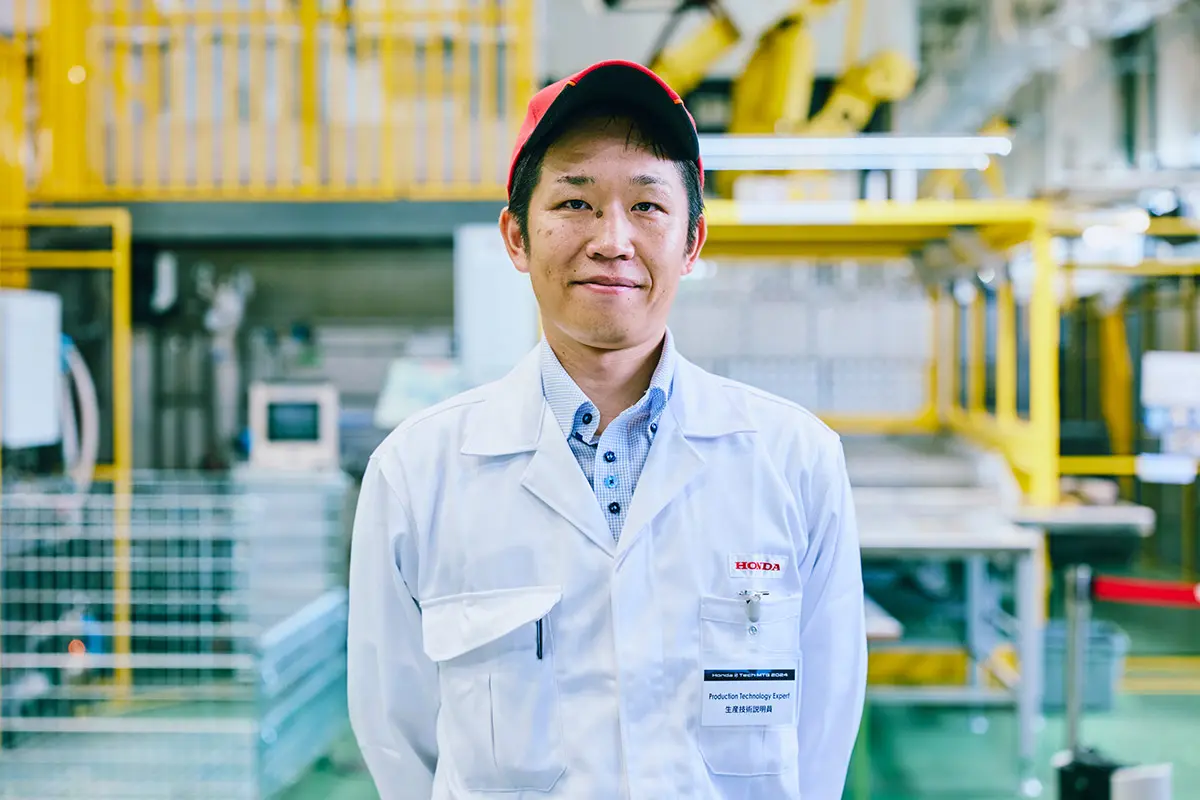
ショートプロセス化をしていくにあたって、技術を手の内化することの重要性について賛同をいただきました。まず、Honda 0シリーズのバッテリーケースを安定的に立ち上げ、生産していくことはもちろんですが、今回得られた知見やノウハウを活かし、ボディー骨格部品などにも適用範囲を拡大することを目指しています。FSWは製品の自由度や生産性を高める重要な手段のひとつであると考えています。
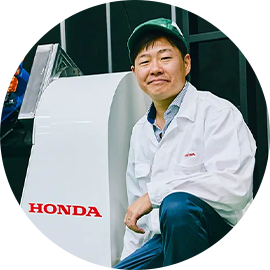
これからEVのバッテリー方式はさまざまに変化することが想定されますが、フレックスセル生産システム導入後、世界中にどうやって広げていくのかなど、前向きな意見をいただきました。フレックスセル生産方式の実現はひとつの実証であり、変化しながら進化し続ける将来のHonda車に生産部門として追従するために重要な出発点だと考えています。
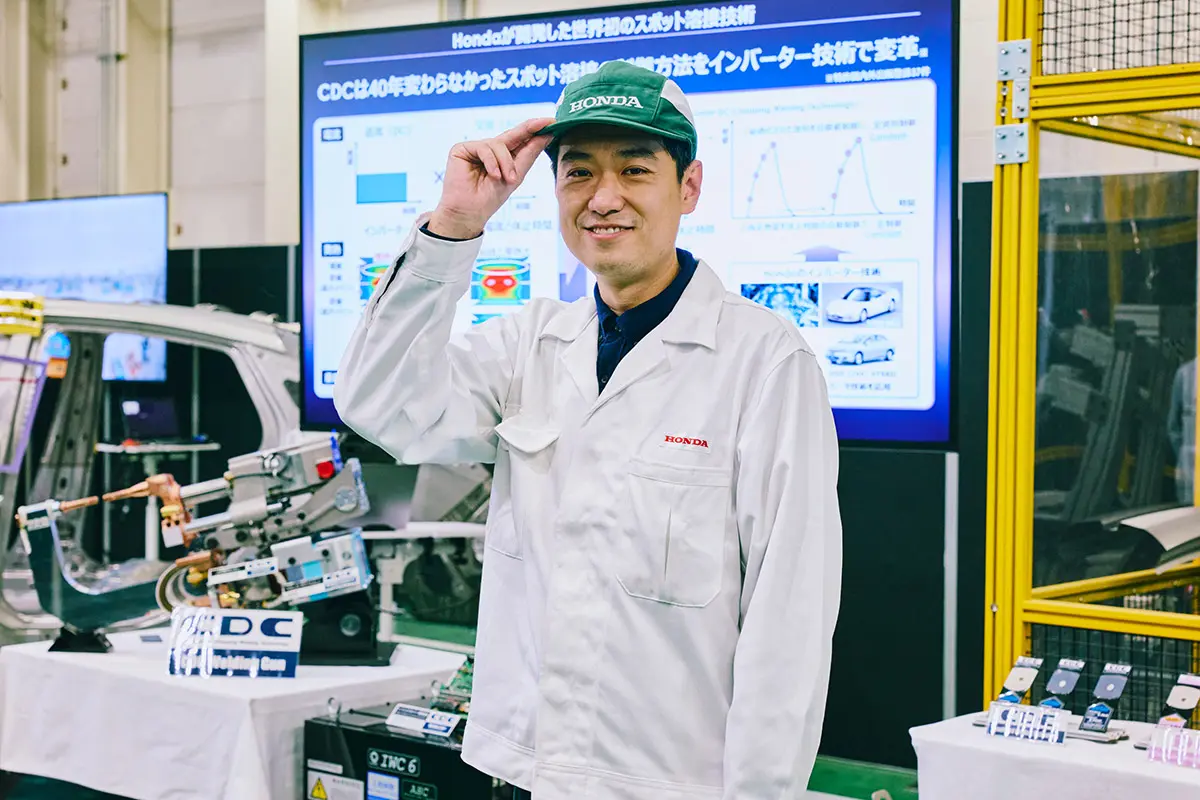
非常にユニークな技術との声を多くいただきました。この技術は、既存のスポット溶接機の溶接ガンとソフトウエアを置換するだけで実現できるため、“Wise”な技術ともいえます。今回のHonda 0シリーズの立ち上げで蓄積したノウハウを活かし、この技術を世界のHondaの製作所に展開し、Honda車をどんどん“Thin”で“Light”にできればと思います。
<関連記事>
この記事をシェアする
この記事は面白かったですか?
- そう思う
- どちらともいえない
- そう思わない
今後の改善の参考にさせていただきます!
従来のものより大きな部品を鋳造するためには、型内にアルミを流し圧力をかけたときに、金型が開かないよう、高い型締め力が必要となります。Honda 0シリーズの生産立ち上げに向け、製造品質の完成度を高めるために今回、適切なサイズの設備である6,000トンクラスの大型鋳造機を国内初導入し、これまでの鋳造技術で培ったノウハウを活かし、工夫を凝らしながら高品質な薄型大物部品の実現を進めています。