Technology
Introduction to the Structure of the HF120, the spirit of engineers who supported the technology and the quality of the HF120, and the award history of the HF120
GE Honda Initiatives
To achieve our mission to deliver the high quality products and services to our customers, we install equipment and build organizations without any compromise.
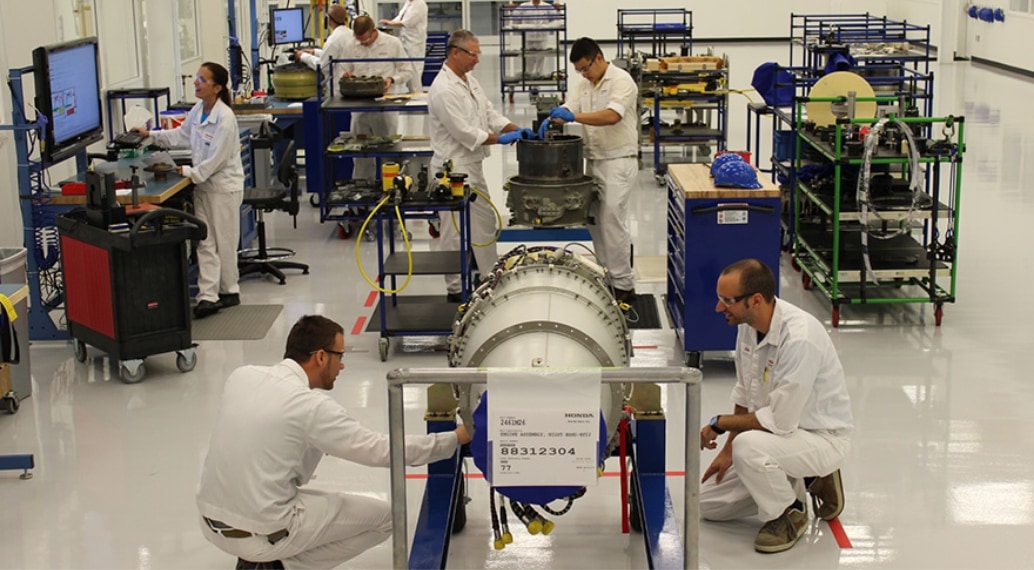
Production plant (Burlington, North Carolina)
Honda Aero, LLC
Production management using IT technology
We register all serial numbers for the major parts in the manufacturing process, and track them to ensure that they are correctly assembled. In addition, we incorporate the traceability management into our daily operation so that we can minimize inconvenience to relevant customers even when a problem occurs.
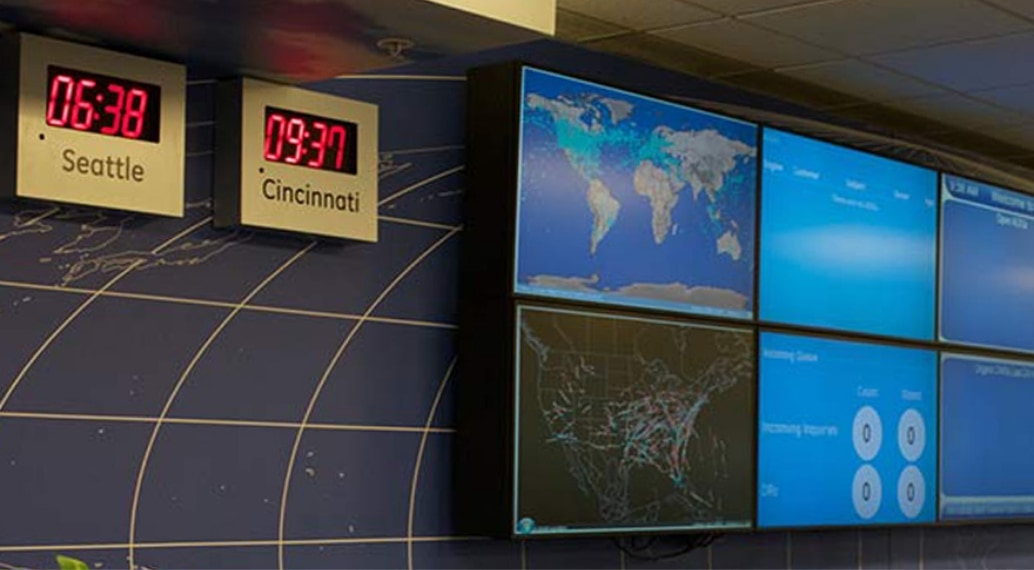
Operations Center (Cincinnati, Ohio)
GE Honda Aero Engines LLC
Exceptional customer support
In order to promptly respond to each customer’s emergency issue and question, we run the Operation Center 24 hours a day, 365 days a year. This around-the-clock service has established a framework that can deal with inquiries quickly and appropriately.
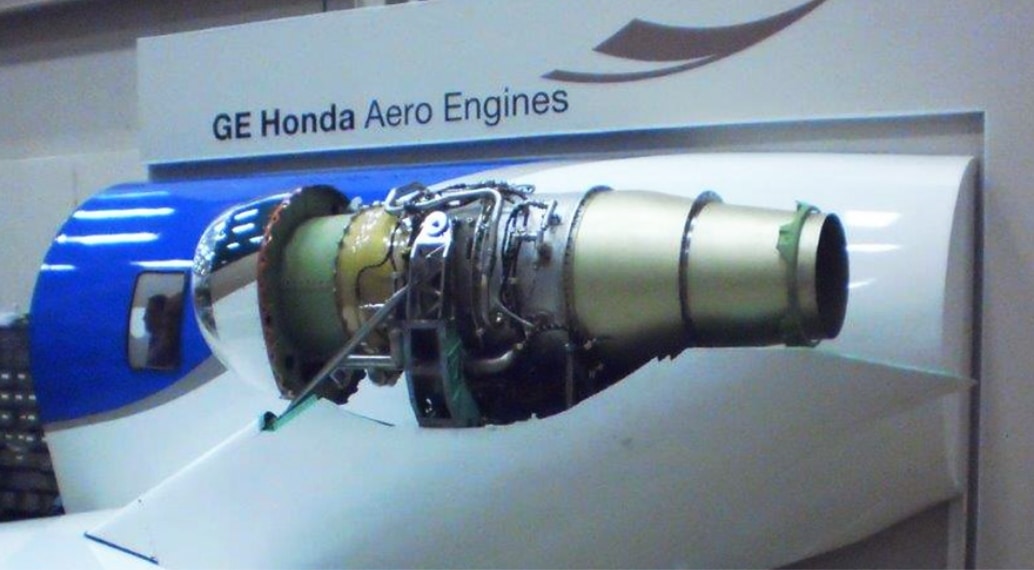
Customer Training Education Center (Cincinnati, Ohio)
GE Honda Aero Engines LLC
Reliable maintenance technology
Maintenance staff members working for service providers are periodically invited to our technical training center to receive trainings so that their expertise in engine repair can be further improved and updated. This training constantly enhances their maintenance technology, keeping our service quality at the highest level of its kind.
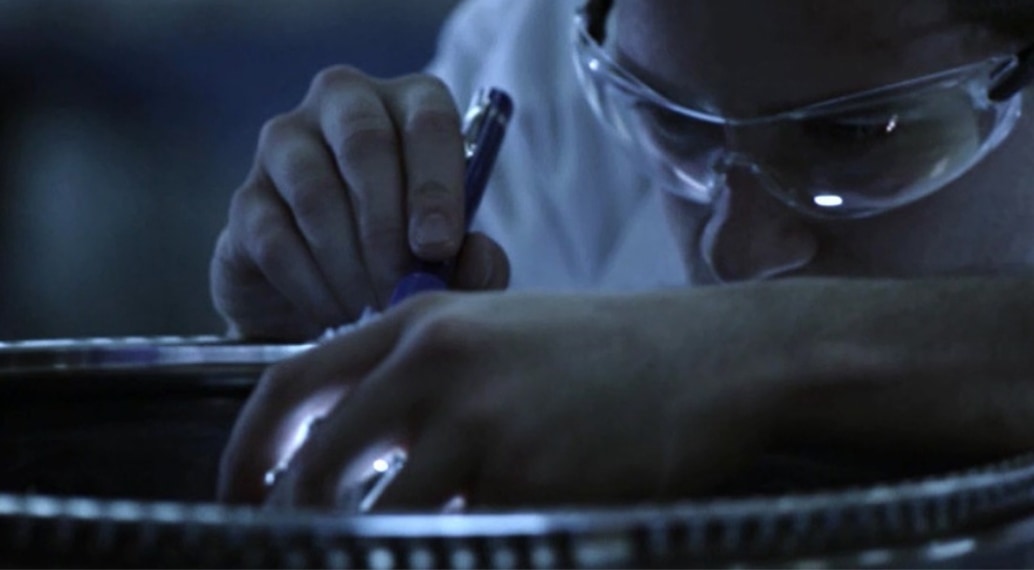
Maintenance Repair and Overhaul Center (Burlington, North Carolina)
Honda Aero, LLC
In the event that a problem happens to a customer‘s engine, and it is difficult for his or her authorized service provider to diagnose and repair the problem, or if the engine reaches the overhaul limit of 5000 cumulative flight hours, the engine can receive a professional maintenance service from highly skilled engine mechanics at the Maintenance Repair and Overhaul Center of Honda Aero, Inc. that has been certified by the governmental authorities of each country.