An Automated Line for Painting and Coating / 1988
Visionary Efforts by the Painting/Coating Departments of Honda's Factories
The process of finishing an auto body where the white bodies assembled in the welding line are coated and painted, is critical to the exterior quality of the completed car. It is a process that puts the final touches on the vehicle to ensure its value to the consumer.
Honda's coating/painting technology was cultivated from know-how acquired through the production of motorcycles, and then applied to automotive manufacturing. Yet, Honda actually began its effort to develop a dedicated coating/painting technology for automobiles in the 1960s, when the company was just getting started in the production of cars.
The Honda Sports S500, which went into production in 1963 at Hamamatsu Plant (currently Hamamatsu Factory), adopted the industry's first anionic electrodeposition undercoating material, which was actually a water-based material charged with a negative electric current.
Then, in 1967, Honda installed a dual-coating line at Suzuka Factory (where two coats, electrodeposition coat and overcoat, were applied), for the production of the TN360, its first mini truck. The next year Honda adopted innovative pearlescent and gold metallic paints for the Honda 1300, which of course was the company's first compact car. These were the earliest in a series of efforts to develop innovative coating technologies.
Honda introduced its NHP movement throughout the corporation in 1972. As part of that movement, Sayama Factory (currently Saitama Factory's Sayama Plant) implemented structural reforms based on the 4RPK (Four-Wheel Vehicle Production Kanto) project. Commensurate with the Civic's shift to production in 1973, the factory made the transition from being a production facility for mini automobiles to one for compact passenger cars. Along with that shift, Sayama Factory's Painting/Coating Department adopted the industry's first dual-coating, dual-bake (two coatings plus two cycles of baking/drying) process, which was based on electrostatic powder coating. In fact, this application technology for powder coating in automotive production earned the Technology Award from the Japan Coating Technology Association in 1976.
Suzuka Factory, on the other hand, introduced a water-based intermediate coating in 1974, moving toward a triple-coating process. As described above, though, Honda's technology for painting and coating evolved through a constant effort by engineers in the respective factories working on behalf of painting and coating operations. The specialists employed the techniques of highly qualified suppliers in order to refine their achievements. The unique technology created from such efforts was a combination of three different undertakings implemented at the Saitama, Sayama, and Suzuka factories, and these facilities competed among one another to hone their own expressions of that technology.
Automating the Line with Welding Robots
Japan emerged as a key worldwide auto exporter in 1980. As export volumes increased, Japanese automobile manufacturers were asked to improve the paint quality of their cars in order to provide sufficient corrosion resistance in certain regions of the U.S. and Europe, where vehicles were subject to damage from the application of salt to icy winter roadways. The manufacturers were also asked to improve the exterior quality of their cars in the hope of answering an emerging consumer preference for expensive-looking cars.
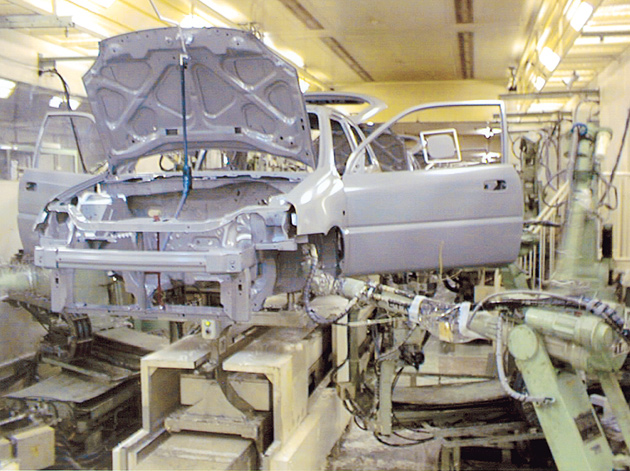
The sealing process used a robot with a larger operating range that was ideal for wide application areas.
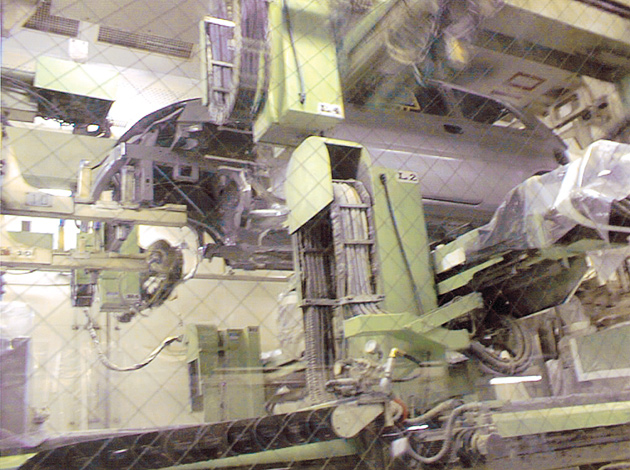
The undercoating robot was capable of applying a coating over the bottom surface of the floor without using masking tape. The use of a dual-head spraygun allowed the robot to handle different coating specifications for multiple models, helping integrate the process.
Most automobiles then employed a triple-coat, triple-bake coating system - the so-called standard process - except for certain luxury models. In this system the body was first cleaned in a pretreatment process before passing through the electro-deposition coating process to receive the rust-prevention treatment. The rust-proofed body was then forwarded to the surface-preparation processes: first to the sealing process, where sealant was applied along the seams between steel sheets for waterproofing and dust-proofing; and then to the undercoating application process, where a protective coating was applied to the underside of the floorpan in order to inhibit rust and excessive vibration. An intermediate coating was then applied over the undercoat to enhance its performance. The final application of an overcoat completed the process.
Honda's coating lines had certain drawbacks, however. Although the methods used by Sayama Plant and Suzuka Factory differed somewhat, the coating lines at both facilities were basically mixed lines comprising automated machines and human operators. As such, the line facilities were substantially large and lengthy. There were also many processes that depended upon operator skills. Each time the number of operators increased, so did the amount of dust that could enter the system and contaminate the coating material. Likewise, production costs were rising as a result. Therefore, in order to achieve a high degree of exterior quality, Honda had to address some challenging questions.
Another concern was the nature of coating/painting lines, in which large quantities of solvents were employed. From the standpoint of work safety, it was preferable that manual operations be minimized or eliminated from the process.
The sealing and undercoat application processes in particular required numerous operators, who had to work in unnatural positions such as crouching forward and leaning back. Also, the operators had to clean their workplace frequently because the area was easily soiled by spilled materials. This was a burden that only added to the fatigue the operators experienced. Moreover, these processes were prone to inconsistencies of quality. In light of such detrimental conditions, sealing and undercoating applications soon topped the list of processes requiring automation.
Honda Engineering (EG) began its effort to automate the coating/painting line in mid-1984. As an initial step, EG directed its attention to surface-preparation processes such as sealant and undercoating applications.
In October of the following year, EG's special development team working on coating projects installed a robot for sealant application on the second line at Suzuka Factory. This prototype, a modified version of the welding robot, was part of a control experiment designed to examine the feasibility of robots for use in mass production. However, the process of sealant application was more complicated than the team had expected, so the experiment served only to highlight numerous areas needing further improvement.
Before work could begin in the sealing operation, the team had to improve on the accuracy of positioning for the body as it was sent down the line. Even a slight offset in its position, which the operators would probably have ignored, could have a significant affect on the robot's performance in applying sealant. Another drawback of the modified welding robot was that it was unable to move smoothly in accordance with the flow of the line. Not only did this prevent the robot from applying a smooth coating of sealant over the welded surface of the car body, it led to inconsistencies in coating thickness. Accordingly, the operators had to correct problems manually in order to stabilize the fluctuating quality of robot operation.
EG's project team also learned that in the coating operation the robot had to process much more information than they had expected. Therefore, in order to process large amounts of data, there was a need to increase the robot's intelligence.
EG introduced a robot for undercoating application to Sayama Plant's second line in 1986. However, the robot was something less than perfect. The body forwarded to the undercoat application process had approximately ten holes in the back of the floor that were used as positioning references during welding or to assemble portions of the drivetrain. During undercoating these holes had to be covered with masking tape, which then had to be removed once the application was completed. Although the undercoating application was being performed by the robot, the attachment and removal of masking tape before and after the application still needed to be done by hand. The matter of automating this step posed an important question for Honda's engineers.
During 1986 and into 1987, the development team created a number of new technologies, including a high-density, high-speed, high-accuracy robot offering a larger range of operation, making it ideal for general areas requiring sealant application. It also provided a sealant supply system and a spraygun capable of controlling the spreading of sealant as it was ejected. The team even worked to enhance the accuracy with which the car body was positioned on the line.
The team also developed a series of new technologies in the area of undercoating application, including a small, orthogonal robot suitable for applying undercoating over the floor's bottom surface; a constant-quantity undercoating supply system for improved accuracy of the application pattern; and a dual-head spraygun capable of coating two sections differently.
A Unique Coating Robot - A Departure from the Norm
Early in 1987, EG was actively engaged in a review of specifications for the new, high-efficiency coating-line system planned for introduction on Suzuka Factory's third line. The system was to be a high-density, integrated body-painting system incorporating all processes up to overcoat application. The concept was to transfer bodies at high speed and use proportionately fast-coating robots to complete the process, resulting in a shorter cycle time.
However, to reduce the cycle time by increasing the target body's feed speed to twice that of a conventional system, EG had to develop new mechanisms by creating original yet fundamental technologies. The development team was thus divided into several small groups in order to work on the core technologies required for the coating process.
In the sealing process, the team began by listing the various pieces of know-how accumulated at Suzuka Factory and Sayama Plant for distribution among the members. Then, based on the technical resources they had identified, the team continued to work on target technologies. These included a high-speed sealant application robot with greater operating range and higher body-positioning accuracy; a spraygun capable of controlling application conditions for the sealant; and a robot for the attachment of grommets after the sealant was applied.
Process integration was further enhanced in the undercoating process with the development of various orthogonal robots having built-in power servomotors. Some of these were designed for floor installation and others were used in hanging positions, in an arrangement that positioned these robots three-dimensionally around the line. In addition, the team developed a new, dual-head spraygun that could memorize the spray pattern for each target model and apply the undercoating only in specified areas by automatically avoiding holes. This led to the development of a coating technology that required no masking. Capable of memorizing spray patterns for multiple models, the new masking-free spraygun produced significant results, one of which was the elimination of steps needed to attach and remove masking tape before and after undercoating. As a result, the application could be done in one step.
The overcoat application process, in which the body's outer panels are painted, requires a high degree of coating technology. At Suzuka, the application of overcoat had been done using a simple, gate-shape automatic coating machine that had been known as a "reciprocator" since the production launch of the H1300 in 1969. The sections handled by the reciprocator covered nearly 80 percent of the overall body. However, coating the front and rear sections of automobiles, as well as the so-called inner-panel coating process - including the inside surfaces of the hood, trunk, and doors - required the skills of experienced operators. Because of this, the process of overcoat application was constantly reliant upon both machines and operators.
The development of a multiple-axis robot was therefore rapidly progressing in order to provide an alternative to the reciprocator. One key element was the action of the sprayguns used to paint various body sections. Normally, the operation of such sprayguns required the deft handwork of skilled operators. However, the reciprocator employed a hydraulic drive system to control the movement of sprayguns, and the bulky wiring cables and hydraulic pipes were limiting the movement of the gun.
The newly developed outer panel's top multirobot was designed to address this problem. That robot, which employed a five-axis configuration using a flameproof power servomotor, could not only move the gun head up and down, as well as in the body's direction of movement, but could also rotate the gun arm. This enabled the robot to perform accurate spray actions along the contours of the body while it was moving on the conveyor.
The team also focused on a part called the bell cup. This component, which was used to spray the coating material, was installed in a bell spraygun attached to the robot. Rotating at a speed of over 30,000 rpm, the bell cup was also subject to current input exceeding 60,000 volts, which was required in the electrostatic coating process. The coating material sprayed from the bell cup along radial lines was charged with electricity and thus attracted by the body surface to form a film coating.
Honda used to purchase its bell sprayguns from an overseas manufacturer. However, seizing upon the opportunity for another joint-development project it had started with a foreign manufacturer, EG began developing its own bell spraygun. With the expertise acquired through that research, EG was able to develop an original bell spraygun without using any of the existing patented technologies. EG's new bell sprayguns were introduced to the third line at the Honda of America Manufacturing (HAM) Plant in December 1989.
Teaching Robots the Skills of Operators
Concurrent with the development of coating robots, a joint development team comprising members of EG development and Suzuka's skilled coating-line operators began a new task. Their objective was to transplant operator techniques to the robots in time for the start of operations on the third line. On the actual line, tracking of the coating process was begun along with the preparation of the overall system.
The angle at which material is sprayed from the gun head is critical to the coating process, as is the gun head speed of movement. Moreover, a distance must be constantly maintained between the gun head and body surface. Through years of experience, the operators learn to control the gun head using their bodies and senses. For example, in the actual coating process they stop the gun just before the coating material being sprayed onto the surface would start to run. The coating film they create is even in all areas, with precision ensured down to a level of microns.
Before this kind of expertise could be passed on to the robot, each separate technique would have to be analyzed in detail. Of course, the skilled operators were also human beings; they simply could not give their very best performance time after time. Therefore, the team recorded its coating operation on video in order to pinpoint the optimal actions. Next, the most effective gun actions were chosen according to three criteria: the spray angle of coating material at the gun head, distance from the body, and the gun's speed of movement. Teaching sheets were then created in order to transplant the coating techniques to the robot.
"Operators acquire their skills through years of experience," said Hiroshi Arai, who was involved in the development as engineer in charge of coatings at EG's Third Engineering Block. "These techniques are therefore very logical, and they truly reflect human wisdom. In today's computer age, the promotion of automation depends on how to incorporate these techniques and make use of that human wisdom."
The task of teaching the robot began in November of that year. A cone-shaped jig was attached to the head of the robot's gun as a means of simulating the spray angle of the coating material. Using a hand-held console, the operators input their skills to the computer. In the beginning, it was quite a struggle. Although the robots were taught the actions exactly as performed by the operators, it did not mean the machines could immediately begin by producing the greatest degree of coating quality.
Since the body surfaces had many curves, the team often found it necessary to fine-tune the data it had entered in order to align the movement of the robot with the actual contours of the body. Another problem was that the teaching sheet specified only the total time of a coating operation. The specific spray pattern used to complete the operation within the specified time depended on the expertise of individual operators. To enable the robot to operate at the same level of effectiveness, trials using a dummy vehicle were repeated in order to determine the optimal spray pattern.
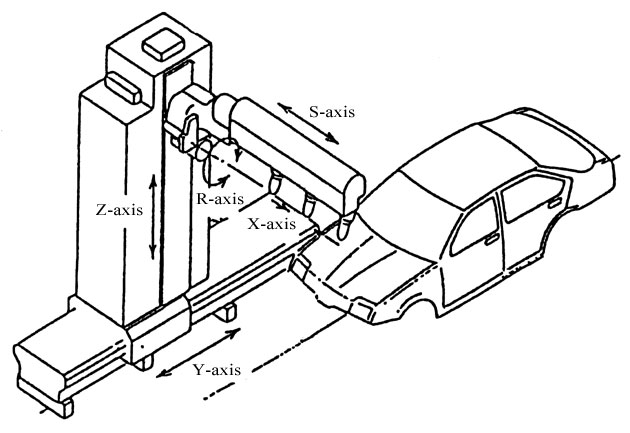
The outer-panel-top multi-coat robots provided a significant increase in the following capabilities of the spray gun.
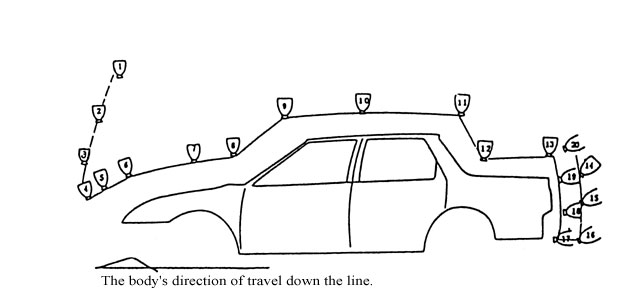
The trajectory of spray from the spray gun indicates that paint is always applied to the body surface at a right angle.
A relatively higher degree of difficulty was encountered in teaching the robot to emulate coating actions along the body's inner panels and there was more limited workspace available. For example, to paint a corner area of the door, the operators would take several steps to complete the coating of the edge at the corner of the door, because doing so allowed them to maintain constant gun speed and ensure even coating. The team attempted teaching the robot to perform a one-shot coating along the edge of the door corner, but the resulting coating film was still uneven. This revealed that the method used by the operators was more practical.
The development team analyzed each individual operator action for assimilation by the robots. Moreover, they repeated that process for each Honda model so that the robots could handle the line being produced by the factory.
Exciting Results from the Coating-Line System
Suzuka Factory introduced its high-efficiency coating line system to mass production in May 1988, dramatically reducing the number of steps needed to complete a car body. In particular, the coating process for the outer panels, which formerly employed a combination of skilled operators and machines, underwent a significant streamlining.
Installed on the line at the intermediate coating and overcoat application stages were several outer-panel-top multicoat robots, which were used to apply coatings over horizontal surfaces, along with outer-panel multicoat robots for vertical surfaces. Of the two, the former solved longstanding problems in the conventional reciprocator by adopting a configuration featuring several sprayguns. This permitted the robot to coat sections at the front and rear of the body that earlier machines had failed to reach. Moreover, the added function of moving the gun arm up and down according to body orientation made it possible for the coating material to be sprayed onto the body surface at a constant right angle. To enhance coating efficiency on the side surfaces of the body, gun arms were installed on the right and left sides of the line. Thus, the new system allowed the distances between these guns to be changed according to the target model, achieving an optimal coating effect. With that, the outer-panel coating line became fully automated, removing the need for operators to work manually.
The multirobots then employed in the inner-panel coating process were equipped with slim arms offering smooth movement and the ability to perform precise, high-speed coating in tight spaces around the body. One of the more significant factors in the achievement of an effective new coating system was the development and installation of dedicated opener/closer robots designed to open and close the hood, trunk, and doors during the coating process.
"In the process of coating the inner panel we had always used door jigs to keep the door in a closed or opened position while the coating was being applied," said Arai. "The robot technology we introduced to the process was developed by combining the wisdom of people experienced on the line, including the use of coating jigs. I believe the total effect of all these efforts was a greater degree of support for Honda's production technology."
The new, high-efficiency coating line employed a number of cutting-edge technologies. By developing its own coating facilities and machines, Honda achieved a significant savings in labor across the entire line. The new system consolidated operations that used to require two lines, yet it still met the production requirement of 1,100 units per day. Furthermore, the overall length of the coating line was reduced by approximately 36 percent. And, because of the reduced line length the time needed to move a workpiece through the coating process was reduced to around 33 percent of what it had been, meaning less liquid inventory. These achievements led to a dramatic reduction in the amount of energy needed to operate the line.
The high-density, integrated body-painting system introduced to Suzuka Factory's third line received the Ohkouchi Memorial Award for Production in 1991.
The Challenge to Develop a Water-Based Coating Technology
Early in 1989, following the successful launch of the high-density, integrated painting system at Suzuka, EG began developing a new paint system for implementation at HAM's East Liberty Plant. The U.S. Congress was then preparing for a 1990 vote on a proposal to drastically amend the Clean Air Act, first adopted in 1970. The proposed amendment promised to impose tighter restrictions on the use of conventional solvents containing volatile organic compounds (VOCs). Therefore, to ensure compliance with the new law, the development team designed a water-based coating system incorporating Honda's original facility and a water-based method already available on the market.
Due to the characteristics of the coating material, however, the use of a water-based coat in the outer panel's coating process resulted in the deposition of metal ions. In response, the EG staff developed a new supply system for the coating material. Another problem was the conductivity of the water-based coating material, which indirectly resulted in an electrostatic coating process having decreased coating efficiency. EG continued its effort to improve the system in order to establish a more effective proprietary water-based coating technology.
EG also developed and installed original wall-mount type robots for the inner-panel coating process. The robot, actually a modified version of the floor-installation type that could be mounted on the wall, had a slim arm that moved very smoothly. It contributed to improved air circulation in the coating booth, where the air would often become stagnant. Moreover, it enhanced the attraction of the coating mist to the body. Coating efficiency was further improved with the installation of a shift base enabling the robot to move in accordance with the movement of the body. The new system even prevented the coating material from splashing back onto the robot and minimized quality problems relating to the coating itself. The result was a much greater degree of productivity at this stage of production.
Developing Technology for a Better Global Environment
EG then developed a new outer-panel coating system based on the water-based coating material in 1992, introducing a water-based electrostatic coating machine with high coating efficiency - known as the EVB, or EG voltage block - to the coating line at Honda of the UK Manufacturing (HUM). This new system not only achieved greater efficiency of coating than the water-based system earlier introduced at HAM, but it reversed the common notion about water-based coating materials by attaining a level of coating efficiency equal to that of organic coating materials. The EVB was an electrostatic coating system in which a tank was filled with water-based coating material prior to each application and the material in the tank was electrically charged. This dramatically enhanced the efficiency of the material as it was sprayed from the EG bell spraygun.
In 1998, EG created the EVB metallic bell spraygun line, which was capable of coating two or more vehicles using an amount of coating material that formerly would have been considered enough to cover just one car. The new system led to a significant integration of the coating process, and was eventually introduced in the factory at Honda of Canada Manufacturing (HCM).
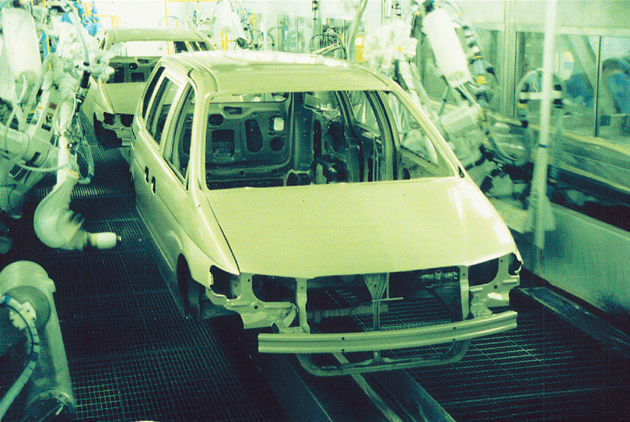
The coating line for the new Odyssey minivan went into operation at HCM in September 1998. Here, a minivan is being painted on the EVB metallic bell spraygun line, which achieved significant improvements in coating efficiency. The new coating line also produced an exceptionally clean work environment.
The coating process had traditionally been seen as one in which the body was painted in a foggy workstation. However, the new line created a cleaner work environment without causing the air to become stagnant. During the process of restructuring the coating line, the wisdom and ideas of many people were combined in order to achieve higher quality in the painting of car bodies.
Currently, water-based materials have become mainstream among the world's automakers. Amid growing concerns over the global environment, manufacturers are endeavoring to minimize the use of VOCs. In response, EG is working to establish new core technologies in the area of coating. With the 21st century fast approaching, preservation of the global environment is bound to grow in importance. Thus the engineers at EG are taking on new challenges in order to develop technologies which will enable mankind to prosper in harmony with the planet.