Establishment of Honda Engineering / 1974
Becoming a World-class Manufacturer
In the 1950s, Honda was well on its way to becoming a leader in the world of motorcycle manufacturing. Honda’s Yamato Plant in Saitama, currently Saitama Factory’s Wako Plant, went into operation in May 1953. In July of that year, its was combined with Shirako Plant, and together they became Saitama Factory. Aoi Plant in Hamamatsu, now Hamamatsu Factory, began operating in 1954.
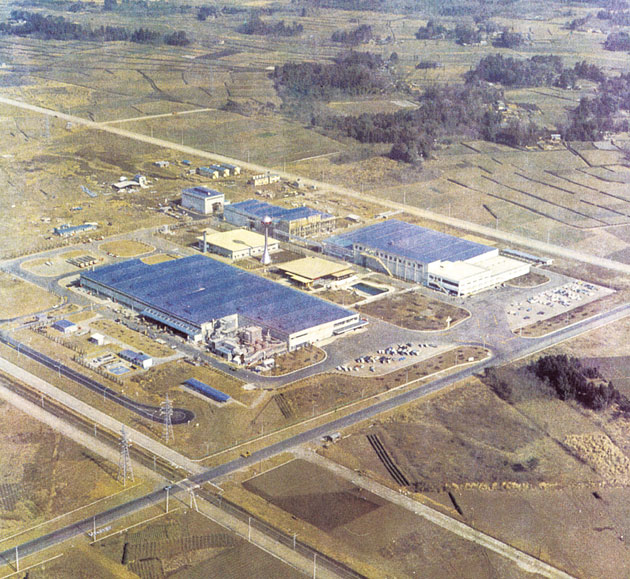
An overview of Sayama Factory soon after the start of operations.
Initially, in order to secure more effective machine processing at the plants, their respective Manufacturing Machinery divisions were intended to produce jigs and modify machines to meet the target specifications. These functions soon expanded, however. By 1956, when Honda expanded its lineup with the Dream and Benly models, the Manufacturing Machinery divisions were already developing original machines to process cylinder heads and crankcases. These were the so-called modular components of their day.
A joint project was established by Saitama Factory (currently Wako Plant) and Hamamatsu Factory in June 1956, in order that Honda might develop a high-precision machining table for use in the manufacture of multiple models. The team developed the Honda Universal Machine, or HUM. As opposed to conventional machining tables, which offered much less flexibility and could not be used to process modular components of different specifications, the HUM delivered multiple-specification processing capability with its replaceable processing units. Each of these comprised a multiple-axis blade section - also called a ganged head - and jigs, which could be changed in modular fashion. With that, Honda’s innovative new machine achieved a superior degree of accuracy, plus a remarkable setup time of just five minutes. Honda made a total of six HUMs, and these units amply demonstrated their capabilities in the production of the 1957 Dream C70 and 1958 Benly C90.
"There weren’t many manufacturers of general machine tools at that time who really understood Honda’s manufacturing philosophy," said Hiroshi Tanabe, who was then assistant manager of Hamamatsu Factory’s Production Engineering Section. "So, we often had a hard time negotiating prices and delivery schedules. Even so, Mr. Honda believed we couldn’t become a competitive manufacturer unless we had the ability to build our own processing machines."
Several changes had in fact been introduced during the pre-production planning for Honda’s new Dream C70 and Benly C90 motorcycles, resulting in significant differences in production format. In those days it was normal for each of the processes on the line to be broken down into a series of steps. This simplified the operations within the processes themselves, increasing the speed of the line and overall efficiency of mass production. However, that approach, for all of its merit, had certain disadvantages. Despite the simplification of processes, line length increased. Moreover, the factory could not achieve a quick, flexible response to model changes or reductions in production volume in the event demand should drop.
Honda’s solution was a machine for "one-chuck, multidirectional simultaneous processing" that could perform many steps at once. The purpose of this was to integrate steps and reduce the number of stations required to process a system of parts.
Eventually, that machine led to the dedicated four-direction horizontal turning machine developed for the Benly C90, and then to the dedicated five-direction drum-turning machine for mass production of Super Cub bikes.
Manufacturing Machinery: A Factory Comes to Life
The Super Cub C100 completed at Saitama Factory in July 1958 was an instant hit upon its release the following month, generating record sales.
Its popularity, in fact, continued well into 1959, with a constant demand in excess of available supplies. Ultimately, production volume reached 15,000 units per month, and this figure was beyond the production capacity of Honda’s Saitama and Hamamatsu factories combined.
Therefore, Soichiro Honda and Takeo Fujisawa decided to build a new production base so that inventories of Super Cub bikes could be maintained. In September of that year, the company purchased a parcel of land with an area of 700,000 square meters on a former factory site of the Imperial Navy in the city of Suzuka, Mie Prefecture, and began building a new plant. Just seven months later, in April 1960, the new Suzuka Factory shifted into operation. The enhancement to Super Cub production provided an additional boost to sales of that model, consolidating Honda’s position as a leading maker of quality motorcycles.
Honda, though, had already taken steps to cope with repeated increases in Super Cub production, recruiting personnel from within and outside the company for assignment to Saitama Factory’s Shirako Plant. This facility had been identified as the center of all Manufacturing Machinery divisions, in order to enhance its ability to design and manufacture production machines. As a result, Shirako’s Manufacturing Machinery Division continued to strengthen and expand as Honda introduced new models and production volumes increased. Then, in September 1960, Honda reorganized the division as an independent operation. The main purpose of the new Manufacturing Machinery factory was to build the processing machines that would optimize the company’s overall process of manufacturing.
"With the processing machines and facilities, it was our objective to increase Honda’s competitiveness in terms of production," said Shigemasa Suzuki, then manager of the factory’s First Design Section. "This may sound exaggerated, but we were told that the processing machines we were making didn’t have to be effective outside Honda. Kiyoshi Kawashima, who was the general manager of Saitama Factory, would even tell us not to design general-purpose machines. I assumed he wanted us to design efficient, highly cost-effective machines, and that of course those kinds of things wouldn’t be available from outside providers."
Honda unveiled its Honda Sports S360 and S500 series small sports cars and the T360 mini truck at the 9th Tokyo Motor Show held October 1962 in Harumi, Tokyo. Japan was at the time embarking on a period of high economic growth, and the new models from Honda - already a newsmaker as the world’s leading motorcycle manufacturer - sparked considerable public interest.
Therefore, the Manufacturing Machinery factory, anticipating growth in car production, began studying a new processing machine for cylinder heads, the parts that required the most processing steps. One of the important requirements in developing such a machine was the incorporation of a space-saving design that would facilitate more effective use of production space. It was necessary because Honda’s automobiles were still being made at the motorcycle production plant.
Based on Mr. Honda’s idea of a rotary system, the Manufacturing Machinery factory completed a single-chuck machine capable of performing what normally would have taken seven dedicated machines to do. Moreover, it allowed the same operator who installed the workpiece to verify the processing of the workpiece upon its return. In that regard, the machine proved a considerable enhancement to operator satisfaction, and this was something Mr. Honda had long pursued as a personal ideal.
Honda began the production of its T360 mini truck at Saitama in June 1963, and in August, the Honda Sports S500 at Hamamatsu. The stamped parts for the two models, including chassis and hood covers, were manufactured at Suzuka Factory for shipment to the two production factories. Then in March 1964, the Hamamatsu facility began production of the S600. However, to prevent gear noise from the S600’s high-revving, high-output engine, an increase in precision would be needed. Accordingly, the Manufacturing Machinery factory had been busily conducting research into high-precision machinery, in addition to the design and manufacturing of dedicated production machines. However, to meet the S600’s target mass-production launch, the factory contacted Reisshauer in Switzerland, a leading manufacturer in the field, to build dedicated gear-grinding machines. When it later discovered that the delivery schedule couldn’t be met, the Manufacturing Machinery factory quickly formed a technological partnership with the Swiss company to manufacture ten units, and these became known as Honda Reisshauer gear-grinding machines.
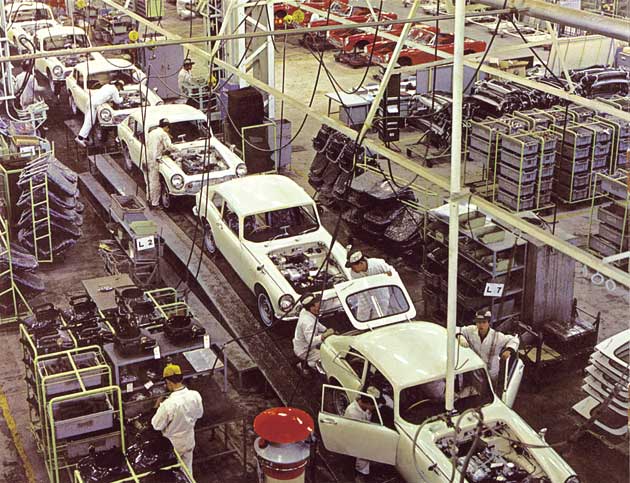
The S600 Coupe on the assembly line at Sayama Factory. The metal casting plant, upon the start of operations in April 1965, initially produced dies for the Coupe.
The Manufacturing Machinery factory, in addition to building machine-processing systems for motorcycle engine parts, soon began handling more automobile production systems in order to keep pace with Honda’s growing output in that area.
Sayama Factory Starts Up: Establishing a System for Car Production
Japan was the proud host of the 1964 Olympic Games, exhibiting the wonders of its capital city, Tokyo, for all the world to see. As a result, the nation enjoyed double-digit economic growth for the first time. It was during this period that Japan, spurred by its staggering new prosperity, began making its rapid transition to an automotive society.
Yet, Honda was already at the peak of its capacity to produce automobiles. At Saitama, Hamamatsu, and Suzuka factories, which were sharing the responsibilities of production, the growing numbers of automobile parts began having an effect on the production of motorcycles, the company’s chief product line. Accordingly, Messrs. Honda and Fujisawa decided it was time to build a dedicated plant for the production of cars. It was thus decided that the company would use the land it had purchased at the Kawagoe/Sayama Industrial Park in Saitama Prefecture in February 1964. The park was conveniently located near the R&D Center and Saitama Factory. Another factor prompting their decision was that Honda had already begun a full-scale plant facility there in September 1963, under the newly established Manufacturing Machinery Special Planning Office. However, Mr. Honda, never one to be content with things as they were - especially the existing system of car production - would often say to the staff, "I wonder if we could build automobiles using a single-piece forming technique, like they do with toy ones." Of course, he had already envisioned the concept for a car, the ultimate embodiment of which was the N360.
Honda thus began building dedicated plants in order to manufacture large stamped parts in metal and plastic, along with the production of the metal dies needed to manufacture them. Moreover, Mr. Honda wanted to utilize the scrap generated from the stamping process. However, rather than transport the waste material to a separate facility for treatment, he wanted to recycle it for use in casting parts. To expand car production, though, it would first be necessary to build a plant complete with body welding/ assembly, paint, and final assembly lines, then transfer to the new plant those functions in complete car assembly found at the Saitama and Hamamatsu factories.
Honda started building its new automobile plant (which is currently Saitama Factory’s Sayama Plant) the following May. Around that time, the company established its Special Planning Office for the construction of a metal casting plant that would enhance the company’s ability to produce large automobile parts in-house. With that, planning got under way for the metal casting plant, its facilities, and equipment. In November, the Manufacturing Machinery factory completed the transfer of facilities from Shirako to Sayama, shifting into operation as the factory’s plant for manufacturing machinery. Through the supervision of the Special Planning Office construction of the casting plant was rapidly progressing. In December, Hamamatsu Factory’s auto production facility was transferred to Sayama Factory’s new plant, whereby it began producing the S600. With that, the expanded Sayama Factory now encompassed auto production, manufacturing machinery, metal casting, and administrative offices.
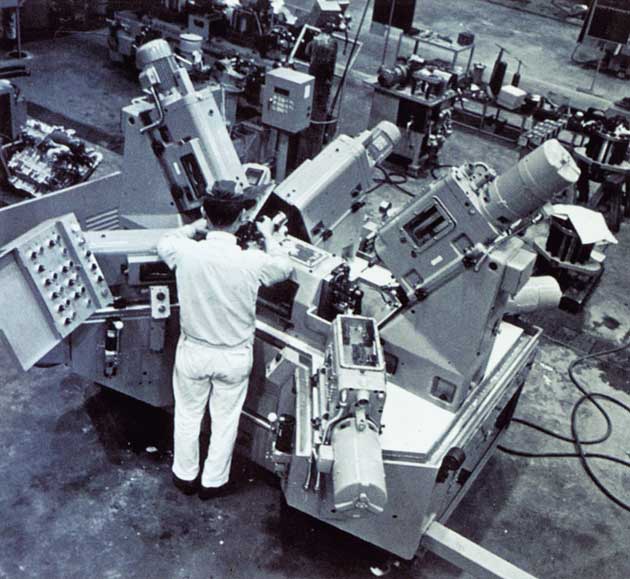
A dedicated production machine being assembled within the plant. Numerous ideas were incorporated in order to achieve optimal processing performance and functions for the target parts.
Sayama began producing the S600 Coupe in March 1965, in addition to the original S600 model. In April, the production facilities for mini trucks of T360 and T500 were transferred from Saitama to Sayama Factory. Concurrently, the metal casting plant’s installation work was being completed where, with its die-processing machines capable of handling large dies, die-spotting machines and trial press machines, operations were soon ready to get under way. At first, the casting plant was in charge of dies for the S600 Coupe, so it did not become fully operational as a pre-production division until it began die production for the N360.
The Vehicle Development Center was established at Saitama Factory in August 1965 to prepare for the production of the new L700 light van, Honda’s first attempt at building a one-box passenger vehicle. The Vehicle Body Development Center’s main objective here was to rectify problems anticipated upon the launch of L700 production and build a framework for full-scale mass-production systems in the areas of automotive press work for frames and body assemblies, including welding.
A press release was issued the following September, after which the L700’s monthly production volume was set at 1,000 units. Seeking a foothold in the car industry, Honda decided that the assurance of prompt shipment would be a critical factor in its success, and therefore shifted L700 production to Sayama Factory in January 1966. Subsequently, Saitama Factory began manufacturing engines for the cars being produced at Sayama Factory.
That October, Honda implemented an organizational change at Sayama. Under the new structure, the manufacturing machinery plant and metal casting plant were renamed the First and Second Manufacturing Machinery plants, respectively. This meant that the functions of the former would expand steadily as Honda made its transition to full-scale auto manufacturing. Thus, in addition to the design and production of machining facilities for engine parts, the plant also became responsible for welding-assembly jigs and facilities for the welding of body assemblies.
A special planning office was established in April 1966 at Sayama Factory, to support building facilities for plastics work and preparing for production. Subsequently, plant construction was started. Inside the stamping plant, a tandem line was installed. The key facility here was a double-action mechanical press that was significantly larger than conventional units. Said to be in the "bolster" size category - meaning that it was large enough to set dies in the press - the machine had a footprint of 4,500 mm x 2,200 mm and output ranging from 1,200 to 700 tons.
Large, deeply drawn parts for automobiles usually would be processed first on a double-action press. Then, the workpiece would be turned 180 degrees using a reversing machine before being forwarded to the next process. This was a conventional process at the time, and initially Honda had used double-action press machines. Starting with production of the N360, Honda gradually introduced single-loading machines, pulling the reversing machines out of the line.
Honda also reduced the die-change time subsequent to changes in target specifications, in order to enhance the efficiency of stamping operations. The result of that effort was the development of original die-change technologies. Other techniques pioneered by the company - such as the single-piece forming of large parts with large press machines and the use of multicavity dies to form right and left parts in sets - were ultimately adopted by other Japanese car makers.
The plastic plant’s facilities boasted an injection machine with a clamping force of 3,300 tons, the world’s longest at the time. Moreover, the casting plant was equipped with a 5-ton/hour, hot-air cupola furnace and high-pressure molding line, providing one-stop production of brake drums from casting and machining all the way through painting.
Preparations for N360 production progressed very nicely, and soon all plant operations were in full swing. Therefore, as part of an effort to embody Mr. Honda’s philosophy on car manufacturing, Sayama Factory was reorganized as a unique production center with functions not found at any other factory. For Honda, which had just started auto production, significant benefits were expected from the factory expansion through the accumulation of expertise regarding auto production and manufacturing techniques.
The N360 Prepares to Launch
Concurrent with the expansion of functions at Sayama, the N Special Planning Office, located inside the factory’s auto plant, was stepping up its operations. Established in April 1966 for the purpose of overseeing production planning for the launch of Honda’s N360 model, the SPO was busy working to ensure the integrity of production engineering along with its administrative duties concerning product quality, quantity and cost.
Personnel at the First Manufacturing Machinery Plant thus entered into collaboration with the N Special Planning Office in order to develop a group of welding machines for subassemblies, along with a machine for main assemblies - the aptly named "Battleship." Upon completion, the machines were transported to the Sayama Auto Plant. Having learned from the initial production of bodies, in which the motorcycle production facilities were involved without much warning in order to meet customer demand, Honda had now designed its new welding machi-nes according to the single-piece forming technique, using large panels for improved accuracy and productivity. Thus, these machines were the basis for subsequent welding machines Honda would develop for use in automobile production. In fact, the entire process was subject to constant change. In order to deal with model changes and demands for higher productivity, processing times had to be reduced and flexibility enhanced on the line.
In November 1966, Sayama Factory implemented an organizational change to establish a system of mass production for the N360. It was hoped that this new system also would ensure a smooth launch for every new model Honda introduced.
According to the new organization, the auto plant was renamed the First Plant, while the First and Second Manufacturing Machinery plants became the Second and Third plants. The Third Plant, once it had absorbed the Special Planning Office, was also given the role of overseeing mass production for plastic working parts, since the latter had been relieved of duty following the completion and startup of stamping, plastic and casting plants. With the additional function, the Third Plant played a key role in the design and production of dies for large plastic parts to be used in new models starting with the Honda 1300, also known as the H1300.
The Challenge: New Technologies in Body Production
Japanese society had made remarkable progress in its move toward adoption of the car, and Honda had responded with an energetic plan to establish itself in the automotive market. Toward that end, the company endeavored to shorten the lead-time from product development through to mass-production, reduce startup losses, and minimize the investment required to launch new models. These things were necessary in order to increase competitiveness against rival makers. To accomplish that, though, Honda would have to establish a comprehensive technology for body production as quickly as possible.
The accuracy of stamping dies is the one area that most assuredly separates a good car body from an inferior one. The design and production of large stamping dies, in particular, requires thorough expertise in forming techniques, so the Third Plant (the former Metal Casting plant) faced several challenges. However, the obstacles brought forth unique solutions, including the use of raised blades for trimming.
The accuracy of dimensions with regard to body contours was another requirement in die production. Since the days of the Metal Casting Plant, the Third Plant had been creating standard models (SM) for external contours, according to dimensional measurements from clay models. These were taken in 100-mm intervals, and were supplemented with external line drawings supplied by Honda R&D. The line drawings were themselves aided immeasurably by the detailed measurements from SMs and numerical values representing body contours. For the inner sheet of a panel, the contours and thickness of the outer sheet were used to create an SM, from which numerical values and line drawings could then be calculated and drawn. To examine the contours of dies, reverse plaster models were created from these SMs. Moreover, the line drawings and numerical values were used as the inspection jigs for the template and panels of welding jig. These were eventually adopted as references in designing exterior/interior parts assembled on the body of the complete car.
Through these and other efforts, the Third Plant evolved a unique technology with which it could convert 3-D body contours into SM-based numerical values and line drawings. While numerous steps were involved in the process of conversion, there was at the same time an effort being made to computerize the process. The technology of contour-to-numerics conversion, in fact, led to the development of Honda’s original CAD/CAM systems and the NC processing systems. These did not require preexisting models at all. The range of original technologies developed by Sayama Plant, together with its convenient location near the R&D Center, further strengthened its collaborative associations with R&D with regard to new model developments. This enabled the plant to grow in the scope and scale of its operations. In light of this, Honda decided to use the Third Plant to design and produce dies for the H1300 body, which was to be manufactured at Suzuka. Subsequently, the design and production of body production dies for each new model would be assigned to the Third Plant regardless of which factory would produce the actual body. Gradually, the Third Plant began to play the role of Honda’s corporate die-tooling division.
Beginning with development of the Honda Life, the Third Plant began supplying to the R&D Center mockup models (resin-based stereoscopic models) made during the SM creation process. There the models were set up so they would closely resemble their real-world descendants, a process that allowed the designers and engineers to refine the characteristics of the final product. Moreover, the Third Plant worked to strengthen its development capabilities with regard to prototype dies, and soon it was supplying the R&D Center with quality close to that of mass-production panels for use on the prototypes. This considerably enhanced the R&D Center’s development operations, while personnel at the Third Plant were able to reflect productivity factors in the drawings and resolve forming-related issues in advance. Thus, the expanded Honda operation achieved the shorter lead-time it needed to ensure a smooth shift to mass production.
New Model Production: Project Teams in Transition
Honda’s new N360 mini passenger car was introduced in March 1967. A result of diligent efforts to overcome production-related problems, the N360 was nevertheless well received for its performance and affordable price. In fact, it was an immediate success, topping the list of highest-selling mini cars in registration units just three months after its market launch.
That April, Honda formed the Automotive Special Planning Office, the responsibility of which was to oversee the construction of Suzuka Factory’s automobile plant and prepare for production of the TN360 mini truck. Experts from different fields of engineering were assembled from the production departments and assigned to the Special Planning Office, where preproduction operations promptly got underway. Plant construction moved along at an amazing pace, and in October - just five months after completion of the plant - the TN360 went into production.
The next year, 1968, saw preparations for the production of the H1300 compact passenger car at Suzuka, augmenting the TN line operating at its automobile plant. The H1300 was Honda’s first passenger model in that category of size and displacement. Boasting a world’s-first - Honda’s original "Duo Dyna Air Cooling" (DDAC) technology - the H1300 had been developed under the direct supervision of Mr. Honda. Actually a high-performance sedan, the car’s performance figures of 175 km and output of 96 horsepower were far beyond anything it its class.
Production of the H1300 engine had been planned mainly by the staff in charge of machine processing at Saitama Factory, where other auto engines were being manufactured. The Saitama staff held numerous discussions with the R&D Center concerning productivity and drawing specifications, in order to determine the design of the machine processing line and outline facilities planning for necessary engine parts. Preparations were carried out in coordination with personnel from Suzuka Factory and Sayama Factory’s Second Plant. Production of the H1300 got under way at Suzuka Factory in May 1969.
The H1300, though, was subject to numerous design changes, even after it had entered the production line. Therefore, to assist the factory with the initial startup, the R&D Center stationed a group of personnel at Suzuka. Staying at the factory over a prolonged period, the group worked to implement these changes. The factory operated the line 24 hours a day, through constant changes, in order to meet the production requirements.
Concurrently, a project team consisting of experts from various fields was put together at Suzuka Factory that June, in order to oversee production preparations for the next model, the Z360. From an office inside Sayama Factory that team, known as PG, worked to promote close communication with the R&D Center, as well as Sayama Factory’s pre-production personnel in charge of manufacturing machinery and metal casting. During the process of production preparation, PG conducted reviews of productivity, production-line design, facilities planning, investments, and costs. Soon, mass-production trials got under way to ensure that the Z360 would launch without a problem. However, without warning, when preparations were in their final stage, Honda decided to move the production to Sayama Factory. The reasons for the decision included the types of models then being manufactured at Sayama and Suzuka.
Honda had always approached pre-production by assembling a project team at the factory where its new model was to be built. The company had done so with the Vehicle Body Development Center, N360 Special Planning Office and TN360 Automobile Special Planning Office. However, this made it hard to maintain continuity between projects and accumulate all the expertise needed to ensure smooth model launches. Accordingly, there was a need to establish a management group that could utilize the expertise of engineers from specific fields. PG was formed as a means of addressing such problems.
Honda established production engineering groups, called HTGs (Honda technical groups), at each factory in August 1970.
The purpose of the HTGs was to draw upon the resources of expert engineers whom Honda was fostering under its Certification System (introduced in 1968), and promote their collaborative efforts with the product-development side. This method was intended to create new production systems by introducing advanced production facilities and methods. HTG projects, many of which were promoted under Mr. Honda’s direct supervision, produced results in several fields. However, the HTGs were dissolved in December 1973, subsequent to the establishment of a new engineering division. Their responsibilities were transferred to the new division, and the engineers returned to their original positions.
Honda Manufacturing Machinery: A Separate Entity
Honda separated Sayama Factory’s Second Plant and established Honda Manufacturing Machinery Co., Ltd., on September 1, 1970.
Manufacturing Machinery was intended to serve as the company’s corporate pre-production division, looking after the needs of every Honda factory. Organized as an autonomous body in charge of engineering development, Honda Manufacturing Machinery worked to create innovative production techniques based on original ideas with the support of acknowledged experts. In fact, Mr. Honda was the company’s first president. As an independent entity Honda Manufacturing Machinery expanded its original function of developing and supplying production facilities for exclusive use by Honda factories. To ensure that these factories had ample supplies of low-cost, high-quality parts, the company also began selling and leasing dedicated production machines and general-purpose machines to its associate suppliers. Moreover, such machines were sold to general customers.
"Honda Manufacturing Machinery was established as an independent company so that it could create new processing methods based on free thinking and develop useful machinery incorporating those methods," said Kiyoshi Kawashima, then the senior managing director of Honda Motor. "We also wanted the company to become a full-fledged manufacturer of dedicated production machines, which it will sell to customers outside the Honda organization.
"Looking into the future, we didn’t want the company to remain simply a manufacturer of machine tools. The underlying concept was that it would eventually provide ‘engineering services.’ By that I mean the integrated services that combined the processing methods and production technologies it had developed."
The role of Honda Manufacturing Machinery expanded in keeping with Honda’s growing activities in car production. It developed automatic jig-changing mechanisms for general automotive welding machines in December, following its establishment, and designed general welding (GW) jigs for small-volume production in time for production of the Life stepvan derivative model. Moreover, it assisted with the launch of the Civic van by developing swing-type general welders.
In addition to these innovations, Honda Manufacturing Machinery was a tireless researcher of new production engineering systems. Early in the fall of 1972, the company carried out production engineering surveys targeting key industries in the U.S. and Europe. More than forty companies took part, including car makers, machine-tool manufacturers, makers of measurement devices and makers of fuel-injection systems. Even think tanks and computer companies were involved.
In the U.S., the staff visited one of the country’s leading machine-tool manufacturers in order to study the operation of their large-scale flexible line, which encompassed a number of NC machines. At the new assembly plant of an internationally renowned automobile manufacturer, they studied industrial robots in operation.
In Japan, research into robotics began in 1967 when the U.S. company AMF (American Machine & Foundry) introduced a robot called "Versatran." Then, within three years robotics had entered the Japanese auto industry. In February 1973, Honda Manufacturing Machinery developed its original HRB600 robot, initiating Honda’s research in that emerging field. With that, Honda Manufacturing Machinery set forth on a quest for new production technologies.
BE: Establishing the Production Preparation System
Honda debuted its new CVCC engine in February 1971, using an innovative low emissions technology as a springboard into the global spotlight. In those days, growing public concern with regard to safety and air pollution had forced automobile manufacturers to look beyond high performance and quality. To survive, it would be essential to provide a diverse line of cars designed to meet the needs of individual consumers.
Amid all this, Sayama Factory implemented an organizational change in September of the same year. The factory’s Second Plant (the former Third Plant renamed after the Honda Manufacturing Machinery spin-off) transferred to the First Plant its mass-production functions for plastics work such as stamping, molding and casting. It then integrated its pre-production functions—primarily molding, design, and die production - with PG (which had successfully completed the Life launch) and restarted it as the Body Engineering Plant, or BE (Body Engineering).
BE’s numerous responsibilities included the development of original technologies regarding body-contour reproduction, along with the design and production of dies. Moreover, BE was to collaborate with engineering groups specializing in body production as well as with Honda Manufacturing Machinery, which was responsible for the design and production of welding machines and fixtures (jigs with welding functions). Thus, it was believed that all Honda factories would receive assistance with body production. Therefore, in order to enhance Honda's production structure in all areas of body production, and increase the company's competitiveness, BE took an active role in engineering development. The group even established a system whereby Honda factories could prepare for the production launch of a new model concurrently with product development at Honda R&D. lt was a very close relationship with the factories that established BE as a critical force in production quality.
The system of production preparation established by BE targeted the following requirements:
[1] A shorter lead-time from pre-production through production
[2] Assurance of both productivity and product performance
[3] Fewer initial problems at the start of mass production
[4] Minimized startup costs and losses
[5] Lower per-model investment in production facilities
These rather lofty goals meant that BE would have to work with Honda R&D, and that anticipated engineering problems would have to be settled prior to mass production. The creation of prototypes was one such method. Furthermore, BE collaborated with Honda's production departments in resolving issues arising from inappropriate production structures. The group proposed new systems of production, supplied dies, welding jigs, and machine equipment, and verified in detail whether or not the target requirements were being met.
BE also established a miniature line inside the plant to conduct trial mass production using the dies and welding facilities that it had already approved for delivery to the various production departments. These trial runs, with participation by the leaders of actual production processes, were intended to familiarize production personnel with the new facilities and help create the manuals needed for production and maintenance, thereby ensuring mass production without any significant problems.
The production preparation system was now in place, and the factory managers and Honda Motor's director in charge turned their attention to the evaluation meetings. These were held at each stage leading to mass production. Through such efforts, the factories' operational structures regarding body production continued to improve,resulting in progressive quality improvements for each succeeding model. Sometimes the improvement effort even led to drastic reforms.
True to its name, BE came to play a critical role in Honda's activities as a car maker. With its wide-ranging expertise, the Body Engineering group brought new methods into play for the enhancement of overall product quality
While the system of preparations for body production was being established, a similar program was under way with regard to engine production. At Saitama Factory in particular, a number of special engineering groups had been put together. Comprising experts in various aspects of engine design,these group worked on development in areas such as heat-treating, forging/casting, die-casting, machine processing and assembly.
With regard to the machine processing of engine parts, the Machine Processing Group was responsible for the development of processing methods and design of production lines. Through a series of reviews conducted wiht the R&D Center covering productivity and drawing specifications, and in close coordination with the factory's Manufacturing Machinery Division in charge of equipment design and production, the Machine Proscessing Group took the lead in preparations. In the process of implementing production preparations for new models, the group was sometimes referred to as EE(Engine Engineering), as opposed to BE. Moreover, EE became a collective reference to the Machine Processing Group and Honda Manufacturing Machinery.
Honda Engineering: Toward the New Era
The auto industry's race to develop new products was making it tougher on Honda. Therefore, in order to maintain growth the company had to diversify product development and achieve higher levels of productivity and flexibility. Moreover, it would need to direct a corporate effort toward the promotion of its composite functions. Honda had to live its image as a group of professionals.
It was against this backdrop that the Engineering Division was established in March 1973. Together with the engineering groups from Saitama Factory's Wako Plant, BE initially comprised the Production Engineering Department in the Engineering Division. Subsequently, however, with the organizational change implemented that November, the department became independent of the Engineering Division and was thereafter known as the Production Engineering Division. Behind the decision to separate the production engineering function was the corporate realization that in order for the company to grow as a global manufacturer it would have to reinforce its production system for enhanced competitiveness.
Accordingly, it would dramatically step up the development of production technologies.
Honda expanded its operations through KD and joint ventures in 1974, while carrying out its technological assistance on behalf of associated companies overseas. In light of its increasingly global operations, Honda was being asked to reshape the existing organizations into a new group structure. In the area of product development, it was becoming more important to enhance quality and cost-effectiveness, both of which were the keys to global competitiveness. At the same time, it was necessary to develop a more diverse lineup of models. This meant there was an urgent need for enhanced production flexibility at all Honda factories, including the parts suppliers. As Takeo Fujisawa had outlined in his "Ideas of the President," an article published in the Honda Company Newsletter, this was an ideas with which Honda had kept faith ever since it began expanding its motorcycle production. Indeed, the company had gone through numerous efforts in search of a more flexible production approach; one with which it could achive constant, full-capacity operations.
Honda, being a manufacturer of motorcycles, automobiles, and power products, thus confronted the immediate need to build a production structure that would allow it to respond to market changes. Since the market was fast becoming a global one, the compamy was in for the fight of its life.
Under such circumstances, Honda decided it would consolidate preproduction functions with regard to production engineering. Accordingly, Honda Engineering Co.,Ltd. (EG) was established on July 1, 1974, as a combined body of Honda Manufacturing Machinery and the Production Engineering Division. The following three items were thus established as key goals in EG's endeavor:
[1] Anticipate changes in the surrounding conditions, as well as corporate needs. Develop appropriate production technologies and methods in order to facilitate newproduct developments and improvements in the company's production structure.
[2] Provide the production departments with highly competitive and timely methods, as part of a labor-saving investment to produce new models, construct new plants for KD and joint ventures or implement structural reforms at associated factories, and to ensure that goals for quality, quantity and cost are attained.
[3] Companies engaging in production and sales now face global competition. Therefore, it is essential that these companies maintain sophisticated production methods. EG will direct its effort to, and accumulate expertise in, the development of production techonologies to meet this need, and by doing so, will fulfill its responsibilities on behalf of the entire Honda group.
A new system was also established to divide various functions affecting the entire Honda group, and in that system, specific functions were laid out. Honda R&D would develop appealing new products, and EG would develop the appropriate production methods to make production feasible. Honda Motor would then ensure efficient production and sales operations.
Ensuring Honda's Production Competitiveness
EG's role would be to ensure Honda's production competitiveness by proposing plans for production lines and processing methods based on the results and expretise that it has accumulated through research and development, and demonstrating ther effectiveness by supplying appropriate dies and machining equipment.
EG has also been instrumental in its collaborative effort with Honda R&D. In addition to proposing productivity improvements in the drawing stage, EG has cooperated in the development of product structures and functional parts, when required as part of Honda's production strategies, by applying its expertise in production engineering. Such efforts have been implemented in the various aspects of Honda products, adding to their perfomance.
A quality front wheel-drive system is the key selling feature in Honda automobiles. In earlier days these front wheel-drive systems incorporated as a key component the constant-velocity (CV) joins manufactured by the domestic supplier T, which was doing business with Honda at the time. However, these joints were being produced under a patent license held by a British company. Therefore, as the use of front-wheel drive spread throughout the Honda line of compact cars, production volume and cost were subjected to the limitations of T's production capacity.
Accordingly, Honda was assisting T in producing constant velocity joints by supplying cold-forged parts from the Wako Plant in Saitama. However, that soon proved insufficient, so the company decided to broaden its support from material parts to machine processing and final assembly. Moreover, it assigned EG the task of overseeing production. As a result of its involvement, EG developed Honda's original constant-velocity joints, the SBJ and EGI (straight bell joint and EG inboard joint). Originating from the cold-forging technology EG had accrued over the years through Saitama Factory operations, the new joints proved highly functional. Moreover, they relieved Honda of any concern over a possible patent infringement. Honda was thus able to manufacture constant-velocity joints needed for all of its automobiles at Saitama Factory's Mohka plant (currently the Tochigi Factory's Mohka plant).
Honda's ultragrinding technology, too, was a result of the effort to develop a new constant-velocity joint. This method increased the grinding capacity with regard to shaft components to a level three times that of a conventional device. Therefore, at a time when Honda's overall production was growing, the ultragrinding technology prevented an additional investment. Furthermore, the existing machines could be modified to perform the process, resulting in increased processing volume. This technology produced a dramatic savings in facilities investment and space, particularly with regard to cam grinding and grinding of valve systems, which were made of materials that would otherwise have been difficult to grind.
The Honda Reisshauer Gear Grinding Machines, which were not achieving the necessary productivity, were upgraded to the ultragrinding specification and reintroduced to the mass production lines for drive gears and driven gears alike. Moreover, the expanded use of geargrinding machines in mass production led to the development of Honda's original ultra gear-grinding machine, offering considerably greater production efficiency.
lncorporating the ultragrinding technology, the new gear machine was the first such device to adopt the non-stop automatic synchronous method. This permitted the operator to install and remove workpieces without having to stop the machine. The invention brought forth significant improvements in productivity, providing higher grinding capacity and reducing the cycle time. lt also contributed to higher product performance by reducing the level of noise from the engine gears.
Honda's ultragrinding technology, in addition to engine-part processing for shaft parts and gears, was applied to a wide range of areas. For example, it was adated to the new manufacturing method (new 3P tank method) Honda had developed for motorcycle fuel tanks, and was incorporated in the ultrasanders used in the finishing of in-house production dies. lndeed, the true benefit of this technology was far greater than anyone could have expected originally. Ultimately it led to the establishment of EG's Kawagoe Plant, which was built to meet the growing demand for precision grinding stones employed in this method.
Honda's product develoment in the area of autobodies was deeply influenced by the company's plastic technology, which the comany had nurtured since its days as a dedicated motorcycle manufacturer. The newly developed plastic parts, including bumpers, gave Honda a serious advantage over its competitors in the world of car design. This difference in approach and perspective led the company to develop an innovative manufacturing method-known as "Padded lnstrument Panel Manufacturing" -which was applied to the crush pad of the instrument panel. A panel made through this method was incorporated in the new Prelude, which went into production in November1978. It achieved that essential combination of productivity and performance, eventually becoming the mainstream method for the production of instrument panel crush pads.
Stamping technology is another key Honda innovation, having given birth to the company's original body structure based on large panels. Thus, after introducing automated machines to the production process and shortening the time needed for die changes and setup, Honda dramaticlly improved stamping productivity in the early 1980s by extensively reducing the number of necessary steps. At least one was eliminated for all parts, and in some cases up to four more were cut out. Honda has since become the industry leader in press technology, with a key development being a transfer press capable of exchanging dies with tandem lines and producing parts using multicavity dies.
EG has played a significant role in Honda's various production strategies, helping the company increase its production competitiveness by providing production facilities with the state of the art engineering equipment have brought forth numerous inventions, including an innovative, high-speed module machine. This device achieved both productivity and flexibility in the processing of modular engine components, resulting in the world's smallest welding assembly line. These technologies, having been a driving force behind the company's production competitiveness, have earned praise and recognition throughout the world of auto manufacturing.