Tech Views — Vol.10 Flangeless & Titanium Fuel Tanks
Flangeless Fuel Tank (2/2)
PART1 -CB1100EX/CB1100RS Flangeless Fuel Tank
Pride and Challenge in Making ‘Cool’ Tanks
The 2017 CB1100’s Flangeless Fuel Tank.
Mention the CB1100 and what comes to mind is the distinctive appearance of its air-cooled engine, its classic frame proportions, its twin shock rear suspension, and so on. This machine manifests a retro-modern feel that has long been a key theme of the Japanese motorcycle industry, while evoking Honda’s history therein and the traditions imbued in the CB line.
The fuel tank mounted on these two newly revised 2017 versions of the CB1100 (the CB1100EX and the CB1100RS) has been causing a stir with its rounded look, which is both classy in appearance while arousing profound feelings of nostalgia among riders of all ages. At the same time, these models were also designed with a look that powerfully emphasizes the individuality of the CB1100.
The manufacturing method used in the production of this fuel tank is referred to as ‘Flangeless.’
Put simply, ‘flangeless’ refers to a specific manufacturing method that bonds the bottom plate of the fuel tank to its upper exterior half, which is the section we most come into contact with.
Conventional fuel tanks are constructed of three main parts, the left and right sides of the upper half, and the bottom, which are all welded together to make the familiar fuel tank shape. When welding the preassembled top half to the bottom, normally a margin along the seam, known as the flange, is used to bond the two halves together. Fuel tanks that leave the flange along their lower outside rims exposed are referred to as flange-type tanks.
Conversely, fuel tanks that have their flange hidden by lap welding along the inside of the contact surfaces are called ‘flangeless’ tanks. The main feature of such tanks is that it allows more individualistic styles to be expressed by eliminating the externally exposed flange.
It may be hard to picture this in a written description, however, let me introduce the differences as previously explained to me by an old hand in the matter.
To use a culinary metaphor, the difference is something like that between a gyoza dumpling (also called a Chinese ‘potsticker’) and an anman, or Chinese red bean paste bun. Try to imagine the difference in shape when their contents are enclosed in their distinctive wrappers. Flange tanks are made in much the same way as gyoza dumplings, in that the edges of the wrapper are joined by pinching them together. In contrast, the flangeless tank is like the anman, in that its bean-paste filling is inserted into a completely round wrapper with no joint line visible. Can you picture that?
So, how did Honda come to make flangeless tanks?
My investigation began here.
Designs to Enhance Both Refinement and Feel
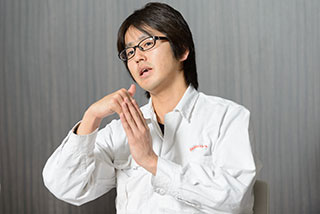
Motoaki Takashima — Press molding department
“A few years ago, there was a movement in the company to try to create more attractive fuel tanks, and flangeless and titanium tanks came up as specific themes. We set out to manufacture a flangeless tank for the new CB1100. However, to accomplish this we had to increase both the number of dies and the number of steps in the production process in order to faithfully reproduce the tank design.
“The normal press molding procedure used to make flange tanks is: molding → cutting → welding. However, when making flangeless tanks, the procedure becomes: molding → cutting → folding the sections to be welded → and finally welding. As a result, more dies and processing steps are required, introducing technical difficulties that make it ill-suited to mass production. However, flangeless tanks exude an impressive sense of style. Our challenge, therefore, was to create a new type of flangeless tank using existing production equipment, and refining our technology.”
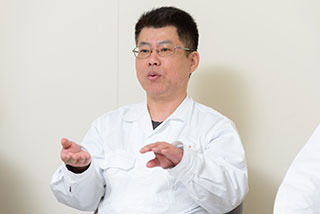
Ryuji Masuda — Press molding simulation analysis
“My department conducts simulations to find the most efficient ways to press-mold the shapes drawn by the designers. Before creating the actual manufacturing dies, we first try to verify the viability of the design by computer. Our goal was to use a combination of existing manufacturing techniques to produce these difficult flangeless tanks, applying the best features of mass production. To achieve this, we worked on improving the molding performance of the mold and press machines so that we could reproduce the tank’s curvature and the depth of its bends with a minimum number of dies. More than simply determiningthe feasibility of the tank shape, we had to achieve a form that also took into consideration subsequent processes such as welding, which are essential stages in the fuel tank manufacturing process. In doing this, we closely liaised with the designers. Since it is necessary to weld three parts—the left, right and bottom—it was also necessary to improve accuracy so that any errors in the actual joining process could be kept to less than 1 millimeter in size.”
This is how the struggle to provide more attractive tanks to larger numbers of riders began. Improvements were sought in all the processes of fuel tank manufacturing.
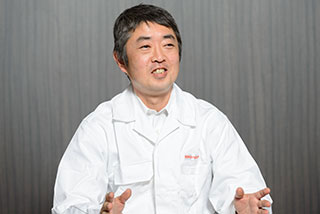
Noriyoshi Kotsubo — Welding department
“We also modified our welding techniques in order to create more attractive looking tanks. Since nearly all fuel tanks, not just of the flangeless type, are formed of thin steel plate, special care is needed when welding because the heat generated can cause distortion in the final product. To construct the CB1100’s tank, we weld three parts together, the tank bottom and the left and right sides of the upper half. However, when welding together the two sides, we didn’t simply layer the sections in the center, as we normally do, but instead used a butt weld at their mating edges. To do this, it was necessary to clamp the parts in a metal die during the welding while still allowing the heat to escape.”
Following preparation of the production equipment used to perform the pressing andwelding of the tank, how did the CB1100’s designers approach the job of creating an attractive tank?
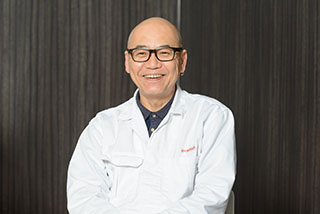
Shoji Yamamoto — Body design
“From a designer’s point of view, the appeal of the flangeless tank lies in the ease with which a sense of depth and complex curvature can be seen from the sides. As a designer, this is the type of expression I’ve always aspired to. In the initial prototypes, we tried making a flangeless tank from the existing CB1100 fuel tank. However, doing that totally changed its look. Moreover, while aiming for an even more refined and modulated form, we tried to create a design that departs somewhat from the basic CB image, and this resulted in the tank we have here. For the logo, we used a slight variation of the HONDA characters created for the old CB750 Four.”
When most tanks are viewed from the side, you can see the flange sticking out like a barrier wrapped around the bottom edge of the tank. However, with the flangeless tank, which doesn’t have this edge, the team were able to achieve a much cleaner-looking shape. Its design invites you to reach out and caress its roundness. Its form also has a lot of depth. However, mounting such a tank on an actual motorcycle turned out to be a tough challenge for the designers, as well.
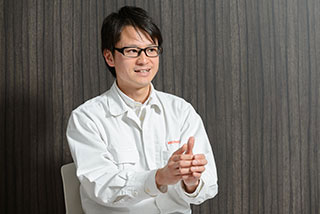
Tomoki Nishijima — Design engineering
“In the case of flange tanks, the welded margin stretches along the bottom edge of the tank. With a flangeless tank, while there’s an area where, for example, the bottom plate and the left and right sections are layered, a welding margin is created, much like the flange tank. However, compared to the flange tank, the weld margin is necessarily wider on the sides. While this may be advantageous in terms of evoking an impressive sense of presence and providing ample fuel capacity, you can run into problems trying to provide enough space for the frame to fit into the space under the tank, particularly in the area between the knees, which really needs to be narrow. So, while trying to maintain a narrower width, we struck a balance between style and function by narrowing the weld margin in this area compared to other parts of the weld. Also, since the front fork comes into close proximity to the tank when the handlebars are turned left and right, we couldn’t let the tank protrude too far forward. Having said that, in terms of style, it also doesn’t look very good if that part of the frame around the steering head is too exposed…”
Yamamoto —
“In terms of design, we wanted to give the tank a sleek, elongated form. We also wanted it to extend from the area where the seat and tank join all the way to the vicinity of the steering head. Above all, appearance is greatly improved if no gaps are visible from the viewpoint of the rider.”
There would be little point in going to the effort of building a flangeless tank if it detracted from the CB1100’s appearance. So the designers exercised the utmost care — down to the smallest millimeter — in pursuing this point.
Nishijima —
“We had a hard time achieving the optimal clearance between the tank and the frame. For instance, when turning the front fork, the harness and throttle cables that reach down from the handlebars also move. We had to tidily contain such movement in the space between the tank and the frame.”
In reality, a lot of painstaking manufacturing skill was adopted in unseen areas in order to embody the ‘cool’ they were seeking.
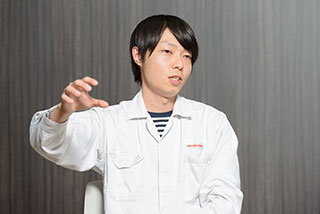
Yasufumi Kitada — Paint department
“To further highlight the appeal of the flangeless tank’s shape, we tried some new ideas in coating as well. We employed a high-quality coating technique which enhances the texture of the clear coat and imparts more thickness and flatness to the clear-coated surface. Much like the pressing department, the paint department worked within the existing conditions of the production line and its equipment to develop a new coating with the finest possible texture.”
How was this achieved?
Kitada —
“Usually, it’s a really time-consuming process trying to give the paint coat a sense of depth. Normally, we apply the clear coat, let it dry, smooth out any imperfections with an ultrafine wet abrasive, and then apply another coat of clear. By repeating this process five times or more, it’s possible to produce a surface with a glass-like sensation of depth. However, such a process is unsuitable for mass production because of the time and effort required. Therefore, we attempted to reproduce the skills of our coating craftsman with new technology, specifically by altering the components that make up the coating, and adjusting the robotic coating operations in the paint booth, and so on. If you look at a reflection in the tank’s surface, I’m sure you’ll appreciate the sense of depth and surface flatness we’ve managed to achieve.”
The cost of a custom paint job is the price one pays for the skill and effort of these coating craftsmen. Starting from initial preparation, this work is incredibly time-consuming, and it is amazing that an almost equivalent finish could be reproduced on the assembly line.
Yamamoto —
“When we know that a high-quality coating will be used, we designers can then aim for greater depth of form while envisioning how that shape will be the visually expressed.”
Nishijima —
“We’re trying to create a sense of ‘cool’ — which represents harmony without compromise between visual design, structural design and manufacturing.”
Again, motorcycles are pleasure-oriented vehicles, and their fuel tanks are the faces of these riding machines. The passion devoted to creating such tanks is an unquantifiable element of performance that captivates riders and passersby alike, and will similarly be conveyed to other models in the months and years ahead. In the final analysis, it became even more apparent that manufacturing closely represents people’s thoughts and dreams. This passion is then transformed into pleasure-oriented mobility through the products that are produced.
It’s my hope that readers will visit their local Honda dealer to experience for themselves the depth, texture and sense of design found in the CB1100EX and CB1100RS’s flangeless fuel tanks.
CB1100EX/RS Flangeless Fuel Tank Manufacturing Process
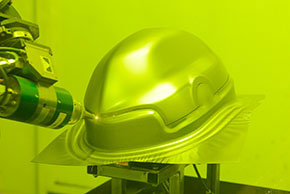
1. The press-molded steel fuel tank parts are trimmed by a robot laser. The trimmed materials are recycled for other uses.
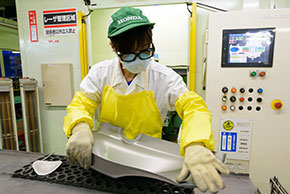
2. The cut-out pieces are visually inspected with the utmost care, then lightly finished by hand in preparation for the next process.
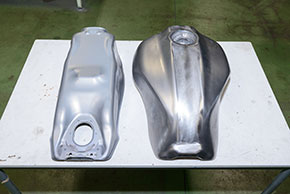
3. The base plate and welded together upper left and right halves of the tank. The shape of the tank can be roughly made out.
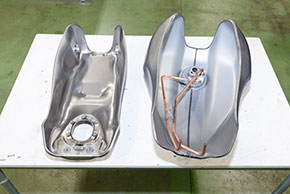
4. The underside of the same parts. Visible inside the tank are the drainpipe, for draining out any gasoline that may leak during servicing, and the breather pipe for venting gasoline fumes.
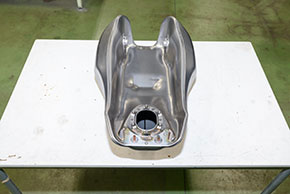
5. Here, the two parts are loosely assembled, and the shape of the tank comes into view.
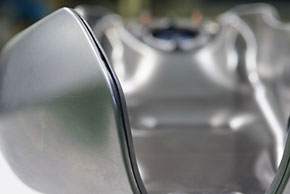
6. This is the margin where the top and bottom halves of the tank will be lap welded. This margin is robot-welded with the utmost precision.
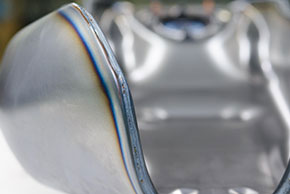
7. After welding, the difference with Photo 6 is clear.
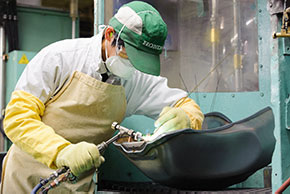
8. Once the tank is welded together, the tip of the drainpipe shown in Photo 4 is manually braze-welded to the base plate. This operation requires considerable skill.
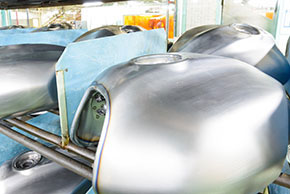
9. With press molding and welding stages done, the tank moves a further step closer to completion. It is then placed on a rack for the next process.
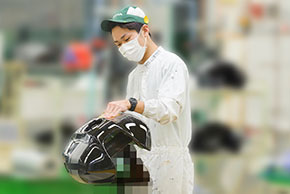
10. After being spray painted in the automated paint booth, this CB1100RS tank proceeds to the stripe application process. Meticulous manual skill ensures a beautiful finish.
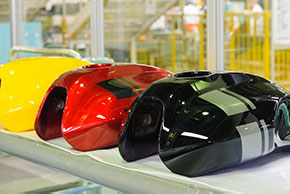
11. After the stripe is applied, the tank is finished with a clear top coat in the final process. The high quality and depth of the coating can be appreciated in the lack of distortion visible in reflected scenery.
- TOP
- Flangeless Fuel Tank
- Titanium Fuel Tank