Evolution of the e:HEV Powertrain
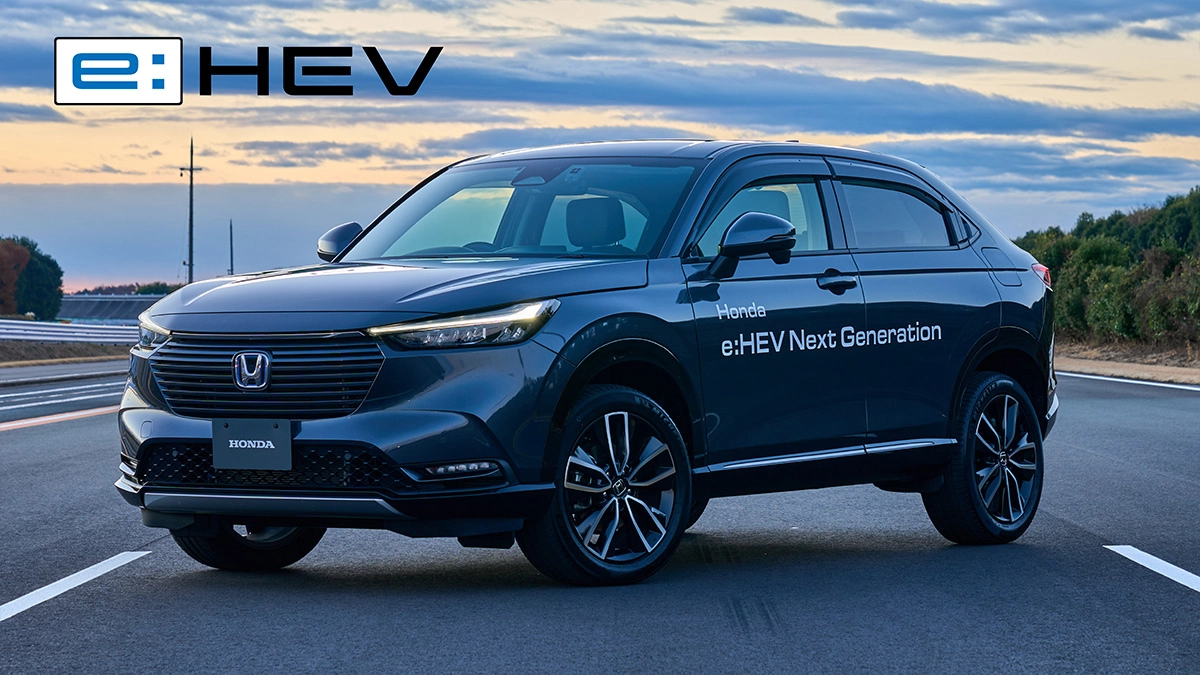
Honda’s Hybrid System Evolution Sustained by Innovative Technology
Honda’s hybrid system first appeared in the first-generation Insight in 1999. The car simultaneously achieved world-leading fuel efficiency (at the time) and driving performance thanks to an aluminum body and Integrated Motor Assist (IMA), Honda’s original compact and lightweight single-motor parallel hybrid system boasting high engine compatibility. In 2012, Honda expanded the choice of hybrid vehicles with the unveiling of three hybrid systems: Sport Hybrid i-DCD, a single-motor hybrid system with separate engine and motor to realize electric vehicle driving; Sport Hybrid i-MMD, a two-motor system and the world’s most efficient (at the time); and Sport Hybrid SH-AWD, combining a V6 engine and three high-output motors to realize high efficiency while enhancing the fun of driving.
The Honda e:HEV two-motor hybrid system series was launched in 2020 and the system continues to evolve as a core technology in the electrification of Honda vehicles.
Honda’s hybrid system evolution
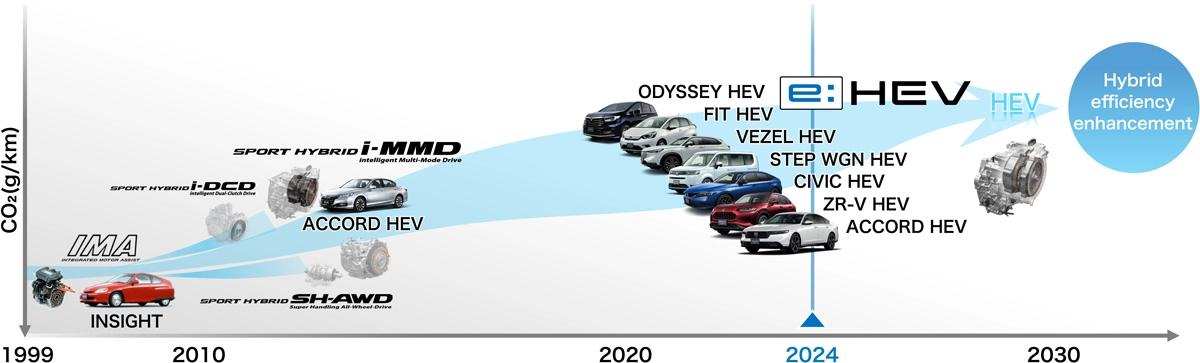
e:HEV—Elevated Levels of Environmental and Driving Performance
Honda’s e:HEV original two-motor hybrid system realizes both outstanding fuel efficiency (environmental performance) and, thanks to a high-output motor, a sophisticated and exhilarating driving experience (driving performance).
High efficiency is realized in all driving situations through automatic and seamless switching between three modes: EV Drive mode, where the vehicle is powered only by electricity from the battery; Hybrid Drive mode, where the vehicle runs off a motor powered by the engine; and an additional Engine Drive mode, unique to Honda, where the engine drives the wheels, directly connected via a clutch.
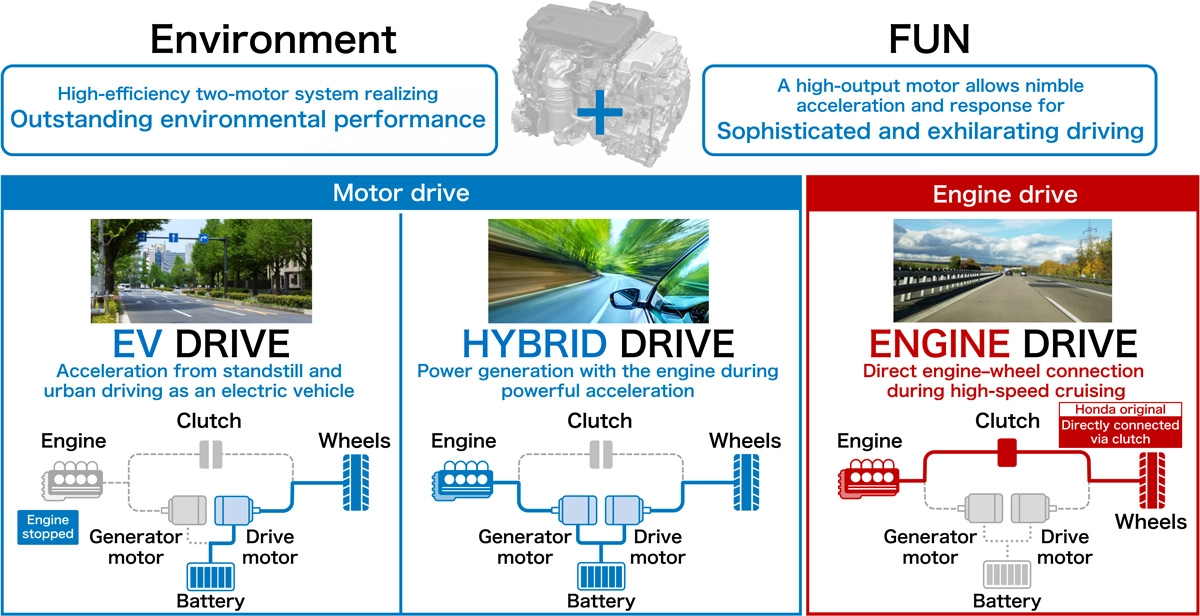
The Next-Generation e:HEV Refined by Sensory-Rich Technologies
The next generation of e:HEV systems will further enhance environmental performance and the sophisticated and exhilarating driving experience through heightened synchronization with driver controls, use of electric all-wheel drive, and other technologies that stimulate the senses. This will involve an overhaul of components, such as the engine and drive unit, and control technology for both small- and medium-sized models.
Advanced Environmental Performance
Combustion of both 1.5-liter and 2.0-liter engines has been improved to realize a stoichiometric air–fuel ratio across the engine’s entire operating range without a reduction in power output. The 1.5-liter engine, in particular, draws on 2.0-liter engine technology, including the direct injection system, to dramatically expand the range in which high efficiency is attained.
Improvements to torque transmission efficiency during direct engine drive and to stoichiometric torque mean fuel efficiency increases with more frequent engagement of Engine Drive mode. In EV Drive and Hybrid Drive modes, too, the world’s highest powertrain efficiency has been achieved by heightening power conversion efficiency and engine efficiency. Honda will also move to raise fuel efficiency of both small- and medium-sized systems by at least 10% alongside platform advancements for medium-sized systems.
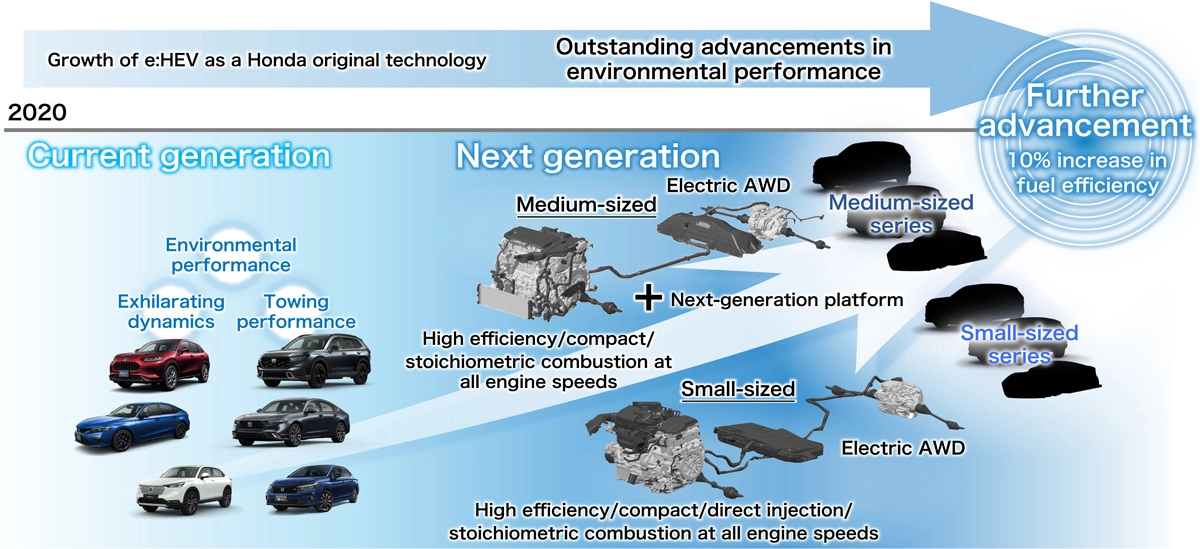
Powertrain efficiency
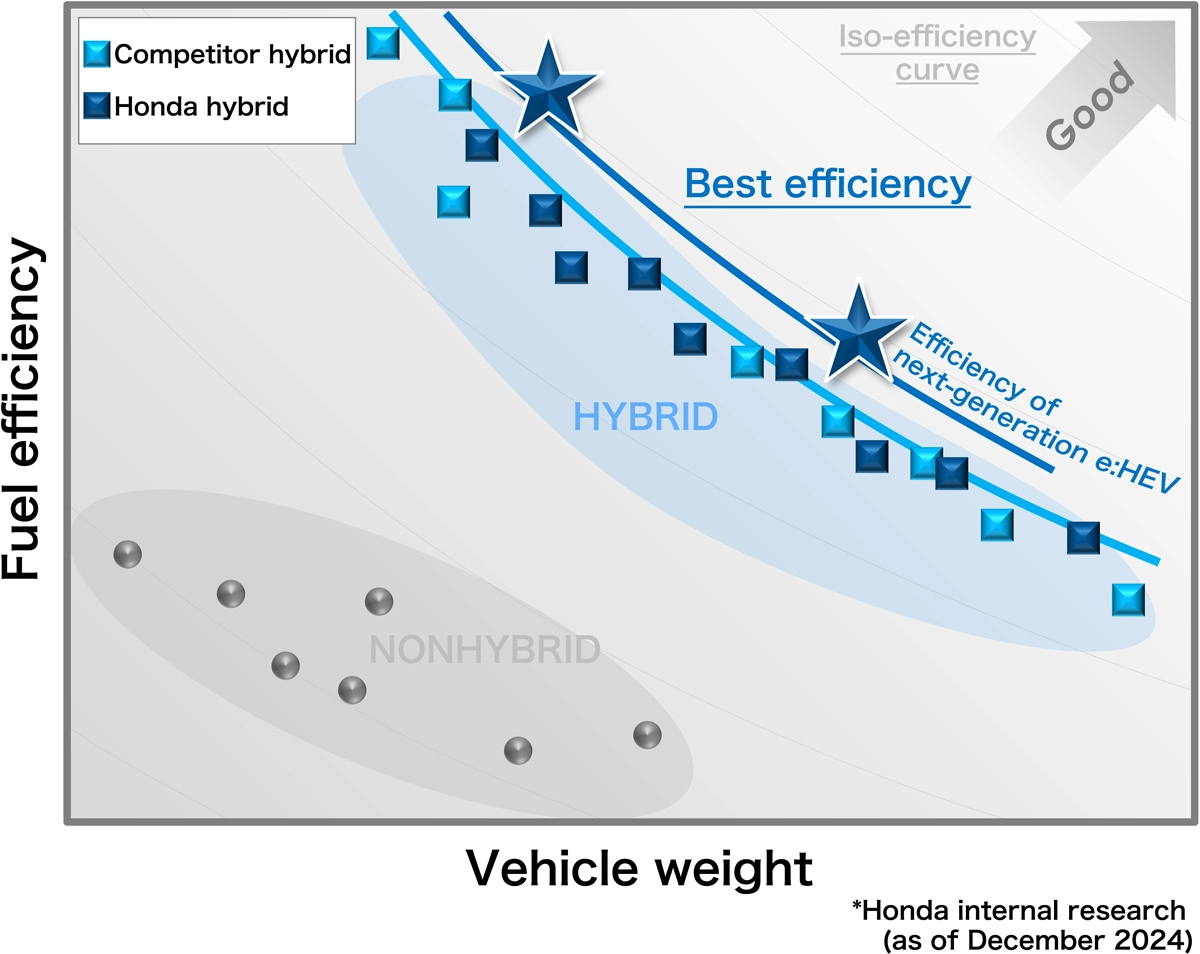
Advanced Driving Performance
The driving appeal of an e:HEV system lies in the nimble response and progressive acceleration produced by its high-output drive motor, as well as superior quietness. In addition, one characteristic of e:HEV technology is Linear Shift Control, which gradually controls engine speed to match the increase in vehicle speed, thereby realizing a rhythmical engine sound like gear changing in a stepped transmission.
During acceleration, Linear Shift Control directly and seamlessly powers the vehicle with the drive motor, at the same time controlling engine speed with the generator motor. Enabling this requires an engine with a wide high efficiency range, a high-efficiency motor, and technology for fine control.
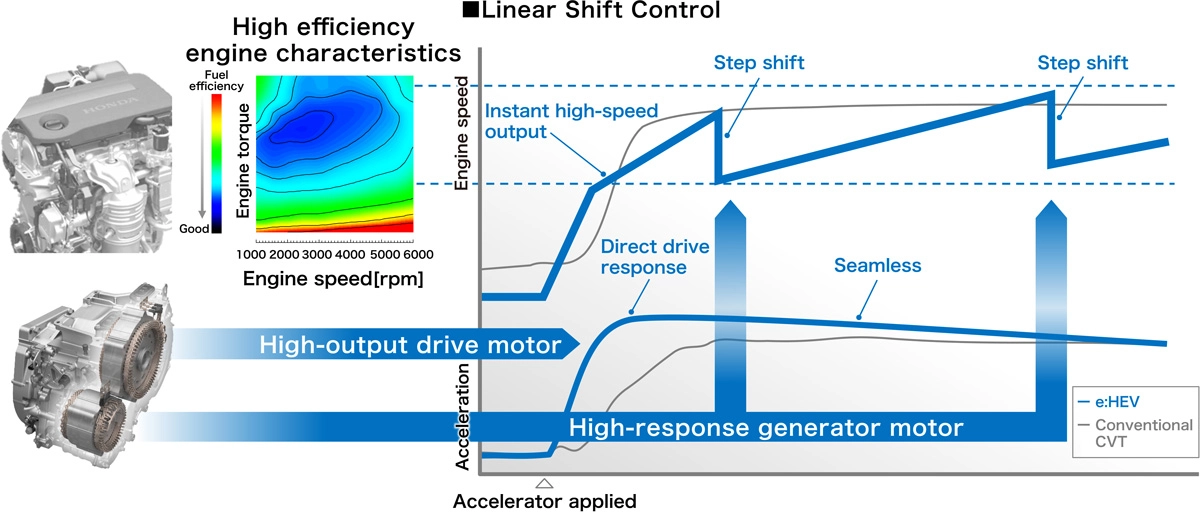
Linear Shift Control has been further advanced for the next-generation e:HEV. The range in which high engine efficiency is attained has been expanded and motor and battery control technology has been improved, creating benefits in diverse scenarios, not only during powerful acceleration. In situations where acceleration is gradual, EV drive continues for longer and the required torque can be produced at lower engine speeds, thereby keeping engine noise lower than road noise, contributing to a quiet and sophisticated cabin space.
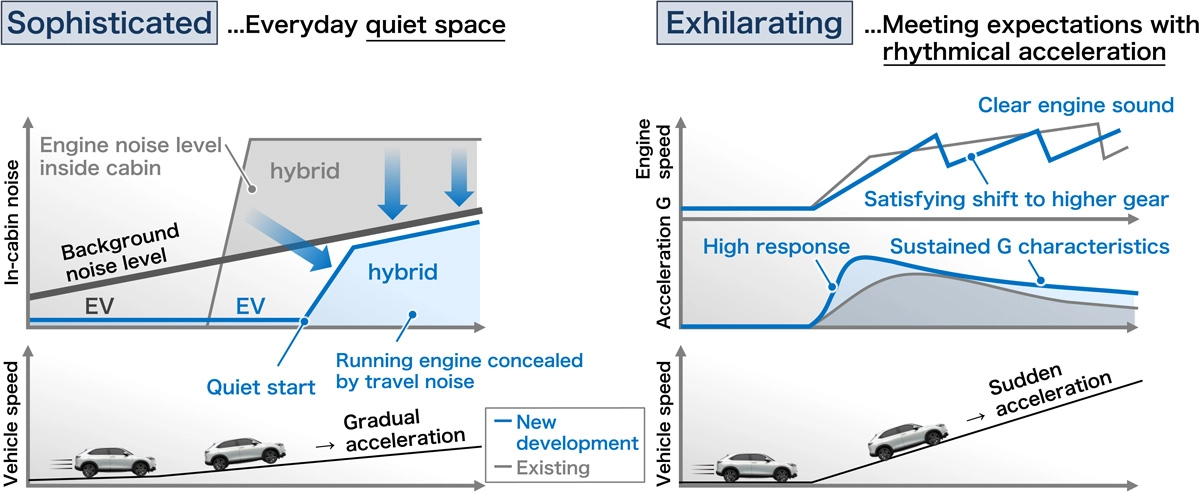
Next-Generation e:HEV System for Medium-Sized Models
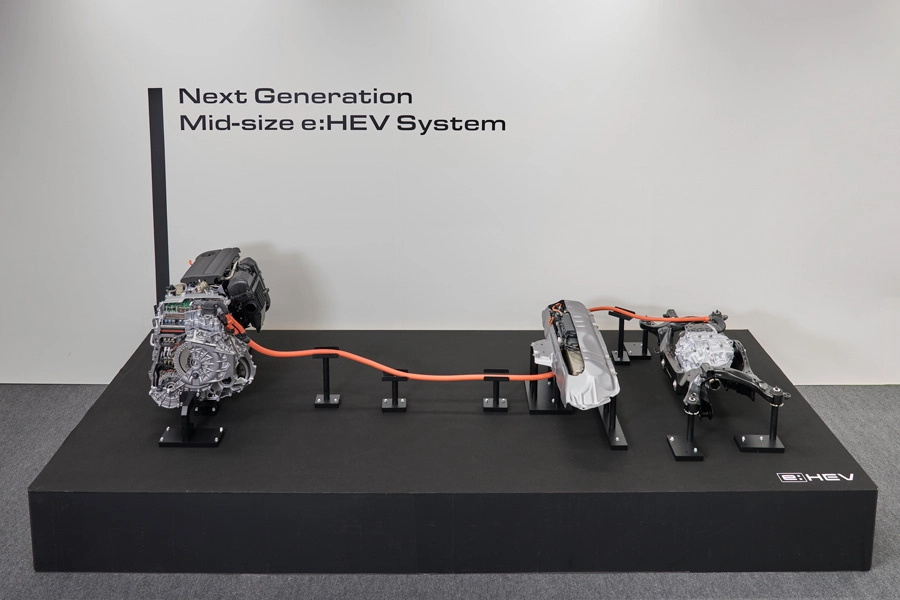
2.0-Liter Direct-Injection Atkinson-Cycle Engine
Honda has developed a new 2.0-liter direct-injection Atkinson-cycle engine compatible with Euro 7 and other international environmental regulations. The aim is to expand the range for high-efficiency combustion by 30% compared to 2018 models by realizing stoichiometric combustion across the engine’s entire operating range.
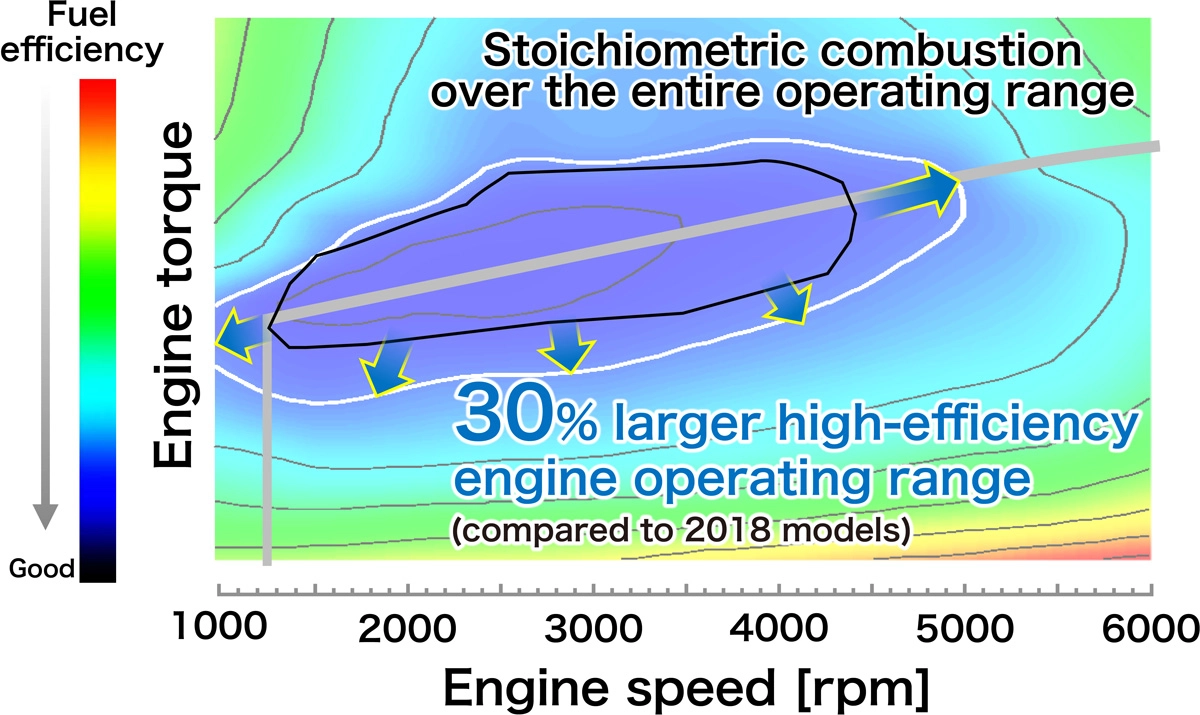
Rapid combustion is enabled by high-tumble intake ports that generate a strong tumbling airflow inside the cylinders, a new tumble-retaining piston design for retaining and strengthening the tumbling airflow, and a multi-stage high-pressure fuel injection system with up to four injections. This realizes improved combustion performance with a stoichiometric air–fuel ratio across the engine’s entire operating range while maintaining output. In addition, the rigidity of the engine structure and crankshaft has been optimized to prevent any increase in vibrations and noise as a result of rapid combustion, thereby achieving quietness together with output.
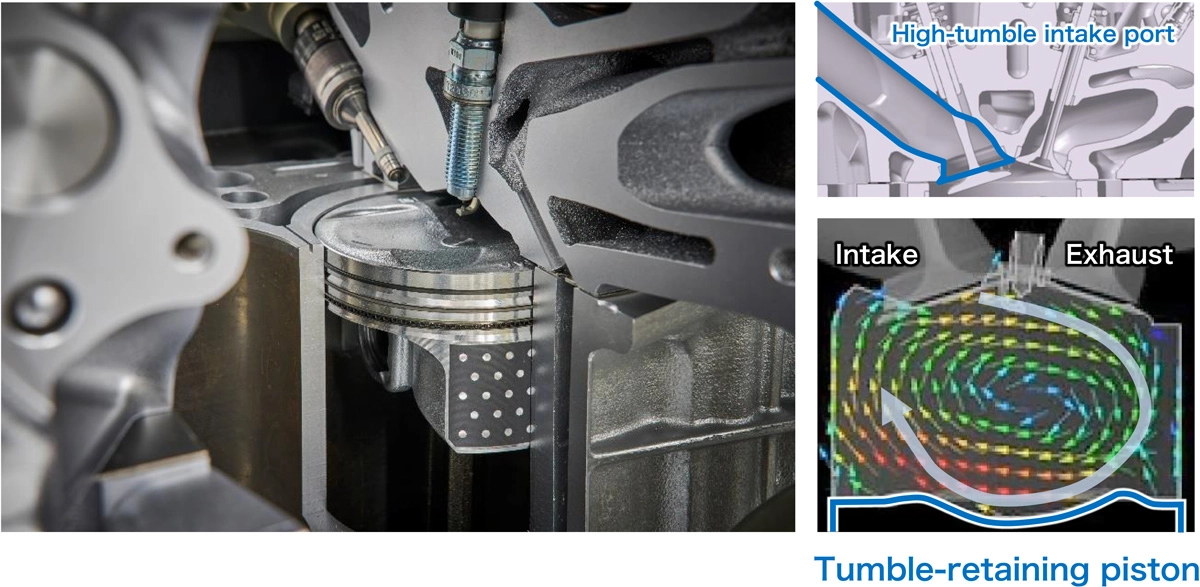
Front Drive Unit
Heightened efficiency and size reductions enhance the packaging efficiency of the drive unit comprising motor, transmission, and PCU.
The front drive unit of the medium-sized e:HEV system employs an electric CVT with two built-in motors arranged in parallel. With two-stage—high and low—gears directly connected to the engine, it ensures fuel efficiency and quietness during high-speed cruising, as well as towing performance.
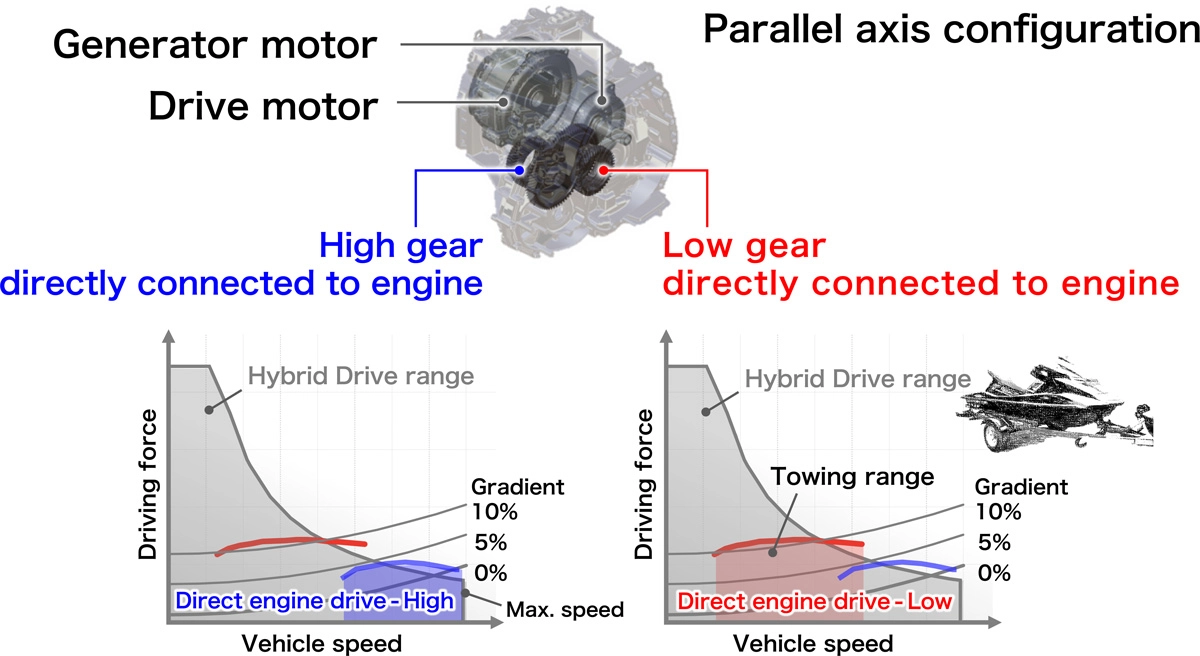
The torque density of the generator motor has been improved by optimizing magnet layout using topology optimization and by increasing the space factor of the stator coil through changes to the shape of insulating paper. The number of magnets has also been reduced. The drive motor’s torque density has been heightened with a new magnetic circuit design that employs magnets free of heavy rare earth elements and makes effective use of magnet torque and reluctance torque. This allows reductions in size and the number of magnets used.
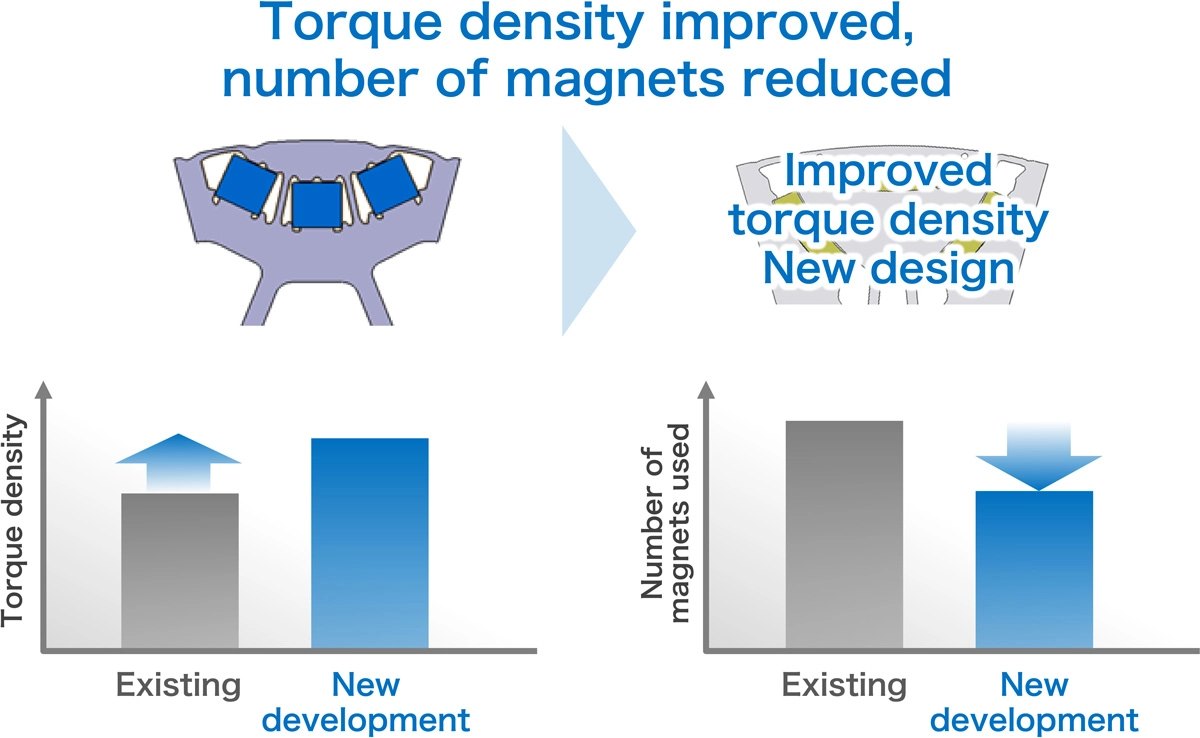
HEV oil cooling, using water as the coolant in place of air, is integrated into the power control unit (PCU) cooling system. The temperature of the HEV oil is controlled using a flow shutter valve to regulate the amount of coolant water fed into the HEV oil cooling system. When the HEV oil temperature is low, the temperature is regulated upward. This lowers the viscosity of the HEV oil, reducing friction, which helps to improve fuel efficiency.
*HEV oil: Transmission oil for use in HEVs.
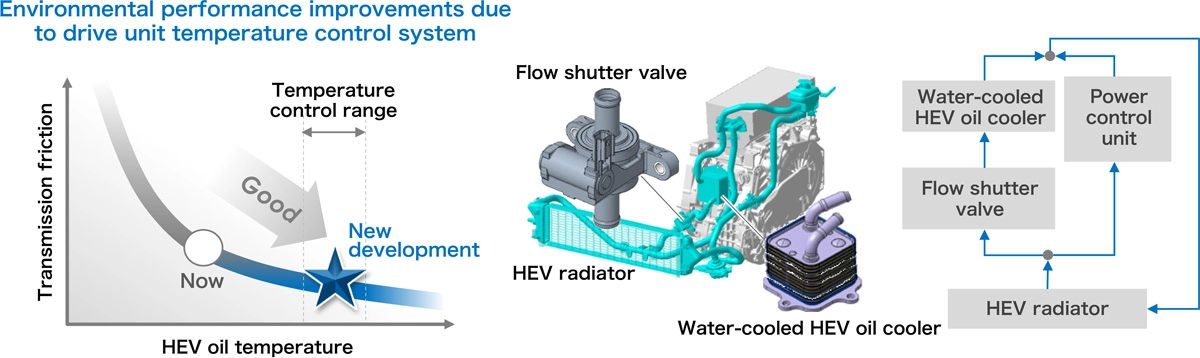
The PCU, which controls the two motors by converting between DC and AC power and stepping voltage up and down, has undergone size and cost reductions through application of direct-mount transmission technology employed since 2016. In addition, high-density packaging of the power module enables the internalization of the rear motor drive inverter, contributing to larger cargo spaces.
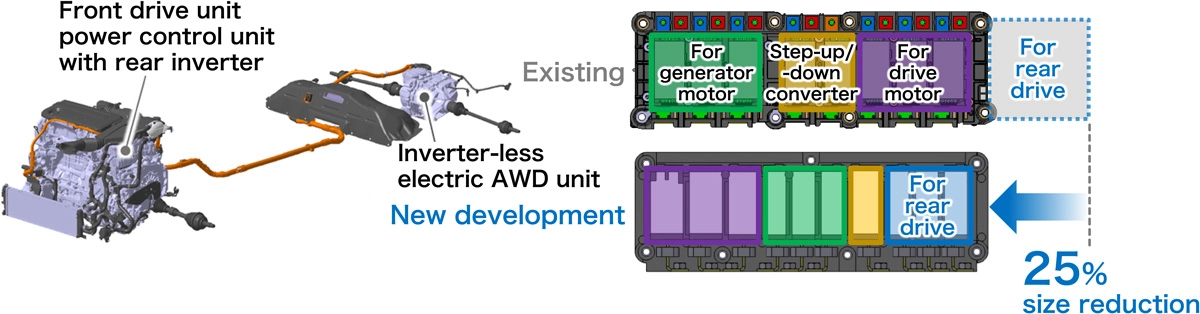
Battery Pack
Honda leveraged the advantages of developing its own battery packs to achieve functional integration with a vehicle’s structural components, reducing total height by 20% compared to battery packs located under the rear seat of current sedans. In SUVs, the use of electric AWD, which does not require a propeller shaft, enables shifting of the battery pack from under the cargo space, where it is now, to under the rear seat, contributing to a larger cargo space.
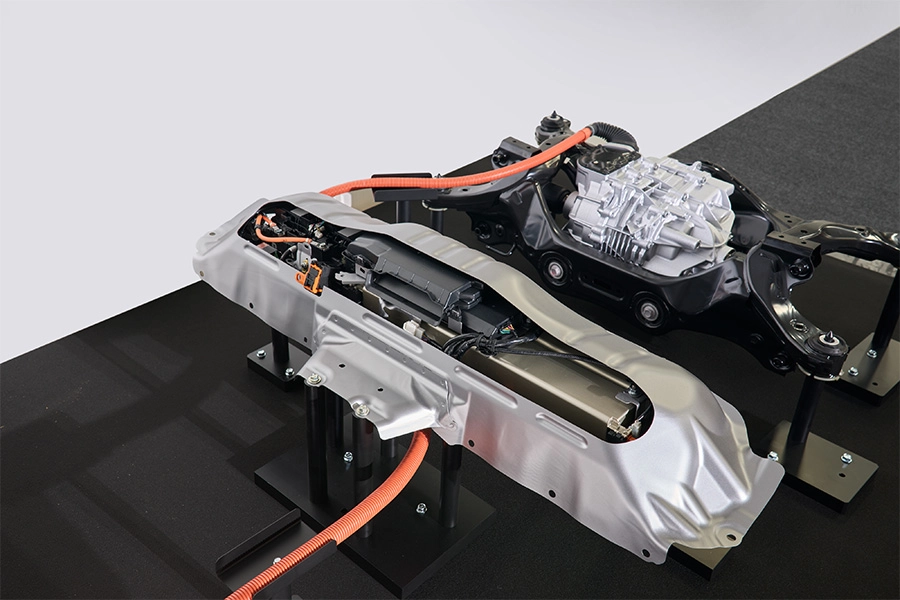
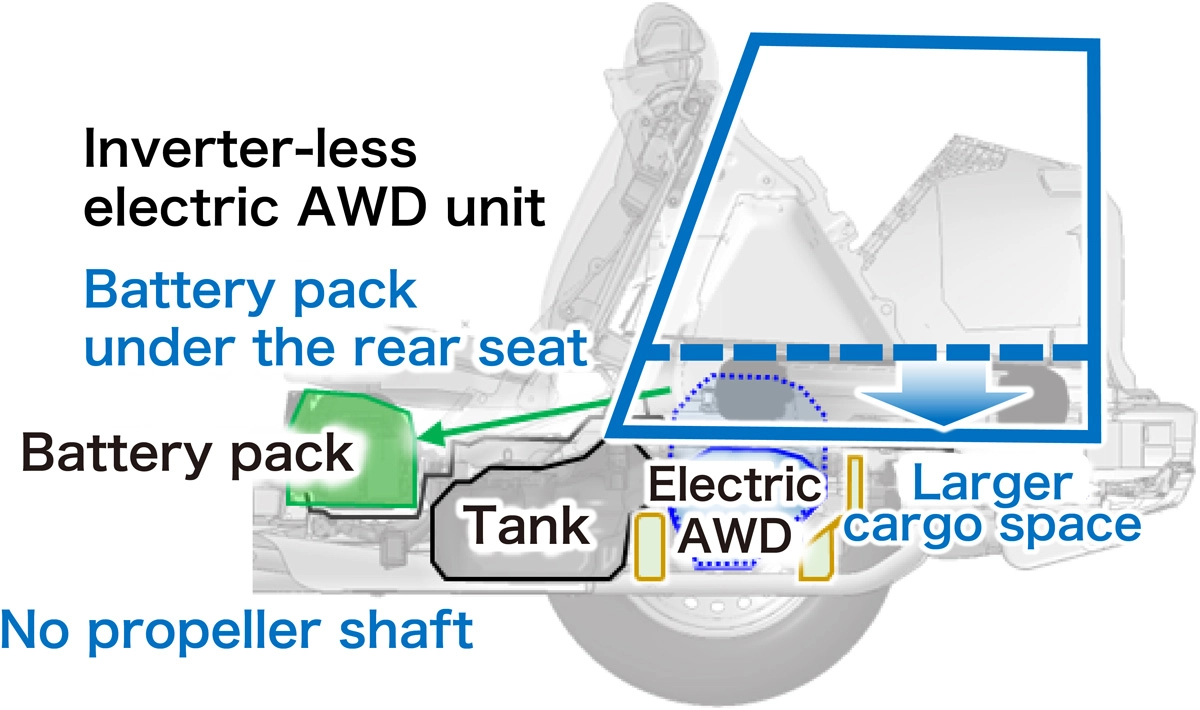
Despite the size reduction, output increases around 10% due to battery cell and control technology advancements.
Next-Generation e:HEV System for Small-Sized Models
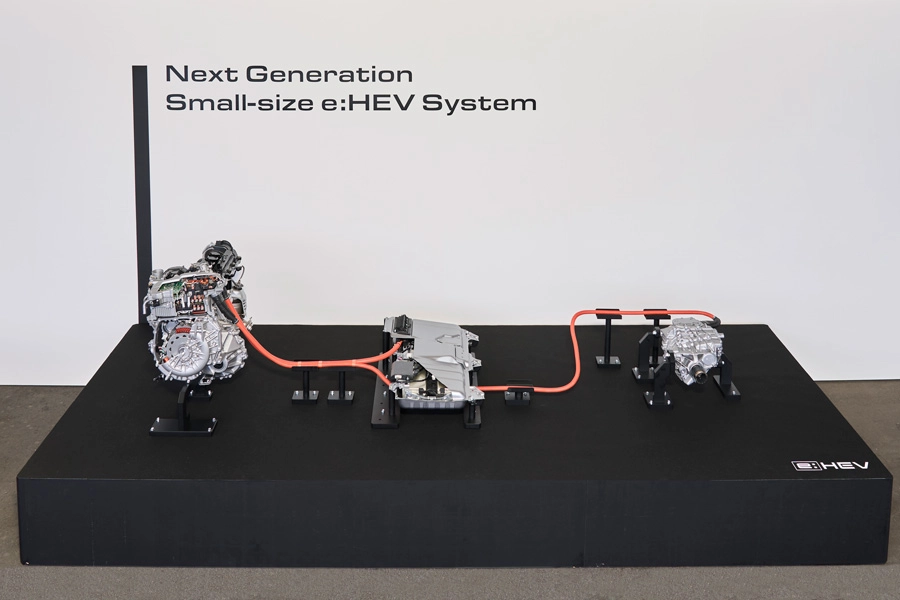
1.5-Liter Direct-Injection Atkinson-Cycle Engine
Honda developed a new 1.5-liter direct-injection Atkinson-cycle engine compatible with international environmental regulations. The aim is to improve output and environmental performance.
Applying combustion concepts that came to fruition with the 2.0-liter direct-injection engine, a direct injection system is adopted. Rapid combustion is realized using high-tumble intake ports and tumble-retaining pistons to heighten turbulence intensity, preventing knock. As a result, stoichiometric torque increases 40% even with enhanced fuel efficiency from achieving stoichiometric combustion across the engine’s entire operating range. To address the increased excitation force that results from rapid combustion, vibration and noise are suppressed by distributing the natural frequencies of engine structural components. For example, crankshaft bending rigidity is increased by 8%.
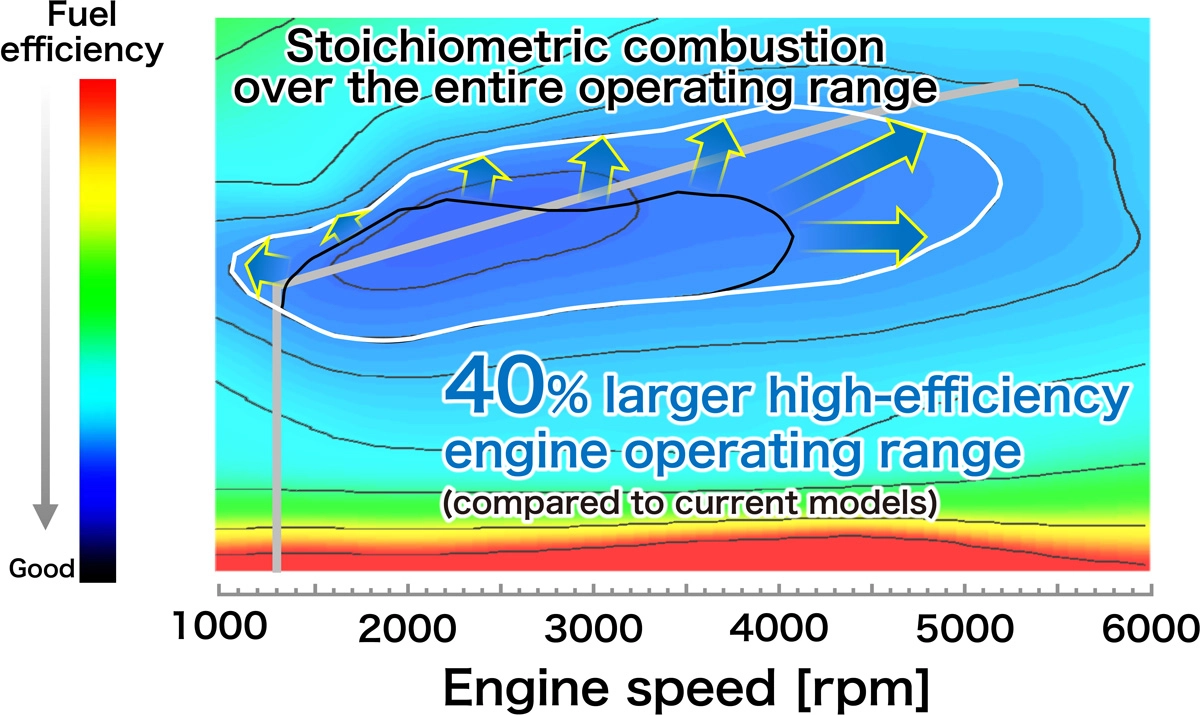
Front Drive Unit
The front drive unit of the small-sized e:HEV system employs an electric CVT with two built-in motors in coaxial arrangement. The generator motor has been made smaller and uses fewer magnets as the performance characteristics required to achieve the same level of output were optimized by increasing rotational speed. As with the medium-sized e:HEV system, the drive motor employs magnets free of heavy rare earth elements and a new magnetic circuit design increases torque density, enabling reduced size, a smaller number of magnets, and high efficiency.
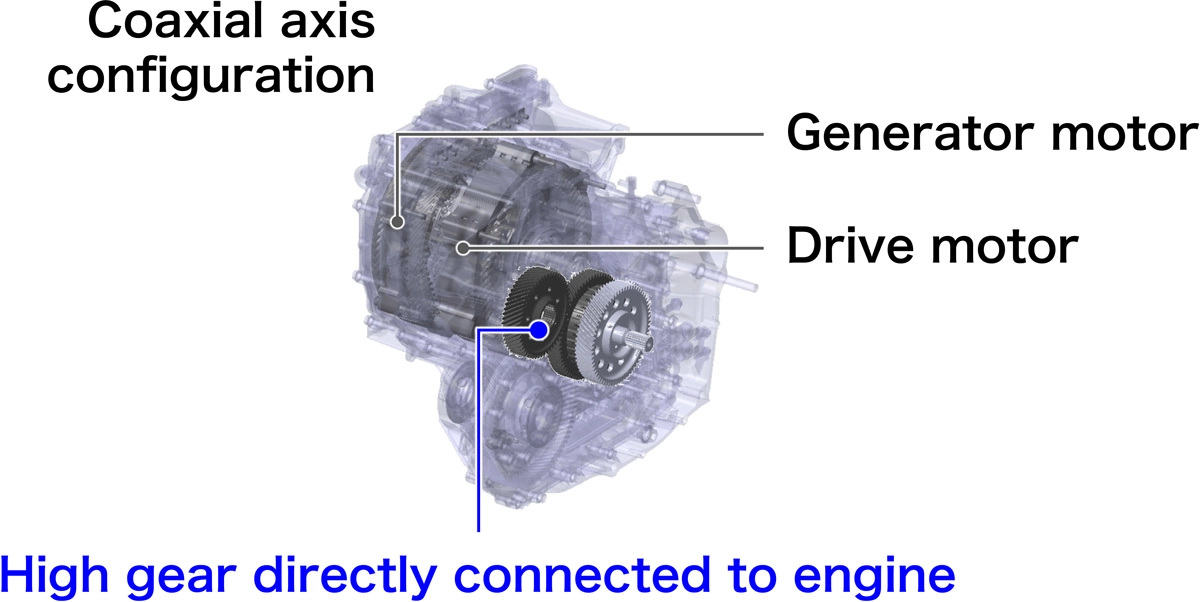
For the transmission, gear losses have been minimized through mirror finishing of the final drive gear. Together with the use of low-viscosity HEV oil, this contributes to low fuel consumption.
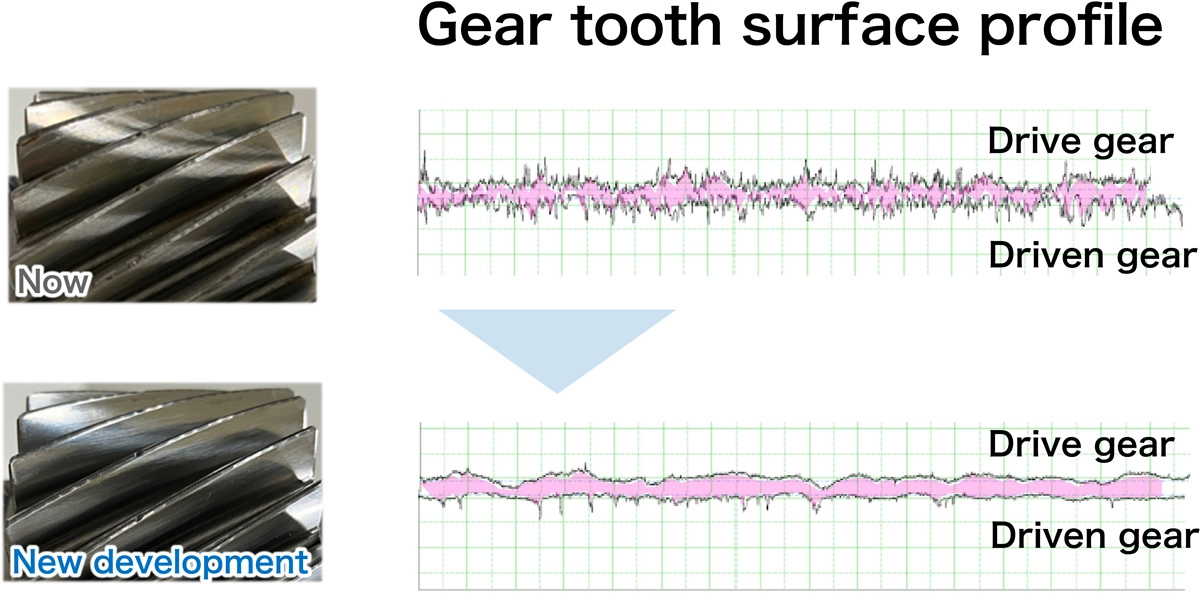
The PCU, which controls drive and generator motors, has been reduced in size, just like in the medium-sized e:HEV system. This enables mounting directly above the transmission even after incorporating the rear motor drive inverter, which contributes to larger cargo spaces.
Battery Pack
Besides reducing the size of the battery module, the total height of the battery pack was reduced by 20%—realizing Honda’s thinnest battery pack—through functional integration of the vehicle’s structural components, just like in the medium-sized e:HEV system. For example, structural components are made to function as a cover for the battery pack. These changes also enable shifting of the battery pack from under the cargo space, where it is now, to under the front seat, contributing to a larger cargo space.
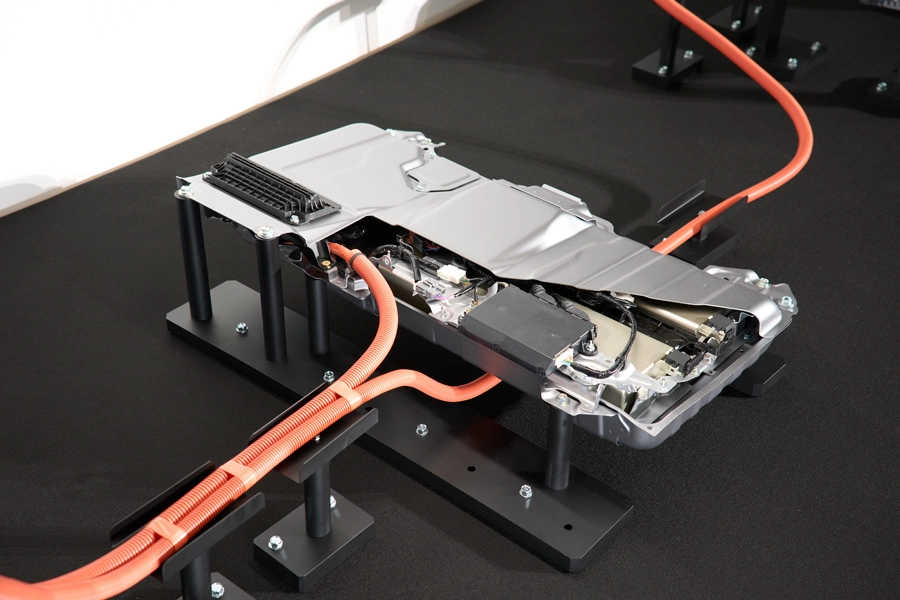
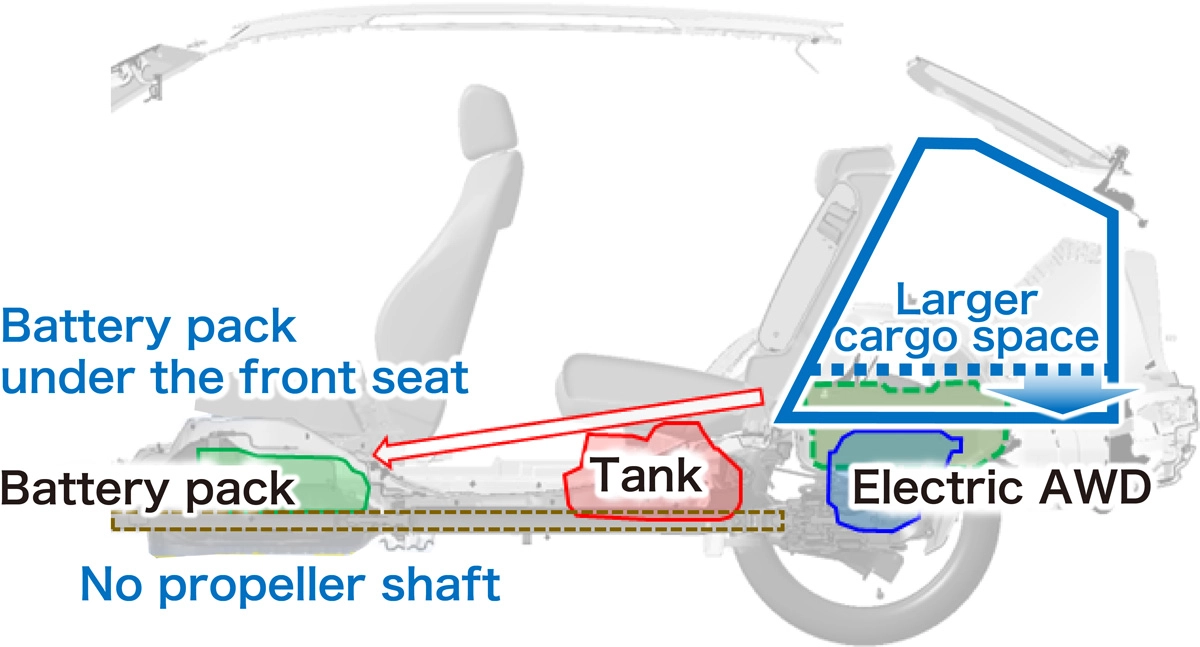
The battery pack employs a new generation of battery cells, realizing a 15% larger usable capacity despite the size reductions. The output level has also been maintained through control technology advancements.
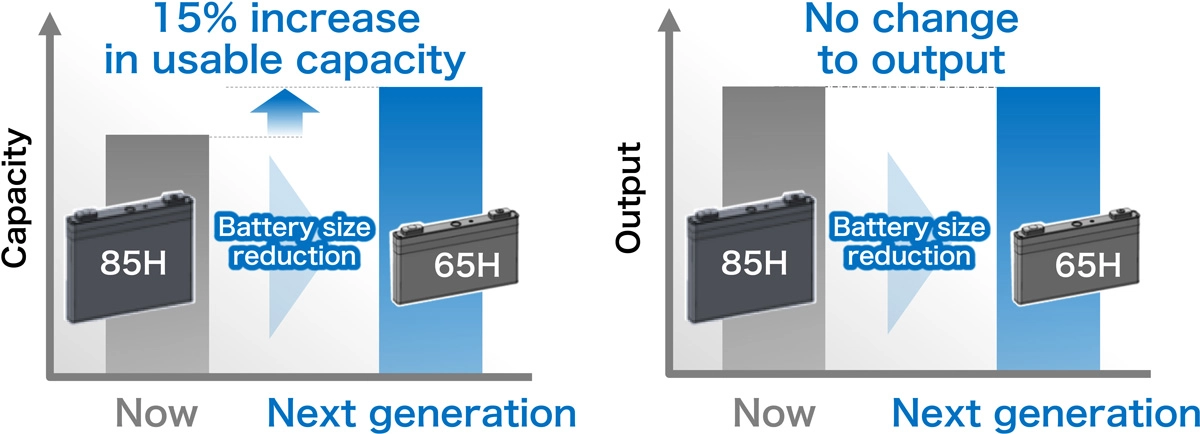
Electric AWD Systems
AWD System for Next-Generation Small-Sized Models
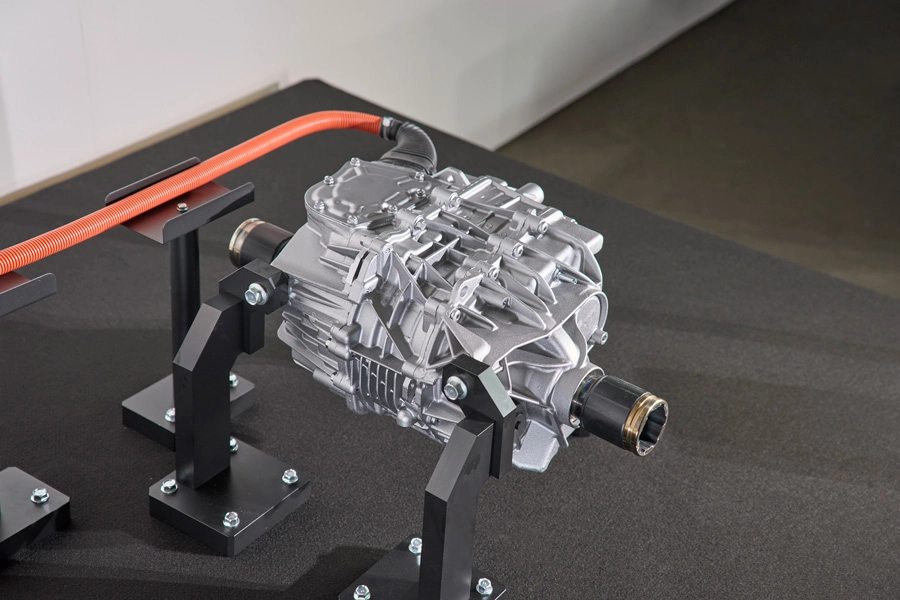
AWD System for Next-Generation Medium-Sized Models
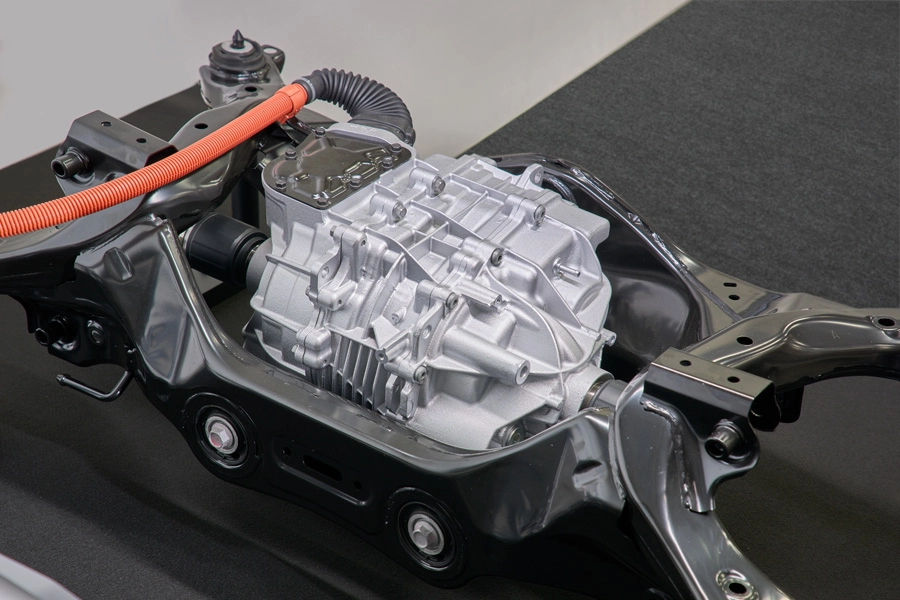
The AWD systems employ a 50-kilowatt-class unit compatible with up to medium-sized models. Leveraging the high precision and high response advantages of electric systems, the aim is to realize even better driving performance.
Front and rear driving force distribution control technology amassed through mechanical AWD system development has been further advanced for optimization of front-rear distribution according to the tire ground contact load. For example, distribution of driving force to the rear wheels increases during acceleration, when the rear wheel load increases. When turning, the ground contact load on the inside wheels decreases, so driving force is appropriately distributed while determining the grip limits on the inside wheels.
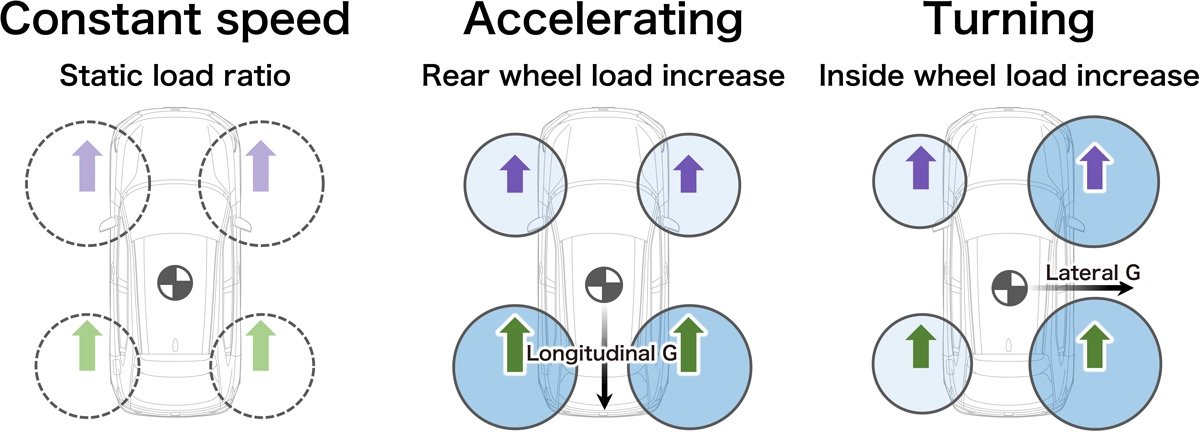
Fine control of tire slippage using high-precision and highly responsive motor torque control enhances the ability to follow a desired driving line, as well as handling stability, regardless of road surface conditions. At the beginning of a turn, distribution prioritizes steering response. Stability is prioritized mid-turn, and traction when exiting the turn. This enables driving at will.
Furthermore, adding extra driving force to the electric AWD depending on the situation delivers even more powerful acceleration performance.
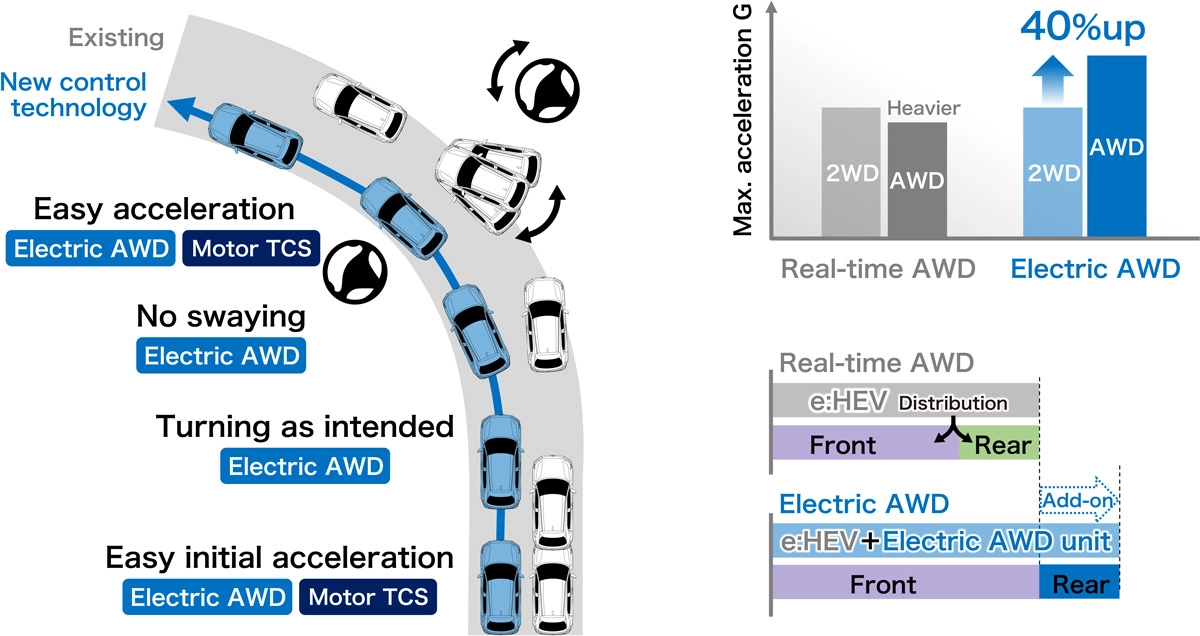
INDEX
TechnologyEvolution of the e:HEV Powertrain