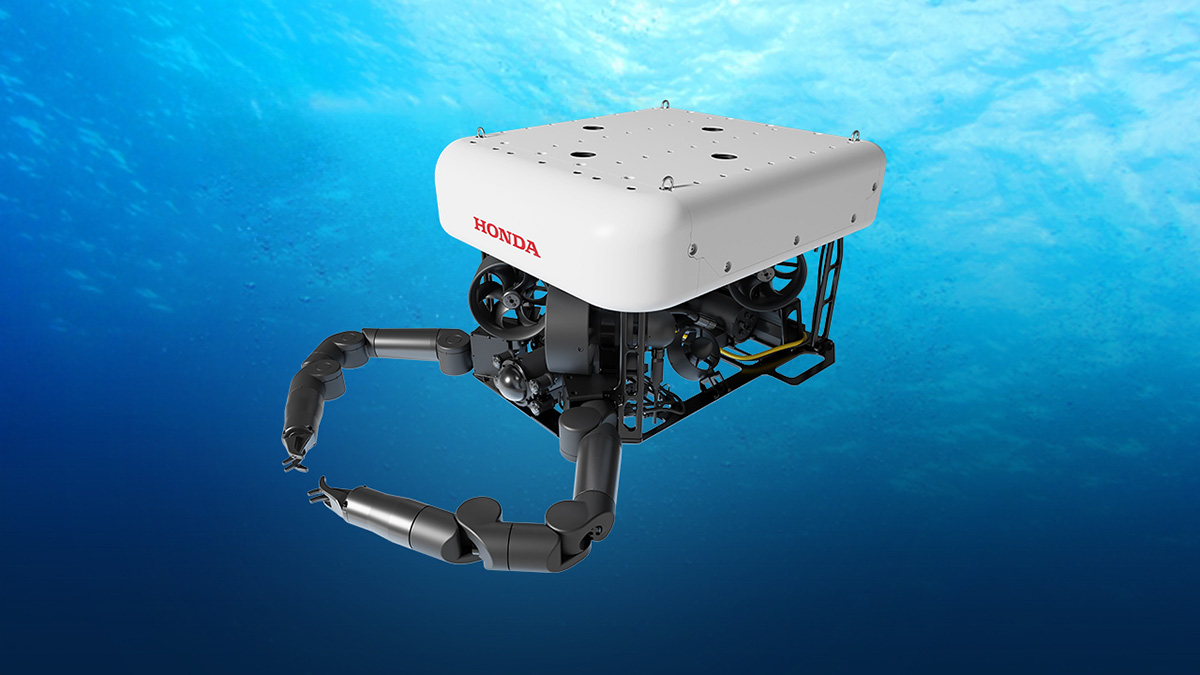
Honda aims to develop mobility for future generations by creating a joy and freedom of mobility that enables people to transcend the constraints of time and place, and augment their every possibility.
As part of these efforts, it is focusing on remotely operated vehicles (ROVs) to act as teleoperated unmanned underwater vehicles. The ROVs would be used in marine environments to conduct maintenance and other work for offshore wind power generation, which is expected to contribute toward carbon neutrality going forward. Through research and development in this area, Honda aims to help realize functions and services that are more user-friendly.
ROV development based on Honda robotics technologies
Offshore power generation is currently attracting attention as an important and growing business area that will help achieve carbon neutrality. One of the challenging aspects of this business is the difficulty of working underwater, which is essential for operating such facilities.
For many years, Honda has been conducting research and development of robotics from two main directions. The first is maximization of the value of time, which enables people to transcend the constraints of time and distance and put their skills to use anytime and anywhere. The second is augmentation of physical capability, which enables people to work in environments that are too harsh for humans and to do work that is too difficult for humans. Considering these robotics technologies to be perfect for the challenge of underwater work, Honda decided to focus on ROVs for operation and maintenance of facilities of offshore wind power generation projects, as an area that could take advantage of Honda’s core technologies.
By developing an ROV that capitalizes on its strengths, Honda hopes to improve the efficiency of offshore wind power generation to coincide with the start of domestic offshore wind power generation toward the end of the 2020s. In this way, it hopes to become a useful partner in carbon neutral initiatives for society.
Vision for Honda robotics
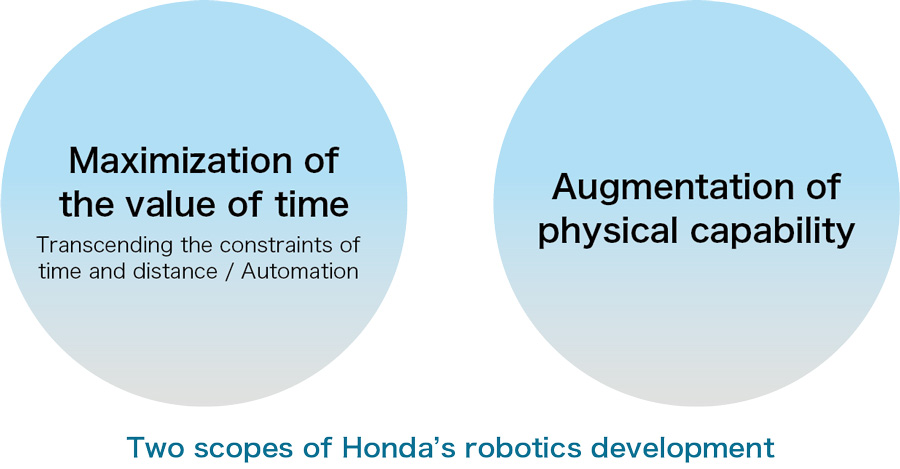
Challenges of underwater work
Offshore wind power generation is under the spotlight as a more powerful and stable source of energy compared to onshore wind power generation. Offshore facilities are often located in areas with stronger winds and where larger wind turbines can be installed. Due to ease of installation, offshore wind power generation facilities were initially constructed by fixing them to the seabed, with the generation facility support structure embedded in the sea floor. However, this method limited the areas for installation as it is only possible in shallow seas. To enable installation of offshore wind power generation facilities in more locations, installing the facilities on floating structures anchored to the seabed will be essential going forward.
Different types of offshore wind power generation
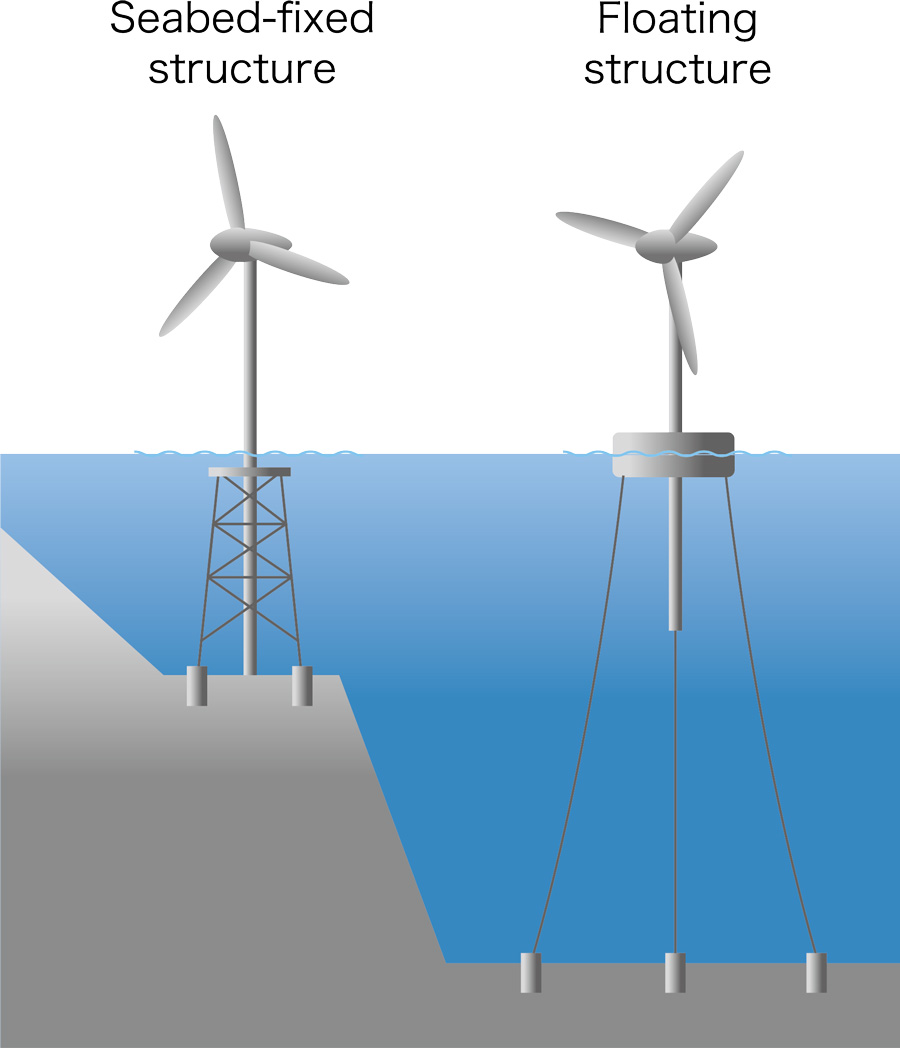
In any case, the underwater structures of offshore wind power generation facilities requires regular maintenance and other work, which is currently performed by ROVs and divers. With divers always in short supply, there will not be enough divers to do the work in the future as the number of facilities increases. Also, the depth of floating facility installation points may preclude the use of divers anyway.
ROV work is expected to include attachment and removal of shackles, and cleaning by removal of organisms attached to the underwater structures when conducting inspections. However, research suggests that currently available ROVs still have room for improvement in terms of work efficiency.
Illustrations of ROV work
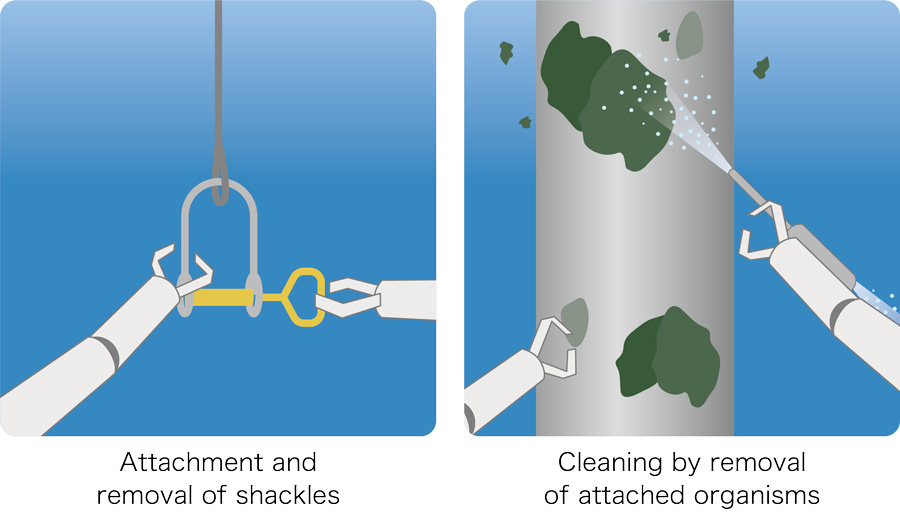
Features and technologies of the Honda ROV concept model
System overview
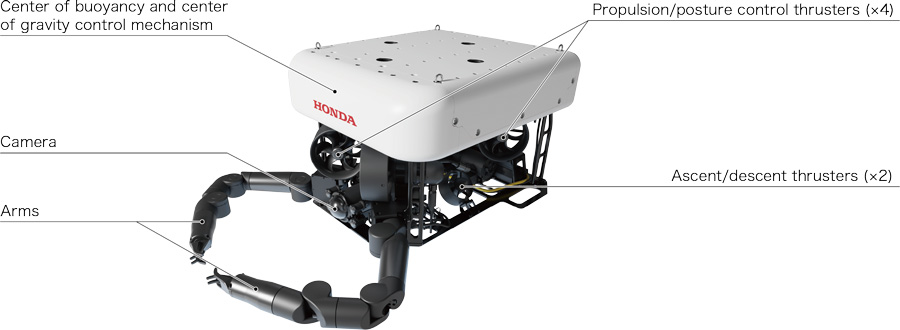
(1) Manipulator/ROV cooperative control facilitates operation through cooperative control of the ROV body and arms
One challenge for current ROVs with arm attachments, which conduct maintenance and other work for offshore wind power generation facilities, is that the body and arms are operated separately. As the ROV approaches its target and the arms are extended, the ocean current may move objects around, so sophisticated operation may be required depending on the current.
Given this issue, Honda is using robotics technologies from its ASIMO humanoid robot to develop an ROV with dramatically improved operability. Honda has accumulated expertise in the reproduction of human functions through engineering to achieve more human-like movement for ASIMO. One of the outcomes of this development is the arm/body cooperative control technology used by Honda’s muscle model for gripping objects. When extending a hand, the body automatically moves forward and twists with the hand movement in a forward-leaning upper body action to grip the object. Honda is applying this technology to the development of its manipulator/ROV cooperative control to integrate control of the ROV body and arm.
Arm/body cooperative control employed by ASIMO
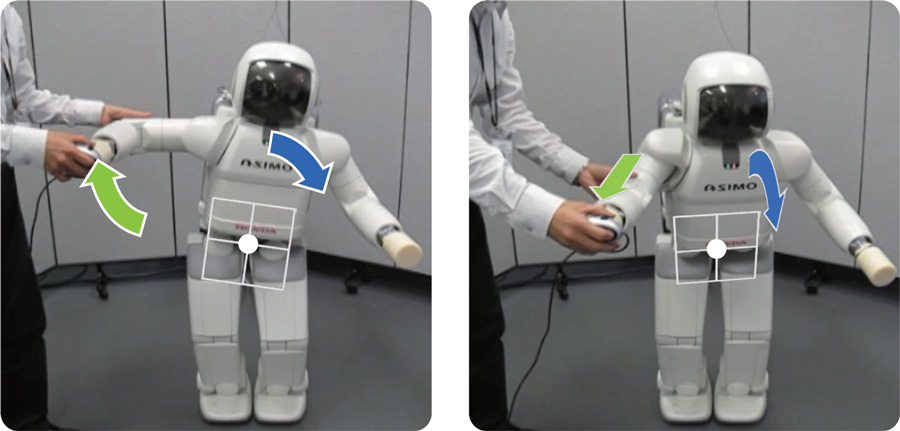
Upper body moves automatically in response to external force to lift the arm or pull it forward
While the ROV body will remain unresponsive within a certain dead zone even if an arm is moved, this technology will control the body position in response to any arm movement beyond this zone. Measuring ROV position (device speed relative to the seabed) with a Doppler velocity log (DVL) measurement system that applies the acoustic Doppler effect, and measuring ROV posture with an inertial measurement unit (IMU), the position and posture of the ROV body can be automatically controlled in response to movement of the arms.
This technology makes operation much simpler because the ROV body will move forward automatically, and posture will be adjusted, to reach the target just by extending the arms forward.
Honda is also working to apply the ASIMO technology to prevent movement of the ROV hands even when the body is moved around by the water current.
In this way, the company is hoping to improve the efficiency of cleaning organisms from structures, which includes enabling cleaning nozzles to be held at a fixed distance from objects while moving side to side.
Illustration of manipulator/ROV cooperative control
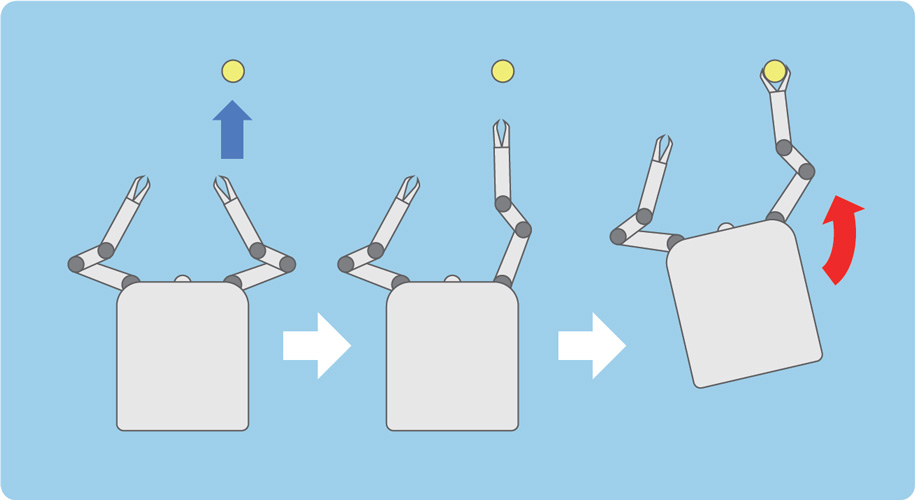
ROV body moves forward automatically just by extending an arm toward an object
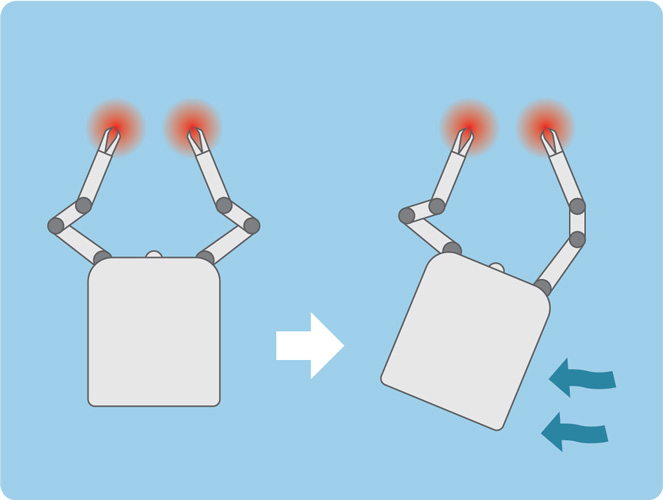
ROV hand position stays the same even when the body is moved around by the water current
Images of arms performing work
Image from external camera
Image from onboard camera
(2) Center of buoyancy and center of gravity control mechanism controls ROV posture by moving buoyancy material forward, backward, left, and right
In addition to the always unstable and changing posture of an ROV in water, the ROV body may lean when moving arms due to the shifting center of gravity, and body posture may be disturbed by water currents, which requires constant posture control.
Currently available ROVs make continual use of thrusters to hover the unit in the manner of a person treading water, and to control its posture. However, it takes some time between a thruster starting to operate and the control taking effect, and the mismatch between intended and actual movement makes operation difficult. The flow of water through the thrusters can also reduce visibility as sediment on the seabed is disturbed.
With this in mind, Honda developed a center of buoyancy and center of gravity control mechanism to control ROV posture. Together with thruster-based posture control, this mechanism moves buoyancy material, installed in the upper part of the ROV body, forward, backward, left, and right to maintain control. The center of buoyancy can be moved by shifting the buoyancy material in accordance with data obtained, including calculations of how far the center of gravity is moved in response to how far the arms are moved, and changes in posture as sensed by the IMU. Posture can then be controlled within certain limits, including maintaining an even keel or bending forward, by using the restoring force generated through a difference between the center of buoyancy and center of gravity. The result is posture control that is energy efficient and more responsive than using thrusters alone.
Also, with the buoyancy material enclosed in a case, the ROV construction makes damage to the equipment unlikely even if the unit strikes an obstacle.
Illustration of the center of buoyancy and center of gravity control mechanism in operation
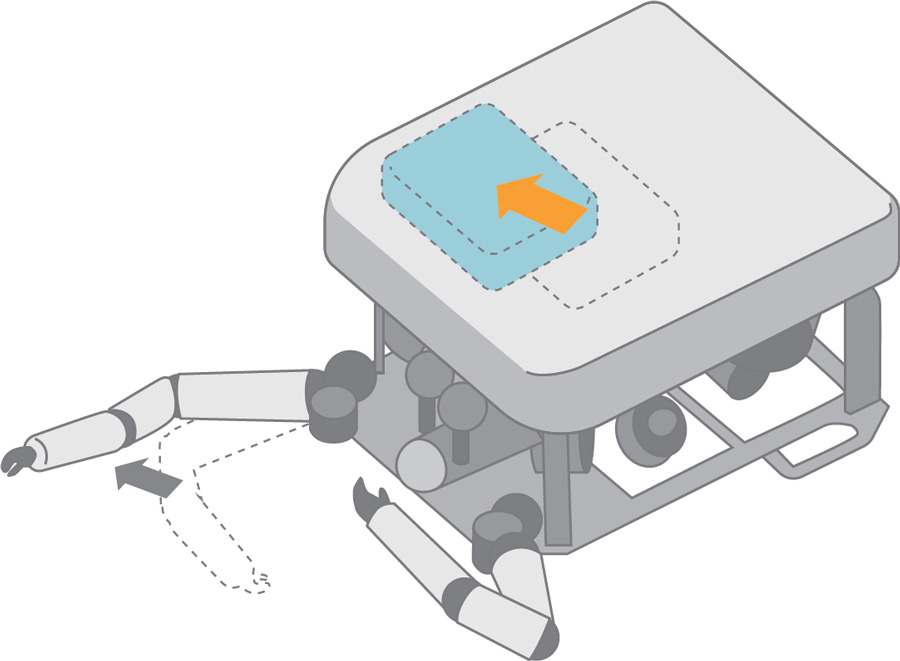
ROV body posture correction in response to arm movement
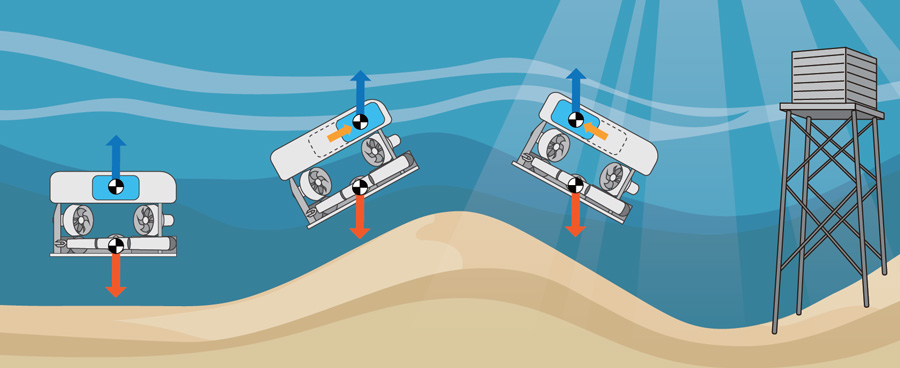
ROV body posture changes according to the topography of the seabed even without the use of thrusters
Effect of using the center of buoyancy and center of gravity control mechanism (comparison between active and inactive states)
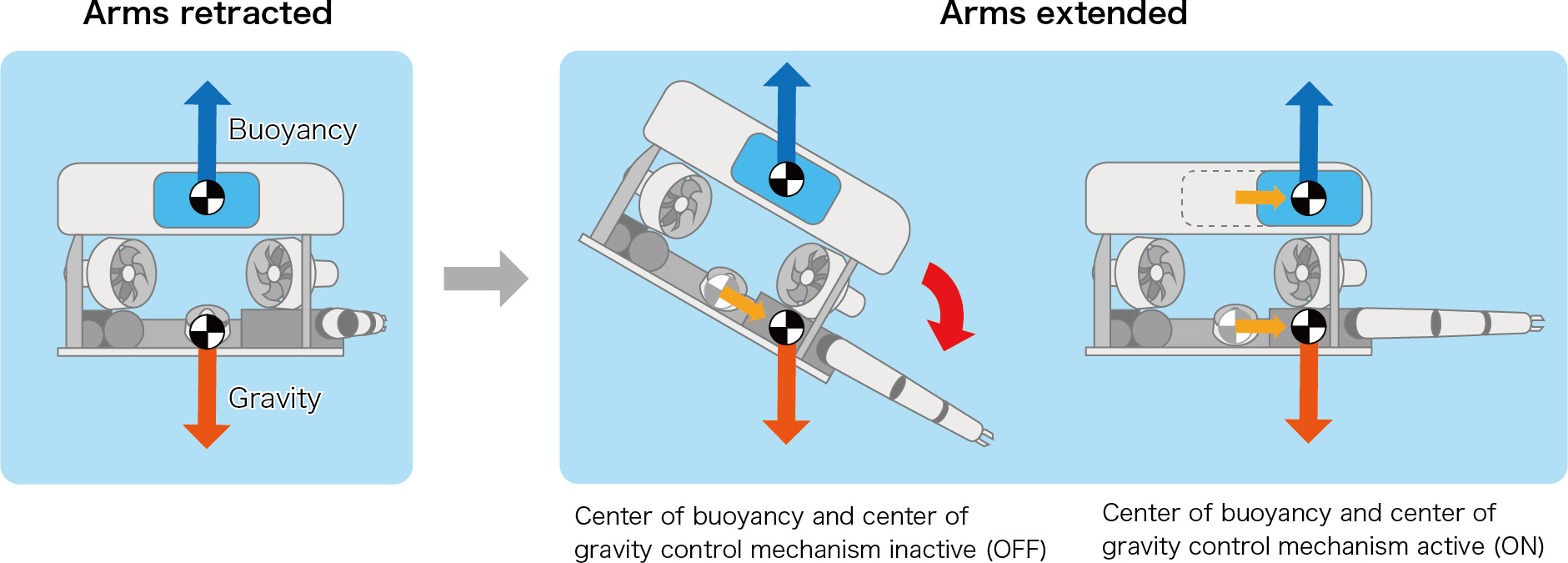
Center of buoyancy and center of gravity control mechanism inactive (OFF)
Center of buoyancy and center of gravity control mechanism active (ON)
(3) Compact, low fluid-resistance body shape improves performance in water currents
Achieving stable ROV operations even in fast-moving water currents requires dynamic performance able to withstand the currents and a body that is largely unaffected by the currents. However, using high output motors to generate sufficient propulsive force from the thrusters means the body becomes larger and more power is consumed.
With an emphasis on greater ease of operation, Honda developed a low fluid-resistance body shape that reduces resistance from water currents to achieve sufficient dynamic performance in the ROV while being operated with portable generators (5.5 kVA) that can be mounted on small boats.
Leveraging aerodynamic technologies cultivated through automobile development, Honda is working to achieve a cruising speed 0.5 knots even against a water current of 2.0 knots*, and a posture that resists disturbance through a compact, low-resistance body.
* 1 knot = 1.852 kilometers/hour
Low fluid-resistance mechanism
ROVs are generally box-like structures, with arms and other protruding auxiliary equipment resulting in a shape that is susceptible to fluid resistance.
Honda’s ROV, on the other hand, has been developed with a center of buoyancy and center of gravity control mechanism enclosed in a case, shaped to reduce resistance, at the top of the body. It also has the complex-shaped auxiliary equipment, designed to minimize protrusions, located together at the bottom of the body to reduce projected area in all directions.
Illustration of fluid simulations
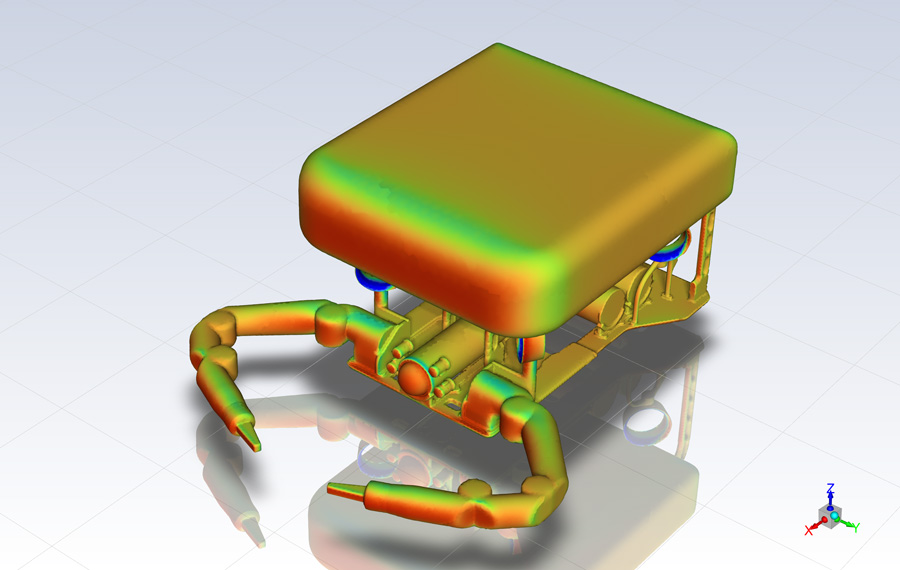
Image of pressure exerted on the ROV when moving forward underwater, with the redder areas indicating higher pressure
Ocean simulation tank testing
Image supplied by West Japan Fluid Engineering Laboratory Co., Ltd.