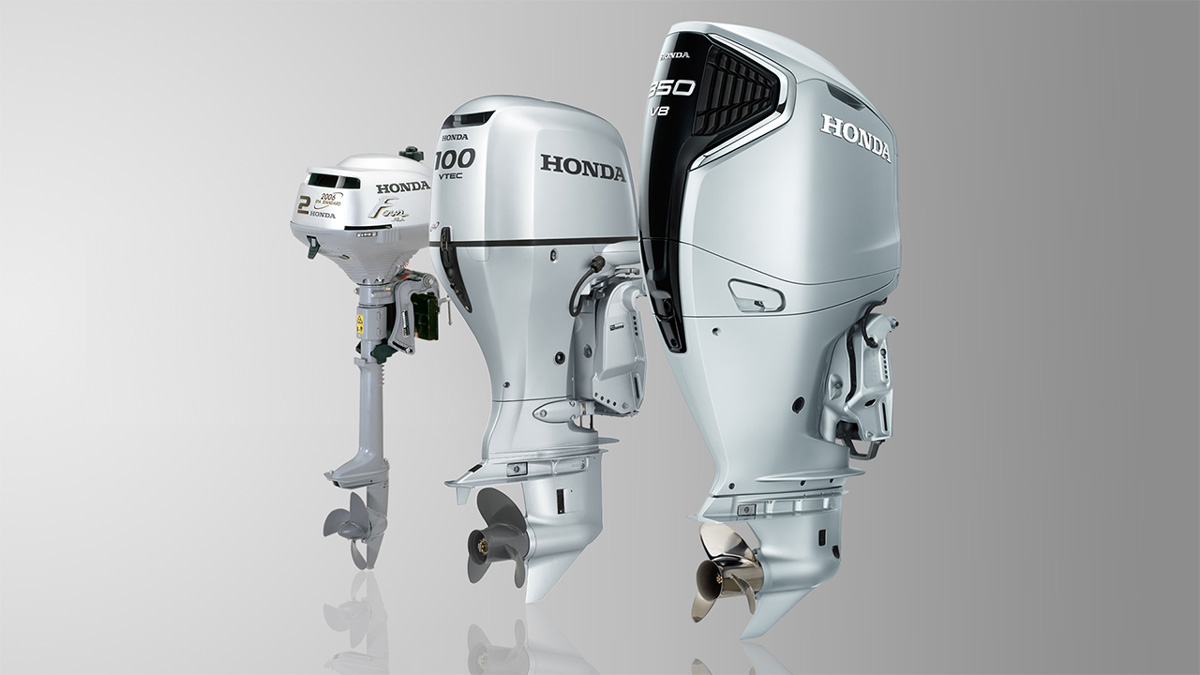
In line with the philosophy of founder Soichiro Honda that “watercraft should not pollute the waters they ply,” Honda has consistently pursued the development of outboard motors with low environmental impact. While two-stroke outboard motors were the norm for many years, Honda worked tirelessly in global markets to sell four-stroke outboard motors that were hampered by higher weights and costs. With four-stroke motors now mainstream due to a swing toward environmental conservation, the company is leveraging its strengths as a power unit manufacturer to focus on developing outboard motors with outstanding environmental performance, quality, and durability.
Inheriting the DNA of Honda Marine, with a 50-Plus-Year Commitment to the Environment
Offering outboard motors equipped with general-purpose four-stroke engines, Honda entered the marine market in 1964, when the majority of outboard motors used two-stroke engines because of their light weight and low-cost production. Honda’s strong commitment to the environment was behind its decision to use four-stroke engines that other companies had totally ignored. The main problem with two-stroke motors was that they had a considerable impact on the marine environment because, due to the structure of outboard motors, they discharged oil together with exhaust gas directly into the water.
While other companies continued making their two-stroke engines, Honda worked independently to evolve its four-stroke engines, which in the process gained popularity for outstanding levels of cleanliness, fuel efficiency, quietness, and durability.
In 1993, Europe issued the Bodensee Regulations concerning emissions from outboard motors. Despite the European regulations being considered the harshest globally at the time, Honda’s outboard motors were thrust into the limelight when they all met the requirements. Triggered by the Bodensee Regulations, four-stroke engines replaced two-stroke as the mainstream option from the mid-1990s.
With outboard motors becoming more high performance, Honda was able to use its experience with automobile development to equip its outboard motors with Variable Valve Timing and Lift Electronic Control (VTEC), Programmed Fuel Injection (PGM-FI), and other advanced technologies. As a result, Honda’s environmentally friendly, high-performance outboard motors are now in use all around the world.
History of Honda Outboard MotorsScroll right for more information
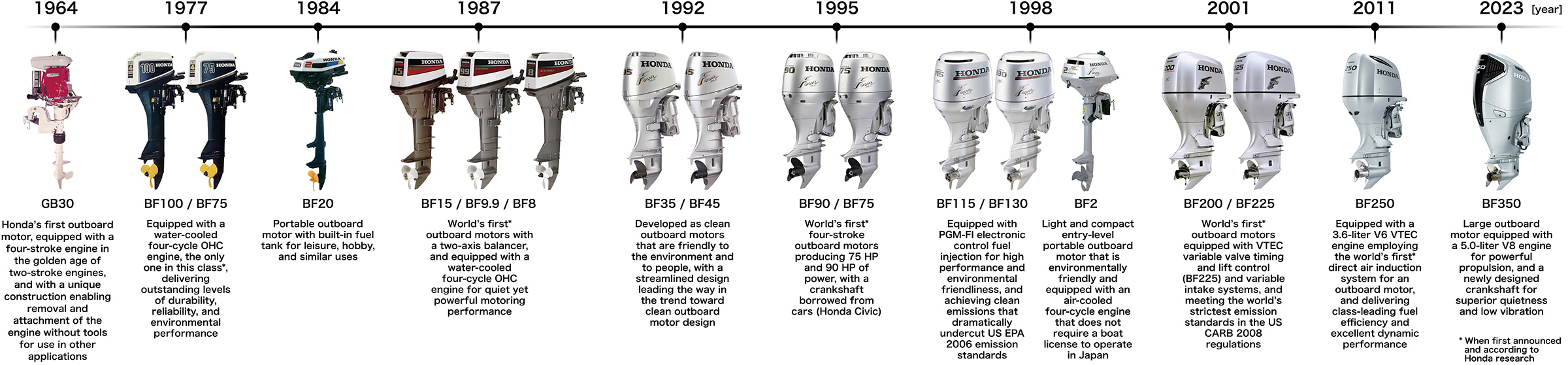
Environmental Performance, Durability, and Reliability Make Honda Outboard Motors the Choice of Professionals
From the outset, Honda’s four-stroke engines gained popularity for ease-of-handling at low speeds, low noise, low vibration, and fuel efficiency, resulting in widespread use by professionals in fishing and other industries. They have also been seen more frequently over recent years in applications such as coast guard patrol boats and high-speed tourism boats.
Due to the high resistance of boats in water, outboard motor engines are regularly operated at high speeds of 5,000–6,000 rpm. Also, unlike cars, boats do not come with brakes, so reverse gear is used to reverse the propeller rotation to slow or stop the boat. Using the motors this way is common in professional use due to the heavy loads carried, so high propulsive force, braking performance, durability, and reliability are required.
As the leader in four-stroke outboard motors, Honda has continued to pursue industry-leading technologies while marinizing its car engines. From propulsive force to braking performance, and fuel efficiency achieved through high-precision lean-burn control, it has established a reputation for outboard motors that are friendly to both the environment and to people.
Basic Structure of Outboard Motors
The general structure of an outboard motor consists of an engine, drive shaft, and propeller, with power from the engine transmitted via the drive shaft to the propeller to generate propulsive force. A clutch shifter is used to select forward or reverse bevel gears to impart forward or reverse rotation to the propeller.
Apart from a portion of small outboard motors, outboard motor engines are water cooled. Unlike cars and motorcycles that use coolant to indirectly cool the engines, they draw in outside water from intakes close to the gearcase to directly cool the engines. Surfaces of cooling channels therefore need to be corrosion resistant, so they are treated to prevent corrosion by salt water and other elements.
Outboard motors also employ a peculiar exhaust system, with exhaust gas from the exhaust manifold being cooled by used engine cooling water and discharged underwater, with that cooling water, from the middle of the propeller.
Basic Structure of Outboard Motors
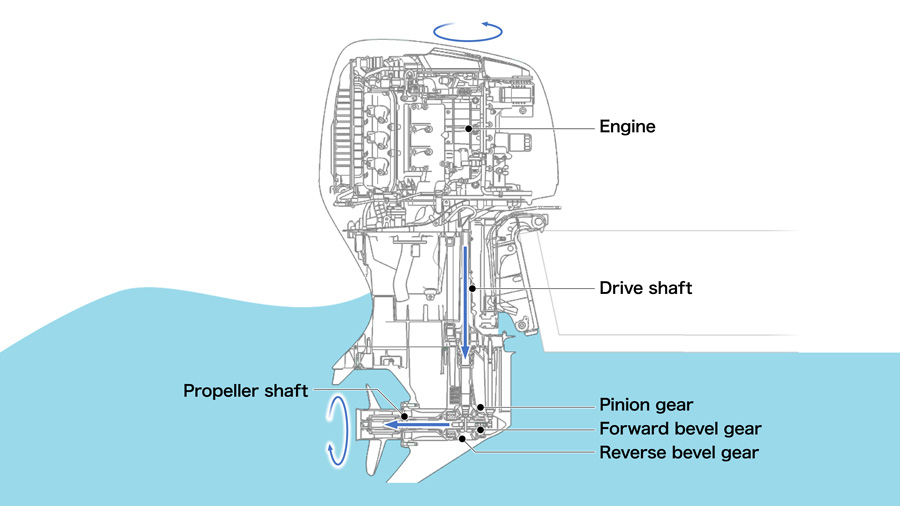
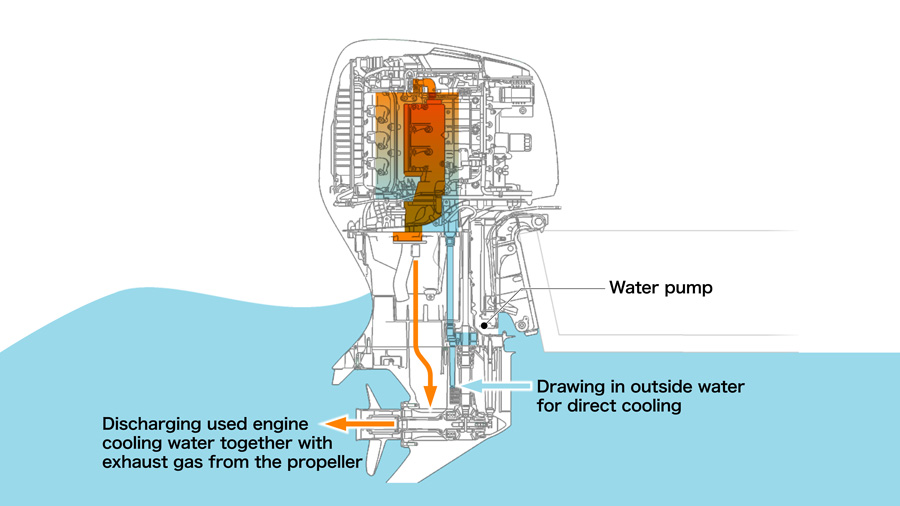
Anti-corrosion measures are important for outboard motors because they are used on the water, and aluminum parts in particular, that are often used on outboard motors, corrode easily in salt water. When aluminum comes into contact with materials that have an electric potential difference in the presence of an electrolyte (salt water) to form an electric circuit, a current flows that corrodes the aluminum. To protect aluminum parts from this process called electrolytic corrosion, outboard motors are equipped with anode metals that act as sacrificial metal. The electrical properties of anode metals mean that they corrode instead of the aluminum parts, which requires them to be regularly replaced to protect the outboard motor from corrosion.
Anode Metals Arrangement
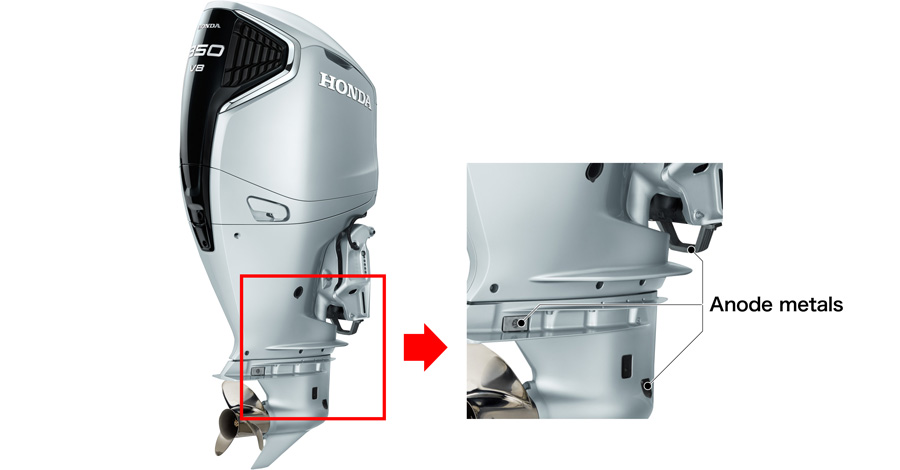
Unique Honda Marinization: Optimizing Car Engines
Honda has utilized the established performance and reliability of its car engine technologies to develop high-performance outboard motors. From its first use of car engine crankshafts and connecting rods on the BF75 and BF90 outboard motors launched in 1995, it has expanded use of common parts to now include valve trains and balancer mechanisms on the BF115 and BF130. From the BF225, it was also able to employ VTEC and variable intake systems for the first time on an outboard motor.
In the process of marinizing its car engines, Honda had to change its lubrication system to enable the crankshaft to be vertically mounted in outboard motors. While sharing the oil lines of car engines, from the main oil gallery to the main driving system and valve train, the outboard motors use a unique oil return line to the oil case together with the addition of cam chain oil jets and optimized piston rings.
For the cooling system, anti-corrosion measures are implemented throughout the cooling water channels due to the intake of outside water for direct cooling. The water is preheated, and temperature stabilized, by the proximity of the intakes to the exhaust channel, which ensures a balanced cooling effect between cylinders. The uppermost cylinder has a tendency to be hotter than the other cylinders, so a thermostat is located close to the uppermost cylinder to prevent overheating. A water jacket is also provided for the exhaust manifold to help cool the exhaust gas.
Main Changes to the Lubrication System
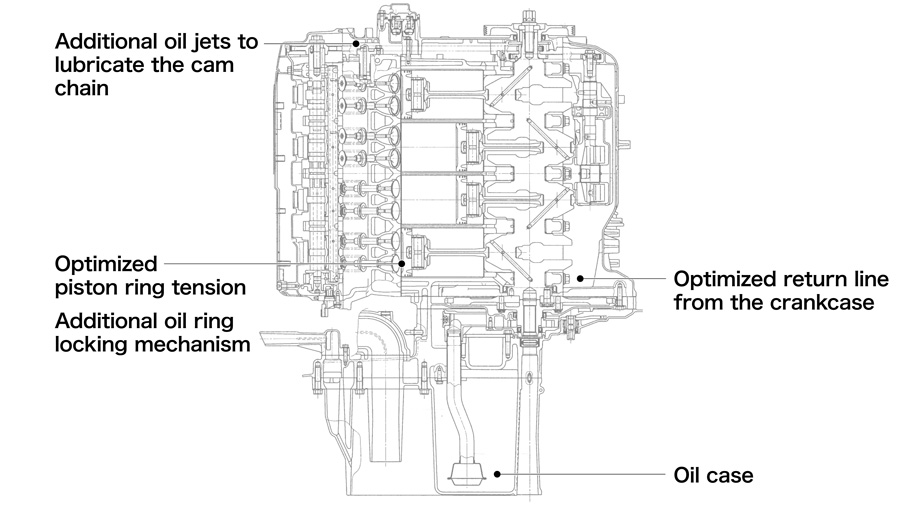
Main Changes to the Cooling System
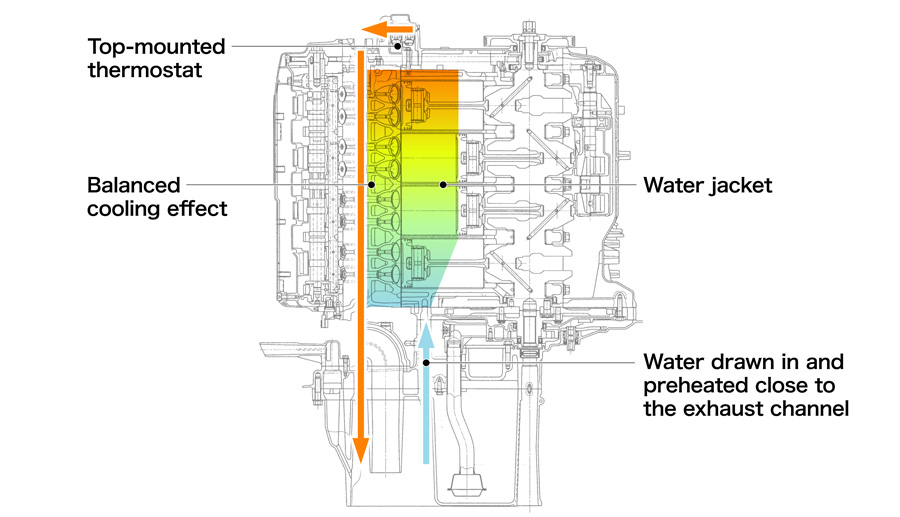
Four Key Technologies Underpinning Honda’s Outboard Motors
Economy Controlled Motor (ECOmo): Fuel Efficiency with Advanced Lean-Burn Control
Outboard motors are frequently operated at cruising speed, where speed is maintained at around 50% to 80% of full-throttle speed. ECOmo is a lean-burn control technology that improves fuel efficiency in this cruising range, compared to conventional outboard motors, by reducing fuel injection amounts below the theoretical optimal amounts.
Models equipped with an oxygen sensor use Honda’s unique oxygen feedback control to achieve more precise lean-burn control and greater fuel efficiency.

■ECOmo-equipped models: BF40–BF350, BFP60 (as of March 2024)
Boosted Low Speed Torque (BLAST): Improving Initial Acceleration
BLAST is Honda’s unique air-fuel ratio and ignition-timing technology developed to improve the fun of boating. Without sufficient power (torque) during initial acceleration, a boat’s bow will lift and stay up without entering the planing mode, where water resistance is reduced and fuel efficiency is improved.
BLAST controls the air-fuel ratio to maximize torque during full-throttle acceleration and, in conjunction with this, it also improves torque through spark-advance control to adjust the ignition timing to near the knocking limit. This technology improves initial acceleration performance to reduce the time required to move to planing mode. As a result, BLAST enables boat operators to experience the joy of boating while achieving outstanding fuel efficiency and environmental performance.
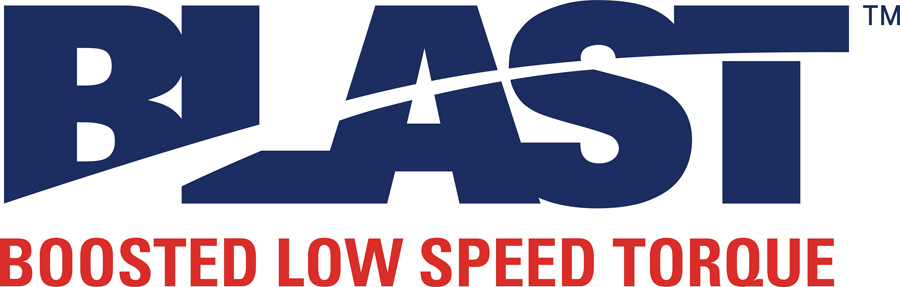
Controlling Air-fuel Ratio
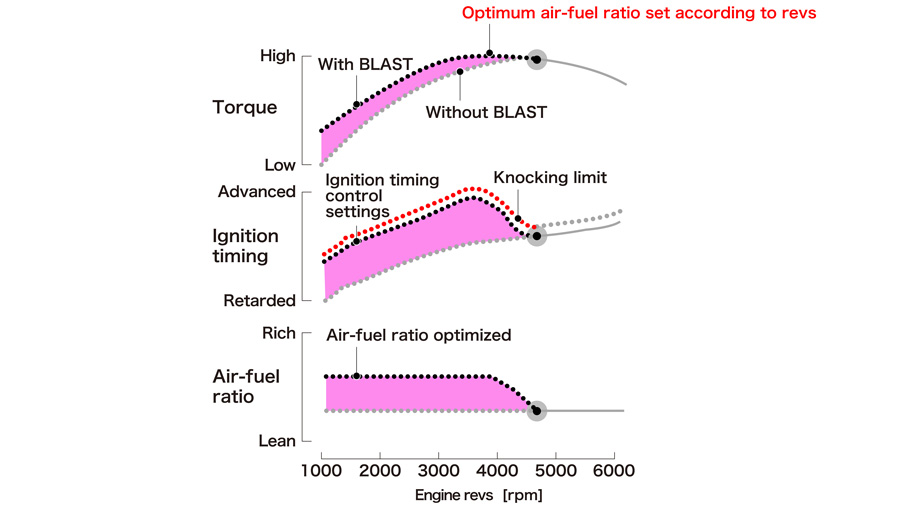
■The name BLAST also conveys the image of explosive and thrilling acceleration.
■BLAST-equipped models: BF40–BF350, BFP60 (as of March 2024)
Variable Valve Timing and Lift Electronic Control (VTEC): Delivering High Torque from Low to High RPM Ranges
While power is important at high speeds due to the resistance of the boat in water, resilience is also required at trolling speeds and other speeds close to idling.
VTEC is a unique Honda technology that employs a variable valve timing and lift control mechanism to improve intake efficiency by adjusting valve opening and timing when the engine speed increases. Delivering high torque in all engine rpm ranges for powerful acceleration from low speeds and steady acceleration through to high speeds, VTEC contributes to better fuel efficiency.

VTEC in Operation
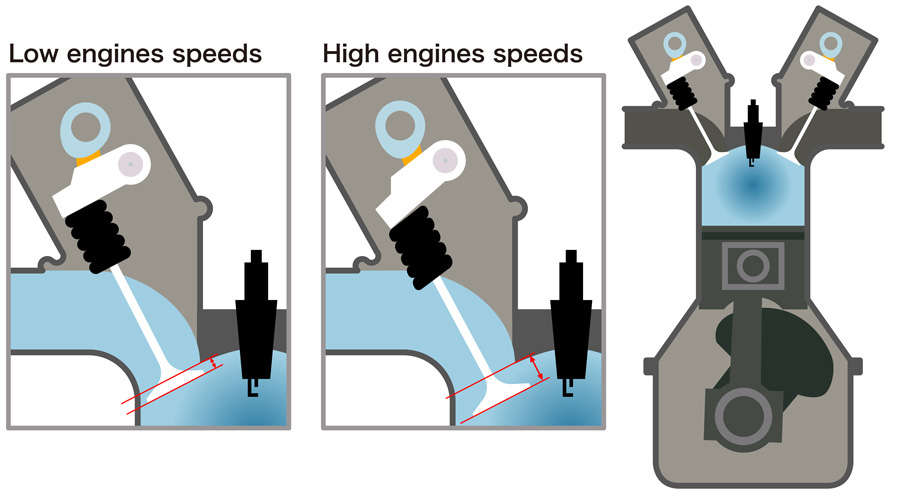
■VTEC-equipped models: BF90, BF100, BF150, BF225, BF250, BF350 (as of March 2024)
Programmed Fuel Injection (PGM-FI): Fuel Injection Optimized to the State of the Engine
PGM-FI is an electronic control fuel injection system that uses an engine control unit (ECU) to calculate and supply optimal fuel injection amounts according to engine operating data collected from various sensors. Waste-free and efficient use of fuel in this way achieves outstanding environmental performance and good fuel efficiency. It also enables smooth engine startup regardless of the season or weather, including on cold mornings
When docking at piers and at other times, boats need to be stopped by shifting the outboard motor between forward and reverse gears. PGM-FI also uses unique outboard motor controls to support such modes of operation, which are different from the operation of cars and motorcycles.

System Illustration
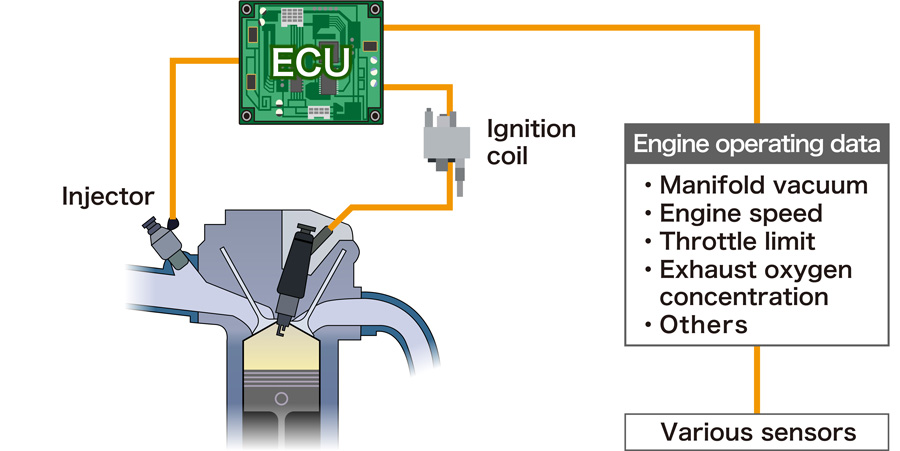
■PGM-FI-equipped models: BF40–BF350, BFP60 (as of March 2024)
Supplying the World with Outboard Motors, with Many High-Quality Models Produced at Hosoe Outboard Engine Plant
While the small 2 HP to 6 HP models are produced elsewhere, Hosoe Outboard Engine Plant is responsible for production and global supply, including to Japan, of 21 outboard motor models*1 ranging from 8 HP to 350 HP. Of those, the 20 models up to and including 250 HP are all manufactured on a single production line. In a single month, the line can produce all of these models, with the order of models changing according to horsepower.
When changing models, the attachments for each model are also changed, requiring line speed to be adjusted. This process improves production quality, while workers skilled on a range of models, together with effectively positioned support personnel, work to maintain that high level of production quality.
*1 As of March 2024 / Small 2 HP to 6 HP outboard motor models are produced by Honda Power Products (China) Co., Ltd.
Dedicated BF350 Cell Production Line Designed for Large, Sophisticated Outboard Motors
Honda’s flagship BF350 outboard motor is assembled by a small team of workers on a dedicated cell production line. Incorporating a range of advanced equipment, the production system developed for the line supports high-performance, high-functionality models.
Divided mainly into an engine area and a frame area, each area is comprised of four production processes*2. With each worker being responsible for multiple tasks, a proprietary work support system was developed to ensure work reliability. Details of each task are displayed on a computer screen, with torque wrenches and other tools connected to the system to provide information on tightening torque and other decisions.
The outboard motors are quite large as well, at over two meters high, so a range of dedicated work jigs have also been developed, such as dedicated trolleys for raising and lowering the motors.
*2 Piston, cylinder head and other sub-assemblies are completed in engine area upstream processes
For many years, Honda has produced high-quality, economical four-stroke outboard motors that are friendly to both the environment and to people. Focusing on this basic concept, it aims to continue providing the world’s most people- and environment-friendly mobility on the water to ever more people going forward.
To this end, Honda will drive a range of initiatives to create people-friendly technologies and environmentally friendly technologies. The former will include research and development of not only outboard motors, but automated docking technologies with a view to automated navigation as well, and the latter will include research and development of electric propulsion systems, starting with small outboard motor models.